Shell煤气化耐硫变换工艺流程研究
Shell煤气化技术

Shell煤气化技术吴迎(中国五环化学工程公司,武汉 430079) 2006-08-041 概述谢尔粉煤加压气化工艺(简称Shell煤气化工艺),是荷兰壳牌公司开发的一种先进的煤气化技术,与先进的德士古(Texaco)水煤浆加压气化技术相比,Shell煤气化具有对煤质要求低,合成气中有效组分 (CO+H2>90%)含量高,原煤和氧气消耗低,环境污染小和运行费用低等特点,已成为近年来国内外设计单位和生产厂家首选的气化工艺。
我国正在设计和建设中的洞庭氮肥厂、柳州化学工业公司等厂家,已将该技术应用于合成氨生产。
湖北化肥厂和安庆化肥厂也准备将该技术用于本厂的“油改煤”制氨流程。
湖北双环科技股份有限公司引进Shell公司基础设计,由我院做工程设计,正在建设规模为800t/d(相当于20万t/a)的工业示范装置,即将投运。
Shell煤气化技术是我国建设大型煤化工项目或中氮肥改造的主要方向。
Shell工艺虽属先进,但投资偏高,一般企业不易接受,建议尽快实现关键技术和设备的国产化。
2 Shell煤气化工艺原理、技术特点及主要设备2.1 Shell煤气化工艺原理Shell煤气化过程是在高温高压下进行的,Shell煤气化属气流床气化。
粉煤、氧气及水蒸汽在加压条件下并流进入气化炉,在极为短暂的时间(3~10s)内,完成升温、挥发分脱除、裂解、燃烧及转化等一系列物理和化学过程,其工艺流程如图1所示,气化工艺指标如表1所示。
2.2 技术特点a.煤种适应性广。
从无烟煤、烟煤、褐煤到石油焦化均可气化,对煤的灰熔融性适应范围宽,即使高灰分、高水分、高含硫量的煤种也同样适应。
b.气化温度约1 600℃,碳转化率高达99%以上,产品气体洁净,不含重烃,甲烷含量低,煤气中有效气体(CO+H2)高达90%以上。
c.氧耗低,单炉生产能力大。
氧气消耗低,比水煤浆气化工艺低15%~25%,因而配套的空分装置投资相对降低;目前已投入运转的单炉气化压力3.0MPa,日处理煤量已达2000t,因此,单炉生产能力大,目前更大规模的装置正在工业化。
Shell炉煤气化工艺介绍

Shell炉煤气化工艺介绍目录1.概述1.1.发展历史1.2. Shell炉煤气化工艺主要特点2.工艺流程2.1. Shell炉气化工艺流程简图2.2.Shell炉气化工艺流程简述3.气化原理3.1粉煤的干燥及裂解与挥发物的燃烧气化3.2.固体颗粒与气化剂(氧气、水蒸气)间的反应3.3.生成的气体与固体颗粒间的反应3.4.反应生成气体彼此间进行的反应4.操作条件下对粉煤气化性能的影响4.1气化压力对粉煤气化性能的影响4.2氧煤比对粉煤气化性能的影响4.3蒸汽煤比对粉煤气化性能的影响4.4.影响加压粉煤气化操作的主要因素4.5煤组分变化的影响4.6 除煤以外进料“质量”变化的影响5.工艺指标6.Shell炉气化工艺消耗定额及投资估算7. 环境评价1.概述1.1.发展历史Shell煤气化工艺(Shell Coal Gasfication Process)简称SCGP,是由荷兰Shell国际石油公司(Shell International Oil Products B. V.)开发的一种加压气流床粉煤气化技术。
Shell煤气化工艺的发展主要经历了如下几个阶段。
(l)概念阶段20世纪70年代初期的石油危机引发了Shell公司对煤气化的兴趣,1972年Shell公司决定开发煤气化工艺时,对所开发的工艺制定了如下标准:①对煤种有广泛的适应性,基本可气化世界上任何煤种;②环保问题少,有利于环境保护;③高温气化,防止焦油和酚等有机副产品的生成,并促进碳的转化;④气化装置工艺及设备具有高度的安全性和可靠性;⑤气化效率高,单炉生产能力大。
根据上述原则,通过固定床、流化床和气流床三种不同连续气化工艺的对比,对今后煤气化工艺的开发形成了如下基本概念:①采用加压气化,设备结构紧凑,气化强度大;②选用气流床气化工艺,生产能力大,气化炉结构简单;③采用纯氧气化,气化温度高,气化效率高,合成气中有效气CO十H2含量高; ④熔渣气化、冷壁式气化炉,熔渣可以保护炉壁,并确保产生的废渣无害,⑤对原料煤的粒度无特殊要求,干煤粉进料,有利于碳的转化。
Shell 煤气化耐硫变换工艺流程研究(整理)
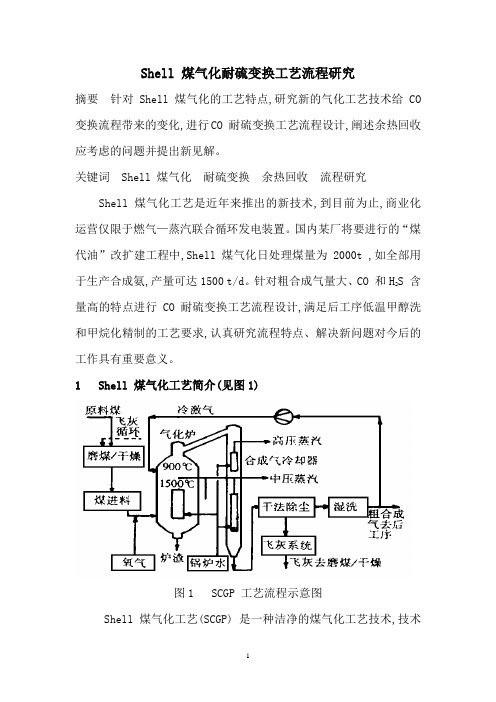
Shell 煤气化耐硫变换工艺流程研究摘要针对Shell 煤气化的工艺特点,研究新的气化工艺技术给CO 变换流程带来的变化,进行CO 耐硫变换工艺流程设计,阐述余热回收应考虑的问题并提出新见解。
关键词Shell 煤气化耐硫变换余热回收流程研究Shell 煤气化工艺是近年来推出的新技术,到目前为止,商业化运营仅限于燃气—蒸汽联合循环发电装置。
国内某厂将要进行的“煤代油”改扩建工程中,Shell 煤气化日处理煤量为2000t ,如全部用于生产合成氨,产量可达1500 t/d。
针对粗合成气量大、CO 和H2S 含量高的特点进行CO 耐硫变换工艺流程设计,满足后工序低温甲醇洗和甲烷化精制的工艺要求,认真研究流程特点、解决新问题对今后的工作具有重要意义。
1 Shell 煤气化工艺简介(见图1)图1 SCGP 工艺流程示意图Shell 煤气化工艺(SCGP) 是一种洁净的煤气化工艺技术,技术开发始于70 年代初期,历经阿姆斯特丹中试装置、汉堡示范装置、休斯敦示范厂的多年运营, 于1998 年1 月1 日在荷兰的Demkolec 工厂实现了整体煤气化燃气—蒸汽联合循环发电(ICGCC) 的商业化运行,气化装置日处理煤2000t 。
SCGP 以干煤粉为原料、纯氧和蒸汽为气化剂,液态排渣,属加压气流床气化。
经干燥后的煤粉用N2加压输送,与氧气和蒸汽一起送入气化炉,在3.5~4.0MPa 压力和1400~1700 ℃的温度范围内发生化学反应。
此操作温度使煤所含灰分熔化并滴到气化炉底部,变成一种玻璃状的炉渣排出,炉渣中C 含量小于0.5%。
在此高温气化下,碳转化率达99 %以上,有效气体(CO+H2) 含量高( ≥90%) ,CO2含量低(1.5%~2.0%) ,CH4极少(50~100μL/L) ,而有害的副产品如酚类、焦油等在此温度下被防止形成。
原煤中的硫在粗合成气中大多H2S 的形式存在,另有少量的COS ,总硫体积含量约为1.5%(原料中硫的质量含量≥5%) 。
净化-22-低水气比耐硫变换新工艺在Shell粉煤气化装置上.
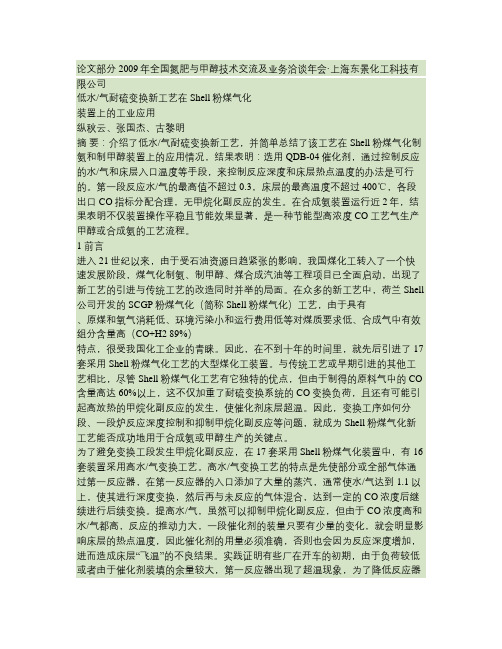
论文部分 2009年全国氮肥与甲醇技术交流及业务洽谈年会·上海东景化工科技有限公司低水/气耐硫变换新工艺在Shell粉煤气化装置上的工业应用纵秋云、张国杰、古黎明摘要:介绍了低水/气耐硫变换新工艺,并简单总结了该工艺在Shell粉煤气化制氨和制甲醇装置上的应用情况,结果表明:选用QDB-04催化剂,通过控制反应的水/气和床层入口温度等手段,来控制反应深度和床层热点温度的办法是可行的。
第一段反应水/气的最高值不超过0.3,床层的最高温度不超过400℃,各段出口CO指标分配合理,无甲烷化副反应的发生。
在合成氨装置运行近2年,结果表明不仅装置操作平稳且节能效果显著,是一种节能型高浓度CO工艺气生产甲醇或合成氨的工艺流程。
1 前言进入21世纪以来,由于受石油资源日趋紧张的影响,我国煤化工转入了一个快速发展阶段,煤气化制氨、制甲醇、煤合成汽油等工程项目已全面启动,出现了新工艺的引进与传统工艺的改造同时并举的局面。
在众多的新工艺中,荷兰Shell 公司开发的SCGP粉煤气化(简称Shell粉煤气化)工艺,由于具有、原煤和氧气消耗低、环境污染小和运行费用低等对煤质要求低、合成气中有效组分含量高(CO+H2 89%)特点,很受我国化工企业的青睐。
因此,在不到十年的时间里,就先后引进了17套采用Shell粉煤气化工艺的大型煤化工装置。
与传统工艺或早期引进的其他工艺相比,尽管Shell粉煤气化工艺有它独特的优点,但由于制得的原料气中的CO 含量高达60%以上,这不仅加重了耐硫变换系统的CO变换负荷,且还有可能引起高放热的甲烷化副反应的发生,使催化剂床层超温。
因此,变换工序如何分段、一段炉反应深度控制和抑制甲烷化副反应等问题,就成为Shell粉煤气化新工艺能否成功地用于合成氨或甲醇生产的关键点。
为了避免变换工段发生甲烷化副反应,在17套采用Shell粉煤气化装置中,有16套装置采用高水/气变换工艺。
高水/气变换工艺的特点是先使部分或全部气体通过第一反应器,在第一反应器的入口添加了大量的蒸汽,通常使水/气达到1.1以上,使其进行深度变换,然后再与未反应的气体混合,达到一定的CO浓度后继续进行后续变换。
Shell粉煤气化_耐硫变换工艺及其催化剂

引言Shell粉煤加压气化工艺(简称Shell煤气化工艺)是荷兰壳牌公司于1972年着手开发、1993年实现工业化的一种新型煤气化技术,该技术具有对煤质要求低、工艺气中有效组分(CO+H2>89%)含量高、原煤和氧气消耗低、环境污染小等特点,在不到十年的时间里,我国就相继引进了20套这种粉煤气化工艺,将该技术用于合成氨、甲醇工程。
在我国着手引进Shell煤气化工艺之前,该技术只是在联合发电装置上有工业化应用的业绩,将该技术应用于氨、甲醇和氢的生产过程中,面临很多困难,首先对变换工艺流程的设计提出了新的难题,因为传统和早先引进的气化工艺制得的原料气中CO体积分数最高不超过48%,而粉煤气化制的工艺气中的CO体积分数高达65%以上,这不仅加重了耐硫变换系统的CO变换负荷,而且还有可能引起高放热的甲烷化副反应,使催化剂床层“飞温”。
因此,如何在不发生甲烷化副反应的前提下进行CO的变换反应,成为该气化工艺能否成功地用于合成氨或甲醇生产的关键。
为了解决这一难题,我国的科研或设计部门开发了与之配套的2种耐硫变换工艺,即:高水/气比变换工艺和低水/气比变换工艺。
目前这2种工艺都已经有工业运行业绩,为我国选用粉煤气化制气的煤化工装置的开车积累了宝贵的经验。
笔者根据近年来对Shell粉煤气化-高浓度CO耐硫变换工艺的研究和为厂家开车服务的经历,坦言该工艺目前还存在的一些问题,并介绍了Shell粉煤气化-低水/气比耐硫变换新工艺的特点和工业运行业绩,期望为业界同行提供参考。
1高水/气比耐硫变换工艺和低水/气比耐硫变换工艺简介在我国引进的Shell粉煤气化制氨或制甲醇的装置中,主要采用高水/气比和低水/气比两种变换工艺。
水/气比既是完成变换反应的基本保证,也是衡量变换工艺优劣的一个重要经济指标。
水/气比低,变换反应深度达不到要求;同时,过低的水/气比还可能引发高放热的甲烷化副反应发生。
水/气比过高,将会增加催化剂床层阻力、并使CO停留时间缩短,导致CO变换率下降,同时也会加重余热回收设备的负荷;另外,当原料煤中的硫化物含量较低时,高水/气比还可能会导致催化剂因发生反硫化反应而失活。
shell煤气化各岗位工艺流程

shell煤气化各岗位工艺流程U-1100磨煤及干燥工艺流程煤流程:原煤和石灰石用皮带从电厂送至本工段的V1101碎煤仓和石灰石仓V1102,再通过称重给料机X1101和X1106计量后送至微负压的磨煤机A1101进行碾磨,并被热风炉F1101送过来的189℃的热风所干燥。
在磨机上部的旋转分离器S1102的作用下,温度为105℃、粒度为10—90微米的煤粉和热气一起从磨机顶部出来,被送至粉煤袋式过滤器S1103(大布袋),在此,煤粉被收集下来,分别经旋转给料机X1105和螺旋输送机X1102、X1104送至粉煤贮仓V1201。
热风流程:热气从大布袋S1103上部出来,经循环风机K1102输送至热风炉F1101,用合成气(原始开车时用柴油)将其从105℃加热至189℃,送往磨煤机A1101,然后和煤粉一起进入大布袋,如此循环。
为避免整个热气循环回路中水分的聚集,根据水分分析数据自动从11FV0110处加入污氮降低其露点,如果回路压力上升,部分热气自动从11PV0109A处放空。
如果系统O2含量超标,污氮就会从11FV0105或11FV0106处加入。
U-1200煤加压进料系统工艺流程粉煤从粉煤贮仓V1201通过重力作用进入煤粉锁斗V1204,煤粉锁斗V1204充满后,将其与所有的低压设备隔离,用高压氮气将其压力升至与煤进料罐V1205平衡,再打开煤锁斗与煤进料罐之间平衡管线的连通阀,一旦煤进料罐V1205达到低料位,打开锁斗排料阀12XV0131/0231/0132/0232卸料。
卸料完毕后将锁斗与煤进料罐隔离,将压力分三次卸至接近常压,然后打开锁斗上部的进料阀12XV0133/0233/0123/0223,接受粉仓的煤粉,锁斗充装完毕后,再次充压,等待下一次的卸料信号。
煤进料罐内温度为80℃、压力为4.2MPa的煤粉在煤循环/给料程序13KS0011/12/13/14的控制下,经过计量和调节后分别进入烧咀。
Shell煤气化技术综述_宋超

Shell 煤气化技术综述宋超(江苏中能硅业科技发展有限公司江苏徐州221000)一、概述Shell煤气化技术是在原K-T气流床煤气化技术的基础上改进而来。
将粒度为100目、水分<10%的煤粉,纯度为>99%的氧气和水蒸气在喷嘴处混合进入煤气化炉进行气化反应,炉内的气化压力为2.0~4.0MPa,温度为1400~1600℃,气化生成的有效煤气成分含量为90%~94%,碳的转化率约为99%(飞灰再循环的条件下)。
二、Shell 煤气化反应原理Shell煤气化反应原理与K-T常压粉煤气化相同,是以干煤粉作为原料,氧气和水蒸气作为气化剂在气流床内进行的气-固两相流态化反应。
干煤粉由氮气或二氧化碳吹入气化炉,气化炉内的气化反应温度很高,在有氧存在的条件下,以燃烧反应为主,在氧气反应完成后进入气化反应阶段,物料在炉内的停留时间一般为3~10s,气化反应很快就达到平衡。
气化产生的粗煤气经粗煤气冷却器冷却后,最终形成以CO、H2为主的煤气。
反应中产生的煤灰熔化后以液态的形式排出气化反应炉。
带粗煤气冷却器(废热锅炉)流程的特点如下:1.结构复杂,昂贵。
1台废锅,如2000t/d要多1个亿的投资。
2.若用于化工,则后续的调比过程需要大量蒸汽,废锅产生的蒸汽约60-70%用于调比,真正能量回收的好处不大,用高投资的废锅而取得的效益不大。
三、原料要求Shell煤气化工艺对煤种有广泛的适应性,由于采用粉煤进料和高温、加压气化,故对煤的粘结性、机械强度、水分、灰分、挥发分等要求不是十分严格,但从技术角度考虑仍有一定要求。
水分(收到基水分):褐煤6%~10%,其它1%~6%,灰分干基<24%,灰熔点FT<1350℃,粒度<0.15mm的>90%。
1.煤的灰熔点是加压干粉气化选择原料的主要条件,一般选择灰熔融流动温度FT在1400℃以下的烟煤,FT超过1500℃的煤不宜采用。
2.煤的活性要好,一般以烟煤和褐煤为主。
3.灰渣的粘温特性碱性组分含量高,一般碱/酸应大于0.3。
Shell粉煤气化低水气比耐硫变换工艺运行总结

迅 速暴涨 到 60o 超 过设备 的设计 温度 (8 , 0 C, 45o c)
严重 威胁设 备 的安全运行 。
1 高水气比耐硫 变换工艺的运行
1 1 高水 气 比工 艺 的设 计思路 . 先将 部 分气 体通 过 第一 变 换炉 , 在一 变之 前 并
122 超 温 、 .. 高水 气 比条件 下 , 化 剂 寿命 急剧 缩 催
摘
要: 分析 S e 粉煤 气化高水气比耐硫 变换X 艺在 生产 中遇到 的频繁 超温 、 hl l - 蒸汽 消耗 高、 艺冷 凝液量 大等问 工
题 , 结 工 业 生产 中针 对 高 水 气 比 工 艺进 行 的技 改措 施 。介 绍 了低 水 气 比 耐硫 变换 工 艺在 Se 粉 煤 气化 高 C 总 hl l O煤
二、 第三变 换 炉 的 反 应 条 件 , 证 变 换 单 元 的变 换 保
6 h 的办 法提 高 水 气 比。由 此也 造 成 了床 层 阻 0t ) /
力增 加 , 到 7 达 0~10 k a 0 P 。在 高温 、 高水气 比 、 高压
差 的操作条 件下 , 化剂性 能快速 衰退 , 催 使用寿命 急
剧缩 短 。一 变人 口温度 由开车初 期的 2 0~ 7 6 2 0℃ , 经过 不到 1 0 0h的运行 和十余次 的开停 车 , 变人 0 一 口温 度 已经 提升 至 2 5~30 q 才 能 达到 催 化剂 的 9 0 C
率、 满足 甲醇合成 单元 的 H C要 求 。同时通 过控 制 /
壳牌 ( hl 粉 煤 加压 气 化 工 艺 是 一 种 先进 的 Se ) 1
反 应推 动力太 大 , 因此 一变 催 化剂 的装 填量 必 须准
利用Shell粉煤气化技术实现合成氨原料
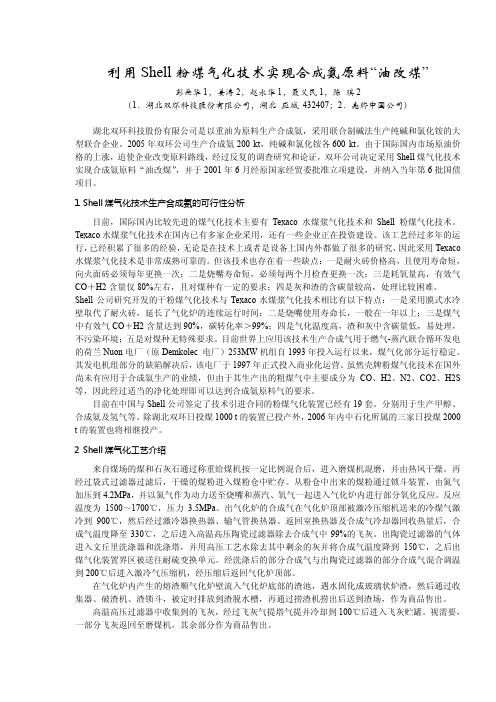
利用Shell粉煤气化技术实现合成氨原料“油改煤”彭爱华1,姜涛2,赵永华1,聂义民1,陈琪2(1.湖北双环科技股份有限公司,湖北应城 432407;2.壳牌中国公司)湖北双环科技股份有限公司是以重油为原料生产合成氨,采用联合制碱法生产纯碱和氯化铵的大型联合企业。
2005年双环公司生产合成氨200 kt,纯碱和氯化铵各600 kt。
由于国际国内市场原油价格的上涨,迫使企业改变原料路线,经过反复的调查研究和论证,双环公司决定采用Shell煤气化技术实现合成氨原料“油改煤”,并于2001年6月经原国家经贸委批准立项建设,并纳入当年第6批国债项目。
1 Shell煤气化技术生产合成氨的可行性分析目前,国际国内比较先进的煤气化技术主要有Texaco水煤浆气化技术和Shell粉煤气化技术。
Texaco水煤浆气化技术在国内已有多家企业采用,还有一些企业正在投资建设。
该工艺经过多年的运行,已经积累了很多的经验,无论是在技术上或者是设备上国内外都做了很多的研究,因此采用Texaco 水煤浆气化技术是非常成熟可靠的。
但该技术也存在着一些缺点:一是耐火砖价格高,且使用寿命短,向火面砖必须每年更换一次;二是烧嘴寿命短,必须每两个月检查更换一次;三是耗氧量高,有效气CO+H2含量仅80%左右,且对煤种有一定的要求;四是灰和渣的含碳量较高,处理比较困难。
Shell公司研究开发的干粉煤气化技术与Texaco水煤浆气化技术相比有以下特点:一是采用膜式水冷壁取代了耐火砖,延长了气化炉的连续运行时间;二是烧嘴使用寿命长,一般在一年以上;三是煤气中有效气CO+H2含量达到90%,碳转化率>99%;四是气化温度高,渣和灰中含碳量低,易处理,不污染环境;五是对煤种无特殊要求。
目前世界上应用该技术生产合成气用于燃气-蒸汽联合循环发电的荷兰Nuon电厂(原Demkolec 电厂)253MW机组自1993年投入运行以来,煤气化部分运行稳定。
其发电机组部分的缺陷解决后,该电厂于1997年正式投入商业化运营。
浅析 SHELL 煤气化技术
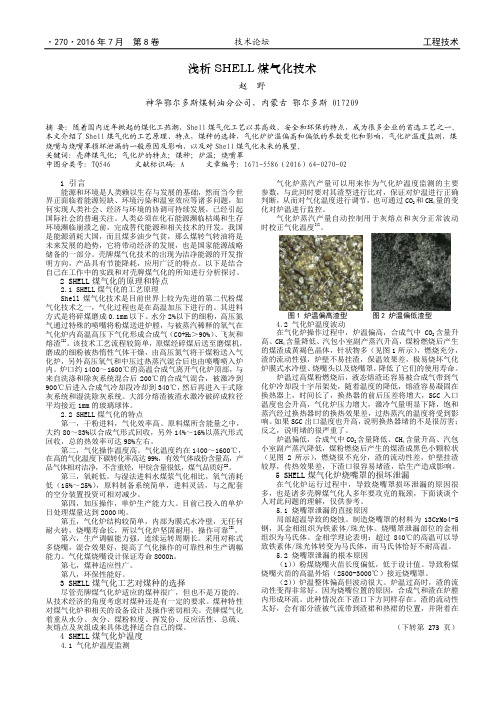
·270·2016年7月 第8卷技术论坛工程技术浅析SHELL煤气化技术赵 野神华鄂尔多斯煤制油分公司,内蒙古 鄂尔多斯 017209摘 要:随着国内近年掀起的煤化工热潮,Shell煤气化工艺以其高效、安全和环保的特点,成为很多企业的首选工艺之一。
本文介绍了Shell煤气化的工艺原理、特点,煤种的选择,气化炉炉温偏高和偏低的参数变化和影响,气化炉温度监测,煤烧嘴与烧嘴罩损坏泄漏的一般原因及影响,以及对Shell煤气化未来的展望。
关键词:壳牌煤气化;气化炉的特点;煤种;炉温;烧嘴罩中图分类号:TQ546 文献标识码:A 文章编号:1671-5586(2016)64-0270-021 引言能源和环境是人类赖以生存与发展的基础,然而当今世界正面临着能源短缺、环境污染和温室效应等诸多问题,如何实现人类社会、经济与环境的协调可持续发展,已经引起国际社会的普遍关注。
人类必须在化石能源濒临枯竭和生存环境濒临崩溃之前,完成替代能源和相关技术的开发。
我国是能源消耗大国,而且煤多油少气贫,那么煤转气转油将是未来发展的趋势,它将带动经济的发展,也是国家能源战略储备的一部分。
壳牌煤气化技术的出现为洁净能源的开发指明方向,产品具有节能降耗,应用广泛的特点。
以下是结合自己在工作中的实践和对壳牌煤气化的所知进行分析探讨。
2 SHELL煤气化的原理和特点2.1 SHELL煤气化的工艺原理Shell煤气化技术是目前世界上较为先进的第二代粉煤气化技术之一,气化过程也是在高温加压下进行的。
其进料方式是将碎煤磨成0.1mm以下、水分2%以下的细粉,高压氮气通过特殊的喷嘴将粉煤送进炉膛,与被蒸汽稀释的氧气在气化炉内高温高压下气化形成合成气(CO+H2>90%)、飞灰和熔渣[1]。
该技术工艺流程较简单,原煤经碎煤后送至磨煤机,磨成的细粉被热惰性气体干燥,由高压氮气将干煤粉送入气化炉,另外高压氧气和中压过热蒸汽混合后也由喷嘴喷入炉内。
Shell粉煤气化工艺运行问题探讨及改进思路
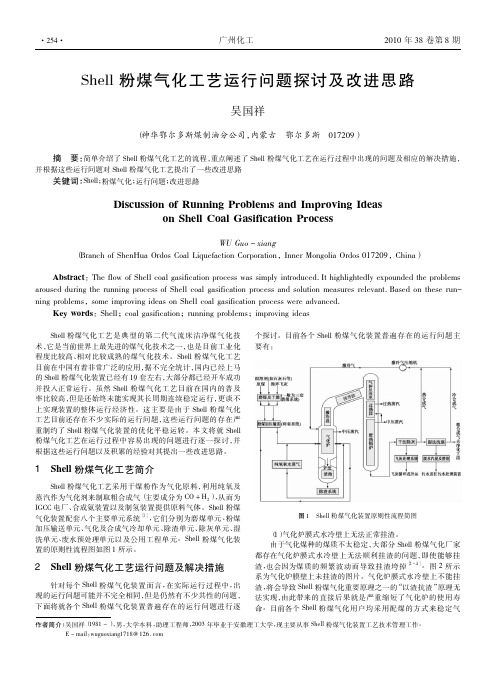
Shell 粉煤气化工艺运行问题探讨及改进思路吴国祥(神华鄂尔多斯煤制油分公司,内蒙古鄂尔多斯017209)摘要:简单介绍了Shell 粉煤气化工艺的流程,重点阐述了Shell 粉煤气化工艺在运行过程中出现的问题及相应的解决措施,并根据这些运行问题对Shell 粉煤气化工艺提出了一些改进思路关键词:Shell ;粉煤气化;运行问题;改进思路Discussion of Running Problems and Improving Ideason Shell Coal Gasification ProcessWU Guo -xiang(Branch of ShenHua Ordos Coal Liquefaction Corporation ,Inner Mongolia Ordos 017209,China )Abstract :The flow of Shell coal gasification process was simply introduced.It highlightedly expounded the problems aroused during the running process of Shell coal gasification process and solution measures relevant.Based on these run-ning problems ,some improving ideas on Shell coal gasification process were advanced.Key words :Shell ;coal gasification ;running problems ;improving ideas作者简介:吴国祥(1981-),男,大学本科,助理工程师,2003年毕业于安徽理工大学,现主要从事Shell 粉煤气化装置工艺技术管理工作。
浅谈Shell煤气化技术

化工技术与开发第40卷我国是一个多煤少油的国家,煤炭资源丰富,原煤产量居世界第一位[1~2]。
在我国,煤炭是发电、化肥、甲醇等能源转化工业的主要原料和燃料,煤炭的生产和消费占一次能源构成的75%[3~4]。
然而人类对能源的需求快速增长,以化石燃料为代表的传统能源日趋枯竭,使得能源供应日益紧张[5]。
同时,能源利用过程中排放的污染物,如粉尘、二氧化硫、氮氧化合物、碳氢化合物、有毒金属化合物、温室气体等,正在急剧破坏地球的生态平衡和人类自身的生存环境。
化石燃料中煤的储量大、价格低廉、供应稳定,但直接燃煤带来的严重环境污染是一个不容忽视的问题。
因此,各国政府在考虑利用储量丰富的煤炭资源时,特别重视洁净煤技术的研究与开发工作[6]。
长期以来,我国煤炭综合利用技术落后,煤炭利用率低下,主要以直接燃烧为主。
据统计在排放的大气污染物中,90%的SO 2、85%的CO 2、70%的烟尘来自煤燃烧[7~8]。
因此,为提高煤炭综合利用率,缓解因煤炭利用所引起的环境污染问题,必须加强洁净煤技术研究。
煤气化技术是煤炭洁净技术转化的核心技术之一,是发展煤化学品(氨,甲醇,二甲醚等)、先进IGCC 发电、多联产系统、制氢、燃料电池等过程工业的基础。
1常见煤气化技术比较煤气化就是以煤炭为原料,采用空气、氧气、CO 2和水蒸汽为气化剂,在一定温度和压力下,通过不完全的燃烧过程,将煤中的固定碳转化成可燃性气体(有效气体成分CO 、H 2、CH 4及副产物CO 2、H 2O 等)的过程[9]。
目前新一代煤气化工艺对煤种适应性广,气化压力高,生产能力大,气化效率高,污染少。
具有代表性的有Texaco (德士古)水煤浆气化工艺、GSP 气化技术、Shell (壳牌)气化技术[10]。
Texaco 水煤浆加压气化炉是两相并流型气化炉,氧气和煤浆通过特制的工艺喷嘴混合后喷入气化炉,在炉内水煤浆和氧气发生不完全氧化还原反应产生水煤气,其反应释放的能量可维持气化炉在煤灰熔点温度以上反应以满足液态排渣的需要。
shell煤气化工艺流程

shell煤气化工艺流程煤气化工艺流程是将煤炭等固体燃料转化为可燃性气体的一种化学过程。
这种工艺流程在煤矿、化工厂和能源生产领域得到广泛应用。
本文将介绍煤气化工艺流程的基本原理和步骤。
1. 煤气化的基本原理煤气化是通过将煤炭等固体燃料暴露在高温和缺氧条件下,使其发生热解反应,生成可燃性气体的过程。
在煤气化过程中,煤炭中的碳氢化合物被分解为一氧化碳、氢气和其他有机物。
2. 煤气化工艺的步骤煤气化工艺通常包括以下几个步骤:2.1 煤炭预处理煤炭预处理包括煤炭的破碎、干燥和粉碎等过程。
这些步骤可以增加煤炭的表面积,提高煤炭与反应介质的接触效果,从而提高煤气化效率。
2.2 煤气化反应煤气化反应是煤气化工艺的核心步骤。
在高温和缺氧条件下,煤炭与反应介质(通常是水蒸气或空气)发生反应。
煤炭中的碳氢化合物被分解为一氧化碳、氢气和其他有机物。
这些反应生成的气体被称为合成气。
2.3 合成气的净化合成气中可能含有杂质如硫化物、氨和灰分等,需要进行净化处理。
净化过程通常包括酸洗、吸附和过滤等步骤,以确保合成气的纯度和稳定性。
2.4 合成气的利用净化后的合成气可以直接用作燃料,也可以进一步转化为其他化学品和燃料。
常见的合成气利用方式包括合成甲醇、合成氨和合成石油等。
3. 煤气化工艺的应用煤气化工艺在能源生产和化工工业中有广泛的应用。
煤气化技术可以将煤炭等固体燃料转化为可燃性气体,提供燃料供给,减少对传统石油和天然气资源的依赖。
同时,煤气化还可以生产有机化学品和石油产品,为化工工业提供原料。
4. 煤气化工艺的优势和挑战煤气化工艺具有以下优势:一是可以利用煤炭等广泛存在的固体燃料资源,减少对传统能源资源的依赖;二是可以减少污染物的排放,提高环境友好性;三是可以生产多种化学品和燃料,提供多样化的产品。
然而,煤气化工艺也面临一些挑战。
首先,煤气化过程需要高温和压力条件,设备成本较高。
其次,煤气化过程中产生的废气和废水需要进行处理和处置,增加了工艺的复杂性和成本。
煤化工技术专业《shell气化的工艺特点和工艺流程》

3设备产气能力高。
由于采用〔3-4MPa〕加压操00t,在同样的生产能力下,shell气化设备尺寸较小,结构紧凑,占
地面积小,相对建设投资也比较低。
德士古气化工
加压操作
艺特点
产气能力提高
shell气化工艺特点
4环境效益好 因为气化在高温下进行,并且原料粒度很小,气化反响进行得较为充分 ,影响环境的副产物很少,属于洁净煤工艺。
干法粉煤进料 气流床粉煤气化
德士古气化工 无烟
艺特点
A煤
Shell气化
工艺技术
褐煤 C
烟煤 B
石油 D焦
shell气化工艺特点
2能源利用率高
工艺采用高温加压气化,气化温度为1400-1600℃,压力为3-4MPa,在此
操作条件下,shell气化工艺的碳转化率高达99%,冷煤气效率为80-85%,合
成气中的有效成分可高达90%以上。
名称
德主要性士能参古数 气化工名称
气化压力/MPa 气化温度/℃
艺特点 3.0-4.0
碳转化率/%
1400-1600
冷煤气效率/%
主要性能参数 约99 80-85
单炉最大投煤量/ (t/d)
合成气耗气量 /(m3/10m3)
2000 330-360
合成气/%
约90
shell气化工艺特点
shell气化属于加压气流床粉煤气化, 以干粉煤进料,纯氧气作为气化剂,液 态排渣,是20世纪末实现工业化的新型 煤气化工艺,是21世纪的煤炭气化主要 开展途径之一。
shell气化工艺特点
1对煤种的适应性广。 由于采用干法粉煤进料以及气流床粉煤气化技术, 能成功处理高灰分、高水分和高硫煤种,理论上从无烟煤、烟煤、褐煤到 石油焦均可气化。
Shell炉煤气化工艺介绍

Shell炉煤气化工艺介绍目录1.概述1.1.发展历史1.2. Shell炉煤气化工艺主要特点2.工艺流程2.1. Shell炉气化工艺流程简图2.2.Shell炉气化工艺流程简述3.气化原理3.1粉煤的干燥及裂解与挥发物的燃烧气化3.2.固体颗粒与气化剂(氧气、水蒸气)间的反应3.3.生成的气体与固体颗粒间的反应3.4.反应生成气体彼此间进行的反应4.操作条件下对粉煤气化性能的影响4.1气化压力对粉煤气化性能的影响4.2氧煤比对粉煤气化性能的影响4.3蒸汽煤比对粉煤气化性能的影响4.4.影响加压粉煤气化操作的主要因素4.5煤组分变化的影响4.6 除煤以外进料“质量”变化的影响5.工艺指标6.Shell炉气化工艺消耗定额及投资估算7. 环境评价1.概述1.1.发展历史Shell煤气化工艺(Shell Coal Gasfication Process)简称SCGP,是由荷兰Shell国际石油公司(Shell International Oil Products B. V.)开发的一种加压气流床粉煤气化技术。
Shell煤气化工艺的发展主要经历了如下几个阶段。
(l)概念阶段20世纪70年代初期的石油危机引发了Shell公司对煤气化的兴趣,1972年Shell公司决定开发煤气化工艺时,对所开发的工艺制定了如下标准:①对煤种有广泛的适应性,基本可气化世界上任何煤种;②环保问题少,有利于环境保护;③高温气化,防止焦油和酚等有机副产品的生成,并促进碳的转化;④气化装置工艺及设备具有高度的安全性和可靠性;⑤气化效率高,单炉生产能力大。
根据上述原则,通过固定床、流化床和气流床三种不同连续气化工艺的对比,对今后煤气化工艺的开发形成了如下基本概念:①采用加压气化,设备结构紧凑,气化强度大;②选用气流床气化工艺,生产能力大,气化炉结构简单;③采用纯氧气化,气化温度高,气化效率高,合成气中有效气CO十H2含量高;④熔渣气化、冷壁式气化炉,熔渣可以保护炉壁,并确保产生的废渣无害,⑤对原料煤的粒度无特殊要求,干煤粉进料,有利于碳的转化。
Shell煤气化技术评述
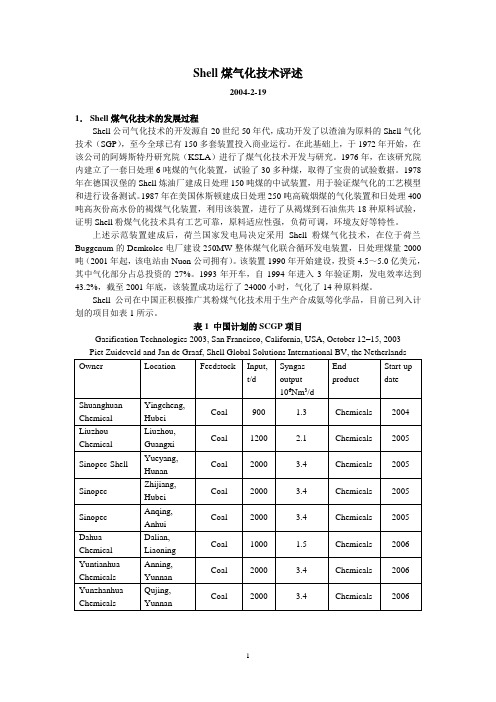
Shell煤气化技术评述2004-2-191.Shell煤气化技术的发展过程Shell公司气化技术的开发源自20世纪50年代,成功开发了以渣油为原料的Shell气化技术(SGP),至今全球已有150多套装置投入商业运行。
在此基础上,于1972年开始,在该公司的阿姆斯特丹研究院(KSLA)进行了煤气化技术开发与研究。
1976年,在该研究院内建立了一套日处理6吨煤的气化装置,试验了30多种煤,取得了宝贵的试验数据。
1978年在德国汉堡的Shell炼油厂建成日处理150吨煤的中试装置,用于验证煤气化的工艺模型和进行设备测试。
1987年在美国休斯顿建成日处理250吨高硫烟煤的气化装置和日处理400吨高灰份高水份的褐煤气化装置,利用该装置,进行了从褐煤到石油焦共18种原料试验,证明Shell粉煤气化技术具有工艺可靠,原料适应性强,负荷可调,环境友好等特性。
上述示范装置建成后,荷兰国家发电局决定采用Shell粉煤气化技术,在位于荷兰Buggenum的Demkolec电厂建设250MW整体煤气化联合循环发电装置,日处理煤量2000吨(2001年起,该电站由Nuon公司拥有)。
该装置1990年开始建设,投资4.5~5.0亿美元,其中气化部分占总投资的27%。
1993年开车,自1994年进入3年验证期,发电效率达到43.2%,截至2001年底,该装置成功运行了24000小时,气化了14种原料煤。
Shell公司在中国正积极推广其粉煤气化技术用于生产合成氨等化学品,目前已列入计划的项目如表1所示。
表1 中国计划的SCGP项目Gasification Technologies 2003, San Francisco, California, USA, October 12–15, 20032.Shell粉煤气化(SCGP)工艺流程图1 SCGP气化工艺流程示意图激冷气Shell煤气化工艺(SCGP)以干煤粉为原料、纯氧作为气化剂,液态排渣,属加压气流床气化(见图1)。
Shell煤气化工艺讲义
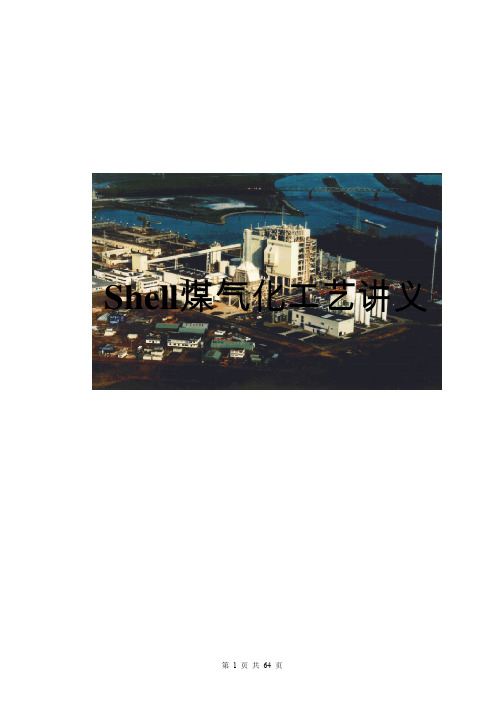
Shell煤气化工艺讲义第一部分煤气化工程的构成 z了解煤气化装置所处的位置及和周边装置的关系z煤气化装置所用的技术和设计基础z选择壳牌煤气化技术的理由1.1 煤气化工程概况: 1.1.1煤气化项目的构成:洞庭煤气化项目是巴陵石化合成氨部原料路线改造工程,同时向双氧水部和己内酰胺部提供氢气源。
项目分为两部分, 一是合资部分,是由中石化(SINOPEC )和壳牌(SHELL CHINA)各出资50%组建的岳阳中石化壳牌煤气化公司,完成煤气化部分;另外是配套部分,由中石化全额出资,完成气体处理和硫回收部分。
图1图1 煤气化项目结构框图合资企业煤气化装置的构成为:卸煤、煤储存及输煤系统由合资企业建设,化装置的设计基础煤气化工艺Shell Coal Gasification Process(SCGP),design coal )2000T ,这是考虑到和荷兰Dem (U-1100),在使用设计煤种产气142000Nm 3/h(H 2+CO)有效由于原料煤由巴陵石化提供,建成后移交巴陵石化管理;磨煤与干燥系统(U-1100),设三条线,按两开一备远行;粉煤加压与给料系统(U-1200)设两条线对应气化炉两对(四个)烧嘴;煤气化及合成气冷却系统(U-1300);除渣系统(U-1400);除灰系统(U-1500);洗涤系统(U-1600);初步水处理系统(U-1700);公用工程系统(U-3***);空分系统(U-4000)。
图 2.煤气化装置方块图。
1.1.2 煤气 煤气化技术采用壳牌粉由壳牌提供基础工艺包 Basic Design and Engineering Package(BDEP),由宁波工程公司做详细设计并进行工程总承包。
装置设计能力为日处理设计煤种(kolec 电厂的煤气化装置设计能力相同,减少技术风险。
向巴陵石化提供142000Nm 3/h(H 2+CO)有效合成气,其中140640 Nm 3/h(H 2+CO)用于合成氨和第三方供氢,剩余部分经过气体处理后返用于煤气化装置;设备设计能力,在使用备用煤(“worst case” coal )时保证产气量142000Nm 3/h(H 2+CO)有效合成气;60%负荷下,产气量为85200 Nm 3/h(H 2+CO)。
shell气化的工艺特点和工艺流程

shell气化的工艺特点和工艺流程The Shell gasification process is a type of advanced technology that converts coal or biomass into syngas, which can be used to produce chemicals, fuels, and electricity. 这种工艺是一种先进技术,可以将煤或生物质转化为合成气,用于生产化学品、燃料和电力。
This process is known for its high efficiency and flexibility, making it a popular choice for industries looking to reduce their carbon footprint and lower their operating costs. 这个过程以高效率和灵活性而闻名,因此受到那些希望减少碳排放和降低运营成本的行业的青睐。
The key feature of Shell gasification technology is the use of a high-temperature, oxygen-starved environment to break down feedstock into syngas. Shell gasification technology has been developed over the years to optimize the production of syngas and minimize the production of waste byproducts. Shell工艺技术的关键特点是利用高温、缺氧环境将原料分解成合成气。
经过多年的发展,Shell气化技术已经得到优化,以最大程度地生产合成气,同时最小化废物副产品的产生。
Shell煤气化工艺的评述和改进意见

Shell煤气化工艺的评述和改进意见作者:唐宏青Shell煤气化过程是目前世界上较为先进的第二代煤气化工艺之一。
按化学工程特征分类,Shell煤气化属气流床气化。
煤粉、氧气及少量水蒸气在加压条件下并流进入气化炉内,在极为短暂的时间内完成升温、挥发分脱除、裂解、燃烧及转化等一系列物理和化学过程,气化产物为以H2和CO 为主的合成气,CO2的含量很少。
1 Shell煤气化技术的发展自20世纪50年代起,壳牌公司就参与了气化技术的开发。
当时,该公司开发了以油为原料的壳牌气化技术(SGP),至今已有150多套装置采用该技术。
在积累了油气化经验后,壳牌公司1972年开始在该公司的阿姆斯特丹研究院(KSLA)进行煤气化技术研究。
1976年,煤气化工艺(SCGP)达到了一定的水平并建立了一座处理煤量为6t/d的试验厂,利用该装置一共试验了30多个不同的煤种。
1978年,在汉堡附近的哈尔堡炼油厂建设了一座处理煤量为150t/d的工厂,公司利用这座装置进行了一系列成功的试验,至1983年该装置停止运转为止,累计运行了6100h,其中包括超过1000h的连续运转,顺利完成了工艺开发和过程优化的任务。
在汉堡中试装置成功运行的基础上,1987年,壳牌公司在美国休斯顿附近的DeerPark石化中心建设了一座规模较大的工厂,这座命名为SCGP 1的示范厂进煤量为每天250t高硫煤或每天400t高湿度、高灰褐煤,共进行了15000h的操作试验。
SCGP 1试验了约18种原料,包括褐煤乃至石油焦。
这些试验结果充分证实壳牌煤气化技术在可靠性、原料灵活性、负荷可调性和环保方面都达到了极高水准,该示范装置的运行是成功的。
1988年,荷兰国家电力局决定由其下属的Demkolec公司在荷兰南部的BuGGenun兴建一座净输出为253MW的煤气化联合循环发电厂(IGCC)。
Shell公司为装置提供专利技术及基础工程设计,其煤气化装置设计能力为单炉日处理煤2000t、气化压力为2.8MPa。
- 1、下载文档前请自行甄别文档内容的完整性,平台不提供额外的编辑、内容补充、找答案等附加服务。
- 2、"仅部分预览"的文档,不可在线预览部分如存在完整性等问题,可反馈申请退款(可完整预览的文档不适用该条件!)。
- 3、如文档侵犯您的权益,请联系客服反馈,我们会尽快为您处理(人工客服工作时间:9:00-18:30)。
Shell 气化炉为水冷壁型式 ,内壁布有水冷却 管 ,副产部分蒸汽 。操作时壁内形成一层渣 ,用 “以渣抗渣”方式保护水冷壁不受侵蚀 。由于不需 要耐火砖绝热层 ,运转周期长 ,可靠性高 ,单炉运 行 ,不需要备用炉 。Shell 煤气化装置能力大 ,气 化压力为 315~410MPa ,单炉煤处理量为 2000 t/ d ,炉子规格为 415 m ,高 1714 m。
体 CO 积 含 CO2
量 CH4 ,
% N2
Ar
H2S/ COS 等
流量/ t·d - 1 摩尔质量/ kg·kmol
温度/ ℃
压力/ MPa
4176 25182 60130 2142 0101 5118 0108 1143 374118 2114 11615 3173
212 变换工艺方案选择 变换工艺方案的选择 ,既要根据 Shell 煤气化
235
115/ < 015
220
表 3 工艺计算条件 ②
入口压力 / 压降 MPa
3171/ 0107 3156/ 0107 3146/ 011
物料名称
温度/ ℃
压力/ MPa
锅炉给水
120
510
副产蒸汽
253
413
补加蒸汽
380
410
上述条件需在流程模拟反复验算后 ,根据 CO 变换反应的平衡浓度及平衡温距等加以调整 。 313 流程初步组织
2) CO 变换是在过量水蒸汽存在下进行的放 热反应 ,工艺气中的湿含量相当高 ,降低反应的起 始温度对化学反应平衡有利 。但当工艺气温度低 到某一程度时可能会达到该压力条件下的露点 。 此时 ,工艺气中会有液滴析出而凝聚于催化剂表 面 ,造成催化剂强度下降 、破裂粉碎 ,引起床层阻 力增加 ,使催化剂活性降低和寿命缩短 。所以 ,催 化剂的操作温度除了要在其本身活性温度范围 内 ,还必须高于气体的露点温度 。从设计角度讲 , 为安全起见 ,通常选择操作温度下限比露点温度 高 25 ℃左右 。
经干燥后的煤粉用 N2 加压输送 ,与氧气和蒸
汽一起送入气化炉 ,在 315~410MPa 压力和 1400 ~1700 ℃的温度范围内发生化学反应 。此操作温 度使煤所含灰分熔化并滴到气化炉底部 ,变成一 种玻璃状的炉渣排出 ,炉渣中 C 含量小于 015 %。 在此高温气化下 ,碳转化率达 99 %以上 ,有效气 体 (CO + H2) 含量高 ( ≥90 %) ,CO2 含量低 (115 % ~210 %) ,CH4 极少 (50~100μL/ L) ,而有害的副 产品如酚类 、焦油等在此温度下被防止形成 。原 煤中的硫在粗合成气中大多以 H2S 的形式存在 , 另有少量的 COS ,总硫体积含量约为 115 % (原料 中硫的质量含量 ≥5 %) 。
1) 补蒸汽 从气 化 来 的 粗 合 成 气 中 水 蒸 汽 含 量 较 少
(4176 %) ,温度较低 (11615 ℃) ,为满足变换反应 的工艺要求 ,需要向粗合成气中补加过热蒸汽 (380 ℃,410MPa) 。入一段炉之前粗合成气是否 需要加热视补蒸汽后的情况而定 。另外 ,入二段 炉之前是采用间接换热方式还是直接激冷 ,要根 据二 、三段 CO 变换反应平衡决定 。
及能耐高硫 、高压 、高水汽分压等优点 ,所以 ,采用 钴钼系宽温耐硫催化剂中变串低变的 CO 变换工 艺路线 ,是顺理成章的选择 。
3 工艺流程组织 311 原则
变换工艺流程的设计是以变换炉的分段及催 化剂的选型为核心 ,结合余热回收进行的 。
1) 根据系统反应的绝热温升 ,为使催化剂在 允许的活性温度范围操作 , 对 于 CO 含 量 高 于 15 %者 ,一般应考虑将变换反应器分为二段或三 段 。尽管 Shell 煤气化送来的粗合成气中 CO 含量 高达 63131 % ,在一段变换 CO 含量降至 10 %以下 时 ,温升将达到 200 ℃左右 。但由于采用了起活 温度低且活性温度范围宽的 QCS 系列钴钼宽温 耐硫催化剂 ,所以将变换反应分为三段 ,使出 CO 变换装置的工艺气中 CO 干基体积最终含量小于 015 %是完全可以达到的 。
的工艺特点 ,也要满足后续甲烷化精制工段的工 艺要求 。
从表 1 中可以看出 ,Shell 煤气化送往变换装 置界 区 的 粗 合 成 气 中 , CO 干 基 体 积 含 量 高 达 63131 % ,如此高的 CO 含量在以往的造气工艺中 是没有先例的 。另外 ,原料煤中的硫含量高 ,使得 粗合 成 气 中 的 H2S 和 COS 体 积 含 量 达 到 约 115 %。如果采用铁络系催化剂 ,高变串中变的工 艺流程 : ①为防止催化剂中毒 ,粗合成气要进行脱 硫 ; ②由于温升的限制 ,变换反应器可能需要四段 甚至五段 ,流程长必然导致换热器数量多 ,换热频 繁 ; ③甲烷化精制工艺要求工艺气中 CO 含量不 能太高 ,否则会消耗过多的原料 H2 并使甲烷化炉 超温 ,而且高变串中变流程 ,CO 干基体积含量只 能降到 3 %左右 。上述 3 点原因决定了不能采用 高变串中变工艺流程 。钴钼系 QCS 系列催化剂 具有起活温度低 、活性温度范围宽 、热稳定性好以
1999
年
大 氮 Large Scale Nitrogenous
肥 Fertilizer
Industry
第 22
卷
第
5
期
Shell 煤气化耐硫变换工艺流程研究
贾丛林
(中国石化集团兰州设计院 ,甘肃兰州 ,730060)
摘要 针对 Shell 煤气化的工艺特点 ,研究新的气化工艺技术给 CO 变换流程带来的变化 ,进行 CO 耐硫 变换工艺流程设计 ,阐述余热回收应考虑的问题并提出新见解 。
1 Shell 煤气化工艺简介 (见图 1)
图 1 SCGP 工艺流程示意图
Shell 煤气化工艺 ( SCGP) 是一种洁净的煤气 化工艺技术 ,技术开发始于 70 年代初期 ,历经阿 姆斯特丹中试装置 、汉堡示范装置 、休斯敦示范厂 的多 年 运 营 , 于 1998 年 1 月 1 日 在 荷 兰 的 Demkolec 工厂实现了整体煤气化燃气 —蒸汽联合 循环发电 ( ICGCC) 的商业化运行 ,气化装置日处 理煤 2000 t 。 SCGP 以干煤粉为原料 、纯氧和蒸汽为气化 剂 ,液态排渣 ,属加压气流床气化 。
340
大 氮 肥
1999 年 第 22 卷
4) 耐硫变换工艺流程设计不是一蹴而就的 。 流程的组织 、各段反应的工艺条件 、换热器和分离 器的数量及位置 、余热回收方式等 ,都是根据合成 氨装置前后工序的工艺特点及要求 ,根据全厂蒸 汽平衡情况 ,结合计算机流程模拟进行反复的局 部调整 ,由简入繁 ,进行多版次的改进而完成的 。 312 工艺计算条件
3) 结合全厂蒸汽平衡情况 ,初步确定的工艺 流程如图 2 所示 。
图 2 Shell 煤气化耐硫变换工艺流程示意图 ①
上述工艺流程中 ,一方面为满足 CO 变换反 应需要补加约 112 t/ h 中压过热蒸汽和淬冷用锅 炉给水 15 t/ h ,另一方面 ,要排放汽提后的 152 ℃ 工艺冷凝 107 t/ h ,这显然是不能接受的 。
3) CO 变换反应是一个大量放热过程 ,变换装 置中存在着数量巨大的高位能和低位能余热 ,对 Shell 煤气化而言更是如此 , 因其粗合成气中的 CO 含量远较其他工艺流程高 。能否合理有效地 利用这些余热 ,直接影响到整个合成氨装置的能 耗。
一段 变 换 将 大 多 数 CO 反 应 掉 , 温 升 高 达 200 ℃。此部分高位能余热可结合全厂蒸汽平衡 情况和变换装置本身的工艺需要加以利用 ,或者 副产中压蒸汽 ,或者过热蒸汽 ,或者将去煤锅炉的 高压锅炉给水预热到更高的温度 。二段至三段之 间的余热可用来预热锅炉给水或工艺冷凝液 。变 换气最终需冷却至 40 ℃以满足后工序低温甲醇 洗的要求 ,为此 ,要设置一台变换气水冷器 。从三 段出口至变换气水冷器 ,未反应的过量水蒸汽在 变换气冷却过程中不断冷凝下来 。大量的低位能 余热除了可副产低压蒸汽外 ,还可将整个装置 (包 括装置外) 的脱盐水从 40 ℃预热到入脱氧槽所需 的温度 。由于此部分余热的温度较低 ,如何利用 好低位能余热颇费思量 。变换装置的能量损失及 消耗主要体现在排出变换装置冷凝液中带走的热 量和循环冷却水的用量上 。
2) 按一段炉入口汽/ 干气 114 进行流程模拟 计算 ,发现二 、三段变换反应平衡温距过小 。三段 出口 CO 含量 0135 %时 ,平衡温距只有 718 ℃,在 催化剂末期难以保证三段出口的 CO 残留量 。在 中压废锅后直接喷入锅炉给水淬冷增湿 ,可提高 CO 变换平衡率 ,并且将工艺气的温度由 280 ℃降 至所设定的二段入口温度 (~235 ℃) 。
311046 342150 373255
25111 26315 27318
从 表 4 可 以 看 出 , 直 接 补 蒸 汽 ( 380 ℃, 410MPa) 后粗合成气的温度高于所设定的一段炉 入口温度 ,故考虑先向过热蒸汽中喷入锅炉水再
与工艺气混合的方案 。蒸汽及锅炉水量由一段炉 入口温度及汽/ 干气 114 来确定 。
收稿日期 :1999 - 03 - 04 。
第5期
贾丛林 1Shell 煤气化耐硫变换工艺流程研究
339
2 变换工艺方案选择 211 界区条件
SCGP 生产的粗合成气经洗涤后送往变换装 置 ,其组成 、温度 、压力等条件如表 1 所示 。
表 1 送往变换装置的粗合成气条件
பைடு நூலகம்
H2O
湿 基
H2
出气化炉的粗合成气温度 1300~1500 ℃,用 循环气体激冷至 900 ℃,然后进入气体冷却器 (即 废锅) 作进一步冷却 ,同时产生高 (中) 压蒸汽 。