芳烃加氢催化剂硫化方案
加氢催化剂硫化方案
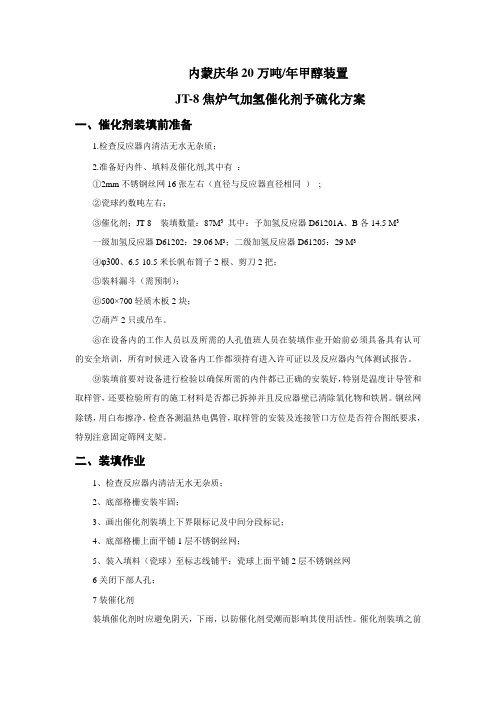
内蒙庆华20万吨/年甲醇装置JT-8焦炉气加氢催化剂予硫化方案一、催化剂装填前准备1.检查反应器内清洁无水无杂质;2.准备好内件、填料及催化剂,其中有:①2mm不锈钢丝网16张左右(直径与反应器直径相同);②瓷球约数吨左右;③催化剂;JT-8 装填数量:87M3其中:予加氢反应器D61201A、B各14.5 M3一级加氢反应器D61202:29.06 M3;二级加氢反应器D61205:29 M3④φ300、6.5-10.5米长帆布筒子2根、剪刀2把;⑤装料漏斗(需预制);⑥500×700轻质木板2块;⑦葫芦2只或吊车。
⑧在设备内的工作人员以及所需的人孔值班人员在装填作业开始前必须具备具有认可的安全培训,所有时候进入设备内工作都须持有进入许可证以及反应器内气体测试报告。
⑨装填前要对设备进行检验以确保所需的内件都已正确的安装好,特别是温度计导管和取样管,还要检验所有的施工材料是否都已拆掉并且反应器壁已清除氧化物和铁屑。
钢丝网除锈,用白布擦净,检查各测温热电偶管,取样管的安装及连接管口方位是否符合图纸要求,特别注意固定筛网支架。
二、装填作业1、检查反应器内清洁无水无杂质;2、底部格栅安装牢固;3、画出催化剂装填上下界限标记及中间分段标记;4、底部格栅上面平铺1层不锈钢丝网;5、装入填料(瓷球)至标志线铺平;瓷球上面平铺2层不锈钢丝网6关闭下部人孔;7装催化剂装填催化剂时应避免阴天,下雨,以防催化剂受潮而影响其使用活性。
催化剂装填之前应先筛去粉尘。
催化剂装填时,从上人孔放入加料帆布筒10.0米左右和漏斗连接;催化剂装填时视装填设备及人员情况,可进行一台或多台反应器的装填作业。
①漏斗内倒入催化剂0.5-1.0吨;可根据具体情况确定。
并用吊车吊至反应器人孔上方,漏斗与帆布筒相连,放入催化剂。
②视吊装催化剂的量,取出漏斗和帆布筒由软梯进入反应器,用木板刮平催化剂;③刮平后,根据具体装填高度,帆布筒剪掉约1米,继续装催化剂,装量根据第一次实际装填情况可调节。
加氢催化剂器外预硫化技术
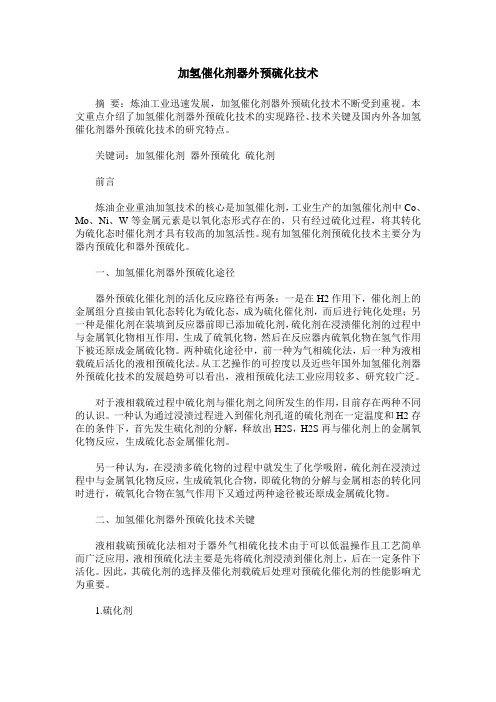
加氢催化剂器外预硫化技术摘要:炼油工业迅速发展,加氢催化剂器外预硫化技术不断受到重视。
本文重点介绍了加氢催化剂器外预硫化技术的实现路径、技术关键及国内外各加氢催化剂器外预硫化技术的研究特点。
关键词:加氢催化剂器外预硫化硫化剂前言炼油企业重油加氢技术的核心是加氢催化剂,工业生产的加氢催化剂中Co、Mo、Ni、W等金属元素是以氧化态形式存在的,只有经过硫化过程,将其转化为硫化态时催化剂才具有较高的加氢活性。
现有加氢催化剂预硫化技术主要分为器内预硫化和器外预硫化。
一、加氢催化剂器外预硫化途径器外预硫化催化剂的活化反应路径有两条:一是在H2作用下,催化剂上的金属组分直接由氧化态转化为硫化态,成为硫化催化剂,而后进行钝化处理;另一种是催化剂在装填到反应器前即已添加硫化剂,硫化剂在浸渍催化剂的过程中与金属氧化物相互作用,生成了硫氧化物,然后在反应器内硫氧化物在氢气作用下被还原成金属硫化物。
两种硫化途径中,前一种为气相硫化法,后一种为液相载硫后活化的液相预硫化法。
从工艺操作的可控度以及近些年国外加氢催化剂器外预硫化技术的发展趋势可以看出,液相预硫化法工业应用较多、研究较广泛。
对于液相载硫过程中硫化剂与催化剂之间所发生的作用,目前存在两种不同的认识。
一种认为通过浸渍过程进入到催化剂孔道的硫化剂在一定温度和H2存在的条件下,首先发生硫化剂的分解,释放出H2S,H2S再与催化剂上的金属氧化物反应,生成硫化态金属催化剂。
另一种认为,在浸渍多硫化物的过程中就发生了化学吸附,硫化剂在浸渍过程中与金属氧化物反应,生成硫氧化合物,即硫化物的分解与金属相态的转化同时进行,硫氧化合物在氢气作用下又通过两种途径被还原成金属硫化物。
二、加氢催化剂器外预硫化技术关键液相载硫预硫化法相对于器外气相硫化技术由于可以低温操作且工艺简单而广泛应用,液相预硫化法主要是先将硫化剂浸渍到催化剂上,后在一定条件下活化。
因此,其硫化剂的选择及催化剂载硫后处理对预硫化催化剂的性能影响尤为重要。
加氢催化剂预硫化方案

1. 引言加氢催化剂是广泛应用于石化工业领域的关键催化剂之一。
为了提高加氢催化剂的活性和稳定性,预硫化技术被广泛应用。
本文将从预硫化的原理、影响因素以及常见的预硫化方案等方面进行探讨。
2. 预硫化的原理预硫化是指在加氢催化剂使用之前,使用硫化物溶液进行处理,使其表面形成一层硫化物膜。
这一膜可以防止催化剂表面被氧化物或其他不活性物质占据,从而提高催化剂的活性和稳定性。
预硫化的原理可以归结为两个方面:•活性金属硫化物的形成:活性金属如镍、钼等能够与硫化物反应形成硫化物,这种硫化物能够促进加氢反应的进行,提高催化剂的反应活性。
•表面硫化膜的形成:硫化物膜可以阻隔外界氧气和不活性物质的侵蚀,减少催化剂的表面被氧化的机会,提高催化剂的稳定性。
3. 预硫化的影响因素预硫化的效果受到多种因素的影响,下面列举了一些主要的影响因素:3.1 硫化剂的选择预硫化过程中使用的硫化剂对催化剂的性能起着至关重要的作用。
常用的硫化剂包括硫化氢(H2S)、二硫化碳(CS2)等。
不同的硫化剂在反应中会产生不同的硫化物,并对催化剂表面的化学状态产生影响。
3.2 预硫化温度和时间预硫化温度和时间是影响预硫化效果的关键因素。
一般来说,高温和长时间的预硫化会使硫化剂更充分地与催化剂发生反应,生成更完善的硫化物膜。
然而,过高的温度可能会导致催化剂的部分活性成分被分解或损失,因此需要根据具体情况选择合适的预硫化温度和时间。
3.3 氛围条件预硫化过程中的气氛条件也会对催化剂的预硫化效果产生影响。
一般情况下,加氢环境中的氢气浓度越高,硫化剂与催化剂的反应速度越快,硫化物膜形成的效果也越好。
4. 常见的预硫化方案4.1 H2S气体预硫化H2S气体预硫化是一种常用的预硫化方式。
预硫化过程中,将催化剂放入加热炉中,通入含有H2S气体的加硫气体。
通过控制炉内温度和气氛浓度,使硫化剂与催化剂表面反应生成硫化物。
4.2 溶液浸泡预硫化溶液浸泡预硫化是另一种常见的预硫化方式。
加氢催化剂硫化方案

制氢装置催化剂硫化方案硫化前准备:1、催化剂已按填装方案填装完毕2、压缩机已试机完成,达到开机条件,所有仪表已联校完成3、制氢系统已用氮气置换合格(O2<0.5%)、气密完成4、准备好硫化剂(DMDS)并注入至硫化剂罐,硫化剂线已试压、吹扫干净(用蒸汽、风彻底吹扫干净)5、准备好硫化用工具:硫化氢检测管、计量水器具、画好升温曲线、记录纸、对讲机消防器具等6、干气、氮气、循环水等已准备就绪LYT-701/LYT-702加氢催化剂硫化1、硫化机理LYT—701/702加氢催化剂活性组份氧化钴、氧化镍、三氧化钼在使用前需将其转化为硫化物才具有活性,这一过程为硫化,其机理为:DMDS(或CS2)+4H2=2H2S+CH4MoO3+2H2S+H2=MoS2+3H2OCoO+H2S=CoS+H2ONi0+ H2S=NiS+H2O硫化时,用干N2-H2(H2≥10%,O2<0.5%)作为硫化原料气,配以适量的CS2或者DMDS,经加热达到一定温度后进入催化剂床层,通常采用循环硫化或一次放空硫化方法。
2、硫化过程1、反应系统气密合格,建立氢气-氮气循环后,进行催化剂硫化。
硫化条件:氢压,MPa ≦0.5MPa循环介质,% N2-H2混合气氢气含量,%(v/v) 30-50空速,h-1 200-500第一个恒温硫化阶段床层温度和时间 230℃恒温6小时第二个恒温硫化阶段床层温度和时间 300℃恒温4-6小时第三个恒温硫化阶段床层温度和时间 350℃恒温4小时硫化剂二甲基二硫或二硫化碳理论需硫量,m %(对催化剂) 约8.0吸硫量计算公式为:⎥⎦⎤⎢⎣⎡⨯+⨯⨯+⨯⨯=C B A c s M C M B M A w w 06.329/806.32306.32s w :理论吸硫量c w :催化剂装量A:MoO 3的百分含量;A M :MoO 3的分子量,143.94B :CoO 的百分含量B M :CoO 的分子量,74.93C:NiO 的百分含量C M :NiO 的分子量,74.70理论生成水重量为:DMDS (或CS 2)注入量计算式:(催化剂量)×8%×94(DMDS 分子量或CS 2)/64(硫分子量)=硫注入量 硫注入量×1.1(10%的余量)=实际硫注入量0.452 吨 气体含硫量计算式:X (气体循环量Nm3)/22.4×0.5%(硫含量)×94(DMDS 分子量或CS2)/64(硫分子量)=X’ Kg 二甲基二硫性质:分子式:CH3SSCH3 分子量:94.20 CAS :624-92-0 淡黄色透明液体。
预加氢催化剂预硫化方案

预加氢催化剂预硫化方案The document was finally revised on 2021中国石化九江分公司30×104t/a重整预加氢装置FH-40C催化剂原则开工方案中国石油化工股份有限公司抚顺石油化工研究院二○○九年四月一、催化剂干燥1、干燥前的准备工作(1)催化剂装填完毕,临氢系统进行氮气置换、气密合格。
催化剂干燥用氮气作介质。
(2)绘出催化剂干燥脱水升、恒温曲线。
(3)催化剂干燥前,各切水点排尽存水,并准备好计量水的器具。
2、干燥示意流程↓N2循环氢分液罐→循环压缩机→换热器→加热炉↑↓分离器←水冷←空冷←换热器←反应器↓放水3、催化剂干燥条件:高分压力:反应器入口温度:250℃循环氮气量:循环压缩机全量循环干燥温度要求见表2。
表2 催化剂干燥温度要求反应器入口温度℃床层温度℃升、降温速度℃/h升、恒温参考时间h常温→250- 10~15 15250~280 ≮200 - 至干燥结束250→<150≯150 20~25 4~54、干燥结束标准高分无明水放出。
5、干燥操作(1)在氮气压力下,循环压缩机全量循环,加热炉点火,以10~15℃/h的升温速度将反应器入口温度升至250℃,开始恒温脱水。
如果催化剂床层最低点温度达不到200℃,可适当提高反应器入口温度,但反应器入口温度≯280℃。
(2)在干燥过程中,每2小时在高分放水一次,并计量。
(3)画出催化剂脱水干燥的实际升、恒温曲线图。
(4)干燥达到结束标准后,以≯25℃/h的降温速度将反应器床层各点温度均降至<150℃,方可引入氢气进行高压气密,合格后进行催化剂预硫化。
二、催化剂预硫化催化剂预硫化是指催化剂在氢气存在下,硫化剂(如DMDS)分解生成H2S,H2S使催化剂金属组分由氧化态转化成相应的硫化态。
在预硫化过程中,关键问题是要避免金属氧化态在与H2S反应转化成硫化态之前被热氢还原。
所以,催化剂预硫化时,必须控制好预硫化温度与循环氢中H2S含量的关系,在H2S未穿透催化剂床层前,床层最高点温度不应超过230℃。
加氢裂化催化剂预硫化操作规程

加氢裂化催化剂预硫化操作规程一、催化剂预硫化的目的加氢裂化催化剂的活性金属组分主要是Mo、Ni、Co和W,同其它新催化剂或再生后的催化剂一样,其所含的活性金属组分(Mo、Ni、Co、W)都是以氧化态的形式存在。
大量的研究和工业实践证明,催化剂经过硫化,活性金属组分由氧化态转化为硫化态,具有良好的加氢活性和热稳定性。
因此,在加氢催化剂接触原料油汽之前,先进行预硫化,将催化剂活性金属组分由氧化态转化为硫化态。
本装置使用的FZC系列保护剂为Mo-Ni系活性金属氧化物,FF-20精制催化剂活性金属为W-Mo-Ni系金属氧化物,FC-14裂化催化剂的活性金属为W-Ni系金属氧化物,予硫化能使MoO3、WO3和NiO转变为具有较高活性的MoS2、WS2和Ni3S2金属硫化物。
催化剂硫化一般分为湿法硫化和干法硫化两种,湿化硫化为在氢气存在下,采用硫化物或馏分油在液相或半液相状态下的预硫化;干法硫化为在氢气存在下,直接用含有一定浓度的H2S或直接向循环氢中注入有机硫化物进行的预硫化。
湿法硫化分为两种:一种为催化剂硫化过程所需要的硫油外部加入的硫化物而来,一种为依靠硫化油自身的硫进行预硫化。
本装置预硫化工艺为干法气相硫化。
使用二甲基二硫化物C2H6S2(DMDS)作为硫化剂。
二、催化剂预硫化的原理催化剂预硫化是基于硫化剂(DMDS)临氢分解生成硫化氢(H2S),H2S与催化剂活性金属氧化态反应转化成相应金属硫化态的反应。
其相关的硫化反应如下:(CH3)2S2+3H2→ 2H2S+2CH4MoO3 + 2H2S + H2→ MoS2 + 3H2O3NiO + 2H2S + H2→ Ni3S2 + 3H2OWO3 + 2H2S + H2→ WS2 + 3H2O三、具备条件(1)经过气密检验和紧急泄压试验,确认系统严密性和联锁系统性能安全可靠。
(2)供氢系统确保稳定可靠,1401-K-101及1401-K-102运转正常。
方案十三(催化剂硫化方案)
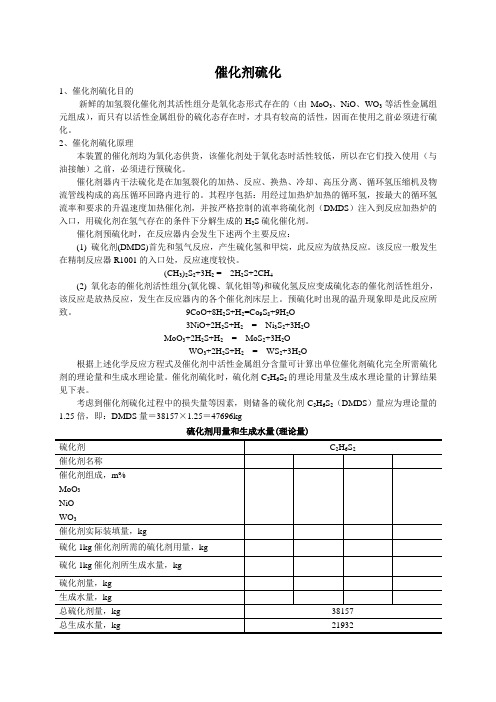
催化剂硫化1、催化剂硫化目的新鲜的加氢裂化催化剂其活性组分是氧化态形式存在的(由MoO3、NiO、WO3等活性金属组元组成),而只有以活性金属组份的硫化态存在时,才具有较高的活性,因而在使用之前必须进行硫化。
2、催化剂硫化原理本装置的催化剂均为氧化态供货,该催化剂处于氧化态时活性较低,所以在它们投入使用(与油接触)之前,必须进行预硫化。
催化剂器内干法硫化是在加氢裂化的加热、反应、换热、冷却、高压分离、循环氢压缩机及物流管线构成的高压循环回路内进行的。
其程序包括:用经过加热炉加热的循环氢,按最大的循环氢流率和要求的升温速度加热催化剂,并按严格控制的流率将硫化剂(DMDS)注入到反应加热炉的入口,用硫化剂在氢气存在的条件下分解生成的H2S硫化催化剂。
催化剂预硫化时,在反应器内会发生下述两个主要反应:(1) 硫化剂(DMDS)首先和氢气反应,产生硫化氢和甲烷,此反应为放热反应。
该反应一般发生在精制反应器R1001的入口处,反应速度较快。
(CH3)2S2+3H2 = 2H2S+2CH4(2) 氧化态的催化剂活性组分(氧化镍、氧化钼等)和硫化氢反应变成硫化态的催化剂活性组分,该反应是放热反应,发生在反应器内的各个催化剂床层上。
预硫化时出现的温升现象即是此反应所致。
9CoO+8H2S+H2=Co9S8+9H2O3NiO+2H2S+H2 = Ni3S2+3H2OMoO3+2H2S+H2= MoS2+3H2OWO3+2H2S+H2= WS2+3H2O根据上述化学反应方程式及催化剂中活性金属组分含量可计算出单位催化剂硫化完全所需硫化剂的理论量和生成水理论量。
催化剂硫化时,硫化剂C2H6S2的理论用量及生成水理论量的计算结果见下表。
考虑到催化剂硫化过程中的损失量等因素,则储备的硫化剂C2H6S2(DMDS)量应为理论量的1.25倍,即:DMDS量=38157×1.25=47696kg硫化剂用量和生成水量(理论量)硫化过程中还可能有不希望发生的副反应:氧化态的催化剂活性组分(氧化镍、氧化钼、氧化钨)被氢气还原,生成金属单质和水,这会极大损害催化剂的活性。
加氢催化剂的硫化_翟京宋
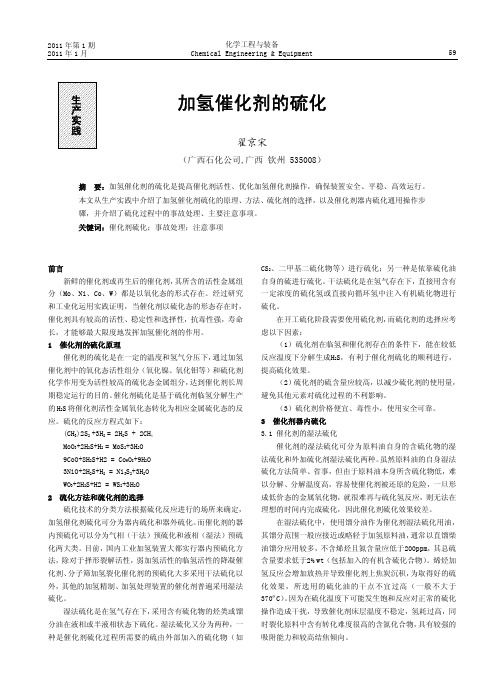
2011 年第 1 期 2011 年 1 月化学工程与装备 Chemical Engineering & Equipment59生产实践摘 前言 1 催化剂的硫化原理 应。
硫化的反应方程式如下: (CH3)2S2 +3H2 = 2H2S + 2CH4 MoO3+2H2S+H2 = MoS2+3H2O 9CoO+8H2S+H2 = Co9O8+9H2O 3NiO+2H2S+H2 = Ni3S2+3H2O WO3+2H2S+H2 = WS2+3H2O 2 硫化方法和硫化剂的选择 硫化。
加氢催化剂的硫化翟京宋(广西石化公司,广西 钦州 535008)要:加氢催化剂的硫化是提高催化剂活性、优化加氢催化剂操作,确保装置安全、平稳、高效运行。
本文从生产实践中介绍了加氢催化剂硫化的原理、方法、硫化剂的选择,以及催化剂器内硫化通用操作步 骤,并介绍了硫化过程中的事故处理、主要注意事项。
关键词:催化剂硫化;事故处理;注意事项CS2、二甲基二硫化物等)进行硫化;另一种是依靠硫化油 自身的硫进行硫化。
干法硫化是在氢气存在下, 直接用含有 一定浓度的硫化氢或直接向循环氢中注入有机硫化物进行 硫化。
在开工硫化阶段需要使用硫化剂, 而硫化剂的选择应考 虑以下因素: (1)硫化剂在临氢和催化剂存在的条件下,能在较低 反应温度下分解生成H2S,有利于催化剂硫化的顺利进行, 提高硫化效果。
(2) 硫化剂的硫含量应较高, 以减少硫化剂的使用量, 避免其他元素对硫化过程的不利影响。
(3)硫化剂价格便宜、毒性小,使用安全可靠。
3 催化剂器内硫化 催化剂的湿法硫化可分为原料油自身的含硫化物的湿 法硫化和外加硫化剂湿法硫化两种。
虽然原料油的自身湿法 硫化方法简单、省事,但由于原料油本身所含硫化物低,难 以分解、分解温度高,容易使催化剂被还原的危险,一旦形 成低价态的金属氧化物, 就很难再与硫化氢反应, 则无法在 理想的时间内完成硫化,因此催化剂硫化效果较差。
加氢催化剂预硫化技术
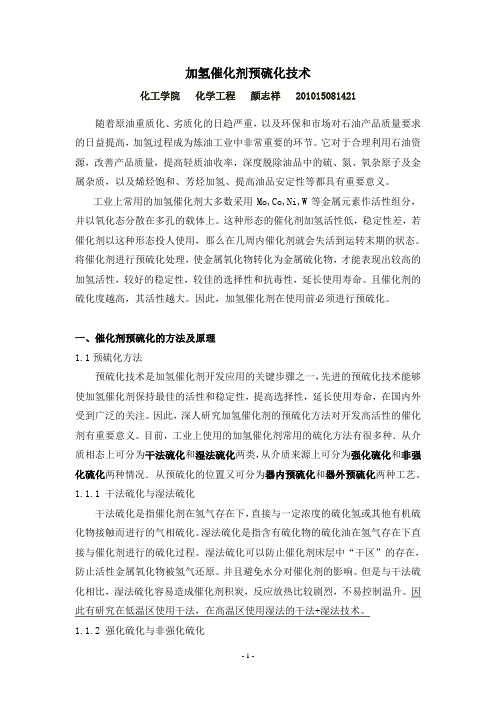
加氢催化剂预硫化技术化工学院化学工程颜志祥 201015081421 随着原油重质化、劣质化的日趋严重,以及环保和市场对石油产品质量要求的日益提高,加氢过程成为炼油工业中非常重要的环节。
它对于合理利用石油资源,改善产品质量,提高轻质油收率,深度脱除油品中的硫、氮、氧杂原子及金属杂质,以及烯烃饱和、芳烃加氢、提高油品安定性等都具有重要意义。
工业上常用的加氢催化剂大多数采用Mo,Co,Ni,W等金属元素作活性组分,并以氧化态分散在多孔的载体上。
这种形态的催化剂加氢活性低,稳定性差,若催化剂以这种形态投人使用,那么在几周内催化剂就会失活到运转末期的状态。
将催化剂进行预硫化处理,使金属氧化物转化为金属硫化物,才能表现出较高的加氢活性,较好的稳定性,较佳的选择性和抗毒性,延长使用寿命。
且催化剂的硫化度越高,其活性越大。
因此,加氢催化剂在使用前必须进行预硫化。
一、催化剂预硫化的方法及原理1.1预硫化方法预硫化技术是加氢催化剂开发应用的关键步骤之一,先进的预硫化技术能够使加氢催化剂保持最佳的活性和稳定性,提高选择性,延长使用寿命,在国内外受到广泛的关注。
因此,深人研究加氢催化剂的预硫化方法对开发高活性的催化剂有重要意义。
目前,工业上使用的加氢催化剂常用的硫化方法有很多种.从介质相态上可分为干法硫化和湿法硫化两类,从介质来源上可分为强化硫化和非强化硫化两种情况.从预硫化的位置又可分为器内预硫化和器外预硫化两种工艺。
1.1.1 干法硫化与湿法硫化干法硫化是指催化剂在氢气存在下,直接与一定浓度的硫化氢或其他有机硫化物接触而进行的气相硫化。
湿法硫化是指含有硫化物的硫化油在氢气存在下直接与催化剂进行的硫化过程。
湿法硫化可以防止催化剂床层中“干区”的存在,防止活性金属氧化物被氢气还原。
并且避免水分对催化剂的影响。
但是与干法硫化相比,湿法硫化容易造成催化剂积炭,反应放热比较剧烈,不易控制温升。
因此有研究在低温区使用干法,在高温区使用湿法的干法+湿法技术。
加氢单元催化剂硫化

一段反应器硫化1.硫化作业前的确认(2台反应器硫化管线的盲板均处于开通状态)(1)确认氢气已经建立正确的循环。
R-102已经用阀门隔离。
循环氢气流程;C-101→B-102→D-102→E107→B-101→R-101→E-107→E-106→E-104→E-101→E-108→D-103→E-114→T-103→D-104→C-101(2)确认D-103的工作压力为2430 KPa,此点压力控制已投自动。
氢气浓度>90%,氢气浓度2小时分析一次。
(3)循环氢流量不低于1000Nm3/h。
E-107壳程旁通关闭,以最大负荷对循环氢升温。
(4)通过调节FV-9111。
来维持系统压力。
(5)打至手动维持稳定的补充量,如氢气浓度降低则加大放散和新氢气的补充。
(6)确认硫化剂槽的液位正常。
硫化剂已用BTX稀释到50%浓度。
(7)点燃B-101给反应器升温,系统以25℃/h的速度进行升温,一段加氢反应器的进口温度TISA-9120A为150℃。
恒温,观察D-103液位待液位升高速度低于4L/h,催化剂干燥结束,继续升温至180°C。
冷却器E-108的冷却水要保证蒸汽能足够冷却。
(8)维持反应器温度在180°C,对达到180°C的部分热紧固,并维持此温度。
然后把反应器温度升高到205℃准备硫化。
2.硫化(1)打开一段加氢反应器硫化剂注入管道阀门,按照泵的操作步骤启动硫化剂注入泵PU-103,调节冲程逐步至50L/H。
(2)在取样口SC-113处每小时取样检查一次循环氢气中硫化氢的含量,当检测出硫化氢且高分罐有水出现后,以25℃/h的速度将第一段加氢反应器R-101的进口温度TI-9136提升至230℃,恒温4小时。
在预硫化过程中,温度最高不能超过245℃。
(3)调节硫化剂注入泵的冲程至100L/H。
(4)当SC-113处硫化氢的含量大于3000ppm时,以25℃/h的速度将反应器进口温度提升至315℃。
加氢催化剂硫化阶段的操作原则

加氢催化剂硫化阶段的操作原则
1.硫化期间,严格执行操作规程中的不得、严禁、必须等字样的内
容;严格执行开工方案及工艺指标;
2.硫化前必须确认高压系统氧含量≤0.1%(体积);
3.硫化期间,高分压力必须≤12.5MPa,为10.5~12.5 MPa;
4.硫化期间,高分气H2纯度≥75%(V),为75~97%(V);
5.硫化期间,高压系统静压降速度≤0.1 MPa / h.
6.硫化期间,只能通过调行程调节注硫量,严禁使用高压注硫泵的
出口阀调节注硫量;
7.硫化启动后注硫量的调整幅度,任何时刻不能单次大幅度,而只
能多次、小幅调整;
8.硫化期间,任一催化剂床层总温升必须控制在≤25℃;
9.硫化期间,R15301第一冷氢阀阀前后压差大于0.4 MPa;R15311
第一冷氢阀前后压差大于0.4 MPa;
10.、硫化期间,“F15301出口温度─R15301第一床层顶温差≤5℃”;
F15311出口温度─R15311第一床层顶温差≤5℃。
12.硫化启动时条件:反应器入口温度175~190℃,反应器入口H2S
含量为3000ppm(V),预期温升≤25℃。
硫化开始后按照硫化方案执行。
加氢催化剂硫化方案
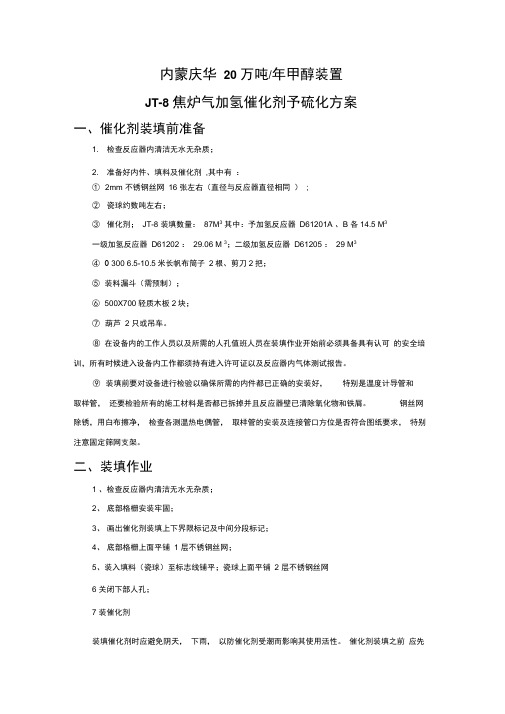
内蒙庆华20 万吨/年甲醇装置JT-8 焦炉气加氢催化剂予硫化方案一、催化剂装填前准备1. 检查反应器内清洁无水无杂质;2. 准备好内件、填料及催化剂,其中有:①2mm 不锈钢丝网16 张左右(直径与反应器直径相同);②瓷球约数吨左右;③催化剂;JT-8 装填数量:87M3其中:予加氢反应器D61201A 、B 各14.5 M3一级加氢反应器D61202 :29.06 M 3;二级加氢反应器D61205 :29 M3④0 300 6.5-10.5米长帆布筒子2根、剪刀2把;⑤装料漏斗(需预制);⑥500X700轻质木板2块;⑦葫芦 2 只或吊车。
⑧在设备内的工作人员以及所需的人孔值班人员在装填作业开始前必须具备具有认可的安全培训,所有时候进入设备内工作都须持有进入许可证以及反应器内气体测试报告。
⑨装填前要对设备进行检验以确保所需的内件都已正确的安装好,特别是温度计导管和取样管,还要检验所有的施工材料是否都已拆掉并且反应器壁已清除氧化物和铁屑。
钢丝网除锈,用白布擦净,检查各测温热电偶管,取样管的安装及连接管口方位是否符合图纸要求,特别注意固定筛网支架。
二、装填作业1 、检查反应器内清洁无水无杂质;2、底部格栅安装牢固;3、画出催化剂装填上下界限标记及中间分段标记;4、底部格栅上面平铺1 层不锈钢丝网;5、装入填料(瓷球)至标志线铺平;瓷球上面平铺2 层不锈钢丝网6 关闭下部人孔;7 装催化剂装填催化剂时应避免阴天,下雨,以防催化剂受潮而影响其使用活性。
催化剂装填之前应先筛去粉尘。
催化剂装填时,从上人孔放入加料帆布筒10.0 米左右和漏斗连接;催化剂装填时视装填设备及人员情况,可进行一台或多台反应器的装填作业。
①漏斗内倒入催化剂0.5-1.0 吨;可根据具体情况确定。
并用吊车吊至反应器人孔上方,漏斗与帆布筒相连,放入催化剂。
②视吊装催化剂的量,取出漏斗和帆布筒由软梯进入反应器,用木板刮平催化剂;③刮平后,根据具体装填高度,帆布筒剪掉约 1 米,继续装催化剂,装量根据第一次实际装填情况可调节。
加氢裂化催化剂湿法硫化的应用及效果
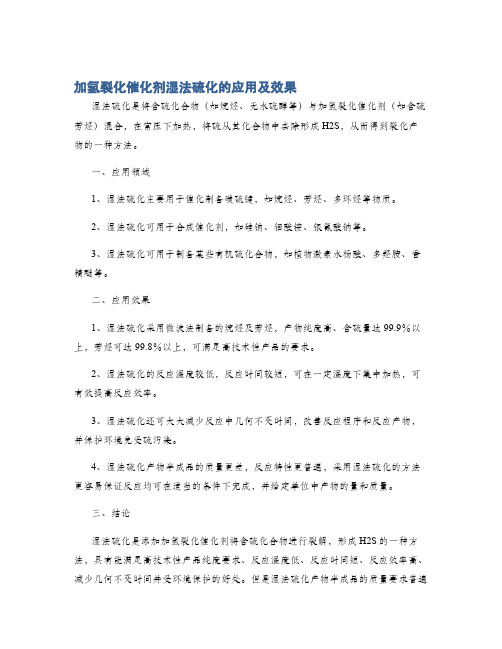
加氢裂化催化剂湿法硫化的应用及效果
湿法硫化是将含硫化合物(如烷烃、无水硫醇等)与加氢裂化催化剂(如含硫芳烃)混合,在常压下加热,将硫从其化合物中去除形成H2S,从而得到裂化产物的一种方法。
一、应用领域
1、湿法硫化主要用于催化制备碳硫键,如烷烃、芳烃、多环烃等物质。
2、湿法硫化可用于合成催化剂,如硅钠、钼酸铵、银氰酸钠等。
3、湿法硫化可用于制备某些有机硫化合物,如植物激素水杨酸、多羟胺、香精醚等。
二、应用效果
1、湿法硫化采用微波法制备的烷烃及芳烃,产物纯度高、含硫量达99.9%以上,芳烃可达99.8%以上,可满足高技术性产品的要求。
2、湿法硫化的反应温度较低,反应时间较短,可在一定温度下集中加热,可有效提高反应效率。
3、湿法硫化还可大大减少反应中几何不变时间,改善反应程序和反应产物,并保护环境免受硫污染。
4、湿法硫化产物半成品的质量更差,反应特性更普遍,采用湿法硫化的方法更容易保证反应均可在适当的条件下完成,并给定单位中产物的量和质量。
三、结论
湿法硫化是添加加氢裂化催化剂将含硫化合物进行裂解,形成H2S的一种方法,具有能满足高技术性产品纯度要求、反应温度低、反应时间短、反应效率高、减少几何不变时间并受环境保护的好处。
但是湿法硫化产物半成品的质量要求普遍
性较差,因此使用湿法硫化时,必须严格控制关键反应参数,以满足产品的质量要求。
加氢催化剂预硫化技术探讨

加氢催化剂预硫化技术探讨摘要:加氢催化剂大多是由Ni,W,Mo,Co等活性金属组分和载体组成,其中金属组分是以氧化态形式分散在载体上,可进行加氢脱硫、氮,加氢脱芳烃及加氢裂化等反应。
研究表明,未经预硫化的催化剂的活性、选择性和稳定性均低于硫化态的催化剂,而且使用寿命较短。
将氧化态的催化剂进行预硫化,使活性金属组分转变为硫化态,可最大限度的发挥加氢催化剂的活性,因而加氢催化剂预硫化技术的开发和应用,成为国内外研究的热点,受到广泛关注。
关键词:加氢;催化剂;预硫化技术1 预硫化机理在加氢催化剂预硫化的过程中会放出大量的热量。
其反应原理是在H2存在的条件下,硫化剂加氢生成H2S,在H2和H2S同时存在的氛围下,加氢催化剂活性金属由氧化态转变为硫化态,预硫化过程分为如下两个反应步骤: 加氢催化剂预硫化可使催化剂中的金属组分由氧化态变成硫化态,处于最佳活性价态。
在H2和H2S同时存在的条件下,金属氧化物上可发生还原反应和硫化反应的竞争,硫化效果的好坏会直接影响催化剂的性能和寿命,由于预硫化过程中放出大量的热,并伴随有水生成,因此预硫化过程中需密切监控反应器床层的温度和循环气中的水含量,防止床层飞温。
2 预硫化方式加氢催化剂的预硫化方式可根据硫化反应进行的场所不同,分为器内预硫化和器外硫化。
器内预硫化是在催化剂装入反应器之后,加入H2和硫化剂将金属活性组分转变为硫化态。
器内预硫化有干法预硫化和湿法预硫化两种方式。
干法预硫化是在H2存在的条件下,使用一定浓度的H2S、在循环气中注入CS2或使用其它有机硫化物;湿法预硫化是在H2存在下,用含硫化合物(如CS2或DMDS 等)的烃类或馏分油在半液相或液相状态下进行硫化。
器外预硫化方式有两种:一种是将新鲜的或者再生后的催化剂进行硫化,再经冷却、钝化和过筛后装填到反应器;另一种是将硫化剂直接添加到氧化态的催化剂上,经处理后装入反应器。
普遍认为,器外预硫化具有开工过程简单、开工时间短、开工成本低、投资小和无污染等优势。
- 1、下载文档前请自行甄别文档内容的完整性,平台不提供额外的编辑、内容补充、找答案等附加服务。
- 2、"仅部分预览"的文档,不可在线预览部分如存在完整性等问题,可反馈申请退款(可完整预览的文档不适用该条件!)。
- 3、如文档侵犯您的权益,请联系客服反馈,我们会尽快为您处理(人工客服工作时间:9:00-18:30)。
焦炉气加氢催化剂予硫化方案
一、催化剂装填前准备
1.检查反应器内清洁无水无杂质;
2.准备好内件、填料及催化剂,其中有:
①2mm不锈钢丝网16张左右(直径与反应器直径相同);
②瓷球约数吨左右;
③催化剂;JT-8 装填数量:87M3其中:予加氢反应器D61201A、B各14.5 M3
一级加氢反应器D61202:29.06 M3;二级加氢反应器D61205:29 M3
④φ300、6.5-10.5米长帆布筒子2根、剪刀2把;
⑤装料漏斗(需预制);
⑥500×700轻质木板2块;
⑦葫芦2只或吊车。
⑧在设备内的工作人员以及所需的人孔值班人员在装填作业开始前必须具备具有认可的安全培训,所有时候进入设备内工作都须持有进入许可证以及反应器内气体测试报告。
⑨装填前要对设备进行检验以确保所需的内件都已正确的安装好,特别是温度计导管和取样管,还要检验所有的施工材料是否都已拆掉并且反应器壁已清除氧化物和铁屑。
钢丝网除锈,用白布擦净,检查各测温热电偶管,取样管的安装及连接管口方位是否符合图纸要求,特别注意固定筛网支架。
二、装填作业
1、检查反应器内清洁无水无杂质;
2、底部格栅安装牢固;
3、画出催化剂装填上下界限标记及中间分段标记;
4、底部格栅上面平铺1层不锈钢丝网;
5、装入填料(瓷球)至标志线铺平;瓷球上面平铺2层不锈钢丝网
6关闭下部人孔;
7装催化剂
装填催化剂时应避免阴天,下雨,以防催化剂受潮而影响其使用活性。
催化剂装填之前应先筛去粉尘。
催化剂装填时,从上人孔放入加料帆布筒10.0米左右和漏斗连接;催化剂装填时视装填设备及人员情况,可进行一台或多台反应器的装填作业。
①漏斗内倒入催化剂0.5-1.0吨;可根据具体情况确定。
并用吊车吊至反应器人
孔上方,漏斗与帆布筒相连,放入催化剂。
②视吊装催化剂的量,取出漏斗和帆布筒由软梯进入反应器,用木板刮平催化剂;
③刮平后,根据具体装填高度,帆布筒剪掉约1米,继续装催化剂,装量根据第
一次实际装填情况可调节。
在整个装填过程中,要求均匀平整,防止粉碎变潮,
勿在催化剂上直接踩踏。
④装入催化剂至分段标记高度后,均匀平整,然后继续装入催化剂。
⑤装入催化剂至额定高度后,扒平后铺2层不锈钢丝网,再装瓷球;
⑥瓷球装到预定高度,扒平后铺一层不锈钢丝网;
7、安装并固定填料压实格栅;
8、安装上人孔。
各加氢反应器催化剂的装填方法基本相同。
三、焦炉气加氢催化剂的硫化
催化剂在正常使用之前,为获得较高的加氢转化活性,应对其进行硫化。
采用H2S为硫化剂时,发生如下反应:
MoO3+2H2S+H2→MoS2+3H2O
系统在试压、试漏结束后,以氮气或其它惰性气体吹净置换后,开始催化剂的升温。
升温时,可用氮气或氢氮气。
在对处理有机硫含量较高,硫形态较复杂的焦炉气原料时,为了获得较高的加氢转化活性,催化剂首次使用时,应进行预硫化,预硫化结束时,催化剂吸硫量约为本身重量的4-5%左右。
预硫化条件推荐如下:
气源:氢氮气或含氢的焦炉气中配入CS2
催化剂床层温度升至180℃以上时可在硫化用气中配入CS2。
空速:200~500h-1,压力:常压或低压(≤0.5MPa)
气体中含硫量:0.5~1.5%(体积)氧含量<0.2%
边升温边预硫化(升温速度20℃/小时),260℃、300℃分别恒温2小时,最终升温至正常的操作温度,再恒温,按催化剂理论吸硫量将CS2加完为止,可认为预硫化结束,然后系统逐步升压到正常操作压力,转入正常操作。
采用CS2为硫化剂时,硫化过程发生的主要反应如下:
CS2+4H2=CH4+2H2S
M 0O 3+2H 2S+M 0S 2+3H 2O
可能出现的副反应有:
CS 2+2H 2=C+2H 2S
CS 2+2H 2=CH 4+S 2
四、升温硫化曲线
(1)、装填完毕后,用气密置换合格,使系统残余氧含量<0.2%,用氮气其它惰性气体升温,升温条件:升温速率为20~30℃/hr ;空速300-500h -1;压力为0.3-.0.5MPa ; 当温度升至160-180℃时,恒定2-3小时,待温度稳定后,切换焦炉气。
(2)、切换焦炉气后,注意床层温度的变化,适时调节入口温度,在160-180℃温度下恒定1-2小时,要求焦炉气中氧含量<0.2%以下。
(3)、在温度恒定之后,开始注硫,气体中含硫量:0.5~1.5%(体积)初期2-4小时气体中硫含量0.5-0.8%(体积),之后可控制在1.0-1.5%(体积)。
待出口气中检测出硫时,开始升温,升温速率20~30℃/小时,220℃恒温,待出口气中检测出硫时,继续升温,升温速率20~30℃/小时,260-280℃恒温,待出口气中检测出硫时,继续升温,升温速率20~30℃/小时,350-380℃恒温,待出口气中检测出0.1%的硫时,或按催化剂理论吸硫量将CS 2加完后,可认为预硫化结束,然后降温吹扫,降温速率20~30℃/小时,等温度降至280℃,出口气中硫含量低于50ppm 时,逐步升压到正常操作压力(升压速率不高于0.5Mpa/10min ),转入正常操作。
催化剂干燥硫化升温曲线
50
100
150
200
250300
350
400
05101520253035
时间 h
温度 ℃
CS2注入量计算式:
催化剂量×5%×76(CS2分子量)/64(硫分子量)=硫化剂(吨)
硫化剂×1.1(10%的余量)= 实际用硫化剂(吨)
气体含硫量计算式:
X(气体量Nm3)/22.4×0.5%(硫含量)×76(CS2分子量)/2=X’ Kg
硫化时温度控制可采用如下方法:
a、调节加热或换热付线,以控制入反应器的温度
b、调节气量及压力的大小
c、控制焦炉气中烯烃含量
d、根据出口气中烯烃含量进行调控
e、调节注硫量,焦炉气中的氧含量要控制在0.2%以下。
五、建议
本次铁钼加氢催化剂原始开车采用予硫化的方法使催化剂硫化。
本此所有加氢催化剂的予硫化应准备硫化剂的注入设备(小型计量泵及小储槽),并在每一反应器入口管道上留一接口,以备硫化剂的注入。
小型计量泵的流量应在0-120升/小时内可调,硫化剂管道应在ф16-20mm,管道的具体走向现场确定
本方案为原则方案在具体装填及开车时,应根据工艺流程及现场装置等条件制定详细的方案。