6评估厌氧消化最佳稀释比
污泥厌氧消化技术的优化实践
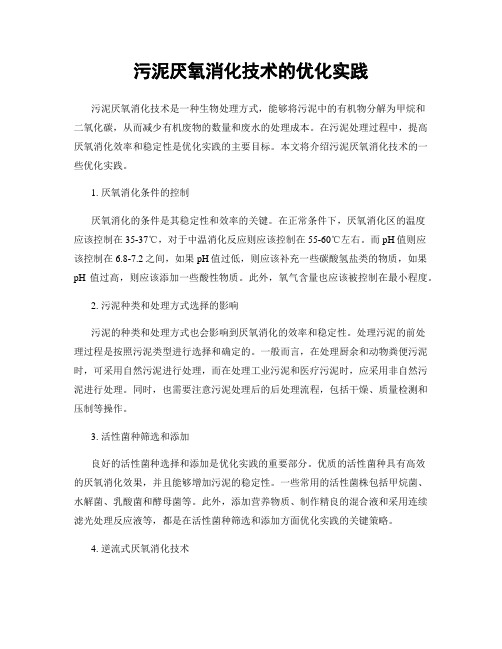
污泥厌氧消化技术的优化实践污泥厌氧消化技术是一种生物处理方式,能够将污泥中的有机物分解为甲烷和二氧化碳,从而减少有机废物的数量和废水的处理成本。
在污泥处理过程中,提高厌氧消化效率和稳定性是优化实践的主要目标。
本文将介绍污泥厌氧消化技术的一些优化实践。
1. 厌氧消化条件的控制厌氧消化的条件是其稳定性和效率的关键。
在正常条件下,厌氧消化区的温度应该控制在35-37℃,对于中温消化反应则应该控制在55-60℃左右。
而pH值则应该控制在6.8-7.2之间,如果pH值过低,则应该补充一些碳酸氢盐类的物质,如果pH值过高,则应该添加一些酸性物质。
此外,氧气含量也应该被控制在最小程度。
2. 污泥种类和处理方式选择的影响污泥的种类和处理方式也会影响到厌氧消化的效率和稳定性。
处理污泥的前处理过程是按照污泥类型进行选择和确定的。
一般而言,在处理厨余和动物粪便污泥时,可采用自然污泥进行处理,而在处理工业污泥和医疗污泥时,应采用非自然污泥进行处理。
同时,也需要注意污泥处理后的后处理流程,包括干燥、质量检测和压制等操作。
3. 活性菌种筛选和添加良好的活性菌种选择和添加是优化实践的重要部分。
优质的活性菌种具有高效的厌氧消化效果,并且能够增加污泥的稳定性。
一些常用的活性菌株包括甲烷菌、水解菌、乳酸菌和酵母菌等。
此外,添加营养物质、制作精良的混合液和采用连续滤光处理反应液等,都是在活性菌种筛选和添加方面优化实践的关键策略。
4. 逆流式厌氧消化技术逆流式厌氧消化技术是一种高效的污泥处理方式,可以提高厌氧消化的稳定性和效率。
研究表明,逆流式厌氧消化技术可以减少氨氮、COD和磷的浓度,同时也可以获得更高的甲烷产量。
该技术的优点在于,能够有效地利用反应器中的废水和气体,从而提高处理效率和降低成本。
5. 电子束辐照处理技术应用近年来,在污泥处理领域中,电子束辐照技术得到了越来越广泛的应用。
该技术包括控制实验方法、辐照设备和小型实验等,可以提高污泥的催化效率和稳定性,从而减少有机废物和废水的处理成本。
厌氧发酵指标测定方法

COD的测定(快速密闭催化消解法)试验步骤:1、取1ml滤液(5000r/min条件下离心10min,过滤)于50ml容量瓶中定容(稀释倍数由滤液SCOD的浓度而定,通常是稀释至1000-2500mg/L,选择消化液Ⅰ),从中量取3ml于消化管(注意干燥)中,每个样品做3个重复;同时以同量的蒸馏水代替样品,做空白试验。
2、依次加入1ml掩蔽剂、3ml消化液(注意准确)、5ml催化剂(每加入一种试剂后都要摇匀),旋紧密封塞,混匀。
3、放入已预热到165℃的消解炉中,消解22min,冷却。
4、将样液移至150ml锥形瓶中,用蒸馏水冲洗消化管(至少洗3次,共约30ml),冲洗液移入锥形瓶中。
5、加3滴邻菲罗啉指示剂,用硫酸亚铁标准溶液滴定,溶液颜色由黄到蓝突变成红褐色为终点,记录硫酸亚铁标准溶液用量(样品的记为V1,空白对照的记为V0)。
6、滴定使用0.05 mol/LFeSO4:先配0.2mol/L FeSO4,然后稀释得到(量取250mL0.2mol/LFeSO4于1000mL容量瓶即得0.05 mol/LFeSO4,标定后使用)标定方法:准确吸取10.00mL重铬酸钾标准溶液(C(1/6K2Cr2O7)=0.2500mol/L)于250mL 锥形瓶中,加水稀释至55mL左右,缓慢加入5mL浓硫酸,混匀,冷却后,加入2-3滴邻菲啰啉指示剂,用0.05 mol/LFeSO4滴定,溶液的颜色由黄色经蓝绿色至红褐色即未终点。
C[FeSO4]=0. 25*10/V计算:COD(mg·L-1)=(V0-V1)×C×8×1000×50/V2V1——滴定样品消耗的硫酸亚铁标准溶液的体积,mLV0——滴定空白消耗的硫酸亚铁标准溶液的体积,mLV2――水样体积,mL,本试验中V2=3mLC——硫酸亚铁标液的浓度,mol·L-150――水样的稀释倍数8――氧(1/2O)摩尔质量V’——硫酸亚铁标准溶液的标定时,用去的硫酸亚铁溶液的体积,mL试剂配制:掩蔽剂:称取30.0g硫酸汞(分析纯)溶于100mL的10%硫酸中。
厌氧池调试步骤及影响因素!
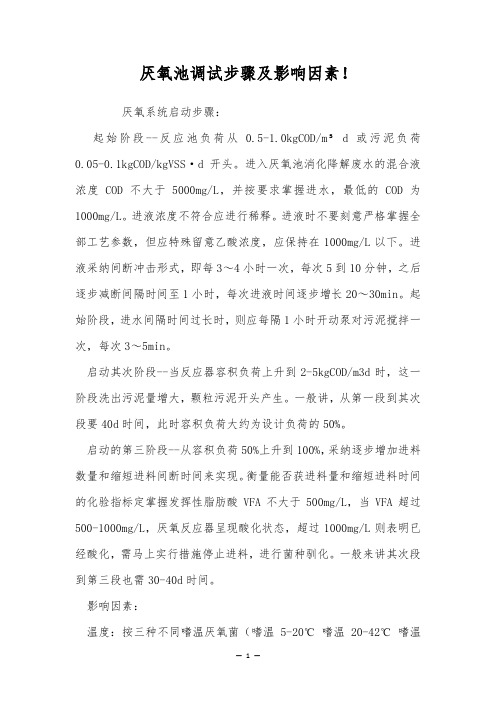
厌氧池调试步骤及影响因素!厌氧系统启动步骤:起始阶段--反应池负荷从0.5-1.0kgCOD/m³d或污泥负荷0.05-0.1kgCOD/kgVSS·d开头。
进入厌氧池消化降解废水的混合液浓度COD不大于5000mg/L,并按要求掌握进水,最低的COD为1000mg/L。
进液浓度不符合应进行稀释。
进液时不要刻意严格掌握全部工艺参数,但应特殊留意乙酸浓度,应保持在1000mg/L以下。
进液采纳间断冲击形式,即每3~4小时一次,每次5到10分钟,之后逐步减断间隔时间至1小时,每次进液时间逐步增长20~30min。
起始阶段,进水间隔时间过长时,则应每隔1小时开动泵对污泥搅拌一次,每次3~5min。
启动其次阶段--当反应器容积负荷上升到2-5kgCOD/m3d时,这一阶段洗出污泥量增大,颗粒污泥开头产生。
一般讲,从第一段到其次段要40d时间,此时容积负荷大约为设计负荷的50%。
启动的第三阶段--从容积负荷50%上升到100%,采纳逐步增加进料数量和缩短进料间断时间来实现。
衡量能否获进料量和缩短进料时间的化验指标定掌握发挥性脂肪酸VFA不大于500mg/L,当VFA超过500-1000mg/L,厌氧反应器呈现酸化状态,超过1000mg/L则表明已经酸化,需马上实行措施停止进料,进行菌种驯化。
一般来讲其次段到第三段也需30-40d时间。
影响因素:温度:按三种不同嗜温厌氧菌(嗜温5-20℃嗜温20-42℃嗜温42-75℃)工程上分为低温厌氧(15-20℃)、中温厌氧(30-40℃)、高温厌氧(50-60℃)三种。
温度对厌氧反应尤为重要,当温度低于最优下限温度时,每下降1℃,效率下降11%。
在上述范围,温度在1-3℃的微小波动,对厌氧反应影响不明显,但温度变化过大(急速变化),则会使污泥活力下降,度产生酸积累等问题。
pH:厌氧水解酸化工艺,对pH要求范围较松,即产酸菌的PH应掌握4-7℃范围内;完全厌氧反应则应严格掌握pH,即产甲烷反应掌握范围6.5-8.0,最佳范围为6.8-7.2,pH低于6.3或高于7.8,甲烷化速率降低。
好氧厌氧营养配比

首先,这个值是经验值,没有确切的数学依据,有人说100:5:1,也有人说是100:4:1,反正是个概数。
为什么有这样一个比例?
1.污泥法无论是厌氧还是好氧,都是一个生物处理的过程。
那么为了让微生物更好的工作和繁殖,需要一个好的培养环境,包括营养物质,温度,pH值等,其中营养物质主要就是指碳源,氮源和含磷无机盐。
2.BOD在这里就是碳源,也是微生物能量的主要来源,一方面要参与能量代谢,又要被用来合成细胞物质,所以比例偏高。
3.N和P主要被用来合成细胞物质,在有氧呼吸中不会被消耗。
所以比例(相对于C)偏低。
4.根据Mc Carty的细菌原生质分子式C60H87N12O23P,C、N、P的比例约为20:5:1,考虑到碳源(BOD)中大多数(80%)被用来进行能量代谢,所以进水时比例为100:5:1。
5.如果N,P偏高,富营养化。
6.如果N, P偏低,微生物不能充分利用碳源合成细胞物质,过量的碳源(能量)将被转化为多糖类以便储存。
如人长胖一样,污泥就会膨胀,同时还会影响到污泥的沉降性能。
这是实际运行过程中,最不愿意出现的情形。
综上所述,人们通过试验确认了一个适合好氧活性污泥法的经验值,通常认为是BOD:N:P=100:5:1。
关于厌氧消化的小知识

厌氧消化的影响因素1、温度温度适宜时.细菌发育正常,有机物分解完全,产气量高。
根据操作温度的不同,可将厌氧消化分为:①低温消化:可不控制消化温度(≤30℃);②中温消化:30-35℃;③高温消化:50-56℃。
实际上,在0-56℃的范围内,产甲烷菌并没有特定的温度限制,然而在一定温度范围内被驯化以后,温度稍存升降(±2℃),都可严重影响甲烷消化作用,尤其是高温消化,对温度变化更为敏感。
因此,在厌氧消化操作运行过程中,应尽量保持温度不变。
2、污泥投配率投配率系指每月加入消化池的新鲜污泥体积与消化池体积的比率,以百分煎计。
根据经验.中温消化的新鲜污泥投配率以6%-8%为宜。
在设计时,新鲜污泥投配率可在5%-12%之间选用。
若要求产气量多,采用下限值;若以处理污泥为主.则可采用上限值。
一般来说,投配率大,则有机物分解程度减少,产气量下降,所需消化池容积小;反之,则产气量增加.所需消化池容积大。
3、营养与碳氮比消化池的营养由投配污泥供给,营养配比中最重要的是C/N比。
C/N比太高,细菌氮量不足,消化液缓冲能力降低,pH值容易下降;C/N比太低,含氮量过多,pH值可能上升到8.0以上,脂肪酸的铵盐发生积累,使有机物分解受到抑制。
据研究,对于污泥消化处理来说, C/N比以(10-20):l较合适,因此,初沉池污泥的消化较好,剩余活性污泥C/N比约为5:1,所以不宜单独进行消化处理。
4、搅拌搅拌操作可以使鲜污泥与熟污泥均匀接触,加强热传导,均匀地供给细菌以养料,打碎液面上的浮渣层,提高消化池的负荷。
20世纪40年代的消化池设有搅拌设施,称标准消化池,其消化时间长,需30-60d。
有搅拌设备的消化池消化时间为l0-15d。
5、酸碱度酸碱度影响消化系统的pH值和消化液的缓冲能力,因此消化系统中有一定的碱度要求。
若碱度不足,可投加石灰、无水氨或碳酸铵进行调节。
但大量投加石灰,常使碱度偏高,泥量增加,应尽量合理利用。
实验六 厌氧污泥活性的测试

实验六 厌氧污泥活性的测试厌氧污泥的活性,实际上是指单位质量的厌氧污泥(以VSS 计)在单位时间内最多能产生的甲烷量,或者,是指单位质量的厌氧污泥(以VSS 计)在单位时间内最多能去除的有机物(以COD 计)。
因此,厌氧污泥活性一般可以用两个参数测量,即最大比产甲烷速率和最大比COD 去除率。
二者的定义分别如下:最大比产甲烷速率(4CH U .m ax ):单位质量的厌氧污泥在单位时间内的最大产甲烷量(mlCH 4/gVSS.d );最大比COD 去除速率(U max.COD ):单位质量的厌氧污泥在单位时间内的最大的COD 降解量(gCOD/gVSS.d )。
一、实验原理厌氧生物处理过程中的有机物降解速率或甲烷生成速率可用第五章中提出的相似的Monod 公式来描述,即:SK XS U dt dS s +⋅⋅-=-max (1) 式中:S ——基质浓度(gCOD 或BOD/L );t ——时间(d );U max ——最大比基质降解速度(d -1); X ——微生物或污泥浓度(gVSS/L ); K s ——饱和常数。
)(dtdSV Y dt dV r g CH -⋅⋅=4 (2) 式中:V CH4——间歇反应开始后的积累甲烷产量(ml ); Y g ——基质的甲烷转化系数(mlCH 4/gCOD ); V r ——间歇反应器的反应区容积(L )。
由(1)、(2)式得:SK XS U V Y dt dV s r g CH +⋅⋅⋅⋅=max 4 (3) 因为厌氧细菌的世代周期一般相对很长,合成量相对较少,在短期内(1~2天内)可以认为厌氧微生物的生物量不会发生变化,即上式中的X 可以认为是一个常数;同时,由于在反应初期基质浓度很高,即可以认为S >>K s ,此时式(3)就可以简化为:X V U X V U Y dtdV r CH r g CH ⋅⋅=⋅⋅⋅=⋅44max max )( (4) 或:441CH CH r U dtdV X V ⋅=⋅⋅max (5) 其中的4CH U .m ax 就是上面提到的厌氧污泥的最大比产甲烷速率。
实验六厌氧污泥活性的测试水处理教案(清华大学课程)

实验六 厌氧污泥活性的测试厌氧污泥的活性,实际上是指单位质量的厌氧污泥(以VSS 计)在单位时间内最多能产生的甲烷量,或者,是指单位质量的厌氧污泥(以VSS 计)在单位时间内最多能去除的有机物(以COD 计)。
因此,厌氧污泥活性一般可以用两个参数测量,即最大比产甲烷速率和最大比COD 去除率。
二者的定义分别如下:最大比产甲烷速率(4CH U .max ):单位质量的厌氧污泥在单位时间内的最大产甲烷量(mlCH 4/gVSS.d );最大比COD 去除速率(U max.COD ):单位质量的厌氧污泥在单位时间内的最大的COD 降解量(gCOD/gVSS.d )。
一、实验原理厌氧生物处理过程中的有机物降解速率或甲烷生成速率可用第五章中提出的相似的Monod 公式来描述,即:SK XS U dt dS s +⋅⋅-=-max (1) 式中:S ——基质浓度(gCOD 或BOD/L );t ——时间(d );U max ——最大比基质降解速度(d -1); X ——微生物或污泥浓度(gVSS/L ); K s ——饱和常数。
)(dtdSV Y dt dV r g CH -⋅⋅=4 (2) 式中:V CH4——间歇反应开始后的积累甲烷产量(ml ); Y g ——基质的甲烷转化系数(mlCH 4/gCOD ); V r ——间歇反应器的反应区容积(L )。
由(1)、(2)式得:SK XS U V Y dt dV s r g CH +⋅⋅⋅⋅=max 4 (3) 因为厌氧细菌的世代周期一般相对很长,合成量相对较少,在短期内(1~2天内)可以认为厌氧微生物的生物量不会发生变化,即上式中的X 可以认为是一个常数;同时,由于在反应初期基质浓度很高,即可以认为S >>K s ,此时式(3)就可以简化为:X V U X V U Y dtdV r CH r g CH ⋅⋅=⋅⋅⋅=⋅44max max )( (4) 或:441CH CH r U dtdV X V ⋅=⋅⋅max (5) 其中的4CH U .max 就是上面提到的厌氧污泥的最大比产甲烷速率。
厌氧生物处理的影响因素有哪些?

厌氧生物处理的影响因素有哪些?1.温度:存在两个不同的最佳温度范围(55℃左右,35℃左右)。
通常所称高温厌氧消化和低温厌氧消化即对应这两个最佳温度范围。
2.pH值:厌氧消化最佳pH值范围为6.8~7.2。
3.有机负荷:由于厌氧生物处理几乎对污水中的所有有机物都有降解作用,因此讨论厌氧生物处理时,一般都以CODcr来分析研究,而不象好氧生物处理那样必须以BOD5为依据。
厌氧处理的有机负荷通常以容积负荷和一定的CODcr去除率来表示。
4.营养物质:厌氧法中碳氮磷的比值控制在CODcr:N:P=(200~300):5:1即可。
甲烷菌对硫化氢的最佳需要量为11.5mg/L。
有时需补充某些必需的特殊营养元素,甲烷菌对硫化物和磷有专性需要,而铁、镍、锌、钴、钼等对甲烷菌有激活作用。
5.氧化还原电位:氧化还原电位可以表示水中的含氧浓度,非甲烷厌氧微生物可以在氧化还原电位小于+100mV的环境下生存,而适合产甲烷菌活动的氧化还原电位要低于-150mV,在培养甲烷菌的初期,氧化还原电位要不高于-330mV。
6.碱度:废水的碳酸氢盐所形成的碱度对pH值的变化有缓冲作用,如果碱度不足,就需要投加碳酸氢钠和石灰等碱剂来保证反应器内的碱度适中。
7.有毒物质。
8.水力停留时间:水力停留时间对于厌氧工艺的影响主要是通过上流速度来表现出来的。
一方面,较高的水流速度可以提高污水系统内进水区的扰动性,从而增加生物污泥与进水有机物之间的接触,提高有机物的去除率。
另一方面,为了维持系统中能拥有足够多的污泥,上流速度又不能超过一定限值。
营养物质对厌氧生物处理的影响体现在哪些方面厌氧微生物的生长繁殖需要摄取一定比例的CNP及其他微量元素,但由于厌氧微生物对碳素养分的利用率比好氧微生物低,一般认为,厌氧法中碳氮磷的比值控制在CODcr:N:P=(200~300):5:1即可。
还要根据具体情况,补充某些必需的特殊营养元素,比如硫化物、铁、镍、锌、钴、钼等。
污水处理污泥厌氧消化技术全解

污水处理污泥厌氧消化技术全解(1)采用两级消化时,一级消化池和一级消化池的停留时间之比可采用1:1、2:1或3:2,其中以采用2:1的最多:一级消化池的液位高度必须能满足污泥自流到一级消化池的需要,地下水位较高时、必须考虑池体的抗浮,对消化池进行清理时最好选择地下水位较低的时候进行。
(2)污泥厌氧消化池一般使用水密性、气密性和抗腐蚀性良好的钢筋混凝土结构,直径通常为6~35m,总高与直径之比为0.8~1.0,内径与圆柱高之比为2:1。
池底坡度为8%,池顶距泥面的高度大于1.5m,顶部集气罩直径一般为2m、高度为1~2m、大型消化池集气罩的直径和高度最好分别大于4m和2m。
(3)污泥厌氧消化池一般设置进泥管、出泥管、上清液排出管、溢流管、循环搅拌管、沼气出管、排空管、取样管、人孔、测压管、测温管等,一般进泥管布置在池中泥位以上、其位置、数量和形式应有利于搅拌均匀、破碎浮渣,污泥管道的最小管径为150mm,管材应耐腐蚀或作防腐处理,同时配备管道清洗设备。
(4)上清液排出管可在不同的高度设置3~4个、最小直径为75mm,并有与大气隔断的措施;溢流管要比进泥管大一级,且直径不小于200mm,溢流高度要能保证池内处于正压状态;排空管可以和出泥管共用同一管道;取样管最小直径为100mm,至少在池中和池边各设一根,并伸入泥位以下0.5m;人孔要设两个,且位置合理。
(5)池四周壁和顶盖必须采取保温措施。
污泥厌氧消化池的影响因素有哪些(1)温度、pH值、碱度和有毒物质等是影响消化过得的主要因素、其影响机理和厌氧废水处理相同。
(2)污泥龄与投配率。
为了获得稳定的处理效果,必须保持较长的泥龄。
有机物降解程度是污泥龄的函数,而不是进泥中有机物的函数。
(3)污泥搅拌。
通过搅拌可以使投加新鲜污泥与池内原有成熟污泥迅速充分地混合均匀,从而达到温度、底物浓度、细菌浓度分布完全一致,加快消化过程,提高产气量。
同时可防止污泥分层或泥渣层。
污水处理厂控制厌氧消化污泥浓度的方法

污水处理厂控制厌氧消化污泥浓度的方法有污泥消化工艺的污水处理厂,投入消化池的污泥浓度一般为2%~6%,多数在4%左右。
在其它条件具备,消化天数一定时,只要提高投入污泥的浓度,在消化池内种泥充分存在的条件下,气体发生量有明显的增加。
为此有些污水处理厂采用浓缩池浓缩后再进消化池或直接加药机械脱水后,再加入消化池的方法来降低含水率,提高消化池内含固率,增加沼气产量。
提高进入消化池污泥浓度有以下优点。
(1)消化天数一定,其它条件具备,投入的污泥浓度提高后,减少了原污泥中的水量,使消化池体积可缩小,一次性投资费用降低。
(2)提高了污泥浓度等于减少了污泥含水量。
在加热消化池内同体积污泥时等于减少了单位加热量。
若污泥浓度增加1倍,则加温所需热量为E′=0.4E+0.2E=0.6E,由此可见,加温热量节约40%。
不过污泥浓度提高后需注意下限问题。
一般不超过6%,否则就得重新选择更强的搅拌装置和特殊的消化池形状。
(3)污泥浓度提高,污泥黏度也增加。
消化池内变得不容易充分混合,需提高搅拌强度和循环泵的功率。
当污泥浓度从5%增加时其黏度陡升。
(4)当污泥浓度在4%~5%时,有突跃点存在,在5%以上时搅拌功率急剧增加,原有的搅拌功率和送泥泵、循环泵的功率需及时增大。
池壁也需改造或重新选择。
厌氧污水处理

厌氧污水处理厌氧污水处理是一种常见的污水处理方法,它能够有效地处理含有有机物的废水,将有机物转化为沼气和沉淀物,达到净化水质的目的。
下面将详细介绍厌氧污水处理的标准格式文本。
1. 污水处理工艺流程:厌氧污水处理普通包括预处理、厌氧消化和后处理三个步骤。
首先,将原始污水通过格栅、沉砂池等预处理设备去除较大的固体颗粒物,然后进入厌氧消化池进行有机物的降解,最后经过后处理设备对沼气和沉淀物进行处理。
2. 厌氧消化池的设计要点:(1)温度控制:厌氧消化池的温度通常控制在30-40摄氏度,可以通过加热或者保温设备来实现。
(2)PH值控制:厌氧消化池的PH值通常在6.5-7.5之间,可以通过添加中性化剂来调节。
(3)有机负荷控制:厌氧消化池的有机负荷通常控制在0.5-1.5kgCOD/m3·d之间,具体根据污水水质和处理效果来确定。
3. 后处理设备:(1)沼气利用:通过厌氧消化产生的沼气可以用于发电、热能供应等方面,提高能源利用效率。
(2)沉淀物处理:厌氧消化后产生的沉淀物可以进行浓缩、脱水处理,然后用于土壤改良等方面。
4. 厌氧污水处理的优势:(1)能够有效处理高浓度有机废水,降低COD和BOD等指标;(2)产生沼气可用于能源回收,节约能源成本;(3)减少废水处理过程中的化学药剂使用,降低运营成本;(4)减少对环境的污染,提高水质的净化效果。
5. 厌氧污水处理的应用领域:(1)城市污水处理厂:厌氧污水处理可用于城市污水处理厂的二级处理工艺,提高处理效果。
(2)工业废水处理:厌氧污水处理适合于食品、饮料、纺织、造纸等工业废水处理领域。
(3)农村污水处理:厌氧污水处理可用于农村地区的污水处理,解决农村环境污染问题。
总之,厌氧污水处理是一种高效、节能、环保的污水处理方法,具有广泛的应用前景。
通过合理设计和运营管理,可以实现污水的净化和资源的回收利用,为环境保护和可持续发展做出贡献。
厌氧发酵指标测定方法(精品)

COD的测定(快速密闭催化消解法)试验步骤:1、取1ml滤液(5000r/min条件下离心10min,过滤)于50ml容量瓶中定容(稀释倍数由滤液SCOD的浓度而定,通常是稀释至1000-2500mg/L,选择消化液Ⅰ),从中量取3ml于消化管(注意干燥)中,每个样品做3个重复;同时以同量的蒸馏水代替样品,做空白试验。
2、依次加入1ml掩蔽剂、3ml消化液(注意准确)、5ml催化剂(每加入一种试剂后都要摇匀),旋紧密封塞,混匀。
3、放入已预热到165℃的消解炉中,消解22min,冷却。
4、将样液移至150ml锥形瓶中,用蒸馏水冲洗消化管(至少洗3次,共约30ml),冲洗液移入锥形瓶中。
5、加3滴邻菲罗啉指示剂,用硫酸亚铁标准溶液滴定,溶液颜色由黄到蓝突变成红褐色为终点,记录硫酸亚铁标准溶液用量(样品的记为V1,空白对照的记为V)。
6、滴定使用0.05 mol/LFeSO4:先配0.2mol/L FeSO4,然后稀释得到(量取250mL0.2mol/LFeSO4于1000mL容量瓶即得0.05 mol/LFeSO4,标定后使用)标定方法:准确吸取10.00mL重铬酸钾标准溶液(C(1/6K2Cr2O7)=0.2500mol/L)于250mL锥形瓶中,加水稀释至55mL左右,缓慢加入5mL浓硫酸,混匀,冷却后,加入2-3滴邻菲啰啉指示剂,用0.05 mol/LFeSO4滴定,溶液的颜色由黄色经蓝绿色至红褐色即未终点。
C[FeSO4]=0. 25*10/V计算:COD(mg·L-1)=(V0-V1)×C×8×1000×50/V2V1——滴定样品消耗的硫酸亚铁标准溶液的体积,mLV——滴定空白消耗的硫酸亚铁标准溶液的体积,mLV2――水样体积,mL,本试验中V2=3mLC——硫酸亚铁标液的浓度,mol·L-150――水样的稀释倍数8――氧(1/2O)摩尔质量V’——硫酸亚铁标准溶液的标定时,用去的硫酸亚铁溶液的体积,mL试剂配制:掩蔽剂:称取30.0g硫酸汞(分析纯)溶于100mL的10%硫酸中。
厌氧消化的影响因素有哪些

厌氧消化的影响因素有哪些厌氧消化是一种微生物通过在缺氧条件下分解有机物质来生产能量的过程。
它广泛应用于工业废弃物处理、农业废弃物处理和能源生产等领域。
厌氧消化的效果受到多种因素的影响,下面将详细介绍其中的一些主要因素。
1.温度:温度是影响厌氧消化过程的关键因素之一、在一定的温度范围内,厌氧消化的速率会随温度的升高而增加。
通常,对于厌氧消化系统来说,适宜的工作温度范围是30-40°C。
当温度过低或过高时,微生物的活性会受到抑制,从而影响厌氧消化过程的效果。
2.pH值:适宜的pH范围对于维持良好的厌氧消化过程非常重要。
多数厌氧消化系统的适宜pH范围为6.5-8.5、过低或过高的pH值都会对微生物的生长和代谢活动产生不利影响,进而影响消化过程的效果。
3.营养物质含量:厌氧消化过程需要碳源、氮源和磷源等营养物质的供应。
适当的营养物质含量可以促进微生物的生长和代谢活动,并有助于提高消化效果。
然而,过多或过少的营养物质供应都会对系统的稳定性和效果产生负面影响。
4.水分含量:适宜的水分含量对于维持良好的厌氧消化过程至关重要。
水分含量过高会导致系统的通气不良,影响微生物的生长和代谢活动;水分含量过低则会导致微生物的生理活动受限,从而影响消化效果。
5.其他环境因素:除了上述因素外,厌氧消化的效果还受到其他环境因素的影响,比如厌氧消化系统中的微生物群落结构,系统的有机物负荷和冲击负荷,以及系统的混合和通气等。
综上所述,厌氧消化的效果受到温度、pH值、营养物质含量、水分含量和其他环境因素的影响。
了解并控制这些因素,可以对厌氧消化系统进行优化,提高系统的稳定性和消化效果。
厌氧氨氧化底物比例

厌氧氨氧化底物比例
厌氧氨氧化底物比例一般指的是在厌氧氨氧化过程中,底物(即
氨氮和有机物)的比例。
厌氧氨氧化是一种生物处理废水的过程,利
用厌氧氨氧化菌将底物转化为硝酸盐(NO3-)。
在厌氧氨氧化底物比例中,最常见的底物比例是以COD(化学需
氧量)和NH3-N(氨氮)为基础。
一般来说,较低的COD/NH3-N比例有助于达到较高的氮负荷去除率。
通常认为,对于大多数废水处理系统,COD/NH3-N比例在 10:1 到15:1 之间是比较合适的。
较低的COD/NH3-N比例有助于维持良好的厌
氧氨氧化反应条件,并提高氮负荷去除率。
然而,底物比例的最佳范围也会受到废水质量、处理系统设计和
运营条件等因素的影响。
因此,在具体的环境中,需要根据实际情况
进行调整和优化。
此外,还有一些其他因素也会影响厌氧氨氧化底物比例,如温度、pH值、溶解氧水平等。
这些因素的变化也可能会对底物比例产生影响,因此在确定底物比例时,需要综合考虑这些因素。
总而言之,厌氧氨氧化底物比例需要综合考虑废水特性、处理系
统要求和操作条件等因素,通过实际测试和调整来确定最佳的底物比例。
厌氧碳氮磷比例

厌氧碳氮磷比例
在微生物代谢过程中,氮,碳,氧,磷是最重要的元素,其中碳氮磷(C:N:P)的比例是控制微生物生长的最重要的因素。
一般来说,在自然环境中,碳氮磷的比例约为100:11:1,
而在厌氧碳氮磷比例中,碳氮磷的比例约为100:1:0.1。
厌氧碳氮磷比例指的是环境中碳,氮,磷的比例,它对微生物的生长有重要的影响。
厌氧碳氮磷比例较高时,氮和磷的摄入量较少,微生物生长和繁殖会受到限制,因此厌氧碳氮磷比例是调节微生物生长和繁殖的重要因素。
厌氧碳氮磷比例的变化也会影响微生物的代谢产物,当厌氧碳氮磷比例较高时,微生物会释放更多的硫酸盐,而当厌氧碳氮磷比例较低时,微生物会释放更多的氨氮和硝酸盐。
因此,厌氧碳氮磷比例也是控制微生物代谢产物的重要因素。
此外,厌氧碳氮磷比例也会影响厌氧微生物的群落结构,当厌氧碳氮磷比例较高时,厌氧细菌会优势生长,而当厌氧碳氮磷比例较低时,厌氧放线菌会优势生长。
因此,厌氧碳氮磷比例也是影响厌氧微生物群落结构的重要因素。
总之,厌氧碳氮磷比例对微生物的生长繁殖,代谢产物,群落结构都有重要的影响,因此,在生态学研究中,对厌氧碳氮磷比例的研究对于了解微生物群落的运行有重要的意义。
关于厌氧消化的小知识

厌氧消化的影响因素1、温度温度适宜时.细菌发育正常,有机物分解完全,产气量高。
根据操作温度的不同,可将厌氧消化分为:①低温消化:可不控制消化温度(≤30℃);②中温消化:30-35℃;③高温消化:50-56℃。
实际上,在0-56℃的范围内,产甲烷菌并没有特定的温度限制,然而在一定温度范围内被驯化以后,温度稍存升降(±2℃),都可严重影响甲烷消化作用,尤其是高温消化,对温度变化更为敏感。
因此,在厌氧消化操作运行过程中,应尽量保持温度不变。
2、污泥投配率投配率系指每月加入消化池的新鲜污泥体积与消化池体积的比率,以百分煎计。
根据经验.中温消化的新鲜污泥投配率以6%-8%为宜。
在设计时,新鲜污泥投配率可在5%-12%之间选用。
若要求产气量多,采用下限值;若以处理污泥为主.则可采用上限值。
一般来说,投配率大,则有机物分解程度减少,产气量下降,所需消化池容积小;反之,则产气量增加.所需消化池容积大。
3、营养与碳氮比消化池的营养由投配污泥供给,营养配比中最重要的是C/N比。
C/N比太高,细菌氮量不足,消化液缓冲能力降低,pH值容易下降;C/N比太低,含氮量过多,pH值可能上升到8.0以上,脂肪酸的铵盐发生积累,使有机物分解受到抑制。
据研究,对于污泥消化处理来说, C/N比以(10-20):l较合适,因此,初沉池污泥的消化较好,剩余活性污泥C/N比约为5:1,所以不宜单独进行消化处理。
4、搅拌搅拌操作可以使鲜污泥与熟污泥均匀接触,加强热传导,均匀地供给细菌以养料,打碎液面上的浮渣层,提高消化池的负荷。
20世纪40年代的消化池设有搅拌设施,称标准消化池,其消化时间长,需30-60d。
有搅拌设备的消化池消化时间为l0-15d。
5、酸碱度酸碱度影响消化系统的pH值和消化液的缓冲能力,因此消化系统中有一定的碱度要求。
若碱度不足,可投加石灰、无水氨或碳酸铵进行调节。
但大量投加石灰,常使碱度偏高,泥量增加,应尽量合理利用。
厌氧好氧的生化调试1讲解

南京德磊科技有限公司厌氧好氧的生化调试目录一、厌氧的生化调试 (4)1. 厌氧的生化调试准备 (4)1.1 厌氧的生化调试概念及原理 (4)1.2 厌氧的生化调试所需仪器 (4)1.3 厌氧生化调试工作人员 (5)1.4 厌氧生化调试备料 (5)2. 厌氧的生化调试运行 (5)2.1 厌氧的生化调试影响因素 (5)2.2 厌氧池的调试操作 (6)3. 厌氧的生化调试具体实例 (7)3.1 UASB厌氧反应器使用须知 (7)3.2 UASB厌氧反应器的调试 (8)4. 厌氧的生化调试常见问题 (11)二、好氧的生化调试 (13)1. 好氧的生化调试准备 (13)1.1 好氧的生化调试概念及原理 (13)1.2 好氧的生化调试所需仪器 (13)1.3 好氧生化调试工作人员 (13)1.4 好氧生化调试备料 (13)2.好氧的生化调试 (14)2.1主要控制条件 (14)2.2好氧生化处理调试操作 (14)2.3生化池运行状态判断 (15)3.好氧的生化调试常见问题 (15)4.日常运行管理 (16)一、厌氧的生化调试1. 厌氧的生化调试准备1.1 厌氧的生化调试概念及原理厌氧处理是利用厌氧菌的作用,去除废水中的有机物,通常需要时间较长。
厌氧过程可分为水解阶段、酸化阶段和甲烷化阶段。
废水厌氧生物处理过程不需另加氧源,故运行费用低。
此外,它还具有剩余污泥量少,可回收能量(CH4)等优点。
其主要缺点是反应速度较慢,反应时间较长,处理构筑物容积大等。
但通过对新型构筑物的研究开发,其容积可缩小。
此外,为维持较高的反应速度,需维持较高的反应温度,就要消耗能源。
图一厌氧的生化调试原理1.2 厌氧的生化调试所需仪器根据厌氧生化调试工艺原理,需要测量的有:pH值,COD,温度。
根据工艺原理,所需测量仪器为:COD检测仪、NH3-N检测仪、pH检测仪、BOD检测仪、DO检测仪、温度计、潜水泵(配软管)、SS。
1.3 厌氧生化调试工作人员一般情况下,完成厌氧的生化调试需要2-3人,其中各人分工为:一人负责检测,检测内容包括pH值,COD,温度等;一人负责调试巡查,一旦发生问题,及时反馈,及时解决;一人负责调水,进水量的控制和污泥量的控制。
实验六 厌氧污泥活性的测试

实验六 厌氧污泥活性的测试厌氧污泥的活性,实际上是指单位质量的厌氧污泥(以VSS 计)在单位时间内最多能产生的甲烷量,或者,是指单位质量的厌氧污泥(以VSS 计)在单位时间内最多能去除的有机物(以COD 计)。
因此,厌氧污泥活性一般可以用两个参数测量,即最大比产甲烷速率和最大比COD 去除率。
二者的定义分别如下:最大比产甲烷速率(4CH U .m ax ):单位质量的厌氧污泥在单位时间内的最大产甲烷量(mlCH 4/gVSS.d );最大比COD 去除速率(U max.COD ):单位质量的厌氧污泥在单位时间内的最大的COD 降解量(gCOD/gVSS.d )。
一、实验原理厌氧生物处理过程中的有机物降解速率或甲烷生成速率可用第五章中提出的相似的Monod 公式来描述,即:SK XS U dt dS s +⋅⋅-=-max (1) 式中:S ——基质浓度(gCOD 或BOD/L );t ——时间(d );U max ——最大比基质降解速度(d -1); X ——微生物或污泥浓度(gVSS/L ); K s ——饱和常数。
)(dtdSV Y dt dV r g CH -⋅⋅=4 (2) 式中:V CH4——间歇反应开始后的积累甲烷产量(ml ); Y g ——基质的甲烷转化系数(mlCH 4/gCOD ); V r ——间歇反应器的反应区容积(L )。
由(1)、(2)式得:SK XS U V Y dt dV s r g CH +⋅⋅⋅⋅=max 4 (3) 因为厌氧细菌的世代周期一般相对很长,合成量相对较少,在短期内(1~2天内)可以认为厌氧微生物的生物量不会发生变化,即上式中的X 可以认为是一个常数;同时,由于在反应初期基质浓度很高,即可以认为S >>K s ,此时式(3)就可以简化为:X V U X V U Y dtdV r CH r g CH ⋅⋅=⋅⋅⋅=⋅44max max )( (4) 或:441CH CH r U dtdV X V ⋅=⋅⋅max (5) 其中的4CH U .m ax 就是上面提到的厌氧污泥的最大比产甲烷速率。
厌氧消化实验
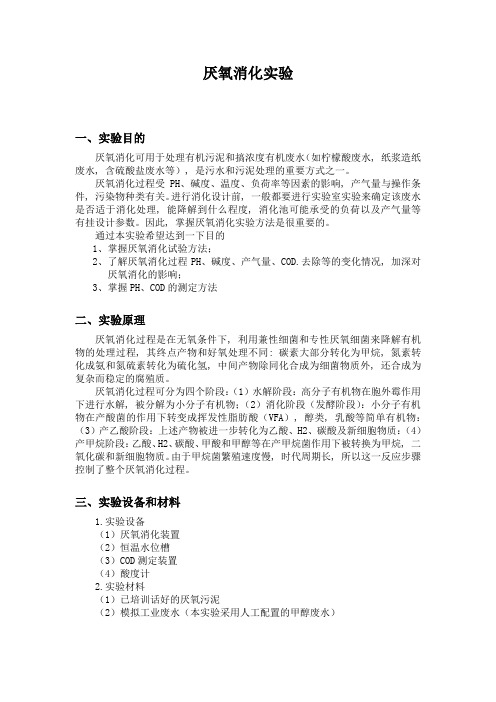
厌氧消化实验一、实验目的厌氧消化可用于处理有机污泥和搞浓度有机废水(如柠檬酸废水, 纸浆造纸废水, 含硫酸盐废水等), 是污水和污泥处理的重要方式之一。
厌氧消化过程受PH、碱度、温度、负荷率等因素的影响, 产气量与操作条件, 污染物种类有关。
进行消化设计前, 一般都要进行实验室实验来确定该废水是否适于消化处理, 能降解到什么程度, 消化池可能承受的负荷以及产气量等有挂设计参数。
因此, 掌握厌氧消化实验方法是很重要的。
通过本实验希望达到一下目的1、掌握厌氧消化试验方法;2、了解厌氧消化过程PH、碱度、产气量、COD.去除等的变化情况, 加深对厌氧消化的影响;3、掌握PH、COD的测定方法二、实验原理厌氧消化过程是在无氧条件下, 利用兼性细菌和专性厌氧细菌来降解有机物的处理过程, 其终点产物和好氧处理不同: 碳素大部分转化为甲烷, 氮素转化成氨和氮硫素转化为硫化氢, 中间产物除同化合成为细菌物质外, 还合成为复杂而稳定的腐殖质。
厌氧消化过程可分为四个阶段:(1)水解阶段:高分子有机物在胞外霉作用下进行水解, 被分解为小分子有机物;(2)消化阶段(发酵阶段):小分子有机物在产酸菌的作用下转变成挥发性脂肪酸(VFA), 醇类, 乳酸等简单有机物:(3)产乙酸阶段:上述产物被进一步转化为乙酸、H2、碳酸及新细胞物质:(4)产甲烷阶段:乙酸、H2、碳酸、甲酸和甲醇等在产甲烷菌作用下被转换为甲烷, 二氧化碳和新细胞物质。
由于甲烷菌繁殖速度慢, 时代周期长, 所以这一反应步骤控制了整个厌氧消化过程。
三、实验设备和材料1.实验设备(1)厌氧消化装置(2)恒温水位槽(3)COD测定装置(4)酸度计2.实验材料(1)已培训话好的厌氧污泥(2)模拟工业废水(本实验采用人工配置的甲醇废水)四、实验步骤1.配置甲醇废水400ml备用。
甲醇废水配比如下: 甲醇2%, 乙醇0.2%, NH4CL0.05%\J甲酸钠0.5%、KH2PO4 0.025%、PH=7.0~~7.5;2.消化瓶内有驯化好的消化污泥混合液400ml, 从消化瓶中倒出50ml消化液;3.加入50ml配置的人工废水, 摇匀后盖紧瓶塞, 将消化瓶放入恒温水浴槽中, 控制温度在35℃左右;4.每隔2h摇动一次, 并记录产气量, 共记录5次, 填入表1.产气量的计算采用排水集气法;5、24小时过后取样分析出水COD, 同时分析进水时的COD, 填入表计算:COD =(( V空白—V )×0.1×8×1000)/ 20V空白= 24.3 ml五、实验结果讨论可以看到废水在厌氧条件下, 在微生物的作用下COD慢慢的被降解, 降解比较稳定。
厌氧反应器参数

厌氧反应器参数概述厌氧反应器是一种用于处理包括有机废水和有机废弃物在内的高有机物浓度废物的设备。
通过通过各种生物过程将有机物质降解成甲烷和二氧化碳等气体,从而达到净化废水和发电的目的。
为了保证厌氧反应器的正常运行和高效处理有机废物,需要合理设置和控制各种参数。
厌氧反应器的参数厌氧反应器的参数包括温度、PH值、有机物质浓度、载体比例、停留时间等。
温度适宜的反应温度是保证厌氧反应器高效运行的重要参数。
温度过高或过低都会对反应产生不利影响。
一般来说,厌氧反应器的适宜温度范围为35-40摄氏度。
过高的温度会导致厌氧菌的活性下降甚至死亡,而过低的温度则会影响反应速率和产气量。
因此,必须严格控制反应器的温度,可以通过加热或换热控制系统来实现。
PH值PH值是指在水溶液中酸碱程度的度量。
对于厌氧反应器来说,适宜的PH范围为6.8-7.4。
过低或过高的PH值都会抑制厌氧菌的生长和代谢,从而影响反应效果。
为了维持合适的PH值,可以在反应器中加入缓冲液,也可通过控制进料过程中的PH值来实现。
有机物质浓度有机物质的浓度是评估废物处理效果的一个关键指标。
厌氧反应器可以处理高浓度有机物质,但过高的浓度会影响反应器内菌种的代谢活性和产气速率。
因此,对于不同类型的有机物,需要确定适宜的进料浓度,以确保反应器能够稳定运行。
载体比例厌氧反应器通常需要加入载体,如碎石、塑料填料等,以提供菌种生长和附着的表面。
适当的载体比例可以增加菌种生长的表面积,促进反应效果。
不同的废物类型和处理规模可能需要选择不同的载体,以达到最佳处理效果。
停留时间停留时间是指废物在反应器中停留的时间。
适当的停留时间可以使废物充分与菌种接触,最大限度地提高有机物的降解率。
停留时间的长短需要根据废物类型、反应器尺寸和处理要求等因素进行调整。
厌氧反应器参数的调整与优化为了使厌氧反应器能够达到更好的废物处理效果,需要进行参数的调整和优化。
温度调整在实际运行中,可以通过加热或冷却系统控制反应器的温度。
- 1、下载文档前请自行甄别文档内容的完整性,平台不提供额外的编辑、内容补充、找答案等附加服务。
- 2、"仅部分预览"的文档,不可在线预览部分如存在完整性等问题,可反馈申请退款(可完整预览的文档不适用该条件!)。
- 3、如文档侵犯您的权益,请联系客服反馈,我们会尽快为您处理(人工客服工作时间:9:00-18:30)。
Assessment of optimum dilution ratio for biohydrogen production by anaerobic co-digestion of press mud with sewage and waterB.Radjaram a ,⇑,R.Saravanane b ,1a Department of Civil Engineering,Pondicherry Engineering College,Puducherry 605014,IndiabEnvironmental Engineering Laboratory,Department of Civil Engineering,Pondicherry Engineering College,Puducherry 605014,Indiaa r t i c l e i n f o Article history:Received 21March 2010Received in revised form 16November 2010Accepted 17November 2010Available online 26November 2010Keywords:Press mud Sewage UASBBiohydrogen Co-digestiona b s t r a c tAnaerobic co-digestion of press mud with water or sewage at ratios of 1:7.5,1:10and 1:12.5were per-formed in continuously fed UASB reactors for hydrogen production.At a constant hydraulic retention time of 30h,the specific hydrogen production rate was 187mL/g volatile solids (VS)reduced during max-imum biohydrogen production of 7960mL/day at a 1:10ratio of press mud to sewage.Chemical oxygen demand (COD)and VS reductions of 61%and 59%were noted on peak biohydrogen yield.A pH range of 5–6was suitable at ambient temperature for entire process;a lower pH was inhibitory.Co-digestion of acidic press mud with sewage controlled pH for fermentation.Hence press mud can be exploited for bio-hydrogen production.Ó2010Elsevier Ltd.All rights reserved.1.IntroductionHydrogen is a promising alternative to carbon-based fuels be-cause it is clean,renewable and has a high energy yield of 122kJ/g (Chang and Lin,2004).At present,hydrogen is produced mainly from fossil fuels,biomass and water using chemical or bio-logical processes.One such biological process is anaerobic hydro-gen fermentation which can utilize highly concentrated organic wastewater and biomass,such as municipal solid wastes and sew-age sludge as raw material (Das and Veziroglu,2001).Press mud is another potential waste source for hydrogen production.About 4%of crushed sugar cane is converted to press mud,and annually about 4.2million tons of press mud is available from the sugar industry in India (Saravanane and Radjaram,1998).It is an acidic,thus mildly corrosive,compressed fibrous waste that contains 5–15%sugar (Partha and Sivasubramanium,2006)and 84%is bio-degradable.Earlier studies on press mud examined the feasibility of methane production by methanogenesis at pH of 8(Saravanane and Radjaram,1998).In contrast,hydrogen production is favoredat an acid pH (G´omez et al.,2006;Mohanakrishna et al.,2010).As a semi-solid material,press mud cannot be fermented unless water or sewage is added.Fermentation can be carried out in anupflow anaerobic sludge blanket (UASB)process since this anaero-bic treatment system has a high treatment efficiency and a short hydraulic retention time (HRT)(Chang and Lin,2004).Fermenta-tion in a continuous stirred tank reactor does not seem practical since this type of reactor was unable to maintain high level of fer-mentative biomass for hydrogen production and its specific hydro-gen production rate was low (Yu et al.,2002).Dilution is a key parameter in anaerobic fermentation as low dilution leads to prod-uct inhibition and high dilution leads to wash out of biomass in reactor (Han and Shin,2004).In the present study water and sew-age were used to dilute press mud to allow efficient fermentation.2.Methods 2.1.SeedSeed sludge was collected from a municipal wastewater treatment plant maintained by the Public Works Department,Pondicherry,India.It was sieved through a wire mesh of Ø0.5mm to remove solid materials that may block the flow in the pump.Cow dung was mixed with water at a 1:2ratio and digested under anaerobic conditions for 30days at a pH between 5and 6by adding HCl/NaOH as needed.The digest was filtered through wire mesh (Ø0.5mm)to remove fibrous materials,mixed with seed sludge at 4:1ratio,and heated to 70°C for 1h to inhibit the methanogens,and used as seed.The characteristics of the seed (fermented cow dung diluted with sludge)are given in Table 1.0960-8524/$-see front matter Ó2010Elsevier Ltd.All rights reserved.doi:10.1016/j.biortech.2010.11.075⇑Corresponding author.Tel.:+914132643007,mobile:+919443748471;fax:+914132643008.E-mail addresses:radjaram@ (B.Radjaram),saravananae@ (R.Saravanane).1Tel.:+914132655281x210,mobile:+919345156037;fax:+914132655101.2.2.Feed substrateThe characteristics of press mud and sewage are given in Table2. In preliminary experiments it was determined that a minimum dilution of1:7.5of press mud and water was necessary to obtain a hydrogen fermentation substrate that can befiltered and ulti-mately used in a continuousflow system.Therefore,feeds for reac-tor R1were prepared for three series of experiments by diluting 4kg press mud with30,40and50L of water to obtain dilution ratios of1:7.5,1:10,and1:12.5,respectively.Feeds for reactor R2 were prepared at the same dilution ratios by adding sewage instead of water.The press mud/sewage and press mud/water mixtures were allowed to soak for4h,filtered through wire mesh (Ø0.5mm)to removefibers and thefiltrate was fed into the reac-tors.The characteristics of the feed substrate are given in Table1.2.3.Bioreactor systemTwo UASB reactors of volume20L each were used in this study. The cylindrical plexiglas reactors had an internal diameter10cm and a height of190cm(H/D>10)with a gas liquid separator at the top(diameter,20cm;height,20cm)with an effluent port at 15cm from the bottom of the gas liquid separator.Seven sampling ports were evenlyfixed over the entire height of the column at 25-cm interval.The gas liquid separator housed an inverted funnel connected to a wet gas meter through aflexible tube for measuring the gasflow rate.The reactor had provisions for feeding from the bottom and removal of effluent from the top.The reactor received feed from a feed tank through a peristaltic pump(Ravel RH P100L) as shown in the schematic diagram(Fig.1).The feed substrate in the feed tank was stirred at every20min for3min with a mechan-ical stirrerfitted in the tank to prevent settlement of solids.2.4.OperationReactors R1and R2were operated with press mud diluted with water and sewage,respectively.HRT wasfixed at30h since a high-er HRT does not lift the particulate substrate in the reactor column. The experiments were started in R1and R2with a1:7.5dilution and performance was observed till steady state was reached in both reactors.The operation was continued at steady state for30 additional days.Then,the dilution was changed to1:10and the performance was monitored for30days.Finally the dilution was changed to1:12.5for another30–34days.The pH of the reactors was between5and6,by adding HCl/NaOH as needed with the feed and the reactors were operated at ambient temperatures (30–38°C)without heating or cooling.2.5.Analytical methodsTemperature,pH and biohydrogen production were measured daily with a thermometer,pH probe and wet gas meter,while the gas composition was analyzed using a gas chromatograph (Nucon GC).The total volatile solids(VS),chemical oxygen demand (COD),volatile fatty acid(VFA),alkalinity,etc.were estimated oncea week by standard methods(APHA,1995).3.Results and discussion3.1.Start-up of UASB reactorDuring the start-up period,the UASB system was fed continu-ously with diluted substrate at a concentration starting from 2500to10,000mg COD/L to reach an organic loading rate(OLR) of8–20g/L/day.The pH in the reactor decreased from6.5to5.5 during the start-up period,while hydrogen production(Fig.2b) and COD removal efficiency(Fig.2c)gradually increased.Biohy-drogen production started on day29in R1,with an uneven output for76days.After76days,both biohydrogen production and COD removal efficiency stabilized in the system,reaching approxi-mately1600mL/day and70%,respectively(Fig.2b and c).Hydro-gen production started on day34in R2with an unsteady output up to day60.After60days both hydrogen yield and COD removal efficiency stabilized.These results revealed that anaerobic acti-vated sludge of reactors R2and R1possessed good acid-tolerance and stable hydrogen production ability,which indicated good acclimatization.3.2.Continuous hydrogen productionR1reached steady-state conditions,defined as consistent hydrogen production with a variation of less than10%,after 90days(Fig.2b).The hydrogen production was1900mL/day with a1:7.5diluted feed.When,the dilution was changed to1:10onTable1Characteristics of seed and feeds of R1and R2for dilutions of1:7.5,1:10and1:12.5.Substrate pH TS TDS TSS TVS TVDS TVSS Total COD Alkalinity VFASeed 6.7610.9 2.058.85 6.81 5.810.4019.03 1.82 Reactor R11:7.5 6.467.7 2.25 5.45 4.651 3.6512.4812.68 1.50 1:10 5.017.7 2.45 5.25 5.5 2.4 3.117.8815.85 5.22 1:12.5 5.6515.4 2.213.2 4.20.8 3.429.95 6.34 1.68Reactor R21:7.5 5.29.97.6 2.3 4.25 2.27 1.9810.5627.36 2.04 1:10 5.187.2 1.5 5.7 3.90.5 3.432.0347.550.34 1:12.5 6.12 6.6 5.620.98 3.2 2.480.728.3219.03 5.52All units are in g/L except pH.Table2Characteristics of press mud and sewage.Parameters a Press mud SewagepH 4.5–57.2COD(%)117.613.6C/N ratio24.0417.5Total solids(%)297.4Moisture content(%)71–Total volatile solid(%)84 5.8Organic carbon(%)48.80 6.1Nitrogen(%) 2.05 1.96Phosphorous(%)0.65–Potassium(%)0.28–Sodium(%)0.18–Calcium(%) 2.7–Sulphate(%) 1.07–Sugar(%)3–Wax(%)1–a Average values.2774 B.Radjaram,R.Saravanane/Bioresource Technology102(2011)2773–2780day120,production gradually reached5000–6000mL/day by day 136.After144days it reached7210mL/day andfinally attained a maximum of7820mL/day during days145–150(Fig.2b).When the dilution was changed to1:12.5on day150,gas production de-clined and did not stabilize(Fig.2b).Maximum hydrogen produc-tion was4.887L/kg press mud at1:10dilution in R1.Reactor R2 took60days to reach steady-state conditions.At a1:7.5press mud:sewage ratio,maximum hydrogen production was1990mL/ day on day89.When the dilution was changed to1:10on day 90,the gas yield dropped below1000mL/day for1week time, but increased thereafter(Fig.4b).The highest hydrogen production of7960mL/day occurred on day115.At a dilution of1:12.5,max-imum hydrogen production was3880mL/day(Fig.4b).Maximum hydrogen of4.990L/kg press mud added was evaluated at a1:10 dilution in R2.These yields are lower than those obtained with wheat feed and sweet sorghum fermentations which were56L/ kg feed at HRT of15h(Hawkes et al.,2008)and10.41L/kg feed (Georgia et al.,2008),respectively;however,the use of such sub-strates for hydrogen production is questionable since they are also used as animal feed.The yields were higher than those achieved with Rhodobacter sphaeroides RV which reached only1.4–1.6L/L reactor volume/day(Fascetti and Todini,1995)and1.3mL/mL por-ous glass media/h(Tsygankov et al.,1994)and required input of light.Earlier studies had demonstrated that sewage sludge diges-tion can produce hydrogen at the rate of3.75mL/min(Nicolau et al.,2008)and that acclimatized anaerobic activated sludge had a hydrogen producing ability as high as10.4m3H2/m3reactor/ day in a continuous reactor with an available volume of9.6L (Ren et al.,1995.The co-digestion experiments with press mud and sewage demonstrated that sewage was able to support hydrogen production since it yields4.99L/kg press mud feed,i.e.0.5m3/m3reactor volume/day.H2%gradually increased with experiment days and reached a maximum of50–55%during consistency periods of study in reac-tors1and2(Figs.2and4b).3.3.Assessment of COD loading rate,%reduction and specific hydrogen production rateCOD removalfluctuated in the initial start-up stage and later stabilized after80days of operation in R1(Fig.2c).COD reduc-tion was60–77%,70%and86%at1:7.5,1:10,and1:12.5dilu-tions,respectively(Fig.2c).The high COD reduction was possible due to the large column height(H/D>10)which pro-vided a long mixing path during substrateflow from inlet to outlet.Filling the column to about one third its heights with biomass allowed maintenance of adequate numbers of hydro-gen-producing bacteria in the reactor.Specific biohydrogen pro-duction rates(SBPR)were10.98,40.6mL,and 2.58mL/g COD reduced/day at maximum hydrogen production at1:7.5,1:10, and1:12.5dilution,respectively(Fig.3a).In R2,COD loading rates varied between6and25g/L/day(Fig.4c)and COD reduc-tions were36–41%,55–61%,and40–41%at the1:7.5,1:10,and 1:12.5dilutions,respectively(Fig.4c).Anaerobic fermentation of food waste in leaching bed reactor gave biohydrogen yield of 21.2–41.5mL/g COD at an HRT of25h(Kim et al.,2004).Biohy-drogen yield was26.13mol/kg COD reduced in molasses fer-mentation(Ren et al.,2006)and 1.8–2.3mM/g COD fed in cheese processing waste water(Yang et al.,2007)whereas in our study41mL/g COD reduced was achieved from a wasteB.Radjaram,R.Saravanane/Bioresource Technology102(2011)2773–27802775substrate by co-digestion.SBPR in R2was20–37,35–41,and 39–51mL/g COD reduced/day at1:7.5,1:10,and1:12.5dilu-tions,respectively(Fig.5a).With a decrease in the dilution ra-tio,substrate becomes dense and product inhibition occurs due to excess VFA accumulation in the reactor,but higher dilu-tion led to wash out of bacteria and decreased biohydrogen pro-duction.Han and Shin(2004)observed a similar outcome in theirstudy.of experiments,(b)biohydrogen yield and%H2,(c)COD loading rate and%reduction,(d)VS loading rate and%reduction of reactor3.4.Appraisal of Volatile solid loading rate,%reduction and SBPRVolatile solid(VS)loading rates reached a maximum of13g/L/ day in R1(Fig.2d).VS reduction was55%,90%,and69%at1:7.5,1:10,and1:12.5dilutions,respectively(Fig.2d).Hydrogen yield gradually increased after75days and was consistently around 1600±150mL/day at a1:7.5dilution with a SBPR of12.77mL/g VS reduced/day on peak output.Though the SPBR was as highas32.81mL/g VS reduced/day,it was not constant.SBPR was62.66 and17.92mL/g VS reduced/day at a1:10and1:12.5dilution, respectively(Fig.3a).The substrate in the feed tank underwent slow hydrolysis which resulted in VS accumulation during the initial stages up to30days(Fig.2d).In R2,VS loading rate varied between3and16g/L/day(Fig.4d).VS reductionfluctuated in the start-up stage and stabilized under steady state condition.VS reduction was between53–63%,57–59%,and40–57%at the 1:7.5,1:10,and1:12.5dilutions,respectively(Fig.4d).SBPR was highest at the1:10dilution as187mL/g VS were reduced per day (Fig.5a).Co-digestion of municipal solid waste and slaughter house waste gave H2yield of52.5–71.3mL/g VS reduced(G´omezet al.,2006)and9.33L H2/g VSS/day was observed in rice winery waste water(Yu et al.,2002),whereas in our co-digestion H2yield was187mL/g/VS reduced.As the reactor had a height/diame-ter>10,1.9times more than the normal UASB reactor(Castello et al.,2009)the biomass concentration increased from the initial level of150to a maximum of1200mm.The digested substrate of low densityfloats and reaches the upper portion of reactor as evident by separation and collapsing of biomass layer in reactor which will be removed at regular period.Haandel van and Lettinga (1994)noted similar observation in theirstudy.3.5.Observation of VFA,alkalinity and pHThe VFA concentration in the effluent of R1was high during the start-up stage and declined gradually(Fig.3c)indicating acid to hydrogen conversion after30days.The later increase was likely due to the accumulation of sludge in the reactor by the digested substrate mass.The sludge was removed daily at a rate of2L at the sampling port and this process reduced VFA accumulation to below15g/L.Before the production increased above1000mL/ day,a separation or parting of biomass layer in the reactor oc-curred at300mm from the inlet port.Subsequently the biomass level was separated by150mm gap of liquid.This separation oc-curred once in every3days showing an effective anaerobic reac-tion by upward movement of digested substrate.The separation layer lasted for4–12h,as the gas rose to the surface and particles settled.The VFA level was constant at a1:10dilution with 9516mg/L(Fig.3c).Sporadically discharging sludge is a feasible means of dealing with sludge production from a biological system. In order to appraise the performance of a UASB reactor,it is imper-ative to know whether the reactor is operated at its utmost sludge holdup.Hence,the reactor could be operated by periodically dis-charging excess sludge,before sludge attains a maximum level (Haandel van and Lettinga,1994).VFA production followed an un-steady profile during start-up in R2,but reached consistency dur-ing steady state gas yield(Fig.5c).The VFA of the effluent was 19,202,180,and240mg/L at1:7.5,1:10and1:12.5dilutions, respectively(Fig.5c).Alkalinity was lower at the1:10dilution in R1(9516mg/L)than at the other dilutions and gave maximum biohydrogen yield (Fig.3d).In R2,alkalinity levels of the feedfluctuated between 60and41g/L during the start-up period,rose to57g/L at the 1:10dilution and declined to19g/L at the1:12.5dilutions (Fig.5d).The hydrogen yield was maximum at elevated alkalinity of feed(57g/L)and effluent(38g/L)while VFA levels were low.Feed pH was maintained between5and6by acidic press mud, an added advantage for fermentation.Studies on municipal solid waste and slaughter house waste fermentation found5–6as opti-mum pH(G´omez et al.,2006)and food waste with sewage sludge co-digestion was at a pH of6(Kim et al.,2004)indicating particu-late substrates requires a pH range of5–6.Due to anaerobic fer-mentation,the pH of the effluent was always near6.3.6.Assessment of VSS/TSS and VFA/alkalinity ratiosThe volatile suspended solids to total suspended solids ratio (VSS/TSS)in the UASB reactor denotes the biomass components of the sludge and variation in VSS/TSS indicates change in biomass components.A VSS/TSS ratio of0.6–0.8has been reported in UASB reactor treating sewage(Haandel van and Lettinga,1994)and0.76 for a HRT of24h in sucrose treated in a UASB reactor was reported by Chang and Lin(2004).At a1:10dilution,a VSS/TSS ratio of1.1 (Fig.3b)and1.45–1.5(Fig.5b)gave maximum biohydrogen yield for R1and R2,respectively.At very low VSS/TSS ratios,the hydro-gen yield decreased due to high sludge productivity which affected the fermentation process.A low VSS/TSS ratio indicates the organic fraction degradation.VFA/alkalinity ratios of0.01for R2and of0.03 for R1in1:10diluted press mud(Figs.3and5b)provided for max-imum hydrogen yields.The concentration of VFA in the feed and effluent showed a considerable increase with increasing organic loading rates(Figs.3and5c).4.ConclusionsDigestion of press mud and sewage at a1:10dilution and at a 30h HRT resulted in the production of approximately2.75L H2/kg press mud.As press mud is of no use other than as soil fertilizer,it could be fully exploited to produce hydrogen.From4.2million tons of press mud available annually in India,it is estimated that 11.55million m3hydrogen could be produced.Only limited acid/ base additions were necessary to maintain a pH of5–6,resulting in cost savings.ReferencesAPHA,1995.Standard Methods for the Examination of Water and Wastewater.American Public Health Association,New York,USA.Castello,E.,Garcı´a y Santos,C.,Iglesias,T.,Paolino,G.,Wenzel,J.,Borzacconi,L., Etchebehere,C.,2009.Feasibility of biohydrogen production from cheese whey using a UASB reactor:links between microbial community and reactor performance.Int.J.Hydrogen Energy34,5674–5682.Chang,F.Y.,Lin,Chiu-Yue,2004.Biohydrogen production using an upflow anaerobic sludge blanket reactor.Int.J.Hydrogen Energy29,33–39.Das, D.,Veziroglu,T.N.,2001.Hydrogen production by biological processes:a survey of literature.Int.J.Hydrogen Energy26,13–28.Fascetti,E.,Todini,O.,1995.Rhodobacter sphaeroides RV cultivation and hydrogen production in a one-and two-stage chemostat.Appl.Micobiol.Biotechnol.44, 300–305.G´omez,X.,Mor´an,A.,Cuetos,M.J.,S´anchez,M.E.,2006.The production of hydrogen by dark fermentation of municipal solid wastes and slaughterhouse waste:a two-phase process.J.Power Sources157(2),727–732.Georgia,A.,Gavala,Hariklia N.,Skiadas,Ioannis V.,Angelopoulos,K.,Lyberatos, Gerasimos,2008.Biofuels generation from sweet sorghum:fermentative hydrogen production and anaerobic digestion of the remaining biomass.Bioresour.Technol.99,110–119.Haandel van,A.C.,Lettinga,G.,1994.Anaerobic Sewage Treatment.Wiley,Inc., London.Han,S.K.,Shin,H.S.,2004.Biohydrogen production by anaerobic fermentation of food waste.Int.J.Hydrogen Energy34,5674–5682.Hawkes,F.R.,Forseya,Helen,Premiera,Giuliano C.,Dinsdalea,Richard M.,Hawkesa, Dennis L.,Guwya,Alan J.,Maddya,Jon,Cherrymana,Samantha,Shineb,James, Autyc,David,2008.Fermentative production of hydrogen from a wheatflour industry co-product.Bioresour.Technol.99,5020–5029.Kim,S.H.,Han,Sun-Kee,Shin,Hang-Sik,2004.Feasibility of biohydrogen production by anaerobic co-digestion of food waste and sewage sludge.Int.J.Hydrogen Energy29,1607–1616.Mohanakrishna,G.,Kannaiah Goud,R.,Venkata Mohan,S.,Sarma,P.N.,2010.Enhancing biohydrogen production through sewage supplementation of composite vegetable based market waste.Int.J.Hydrogen Energy35,533–541. Nicolau,J.M.,Dinsdale,Richard,Guwy,Alan,2008.Hydrogen production from sewage sludge using mixed microflora inoculum:effect of pH and enzymatic pretreatment.Bioresour.Technol.99,6325–6331.Partha,N.,Sivasubramanium,V.,2006.Recovery of chemicals from press mud-A sugar industry waste.Indian Chem.Eng.Sect.A48(3),160–163.Ren,N.Q.,Li,Jianzheng,Li,Baikun,Wang,Yong,Liu,Shirui,2006.Biohydrogen production from molasses by anaerobic fermentation with a pilot-scale bioreactor system.Int.J.Hydrogen Energy31(15),2147–2157.Ren,N.Q.,Wang, B.Z.,Ma, F.,1995.Hydrogen bio-production of carbohydrate fermentation by anaerobic activated sludge process.Proc.Water Environ.Fed.Annu.Conf.Exposure68,145–153.Saravanane,R.,Radjaram,B.,1998.Integrated biomethanation system for waste management of sugar industry.J.Inst.Public Health Eng.(1),22–29. Tsygankov,N.A.,Hirata,Y.,Miyake,M.,Asada,Y.,Miyake,J.,1994.Photobioreactor with photosynthetic bacteria immobilized on porous glass for hydrogen photoproduction.J.Ferment.Bioeng.77(5),575–578.Yang,P.,Zhang,R.,Mcgarvey,J.A.,Benemann,J.,2007.Biohydrogen production from cheese processing wastewater by anaerobic fermentation using mixed microbial communities.Int.J.Hydrogen Energy32,4761–4771.Yu,H.,Zhu,Zhenhu,Hu,Wenrong,Zhang,Haisheng,2002.Hydrogen production from rice winery wastewater in an upflow anaerobic reactor by using mixed anaerobic cultures.Int.J.Hydrogen Energy27,1359–1365.2780 B.Radjaram,R.Saravanane/Bioresource Technology102(2011)2773–2780。