机加工检验表格
机械零件质量检验报告表模板

机械零件质量检验报告表模板【中英文实用版】英文文档内容:Mechanical Part Quality Inspection Report TemplateIntroduction:This report template is designed to provide a comprehensive overview of the quality inspection process for mechanical parts.It includes essential details such as the part number, inspection date, and inspector"s name.The template also lists the specific criteria and standards that the parts are evaluated against, including dimensional accuracy, material specifications, and surface finish.sections:1.Part Identification:- Part Number: [Insert Part Number]- Description: [Insert Part Description]- Manufacturer: [Insert Manufacturer Name]- Lot/Serial Number: [Insert Lot/Serial Number]2.Inspection Date:- [Insert Inspection Date]3.Inspector"s Name:- [Insert Inspector"s Name]4.Inspection Criteria:- Dimensional Accuracy: [Insert applicable standards and tolerances]- Material Specifications: [Insert applicable material standards and requirements]- Surface Finish: [Insert applicable surface finish standards and requirements]- Other: [Insert any other relevant inspection criteria]5.Inspection Results:- [Insert detailed description of inspection results, including any deviations from the specified criteria]6.Conclusion:- [Insert conclusion statement regarding the overall quality of the parts]- [Insert any necessary recommendations or corrective actions]7.Signatures:- [Insert Inspector"s Signature]- [Insert Supervisor"s Signature]- [Insert Date]ote: This template can be customized to meet specific company or project requirements.中文文档内容:机械零件质量检验报告模板引言:本报告模板旨在提供关于机械零件质量检验过程的全面概述。
镗床加工现场安全检查表

2、无单独接地保护的电动机,底面不允许涂油漆,不允许加绝缘垫,以保证电机与床身之间导电的连续性。
3、保护接地连接可靠,并有明显标志。
4、操纵按钮、指示盘、仪表等应齐全、完好、灵敏可靠,标识清晰。
3
联锁
装置
1、主轴和径向刀架送刀快速移动时,工作台不能回转运动。
2、工作台横、纵向进刀电路不能同时接通。主轴箱工作进刀与工作台纵向进倒的电路不能同时接通。
3、变换转速或变换进刀量时,在操纵手柄定位之前,主电机不能接通。
4、进刀与快速移动电气线不能同时接通。
4
限制
装置
1、镗床必须有主轴箱、主轴和上、下滑座的限位装置。
镗床加工现场安全检查表
序
号
检查
项目
检查内容提示
检查情况
记录
1
控制
机构
1、主轴制动系统必须灵敏可靠,当变速手柄处于停止位置时,揿下“停止”按钮应能迅速刹住主轴转动。
2、平旋盘径向进给时,主轴应退到最后,禁止径向刀架超出极限。不用径向刀架时,必须将离合器脱开。
2
工作台
工作台上下滑座作纵向、横向移动时,必须将夹紧装置的手柄放松。机床启动前,应将工作台不进给的部分锁紧。
机加工制程检验记录表
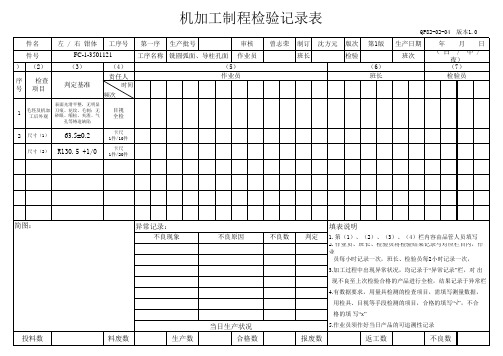
件名
左 / 右 钳体 工序号 第一序 生产批号
审核
(1 件号 ) (2)
序 检查 号 项目
FC-1-3501121
工序名称 铣圆弧面、导柱孔面 作业员
(3) 判定基准
(4) 责任人
时间
(5) 作业员
频次
表面光滑平整,无明显
1
毛坯及机加 刀痕、花纹、毛刺;无 工后外观 砂眼、缩松、夹渣、气
生产数
不良原因
当日生产状况 合格数
不良数
判定
填表说明
1.第(1)、(2)、(3)、(4)栏内容由品管人员填写 2.作业员、班长、检验员将检验结果记录与对应栏目内,作 业
员每小时记录一次,班长、检验员每2小时记录一次,
3.加工过程中出现异常状况,均记录于“异常记录”栏,对 出
现不良至上次检验合格的产品进行全检,结果记录于异常栏
孔等铸造缺陷
目视 全检
2 尺寸(1) 63.5±0.2 尺寸(2) R130.5 +1/0
卡尺 1件/10件
卡尺 1件/20件
曾志荣 制长
QP82-02-04 版本1.0
生产日期 班次
年月日 (白 / 中/
夜) (7)
检验员
简图: 投料数
异常记录: 不良现象
料废数
4.有数据要求,用量具检测的检查项目,需填写测量数据, 用检具、目视等手段检测的项目,合格的填写“√”,不合 格的填 写“х”
5.作业员须作好当日产品的可追溯性记录
报废数
返工数
不良数
机加工记录表格

各部门:2005年12月21~22日,安排公司质量管理体系内审,请各部门及早做好安排。
本次内审是我公司迎接外审前的一次符合性审核,各部门要充分重视。
编制:批准:日期:
检查表
XB-C-53
受审核部门:审核员:审核日期:
条款
审核内容
现场审核记录
编制:批准人:日期:第页共页
不符合项报告
序号:XB-C-54
序号
文件名称
编号
实施日期
修订状态
备注
受控文件清单
序号:XB-C-01
序号
文件名称
编号
实施日期
修订状态
备注
质量记录清单
XB-C-06
序号
记录编号
记录名称
管理部门
保存期限
(电话)
物
资
类
别
营业资格
生
产
许
可
证
行
业
监
查
结
果
产品质量情况
人
员
责
素
市
场
信
誉
生
产
能
力
价
格
是
否
合
理
以
往
供
货
服
务
调查人
日期
主管领导评价结果
签字
日期
注:供方需提供资质证明复印件,主管领导评价结果为“优”和“良”的供方,可进入《合格供方名单》
合格供方名录
序号:XB-C-24
序号
供方名称
产品名称(型号)
物资类别
合同更改内容:
合同更改需通知部门人:
填写人
批准
日期
机加工审核检查表

21 管理层
与最高管理层交流,了解组织对内外环境的分析,相关方对企业的期望或 要求,为完成质量环境安全方针、目标采取的措施,以及在持续改进方面 所做的工作,管理评审
GB/T19001-2016 5.2.2,7.3 7.4 5.3 7.2,7.1.2
7.1.3 7.1.4
对应条款 GB/T24001-2016
11
现场观察操作人员是否按规定进行首检、互检与专检,并做好检验记录 (记住本批产品及原材料)
12
现场观察操作人员是否按规定做好产品的防护、以及合格品、不合格品、 废的消防器材是否按期进行检查,讯问操作人员如何使用消防器 材?是否进行培训,并根据需要查询记录
根据操作人员使用的原材料,到仓库检查此原材料是否贯彻了先入先出的 14 原则?并同时现场观察物料的管理水平,如帐卡物是否一致?物料标示、
18 根据销售合同,查研发设计部的研发设计条款及设计变更,并查看是否考 研发部 虑了从生命周期的不同阶段考虑了环境、安全因素
19 质量部
根据操作者及使用的测量工具,到质量部查工具台帐及检测报告及周期内 的质量绩效情况(是否有改进),产品放行情况,让步接受情况(降 低),并同时检查环境、安全因素,内部质量审核
7.2,8.1,8.2 6.1,8.5.2,8.5.3,8.5.4
8.4,9.1.3
8.1
8.2,8.3,8.5.4,8.5.5 9.1.2,9.1.3
8.1
8.3,8.5.6
8.1
7.1.5,8.6,8.7 9.1.1,9.1.3,9.2,10.2,10.3
8.1
4.4.2,4.4.6,4.4.7 4.4.6 4.4.6 4.4.6 4.4.6
20 到操作工为例,人事部门查岗位职责、年度培训的编制情况,人员能力的 人事部 确认情况,培训效果的验证情况,关键岗位人员的流失情况
机加工自检记录单
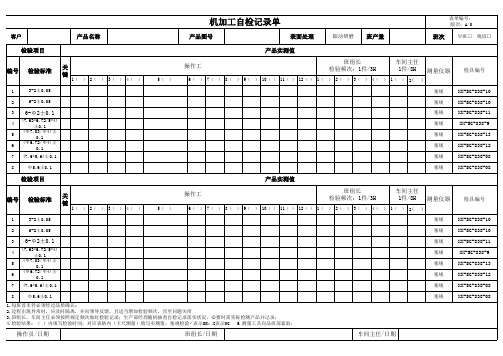
塞规
检具编号 XX-SG-838-10
2
6-2±0.05
塞规
XX-SG-838-10
3 6-Φ2±0.1
4
(7.63*6.72/5*4) ±0.1
5
(Φ7.03/Φ4)± 0.1
6
(Φ6.72/Φ4)± 0.1
7 (7.6*5.6)±0.1
塞规
XX-SG-838-11
塞规
XX-SG-838-9
塞规
XX-SG-838-13
客户
产品名称Biblioteka 机加工自检记录单产品图号
表面处理
振动研磨 班产量
表单编号: 版次:A/0
班次
早班□ 晚班□
检验项目
产品实测值
编号 检验标准
1
3-2±0.05
关
键
1( ) 2( ) 3( ) 4( )
5( )
操作工
班组长 检验频次:1件/3H
车间主任 1件/8H 测量仪器
6( ) 7( ) 8( ) 9( ) 10( ) 11( ) 12( ) 1( ) 2( ) 3( ) 4( ) 1( ) 2( )
塞规
检具编号 XX-SG-838-10
2
6-2±0.05
塞规
XX-SG-838-10
3 6-Φ2±0.1
4
(7.63*6.72/5*4) ±0.1
5
(Φ7.03/Φ4)± 0.1
6
(Φ6.72/Φ4)± 0.1
7 (7.6*5.6)±0.1
塞规
XX-SG-838-11
塞规
XX-SG-838-9
塞规
XX-SG-838-13
塞规
XX-SG-838-12
车削加工安全检查表

车削加工安全检查表1. 工作环境安全:- 确保车削加工区域干燥通风;- 清理工作区域,确保没有杂物、碎屑等;- 确保工作区域有足够的照明设备;- 周围没有易燃物品和爆炸品;- 避免使用明火等危险物品。
2. 机床安全:- 确保机床、刀具和夹具的安装牢固;- 定期检查和维护机床,确保机床的正常运行;- 检查和维护液压和气动系统,确保其正常工作;- 确保机床的保护罩和安全装置完好,防止操作人员意外伤害。
3. 个人防护:- 操作人员应佩戴符合标准的安全帽、护目镜、耳塞或耳罩以及防护手套;- 确保操作人员穿着合适的工作服,避免裤脚过长、袖口过宽等;- 穿戴合适的防滑鞋,以避免滑倒造成意外伤害;- 长发应绑起或戴上帽子,避免被转动的刀具缠绕。
4. 刀具安全:- 使用合适的刀具和夹具,确保其质量和正常使用;- 确保刀具刃口尖锐,避免使用钝刀;- 更换磨损和损坏的刀具;- 使用刀具时,不要过度切削,以免刀具断裂或产生过分的振动。
5. 加工件固定:- 确保加工件固定牢固,避免在加工过程中发生移位或跳动;- 使用合适的夹具和工装以固定加工件;- 避免长而窄的加工件,以减少振动和走刃。
6. 操作规范:- 操作人员应经过专业培训,掌握正确的操作技巧;- 操作人员应仔细阅读机床的使用说明书,并按照正确的程序操作;- 在操作之前,确保机床和工件处于停止状态;- 在开始加工之前,检查和调整机床的各项参数,确保其正常运行;- 加工过程中,操作人员应注意观察机床和加工件的运行情况,及时调整和处理异常情况;- 加工完成后,关闭机床和相应的系统。
7. 紧急情况处理:- 预先了解和掌握机床的紧急停车和急停装置的使用方法;- 预先了解和掌握相关紧急救援措施,如灭火器的使用方法、急救知识等;- 发生紧急情况时,及时采取相应的紧急处置措施,并及时报告相关人员。
以上是车削加工安全检查表的内容,希望能够对您的工作提供一定的参考和帮助。
金属切削机床铣削加工安全检查表范本(2篇)
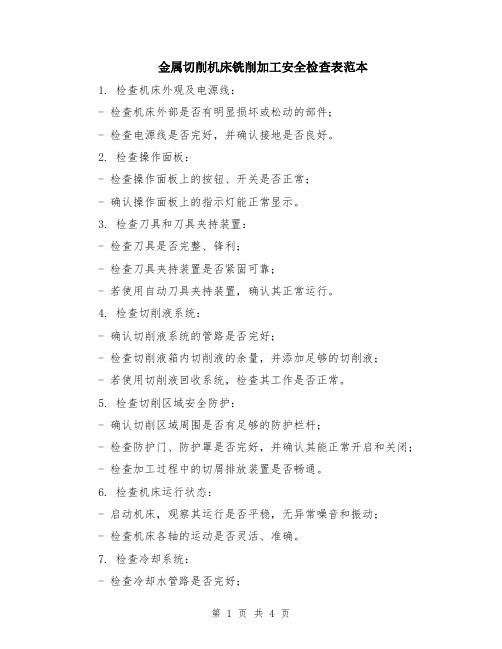
金属切削机床铣削加工安全检查表范本1. 检查机床外观及电源线:- 检查机床外部是否有明显损坏或松动的部件;- 检查电源线是否完好,并确认接地是否良好。
2. 检查操作面板:- 检查操作面板上的按钮、开关是否正常;- 确认操作面板上的指示灯能正常显示。
3. 检查刀具和刀具夹持装置:- 检查刀具是否完整、锋利;- 检查刀具夹持装置是否紧固可靠;- 若使用自动刀具夹持装置,确认其正常运行。
4. 检查切削液系统:- 确认切削液系统的管路是否完好;- 检查切削液箱内切削液的余量,并添加足够的切削液;- 若使用切削液回收系统,检查其工作是否正常。
5. 检查切削区域安全防护:- 确认切削区域周围是否有足够的防护栏杆;- 检查防护门、防护罩是否完好,并确认其能正常开启和关闭;- 检查加工过程中的切屑排放装置是否畅通。
6. 检查机床运行状态:- 启动机床,观察其运行是否平稳,无异常噪音和振动;- 检查机床各轴的运动是否灵活、准确。
7. 检查冷却系统:- 检查冷却水管路是否完好;- 检查冷却液箱内冷却液的余量,并添加足够的冷却液;- 检查冷却系统的温度和压力是否在正常范围内。
8. 检查机床润滑系统:- 确认润滑油箱内润滑油的余量,并添加足够的润滑油;- 检查润滑系统管路是否完好;- 检查润滑系统的工作是否正常,无异常的润滑点。
9. 检查电气系统:- 检查电气线路是否完好,无短路或接触不良;- 检查电气设备的接地是否良好;- 若使用变频器进行控制,检查其工作是否正常。
10. 检查运输锁定装置:- 检查运输锁定装置是否已全部解除。
11. 检查紧固件:- 检查机床上的紧固件是否全部紧固可靠。
12. 检查安全标识:- 检查机床上的安全标识是否清晰可见;- 确认操作人员是否了解并遵守相应的安全规范。
以上为金属切削机床铣削加工安全检查表范本,详细检查内容,请根据具体机床的型号和使用情况进行相应的调整和补充。
请在使用任何机床之前,先进行安全检查,确保操作人员的安全。
机加工首件检验记录表

总结
最终判定结果
□合格 □不合格
是否同意量产: □是 □否
检验员签名:
注意事 1、所有项目均需连续检查最少2件。 项 2、根据质量统计的不良项目进行持续跟进。
1、产品新开机生产时,由最终工序准备好2个样件置于待检区,并通知检验员,检查判定合格后生产。
填写 2、检验员判定合格后从样品中随机挑选1个样件,进行首件标识。并连同巡检记录表一起置于产线最终检查工位。 说明 3、适用范围:产品新开机、变更工艺/参数、变更材料等均需要进行首件检查。
4、检查结果:合格项目打“√”,不合格项目打“×”,无此检查项目打“0”;本表单保留一年。
机加工首件检验记录表
编号: 版本:A/0
零件号
首件 信息 □开机首检
□其他:
产品名称 □生产参数变更 □材料变更
项目
检验标准
12原料来自机台编号生产日期检验依据
□工程图纸 □标准样件 □产品标准 □其它
实测值
3
4
5
判定
检验时间
时 分
备注
检查 尺寸 记录
外观
□变形 □孔毛刺 □飞边毛刺 □划伤 □疤瘤 □烧穿 □未焊透
金属切削机床安全检查表

金属切削机床安全检查表金属切削机床是一种常用的机械设备,用于加工金属材料,具有高效、精确的加工能力。
然而,由于其复杂的结构和高速旋转的刀具,金属切削机床存在一定的安全隐患。
为了确保操作者的安全和机械设备的正常运行,需要定期进行安全检查。
下面是金属切削机床的安全检查表,包括机器外观、电气系统、传动系统、润滑系统和使用环境等方面的内容。
一、机器外观检查1. 检查机器外观是否完好无损,有无明显变形、破损等情况。
2. 检查机器底座是否平稳,有无松动或虚动现象。
3. 检查机器上的警示标识是否齐全清晰,有无脱落或模糊不清。
二、电气系统检查1. 检查电源插头和插座是否良好接触,有无松动或破损。
2. 检查电线是否完好无损,有无破损、断裂或长时间使用导致老化的情况。
3. 检查电气设备的开关、按钮和指示灯是否正常工作,有无故障或卡住现象。
4. 检查电气设备的保护装置是否正常运行,如短路保护、漏电保护等。
三、传动系统检查1. 检查刀具传动系统的皮带、链条、齿轮等传动部件是否完好无损,有无磨损、断裂或松动的情况。
2. 检查传动系统的轴承是否润滑良好,有无异常噪音或高温现象。
3. 检查传动系统的轴承是否存在松动或偏移现象,有无需要调整或更换的情况。
4. 检查传动系统的传动比是否正常,有无异常或异音。
四、润滑系统检查1. 检查润滑油的液位是否正常,有无过高或过低的情况。
2. 检查润滑油的质量是否良好,有无混杂杂质或变质情况。
3. 检查润滑系统的管道和阀门是否正常,有无老化、渗漏或堵塞的情况。
4. 检查润滑系统的润滑点是否润滑良好,有无异常磨损或缺少润滑的情况。
五、使用环境检查1. 检查机器周围的工作环境是否整洁无杂物,有无积尘或堆积物的情况。
2. 检查机器的通风系统是否畅通良好,有无堵塞或异常噪音的情况。
3. 检查机器周围是否有明火、易燃物品或其他危险物品,有无可能引发火灾或爆炸的情况。
4. 检查机器的使用区域是否明确标识,有无规范的作业区域和安全通道。
机械加工检验标准

Test
耐温差试验
以温度循环机:60℃至-5℃间以30分钟为cycle,共计10cycle,再做方格硬度冲击试验,不得有破裂或脱落现象;
ˇ
Testing
耐盐雾试验
5%NaCI于盐水喷雾状试验机试验72hrs后进行方格硬度冲击试验,不得有破裂或脱落现象;
ˇ
Test
耐照射试验
15w,140v紫外灯距离30cm照射4hrs,色泽不得有差异及物性降低现象;
ˇ
Testing
硬度试验
以三菱F-H铅笔笔尖磨平,以45;斜角1kg,荷重于试验面反向推书测验以橡皮去除面笔迹后,检视表面,不得任何刮伤;
ˇ
Testing
冲击试验
以冲击试验机,球径",荷重500g自由落下,高度350mm,直接冲击喷涂表面,涂料不得有破裂或脱落现象;
ˇ
Test
耐溶剂试验
95%浓度之药用酒精,加压于棉布或纱布上,行程50mm来回50次,涂膜不得见底或漆附着于棉布;
C面:长度≦8mm容许2点宽度≦0.4mm
ˇ
检验区域:检查表面依零件组装后之位置可分为三面
A面:产品于使用者正面可见部分如面板上盖
B面:产品于使用者正面不可见部分如左右侧面
C面:产品底面及背面
品名:Paint涂装&涂料
Inspection Item
检验项目
Quality Standard
品质需求
Defect Class
ˇ
品名:Foundry压铸类
Inspection Item
检验项目
Quality
品质需求
Defect Class
缺点等级
MA
MI
外观检验
内审检查表(机加工车间)

有无搬运过程中防泄漏的规定?
废弃物污染源及废弃物种类有哪些?如何控制?
符合√
请说明哪些产品和状态需要标识
现场观察原料领用、半成品、待检品、不合格品状态标Байду номын сангаас是否适宜、完好、清晰。
说明产品追溯方式,追溯一个不合格品的供方和发货人员。
◆
1、查是否按要求进行了相应的区域标识,检验状态标识、产品类别标识 2、根据这些标识是否能有效追溯?是否为唯一性标识?
Q 9.1.3分析和评价 提供数据分析结果得到利用的证据。抽样应关注:不同类别的数据、不同时期数据以及
E/
落实效果的证据。
◆1、是否以周报/月报对来料、制程、出货、客诉等相关数据进行统计和分析?
●查见《机加工车间生产计划》、 《生产任务单》。车间主管每阶段 定时向生管部反馈完成情况。 ●车间每月统计的相关的质量、环 境考核目标为: 冲压件合格率、废品率
现场审核情况记录
结果判定
QE 7.1资源 Q 7.1.3基础设施
请说明车间管控的设备设施有哪些? 出示设备台帐和基础资料。 出示设备安全操作规程。 出示设备保养和维护的计划及记录,抽样(关注对产品质量和人员安全影响大的设备的 有效管控)。 请说明出现设备异常(含影响交期和存在重大安全隐患)情况如何处置。 现场观察在用设备的完好情况。 现场观察设备是否处于安全状态(查找设备方面的安全隐患,结合辨识的危险源和操作 规程)。
提供的控制
1、查生产现场是否有对应产品的工艺要求,产品检验标准、首件等?
查看2-3运行记录表
Q 8.5.6变更控制 2、现场使用的SOP参数是否与实际作业相符合?
均有按要求填写。
E/
3、检测产品使用的设备是否与SOP或SIP要求一致,此检测设备的检测范围是否能满足 ●
缺陷对照表 机加工检验用

缺陷查阅表
SG-02-2010 A/QX02
铸件缺陷分类
分为:多肉类,孔洞类,裂纹、冷隔类,表面缺陷,残缺类, 形状及重量差错类,夹杂类,性能/成分/组织不合格等八类缺陷
1 多肉类 2 孔洞类 3 裂纹、冷隔类 4 表面缺陷类 5 残缺类缺陷分类查阅表:1.1 飞边 1.2 毛刺
7 夹杂类 8 性能/成分/组织类
7.1 夹砂
(砂眼) 7.2 硬点
8.1 物理性能、力学性能和化学成分不合格 8.2
组织异常
废件原因
附 加
1.3
铸瘤
2.1 气孔 2.2 砂眼 2.3 针孔 2.4 疏松
3.1 裂纹 3.2 冷隔
4.1
表面粗糙
4.2
凊砂不干 净
4.3
沟槽
4.4
皱皮
4.5
5.1 损伤 (5.11磕碰)(5.12缺角) 5.2 无余量
焊补
6 形状及重量差错类
6.1 错箱 6.2 偏芯 6.3 变形 6.4 尺寸差错 6.5 重量差错