试样制备(工艺规程)
金相检验操作规程

金相检验操作规程1.试样金相试样面积小于400mm2,厚(高)度15-20mm为宜。
若试样面积过小,应经镶嵌后再进行磨制。
低倍组织酸侵试样厚度(高)度为20mm左右,酸侵低倍试样检测面应经过车加工或磨加工,表面粗糙度应不大于1.6μm。
试样检测面不得由油污及加工伤痕,必要时应预先清除。
试样的标识应清晰。
2.高倍检验操作规程2.1金相试样制备操作规程2.1.1金相试样的切取试样切取的方向、部位和数量,应根据有关技术条件的规定。
试样可用手锯、锯床或切割机等切取,必要时也可用气割法切取,但烧割边缘必须与正式试样保持相当距离,以去除热影响区。
取好的试样先在平面磨床或砂轮机上把检测面磨平,磨面上的磨痕应均匀一致。
磨样时应对试样进行冷却,以免金属组织受热发生变化。
2.1.2金相试样的磨制试样需经粗磨和细磨,粗磨用水磨砂纸,细磨用金相砂纸,应根据需要选择合适的砂纸及磨制道次。
磨样时须把前一道的磨痕磨去,方向与前一道的工序相垂直。
磨样时要防止试样磨面温度过高而使组织发生变化。
2.1.3金相试样的抛光常用的时机械抛光的方法,即把经过细磨的试样在抛光机上进行抛光。
抛光织物采取丝绒或绸布,抛光粉采用金刚砂。
抛光面光洁度要达到镜面,不允许有夹杂物拖尾、麻点、过热等现象,抛光后将试样清洗干净。
2.1.4金相试样化学侵蚀操作规程试样侵蚀前抛光面应保持干净,不得有油污或指痕,以免影响所显示组织的清晰度。
试样在盛有侵蚀剂的器皿中侵蚀,侵蚀时试样应轻微摆动,但不可擦伤抛光面。
应根据不同的需要选择侵蚀剂,并注意侵蚀适度。
侵蚀后试样应保持干燥(在酒精中浸泡、用电吹风吹干),以待观察。
配置侵蚀剂时遵照先加酒精或水、后加酸液的顺序。
侵蚀操作时要注意安全,防止酸液或酸雾对人体造成伤害。
2.2金相显微镜操作规程操作者在使用显微镜前,应仔细阅读显微镜的使用说明书,了解显微镜的功能及使用方法。
初学者操作显微镜应在专人指导下进行。
测试前应保持操作者的手及试样清洁干燥。
原材料复验试样制备通用工艺规程

原材料复验试样制备通用工艺规程编制审核批准XX公司发布原材料复验试样取样通用工艺规程1 主题内容与适应范围1.1 本规程规定了压力容器用钢板、钢带、钢管、圆钢、锻件及其它型钢等原材料复验时试样取样与加工的方法和要求。
1.2 本规程适用于本公司制造的钢制压力容器产品用材料的复验。
其它材料的复验亦可参照执行。
2 总则材料复验试样的制备除符合本规程的规定外,还应遵守国家颁布的有关法令、法规、标准、本公司其它相应规程和图样及专用工艺文件的要求。
3 取样3.1 试样应在外观及尺寸合格的钢材上切取。
切取试样样坯时,应防止因受热、加工硬化及变形而影响其力学性能及工艺性能。
用火焰切割法切取样坯时,从样坯切割线至试样边缘必须留有足够的加工余量,一般不小于钢材的厚度或直径,但最小不得小于20mm。
对厚度或直径大于60mm的钢材,其加工余量可适当减小。
3.2 试样样坯切取位置及方向3.2.1 钢板应在钢板端部垂直于扎制方向切取拉伸、弯曲、冲击试样样坯。
对纵扎钢板,应在距边缘为板宽1/4图3-1 钢板切取样坯的示意图3.2.2 扁钢应从扁钢端部沿扎制方向距边缘为1/3处切取拉伸、弯曲和冲击样坯。
如图3-2所示。
应接近钢管内壁,样坯部位如图3-4所示。
3.2.4.3 钢管的冲击试样样坯应靠近内壁切取,试样缺口应垂直内壁,取样方向符合有关产品或标准的规定。
3.2.4.4 钢管的弯曲、扩口、缩口、压扁和卷边可以在任意部位切取样坯。
3.2.5.1 取样数量热处理单件重量小于或等于3500kg的锻件取一组试样(1个拉伸、3个冲击),热处理单件重量大于3500kg的锻件取两组试样(每组1个拉伸、3个冲击),两组试样位置间隔180°,如锻件长度大于直径的1.5倍时,则应在锻件两端各取一组试样。
3.2.5.2 取样方向锻件(不含条形)宜取切向试样,当不能制取切试样时,则取纵向或径向试样。
条形锻件宜取纵向试样。
3.2.5.3 取样部位筒形锻件和环形锻件的试样应取自锻件的端部,从壁厚的1/2处取样,见图3-5a)和图3-5b)。
实验金相试样的制备

实验金相试样的制备一、实验目的1.熟悉金相显微试样的制备过程2.了解掌握金相显微试样的制备方法二、概述在利用金相显微镜作金相显微分析时,必须首先制备金相试样,我们在显微镜中所观察到的显微组织,是靠光线从试样观察面上的反射来实现的。
若试样观察面上的反射光能进入物镜。
我们就可以从目镜中观察到反射的象,否则就观察不到。
图2-1 光线在不同表面上的反射情况由图2-1所示可见,未经制备的试样的表面相当于无数多个与镜筒不垂直的平滑表面,这是不能成象的。
因此,我们要先把试样观察面制备成光滑平面。
但是光滑平面在显微镜下只看到光亮一片,而不能看到显微组织结构特征,故还须用一定的浸蚀剂浸蚀试样观察面,使某些耐浸蚀弱的区域不同程度地受到浸蚀而呈现微观察的凸凹不平。
这些区域的反射光线被散射而呈暗色。
由于明暗相衬,在显微观察中就能表示试试样磨面组织结构的特征了。
金相试样的制备包括试样的切取、镶嵌、磨制抛光、锓蚀等五个步骤。
1. 取样试样应根据分析目的和要求在有代表的位置上截取。
一般地说,取横截面主要观察:1、试样边缘到中心部位显微组织的变化。
2、表层缺陷的检验、氧化、过滤、折叠等。
3、表面处理结果的研究,如表面淬火、硬化层、化学热处理层、镀层等。
4、晶粒度测定等。
通过纵截面可观察:1、非金属夹杂;2、测定晶粒变形程度;3、鉴定带状组织及通过热处理消除带状组织的效果等。
试样一般可用手工切割、机床切割、切片机切割等方法截取(试样大小为φ12×12mm圆柱体或12×12×12mm的立方体)。
不论采用哪种方法,在切取过程中均不宜使试样的温度过高,以免引起金属组织的变化,影响分析结果。
2. 镶嵌当试样的尺寸太小(如金属丝、薄片等)时,直接用手来磨制很困难,需要使用试样夹或利用样品镶嵌机,把试样镶嵌在低熔点合金或塑料(如胶木粉、聚乙烯及聚合树脂等)中,如图2-2所示。
图2-2 试样的镶嵌(见实验室挂图)3. 磨制试样的磨制一般分粗磨和细磨两道工序。
金相试样的制备

腐蚀边抛光可提高抛光效能。
3、电解抛光
电解抛光是在一定的电解液中进行的,最简单 的电解抛光装置如图所示。
试样作阳极,选用耐蚀金属材料为阴极(如不 锈钢、铂、铅等)。在接通直流电源后,阳极表面 产生选择性溶解,逐渐使阳极表面的磨痕消去。通 常认为,电解抛光时在阳极表面与电解液之间将形 成一层具有较大电阻率的薄膜层。样品的表面高低 不平,致使这层薄膜的厚度不均匀。表面凸出部分 的薄膜厚度比凹下去的部分要薄些,因此凸出部分 的电流密度大,此处阳极溶解快,凸出部位渐趋平 坦。
金相显微试样的制备
➢ 实验目的
1)了解金相显微试样制备原理,熟悉金相显微试样的制备过 程。
2)初步掌握金相显微试样的制备方法。
➢ 实验设备及材料
1)金相显微镜、砂轮机、镶嵌机、预磨机、抛光机、吹风 机。 2)待制备的金相试样。 3)不同粗细的金相砂纸一套、抛光剂、浸蚀剂、无水酒 精、玻璃板、脱脂棉,竹夹子等。
检测脱碳层、化学热处理的渗层、淬火层、晶粒度等,应取横向截面。
夹在具接应 通选直择流与电试源在样后化硬,度阳学、极化表抛学面光性产能生时近选似择,的性影材溶料解响。,逐抛渐使光阳质极表量面的的磨可痕消控去。参数有:抛光液的组分、浓度、 试常样用作 的阳砂温极纸,号度选数,用有耐2以0蚀0、金及4属00抛材、料6光0为0阴、时极80间(0号如等几不种锈,,钢号需、小铂根者、磨铅据粒等较)具粗。,体号情大者况较细制。定合适的工艺规程。
化学抛光蒸一般馏总水不太的理想化,学若和抛机械光抛剂光结,合,对利碳用化钢学抛、光剂一边般腐蚀低边抛合光金可提钢高抛的光退效能火。 、淬火组织进行化
焊接工艺评定试验试样取样工艺规程

焊接工艺评定试验试样取样工艺规程Company number:【0089WT-8898YT-W8CCB-BUUT-202108】焊接工艺评定试验试样取样通用工艺规程1主题内容与适应范围本规程规定了钢制焊接压力容器焊接工艺评定试验试样加工方法和要求。
本规程适用于本公司钢制压力容器焊接工艺评定。
2总则焊接责任工程师应根据公司需要确定焊接工艺评定项目。
焊接工艺评定所用设备、仪表应处于正常工作状态,钢材、焊接材料必须符合相应标准,并由本公司技能熟练的焊工使用本公司焊接设备焊接试板。
3试样制备试样取样及尺寸、要求3.1.1焊接工艺评定的小铁研抗裂试样应符合图3-1规定图3-13.1.2取样要求a) 所有切口不得用剪板机剪切b) 所有棱角都应倒成R2圆角(除焊缝外);c) 在所有试样端头打上钢印;d) 所有试样表面不得有碰伤;e) 试样数量:5件。
试样取样位置3.2.1板材取样3.2.1.1板材对接焊缝工艺评定试样的类别和数量见表3-1,试样取样位置见图3-2。
(a)不取侧弯试样时(b)取侧弯试样时图3-2 板材取样位置图(未完)(c)取纵向弯曲试样时图3-2 板材取样位置图(续完)3.2.1.2 试样要求a) 试件角变形超过3°时,应在无损检测前进行冷校平。
b) 试件经外观检查和无损检测合格后,允许避开缺陷取样。
c) 力学性能试样应以机械法去除焊缝余高,使之与母材平齐。
d) 应在试样端头和剩余试件的先焊面打上钢印标记。
3.2.2 管材取样3.2.2.1 管材对接焊缝试件取样位置见图3-3。
3.2.2.2 试样要求管材对接焊缝的试样要求按本规程的3.2.1.2条之规定进行。
表3-1(a) 拉力试样为整管时弯曲试样位置图3-3 管材取样位置图(未完)(b)不要求冲击试验时(c) 要求冲击试验时1—拉力试样; 2—面弯试样; 3—背弯试样; 4—侧弯试样;5—冲击试样;③⑥⑨12—钟点记号,为水平固定位置焊接时的定位标记。
焊接工艺设计评定试验试样取样工艺设计规程完整

焊接工艺评定试验试样取样通用工艺规程1主题内容与适应范围1.1本规程规定了钢制焊接压力容器焊接工艺评定试验试样加工方法和要求。
1.2本规程适用于本公司钢制压力容器焊接工艺评定。
2 总则2.1焊接责任工程师应根据公司需要确定焊接工艺评定项目。
2.2焊接工艺评定所用设备、仪表应处于正常工作状态,钢材、焊接材料必须符合相应 标准,并由本公司技能熟练的焊工使用本公司焊接设备焊接试板。
3 试样制备3.1试样取样及尺寸、要求3.1.1焊接工艺评定的小铁研抗裂试样应符合图3-1规定横截面图3-13.1.2取样要求§(C ( CJ0X5^50 6080200, --------------------------a)所有切口不得用剪板机剪切b)所有棱角都应倒成R2圆角(除焊缝外);c)在所有试样端头打上钢印;d)所有试样表面不得有碰伤;e)试样数量:5件。
3.2试样取样位置321板材取样3.2.1.1板材对接焊缝工艺评定试样的类别和数量见表3-1,试样取样位置见图3-2舍1i1弃拉伸ii试样背弯ii试样面弯iii试样备i i用才匕才忑冃弯IIi试样面弯11丄试样拉伸ii试样冲击ii试样舍11弃舍111弃侧弯i1试样拉伸1I试样侧弯I11试样备I1用侧弯II试样拉伸111试样侧弯11试样冲击11试样舍1弃(a)不取侧弯试样时(b)取侧弯试样时图3-2板材取样位置图(未完)321.2试样要求a)试件角变形超过3°时,应在无损检测前进行冷校平。
b)试件经外观检查和无损检测合格后,允许避开缺陷取样。
c)力学性能试样应以机械法去除焊缝余高,使之与母材平齐d)应在试样端头和剩余试件的先焊面打上钢印标记。
3.2.2管材取样3.221管材对接焊缝试件取样位置见图3-33.222试样要求管材对接焊缝的试样要求按本规程的 3.2.1.2条之规定进行表3-1(a)拉力试样为整管时弯曲试样位置图3-3管材取样位置图(未完)(b)不要求冲击试验时(c)要求冲击试验时1 —拉力试样;2 —面弯试样;3—背弯试样;4 —侧弯试样;5—冲击试样;③⑥⑨12 —钟点记号,为水平固定位置焊接时的定位标记。
力学性能试验操作工艺规程
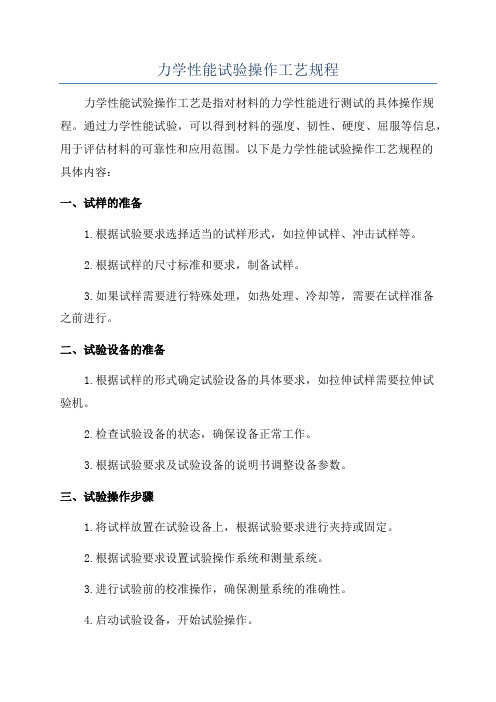
力学性能试验操作工艺规程力学性能试验操作工艺是指对材料的力学性能进行测试的具体操作规程。
通过力学性能试验,可以得到材料的强度、韧性、硬度、屈服等信息,用于评估材料的可靠性和应用范围。
以下是力学性能试验操作工艺规程的具体内容:一、试样的准备1.根据试验要求选择适当的试样形式,如拉伸试样、冲击试样等。
2.根据试样的尺寸标准和要求,制备试样。
3.如果试样需要进行特殊处理,如热处理、冷却等,需要在试样准备之前进行。
二、试验设备的准备1.根据试样的形式确定试验设备的具体要求,如拉伸试样需要拉伸试验机。
2.检查试验设备的状态,确保设备正常工作。
3.根据试验要求及试验设备的说明书调整设备参数。
三、试验操作步骤1.将试样放置在试验设备上,根据试验要求进行夹持或固定。
2.根据试验要求设置试验操作系统和测量系统。
3.进行试验前的校准操作,确保测量系统的准确性。
4.启动试验设备,开始试验操作。
5.根据试验要求记录试验数据,如载荷-位移曲线、应力-应变曲线等。
6.根据试验要求进行试验的停止和数据处理。
四、试验结果的评估1.根据试验数据计算所需的力学性能参数,如屈服强度、抗拉强度、断裂伸长率等。
2.对试验结果进行详细分析,包括异常数据、数据重复性和可靠性等。
3.将试验结果与标准或规范进行对比,评估材料的性能水平。
4.编写试验报告,详细描述试验过程和结果。
以上是力学性能试验操作工艺规程的一般内容。
根据具体的试验要求和材料特性,可能会有一些调整或增加。
在进行力学性能试验时,必须严格按照规程进行操作,确保试验结果的准确性和可靠性,以提供可靠的数据支持材料选择和设计。
现场试样制取及养护管理制度

现场试样制取及养护管理制度一、试样制取管理1.试样制取前,应根据试验要求和目的,明确所需试样的性质、数量和制取方式,并编制试样制取计划。
2.在试样制取过程中,应按照标准操作规程进行操作,确保试样的准确性和代表性。
3.在制取试样前,应对试样制取设备和器材进行验证和检查,确保其满足试验要求和质量控制要求。
4.制取试样前,应清洗并消毒试样制取设备和器材,以防止交叉污染。
5.试样制取时,应注意避免试样受到外界污染或损坏,确保试样的完整性和可靠性。
6.制取试样时,应按照规定的方法或程序进行标识、记录和保存,以便于识别和管理。
7.制取试样后,应及时交付给试验人员,并告知试样的制取条件、时间和位置等重要信息。
8.制取试样后,应将试样制取设备和器材进行清洁和保养,确保其良好的状态和功能。
二、试样养护管理1.试样在制取后,应根据试验要求和试样性质,采取适当的养护措施,确保试样的稳定性和可靠性。
2.试样养护期间,应定期检查试样的状态,如有异常情况应及时处理和记录。
3.试样养护期间,应保持试样的温度、湿度和光照等环境条件的稳定性,避免因环境变化导致试样性质变化。
4.试样养护期间,应避免试样受到外界污染,如需进行操作或分析,应遵守相应的操作规程和安全措施。
5.试样养护期间,应注意试样的保存方式和有效期,如有需要,应进行试样保存试验以确定试样的质量和稳定性。
6.试样养护期间,如有需要,应进行试样品质把关试验,以确保试样的质量和符合试验要求。
7.试样养护期间,应将试样和试样制取记录进行归档管理,并保留适当的时间,以备审查和追溯。
三、管理控制要求1.对试样制取过程进行规范,确保试样的准确性和代表性。
2.对试样制取设备和器材进行验证和检查,确保其满足试验要求和质量控制要求。
3.对试样制取人员进行培训和考核,提高其对试样制取的认识和技术能力。
4.对试样养护环境进行监控和调整,确保试样的稳定性和可靠性。
5.对试样进行标识、记录和管理,确保试样信息的完整性和可追溯性。
玻璃可见光透射比、遮阳系数试验操作规程

玻璃可见光透射比、遮阳系数试验操作规程
1、试样制备:试样为6块(3块试验,3块备用)于制品相同材料,在相同工艺条件下制作,或者直接从制品上切取的尺寸为100mm*100mm的试验片。
试验前用浸有无水乙醇(或乙醚)的脱脂棉清洗试样。
2、检测前需注明阳光入射面,如入射面为普通玻璃或者涂覆玻璃或者Low-E 玻璃。
3、接通电源,打开仪器和电脑,点击GOptic_SDS软件。
4、在操作屏幕中依次输入试样编号、玻璃层数、层间距离、玻璃种类等
5、按照透射率、正反射比、反反射比的试验顺序依次放入待测试样玻片。
6、透射比试验中,普通玻璃不区分正反面,涂覆或Low-E等其他玻璃检测时,镀膜面放内侧即光线入射面。
7、正反射比试验中,普通玻璃不区分正反面,涂覆或Low-E等其他玻璃检测时,镀膜面向上。
8、反反射比试验中,普通玻璃不区分正反面,涂覆或Low-E等其他玻璃检测时,镀膜面向下。
9、按照规范要求完成试验。
10、试验结束后导出试验数据,关闭机器,切断电源。
南通耀华建设工程质量检测有限公司。
金相试样制备实验报告

金相试样制备实验报告实验目的,通过金相试样制备实验,掌握金相试样的制备方法和步骤,为金相显微组织观察提供合适的试样。
实验原理,金相试样制备是指将金属试样经过一系列的制备工艺,使其表面光洁度和平整度达到一定要求,为后续金相显微组织观察提供条件。
金相试样制备的主要步骤包括切割、打磨、抛光和腐蚀等。
实验仪器和试剂,金相试样制备实验所需的仪器包括金相显微镜、金相试样制备机、金相显微组织观察系统等;试剂包括金相试样制备用的切割液、打磨液、抛光液、腐蚀液等。
实验步骤:1. 切割,将金属试样切割成符合要求的形状和尺寸,注意切割时要保持试样表面的平整度和光洁度。
2. 打磨,用打磨机对切割好的试样进行打磨,逐渐将试样表面的瑕疵和粗糙度去除,直至试样表面光洁度达到要求。
3. 抛光,将经过打磨的试样放入抛光机中进行抛光处理,使试样表面光洁度更加提高,同时去除打磨过程中产生的热损伤层。
4. 腐蚀,将经过抛光的试样放入腐蚀液中进行腐蚀处理,腐蚀时间和腐蚀液的浓度要根据试样材料和要求来确定,腐蚀后的试样表面应平整光滑。
实验结果,经过以上步骤的处理,制备好的金相试样表面光洁度和平整度符合要求,可以进行金相显微组织观察。
实验结论,通过本次金相试样制备实验,掌握了金相试样制备的基本方法和步骤,为后续金相显微组织观察提供了合适的试样。
同时也加深了对金相试样制备原理和工艺的理解,为今后的金相分析和研究打下了基础。
实验注意事项:1. 实验过程中要注意安全,避免发生意外伤害。
2. 切割、打磨、抛光和腐蚀等步骤要严格按照要求进行,注意操作技巧和方法。
3. 实验仪器和试剂的使用要符合操作规程,保持仪器的清洁和良好状态。
4. 实验结束后要及时清理和整理实验场地和仪器设备,保持实验室的整洁和安全。
通过本次金相试样制备实验,不仅提高了实验操作技能,还加深了对金相试样制备原理和工艺的理解,为今后的金相分析和研究打下了基础。
希望通过不断的实验实践和学习,能够更加熟练地掌握金相试样制备技术,为科研工作和实际应用提供更好的支持。
NACE SP0775-2013油田作业中腐蚀试样的制备、安装、分析和解释标准操作规程(中文翻译版)

NACE SP0775-2013油田作业中腐蚀试样的制备、安装、分析和解释标准操作规程(中文翻译版)本NACE国际标准代表了已审查本文件、其范围和条款的个别成员的共识。
其接受并不在任何方面妨碍任何人,无论其是否采用了本标准,制造、销售、购买或使用不符合本标准的产品、工艺或程序。
本NACE国际标准中的任何内容均不得解释为通过暗示或其他方式授予任何权利,以制造、销售或使用与专利证书所涵盖的任何方法、装置或产品有关的任何方法、装置或产品,或赔偿或保护任何人免受专利证书侵权的责任。
本标准代表最低要求,不应解释为对使用更好的程序或材料的限制。
本标准也不适用于与主题相关的所有情况。
不可预测的情况可能会否定本标准在特定情况下的有用性。
NACE国际对其他方对本标准的解释或使用不承担任何责任,仅对NACE国际根据其管辖程序和政策发布的官方NACE国际解释承担责任,这些程序和政策禁止个人发布解释志愿者。
本NACE国际标准的用户负责审查适当的健康、安全、环境和法规文件,并在使用本标准之前确定其适用性。
本NACE国际标准不一定涉及与使用本标准中详述或提及的材料、设备和/或操作相关的所有潜在健康和安全问题或环境危害。
本NACE国际标准的用户还应负责制定适当的健康、安全和环境保护措施,必要时与适当的监管机构协商,以在使用本标准之前达到任何现行适用的监管要求。
警告:NACE国际标准接受定期审查,并可根据NACE技术委员会程序随时修订或撤销。
NACE 国际要求在不迟于首次出版之日起五年内,以及自每次重申或修订之日起,采取行动重申、修订或撤回本标准。
提醒用户获取最新版本。
NACE国际标准的购买者可通过联系NACE国际第一服务部(地址:德克萨斯州休斯顿市South Creek路1440号,邮编:77084-4906)(电话+1281-228-6200)获得所有标准和其他NACE国际出版物的最新信息。
重申201 2-09-05重申2005-04-07修订1999-06-25修订1991修订1987批准1975美国腐蚀工程师协会South Creek路1440号。
原材料复验试样制备通用工艺规程

原材料复验试样制备通用工艺规程编制审核批准XX公司发布原材料复验试样取样通用工艺规程1 主题内容与适应范围1.1 本规程规定了压力容器用钢板、钢带、钢管、圆钢、锻件及其它型钢等原材料复验时试样取样与加工的方法和要求。
1.2 本规程适用于本公司制造的钢制压力容器产品用材料的复验。
其它材料的复验亦可参照执行。
2 总则材料复验试样的制备除符合本规程的规定外,还应遵守国家颁布的有关法令、法规、标准、本公司其它相应规程和图样及专用工艺文件的要求。
3 取样3.1 试样应在外观及尺寸合格的钢材上切取。
切取试样样坯时,应防止因受热、加工硬化及变形而影响其力学性能及工艺性能。
用火焰切割法切取样坯时,从样坯切割线至试样边缘必须留有足够的加工余量,一般不小于钢材的厚度或直径,但最小不得小于20mm。
对厚度或直径大于60mm的钢材,其加工余量可适当减小。
3.2 试样样坯切取位置及方向3.2.1 钢板应在钢板端部垂直于扎制方向切取拉伸、弯曲、冲击试样样坯。
对纵扎钢板,应在距边缘为板宽1/4图3-1 钢板切取样坯的示意图3.2.2 扁钢应从扁钢端部沿扎制方向距边缘为1/3处切取拉伸、弯曲和冲击样坯。
如图3-2所示。
应接近钢管内壁,样坯部位如图3-4所示。
3.2.4.3 钢管的冲击试样样坯应靠近内壁切取,试样缺口应垂直内壁,取样方向符合有关产品或标准的规定。
3.2.4.4 钢管的弯曲、扩口、缩口、压扁和卷边可以在任意部位切取样坯。
3.2.5.1 取样数量热处理单件重量小于或等于3500kg的锻件取一组试样(1个拉伸、3个冲击),热处理单件重量大于3500kg的锻件取两组试样(每组1个拉伸、3个冲击),两组试样位置间隔180°,如锻件长度大于直径的1.5倍时,则应在锻件两端各取一组试样。
3.2.5.2 取样方向锻件(不含条形)宜取切向试样,当不能制取切试样时,则取纵向或径向试样。
条形锻件宜取纵向试样。
3.2.5.3 取样部位筒形锻件和环形锻件的试样应取自锻件的端部,从壁厚的1/2处取样,见图3-5a)和图3-5b)。
sem生物样品制备步骤

sem生物样品制备步骤
SEM(扫描电子显微镜)是一种高分辨率的显微镜,常用于观察生物样品的微观结构。
生物样品制备是SEM观察的关键步骤之一,以下是一般的生物样品制备步骤:
1. 固定样品,首先,生物样品需要被固定以保持其原始结构。
常用的固定剂包括乙醛、戊二醛或glutaraldehyde等。
固定样品的方法可以根据具体的样品类型而有所不同。
2. 脱水,固定后的样品需要被脱水以去除水分,通常使用酒精逐渐替代水分。
这个过程需要逐渐提高酒精浓度,最终将样品置于无水酒精中。
3. 干燥,脱水后的样品需要被干燥以去除残留的溶剂。
常用的干燥方法包括自然干燥、临界点干燥或者冻干等。
4. 样品制备,干燥后的样品需要被切割、切片或者表面处理以展示所需的结构。
这可能涉及到金属喷镀以增加导电性,或者使用特殊的切割技术。
以上是一般的SEM生物样品制备步骤,不同类型的生物样品可能需要特定的处理步骤。
在进行SEM观察之前,样品制备的质量对于最终观察结果至关重要。
希望这些信息能够帮助到你。
试样的采取和制备通则

有多少,是静止物料还是流动物料,是已包装的还
是散装的,有无危险性等。对待采物料的状况了解
得越多,越有利于采样工作。
(3)、制订采样方案。 (4)、选定采样装置、明确采样技术。所述采样
装置,除了采样用的工具设备外,样品容器也应包
括在内。
(5)、采取样品,并将其制备成最终样品。
4、采样方案
采样前必须制定采样方案。
用户验收物料的质量依据。
16. 成分试样:为了分析试样或批样的化学成 分,按规定取制样方法从制备样品中取出的供 成分分析用试样。 17. 熔炼分析:熔炼分析是指在冶炼过程中采
取试样并对其进行的化学分析.分析结果表示
同一炉或同一罐钢液的平均化学成分。
18. 成品分析:成品分析是指在经过加工的成品钢 材(包括钢坯)上采取试样,然后对其进行的化学分 析。成品分析主要用于验证化学成分,又称验证 分析。由于钢液在结晶过程中产生元素不均匀分 布 (偏析),成品分析的值有时与熔炼分析的值不 同。
数就不同。(化产品要专讲)
(2)、样品量
在满足需要的前提下,样品量越少越好。但其
量至少应满足下列要求: ① 至少要够三次重复检测的需要; ② 当需要留存备考样品时,必须满足备考样品的 需要;
23. 系统取样:从一交货批中以一定的时间或 质量间隔取份样,最初的份样从第一间隔内随 机取样。 24. 误差:测量值与真值之差。 25. 随机误差:测量值有时高于或低于真值的
误差,但大多数次的总和趋近于零。
26. 系统误差:测量值总是高于或低于真值的误 差。 27. 偏差:测得值与一组测得值的平均值的差。 28. 样品的分用:在制样的一定阶段将样品分开,
(一)采样
从物料总体中取得具有充分代表性的样品的
土壤样品制备规程
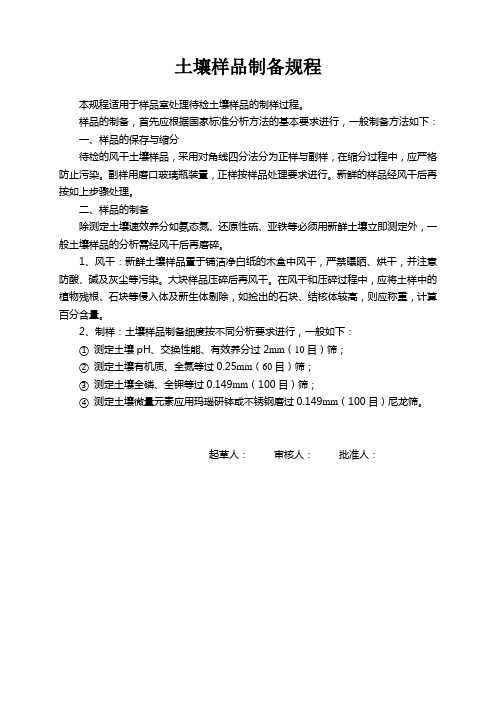
土壤样品制备规程
本规程适用于样品室处理待检土壤样品的制样过程。
样品的制备,首先应根据国家标准分析方法的基本要求进行,一般制备方法如下:
一、样品的保存与缩分
待检的风干土壤样品,采用对角线四分法分为正样与副样,在缩分过程中,应严格防止污染。
副样用磨口玻璃瓶装置,正样按样品处理要求进行。
新鲜的样品经风干后再按如上步骤处理。
二、样品的制备
除测定土壤速效养分如氨态氮、还原性硫、亚铁等必须用新鲜土壤立即测定外,一般土壤样品的分析需经风干后再磨碎。
1、风干:新鲜土壤样品置于铺洁净白纸的木盒中风干,严禁曝晒、烘干,并注意防酸、碱及灰尘等污染。
大块样品压碎后再风干。
在风干和压碎过程中,应将土样中的植物残根、石块等侵入体及新生体剔除,如捡出的石块、结核体较高,则应称重,计算百分含量。
2、制样:土壤样品制备细度按不同分析要求进行,一般如下:
①测定土壤pH、交换性能、有效养分过2mm(10目)筛;
②测定土壤有机质、全氮等过0.25mm(60目)筛;
③测定土壤全磷、全钾等过0.149mm(100目)筛;
④测定土壤微量元素应用玛瑙研钵或不锈钢磨过0.149mm(100目)尼龙筛。
起草人:审核人:批准人:。
第一章试样的采集与制备08

17
0.5m
1~2m 图1-1 物料堆上采样点的分布
h=0.3m m=5kg
18
一、固态物料的采样
1、物料堆中采样
对于袋(或桶)装的工业产品,每一袋(或 桶)为一件。多少件为一个化验单位,视不同产 品而定。如对于袋装化肥,通常规定50件以内抽 取5件;51~100件,每增10件,加取1件;101~ 500件,每增50件,加取2件;501~1000件以内 ,每增100件,加取2件;1001~5000件以内,每 增100件,加取1件。将子样均匀地分布该批物料 中,然后用采样工具进行采集。 例如,某批化肥为2000件,则应抽取的件数为: 5 + 5×1 + 8×2 + 5×2 + 10×1 = 46件
28
(二)采样设备
一般运行的生产设备上安装有采样阀。气 体采样装置一般由采样管、过滤器、冷却器及 气样容器组成。
采样管 玻璃、瓷或金属制成 过滤器 装有玻璃丝,用于除去 四部分结构 气体中的机械杂质 冷却器 大于2000 C的气体需冷却 气体容器 装采来的毛样
29
1-气体管道;2-采样管;3-过滤器;4-冷却器; 5-导气管;6-冷却水入口;7-冷却水出口;8,9-冷却管
图1-7 气体采样装置
30
(三)采样方法 1、常压状态气体采样
气体状态:等于大气压或低正压或低负压
采样方法:封闭液采样法
使用容器:采样瓶或采样管
31
采样装置图如下所示:
图1-8 采样瓶
图1-9 气样管
32
2、正压状态气体采样
气体状态:气体压力远远高于大气压力的为
正压气体;
采样工具:采样瓶、采样管、橡皮气囊或直
实验七 金相试样的制备及显微分析
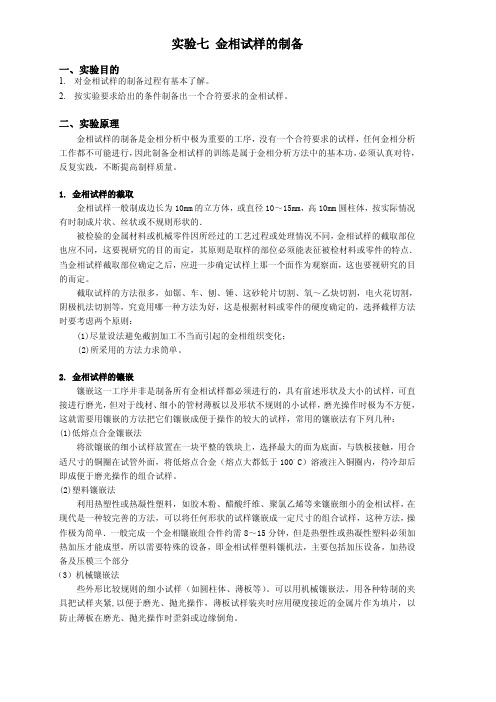
实验七金相试样的制备一、实验目的1.对金相试样的制备过程有基本了解。
2.按实验要求给出的条件制备出一个合符要求的金相试样。
二、实验原理金相试样的制备是金相分析中极为重要的工序,没有一个合符要求的试样,任何金相分析工作都不可能进行,因此制备金相试样的训练是属于金相分析方法中的基本功,必须认真对待,反复实践,不断提高制样质量。
1.金相试样的截取金相试样一般制成边长为10mm的立方体,或直径10~15mm,高10mm圆柱体,按实际情况有时制成片状、丝状或不规则形状的.被检验的金属材料或机械零件因所经过的工艺过程或处理情况不同,金相试样的截取部位也应不同,这要视研究的目的而定,其原则是取样的部位必须能表征被检材料或零件的特点.当金相试样截取部位确定之后,应进一步确定试样上那一个面作为观察面,这也要视研究的目的而定。
截取试样的方法很多,如锯、车、刨、锤、这砂轮片切割、氧~乙炔切割,电火花切割,阴极机法切割等,究竟用哪一种方法为好,这是根据材料或零件的硬度确定的,选择截样方法时要考虑两个原则:(1)尽量设法避免截割加工不当而引起的金相组织变化;(2)所采用的方法力求筒单。
2.金相试样的镶嵌镶嵌这一工序并非是制备所有金相试样都必须进行的,具有前述形状及大小的试样,可直接进行磨光,但对于线材、细小的管材薄板以及形状不规则的小试样,磨光操作时极为不方便,这就需要用镶嵌的方法把它们镶嵌成便于操作的较大的试样,常用的镶嵌法有下列几种:(1)低熔点合金镶嵌法将欲镶嵌的细小试样放置在一块平整的铁块上,选择最大的面为底面,与铁板接触,用合适尺寸的铜圈在试管外面,将低熔点合金(熔点大都低于100。
C)溶液注入铜圈内,待冷却后即成便于磨光操作的组合试样。
(2)塑料镶嵌法利用热塑性或热凝性塑料,如胶木粉、醋酸纤维、聚氯乙烯等来镶嵌细小的金相试样,在现代是一种较完善的方法,可以将任何形状的试样镶嵌成一定尺寸的组合试样,这种方法,操作极为简单.一般完成一个金相镶嵌组合件约需8~15分钟,但是热塑性或热凝性塑料必须加热加压才能成型,所以需要特殊的设备,即金相试样塑料镶机法,主要包括加压设备,加热设备及压模三个部分(3)机械镶嵌法些外形比较规则的细小试样(如圆柱体、薄板等)。
矿石及产品加工检验技术规程

矿石及产品加工检验技术规程第一节样品加工技术标准一. 块状矿样1.适用范围:适用于地质样、原矿样等块状样品的加工。
2.加工技术规程(1)矿石样品如有>40mm的矿块时,先用手锤砸碎,将试样放入干燥箱烘干。
(2)分别采用小型鄂式、盘磨破碎机对样品进行二至三段碎矿,最终排矿粒度要小于3mm。
(3)在各个破碎阶段,每加工一个样品后,必须将破碎腔内和漏斗内等处的矿石清扫干净,以免混样和污染。
(4)将破碎后的矿样在操作台上用堆锥法或翻滚法重复三次混匀。
(5)用槽式分样器或用四分法缩分试样,一般留取4g左右。
(6)将缩分出的2g左右试样作为正样进行细碎,缩分出的另外2g左右试样作为副样保存。
(7)正样和副样的样袋上必须按样品标签将试样名称、编号、加工日期、制样人、分析项目填写清楚。
(8)把正样放在干燥中,温度控制在1〜1050C烘烤1h。
(9)将正样装入棒磨机滚筒,将棒磨滚筒置于棒磨机中进行磨碎,磨碎时间一般为1.5〜2h,最终排矿粒度应小于0.074mm(-2目)。
(10)将磨好的试样在操作台上用对角线翻滚法混匀后装入试样袋,正样送实验室。
副样送副样保存室保存。
3.操作要求(1)对于块状样品的混匀、缩分等操作都必须用地质样专用操作台。
(2)对于块状样品的细磨必须用地质样专用棒磨滚筒。
(3)对于块状样品的加工使用的其它器具也必须是地质样专用器具。
4.加工工具(1)手锤。
(2)鄂式破碎机。
(3)圆盘粉碎机。
(5)刷子。
(6)槽式缩分器。
(7 )棒磨机。
(8)干燥箱。
(9)托盘天平。
(10 )混样胶皮。
(11 )样品。
二. 粉状矿样1.适用范围:适用于选矿原矿、尾矿、精矿及矿粉等粉状试样的加工。
2.加工技术规程(1 )将样品放入干燥箱烘干,干燥箱温度应该控制在1〜1050C。
(2)将烘干后的样品倒在操作台上用滚碾碾碎。
(3)将碾碎的样品放在混匀布上用对角线翻滚法充分混合均匀。
(4)将混合均匀的样品用四分法进行缩分数次。
金相试样的制备.
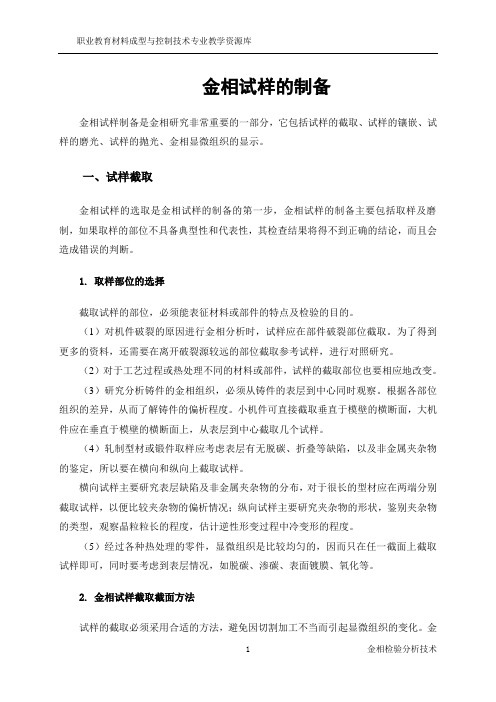
金相试样的制备金相试样制备是金相研究非常重要的一部分,它包括试样的截取、试样的镶嵌、试样的磨光、试样的抛光、金相显微组织的显示。
一、试样截取金相试样的选取是金相试样的制备的第一步,金相试样的制备主要包括取样及磨制,如果取样的部位不具备典型性和代表性,其检查结果将得不到正确的结论,而且会造成错误的判断。
1. 取样部位的选择截取试样的部位,必须能表征材料或部件的特点及检验的目的。
(1)对机件破裂的原因进行金相分析时,试样应在部件破裂部位截取。
为了得到更多的资料,还需要在离开破裂源较远的部位截取参考试样,进行对照研究。
(2)对于工艺过程或热处理不同的材料或部件,试样的截取部位也要相应地改变。
(3)研究分析铸件的金相组织,必须从铸件的表层到中心同时观察。
根据各部位组织的差异,从而了解铸件的偏析程度。
小机件可直接截取垂直于模壁的横断面,大机件应在垂直于模壁的横断面上,从表层到中心截取几个试样。
(4)轧制型材或锻件取样应考虑表层有无脱碳、折叠等缺陷,以及非金属夹杂物的鉴定,所以要在横向和纵向上截取试样。
横向试样主要研究表层缺陷及非金属夹杂物的分布,对于很长的型材应在两端分别截取试样,以便比较夹杂物的偏析情况;纵向试样主要研究夹杂物的形状,鉴别夹杂物的类型,观察晶粒粒长的程度,估计逆性形变过程中冷变形的程度。
(5)经过各种热处理的零件,显微组织是比较均匀的,因而只在任一截面上截取试样即可,同时要考虑到表层情况,如脱碳、渗碳、表面镀膜、氧化等。
2. 金相试样截取截面方法试样的截取必须采用合适的方法,避免因切割加工不当而引起显微组织的变化。
金相试样的选取分为:(1)纵向取样;纵向取样是指沿着钢材的锻轧方向进行取样。
主要检验内容为:非金属夹杂物的变形程度、晶粒畸变程度、塑性变形程度、变形后的各种组织形貌、热处理的全面情况等。
(2)横向取样;横向取样是只垂直于钢材锻扎方向取样。
主要检验内容为:金属材料从表层到中心的组织、显微组织状态、晶粒度级别、碳化物网、表层缺陷深度、氧化层深度、脱碳层深度、腐蚀层深度、表面化学热处理及镀层厚度等。
- 1、下载文档前请自行甄别文档内容的完整性,平台不提供额外的编辑、内容补充、找答案等附加服务。
- 2、"仅部分预览"的文档,不可在线预览部分如存在完整性等问题,可反馈申请退款(可完整预览的文档不适用该条件!)。
- 3、如文档侵犯您的权益,请联系客服反馈,我们会尽快为您处理(人工客服工作时间:9:00-18:30)。
工业锅炉典型工艺规程
试样制备
1 主题内容与适用范围
本规程规定了锅炉产品焊接试件及其制备与验收应遵守的规则。
本规程适用于介质出口压力不大于2.5MPa的锅炉受压元件焊接接头的焊接试件和试样的制备与验收。
2 引用标准
GB 228 金属拉力试验法
GB 232 金属弯曲试验方法
GB 2108 金属夏比(V型缺口)冲击试验方法
JB/T 1614 锅炉受压元件焊接接头机械性能检验方法
QB/HG J1210 钢印及标记移植
3 技术要求
3.1 试件设置
符合《蒸汽锅炉安全技术监察规程》和《热水锅炉安全技术监察规程》(以下简称《安规》)中的要求。
3.2 试件准备
3.2.1 备料
3.2.1.1 试件材料的牌号和炉批号应与产品相同。
3.2.1.2 试件下料应在产品所用材料的余料上同时截取,试件坯料的平面度不大于1mm,否则予以校平。
3.2.2 标记
3.2.2.1 试件上应打上材质入厂检验编号和试件编号钢印。
3.2.2.2 准备好的试件坯料应经检查合格才能进入装配工序。
3.2.3 坡口型式
3.2.3.1 试件的坡口型式应和产品的焊缝坡口型式相同。
3.2.3.2 试件坡口加工方法应和产品的焊缝坡口加工方法相同。
3.2.4 试件尺寸
3.2.
4.1 锅筒纵(环)缝试板尺寸为300×150mm。
3.2.
4.2 集箱、管道的对接环缝试件尺寸是沿其焊缝两侧分别截取100mm。
3.2.4.3 受热面管子对接试件尺寸是沿其焊缝两侧分别截取100mm。
3.3试件的装配与焊接
3.3.1 试件的装配
3.3.1.1 装配前试件焊缝端面及两侧20mm范围内应予清理并露出金属光泽。
3.3.1.2 纵缝检查试板装配应作为产品纵缝的延长部分,装配偏差与产品纵缝装配要求相一致。
装配时应在其首道焊的背面定位焊后焊固在产品焊缝上(在有材料编号的一端装焊收弧板,另一端与产品装配),要求试板对接缝与产品纵缝对准在同一直线上,并要防止焊后过度翘曲(一般以不翘出基准线5度为宜),对于模拟焊接试件应单独装配。
3.3.1.3 试件装配后应经检验合格后,才能进入焊接工序。
3.3.2 焊接
3.3.2.1 试件焊接所用的焊接材料、焊接设备和工艺条件应与产品相同,并由焊该产品的同一焊工焊接,焊后打上焊工代号钢印。
3.3.2.2 纵缝检查试板的焊接应作为产品纵缝的延长部分焊接,模拟试件单独焊接。
3.4 试件焊后处理及检查
3.4.1 试件与产品需分离的应在原焊固处气割,并避免损伤产品。
3.4.2 试件焊缝外观应符合产品焊缝检查标准的要求,合格后进入探伤工序。
3.4.3 试件焊缝应作100%射线探伤,其合格标准应与产品焊逢的合格标准相同,并作出评定报告。
3.4.4 试件焊缝返修时其返修工艺应与产品焊缝返修工艺相同,返修后应按(3.4.2和3.4.3条)进行检查。
3.4.5 试件所代表的产品需进行焊后热处理时,试件应随产品同炉进行,热处理必须在焊缝射线探伤合格后进行。
3.5 试样制备
3.5.1 试样备料
3.5.1.1 试样样坯应在外观检查和无损探伤合格后的检查试件无缺陷部位上
切取(祥见《安规》附录)。
3.5.1.2 试件数量
3.5.1.2.1 为检查焊接接头整个厚度上的抗拉强度,应从检查试板上沿焊缝的横向切取一个焊接接头拉力试样。
管子对接接头的拉力试样应从焊接试件上切取二个,亦可用整根焊接试件作拉力试验以代替二个拉力试样的试验。
3.5.1.2.2 当板厚大于10mm时,应从纵缝检查试板上沿焊缝纵向切取全焊缝金属拉力试样一个。
3.5.1.2.3 从检查试板上沿焊缝的横向切取二个焊接接头的弯曲试样,其中一个为面弯试样,一个为背弯试样。
对于异种钢接头,可用纵向弯曲试样代替横向弯曲试样。
管子对接接头的弯曲试样应从焊接试件上切取二个,一个面弯,一个背弯。
若焊接工艺评定时有管子背弯项目,产品可不做背弯试验。
但检查试件的未焊透及内凹深度不超过下表规定。
试样与焊件同时热处理),其边缘应留有足够的加工余量,以保证加工后彻底去除因气割产生的热影响区。
按取样手段的不同,须留不同的加工余量,一般气割下料留8-12mm,机加工下料留3-5mm,试件越厚留加工余量越大。
3.5.1.4 焊接接头试样和试件余料应保留三个月(以该批产品最后一台入库日期起算),以便对焊接接头机械性能进行复查。
3.5.1.5 加工好的试样应打上试样编号钢印,经检验合格后,方可进行试验。
3.5.2 试样加工
3.5.2.1 拉力试样
3.5.2.1.1 钢板、管子对接接头拉力试样(试样形状和尺寸见《安规》)
a.机加工下料;
b.用打磨或机加工方法清除高于母材表面的焊缝部分,使清除后焊缝金
属局部高出母材表面不超过0.5mm;
c.刨加工四周,粗糙度达到Ra12.5um;
d.铣加工圆弧半径及两平行平面,粗糙度达到Ra3.2um;
e.检验、打钢印标记并移植原编号。
3.5.2.1.2 全焊透金属拉力试样(试样形状和尺寸见《安规》)
a.机加工下料;
b.粗车各外圆及端面,粗糙度达到Ra12.5um;
c.精车外圆,粗糙度达到Ra0.8umm;
d.检验、打钢印标记并移植原编号。
3.5.2.2 弯曲试样(试样形状和尺寸见《安规》)
a.机加工下料;
b.用打磨或机加工方法清除高于母材表面的焊缝部分,试样受拉面应保留焊缝两侧中至少一侧的母材原始表面;
c.刨加工四周,粗糙度达到Ra12.5um;
d.修挫试样拉伸面的棱角,圆角半径不大于2mm;
e.检验、打钢印标记并移植原编号。
3.5.2.3 冲击试样(试样形状和尺寸见GB2106)
a.机加工下料;
b.刨加工各平面,留余量0.3-0.4mm;
c.磨削四个平面,粗糙度达到Ra0.8um;
d.划缺口线;
e.铣加工V型缺口,留余量0.1-0.2mm;
f.磨削V型缺口,粗糙度达到Ra0.8um;
g.检验、打钢印标记并移植原编号。
3.6 焊缝机械性能试验
3.6.1 拉力试验按GB228规定的方法进行。
3.6.2 弯曲试样按GB232规定的方法进行。
3.6.3 冲击试验按GB2106规定的方法进行。
3.6.4 各项试验的合格标准见《安规》。
3.6.5 试验结果的记录及记录保存期限见JB/T1614。