ASME CODE CASE 2115-1与 HK40焊接裂纹及修复
三类压力容器焊缝裂纹修补方案

三类压力容器焊缝裂纹修补方案三类压力容器焊缝裂纹修补方案一、编制依据1.TSG-R0004-2009《压力容器安全技术监察规程》2.GB150-1998《钢制压力容器》3.JB/T4709-2000《钢制压力容器焊接规程》4.JB/T4730-2005 压力容器无损检测二、主题内容与适用范围2.1 工程项目简介本方案提出了检修过程的详细质量标准、相关技术及安全注意事项。
聚合釜是聚丙烯生产的主要设备,其设计压力 4.0MPa 、转速55r/min、轴直径为150mm。
三、设备修前运行状况与检修原因由于聚合釜R-801/4在生产运行过程釜体与夹套之间有内漏现象,经兰石所做磁粉探伤发现底部喷料口法兰与釜体及夹套焊缝西侧有约165mm裂纹,中部热偶焊缝处约有80mm裂纹。
制定了聚合釜R-801/4缺陷处理方案,消除该设备隐患。
见图:R-801/4设备参数(表一)设备类型介质压力(Mpa)温度 (℃) 规格重量(t)材质容积 (m3)R-801/4聚合釜设备参数三类丙烯、粉料操作:3.6设计:4.0操作:83设计:100Φ2000*8216 14.917主体材质16MNR(δ=30mm)12四、检修内容4.1、检修前准备工作4.1.1、设备内介质彻底排空,置换合格后加盲板隔离。
对R-801/4进行氮气置换,置换合格后加盲板与系统隔离。
4.1.2、备好有限空间作业的安全防护用具;4.1.3、提前接好临时电源;4.1.4、准备好碳弧气刨、打磨工具;4.1.5、上下人孔安装风机低吹高吸;4.1.6、准备好图纸、技术方案,必要的施工方案。
4.1.7、联系电气停R-801/4搅拌电机、循环油泵电机,上锁挂签。
4.2、缺陷处理程序:缺陷、坡口修磨(碳弧气刨、砂轮机)——渗透检测(直至缺陷消除)——缺陷修补——射线检测——局部热处理——水压试验。
4.2.1、缺陷、坡口修磨(碳弧气刨、砂轮机两种方式结合):4.2.1.1焊缝表面的气孔、夹渣及焊瘤等缺陷,应本着焊缝打磨后不低于母材的原则,用砂轮磨掉缺陷。
焊接缺陷的检测与修复技术

焊接缺陷的检测与修复技术引言焊接是金属加工领域中一种重要的连接工艺,但由于操作不当或材料问题,焊接过程中常常会出现一些缺陷,这些缺陷可能对焊接接头的强度和耐久性产生不利影响。
因此,及时检测和修复焊接缺陷是保证焊接接头质量和安全性的重要环节。
本文将介绍常见的焊接缺陷类型、检测方法以及相应的修复技术。
一、焊接缺陷类型在焊接过程中常见的缺陷类型包括气孔、夹渣、裂纹、焊缝不良形态等。
它们的形成原因各异,下面将逐一介绍:1. 气孔气孔是焊接缺陷中最常见的一种,指的是焊缝内部存在的小气泡。
气孔的形成原因主要有以下几点: - 动作不稳定:焊工操作时不稳定的手部动作会导致气体陷入焊缝中。
- 材料问题:焊接材料中的含氧量过高,或者含有水分等气体,也会导致气孔的产生。
- 焊接工艺参数不合理:焊接电流、电压、焊接速度等参数设置不合理会导致气孔的形成。
2. 夹渣夹渣是指焊缝中存在的夹杂物,主要是一些未熔化的焊接剂、氧化物等。
夹渣的形成原因主要有以下几点: - 渣池不稳定:焊工操作不当,焊接电流过大、速度过快等会导致焊缝中存在未熔化的焊接剂。
- 焊接材料不洁净:焊接材料表面存在油污、铁锈等,会导致未熔化的金属残留在焊缝中。
- 焊接工艺不合理:焊接参数设置不合理,如电流过小、焊枪摆动过快等,会导致夹渣的产生。
3. 裂纹裂纹是焊接缺陷中最为严重的一种,它会导致焊接接头的强度降低甚至完全破坏。
裂纹的形成原因主要有以下几点: - 焊接变形过大:焊接时由于热收缩或冷却速度过快等会导致焊接接头产生应力,进而引起裂纹。
- 硬化层过脆:焊接过程中产生的硬化层过脆,受到外力影响容易发生裂纹。
- 焊接材料质量问题:焊接材料含有质量问题,如材料中存在夹杂物、劣质金属等,会影响焊接接头的强度。
4. 焊缝不良形态焊缝不良形态是指焊接接头的形态与规定要求不符,例如焊缝过宽、过窄、过高、过低等。
不良形态会降低焊接接头的强度和耐久性,需要及时予以修复。
钢结构焊接工艺中的缺陷检测与修复

钢结构焊接工艺中的缺陷检测与修复钢结构作为一种重要的建筑材料,广泛应用于现代工程领域。
正确认识钢结构焊接工艺中的缺陷,并且采取有效的检测和修复措施,对保障钢结构的安全性和可靠性具有重要意义。
本文将针对钢结构焊接工艺中的常见缺陷进行探讨,并分析相应的检测方法及修复技术。
一、焊接工艺中的常见缺陷1. 焊缝咬边缺陷:焊缝咬边缺陷是指焊缝与母材之间存在缺陷或者缺少金属堆积的情况。
其主要原因是焊接电弧由于一些外部因素的影响,导致焊缝边缘没有充分熔化或凝固,从而形成焊缝咬边缺陷。
为了检测咬边缺陷,可以使用超声波探伤等无损检测方法。
2. 气孔缺陷:气孔缺陷是指焊接过程中由于焊膏中的气体无法完全释放,导致在焊缝内部形成气孔的现象。
气孔缺陷对钢结构的强度和密封性产生严重影响。
常用的检测方法包括X射线和γ射线检测。
3. 焊接接头裂纹:焊接接头裂纹是指焊缝和母材之间或者焊缝内部出现的裂纹。
接头裂纹可能由于焊接过程中的温度变化和残余应力的影响而产生。
对于检测接头裂纹,可以采用磁粉探伤法或者渗透液探伤法。
二、缺陷检测方法1. 超声波探伤法: 超声波探伤是一种常用的无损检测方法,通过超声波的传播和反射来判断材料内部是否存在缺陷。
超声波探伤方法对于检测焊接缺陷具有较高的精度和可靠性。
2. X射线和γ射线检测: X射线和γ射线检测是常用的检测方法,可以有效检测焊接缺陷中的气孔、裂纹等缺陷。
这些方法对于检测较大厚度的钢结构具有较好的穿透能力。
3. 磁粉探伤法: 磁粉探伤法是一种利用电磁感应原理进行检测的方法,适用于检测钢结构焊缝中的裂纹等缺陷。
该方法灵敏度高,对于表面裂纹的检测效果较好。
三、缺陷修复技术1. 补焊修复: 对于焊缝缺陷较小的情况,可以通过补焊的方式进行修复。
补焊时需要注意焊接参数的选择和焊接工艺的合理控制,以确保修复焊缝的质量。
2. 切割修复: 对于严重的焊缝缺陷,可以采用切割修复的方式。
切割修复需要根据缺陷的具体情况,选择合适的切割方法和设备,并在修复后重新进行焊接工艺验证。
焊接修复法特点及应用

焊接修复法特点及应用焊接修复法是指通过焊接技术对损坏或破裂的材料进行修复的方法。
焊接修复法具有以下几个特点:1. 灵活性:焊接修复法可以适用于多种材料的修复,如金属、塑料等。
而且可以对不同类型的材料进行修复,不受材料的硬度、厚度等限制。
2. 经济性:焊接修复法相对于替换原材料而言,成本较低。
通过焊接修复法,可以将部分或全部破碎的材料重组,而不需要完全更换材料,从而节约了修复成本。
3. 高强度:焊接修复法可以在原有材料的破裂部位重新连接,形成牢固的接头。
焊接修复后的材料具有与原材料相近的强度,可以承受一定的载荷。
4. 可靠性:焊接修复法修复的材料具有良好的密封性和耐蚀性,可以避免进一步的损坏。
焊接修复方法确保了修复处的接缝牢固且可靠,能够满足工作环境的要求。
5. 快速性:焊接修复法修复过程相对简便,操作方便,并且修复时间相对较短。
可以在较短的时间内将破裂的部件修复完毕,减少了生产和维护过程中的停机时间。
焊接修复法主要应用于以下几个方面:1. 金属结构修复:焊接修复法可以修复金属结构中的破损、破裂等问题。
常见的应用包括焊接修复钢结构、铁路轨道、桥梁等。
2. 机械设备维修:焊接修复法可以修复机械设备中的破损或连接部件的断裂。
常用于修复发动机、轴承、齿轮等。
3. 管道修复:焊接修复法可以修复管道系统中的破损、漏水等问题。
常用于修复石油、天然气等管道系统。
4. 车辆修复:焊接修复法可以修复车辆中的破损或变形问题。
常用于修复汽车车身、发动机、车轮等。
除此之外,焊接修复法还可以应用于冶金、航空航天、建筑等领域中对材料进行修复。
总的来说,焊接修复法是一种常用的修复方法,具有灵活性、经济性、高强度、可靠性和快速性等特点,被广泛应用于多个领域中。
厚板焊缝返修方案
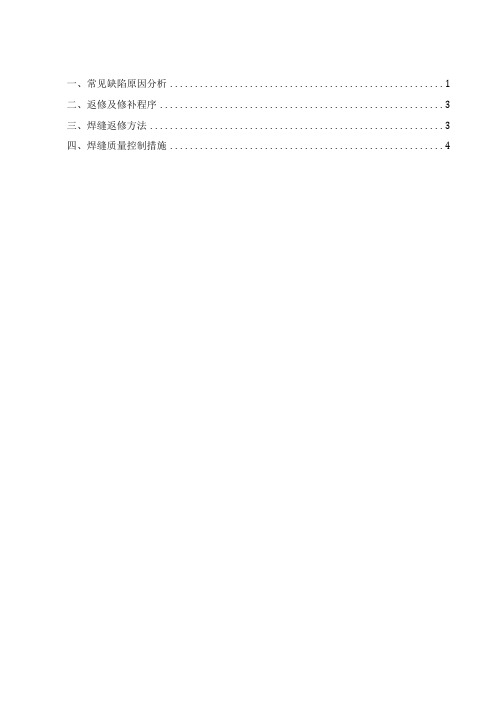
一、常见缺陷原因分析 (1)二、返修及修补程序 (3)三、焊缝返修方法 (3)四、焊缝质量控制措施 (4)焊接是安装工程中一项比较重要的工序,焊接接头的存在会直接危及整个结构的质量及安全运行。
因此,将焊接接头缺陷尽量控制在规范允许范围内是每个焊接操作人员及工程管理人员应尽的责任。
一、常见缺陷原因分析常见的焊接接头缺陷主要有咬边、焊瘤、凹坑、夹渣、根部未焊透、未熔合和裂纹及裂缝等。
1、外观缺陷(1)咬边咬边是指沿着焊趾,在母材部分形成的凹陷或沟槽,它是由于电弧将焊缝边缘的母材熔化后没有得到熔敷金属的充分补充所留下的缺口。
咬边最大的危害是损伤了母材,使母材有效截面减小,也会引起应力集中。
产生咬边的主要原因是电弧热量太高,即电流太大,运条速度太小所造成的。
焊条与工件间角度不正确,摆动不合理,电弧过长,焊接次序不合理等都会造成咬边。
(2)焊瘤焊缝中的液态金属流到加热不足未熔化的母材上或从焊缝根部溢出,冷却后形成的未与母材熔合的金属瘤即为焊瘤。
焊瘤主要是由于焊接电流过大或焊接速度过慢引起的,它的危害是焊瘤处易应力集中且影响整个焊缝的外观质量。
(3)凹坑凹坑指焊缝表面或背面局部的低于母材的部分。
凹坑多是由于收弧时焊条(焊丝)未作短时间停留造成的(此时的凹坑称为弧坑)仰立、横焊时,常在焊缝背面根部产生内凹。
凹坑减小了焊缝的有效截面积,弧坑常带有弧坑裂纹和弧坑缩孔。
(4)未焊满未焊满是指焊缝表面上连续的或断续的沟槽。
填充金属不足是产生未焊满的根本原因。
焊条过细,运条不当等会导致未焊满。
(5)其他表面缺陷:①成形不良指焊缝的外观几何尺寸不符合要求。
有焊缝超高,表面不光滑,以及焊缝过宽,焊缝向母材过渡不圆滑等。
②错边指两个工件在厚度方向上错开一定位置,它既可视作焊缝表面缺陷,又可视作装配成形缺陷。
③塌陷单面焊时由于输入热量过大,熔化金属过多而使液态金属向焊缝背面塌落,成形后焊缝背面突起,正面下塌。
④表面气孔及弧坑缩孔。
机械压力机焊接齿轮裂纹修复
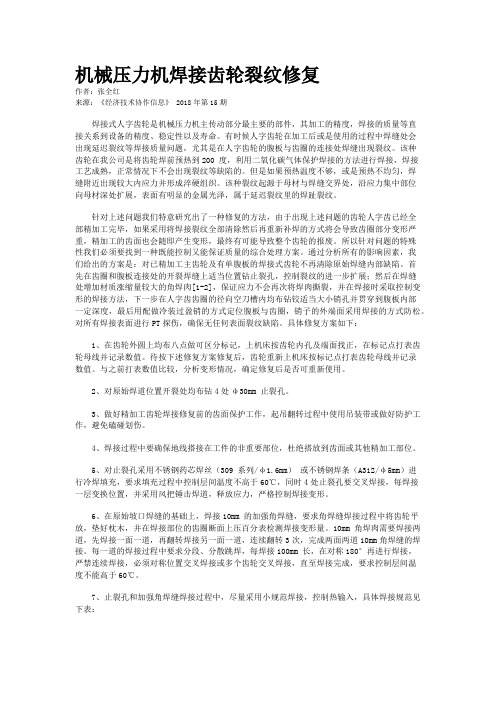
机械压力机焊接齿轮裂纹修复作者:张全红来源:《经济技术协作信息》 2018年第15期焊接式人字齿轮是机械压力机主传动部分最主要的部件,其加工的精度,焊接的质量等直接关系到设备的精度、稳定性以及寿命。
有时候人字齿轮在加工后或是使用的过程中焊缝处会出现延迟裂纹等焊接质量问题,尤其是在人字齿轮的腹板与齿圈的连接处焊缝出现裂纹。
该种齿轮在我公司是将齿轮焊前预热到200 度,利用二氧化碳气体保护焊接的方法进行焊接,焊接工艺成熟,正常情况下不会出现裂纹等缺陷的。
但是如果预热温度不够,或是预热不均匀,焊缝附近出现较大内应力并形成淬硬组织。
该种裂纹起源于母材与焊缝交界处,沿应力集中部位向母材深处扩展,表面有明显的金属光泽,属于延迟裂纹里的焊趾裂纹。
针对上述问题我们特意研究出了一种修复的方法,由于出现上述问题的齿轮人字齿已经全部精加工完毕,如果采用将焊接裂纹全部清除然后再重新补焊的方式将会导致齿圈部分变形严重,精加工的齿面也会随即产生变形,最终有可能导致整个齿轮的报废。
所以针对问题的特殊性我们必须要找到一种既能控制又能保证质量的综合处理方案。
通过分析所有的影响因素,我们给出的方案是:对已精加工主齿轮及有单腹板的焊接式齿轮不再清除原始焊缝内部缺陷。
首先在齿圈和腹板连接处的开裂焊缝上适当位置钻止裂孔,控制裂纹的进一步扩展;然后在焊缝处增加材质涨缩量较大的角焊肉[1-2],保证应力不会再次将焊肉撕裂,并在焊接时采取控制变形的焊接方法,下一步在人字齿齿圈的径向空刀槽内均布钻铰适当大小销孔并贯穿到腹板内部一定深度,最后用配做冷装过盈销的方式定位腹板与齿圈,销子的外端面采用焊接的方式防松。
对所有焊接表面进行PT探伤,确保无任何表面裂纹缺陷。
具体修复方案如下:1、在齿轮外圆上均布八点做可区分标记,上机床按齿轮内孔及端面找正,在标记点打表齿轮母线并记录数值。
待按下述修复方案修复后,齿轮重新上机床按标记点打表齿轮母线并记录数值。
与之前打表数值比较,分析变形情况,确定修复后是否可重新使用。
工程机械常见焊接开裂与修复技术
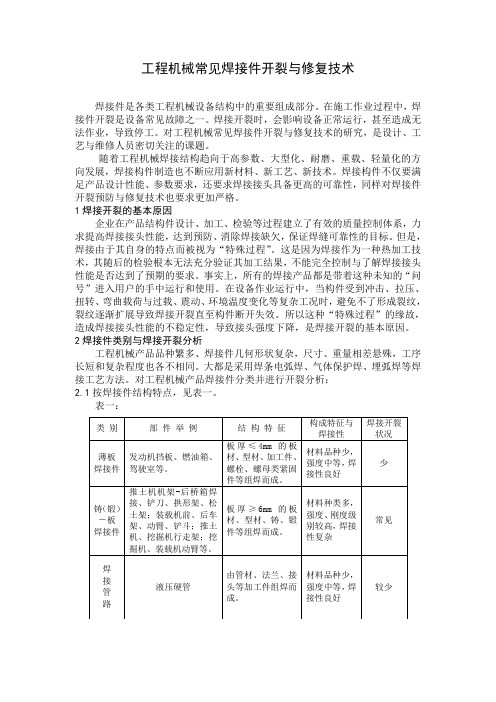
工程机械常见焊接件开裂与修复技术焊接件是各类工程机械设备结构中的重要组成部分。
在施工作业过程中,焊接件开裂是设备常见故障之一。
焊接开裂时,会影响设备正常运行,甚至造成无法作业,导致停工。
对工程机械常见焊接件开裂与修复技术的研究,是设计、工艺与维修人员密切关注的课题。
随着工程机械焊接结构趋向于高参数、大型化、耐磨、重载、轻量化的方向发展,焊接构件制造也不断应用新材料、新工艺、新技术。
焊接构件不仅要满足产品设计性能、参数要求,还要求焊接接头具备更高的可靠性,同样对焊接件开裂预防与修复技术也要求更加严格。
1焊接开裂的基本原因企业在产品结构件设计、加工、检验等过程建立了有效的质量控制体系,力求提高焊接接头性能,达到预防、消除焊接缺欠,保证焊缝可靠性的目标。
但是,焊接由于其自身的特点而被视为“特殊过程”。
这是因为焊接作为一种热加工技术,其随后的检验根本无法充分验证其加工结果,不能完全控制与了解焊接接头性能是否达到了预期的要求。
事实上,所有的焊接产品都是带着这种未知的“问号”进入用户的手中运行和使用。
在设备作业运行中,当构件受到冲击、拉压、扭转、弯曲载荷与过载、震动、环境温度变化等复杂工况时,避免不了形成裂纹,裂纹逐渐扩展导致焊接开裂直至构件断开失效。
所以这种“特殊过程”的缘故,造成焊接接头性能的不稳定性,导致接头强度下降,是焊接开裂的基本原因。
2焊接件类别与焊接开裂分析工程机械产品品种繁多、焊接件几何形状复杂,尺寸、重量相差悬殊,工序长短和复杂程度也各不相同。
大都是采用焊条电弧焊、气体保护焊、埋弧焊等焊接工艺方法。
对工程机械产品焊接件分类并进行开裂分析:2.1按焊接件结构特点,见表一。
表一:2.2按焊接件功能,见表二。
表二2.3按钢材强度级别,见表三。
表三通过以上对焊接件分类与焊接开裂的分析可以看出,焊接件开裂主要集中在工作装置类构件。
这是因为此类焊接件不仅结构复杂、承受大的工作载荷,抗变形能力差,而且采用的钢材品种多、强度级别高,焊接施工难度大。
焊接裂纹的分析与处理
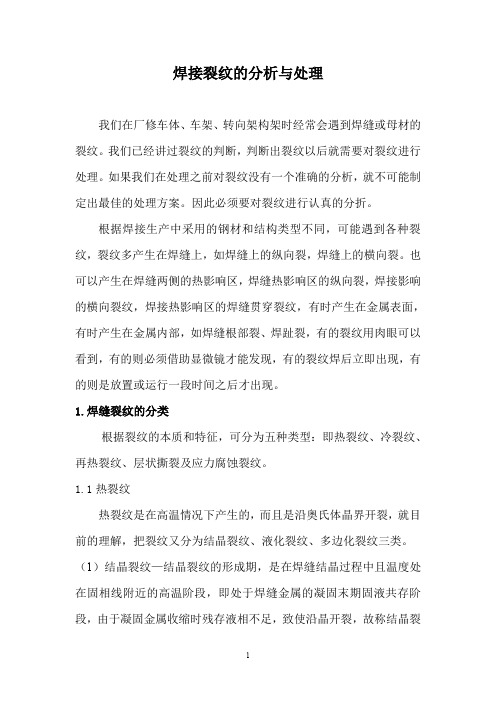
焊接裂纹的分析与处理我们在厂修车体、车架、转向架构架时经常会遇到焊缝或母材的裂纹。
我们已经讲过裂纹的判断,判断出裂纹以后就需要对裂纹进行处理。
如果我们在处理之前对裂纹没有一个准确的分析,就不可能制定出最佳的处理方案。
因此必须要对裂纹进行认真的分折。
根据焊接生产中采用的钢材和结构类型不同,可能遇到各种裂纹,裂纹多产生在焊缝上,如焊缝上的纵向裂,焊缝上的横向裂。
也可以产生在焊缝两侧的热影响区,焊缝热影响区的纵向裂,焊接影响的横向裂纹,焊接热影响区的焊缝贯穿裂纹,有时产生在金属表面,有时产生在金属内部,如焊缝根部裂、焊趾裂,有的裂纹用肉眼可以看到,有的则必须借助显微镜才能发现,有的裂纹焊后立即出现,有的则是放置或运行一段时间之后才出现。
1.焊缝裂纹的分类根据裂纹的本质和特征,可分为五种类型:即热裂纹、冷裂纹、再热裂纹、层状撕裂及应力腐蚀裂纹。
1.1热裂纹热裂纹是在高温情况下产生的,而且是沿奥氏体晶界开裂,就目前的理解,把裂纹又分为结晶裂纹、液化裂纹、多边化裂纹三类。
(1)结晶裂纹—结晶裂纹的形成期,是在焊缝结晶过程中且温度处在固相线附近的高温阶段,即处于焊缝金属的凝固末期固液共存阶段,由于凝固金属收缩时残存液相不足,致使沿晶开裂,故称结晶裂纹,由于这种裂纹是在焊缝金属凝固过程中产生的,所以也称为凝固裂纹。
结晶裂纹的特征:存在的部位主要在焊缝上,也有少量的在热影响区,最常见的是沿焊缝中心长度方向上开裂,即纵向裂,断口有较明显的氧化色,表面无光泽,也是结晶裂纹在高温下形成的一个特征。
(2)液化裂纹—焊接过程中,在焊接热循环峰值温度作用下,在多层焊缝的层间金属以及母材近缝区金属中,由于晶间层金属被重新熔化,在一定的收缩应力的作用下,沿奥氏体晶界产生的开裂,称为“液化裂纹”也称“热撕裂”。
液化裂的特征:①易产生在母材近缝区中紧靠熔合线的地方(部分溶化区),或多层焊缝的层间金属中。
②裂纹的走向,在母材近缝区中,裂纹沿过热奥氏体晶间发展;在多层焊缝金属中,裂纹沿原始柱状晶界发展,裂纹的扩展方向,视应力的最大方向而定,可以是横向或纵向;并在多层焊焊缝金属中,液化裂纹可以贯穿层间;在近缝区中的液化裂纹可以穿越熔合线进入焊缝金属中。
焊接接头表面裂纹检测与修复技术

焊接接头表面裂纹检测与修复技术焊接接头作为工程结构中常用的连接方式之一,其质量直接关系到整个结构的安全性和稳定性。
然而,在焊接过程中,由于材料的热膨胀和收缩,以及焊接参数的控制等因素,往往会导致接头表面出现裂纹。
这些裂纹如果得不到及时的检测与修复,将会对结构的使用寿命和安全性产生严重影响。
因此,焊接接头表面裂纹的检测与修复技术显得尤为重要。
一、焊接接头表面裂纹的检测技术焊接接头表面裂纹的检测技术主要包括目视检测、超声波检测和磁粉检测等方法。
1. 目视检测目视检测是最简单、最常用的检测方法之一。
通过肉眼观察焊接接头表面是否存在裂纹来判断其质量。
然而,目视检测只能发现较大的裂纹,对于微小裂纹的检测效果较差。
因此,在实际应用中,目视检测常常与其他检测方法结合使用,以提高检测的准确性和可靠性。
2. 超声波检测超声波检测是一种常用的无损检测方法,通过将超声波传入焊接接头中,利用声波的传播和反射特性来检测裂纹的存在和位置。
超声波检测具有高灵敏度、高准确性和非破坏性等优点,可以有效地检测到微小裂纹。
然而,超声波检测设备价格较高,操作技术要求较高,需要经过专门的培训才能熟练掌握。
3. 磁粉检测磁粉检测是一种利用磁场和磁性粉末来检测裂纹的方法。
通过在焊接接头表面涂覆磁性粉末,并施加磁场,当存在裂纹时,磁粉末会在裂纹处形成磁粉堆积。
通过观察磁粉堆积的形状和颜色来判断裂纹的存在和位置。
磁粉检测具有操作简便、成本低廉的优点,但对于深埋在焊缝内部的裂纹检测效果较差。
二、焊接接头表面裂纹的修复技术焊接接头表面裂纹的修复技术主要包括打磨修复、填补焊接和焊接补焊等方法。
1. 打磨修复打磨修复是最常用的修复方法之一。
通过使用砂轮、砂纸等工具将焊接接头表面的裂纹打磨平整,然后进行喷漆或其他保护措施,以防止裂纹再次出现。
打磨修复的优点是操作简单、成本低廉,但对于深度较大的裂纹效果较差。
2. 填补焊接填补焊接是一种常用的修复方法,通过在裂纹处进行填补焊接,使焊接接头表面恢复完整。
钢结构裂纹的修复方法
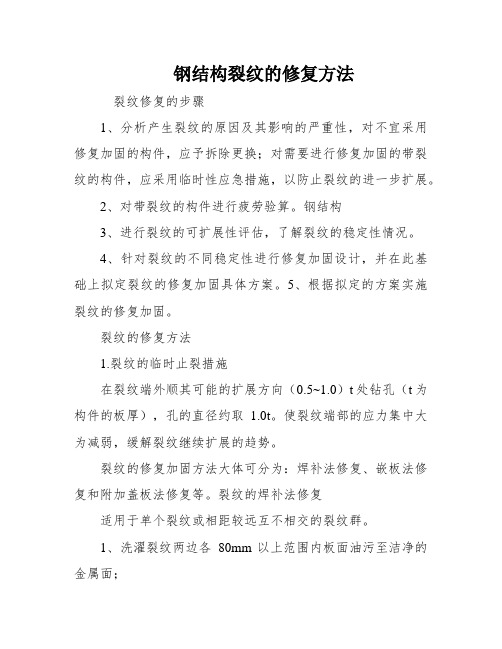
钢结构裂纹的修复方法裂纹修复的步骤1、分析产生裂纹的原因及其影响的严重性,对不宜采用修复加固的构件,应予拆除更换;对需要进行修复加固的带裂纹的构件,应采用临时性应急措施,以防止裂纹的进一步扩展。
2、对带裂纹的构件进行疲劳验算。
钢结构3、进行裂纹的可扩展性评估,了解裂纹的稳定性情况。
4、针对裂纹的不同稳定性进行修复加固设计,并在此基础上拟定裂纹的修复加固具体方案。
5、根据拟定的方案实施裂纹的修复加固。
裂纹的修复方法1.裂纹的临时止裂措施在裂纹端外顺其可能的扩展方向(0.5~1.0)t处钻孔(t为构件的板厚),孔的直径约取1.0t。
使裂纹端部的应力集中大为减弱,缓解裂纹继续扩展的趋势。
裂纹的修复加固方法大体可分为:焊补法修复、嵌板法修复和附加盖板法修复等。
裂纹的焊补法修复适用于单个裂纹或相距较远互不相交的裂纹群。
1、洗濯裂纹两边各80mm以上范围内板面油污至洁净的金属面;2、用碳弧气刨或风铲将裂纹边缘加工出坡口,直达裂纹端部的姑且止裂钻孔。
坡口形式根据板厚和施工条件按现行《气焊、手工电弧焊及气体保护焊焊缝坡口的基本形式和尺寸》的要求选用;3、将裂纹两侧及端部金属预热至100℃~150℃,并在焊接过程当中保持此温度;4、采用与母材相婚配的低氢型焊条或超低氢型焊条施焊;钢结构5、尽可能用小直径焊条以分层逆向焊施焊,每一焊道焊完后宜立即锤击;6、按设计和《钢结构工程施工及验收规范》的要求验收焊缝质量;7、对承受动力荷载的构件,焊补后其表面应磨光,使之与原构件表面齐平,磨削痕迹线应大体与裂纹切线方向垂直;8、对重要结构或厚板构件,焊补后应立即进行退火处理。
裂纹的嵌板法修复合用于网状、分叉裂纹区和有破碎、过烧或烧穿等缺点的梁、柱腹板部位裂纹。
1、检查肯定缺点的范围;2、将缺陷部位切除,宜切成带圆角的矩形孔、切除部分的尺寸均应比缺陷范围的尺寸大100mm;3、用等厚度同材质的嵌板嵌入切除部位,嵌入板的长宽边缘与切除孔间二个边应留有2~4mm的间隙,并将其边缘加工成对接焊缝要求的坡口形式;4、嵌板定位后,将孔口四角区域预热至100~150℃,按顺序采用分段分层逆向焊法施焊;5、检查焊缝质量,打磨焊缝余高,使之与原构件表面XXX。
裂纹返修工艺

焊缝及母材裂纹的修补工艺1、必须用酸蚀、磁粉检查、着色渗透检查或其它可靠的方法确定裂纹的范围。
2、对待修补焊接处进行预热,预热温度如表1。
3、达到预热到规定温度后,立即用碳弧气刨去除裂纹,和超出裂纹两端各延长50mm。
4、严禁用氧-乙炔方法刨槽。
5、对于裂纹,必须用MT或PT方法检查,以确定裂纹部分已被彻底去除;6、对待修补焊接处及邻近母材清洁,除去油污,铁锈,氧化铁及MT或PT的粘附物质。
7、对待修补焊接处进行预热,最低预热温度和层间温度如表1所示:8或GMAW方法进行焊接,焊接规范参数等要求见WPS。
9、对修补焊接的质量必须经UT或RT,有时也需用MT或PT作为辅助的检查手段,以确定已无不合格缺陷。
10、修补焊接的焊缝应与母材或焊缝表面齐平,否则应用机械打磨的方法使之齐平。
11、焊缝的修补焊接应在无荷载(包括构件重量)状态下进行。
这一状态应延续至焊缝经必要的NDT(UT、MT等)检测并合格为止。
Cracks In Base Metal And Weld Repair Process1、The extent of the crack shall be ascertained by use of acid etching,MT,PT,or other equally positive means.2、Repair welding Department preheat treatment, the preheating temperature astab.1.3、Preheat temperature up to the required temperature,Immediately,remove crackusing carbon arc gas.and the crack and sound metal 50mm beyond each end of the crack shall be removed.4、Prohibited use of oxy - acetylene method plow groove.5、Crack, or PT MT method must be inspected to ensure that some cracks have been completely removed;6、Repair welding near the base metal cleaning, removing oil, rust, iron oxide andMT or PT adhesive material.7、Welding Department to prepare for preheating,preheat temperature andinterpass temperature, as shown in table 1 :using SMAW、FCAW or GMAW welding methods.9、The quality of repair welding must be verified by the UT or RT, MT, or PTsometimes required as a supplementary means of inspection. To identifydefects have been removed.10、Repair welding of metal or weld seam with the Chi-ping, Otherwise, themethod of mechanical polishing so Chi-ping .11、Weld repair should be under no load condition (including components weight).The state should continue to weld on the necessary NDT (UT, MT) and passthe testing.。
焊缝出现裂纹处理方法

焊缝出现裂纹处理方法焊接是一种常见的金属连接方式,但难免会出现一些问题。
焊缝出现裂纹是其中一种比较常见的问题。
这会导致焊接强度下降,甚至会影响工件的正常运行和使用寿命。
本文将介绍焊缝出现裂纹的处理方法。
1.预防裂纹的出现首先要做的是预防裂纹的出现。
预防措施包括:(1).选用合适的焊接材料。
应选择符合工件物理性能和化学成分的焊接材料,以确保焊接质量。
(2).确保焊接区域的表面清洁。
在焊接前,应将焊接区域的表面清洁干净,以便进行完美的焊接。
(3).恰当的焊接电流和电压。
应根据焊接材料的性质,在可接受的范围内选择适当的焊接电流和电压。
(4).保持适当的焊接速度。
应保持恰当的焊接速度和焊接温度,以确保焊接均匀和充分。
2.焊缝出现裂纹的处理(1).退火处理。
如果焊缝出现裂纹,可能是焊接后材料产生了内部应力。
应该对焊接件进行退火处理,以消除这些应力。
在退火处理过程中,需要将焊接件放置在还原气体中,加热到一定温度,然后缓慢冷却。
(2).机械加工。
可以通过机械加工把焊缝重新磨平或是用铣床将焊缝变成V形溝后重新焊接,以消除因为焊接引起的问题。
(3).重做焊缝。
如果焊缝的裂纹严重并且处理措施无效,则需要重新焊接。
重新焊接时应使用正确的焊接材料以及合适的焊接参数,以确保焊接质量。
(4).使用补丁或补焊。
对于一些小型的裂缝,可以使用补丁或补焊来修复。
选择合适的补丁或补焊材料,并根据需要进行特定的操作。
以保持金属之间的连续性,从而让修补后的焊缝拥有相同的机械性能和表面光洁度。
3.总结通过以上几种方法,我们可以有效地处理焊缝出现裂纹这一常见问题。
在焊接过程中,我们应遵循正确的焊接流程,并严格控制焊接参数,以保证工件的质量和性能。
对于裂纹的出现,我们要及时采取相应的措施,以避免影响工件的正常使用。
工程机械裂缝焊接修复方案

工程机械裂缝焊接修复方案一、前言工程机械在长时间使用过程中,由于各种原因可能会出现裂缝现象,这些裂缝的存在不仅影响了机械的使用寿命,也可能带来安全隐患,因此及时修复裂缝显得尤为重要。
在裂缝修复中,焊接是一种常见的修复方式,通过对裂缝进行焊接处理可以有效地恢复机械的强度和密封性。
本文将针对工程机械裂缝的焊接修复进行详细讨论,包括裂缝类型、裂缝焊接材料、焊接工艺和注意事项等方面,希望可以为相关人员提供参考。
二、裂缝类型工程机械裂缝可以分为表面裂缝和内部裂缝两种类型。
1. 表面裂缝:表面裂缝是指裂缝完全暴露在外部的裂缝,通常是由外部冲击或者机械应力等原因造成的,裂缝的位置和形态相对容易观察和诊断。
2. 内部裂缝:内部裂缝是指裂缝位于机械内部的裂缝,通常是由于疲劳、焊接质量、材料缺陷等原因导致的,裂缝的位置和形态相对难以观察和诊断。
根据裂缝的类型进行分类,对于不同类型的裂缝需要采取不同的焊接修复方案。
三、裂缝焊接材料裂缝焊接材料的选择对修复效果至关重要,常见的裂缝焊接材料包括焊条、焊丝、焊剂等,针对不同的裂缝类型和材料特性可以选择不同的焊接材料。
1. 焊条:焊条是一种焊接材料,主要用于电弧焊和其他热焊接方法,焊条的种类繁多,包括低合金焊条、中合金焊条、高合金焊条等,可以根据裂缝的类型和机械材料的特性选择合适的焊条进行修复。
2. 焊丝:焊丝是一种焊接材料,主要用于气体保护焊、电弧焊等焊接方法,焊丝的种类也非常丰富,包括氩弧焊丝、镍基焊丝、铁素体不锈钢焊丝等,可以根据具体情况选择适合的焊丝进行修复。
3. 焊剂:焊剂是一种辅助焊接材料,用于提高焊接质量和效率,常见的焊剂包括焊剂粉末、液体焊剂等,可以在焊接过程中提供保护和辅助作用。
以上所提到的焊接材料都需在选择时考虑到材料的强度、耐磨性、抗腐蚀性等特性,以及与被修复材料之间的兼容性。
四、焊接工艺1. 准备工作:在进行裂缝修复焊接前,需要对机械进行彻底的清洁和准备工作,包括清理裂缝周围的杂质和油污,确保焊接区域干净并去除氧化物。
高压管道焊口母材裂纹处理流程
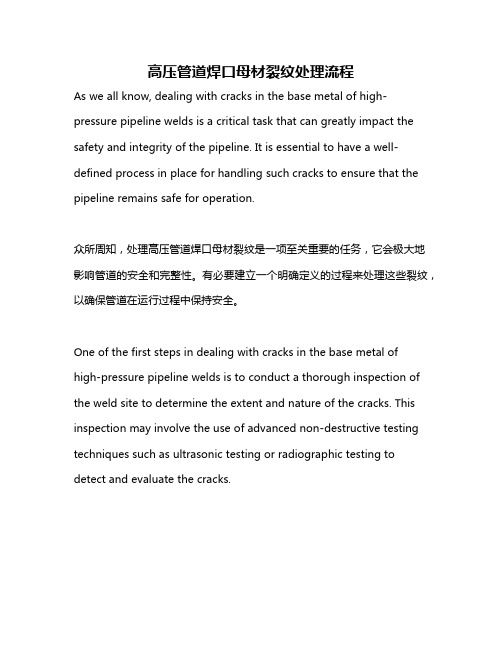
高压管道焊口母材裂纹处理流程As we all know, dealing with cracks in the base metal of high-pressure pipeline welds is a critical task that can greatly impact the safety and integrity of the pipeline. It is essential to have a well-defined process in place for handling such cracks to ensure that the pipeline remains safe for operation.众所周知,处理高压管道焊口母材裂纹是一项至关重要的任务,它会极大地影响管道的安全和完整性。
有必要建立一个明确定义的过程来处理这些裂纹,以确保管道在运行过程中保持安全。
One of the first steps in dealing with cracks in the base metal ofhigh-pressure pipeline welds is to conduct a thorough inspection of the weld site to determine the extent and nature of the cracks. This inspection may involve the use of advanced non-destructive testing techniques such as ultrasonic testing or radiographic testing to detect and evaluate the cracks.处理高压管道焊接基材裂纹的第一步是对焊接现场进行彻底检查,以确定裂纹的程度和性质。
焊接热裂纹气孔缺陷成因及解决方法

焊接热裂纹气孔缺陷成因及解决方法焊接热裂纹和气孔缺陷是焊接过程中常见的质量问题,其成因和解决方法如下所述:焊接热裂纹的成因:1. 金属材料的热裂敏感性:某些金属材料在焊接过程中易产生热裂纹,例如低合金钢、不锈钢等。
2. 焊接残余应力:焊接过程中产生的残余应力超过材料的承受能力,导致热裂纹的产生。
3. 高温区热处理:焊接过程中,高温区域的快速冷却和热应力可以引起热裂纹。
焊接热裂纹的解决方法:1. 选择适当的焊接材料:对于易产生热裂纹的材料,应选择抗裂纹性好的焊接材料。
2. 控制焊接热输入:通过控制焊接参数,如预热温度、焊接速度等,控制焊接热输入,减少热裂纹的产生。
3. 采用合理的焊接顺序:合理的焊接顺序可以减小残余应力,降低热裂纹的风险。
4. 进行后热处理:合适的后热处理可以减小残余应力,降低热裂纹的产生。
气孔缺陷的成因:1. 气体溶解度:焊接过程中,溶解在焊池中的气体(如氮气、氧气等)在加热过程中难以消除,形成气孔。
2. 气体污染:焊接材料表面或环境中存在杂质或油污等物质,会导致气体释放,形成气孔。
3. 不稳定的焊接电弧:不稳定的电弧容易引入空气,形成气孔。
气孔缺陷的解决方法:1. 提高焊接材料的清洁度:在焊接前应确保焊接材料表面干净,避免油污和杂质的存在。
2. 使用合适的保护气体:在焊接过程中使用合适的保护气体,如纯氩气或二氧化碳气体,以减少气体溶解度。
3. 控制焊接电弧的稳定性:通过调整焊接电流和电弧稳定器等,保持焊接电弧的稳定性,减少气孔的产生。
4. 加大气孔检测力度:使用超声波扫描、X射线检测等方法对焊接接头进行检测,及时发现并修复气孔缺陷。
5. 选择适当的焊接工艺和焊接参数,以提高焊接质量。
裂纹维修方法

金属结裂纹维修的方法及其止裂金属结构裂纹维修的方法及其止裂原理分析摘要:目前,金属结构均面临着普遍的疲劳问题以及产生疲劳裂纹带来的维修问题。
阐述了金属疲劳损伤问题产生的机理,提出可能的维修方法及其优缺点,为金属结构的的设计与维修提供依据。
关键词:疲劳损伤裂纹维修前言起重机金属结构常见的故障有裂纹、变形、严重锈蚀、刚度不够等。
其中裂纹是门机最为常见的故障,占金属机构故障的80%以上。
虽然金属结构的设计都符合常规设计的强度要求,但往往还是不可避免有裂纹产生。
这是因为材料内部总难免在夹渣、气孔,加工的过程中可能有毛刺、划伤,焊接过程中存在未焊透等。
在变应力的作用下,存在缺陷的部位或者应力最大部位往往最先出现疲劳裂纹,随着应力循环次数的增加,裂纹缓慢扩展直至达到临界尺寸而破坏。
工程断裂力学认为,裂纹体存在一个临界裂纹长度ac。
当存在的裂纹长度a<ac时,表示该裂纹体可以继续使用,如果a≥ac,表示该裂纹体不可使用。
ac 是可通过材料的断裂韧性常数KIC和材料应力场的分布数据求得在计算ac时,可近似的采用σmin=0,即不吊重时,构件裂纹处的应力为0。
这样计算值ac小于实际值,同时也有利于作出更安全的判断。
σmax可通过应力测量测出或者有限元法算出,f表示修正系数。
断裂力学的判断标准是在能量平衡理论中称为裂纹扩展阻力GIC的断裂韧性,它是材料固有的力学性能,表示裂纹体抵抗断裂的能力。
当裂纹的推动力G1达到裂纹的扩展阻力的时候,裂纹就会扩展。
推力曲线与阻力曲线的关系见图1。
图1 推动力与阻力曲线示意图从图1中可以看出,裂纹扩展阻力GIC随着裂纹推动力G1增大而增大。
当推动力G1<G″1,裂纹是不会扩展的。
当推动力增长到G1=G″1,裂纹扩展了Δa后,GIC的增长速度快于G1增长的速度,裂纹就会停止扩展。
当推动力增长到G1,时,裂纹长度增长了Δa″时,裂纹推动力增长的速度将始终大于裂纹阻力的增长速度,裂纹体就会失稳继续扩展下去,直至断裂。
焊 缝裂纹缺陷 返 修 方 案
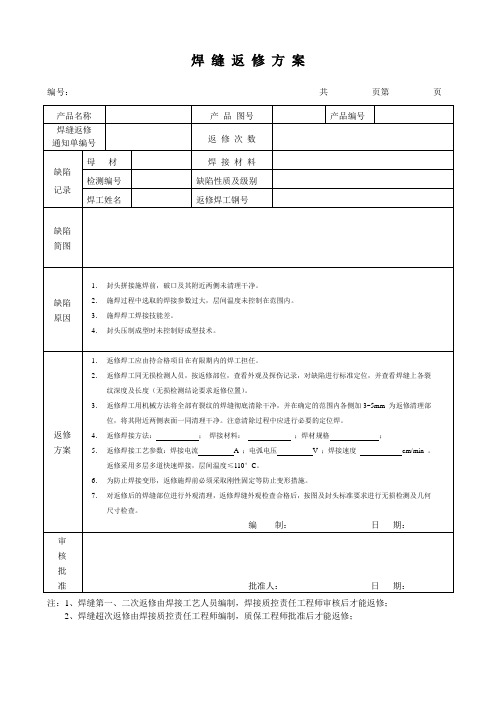
审
核批Biblioteka 准批准人:日期:注:1、焊缝第一、二次返修由焊接工艺人员编制,焊接质控责任工程师审核后才能返修;
2、焊缝超次返修由焊接质控责任工程师编制,质保工程师批准后才能返修;
焊缝返修记录
编号:
返修通知单编号
返修方案编号
母材牌号
板厚(规格)
补焊材料
缺陷消除方法
焊工钢印号
焊工姓名
焊缝返修工艺说明:
焊缝返修记录:
焊接层次
电流种类与极性
焊条(丝)直径(mm)
焊接电流
(A)
电弧电压
(V)
焊接速度
(m/h)
备注
检查结果
检验员:日期:
焊缝返修方案
编号:共页第页
产品名称
产品图号
产品编号
焊缝返修
通知单编号
返修次数
缺陷
记录
母材
焊接材料
检测编号
缺陷性质及级别
焊工姓名
返修焊工钢号
缺陷
简图
缺陷
原因
1.封头拼接施焊前,破口及其附近两侧未清理干净。
2.施焊过程中选取的焊接参数过大,层间温度未控制在范围内。
3.施焊焊工焊接技能差。
4.封头压制成型时未控制好成型技术。
返修
方案
1.返修焊工应由持合格项目在有限期内的焊工担任。
2.返修焊工同无损检测人员,按返修部位,查看外观及探伤记录,对缺陷进行标准定位,并查看焊缝上各裂纹深度及长度(无损检测结论要求返修位置)。
3.返修焊工用机械方法将全部有裂纹的焊缝彻底清除干净,并在确定的范围内各侧加3~5mm为返修清理部位,将其附近两侧表面一同清理干净。注意清除过程中应进行必要的定位焊。
ASME CODE CASE 2115-1与 HK40焊接裂纹及修复

ASME CODE CASE 2115-1与 HK40焊接裂纹及修复ASME CODE CASE 2115-1 与HK40异种钢焊接裂纹的产生及消除内容提要:2021年笔者在监造某CFB(循环流化床)锅炉项目的过程中,发现末级过热器CODE CASE2115-1蛇型管排与HK40搭扣焊接角焊缝出现了穿透性裂纹,进一步PT(着色)检查后发现多数焊道表面存在裂纹,采用更严格的工艺也无法解决,经过与厂家一道进行分析,修改了焊接工艺,采用了合格的原材料,对焊件全面返修,消除了焊接裂纹,避免了不合格产品出厂。
1.情况简介2021年笔者在某锅炉厂监造一台超高压循环流化床锅炉。
其中的三级和末级过热器蛇型管排由日本住友开发的新型奥氏体不锈耐热钢无缝钢管(材料为ASME标准 CODE CASE 2115-1,φ44.8×7.5)与铸造奥氏体不锈钢搭扣(HK40,δ=10mm)之间进行角焊缝焊接。
焊接方法为焊条电弧焊,焊材为美国进口的E310-16焊条,焊材经过验收合格;焊接工艺评定已经合格,并且得到客户批准。
焊工为经过ASME标准考试合格的焊工,母材为客户方面提供,并且提供了材质合格证。
在焊接过程中经常在包角处出现收弧裂纹,厂家在对裂纹进行打磨、补焊后,又着色检验,确认返修合格之后按照正常程序进行了稳定化热处理。
在稳定化热处理之后按照程序对该蛇型管排的搭扣焊缝进行了100%PT着色检验,结果又发现了多处表面裂纹,均为纵向裂纹,主要分布于包角部位及收弧部位。
厂家对裂纹进行了打磨清理后进行了补焊,至此完成了该蛇型管排的焊接工作,开始将管排安装至过热器模块。
1.1发现问题:该厂某QC检查人员于日常检查中发现堆放的蛇型管排中有一个搭扣已经发生通贯性裂纹,见图片(一)。
裂纹端部位于角焊缝热影响区图一、搭扣角焊缝出现裂纹厂家把此问题作为不合格项进行处理,最后意见是切除这个发生裂纹的搭扣,更换一个新搭扣,焊接之后再重新进行稳定化处理。
- 1、下载文档前请自行甄别文档内容的完整性,平台不提供额外的编辑、内容补充、找答案等附加服务。
- 2、"仅部分预览"的文档,不可在线预览部分如存在完整性等问题,可反馈申请退款(可完整预览的文档不适用该条件!)。
- 3、如文档侵犯您的权益,请联系客服反馈,我们会尽快为您处理(人工客服工作时间:9:00-18:30)。
ASME CODE CASE 2115-1 与HK40异种钢焊接裂纹的产生及消除内容提要:2006年笔者在监造某CFB(循环流化床)锅炉项目的过程中,发现末级过热器CODE CASE2115-1蛇型管排与HK40搭扣焊接角焊缝出现了穿透性裂纹,进一步PT(着色)检查后发现多数焊道表面存在裂纹,采用更严格的工艺也无法解决,经过与厂家一道进行分析,修改了焊接工艺,采用了合格的原材料,对焊件全面返修,消除了焊接裂纹,避免了不合格产品出厂。
1.情况简介2006年笔者在某锅炉厂监造一台超高压循环流化床锅炉。
其中的三级和末级过热器蛇型管排由日本住友开发的新型奥氏体不锈耐热钢无缝钢管(材料为ASME标准CODE CASE 2115-1,φ44.8×7.5)与铸造奥氏体不锈钢搭扣(HK40,δ=10mm)之间进行角焊缝焊接。
焊接方法为焊条电弧焊,焊材为美国进口的E310-16焊条,焊材经过验收合格;焊接工艺评定已经合格,并且得到客户批准。
焊工为经过ASME标准考试合格的焊工,母材为客户方面提供,并且提供了材质合格证。
在焊接过程中经常在包角处出现收弧裂纹,厂家在对裂纹进行打磨、补焊后,又着色检验,确认返修合格之后按照正常程序进行了稳定化热处理。
在稳定化热处理之后按照程序对该蛇型管排的搭扣焊缝进行了100%PT着色检验,结果又发现了多处表面裂纹,均为纵向裂纹,主要分布于包角部位及收弧部位。
厂家对裂纹进行了打磨清理后进行了补焊,至此完成了该蛇型管排的焊接工作,开始将管排安装至过热器模块。
1.1发现问题:该厂某QC检查人员于日常检查中发现堆放的蛇型管排中有一个搭扣已经发生通贯性裂纹,见图片(一)。
裂纹端部位于角焊缝热影响区图一、搭扣角焊缝出现裂纹厂家把此问题作为不合格项进行处理,最后意见是切除这个发生裂纹的搭扣,更换一个新搭扣,焊接之后再重新进行稳定化处理。
考虑到该搭扣的裂纹端部位于位于角焊缝的热影响区,笔者提出应该检查其余的搭扣焊缝,增加检测的比例。
在增加的15片管排进行着色检验之后,其中14片发现裂纹(纵向)。
因此厂家100%检查所有管排上搭扣的焊缝,结果发现几乎每一片蛇型管排上的搭扣角焊缝均有裂纹发生。
1.2 多次返修并查找裂纹产生的原因1.2.1 该厂返修工艺简述如下:打磨去除所有的裂纹,打磨裂纹之后焊缝形状平滑过渡的区域不需要修补,其余部分进行补焊(补焊工艺与原工艺相同)。
在补焊完又进行100%着色检验,合格之后进行1100℃-1150℃温度下“热矫正”释放应力。
最后再次100%着色检查热矫正区域。
为了保证返修质量,厂家对返修焊工进行了专门有针对性的培训,要求特别注意起弧、收弧处的技术,增加收弧处的焊肉厚度,和采用小线能量、小摆动、快焊速、每一层的焊缝接头错开、严格控制层间温度小于100℃等细节。
1.2.2 做试验检验裂纹并复验焊材将3片管排有裂纹的地方进行打磨,不做返修,在100%着色检验之后,等待24小时之后再次进行着色检验,结果再次发现裂纹。
另外厂家对使用的E310-16焊材进行了复验,结果表明焊接材料合格。
1.2.3 返修中发现裂纹,厂家更换返修工艺由于厂家在返修过程中,使用E310-16焊条进行返修焊接,发现依然有裂纹产生,所以决定改为使用抗裂性良好的镍基焊材(焊条ENiCrFe-2或焊丝ERNiCr-3)进行补焊,相应的焊接工艺评定也已经得到客户方面的确认。
1.2.4 返修后再次抽查又发现裂纹根据2.2的实验结果,笔者怀疑有裂纹扩展到表面的可能性,再次对返修完毕经100%PT 着色检验合格,且放置48小时以上的蛇型管排再次进行PT着色检验。
检验结果显示,很多搭扣角焊缝仍然纵向裂纹,个别搭扣表面出现裂纹,仅一次抽查3排最多发现38处搭扣角焊缝裂纹,至此返修失败。
裂纹见图二、图三:图二返修后放置48小时后出现的裂纹裂纹最大长度15mm,焊道中央,方向均纵向。
图三返修后放置48小时后出现的裂纹2.对相关材料的介绍和裂纹产生原因的分析2.1 CODE CASE 2115-1无缝钢管和HK40搭扣以及焊材化学成分及力学性能简介2.1.1 CODE CASE 2115-1无缝钢管成分及力学性能该材料为奥氏体不锈钢无缝管(25Cr-20Ni-Cb-N),为日本住友开发,牌号“HR3C”,并以“TP310HCbN”级别号列入2001版“SA-213/SA213M标准”。
化学成分见表一:力学性能见表二:表一:CODE CASE 2115-1无缝钢管化学成分2.1.2 HK40搭扣化学成分及力学性能该材料为美国ASTM标准中A351/A351M的奥氏体不锈钢铸造件,化学成分见表三:力学性能见表四:表三:HK40搭扣化学成分2.1.3 焊条E310-16化学成分及力学性能焊条E310-16是符合A WS A5.4标准的奥氏体不锈钢焊条,未经稀释的焊缝金属化学成分要求见表五,力学性能见表六:表五:焊条E310-16化学成分2.1.4 焊丝ER NiCr-3化学成分及力学性能焊丝ER NiCr-3是符合A WS A5.14/A5.14M标准的镍基焊丝,其化学成分见表七,力学性能见表八:表七焊丝ER NiCr-3化学成分表八:焊丝ER NiCr-3未经稀释的焊缝金属力学性能2.1.5.焊条E NiCrFe-2化学成分及力学性能焊条E NiCrFe-2是符合A WS A5.11标准的镍基焊条,未经稀释的焊缝金属化学成分见表九,力学性能见表十:表十:焊条E NiCrFe-2未经稀释的焊缝金属力学性能2.2 对裂纹成因的分析对裂纹成因分析从以下三个角度进行,一为对两种母材分析,二为对焊材分析,三为对裂纹形态分析,四、进一步分析2.2.1对母材的分析2.2.1.1 25-20型不锈钢的特性CODE CASE 2115-1 和HK40 合金成分中Cr、Ni含量上看属于25-20型的典型锅炉用耐热钢,金相组织为单一奥氏体,它无磁性,具有高的热强性和优良的耐腐蚀性,焊接的主要问题是它们具有较强的热裂纹倾向。
有资料显示热裂纹常常起源于焊接缺陷,在单一奥氏体不锈钢焊接中如果不能有效避免焊接缺陷,即使焊后对这些缺陷进行修补也不能消除微裂纹,甚至可能会引起新的热裂纹。
但是奥氏体不锈钢焊接性优于其它不锈钢,在任何温度都不会发现相变,而且对氢脆不敏感,在焊态下奥氏体不锈钢接头也有较好的塑性和韧性,延迟裂纹通常不会产生。
2.2.1.2 其他元素的影响CODE CASE 2115-1钢中添加的微量元素Nb,可以使碳化物稳定,增加热强性,对低熔点相形成的影响也很重要,容易在焊缝金属和热影响区中引起裂纹,来自国外的资料说“大量经验数据表明全奥氏体焊缝,铌对热裂纹有不利影响”。
HK40为奥氏体不锈钢铸件的含碳量较高(0.35-0.45)目的是保证浇铸时铁水有足够的流动性,显然不利于焊接,作为铸件要保持足够的流动性,但是随着含碳量的增高,可焊性变差。
但是作为奥氏体不锈钢,在正常条件下焊接应该不会产生延迟裂纹。
2.2.3 结论:考虑到焊缝为单一奥氏体,以及CODE CASE 2115-1钢中添加的合金元素铌对热裂纹有不利影响,并且铸件中含碳量较高,判断该组合的焊缝热裂倾向较高。
2.2.2 对焊接材料分析2.2.2.1.25-20型奥氏体焊接材料对于本项目中CODE CASE 2115-1无缝钢管与HK40搭扣之间的角焊缝不是受压件焊缝,厂家对该材料进行焊接工艺评定时做了宏观金相实验,用来支持角焊缝的焊接工作,厂家最初使用的E310-16焊条焊接材料,焊道熔敷金属属于单一奥氏体,根据2.2节的分析,不利于控制热裂纹。
并且E310-16,其高温性能不及CODE CASE 2115-1,因为后者是25-20型奥氏体不锈钢的改进型新钢种,后者的专用焊材为日本住友公司开发的HR3C,E310-16焊道熔敷金属属于单一奥氏体不锈钢,其成分中没有针对性解决25-20型奥氏体不锈钢添加的微量元素Nb 和碳之后热裂性增强的问题。
结论:E310-16焊条不适合焊接CODE CASE 2115-1与HK40之间的焊缝,虽然符合ASME 规范的要求, 但是实践证明, 仅仅符合规范还是不够的,因为使用该焊材实践中无法解决热裂纹多发的问题。
2.2.2.2 镍基焊接材料ASME CODE CASE中明确规定,对于CODE CASE 2115-1无缝钢管材料的受压件对接环缝,必须使用ENiCrFe-2或者ERNiCr-3来焊接。
ASME规范中并未强制使用镍基焊接材料进行非受压件的角焊缝焊接,但是从本事件的热裂纹多发来分析,使用镍基焊接材料有以下两种好处:-避免得到单一奥氏体焊缝;-镍基焊接材料的熔敷金属具有更好的抗裂性。
结论:采用镍基焊材进行焊接CODE CASE 2115-1与HK40之间的角焊缝更适合。
2.2.3 从裂纹形态分析2.2.3.1针对现场出现的裂纹自始至终均为纵向来看,尤其是焊接后立即会出现的少量纵向裂纹,据此可以判断现场发现的裂纹应该属于热裂纹;2.2.3.2由于现场的裂纹均是在着色检验合格之后出现的,说明裂纹存在扩展现象。
根据2.2.1.1的分析,该表面裂纹有可能是焊工操作不当造成焊接缺陷并进一步引发热裂纹。
. 2.2.3.4 从裂纹出现数量很多来判断,还有可能是实际材料的化学成分方面出现问题造成微裂纹在低应力下扩展或者在焊接返修之后扩展.。
.2.2.4 进一步分析厂家决定对所有使用的母材及焊材进行化学成分复验,结果表明其它材料均合格,搭扣的成分严重超标。
见表十二表十二:HK40 搭扣成分化验结果一例:塑性和韧性,并且在焊接冶金过程中进入熔池导致焊道中尤其是热影响区中含碳量超过正常数值,使焊缝及热影响区塑性和韧性大幅度下降,从而使焊缝在低应力状况下发生裂纹扩展。
3.提出解决方案并实施通过以上分析,制定解决方案从三个方面进行:3.1 解决搭扣材料不合格:切除所有HK40搭扣,并更换全部搭扣。
3.2提高焊缝金属的抗裂性:改用镍基焊材(ER NiCr-3)进行焊接。
3.3 避免焊接缺陷的产生,减少引发热裂纹的因素:3.3.1 选择熟练的焊工并进行严格的专门培训,要求特别注意起弧、收弧处避免裂纹的技术,小热输入、小电流、快焊速、每一层的焊缝接头错开、严格控制层间温度小于100℃等措施。
3.3.2 规定重新焊接HK40搭扣使用钨极氩弧焊工艺进行焊接,因为使用钨极氩弧焊比使用焊条电弧焊更容易获得优质接头。
厂家对第二批重新更换的搭扣母材进行了化学成分的分析,结果表明搭扣的成分符合规范要求。
接着厂家按照制定的解决方案焊接完毕,进行了100%PT着色检验,结果合格。
然后按照最初的程序在焊接之后进行稳定化热处理,热处理之后,对搭扣焊缝再次进行100%PT着色检验,未发现裂纹。