硫化工艺1
第13章 硫化工艺
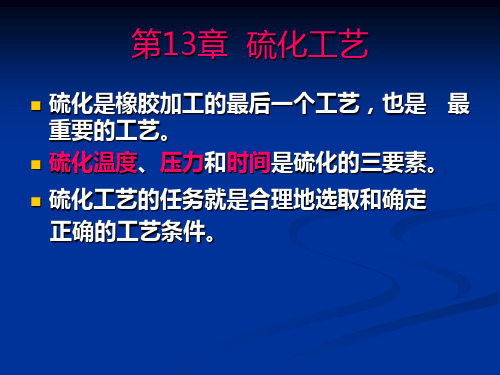
2、了解常用硫化介质及特点
3、了解热硫化方法
4、掌握硫化条件的选取和确定
§13.1 正硫化及其测定方法
一.正硫化及正硫化时间
二.正硫化的测定方法
(一)物理-化学法 (二)物理性能测定法 (三)专用仪器法
一.正硫化及正硫化时间
正硫化:又称最宜硫化,指橡胶的主要性能达到 或接近最佳值的硫化状态。 正硫化时间:橡胶达到正硫化状态所需要的时间。 正硫化是一个范围,而不是一个点。 理论正硫化时间:扭矩最高点对应的时间; 工艺正硫化时间:扭矩达到M90对应的时间; 工程正硫化时间:生产上主要的性能指标达到最 佳值所需要的正硫化时间。对薄的橡胶制品(厚 度少于6mm),工程正硫化时间等于由硫化仪测 得的工艺正硫化时间,而厚度大于6mm时,胶料 的导热性差及骨架材料的复杂性使硫化时间的确 定变得复杂,一般取最小和最大硫化效应的时间 范围作为工程正硫化时间.
4T 4T + 2S +M H+ H + 2S ++ M
8
二.正硫化的测定方法
门尼值
(三)专用仪器法
门尼粘度计法:早期使用的 仪器。取T5为门尼焦烧时间, T35 为门尼硫化时间,则正硫 化时间为:
正硫化时间=T5+10(T35-T5)
转矩
△30 T5
△5
T35 硫化时间
硫化仪法 适用于薄制品
第13章 硫化工艺
硫化是橡胶加工的最后一个工艺,也是 最重要的工艺。 硫化温度、压力和时间是硫化的三要素。 硫化工艺的任务就是合理地选取和确定 正确的工艺条件。
一、本章主要内容
(一)正硫化及预测方法. (二)硫化条件的选取和确定. (三)硫化介质 (四)硫化方法
硫化工艺过程控制

硫化工艺过程控制1. 硫化工艺概述硫化是一种常见的化学工艺,用于制造硫化橡胶、硫化塑料等材料。
硫化过程控制是确保硫化反应达到所需质量和性能的关键因素。
本文将介绍硫化工艺的基本原理和常见的过程控制方法。
2. 硫化反应的原理硫化反应是将天然橡胶或合成橡胶中的不饱和键与硫化剂发生反应,形成交联结构的过程。
硫化剂在反应中起着催化剂的作用,加速反应速度。
硫化反应过程中主要涉及以下几个方面的控制:•反应温度:反应温度不同会导致反应速度和交联结构的形成不同。
•反应时间:反应时间决定了反应程度和硫化物的生成。
•硫化剂浓度:硫化剂浓度的调控可以控制反应速度和交联密度。
3. 硫化工艺的过程控制方法3.1 温度控制硫化反应温度是影响硫化速率和硫化物结构的重要因素。
温度过低会导致反应速度慢,交联结构不完全;温度过高会导致反应过度,交联结构过强。
要控制硫化反应温度,可以采用以下方法:•传统控制方法:传统控制方法是通过控制加热器的功率或控制炉内的加热介质温度来实现温度控制。
•PID控制方法:PID控制方法是通过传感器测量温度,根据反馈信号进行控制,使温度稳定在设定值附近。
3.2 时间控制硫化反应时间是控制硫化程度的重要因素。
过长的反应时间会导致硫化过度,而过短的反应时间会导致交联结构不完全。
要控制硫化反应时间,可以采用以下方法:•手动控制方法:通过观察反应过程中硫化物的形成情况来控制硫化反应时间。
•自动控制方法:使用计时器或自动控制系统来控制硫化反应时间。
3.3 硫化剂浓度控制硫化剂浓度是影响硫化反应速度和交联结构的重要因素。
浓度过高会导致反应速度过快,交联结构过强;浓度过低会导致反应速度慢,交联结构不完全。
要控制硫化剂浓度,可以采用以下方法:•手动控制方法:通过调整硫化剂的投入量来控制硫化剂浓度。
•自动控制方法:使用流量控制器和比例控制器来控制硫化剂的投入量,从而实现硫化剂浓度的控制。
4. 硫化工艺的优化为了提高硫化工艺的效率和产品质量,可以采取以下优化措施:•优化硫化剂选择:选择适合特定反应条件的硫化剂,可以提高反应速率和交联结构的形成。
硫化工艺
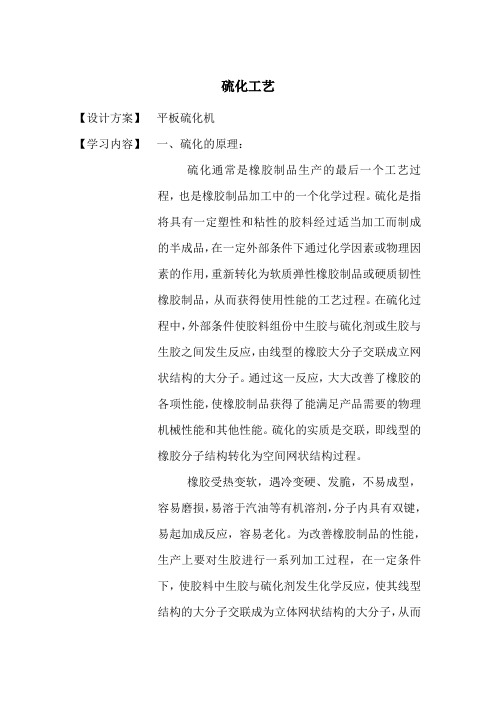
硫化工艺【设计方案】平板硫化机【学习内容】一、硫化的原理:硫化通常是橡胶制品生产的最后一个工艺过程,也是橡胶制品加工中的一个化学过程。
硫化是指将具有一定塑性和粘性的胶料经过适当加工而制成的半成品,在一定外部条件下通过化学因素或物理因素的作用,重新转化为软质弹性橡胶制品或硬质韧性橡胶制品,从而获得使用性能的工艺过程。
在硫化过程中,外部条件使胶料组份中生胶与硫化剂或生胶与生胶之间发生反应,由线型的橡胶大分子交联成立网状结构的大分子。
通过这一反应,大大改善了橡胶的各项性能,使橡胶制品获得了能满足产品需要的物理机械性能和其他性能。
硫化的实质是交联,即线型的橡胶分子结构转化为空间网状结构过程。
橡胶受热变软,遇冷变硬、发脆,不易成型,容易磨损,易溶于汽油等有机溶剂,分子内具有双键,易起加成反应,容易老化。
为改善橡胶制品的性能,生产上要对生胶进行一系列加工过程,在一定条件下,使胶料中生胶与硫化剂发生化学反应,使其线型结构的大分子交联成为立体网状结构的大分子,从而使胶料具备高强度、高弹性、抗腐蚀等优良性能。
二、硫化的方法1、温室硫化法温室硫化法用于需求在室温及不加压的条件下进行硫化的场合。
室温硫化通常将硫化剂与溶剂、惰性配合剂等配成一个组份,橡胶、树脂等与其他配合剂配成另一组分,使用是进行混合。
2、冷硫化法把制成品浸入2%-5%的一氯化硫的溶液中,时间从几秒到几分钟不等。
3、热硫化法⑴、间歇式硫化①、热水槽硫化法此法为直接常压硫化法,把需要硫化的产品浸于热水或盐水,适于乳胶薄膜制品的硫化。
②、烘房、烘箱热空气硫化法此法也为直接常压硫化法,该方法有两种方式,一是把半成品放在加热室中加热硫化;另一种是烘箱硫化,适用于某些特种橡胶制品的二次硫化。
③、硫化罐硫化硫化罐硫化工艺借助飞的硫化设备为硫化罐。
根据硫化介质的不同,硫化罐硫化工艺又有如下几种主要硫化方法:A、直接饱和蒸汽硫化法a、开放式硫化法b、包层硫化法c、埋粉硫化法d、模型硫化法B、热空气硫化法C、热空气-蒸汽混合硫化法⑵、外加压式硫化工艺①、平板硫化机模压硫化法采用这种方法可同时进行胶料在模具型腔内加压流动成型和胶料在硫化温度及硫化压力下发生硫化反应这两个过程。
橡胶硫化工艺流程
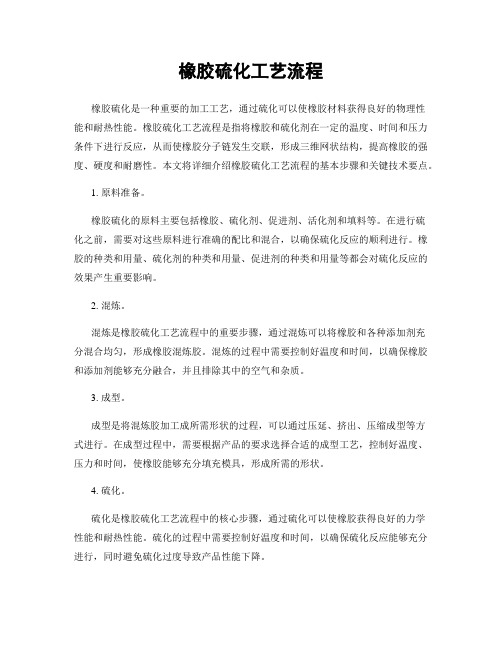
橡胶硫化工艺流程橡胶硫化是一种重要的加工工艺,通过硫化可以使橡胶材料获得良好的物理性能和耐热性能。
橡胶硫化工艺流程是指将橡胶和硫化剂在一定的温度、时间和压力条件下进行反应,从而使橡胶分子链发生交联,形成三维网状结构,提高橡胶的强度、硬度和耐磨性。
本文将详细介绍橡胶硫化工艺流程的基本步骤和关键技术要点。
1. 原料准备。
橡胶硫化的原料主要包括橡胶、硫化剂、促进剂、活化剂和填料等。
在进行硫化之前,需要对这些原料进行准确的配比和混合,以确保硫化反应的顺利进行。
橡胶的种类和用量、硫化剂的种类和用量、促进剂的种类和用量等都会对硫化反应的效果产生重要影响。
2. 混炼。
混炼是橡胶硫化工艺流程中的重要步骤,通过混炼可以将橡胶和各种添加剂充分混合均匀,形成橡胶混炼胶。
混炼的过程中需要控制好温度和时间,以确保橡胶和添加剂能够充分融合,并且排除其中的空气和杂质。
3. 成型。
成型是将混炼胶加工成所需形状的过程,可以通过压延、挤出、压缩成型等方式进行。
在成型过程中,需要根据产品的要求选择合适的成型工艺,控制好温度、压力和时间,使橡胶能够充分填充模具,形成所需的形状。
4. 硫化。
硫化是橡胶硫化工艺流程中的核心步骤,通过硫化可以使橡胶获得良好的力学性能和耐热性能。
硫化的过程中需要控制好温度和时间,以确保硫化反应能够充分进行,同时避免硫化过度导致产品性能下降。
5. 后处理。
硫化完成后,还需要进行后处理工艺,如冷却、清洗、修整等,以确保产品的质量和外观。
同时还需要进行产品的检验和包装,最终将产品送往市场。
总之,橡胶硫化工艺流程是一个复杂而精细的加工过程,需要严格控制各个环节,以确保产品的质量和性能。
只有在每个步骤中严格执行工艺要求,才能生产出符合要求的橡胶制品。
希望本文对橡胶硫化工艺流程有所帮助,谢谢阅读。
橡胶硫化—硫化工艺条件(橡胶加工课件)

一 硫化历程—硫化概念、原理与正硫化
二 硫化工艺条件—硫化三要素
三 硫化方法—工艺与设备 四 硫化质量分析—问题与对策
1.硫化工艺条件—温度
❖ 硫化工艺条件即硫化三要素—温度,时间和压力; ❖ 硫化温度是硫化反应的最基本条件。 ❖ 硫化温度高,硫化速度快,生产效率高;反之生产效率低 ❖ 硫化温度:电(硫化介质)间接加热,硫化介质直接加热或红
外、辐射能加热等。 硫化介质是传递热能的物质,如饱和蒸汽、过热水、热空气、
熔融盐、固体微粒等。
1.硫化工艺条件—温度
❖ 提高硫化温度会导致以下问题: ①引起橡胶分子链裂解和硫化返原,导致力学性能下降; ②使橡胶制品中的纺织物强度降低; ③导致胶料焦烧时间缩短,减少了充模时间,造成制品局
部缺胶; ④由于厚制品会增加制品的内外温差,导致硫化不均。
方程可计算出130℃和150℃时的等效硫化时间( K=2 )。
程度或胶料在一定温度下的硫化速度
t 100
I K 10
3.硫化工艺条件—硫化时间
例1:某制品正硫化条件为148℃×10min,K=2,问硫化温 度改为153℃、158℃、138℃时其等效硫化时间应分别是 多少?
3.硫化工艺条件—硫化时间
例2 某胶料的硫化温度系数为2.17,当140℃时正硫化时 间为68min,求135℃下的硫化时间。
❖ 硫化温度选择应根据制品的类型、胶种、硫化体系及其他方
面综合考虑。
不同胶种的硫化温度
不同硫化体系的硫化温度
2.硫化工艺条件—压力
❖ 硫化压力:机械压力,硫化介质,包覆层(钢丝,包布,铅)提供; 有些制品常压。 ❖ 硫化压力作用:
(1) 防止气泡; (2)提高致密性; (3)流动,充模,花纹清晰; (4)提高附着力。 ❖ 硫化压力应根据胶料配方、可塑性及产品结构等决定。
硫化工艺

硫化工艺硫化(Vulcanization) (引申定义)硫化过程中发生了硫的交联,这个过程是指把一个或更多的硫原子接在聚合物链上形成桥状结构。
反应的结果是生成了弹性体,它的性能在很多方面都有了改变,硫化剂可以是硫或者其它相关物质。
“硫化”一词有其历史性,因最初的天然橡胶制品用硫磺作交联剂进行交联而得名,随着橡胶工业的发展,现在可以用多种非硫磺交联剂进行交联。
因此硫化的更科学的意义应是“交联”或“架桥”,即线性高分子通过交联作用而形成的网状高分子的工艺过程。
硫化过程中发生了硫的交联,这个过程是指把一个或更多的硫原子接在聚合物链上形成桥状结构。
反应的结果是生成了弹性体,它的性能在很多方面都有了改变,硫化剂可以是硫或者其它相关物质。
从物性上即是塑性橡胶转化为弹性橡胶或硬质橡胶的过程。
“硫化”的含义不仅包含实际交联的过程,还包括产生交联的方法。
硫化过程可分为四个阶段,各阶段的特点:通过胶料定伸强度的测量(或硫化仪)可以看到,整个硫化过程可分为硫化诱导,预硫,正硫化和过硫(对天然胶来说是硫化返原)四个阶段。
硫化诱导期(焦烧时间)内,交联尚未开始,胶料有很好的流动性。
这一阶段决定了胶料的焦烧性及加工安全性。
这一阶段的终点,胶料开始交联并丧失流动性。
硫化诱导期的长短除与生胶本身性质有关,主要取决于所用助剂,如用迟延性促进剂可以得到较长的焦烧时间,且有较高的加工安全性。
硫化诱导期以后便是以一定速度进行交联的预硫化阶段。
预硫化期的交联程度低,即使到后期硫化胶的扯断强度,弹性也不能到达预想水平,但撕裂和动态裂口的性能却比相应的正硫化好。
到达正硫化阶段后,硫化胶的各项物理性能分别达到或接近最佳点,或达到性能的综全平衡。
正硫化阶段(硫化平坦区)之后,即为过硫阶段,有两种情况:天然胶出现“返原”现象(定伸强度下降),大部分合成胶(除丁基胶外)定伸强度继续增加。
对任何橡胶来说,硫化时不只是产生交联,还由于热及其它因素的作用产生产联链和分子链的断裂。
硫化工艺过程

硫化工艺过程Document serial number【KKGB-LBS98YT-BS8CB-BSUT-BST108】硫化工序工艺规程一、硫化过程输送带在平板硫化机上(单层或双层)采用恒温分段硫化。
硫化前检查好半成品的规格,配用相应厚度的垫铁和顶铁,带胚拖入平板空间按规定拉伸后,用低压将垫板顶起,再换用高压顶紧,并按工艺标准中规定条件进行硫化。
二、带胚硫化拉长规定(一)涤棉帆布输送带4层及4层以下拉长3-4%5层及5层以上拉长浸胶涤棉帆布输送带拉长量相应减少%。
花纹输送带拉长:鱼骨花纹输送带拉长3-4个花纹圆柱花纹(高倾角)输送带拉长个花纹。
(二)尼龙、EP输送带:%一、成品胶带冷定伸规定(一)涤棉输送带 2-3%尼龙输送带 %EP输送带 2-3%(二)冷定伸方法:成品胶带出锅以后,待下锅硫化拉长一结束,应立即用拉出机将胶带拉直,然后开动冷伸夹板按照规定冷伸量进行冷定伸,并须开动风扇降温,其间隔不得多于1分钟。
下锅前5分钟关闭风扇,落下冷伸夹板。
(三)两条胶带接头时或第一锅与最后一锅与牵引带有接头时,涤棉输送带与EP输送带冷伸量可减少至1-2%,尼龙输送带冷伸量可减少至2-3%。
二、硫化压缩比规定涤棉帆布输送带:8-18%(包括耐寒、耐热、耐酸碱、耐油)尼龙、EP输送带:8-15%注:应按带胚实际厚度计算配备垫铁。
三、硫化条件(包括硫化方法、硫化温度、硫化时间、硫化压力)(一)硫化方法的规定不闭汽只预热的输送带:各种运输带均采用不闭汽只预热的方法,其方法如下:带胚上锅后低压预热1-2分钟,放高压1-2分钟,预热时间计算在正硫化时间内。
(二)硫化温度及时间的规定NN300、EP300时布层数P的系数应改为分NN350、EP350时布层数P的系数应改为分2、表内:T—正硫化时间(分)计算到小数点后一位,四舍五入。
P—胶带布层数A、B—上、下覆盖胶厚度mm3、耐高温输送带硫化条件限于113-胶料。
4、如无特殊规定,普通、耐热涤棉帆布输送带均采用汽压硫化。
橡胶硫化工艺(1)

促进剂
活化剂
硫磺
促进剂多硫化合物 橡胶
橡胶分子链的多硫化合物
分解 自由基(或离子)
橡胶
交联反应
网络 形成 阶段
交联重排、裂解、主链改性 硫化胶
第一阶段:诱导阶段
先是硫磺、活化剂、促进 剂相互作用,使活化剂在 胶料中溶解度增加,活化 促进剂,使促进剂与硫磺 之间反应生成一种活性更 大的中间产物;然后进一 步引发橡胶分子链产生可 交联的橡胶大分子自由基。
Ø 工艺正硫化时间:指硫化曲线上M90 所对应的硫化时间,即T90;
Ø 二者都是有硫化曲线得到的。
橡胶硫化工艺(1)
Ø 胶料各项性能在某一时间不可能都处于最佳
值,必须综合考虑,生产上根据某些主要指
标来选择正硫化时间,具有工程实际意义,
称为工程正硫化时间。
Ø 当制品厚度小于6mm时,采用T90作为工程正 硫化时间;而大于6mm时,脱模后仍能产生
促进剂
活化剂
硫磺 第三阶段:网络形成阶段
期 阶
促进剂多硫化合物 橡胶
此阶段的前期交联反应
段 橡胶分子链的多硫化合物 已趋完成,初始形成的
交联 反应
分解
自由基(或离子) 交联键发生网络
网络 交联重排、裂解、主链改性 趋于稳定,获得性能稳
形成 阶段
硫化胶
定的硫化胶。
橡胶硫化工艺(1)
(三)硫化曲线及其参数
ML-最小转矩 ; MH-最大转矩; ΔM-最大与最小转矩差; M10= ML +10% ΔM M 90= ML +90% ΔM ;
TH-理论正硫化时间; T10-焦烧时间,M10对应的时间; T90- 工艺正硫化时间,M90对应的时间
橡胶硫化工艺(1)
硫化 生产工艺
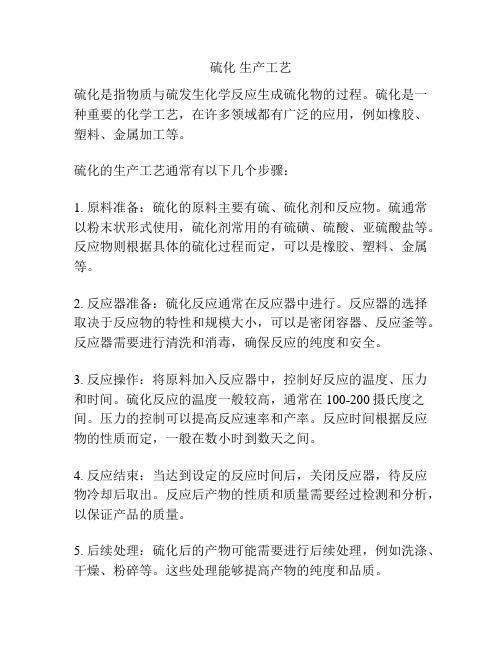
硫化生产工艺硫化是指物质与硫发生化学反应生成硫化物的过程。
硫化是一种重要的化学工艺,在许多领域都有广泛的应用,例如橡胶、塑料、金属加工等。
硫化的生产工艺通常有以下几个步骤:1. 原料准备:硫化的原料主要有硫、硫化剂和反应物。
硫通常以粉末状形式使用,硫化剂常用的有硫磺、硫酸、亚硫酸盐等。
反应物则根据具体的硫化过程而定,可以是橡胶、塑料、金属等。
2. 反应器准备:硫化反应通常在反应器中进行。
反应器的选择取决于反应物的特性和规模大小,可以是密闭容器、反应釜等。
反应器需要进行清洗和消毒,确保反应的纯度和安全。
3. 反应操作:将原料加入反应器中,控制好反应的温度、压力和时间。
硫化反应的温度一般较高,通常在100-200摄氏度之间。
压力的控制可以提高反应速率和产率。
反应时间根据反应物的性质而定,一般在数小时到数天之间。
4. 反应结束:当达到设定的反应时间后,关闭反应器,待反应物冷却后取出。
反应后产物的性质和质量需要经过检测和分析,以保证产品的质量。
5. 后续处理:硫化后的产物可能需要进行后续处理,例如洗涤、干燥、粉碎等。
这些处理能够提高产物的纯度和品质。
硫化工艺的选择和优化取决于具体应用的要求。
在橡胶工业中,硫化是一种常用的工艺,可以增强橡胶的强度、弹性和耐磨性。
硫化的机理是通过硫与橡胶中的双键反应,形成交联结构,从而增加橡胶的强度和耐热性。
总的来说,硫化是一种重要的化学工艺,通过控制好反应条件和使用合适的原料,可以获得高质量的硫化产物。
随着科技的发展,硫化工艺也在不断创新和改进,以满足不同领域的需求。
硫化工艺过程

硫化工艺过程Document serial number【UU89WT-UU98YT-UU8CB-UUUT-UUT108】硫化工序工艺规程一、硫化过程输送带在平板硫化机上(单层或双层)采用恒温分段硫化。
硫化前检查好半成品的规格,配用相应厚度的垫铁和顶铁,带胚拖入平板空间按规定拉伸后,用低压将垫板顶起,再换用高压顶紧,并按工艺标准中规定条件进行硫化。
二、带胚硫化拉长规定(一)涤棉帆布输送带4层及4层以下拉长3-4%5层及5层以上拉长浸胶涤棉帆布输送带拉长量相应减少%。
花纹输送带拉长:鱼骨花纹输送带拉长3-4个花纹圆柱花纹(高倾角)输送带拉长个花纹。
(二)尼龙、EP输送带:%一、成品胶带冷定伸规定(一)涤棉输送带 2-3%尼龙输送带 %EP输送带 2-3%(二)冷定伸方法:成品胶带出锅以后,待下锅硫化拉长一结束,应立即用拉出机将胶带拉直,然后开动冷伸夹板按照规定冷伸量进行冷定伸,并须开动风扇降温,其间隔不得多于1分钟。
下锅前5分钟关闭风扇,落下冷伸夹板。
(三)两条胶带接头时或第一锅与最后一锅与牵引带有接头时,涤棉输送带与EP 输送带冷伸量可减少至1-2%,尼龙输送带冷伸量可减少至2-3%。
二、硫化压缩比规定涤棉帆布输送带:8-18%(包括耐寒、耐热、耐酸碱、耐油)尼龙、EP输送带:8-15%注:应按带胚实际厚度计算配备垫铁。
三、硫化条件(包括硫化方法、硫化温度、硫化时间、硫化压力)(一)硫化方法的规定不闭汽只预热的输送带:各种运输带均采用不闭汽只预热的方法,其方法如下:带胚上锅后低压预热1-2分钟,放高压1-2分钟,预热时间计算在正硫化时间内。
(二)硫化温度及时间的规定硫化温度时间按下表及说明执行说明:1、当NN250、EP250时布层数P的系数应改为分NN300、EP300时布层数P的系数应改为分NN350、EP350时布层数P的系数应改为分2、表内:T—正硫化时间(分)计算到小数点后一位,四舍五入。
橡胶的硫化工艺
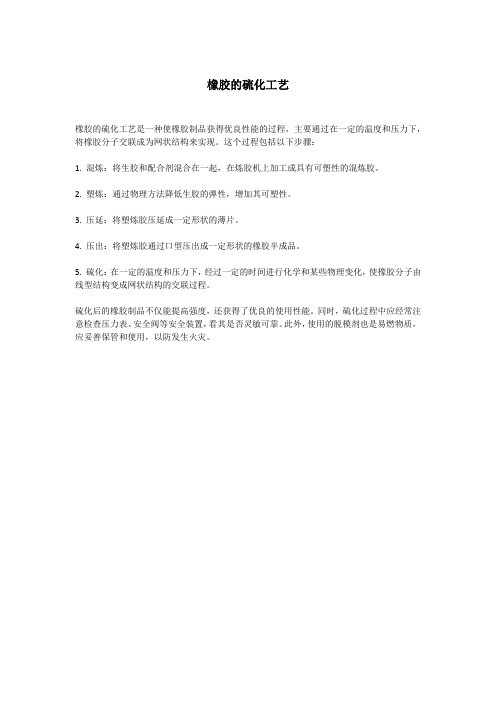
橡胶的硫化工艺
橡胶的硫化工艺是一种使橡胶制品获得优良性能的过程,主要通过在一定的温度和压力下,将橡胶分子交联成为网状结构来实现。
这个过程包括以下步骤:
1. 混炼:将生胶和配合剂混合在一起,在炼胶机上加工成具有可塑性的混炼胶。
2. 塑炼:通过物理方法降低生胶的弹性,增加其可塑性。
3. 压延:将塑炼胶压延成一定形状的薄片。
4. 压出:将塑炼胶通过口型压出成一定形状的橡胶半成品。
5. 硫化:在一定的温度和压力下,经过一定的时间进行化学和某些物理变化,使橡胶分子由线型结构变成网状结构的交联过程。
硫化后的橡胶制品不仅能提高强度,还获得了优良的使用性能。
同时,硫化过程中应经常注意检查压力表、安全阀等安全装置,看其是否灵敏可靠。
此外,使用的脱模剂也是易燃物质,应妥善保管和使用,以防发生火灾。
橡胶硫化工艺
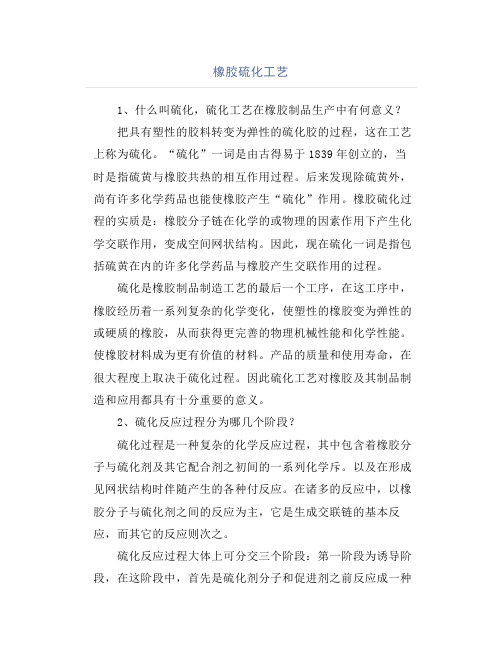
橡胶硫化工艺1、什么叫硫化,硫化工艺在橡胶制品生产中有何意义?把具有塑性的胶料转变为弹性的硫化胶的过程,这在工艺上称为硫化。
“硫化”一词是由古得易于1839年创立的,当时是指硫黄与橡胶共热的相互作用过程。
后来发现除硫黄外,尚有许多化学药品也能使橡胶产生“硫化”作用。
橡胶硫化过程的实质是:橡胶分子链在化学的或物理的因素作用下产生化学交联作用,变成空间网状结构。
因此,现在硫化一词是指包括硫黄在内的许多化学药品与橡胶产生交联作用的过程。
硫化是橡胶制品制造工艺的最后一个工序,在这工序中,橡胶经历着一系列复杂的化学变化,使塑性的橡胶变为弹性的或硬质的橡胶,从而获得更完善的物理机械性能和化学性能。
使橡胶材料成为更有价值的材料。
产品的质量和使用寿命,在很大程度上取决于硫化过程。
因此硫化工艺对橡胶及其制品制造和应用都具有十分重要的意义。
2、硫化反应过程分为哪几个阶段?硫化过程是一种复杂的化学反应过程,其中包含着橡胶分子与硫化剂及其它配合剂之初间的一系列化学斥。
以及在形成见网状结构时伴随产生的各种付反应。
在诸多的反应中,以橡胶分子与硫化剂之间的反应为主,它是生成交联链的基本反应,而其它的反应则次之。
硫化反应过程大体上可分交三个阶段:第一阶段为诱导阶段,在这阶段中,首先是硫化剂分子和促进剂之前反应成一种活性更大的中间化合物,然后进一步引发橡胶分子链,产生可交联的游离基。
第二阶段为交联反应阶段,即可交联的游离基与橡胶分子链之前产生连锁反应,生成交联键。
第三阶段为网构成熟阶段,在这阶段中的前半阶段中交联反应已趋于完成,已形成的交联键开始发生重排和裂解等反应,出现交联与裂解的两种过程,在这阶段的后半段,交联反应已基本停止,随之而发生的主要是交联键重排和热裂解等的反应,最后即得到硫化胶。
3、橡胶硫化后其性能为何会发生变化?是怎样变化的?物质的性质决定于物质的结构。
未硫化橡胶的线型大分子呈卷曲状并处于自由运动状态,当受外力作用时,大分子链段易发生位移,即存在较大的塑性流动,硫化后,柔软的长链橡胶分子通过交联变成空间网状结构,因而大分子链的相对运动受到一定限制。
硫化工艺

硫化工艺硫化工艺对粘接强度起至关重要的作用。
硫化过程中必需具备的条件是指:温度、时间和压力,一般统称皮带硫化胶接的“三要素”。
1、硫化温度:一般控制在145°c+-5°c,也有皮带产家根据芯层耐热度和胶带厚度来规定该胶带的硫化温度。
2、硫化时间:是指硫化过程中保温时间是25~35分钟。
然后开始断电降温。
3、硫化压力:硫化机开启电源前,需用打压泵对接头施以一定的压力。
通常情况下取0.8~1Mpa即可。
之后,开启电源进行升温。
当温度达到100度时,将水压加至2Mpa。
当温度达到145~150°c时进行保温。
4、硫化过程应严格按照操作规程进行,切不可操之过急。
防止因温度过高导致过硫及温度过低不能硫化,而影响粘接质量。
5、硫化结束后把电源关了,让皮带接头进行保养一段时间。
等待硫化机温度降至70°c以下,方可拆除硫化机。
但皮带不可马上工作运料,待3~5小时后才开始工作。
输送带硫化质量问题一、1、硫化面有气泡和局部粘接不好的原因:○1硫化面有气泡和局部粘接不好的现象是硫化接头的大敌。
有气泡其是一种内部粘接不好的外在表现。
这种气泡主要是产生在两心胶,最后在硫化过程中透过在盖胶的硫化面形成内部气泡。
○2空气、温度相对较大,水分不易清除在硫化时内部形成气泡。
○3局部粘接不好,多为结合面不干净以及胶糊的成份和原输送带的成份不附所造成。
2、人为因素的影响:○1胶糊浆未充分干燥便开始硫化,从而导致内部在高温时产生气泡。
○2硫化时压力、温度不均。
3、跑胶的原因:○1跑胶的原因主要是胶接用料不准确,且硫化时硫化两侧板档胶固定不实,厚度与原皮带相差远。
硫化过程中,上下箱体加压时,胶浆溶化便从两侧流出,形成跑胶。
结果会导致因硫化压力不足所形成的低强度接头。
陆振国2009年7月5日。
硫化及硫化工艺1
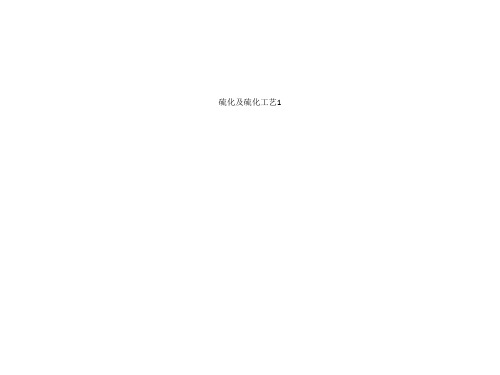
硫化及硫化体系 目录
• 1 氮气硫化及保压硫化 • 2硫化理论的基本概念 • 3有效和半有效硫化体系 • 4硫化体系的应用 • 5硫化助剂的标准及其检测
硫化及硫化体系--氮气硫化及保压硫化
• 氮气硫化节省蒸汽降低成本。取消了水加热和泵送, 从而减少了硫化能量费用60~80%。
硫化及硫化体系--氮气硫化及保压硫化
• 提高了劳动生产力。取消了热水加压等步骤,硫化时 间缩短了约10%,硫化结束后排空氮气耗时也较短。 胶囊寿命延长,减少了换胶囊停机时间。
• 提高管路寿命。氮气可以减轻管路、阀门等的腐蚀, 减少了设备维修保养(取消了水泵、加热器等)。消 除跑冒滴漏,氮气输送管路不允许有此现象;制氮时 的氧气可以输入锅炉助燃,提高燃烧效率。
硫化及硫化体系--氮气硫化及保压硫化
变压吸附法是利用高效能、高选择性的固体吸附剂 对氧或氮优先吸附的性能,把空气中的氧和氮分离出 来。
常用分子筛吸附剂(CMS)的原理:氧和氮在碳分子 筛上的吸附速度相差较大,短时间内氧分子被大量吸 附,氮分子吸附很少,使氮富集在气相中,氧留在分 子筛中。整个吸附过程在加压情况下进行,当吸附压 力降到常压时,被吸附的氧从分子筛的微孔中脱附(解 吸),分子筛获得再生。常规的碳分子筛制氮装置有两 个碳分子筛吸附塔,当一只吸附塔在进行吸氧产氮时, 另一只吸附塔在脱氧再生,如此交替循环连续不断的产 出氮气,氮的纯度为99.995 %~99.999%。
7 氮气 进
8 9 10
氮气
抽
排空
回收
真空
时间 0.2 4.0--5.0 0.8 0.2 1.0 1.0 5.0--14.0 0.2 0.4 0.2 min
硫化及硫化体系--氮气硫化及保压硫化
硅胶制品硫化的工艺

硅胶制品硫化的工艺
硅胶制品硫化是指将硅胶制品经过一定的加工后,通过加热处理使其分子间发生交联作用,从而增强其物理性能和耐热性能的一种工艺。
硅胶制品硫化的工艺有以下几个步骤:
1. 混合: 将硅胶原料和各种添加剂混合均匀,经过搅拌、压缩、挤出等加工方式制成所需的硅胶制品。
2. 成型: 将混合好的硅胶原料放入成型模具中,根据所需制品的形状、大小等进行压制和成型。
3. 预硫化: 成型后的硅胶制品进行预硫化处理,即在高温下加热硅胶制品,使硅胶分子链发生断裂并与周围分子链发生互相交联,形成网状结构,从而增强硅胶制品的物理性能和耐热性能。
4. 二次硫化: 预硫化后的硅胶制品进行二次硫化处理,即在更高的温度下加热硅胶制品,使其分子链更加稳定,从而增强其物理性能和耐热性能。
硅胶制品硫化的工艺需要在一定的温度、时间和压力等条件下进行,不同的硅胶制品和生产要求需要采用不同的硫化工艺和设备。
- 1 -。
硫化工程工艺标准

拉伸高度视胶囊的型号来确定
拉 度伸
高
2021/8/2
6
2.3、定型高度
G/T投入到模具,定型时的高度 定型高度过高,会产生窝气等不良。
4、拉伸高度与定型高度测量方法
如图:模具下卡盘到上卡盘的 一半
定 度型
高
2021/8/2
7
2.3、硫化时间及步序设定
依据硫化施工表和硫化工艺表对硫化步序进行设定。
2021/8/2
8
3、硫化异常处理规定
项目
超过硫化时间的70% 未达到硫化时间的70% 不同规格的胎胚同时硫化时
的硫化时间
允许值 ( 临时措施 ) 加剩余硫化时间 剩余硫化时间再加3min
以硫化时间长的为基准
4、硫化停机延时规定
备注
成品胎单独保管, 进行品质判定
后充气轮辋宽度(mm) 后充气压力(MPa)
胶囊定型高度(mm) 胶囊拉伸高度(mm)
2021/8/2
标准值
1.7 2.5
1
0.35 -0.03 2.3
206
178 178 标准 标准 0.2 标准 标准
允许值 主管 -0.2 ~ +0.1 ±0.1.5
硫化机 -0.2 ~ +0.1
±0.1.5
±0.1
---
±0.05 ±0.005 -0.2 ~+0.3
-----0.2 ~ +0.3
-6 ~ +3
-6 ~ +3
---------
-----
-2 ~ +3 -2 ~ +3
±50 ±5 ±0.02 ±10 ±10
硫化工艺
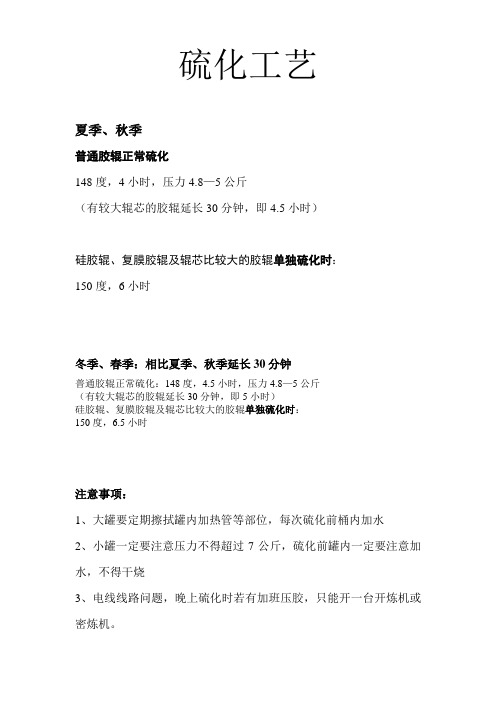
硫化工艺
夏季、秋季
普通胶辊正常硫化
148度,4小时,压力4.8—5公斤
(有较大辊芯的胶辊延长30分钟,即4.5小时)
硅胶辊、复膜胶辊及辊芯比较大的胶辊单独硫化时:
150度,6小时
冬季、春季:相比夏季、秋季延长30分钟
普通胶辊正常硫化:148度,4.5小时,压力4.8—5公斤
(有较大辊芯的胶辊延长30分钟,即5小时)
硅胶辊、复膜胶辊及辊芯比较大的胶辊单独硫化时:
150度,6.5小时
注意事项:
1、大罐要定期擦拭罐内加热管等部位,每次硫化前桶内加水
2、小罐一定要注意压力不得超过7公斤,硫化前罐内一定要注意加水,不得干烧
3、电线线路问题,晚上硫化时若有加班压胶,只能开一台开炼机或密炼机。
- 1、下载文档前请自行甄别文档内容的完整性,平台不提供额外的编辑、内容补充、找答案等附加服务。
- 2、"仅部分预览"的文档,不可在线预览部分如存在完整性等问题,可反馈申请退款(可完整预览的文档不适用该条件!)。
- 3、如文档侵犯您的权益,请联系客服反馈,我们会尽快为您处理(人工客服工作时间:9:00-18:30)。
硫化工艺
在电厂生产中,皮带的硫化是最常见的粘接方法,其主要优点有接口严密,使用寿命长,对皮带损伤小等。
下面主要介绍一下硫化的工艺流程:
一、准备工作:
工器具:打磨机、角磨机、壁纸刀、钢板尺,砂纸、胶料、洗料、毛刷、不锈钢盆、标线用具、硫化机、铁剪子、卷尺、钢板尺、电动打压泵、卡子,钢丝绳,吊装带、120#汽油、塑料等。
二、皮带置换:
1、将皮带配重吊起。
2、将旧皮带用卡子卡住,防止皮带滑落。
3、断开旧皮带,并将新皮带与其连接(用螺栓的连接),打开卡子。
4、使用车等器具将旧皮带拉出,使之新皮带置换至托辊架上。
5、用卡子将皮带卡死,并将新旧连接处断开。
三、皮带扒口:
如图所示:
帆布带切口
钢丝带切口
四、胶带粘接
(一)、帆布袋
1、将下硫化条铺上,放上下硫化板,铺上报纸或白布,将接口放置其上。
2、将扒好的帆布带使用打磨机打磨,去掉残留胶料。
3、使用120#汽油清洗接口,并使用壁纸刀片刮洗接口,并用塑料盖上,避免灰尘落上
切口。
4、同上将另一切口打磨、清洗。
5、待接口干燥后,涂抹胶2—3遍。
6、待胶用手触摸,有拉丝现象后,铺上胶料,在涂抹胶,盖上塑料,合口。
如图所示:
7、去掉夹层塑料。
8、盖上硫化板,之后放上水压带,加上铝板,压上硫化条,并使用螺栓紧固。
如图:
9、连接硫化机,打压泵。
(二)、钢丝带粘接
1、将下硫化条铺上,放上下硫化板,铺上报纸或白布,将接口放置其上。
2、将扒好的钢丝带用砂纸进行打磨(留部分胶),胶面使用打磨机打磨。
3、使用120#汽油清洗钢丝,另一接口同上。
4、待接口干燥后,涂抹胶2—3遍。
5、待胶用手触摸,有拉丝现象后,铺上胶料,将接口放置其上对齐,再涂抹胶,最后
在铺胶料。
如图:
6、盖上硫化板,之后放上水压带,加上铝板,压上硫化条,并使用螺栓紧固。
7、连接硫化机,打压泵。
五、硫化
1、连接好硫化机,打压泵。
3、降温,恒温后拔掉电源,使其自动降温至80℃。
4、拆除设备,清理现场。
六、恢复设备运行。