配气机构凸轮型线优化设计参考资料
LJ750发动机配气凸轮设计计算书

LJ750发动机配气凸轮型线设计计算书配气机构的设计思想:配气机构是发动机的重要组成部分,一台发动机的经济性能是否优越,工作是否可靠,噪声与振动能否控制在较低的限度,常常与其配其机构的设计是否合理密切关系。
特别对于高速大功率发动机,因对其较高性能指标的设计要求,配气机构的设计及其零部件的设计和制造就更加重要和严格。
配气机构的设计涉及到如下诸多问题:1.如果根据具体的机型的要求选取合理的函数凸轮型线并进行有关特性参数的计算和分析;2.配气机构方案选择及其气门的结构布置;3.对于高速配气机构来说,必须进行配气机构的动力学计算;4.在设计过程中,需要考虑很多重要的因素,如配气相位,平稳性(包括气门速度,加速度,脉冲数值大小及有无飞脱,落座反跳等),充气性能,润滑性能,凸轮与挺拄之间的接触应力等问题;因此,进行配气机构的设计往往需要很大的工作量,特别是为了获得一个最优的设计方案。
为了简化工作量,在目前国内外的设计中,常常采用参考某些成功机型的方法,来获得设计一台新发动机所需要的配气机构。
为此,在本设计了,参考了CBR900发动机的配气机构,通过对该机型配气机构的特性进行分析,并对提出的几种方案的凸轮型线进行的对比,最终获得了LJ750发动机配气机构的有关数据。
对比的结果最终还是采用了和CBR900发动机相同的配气结构,因此涉及到配气结构的许多动力学计算在这里都略去了。
本章主要介绍了多项动力凸轮设计的基本原理及其准则,并对CBR900发动机的凸轮型线进行了细致的分析和研究,在此基础上提出了LJ750发动机的配气机构。
一、凸轮型线类型的选择配气机构是发动机的一个重要系统,其设计好坏对发动机的性能、可靠性和寿命有极大的影响。
其中凸轮型线设计是配气机构设计中最为关键的部分,在确定了系统参数后,重要的问题是根据发动机的性能和用途,正确选择凸轮型线类型及凸轮参数。
凸轮型线有多种,如复合正弦,复合摆线,低次方,高次方,多项动力,谐波凸轮等。
汽油机凸轮型线改进设计_杨靖

第36卷 第11期2009年11月湖南大学学报(自然科学版)Journal of H unan U niversity(Nat ur al Sciences)V ol.36,No.11N o v 2009文章编号:1674-2974(2009)11-0021-06汽油机凸轮型线改进设计*杨 靖1 ,冯仁华1,邓帮林2,樊明明1(1.湖南大学机械与运载工程学院,先进动力总成技术研究中心,湖南长沙 410082;2.湖南奔腾动力科技有限公司,湖南长沙 410205)摘 要:应用配气机构模拟计算软件AVL-T YCON对国内某四缸汽油机配气机构进行运动学、动力学分析.结果显示,原机配气机构存在的进、排气门升程丰满系数较低,进排气凸轮与挺柱间的最大接触应力大等不足.本文根据其不足之处,通过重新设计进、排气凸轮型线,解决了原机配气机构存在的问题,提高了配气机构的可靠性和寿命,而且提高了充气效率和发动机整机性能.关键词:汽油机;配气机构;凸轮型线中图分类号:U464.134.3 文献标识码:AImprovement Design of Gasoline Engine Cam ProfileYANG Jing1 ,FENG Ren-hua1,DENG Bang-lin2,FA N M ing-ming1(1.Co llege o f M echanical and Vehicle Eng ineer ing,Research Center fo r A dvanced Po wer train T echnolog y,H unan U niv,Chang sha,Hunan 410082,China; 2.P eteco Company,L T D o f Hunan,Changsha,H unan 410205,China)Abstract:T he w idely used valve-train sim ulation software,AVL-T YCON,w as applied to perform bo th kinem atic and dynamic simulations for the v alve-train of a fo ur-cy linder gaso line engine.Sim ulation results indicate that the orig inal valve-train has some desig n draw backs,such as the plum p coefficient of the intake and exhaust valve being cow,the contact str esses betw een cam and tappet being g reater,w hich m ay lead to durability issues.The intake and ex haust cams w ere then r edesigned via computer simulation opt-i m ization,w hich not o nly so lved the primary design issues and but also im prov ed the durability.The eng ine performance simulation r esults also indicate an im pr ovement to the full load v olumetric efficiency,w hich results in an increase o f maxim um eng ine pow er o utput.Key words:gaso line eng ine;valve-train;cam profile配气机构是发动机的重要组成部分,其性能的好坏,直接影响到发动机的动力性、经济性和可靠性,并对发动机噪声与振动产生直接影响[1].近年来,随着发动机低排放、高速化的发展趋势,对其性能指标要求越来越高,要求其在高速运行的条件下仍然能够平稳、安全可靠地工作,因此对配气机构设计的要求也越来越高[2-3].本文应用专门的配气机构模拟分析软件,建立某四缸汽油机配气机构运动学、动力学模型,进行相关计算,评价其运动学和动力学性能.并重新设计凸轮型线,使换型线后配气机构的运动学、动力学特性更好,提高整机性能.*收稿日期:2009-04-08基金项目:国家高新技术研究发展计划(863计划)资助项目(2008AA11A114)作者简介:杨 靖(1957-),女,湖南长沙人,湖南大学教授通讯联系人,E-mail:yangjing10@湖南大学学报(自然科学版)2009年1 配气机构性能评价准则要保证发动机具有良好的工作性能,配气机构就要满足相应的要求.评价配气机构的性能主要有以下几个方面:1)使配气机构具有良好的充气性能.反映气门通过能力大小用 气门瞬时通路面积或 时面值 来表示.为了便于比较各种具有不同工作段包角和最大升程的凸轮对充气性能的影响效果,这里用丰满系数作为评价指标:= a y( )d /y max( a- ),(1)式中:y max为气门最大升程; a为气门关闭时的凸轮轴转角; 为气门开启时的凸轮轴转角.一般认为丰满系数较大对充气性能是有利的,但并非绝对如此,如果一味追求大的丰满系数而使机构可靠性和平稳性变得很差,结果就无法得到良好的充气性能.2)使配气机构工作平稳,振动和噪音较小.配气机构的平稳性,以及是否存在飞脱和落座反跳等现象,需要通过配气机构动力学计算来验证.一般用气门加速度曲线变化率的最大值范围来评价气门运动的平稳性.气门运动加速度变化率最大值定义为最大跃度值.如果最大跃度值小于1000mm/rad3,表明气门运动具有较好的平稳性.3)凸轮与挺柱间的接触应力不应过大.配气凸轮与挺柱是发动机中一对重要的摩擦副,很容易发生过早磨损、擦伤、劈裂等故障.在设计阶段要对凸轮与挺柱间接触应力进行计算和校核.凸轮与挺柱间的接触应力可按下面公式计算:c=0.564F1+ 21 21- 21E1+1- 22E2W.(2)式中:F为凸轮与挺柱间的法向作用力; 1, 2分别为凸轮与挺柱在接触点的曲率半径;E1,E2分别为凸轮与挺柱材料的弹性模量; 1, 2分别为相应材料的泊松比;W为接触线宽度.4)凸轮应有良好的润滑特性.凸轮型线设计时,应使凸轮与挺柱处于较好的润滑状态,以提高凸轮与挺柱摩擦副的可靠性与寿命.可用油膜厚度或者流体动力学润滑系数作为凸轮设计的评价指标.凸轮与平面挺柱的油膜厚度计算公式为:min=k0(R0+h)2(R0+h)2-(R0+h).(3)式中:R0为凸轮基圆半径;h为挺柱升程; 为接触点处凸轮廓线曲率半径;k0为已知常数.流体动力学润滑系数N r定义为N r=R0+h.(4)平面挺柱的最小润滑系数要求在凸轮桃尖 30度凸轮转角范围内,其在0.15~0.3之间[4].2 配气机构的建模及原机配气机构分析2 1 配气机构结构该汽油机配气机构采用双顶置凸轮轴、四气门、凸轮直接驱动气门的形式.配气机构主要由凸轮轴、耐磨垫片和气门弹簧套等7部分组成.结构简图如图1所示.1-凸轮轴;2-耐磨垫片;3-气门弹簧套;4-进气门;5-气门锁夹;6-排气门;7-气门弹簧图1 配气机构结构简图F ig.1 St ruct ur e diagr am of the valve-train2 2 配气机构计算仿真模型应用AVL-T YCON软件建立配气机构计算模型,选取和设置各部件质量、刚度、阻尼等参数及发动机相关参数进行计算分析.配气机构计算模型如图2所示.图2中配气机构计算仿真模型由10个单元组成.2 3 模型相关参数选取和设置模型中各部件质量、刚度、阻尼等参数通过三维CAD软件和有限元分析软件获取.计算中气门系统等效为二质量当量系统,包括气门侧质量和凸轮侧质量.二质量单元由一根代表气门系统刚度的弹簧相连,气门弹簧使两质量与上述弹簧保持接触[5-6].22第11期杨 靖等:汽油机凸轮型线改进设计图2 配气机构计算仿真模型F ig.2 Simulatio n mo del of the valve-tr ain2 4 原机配气机构分析将原机的进、排气凸轮型线导入模型中的凸轮模块中,经计算得到原机配气机构的技术参数和性能参数,见表1和表2.经分析,发现原机配气机构存在以下不足:表1 配气机构主要技术参数Tab.1 Major technical parameters of the valve-train技术参数原机新设计的凸轮型线进气排气进气排气气门升程/mm8.897.6258.937.7凸轮升程/mm9.077.9259.18气门间隙/mm0.140.280.140.28基圆半径/mm18181818挺柱直径/mm30303030凸轮轴标定转速/(r min-1)2875287528752875缓冲段高度/mm0.180.30.180.3凸轮总作用角/ CaA172166167176进气相位角/ CA 提前30 开启滞后68 关闭提前21 开启滞后65 关闭排气相位角/ CA 提前54 开启滞后19 关闭提前52 开启滞后15 关闭气门重叠角/ CA49361)进、排气门升程丰满系数较低,不利于发动机获得较高的充气效率;2)进、排气凸轮型线部分段不光滑,导致最大跃度值超过了正常的范围,使配气机构的振动加剧;3)进、排气凸轮与挺柱的最大接触应力大,凸轮与挺柱间的磨损较大;4)进、排气凸轮与挺柱间的润滑系数低于常规值范围,因此进、排气凸轮与挺柱的液体动力学润滑条件不好.针对原机配气机构存在的问题,并结合厂家对改进后发动机的标定功率由原来的87.1kW提高到91.5kW的目标要求,配气凸轮型线的优化改进方向是:1)改善进气门充气性能和排气门的排气性能,即提高进、排气门升程丰满系数;2)改善进、排气凸轮与挺柱间的润滑条件,并协调好润滑条件、凸轮与挺柱间的接触应力、气门弹簧裕度等相互之间的影响;3)使进、排气凸轮型线各部分连接光滑,将凸轮跃度值控制在允许范围内.表2 配气机构主要性能参数Tab.2 Major perf ormance parameters of the valve-train 技术参数原机凸轮型线新设计的凸轮型线进气排气进气排气气门升程丰满度0.4960.530.5640.563挺柱最大几何速度/(mm/( ))0.2490.2270.2470.222挺柱最大正加速度/(mm/( ))0.02570.02250.02430.0244挺柱最大负加速度/(mm/( ))-0.0073-0.0069-0.0066-0.0059凸轮最大跃度/(m m rad-3)151642201075994凸轮最小曲率半径/mm 3.19 3.278 5.399 6.573凸轮与挺柱间的最大接触应力/M Pa552.6533.3443.8377.6气门最小弹簧裕度 1.19 1.233 1.249 1.297凸轮与挺柱最小润滑系数0.1180.1260.1990.253 凸轮型线改进设计3 1 缓冲段的设计新凸轮型线的缓冲段的设计直接选用余弦函数,通过设置缓冲段高度和缓冲段末端速度就可以在TYCON中的Cam Desig n模块里很方便的获得.3 2 工作段的设计根据凸轮型线工作段设计方法,结合原机配气机构的特点,并综合考虑优化设计的凸轮型线要达到的要求,进、排气凸轮工作段的设计均采用多项动力凸轮的方法,用高次多项式函数来表达,并结合前面所设计的缓冲段,二者共同构成完整的凸轮型线.工作段气门升程函数为:h=(h max-h r)(1+C2 2+C4 4+C p p+C q q+C r r+C s s).式中:h max为凸轮最大升程;h r为凸轮缓冲段高度; C2~C s为待定系数,p,q,r和s为幂指数; =1- - 0B,其中 为凸轮工作角度值, 0为凸轮缓冲段23湖南大学学报(自然科学版)2009年包角, B 为凸轮工作段半包角.利用TYCON 中的Cam Desig n 模块,按照配气凸轮设计准则,将幂指数的选取目标定为机构运动平稳性,通过设置凸轮与挺柱的最大接触应力、凸轮曲率半径、凸轮的最大允许跃度和挺柱的最大直径等限制条件,设计出新的凸轮型线.经运算,最终择优确定一组,幂指数为进气凸轮:p =16,q =28,r =42,s =52;排气凸轮:p =16,q =28,r =40,s =50.多项式中的各项系数根据边界条件求得:因气门在缓冲段终点处开启,该处的气门升程、速度、加速度均为零,但挺柱的升程、速度则应与基本工作段连续;并考虑到气门与当量挺柱运动规律间的关系列出相应的方程组,解出各系数.经过计算,新设计的进、排气凸轮工作段函数为h int =8.93(1-1.4884 2+0.2 4+0.6666 16-0.5835 28+0.2823 42-0.0771 52),h exh =7.7(1-1.3818 2+0.15 4+0.4043 16-0.2197 28+0.051 40-0.0039 50).凸轮的新老型线如图3所示.配气机构的主要技术参数对比见表 1.凸轮转角/ CaA图3 凸轮升程曲线Fig.3 Cam lift cur ves4 换型线后配气机构运动学、动力学分析4 1 凸轮型线评价及配气机构运动学分析利用TYCON 对新设计的凸轮型线评价和配气机构运动学分析,配气机构的性能参数比较见表2.根据表2中的参数可以看出:1)新设计的进、排气门升程丰满系数都比原机有所提高,进、排气门升程丰满系数分别提高了13.7%,6.2%,且气门开启和关闭更加迅速,这样可以提高充气效率,从而可以提高发动机功率;2)新设计的进、排气凸轮型线的跃度值在1000mm/rad 3左右,均在正常范围之内,且和原机相比减小了很多,因此可以减小从动件的振动,使配气机构运动更加平稳;3)新设计的进、排气凸轮的最小曲率半径都比原机大,有力地改善了凸轮与挺柱间的润滑条件[7];4)由于该发动机凸轮采用45号钢,而平面挺柱采用冷激铸铁,凸轮与平面挺柱的许用接触应力为650MPa.改进后进、排气凸轮与挺柱的接触应力均满足许用值要求,且比原机小,因此,减小了该摩擦副间的磨损;5)新设计的进、排气凸轮的最小润滑系数有明显的提高,且都在较理想的范围内,这将改善凸轮与挺柱间的液体动力学润滑条件,减小磨损;6)采用新设计的凸轮型线和原机的气门最小弹簧裕度值都较理想,进、排气门弹簧的预紧力和刚度合适,说明新设计的凸轮型线与气门弹簧匹配得较好,这样从动件和凸轮表面不会跳开,而且早期磨损小,驱动功率也较小.4 2 配气机构动力学分析4.2.1 动力学分析的必要性作配气机构运动学计算时将其零部件视为完全刚性,以升程曲线丰满系数大小和最大正、负加速度值等参数来判断凸轮设计的优劣.但实际配气机构是一个弹性系统,工作时机构的弹性变形会使位于传动链末端气门处的运动产生很大畸变,即气门的升程、速度特别是加速度等运动规律 失真 .气门的运动有时迟于挺柱,有时则超越于挺柱,使传动链脱节、气门的开闭不正常、飞脱、反跳、整个机构振动噪声加大,甚至机构的正常工作遭到破坏.随着发动机转速的提高,机构的运动件受力以及振动增大,上述 失真 现象成为发动机转速提高的障碍,因此需要进行配气机构的动力学分析,研究机构弹性变形下的气门运动规律[8].4.2.2 动力学分析结果通过对原机和改型线后配气机构的动力学分析,结果如下:1)发动机标定转速为5750r/min 时气门的升程、速度、加速度、落座力曲线,如图4~图7所示.凸轮转角/ CaA图4 气门升程曲线Fig.4 Simulated valve lift curves24第11期杨 靖等:汽油机凸轮型线改进设计从图4可以看出,原机和改型线后进、排气门开启和关闭正常,无反跳和二次开启现象;气门最大落座速度一般要求小于0.5m/s,否则会使气门和气门座很快磨损.图5中原机进气门最大落座速度为0.315m/s,排气门最大落座速度为0.313m/s,而换新设计的型线后进气门最大落座速度为0.258m/s,排气门最大落座速度为0.17m/s,这样可减小气门与气门座的磨损.图6中改进后进、排气门加速度比原机有所改善.从图7中气门座受力曲线可以看出改进后进、排气门落座力比原机小.凸轮转角/ CaA图5 气门速度曲线Fig.5 Simulated valve velocity curves凸轮转角/ CaA图6 气门加速度曲线Fig.6 Simulated valve accelerationcurves凸轮转角/ CaA图7 气门落座力曲线Fig.7 Simulated valve seating forces2)凸轮与挺柱的动力学接触应力曲线,如图8所示.从图8中可以看出,原机和改进后在发动机标定转速5750r/min 时均无飞脱现象,且改型线后进、排气凸轮与挺柱的动力学最大接触应力均比原机小,这样磨损也减小.3)气门弹簧动力学特性,如图9所示.换新设计的凸轮型线后,进、排气门弹簧动力学特性较好,无并圈和大的冲击现象发生.凸轮转角/ CaA图8 凸轮与挺柱动力学接触应力曲线(n =5750r/min)Fig.8Simulated dynamics contact stresses between cam and tappet (n =5750r/min)凸轮转角/ CaA图9 换新设计的凸轮型线后气门弹簧各弹性质点升程曲线(n =5750r/min)Fig.9 Displacement diagram of the elastic particles in the valve spring,optimized cam profile (n =5750r/min)5 发动机性能模拟计算通过GT -POWER 对发动机性能进行模拟计算,先利用原机试验数据对性能仿真模型进行标定,然后换新设计的进、排气凸轮型线对发动机的性能进行模拟计算.发动机在全负荷时的功率曲线如图10所示.从图10中可以看出,原机试验值和模拟值误差很小,说明模型标定较准确,性能计算模拟值准确度较高;采用新设计的凸轮型线后,发动机的功率和原机相比有一定的提高,在标定转速5750r/min 时,标定功率为91.7kW,与原机相比提高了5.28%.25湖南大学学报(自然科学版)2009年发动机转速/(r min-1)图10 发动机功率曲线Fig.10 Comparison of full load engine power6 结 论1)通过对原机配气机构的运动学、动力学计算分析,找出了其存在的问题,并重新设计了满足要求的进、排气凸轮型线;2)采用新设计的凸轮型线后,进、排气门升程丰满系数均有所提高,这将有利于发动机充气系数的提高;3)采用新设计的凸轮型线后,配气机构的机械性能有改善,整个配气机构工作更加可靠、气门落座平稳,无反跳、飞脱等现象;不但解决了原机凸轮型线部分段不光滑、跃度值大、润滑条件不太理想等问题,而且也使配气机构的振动、噪声、磨损减小;4)采用新设计的凸轮型线后,发动机的标定功率可由原来的87.1kW提高到91.7kW,达到了目标要求.参考文献[1] 陈家瑞.汽车构造[M].北京:机械工业出版社,2005. CHEN Ji a-rui.Automobile structure[M].Beijing:M achi nery Indus-try Press,2005.(In Chinese)[2] 刘彪,翟爽.高速车用发动机非对称配气凸轮形线设计方法研究[J].湖南大学学报:自然科学版,2003,30(1):50-53.LIU Biao,ZHAI Suang.Design method on non-symmetri cal valve-train cam profile of high-speed vehicular engines[J].Journal of Hunan University:Natural Sciences,2003,30(1):50-53.(In Chinese) [3] 卢月娥,任述光,杨大平.内燃机配气凸轮机构型线的动力学优化设计[J].湖南农业大学学报,2002,28(6):522-524.LU Yue-e,REN Shu-guang,YANG Da-pi ng.Optimized dynamics design of di stri bution cam mechani sm in internal combus tion engine [J].Journal of Hunan Agricultural University,2002,28(6):522-524.(In Chi nese)[4] 刘建美.发动机配气机构凸轮挺柱的弹流润滑设计[J].小型内燃机与摩托车,2008,37(5):26-27.LIU J ian-mei.Elastic fluid l ubrication design of the cam tappet i n ad-mi ssion gear of engine[J].Smal l Internal Combustion Engi ne and M o-torcycle,2008,37(5):26-27.(In Chi nese)[5] 吕林,王永波.车用发动机配气机构运动学和动力学分析[J].武汉理工大学学报,2006,30(6):1011-1014.LV Lin,W ANG Yong-bo.Ki nematic and dynamic analysis on valve train of vehicle engine[J].Journal of Wuhan University of Technolo-gy,2006,30(6):1011-1014.(In Chinese)[6] AVL TYCON User s Guide[Z].Versi on4.0.1,2004.[7] 仇涛,刘兴华,刘福水.摩托车配气机构的磨损分析及改进设计研究[J].内燃机工程,2008,29(4):51-54.CH OU Tao,LIU Xing-hua,LIU Fu-shui.Analys is and improvement for valve train of motorcycle[J].Internal Combus tion Engine Eng-i neering,2008,29(4):51-54.(In Chinese)[8] 张晓蓉,朱才贵,吴佳芸.内燃机配气机构系统动力学分析[J].重庆大学学报,2008,31(3):294-298.ZHANG Xiao-rong,ZH U Ca-i gui,WU Ji a-yun.System dynamic a-nalys is of engine valve-train[J].Journal of Chongqing University, 2008,31(3):294-298.(In Chi nese)26。
凸轮型线设计说明
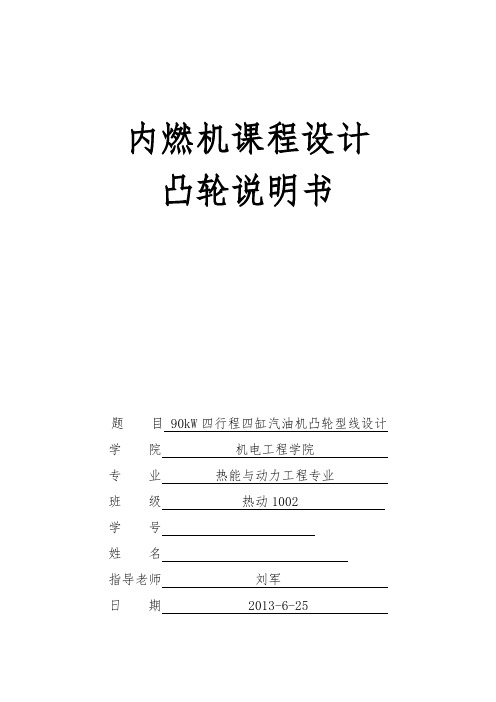
内燃机课程设计凸轮说明书题目 90kW四行程四缸汽油机凸轮型线设计学院机电工程学院专业热能与动力工程专业班级热动1002 学号姓名指导老师刘军日期 2013-6-2590kW四行程四缸汽油机凸轮型线设计前言四冲程汽车发动机都采用气门式配气机构,其功用是按照发动机的工作顺序和工作循环要求,定时开启和关闭各缸的进、排气门,使新气进入气缸,废气从气缸排出。
其中,凸轮机构作为机械中一种常用机构,在自动学和半自动学当中应用十分广泛,凸轮外形设计在配气机构设计中极为重要,这是由于气门开关的快慢、开度的大小、开启时间的长短都取决于配气机构的形状。
因此,配气凸轮的外形设计和配气凸轮型线设计就决定了时间的大小、配气机构各零件的运动规律及其承载情况。
任务书首先对凸轮进行设计,然后利用最大速度和最大加速度位置基于高次方程凸轮运动规律进行凸轮型线的优化设计,建立数学模型,并设计图论过渡段和绘制图轮廓图。
凸轮的设计1.给定的参数及要求(1)凸轮设计转速nc=4636r/min;(2)进气门开启角233°(曲轴转角),凸轮工作段包角116.5°;(3)排气门开启角220°(曲轴转角),凸轮工作段包角110°;(4)气门重叠角15°(曲轴转角),凸轮转角7.5°;(5)凸轮基圆直径 28mm;(6)进气门最大气门升程hvmax =8.2,排气门最大气门升程hvmax=8。
2.凸轮型线类型的选择配气机构是发动机的一个重要系统,其设计好坏对发动机的性能、可靠性和寿命有极大的影响。
其中凸轮型线设计是配气机构设计中最为关键的部分,在确定了系统参数后,重要的问题是根据发动机的性能和用途,正确选择凸轮型线类型及凸轮参数。
凸轮型线有多种,如复合正弦,复合摆线,低次方,高次方,多项动力,谐波凸轮等。
其中,高次方、多项动力、谐波凸轮等具有连续的高阶倒数的凸轮型线,具有良好的动力性能,能满足较高转速发动机配气机构工作平稳性的要求。
06-某发动机凸轮型线的优化设计及分析_吉利汽车苏圣等

凸轮型线的设计及分析苏圣胡景彦李慧军刘云卿杜宝杰吴丰凯吴小飞(浙江吉利汽车技术中心有限公司,浙江杭州 311228)摘要:本文主要描述通过工程软件计算出来的分析结果来进行指导凸轮型线的设计,最后通过发动机试验验证了新设计的凸轮型线满足设计要求。
关键词:汽油机凸轮型线阀系动力学特性单阀系动力学正时机构动力学主要软件:A VL EXCITE Timing drive、A VL Boost1. 前言在发动机的配气机构中,凸轮的凸轮型线不仅对发动机的动力性能有影响,同时也对发动机的机械噪声和零部件的磨损情况都有直接的影响。
所以优化设计一个比较好的凸轮型线既要考虑发动机的热力学性能又要关注发动机的机械性能,同时还要满足凸轮型线的加工要求。
只有上述几个条件全部满足要求才能进行加工生产并且测试。
设计凸轮型线总共分成5个阶段。
第一阶段为热力学预测阶段,在该阶段中主要设计一条热力学性能最优的气门升程曲线。
第二阶段为凸轮型线设计阶段,在该阶段中参照热力学设计的气门升程曲线并且根据运动学原理设计一条满足动力学性能的凸轮型线。
第三阶段对设计完成的凸轮型线进行单阀系的动力学校核,如果不满足动力学要求,则返回第二阶段重新设计凸轮型线。
第四阶段进行多阀系动力学分析,观察各个指标是否满足设计要求,如果不满足要求返回第二阶段重新设计。
第五阶段就是将设计完成的凸轮型线移交给供应商进行加工。
下图为凸轮型线的设计流程。
图1 凸轮型线设计流程2. 设计过程2.1 热力学预测目前某款1.5升GDI发动机最大功率为78kW,要比预期的发动机功率小5kW,为了提高发动机功率,采取的措施为更改发动机的进排气凸轮。
首先根据某1.5升GDI发动机参数进行搭建热力学模型,并且反复调试该热力学模型直到热力学各个工况的计算结果与实际中测得相对应工况中的试验结果相吻合为止。
热力学模型如下图所示。
图2 热力学模型利用上述的热力学软件,计算4种进气门升程和4这种排气门升程,计算出相应的功率和扭矩。
凸轮优化设计

一.配气凸轮优化设计1.1配气凸轮结构形式及特点配气凸轮是决定配气机构工作性能的关键零件,如何设计和加工出具有合理型线的凸轮轴是整个配气系统设计中最为重要的问题。
对内燃机气门通过能力的要求,实际上就是对由凸轮外形所决定的气门升程规律的要求,气门开启迅速就能增大时面值,但这将导致气门机构运动件的加速度和惯性负荷增大,冲击、振动加剧、机构动力特性变差。
因此,对气门通过能力的要求与机构动力特性的要求间存在一定矛盾,应该观察所设计发动机的特点,如发动机工作转速、性能要求、配气机构刚度大小等,主要在凸轮外形设计中兼顾解决发动机配气凸轮外形的设计也就是对凸轮从动件运动规律的设计。
从动件升程规律的微小差异会引起加速度规律的很大变动,在确定从动件运动规律时,加速度运动规律最为重要,通常用其基本工作段运动规律来命名,一般有下面几种:1.1.1等加速凸轮等加速凸轮的特点是其加速度分布采取分段为常数的形式,其中又可分为两类,一类可称为“正负零型”,指其相应的挺柱加速度曲线为正—负—零:另一类可称“正零负型”,指其加速度曲线为正一零一负。
当不考虑配气机构的弹性变形时,对最大正负加速度值做一定限制且在最大升程、初速度相同的各种凸轮中,这种型式的凸轮所能达到的时面值最大。
等加速型凸轮常常适用于平稳性易保证,而充气性能较差的中低速柴油机中。
但就实际情况而言,配气机构并非完全刚性,等加速凸轮加速度曲线的间断性必然会影响机构工作平稳性,在高速内燃机中一般不采用等加速型凸轮[9]。
1.1.2组合多项式型组合多项式型凸轮的基本段为一分段函数,它由几个不同的表达式拼接而成。
通过调整各段所占角度及函数方程,获得不同斜率的加速度曲线。
组合多项式型凸轮时面值大,而且能够方便地控制加速度变化率及确保正、负加速段间的圆滑过渡,可以较好地协调发动机充气性能及配气机构工作平稳性的要求[7]。
由于凸轮从动件运动规律由若干函数组成,在各段间联结点处不易保证升程规律三阶以上导数的连续性,可能会影响配气机构工作的平稳性,组合多项式型凸轮主要应用在要求气门时面值大和较好动力性能的情形。
WD618.42柴油机配气凸轮型线的改进设计

l. 5 5
WD 1. 2柴ቤተ መጻሕፍቲ ባይዱ油机是 潍 柴 动力 新 投 放 市 场 的功 68 4 率 较 大 的车 用 发 动机 , 在试 验 阶段 发 现 该 机 型存 在
缸 径 × 行 程/ m a r 标 定 功 率 / W k
文 章 编 号 :00 02(06 0 -00 0 10 - 9520) 5 5 - 4
2 0 9 7 0 6
WD 1 . 2柴 油机 配气 凸轮 型线 的 改进 设 计 6 4 8
乔 军 ’ 国祥 。李
( . 柴 动力股 份 有限公 司 , 1潍 潍坊 2 1 0 ;. 6 0 1 2 山东 大学 能源 与 动力 T程 学 院)
pr s u e d c e s d a lt l. e s r e r a e ite
摘 要 :利用 B X S ( )T和 T C N软件 对 WD 1. 2柴油机及 其配 气机 构建 立仿 真计算模 型 , Y O 684
进 行 了联合计 算。对 配气相位进行 了重新选择 , 大凸轮 升程 和轮廓 线 函数 也进行 了优 化 , 高 最 提 了充 气效率 降低 了进排 气凸轮 最大接触 应 力。通过 台架试验 结 果对 比证 明 , 柴油机 采 用改进 后
发 火 顺 序 最 高燃 烧 压 力 / a MP 冷 态 气 门 间 隙/ m a r
l53624 ———— l. 5 3 进 . 5 排 . 气0 3 , t0 4
进 气 广 开 3 . 。 A I ) J 6 5 【 j 【 ’ TI ’
Ab t a t I h ril,t esmu ain m o eso D6 8 4 is le gn n t av r i r e sr c : n t ea tce h i lt d l f o W 1 . 2 de e n i ea d isv letan we es t
凸轮型线设计

序号:编码:重庆理工大学第二十四届“开拓杯〞学生课外学术科技作品竞赛参赛作品作品名称:配气凸轮型线设计作品类别: A类别:自然科学类学术论文科技创造制作C哲学社会科学类学术论文与社会调查报告配气凸轮型线设计摘要:配气机构是内燃机重要组成局部,它控制着内燃机的换气过程,其设计优劣直接影响着内燃机的动力性,经济性和排放性以及工作可靠性。
今年来随着内燃机的高速化,低排放化的趋势,人们对其配气机构的性能要求越来越高。
而凸轮型线配气机构的核心局部,其设计的合理性影响着配气机构的各个性能指标。
凸轮型线的设计既要保证获得尽可能的大时面值和饱满系数以提高换气效率,又要保证加速度曲线连续,、无突变。
本次论文针对以上情况,设计出一款缸径为68的配气凸轮,并对其性能做出相应的评价。
关键词:配气机构凸轮升程凸轮型线Abstract:Airdistribution mechanism is animportant part ofthe internal combustion engine,which controls the gasexchang e process of the internalcombustion engine,thedesignofwhich has a direct impact on theengine power,economy andemissions aswell aswork reliability.Thisyear,with the high speed of theinternal combustion engine,thetrend of lowemission,the performance requirements of thegasdistributionagenciesaregettinghigherandhigher.And thecorepartofthecamtypeairdistributionmechanism,the rationalityofitsdesignaffectstheperformanceindexesofthe airdistribution mechanism.The design of the cam profile is notonlytoensurethatthefacevalueandfullnesscoefficientareobtained asmuchas possible to improvethe ventilationefficienc y,but alsotoensure that the acceleration curveiscontinuous,andthereisnomutation.Thispaper,inviewofthe abovesituation,designabore68ofthecam,andmakethe correspondingevaluationonitsperformance.Keyword:Valvetrain Camlift Camprofile1.凸轮设计的根本原那么凸轮的设计即凸轮外轮廓线的设计,凸轮廓线有两种表示方法:1〕型线式,给出凸轮对应的挺柱升程曲线以及基圆半径,2〕外型式,给出轮廓形的几何形状和曲线方程。
凸轮型线设计与配气机构动力学分析

Kinematics Result
Intake Side Valve Lift
Kinematics Result
Kinematics Result
Kinematics Result
Kinematics Result
Kinematics Result
Dynamics Results
Dynamics Results
凸轮型线设计与配气机构动力学分析
代秀红
奇瑞汽车有限公司
内容概要
1. 单配气机构发动机凸轮型线设计 2. 单配气机构动力学分析
单配气机构形式及计算模型1
单配气机构形式及计算模型2
• 以模型2计算为例 • 基于三条满足热力学要求型线的机构运动学、 动力学计算结果如下所示,均满足运动学、动 力学要求
Dynamics Results
Dynamics Results
Dynamics Results
Dynamics Resulቤተ መጻሕፍቲ ባይዱs
结论与展望
• 采用TYCON软件设计了某机凸轮型线,符合 发动机热力性能要求 • 希望以后能将正时轮系的设计计算应用起来
柴油机配气凸轮型线研究
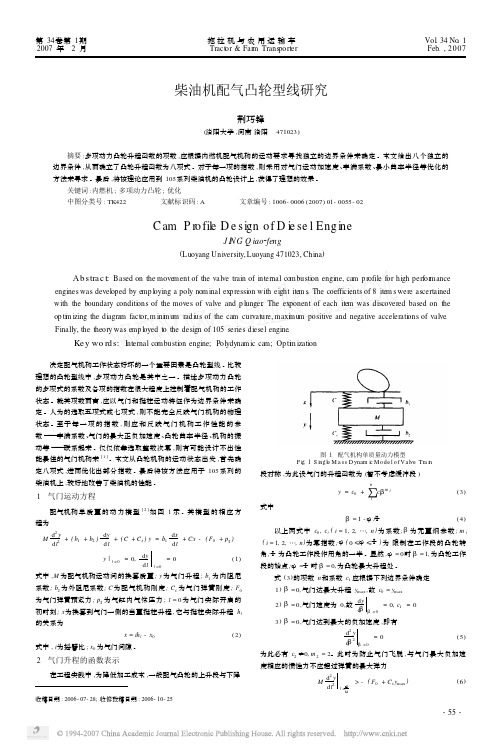
柴油机配气凸轮型线研究荆巧锋(洛阳大学,河南洛阳 471023)摘要:多项动力凸轮升程函数的项数,应根据内燃机配气机构的运动要求寻找独立的边界条件来确定。
本文给出八个独立的边界条件,从而确立了凸轮升程函数为八项式。
对于每一项的指数,则采用对气门运动加速度、丰满系数、最小曲率半径等优化的方法来寻求。
最后,将该理论应用到105系列柴油机的凸轮设计上,获得了理想的效果。
关键词:内燃机;多项动力凸轮;优化中图分类号:TK422 文献标识码:A 文章编号:1006-0006(2007)01-0055-02C am P r o fil eD e s i gn o f D i e se l Eng i neJ I N G Q iao 2feng(Luoyang University,Luoyang 471023,China )Ab s tra c t:Based on the movement of the valve train of internal combusti on engine,ca m p r ofile f or high perf or manceengines was devel oped by e mp l oying a poly nom inal exp ressi on with eight ite m s .The coefficients of 8ite m s were ascertained with the boundary conditi ons of the moves of valve and p lunger .The exponent of each item was discovered based on the op ti m izing the diagra m fact or,m ini m u m radius of the ca m curvature,maxi m u m positive and negative accelerati ons of valve .Finally,the theory was e mp l oyed t o the design of 105series diesel engine .Key wo rd s:I nternal combusti on engine;Polydynam ic ca m;Op ti m izati on 决定配气机构工作状态好坏的一个重要因素是凸轮型线。
内燃机配气机构凸轮的设计

内燃机配气机构凸轮的设计
内燃机配气机构中,凸轮是最重要的零件之一,负责控制气门的
开启和关闭。
其设计需要考虑诸多因素,如气门开启角度、开启时间、开启速度等。
凸轮的形状通常为椭圆形或者正弦型,具体的形状与气门的开启
方式有关。
在设计凸轮时,需要分析气门的运动规律以及发动机的性
能要求,确定凸轮的最佳形状。
此外,凸轮的位置和大小也需要设计。
凸轮的位置通常与曲轴的
角度有关,而凸轮的大小则取决于发动机的排量和功率等因素。
在设
计时,需要根据实际情况进行具体的计算和调整。
总之,内燃机配气机构凸轮的设计复杂而关键,需要综合考虑多
种因素,以确保发动机的性能和可靠性。
汽车发动机配气机构配气凸轮型线优化设计
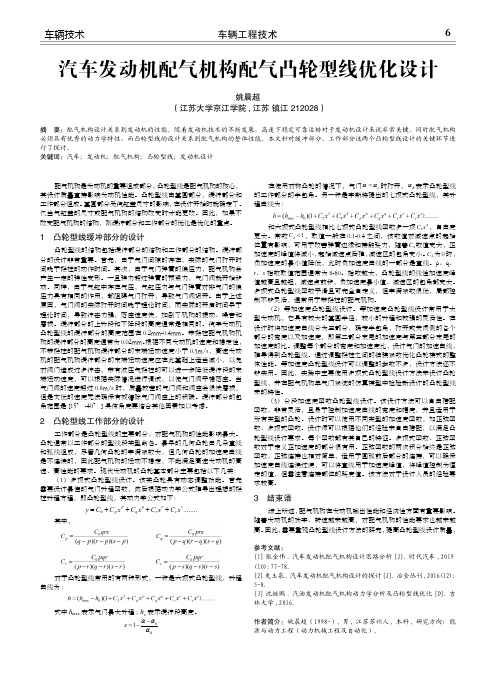
车辆工程技术6车辆技术汽车发动机配气机构配气凸轮型线优化设计姚晨超(江苏大学京江学院,江苏 镇江 212028)摘 要:配气机构设计关系到发动机的性能。
随着发动机技术的不断发展,高速下稳定可靠运转对于发动机设计来说非常关键,同时配气机构必须具有优秀的动力学特性,而凸轮型线的设计关系到配气机构的整体性能。
本文针对缓冲部分、工作部分这两个凸轮型线设计的关键环节进行了探讨。
关键词:汽车;发动机;配气机构;凸轮型线;发动机设计配气机构是发动机的重要组成部分,凸轮型线是配气机构的核心,其设计质量直接影响发动机性能。
凸轮型线由基圆部分,缓冲部分和工作部分组成。
基圆部分受汽缸盖尺寸的影响,在设计开始时就确定了。
仅当气缸盖的尺寸或配气机构的结构改变时才能更改。
因此,如果不改变配气机构的结构,则缓冲部分和工作部分的优化是优化的重点。
1 凸轮型线缓冲部分的设计凸轮型线的结构包括缓冲部分的结构和工作部分的结构。
缓冲部分的设计非常重要。
首先,由于气门间隙的存在,实际的气门打开时间晚于挺柱的动作时间。
其次,由于气门弹簧的偏压力,配气机构会产生一定的弹性变形。
一旦弹力超过弹簧的预紧力,气门阀就开始移动。
同样,由于气缸中存在气压,气缸压力与气门弹簧对排气门的偏压力具有相同的作用,都阻碍气门打开,导致气门阀迟开。
由于上述原因,气门阀的实际打开时间晚于理论时间,而实际的开启时间早于理论时间,导致冲击力强,落座速度快,加剧了机构的振动、噪音和磨损。
缓冲部分的上升段和下降段的高度通常是相同的。
汽车发动机凸轮型线的缓冲部分的高度范围在0.2mm-0.4mm。
带挺柱配气机构机构的缓冲部分的高度通常为0.02mm。
根据不同发动机的速度和稳定性,不带挺柱的配气机构缓冲部分的末端运动速度小于0.3m/s,高速发动机的配气机构缓冲部分的末端运动速度应在此基础上适当减小,以免对阀门造成过多冲击,带有液压气挺柱的可以进一步降低缓冲段的末端运动速度,可以根据实际情况进行调试,以使气门阀平稳落座。
第二节 配气机构运动学和凸轮型线设计

第二节 配气机构运动学和凸轮型线设计一、平底挺柱的运动规律大多数挺柱是平底形式。
而且无论是何种挺柱形式,在凸轮加工时一般也都需要运用平底挺柱的运动规律,因此先重点研究平底挺柱的运动规律。
平底挺柱运动关系简图如图5-9所示。
因为速度三角形与AOB ∆相似所以 AOr AB h c t ω= ,ct e h ω= 又因为 ct c c t t t h dtd d dh dt dh h ωϕϕ'=== (5-8) 所以 c t c he ωω'=, t h e '= (5-9)从以上的推导可以看出,当采用平底挺柱时,挺柱凸轮的接触点与挺柱轴线的偏心距值就等于平底挺柱的几何速度值(mm/rad )。
因此,设计时为保证接触点不落在挺柱底面之外,平底挺柱的底面半径要大于最大偏心距,也就是在数值上要大于挺柱的最大几何速度max⎪⎪⎭⎫ ⎝⎛ctd dh ϕ。
另外,由rr r h v OA r OB v c t t c t ωω=+→=0 得 ()c t t h r v ω+=0 (5-10) 式中,t v 是挺柱相对凸轮表面的滑动速度,或者是接触线沿凸轮表面的移动速度c v i 与沿挺柱表面的移动速度it v 之差。
二、凸轮外形与平底挺柱运动规律间的关系设接触点A 沿挺柱表面的移动速度为it v ,接触点A 沿凸轮轴表面的移动速度为ic v 。
则c t cc t t i h dtd d h d dt h d dt de v ωϕϕ''='='==t (5-11) 如图5-10所示,假设ρ为接触点A 的曲率半径,c c d ϕϕ≈∆,则点A 沿凸轮表面移动的速度为c c cc c c c icd dl dt d d dl dt A dA v ρωωϕϕϕ====21 (5-12) 则挺柱相对凸轮表面的滑动速度为()c t c t c it ic t h r h v v v ωωρω+=''-=-=0 (5-13)图5-9 平底挺柱运动关系简图 图5-10接触点变化示意图所以凸轮各点的曲率半径ρ为t t h h r ''++=0ρ设计中要保证曲率半径不能为负值,且min ρ应大于3mm ,以保证较小的接触应力。
柴油机高次方配气凸轮型线的动力学优化设计

柴油机高次方配气凸轮型线的动力学优化设计杨小华!俞水良!胡青!冯迎霞"同济大学机械学院!上海!""$$%#摘要!本文基于单质量动力学模型!采用非线性规划法!对柴油机配气凸轮型线进行了以丰满系数为目标函数"以凸轮与挺柱间接触应力等为约束条件的动力学优化设计及探讨#文中选择了高次方凸轮!并以%&’!#"()柴油机为例!给出了详细的优化计算结果$关键词!柴油机%配气机构%凸轮型线%动力学优化设计中图分类号!*+#!!文献标识码!,文章编号!%""-.-#-!/!""#0"!.""#"."#收稿日期&!""$’%!’%1%前言配气机构是内燃机的重要组成部分!其设计合理与否直接关系到整机工作的可靠性"耐久性!并影响整机的动力性能"经济性能"排放性能$内燃机配气机构的弹性变形将引起气门的激烈振动!严重时使气门产生(飞脱)和(反跳)现象!破坏气门机构的正常运行$配气凸轮型线优化设计的任务就是在确保配气机构能可靠工作的前提下寻求最佳的凸轮设计参数$凸轮型线的设计已从静态设计"动态设计发展到动力学优化设计2%3!4!后者考虑配气机构的弹性变形!可更精确地描述配气机构的运动和受力情况!并统一考虑机构动态参数与凸轮型线!从而实现凸轮型线的最优化设计$高次方凸轮是应用比较广泛的一种整体式函数凸轮!挺柱升程曲线为统一的高次多项式!因而加速度曲线是连续函数!没有突变!机构平稳性较好$本文采用单质量动力学模型用高次方凸轮进行了优化设计研究!并以%&’!#"()柴油机为例!给出了优化计算结果!并与原型线进行了比较$!凸轮型线的选择*%+凸轮缓冲段型线的选择缓冲段型线选择余弦曲线方程!其挺柱*从动件+升程方程为&!/!5"!"/%.6789"!:!!"55!"!!!!"*%+式中&!/!5’缓冲段挺柱的升程!下同%!"’缓冲段高度!下同%!’凸轮轴转角!下同%!"’缓冲段半包角!下同$*!+凸轮工作段型线的选择实践中发现%&’!#"()柴油机在配气机构可靠性方面尚需改进$工作段型线种类较多3而高次方函数凸轮在可靠性方面有优势$故本设计中!凸轮工作段型线选择高次方函数曲线方程!其挺柱升程表达式为&!/#5;$"<$%#%&$’#’&$(#(&$)#)*!+其中&#;%./!.!"5:!*!!"!!!!*式中&%+!!’,(")作为设计变量,!,-/#%3#!3#$5.;/’/(/)5*%!0为工作段半包角%而1""1%"1’"1("1)等为待定系数!可通过以下五个边界条件由=>?88.)7@A>B 消去法求解确定&工作段挺柱始点升程&!9#5C #;%;!"*$+工作段挺柱始点速度&29#5C #;%;2"*#+工作段挺柱始点加速度&39#5C #;%;"*1+工作段挺柱始点升程的三阶导数&!9$59#5C #;%;"*&+挺柱最大升程&!9#5C #;";!"<!45#*D +以上式中&!9#5’工作段挺柱的升程!下同%29#5’工作段挺柱速度!下同%2"’缓冲段末端挺柱速度!下同%39#5’工作段挺柱加速度!下同%!E>F ’工作段内挺柱最大升程3下同$$配气凸轮机构的动力学模型考虑到完全体现配气机构特点的计算系统的复杂性!为便于计算!本文采用单质量动力学计算模型2$4$如图%所示!它是考虑阻尼"气门间隙"气缸内燃气作用力等因素后形成的计算模型!当量质量的运动微分方程及初始条件为&6#!A !7A !!;.*898%0A 7A !.9191:+791-#9!0<8!"%!& !!#$"’%!$&%!&%(&’!)!"")*’*!!)!"")""+#式中$(%当量质量&包含气门质量及其它传动件换算到气门处的质量’"%凸轮轴旋转角速度’’%!&%气门升程&下同’)()*%分别为内阻尼系数和外阻尼系数’+%配气机构的刚度&代表整个传动链的弹性&可通过实测或计算得到’+,%气门弹簧刚度’"%!&%当量凸轮升程也即气门的理论升程&等于-!. %!&/""&其中-为摇臂比&""为气门间隙’下同’0"%气门弹簧预紧力’%%进(排气指数&进气时取"&排气时取,’0&%!&%气缸内气体压力’!""%气门刚开启时凸轮的转角)运用-./01’2.334法对此二阶微分方程求数值解可求出’%!&(*’5*!&从而回代"(#式也求得*!’5*!!&这样就确定了气门的运动规律*#动力学优化设计模型及其求解策略",#目标函数和约束条件内燃机各项性能指标的要求&使得配气凸轮型线的设计成为多目标规划问题*即要求充气性能达到最佳&机构工作平稳性好&振动小&不出现飞脱和反跳&凸轮的最小曲率半径不应太小&以保证凸轮的使用寿命等*由于各目标相互间的矛盾和牵制&通常情况下最优解并不存在*同时&由于设计的目标函数与约束条件中会包含自变量的非线性函数&因此该规划问题又是非线性规划问题&使得求解尤为困难*考虑到上述情况&本文从保证气门的充气性能尽可能大的角度出发&取凸轮型线的丰满系数#作为优化的目标函数&其它方面性能指标作约束条件处理&从而把多目标非线性规划问题转化为单目标非线性规划问题&采用极小化优化方法求解*优化设计的目的是满足约束条件的前提下使$尽可能大&故将目标函数在数值上取为$的负值&建立动力学优化设计模型式如下$67/0"1#)’%"1#","# $"1#),.648%."9.648’""-9+**9,9+229,9+339,9+449,&约束条件$0,):’:,!"0!):!’:!"0$);’;,!"0#);!’;!"0<)=’=,!"0>)=!’=!"0?);’:!!/0()=’;!!60+)8%!&’@%!&!"0,")-67/’-A!"0,,)B4648C’4648!"0,!)467/’B467/C!"0,$)BD E4FF C’D E4FF!"0,#)B4E4FF C’4E4FF!"0,<)B&C’&!"0,>)G H’BG H C!"","#式中$:,+;,(=,%设计变量的下限’:!(;!(=!%设计变量的上限’5(6%正整数’-A%凸轮型线最小曲率半径许用值’-67/%凸轮型线最小曲率半径’4648%气门最大加速度’B4648C%气门最大加速度许用值’467/%气门最小加速度’B467/C%气门最小加速度许用值’D E4FF%气门落座速度’BD E4FF C%气门落座速度许用值’4E4FF%气门落座加速度’B4E4FF C%气门落座加速度许用值’&%凸轮与挺柱间的接触应力’B&C%凸轮与挺柱间的接触应力许用值’G H%气门活塞间距离’BG H C%气门活塞间距离许用值*对各约束条件的含义的描述如下$0,I0(用以确定设计变量的取值范围及规律&并要求为偶数’0+用以控制机构不出现飞脱’0,"用以控制凸轮型线的最小曲率半径&最小曲率半径对凸轮与挺柱间的接触应力和可加工性等有很大影响’0,,最大正加速度&其对配气机构的运动规律(机构的振动(噪声(飞脱和机构工作的平衡性有很大影响’0,!I0,#用以控制气门最大负加速度(落座时速度!落座时加速度限制气门落座后反跳"%&’用以控制凸轮与挺柱间的最大接触应力不超过许用值"%&(用以控制气门活塞间距离不小于许用值#$!%优化模型的求解策略高次多项式凸轮挺柱升程曲线的幂指数!&"&#&$为正整数’为离散变量’对此类约束非线性规划问题的优化模型进行求解’一般可用网格法#但考虑到计算效率’本文采用离散复合形法)#*求解+它是在复合形法基础上发展起来的一种解离散变量约束最优化问题的直接法’其初始顶点可以是非可行点#寻优迭代过程是计算离散复合形各顶点的目标函数值’找出其中函数值最大的一点称最差点%&及除最差点外其它各点的形心%’+并以%&为基点’以()*’+%&为离散一维探索方向’进行离散一维探索’可有反射&扩张和压缩等过程’不断地丢掉最差点代之以目标函数值有所下降的一个新点’如此重复计算’使新的离散复合形不断地向约束离散最优点靠拢’直到满足计算精度为止#离散复合形法的计算程序框图见图!#’计算实例及分析按上述数学和优化设计计算模型’用,--语言编制了相关的计算程序’并在标定工况下对&(.!#"/0柴油机配气机构重新进行了探讨#新型线的优化计算结果与原型线的比较见表&#表&结果表明(与原型线相比’新型线所对应的排气表&&(.!#"/0柴油机动力学优化计算结果排气凸轮特征值!!!!原型线新型线1&23"&2(4!"2(!3&&"2’3#4"4.5678!2!&8&29&-!2’$-!2"9656789&(8($#-&#$!-&!3$.:6;;"2(#"2’"""567&&(#4($<5=>!!$!$3"8!&!!"8&"""?.5=>&"29$&$29!注!18机构平稳性系数".5678气门最大速度#5@A ""5678最大凸轮与挺柱间的接触应力BC6"?.5=>8气门活塞间最小距离#55$泵中!有!%&"’#%($%)%%)%!)%$*"+#!!&",#!)$!)%%)%!)%$*"-$由于辅射流泵出口与主射流泵吸液口相连!故有%&’!&&(%&.$)’!&)*%&/$考虑到所吸液体压力近似为"!+,%&"将上述&+$’"-$’".$’"/$四方程联立求解!可得出双级射流装置的基本性能方程($0$基本性能方程的分析"%$混合比由以上公式可得总混合比为%$%&$%$!%1$%1$!"%"$从该式可知$-$%)$-$!)即总混合比小于任一单一射流泵的混合比!假设$%&$!&"0!)总混合比可达到"0"$以下!符合植保机械和清洗机械的要求)&!#压强比由于!%2%!!!2%可得!.!%1!!3!%!!4567’!%)!!*即压强比高于任一单一射流泵的压强比!因而说明压力损失小!能量损失比单一射流要小)#实验结果与理论计算的比较由于射流嘴出口直径较小)加工困难)只有加工后实测数值作为实验参数)取主射流泵#%&!0%"’$0"8辅射流泵#!&$0+"’!0%"!得出的实验结果如表%!与理论计算对比!误差约为%"9左右)8结论由实验与理论方程可知!用串联方式连接射流泵!可使混合比进一步下降!同时还可提高压强比!使得该装置更符合使用要求!并说明建立的数学方程模型是可行的)但是!由于试验条件所限!试验样本不多!需要进一步进行相关的研究)参考文献!:%;何培杰!吴春笃等0射流泵混药装置试验研究:<;0农业机械学报!!""%!"##$8-=+"0:!;王荣0植保机械理论与设计:<;0长春$吉林人民出版社!!""!0:$;陆宏圻0射流泵技术的理论与应用:<;0北京$北京水利电力出版社!%/./0*******************第一作者简介!李羊林!男!%/+$年生!江苏泰州人!博士研究生)研究领域%机械)已发表论文8篇)%编辑$滕召旗&表%实验结果#%#!!$!与理论误差$与理论误差!0%"$0+""088.%>!80/!0%9$0"9!0%"!0%""0+"!%>%+0#80-9.0!9$0"8$0+""0#!-%>$+0!3$0893%0!9$0"8!0%""0#++%>!$0$-0%9+0$9%上接第$#页&机构其丰满系数+时面值有所减小!因而流通性能有所下降,?值在合理范围!可满足机构平稳性要求,曲率半径在合理范围&正值4!55’负值小于3$""55#!表明凸轮是可加工的,气门与活塞间距在$55以上!两者不会相碰,气门的最大速度’最大加速度和落座速度有明显减小,凸轮与挺柱间接触应力的最大值明显减小)对%+@!#"AB 柴油机而言!实践中要求对其配气机构可靠性予以更多关注!尤其对其排气机构!流通性能稍有降低尚可接受!因此计算结果是令人满意的)图$’图#和图8分别给出了在动力学优化基础上所获得的%+@!#"AB 柴油机排气门的速度’加速度’凸轮与挺柱之间接触应力计算结果)由图可见!速度’加速度和接触应力曲线均连续!表明优化设计的排气机构未出现-飞脱.或-反跳.)排气门的速度+加速度+凸轮与挺柱之间接触应力曲线表现出不同程度的波动!这种结果是合理的)这一方面体现了配气机构确实存在弹性变形!另一方面与该柴油机在排气门开启时很高的排气压力&约%<C6$对排气门头部的作用力有关)对该柴油机的进气机构也进行了同样计算!也获得了满意的结果)限于篇幅!本文不再给出有关曲线图)+结束语本文选择了高次方凸轮!并基于柴油机配气机构单质量动力学模型!采用非线性规划法!编制了以丰满系数为目标函数+以凸轮与挺柱间接触应力+气门落座速度等为约束条件的动力学优化设计计算程序)结果表明!按上述数学和优化设计计算模型所编制的计算程序可以进行配气机构的动力学优化设计计算,以%+@!#"AB 柴油机配气机构为例进行的计算结果证实!与原型线相比!该柴油机采用新型线后其配气机构在可靠性方面有明显改进)参考文献!:%;李惠珍!高峰0配气凸轮型线动态优化设计:B;0内燃机学报!%//"),#*0:!;DE6FGHI)B0J0K L65MNFHF)B00D GNOPINQRPHG N5MEH5HFP6PNSF ST UHFHPNV 6EUSINPW5TSI V65OW6MH SMPN5NX6PNSF :A;0DGY6FVHO NF ZS5MRP6PNSF6E <HVW6FNVO [NPW C6I6EEHE 6FG \NOPINQRPHG CIS]VHOONFU M0!"/3%-0:$;尚汉冀0内燃机配气凸轮机构3设计与计算:<;0上海$复旦大学出版社!%/..0:#;刘惟信0机械最优化设计%第二版&:<;0北京$清华大学出版社!%//#0*******************第一作者简介%杨小华!男!%/+.年生!浙江江山人!讲师!硕士)研究领域%内燃机系统与机构优化+工作过程模拟)已发表论文$篇)%编辑$滕召旗&!!!!!!!!!!!!!!!!!!!!!!!!!!!!!!!!!!!!!!!!!!!!!!!!!!!!!!!!!。
增压柴油机配气相位与凸轮型线的优化

图 2 功 率 和 有 效 燃 油 消 耗率 对 比 曲线
发 动 机 转 透 ,’ n r mi
\ 赠嚣温察
转 速和 负 荷 的 变 化 而 变 化 。最 佳 的 配气 相 位 应 使 发 动机在 很短 的换 气 时 间 内充人 最 多 的新 鲜 空 气 , 并 使排气 阻力 最小 , 气 残 留量 最 少 _ 。发 动机 转 废 5 J
缸径 ×冲程/ m m
压缩 比
9 5×1 5 0 1 1 8:
2
每缸气 门数
进 气 方 式
连杆 长度/ m m
增压 中冷
10 7 l —弓・ —4—I 2
耗 高和配 气 机 构存 在 的 冲击 、 跳 问 题 , 优 化 配 反 从 气 相位和 改变 凸轮 型线 的角 度 着 手 , 合 发 动机 性 结
9 / 0 2 36 0
25 2o o 24 0 8 / 0 - 0
第一作者简介 : 雷基林 , 讲师 , 士研究生 , 究方 向: 博 研 内燃 机设计 与结构优化 ,・ a : ein i .o 。 Em i lji n em l i @s a l
注 :C 表示 发 动 机 油 轴转 角 。 。A
褂 雷 忙
童
轻微跳 动 , 能会造 成 凸轮 与挺 柱 问 的接 触 应 力增 可 大 以及 配 气 机 构 的振 动 加 剧 , 用 寿 命 下 降 等 影 使 响; 进气 门在 开启 和关 闭 时 及排 气 门在 关 闭时 均存 在很大 的波 动 , 成 气 门 与气 门座 的 冲 击 , 利 于 造 不 减小配 气 机 构 的振 动 和 噪 声 ; 气 门 的落 座 力 稍 排 大, 可能 加重 气 门和 气 门座 的磨 损 ; 气 门落 座 时 排
- 1、下载文档前请自行甄别文档内容的完整性,平台不提供额外的编辑、内容补充、找答案等附加服务。
- 2、"仅部分预览"的文档,不可在线预览部分如存在完整性等问题,可反馈申请退款(可完整预览的文档不适用该条件!)。
- 3、如文档侵犯您的权益,请联系客服反馈,我们会尽快为您处理(人工客服工作时间:9:00-18:30)。
一、绪论1.1引言配气机构是内燃机的重要组成部分。
它的功能是实现换气过程,即根据气缸的工作次序,定时地开启和关闭进、排气门,以保证气缸吸入新鲜空气和排除燃烧废气。
一台内燃机的经济性能是否优越,工作是否可靠,噪音与振动能否控制在较低的限度,常常与其配气机构设计是否合理有密切关系。
设计合理的配气机构应具有良好的换气性能,进气充分,排气彻底,即具有较大的时面值,泵气损失小,配气正时恰当。
与此同时,配气机构还应具有良好的动力性能,工作时运动平稳,振动和噪音较小,不发生强烈的冲击磨损等现象,这就要求配气机构的从动件具有良好的运动加速度变化规律,以及合适的正、负加速度值.内燃机配气凸轮机构是由凸轮轴驱动的,配气机构的这些性能指标很大程度上取决于配气凸轮的结构。
本文从改进配气凸轮型线设计角度来进行配气机构优化设计研究。
1.2配气凸轮型线设计凸轮机构从动件滚子直接与凸轮轮廓而接触并产生相对运动,利用滚子的滚动以减小因相对运动产生的摩擦与磨损,以提高机构的寿命和可靠性。
在设计凸轮型线时首先满足从动件的运动规律。
从动件运动规律的应满足下列要求:①应保证能获得尽量大的时间断面值,气门开启和关闭要快以求在尽可能小的凸轮转角内气门接近全开位置。
②应保证配气机构各零件所受的冲击和振动尽可能小,以求大得配气机构工作得平稳性和可靠性。
为满足以上从动件的设计要求,一条良好的凸轮型线应能保证:①适宜的配气相位。
使配气相位符合发动机的特性要求,如功率、油耗、怠速及最大功率和扭矩时的转速等,保证配气机构获得尽可能大的时面值或丰满系数,以提高内燃机的充气效率和降低残余废气系数。
②使发动机具有较好的充气性能。
由于发动机的形式不同,需要的气门运动规律也就有所不同。
例如球形燃烧室内燃机希望进气门尽快开启使空气尽早流入;而高速汽油机希望进气开始时缓慢一些,以便更好的利用惯性充气。
③适宜的从动件加速度。
加速度不宜过大或者带突变,加速度曲线应尽可能连续。
负加速度曲线能和气门弹簧力相适应,正加速度大则增加对配气机构刚度要求。
④气门离座及落座时,要具有恒定的速度,称之为初速度及终速度。
这个速度如果对高将对气门落座不利;反之,则会增加过渡段长度,这样不容易保证配气相位的精确。
⑤最大升程时,速度必须为零。
⑥要适应发动机总布置要求的尺寸限制。
、图1.2凸轮外形及缓冲段1.2.1缓冲段设计配气凸轮所对应的挺柱升程曲线在上升段及下降段各有一缓冲段。
如图1.2所示,从动件在凸轮外形上的B点开始升起,在B′点停止。
设计中应保证气门最迟在A点开启,最早在A′点落座。
设计缓冲段升程曲线,需要从三个基本参数的选择着手:缓冲段包角α,缓冲段全升程h 和缓冲段末端的速度V。
在这三个参数中,在缓冲段全升程h的选定是比较关键的。
在选h时,重要的一点是必须考虑到配气结构的弹性变形。
缓冲段包角α的选择应与h的选取相配合。
如果h 增大,α也要相应的增大。
缓冲段末端的从动件速度V既影响到缓冲段的形态又影响到基本段的形态,因而是一个比较重要的参数。
当缓冲段速度降低之后,工作段的正加速增大了,而凸轮是与摇臂上的圆弧接触,对气门运动能起一定缓冲作用。
故可将凸轮缓冲段的速度减小,以减轻接触时的冲击。
上升缓冲段与下降缓冲段的设计可以是相同的,也可以是不同的。
为了是气门开启较快而关闭时落座速度又不致过大,本设计将上升缓冲段包角取得较短,而将下降缓冲段包角取得较长。
本设计采用的是正弦一等速型缓冲曲线,该曲线使气门开启与落座平稳,并大大减小了气门冲击与噪声,曲线方程如下:1)摇臂摆角升程段的缓冲段正弦段:]//sin /[1111la ππϕψββψ)(N N -= ββψπϕω1111la /]/cos 1[)(N N -= ββψπϕπε211121la //sin )(N N = 匀速段:ψβψϕψla111lb )0.1/(1/+--=N N )( ])1/[(*11lb 1βψω-=N N 0.0=ε2)摇臂摆角的回程段匀速段:][4312)(ββββϕθ++--= ψβψθψa 2222b 20.1/1/+--=)()(N Nβψω2a 22/*0.2N —= 0.0=ε 正弦段:][b2431a 2)(βββββϕθ+++--= ]//sin /[2222a 2N ππθθψββψ)(-=N ]//cos /[222222a 2βββψπθω)(N N N --= ββψπθπε222222a 2//sin )(N N = 1.2.2工作段设计 配气凸轮升程曲线中的主要部分是工作段,故凸轮的分类与定名也是参照工作段升程曲线或加速度曲线的类型。
早期的配气凸轮,其廓形一般是由几种圆弧段或直线段组成的,这类几何形状简单的凸轮可成为几何凸轮。
几何凸轮的主要缺点是加速度曲线有间断,对配气结构工作平稳性有不利影响,其优点除结构简单外,主要是丰满系数大,对提高充气性能有利。
比较几种型线:①复合正弦抛物线型凸轮的挺柱运动规律由三段组成。
第一段φ1为正加速度段,加速度曲线由1/2波正弦曲线构成。
第二段φ2为负加速度段的一小部分,加速度曲线由1/4波正弦曲线构成。
第三段}3为负加速度的基本部分,加速度曲线由抛物线构成。
凸轮型线设计中,如果正加速度段必,越小,则挺柱开始阶段上升越快,时值面也就越大。
对于刚度较小的配气机构,特别是下置式凸轮机构,由于正加速度值的急剧增大,容易使气门产生跳动或振动,增加配气机构的噪音和磨损。
对于挺柱的升程、速度、加速度、凸轮的最小曲率半径、时值面、丰满系数等参数应进行多方案设计计算,寻求最优设计方案。
这种凸轮型线的从动件升程丰满系数较大,但高速动态性能不好,加速度曲线不连续,附加冲击载荷较大,只适合低速发动机,其特点是在低速时充气性能较好。
②FB2型凸轮所对应的加速度曲线,是由复合正弦凸轮加速度曲线和等加速度曲线综合而成的。
原复合正弦凸轮的加速度曲线在正加速度段为半波正弦曲线,在负加速度段为1/4波正弦曲线;而FB2型凸轮的加速度曲线,则是在正加速度段将半波正弦曲线中插进一段等加速度段,而将负加速度段改成由两段组成:第一段是1/4波正弦曲线,第二段为等加速度曲线。
这种型线的特性对高速发动机是比较适用的,但是,在接点处有脉冲,易产生冲击。
③N次谐波型用简化的动力学模型将升程曲线展开为有限项的级数,而把高阶简谐分量接近零,从而减少机构的共振。
这种凸轮型线的公式推导比较简单,设计参数比较好调整。
但这种凸轮仍不能满足高速发动机的要求。
因为这种凸轮的挺柱升程丰满系数较小,气门的落座速度较大,气门冲击较大。
使气门落座速度值减小,挺柱升程丰满系数更小,充气性能恶化。
④高次多项式型的项数和幂次的选取有一定的任意性。
但是丰满度和重启性能较差。
综合以上几种典型型线的特点,为了保证配气机构进气充分,排气干净,具有较高的充气效率,减小配气噪声,本设计提出了一种非对称的分段函数组合凸轮,该凸轮的主要特点是运动规律的连续性,加速度曲线连续,因此不会引起惯性力的突变。
工作段采用非对称设计,与对称型凸轮相比,它可以增大气门的开启时间,改善充气,还可以更好的利用排气能量,把气门的开启的速度设计成大于气门关闭的速度。
由于非对称凸轮型线设计的重要前提是为改善配气机构的动力性能;对于非对称运动规律,设计中先设计上升段,然后设计下降段,并且满足如下条件:1)上升段与下降段交界处升程曲线连续。
2)在交界处速度曲线连接,且皆为零。
3)在交界处加速度曲线联系,且达到最大负加速度。
经过计算可得出新的凸轮型线根据数据可画出凸轮型线示意图(1.2.2)图1.2.2凸轮型线示意图二、总结论文通过研究以往的内燃机配气机构凸轮型线结构和凸轮型线设计理论,提出并构造了新型配气凸轮型线。
该型线能保证配气机构获得尽可能大的时面值或丰满系数,以提高内燃机的充气效率和降低残余废气系数,实现了下降段与上升段实现了非对称连接,以获得较低的气门落座速度。
加速度曲线光滑连续、无突变,且正负加速度绝对值限定在允许范围内,负加速度段对气门弹簧适应性,同时具有较小的表面接触应力,以保证配气机构能平稳、低噪声、可靠地工作。
参考文献[1]付光琦等,高次方多项非对称高速车用柴油机配气凸轮型线设计,内燃机学报Vol. 19 (2001) No. 1, P26-28[2]尚汉冀,配气凸轮机构设计与计算,第一版,1988.4,复旦大学出版社,p27-32[3]石永刚,徐振华,凸轮机构设计,第一版,1989,上海科学技术出版社,p135-137[4]毛琦波等,配气凸轮优化设计综述,江苏理工大学学报,1997.5,第18卷第3期,p27-31[5]吴建华,汽车发动机原理,第一版,2008,机械工业出版社[6]陈家瑞,汽车构造,第二版,2006,机械工业出版社,P79-101[7]徐其龙,影响柴油机发展的相关因素及对策.小型内燃机,1995(2): 4-9[8]翟爽.高速柴油机配气机构优化设计方法与配气凸轮型线设计软件研究.〔硕士学位论文〕长沙:湖南大学,2002[9]马永有,黄亚宇,初学丰.内燃机配气机构凸轮型线设计方法研究.昆明理工大学学报,1999 (4):15-20[10]杨小华,俞水良,胡青,冯迎霞.柴油机高次方配气凸轮型线的动力学优化设计.机电工程技术,2004 (2): 40-43[11]袁银南.顶置凸轮轴式配气机构设计的若干问题.内燃机工程,1999 (2): 3945以下无正文仅供个人用于学习、研究;不得用于商业用途。
For personal use only in study and research; not for commercial use.仅供个人用于学习、研究;不得用于商业用途。
Nur für den persönlichen für Studien, Forschung, zu kommerziellen Zwecken verwendet werden.Pour l 'étude et la recherche uniquement à des fins personnelles; pas à des fins commerciales.仅供个人用于学习、研究;不得用于商业用途。
толькодля людей, которые используются для обучения, исследований и не должны использоваться в коммерческих целях.For personal use only in study and research; not for commercial use。