4-3机械制造技术基础 课件
合集下载
机械制造技术基础通用课件

02
03
04
定义
车削加工是一种通过工件和刀 具的相对运动来切除多余材料
的方法。
适用范围
适用于加工圆柱形、圆锥形等 回转体零件。
加工特点
具有较高的加工精度和表面质 量,适用于粗加工和精加工。
应用实例
车削加工可用于加工轴、齿轮 等机械零件。
铣削加工
定义
铣削加工是一种通过刀具的旋 转和工件的移动来切除多余材
01
02
03
量具的种类与使用
讲解量具的种类和用途, 包括卡尺、千分尺等,以 及使用量具的注意事项。
检具的设计与制作
讲解检具的设计原则和方 法,以及制作检具的过程。
量具与检具的选用
根据检测需求,选择合适 的量具和检具,包括量具 的精度等级、检具的制作 材料等。
机械制造质量管理与控制
质量管理体系与质量控制流程
刀具与夹具
刀具的材料与结构
讲解刀具的材料的选用,包括高速钢、硬质合金 等,以及刀具的结构,如尖刀、铣刀等。
夹具的设计与使用
讲解夹具的设计原则和方法,以及使用夹具的注 意事项,包括夹具的安装、工件的定位等。
刀具与夹具的选用
根据加工需求,选择合适的刀具和夹具,包括刀 具的锋利度、夹具的精度等。
量具与检具
机械制造工艺基础
工艺规程与工艺流程
工艺规程
工艺规程是规定零件制造工艺过程和操作方法的工艺文件,是机械制造过程中 重要的指导性文件。
工艺流程
工艺流程是指制造过程中原材料转化为成品的过程,包括各工序的顺序、内容、 方法等。
加工精度与加工误差
加工精度
加工精度是指零件加工后的实际几何参数与理想几何参数的符合程度,包括尺寸 精度、形状精度和位置精度。
机械制造技术基础课件(第1章)PPT课件

夹具
钻床夹具
铣床夹具
12
第12页/共16页
装配
装配
13
第13页/共16页
第一章 导论
一、制造业与机械制造技术 二、机械制造(冷加工)学科的范畴、研究内容 及特点
零件的机械加工工艺过程是研究如何利用切削的原理使
工件成形而达到预定的设计要求(尺寸精度,形状、位置精度和表面质量 要求)。
机器的装配工艺过程是研究如何将零件或部件进行配合和
3.掌握拟订机械加工工艺规程和机器装配工艺规 程拟订的基本知识及有关计算方法,具有拟订 中等复杂程度零件机械加工工艺规程的能力;
4.掌握机械加工精度和表面质量的基本理论和基 本知识,初步具备分析解决现场工艺问题的能 力;
5. 了解先进制造技术和先进制造模式的 发展概况,初步具备对制造系统、 制造模式选择决策的能力。
简介
课程宗旨
➢ 掌握机械制造技术的基础知识、基本理论和基本方法。 ➢ 通过课程学习及实验、生产实习及课程设计等实践环节 训练,培养分析和解决机械制造工程问题基本能力。
➢ 了解机械制造领域的最新成就和发展趋势。
主要内容
➢ 导论(1学时)
➢ 制造工艺装备(15学时)
➢ 切削过程及其控制(8学时)
➢ 机械加工质量分析与控制(10学时)
连接,使之成为半成品和成品,并达到要求的装配精度的工艺过程。
14
第14页/共16页
三、先进制造技术的特点及发展趋势
特征:1.物资流、信息流、资金流 2.敏捷制造、可持续发展 3.技术与管理的结合
发展趋势:自动化、集成化、和智能化 高精度方向 可持续发展
•规模效益、精良生产
四、本课程的内容和学习要求
3
第3页/共16页
机械制造技术基础-课件

车刀在结构上可 分为整体车刀、焊 接装配式车刀和机 械夹固刀片的车刀。 如图15、16所示。
图15
图16
(2)孔加工刀具
孔加工刀具一般 可分为两大类:一 类是从实体材料上 加工出孔的刀具, 常用的有麻花钻、 中心钻和深孔钻等; 另一类是对工件上 已有孔进行再加工 用的刀具,常用的 有扩孔钻、铰刀及 镗刀等。
在法平面参考系中,只需标注γn 、 αn 、 κr 和λs四个角度即可确 定主切削刃和前、后刀面的方位。在假定工作平面参考系中,只 需标注γf 、αf 、γp 、 αp 四个角度便可确定车刀的主切削刃和前、 后刀面的方位。
四、刀具的工作角度
在实际的切削加工中,由于刀具安装位置和进给运动的影响,上 述标注角度会发生一定的变化。角度变化的根本原因是切削平面、 基面和正交平面位置的改变。以切削过程中实际的切削平面Ps、基 面Pr和主剖面P0为参考平面所确定的刀具角度称为刀具的工作角度, 又称实际角度。
(6)刀尖 主切削刃和副切削刃连接处的一段刀刃。它可以是小 的直线段或圆弧。
具体参见切削运动与切削表面图和车刀的组成图。其它各类刀具,
如刨刀、钻头、铣刀等,都可以看作是车刀的演变和组合。
刨刀
图4
钻头
(二)刀具角度的参考系
为了确定刀具切削
部分各表面和刀刃的空 间位置,需要建立平面 参考系。按构成参考系 时所依据的切削运动的 差异,参考系分成以下 两类:
2、车刀安装偏斜对工作角度的影响
图12
当车刀刀杆的纵向轴线与进给方向不垂直时,将会引起 工作主偏角κre和工作副偏角κre‘的变化,如上图所示。
(二)进给运动对工作角度的影响
1、横向 进给运 动对工 作角度 的影响
图13 车端面或切断时,加工表面是阿基米德螺旋面,如上图所示。因此,实际 的切削平面和基面都要偏转一个附加的螺旋升角μ,使车刀的工作前角γoe增 大,工作后角αoe减小。一般车削时,进给量比工作直径小很多,故螺旋升 角μ很小,它对车刀工作角度影响不大,可忽略不计。但在车端面、切断和 车外圆进给量(或加工螺纹的导程)较大,则应考虑螺旋升角的影响。
图15
图16
(2)孔加工刀具
孔加工刀具一般 可分为两大类:一 类是从实体材料上 加工出孔的刀具, 常用的有麻花钻、 中心钻和深孔钻等; 另一类是对工件上 已有孔进行再加工 用的刀具,常用的 有扩孔钻、铰刀及 镗刀等。
在法平面参考系中,只需标注γn 、 αn 、 κr 和λs四个角度即可确 定主切削刃和前、后刀面的方位。在假定工作平面参考系中,只 需标注γf 、αf 、γp 、 αp 四个角度便可确定车刀的主切削刃和前、 后刀面的方位。
四、刀具的工作角度
在实际的切削加工中,由于刀具安装位置和进给运动的影响,上 述标注角度会发生一定的变化。角度变化的根本原因是切削平面、 基面和正交平面位置的改变。以切削过程中实际的切削平面Ps、基 面Pr和主剖面P0为参考平面所确定的刀具角度称为刀具的工作角度, 又称实际角度。
(6)刀尖 主切削刃和副切削刃连接处的一段刀刃。它可以是小 的直线段或圆弧。
具体参见切削运动与切削表面图和车刀的组成图。其它各类刀具,
如刨刀、钻头、铣刀等,都可以看作是车刀的演变和组合。
刨刀
图4
钻头
(二)刀具角度的参考系
为了确定刀具切削
部分各表面和刀刃的空 间位置,需要建立平面 参考系。按构成参考系 时所依据的切削运动的 差异,参考系分成以下 两类:
2、车刀安装偏斜对工作角度的影响
图12
当车刀刀杆的纵向轴线与进给方向不垂直时,将会引起 工作主偏角κre和工作副偏角κre‘的变化,如上图所示。
(二)进给运动对工作角度的影响
1、横向 进给运 动对工 作角度 的影响
图13 车端面或切断时,加工表面是阿基米德螺旋面,如上图所示。因此,实际 的切削平面和基面都要偏转一个附加的螺旋升角μ,使车刀的工作前角γoe增 大,工作后角αoe减小。一般车削时,进给量比工作直径小很多,故螺旋升 角μ很小,它对车刀工作角度影响不大,可忽略不计。但在车端面、切断和 车外圆进给量(或加工螺纹的导程)较大,则应考虑螺旋升角的影响。
机械制造技术基础(课件全)
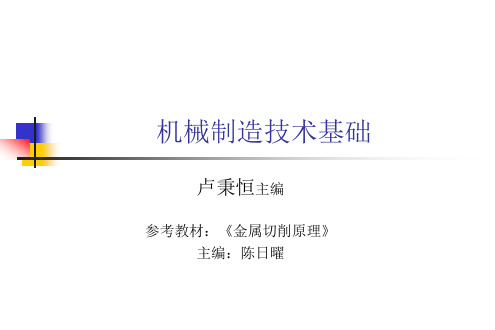
孔的加工工艺
1、位置度精度要求不高的中、小孔加工工艺 钻、铰 钻、扩、铰 2、位置度精度要求较高的中、小孔加工工艺 钻、镗 钻、扩、镗、(铰)。 3、直径较大孔(D>50 mm)变化分类
传统成形方法
传统成形加工
塑性加工方法
加温加压成型加工
机械加工方法
锻压、轧压、冷挤、 热挤等加工
铸造、粉末冶金等
切削加工:车、铣、钻、 镗等 磨削加工:磨、研磨、 抛光等
特种成形方法
特种成形方法
高能加工
电及化学加工
电火花、线切割、三束(离子、 电子、激光束)等加工
特点
1、成形运动:砂轮旋转;工件旋转或移动。 2、加工过程平稳。 3、磨削效率低。 4、易加工脆、硬材料。 5、磨削时产生大量热。
加工精度
一般磨削加工:精度—IT6~IT4;表面粗糙度—Ra1.25~0.01um。 精磨时:表面粗糙度—Ra0.1~0.008um.
适用范围
平面—平面磨床 内外圆柱面—内、外圆磨床 圆锥面、异形面—
一、车削加工
特点
1、成形运动:工件旋转;刀具相对工件移动。 2、易保证各加工表面间的位置精度。 3、切削过程平稳。 4、切削效率高。 5、刀具简单。
加工精度
普通车削加工:精度—IT8~IT7;表面粗糙度—Ra6.3~1.6um。 精车时:精度—IT6~IT5;表面粗糙度—Ra0.4~0.1um. 超精密车削:表面粗糙度—Ra0.04um
电解加工、电化学抛光等
成形方法按制造过程中质量M的变化分类
按由原材料制造成 零件的过程中,质 量M的变化分类
△M<0 (质量减少)
△M=0 (质量基本不变)
机械制造技术基础PPT.

• 图3.2 表示了 零件表 面的成 形过程。 母线和 导线统 称为发 生线
切削加工中发生线是由刀具的切削刃和工件间的相对运动得到 的,形成发生线的方法有以下四种:
①轨迹法 它是利用刀具作一定规律的轨迹运动对工件进行加 工的方法,图3.3(a)所示。轨迹法形成发生线时,需要一个独立的
成形运动。
②成形法 刀具的切削刃与所需要形成的发生线完全吻合,图 3.3(b)所示。成形法形成发生线,不需要成形运动。 ③相切法 它是利用刀具边旋转边作轨迹运动对工件进行加工 的方法,如图3.3(c)所示。采用相切法生成发生线时,需要两个相互
3.1.3机床的主要技术参数
3.1.3.1尺寸参数
• 机床的尺寸参数是指机床的主要结构尺寸。
例如,对于卧式车床,主参数(床身上工件最 大回转直径)和第二主参数(最大工件长度)外,有 时还要确定在刀架上的工件最大回转直径和主轴 孔内允许通过的最大棒料直径等
3.1.3.2运动参数
⑴主运动参数 ①主轴转速
对于回转运动的机床:
②主轴最低和最高转速(nmin、nmax)的确定
*
③有级变速时主轴转速序列 主运动的有级变速的转速数列一般采用等比数列 如某机床的分级变速机构共有级Z,其中n1=nmin、 nZ=nmax,Z级转速分别为: n1 , n2 , … , nj , nj+1 , … , nZ 各级之间满足等比数列关系,即: z nj+1= nj φ
nZ= n1φZ-1
④标准公比 国标规定标准公比值为1.06, 1.12,1.26,1.41, 1.58,1.78,2 共七个。 它们之间的关系见P60表3.5
⑵进给运动参数 大部分机床(如车床、钻床等)的进给
量用工件或刀具每转的位移(mm/r)表示。
机械制造技术ppt课件(完整版)

单击此处添加副标题
机械制造技术课件
汇报人:
目录
01 02 03 04 05 06
机械制造概述 传统机械制造技术 现代机械制造技术 机械制造工艺流程 机械制造质量控制 机械制造的未来发展
01
机械制造概述
机械制造的定义
机械制造是将原材料转化为成品的生产过程。 机械制造包括产品设计、工艺设计、加工制造、检测和质量控制等环节。 机械制造广泛应用于各个领域,如航空、汽车、机床等。 机械制造的核心目标是提高生产效率、降低成本、保证产品质量。
05
机械制造质量控制
质量控制的方法
统计过程控制 测量系统分析 过程能力分析 质量改进方法
质量检测的步骤
检测计划制定 检测工具准备 样品选择与制备 检测数据记录与分析
质量问题的解决
确定问题:明确机械制造过程中出现的质量问题
分析原因:分析问题产生的原因,如材料、工艺、设备等
制定措施:根据分析,制定相应的解决措施,如改进工艺、更换材料、 调整设备等 实施方案:按照制定的措施实施方案,并对实施过程进行监控和调 整
精密加工技术
定义:使用精密机床和精细加工刀具进行加工 分类:超精加工、镜面加工、纳米加工等 应用:航空航天、医疗器械、光学仪器等领域 发展趋势:高精度、高效率、智能化
04
机械制造工艺流程
零件的定位与装夹
定位原理:六点 定位原理,限制 工件的自由度
装夹方法:如三 爪卡盘、四爪卡 盘等,固定工件
定位元件:如V 形块、定位销等, 限制工件的自由 度
焊接工艺及 设备
焊接种类及 特点
焊接应用及 发展
切削加工技术
定义:利用切削 工具从工件上切 除多余材料的加 工方法
分类:车削、铣 削、钻孔、刨削、 磨削等
机械制造技术课件
汇报人:
目录
01 02 03 04 05 06
机械制造概述 传统机械制造技术 现代机械制造技术 机械制造工艺流程 机械制造质量控制 机械制造的未来发展
01
机械制造概述
机械制造的定义
机械制造是将原材料转化为成品的生产过程。 机械制造包括产品设计、工艺设计、加工制造、检测和质量控制等环节。 机械制造广泛应用于各个领域,如航空、汽车、机床等。 机械制造的核心目标是提高生产效率、降低成本、保证产品质量。
05
机械制造质量控制
质量控制的方法
统计过程控制 测量系统分析 过程能力分析 质量改进方法
质量检测的步骤
检测计划制定 检测工具准备 样品选择与制备 检测数据记录与分析
质量问题的解决
确定问题:明确机械制造过程中出现的质量问题
分析原因:分析问题产生的原因,如材料、工艺、设备等
制定措施:根据分析,制定相应的解决措施,如改进工艺、更换材料、 调整设备等 实施方案:按照制定的措施实施方案,并对实施过程进行监控和调 整
精密加工技术
定义:使用精密机床和精细加工刀具进行加工 分类:超精加工、镜面加工、纳米加工等 应用:航空航天、医疗器械、光学仪器等领域 发展趋势:高精度、高效率、智能化
04
机械制造工艺流程
零件的定位与装夹
定位原理:六点 定位原理,限制 工件的自由度
装夹方法:如三 爪卡盘、四爪卡 盘等,固定工件
定位元件:如V 形块、定位销等, 限制工件的自由 度
焊接工艺及 设备
焊接种类及 特点
焊接应用及 发展
切削加工技术
定义:利用切削 工具从工件上切 除多余材料的加 工方法
分类:车削、铣 削、钻孔、刨削、 磨削等
机械制造基础知识PPT课件

IT7~IT8 IT6~IT7
IT5
0.4~0.8 0.1~0.4
以亚泰老总黄来兴的一句话开始
现在的大学生都愿意在办公室画图,我们的主 要图纸都是购买或测绘的。
懂工艺的太少,我们是有图做不出来。
.
1
一 机械制造基础知识
第一节 第二节 第三节 第四节 第五节 第六节 第七节 第八节 第九节 第十节
机械的生产过程和工艺过程
零件的工艺分析
ห้องสมุดไป่ตู้
(重点)
毛坯的选择
元件装夹和定位基准的选择(难点)
加工
(续) 结构工艺性好
同一宽度尺寸的退刀槽, 使用一把刀具即可加工
加工面减小,节省工时, 减少刀损耗且易保证平面 度要求
内壁孔出口处平整,钻孔 方便,易保证孔中心位置
将阶梯轴的两个键槽设计 在同一方向上,一次装夹 即可对两个键槽加工
.
23
第三节 毛坯的选择
选择毛坯的基本任务是选定毛坯的制造方法及其 制造精度。
产品品种基本固定,但数 量少,品种较多,需要周期性 地轮换生产,大多数工作地点 的加工对象是周期性的变换。
产品品种固定,每种产品数
量很大,大多数工作地点的加工
的对象固定不变。例如,汽车、
轴承制造等一般属于大量生产。
.
10
表1-4 各种生产类型工艺过程的主要特点
生产类型 工艺特征
工件的互换性
单件生产
.
3
二 工艺过程及其组成
1.工艺过程
把生产过程中改变生产对象的形状、尺寸、相 对位置和物理、力学性能等,使其成为成品或半成品 的过程称为工艺过程。
工艺过程可根据其具体工作内容分为铸造、 锻造、冲压、焊接、机械加工、热处理、 表面处理、装配等不同的工艺过程。
机械制造技术基础课件第一章

要是发生形状变化,而质量基本不变。 • 1.3△m>0材料累积工艺
△m>0, 20世纪80年代出现额快速成形技术,在成形中通过 材料获得所需形状,这种造形方法又称为材料累加法。
1.2 机械加工方法
1.车削
2.洗削
机
3.刨削
械 加
4.钻削和镗削
工
5.齿面加工
方
6.复杂曲面加工
法
7.磨削
8.特种加工
1.2 机械加工方法
机械加工方法
第一章
机械加工方法
1.1 零件的成形方法 1.2 机械加工方法
1.1 零件的成形方法
• 第一节零件的成形方法 • 1.零件成形方法
• 1.1△m<0材料去除工艺 △m<0, 传统切削加工方法,包括磨料磨削、特种加工等, 再制造过程中通过材料逐渐被切削而获得需要的几何形状。
• 1.2△m=0材料成形工艺 △m=0,铸造、锻造及模具成形工艺中,在成形前后,材料主
1.2 机械加工方法
逆铣时,铣削分力F纵与进给方向相反, F纵的作用始终是 使丝杠螺纹右侧面贴紧螺母,不会产生工作台窜动现象,能
够保证工作台实现平稳进给。
3.刨削(自学) 4.钻削和镗削(自学) 5.齿面加工
齿轮加工机床的种类繁多,构造各异,加工方法也各不相同, 按齿面加工原理来分,有范成法和成形法。
•
安全象只弓,不拉它就松,要想保安 全,常 把弓弦 绷。20.10.2406:37:4306:37Oc t-2024- Oct-20
•
加强交通建设管理,确保工程建设质 量。06:37:4306:37:4306:37Saturday, October 24, 2020
•
安全在于心细,事故出在麻痹。20.10.2420.10.2406:37:4306:37:43October 24, 2020
△m>0, 20世纪80年代出现额快速成形技术,在成形中通过 材料获得所需形状,这种造形方法又称为材料累加法。
1.2 机械加工方法
1.车削
2.洗削
机
3.刨削
械 加
4.钻削和镗削
工
5.齿面加工
方
6.复杂曲面加工
法
7.磨削
8.特种加工
1.2 机械加工方法
机械加工方法
第一章
机械加工方法
1.1 零件的成形方法 1.2 机械加工方法
1.1 零件的成形方法
• 第一节零件的成形方法 • 1.零件成形方法
• 1.1△m<0材料去除工艺 △m<0, 传统切削加工方法,包括磨料磨削、特种加工等, 再制造过程中通过材料逐渐被切削而获得需要的几何形状。
• 1.2△m=0材料成形工艺 △m=0,铸造、锻造及模具成形工艺中,在成形前后,材料主
1.2 机械加工方法
逆铣时,铣削分力F纵与进给方向相反, F纵的作用始终是 使丝杠螺纹右侧面贴紧螺母,不会产生工作台窜动现象,能
够保证工作台实现平稳进给。
3.刨削(自学) 4.钻削和镗削(自学) 5.齿面加工
齿轮加工机床的种类繁多,构造各异,加工方法也各不相同, 按齿面加工原理来分,有范成法和成形法。
•
安全象只弓,不拉它就松,要想保安 全,常 把弓弦 绷。20.10.2406:37:4306:37Oc t-2024- Oct-20
•
加强交通建设管理,确保工程建设质 量。06:37:4306:37:4306:37Saturday, October 24, 2020
•
安全在于心细,事故出在麻痹。20.10.2420.10.2406:37:4306:37:43October 24, 2020
机械制造技术基础 PPT课件

12
1.2机械制造业的发展及其在国民济中的地位
新制造模式与传统制造模式比较举例
CE并行工程是对产 品及相关过程(制造 过程和支持过程)进 行并行、一体化设计 的一种系统化的工作 模式。这种工作模式 力图使设计者从一开 始就考虑到产品全生 命周期中所有因素, 以最大限度地缩短产 品开发周期,减少设 计失误。
因为制造技术是制造企业的技术支柱,是制造企业持续 发展的根本动力。所以机械制造技术是机械制造业的技 术支柱,是机械制造企业持续发展的根本动力。 “机械制造技术基础” 其主要目标,同学们通过本 课称的学习,掌握有关机械制造技术的基础知识、基本 理论和基本方法。通过本课程的学习及相关实验练习生 产实习及课程设计等实践性教学环节的训练,使学生具 备具备分析和解决有关机械制造问题的基本能力。
生产过程 • 制造过程 生产财富 • 产品
是完成制造活动所需的一切手段的总和: 制造技术: •运用一定的知识和技能, •操纵可以利用的物质和工具, •采取各种有效的方法等。
制造技术是制造企业的技术支柱,是制造企业持续发展的根本动力。 美国国家生产力委员会所作的一项调查表明,在企业生产力构成中, 制造技术的作用约占62% 。
7
1.2机械制造业的发展及其在国民经济中的地位
作坊式手 工劳动生 产方式
近代生产 方式
大批量生 产方式
多品种小 批量生产 方式
新制造哲 理于生产 模式
机械制造业的发展
8
1.2机械制造业的发展及其在国民经济中的地位
近代生产方式
18世纪70年代 以瓦特改进蒸汽机为代表,引发了第一次工业革命,产生 了近代工业化的生产方式,手工劳动逐渐被机器生产所代 替,机械制造业逐渐形成规模。 19世纪中叶 电磁场理论的建立为发电机和电动机的产生奠定了基础, 从而迎来了电气化时代。以电力作为动力源,使机械结构 发生了重大的变化。与此同时,互换性原理和公差制应运 而生。所有这些使机械制造业发生了重大变革,并进入了 快速发展时期。
机械制造基础ppt课件

使用教材:
倪小丹等主编。《机械制造技术基础》[M],清华大学 出版社,07.3 参考教材:
1.张世昌等主编。《机械制造技术基础》[M], 高教出版社, 2008.12 2.王启平主编,《机械制造工艺学》[M], 哈尔滨工业大学出 版社,2002. 3.陈日曜主编。《金属切削原理》[M],机械工业出版社,1993.
第1章 机械制造技术基础概述
(时间:4次课,8学时)
机械制造技术基础
主讲:刘曙光
地址:J8楼 409室 Tel: 81217(O) E-mail: sxlsg@ qq: 1187288926
课程介绍
《机械制造技术基础》是机械类各专业
本
课 程
的主干专业技术基础课程。通过本课程的教
+
n——主运动的转速(单位为r/min)
+ (2)进给量f 当主运动旋转一周时,刀具(或工件)沿进给方向上的位 移量f。进给量的大小也反映了进给速度(单位为mm/min)的大小,关系
为
1.1.2 切削加工成形运动和切削用量
+ 背吃刀量 车削时(单位为mm)是工件上待加工表面与已 加工表面间的垂直距离:
+ 1. 成形运动 + (1)主运动 直接切除工件上的切削层,以形成工件以加工表面的基本
运动。主运动的速度最高,消耗功率最大,机床的主运动只有一个。主 运动可以由工件或由刀具完成,车削时的主运动是工件的旋转运动。 + (2)进给运动 是指不断把切削层投入切削的运动。进给运动的速度较 低,消耗的功率较小。进给运动不限于一个,可以是连续的,也可以是 间歇性的。 + 切削时,工件上形成三个不断变化着的表面(见图1.4): + 已加工表面 指经切削形成的新表面,它随着切削运动的进行逐渐扩大。 + 待加工表面 指即将被切除的表面。它随着切削运动的进行,逐渐缩小, 直至全部切去。 + 过渡表面 指切削刃正在切削的表面。
机械制造技术基础课件-chapter4-section3new

(c)
single-blade boring tool
Advantage: simple, easy to make, general purpose, often used Can you tell the disadvantage?
Double blade boring tool
Material:
(4) core drill(IT10-IT11,Ra6.3~3.2)(扩孔钻)
Integral type
Carbide tipped type
Accuracy: IT10IT11
Roughness:6.3~3.2 m
Size: 10~ 80mm
Rotational type
(5) Counter boring drill (锪钻)
The main geometry for twist drill are: the helical angle (24~30) 螺旋角, the tip angle 2(118~130)锋角, rake angle 前角, relief angle 后角 and Chisel edge angle横刃斜角 Lip relief angle 钻缘 后角
1-head(头部);2-neck(颈部);3-cone transition (过渡圆锥);4- frond leading part(前导部) 5- cutting part (切削部);6- calibrating part(校准部);7-rear leading part(后导部);8-tail (尾部)
(6) Reamer(IT6~IT11,Ra 1.6-0.2) 铰刀
Working part
neck
shank
- 1、下载文档前请自行甄别文档内容的完整性,平台不提供额外的编辑、内容补充、找答案等附加服务。
- 2、"仅部分预览"的文档,不可在线预览部分如存在完整性等问题,可反馈申请退款(可完整预览的文档不适用该条件!)。
- 3、如文档侵犯您的权益,请联系客服反馈,我们会尽快为您处理(人工客服工作时间:9:00-18:30)。
图1
2)定位基准面和定位元件本身的制造误差所引起的定位误差,称 基准位置误差,即定位基准的相对位置在加工尺寸方向上的最大 变动量,以△jw表示。故如图2有:
△jw =△D+△d +△
图2
应注意的两个问题: ①只用调整法加工一批零件才产生定位误差,用试切法不产生定 位误差; ②定位误差是一个界限值(有一个范围)。
二、定位误差的计算
定位误差可按下述方法进行分析计算:一是先分别求出基准 位移误差和基准不重合误差,再求出其在加工尺寸方向上的矢量 和,即△d = △jb + △jw
另一种是按最不利情况,确定一批工件设计基准的两个极限 位置,再根据几何关系求出此两位置的距离,并将其投影到加工 尺寸上,便可求出定位误差。 常见定位方式定位误差计算 (1)以平面定位时的定位误差计算 平面度误差很小,定位副制造不准确误差可忽略,所以定 位误差主要由基准不重合引起。 (2)以圆孔定位时的定位误差计算 ① 工件孔与定位心轴无间隙配合,不存在定位副制造不准确误 差,定位精度较高。 ② 工件单向靠紧定位,如定位心轴水平放置,或在夹紧力作用 下单向推移工件靠紧定位。如图3
定位心轴水平放置
单向推移工件靠紧定位
图3 孔 Dmax=D+TD Dmin=D 轴 dmax=d
dmin=d- Td
A
O1Omax= OA-O1A=(D+TD)/2-(d- Td) /2 O1Omin= D/2-d/2
因基准位移造成的加工误差为:
△jw= O1Omax- O1Omin=(TD + Td) /2
(3)以外圆定位时的定位误差计算
工件在V形块上定位
① 工序尺寸以H1标注,其定位误差为: Δd1=O1O2=O1C-O2C d-Td 1 = Td 1 d 1 = sinα - 2 sinα 2 2 sinα 2 2 2
② 工序尺寸以H2标注,其定位误差为: Δd2=A1A2=A1O1+O1O2-A2O2 d Td 1 - d-Td = Td 1α + 1 = + 2 sinα 2 sin 2 2 2 2
制订夹具公差时,应保证夹具的定位、制造和 调整误差的总和不得超过零件公差的1/3。
第三节 定位误差分析
所谓定位误差,是指由于工件定位造成的加工面相对工序 基准的位置误差。因为对一批工件来说,刀具经调整后位置是 不动的,即被加工表面的位置相对于定位基准是不变的,所以 定位误差就是工序基准在加工尺寸方向上的最大变动量。 ①△总≤δ 其中△总为多种原因产生的误差总和,δ是工件被 加工尺寸的公差,△总包括夹具在机床上的装夹误差,工件在 夹具中的定位误差和夹紧误差,机床调整误差,工艺系统的弹 性变形和热变形误差,机床和刀具的制造误差及磨损误差等。 •②△定+ω≤δ 其中,ω除定位误差外,其他因素引起的误 差总和,可按加工经济精度查表确定。 •所以由①和②知道:△定≤δ-ω (是验算加工工件合格与 否的公式) • 或者:△定≤1/3δ(也是验算加工工件合格与否的公式)
③ 工序尺寸以H3标注,其定位误差为: Δd3=B1B2=O2B2+O1O2-O1B1 Td 1 d-Td Td 1 d = + 2 sinα - 2 = 2 sinα - 1 2 2 2
通过以上计算,可得出如下结论: 1) △dw ∝ △d,即定位误差随工件误差的增大而增大; 2) △dw 与V形块夹角α 有关,随α 增大而减小,但定位稳定性 变差,故一般取α =90°; 3) △dw与工序尺寸标注有关,本例中△dw2>△dw1>△dw3 。 注:这种按极限尺寸计算的定位误差通常偏大,与实际情况不完 全符合,这是因为加工中获得极限尺寸的概率很小。
一、定位误差及其产生的原因
1、定义:定位误差 是工件在夹具中定 位,由于定位不准 造成的加工面相对 于工序基准沿加工 要求方向上的最大 位置变动量。 2、定位误差的产生 的原因: 1) 定位基准与工 序基准不一致所引 起的定位误差,称 基准不重合误差, 即工序基准相对定 位基准在加工尺寸 方向上的最大变动 量,以△jb表示。 如图1所示.
三、保证加工精度实现的条件 若规定工件的加工允差为δ工件,以Δ夹具表示与采 用夹具有关的误差,以Δ加工表示除夹具外与工艺系统 其它因素(如机床误差、刀具误差、受力受热变形等) 有关的加工误差,为保证工件的加工精度要求,必须 满足误差计算不等式:
δ工件≥Δ夹具+Δ加工
此不等式即为保证加工精度的条件,称为采用夹具加工时 的误差计算不等式。 上式中的Δ夹具包括了有关夹具设计与制造的各种误差,如 工件在夹具中定位、夹紧时的定位夹紧误差、夹具在机床上安 装时的安装误差、确定刀具位置的元件和引导刀具的元件与定 位元件之间的位置误差等。