XN-691_Spec
CHIP Ferrite Bead BLM15XXXXXSN1X SPEC

Resistance element becomes dominant at high frequencies.
)
■ Unit Mass(Typical value) 0.001g
5.Marking
No marking.
MURATA MFG.CO.,LTD.
Spec.No.JENF243A-0018AD-01
Reference Only
P1/10
Chip Ferrite Bead BLM15□□□□□SN1□ Reference Specification
1.Scope
This Reference specification applies to Chip Ferrite Bead BLM15_SN series.
Remark
For high speed signal line
MURATA MFG.CO.,LTD.
Spec.No.JENF243A-0018AD-01
Reference Only
DC Resistance Impedance () (Note) ( max.) (at 100MHz,Under Standard Rated Current Testing Condition) (mA) Initial Values Values After Typical at 85℃ at 125℃ Testing 5~15 30±25% 60±25% 80±25% 120±25% 33±25% 60±25% 80±25% 120±25% 180±25% 220±25% 330±25% 470±25% 600±25% 10 30 60 80 120 33 60 80 120 180 220 330 470 600 1000 2200*
NI 67xx Pinout Labels for the SCB-68说明书

NOTE TO USERSNI 67xx Pinout Labels for the SCB-68Analog Output Modules/Devices Using the 68-Pin Shielded Connector BlockIf you are using an NI 67xx (formerly referred to as AO Series) analog output device or module with the SCB-68, you can print and attach a connector-specific pinout label to the cover of the connector block for easy connection reference. This document provides labels for the following models:•NI 6703•NI 6704•NI 6711•NI 6713•NI 6715•NI 6722•NI 6723•NI 6731•NI 6733•NI 6738•NI 6739Use the following label if you are connecting the SCB-68SCB-68 to the NI6703 model.Figure 1. NI 67032||NI 67xx Pinout Labels for the SCB-68 Note To UsersUse the following label if you are connecting the SCB-68 to the NI6704 model.Figure 2. NI 6704NI 67xx Pinout Labels for the SCB-68 Note To Users|© National Instruments|3Use the following label if you are connecting the SCB-68 to the NI6711/6731 models.Figure 3. NI 6711/67314||NI 67xx Pinout Labels for the SCB-68 Note To UsersUse the following label if you are connecting the SCB-68 to Connector0 of theNI6713/6722/6723/6733 models.Figure 4. NI 6713/6722/6723/6733 Connector 0NI 67xx Pinout Labels for the SCB-68 Note To Users|© National Instruments|5Figure 5. NI 6723 Connector 16||NI 67xx Pinout Labels for the SCB-68 Note To Usersmodels with the SHC68-68-A2 cable.1Figure 6. NI 6738/6739 Connector 0 with SHC68-68-A2 Cable1 Refer to Figure8 if you are using the NI 6738/6739 with the SH68-C68-S cable and NI PXIe-6738 Adapter or NI PXIe-6739 Adapter.NI 67xx Pinout Labels for the SCB-68 Note To Users|© National Instruments|7with the SHC68-68-A2 cable.1Figure 7. NI 6739 Connector 1 with SHC68-68-A2 Cable1 Refer to Figure9 if you are using the NI 6739 with the SH68-C68-S cable and NI PXIe-6739 Adapter. 8||NI 67xx Pinout Labels for the SCB-68 Note To Usersmodels with the SH68-C68-S cable and NI PXIe-6738 Adapter or NI PXIe-6739 Adapter. Figure 8. NI 6738/6739 Connector 0 with SH68-C68-S Cable and NI PXIe-6738/6739AdapterNI 67xx Pinout Labels for the SCB-68 Note To Users|© National Instruments|9with the SH68-C68-S cable and NI PXIe-6739 Adapter.Figure 9. NI 6739 Connector 1 with SH68-C68-S Cable and NI PXIe-6739 AdapterRefer to the NI Trademarks and Logo Guidelines at /trademarks for more information on NI trademarks. Other product and company names mentioned herein are trademarks or trade names of their respective companies. For patents covering NI products/technology, refer to the appropriate location: Help»Patents in your software, the patents.txt file on your media, or the National Instruments Patents Notice at/patents. You can find information about end-user license agreements (EULAs) and third-party legal notices in the readme file for your NI product. Refer to the Export Compliance Information at /legal/export-compliance for the NI global trade compliance policy and how to obtain relevant HTS codes, ECCNs, and other import/export data. NI MAKES NO EXPRESS OR IMPLIED WARRANTIES AS TO THE ACCURACY OF THE INFORMATION CONTAINED HEREIN AND SHALL NOT BE LIABLE FOR ANY ERRORS. U.S. Government Customers: The data contained in this manual was developed at private expense and is subject to the applicable limited rights and restricted data rights as set forth in FAR 52.227-14, DFAR 252.227-7014, and DFAR 252.227-7015.© 2018 National Instruments. All rights reserved.377334A-01Apr6。
NPort 6150 6250 Series Quick Installation Guide

P/N: 1802061500016 *1802061500016*NPort 6150/6250 Series Quick Installation GuideEdition 9.0, November 2016Technical Support Contact Information/supportMoxa Americas:Toll-free: 1-888-669-2872 Tel: 1-714-528-6777 Fax: 1-714-528-6778 Moxa China (Shanghai office): Toll-free: 800-820-5036 Tel: +86-21-5258-9955 Fax: +86-21-5258-5505 Moxa Europe:Tel: +49-89-3 70 03 99-0 Fax: +49-89-3 70 03 99-99 Moxa Asia-Pacific:Tel: +886-2-8919-1230 Fax: +886-2-8919-1231 Moxa India:Tel: +91-80-4172-9088 Fax: +91-80-4132-10452016 Moxa Inc. All rights reserved.OverviewThe NPort 6150/6250 series secure serial device servers provide reliable serial-to-Ethernet connectivity for a wide range of serial devices. The NPort 6150/6250 support TCP Server, TCP Client, UDP, andPair-Connection operation modes to ensure the compatibility of network software. In addition, the NPort 6150/6250 also support Secure TCP Server, Secure TCP Client, Secure Pair-Connection, and Secure Real COM modes for security critical applications such as banking, telecom, access control, and remote site management.Package ChecklistBefore installing a NPort 6150/6250 secure device server, verify that the package contains the following items:• 1 NPort 6150 or NPort 6250•Power adapter (does not apply to -T models)• 2 wallmount ears•Documentation and software CD•Quick installation guide (this guide)•Warranty cardOptional Accessories•DK-35A: DIN-rail mounting kit (35 mm)•DIN-rail power supply•CBL-RJ45M9-150: 8-pin RJ45 to male DB9 cable•CBL-RJ45M25-150: 8-pin RJ45 to male DB25 cableNOTE: Please notify your sales representative if any of the above items are missing or damaged.Hardware IntroductionNPort 6150NPort 6250Reset Button—Press the Reset Button continuously for 5 sec to load factory defaults. Use a pointed object, such as a straightened paper clip or toothpick, to press the reset button. This will cause the Ready LED to blink on and off. The factory defaults will be loaded once the Ready LED stops blinking (after about 5 seconds). At this point, you should release the reset button.LED IndicatorsAdjustable pull high/low resistor for RS-422/485 (150 K Ω or 1 K Ω)Jumpers are used to set the pull high/low resistors. The default is 150 kΩ. Short the jumpers to set this value to 1 kΩ. Do not use the 1 kΩ setting with RS -232 mode, since doing so will degrade the RS-232 signals and shorten the communication distance.Hardware Installation ProcedureSTEP 1: Connect the 12-48 VDC power adaptor to the NPort 6150 andthen plug the power adaptor into a DC outlet.STEP 2: For first-time configuration, use a cross-over Ethernet cable toconnect the NPort 6150 directly to your computer’s Ethernet cable. For connecting to a network, use a standardstraight-through Ethernet cable to connect to a hub or switch.STEP 3: Connect the NPort 6150’s serial port to a serial device.Placement OptionsThe NPort 6150/6250 can be placed flat on a desktop or other horizontal surface. In addition, you may use the DIN-rail or wallmount options, as illustrated below.WallmountDin RailSoftware Installation InformationThe Documentation and software CD contains the user’s manual, NPort Search Utility, and the PComm Lite Suite. Insert the CD into yourcomputer’s CD-ROM drive and follow the on-screen instructions. Please refer to the user’s manual for additional details on using the NPort Search Utility and PComm Lite.Pin Assignments and Cable WiringTwo serial cables for connecting the NPort 6150 to a serial device can be purchased separately. The wiring diagrams for the two cables are shown below.。
GigaSPEED XL 3071E-B ETL Verified Category 6 U UTP
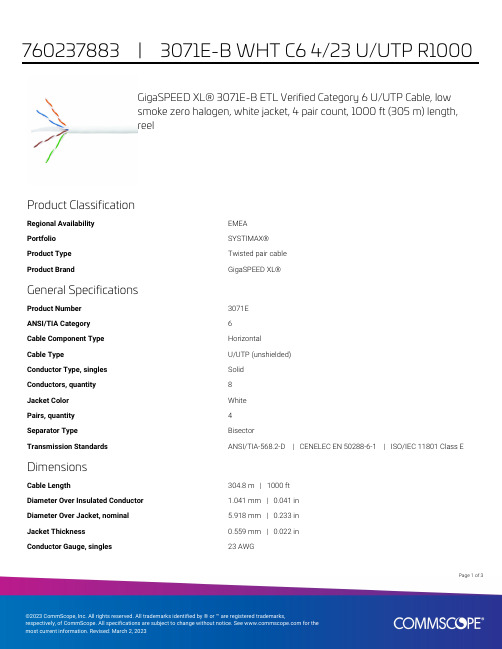
GigaSPEED XL® 3071E-B ETL Verified Category 6 U/UTP Cable, lowsmoke zero halogen, white jacket, 4 pair count, 1000 ft (305 m) length,reelProduct ClassificationRegional Availability EMEAPortfolio SYSTIMAX®Product Type Twisted pair cableProduct Brand GigaSPEED XL®General SpecificationsProduct Number3071EANSI/TIA Category6Cable Component Type HorizontalCable Type U/UTP (unshielded)Conductor Type, singles SolidConductors, quantity8Jacket Color WhitePairs, quantity4Separator Type BisectorTransmission Standards ANSI/TIA-568.2-D | CENELEC EN 50288-6-1 | ISO/IEC 11801 Class E DimensionsCable Length304.8 m | 1000 ftDiameter Over Insulated Conductor 1.041 mm | 0.041 inDiameter Over Jacket, nominal 5.918 mm | 0.233 inJacket Thickness0.559 mm | 0.022 inConductor Gauge, singles23 AWG13Page ofCross Section DrawingElectrical Specificationsdc Resistance Unbalance, maximum 5 %dc Resistance, maximum7.61 ohms/100 m | 2.32 ohms/100 ftDielectric Strength, minimum2500 VdcMutual Capacitance at Frequency 5.6 nF/100 m @ 1 kHzNominal Velocity of Propagation (NVP)70 %Operating Frequency, maximum300 MHzOperating Voltage, maximum80 VRemote Powering Fully complies with the recommendations set forth by IEEE 802.3bt (Type4) for the safe delivery of power over LAN cable when installed accordingto ISO/IEC 14763-2, CENELEC EN 50174-1, CENELEC EN 50174-2 or TIATSB-184-ASegregation Class cMaterial SpecificationsConductor Material Bare copperInsulation Material PolyolefinJacket Material Low Smoke Zero Halogen (LSZH)Separator Material PolyolefinPage of23Mechanical SpecificationsPulling Tension, maximum11.34 kg | 25 lbEnvironmental SpecificationsInstallation temperature0 °C to +60 °C (+32 °F to +140 °F)Operating Temperature-20 °C to +60 °C (-4 °F to +140 °F)Acid Gas Test Method EN 50267-2-3EN50575 CPR Cable EuroClass Fire Performance B2caEN50575 CPR Cable EuroClass Smoke Rating s1aEN50575 CPR Cable EuroClass Droplets Rating d0EN50575 CPR Cable EuroClass Acidity Rating a1Environmental Space Low Smoke Zero Halogen (LSZH)Smoke Test Method IEC 61034-2Packaging and WeightsCable weight38.097 kg/km | 25.6 lb/kftPackaging Type ReelRegulatory Compliance/CertificationsAgency ClassificationCENELEC EN 50575 compliant, Declaration of Performance (DoP) availableCHINA-ROHS Below maximum concentration valueISO 9001:2015Designed, manufactured and/or distributed under this quality management system REACH-SVHC Compliant as per SVHC revision on /ProductCompliance ROHSCompliantPage of33。
BF6910(BF6911)ASXX规格书
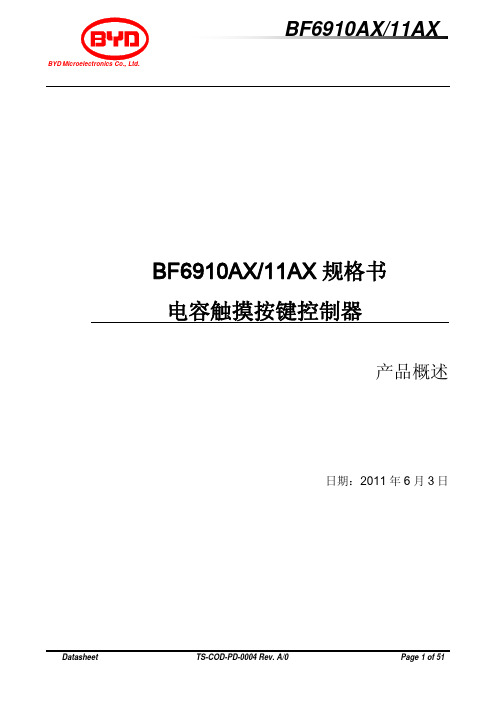
3.1 引脚图 ....................................................................................................................................................... 6 3.2 引脚描述 ................................................................................................................................................... 6
Endress+Hauser Cerabar S Deltabar S Evolution软件更

Manufacturer Informationfor users regarding software updates(following the NAMUR recommendation 53)1Type of deviceField device / signal processing deviceMonitoring- / operation system / hand held terminal etc.Modem / interfaceManufacturer :Endress+Hauser GmbH+Co. KG, 79689 MaulburgDevice :Cerabar S / Deltabar S EvolutionType :PMC71, PMP71/75, PMD70/75, FMD76/77/78Previous software version :02.01.03How can the previous software version number be identified:via HART command #0 / via ToF-Tool or on-site: Group Selection ->Operating Menu --> Transmitter Info --> Transmitter Data -->Software Version2Firmware/SoftwareNew firm-/software version :02.10.40Description of the modification in comparison with the predecessor version:New Level Mode "Easy"Enhanced Safety of Parametrization for Level EasySIL Mode for Level EasyEnhanced Possibilities of LinearizationHART Burst ModeEnhanced possibilities for the use of HistoROMCorrections in:-Low Flow Cut Off for Flow Measurement-Copying Data from HistoROM into transmitter3CompatibilityIs the newly installed firmware/software compatible with the operating tools?YesNo, description:New DD for ToF-Tool needed (available with ToF-Tool V4.00 from week 26/2006)New DD for DXR375 needed (available with DevRev21 from week 26/2006)New DTM for Fieldcare needed (available with FieldCare V02.02.00 from week 27/2006)Manufacturer Informationfor users regarding software updates(following the NAMUR recommendation 53)Is a firm/software update generally recommended?Yes, reasons:The firm-/software update can be performed by means of …No, reasons:The new software enhances the transmitter behaviour in certain applications and use cases, e.g. in easier parametrization in level applications.4Instruction manualIs a new instruction manual necessary due to the modification of the firm-/software? YesNoWhich manual corresponds to the new firm-/software:Device Communication options Manual Marking Cerabar SPMC71,PMP71/75Deltabar SPMD70/75,FMD76/77/78HART HART Cerabar S PMC71, PMP71/75 Pressure Transmitter Deltabar S PMD70/75, FMD76/77/78 Differential Pressure Transmitter BA 271P/00/en/08.06 71027246 Software version 2.10 BA270P/00/en/08.06 71027244 Software version 2.10The new instruction manuals can be referred in Internet: -area …DOWNLOAD“-declaration of the device and kind of manual5PriceChange in price of device in comparison with the predecessor version?Yes, new list price and update costs (without installation) are enclosuredNo。
NOVATEK-ELECTRO LTD 产品说明书:UBZ-301(10-100A)通用感应电机保护

NOVATEK-ELECTRO LTDResearch-and-Manufacture CompanyUBZ-301 (10-100A)UNIVERSAL INDUCTIONMOTOR PROTECTION UNITUSERS MANUALCONTROLS DESCRIPTION AND DIMENSIONS DIAGRAM 4151. Control for nominal current setting, Inom;2. Control for operating current setting, Iop (% Inom);3. Control for T2 (double overload trip) delay setting;4. Combined trip adjustment control for Umin/Umax;5. Control for phase imbalance adjustment, PI;6. Control for trip threshold for the minimum current, Imin (%Inom);7. Control for automatic reset delay setting, Ton;8. Green LED indicating for the mains voltage presence;9,10,11. Red LEDs indicating faults for insulation, overload and U fault respectively;12. Green LED indicating for load energization;13. Output terminals;14. Input terminals (10,11,12 are used for the connection with the BO-01 exchange unit);15. Insulation monitoring terminal.1 APPLICATIONSThe UBZ-301(10-100A)universal induction motor protection unit is designed for the continuous monitoring of the mains voltage parameters and for RMS phase/line currents of 3-Phase AC 380V/50Hz electrical equipment monitoring, primarily, of induction motors whose power is from 5kW up to 50 kW, isolated neutral system included.The unit provides full and effective protection of electrical equipment by a magnetic starter (contactor) coil control.The unit isolates electrical equipment from the running system and/or disables its start. This is performed in the following cases:1. when the mains voltage is of poor quality (unallowable voltage jumps, phase loss, incorrect phase sequence and phase «coincidence», phase/line voltage imbalance);2. when mechanical overloads (symmetrical phase/line current overload) take place. The unit performs overload protection with a dependent time delay;3. when phase/line current asymmetrical overloads induced by faults inside the motor occur. The unit performs protection from phase current imbalance and further disables an automatic reset;4. when phase current asymmetry without overload occurs that is induced by the insulation fault inside the motor and/or the power cable;5.when motor load is lost(«dry stroke»for pumps).The unit provides the minimum start and/or operating current protection;6. when insulation level to frame is abnormally low. The unit performs insulation level test before start and if the insulation is poor the start is disabled.7.when stator winding ground-to-fault occurs during operation. The unit performs the ground leakage current protection.The UBZ-301 (10-100A) provides:•a simple and accurate electromotor nominal current setting by nominal current standard scale;•the electromotor operating current setting that differs from standard values;•overload tripping with a dependent time delay (the current-time characteristic curve is plotted for a conventionally cold motor). The motor heat balance differential equation is being solved in the operation process. This approach enables to take account of the preceding electromotor status and to make a decision on heat overload presence with the maximum validity. This method also permits to allow for a motor start heating and to restrict (at the customer’s option) amount of starts per unit time;•shift of current-time characteristic curve along the current-axis and along time-axis as well;•setting of trip thresholds for the minimum/the maximum voltage,line voltage&phase current imbalance, and also for automatic reset delay at the personal customer’s discretion;•fault type indication, the mains voltage presence indication, current range indication the unit is adjusted to, and load energization indication;•the data exchange and transfer to the local computer network according to the RS-485 MODBUS record through the BO-01 exchange unit (BO-01 is supplied on order).2 DESCRIPTIONThe unit is a microprocessor-based digital device that provides a high degree of reliability and accuracy. The unit doesn’t need any auxiliary supply because it retrieves it's energy demand out of the measurement signal: it’s self-powered by the voltage to be monitored. Simultaneous isolated independent monitoring for the mains voltage and phase currents permits to detect the type of occurring fault and to provide a different decision-making logic for each fault type. When the mains voltage faults occur the unit performs automatic load reset on return voltage parameters to normal operating conditions. If a fault is induced by abnormal condition inside the motor(phase current imbalance at the symmetrical mains voltage,leakage current presence etc.) restart is disabled.The unit is stocked with three toroidal current transducers. Two of them are the phase/line current transducers (TT1, TT2), power phase cables are pulled through them. The third transducer is the differential current transducer(DCT)that has an enlarged diameter,because three power phase cables are pulled through it. By the 6, 7, 8, 9 terminals the unit is connected in parallel to the mains supply to be monitored. The unit output is provided with N.O. and N. C. contacts (the 1, 2, 3, 4 terminals). The output 3-4 terminals are connected in series with the starter coil power supply (with control circuit). The5terminal is designed to monitor the insulation level. The unit wiring diagram is shown below.When the unit trips the load is de-energized by a break in the magnetic starter coil power circuit through the N. C. 3-4 contacts.Table 1 - The 1-2-3-4 output contacts specificationMax. current for~ 250 V A. C.Max. powerMax sustained safevoltage ~Max. current for U = 30V D.C.Cosφ = 0.43A 2000VA 460V 3ACosφ = 1.05ANominal parameters and trip thresholds are set by front-panel screwdriver potentiometers.Nominal current setting. Nominal current is set by № 1 potentiometer. There are eleven positions of the potentiometer. Each position corresponds to the specific standard nominal current scale value (see below Table of Nominal Currents). Each position is characterized by the specific number of blinks that the green «On» LED makes. To set the nominal current one needs to bring out potentiometer control arm to a corresponding position; when the unit is energized the number of blinks «On» LED must correspond to the Table below. One needs to take into account that there are «dead bands» between the positions where «On» LED glows without blinks and where the nominal current is indefinite.In order to set operating value which is different from the nominal one that is specified in the nominal current table, it’s recommended the № 1 potentiometer to set to the position corresponding to the nearest value from the nominal current scale, and by the № 2 potentiometer one can increase or decrease the necessary value in % from the set value.Table 2 - Nominal current tablePotentiometer №1 devisionsNom. current, АGreen LED «On» blink1101bl.- pause 212,52bl.- pause 3163bl.- pause 4204bl.- pause 5255bl.- pause 6326bl.- pause 7407bl.- pause 8508bl.- pause 9639bl.- pause 108010bl.- pause 1110011bl.- pauseNOTE S:1.Continuous green «On» LED glow means that the potentiometer is set in «dead band». One needs to set the potentiometer so as the green LED blinked and the number of blinks corresponded to the set nominal current.2.Nominal currents setting is to be performed correcting for load connections (Wye/Delta), according to ratings of engine.Controls and adjustmentsThe unit has seven independent controls. For user’s convenience screwdriver slots of adjusting potentiometers are brought out to the unit front panel.•№1 – «Inom» - nominal current setting; there are eleven positions and each position corresponds to the specific current from the nominal currents table;•№2 – «Iop» - operating current; it is set in ± 15 percent of nominal current, it has ten scale marks;•№3 – «T2» - overload trip delay when there is double overload for operating current set; in the central position T2 ≈ 58-60 seconds The minimum time delay is 10 seconds, the maximum time delay is 100 seconds. The control shifts current-time characteristic dependence along time axis;•№4 – «Unom(%)» - combined control for Umax/Umin threshold in percent of the nominal voltage; according to this setting before the load energization the unit is checking the mains voltage level and, depending on its value, permits or forbids the load energization; after the load has been energized the voltage monitoring is going on but the load de-energization decision is made for currents;•№5 – «PI%» - trip threshold control for line voltage imbalance and RMS phase current imbalance; it has ten scale marks. The parameter is calculated as the difference between the maximum and the minimum values, in percent of the maximum value. If current imbalance percentage is twice as much as voltage imbalance percentage then it’s supposed that the imbalance is induced by fault conditions inside the motor. The automatic reset is forbidden and the unit is disabled;•№6 – «Imin» - trip threshold control for the minimum operating current, in percent of operating current set. It has ten scale marks from 0% to 75%: in «0» position this control is off;•№7 – «Ton» - automatic reset delay, it is within 0 – 600 seconds range; the scale is logarithmic.Indication•the green «ON» LED indicates that voltage exists in the mains. In the blink mode of glow the blink number between pauses corresponds to the specific nominal current from the nominal current table; there is a continuous glow in a «dead band». One needs to set a nominal current in the blink mode of operation;•the green «Load» LED indicates that the load is energized (the 3-4 terminals are closed);•the red «Insulation» LED lights up with continuous glow before the start if the stator/ power cable winding insulation level is abnormally low (less than 500 kOhms), and also during operation when there is a tripping for differential current; the unit is disabled;•the red «U Fault» LED glows when the mains voltage fault has occurred. The blink mode of operation switches on when there is undervoltage/overvoltage, phase imbalance for the mains voltage, voltage is not present on all three phases;•incorrect phase sequence or phase coincidence induces the mode of operation when all three red LEDs are blinking in turn;•the red «Overload» LED blinks when the average phase current exceeds the nominal one. After the unit has tripped for overload this LED comes to glow during 0.9 AR (automatic reset) delay.4 TECHNICAL BRIEFNominal line voltage, V380Mains frequency, Hz45-55Nominal current range in UBZ-301 10-100, А10-100Operating current setting range, % of nominal±15Double overload delay adjustment range, sec10-100Voltage threshold adjustment range, % of nominal±(5-20)Phase imbalance adjustment range, %5-20Trip threshold adjustment range for the minimum current, % of nominal0-75Automatic reset delay adjustment range ( Тon), sec0-600First energization load delay when Тon= 0, sec2-3Trip delay for current overload According to current-time characteristic curveTrip delay for voltage fault, sec2Trip delay for current fault (overload excluded), sec2 Fixed trip point for leakage current, А 1.0 Insulation resistance threshold, kОhms500±20 Voltage hysteresis, V10/17 Heat hysteresis, % of stored-up heat after load de-energization33Trip threshold accuracy for current, % of nominal current, not more than2-3 Trip threshold accuracy for voltage, V, not more than3 Phase imbalance accuracy, %, not more than 1.5 Operating voltage range, % of nominal one50-150 Power consumption (under load), VA, not more than 3.0 Maximum switched current of output contacts, A5 Output contact life:- under 5A load , operations, no less than - under 1A load , operations, no less than 100 000 1 000 000Enclosure:- apparatus- terminal block IP40 IP20Operating temperature range, °C from -35 to +55 Storage temperature, °C from -45 to +70 Weight, kg, not more than0.200Case dimensions 4 modules of S-typeMounting standard 35 mm DIN-railMounting position arbitrary5 OPERATION1. After supply voltage has been applied to the unit and before the output relay is energized the unit checks:•a stator winding insulation level to frame. If insulation resistance is below 500±20 kOhms, the load is not energized. The red «Insulation» LED glows;•the mains voltage quality,i.e.if voltage is present on all three phases,if the mains voltage is symmetrical, what the RMS line voltage value is like. When any of inhibit factors is present, the load is not energized, the red «U Fault» LED blinks;•a correct phase sequence, and phase «non-coincidence». When any of inhibit factors is present, the load is not energized, all red LEDs are blinking in turn; If all the parameters are normal, the outlet relay will be energized after Ton delay has expired (the 3-4 contacts are being closed and the 1-2 contacts are being opened) - the green «Load» LED glows. If load currents are absent (there are no less 2% of nominal one) the reason is that the load is de-energized. Voltage monitoring and insulation level is going. Output relay of unit is de-energized if inhibit factors are present in pause without currents;2. After the load is energized the unit performs voltage and current monitoring. The decision on load de-energization is made according to the following factors:•RMS current exceeds the nominal (operating) current (set by №№ 1, 2, 3 potentiometers); if there is current overload without heat overload the red «Overload» LED blinks but the load is not de-energized. If current overload induces heat overload the load is de-energized. The red «Overload»LED glows and is ON during 0.9Ton. The automatic reset is permitted;•current imbalance (set by №5 potentiometer) is twice exceeds the mains voltage imbalance; the load is de-energized, all red LEDs glow, the unit is disabled, the automatic reset is forbidden. To enable the unit one needs to remove supply voltage from the unit. It’s supposed that this type of fault is induced by abnormal conditions inside the motor;•current imbalance (set by №5 potentiometer) is less than twice exceeds voltage imbalance; the load is de-energized, the red «U Fault» LED glows, the automatic reset is permitted;•current imbalance (set by №5 potentiometer) is less than voltage imbalance; the load is de-energized, the red «U Fault» LED blinks, the automatic reset is permitted;•the average current value is less than Imin (set by №6 potentiometer); the load is de-energized, all red LEDs blink simultaneously, the unit is disabled, the automatic reset is forbidden. To enable the unit one needs to remove the supply voltage from the unit.Electromotor protection against heat overloadThe electromotor heat balance equation is being solved as the work advances. It’s supposed that:•the motor was cold before start;•during operation the motor releases the heat which is proportional to the current square;•after the stop the motor cools down exponentially.Below is the current-time characteristic curve with different T2 values (set by №3 potentiometer), where:•I/In – current ratio relative to the nominal current;•T/T2 -- actual trip delay relative to T2 (set by № 3 potentiometer).Current-time characteristic dependenceThe current-time characteristic dependence shown in the tables below is given for the standard recommended T2 value (the №3 potentiometer middle position corresponds to 60 seconds when double overload occurs):I/Inom 1.1 1.2 1.4 1.72 2.73456781015Тsec36524714888.66036.424.613.58.5 5.9 4.3 3.3 2.10.9After the load has been de-energized owing to the heat overload it will automatically be energized again:•according to heat hysteresis if time delay Ton=0, i. e. the motor must cool down 33% of the stored up heat;•according time delay Ton (№ 7 potentiometer) if Ton isn’t equal 0.By suitable selection of different Ton values, heat hysteresis considered, one can reduce number of starts per time unit because in the intermittent cycle the unit stores heat quantity released at the start of the motor.6 PRELIMINARY STARTING PROCEDURE AND SERVICE MANUALThe unit produced is completely ready for operation and needs no special pre-starting procedure measures. Owing to digital technology all the unit settings are aligned quite accurate, so no control devices are needed to adjust them. Use of the unit according to specifications above and the present service manual, continuous work included, relieves of preventive maintenance during service life. To put the unit in operation one must follow operating instructions given below:1.To set nominal (operating) current, trip thresholds, trip delays and reset delay by potentiometer's contact arms.2.To connect the unit according to the wire diagram given below:•by the 6(L1), 7(L2), 8(L3), 9(N) terminals the unit is connected in parallel to the mains supply to be monitored;•two current transducers (each one of them is put on two power phase wires that carry the load) are connected to the 13, 14, 15, 16 terminals; in connecting one has to consider the transducers grading;1st transducer– the beginning – the 13 terminal, the end – the 14 terminal;2nd transducer– the beginning – the 15 terminal, the end – the 15 terminal;•a differential current transducer that is put on the three power phase wires must be connected to the 17, 18 terminals (the connection grading is unimportant);•the 5 insulation monitoring terminal is connected to one of the MS output contacts;•output contacts (the 3-4 terminals) are connected to the MS coil power supply circuit (control circuit);•the BO-01 exhange and date transfer unit is connected to the 10, 11, 12 terminals (this unit is supplied on order).3.To apply a voltage to the unit. The correct setting of nominal current is checked by the number of blinks that the green LED makes. After Ton has expired (if there are no factors that can forbid energizing) the output relay of the unit is energized. If Ton=0, the first energizing will occur after 2-3 sec delay has expired.NOTE - The unit must be connected subject to the safety regulations. To set settings is recommended in «off» state. To set settings alive is permitted in the test conditions subject to the safety regulations.ATTENTION!If immediately after the load has been energized the unit de-energizes it and disables it for current imbalance,the incorrect polarity of the current transducers TT1or TT2 connection may be a reason. Then it’s recommended to change one of the transducers connection by reversing the places“the beginning-the end”of the13-16terminals.If the effect pointed above repeats when the load is re-energized it means that the transducers were connected correctly and the imbalance arose from EM and/or power cable fault.NOTES:1 Transducers are mounted by plastic clamps (they are component parts of supplies).2 The phase wires which are passing through the differential transducer to try to symmetrize in the centerof the transducer.WIRING DIAGRAMDT–differential current transducer (differential current transformer);CT1,CT2–current--transducers;BO-01– exchange and date transfer unit (on order)NOTE:1 “START”-button and “STOP”-button can be connected to MSC power supply circuit if necessary;2 The 220V MSC connection is shown here. The 380V MSC power supply circuit is analogous, coil power is applied from different phases through the 3-4 contacts;3 If BO-01 is absent the 10, 11, 12 terminals are not used.7 STORAGE AND SHIPPING CONDITIONSThe unit in manufacturer package should be stored in enclosed rooms at –45 to +70 °C and exposed to no more than 80% of relative humidity when there are no fumes in the air that exert a deleterious effect on package and the unit material. The Buyer must provide the protection of the unit against mechanical damages in transit.8 WARRANTYNovatek-Electro LTD. Company warrants a trouble-free operation of the UBZ-301 (10-100A) unit manufactured by it within 36 months from the date of sale, provided:•the proper installation;•the safety of the inspection quality control department seal;•the integrity of the case, no traces of an opening, cracks, spalls etc.。
NI PXIe-7975R NI FlexRIO

DEVICE SPECIFICATIONSNI PXIe-7975RNI FlexRIO™ FPGA Module for PXI ExpressThis document lists the specifications for the NI PXIe-7975R (NI 7975R) FPGA module. Specifications are subject to change without notice. For the most recent device specifications, refer to /manuals. Refer to your adapter module documentation for the adapter module specifications.Note Typical values are representative of an average unit operating at roomtemperature. These specifications are typical at 25 °C unless otherwise noted. ContentsHow to Use Your NI FlexRIO Documentation Set (2)Reconfigurable FPGA (3)FPGA Digital Input/Output (4)Onboard DRAM (4)Bus Interface (4)Maximum Power Requirements (5)Physical (5)NI FlexRIO FPGA Module Signals (5)Maximum Working V oltage (6)Environment (7)Operating Environment (7)Storage Environment (7)Shock and Vibration (7)Compliance and Certifications (8)Safety (8)Electromagnetic Compatibility (8)CE Compliance (8)Online Product Certification (9)Environmental Management (9)Worldwide Support and Services (9)How to Use Y our NI FlexRIO Documentation Set Figure 1. How to Use Y our NI FlexRIO Documentation SetTable 1. NI FlexRIO Documentation Locations and Descriptions2| | NI PXIe-7975R SpecificationsTable 1. NI FlexRIO Documentation Locations and Descriptions (Continued)Reconfigurable FPGAFPGA Kintex-7 XC7K410T ............................................................................LUTs254,200 ............................................................................DSP48 Slices (25 × 18 Multiplier)1,540 ............................................................................Embedded Block RAM (kbits)28,620 ............................................................................Default timebase40 MHz ............................................................................Timebase reference sources PXI Express 100 MHz (PXIe_CLK100) ............................................................................Timebase accuracy±100 ppm, 250 ps peak-to-peak jitter ............................................................................ ............................................................................Data transfers DMA, interrupts, programmed I/ONumber of DMA channels32 ............................................................................NI PXIe-7975R Specifications| © National Instruments| 3FPGA Digital Input/OutputNumber of general-purpose channels136, configurable as 136 single-ended, ............................................................................68 differential, or a combination of both1 Channels per bank....................................................................Bank 0/Bank 148Bank 240....................................................................Compatibility Configured through the FPGA and based on ............................................................................the attached adapter module; 1.2 V, 1.5 V,1.8 V,2.5 V, and3.3 V I/O standards (refer to).Protection Refer to . ............................................................................Current Refer to . ............................................................................Maximum I/O data rates....................................................................Single-ended400 Mb/sDifferential 1 Gb/s for LVDS.................................................................... ............................................................................Multi-region clock inputs6Single-region clock inputs5 ............................................................................Connection resources PXI triggers, PXI_CLK10, PXI star trigger, ............................................................................PXIe_DStarA, PXIe_DStarB, PXIe_DStarC,and PXIe_Sync100Onboard DRAMMemory size 2 GB single bank ............................................................................Maximum theoretical data rate10.5 GB/s ............................................................................Bus InterfaceForm factor x4 PXI Express, specification v2.1 compliant ............................................................................Slot compatibility x4, x8, and x16 PXI Express or PXI Express ............................................................................hybrid slots1The 136 channels span across three FPGA banks.4| | NI PXIe-7975R SpecificationsMaximum Power RequirementsNote Power requirements are dependent on the adapter module and contents of theLabVIEW FPGA VI used in your application.+3.3 VDC (±5%) 3 A ............................................................................ ............................................................................+12 V 3 APhysical18.8 cm × 12.9 cm (7.4 in. × 5.1 in.) ............................................................................Dimensions (not includingconnectors)Weight190 g (6.7 oz) ............................................................................NI FlexRIO FPGA Module SignalsThe following figure shows the available signals on the NI FlexRIO FPGA module. Refer to your adapter module specifications for your adapter module pinout.NI PXIe-7975R Specifications| © National Instruments| 5Figure 2. NI FlexRIO FPGA Module Front Panel Connector Pin Assignment andLocationsPCBPCBPCBPCBNote Pins S72 and S146 are shorted together on the NI 7975R.Maximum Working VoltageNote Maximum working voltage refers to the signal voltage plus the common-mode voltage.............................................................................Channel-to-earth 0 V to 3.3 V , Measurement Category I ............................................................................Channel-to-channel 0 V to 3.3 V , Measurement Category I6 | | NI PXIe-7975R SpecificationsCaution Do not use this device for connecting to signals in MeasurementCategories II, III, or IV.EnvironmentMaximum altitude2,000 m (800 mbar) (at 25 °C ambient ............................................................................temperature)Pollution Degree2 ............................................................................Indoor use only.Operating EnvironmentAmbient temperature range0 °C to 55 °C (Tested in accordance with ............................................................................IEC-60068-2-1 and IEC-60068-2-2. MeetsMIL-PRF-28800F Class 3 low temperaturelimit and MIL-PRF-28800F Class 2 hightemperature limit.)Relative humidity range10% to 90%, noncondensing (Tested in ............................................................................accordance with IEC-60068-2-56.) Storage Environment ............................................................................Ambient temperature range-20 °C to 70 °C (Tested in accordancewith IEC-60068-2-1 and IEC-60068-2-2.) Relative humidity range5% to 95%, noncondensing (Tested in ............................................................................accordance with IEC-60068-2-56.) Shock and VibrationOperating shock30 g peak, half-sine, 11 ms pulse (Tested in ............................................................................accordance with IEC-60068-2-27. MeetsMIL-PRF-28800F Class 2 limits.)Random vibrationOperating 5 Hz to 500 Hz, 0.3 g rms....................................................................Nonoperating 5 Hz to 500 Hz, 2.4 g rms (Tested in accordance ....................................................................with IEC-60068-2-64. Nonoperating testprofile exceeds the requirements ofMIL-PRF-28800F, Class 3.)NI PXIe-7975R Specifications| © National Instruments| 7Compliance and CertificationsSafetyThis product is designed to meet the requirements of the following electrical equipment safety standards for measurement, control, and laboratory use:•IEC 61010-1, EN 61010-1•UL 61010-1, CSA 61010-1Note For UL and other safety certifications, refer to the product label or the OnlineProduct Certification section.Electromagnetic CompatibilityThis product meets the requirements of the following EMC standards for electrical equipment for measurement, control, and laboratory use:•EN 61326-1 (IEC 61326-1): Class A emissions; Basic immunity•EN 55011 (CISPR 11): Group 1, Class A emissions•EN 55022 (CISPR 22): Class A emissions•EN 55024 (CISPR 24): Immunity•AS/NZS CISPR 11: Group 1, Class A emissions•AS/NZS CISPR 22: Class A emissions•FCC 47 CFR Part 15B: Class A emissions•ICES-001: Class A emissionsNote In the United States (per FCC 47 CFR), Class A equipment is intended foruse in commercial, light-industrial, and heavy-industrial locations. In Europe,Canada, Australia, and New Zealand (per CISPR 11), Class A equipment is intendedfor use only in heavy-industrial locations.Note Group 1 equipment (per CISPR 11) is any industrial, scientific, or medicalequipment that does not intentionally generate radio frequency energy for thetreatment of material or inspection/analysis purposes.Note For EMC declarations, certifications, and additional information, refer to theOnline Product Certification section.CE ComplianceThis product meets the essential requirements of applicable European Directives, as follows:•2006/95/EC; Low-V oltage Directive (safety)•2004/108/EC; Electromagnetic Compatibility Directive (EMC)8| | NI PXIe-7975R SpecificationsOnline Product CertificationTo obtain product certifications and the DoC for this product, visit /certification, search by model number or product line, and click the appropriate link in the Certification column. Environmental ManagementNI is committed to designing and manufacturing products in an environmentally responsible manner. NI recognizes that eliminating certain hazardous substances from our products is beneficial to the environment and to NI customers.For additional environmental information, refer to the Minimize Our Environmental Impact web page at /environment. This page contains the environmental regulations and directives with which NI complies, as well as other environmental information not included in this document.Waste Electrical and Electronic Equipment (WEEE)EU Customers At the end of the product life cycle, all products must be sent to aWEEE recycling center. For more information about WEEE recycling centers,National Instruments WEEE initiatives, and compliance withWEEE Directive 2002/96/EC on Waste Electrical and Electronic Equipment, visit/environment/weee.电子信息产品污染控制管理办法(中国RoHS)中国客户National Instruments符合中国电子信息产品中限制使用某些有害物质指令(RoHS)。
SPEC LH096T-IG13 VER A
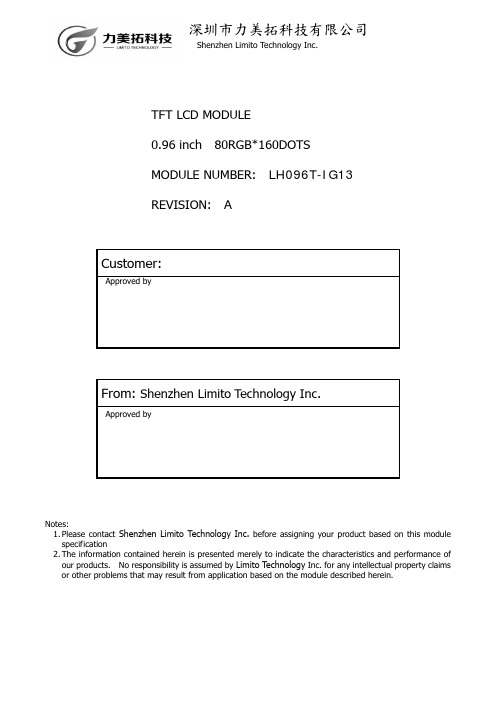
Symbol TP0 TP1 SDA SCL RS RESET CS GND NC VDD LEDK LEDA GND
Description Touch Pin,If not used,please open this pin. Touch Pin,If not used,please open this pin. SPI interface input/outpur pin. This pin is used to be serial interface clock. Display data/command selection pin in 4-line serial interface. This signal will reset the device,Signal is active low. Chip selection pin,Low enable,High disable. Power Ground. No Connect. Power Supply for Analog LED Canthode LED Anode Power Ground.
1. General Description
深圳市力美拓科技有限公司
Shenzhen Limito Technology Inc.
1.1 Description LH096T-IG13 is a 80RGBX160 dot-matrix TFT LCD module. This module is composed of a TFT LCD Panel, driver ICs, FPC and a Backlight unit.
1.1
g
Item
Date
Remark
深圳市力美拓科技有限公司
HT-69020NP-0, HT-69030NP-0 Duct Probe RH Transmitt

HT-69020NP-0, HT-69030NP-0 Duct Probe RHTransmitter Installation GuideIntroductionThe HT-69 Series Duct Probe Relative Humidity (RH)Transmitters use a highly accurate and reliable thermosetpolymer-based capacitance humidity sensor and state-of-the-art digital linearization and temperature-compensated circuitry to monitor humidity levels in a duct. The humidity sensor is encapsulated in a 60 micron HDPE filter at the end of a 9 in. (230 mm) stainless steel (S/S) probe and a compact enclosure.Figure 1: HT-69 Duct Probe RH Transmitter DimensionsFigure 2: Dimensions of the HT-69 Duct Probe RH Transmitter*241102556A*Part No. 24-11025-56 Rev. A2022-11-11MountingThe transmitter installs directly into any air duct with a minimum width or diameter of 10 in. (25.5 cm).-Select a suitable installation area in the middle of the duct wall.-To achieve the best reading, do not place in an area where air stratification may be present.-Mount the sensor at least 5 ft. (1.5 m) in either direction from elbows, dampers, filters, or other duct restrictions.-Avoid areas that expose the transmitter to vibrations or rapid temperature changes.To install the transmitter, complete the following steps:1.When you select a suitable spot, drill a 0.6 in. (15mm) to 0.75 in. (20 mm) hole for the probe.2.Slide the probe into the drilled hole until the enclosure is flush against the duct. The airflow direction is not important.3.Secure the enclosure to the duct with two No. 10 x 1 in. (25 mm) self-tapping screws (not provided).4.Tighten the screws until the enclosure is tight against the duct so that there is no movement of the enclosure. A foam gasket on the back of the enclosure provides a tight seal against any air leaks. See Step 1 in Figure 3.5.The enclosure includes a hinged cover with a latch.To open the cover, pull slightly on the latch on the right side of the enclosure. At the same time, pull on the cover as shown in Step 2 of Figure 3.6.A 0.5 in. NPT threaded connection hole is in the bottom of the enclosure. Screw the EMT or cable gland connector into the threaded connection holeuntil tight. See Step 3 in Figure 3.Note: Preferably use weatherproof EMT or cable gland fittings. The E-style enclosure includes 0.5 in. NPT to M16 thread adaptor and cable gland fitting.7.Make wire connections as shown in the wire diagram in Wiring .8.Swing the door closed until it securely latches. For added security, install the two provided screws in the integrated screw tabs. See Step 4 of Figure 3.Wiring•Deactivate the 24 VAC/DC power supply before you make all connections to the device to prevent electrical shock or equipment damage.•Use 14 AWG to 22 AWG shielded wiring for allconnections and do not locate the device wires in the same conduit with wiring that supplies inductive loads such as motors. Make all connections in accordance with national and local codes.•Pull at least 6 in. (15 cm) of wire into the enclosure,then complete the wiring connection according to the wire diagram for the applicable power supply and output signal type. See Figure 4.•Place the output switch in the required position to select the required signal output type (mA or VDC), as shown in Step 2 of Figure 4. The factory default setting is 4 mA to 20 mA.•If you select mA, no further output set up is required.If you select VOLT output as shown in Figure 5, place the voltage output switch to the required span position,that is 10 VDC = 0 VDC to 10 VDC. The factory default setting is 0 VDC to 10 VDC. See Step 1 of Figure 4.•Connect the DC positive or the AC voltage hot side to the PWR terminal. For voltage output or AC power,connect the supply common to the COM terminal.The device is reverse voltage-protected and does not operate if you connect it backwards. The device contains a half-wave power supply so the supplycommon is the same as the signal common. See Step 3of Figure 4.•The analog output is available on the OUT terminal.Check the controller Analog Input to determine the correct connection before you apply power as shown in Step 3 of Figure 4.Figure 3: Mounting the HT-69 Duct Probe RH TransmitterFigure 4: Wiring of the HT-60 Duct Probe TransmitterTechnical specificationsTable 1: HT-69020NP-0, HT-69030NP-0 Duct Probe RH Transmitter technical specificationsThe performance specifications are nominal and conform to acceptable industry standards. For application at conditions beyond these specifications, consult the local Johnson Controls office. Johnson Controls shall not be liable for damages resulting from misapplication or misuse of its products.Product warrantyThis product is covered by a limited warranty, details of which can be found at / buildingswarranty.Software termsUse of the software that is in (or constitutes) this product, or access to the cloud, or hosted services applicable to this product, if any, is subject to applicable end-user license, open-source software information, and other terms set forth at /techterms. Your use of this product constitutes an agreement to such terms. PatentsPatents: https://Single point of contactContact informationContact your local branch office: /locationsContact Johnson Controls: /contact-us© 2022 Johnson Controls. All rights reserved. All specifications and other information shown were current as of document revision and。
MURATA LQW18AN_00系列芯片电容器(芯片电感)产品说明书
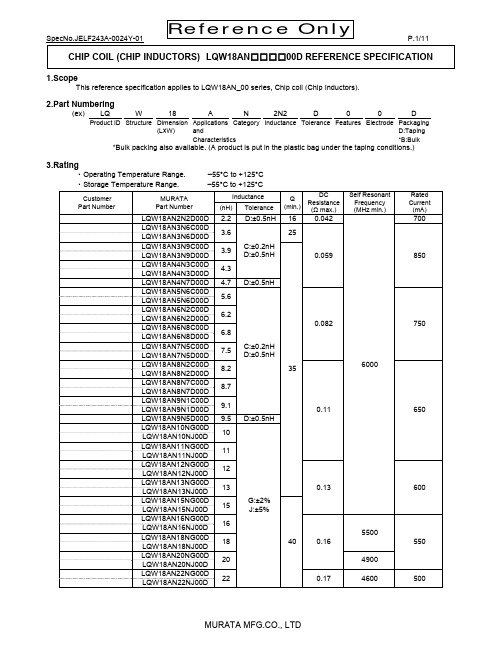
SpecNo.JELF243A-0024Y-01 P.1/11Reference OnlyCHIP COIL (CHIP INDUCTORS) LQW18AN □□□□00D REFERENCE SPECIFICATION1.ScopeThis reference specification applies to LQW18AN_00 series, Chip coil (Chip Inductors).2.Part Numbering(ex) LQ W 18 A N 2N2 D 0 0 DProduct ID Structure Dimension Applications Category Inductance Tolerance Features Electrode Packaging(L×W) andD:Taping Characteristics*B:Bulk *Bulk packing also available. (A product is put in the plastic bag under the taping conditions.)3.Rating・Operating Temperature Range. –55°C to +125°C ・Storage Temperature Range. –55°C to +125°CCustomer Part NumberMURATA Part NumberInductance Q (min.)DC Resistance (Ω max.)Self Resonant Frequency (MHz min.)Rated Current (mA)(nH)ToleranceLQW18AN2N2D00D 2.2D:±0.5nH 160.042 6000700LQW18AN3N6C00D 3.6C:±0.2nH D:±0.5nH250.059 850LQW18AN3N6D00D LQW18AN3N9C00D 3.935LQW18AN3N9D00D LQW18AN4N3C00D 4.3 LQW18AN4N3D00D LQW18AN4N7D00D 4.7D:±0.5nHLQW18AN5N6C00D 5.6C:±0.2nH D:±0.5nH0.082 750LQW18AN5N6D00D LQW18AN6N2C00D 6.2 LQW18AN6N2D00D LQW18AN6N8C00D 6.8 LQW18AN6N8D00D LQW18AN7N5C00D 7.5 LQW18AN7N5D00D LQW18AN8N2C00D 8.20.11 650LQW18AN8N2D00D LQW18AN8N7C00D 8.7 LQW18AN8N7D00D LQW18AN9N1C00D 9.1 LQW18AN9N1D00D LQW18AN9N5D00D 9.5D:±0.5nHLQW18AN10NG00D 10G:±2% J:±5%LQW18AN10NJ00D LQW18AN11NG00D 11 LQW18AN11NJ00D LQW18AN12NG00D 120.13 600LQW18AN12NJ00D LQW18AN13NG00D 13 LQW18AN13NJ00D LQW18AN15NG00D 1540 LQW18AN15NJ00D LQW18AN16NG00D 160.165500550LQW18AN16NJ00D LQW18AN18NG00D 18 LQW18AN18NJ00D LQW18AN20NG00D 204900LQW18AN20NJ00D LQW18AN22NG00D 220.17 4600 500LQW18AN22NJ00DSpecNo.JELF243A-0024Y-01 P.2/11Reference OnlyCustomerPart NumberMURATA Part NumberInductance Q (min.)DC Resistance (Ω max.)Self Resonant Frequency (MHz min.)Rated Current (mA)(nH)ToleranceLQW18AN24NG00D 24 G:±2%J:±5%400.213800 500LQW18AN24NJ00D LQW18AN27NG00D 27 3700 440 LQW18AN27NJ00D LQW18AN30NG00D 300.23 3300420LQW18AN30NJ00D LQW18AN33NG00D 33 3200 LQW18AN33NJ00D LQW18AN36NG00D 360.26 2900400LQW18AN36NJ00D LQW18AN39NG00D 39 2800 LQW18AN39NJ00D LQW18AN43NG00D 430.292700380LQW18AN43NJ00D LQW18AN47NG00D 47382600 LQW18AN47NJ00D LQW18AN51NG00D 51 0.33 2500 370LQW18AN51NJ00D LQW18AN56NG00D 56 0.35 2400 360LQW18AN56NJ00D LQW18AN62NG00D 62 0.51 2300 280LQW18AN62NJ00D LQW18AN68NG00D 68 0.38 2200 340 LQW18AN68NJ00D LQW18AN72NG00D 72340.56 2100270LQW18AN72NJ00D LQW18AN75NG00D 75 2050LQW18AN75NJ00D LQW18AN82NG00D 82 0.60 2000 250LQW18AN82NJ00D LQW18AN91NG00D 91 0.64 1900 230 LQW18AN91NJ00D LQW18ANR10G00D 1000.68 1800 220 LQW18ANR10J00D LQW18ANR11G00D 110321.2 1700 200 LQW18ANR11J00D LQW18ANR12G00D 120 1.3 1600 180 LQW18ANR12J00D LQW18ANR13G00D 130 1.4 1450 170 LQW18ANR13J00D LQW18ANR15G00D 150 1.5 1400 160 LQW18ANR15J00D LQW18ANR16G00D 1602.1 1350 150 LQW18ANR16J00D LQW18ANR18G00D 18025 2.2 1300 140 LQW18ANR18J00D LQW18ANR20G00D 200 2.4 1250120LQW18ANR20J00D LQW18ANR22G00D 220 2.5 1200LQW18ANR22J00D LQW18ANR27G00D 270303.4 960 110 LQW18ANR27J00D LQW18ANR33G00D 3305.580085LQW18ANR33J00D LQW18ANR39G00D 390 6.2 80 LQW18ANR39J00D LQW18ANR47G00D 4707.0 700 75LQW18ANR47J00DSpecNo.JELF243A-0024Y-01 P.3/11Reference Only4. Testing Conditions《Unless otherwise specified》《In case of doubt》Temperature : Ordinary Temperature / 15°C to 35°C Temperature: 20°C±2°CHumidity : Ordinary Humidity / 25%(RH) to 85%(RH) Humidity : 60%(RH) to 70%(RH)Atmospheric Pressure : 86kPa to 106 kPa5.Appearance and Dimensions■Unit Mass (Typical value)0.003g(in mm).Reference OnlySpecNo.JELF243A-0024Y-01 P.4/11SpecNo.JELF243A-0024Y-01 P.5/11Reference Only8.Environmental Performance It shall be soldered on the substrate.No. Item Specification Test Method 8.1 Heat Resistance Appearance:No damage Inductance Change: within ±5% Q Change: within ±20% Temperature:125°C±2°CTime:1000h (+48h,0h) Then measured after exposure in the room condition for 24h±2h.8.2 Cold Resistance Appearance:No damage Inductance Change: within ±5% Q Change: within ±20%Temperature:-55°C±2°CTime:1000h (+48h,-0h) Then measured after exposure in the roomcondition for 24h±2h.8.3 Humidity Temperature:40°C±2°CHumidity:90%(RH) to 95%(RH) Time:1000h (+48h,-0h)Then measured after exposure in the room condition for 24h±2h.8.4 Temperature Cycle 1 cycle:1 step:-55°C±2°C / 30min±3 min2 step:Ordinary temp. / 10min to 15 min3 step:+125°C±2°C / 30min±3 min4 step:Ordinary temp. / 10min to15 min Total of 10 cyclesThen measured after exposure in the room condition for 24h±2h.9.Specification of Packaging9.1 Appearance and Dimensions of paper tape (8mm-wide)(in mm)9.2 Specification of Taping(1) Packing quantity (standard quantity)4,000 pcs. / reel(2) Packing MethodProducts shall be packed in the cavity of the base tape and sealed by top tape and bottom tape. (3) Sprocket holeThe sprocket holes are to the right as the tape is pulled toward the user. (4) Spliced pointBase tape and Top tape has no spliced point. (5) Missing components numberMissing components number within 0.1 % of the number per reel or 1 pc., whichever is greater, and are not continuous. The Specified quantity per reel is kept.9.3 Pull StrengthTop tape 5N min.Bottom tape4.0±0.1φ1.5±2.0±0.054.0±0.1Direction of feed1.1max.1.0±0.051.8±0.058.0±0.23.5±0.051.75±0.10.10SpecNo.JELF243A-0024Y-01 P.6/11Reference Only9.4 Peeling off force of cover tapeSpeed of Peeling off 300mm/min Peeling off force0.1N to 0.6N(minimum value is typical)9.5 Dimensions of Leader-tape,Trailer and ReelThere shall be leader-tape ( top tape and empty tape) and trailer-tape (empty tape) as follows.9.6 Marking for reelCustomer part number, MURATA part number, Inspection number(∗1) ,RoHS Marking (∗2), Quantity etc ・・・∗1) <Expression of Inspection No.> □□ OOOO ×××(1) (2) (3)(1) Factory code(2) Date First digit: Year / Last digit of yearSecond digit: Month / Jan. to Sep. → 1 to 9, Oct. to Dec. → O, N, D Third, Fourth digit : Day(3) Serial No.∗2) <Expression of RoHS Marking >ROHS – Y (△)(1) (2)(1) RoHS regulation conformity parts.(2) MURATA classification number9.7 Marking for Outside package (corrugated paper box)Customer name, Purchasing order number, Customer part number, MURATA part number, RoHS Marking (∗2) ,Quantity, etc ・・・9.8. Specification of Outer CaseOuter Case Dimensions(mm)Standard Reel Quantityin Outer Case (Reel)W D H 186 186 93 5∗ Above Outer Case size is typical. It depends on a quantity of an order.10. ! CautionLimitation of ApplicationsPlease contact us before using our products for the applications listed below which require especially high reliability for the prevention of defects which might directly cause damage to the third party's life, body or property.(1) Aircraft equipment (6) Transportation equipment (vehicles, trains, ships, etc.) (2) Aerospace equipment (7) Traffic signal equipment (3) Undersea equipment (8) Disaster prevention / crime prevention equipment (4) Power plant control equipment (9) Data-processing equipment (5) Medical equipment (10) Applications of similar complexity and /or reliability requirements to the applications listed in the aboveF165to 180degreeTop tapeBottom tape Base tapeWDLabelHSpecNo.JELF243A-0024Y-01 P.7/11Reference Only11. NoticeProducts can only be soldered with reflow.This product is designed for solder mounting.Please consult us in advance for applying other mounting method such as conductive adhesive.11.1 Land pattern designingRecommended land patterns for reflow soldering are as follows:These have been designed for Electric characteristics and solderability.Please follow the recommended patterns. Otherwise, their performance which includes electrical performance or solderability may be affected, or result to "position shift" in soldering process.(in mm)11.2 Flux, Solder・Use rosin-based flux.Includes middle activator equivalent to 0.06(wt)% to 0.1(wt)% Chlorine.Don’t use highly acidic flux with halide content exceeding 0.2(wt)% (chlorine conversion value). Don’t use water-soluble flux. ・Use Sn-3.0Ag-0.5Cu solder.・Standard thickness of solder paste : 100μm to 150μm.11.3 Reflow soldering conditions・Pre-heating should be in such a way that the temperature difference between solder and product surface is limited to 150°C max. Cooling into solvent after soldering also should be in such a way that the temperature difference is limited to 100°C max.Insufficient pre-heating may cause cracks on the product, resulting in the deterioration of products quality.・Standard soldering profile and the limit soldering profile is as follows.The excessive limit soldering conditions may cause leaching of the electrode and / or resulting in the deterioration of product quality.・Reflow soldering profileStandard Profile Limit Profile Pre-heating 150°C ~180°C 、90s ±30s Heating above 220°C 、30s ~60s above 230°C 、60s max. Peak temperature 245°C ±3°C 260°C,10s Cycle of reflow 2 times 2 timesA 0.6 to 0.8B 1.9 to 2.0 C0.7 to 1.0Limit ProfileStandard Profile90s±30s230℃260℃245℃±3℃220℃30s ~60s60s max.180150Temp.(s)(℃)Time.resistSpecNo.JELF243A-0024Y-01 P.8/11Reference Only11.4 Reworking with soldering ironThe following conditions must be strictly followed when using a soldering iron.Pre-heating 150°C,1 min Tip temperature 350°C max. Soldering iron output 80W max. Tip diameter φ3mm max. Soldering time 3(+1,-0)sTime 2 timesNote :Do not directly touch the products with the tip of the soldering iron in order to prevent thecrack on the products due to the thermal shock.11.5 Solder Volume・Solder shall be used not to be exceeded the upper limits as shown below.・Accordingly increasing the solder volume, the mechanical stress to Chip is also increased. Exceeding solder volume may cause the failure of mechanical or electrical performance.1/3T ≦t ≦TT :thickness of product11.6 Product’s locationThe following shall be considered when designing and laying out P.C.B.'s.(1) P.C.B. shall be designed so that products are not subject to the mechanical stress due to warping the board.[Products direction ]Products shall be located in the sidewaysdirection (Length:a <b) to the mechanical stress.(2) Components location on P.C.B. separation.It is effective to implement the following measures, to reduce stress in separating the board.It is best to implement all of the following three measures; however, implement as many measures as possible to reduce stress.Contents of MeasuresStress Level (1) Turn the mounting direction of the component parallel to the board separation surface. A > D *1 (2) Add slits in the board separation part.A >B (3) Keep the mounting position of the component away from the board separation surface. A > C*1 A > D is valid when stress is added vertically to the perforation as with Hand Separation.If a Cutting Disc is used, stress will be diagonal to the PCB, therefore A > D is invalid.〈Poor example〉〈Good example〉baSeamSlitADBCbaLength:a <bReference OnlySpecNo.JELF243A-0024Y-01 P.9/11(3) Mounting Components Near Screw HolesWhen a component is mounted near a screw hole, it may be affected by the board deflection that occurs duringthe tightening of the screw. Mount the component in a position as far away from the screw holes as possible.11.7 Cleaning ConditionsProducts shall be cleaned on the following conditions.(1) Cleaning temperature shall be limited to 60°C max.(40°C max for IPA)(2) Ultrasonic cleaning shall comply with the following conditions with avoiding the resonancephenomenon at the mounted products and P.C.B.Power : 20 W / l max. Frequency : 28kHz to 40kHz Time : 5 min max.(3) Cleaner1. Alcohol type cleanerIsopropyl alcohol (IPA)2. Aqueous agentPINE ALPHA ST-100S(4) There shall be no residual flux and residual cleaner after cleaning.In the case of using aqueous agent, products shall be dried completely after rinse with de-ionizedwater in order to remove the cleaner.(5) Other cleaning Please contact us.11.8 Resin coatingThe inductance value may change due to high cure-stress of resin to be used for coating/molding products.An open circuit issue may occur by mechanical stress caused by the resin, amount/cured shape of resin, oroperating condition etc. Some resin contains some impurities or chloride possible to generate chlorine byhydrolysis under some operating condition may cause corrosion of wire of coil, leading to open circuit.So, please pay your careful attention in when you select resin in case of coating/molding the productswith the resin.Prior to use the coating resin, please make sure no reliability issue is observed by evaluating productsmounted on your board.11.9 Caution for use・Sharp material such as a pair of tweezers or other material such as bristles of cleaning brush , shall not be touched to the winding portion to prevent the breaking of wire.・Mechanical shock should not be applied to the products mounted on the board to prevent the breaking of the core.11.10 Notice of product handling at mountingIn some mounting machines,when picking up components support pin pushes up the components from thebottom of base tape. In this case, please remove the support pin. The support pin may damage the componentsand break wire.In rare case ,the laser recognition can not recognize this component. Please contact us when you use laserrecognition. (There is no problem with the permeation and reflection type.)11.11 Handling of a substrateAfter mounting products on a substrate, do not apply any stress to the product caused by bending or twisting to thesubstrate when cropping the substrate, inserting and removing a connector from the substrate or tightening screwto the substrate.Excessive mechanical stress may cause cracking in the product.Bending TwistingReference OnlySpecNo.JELF243A-0024Y-01 P.10/1111.12 Storage and Handing Requirements(1) Storage periodUse the products within 12 months after delivered.Solderability should be checked if this period is exceeded.(2) Storage conditions・Products should be stored in the warehouse on the following conditions.Temperature :-10°C to 40°CHumidity :15% to 85% relative humidity No rapid change on temperature and humidity・Don't keep products in corrosive gases such as sulfur,chlorine gas or acid, or it may causeoxidization of electrode, resulting in poor solderability.・Products should not be stored on bulk packaging condition to prevent the chipping of thecore and the breaking of winding wire caused by the collision between the products.・Products should be stored on the palette for the prevention of the influence from humidity,dust and so on.・Products should be stored in the warehouse without heat shock, vibration, direct sunlight and so on.(3) Handling ConditionCare should be taken when transporting or handling product to avoid excessive vibration ormechanical shock.12.! Note(1)Please make sure that your product has been evaluated in view of your specifications with our product beingmounted to your product.(2)You are requested not to use our product deviating from the reference specifications.(3)The contents of this reference specification are subject to change without advance notice.Please approve our product specifications or transact the approval sheet for product specificationsbefore ordering.Reference OnlySpecNo.JELF243A-0024Y-01 P.11/11Mouser ElectronicsAuthorized DistributorClick to View Pricing, Inventory, Delivery & Lifecycle Information:M urata:LQW18AN10NG00D LQW18AN10NJ00D LQW18AN11NG00D LQW18AN11NJ00D LQW18AN12NG00D LQW18AN12NJ00D LQW18AN13NG00D LQW18AN13NJ00D LQW18AN15NG00D LQW18AN15NJ00D LQW18AN16NG00D LQW18AN16NJ00D LQW18AN18NG00D LQW18AN18NJ00D LQW18AN20NG00D LQW18AN20NJ00D LQW18AN22NG00D LQW18AN22NJ00D LQW18AN24NG00D LQW18AN24NJ00D LQW18AN27NG00D LQW18AN27NJ00D LQW18AN2N2D00D LQW18AN30NG00D LQW18AN30NJ00D LQW18AN33NG00D LQW18AN33NJ00D LQW18AN36NG00D LQW18AN36NJ00D LQW18AN39NG00D LQW18AN3N6C00D LQW18AN3N6D00D LQW18AN3N9C00D LQW18AN3N9D00D LQW18AN43NG00D LQW18AN43NJ00D LQW18AN47NG00D LQW18AN47NJ00D LQW18AN4N3C00D LQW18AN4N3D00D LQW18AN4N7D00D LQW18AN51NG00D LQW18AN51NJ00D LQW18AN56NG00D LQW18AN56NJ00D LQW18AN5N6C00D LQW18AN5N6D00D LQW18AN62NG00D LQW18AN62NJ00D LQW18AN68NG00D LQW18AN68NJ00D LQW18AN6N2C00D LQW18AN6N2D00D LQW18AN6N8C00D LQW18AN6N8D00D LQW18AN72NG00D LQW18AN72NJ00D LQW18AN75NG00D LQW18AN75NJ00D LQW18AN7N5D00D LQW18AN82NG00D LQW18AN82NJ00D LQW18AN8N2D00D LQW18AN8N7D00D LQW18AN91NG00D LQW18AN91NJ00D LQW18AN9N1D00D LQW18AN9N5D00D LQW18ANR10G00D LQW18ANR10J00D LQW18ANR11G00D LQW18ANR11J00D LQW18ANR12G00D LQW18ANR12J00D LQW18ANR13G00D LQW18ANR13J00D LQW18ANR15G00D LQW18ANR15J00D LQW18ANR16G00D LQW18ANR16J00D LQW18ANR18G00D LQW18ANR18J00D LQW18ANR20G00D LQW18ANR20J00D LQW18ANR22G00D LQW18ANR22J00D LQW18ANR27G00D LQW18ANR27J00D LQW18ANR33G00D LQW18ANR33J00D LQW18ANR39G00D LQW18ANR39J00D LQW18ANR47G00D LQW18ANR47J00D LQW18AN9N1C00D LQW18AN8N7C00D LQW18AN7N5C00D LQW18AN8N2C00D。
KSZ9021RN to KSZ9031RNX Migration Guide
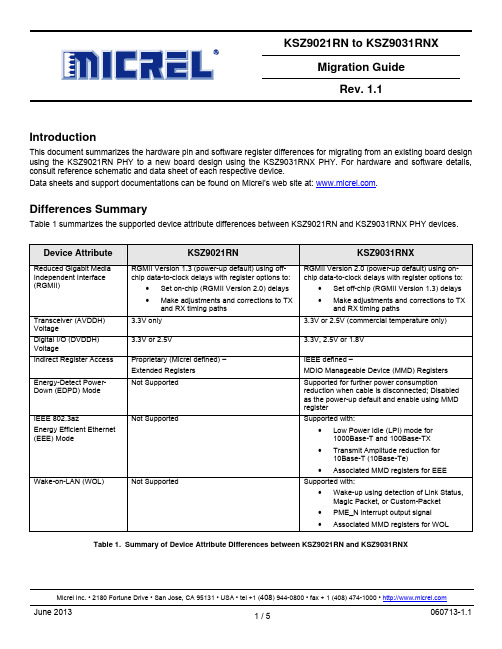
KSZ9021RN to KSZ9031RNXMigration GuideRev. 1.1IntroductionThis document summarizes the hardware pin and software register differences for migrating from an existing board design using the KSZ9021RN PHY to a new board design using the KSZ9031RNX PHY. For hardware and software details, consult reference schematic and data sheet of each respective device.Data sheets and support documentations can be found on Micrel’s web site at: .Differences SummaryTable 1 summarizes the supported device attribute differences between KSZ9021RN and KSZ9031RNX PHY devices.Device Attribute KSZ9021RN KSZ9031RNXReduced Gigabit Media Independent Interface (RGMII) RGMII Version 1.3 (power-up default) using off-chip data-to-clock delays with register options to:•Set on-chip (RGMII Version 2.0) delays•Make adjustments and corrections to TXand RX timing pathsRGMII Version 2.0 (power-up default) using on-chip data-to-clock delays with register options to:•Set off-chip (RGMII Version 1.3) delays•Make adjustments and corrections to TXand RX timing pathsTransceiver (AVDDH)Voltage3.3V only 3.3V or 2.5V (commercial temperature only)Digital I/O (DVDDH)Voltage3.3V or 2.5V 3.3V, 2.5V or 1.8VIndirect Register Access Proprietary (Micrel defined) –Extended Registers IEEE defined –MDIO Manageable Device (MMD) RegistersEnergy-Detect Power-Down (EDPD) Mode Not Supported Supported for further power consumptionreduction when cable is disconnected; Disabledas the power-up default and enable using MMDregisterIEEE 802.3azEnergy Efficient Ethernet (EEE) Mode Not Supported Supported with:•Low Power Idle (LPI) mode for1000Base-T and 100Base-TX•Transmit Amplitude reduction for10Base-T (10Base-Te)•Associated MMD registers for EEEWake-on-LAN (WOL) Not Supported Supported with:•Wake-up using detection of Link Status,Magic Packet, or Custom-Packet•PME_N interrupt output signal•Associated MMD registers for WOL Table 1. Summary of Device Attribute Differences between KSZ9021RN and KSZ9031RNXPin DifferencesTable 2 summarizes the pin differences between KSZ9021RN and KSZ9031RNX PHY devices. Pin #KSZ9021RNKSZ9031RNXPin NameType Pin FunctionPin NameTypePin Function1 AVDDH P 3.3V analog V DD AVDDH P 3.3V/2.5V (commercial temp only) analog V DD 12 AVDDH P 3.3V analog V DD AVDDH P 3.3V/2.5V (commercial temp only) analog V DD 13VSS_PSGndDigital groundNC–No connectThis pin is not bonded and can be connected to digital ground for footprint compatibility with the Micrel KSZ9021RN Gigabit PHY.16 DVDDH P3.3V / 2.5V digital V DD DVDDH P 3.3V, 2.5V, or 1.8V digital V DD_I/O 17 LED1 /PHYAD0I/OLED Output:Programmable LED1 OutputConfig Mode:The pull-up/pull-down value is latched as PHYAD[0] during power-up / reset.LED1 /PHYAD0 /PME_N1I/O LED1 output:Programmable LED1 outputConfig mode:The voltage on this pin issampled and latched during the power-up/reset process to determine the value of PHYAD[0].PME_N output:Programmable PME_N output (pin option 1). This pin function requires an external pull-up resistor to DVDDH (digital V DD_I/O ) in a range from 1.0k Ω to 4.7k Ω. When asserted low, this pin signals that a WOL event has occurred.When WOL is not enabled, this pin function behaves as per the KSZ9021RN pin definition.This pin is not an open-drain for all operating modes.34 DVDDH P3.3V / 2.5V digital V DD DVDDH P 3.3V, 2.5V, or 1.8V digital V DD_I/O38 INT_N O Interrupt OutputThis pin provides aprogrammable interrupt output and requires an external pull-up resistor to DVDDH in the range of 1K to 4.7K ohms for active low assertion.INT_N/O Interrupt OutputThis pin provides aprogrammable interrupt output and requires an external pull-up resistor to DVDDH in the range of 1K to 4.7K ohms for active low assertion.This pin is an open-drain.PME_N2 PME_N output: Programmable PME_N output (pin option 2). When asserted low, this pin signals that a WOL event has occurred.When WOL is not enabled, this pin function behaves as per the KSZ9021RN pin definition. This pin is not an open-drain for all operating modes.40 DVDDH P 3.3V / 2.5V digital V DD DVDDHP3.3V, 2.5V, or 1.8V digitalV DD_I/O47 AVDDH P 3.3V analog V DD NC–NoconnectThis pin is not bonded and canbe connected to AVDDH powerfor footprint compatibility withthe Micrel KSZ9021RN GigabitPHY.48 ISET I/O Set transmit output levelConnect a 4.99KΩ 1%resistor to ground on thispin. ISET I/O Set the transmit output levelConnect a 12.1kΩ 1% resistorto ground on this pin.Table 2. Pin Differences between KSZ9021RN and KSZ9031RNXStrapping Option DifferencesThere is no strapping pin difference between KSZ9021RN and KSZ9031RNX.Register Map DifferencesThe register space within the KSZ9021RN and KSZ9031RNX consists of direct-access registers and indirect-access registers.Direct-access RegistersThe direct-access registers comprise of IEEE-Defined Registers (0h – Fh) and Vendor-Specific Registers (10h – 1Fh). Between the KSZ9021RN and KSZ9031RNX, the direct-access registers and their bits have the same definitions, except for the following registers in Table 3.Direct-access RegisterKSZ9021RN KSZ9031RNXName Description Name Description3h PHYIdentifier2 Bits [15:10] (part of OUI) – same asKSZ9031RNXBits [9:4] (model number) – unique forKSZ9021RNBits [3:0] (revision number) – uniquedepending on chip revision PHY Identifier 2 Bits [15:10] (part of OUI) – same asKSZ9021RNBits [9:4] (model number) – unique forKSZ9031RNXBits [3:0] (revision number) – uniquedepending on chip revisionBh ExtendedRegister –Control Indirect Register AccessSelect read/write control andpage/address of Extended RegisterReserved ReservedDo not change the default value ofthis registerCh ExtendedRegister –Data Write Indirect Register AccessValue to write to Extended RegisterAddressReserved ReservedDo not change the default value ofthis registerDh ExtendedRegister –Data Read Indirect Register AccessValue read from Extended RegisterAddressMMD Access –ControlIndirect Register AccessSelect read/write control and MMDdevice addressEh Reserved ReservedDo not change the default value ofthis register MMD Access –Register/DataIndirect Register AccessValue of register address/data for theselected MMD device address1Fh, bit [1] Software Reset 1 = Reset chip, except all registers0 = Disable resetReserved ReservedTable 3. Direct-access Register Differences between KSZ9021RN and KSZ9031RNXIndirect-access RegistersThe indirect register mapping and read/write access are completely different for the KSZ9021RN (uses Extended Registers) and KSZ9031RNX (uses MMD Registers). Refer to respective devices’ data sheets for details.Indirect registers provide access to the following commonly used functions:•1000Base-T link-up time control (KSZ9031RNX only)• Pin strapping status• Pin strapping override•Skew adjustments for RGMII clocks, control signals, and datao Resolution of skew steps are different between KSZ9021RN and KSZ9031RNX•Energy-Detect Power-Down Mode enable/disable (KSZ9031RNX only)•Energy Efficient Ethernet function (KSZ9031RNX only)•Wake-on-LAN function (KSZ9031RNX only)Revision HistoryRevision Date Summary of ChangesMigration Guide created1.0 12/7/121.1 6/7/13 Indicate PME_N1 (pin 17) for KSZ9031RNX is not an open-drain.Indicate INT_N (pin 38) is an open-drain for KSZ9021RN, but is not an open-drain for KSZ9031RNX.Indicate direct-access register 1Fh, bit [1] difference.。
富士达电梯故障代码讲解

在安装富士达电梯时动慢车有时会发生故障造成电梯慢车不运行1、电机不得电--#36不吸合--#1E -- 未吸合造成2、电机得电但不开闸--抱闸检测回路断开-- 故障6 系3、电机得电但开闸不走--抱闸检测回路不断开-- 故障6 系4、电梯在机房可以走慢车在轿顶不运行--防撞头开工未封、轿顶通讯不良呼叫记录开始:按动上按钮,同时将EQDO 开关切到ON ,然后放开。
实行:按动上按钮,上面的一层(按住2 秒以上,顶层)即被预约。
按动下按钮,下面的一层(按住2 秒以上,底层)即被预约。
按住中按钮,以上被预约的楼层即被记录下来。
保持按住中按钮,门将被关闭。
结束:将EQDO 开关切到OFF 。
安装运行开始:将轿顶、轿内的自动/ 手动开关均切换到自动位。
按住下按钮,同时将EQDO 开关切到ON ,然后放开按钮。
运转:按动上按钮,轿厢慢车向上。
按动下按钮,轿厢慢车向下。
结束:将EQDO 开关切到OFF 。
楼层选择器的错开开始:按住上按钮,同时将EQDO 开关切到ON ,然后放开按钮实行:按动上按钮,上面的一层(按住2 秒以上,顶层)即被预约。
按动下按钮,下面的一层(按住2 秒以上,底层)即被预约。
按住中按钮,以上被预约的楼层上的选择器即错开。
结束:将EQDO 开关切到OFF在“呼叫记录”,“楼层选择器的错开”的实行过程中,所记录的呼叫楼层和选择器错开的楼层将会在LED 的bit0~bit7 上以2 进制数显示出来。
(操作开始之初显示的是当时轿厢所处的楼层)bit 7 □□□□□□□□□□□□bit 6 □□□□□□□□□□□□bit 5 □□□□□□□□□□□□bit 4 □□□□□□□□□□□□bit 3 □□□□□□□■■■■■bit 2 □□□■■■■□□□□■bit 1 □■■□□■■□□■■□bit 0 ■□■□■□■□■□■□表示--1--2--3--4--5--6--7--8--9--10-11-12 ……平常表示【SEL=0 数据=0 】时LED 的显示灯亮高速闪动低速闪动熄灭Bit7有项目代码------无项目代码Bit6地震时管制运行火灾时,自备电,漏水时的管制停车运转平常Bit5与IF61 ,IF66 通信断开------与IF61 ,IF66 通信正常Bit4与SV ,其它号机通信断开与SV ( MAIN )通信断开---与SV ,其它号机通信正常Bit3与COB/ 候梯厅电脑通信断开---*6与COB/ 候梯厅电脑通信正常Bit2启动禁止高速运转禁止---高速运转可能Bit1门关闭完成位置门中间位置---门打开完成位置Bit0门区内------门区外富士达电梯控制屏操作方法E411中文翻译( 故障灯)1.DZ或ADZ 与MCSS的命令状态不一致2.超过110%的额定速度3.终端超速4.SPPT反馈速度与MCSS 指令速度差超过一定范围5.SPPT 反馈速度与PVT反馈速度之差大于一定值6.U. D 继电器状态与命令状态不一致7.DZ感应器故障,感应器坏(于距平层600ms至2000ms之间检查三只感应器,感应器应在OFF状态)8.SC 继电器状态与MCSS给出的指令不相符9.安全回路断开(此时EES继电器应吸合)10.拯救运行失败11.心脏跳动。
掺铒光纤放大器 第2部分:L波段掺铒光纤放大器-最新国标
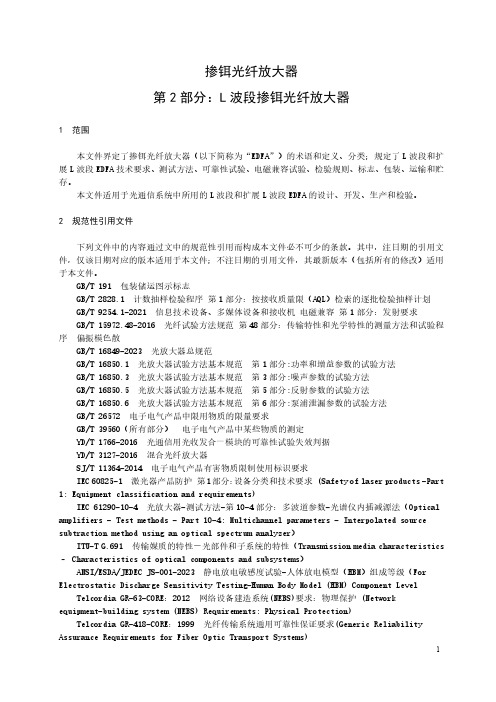
掺铒光纤放大器第2部分:L波段掺铒光纤放大器1范围本文件界定了掺铒光纤放大器(以下简称为“EDFA”)的术语和定义、分类;规定了L波段和扩展L波段EDFA技术要求、测试方法、可靠性试验、电磁兼容试验、检验规则、标志、包装、运输和贮存。
本文件适用于光通信系统中所用的L波段和扩展L波段EDFA的设计、开发、生产和检验。
2规范性引用文件下列文件中的内容通过文中的规范性引用而构成本文件必不可少的条款。
其中,注日期的引用文件,仅该日期对应的版本适用于本文件;不注日期的引用文件,其最新版本(包括所有的修改)适用于本文件。
GB/T191包装储运图示标志GB/T2828.1计数抽样检验程序第1部分:按接收质量限(AQL)检索的逐批检验抽样计划GB/T9254.1-2021信息技术设备、多媒体设备和接收机电磁兼容第1部分:发射要求GB/T15972.48-2016光纤试验方法规范第48部分:传输特性和光学特性的测量方法和试验程序偏振模色散GB/T16849-2023光放大器总规范GB/T16850.1光放大器试验方法基本规范第1部分:功率和增益参数的试验方法GB/T16850.3光放大器试验方法基本规范第3部分:噪声参数的试验方法GB/T16850.5光放大器试验方法基本规范第5部分:反射参数的试验方法GB/T16850.6光放大器试验方法基本规范第6部分:泵浦泄漏参数的试验方法GB/T26572电子电气产品中限用物质的限量要求GB/T39560(所有部分)电子电气产品中某些物质的测定YD/T1766-2016光通信用光收发合一模块的可靠性试验失效判据YD/T3127-2016混合光纤放大器SJ/T11364-2014电子电气产品有害物质限制使用标识要求IEC60825-1激光器产品防护第1部分:设备分类和技术要求(Safety of laser products-Part 1:Equipment classification and requirements)IEC61290-10-4光放大器-测试方法-第10-4部分:多波道参数-光谱仪内插减源法(Optical amplifiers-Test methods-Part10-4:Multichannel parameters-Interpolated source subtraction method using an optical spectrum analyzer)ITU-T G.691传输媒质的特性-光部件和子系统的特性(Transmission media characteristics –Characteristics of optical components and subsystems)ANSI/ESDA/JEDEC JS-001-2023静电放电敏感度试验-人体放电模型(HBM)组成等级(For Electrostatic Discharge Sensitivity Testing-Human Body Model(HBM)Component Level Telcordia GR-63-CORE:2012网络设备建造系统(NEBS)要求:物理保护(Networkequipment-building system(NEBS)Requirements:Physical Protection)Telcordia GR-418-CORE:1999光纤传输系统通用可靠性保证要求(Generic Reliability Assurance Requirements for Fiber Optic Transport Systems)Telcordia GR-468-CORE:2004电信设备用光电子器件通用可靠性保证要求(GenericReliability Assurance Requirements for Optoelectronic Devices Used in Telecommunications Equipment)Telcordia GR-1312-CORE:1999光纤放大器和专有波分复用系统总规范(Generic Requirements for Optical Fiber Amplifiers and Proprietary Dense Wavelength-Division Multiplexed Systems)3术语和定义GB/T 16849-2023界定的以及下列术语和定义适用于本文件。
PSX691U配置工具维护手册
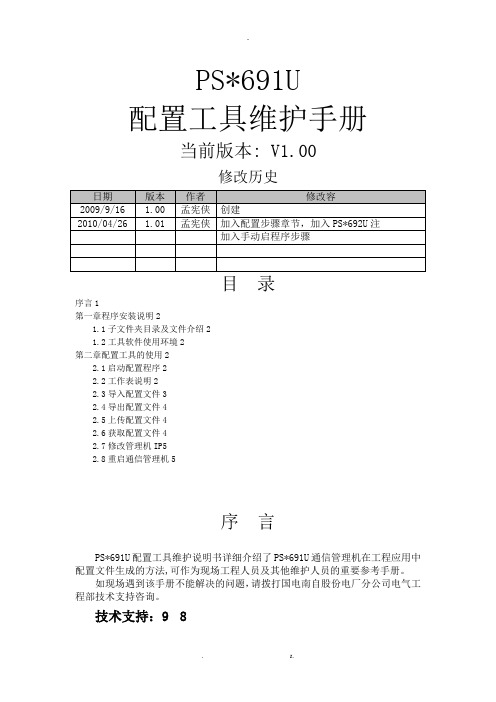
PS*691U配置工具维护手册当前版本: V1.00修改历史目录序言1第一章程序安装说明21.1子文件夹目录及文件介绍21.2工具软件使用环境2第二章配置工具的使用22.1启动配置程序22.2工作表说明22.3导入配置文件32.4导出配置文件42.5上传配置文件42.6获取配置文件42.7修改管理机IP52.8重启通信管理机5序言PS*691U配置工具维护说明书详细介绍了PS*691U通信管理机在工程应用中配置文件生成的方法,可作为现场工程人员及其他维护人员的重要参考手册。
如现场遇到该手册不能解决的问题,请拨打国电南自股份电厂分公司电气工程部技术支持咨询。
技术支持:9 8第一章程序安装说明PS*691U配置工具采用绿色安装方式,只需COPY到计算机上即可。
1.1子文件夹目录及文件介绍以D:\为COPY路径举例介绍,图示如下:由图可见,PS*691UCFG目录下包含,DOC、PS*691UFTPTools两个子目录,bdconfig.ini、PS*691U_CFG.*lsm和PS*691U配置.*ls*3个文件。
具体子目录及文件解释如下:1、DOC目录下存放一些工具的使用手册;2、PS*691UFTPTools目录存放用于配置文件上传/下载的工具软件;3、Bdconfig.ini是PS*691U示例配置文件;4、PS*691U_CFG.*lsm是配置脚本文件;5、PS*691U配置.*ls*是PS*691U的配置工具程序。
1.2工具软件使用环境操作系统:Microsoft Windows *P以上.Net环境:Microsoft .Net Framework 2.0以上E*cel: Office 2007第二章配置工具的使用2.1启动配置程序双击PS*691U配置.*ls*文件2.2工作表说明配置工具下方有工作表导航图,如下图所示:配置工具工作表包括型号模板首页、基本信息、测量模板、保护测量模板、遥信模板、运行告警模板、保护动作模板、遥脉模板、遥控模板、遥调模板、定值区间模板、定值模板、压板模板、扰动记录模板、、LAN、设备信息、转发基本信息、转发遥测信息、转发遥信信息、转发遥脉信息。
Elkay Lustertone Stainless Steel 25英寸x22英寸x8-1 8英寸

PRODUCT SPECIFICATIONSElkay Lustertone Stainless Steel 25" x 22" x 8-1/8", Single Bowl Top Mount Sink with Perfect Drain. Sink is manufactured from 18 gauge 304 Stainless Steel with a Lustertone finish, Center drain placement, and Sides and Bottom pads.Cutout Dimensions for Top Mount Installation:24-3/8" x 21-3/8" (619mm x 543mm) with 1-1/2" (38mm) corner radiusPerfect Drain: Seamlessly welded stainless steel collar eliminates the gap between a traditional drain and the sink for a sanitary and gap free installation. An InSinkErator® garbage disposer can be installed on either sink bowl for user convenience. Patent PendingIncluded with Product:One LKPD1 Perfect Drain and StrainerAMERICAN PRIDE. A LIFETIME TRADITION.Like your family, the Elkay family has values and traditions that endure. For almost a century, Elkay has been a family-owned and operated company, providing thousands of jobs that support our families and communities.Sinks are listed by IAPMO ®as meeting the applicablerequirements of the Uniform Plumbing Code ®, International Plumbing Code ®, and National Plumbing Code of Canada.Product Compliance:ASME A112.19.3/CSA B45.4 BUY AMERICAN ACTAccessory: ASME A112.18.2/CSA B125.2Clean and Care Manual (PDF)Installation Instructions (PDF) - 74180147Installation Instructions (PDF) - 74180289_Disposer Installation Instructions (PDF) - 74180340-USA_Drain Limited Lifetime Warranty (PDF)Similar models are available with: extra deep bowlsHole Drilling Configurations:PART:________________________________QTY: _____________ PROJECT:______________________________________________ CONTACT:______________________________________________ DATE:__________________________________________________ NOTES:_________________________________________________APPROVAL:_____________________________________________Installation Profile:。
- 1、下载文档前请自行甄别文档内容的完整性,平台不提供额外的编辑、内容补充、找答案等附加服务。
- 2、"仅部分预览"的文档,不可在线预览部分如存在完整性等问题,可反馈申请退款(可完整预览的文档不适用该条件!)。
- 3、如文档侵犯您的权益,请联系客服反馈,我们会尽快为您处理(人工客服工作时间:9:00-18:30)。
Operating Voltage
DC 3.3V ± 5%
Power Biblioteka onsumption11b 11g 11n TX : ≦ 850mA TX : ≦ 750mA TX : ≦ 750mA RX : ≦ 650mA RX : ≦ 650mA RX : ≦ 650mA
Enhanced Multimedia Support
XN-691 employed WMM (WiFi Multimedia) technology, enabling multimedia applications to secure the largest bandwidth share in a wireless network. Complying to the IEEE 802.11e WLAN QoS draft standard, this product will improve users’ Internet experience from plain data transmission to rich multimedia enjoyment without waiting.
XN-691 is a draft 2.0 802.11n wireless miniPCI that delivers incomparable wireless performance for your environment. This wireless miniPCI delivers up to 5x faster speeds than 802.11g while staying backward compatible with 802.11g and 802.11b networks.
MIMO (Multiple-input multiple-output ) Technologies
With WPS support, the highest level of security will be automatically established between the wireless router that embedded XN-691 and WPS-enabled wireless clients to protect the wireless traffic from hackers or unauthorized users. The wireless router that embedded XN-691 is equipped with easy security setup. Simply with one button pushed, users can easily configure the wireless client to connect with the wireless router embedded XN-691.
Radio
Antenna Output Power @ 25℃ (for CE) Sensitivity 3 U.FL-R-SMT compliant connectors (2T3R) IEEE 802.11b 18dBm (max) IEEE 802.11g 17dBm (max) IEEE 802.11n 17dBm @ HT20 (max) 17dBm @ HT40 (max) IEEE 802.11n 2.4GHz HT20 ≦ -68dBm (MCS15) HT40 ≦ -65dBm (MCS15)
IEEE 802.11b 11Mbps ≦ -84dBm
IEEE 802.11g 54Mbps ≦-72dBm
Operating Frequency
North America : 2.412 GHz ~ 2.462 GHz (CH1 ~ CH11)
Japan : 2.412 GHz ~ 2.484 GHz (802.11b only ; 802.11g : CH13)
Environment Specification
Operating Temperature Storage Temperature Operating/Storage Humidity 0 ~ 55 ℃ -20 ~ 70 ℃ 20 to 95% RH
Warranty
12 months
XN-691
IEEE 802.11b/g/n 2.4GHz Wireless Mini-PCI Card
•High-speed Wireless-N (draft 802.11n v2.0 ) networking, data Rate up to 300Mbps at 40MHz •Linux drivers support with the complete software feature sets •MIMO technology with 3 antenna connectors available •Complied with IEEE802.11b/g Ultimate Performance
*Draft-N complaint refers to the compliance of IEEE802.11N draft 2.0
Product Description
IEEE 802.11n Draft 2.0 compliant 2.4GHz WLAN Mini-PCI Card
Host Interface
Software Specification
Supported OS Security Linux only WEP/WAP-PSK,WPA-enterprise/WPA2-PSK,WPA2-enterprise
Physical Specification
Dimension Weight 59.6mm(L) * 44.45mm(W) * 3.5mm(H) ≦ 15 g
Europe ETSI : 2.412 ~ 2.472 GHz Modulation IEEE 802.11b (DSSS): CCK, DQPSK, DBPSK IEEE 802.11g (OFDM/DSSS): QAM-64, QAM-16, QPSK, BPSK IEEE 802.11n (OFDM/DSSS): QAM-64, QAM-16, QPSK, BPSK