铸造工艺设计讲课用
铸造工艺基础大全课件
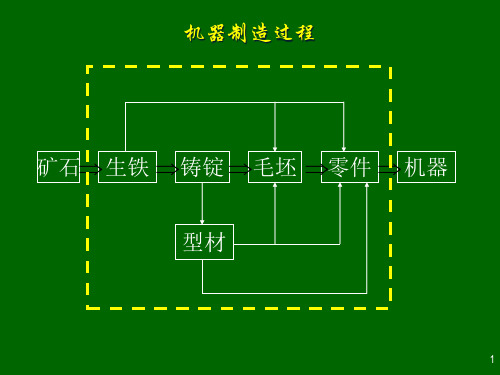
30
二 .铸件旳变形与预防 由铸造应力旳形成过程可知,铸件旳变形发生 在铸造应力超出材料旳屈服极限时。所以预 防铸件产生变形旳根本措施是消除铸造应力。 另外还能够从工艺上采用措施 1)反变形-----制造模型时采用反变形。 2)变化铸件构造----如改用弯轮辐替代直轮辐 3)设置拉筋----在铸造应力集中旳部位设置拉 筋,热处理后清除 4)控制打箱时间。
应力。 内应力发生在铸件凝固后来旳继续冷却过程中, 一般以为由下列三种情形产生: 1)二次结晶时,新相与旧相体积不同,膨胀与收缩将 产生----相变应力。 2)温度分布不同,各处收缩量不同步,内部相互制约, 产生---热应力。 3)收缩时受到铸型、型芯旳阻碍,产生----收缩应力。
26
应力状态------拉应力和压应力、剪应力。 应力性质-----分为临时应力和残余应力。 1 .热应力----因为铸件旳壁厚不均匀、各部分旳 冷却速度不同,使得在同一时期内铸件各部 分收缩不一致而引起旳应力。
机器制造过程
矿石生铁 铸锭 毛坯 零件 机器 型材
1
第二节 铸造
第一 铸造工艺基础 铸造----将液态合金浇注到与零件形 状、尺寸相适应旳铸型空腔中,待 其冷却凝固,以取得毛坯或零件旳 生产措施称为铸造。 影响铸件质量旳原因诸多,其中合 金旳铸造工艺性就是主要原因之一。
2
3
铸造生产过程
§1 液态合金旳充型 充型----液态合金填充铸型旳过程。 充型能力-----液态合金充斥铸型型腔,取得 形状完整、轮廓清楚铸件旳能力。 影响充型能力旳主要原因有: 一 .合金旳流动性 流动性----液态合金本身旳流动能力。
27
再结晶温度以上时,金 属处于塑性状态,不产
铸造工艺学课件(全)

k:安全系数1.3~1.5
特殊定位芯头
铸造工艺流程图: 砂箱制 作准备
型砂准备
模型制 作准备
芯盒制 作准备 芯砂准备
芯骨制作
制芯
合箱检验
造型
下芯
合箱
浇注
冷却凝固 落砂开箱 去除浇冒口
熔炼
热处理 铸件
清理打磨 去毛刺
砂箱高 度过高
多箱造型控 制砂箱高度
例5:受力件的分型面的选择不应消弱铸 件结构强度。
例6:注意减轻铸件清理和机械加工量。
砂芯设计
➢砂芯本体设计 ➢芯头设计
本体设计的典型实例
分盒面2
分盒面1
1、能制作出来;
2、能进行烘干;
3、如果自硬,则不 需烘干,在型内干 后直接取出使用。
砂芯本体设计的基本步骤
4、作业:抄画教材图,并说明选择图中 浇注位置和分型面的原因。
5、确定下面铸件的浇注位置和分型面
浇注位置的确定
判定浇注位置的优先次序为:
保证铸件质量→凝固方式→ 充型→工艺操作
例1:铸件主要加工面或重要加工面,应尽 量置于下部或垂直放置。
重要面
重要面
图 3-2-36
例2:能保证顺序凝固。例如,厚大部分在上部,或 按一定次序厚大部分靠近冒口。
确定砂芯总体形状 定位形式初定(芯头位置) 制作过程(分盒面确定) 砂芯分解 分解后砂芯之间的定位
砂芯放置方式(考虑烘干或相关制作过程) 再定各砂芯间的定位方式 确定砂芯组合方式 终定砂芯
例1:保证铸件内腔尺寸精度:铸件内 腔尺寸较严的部分应当由同一半砂芯 形成,避免为分盒面分割。
教学课件第四节铸造工艺设计

第5页
二、铸造成形工艺参数的选择
工艺参数
机械加工余量 起模斜度 铸造圆角 收缩率 型芯的形状和尺寸
第6页
机械加工余量:铸件上为切削加工而加大的尺寸; 铸件上标有加工符号的表面,必须留有。大小根 据合金种类、生产批量、铸件大小、加工面在铸 型中的位置确定
附表 灰铸铁件的机械加工余量(mm)
1、铸造工艺对铸件结构的要求 2、合金的铸造性能对铸件结构的要求
第 15 页
1、铸造工艺对铸件结构的要求
(一)铸件的外形设计 1.铸件应避免外部侧凹以便于起模,减少分型面
端盖的设计
1、铸造工艺对铸件结构的要求
(一)铸件的外形设计 2. 应尽量使分型面平直 平直的分型面可避免操作费时的挖砂造型或假箱造型; 同时,铸件的毛边少,便于清理。
中 下
返回
图例 铸造大平板
模型图
上 下 上 下
返回
H1
H2
浇口
上 下 上 下
图例 某箱体铸件
返回
明冒口
上 中
上 中
中 下
暗冒口
图例 卷扬筒铸件
中 下
返回
上 中 中 下
更详细示意
上 下
返回
方案2
方案1
避免活块的例子
返回
减少型芯的例子
方案1
方案2
方案1: 必须制作型芯
方案2: 可以自带型芯
第7页
铸件上的孔、槽:大孔应铸出,如果该孔需切削 加工,则要加余量;小孔不必铸出,留待机械加 工更经济
表3-1 砂型铸造最小铸孔(mm)
铸造合金
壁厚
最小孔径
3-10
6-10
灰铸铁
20-25
10-15
教学课件:第四节铸造工艺设计

数字化技术可以帮助设计师快速 准确地预测铸造过程中可能出现 的问题,提高设计效率和产品质
量。
数字化技术还可以实现远程协作 和在线评审,提高工作效率和降
低沟通成本。
环保材料的使用
随着环保意识的提高,铸造行 业开始广泛使用环保材料,如 再生材料、低铅材料等。
使用环保材料可以降低生产过 程中的污染排放,提高企业的 环保意识和社会责任感。
提高铸造工艺设计水平的建议
培养专业人才
加强铸造工艺设计人才的培养和引进,建 立完善的人才激励机制,提高设计人员的
专业素质和创新能力。
A 加强科技创新
鼓励企业加大科技研发投入,引进 先进技术和设备,提高铸造工艺的
技术水平和生产效率。
B
C
D
加强行业合作与交流
加强企业间的合作与交流,共同推动铸造 工艺设计的进步和发展,实现资源共享和 优势互补。
推进数字化转型
利用数字化技术实现铸造工艺设计的智能 化和精细化,提高设计效率和产品质量。
THANKS
感谢观看
考虑浇注系统的排渣和排气性 能,以避免铸造缺陷的产生。
对浇注系统进行优化设计,降 低金属液的消耗和能源件的结构和工艺要求,合理设 置冒口的位置和大小。
考虑冒口和出气孔的散热性能,以避 免铸件产生缩孔和裂纹等缺陷。
设计出气孔的位置和大小,以确保金 属液在充型过程中能够顺利排出气体。
铸造工艺设计的流程
确定浇注系统
设计合理的浇注系统,确保金 属液能够平稳、均匀地流入型
腔。
确定冒口和冷铁
根据铸件的要求和铸造方法, 设计合适的冒口和冷铁,控制 铸件的冷却速度和补缩效果。
确定工艺参数
根据铸件的要求和生产条件,选 择合适的工艺参数,如金属液的 成分、浇注温度、浇注速度等。
最新1.3铸造工艺设计课件教学讲义ppt
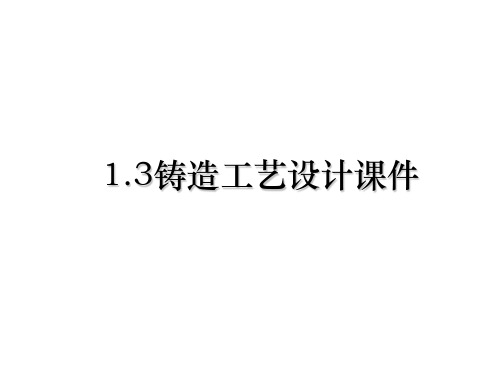
✓铸件最小壁厚与 合金种类、铸件尺 寸等因素有关。
19
1.3 铸造工艺设计 铸件壁厚不易过厚 ✓ 过大的壁厚会引起铸件晶粒粗大,强度下降,
产生缩孔、缩松等缺陷
20
1.3 铸造工艺设计 ➢2、铸件壁厚尽量均匀 ✓壁厚不均易产生缩孔和缩松,内应力和变形、开 裂等缺陷。
30
1.3 铸造工艺设计
❖ 浇注位置选择原则 ➢ 重要面朝下 ➢ 大平面朝下 ➢ 薄壁部分置于铸型下部或使其处于垂直或 倾斜位置 ➢ 厚大部分朝上或侧面 ➢ 型芯少而稳定
31
1.3 铸造工艺设计 ➢ 重要面朝下 ✓ 铸件上部易产生砂眼、气孔、夹渣等缺陷,且晶
粒较粗大。重要加工面应朝下或位于侧面;重要 加工面有数个时,应将较大的平面朝下。
➢ 选择浇注系统类型。 ➢ 确定内交道在铸件上的位置、数目和金属液引入方
向。 ➢ 决定直浇道的位置和高度。 ➢ 计算浇注时间并核算金属上升速度。 ➢ 计算阻流截面积S阻。 ➢ 确定浇口比并计算各组员截面积。 ➢ 绘出浇注系统图。
42
1.3 铸造工艺设计 2.铸件分型面的选择 ✓ 指上、下、左、右砂型间的接触面,应能在保
简化内腔自带型芯
13
1.3 铸造工艺设计
框形与肋板结构
肋板与框架立体图
14
✓ 型芯在铸型中应支撑牢固
1.3 铸造工艺设计
内腔是否连通立体图 内腔连通不连通零件图
内腔连通不连通型芯放置
15
1.3 铸造工艺设计
✓ 增加型芯头或工艺孔,以固定型芯,同时便于 型芯固排清
封闭内腔立体图
封闭内腔零件图 封闭内腔型芯无法取出
➢ 浇口杯 ➢ 直浇道 ➢ 横浇道 ➢ 内浇道
铸造工艺设计工艺流程培训课程

铸造工艺设计工艺流程培训课程一、介绍铸造工艺设计是铸造行业中至关重要的环节之一,它直接影响到铸造产品的质量和成本。
本课程旨在系统地介绍铸造工艺设计的基本原理、流程和技术要点,帮助学员掌握铸造工艺设计的关键技能,提升在实际工作中的应用能力。
二、课程大纲1.铸造工艺设计概述–铸造工艺设计的定义和意义–铸造工艺设计的基本原理2.铸造工艺设计流程–铸型设计–浇注系统设计–固化系统设计–冷却系统设计–除尘系统设计3.铸造工艺设计技术要点–材料的选择–模具设计–热处理工艺–排气系统设计4.铸造工艺设计案例分析–不同材料的铸造工艺设计–复杂铸件的工艺设计–高精度铸造工艺设计三、教学方法本课程采用理论讲解、案例分析和实践操作相结合的教学方法。
学员将通过课堂学习和实际操作,加深对铸造工艺设计的理解,并掌握实际操作技能。
四、目标群体适合从事铸造行业的工程技术人员、铸造工艺设计师以及对铸造工艺设计感兴趣的人员参加。
五、学习成果经过本课程学习,学员将掌握以下技能: - 熟悉铸造工艺设计的基本原理 - 熟练掌握铸造工艺设计的流程和方法 - 能够运用所学知识解决铸造工艺设计中的实际问题 - 提升铸造产品的质量和成本控制能力六、结业证书学员参加课程培训并通过考核后,将获得铸造工艺设计工艺流程培训课程结业证书,证明其在该领域具备一定的知识和技能。
七、总结铸造工艺设计工艺流程培训课程旨在为铸造行业的从业人员提供一次系统的学习和培训机会,帮助他们更好地掌握铸造工艺设计的技能,提高工作效率和质量。
希望通过本课程的学习,学员能够在实际工作中取得更好的成绩,为铸造行业的发展贡献自己的力量。
感谢大家的参与和支持!。
铸造工艺设计工艺流程培训课程
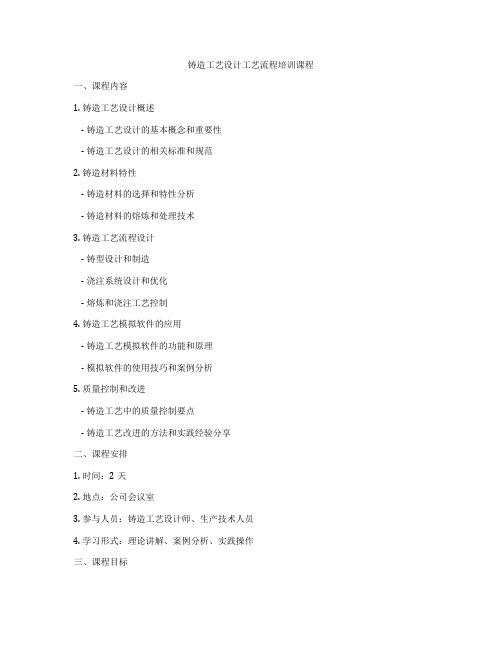
铸造工艺设计工艺流程培训课程一、课程内容1. 铸造工艺设计概述- 铸造工艺设计的基本概念和重要性- 铸造工艺设计的相关标准和规范2. 铸造材料特性- 铸造材料的选择和特性分析- 铸造材料的熔炼和处理技术3. 铸造工艺流程设计- 铸型设计和制造- 浇注系统设计和优化- 熔炼和浇注工艺控制4. 铸造工艺模拟软件的应用- 铸造工艺模拟软件的功能和原理- 模拟软件的使用技巧和案例分析5. 质量控制和改进- 铸造工艺中的质量控制要点- 铸造工艺改进的方法和实践经验分享二、课程安排1. 时间:2天2. 地点:公司会议室3. 参与人员:铸造工艺设计师、生产技术人员4. 学习形式:理论讲解、案例分析、实践操作三、课程目标通过本次培训,参与人员将能够掌握铸造工艺设计的基本理论和实践技巧,提高铸造工艺设计水平,增强质量控制意识,提高产品质量和生产效率。
培训的内容将围绕铸造工艺设计的全流程展开,通过理论讲解和实际操作相结合的培训方式,帮助参与人员系统地掌握铸造工艺设计的各个环节,提高其技术水平和实操能力。
通过培训课程的学习,参与人员将能够在以后的工作中更加熟练地进行铸造工艺设计,并能够结合实际工作经验进行质量控制和工艺改进,为公司的产品质量和生产效率提升贡献自己的力量。
对于铸造工艺设计师和生产技术人员来说,掌握铸造工艺设计的相关知识是至关重要的。
铸造工艺设计是整个生产过程中的一项关键环节,它直接影响着产品的质量、成本和生产效率。
因此,本次培训课程将着重介绍铸造工艺设计的概念、原理、流程和实践技巧,以及如何运用铸造工艺模拟软件来优化设计和控制生产过程。
首先,课程将从铸造工艺设计的概述开始,介绍铸造工艺设计的基本概念和其在整个生产过程中的重要性。
参与人员将了解到铸造工艺设计的意义不仅仅在于制定生产流程和工艺参数,更在于对铸造材料进行合理选用和设计,以确保产品质量和生产效率。
接着,课程将详细介绍铸造材料的特性,包括铸造材料的选择和特性分析,以及铸造材料的熔炼和处理技术。
铸造工艺设计讲课用53页PPT

16、自己选择的路、跪着也要把它走 完。 17、一般情况下)不想三年以后的事, 只想现 在的事 。现在 有成就 ,以后 才能更 明。 19、学习的关键--重复。
20、懦弱的人只会裹足不前,莽撞的 人只能 引为烧 身,只 有真正 勇敢的 人才能 所向披 靡。
谢谢你的阅读
❖ 知识就是财富 ❖ 丰富你的人生
71、既然我已经踏上这条道路,那么,任何东西都不应妨碍我沿着这条路走下去。——康德 72、家庭成为快乐的种子在外也不致成为障碍物但在旅行之际却是夜间的伴侣。——西塞罗 73、坚持意志伟大的事业需要始终不渝的精神。——伏尔泰 74、路漫漫其修道远,吾将上下而求索。——屈原 75、内外相应,言行相称。——韩非
- 1、下载文档前请自行甄别文档内容的完整性,平台不提供额外的编辑、内容补充、找答案等附加服务。
- 2、"仅部分预览"的文档,不可在线预览部分如存在完整性等问题,可反馈申请退款(可完整预览的文档不适用该条件!)。
- 3、如文档侵犯您的权益,请联系客服反馈,我们会尽快为您处理(人工客服工作时间:9:00-18:30)。
设计依据:
在进行铸造工艺设计前,设计者应掌握生产 任务和要求,熟悉工厂和车间的生产条件, 这些是铸造工艺设计的基本依据.
设计内容: 铸造工艺设计内容的繁简程度,主要决定于 批量的大小,生产要求和生产条件.一般包括 下列内容:铸件(毛坯)图,铸造工艺图,上 下模板图,铸型装配图(合箱图),芯盒图, 工艺卡及技术说明书.
(2)分型面少,少用三箱;尽量减少型芯 的数量。
(3)少挖砂,分型面平直
3. 确定主要铸造工艺参数
(1) 加工余量 Machining Allowance(手册查找)
根据铸件精度等级、尺寸及重量允许偏差确定
加工余量是指铸件表面留出的准备切削去 的金属层厚度,根据尺寸公差等级和加工 余量等级确定。工艺图中用红色表示。
(4)砂芯边界线,如果和零件线或加工余量线、 冷铁线等重合时,则省去砂芯边界线。 (5)在剖面图上,砂芯线和加工余量线相互关系 处理上,不同工厂有不同做法:一种认为砂芯是 “透明体”,因而被芯子遮住的加工余量线部 分亦绘出,结果使加工余量红线贯穿整个砂芯 剖面 ;另一种认为 :砂芯是“非透明体”,因而, 被砂芯遮住的加工余量线不绘出。推荐后一种 方法,这种图面线条较少、清晰、便于观察。
(6)所标注的各种工艺尺寸或数据,不要盖住 产品图上的数据,应方便工人操作,符合工厂 的实际条件。例如标注拔模斜度,对于手工木 模,则应尽量标注尺寸(毫米)或比例(1/50);对 于金属模则应标注角度,而且所注角度应和工 厂常用铣刀角度相对应。
分型面 浇注位置 加工余量 冒口的形状和尺寸 浇口的形状和尺寸 砂芯个数和形状, 芯头形式、 尺寸和间隙 拔模斜度
芯头分为垂直型芯头和 水平型芯头,主要确定 芯头长度、斜度和间隙。 长度取决于型芯的直径 和长度。
型芯头长度的确定:为增加型芯的稳 定性,下芯头斜度小、高度大;为便 于合型,上芯头斜度大、高度小。可 查手册。
芯头间隙的确定:为便于下芯,芯头 与芯座之间应留有1-4mm的间隙 •5、砂型中铸件数目的确定 ——根据砂箱及零件的尺寸
•(2) 起模斜度 Pattern Draft, 为便于起模,在垂直于分型面的表面增 加的斜度。(铸件的斜度用红色表示)
•(3)铸造收缩余量 Casting Shrinkage Allowance。 为补偿铸件收缩,在模样上增大的尺寸为收缩 余量。
•(4)铸造圆角 Curving of Casting。制模时,壁的 连接和转角处要做成圆弧过渡、即铸 造圆角。 外圆角:Bull Nose 内圆角:Filleted Corner 内圆角半径:Fillet Radius 小铸件外圆角半径取2-8mm,内 圆角半径取4-16mm。
冒口、冷铁、加强筋设计
参造课本与手册
三. 绘制铸造工艺图 Foundry Molding Drawing
绘制程序
1、给定的零件图照抄; 2、在有关视图上标出不铸孔、槽、台阶及加工余量; 3、绘制拔模斜度; 4、标注浇注位置与分型面; 5、汇出砂芯形状、分块、芯头间隙、压紧环、防压 环、集砂槽及有关尺寸; 6、绘制浇冒口系统; 7、绘出冷铁、铸筋、活块,标出有关尺寸和数量; 8、标出铸造收缩率; 9、写出工艺图的技术要求和简易工艺说明。
按截面积比分类:封闭,开放式浇 注系统
:封闭式浇注系统有较好的阻渣能力,可防止金属液卷入 气体,消耗金属少,清理方便.缺点是:进入型腔的金属 液流速度高,易产生喷溅和冲砂,使金属氧化,使型内 金属液发生扰动,涡流和不平静.开放式浇注系统的优 点:进入型腔时金属液流速度小,充型平稳,冲刷力小, 金属氧化轻.缺点:阻渣效果稍差,内浇道较大,金属消 耗略多.(阻流截面积)奥赞公式: ;对于底注式: = -P/2 对于顶注式: = , P为阻流以上的型腔高度, 为阻流以上的金属压力头。 铸钢件和铸铁件浇注的不同
2、了解零件的技术要求,包括重要的加工面、公差配合、 表面粗糙度、材质及牌号、铸件尺寸与重量公差及其它特 殊要求。 3、审查零件结构是否符合铸造工艺要求。
4、预见零件可能产生的铸造缺陷,以便在选择铸造工艺 方案时采取相应的技术措施,保证铸件质量。
二、确定铸造工艺方案
1、选择铸造(造型)方法 2、确定浇注位置和分型面 3、铸造工艺参数的选择 4、砂芯设计 5、砂型中铸件数目的确定
面,以免产生浇不到、冷隔等缺陷。
(4)铸件的厚大部分应置于上部或侧
面,便于安置浇、冒口补缩。
2. 选择分型面应使工艺简单、操 作方便。 The Choose of Mold Joint
分型面选择原则:
四少两便
少用砂芯 少用活块 便于清理 便于合箱
(1)使铸件或主要型芯位于同一铸型以 避免错箱
浇注位置:浇注时铸件在铸型中所处的空 间位置。 浇注位置的确定原则是应保证铸件质量。 也涉及铸件尺寸精度及造型工艺过程。 应考虑:
确定原则:
(1)铸件重要加工面应朝下或处于侧面
(2)铸件的大平面尽可能朝下,
因为型腔顶面浇注时烘烤严重,型 砂易开裂、形成夹砂。
(3)铸件的薄壁部分应朝下或处于侧
五、设计说明书
1、首先在封面上写出设计题目、设计者 及班级、指导教师、年月日。 2、第二页为目录 。 3、然后是设计过程,按前面所讲设计顺 序写,对工艺设计中的特殊问题(如, 浇注位置、分型面等)要重点分析论证。 4、结束语 5、参考文献,与说明书中得引用对上, 用[1]标准。
六、设计成果资料装订要求
课程设计
——铸造工艺(工装)设计 Foundry Technology
设计目的
1、巩固、加深和运用铸造工艺学及其它 专业课和基础课知识; 2、使学生较系统地掌握铸造工艺及模具 设计的基本知识、基本方法和技能;
3、锻炼查阅资料和手册的基本能力,提 高绘图能力。
本次课程设计任务
设计时间:4周(17-20) 设计任务: 1、根据所给零件图进行结构分析; 2、根据零件结构特点和给定的铸造条件确定铸 造工艺,画出工艺图; 3、根据确定的工艺画出上、下模板图; 4、写出设计说明书,题目一律为“零件名称” 铸造工艺及工装设计; 给定标准砂箱尺寸: 850×550×165/165cm; 机器批量造型。
铸铁件浇注系统设计步骤:
1、选择浇注系统类型。 2、确定内浇道在铸件上的位置,数目和金属 引入方向。 3、决定直浇道的位置和高度(已给出)。 4、计算浇注时间并核算金属上升速度。 5、计算阻流截面积S阻。 6、根据选定的浇注系统类型按经验比例或理 论计算,确定浇口比,并计算各组元截面积 及尺寸,并查表加以圆整化,尽量做到标准 化。 7、绘出浇注系统图形。
设计中:特殊的圆角半径标出,通用的标准技 术说明中
(5)铸孔与非铸孔、槽与台阶是 否铸造确定
1、根据孔槽的径/深比确定是否铸出。 2、不铸出用红色标注, 3、铸出选用砂台或芯子。
•4、芯头设计 Cores Print Design。 是型芯的重要组成部分,起定位、支 撑和排出型芯内气体的作用。
铸造工艺图表达的内容
浇注位置,分型面,分模面,活块,本模的类 型和分型负数,加工余量,拔模斜度,不铸孔 和沟槽,砂芯个数和形状,芯头形式、尺寸和 间隙,分盒面,芯盒的填砂 ( 射砂 ) 方向,砂芯 负数,砂型的出气孔,砂芯出气方向、起吊方 向,下芯顺序,芯撑的位置、数目和规格,工 艺补正量,反变形量,非加工壁厚的负余量, 浇口和冒口的形状和尺寸,冷铁形状和个数, 收缩筋 ( 割筋 ) 和拉筋形状、尺寸和数量,和铸 件同时铸造的试样,铸造收缩率等
浇注系统的基本分类:(按内浇道在铸件上的位置分类) 1 顶注式浇注系统(简单式,楔形式,压变式,鱼淋式,搭边式) 2 底注式浇注系统(基本形式,牛角式,底雨淋式) 3 中间注入式浇注系统. 4 阶梯式浇注系统(多直浇道的阶梯式,用塞球发控制的阶梯 式,控制各组元比例的阶梯式,带缓冲或反直浇道的阶梯式).
铸造工艺图是在零件图上用规定的工艺 符号表示铸造工艺内容的图形。图中应 表示出铸件的浇注位置、分型面、铸造 工艺参数(机械加工余量,拔模斜度, 铸造收缩率,型芯的数量、形状及固定 方法和浇注系统等。
铸造工艺图是制造模样、芯盒、造型、 造芯和检验铸件的依据。
注意事项
(1)每项工艺符号只在某一视图或剖视图上表示 清楚即可。不必在每个视图上反应所有工艺符 号,以免符号遍布图纸、互相重叠。 (2) 加工余量的尺寸,如果顶面、孔内和底、 侧面数值相同时,图面上不标注尺寸,可填写 在图纸背面的“木模工艺卡”中,也可写在技 术条件中。 (3) 相同尺寸的铸造圆角、等角度的拔模斜度, 图形上可不标注,只写在技术条件中。
四、模板设计(绘制模板装配图)
板装配图按机械制图规定绘制; 3、根据已确定的工艺方案和工艺图的形状、大小要求 及给定型板尺寸进行设计布件; 4、模板装配图上应包括:模底板、模样、浇冒口系统、 出气孔、模样的定位与固定装置、砂箱的定位装置、 模板在造型机上的紧固装置; 5、模样设计包括:材料选择、尺寸计算和结构确定; 6、模样与底板装配:模样在底板上的布置和排列方式, 装配形式、定位和紧固形式等。各种标准件查机械零 件手册。按标准绘制。特别注意:单面模板上下模样 必须对位,保证铸件不产生错箱; 7、写出模板技术要求; 8、完成模板装配图的标题栏和明细表。(模板上只标 装配尺寸,包括配合种类与形位公差)
1、完成设计后,将设计说明书装订成册。 次序:设计说明书封面、设计任务书、说明 书正文、封底、 2、将全部图纸折叠成3号图面大小。利用电 脑绘图的同学另外提供电子版一份。(刻在 光盘上) 3、最后将全部设计成果装入资料袋中,袋 上写明:铸造工艺课程设计、设计题目、班 级、学生姓名、学号、指导教师、年月日。 然后交给指导教师。