微小尺寸零件表面缺陷光学检测方法
外观检测方法
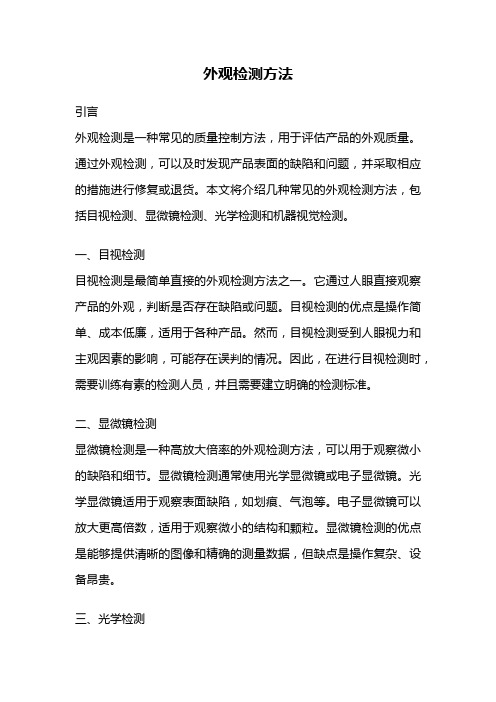
外观检测方法引言外观检测是一种常见的质量控制方法,用于评估产品的外观质量。
通过外观检测,可以及时发现产品表面的缺陷和问题,并采取相应的措施进行修复或退货。
本文将介绍几种常见的外观检测方法,包括目视检测、显微镜检测、光学检测和机器视觉检测。
一、目视检测目视检测是最简单直接的外观检测方法之一。
它通过人眼直接观察产品的外观,判断是否存在缺陷或问题。
目视检测的优点是操作简单、成本低廉,适用于各种产品。
然而,目视检测受到人眼视力和主观因素的影响,可能存在误判的情况。
因此,在进行目视检测时,需要训练有素的检测人员,并且需要建立明确的检测标准。
二、显微镜检测显微镜检测是一种高放大倍率的外观检测方法,可以用于观察微小的缺陷和细节。
显微镜检测通常使用光学显微镜或电子显微镜。
光学显微镜适用于观察表面缺陷,如划痕、气泡等。
电子显微镜可以放大更高倍数,适用于观察微小的结构和颗粒。
显微镜检测的优点是能够提供清晰的图像和精确的测量数据,但缺点是操作复杂、设备昂贵。
三、光学检测光学检测是一种利用光学原理检测产品外观的方法。
常用的光学检测方法包括透射光学检测和反射光学检测。
透射光学检测适用于透明或半透明材料的检测,如玻璃、塑料等。
反射光学检测适用于不透明材料的检测,如金属、陶瓷等。
光学检测的优点是非接触式检测,可以快速扫描大面积的产品外观,但受到光线和环境的影响,可能存在误判的情况。
四、机器视觉检测机器视觉检测是一种利用计算机视觉技术进行外观检测的方法。
它通过摄像机和图像处理算法,对产品的图像进行分析和判断。
机器视觉检测可以实现自动化和高速检测,减少了人为因素的干扰。
它适用于各种产品的外观检测,如电子产品、汽车零部件等。
机器视觉检测的缺点是设备和算法的复杂性,需要专业知识和技术支持。
结论外观检测是一种重要的质量控制方法,可以帮助企业及时发现和解决产品外观质量问题。
不同的外观检测方法具有各自的优缺点,可以根据产品特性和要求选择适合的方法。
零件光学超精密加工检测技术
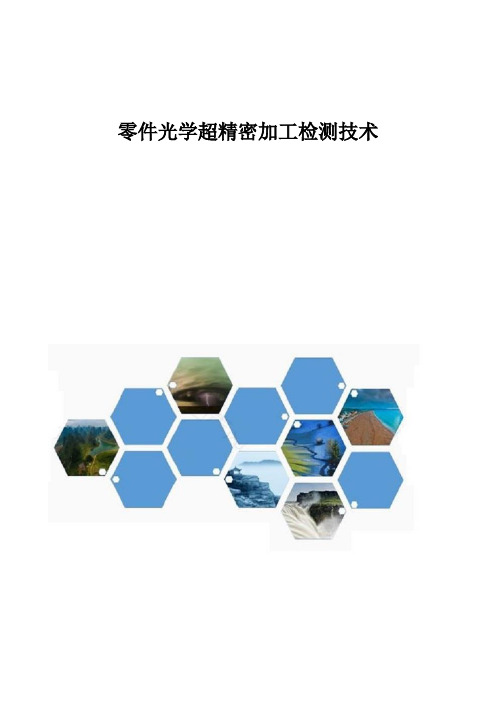
零件光学超精密加工检测技术摘要:随着数字数控机床和加工平台的产生与发展,机械零件的加工方式也向着大批量、专一化方向发展。
导致对机械零件的需求也逐渐加大,零件的尺寸和表面加工质量是否符合标准使用要求是影响机械零件正常工作的关键,因此,对机械零件的光学超精密检测成为主要研究任务。
机械零件表面的加工质量和尺寸大小虽然对零件的正常使用影响较低,但直接影响零件的可靠性、质量和使用寿命,而机械零件使用时间决定零件经济效益。
随着光学超精密加工技术的不断发展,零件光学超精密加工检测技术已成为超精密加工迫在眉睫的关键难题。
人工智能技术是一种新兴的用于模拟、延伸和扩展的智能理论、方法、技术及应用系统的一门新的技术科学。
人工智能技术中的机械学习法,使机械零件的光学超精密检测过程大大简化,并将操作结果保存在存储器中,便于后续光学超精密检测过程的快速执行。
关键词:光学检测;现状;发展引言单参数精密测量是精密测量中最简单的问题,近年来在复杂探测等问题中有了重要应用。
多参数精密测量复杂得多,参数之间存在精度制衡。
如何减少参数之间的精度制衡以实现多参数最优测量,是多参数精密测量的重要问题之一。
为了消除参数之间的精度制衡,研究人员将单参数测量实验中控制增强的次序测量技术应用到多参数测量中,通过调控测量系统动力学演化,完全解决了正演化算法中参数之间的精度制衡问题,实现了最优测量。
1测量系统将四组视觉传感器单元(包括CCD相机和激光器)分别竖直放置于精密零件两侧,垂直于精密零件中轴线,安装在精密零件两侧的立柱上;其中两组视觉传感器单元放置于精密零件一侧立柱上,另外两组视觉传感器单元放置于精密零件另一侧立柱上。
首先利用激光跟踪仪建立基坐标系统,然后对每个视觉传感器单元进行相机参数标定、光平面参数方程标定以及全局标定,最终得到相机的内参矩阵、相机到基坐标系下的全局标定矩阵以及激光平面在基坐标系下的平面方程,完成系统使用以及测量前的预处理。
光学零件表面疵病标准

学零件表面疵病标准擦痕、麻点说明(美国军用标准:MIL-O-13830A/)1.目的:光学零件表面质量说明及可接受缺陷(defects)规定,陆军用擦痕、麻点说明,MIL-13830A为了在实际检验中领会,执行此标准,特做以下文字规定。
擦痕(scratch)和麻点(dig)用两个代表其限制尺寸的号数来标记。
第二个号为麻点号。
擦痕指相对较长的缺陷,一般长比宽在20:1左右,如:擦痕、划丝、划伤等。
麻点指点状缺陷,一般为圆的如麻点、麻坑包含物等。
擦痕的判断可参考有关擦痕标准。
2.擦痕擦痕号(第一个号)表示擦痕最大宽度。
球面光学零件:擦痕的宽度等于最大宽度时其长度不能大于零件直径或有效孔径的25%。
每个零件不能多于两条擦痕。
柱面光学零件在直径20mm的范围内。
擦痕宽度等于最大宽度时,擦痕长度不大于5mm可以允许。
允许擦痕的最多数目为该有效柱面上直径为20mm的区域的多少。
例如:πDH=柱面面积(有效面积)其中:D=柱面镜的过光长度(高度)H=柱面镜的过光长度(高度)π=有效柱面面积/π20mm2=允许擦痕最大数当存在最宽擦痕,如果较小宽度的擦痕符合下面公式,可以接受。
∑(N×(L/D))≤(Nmax)/2其中:D=直径,N=测量的擦痕数,L=擦痕长度,Nmax=规定的擦痕号光学零件中擦痕数乘以擦痕长度和零件直径之比的和不大于擦痕号(规定)的一般可以接受。
一个擦痕其宽度大于擦痕规定数的(英寸),则不能接收。
当无最宽擦痕时,擦痕不能超过以下公式:光学零件中擦痕数乘以擦痕长度和零件直径之比的和不大于擦痕号,则可以接受。
小于10(宽)可以忽略。
3.麻点麻点号表示最大直径的麻点。
麻点号是以最大麻点的直径给出,单位为1/100mm(一丝)。
直径为20mm 的范围内最大直径的麻点不能超过一个。
如果麻点的直径超过规定尺寸则不接受(不规则麻点的直径为长径和短径之和除2)。
当最大直径麻点存在时,麻点符合以下尺寸则认为合格:∑D≤(Dmax)其中:D=麻点直径Dmax=规定允许的最大麻点直径。
无损检测技术中的光学检测方法详解

无损检测技术中的光学检测方法详解光学检测在无损检测技术中占据着重要的地位,它不仅能够快速准确地检测材料表面的缺陷,而且具有非破坏性的特点。
本文将详细介绍光学检测在无损检测中的应用及其原理。
光学检测方法主要包括视觉检测、红外热像检测和激光检测等。
其中,视觉检测是最常用的一种方法,通过人眼观察材料表面的变化来判断是否存在缺陷。
这种方法简单直观,适用于对表面缺陷进行初步检测,但对于微小缺陷的检测效果有限。
红外热像检测则利用物体发出的热能辐射来探测其表面的温度变化。
通过红外热像仪,可以将物体的表面温度转化为可见的图像,从而判断是否存在缺陷。
由于热像检测可以实时观测到物体的温度分布,因此可以非常准确地检测到潜在的缺陷。
激光检测是一种利用激光光源和光学传感器对材料进行扫描的方法。
通过测量激光的反射或散射,可以判断材料表面是否有缺陷。
激光检测具有高分辨率、高灵敏度和快速检测的特点,可以对微小缺陷进行准确的定位和识别。
除了以上几种方法,还有一些高级的光学检测技术,如照相测距法、摄影测距法、干扰法等。
这些方法利用光学原理和成像技术,对材料进行更加细致和精确的检测。
例如,照相测距法通过测量物体在两张照片上的位置差异来计算出物体的大小和形状。
摄影测距法则通过测量摄影图像中物体的像素大小来推测物体的实际大小。
干扰法则利用干涉现象来观察材料表面的微小变化,从而判断是否存在缺陷。
光学检测技术在无损检测中的应用非常广泛。
在制造业中,光学检测可以用来检测产品的外观缺陷、尺寸偏差和形状变化等。
在航空航天领域,光学检测可以用来检测飞机表面的裂纹和疲劳损伤。
在医学领域,光学检测可以用来检测人体表面的皮肤病变和眼睛疾病等。
在光学检测技术的发展过程中,还出现了一些新的技术和方法,如数字图像处理、光学成像和机器视觉等。
这些技术的应用使得光学检测更加智能化和自动化,大大提高了检测的准确性和效率。
总之,光学检测技术在无损检测中具备独特的优势,它能够快速准确地检测材料表面的缺陷,为生产和生活中的各个领域提供了重要的支持。
一种微小表面缺陷的机器视觉检测方法
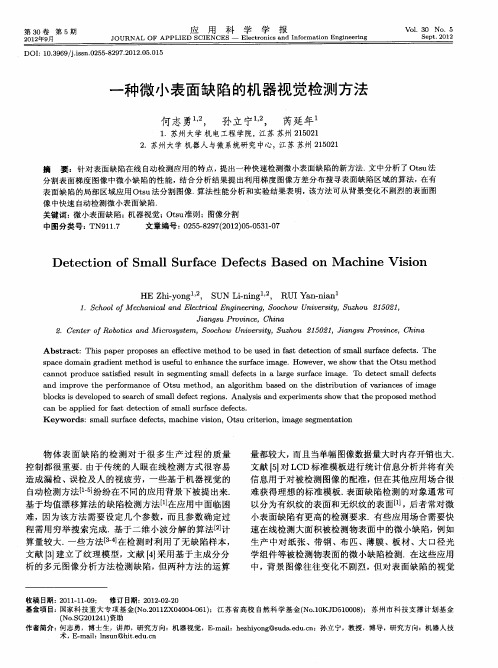
物 体表 面缺 陷 的检 测对 于很 多 生产 过程 的质量 控制都 很重要. 由于传统 的人眼在线检 测方式很 容易
量都较大 , 而且当单幅图像数据量大 时内存开销也大.
造成漏 检 、 误检及 人 的视疲 劳 , 一些基 于机器视 觉 的 自动检测方法 【5 1】 - 纷纷在 不同的应用背景下被 提 出来. 基于均值漂移 算法 的缺 陷检测 方法 [在应用 中面 临 困 1 ]
像 中快 速 自动 检 测 微 小 表 面 缺 陷 .
关键词 :微小表面缺陷 ; 机器视觉 ; s 准则 ;图像分割 Otu
中图分类号: N 1. T 91 7
文章编号: 25 272 1)5 5 1 7 05— 9(020— 3— 8 0 0
D e e t o f S a lSur a e D e e t s d o a hi ii n t c in o m l fc f c s Ba e n M c ne V so
第3 卷 第5 0 期
2 2 9 01 年 月
应
用
科
学
学
报
Vb .3O No.5 1
S p . 01 e t2 2
J OURNAL OF APPLI ED CI S ENCES — Elc r n c n nfr a in En ie rn e to isa d I o m to gn e ig
c n o r d c a if d r s l n s g e tn m a ld f c s i a g u f c ma e a n t p o u e s ts e e u t i e m n i g s l e e t n a lr e s r a e i g .To d t c m a ld f c s i e e ts l ee t adi n mpr v h ro m a c f Ot u me h d,a l o ih ba e n t e d s rb t o f v i n e fi a e o e t e pe f r n e o s t o n a g rt m s d o h it i u i n o a a c s o r m g
(美军标)光学零件表面疵病标准-MIL13830A(摘要)
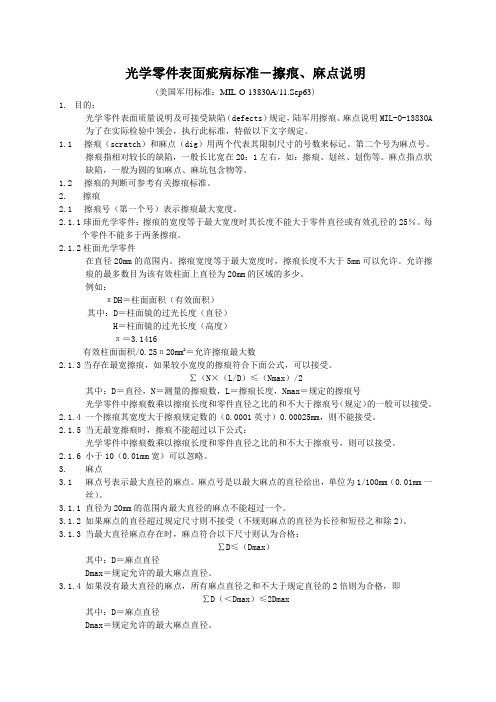
光学零件表面疵病标准-擦痕、麻点说明(美国军用标准:MIL-O-13830A/11.Sep63)1.目的:光学零件表面质量说明及可接受缺陷(defects)规定,陆军用擦痕、麻点说明MIL-O-13830A 为了在实际检验中领会,执行此标准,特做以下文字规定。
1.1擦痕(scratch)和麻点(dig)用两个代表其限制尺寸的号数来标记。
第二个号为麻点号。
擦痕指相对较长的缺陷,一般长比宽在20:1左右,如:擦痕、划丝、划伤等。
麻点指点状缺陷,一般为圆的如麻点、麻坑包含物等。
1.2擦痕的判断可参考有关擦痕标准。
2.擦痕2.1擦痕号(第一个号)表示擦痕最大宽度。
2.1.1球面光学零件:擦痕的宽度等于最大宽度时其长度不能大于零件直径或有效孔径的25%。
每个零件不能多于两条擦痕。
2.1.2柱面光学零件在直径20mm的范围内。
擦痕宽度等于最大宽度时,擦痕长度不大于5mm可以允许。
允许擦痕的最多数目为该有效柱面上直径为20mm的区域的多少。
例如:πDH=柱面面积(有效面积)其中:D=柱面镜的过光长度(直径)H=柱面镜的过光长度(高度)π=3.1416有效柱面面积/0.25π20mm2=允许擦痕最大数2.1.3当存在最宽擦痕,如果较小宽度的擦痕符合下面公式,可以接受。
∑(N×(L/D)≤(Nmax)/2其中:D=直径,N=测量的擦痕数,L=擦痕长度,Nmax=规定的擦痕号光学零件中擦痕数乘以擦痕长度和零件直径之比的和不大于擦痕号(规定)的一般可以接受。
2.1.4 一个擦痕其宽度大于擦痕规定数的(0.0001英寸)0.00025mm,则不能接受。
2.1.5 当无最宽擦痕时,擦痕不能超过以下公式:光学零件中擦痕数乘以擦痕长度和零件直径之比的和不大于擦痕号,则可以接受。
2.1.6 小于10(0.01mm宽)可以忽略。
3. 麻点3.1 麻点号表示最大直径的麻点。
麻点号是以最大麻点的直径给出,单位为1/100mm(0.01mm一丝)。
高曲率微小零件表面缺陷及外形尺寸测量系统研究

第37卷,增刊红外与激光工程2008年4月V ol.37SupplementInfrared and Laser EngineeringApr.2008收稿日期:2008-04-21作者简介:葛文谦(1977-),男,黑龙江大庆人,博士生,主要从事视觉检测和图像处理等方面的研究。
Email:gewenqian@导师简介:赵慧洁(66),女,辽宁沈阳人,教授,主要从事机器视觉、光电精密测试、遥感信息处理等方面的研究。
jz @高曲率微小零件表面缺陷及外形尺寸测量系统研究葛文谦,赵慧洁(北京航空航天大学仪器科学与光电工程学院,北京100083)摘要:针对高曲率零件表面缺陷检测及外形尺寸测量的问题,设计实现了基于机器视觉的兼顾缺陷检测及外形尺寸测量两种功能的测量系统。
在同一系统中,固定的光学系统放大倍数能满足检测表面微米级大小缺陷的要求,对外形尺寸测量要移动零件,拍摄多幅边缘图像,记录移动距离并计算零件两侧边缘在图像中的距离,得到最终的外形尺寸。
解决了表面缺陷高精度检测和外形尺寸大范围测量的矛盾。
实验证明:系统具有可靠、高效的特点。
关键词:表面缺陷;图像处理;机器视觉;尺寸测量中图分类号:TP391文献标识码:A文章编号:1007-2276(2008)增(几何量)-0274-05Measure system of sur face flaw and contour dimension of highcurvature bitty partGE Wen-qian ,ZHAO Hui-jie(Coll ege of Ins trument Sci ence and Phot o-Electricity Engineering,Beij ing University of Aeronautics and Astronaut ics,Beijing 100083)Abstr act:Aimed at the problem of high curvature bitty part surface flaw and boxed dimension,a whole based on machine vision program which balances between the flaw detection and dimension measurement is designed,the requirement of micron flaw in surface detection is satisfied,the boxed dimension measurement is accomplished by moving the part and taking several edge images,recording the moving distance and counting the distance of edges in image,combining the two distances then getting the boxed dimension.Resolve the contradiction of high precision surface flaw detection and boxed dimension large-scale m easure.Experiment showed that the system is dependable and efficient.Key wor ds:Surface flaw;Im age processing;Machine vision;Dim ension m easurement0引言工业生产中一些微小零件往往决定着产品的关键性能,其加工和测量的难度大,对外形尺寸和表面光洁度都有较高的要求。
光学零件检验方法

光学零件检验方法光学零件的检验方法是确保光学零件质量和性能的重要步骤。
以下是常见的光学零件检验方法:1.外观检验:外观检验是最简单和最常见的检验方法之一、它涉及对光学零件表面的检查,以确保没有明显的缺陷、瑕疵或污染。
常用的外观检查仪器有放大镜、显微镜和光谱仪等。
2.尺寸检验:尺寸检验是测量光学零件尺寸和形状的方法。
常用的尺寸测量仪器有投影仪、坐标测量机和光学分光计等。
这些仪器可以精确测量光学零件的长度、宽度、直径、圆度和平面度等。
3.表面粗糙度检验:表面粗糙度是表面微小不规则性的度量标准,对光学零件的性能具有重要影响。
常用的表面粗糙度检测仪器有光学轮廓仪、表面粗糙度仪和压电表面粗糙度仪等。
4.平整度检验:平整度是表面平坦性的度量标准,对光学零件的质量和性能有着重要影响。
常用的平整度测量仪器有检测平台和激光干涉仪等。
5.光学性能检验:光学性能检验涉及到对光学零件传输、透射、反射、折射、散射等光学性能的测量和评估。
常用的光学性能测量仪器有光谱仪、干涉仪、激光测距仪和分光光度计等。
6.工作环境检验:在一些特殊应用中,光学零件需要在特定的环境条件下工作,比如高温、低温、高湿度或低湿度等。
在这种情况下,光学零件的工作环境稳定性也需要进行检验。
7.强度检验:一些光学零件可能会经受较大的外力作用,因此需要进行强度检验。
常用的强度检验方法包括拉伸测试、弯曲测试、冲击测试和疲劳测试等。
总之,光学零件的检验方法是多样的,根据具体需要选择合适的检验方法进行检验,以确保光学器件的质量和性能符合要求。
光学表面微缺陷的高对比度暗场成像检测方法

(a)无散斑抑制器的 0.1 mm 划痕的暗场图像
(b)0.1 mm 划痕的暗场图像
(c)无散斑抑制器的栅格透射 (d)栅格透射板的暗场图像 板的暗场图像
图 2 散斑抑制器对 CAM 系统的影响
2 实验结果
CAM 的系统组成如图 3 所示,从左到右依次 为激光器、散斑抑制器、聚光镜、被测件、遮挡片、 显微物镜、管镜、相机、计算机等,它们均置于高精 密光学平台上,所有元件均由光具座调节至同一 光轴上。
场图像如图 5 所示。从图中可以看出,明场图像 数字和线的中间透明区域均呈现明亮的像;而暗 场图像对比度高,可以看到更多的细节,并且可以 明显看出数字和线条的中间透明区域是黑的、并
关键词:光学元件加工;缺陷检测;暗场显微成像 中图分类号:TN247 文献标识码:A 文章编号:1672-4801(2019)01-086-03 DOI:10.19508/ki.1672-4801.2019.01.025
在光学元件的加工过程中或加工后某些不适 当的处置会产生表面局部缺陷[1-3],被称为光学元 件表面缺陷(表面疵病),其中最常见的是麻点和 划痕[4-6]。缺陷在光学系统中属于散射源[7],会对元 件性能产生影响,尤其是在强激光应用中表面缺 陷将降低损伤阈值、诱导损伤,直接降低系统的安 全性[8]。因此,在光学元件加工中需要对表面缺陷 进行检测和控制,而其中微小缺陷检测一直是一 个难题。目前存在的方法中,暗场显微检测法[9,10] 由于原理简单、检测精度高、分辨率高、对比度高 的优点成为目前缺陷检测的主流方法,使用比较 广泛。通常光在穿透纯净无缺陷的光学元件时, 不会改变传播光路。而缺陷可以看作是由许许多 多的微平面构成的,这些微平面使光的出射方向 各不相同,因此会产生散射光,其中一部分偏离理 想传播光路。暗场显微检测法利用了缺陷产生散 射光的这一性质,利用表面及亚表面缺陷形成的 散射光使得缺陷成暗背景下的明亮像。相同条件 下暗场成像比明场成像具有更高的对比度和清 晰度。
无损检测技术中的光学检测方法详解
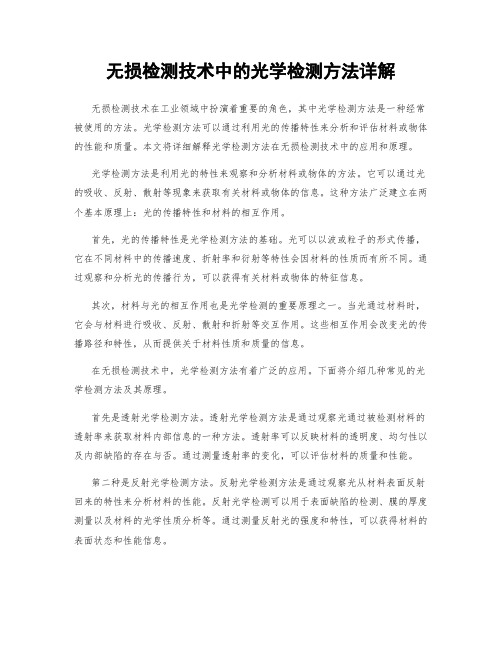
无损检测技术中的光学检测方法详解无损检测技术在工业领域中扮演着重要的角色,其中光学检测方法是一种经常被使用的方法。
光学检测方法可以通过利用光的传播特性来分析和评估材料或物体的性能和质量。
本文将详细解释光学检测方法在无损检测技术中的应用和原理。
光学检测方法是利用光的特性来观察和分析材料或物体的方法。
它可以通过光的吸收、反射、散射等现象来获取有关材料或物体的信息。
这种方法广泛建立在两个基本原理上:光的传播特性和材料的相互作用。
首先,光的传播特性是光学检测方法的基础。
光可以以波或粒子的形式传播,它在不同材料中的传播速度、折射率和衍射等特性会因材料的性质而有所不同。
通过观察和分析光的传播行为,可以获得有关材料或物体的特征信息。
其次,材料与光的相互作用也是光学检测的重要原理之一。
当光通过材料时,它会与材料进行吸收、反射、散射和折射等交互作用。
这些相互作用会改变光的传播路径和特性,从而提供关于材料性质和质量的信息。
在无损检测技术中,光学检测方法有着广泛的应用。
下面将介绍几种常见的光学检测方法及其原理。
首先是透射光学检测方法。
透射光学检测方法是通过观察光通过被检测材料的透射率来获取材料内部信息的一种方法。
透射率可以反映材料的透明度、均匀性以及内部缺陷的存在与否。
通过测量透射率的变化,可以评估材料的质量和性能。
第二种是反射光学检测方法。
反射光学检测方法是通过观察光从材料表面反射回来的特性来分析材料的性能。
反射光学检测可以用于表面缺陷的检测、膜的厚度测量以及材料的光学性质分析等。
通过测量反射光的强度和特性,可以获得材料的表面状态和性能信息。
另外一种常见的光学检测方法是散射光学检测方法。
散射光学检测方法是通过观察被材料散射的光的特性来评估材料中的颗粒、缺陷以及微观结构等信息。
散射光的强度和分布可以提供关于材料内部结构和组成的重要指示。
此外,干涉光学检测方法也是一种常用的光学检测方法。
干涉光学检测方法是通过观察光的干涉现象来分析材料的性能和质量。
光学零件表面疵病标准

光学零件表面疵病标准文稿归稿存档编号:[KKUY-KKIO69-OTM243-OLUI129-G00I-FDQS58-光学零件表面疵病标准擦痕、麻点说明(美国军用标准:MIL-O-13830A/11.Sep63)1.目的:光学零件表面质量说明及可接受缺陷(defects)规定,陆军用擦痕、麻点说明,MIL-13830A为了在实际检验中领会,执行此标准,特做以下文字规定。
1.1擦痕(scratch)和麻点(dig)用两个代表其限制尺寸的号数来标记。
第二个号为麻点号。
擦痕指相对较长的缺陷,一般长比宽在20:1左右,如:擦痕、划丝、划伤等。
麻点指点状缺陷,一般为圆的如麻点、麻坑包含物等。
1.2 擦痕的判断可参考有关擦痕标准。
2.擦痕2.1 擦痕号(第一个号)表示擦痕最大宽度。
2.1.1 球面光学零件:擦痕的宽度等于最大宽度时其长度不能大于零件直径或有效孔径的25%。
每个零件不能多于两条擦痕。
2.1.2 柱面光学零件在直径20mm的范围内。
擦痕宽度等于最大宽度时,擦痕长度不大于5mm可以允许。
允许擦痕的最多数目为该有效柱面上直径为20mm的区域的多少。
例如:πDH=柱面面积(有效面积)其中:D=柱面镜的过光长度(高度) H=柱面镜的过光长度(高度)π=3.1416有效柱面面积/0.25π20mm2=允许擦痕最大数 2.1.3 当存在最宽擦痕,如果较小宽度的擦痕符合下面公式,可以接受。
∑(N×(L/D))≤(Nmax)/2其中:D=直径,N=测量的擦痕数,L=擦痕长度,Nmax=规定的擦痕号光学零件中擦痕数乘以擦痕长度和零件直径之比的和不大于擦痕号(规定)的一般可以接受。
2.1.4 一个擦痕其宽度大于擦痕规定数的(0.0001英寸)0.00025mm,则不能接收。
2.1.5 当无最宽擦痕时,擦痕不能超过以下公式:光学零件中擦痕数乘以擦痕长度和零件直径之比的和不大于擦痕号,则可以接受。
2.1.6 小于10(0.01mm宽)可以忽略。
光学面型检测标准

光学面型检测标准一、检测标准概述光学面型检测是光学元件质量检测的重要环节,其目的是确保光学元件的表面质量符合设计要求和实际应用需求。
本标准主要规定了光学面型的检测标准,包括表面粗糙度、表面平整度、表面缺陷和表面镀膜等方面的检测要求和方法。
二、光学面型检测标准1. 光学面型应符合设计要求,表面光滑、平整,无划痕、裂纹、气泡等缺陷。
2. 光学面型的尺寸精度应符合相关标准,如《光学零件尺寸公差》等。
3. 光学面型的表面粗糙度应符合设计要求,一般要求在Ra 0.05-0.2之间。
4. 光学面型的表面平整度应符合设计要求,一般要求在λ/4以内(λ为测试波长)。
三、表面粗糙度检测标准1. 表面粗糙度应采用轮廓仪进行测量,测量范围应覆盖整个表面。
2. 测量时应选用合适的测量参数,如采样长度、评定长度等,确保测量结果的准确性。
3. 表面粗糙度的合格标准应符合设计要求,一般要求在Ra 0.05-0.2之间。
四、表面平整度检测标准1. 表面平整度应采用干涉仪进行测量,测量时应避免外界干扰,如振动、气流等。
2. 测量时应根据不同的表面形状和材料选择合适的测试条件,如干涉仪型号、光源波长等。
3. 表面平整度的合格标准应符合设计要求,一般要求在λ/4以内(λ为测试波长)。
五、表面缺陷检测标准1. 表面缺陷应采用显微镜或自动外观检测设备进行观察和检测。
2. 检测时应根据不同的缺陷类型和大小选择合适的放大倍数和观察角度。
3. 表面缺陷的合格标准应符合设计要求和相关标准,如《光学零件外观缺陷公差》等。
六、表面镀膜检测标准1. 表面镀膜应采用光谱仪、电子显微镜等设备进行检测,了解膜层的厚度、硬度、反射率等性能指标。
2. 检测时应选择合适的测试条件和测试点分布,确保测试结果的代表性。
3. 表面镀膜的合格标准应符合设计要求和相关标准,如《光学零件表面镀膜技术条件》等。
七、光学面型检测方法1. 采用轮廓仪进行表面粗糙度测量时,应按照仪器使用说明书进行操作,并选择合适的测量参数。
机械工程中的光学成像检测技术

机械工程中的光学成像检测技术引言:在机械工程领域,光学成像检测技术被广泛应用于各种工艺过程的质量控制和产品检测中。
光学成像检测技术通过利用光学原理和成像设备,能够高效、准确地获取目标物体的信息,为机械工程师提供了重要的分析与决策依据。
一、光学成像检测技术的原理光学成像检测技术基于光的物理性质,光线经过物体后被接收器接收并转化成图像。
其原理主要包括光源的发射、光线的传播、物体的反射或透射、成像系统的接收与重建等。
其中,光源的选择和调节、透镜系统的设计以及信号处理等环节对成像效果至关重要。
二、应用领域一:表面缺陷检测在机械工程领域的生产过程中,表面缺陷的检测对于产品质量的控制至关重要。
光学成像技术可以帮助工程师检测出各种类型的表面缺陷,如裂纹、压痕、划痕等。
借助高分辨率的摄像设备和适当的光源,工程师可以清晰地观察到目标物体表面的细微差异,及早发现并解决表面缺陷问题,保证产品的质量。
三、应用领域二:尺寸测量与定位光学成像技术在机械工程领域也用于尺寸测量和定位。
通过光学相机和计算机视觉技术的结合,工程师可以准确地测量出目标物体的尺寸和位置信息。
这对于机械工程师来说是非常重要的,因为尺寸和位置的精确度直接影响到工件的装配和使用效果。
四、应用领域三:动态监测与分析光学成像技术还可以用于机械设备的动态监测和分析。
通过安装高速拍摄设备和光学传感器,工程师可以实时观测机械设备运行过程中的各种参数和状态。
这有助于工程师及时发现异常情况,进行故障排除和性能优化,提高设备的可靠性和效率。
五、应用领域四:材料显微分析光学成像技术在机械工程领域还被广泛应用于材料显微分析。
通过光学显微镜和其他相关设备,工程师可以观察目标材料的微观结构,分析材料的组织和性质。
这对于材料工程师来说非常重要,因为它可以帮助他们研究材料的性能和寿命,并选择适合的材料用于实际生产。
结论:光学成像检测技术在机械工程领域扮演着重要的角色。
它不仅能够应用于表面缺陷检测、尺寸测量和定位、动态监测与分析、材料显微分析等多个应用领域,还能够大大提高产品质量和生产效率。
光学成像技术在表面缺陷检测中的应用研究
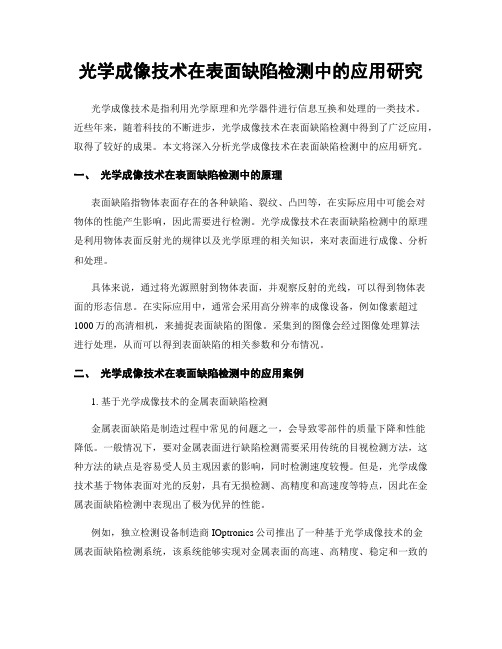
光学成像技术在表面缺陷检测中的应用研究光学成像技术是指利用光学原理和光学器件进行信息互换和处理的一类技术。
近些年来,随着科技的不断进步,光学成像技术在表面缺陷检测中得到了广泛应用,取得了较好的成果。
本文将深入分析光学成像技术在表面缺陷检测中的应用研究。
一、光学成像技术在表面缺陷检测中的原理表面缺陷指物体表面存在的各种缺陷、裂纹、凸凹等,在实际应用中可能会对物体的性能产生影响,因此需要进行检测。
光学成像技术在表面缺陷检测中的原理是利用物体表面反射光的规律以及光学原理的相关知识,来对表面进行成像、分析和处理。
具体来说,通过将光源照射到物体表面,并观察反射的光线,可以得到物体表面的形态信息。
在实际应用中,通常会采用高分辨率的成像设备,例如像素超过1000万的高清相机,来捕捉表面缺陷的图像。
采集到的图像会经过图像处理算法进行处理,从而可以得到表面缺陷的相关参数和分布情况。
二、光学成像技术在表面缺陷检测中的应用案例1. 基于光学成像技术的金属表面缺陷检测金属表面缺陷是制造过程中常见的问题之一,会导致零部件的质量下降和性能降低。
一般情况下,要对金属表面进行缺陷检测需要采用传统的目视检测方法,这种方法的缺点是容易受人员主观因素的影响,同时检测速度较慢。
但是,光学成像技术基于物体表面对光的反射,具有无损检测、高精度和高速度等特点,因此在金属表面缺陷检测中表现出了极为优异的性能。
例如,独立检测设备制造商IOptronics公司推出了一种基于光学成像技术的金属表面缺陷检测系统,该系统能够实现对金属表面的高速、高精度、稳定和一致的检测,避免了传统目视检测方法容易导致的错误和漏检问题。
通过对系统进行实验和应用,证明了该系统在金属表面缺陷检测中有着较好的应用效果和工程价值。
2. 基于光学成像技术的玻璃表面缺陷检测玻璃制品在生产过程中难免会产生一些表面缺陷,这些缺陷会影响到玻璃的光学性能和外观效果。
传统的玻璃缺陷检测方法主要是采用目视检测加初步过滤的方式,但这种方式存在易疲劳、漏检率高的问题。
光学元件表面划痕的可视化检测

光学元件表面划痕的可视化检测潘永强;刘鹏【摘要】Optical element surface defects affect the function and appearance of components. The defects image acquired through microscopic imaging method is processed by the image processing toolbox of Matlab, then the gray value and physical dimension with the number of pixels are extracted. The actual size of scratches is easy to calculate approximatively according to the size of pixel and the magnification factor of microscope objective. According to the experiment; The longest scra tch is 104. 33 fim,the shortest is 5. 57μm,the widest is 2. 37 μm,the narrowest is 1. 30 μm; The maximum of gray value of scratches is 175, the minmum is 97.%光学元件表面缺陷的存在会影响元件的功能和美观.应用显微成像法完成对缺陷图像的采集,运用Matlab图像处理工具对缺陷图像进行图像处理,提取出划痕缺陷的灰度值特征和几何像素数尺寸特征.根据CCD传感器的像素尺寸和显微物镜的放大倍数从而近似得出划痕的实际尺寸.实验中所测得的划痕最长有104.33μm,最短为5.57 μm;最宽为2.37 μm,最窄为1.30μm;灰度均值最大为175,最小为97.【期刊名称】《西安工业大学学报》【年(卷),期】2012(032)006【总页数】4页(P447-450)【关键词】划痕;显微成像法;CCD;Matlab;灰度值;几何尺寸【作者】潘永强;刘鹏【作者单位】西安工业大学光电工程学院,西安710032;西安工业大学光电工程学院,西安710032【正文语种】中文【中图分类】TP751.2光学元件的质量好坏对光学仪器的性能有着直接的影响.因此,光学元件质量的改善对光学仪器的整体质量的提高有着极其重要的意义.现代光学元件的检测比现代光学元件的制造难度更高.光学元件的检测的任务十分繁多而重要[1].在生产过程中,光学元件经过切割铣磨成型、粗磨细磨、抛光等过程后,元件表面整体上虽然光滑和平整,但难免会产生瑕疵和缺陷问题,如麻点和划痕等.缺陷的存在不只是影响了元件的美观,更是影响了元件及其所在的系统的功能.主要表现为散射、衍射花纹、膜层破坏、激光损伤等.划痕缺陷往往在长度方向上具有几何尺寸较大的特点,所以其对元件表面质量的影响更大.当光束入射到元件表面时,划痕会对光束强度产生调制作用,从而使划痕长度方向上的两侧形成一系列对称分布的光强增强区域,这种光强度分布不均匀现象会使元件局部温度急剧升高而导致严重损伤[2].以前对于光学元件损伤的检测,主要采用目测法.虽然人眼识别简单易行,没有仪器设备等方面的限制,但其最大缺点是不能进行精密度量,检测周期长且误差较大.目前,光学元件缺陷检测的方法较多,国内外大都根据缺陷对光的散射[3]、衍射特性来检测精密光学表面的缺陷,按检测方法主要分为成像法和能量法[4].文中的检测对象是小口径光学元件,采用的检测方法是显微成像法[5].1 显微成像法1.1 显微成像法的基本原理当入射平行光束以一定角度斜入射到光滑表面上时[6],若光束入射的光斑范围内没有缺陷,光束将遵循反射或折射规律传播(如图1(a)),若入射的光斑范围内有缺陷(如图1(b)),入射光束将被缺陷无规则地反射即散射.图1 斜入射的光学特性Fig.1 Optical property of grazing incidence如果在被检表面上方放置成像物镜,对于图1(a)所示情况,物镜的成像平面一片黑,对于图1(b)所示情况,将有光束进入成像物镜并被物镜成像,表面缺陷成了“第二光源”.而且无论是划痕还是麻点都会产生漫反射光,尽管对于不同的缺陷类型或不同的深层构造其散射光的强度和频谱分布不同,我们关心的不是“第二光源”的发光强度和散射角,而是它的“发光面积”.“第二光源”的发光面积和形状必须与缺陷的表层完全相同.激光束一定的入射角入射到光学元件表面,缺陷产生的第二光源被显微物镜成像于光电接收器上,即CCD接收面上,CCD接收的图像信息经处理后在计算机上显示.被检元件载于工作台上.1.2 检测系统检测系统主要包括照明光源、显微物镜、CCD传感器和计算机三部分.检测系统示意图如图2所示.图2中,照明光源为激光光源,所选激光光源波长为632.8nm,功率为2mW;显微物镜、转接筒、光电耦合器件CCD和计算机共同构成图像采集系统.实验中所选CCD为AD-081GE型黑白CCD.图2 检测系统示意图Fig.2 Diagram of detecting system2 数字图像处理数字图像处理是采用一定的算法对数字图像进行处理,以获得人眼视觉或者某种接收系统所需要的图像过程.其基础是数学,主要任务是进行算法设计和算法实现.目前,数字图像处理技术已经在不同领域得到重视,取得巨大成就.根据不用领域的要求,数字图像处理技术可以分为许多分支技术.课题中图像处理的具体过程如图3所示.图3 数字图像处理流程图Fig.3 Flow diagram of digital image processing通过显微检测系统对元件表面进行缺陷图像采集,选取其中一幅图像如图4所示.首先对采用中值滤波法对原始图像进行去噪处理,在不影响原图像质量的前提下改善图像视觉效果,使其中的缺陷更加突出和明显.然后是进行图像分割.图像分割的目的就是将感兴趣的目标部分与前景部分区分开,区分的依据是目标相比较于前景具有某些独特的性质,如像素的灰度值、物体轮廓曲线、纹理或彩色图像的颜色等.在缺陷灰度图像中,缺陷部分与背景相比具有区域灰度值高、轮廓曲线明显的特点,利用缺陷的这些特点实现缺陷与背景的分割.图4 元件表面的缺陷Fig.4 Defects of element surface图像分割的效果如图5所示.图像分割的技术很多,总体分为区域分割法和边缘检测法[7].阈值分割法是区域分割法中的常用方法.边缘检测法则是通过连接目标区域的边界像素来实现分割目的.由于缺陷具有较明显的边缘轮廓特性,而且课题需要检测其几何尺寸大小,因此采用Canny算子边缘检测法进行缺陷分割.Canny 算子具有边缘定位精度高的特点.图5 分割后的图像Fig.5 Segmented image of defects3 划痕缺陷的特征提取3.1 缺陷子图像的标记原图像分割后,缺陷部分已经同背景分离,背景变为黑色(灰度值为0),缺陷部分变为白色(灰度值为255).为了求取缺陷的特征,标识每个独立的缺陷子图像,即对缺陷子图像进行标记.标记后,如图6所示.通过大量的缺陷特征提取和缺陷识别后,可以划分缺陷1、缺陷2、缺陷10、缺陷17和缺陷19为划痕缺陷,分别定为划痕1~5.图6 缺陷位置标记图Fig.6 Signature of defects3.2 划痕的特征内容缺陷检测中图像的特征内容一般包括图像的幅度特征、统计特征、几何特征以及变换系数特征.这里采用图像的灰度特征和几何特征来描述图像中的缺陷.通过采用Matlab图像处理和数据采集后,得出划痕缺陷的数据,见表1.表1 划痕缺陷的特征值Tab.1 Characteristic value of scratches划痕序号划痕长度/像素划痕宽度/像素划痕灰度均值划痕最大灰度值划痕1划痕2划痕3划痕4划痕5 25.400 0 475.934 1 332.973 7 101.900 8 157.941 0 6.383 6 10.849 4 8.659 1 5.769 8 5.917 9 96.601 5 117.414 9 175.456 5 128.483 8 119.751 3 115 156 251 163 157表1中划痕的长度和宽度的数值是划痕所占用的像素数.AD-081GE型CCD的像素大小为4.65μm×4.65μm,并且显微物镜的放大倍数为30倍,通过计算,可以近似得出划痕的实际尺寸,并对灰度值做取整的近似处理,见表2.表2 划痕缺陷的实际尺寸和灰度值Tab.2 Physical dimension and grey level of scratches划痕序号划痕长度/像素划痕宽度/像素划痕灰度均值划痕最大灰度值115 156 251 163 157划痕1划痕2划痕3划痕4划痕5 5.57 104.33 73.00 22.33 34.63 1.40 2.37 1.90 1.27 1.30 97 117 175 128 120在求划痕的实际尺寸时,本文做了近似处理,暂时忽略了微米级缺陷对光线的散射影响,近似认为系统的放大倍数仍符合线性关系,从而由缺陷的图像中的尺寸直接求出其实际尺寸.4 结论文中采用显微成像法实现了对光学元件表面微缺陷划痕的检测,并应用Matlab图像处理工具对所采集的缺陷图像进行采集、处理和缺陷特征的提取,实现了微米级划痕缺陷的初步检测,所测数据显示检测对象的划痕最长达104.33μm,最短有5.57μm;最宽是2.37μm,最窄为1.30μm;划痕灰度均值最大为175,最小为97.元件表面质量等级划分的依据是缺陷的灰度值特征和几何尺寸大小,划痕的灰度特征值和几何尺寸特征的测量为以后进行元件表面质量的分级提供了可靠的依据.【相关文献】[1]机械工业部仪器仪表工业局.光学元件技术要求[S].北京:机械工业出版社,1984.Ministry of Machinery Industry Instrumentation Industry Bureau.Technical Requirements for Optical Element[S].Beijing:Machinery Industry Press,1984.(in Chinese)[2]杨浩,冯国英,韩敬华,等.光学元件的表面划痕及其对入射激光的调制作用[J].强激光与粒子束,2006,18(11):1832.YANG Hao,FENG Guo-ying,HAN Jing-hua,etal.Scratches on Optical Component Surface and Its’Modulation on Injecting Laser [J].High Power Laser and Particle Beams,2006,18(11):1832.(in Chinese)[3]ELSON J M.Theory of Light Scattering from a Rough Surface with an Inhomogenous Dielectric Permittivity[J].Phys Rev B,1984,30:5460.[4]李艾星,杨天饴,张颖.基于机器视觉的精密光学元件表面疵病识别初步研究[J].重庆邮电大学学报:自然科学版,2007,19(4):442.LI Ai-xing,YANG Tian-yi,ZHANGYing.Preliminary Research of Surface Defect Recognition Based on Machine Vision[J].Journal of Chongqing University of Posts and Telecommunications:Natural Science Edition,2007,19(4):442.(in Chinese)[5]BAKER L R.Inspection of Surface Flaws by Comparator Microscopy[J].Appl Opt,1988,27(22):4620.[6]王元庆.表面疵病的掠射法检测[J].应用激光,1998,18(2):55.WANG Yuan-qing.Measurement of Surface Flaw by Grazing Incidence[J].Applied Laser,1998,18(2):55.(in Chinese)[7]CASTLEMAN K R.数字图像处理[M].朱志刚,林学訚,石定机,等译.北京:电子工业出版,1998.CASTLEMAN K R.Digital Image Processing[M].ZHU Zhi-gang,LIN Xue-yin,SHI Ding-ji,et al,Translation.Beijing:Publishing House of Electronics Industry,1998.(in Chinese)。
表面质量分级与缺陷检验的方法
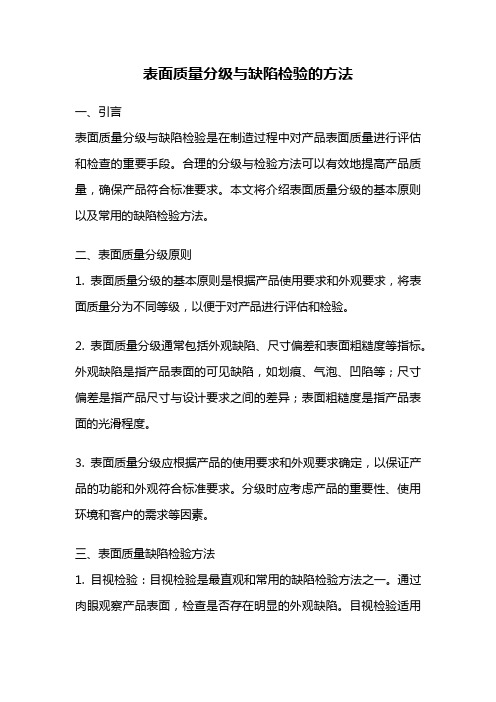
表面质量分级与缺陷检验的方法一、引言表面质量分级与缺陷检验是在制造过程中对产品表面质量进行评估和检查的重要手段。
合理的分级与检验方法可以有效地提高产品质量,确保产品符合标准要求。
本文将介绍表面质量分级的基本原则以及常用的缺陷检验方法。
二、表面质量分级原则1. 表面质量分级的基本原则是根据产品使用要求和外观要求,将表面质量分为不同等级,以便于对产品进行评估和检验。
2. 表面质量分级通常包括外观缺陷、尺寸偏差和表面粗糙度等指标。
外观缺陷是指产品表面的可见缺陷,如划痕、气泡、凹陷等;尺寸偏差是指产品尺寸与设计要求之间的差异;表面粗糙度是指产品表面的光滑程度。
3. 表面质量分级应根据产品的使用要求和外观要求确定,以保证产品的功能和外观符合标准要求。
分级时应考虑产品的重要性、使用环境和客户的需求等因素。
三、表面质量缺陷检验方法1. 目视检验:目视检验是最直观和常用的缺陷检验方法之一。
通过肉眼观察产品表面,检查是否存在明显的外观缺陷。
目视检验适用于表面缺陷较大且易于观察的产品。
2. 人工触感检验:人工触感检验是通过手触产品表面,检查是否存在凹凸不平、粗糙等缺陷。
这种方法适用于对产品表面质量要求较高的情况,但对操作人员的要求也较高。
3. 光源照明检验:光源照明检验是利用光源照射产品表面,通过观察光线反射情况来判断表面质量。
这种方法适用于检验产品表面的光滑度和反光性。
4. 仪器检测:仪器检测是利用专业仪器设备对产品表面进行定量分析和检测。
常用的仪器包括显微镜、光学投影仪、三坐标测量仪等。
仪器检测可以准确地测量表面缺陷的大小、形状和位置等信息。
5. 磁粉检验:磁粉检验是一种常用的金属表面缺陷检验方法。
通过在产品表面涂布磁性粉末,然后施加磁场,观察磁粉在表面缺陷处的聚集情况,来判断表面是否存在缺陷。
6. 超声波检测:超声波检测是一种利用超声波传播特性来检测材料内部和表面缺陷的方法。
通过超声波的传播速度和反射信号来判断表面缺陷的位置和大小。
kaken 检测方法

kaken 检测方法【实用版3篇】目录(篇1)一、引言二、Kaken 检测方法的概念与原理三、Kaken 检测方法的具体步骤四、Kaken 检测方法的优势与应用五、结论正文(篇1)一、引言随着科技的发展,各类电子产品日益普及,电子产品的安全检测也变得越来越重要。
其中,Kaken 检测方法是一种针对电子产品安全性能的检测方法。
本文将详细介绍 Kaken 检测方法的概念与原理、具体步骤、优势与应用。
二、Kaken 检测方法的概念与原理Kaken 检测方法是一种针对电子产品的安全性能进行检测的方法,其源于日本,意为“加严”。
该方法主要通过对电子产品的电路进行检测,以评估其安全性能。
Kaken 检测方法的原理是利用特定的检测设备,对电子产品的电路进行加严测试,以检测潜在的安全隐患。
三、Kaken 检测方法的具体步骤Kaken 检测方法的具体步骤如下:1.确定检测对象:首先,需要确定需要进行 Kaken 检测的电子产品。
2.准备检测设备:检测设备包括示波器、信号发生器、万用表等。
3.设定检测参数:根据检测对象的特点,设定合适的检测参数,如测试电压、测试频率等。
4.进行检测:连接检测设备,对电子产品的电路进行加严测试,观察设备的反应,以检测潜在的安全隐患。
5.分析检测结果:根据检测数据,分析电子产品的安全性能,并提出改进措施。
四、Kaken 检测方法的优势与应用Kaken 检测方法具有以下优势:1.高效性:Kaken 检测方法可以快速地对电子产品的电路进行检测,提高检测效率。
2.准确性:Kaken 检测方法可以对电子产品的电路进行全面的测试,有效识别潜在的安全隐患。
3.可靠性:Kaken 检测方法经过多年的实践检验,具有较高的可靠性。
Kaken 检测方法广泛应用于电子产品的研发、生产、质量控制等领域,对保障电子产品的安全性能起到了重要作用。
五、结论Kaken 检测方法是一种有效的电子产品安全性能检测方法,具有高效性、准确性和可靠性等优势,在电子产品的研发、生产、质量控制等领域具有广泛的应用前景。
品检中常见的产品缺陷与检测方法
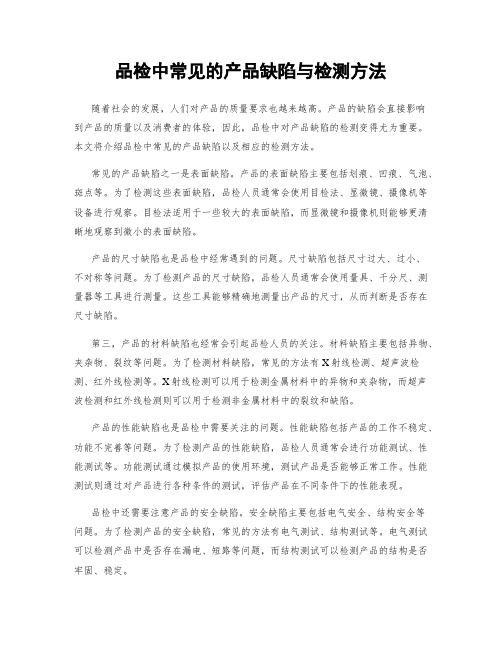
品检中常见的产品缺陷与检测方法随着社会的发展,人们对产品的质量要求也越来越高。
产品的缺陷会直接影响到产品的质量以及消费者的体验,因此,品检中对产品缺陷的检测变得尤为重要。
本文将介绍品检中常见的产品缺陷以及相应的检测方法。
常见的产品缺陷之一是表面缺陷。
产品的表面缺陷主要包括划痕、凹痕、气泡、斑点等。
为了检测这些表面缺陷,品检人员通常会使用目检法、显微镜、摄像机等设备进行观察。
目检法适用于一些较大的表面缺陷,而显微镜和摄像机则能够更清晰地观察到微小的表面缺陷。
产品的尺寸缺陷也是品检中经常遇到的问题。
尺寸缺陷包括尺寸过大、过小、不对称等问题。
为了检测产品的尺寸缺陷,品检人员通常会使用量具、千分尺、测量器等工具进行测量。
这些工具能够精确地测量出产品的尺寸,从而判断是否存在尺寸缺陷。
第三,产品的材料缺陷也经常会引起品检人员的关注。
材料缺陷主要包括异物、夹杂物、裂纹等问题。
为了检测材料缺陷,常见的方法有X射线检测、超声波检测、红外线检测等。
X射线检测可以用于检测金属材料中的异物和夹杂物,而超声波检测和红外线检测则可以用于检测非金属材料中的裂纹和缺陷。
产品的性能缺陷也是品检中需要关注的问题。
性能缺陷包括产品的工作不稳定、功能不完善等问题。
为了检测产品的性能缺陷,品检人员通常会进行功能测试、性能测试等。
功能测试通过模拟产品的使用环境,测试产品是否能够正常工作。
性能测试则通过对产品进行各种条件的测试,评估产品在不同条件下的性能表现。
品检中还需要注意产品的安全缺陷。
安全缺陷主要包括电气安全、结构安全等问题。
为了检测产品的安全缺陷,常见的方法有电气测试、结构测试等。
电气测试可以检测产品中是否存在漏电、短路等问题,而结构测试可以检测产品的结构是否牢固、稳定。
综上所述,品检中常见的产品缺陷有表面缺陷、尺寸缺陷、材料缺陷、性能缺陷以及安全缺陷。
针对这些缺陷,品检人员可以采用目检法、显微镜、摄像机、量具、千分尺、测量器、X射线检测、超声波检测、红外线检测、功能测试、性能测试、电气测试、结构测试等方法进行检测。
- 1、下载文档前请自行甄别文档内容的完整性,平台不提供额外的编辑、内容补充、找答案等附加服务。
- 2、"仅部分预览"的文档,不可在线预览部分如存在完整性等问题,可反馈申请退款(可完整预览的文档不适用该条件!)。
- 3、如文档侵犯您的权益,请联系客服反馈,我们会尽快为您处理(人工客服工作时间:9:00-18:30)。
本 文 以典 型 微 小 尺 寸 环 形 零 件 ( 径 小 于 1 外 0 m 内径小 于 6m 为对 象 , m, m) 从零 件 的表 面 特 征 、 缺 陷类 型及 检测 算 法 出 发 , 立 一 种 基 于 机 器 视 觉 的 建
9. 6 5% . Alo,t e e pei e t e i t o r cn s ,r p d t n r cs n s . s h x rm n sv rf isc re t e s a i iy a d p e ie e s y Key wor ds:i f r ain p o e sn n o m to r c s i g;mir — o p n n ;s f c ee td tci n; i a e r c g i o c o c m o e t ura e d f c ee to m g e o nt n;m a i —
chi son ne vi i
精 密 微 小 尺 寸 零 件 对 材 料 特 性 、 面 质 量 、 构 表 结
在加 工 表 面 产 生 砂 眼 、 痕 、 纹 、 坑 等 微 观 缺 划 裂 麻
陷 。这些 缺 陷不 仅 影 响零 件 外 观 , 重 要 是 降低 更 零 件 的抗 腐蚀 性 、 磨 性 、 劳 极 限 等使 用 性 能 , 抗 疲 直 接影 响零件 本身及 使 用该 零 件 设 备 的使 用 寿 命 , 限 制 了设 备性 能 的发 挥 , 给安 全 使 用 带 来 极 大 的 隐 也
陷 的 识 别 与 检 测 , 陷 识 别 率 达 9 . % .实 验 验 证 了理 论 分 析 及 表 面 缺 陷 检 测 算 法 的 正 确 性 , 用 缺 65 可 于微 小尺 寸零件 表 面缺 陷的精确 检验 。
关 键词 : 息处 理技 术 ;微 小尺 寸零件 ; 面缺 陷检 测 ;图像 识别 ;机器 视 觉 信 表
形状 、 可靠 性 等方面 的要 求高
。
微小零 件 的制造 主要 通过 粉末成 型 、 械加 工 、 机
真 空烧结 、 刻 技 术 、 光 MEMS等 工 艺 方 法 实 现 , 于 由
生产 工艺 的复杂 性 、 多样性 , 加工 的过程 中往 往会 在
收 稿 日期 : 0 9—1 2 20 1— 5
L a —h u ,YU Hu — o g ,YU Z a gj n I n ,XU Jn k i, IXio z o ad n h n —i g ,L U Ya a i— a
( . c o lo c a ia a d E etia En iern , h n c u ies yo ce c n e h ooy 1 S h o fMe h ncl n lcr l gn eig C a g h nUnv ri f in ea dT c n lg c t S
Ch n e un 3 22,ii Chna; Cha g h n t u e o tc Fi e ha is a d Ph sc , a g h 1 00 Jl n, i 2. n c un I si t fOp is, ne M c n c n y i s t
C ieeAc d myo ce cs C a g h n 10 3 Jl , hn ) hn s a e fS in e , h n c u 0 3,i n C ia 3 i
度方 差 加权信 息 熵 算 法 来 抑 制 零 件 表 面 随机 纹理 ,
提 取 微 小 零 件 表 面 缺 陷 , 现 微 小 尺 寸 零 件 表 面 缺 实 陷检 测 。 实 验 结 果 表 明 , 文 所 提 出 算 法 能 够 有 效 本 地进 行微 小 尺寸 零件 表面 缺 陷检测 。
a g rt m sng we g t d i f r a i n e to y o m a e g a i n a i n e wa r p s d t u r s h a l o ih u i i h e n o m to n r p f i g r d e tv ra c s p o o e o s pp e s t e r n— d m u a e t x u e, e ta t t e fa n d t c h a n t e mi r — o o s r c e t r f x r c h ws a d e e t t e f ws i h c o c mp n n . Ex e i n e u t l l o et p r me t r s ls
(. 1 长春 理 工 大 学 机 电工 程 学 院 ,吉林 长 春 1 0 2 ; 3 0 2 2 中国 科 学 院 长 春 光 学 精 密 机 械 与物 理 研 究 所 ,吉林 长 春 1 0 3 ) . 3 0 3
摘 要 :为 实 现 微 小 尺 寸 零 件 表 面 缺 陷 的 快 速 精 确 检 验 , 微 小 尺 寸 零 件 表 面 缺 陷 光 学 检 测 技 对
于超 声 波 、 线 、 磁 涡 流 等 的 检 测 方式 , 种 方 式 射 电 这 普遍 存 在着 检测 效率 低 、 准确 性差 、 境要 求 高等 弊 环
病 。 , 不 适 合 微 小 尺 寸 零 件 表 面 缺 陷 快 速 精 确 。 并
检测 ; )人 工 目测 检测 方 式 , 方法 存 在 着 检 测 效 2 该
s w ha h l o i m a fe tv l d t c h a , a d t e o n to ae o h ee t i b u ho t tt e ag rt h c n ef cie y ee tt e f ws l n he r c g iin r t f t e d f c s a o t
作者 简 介 : 晓 舟 ( 9 3 ) , , 教 授 。E m i i a z o ld @ s n c i 李 16 一 男 副 - al x oh ug x i . o :l i a n
第 7期
微
83 7
患 。 因此 , 何快 速 精 确 检 验 微 小 尺 寸 零 件 的 微 观 如 表 面缺 陷成 为急 需解 决 的问题 。 目前 , 件缺 陷检 测 主要 采 用 2种 方 式 :1 零 )基
率低 、 检率 高 、 能 在 线检 测 等 缺 陷 , 提 高 检 测 误 不 为 精度 , 目测必 须在 强光 下进 行 , 检测 者视 力危 害极 对
大 , 至 造成 永久 性损 伤 。 甚
刘 良江 等 用 低 维 灰 度信 息 来 描述 磁 环 特 征 ,
提 出 基 于 灰 度 直 方 图 和 支 持 向 量 机 的 微 小 磁 环 自动
t a ee t n tc n lg a tde .T kn y ia co r g c mp n n so jc n o sd r g i ld tci e h oo y w ssu id a ig atpc lmir i o o e ta be ta d c n iei c o n n
第 3 2卷第 7期 20 11年 7月
兵
工
学
报
Vo . 2 1 3 NO 7 .
ACTA ARM AM ENTARI I
J 1 2 1 u. 01
微 小 尺 寸 零件 表 面缺 陷 光 学检 测 方法
李 晓舟 ,于 化 东 ,于 占江 ,刘岩 ,许 金 凯
首先 , C D光 学 系统 获取 的待 检 图像 进 行频 域 变 将 C 换 , 利用 巴 特 沃 斯 高 通 ( H F 并 B P )自适 应 滤 波 器 进 行 滤 波 , 制 表面 随机 纹理 和 背景 噪声 , 抑 进行 第一 重
微小 尺 寸零件 表 面 缺 陷 光学 检 测 系统 , 出 图 像 梯 提
术 进行 了研 究。 以典 型微 小尺 寸环 形零 件为研 究 对象 , 零件 的表 面特 征 、 陷类型及 检测 算 法 出 从 缺
发, 建立 了基 于机器 视觉 的微 小尺 寸零件 表面缺 陷光学检 测 系统 ; 过对微 小尺 寸环形 零件表 面缺 通
陷纹理特 征研 究 , 出图像 梯度 方差 加权 信息 熵算 法抑 制 表 面 随机 纹理 , 取 微 观 表 面缺 陷, 行 提 提 进 微 小尺 寸零件缺 陷的检测 。实 验结果 表 明 : 检测 算法 能够 快速 有效 地 进 行微 小 尺 寸零 件 表 面缺 该
中 图 分 类 号 :T 3 14 P 9. 文 献 标 志 码 :A 文 章 编 号 : 0 01 9 ( 0 1 0 —8 20 10 —0 3 2 1 ) 70 7 .6
Op i a ns c i n M e h d f r S f c f c s o i r c m po nt tc lI pe to t o o ur a e De e t f M c o- o ne s
iss Fa e f aurs a d d f c haa t rsis,a p ia e e t n s se wa sa ih d o h sso t u f c e t e n ee tc r ce itc n o t ld tc i y tm s e tbl e n t e ba i f c o s ma h n iin a a tr e o n to c i e v so nd p te n r c g iin. T r ug t d e ft u a e fa tx u e i h o h o h su is o he s r c w e t r n t e c mpo n , a f l ne t n
背景 抑制 ; 次 , 傅 里 叶逆变 换后 的图像通 过滤 波 其 将
操作 对 图像 的灰度 分 布进 行 调 整 , 现对 背 景 和 随 实 机纹 理进 行第 二重 背 景抑 制 ; 经过 两重 抑制 , 图像 上 的背 景杂 波减 少 , 通 过 图像 二 值 分 割 、 界 去 除 、 再 边