Mapping Customer-Supplier Relationships
(整理)6西格玛培训笔记.

六西格玛黑带培训2008年7月22日星期二1)六西格玛(6SIGMA)的概念Y=F(X)(Y=顾客X=PROCESS 工程)为满足顾客的要求进行的改善过程活动。
SIX SIGEMA 广义范围:6δ狭义范围:经营的视角:通过6SIGMA 更换工作的方式,运营哲学运营的视角:使用统计技法解决业务中的问题。
2)Define Measure Analyze Improve Control定义Y(顾客的要求不断再变,举例:色像不良(Y的指标:灰度,亮度等)顾客所重要的CTQCTQ = Critical to quality (核心质量特性)※定义阶段的核心内容是CTQ3)Measure(测量阶段)举例:色像不良(现水平的把握)4)Analyze (分析)为什么出现这样结果?(通过5M1E 分析,有疑问的因子全部找出来)。
VITAL FEW X`S 少数核心因子5)Improve(改善)Y收率=F(X)(温度?,浓度?,压力?指定的最佳化情况下不变)6)Control(管理)原位置管理的相关控制。
7) Define 阶段Roadmap定义阶段分为3个阶段(选定项目,项目的定义,批准项目)项目名:为了什么目的使用什么手段改善什么对象以%改善1.课题选定背景1)事业性侧面(卖出额,利益,M/S等)举例:因为什么问题,对公司的形象,利益等有影响等2)生产性侧面(跟竞争对象的人均生产能力低等)3)品质侧面(不良率,顾客满意率等)4)战略性的联系5)环境,安全侧面,法规…..6)其他….2. 现象及问题(对问题的阐述)举例;更详细的描述问题(如3000PPM时生产费用增加)具体的资料化(细分化)DATA(数据)→指标或者具体钱数等.问题和问题点的不同 (问题是大范围,问题点是小范围或者要素)3. VOC (顾客的要求事项)→CCR (顾客核心要求事项)Critical customer requirement →CTQ(核心品质特性)(REAL 顾客要求准确的添加)时间/金钱/人员/把顾客所有的要求的完成的话,先要把重要举例:CTQ是以专业术语(如GAP,厚度)CCR=CTQ 有时候可以成为一样的CTQ 通过CHART 来选定4.CTQ的运营的定义(O.D: Operational Definition)1)为了避免沟通上的差异,需要运营的定义.2)范围:3)计算式:4)不良类型设定:5. 课题的范围(SIPOC) Process MappingSupplier INPUT Process Output Customer(供应者) (输入) (工程) (产出物) (顾客)6. 目标设定1) Bench marking2) 理论的依据3) 以往的最佳值(挑战性目标50%)7. 日程计划Detail(详细) 计划8. Team 构成Champion→Process Owner→MBB(CONSULTANT)→BB→组员1)作用 2)责任 3)贡献度2008年7月23日星期三 13:00~17:001)TEAM 任务书课题选定背景:(目的)我们为什么要工作?(对业务的影响)项目描述书:经历了哪些失败?有哪些错误?有哪些改善的机会?目标描述书:我们改进目的和目标是什么?(成功的基准)项目范围:哪些过程作为对象?是小组执行的范围吗?不是我们执行的范围是?(界限)日程计划:是否合理的各项活动的日程?是否在期限内执行?(活动)TEAM构筑:谁是倡导者/黑带大师/过程负责人?谁是小组组成人员?他们的责任范围是?(谁,执行什么?)2)投石器实验制定任务书(选定项目背景,问题描述书,目标描述书,项目范围,推进项目日程,推进小组。
六西格玛案例PPT课件
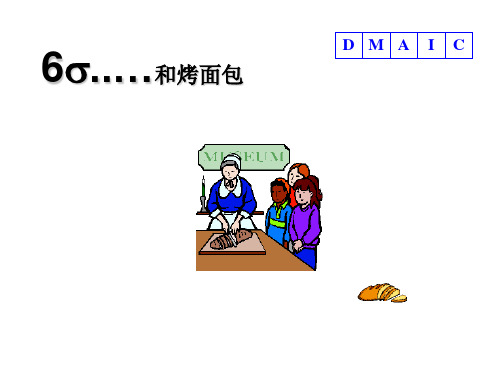
“重复性”和“再现性 ”提供了有效的衡量方法
Panel Member
Loaf 1 Loaf 2 Loaf 3
A 5 8 9 B 4 9 1 C 4 9 2 D 8 9 8 E 4 8 2 F 5 9 1 G 8 9 2
6s..…和烤面包
D
M
A
I
C
D
M
A
I
C
项目选择的理由(背景) 为什么要做这个项目? 确定CTQ/Y(关键质量特性) 顾客是谁? 顾客的要求是什么? 什么是关键质量特性?
D阶段
FLOUR
“BETTER BREAD” 公司
面粉
酵母
D
M
A
I
C
项目背景
市场上品牌越来越多,竞争越来越激烈 消费者的消费档次在不断提升 近3个月来日销量持续下降(-14%) 经市场调查顾客减少购买的主要原因是面包的质量 要提升面包质量,增加市场竞争力
D
M
A
I
C
测量系统验证结果
测量系统基本可以信赖,但不是很好
…..为Y(口感) 建立初始流程能力
我们现在的流程能力怎么样?
D
M
A
I
C
…..为Y(口感) 建立流程能力
7 6 5 4 3 2 1
1 2 3 4 5 6 7 8 9 10
我们如何定义改进?
把竞争对手作为标杆 聚焦在缺陷上(即: 口感分值<7) 确定什么是一个“可以接受的s水平” 设立相应的改进目标
D
M
A
I
C
…..确定导致Y(口感)变异的因素
我们怎样确定潜在的导致变异的因素(Xs)?
D
M
A
I
SIPOC及应用
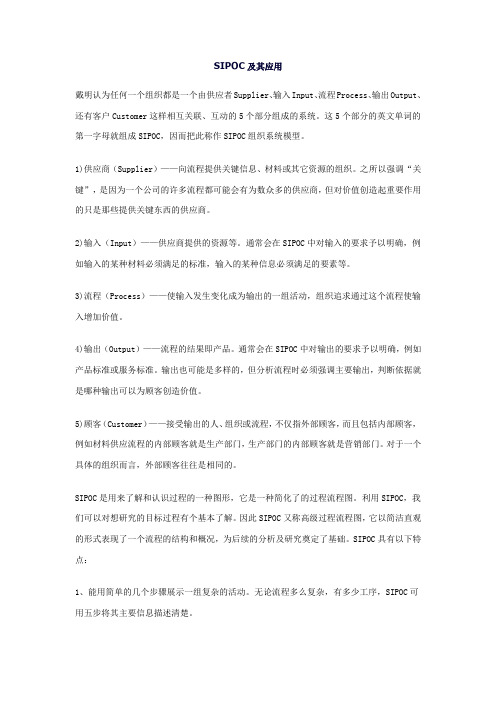
SIPOC及其应用戴明认为任何一个组织都是一个由供应者Supplier、输入Input、流程Process、输出Output、还有客户Customer这样相互关联、互动的5个部分组成的系统。
这5个部分的英文单词的第一字母就组成SIPOC,因而把此称作SIPOC组织系统模型。
1)供应商(Supplier)——向流程提供关键信息、材料或其它资源的组织。
之所以强调“关键”,是因为一个公司的许多流程都可能会有为数众多的供应商,但对价值创造起重要作用的只是那些提供关键东西的供应商。
2)输入(Input)——供应商提供的资源等。
通常会在SIPOC中对输入的要求予以明确,例如输入的某种材料必须满足的标准,输入的某种信息必须满足的要素等。
3)流程(Process)——使输入发生变化成为输出的一组活动,组织追求通过这个流程使输入增加价值。
4)输出(Output)——流程的结果即产品。
通常会在SIPOC中对输出的要求予以明确,例如产品标准或服务标准。
输出也可能是多样的,但分析流程时必须强调主要输出,判断依据就是哪种输出可以为顾客创造价值。
5)顾客(Customer)——接受输出的人、组织或流程,不仅指外部顾客,而且包括内部顾客,例如材料供应流程的内部顾客就是生产部门,生产部门的内部顾客就是营销部门。
对于一个具体的组织而言,外部顾客往往是相同的。
SIPOC是用来了解和认识过程的一种图形,它是一种简化了的过程流程图。
利用SIPOC,我们可以对想研究的目标过程有个基本了解。
因此SIPOC又称高级过程流程图,它以简洁直观的形式表现了一个流程的结构和概况,为后续的分析及研究奠定了基础。
SIPOC具有以下特点:1、能用简单的几个步骤展示一组复杂的活动。
无论流程多么复杂,有多少工序,SIPOC可用五步将其主要信息描述清楚。
2、可以用来展示整个组织的业务流程。
SIPOC可以简单描述一个组织的业务过程,既可以对总体流程作以描述,也可以对各子流程分别作以描述,然后根据流程顺序将各SIPOC连接成一张总的流程图。
SupplierManagement供应商管理

流程图
Supplier
资源 战略
执行 Supplier 调查
实地稽核
供应商 改善与后续稽核
商谈质量协议
Supplier
质量状况
BPI
选择供应商
质量管理计划
(OTPV and Supplier)
设计评审
(OTPV or Supplier)
新产品准备会
SQE Program
SupplierManagement供应商管理
调查/ 问卷 公司的基本咨讯/管理团队/员工人数&生产设备/认证/客户群/文献/质量体系 给 supplier一个初步的评估(评分) 给Supplier一段时间自我整顿/准备正式稽核
SupplierManagement供应商管理
调查/问卷 – 基本内容 公司基本资料 ✓ 名称/地址 & 位置 ✓ 联系方式 ✓ 子公司/控股公司 ✓ 贸易 & 产品 ✓ 投资 & 年收入状况
SupplierManagement供应商管理
改善 and 追踪稽核 追踪稽核其改善对策的有效性 追踪稽核只是针对已经发现的有限问题点,所以评分不能改变
SupplierManagement供应商管理
改善 and追踪稽核
“ CLCA 格式”
SupplierManagement供应商管理
品质协议 某些产品品质的特定要求 需要相关法律、法规认可 当拟订商业合同或变更品质要求时可能需要重新商议品质合约
相关认证
✓ ISO9000 ✓ ISO14000 ✓ UL/ CE ✓ 其他
SupplierManagement供应商管理
调查/问卷 – 基本内容
精益成本管理的八项原则
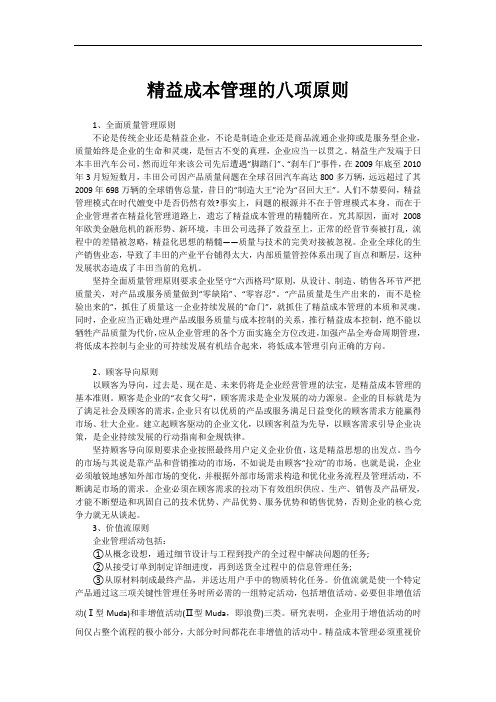
精益成本管理的八项原则1、全面质量管理原则不论是传统企业还是精益企业,不论是制造企业还是商品流通企业抑或是服务型企业,质量始终是企业的生命和灵魂,是恒古不变的真理,企业应当一以贯之。
精益生产发端于日本丰田汽车公司,然而近年来该公司先后遭遇“脚踏门”、“刹车门”事件,在2009年底至2010年3月短短数月,丰田公司因产品质量问题在全球召回汽车高达800多万辆,远远超过了其2009年698万辆的全球销售总量,昔日的“制造大王”沦为“召回大王”。
人们不禁要问,精益管理模式在时代嬗变中是否仍然有效?事实上,问题的根源并不在于管理模式本身,而在于企业管理者在精益化管理道路上,遗忘了精益成本管理的精髓所在。
究其原因,面对2008年欧美金融危机的新形势、新环境,丰田公司选择了效益至上,正常的经营节奏被打乱,流程中的差错被忽略,精益化思想的精髓——质量与技术的完美对接被忽视。
企业全球化的生产销售业态,导致了丰田的产业平台铺得太大,内部质量管控体系出现了盲点和断层,这种发展状态造成了丰田当前的危机。
坚持全面质量管理原则要求企业坚守“六西格玛”原则,从设计、制造、销售各环节严把质量关,对产品或服务质量做到“零缺陷”、“零容忍”。
“产品质量是生产出来的,而不是检验出来的”,抓住了质量这一企业持续发展的“命门”,就抓住了精益成本管理的本质和灵魂。
同时,企业应当正确处理产品或服务质量与成本控制的关系,推行精益成本控制,绝不能以牺牲产品质量为代价,应从企业管理的各个方面实施全方位改进,加强产品全寿命周期管理,将低成本控制与企业的可持续发展有机结合起来,将低成本管理引向正确的方向。
2、顾客导向原则以顾客为导向,过去是、现在是、未来仍将是企业经营管理的法宝,是精益成本管理的基本准则。
顾客是企业的“衣食父母”,顾客需求是企业发展的动力源泉。
企业的目标就是为了满足社会及顾客的需求,企业只有以优质的产品或服务满足日益变化的顾客需求方能赢得市场、壮大企业。
客户动态管理 英语
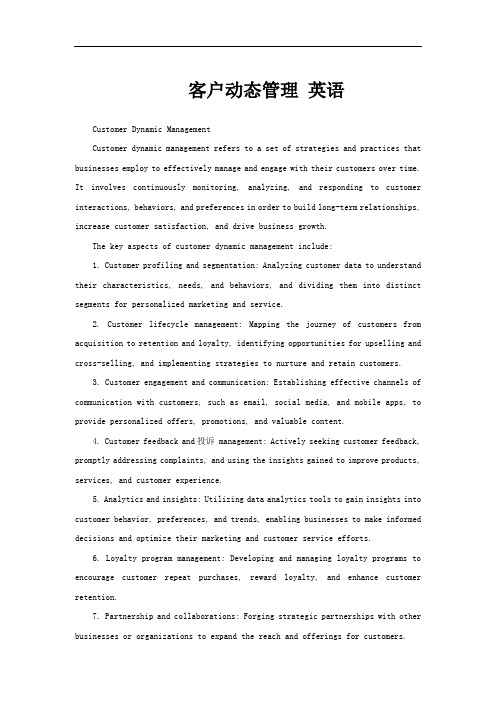
客户动态管理英语Customer Dynamic ManagementCustomer dynamic management refers to a set of strategies and practices that businesses employ to effectively manage and engage with their customers over time. It involves continuously monitoring, analyzing, and responding to customer interactions, behaviors, and preferences in order to build long-term relationships, increase customer satisfaction, and drive business growth.The key aspects of customer dynamic management include:1. Customer profiling and segmentation: Analyzing customer data to understand their characteristics, needs, and behaviors, and dividing them into distinct segments for personalized marketing and service.2. Customer lifecycle management: Mapping the journey of customers from acquisition to retention and loyalty, identifying opportunities for upselling and cross-selling, and implementing strategies to nurture and retain customers.3. Customer engagement and communication: Establishing effective channels of communication with customers, such as email, social media, and mobile apps, to provide personalized offers, promotions, and valuable content.4. Customer feedback and投诉 management: Actively seeking customer feedback, promptly addressing complaints, and using the insights gained to improve products, services, and customer experience.5. Analytics and insights: Utilizing data analytics tools to gain insights into customer behavior, preferences, and trends, enabling businesses to make informed decisions and optimize their marketing and customer service efforts.6. Loyalty program management: Developing and managing loyalty programs to encourage customer repeat purchases, reward loyalty, and enhance customer retention.7. Partnership and collaborations: Forging strategic partnerships with other businesses or organizations to expand the reach and offerings for customers.By implementing customer dynamic management, businesses can proactively adapt to changing customer needs and market dynamics, delivering personalized experiences, and building strong, long-lasting customer relationships. This ultimately leads to increased customer loyalty, higher customer lifetime value, and sustainable business growth.。
价值流图--课件

31
五、绘制价值流现状图
第一步:画出代表客户、供应商和生产控制中心的图标
生产控制中心
**供应商
**客户
用同样的图标代表客户和供应商 将客户的图标画在纸张的左上角 将供应商的图标画在纸张的左上角 在客户和供应商的图标之间画出生产控制中心(PMC)的图标
32
第二步:在客户图标的下方画一个数据框,将客户的需求 填入其中
设计 流程
概念 订单
生产 流程
订单执 行流程
原材料 产成品交付
时间 现金
6
3、企业经营活动三大流动主体
供应商
资资金金流流、、信信息息流流、、物物流流
企业经 营过程
客户
资资金金流流、、信信息息流流、、物物流流
我们今天接触的价值流是工艺流程、物流、价值流的统一
7
二、价值流图析
1、何谓价值流图: 用目视化手段以描述整体价值流,包含物流及信
19
C、目标价值流选择原则
• 建议不要选择过于简单的价值流,也不要选择太复杂的价 值流 • 建议选择一条所包含的机加工作业不超过1项的价值流 • 建议选择一条所包含的原材料供应商不超过3家的价值流 • 建议选择一条所包含的作业或中转环节不超过12项的价值 流 • 价值流管理初期可选择简化的PQ分析法,即对产品数量约 占总产量的20%的价值流作为可考虑的备选对象。
周期时间:Cycle Time(C/T) 设备利用率:Available Work Time(Uptime),加工 时间、可利用时间
27
B、标准在制品相关数据 标准在制品数量(WIP)=工作时间内的老化
时间/生产节拍
工作时间内老化时间(因工艺必须的停滞 时间)
品质常用语解释

ST : Standard Time,一个工艺所需要的标准时间。 T/T: Tack Time,生产线的单件产品生产时间。 ODM/OEM : Original Design(Equipment) Manufactures,原始装置(设备)制造商品。 Histogram : 柱状图,设定几个区间,画出Data的所在范围,并标记其发生频度的图形。 Blank Chart : 空白表格,无数据的,按照进展方向画出大体Output Image的方法。 Pareto Chart : 根据“20%的ISSUE导致80%的问题”的统计理论,对问题的核心进行分析时使用的工具。 5Why : 5次Why,找寻问题的根本原因时使用的工具。 As is Mapping : 画出As is(改善前现在的Image)及To Be(改善后日后所要达成的Image),并找出变化Point的方法。 Key Words : 关键字或词。 Neck : 做某种事项的过程中,成为障碍的,或需要事先解决的最为薄弱的部分。
常用语解释
DA事业本部 : Digital Appliance 事业本部。 TDR : Tear Down Redesign,是一种临时的,为创造某种独特的产品和服务而竭尽全力承担责任的革新活动。 1人1P : 1人1Project,指以DMAIC促进的6σ改善活动。 NWT : Natural Work Team,指以PDCA促进的现场自主改善活动。 Big Y : 为了实现愿景目标(一等LG),需要迫切解决并集中组织力量解决的事业课题。 KPI : Key Performance Indicator,关键成果指标,定量化的、能够测定并体现课题全部活动成果的指标。 CTQ : Critical to Quality,站在顾客角度,影响产品品质的核心特征值,CTQ必须要可以测量。 QCD : Quality、Cost、Delivery,指找寻CTQ时在顾客及公司本身能力上的3大主要方向。 Major Objective : 在给定时间内为解决Big Y,而进一步选定的能够很快解决并与其他业务相关联的核心活动或业务领域。 Action Plan : 为了实现革新vision和KPI目标而确立的一系列步骤或活动。
供应链运作参考模型课件

Membership
750+ SCC members, Composition 40%: Practitioners 25%: Enabling Technology Providers 20%: Consultants 15%: Universities, Associations, Government Organizations
Best Practices Analysis
Process Reference Model
Capture the “as-is” state of a process and derive the desired “to-be” future state
Business Process Reengineering
Characterize the management practices and software solutions that result in “best-in-class” performance
What is a process reference model?
Process reference models integrate the well-known concepts of business process reengineering, benchmarking, and process measurement into a cross-functional framework
M2 Make-to-Order
M3 Engineer-to-Order
D1 Deliver Stocked Products
D2 Deliver MTO Products
SIPOC是什么
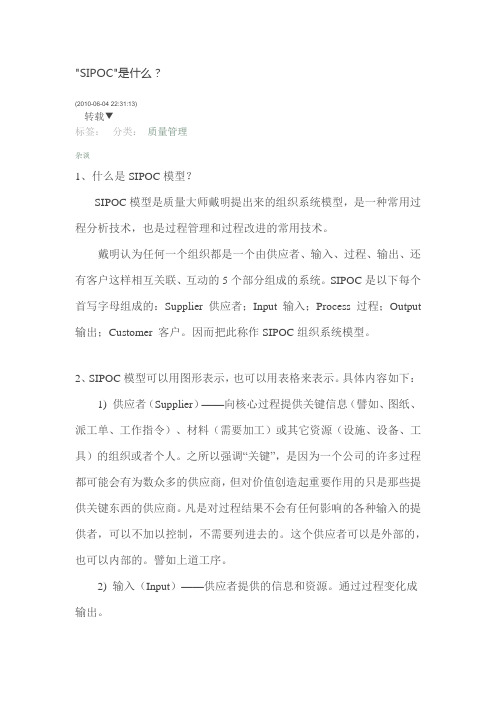
"SIPOC"是什么?(2010-06-04 22:31:13)转载▼分类:质量管理标签:杂谈1、什么是SIPOC模型?SIPOC模型是质量大师戴明提出来的组织系统模型,是一种常用过程分析技术,也是过程管理和过程改进的常用技术。
戴明认为任何一个组织都是一个由供应者、输入、过程、输出、还有客户这样相互关联、互动的5个部分组成的系统。
SIPOC是以下每个首写字母组成的:Supplier 供应者;Input 输入;Process 过程;Output 输出;Customer 客户。
因而把此称作SIPOC组织系统模型。
2、SIPOC模型可以用图形表示,也可以用表格来表示。
具体内容如下:1) 供应者(Supplier)——向核心过程提供关键信息(譬如、图纸、派工单、工作指令)、材料(需要加工)或其它资源(设施、设备、工具)的组织或者个人。
之所以强调“关键”,是因为一个公司的许多过程都可能会有为数众多的供应商,但对价值创造起重要作用的只是那些提供关键东西的供应商。
凡是对过程结果不会有任何影响的各种输入的提供者,可以不加以控制,不需要列进去的。
这个供应者可以是外部的,也可以内部的。
譬如上道工序。
2) 输入(Input)——供应者提供的信息和资源。
通过过程变化成输出。
3) 过程(Process)——使输入变成输出的一组活动,应当关注增加价值,如果不增值的,应当设法消除它,现在不能消除,以后创造条件消除它。
4) 输出(Output)——过程的结果即产品(包括半成品)。
5) 顾客(Customer)——过程输出的接受者,组织或个人。
不仅指外部顾客,而且包括内部顾客,例如材料采购过程的输出结果是原材料,内部顾客就是生产部门,生产部门的内部顾客就是营销部门。
3、SIPOC的作用和优点1) 界定过程范围。
凡是确定在SIPOC中的因素,必须加以控制。
如果有变化,一般应当用5M1H(人、机、料、法、测、环)控制程序来控制的。
精益生产管理实务研究

三、七大浪费
29
增值与非增值
只增加价值的动作
组装 改变形状 改变性能 包装
与工作无关的动作
纯 增 价
浪 简 单 动 费 作
等待工作 制造理由 聊天 四处走动
值
低效率的动作
*人 紧急指导工作 技术性工作 附加的工作(设计变更) *设备 能力低(加工能力) 部件损伤(顶针) 不良品
生产活动 效 价 值 作
没有谁已经“精益”
• “精益”是相对的– 为什么要和他人比? – 为什么不和自己比?
• 持续改善意味着你永远没有终点
– 你永远没有足够“精益”
• 精益之旅不是百米赛跑,而是马拉松
– 你能坚持20年吗? – 你能坚持着持续改善下去吗?
• 理解耐心和拖延的区别
精益的特征是什么
• • • • • • 持续的改善和积极地减少浪费 将重心放在为客户创造价值上 (包括内部客户) 能灵活地对变化的需求做出响应 有能力应对市场的需求 提供必要的挑战 将组织和企业的外部沿伸完全的结合为一个整体
员工激励和员工自主的6个基本点
1. 日常交流:TOP 5 2. 日常管理工作的标准化:工作日志 3. 日常工作技能掌握:工作基础 4. 合理化建议:组织激励
5. 任务转移:组织高效
6. 管理员工培训:“养兵一时,用兵千日”
员工自主审核内容
1. 工作环境Work environment
① 安全Safety ② 工作环境Work environment
精益现场改善实战训练营
主讲人:王嵬威
1
共同语言
问 集 好----- 听音乐,准时到场
新鲜的空气---- 请不要在教室内吸烟
封闭的环境---- 排除一切外部干扰
制造企业常用术语英文缩写及全称
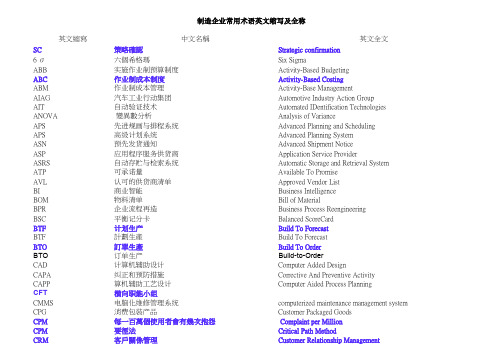
制造企业常用术语英文缩写及全称英文縮寫中文名稱英文全文SC策略確認Strategic confirmation6 σ六個希格瑪Six SigmaABB实施作业制预算制度Activity-Based BudgetingABC作业制成本制度Activity-Based CostingABM作业制成本管理 Activity-Base ManagementAIAG汽车工业行动集团Automotive Industry Action GroupAIT自动验证技术Automated IDentification Technologies ANOVA 變異數分析Analysis of VarianceAPS先进规画与排程系统Advanced Planning and SchedulingAPS高级计划系统Advanced Planning SystemASN预先发货通知Advanced Shipment NoticeASP应用程序服务供货商Application Service ProviderASRS自动存贮与检索系统Automatic Storage and Retrieval SystemATP可承诺量 Available To PromiseAVL认可的供货商清单Approved Vendor ListBI 商业智能Business IntelligenceBOM物料清单Bill of MaterialBPR企业流程再造Business Process ReengineeringBSC平衡记分卡Balanced ScoreCardBTF计划生产Build To ForecastBTF 計劃生產Build To ForecastBTO訂單生產Build To OrderBTO订单生产Build-to-OrderCAD计算机辅助设计Computer Added DesignCAPA纠正和预防措施Corrective And Preventive ActivityCAPP算机辅助工艺设计Computer Aided Process PlanningCFT横向职能小组CMMS电脑化维修管理系统computerized maintenance management system CPG消费包装产品Customer Packaged GoodsCPM每一百萬個使用者會有幾次抱怨 Complaint per MillionCPM 要徑法 Critical Path MethodCRM客戶關係管理 Customer Relationship ManagementCRP产能需求规划Capacity Requirements Planning CS 顧客滿意度 Customer SatisfactionCTO客製化生產Configuration To OrderCTQ品質關鍵 Critical to qualityDBR限制驱导式排程法 Drum-Buffer-RopeDCP动态控制计划(尺寸控制计划)DFMEA设计失效模式及后果分析DFSS 六個希格瑪設計 Design for six sigmaDHR器械历史文件Device History RecordDMT成熟度验证Design Maturing TestingDOE實驗設計 Design of experimentDOE试验设计DPM每百萬單位的缺點數Defects per millionDPMO每百萬個機會的缺點數Defects per million opportunities DPU單位缺點數Defects per unitDRP运销资源计划Distribution Resource Planning DSS決策支援系統Decision Support SystemDVP&R设计验证计划和报告DVT設計驗證 Design Verification Testing EBOM工程设计BOMEC設計變更/工程變更Engineer ChangeEC电子商务Electronic CommerceECRN原件规格更改通知Engineer Change Request Notice EDI电子数据交换Electronic Data Interchange) EIS主管决策系统Executive Information System EMC電磁相容 Electric Magnetic Capability EMEA欧洲、中东和非洲EOQ基本经济订购量 Economic Order QuantityERP企业资源规划Enterprise Resource Planning ETO按订单设计FAE应用工程师Field Application Engineer FCST预估ForecastFMA失效模式分析FMEA故障型態與效應分析Failure mode and effect analysis FMS弹性制造系统Flexible Manufacture System FQC成品质量管理Finish or Final Quality ControlFTC首次能力Gage R & R 量規重複能力與重製能力 Gage repeatability & reproducibilityGR&R 量具的重复性和再现性HMI人机界面Human Machine InterfaceIP网际协议Internet ProtocolIPQC制程质量管理In-Process Quality ControlIQC 進料品質管制 Incoming Quality ControlIRR内部收益率Internal Rate of ReturnISAR首批样品认可Initial Sample Approval RequestISO國際標準組織International Organization for Standardization JIT实时管理Just In TimeKM 知識管理Knowledge ManagementKPI关键绩效指标Key Performance IndexL4L逐批订购法Lot-for-LotLAN局域网Local Area NetworkLCL管制下限Lower control limitLDAP轻量级目录访问协议Lightweight Directory Access Protocol LPCL 前置管制下限Lower Per-control LimitLSL規格下限Lower Specification LimitLTC最小总成本法 Least Total CostLUC最小单位成本Least Unit CostMAN城域网Metropolitan Area NetworkMBOM生产制造物料清单MCT制造周期时间Manufacturing Cycle TimeMDM制造数据管理Manafacturing Data ManagementMES制造执行系统Manufacturing Execution SystemMHE物料处理设备Manufacturing Execution SystemMO制令Manufacture OrderMPS主生产排程 Master Production ScheduleMRO请修(购)单Maintenance Repair OperationMRP物料需求規劃 Material require planningMRP物料需求规划Material Requirement PlanningMRPII制造资源计划 Manufacturing Resource PlanningMTO按订单生产Make to OrderMTS库存生产Make-to-StockNCR—不合格Non-conformanceNFCF更改预估量的通知Notice for Changing ForecastNPV净现值Net Present ValueOBOM订单BOMODM 委託設計與製造Original Design & ManufactureOEM委托代工Original Equipment ManufactureOEM原始设备制造商Original Equipment ManafacturerOLAP在线分析处理On-Line Analytical ProcessingOPC用于过程控制的对象链接和嵌入OLE for Process ControlOPT最佳生產技術 Optimized Production TechnologyOQC出貨品質管制Out-going Quality ControlPA 專案核准Program approvalPAPC生产和流程控制Production and Process ControlPBOM工艺规划BOMPCL 前置管制中心限 Per-control Central LimitPDCA PDCA管理循環 Plan-Do-Check-ActionPDM产品数据管理Product Data ManagementPDM产品数据管理系统Product Data ManagementPERT计划评核术 Program Evaluation and Review Technique PFMEA过程失效模式及后果分析PLM产品生命周期管理Product Lifecycle ManagementPO訂單Purchase OrderPO订单Purchase OrderPOH预估在手量Product on HandPP回收期Payback PeriodPQP产品质量策划PQPT 产品质量策划小组PR采购申请Purchase RequestPR 產品確認Product readinessQA 品質保證 Quality AssuranceQC 品質管制Quality ControlQCC 品管圈 Quality Control CircleQE品质工程Quality EngineeringQFD品質機能展開 Quality function deploymentQFD质量功能展开QSR质量体系要求RCCP粗略产能规划 Rough Cut Capacity PlanningRMA 退貨驗收 Returned Material ApprovalROP再訂購點Re-Order PointROP再订购点 Re-Order PointSBOM销售BOMSCADA数据采集和监视控制Supervisory Control and Data Acquisition SCM 供應鏈管理Supply Chain ManagementSCV供应链可见性Supply Chain VisibilitySFA自动销售Sales Force AutomationSFC 現場控制 Shop Floor ControlSFMEA 系统失效模式及后果分析SI策略形成 Strategic intentSIS策略信息系统 Strategic Information SystemSO 訂單 Sales OrderSOA面向服务架构Service Oriented ArchitectureSOR 特殊訂單需求 Special Order RequestSPC统计过程控制Statistic process controlSPC 統計制程管制Statistical Process ControlTAV全部资产可视化Total Assets VisualizationTCP传输控制协议Transfer Control ProtocolTGR 运行情况良好TGW 运行情况不良Time to Market即时上市/及时切入生产Time to Money即时变现/及时大量交货Time to Volume即时量产/及时大量生产TOC 限制理論 Theory of ConstraintsTPM全面生产管理Total Production ManagementTQC 全面品質管制Total Quality ControlTQM 全面品質管理 Total Quality ManagementUCL 管制上限Upper control limitUPCL前置管制上限Upper Per-control LimitUSL規格上限Upper Specification LimitVE/VA价值工程/价值分析VMI供货商免费存放Vendor Managed InventoryWAN广域网Wide Area NetworkWIP在製品Work In Processσ, s 標準差 Standard deviationσ2, S2 變異數 VariancePP生产验证Production ProveoutTTO工装设备试运行 Tool Try-Out(J1)整车投产Job 1DFMEA故障模式影响分析设计Design Failure Mode Effects AnalysisDVP设计验证计划Design Verification PlanDVP&R设计验证计划和结果 Design Verification Plan & ReportFMEA故障模式影响分析Failure Mode Effects AnalysisFPDS福特产品开发系统 Ford Product Development SystemGYR 绿-黄-红 Green-Yellow-RedMRD 物料要求到厂日Material Required DateOTT可以开模 OK-TO-TOOLTKO工装启动Tooling-Kick-OffOEM 设备最初制造厂 Original Equipment ManufacturerFtF/F2F面对面会议 Face To FacePV 产品验证 Production ValidationOTS 完全工装样件Off-Tooling-SampleQOS质量运作体系Quality Operating SystemTS-16949 技术规范-16949Technical Specification – 16949APQP 先期产品质量计划Advanced Product Quality PlanningIPD进厂日 In Plant DatePPM零件的百万分比率(适用于供应商不合格零件)Parts per Million (applied to defective Supplier parts) PPAP 生产件批准程序Production Part Approval ProcessPre-PV 产品预先验证Pre -Production ValidationDMAIC定义、测量、分析、改进、管理CTQ质量特性值FMEA故障模式及影响分析QFD质量功能展开PTS 课题跟踪系统Project Tracking SystemDPU单位产品缺陷数DPO每个机会的缺陷数;VOC顾客的要求(voice of the customer)Project课题Process过程Procedures程序Sample样本QCD质量、成本、交货期Quality, Cost, DeliveryTarget公差中心COPQ劣质成本R&R重复性和再现性Cp短期过程能力指数,以 Process Capability Index表示过程能力指数.(Cp=T/6σ,T为技术规范的公差幅度);Cpk长期过程能力指数,平均值与目标值不同时(产品质量分布的均值与公差中心不重合时)的过程能力指数。
六标准差评估与改善系统

(began in 1949): Toyota Production System – Taiichi Ohno, Shigeo Shingo
Japanese quality Movement – Taguchi, Ishikawa
Reconstruction of Japan – Quality Circles, Kaizen 1940: Statistical Sampling techniques – W. Edwards Deming
DMAIC(界定→衡量→分析→改善→控制) DMADV(界定→衡量→分析→設計→驗證)。
2013/8/7
中国最大的资料库下 载
17
前言:六標準差的三大引擎
2013/8/7
中国最大的资料库下 载
18
前言:六標準差的策略與改善模式
2013/8/7
中国最大的资料库下 载
ቤተ መጻሕፍቲ ባይዱ
2013/8/7
前言:六標準差的六項要件
1. 2. 3. 4. 5. 6. 真誠關心顧客 憑資料和事實管理 流程為重並加以管理和改進 主動管理 打破藩籬的協力合作 追求完美、容忍失敗
中国最大的资料库下 载
2013/8/7
8
前言:六標準差的成功案例
奇異電子公司的案例 六標準差永遠改變了奇異。每位員工— 從黑帶訓練營出來的六標準差狂熱份子, 到工程師、查帳員、科學家,以及要帶 領奇異進入新世紀的高階主管--都是六標 準的忠實信徒。這家公司正在實踐六標 準差。 奇異公司董事長威爾許 (John Welch)
前言:六標準差的重要性
面對新時代的來臨,產業必頇重新調整 腳步,不但注重生產的效率,更要提高 產品的品質與價值。 6σ(六標準差)具有獨特的之流程核心 技術、多重運用工具與強勢之領導管理 策略 。
TOM (全面订单管理)模型

TOM (全面订单管理)模型来源:互联网【摘要】:TOM模型,即全面订单管理模型,涵盖了从客户的需求到订单履行的整个过程,文中对TOM模型的四个组成方阵:资源管理、需求管理、制造管理和可供应能力管理进行了解释。
TOM模型(Total Order Management)是美国OPD公司的“产品”,在ISC项目关注阶段由IBM顾问引入进HWT。
TOM模型,即全面订单管理模型,顾名思义,它主要是关注企业在订单履行方面的管理。
TOM模型涵盖了从客户的需求到订单履行的整个过程(见图1),主要包括资源管理、需求管理、制造管理和可供应能力管理这四个模块。
此外,TOM 模型和其他业务部门还存在着接口:来自销售部门的市场无约束的预测,来自行销部门的客户层次、产品策略的信息,来自制造部门的物料/产能供应的信息。
通过这些相关环节,最后是计划的执行。
这里的“执行”,其涵盖的范围要比订单履行的含义更广,不仅包括工厂中的订单履行,还包括采购下单等活动,即任何有利于订单履行的活动都包含在执行范围内的。
附图1TOM模型强调的是,由于市场是在不断变化的,因此在生产过程中保持一个连续的、一致的单一计划是非常重要的。
如何保证计划的一致性?这就需要一套计算机化的系统,把响应市场需求的周期尽可能缩短,同时,制定出一系列应对的规则,这样,生产体系就会首先响应最重要、最紧急得需求,而非最近的、或者是叫得最响的需求。
因此,TOM模型的特点就在于它是一个计算机化的、有规则体系的、严格控制的计划流程。
流程、规则和数据是TOM模型中不可或缺的部分,其中,规则是其非常重要的一个部分,也正是支持企业运作的部分。
TOM模型由四个方阵组成:资源管理、需求管理、制造管理和可供应能力管理(见图2)。
图例:规则数据流程附图2在资源管理方阵中,通过资源合理化流程,对供应(考虑约束资源的状况)和需求(无约束的需求预测)进行一个较高层次的匹配,输出一个可行的发货计划给需求管理方阵。
系统梳理公司供应链上下游供应关系
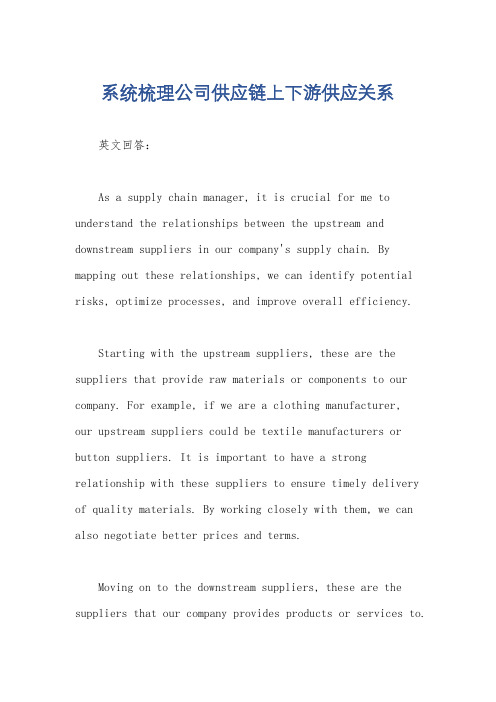
系统梳理公司供应链上下游供应关系英文回答:As a supply chain manager, it is crucial for me to understand the relationships between the upstream and downstream suppliers in our company's supply chain. By mapping out these relationships, we can identify potential risks, optimize processes, and improve overall efficiency.Starting with the upstream suppliers, these are the suppliers that provide raw materials or components to our company. For example, if we are a clothing manufacturer,our upstream suppliers could be textile manufacturers or button suppliers. It is important to have a strong relationship with these suppliers to ensure timely delivery of quality materials. By working closely with them, we can also negotiate better prices and terms.Moving on to the downstream suppliers, these are the suppliers that our company provides products or services to.For example, if we are a software company, our downstream suppliers could be IT consulting firms or software distributors. It is important to understand the needs and expectations of these suppliers to deliver products or services that meet their requirements. Building strong relationships with downstream suppliers can lead to repeat business and referrals.In some cases, a supplier can be both upstream and downstream. For example, if we are a food manufacturer, a farmer who supplies us with raw ingredients could also be a customer who buys our finished products. These types of relationships are complex but can be mutually beneficial if managed effectively.中文回答:作为供应链经理,我必须了解公司供应链中上游和下游供应商之间的关系。
精益制造推进中英文对照表

FIFO(First In, First Out)先进先出 SPC(Statistic Process Control)统计制程管制 SCM(Supply Chain Management)供应链管理 WIP(Work In Process)在制品 DMAIC (Define Measure Analyze Improve Control) 定义、测量、分析、改善、控 制 QCDSMP (Quality Cost Delivery Safety Productivity Moral) 品质、成本、交期、 安全、效率、士气 SWOT (StrengthWeakness Opportunity Threat) 优势、劣势、机遇、威胁 BSC (Balanced Score Card) 平衡计分卡 SIPOC (Supplier-Input-Process-Output-Client) 供应商、输入、流程、输出、客户 IE (IndustrialEngineering) 工业工程 JIT (Just In Time) 准时制生产 TPS (Toyota Production System) 丰田生产系统 VSM (Value Stream Mapping) 价值流图 SMED (Single Minute Exchange of Die) 快速换模 VOC (Voice of Customer) 客户声音 CTQ (Critical To Quality) 关键性质量要素 QFD (Quality Function Deployment) 质量功能展开 DPMO (Defects Per Million Opportunities)一百万个缺陷机会中实际缺陷数 DPU (Defects Per Unit) 单位缺陷数 COPQ (Cost Of Poor Quality) 不良质量成本