玻璃原料的COD值控制
现代玻璃生产对玻璃原料的要求

精心整理《现代玻璃生产对玻璃原料的要求》之氧化还原性章节现代玻璃生产对玻璃原料的要求玻璃原料的成份控制、粒度控制和COD(化学氧需要量)值控制是高效、优质和低耗熔制玻璃的三要素。
玻璃原料的成份控制对于玻璃原料,不仅要求它的有效氧化物的含量高,有害杂质少,难熔重金属氧化物的含量极少,更重要的是氧化物含量的波动要小。
现代化自动称量系统不能分辨原料中氧化物的变化,因此即使原料称量再准,若其氧化物含量变化很大,熔制出的玻璃的成份仍会波动。
所以,必须严格控玻璃。
砂子????????????白云石????????????石灰石????????????长石??????????????表中所列数据与我国许多玻璃工厂的实际情况相差悬殊,但这毕竟是努力目标,说明要想提高熔化率,这是不可忽视的环节。
??有的原料虽然在有效氧化物的含量和波动方面都比较满意,但是含有过量的难熔重矿物(简称RHM),这种原料也不能算是满意的,甚至根本不能用。
因为难熔重矿物在熔制玻璃过程中极难熔解,残留在成品玻璃中形成玻璃缺陷。
下表是主要玻璃原料中常见的难熔重矿物名称。
一些主要玻璃原料中常见的难熔重矿物原料名称????难熔重矿物的名称砂子????硅线石??兰晶石??红线石??锆英石????尖晶石??刚??玉??铬铁矿??高岭土石灰石????刚??玉??尖晶石??铬铁矿白云石????刚??玉??尖晶石??铬铁矿长石????硅线石??刚??玉??锆英石??铬铁矿????尖晶石??锡??石??蛇纹绿柱石?这些难熔重矿物的粒子愈大,完整地通过熔窑的机会就愈多。
所以对难熔重矿物从粒子大小和数量两个方面都作了规定。
检查方法是取400g原料样品,在分液漏斗中用重液(如四溴乙烷)分离,再用纯碱溶洗,最后在岩相显微镜下数粒数并鉴别矿物类型。
一般控制的限度如下:40?对如何在??????砂子????????????????????????白云石????????????0.5—1.0主要部分??25??????<0.5??<10 ????28??????<0.1??<10????45石灰石???>2.0??<15????0??????>1.0??>20??????0??????0.5—1.0主要部分??6??????<0.5??<10????53??????<0.1??<10????41长石????>0.4??0??????24??????>0.3??<5??????22??????0.1—0.3主要部分????26????<0.1??<0??????28?由于我国绝大多数玻璃工厂尚未控制粒度,所以表中所列数据仅是概略值,即使同一工厂,这批进厂的原料与下批进厂的原料,其粒度能相差很多,另外,可以看出我国原料中细粒级组分的含量过多。
玻璃制造车间排放标准
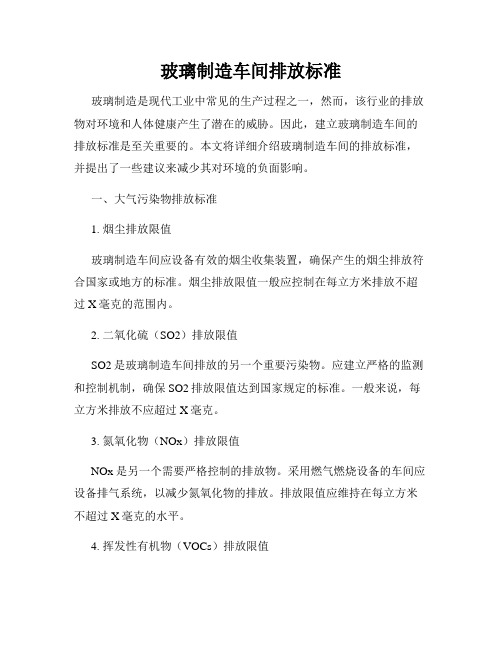
玻璃制造车间排放标准玻璃制造是现代工业中常见的生产过程之一,然而,该行业的排放物对环境和人体健康产生了潜在的威胁。
因此,建立玻璃制造车间的排放标准是至关重要的。
本文将详细介绍玻璃制造车间的排放标准,并提出了一些建议来减少其对环境的负面影响。
一、大气污染物排放标准1. 烟尘排放限值玻璃制造车间应设备有效的烟尘收集装置,确保产生的烟尘排放符合国家或地方的标准。
烟尘排放限值一般应控制在每立方米排放不超过X毫克的范围内。
2. 二氧化硫(SO2)排放限值SO2是玻璃制造车间排放的另一个重要污染物。
应建立严格的监测和控制机制,确保SO2排放限值达到国家规定的标准。
一般来说,每立方米排放不应超过X毫克。
3. 氮氧化物(NOx)排放限值NOx是另一个需要严格控制的排放物。
采用燃气燃烧设备的车间应设备排气系统,以减少氮氧化物的排放。
排放限值应维持在每立方米不超过X毫克的水平。
4. 挥发性有机物(VOCs)排放限值需要密切关注挥发性有机物的排放情况。
对于玻璃制造车间,特别是在有机溶剂使用情况下,应采取措施降低VOCs的排放。
排放限值的确定应基于国家或地方的相关标准。
二、废水排放标准1. 总氮(TN)和总磷(TP)排放限值玻璃制造车间的废水通常含有大量的氮和磷。
因此,应设备废水处理系统,确保排放的总氮和总磷含量在国家规定的限值范围内。
一般而言,总氮排放限值应控制在X毫克/升以内,总磷排放限值应控制在X毫克/升以内。
2. 悬浮物(SS)排放限值玻璃制造车间的废水中通常含有较高的悬浮物浓度。
必须采取适当的措施和处理设备,以控制悬浮物的排放限值。
排放限值建议维持在每升不超过X毫克的水平。
3. pH值和化学需氧量(COD)排放限值废水排放的pH值和COD含量对环境产生显著影响。
应确保排放的pH值在国家规定的范围内,建议维持在X到X之间。
同时,COD排放限值应控制在X毫克/升以下。
三、噪声排放标准1. 车间噪声限制玻璃制造车间通常存在高噪声环境。
玻璃的原料
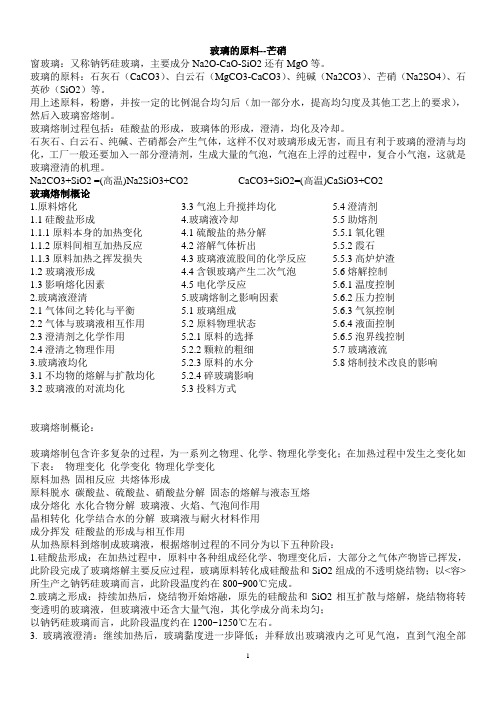
玻璃的原料--芒硝窗玻璃:又称钠钙硅玻璃,主要成分Na2O-CaO-SiO2还有MgO等。
玻璃的原料:石灰石(CaCO3)、白云石(MgCO3-CaCO3)、纯碱(Na2CO3)、芒硝(Na2SO4)、石英砂(SiO2)等。
用上述原料,粉磨,并按一定的比例混合均匀后(加一部分水,提高均匀度及其他工艺上的要求),然后入玻璃窑熔制。
玻璃熔制过程包括:硅酸盐的形成,玻璃体的形成,澄清,均化及冷却。
石灰石、白云石、纯碱、芒硝都会产生气体,这样不仅对玻璃形成无害,而且有利于玻璃的澄清与均化,工厂一般还要加入一部分澄清剂,生成大量的气泡,气泡在上浮的过程中,复合小气泡,这就是玻璃澄清的机理。
Na2CO3+SiO2 =(高温)Na2SiO3+CO2 CaCO3+SiO2=(高温)CaSiO3+CO2玻璃熔制概论1.原料熔化1.1硅酸盐形成1.1.1原料本身的加热变化1.1.2原料间相互加热反应1.1.3原料加热之挥发损失1.2玻璃液形成1.3影响熔化因素2.玻璃液澄清2.1气体间之转化与平衡2.2气体与玻璃液相互作用2.3澄清剂之化学作用2.4澄清之物理作用3.玻璃液均化3.1不均物的熔解与扩散均化3.2玻璃液的对流均化3.3气泡上升搅拌均化4.玻璃液冷却4.1硫酸盐的热分解4.2溶解气体析出4.3玻璃液流股间的化学反应4.4含钡玻璃产生二次气泡4.5电化学反应5.玻璃熔制之影响因素5.1玻璃组成5.2原料物理状态5.2.1原料的选择5.2.2颗粒的粗细5.2.3原料的水分5.2.4碎玻璃影响5.3投料方式5.4澄清剂5.5助熔剂5.5.1氧化锂5.5.2霞石5.5.3高炉炉渣5.6熔解控制5.6.1温度控制5.6.2压力控制5.6.3气氛控制5.6.4液面控制5.6.5泡界线控制5.7玻璃液流5.8熔制技术改良的影响玻璃熔制概论:玻璃熔制包含许多复杂的过程,为一系列之物理、化学、物理化学变化;在加热过程中发生之变化如下表:物理变化化学变化物理化学变化原料加热固相反应共熔体形成原料脱水碳酸盐、硫酸盐、硝酸盐分解固态的熔解与液态互熔成分熔化水化合物分解玻璃液、火焰、气泡间作用晶相转化化学结合水的分解玻璃液与耐火材料作用成分挥发硅酸盐的形成与相互作用从加热原料到熔制成玻璃液,根据熔制过程的不同分为以下五种阶段:1.硅酸盐形成:在加热过程中,原料中各种组成经化学、物理变化后,大部分之气体产物皆已挥发,此阶段完成了玻璃熔解主要反应过程,玻璃原料转化成硅酸盐和SiO2组成的不透明烧结物;以<容>所生产之钠钙硅玻璃而言,此阶段温度约在800~900℃完成。
玻璃原料及配合料COD值测定中问题探讨

作者简介 :李欣 ( 1 9 7 7 -),男 ,河北省南玻玻璃有限公司 ,化验主管 ,研究方向 : 化学 。
r 1 n n —c × ( 一 )  ̄ 3 . 0 0 3  ̄ 1 0 0 0
C 一 一 — —
晰
按 照 以上 内容操作 ,实测 检测结果 ,重复性限达不 到5 %。经 查 阅资料 和实验 验证 ,问题及 探讨解 决办 法
如下 :
1 . 硫酸 亚铁铵标准滴定 溶液不稳定 ,浓度随时 间变 化 。采取措 施 :配制完成 的溶液 ,加入少 量铝片 ,可使 溶液保 持浓度稳定 ;使 用前吸取清 液标定 ,现用现 标。 如不使 用铝片 ,硫酸亚铁 铵溶液浓度 变化很快 ,当天标 定完成 ,第 二天再次标 定 ,浓度 即发 生变化 。铝片 能起 到很好 的保护作用 。 2 . 滴 定误 差。玻璃 行业 原料及 配合料 C O D值均 处 于5 0 0以下 ,采用 原方法无 法满足重复性 限要求 。经 多 次试 验 ,待测 样 品 C O D e 值约 5 0 0以下 ,采取措 施 :减 小 重铬 酸 钾溶 液 浓度 ,减 小硫 酸 亚铁 铵 溶液 浓 度 ,符 合样 品低 C O D的特点 ,也能 满足 重复 性 限 的要 求 。改 变 的试 验 条 件 为 ,重铬 酸 钾 标 准溶 液 C ( 1 / 6 k C r 2 0 ) 0 . 0 5 m o l / L , 硫酸亚铁铵标准滴定溶液 c 【 ( N H 4 ) 2 F e ( S O )
称取 2 g 试样 , ,精 确 至 0 . 0 0 0 1 g ,置 于 2 5 0 mL蒸 馏 锥形烧瓶 中 。加入 0 . 1 g 硫 酸汞 ,加入 2 0 . 0 m L水 , 摇匀。 移人 1 0 m L重 铬酸钾标准溶液 ,摇 匀 ,再缓慢加入 3 0 m L 硫 酸一硫 酸银溶液 ,摇匀 。 将 锥 形蒸 馏 烧 瓶置 于 调 温 电炉 上 ,接 蛇形 冷 凝 回 流 管 下端 ,冷 凝 回流管 上 口用橡 胶 塞 塞 紧 ,加 热 至 沸 腾 。 自溶液 开始沸 腾时计 时 ,保持微 沸状态 ( 1 2 0±5 ) m i n 。 停止加 热 , 戴上 线手套 , 松开冷凝管下端 , 稍 留缝 隙 , 用4 0 m L水 自冷凝 管上 端 冲洗 冷凝 管 内壁 后 ,取 下锥 形 瓶 ,再 用水 冲洗烧瓶 内壁 ,稀 释至 1 4 0 mL 。水 浴冷却 至 室 温 ,加入 3 滴试 亚铁灵 指示剂 ,用硫酸 亚铁铵标 准溶 液滴定 ,溶液 的颜 色 由黄色经蓝绿 色刚变 为红褐色为 终 点。 同时进行 空 白试验 ,采用与试 样测定 完全相 同的分 析步骤 、器皿 、试剂和用量 ,平行操作 。 三 、结果计算 : 试样 C O D C值 ,单位为毫克 每千克 ( m g / k g ),按以 下公式计 算
玻璃用原材料控制标准
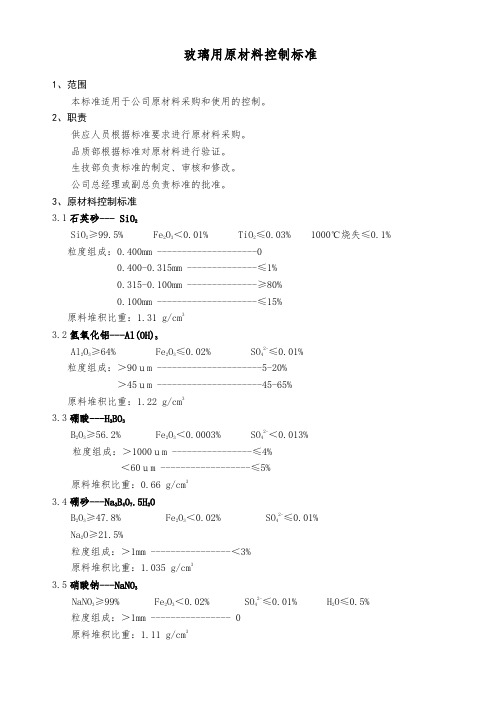
玻璃用原材料控制标准1、范围本标准适用于公司原材料采购和使用的控制。
2、职责供应人员根据标准要求进行原材料采购。
品质部根据标准对原材料进行验证。
生技部负责标准的制定、审核和修改。
公司总经理或副总负责标准的批准。
3、原材料控制标准3.1石英砂--- SiO2SiO2≥99.5% Fe2O3<0.01% TiO2≤0.03% 1000℃烧失≤0.1%粒度组成:0.400mm --------------------00.400-0.315mm --------------≤1%0.315-0.100mm --------------≥80%0.100mm --------------------≤15%原料堆积比重:1.31 g/cm33.2氢氧化铝---Al(OH)3Al2O3≥64% Fe2O3≤0.02% SO42-≤0.01%粒度组成:>90um ---------------------5-20% >45um ---------------------45-65% 原料堆积比重:1.22 g/cm33.3硼酸---H3BO3B 2O3≥56.2% Fe2O3<0.0003% SO42-<0.013%粒度组成:>1000um ----------------≤4% <60um ------------------≤5% 原料堆积比重:0.66 g/cm33.4硼砂---Na2B4O7.5H2OB 2O3≥47.8% Fe2O3<0.02% SO42-≤0.01%Na2O≥21.5%粒度组成:>1mm ----------------<3% 原料堆积比重:1.035 g/cm33.5硝酸钠---NaNO3NaNO3≥99% Fe2O3<0.02% SO42-≤0.01% H2O≤0.5%粒度组成:>1mm ---------------- 0 原料堆积比重:1.11 g/cm33.6氯化钠---NaClNaCl≥98.5% Fe2O3<0.02% H2O≤0.1%粒度组成:>1mm ---------------- 0 原料堆积比重:0.985 g/cm33.7碳酸钾---K2CO3K 2CO3≥98.8% Fe2O3<0.001% SO42-≤0.05%粒度组成:>1mm ---------------- 0原料堆积比重:1.31 g/cm34、采购和使用4.1严格按原材料控制标准进行采购和使用。
混酸消解法测定浮法玻璃原料COD值

10为解决世界性的能源短缺与环境污染的问题,全氧燃烧技术的开发与应用已经迫在眉睫。
在全氧燃烧条件下,其燃烧产物的成分、性质已经发生了比较明显的变化,浮法玻璃生产中的氧化还原数(REDOX)必须进行相应的调整。
玻璃原料的COD迅速、准确测定是进行玻璃熔体REDOX控制的基础。
因此研究适合玻璃原料COD值的测定方法具有十分重要和现实的意义。
浮法玻璃原料的COD值是指用C当量(×)表示的各种原料中所含还原性物质的量,通常,其测试方法是借用水质化学需氧量(COD)测定所采用的重铬酸钾回流法(GB11914-89,以下简称标准法)。
这种方法测试结果准确,但耗时长、成本高、二次污染大,已越来越不适应现代工业高效、节能和可持续发展的要求。
混酸消解法是利用一定比例的硫酸和磷酸混酸代替标准法中的浓硫酸,在较短时间内达到消解目的的快速测定水质COD的方法,具有耗时短、实验成本低、简单易行,易于推广等特点。
但是,有关混酸消解法测定玻璃原料COD的文献目前还未见报道。
基于此,本文以标准法测定结果为参照,根据各种浮法玻璃原料的特点,探讨了混酸法测定浮法玻璃原料COD的影响因素和最佳实验条件,旨在为准确控制浮法玻璃熔体的REDOX提供计算基础。
10-[1-4][5][6]6混酸消解法测定浮法玻璃原料COD值李豫梅刘小青许亚文张开谢峻林(武汉理工大学硅酸盐材料教育部重点实验室武汉市430070)minmin摘要关键词中图分类号:TQ171文献标识码:A文章编号:1003-1987(2009)03-0010-0为提高浮法玻璃原料化学需氧量(COD)的测定效率,研究了混酸消解法测定浮法玻璃原料COD值的影响因素和最佳实验条件。
根据原料的物质组成、加工工艺及其在酸性水溶液中溶解能力的不同,浮法玻璃原料可分为易溶的化工原料、难溶的钙质矿物原料和难溶的硅质矿物原料三种类型。
利用正交实验研究了不同原料种类、不同的硫酸和磷酸比例及其不同加入顺序、不同混酸消解时间等三种因素对混酸消解法测定COD值实验结果的影响,结合平行实验得到了混酸消解法测定不同类型原料COD值的最佳实验条件。
玻璃配料工技术等级考核应知应会试题、参考答案(完整版)

玻璃配料工技术等级考核应知应会试题及参考答案一、应知A、名词解释:1、玻璃成份:是指构成各种氧化物及其配比,它是决定玻璃的物理、化学性质的重要因素。
2、辅助原料:能够改善玻璃的熔化、澄清等工艺性能和玻璃制品的物化性质的原料。
3、主要原料:是形成玻璃结构主体原料,它们决定着玻璃的基本物理、化学性质。
这些原料熔融及反应后,即生成硅酸盐结构,成为玻璃液的主体。
4、助熔剂:在一定玻璃组成中,加入某些少量原料后,不改变玻璃组成或改变的非常少,然而由于这些原料的引入加速了熔制的效果,这种原料称为助熔剂。
5、玻璃的密度:表示玻璃单位体积的质量。
常用单位是g/Cm3。
6、物料容重:单位容积内所容纳的物料的重量称为物料容重。
常用单位为吨/米3。
7、休止角:粉料经小孔连续地下落到平面上时,堆积成的锥体母线与水平面的夹角(也称静止角,堆积)8、筛分:利用具有一定大小孔径的两面,将粉料按其颗粒大小不同,分为若干级别的过程。
9、安全电压:是防止触电事故的基本措施之一,是低压电气安装方面的应该准值。
10、产品质量:是产品满足使用要求所具有的特性即适用性。
11、浮法工艺:它的生产过程是将熔融好的玻璃液通过流槽连续地流入充满锡液的锡槽内,在重力和表面张力的作用下,使玻璃液自动摊平,在拉边机及其它的附属设备的帮助下的成型生产工艺。
12、粉碎比:粉碎前料块的粒度直径与粉碎后的料块粒度直径之比。
即i=d前/d后。
13、粘度:也就是物质的内摩擦力。
14、比表面积:单位重量粉料的总表面积。
15、筛分效率:是指筛下产品中某级颗粒重与入筛原料中同一级颗粒重量之比。
16、澄清剂:往玻璃配合料或玻璃熔体中加入一种高温时本身能气化或分解出气体,以促进排除玻璃中气泡的物质。
17、气力输送:以空气作为动力,应用于粉料的输送,有吸入式和互送式两种方法。
18、空气过剩系数:燃料燃烧时实际助燃空气的供给量和燃料完全燃烧理论需要空气量的比值。
19、反混合:指粒子具有某些特殊性能,而优先占据系统中的基本部位。
玻璃原料、配合料COD值测定检验规程

玻璃原料、配合料COD值测定检验规程1、适用范围:适用于玻璃原料、配合料等的氧化还原值的测定。
2、实验原理:在试样中加入一定量的重铬酸钾标准溶液,并在强酸介质下用银盐作催化剂,经沸腾回流后,以试亚铁灵做指示剂,用硫酸亚铁铵标准滴定液滴定试样中未被还原的重铬酸钾,由消耗的硫酸亚铁铵的量算出样品中还原物质的量。
3、剂:3.1、硫酸银:化学纯;3.2、硫酸汞:化学纯;3.3、硫酸:密度1.84g∕ml;3.4、硫酸银——硫酸溶液:向1L浓硫酸中加入10g硫酸银,放置1~2天使之溶解并混匀,使用前小心摇动;3.5、重铬酸钾标准溶液c(K2C r2O7)=0.25mol/L,准确称取在105℃干燥2h的重铬酸钾(12.258±0.0005g),溶于水中,移入1000ml容量瓶中,用水稀释至刻度,摇匀。
3.6、硫酸亚铁铵标准滴定液:称取50~60g硫酸亚铁铵【(NH4)2Fe(SO4)26H2O】溶于500ml水中,边搅拌边加入20ml浓硫酸,使其溶解,冷却,移入1000ml容量瓶中,用水稀释至刻度,摇匀,临用前须用重铬酸钾标准溶液进行标定;标定:准确吸取10.00ml重铬酸钾标准溶液于锥形瓶中,用水稀释至约80ml,加入30ml 硫酸,混匀,冷却后加3滴试亚铁灵指示剂,用硫酸亚铁铵滴定至溶液由黄色经蓝绿色刚变为红褐色为终点。
硫酸亚铁铵标准滴定溶液的实际浓度c(mol/l)按式(1)计算:C=式中:V1——吸取重铬酸钾标准溶液的体积,ml;V——消耗硫酸亚铁铵标准溶液滴定溶液的体积,ml;0.25——重铬酸钾标准溶液的浓度,mol/l。
3.7、试亚铁灵指示剂:称取1.5g领菲罗啉,0.7g硫酸亚铁溶于水中,稀释至100ml,贮存于棕色试瓶中;3.8、流装置:带有24号标准磨口的250nl锥形瓶的全玻璃回流装置。
回流冷凝管长度为300-500mm;3.9、热装置;3.10、常用实验室仪器。
4、分析步骤称取1-2g试样,精确至0.0001g,置于250ml锥形瓶中。
玻璃制品行业废水排放标准

玻璃制品行业废水排放标准一、水污染物排放浓度限值玻璃制品行业废水排放应符合国家或地方制定的水污染物排放标准。
其中,主要的控制项目包括化学需氧量(COD)、生化需氧量(BOD)、悬浮物、动植物油、石油类、阴离子表面活性剂、氨氮、总磷、氟化物等。
各控制项目的排放浓度限值应符合相关标准要求。
二、水污染物排放流量限值玻璃制品行业的废水排放还应符合水污染物排放流量的限值。
在特定的单位时间内,废水排放的流量应控制在一定的范围内。
流量限值应根据行业特点和地方环保要求制定,确保废水排放符合环境保护的要求。
三、水污染物排放去向要求玻璃制品行业废水排放的去向应符合相关规定。
一般来说,废水应排入专门的污水处理设施进行处理,或者排入公共污水处理系统。
未经处理或未达到排放标准的废水不得直接排放到自然水体中。
四、水污染物排放时间要求玻璃制品行业废水排放的时间应符合相关规定。
一般来说,废水应连续排放,且排放时间应避开用水高峰期。
在特殊情况下,如设备检修、生产故障等,废水排放应提前申报并按照应急预案进行处理。
五、废水处理设施要求玻璃制品企业应配备合适的废水处理设施,确保废水在排放前得到有效处理。
设施应按照环保要求进行设计、安装和运行,确保其处理能力与生产能力相匹配,并定期进行维护和检修。
六、废水监测要求玻璃制品企业应建立废水监测制度,对废水排放进行定期或实时监测。
监测项目应包括主要污染物浓度、流量、pH值等指标,以及时掌握废水排放状况并采取相应措施。
同时,应按照要求向相关部门报送监测数据。
七、环保管理要求玻璃制品企业应建立完善的环保管理体系,明确各级管理人员在废水排放方面的职责。
应制定废水处理方案和应急预案,加强员工培训,提高全体员工的环保意识和技能水平。
同时,应定期对废水处理设施进行检查和维护,确保其正常运行。
八、违规处罚要求对于违反废水排放标准的玻璃制品企业,应按照相关法律法规进行处罚。
处罚措施包括罚款、责令停产整顿等。
对于多次违规的企业,应加大处罚力度,确保其遵守环保法规。
玻璃原料及混合料质量的精确控制 (2)

玻璃原料及混合料质量的精确控制在玻璃生产过程中,各工序之间连续性很强,环环相扣,互相制约,彼此影响很大。
在原料的管理,原料加工和配合料制备过程中的细小错误都可能造成生产的不稳定,甚至酿成大的生产事故。
多年来根据生产实践总结出的玻璃生产的“大四稳”——原料稳、燃料稳、熔化稳、成型稳,其中原料稳列为前提,做为玻璃生产的基础稳。
在近几年新上生产线中,由于科学技术的发展,自动化程序和设备性能的进步,使混合料的控制水平已有了大幅度的提高。
在配合料制备过程中其称量系统和调合系统的关键部位多数引进了进口设备,装备水平有了大幅度的提高,对于减少成分波动提高混合料质量方面已有了相当大的改观。
但目前在原料生产工艺中,其质量控制和检测手段仍有不少的问题,离优质玻璃的生产要求有一定的差距,常常造成玻璃生产的不稳定,导致出现气泡、夹杂物等玻璃的质量缺陷,同时也对熔化率和窑龄产生直接影响。
有些先进企业在制定原料标准方面,内容与国家标准相当,但指标略高于国家标准,有的还增加了国家标准没有的要求。
通过精确控制玻璃原料及混合料的质量,努力创建自己的品牌产品,提高市场竞争力,最大限度的提高企业的经济效益。
1、做好原料进厂的质量控制工艺部门加强对矿点的加工工艺指导和质量检查。
定期到矿点了解矿山变化情况,从源头上控制进厂原料质量。
认真对原料的成分、水分、粒度、成分均匀性、难熔重矿物的检验,严格按质量标准进行控制。
为了把好合格原料进厂关,玻璃企业有的派人常驻矿山进行质量管理及把关。
多数只在厂内对进厂原料通过外观检查、化验分析进行质最把关。
但在检查把关时只对原料的成分、水分、粒度进行检验和对外观有无明显污染进行检查,各工厂对以上检验方法都比较熟悉和重视。
但一般对原料的成分均匀性、难熔重矿物的含量不进行检查与检验。
如果一批料出现成分不均匀,波动大,容易造成玻璃生产的不稳定。
如果难熔重矿物含量、粒度超过标准要求时,玻璃板面会出现严重夹杂物,且原因不易查找。
配合料的cod值不同对玻璃熔化质量的影响

COD值代表原料的化学需氧量。各种玻璃原
项 目 资 助 :国家 重:兰 静 (1 9 8 9 - ) , 工 程 师 ,主要从事电子玻璃料方研发与检测研究。 通 讯 作 者 :曾 召 (1 9 8 6 - ) , 工 程 师 ,主要从事电子玻璃产品研发与检测技术。
C0 2+ H20
(1)
K2Cr20 7+ ( NH4) 2F e ( S0 4) 2+ H2S0 4— >
K2S0 4+ Cr2 ( S0 4) 3+ Fe2 ( S0 4) 3+ ( NH4) 2S0 4+
关 [1]。因此,在玻璃组成及熔制工艺温度不变的 前提 下 ,炉内气氛的组成及压力,即炉内氧化还 原气氛的控制非常重要,原料或者窑炉的氧化还 原性发生波动都会影响玻璃液的熔化、澄清和均 化 ,从而影响玻璃质量。因此,可以通过测定配 合料的氧化还原指数,并辅以对窑炉氧化还原气 氛的控制来提高玻璃的气泡品质。
的重铬酸钾标准溶液,并在强酸介质下用银盐作
催化剂,经沸腾回流后,原 材 料 (含 碳 物 质 )中
的 碳 被 重 铬 酸 钾 氧 化 ,而重铬酸钾中的一部分
Cr6+被还原为Cr3+。用硫酸亚铁铵标准滴定液滴定
试样中未被还原的重铬酸钾,溶液的颜色由黄色
经蓝绿色变为红褐色为终点;由消耗的硫酸亚铁
铵的量算出第一步未消耗的重铬酸钾的量,再由
Effect of COD of Glass Batches on the Melting Quality of Glass LANJing1,ZENGZhao1,WANGDacheng1,YANGZhi2, WEIMinsheng2, KONGLingxin1
现代玻璃生产对玻璃原料的要求

现代玻璃生产对玻璃原料的要求《现代玻璃生产对玻璃原料的要求》之氧化还原性章节现代玻璃生产对玻璃原料的要求玻璃原料的成份控制、粒度控制和COD(化学氧需要量)值控制是高效、优质和低耗熔制玻璃的三要素。
玻璃原料的成份控制对于玻璃原料,不仅要求它的有效氧化物的含量高,有害杂质少,难熔重金属氧化物的含量极少,更重要的是氧化物含量的波动要小。
现代化自动称量系统不能分辨原料中氧化物的变化,因此即使原料称量再准,若其氧化物含量变化很大,熔制出的玻璃的成份仍会波动。
所以,必须严格控制进厂的玻璃原料的成分,使它的波动控制在工艺上允许的波动范围内。
下表是国际上目前推荐的玻璃原料成分控制界限,主要是对平板、瓶罐、器皿玻璃等钠钙硅酸盐玻璃。
推荐的钠钙硅酸盐玻璃用主要天然玻璃原料的成分控制界限表原料名称氧化物边界值(%)允差(%)砂子 S iO2 ≥±Al2O3 <±Fe2O3 <±白云石酸不溶物<±Al2O3 <±Fe2O3 <±石灰石酸不溶物<1 ±Al2O3 <±Fe2O3 <±长石Al2O3 ≈±Fe2O3 <±Na(K)2O ≈10±边界值数据下降,意味着杂质含水量增多,更重要的是意味着有效氧化物的允差变大。
表中所列数据与我国许多玻璃工厂的实际情况相差悬殊,但这毕竟是努力目标,说明要想提高熔化率,这是不可忽视的环节。
有的原料虽然在有效氧化物的含量和波动方面都比较满意,但是含有过量的难熔重矿物(简称RHM),这种原料也不能算是满意的,甚至根本不能用。
因为难熔重矿物在熔制玻璃过程中极难熔解,残留在成品玻璃中形成玻璃缺陷。
下表是主要玻璃原料中常见的难熔重矿物名称。
一些主要玻璃原料中常见的难熔重矿物原料名称难熔重矿物的名称砂子硅线石兰晶石红线石锆英石尖晶石刚玉铬铁矿高岭土石灰石刚玉尖晶石铬铁矿白云石刚玉尖晶石铬铁矿长石硅线石刚玉锆英石铬铁矿尖晶石锡石蛇纹绿柱石这些难熔重矿物的粒子愈大,完整地通过熔窑的机会就愈多。
浮法玻璃原料cod值测定在生产中的应用

浮法玻璃是世界上应用最广泛的玻璃生产工艺之一,其制备工艺对原料的质量要求极高。
在浮法玻璃原料的生产过程中,COD值测定是一项非常重要的质量控制指标。
本文将从浮法玻璃的生产工艺、原料质量要求和COD值测定的应用等方面进行全面探讨,以帮助读者更深入地了解浮法玻璃原料COD值测定在生产中的应用。
一、浮法玻璃的生产工艺浮法玻璃是一种通过在熔融锡水面上浮铸玻璃带,使玻璃带具有均匀厚度和平整表面的工艺。
这种工艺制备的玻璃广泛用于建筑、家具、家电等领域。
在浮法玻璃的生产过程中,原料的质量对产品的质量起着决定性的作用,而COD值则是评价原料质量的重要参数之一。
二、原料质量要求在浮法玻璃的生产中,主要的原料包括石英砂、碳酸钠、石灰石等。
这些原料的质量对玻璃的成色、透明度、力学性能等都有着重要影响。
其中,有机物质的含量对玻璃的质量影响尤为显著,而COD值正是用来评价原料中有机物质含量的重要指标。
三、COD值测定在生产中的应用1. 样品的制备在进行COD值测定时,首先需要将原料样品进行制备。
通常情况下,取一定量的原料样品,将其溶解或者进行适当的预处理,使有机物质充分释放出来,从而便于后续的COD值测定。
2. 测定方法测定COD值的方法有多种,常用的包括高温炼句法和紫外光催化氧化法等。
根据实际情况选择合适的测定方法,进行测定工作。
3. 结果分析根据测定得到的COD值,可以对原料的质量进行评估。
有机物质含量高的原料会对玻璃的质量造成负面影响,因此及时了解原料的COD值是非常重要的。
四、总结与展望通过本文的介绍,相信读者对浮法玻璃原料COD值测定在生产中的应用有了更深入的了解。
在未来的生产实践中,我们应该更加重视原料的质量控制,确保原料符合要求,从而生产出更加优质的浮法玻璃产品。
我们也希望在COD值测定方面能够有更多的创新和突破,使其在生产实践中发挥出更大的作用。
个人观点和理解作为一名从事玻璃生产工作多年的专业人士,我深知原料的质量对产品质量的重要性。
“碳粉”在玻璃生产中的作用

“碳粉”在玻璃生产中的作用国玻璃"碳粉''在玻璃生产中的作用段谦25——中国建材国际工程有限公司广东深圳518054摘要:本文通过实际发生的生产实例.重新阐述了碳粉对玻璃生产的影响机理,从另一个角度进一步说明了碳粉在玻璃生产中的作用,对实际生产可以起到很好的指导作用.关簟词:澄清刺;还原荆;玻璃澄清和均化ApplicationofcarbonpowderinglassproductionDuanOianChinaTriumphInternationalEngineeringCo.,LtdShenzhenGuangdong518054 Abstract:Thispaperexpoundstheinfluencemechanismofcarbonpowderinglassproductio nbasedonactualproductionexamples,andfurtherexplainsthefunctionofcarbonpowderinglassproduction,so髂toprovidetheguidanceforactualproduction.Keywords:refiningagent;t~lucingagent;glassrefiningandhomogenizingl实例介绍某浮法玻璃厂在2000年,曾出现过一起罕见的,造成连续一个多月生产不出合格成品玻璃的生产质量事故,这起事故起初的情况表现为,位于窑内泡界线前端的料堆熔化变缓慢,难熔,致使泡界线后5小结移;整个窑内火焰空间呈暗黑状,而成品玻璃板表面则出现许多熔融或未熔石英疙瘩.类似情况之前在该厂也曾出现过,当时的处理措施是直接降低配料中的硅砂用量,以减轻熔化难的现象.因此出现这种状况后,值班经理凭直觉认为可以采取同样的方式处理,于是当即通知当班配采用库尔曼图解法计算主动土压力时,选定的任意破坏面越密,墙后土体被分割的越多,得到的主动土压力越准确.采用库尔曼图解法确定了墙后土体的实际破坏面后,应根据理论力学中质心运动定理求解破坏土体的质心;同样在计算挡墙各部分重心到墙趾板顶点C的距离x时,也须运用质心运动定理求解.计算挡墙的抗倾覆,抗滑移系数时必须使用荷载标准值,配筋计算中必须使用设计值.在初步设计时,玻璃厂家一般总是要求扶壁设置在挡墙的外侧这样可以使挡墙内部有足够的使用空间,但这种做法会使挡墙的造价大大增加.而把扶壁设置在内侧,利用扶壁式挡墙的墙板作为挡墙计算单元的受压翼缘可使挡墙扶壁的纵向受拉钢筋大大减小,从而降低结构造价,虽然牺牲了部分使用空间,但仍可满足使用要求.为使扶壁柱的纵向配筋有一定的安全储备,将挡墙扶壁的受压翼缘取为2m.初步设计时,挡墙基底采用直线式底面,利用抗滑键来满足抗滑移要求,考虑到现场施工的方便与经济,改用仰角式底面,利用竖向力的分力平衡部分水平土压力的分力,由于竖向力较大,故仰角在不太大的情况下即可满足设计要求.施工开挖要求开挖到仰角最低点,超挖部分采用C20素混凝土回填至设计标高,这样可使施工更加的方便快捷.关于墙踵板的配筋计算,只是近似认为如图5所示,按最不利情况初步估算出踵板在一个方向的一种配筋,考虑到整个底板的共同工作,尤其在扶壁范围内的底板,在工程实际中近似将其视为通体梁设置其配筋,在满足计算及构造配筋的前提下,使底板的配筋能够具有一定的安全系数.挡墙下地基处理采用水泥粉煤灰碎石桩法(CFG),是当地较常用的一种地基处理方法,按《建筑地基处理技术规范》JGJ79—2002要求必须设计出具体桩的排列形式,桩身的直径以及桩的长度,当地的专业施工单位只要求提供地基土的处理范围及复合地基承载力特征值,其余均由施工单位自行解决.国玻璃料降低硅砂用量2千克/每副,但第二天,窑内情况并没有像预期的那样好转.随即又在白班继续降低硅砂用量,同时在熔制工艺上做了一系列调整,包括提高熔制温度等手段,然而窑内情况仍未见好转.又连续数天分数次降低硅砂用量累计达十几公斤,但生产形势仍然未见改观,观察窑内的气氛和火焰空间依然是阴沉沉的,并且奇怪的是,在连续降低硅砂用量的情况下,x荧光仪检测出的玻璃成分SiO含量仍然居高,远高于配方值,这种怪异现象非常令人费解,于是将玻璃表面磨去一层,通过检测发现,玻璃内部SiO含量比其表层要低得多,且接近降低硅砂用量后的料方值,这种状况持续影响生产一个多月,成品率降到了前所未有的程度.在此情况下,厂领导动员所有的工艺技术人员下到车间,对生产工序进行彻底排查,寻找原因.笔者作为原料工艺技术人员,主要对原料车间的工序进行排查.在连续数天的排查中,对配料的误差和原料成分等生产报表及化验数据进行详细分析,均未发现异常情况.后通过与配料操作人员的深入交谈,他们反映的一个情况引起了笔者的重视, 他们反映最近一段时期以来,配合料在混合机排料斗堵塞的情况频繁发生,这是以前很少出现的.再观察配合料的外观,笔者发现颜色明显比以往更深, 然而配合料化验的数据却均为正常.接着从原料库取样发现,硅砂的颜色同样比以往的硅砂颜色明显偏黑.据此笔者大胆提出了一种观点,即可能硅砂原料中带人的可烧失杂质增加,从而变相的增加了碳粉用量的看法,并建议对目前使用的原料和以往使用原料进行烧失量对比.实验室对比结果表明,目前使用的硅砂原料的烧失量是以往使用硅砂原料的烧失量的2倍.与此同时,热端技术人员的技术分析,也从前期的工艺调整记录中,发现在一个多月以前,为了进一步减少玻璃中的微气泡,曾多次增加配合料中碳粉的用量.针对这一情况,工艺人员查阅了有关技术书资料,通过反复多次技术分析论证,症结逐渐显露.紧接着在当天中班开始配料时,有点放矢的调低配方中的碳粉含量.根据时间推算,当天中班调整后的配合料应该在5—6h后开始进入窑炉.于是进行跟踪观察,从当天晚二十时开始,调整后的配合2oo9军曩5用__——_-——_一料进入窑内,大约在零时窑内情况即逐渐开始了好转,到凌晨一时左右,窑内的状况开始了明显的变好,熔化变得剧烈,料堆熔化加快,泡界线开始前移, 并且窑内气氛逐渐变得明亮起来.调料后窑内情况变化之快,出乎所有人的预料,至当天夜班后期,玻璃板质量逐步恢复正常,并开始玻璃正常采板装箱, 至第二天白班,生产已完全恢复正常.2碳粉作用机理分析众所周知,玻璃配合料中加入少量芒硝,主要是作为高温澄清剂使用的.这在现有的专业理论书籍中早已阐述过,即芒硝的热分解温度通常较高,为1120~1220~C,其在还原剂的作用下,分解温度可降到了500~700't2.因此,还原剂用量的多少,对玻璃生产将产生不同的影响,当用量不足时,NaaSO4不能充分分解,会产生过量的"硝水",对熔炉耐火材料的侵蚀加大,并使玻璃产生白色的芒硝泡;当用量过多时,会使玻璃中的FeO还原成FeS和Fe2S3,与多硫化钠反应形成棕色的着色团一硫铁化钠,从而使玻璃呈现棕色.在熔制纯碱一芒硝配合料时,通常为了芒硝得到完全分解,熔化部内需要保持还原气氛,而在最后的小炉区域,即澄清部又必须维持氧化焰,以烧掉过剩的碳粉.但上述理论应用到本文案例中,就很难得到科学合理的解释.因此,随着玻璃生产过程中新情况新问题的不断出现,对玻璃熔制的理论需要进一步完善.具体就芒硝与碳粉对玻璃生产的作用需要进一步诠释. 尤其当还原剂过多时,且还原剂多到在澄清部的氧化焰已不足以能烧掉过剩的碳粉时,此种情况对玻璃熔制产生的影响,在以往的理论中尚未找到准确的阐述,即使提及,也只是泛泛带过,对实际生产没有准确的指导意义.但实际生产中还原剂过多或过少对玻璃生产造成的影响远比使玻璃着色或出现"硝水"更复杂更严重的多.由本文的案例可知,当还原剂过多时,即在500—700~C时,Na2SO4已完全反应分解,其与SiOz 及其它组分反应,产生的气泡,使得其对玻璃的澄清作用提前发生;然而对于玻璃的澄清带即在1120~1400%时,真正需要对玻璃起高温澄清作用时, NaSO已经完全消耗殆尽.实际上,玻璃生产过程中最重要的反应是熔化速度最慢的石英砂颗粒的溶国玻璃臻鄹黼_-—-___●20O9军曩5翔解过程,待进行到玻璃的澄清阶段时,玻璃原料中其它组分的基本反应已大体完成.此阶段的玻璃液变成了由硅酸盐和大量游离siO:组成的不透明烧结物以及残留的未熔解SiO颗粒.在澄清段,这些游离SiO不透明烧结物和残留的未熔解SiO颗粒,本该借助未完全分解的残余NaSO在高温时分解,释放出Na和SO,,0:气体,并通过这些气体在玻璃液中的上升排出过程,带动玻璃液翻腾.硫酸盐分解排气的过程具有三个非常重要的作用:作用之一是表面活性剂作用,芒硝基本不溶于熔融钠一钙一硅玻璃,在高于永久性的初生硅酸盐液相生成温度(约1038—1093℃)时,它集聚在玻璃熔体中的所有界面上,即未熔化的配合料粒子,气泡和熔体表面本身彼此间的界面.这样,芒硝大大增加了熔体的流动性以及这些界面处的"润滑能力",使气体容易排出,是硅酸盐反应速率加快;作用二是界面湍动作用, NaSO在高温时,分解释放出Na和SO,,0气体,它们在玻璃熔体中溶解,在为分解的液态硫酸盐和玻璃之间的界面上被传输到玻璃中,这种传输搅乱了界面张力,使熔体在界面处翻腾搅拌,使得游离SiO: 不透明烧结物和未熔融石英颗粒的熔融和溶解速度加速,并且在玻璃液流表层SiO:含量高的组分获得向其它组分中加速扩散,从而使玻璃熔体得到了均化,最终得到溶质均匀的玻璃液;作用之三是排气作用,大约在1428℃时,芒硝分解的SO,0气体部分分压达到了一个大气压,在玻璃中,产生了气泡.这些气泡在上升过程中把含钠高的玻璃液传输到玻璃液上表面含钠低的玻璃液中,又进一步使玻璃得到均化,并对玻璃液起到高温澄清,排除玻璃液中的气泡;总而言之,熔窑中温度高于1428oC的澄清区,只有熔体中还有未分解的芒硝存在,才会有这3个作用对玻璃液起到澄清和均化作用.就本案例而言,由于原料中还原剂增加,使得在澄清阶段之前,芒硝已被完全分解.澄清时所需的芒硝高温澄清作用消失了,游离SiO组成的不透明烧结物和未熔融石英颗粒得不到有效的溶解,不能向其它组分的液相中有效扩撒和均化,而是浮在玻璃液流表面,这也解释了为什么上述事故发生时,玻璃板表面SiO含量远高于板内层的原因.随着生产好转,再对成品玻璃的表层和内层玻璃成分分别做x荧光仪检测,结果表明在生产正常情况下,玻璃的SiO:含量就基本上表里如一. 27——通过对上述案例分析,碳粉用量在玻璃生产中的作用非常微妙,多与少对生产都会起到很大的影响,难怪此次事件后,槽窑部的工人们戏称碳粉是玻璃生产的兴奋剂,可见其在生产中的重要性可见一斑d值得提及的是,曾经在该厂生产中,为了减少玻璃中的微气泡,人为增加碳粉的用量,造成不该发生的质量事故,是值得同行生产厂家很好地吸取经验教训的.3合理设定配合料中芒硝和碳粉的比例从本文发生的案例说明,玻璃生产必须有效,合理控制配合料中的芒硝和碳粉的比例,根据有关文献,目前国际上先进的玻璃生产厂家,是通过控制玻璃熔制过程的Redox(还原和氧化势)值来进行控制,也既是通过检测配合料中的原料含有的有机物和碳质物,这些物质相当于向配合料中引入还原剂一碳,测定方法称为玻璃原料的COD值测定法,再经过反复试验,修正,得出一系列原料的相对应的COD数值,然后通过一定的计算方法得出配合料的氧化和还原势Redox值,再对生产进行指导和调整.但目前这些具体的计算方法和如何应用还只有少数国际先进的玻璃生产厂家掌握.我国玻璃生产厂能够使用这种方法的厂家很少.而笔者认为根据本文案例,可以得到一个更简单的手段来调整芒硝和碳粉的合适比例,即根据本文案例处理过程的发现,玻璃配合料中碳粉含量越高,则浮在玻璃表面的SiO:成分含量越高,那么可以通过检测玻璃表面与里层SiO:成分含量,比较里外之间成分的差异,当里外成分基本一致时,说明芒硝和碳粉的比例是合适的;当表面成分高于里层时, 说明碳粉含量偏高,应该适当调低碳粉用量.这一手段在生产中简便易行,值得各玻璃生产厂家掌握和应用.。
玻璃调料常识
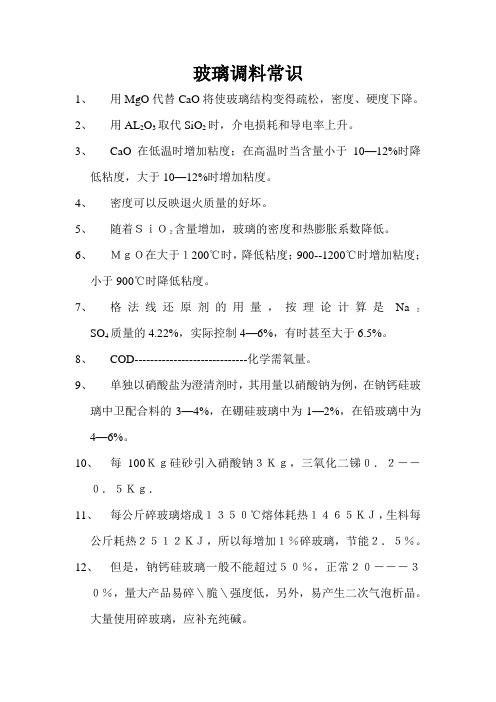
玻璃调料常识
1、用MgO代替CaO将使玻璃结构变得疏松,密度、硬度下降。
2、用AL2O3取代SiO2时,介电损耗和导电率上升。
3、CaO在低温时增加粘度;在高温时当含量小于10—12%时降
低粘度,大于10—12%时增加粘度。
4、密度可以反映退火质量的好坏。
5、随着SiO2含量增加,玻璃的密度和热膨胀系数降低。
6、MgO在大于1200℃时,降低粘度;900--1200℃时增加粘度;
小于900℃时降低粘度。
7、格法线还原剂的用量,按理论计算是Na2
SO4质量的4.22%,实际控制4—6%,有时甚至大于6.5%。
8、COD-----------------------------化学需氧量。
9、单独以硝酸盐为澄清剂时,其用量以硝酸钠为例,在钠钙硅玻
璃中卫配合料的3—4%,在硼硅玻璃中为1—2%,在铅玻璃中为4—6%。
10、每100Kg硅砂引入硝酸钠3Kg,三氧化二锑0.2――
0.5Kg.
11、每公斤碎玻璃熔成1350℃熔体耗热1465KJ,生料每
公斤耗热2512KJ,所以每增加1%碎玻璃,节能2.5%。
12、但是,钠钙硅玻璃一般不能超过50%,正常20―――3
0%,量大产品易碎\脆\强度低,另外,易产生二次气泡析晶。
大量使用碎玻璃,应补充纯碱。
玻璃原料、配合料COD值测定检验规程.

玻璃原料、配合料COD值测定检验规程1、适用范围:适用于玻璃原料、配合料等的氧化还原值的测定。
2、实验原理:在试样中加入一定量的重铬酸钾标准溶液,并在强酸介质下用银盐作催化剂,经沸腾回流后,以试亚铁灵做指示剂,用硫酸亚铁铵标准滴定液滴定试样中未被还原的重铬酸钾,由消耗的硫酸亚铁铵的量算出样品中还原物质的量。
3、剂:3.1、硫酸银:化学纯;3.2、硫酸汞:化学纯;3.3、硫酸:密度1.84g∕ml;3.4、硫酸银——硫酸溶液:向1L浓硫酸中加入10g硫酸银,放置1~2天使之溶解并混匀,使用前小心摇动;3.5、重铬酸钾标准溶液c(K2Cr2O7)=0.25mol/L,准确称取在105℃干燥2h的重铬酸钾(12.258±0.0005g),溶于水中,移入1000ml容量瓶中,用水稀释至刻度,摇匀。
3.6、硫酸亚铁铵标准滴定液:称取50~60g硫酸亚铁铵【(NH4)2Fe(SO4)26H2O】溶于500ml水中,边搅拌边加入20ml浓硫酸,使其溶解,冷却,移入1000ml容量瓶中,用水稀释至刻度,摇匀,临用前须用重铬酸钾标准溶液进行标定;标定:准确吸取10.00ml重铬酸钾标准溶液于锥形瓶中,用水稀释至约80ml,加入30ml硫酸,混匀,冷却后加3滴试亚铁灵指示剂,用硫酸亚铁铵滴定至溶液由黄色经蓝绿色刚变为红褐色为终点。
硫酸亚铁铵标准滴定溶液的实际浓度c(mol/l)按式(1)计算:C=式中:V1——吸取重铬酸钾标准溶液的体积,ml;V——消耗硫酸亚铁铵标准溶液滴定溶液的体积,ml;0.25——重铬酸钾标准溶液的浓度,mol/l。
3.7、试亚铁灵指示剂:称取1.5g领菲罗啉,0.7g硫酸亚铁溶于水中,稀释至100ml,贮存于棕色试瓶中;3.8、流装置:带有24号标准磨口的250nl锥形瓶的全玻璃回流装置。
回流冷凝管长度为300-500mm;3.9、热装置;3.10、常用实验室仪器。
4、分析步骤称取1-2g试样,精确至0.0001g,置于250ml锥形瓶中。
玻璃原料COD值的测定
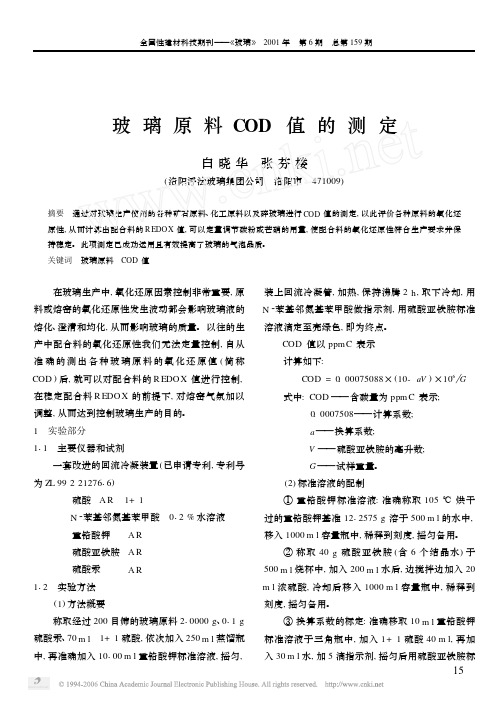
玻璃原料COD值的测定白晓华 张芬楼(洛阳浮法玻璃集团公司 洛阳市 471009)摘要 通过对玻璃生产使用的各种矿石原料、化工原料以及碎玻璃进行COD值的测定,以此评价各种原料的氧化还原性,从而计算出配合料的R EDOX值,可以定量调节碳粉或芒硝的用量,使配合料的氧化还原性符合生产要求并保持稳定。
此项测定已成功运用且有效提高了玻璃的气泡品质。
关键词 玻璃原料 COD值 在玻璃生产中,氧化还原因素控制非常重要,原料或熔窑的氧化还原性发生波动都会影响玻璃液的熔化、澄清和均化,从而影响玻璃的质量。
以往的生产中配合料的氧化还原性我们无法定量控制,自从准确的测出各种玻璃原料的氧化还原值(简称COD)后,就可以对配合料的R EDO X值进行控制,在稳定配合料R EDO X的前提下,对熔窑气氛加以调整,从而达到控制玻璃生产的目的。
1 实验部分111 主要仪器和试剂一套改进的回流冷凝装置(已申请专利,专利号为Z L9922127616) 硫酸 A R 1+1 N2苯基邻氮基苯甲酸 012%水溶液 重铬酸钾 A R 硫酸亚铁胺 A R 硫酸汞 A R112 实验方法(1)方法概要称取经过200目筛的玻璃原料210000g、011g 硫酸汞、70m l 1+1硫酸,依次加入250m l蒸馏瓶中,再准确加入10100m l重铬酸钾标准溶液,摇匀,装上回流冷凝管,加热,保持沸腾2h,取下冷却,用N2苯基邻氮基苯甲酸做指示剂,用硫酸亚铁胺标准溶液滴定至亮绿色,即为终点。
COD值以ppm C表示计算如下: COD=0.00075088×(10-aV)×106 G式中:COD——含碳量为ppm C表示;0.0007508——计算系数;a——换算系数;V——硫酸亚铁胺的毫升数;G——试样重量。
(2)标准溶液的配制①重铬酸钾标准溶液:准确称取105℃烘干过的重铬酸钾基准1212575g溶于500m l的水中,移入1000m l容量瓶中,稀释到刻度,摇匀备用。
做COD注意事项

做COD 注意事项
滴水样时消耗溶液滴定数太低,未稀释的水样进行稀释,已稀释的加大稀释倍数;稀释后的消耗溶液滴定数太高,降低稀释倍数。
做样前,必须先开水龙头,以免发生事故;做样完毕关闭水龙头。
水流大小要适中,太大容易造成管破裂,太低冷凝不好造成结果不准。
必须注意加防暴珠。
邻苯二甲酸氢钾标准溶液,理论COD值为500mg/L,如果校准实验的结果大于该值的96%(480mg/L以上),即可认为实验步骤基本上是适宜的,否则,必须寻找失败的原因,重复试验,使之达到要求。
水样要采集于玻璃瓶中,应尽快分析。
培训计划
重新培训一次COD做法,注意事项,现场看做样过程,纠正错误手法。
培训时间人员。
- 1、下载文档前请自行甄别文档内容的完整性,平台不提供额外的编辑、内容补充、找答案等附加服务。
- 2、"仅部分预览"的文档,不可在线预览部分如存在完整性等问题,可反馈申请退款(可完整预览的文档不适用该条件!)。
- 3、如文档侵犯您的权益,请联系客服反馈,我们会尽快为您处理(人工客服工作时间:9:00-18:30)。
玻璃原料的COD值控制COD值是化学氧需要量的英文缩写(Chemical Oxygen Demand)。
它的含义是各种玻璃原料中会程度不同地含有一些含碳物质,在玻璃熔制过程中,它们也和加入的碳粉一样,影响着熔窑的熔制气氛。
把这些含碳物质通过一定的测定方法并折合为ppm C量来表示,就称该测定值为COD值。
以往,在玻璃制造中,用芒硝做澄清剂时,只规定加入占芒硝用量一定百分比的碳粉,而不考虑玻璃原料也会带入碳。
有时,玻璃原料带入的碳量相当可观,如果这部分碳量不加以控制,对熔制过程很不利。
要想了解为什么要控制玻璃原料的COD值,还需要首先了解一下“还原性硫澄清”这项国际上普遍推广的新技术进展。
1.还原性硫澄清——70年代未玻璃熔制上的一项新进展。
还原性硫澄清是国际上近十几年在玻璃制备过程方面的一大进展,几乎已普遍应用于平板、器皿、医药等玻璃的生产中。
在英、美及欧洲,大多数瓶罐和器皿玻璃都已采用还原性硫澄清。
英国Pilkington玻璃公司宣布他在全世界的浮法玻璃熔窑及压延玻璃熔窑已实现了还原性硫澄清。
这项技术能显著降低熔化温度、提高窑炉产出率、改善玻璃质量和色调稳定性。
从技术上讲,它是将在玻璃熔化和澄清中的作用进行最优化的控制。
先要说明在玻璃熔化和澄清中单有硫酸盐时的作用,因为这对理解还原性硫澄清是至关重要的。
硫酸盐在玻璃熔化和澄清中的作用可概括为三条:1)表面活性剂作用硫酸盐基本上不溶于钠-钙-硅玻璃,在高于永久性的初生硅酸盐液相生成温度(约1038-1093℃)时,它集聚在玻璃熔体中的所有界面上(即未熔化的配合料粒子、气泡和熔体表面本身彼此间的界面)。
这样,硫酸盐大大增加了熔体的流动性以及这些界面处的“润湿能力”,使气体容易排出,使硅酸盐反应速率加快。
2)界面湍动作用在大于1288℃时,Na2SO4的热分解(在有玻璃存在时)开始明显。
随着分解进行,分解产物(Na2O、SO2、O2)在玻璃熔体中是熔解的,它们在未分解的液态硫酸盐和玻璃之间的界面上被传输到玻璃中。
这种物料传输扰乱了界面张力,释放出大量能量,因而使熔体在界面处产生一种剧烈的湍动作用。
这种“界面湍动”已由Bruckner在水-有机系统和玻璃熔体中都看到了并作了说明,在有机溶液中的还拍了图片。
“界面湍动”效应使没有反应的配合料粒子的溶解速率大大加快,使气泡通过熔体上升得更快(与无硫酸盐的熔体相比),玻璃也均化得更快,并且带有微区均化性质。
3)排气作用在大约1428℃时,硫酸盐分解产物的部分分压达到了一个大气压,在玻璃中产生了气泡。
这些气泡在上升过程中把钠从含钠高的玻璃区传输到熔体上部含钠低的玻璃区,又进一步使玻璃得到均化。
没有排尽而残留的气泡在玻璃冷却时又重新溶于溶体。
只要熔体中还有未分解的硫酸盐存在,熔窑中温度高于1428℃的区域,这三个作用都在同时起作用。
遗憾的是SO42-在玻璃中的溶解度比较小,(以SO3表示为0.15%到0.30%),非常少量的硫酸盐能产生大量的气泡(在玻璃熔化温度下,0.01% SO3完全分解能产生相当于玻璃熔体体积的20%上下的总气泡体积),因而,窑炉中熔化池温度高再加上硫酸盐浓度过剩时,在热点区或靠近热点区可能带来泡沫问题。
多年生产经验说明,在用硫酸盐的同时,加入一些还原性物质(最常用的是碳)可以防止形成硝水。
后来人们才发现这些还原性物质使硫酸盐反应生成一部分硫化物,正是这些硫化物使硫酸盐的澄清作用更有效。
随着研究的深化,又进一步认识到将还原性增强到一定程度,能使硫酸盐在玻璃熔化和澄清中的作用达到最佳状态。
人们将这项技术称之为“还原性硫澄清”。
硫酸盐和硫化物一起作用时对熔化的好处可以用三个方面的机理来说明:1)最主要的是Na2SO4与碱金属或碱土金属硫化物反应发生化学分解,这种分解在低得多的温度下(大约900℃)就开始了,而单独使用硫酸盐时,热分解温度大约为1288℃。
因而硫酸盐的“表面活性剂”作用和“界面湍动”作用能够在初生熔体温度(1038℃)以上时都在作用,并持续直至硫酸盐—硫化物反应完成为止。
2)硫酸盐—硫化物反应使几乎所有配合料中含有的硫在熔化过程的早期就呈SO2从熔体逸出,因而使窑炉热点处产生泡沫的可能性最小(因残留硫酸盐分解而产生),或者使后期在澄清部、料道和成型机处产生二次气泡(因玻璃的氧化态变化而产生,下面会详细讨论)的可能性最小。
3)在热台显微镜上已经看到,这些熔体上部气氛中有SO2时,对表面张力有影响,从而使上升的气泡一到达熔体表面就破裂,而不会积聚在玻璃表面形成泡沫。
Budd公布了玻璃中硫溶解度与玻璃氧化还原势的关系曲线,它能更定量地说明还原性硫澄清对提高玻璃澄清速率和防止气泡问题产生的好处。
他熔制了好些玻璃成分(每一个都含有恒定的硫和铁的总量),但氧化态不同,从高氧化到高还原(靠在配合料中加入碳或氧化铝来控制)。
然后分析玻璃总硫含量(以SO3表示),并将这些数据对每个玻璃的氧化态(以分析出的玻璃中亚铁离子和铁离子的相对量表示)作图。
Budd的这些图被综合在一起并以线性比例尺画出如下图所示。
曲线的左边表示氧化性玻璃,朝右边氧化态减弱。
在曲线最低点附近和右侧产生黄色玻璃。
图中曲线的显著特点是有一个最低点,其两侧的坡度都比较陡。
澄清最好、不易产生气泡的玻璃应落在最低点的附近,因为这些玻璃的氧化态和还原态的任意变化都会使硫溶解度增大,因而因气态硫化合物逸出而形成小气泡和气泡的机会就少。
位于近曲线左端的玻璃成分(氧化性玻璃)当向还原性偏移时会产生气泡,因为这时硫溶解度降低,位于曲线右端的玻璃(还原性玻璃)当向氧化性偏移时也会产生气泡,其理由一样;当然,这要在产生二次气泡的物理前提被满足时才成立,如有泡核存在,或气体产物有足够压力。
曲线的坡度陡(尤其是右侧),说明氧化态上只要有非常小的变化就能使硫溶解度有相当大的变化,因而也使玻璃的澄清速率和稳定性显著变化。
Budd的数据和曲线启示我们,在玻璃配合料中加入还原性化合物会使玻璃中的硫溶解度降低,也就是说,玻璃成分应朝着图中的最低值向下向右移动。
实验室和工厂的许多试验都证明了这个启示,还原性硫澄清的玻璃与相应的偏氧化性澄清相比,澄清得更快,更不易产生二次气泡。
要注意,该图的绝对值只适用于Budd所试验的玻璃成分。
玻璃中碱或铁含量的变化能大大影响亚铁—铁比值,因而曲线的绝对位置是玻璃成分的函数,但是对大多数钠钙玻璃成分而言,曲线的一般形状都是如此。
2.玻璃熔制过程的Redox数控制。
控制熔制过程中玻璃的氧化还原势态,过去往往只注意窑炉燃烧气氛的氧化还原性,忽略了加入窑炉中的配合料的氧化还原势,而后者往往起到更重要作用。
所以,也必须对后者同时进行控制。
这种控制叫做Redox数控制。
“Redox”是“Reducing & Oxydizing Potential”(氧化和还原势)的缩写。
玻璃配合料的Redox数主要由加入的氧化剂和还原剂构成,但是玻璃原料中往往含有有机物或碳质物,有时其数量相当可观,这些物质相当于向配合料中引入还原剂碳。
有一种测定方法,它将这些物质换算为当量的碳,这种测定方法称为玻璃原料的COD值测定方法。
目前国际上有两种计算Redox数的方法。
一种是英国Calumite 公司的方法,另一种是美国FMC公司的方法。
不同的方法所用的因素值也不同。
表中所列蝗是美国FMC公司所用方法的氧化—还原因素值。
这些数值的确定,最先是对一些有明显氧化、还原能力的原料,如芒硝、碳、硝酸钠、水等,指定了一些数值,然后经过反复试验、修正后,才提到如表所列数据。
这些经验数值都是以每2000lb砂为基数、引入1lb氧化剂或还原剂所取得的。
我国料单表示方法与英美有所不同,因此在实际应用这些参考数据时,要考虑这一差别。
为了叙述的方便,在下面举例中仍保留了英制单位。
表中是玻璃中常见原料的COD曲线值及变化范围。
如果以Redox数作用Budd曲线的横坐标,就可以作成如图所示的函数曲线。
图中左边的较低负数的玻璃成分被认为是氧化系统,而朝右边就更趋还原性。
对还原性硫澄清而言,最好的澄清区位于Redox值为—20到—50的范围。
玻璃熔化中常用的经验氧化—还原因素表物料氧化物料氧化1 lb芒硝 +1.01 lb石膏(. 2H2O) +0.91 lb重晶石+0.61 lb硝(NaNO3)+3.01%H2O(配合料) +4.0碎玻璃?苛性钠(NaOH)?空气/燃料比? 1 lb纯碳 -23.71 lb细媒粉-16.01 lb硫 -13.31 lb硫铁矿(FeS2) -6.51 lb萤石(CaF2) -1.81 lb食盐(NaCl) -1.01 lb氧化亚铁(FeO) -1.01 lb白砒(As2O3)?表中有?者为目前尚未确定它们的定量值。
各种玻璃原料的COD值 ppm C物料范围典型值砂子 70—270 150石灰石100—880 500海水石灰石 4000—4400 4200纯碱 20—150 75长石 100—350 260高炉炉渣 9000—12000 10000碳(煤) 590000—680000 650000芒硝(人造丝附产)70—120 100芒硝(造纸附产) 600—750 635在该范围内玻璃有低的硫含量。
低的硫溶解度能使SO2更快地逸出,因而加快了澄清速率,降低了再生泡出现的可能。
还原性硫澄清对生产的控制水平要求较高,因这它已靠近曲线的最低点,如果还原性波动达到或超过此点,玻璃将产生黄色条带。