晶间腐蚀试验报告
M3307 用于1、2、3级设备的奥氏体不锈钢钢板RCCM中文版法国民用核电标准
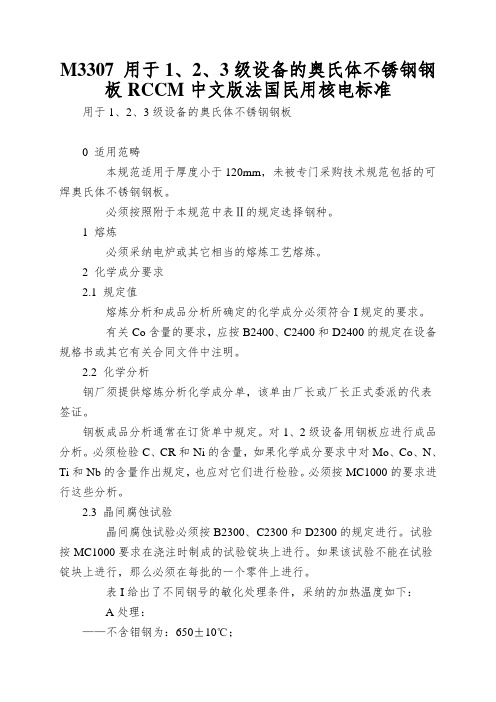
M3307 用于1、2、3级设备的奥氏体不锈钢钢板RCCM中文版法国民用核电标准用于1、2、3级设备的奥氏体不锈钢钢板0 适用范畴本规范适用于厚度小于120mm,未被专门采购技术规范包括的可焊奥氏体不锈钢钢板。
必须按照附于本规范中表Ⅱ的规定选择钢种。
1 熔炼必须采纳电炉或其它相当的熔炼工艺熔炼。
2 化学成分要求2.1 规定值熔炼分析和成品分析所确定的化学成分必须符合I规定的要求。
有关Co含量的要求,应按B2400、C2400和D2400的规定在设备规格书或其它有关合同文件中注明。
2.2 化学分析钢厂须提供熔炼分析化学成分单,该单由厂长或厂长正式委派的代表签证。
钢板成品分析通常在订货单中规定。
对1、2级设备用钢板应进行成品分析。
必须检验C、CR和Ni的含量,如果化学成分要求中对Mo、Co、N、Ti和Nb的含量作出规定,也应对它们进行检验。
必须按MC1000的要求进行这些分析。
2.3 晶间腐蚀试验晶间腐蚀试验必须按B2300、C2300和D2300的规定进行。
试验按MC1000要求在浇注时制成的试验锭块上进行。
如果该试验不能在试验锭块上进行,那么必须在每批的一个零件上进行。
表I给出了不同钢号的敏化处理条件,采纳的加热温度如下:A处理:——不含钼钢为:650±10℃;——含钼钢为:675±10℃。
——不含钼钢为:700±10℃;——含钼钢为:725±10℃。
腐蚀试验后,如果试样在声响中发出清脆的金属声,在弯曲试验中无裂纹和开裂现象,则该腐蚀试验合格。
若有疑咨询,可用金相法予以判定是否存在晶间腐蚀。
3 制造3.1 制造程序关于1、2级设备钢板,制造商在开始制造前须制订包括以下内容的制造程序:a)钢的冶炼方式;b)钢锭的重量和类型;c)要紧热加工操作特性;d)钢锭头、尾切除百分比;e)钢板处在钢锭中的位置,专门是有关于钢锭轴线的最终轧制方向;f)要紧轧制方向;g)要紧冷加工操作特性(用于冷精整钢板);h)中间热处理和最终力学性能热处理条件;i)带有验收试验用试料位置的图;j)在试料上截取试样的平面图。
晶间腐蚀检测报告
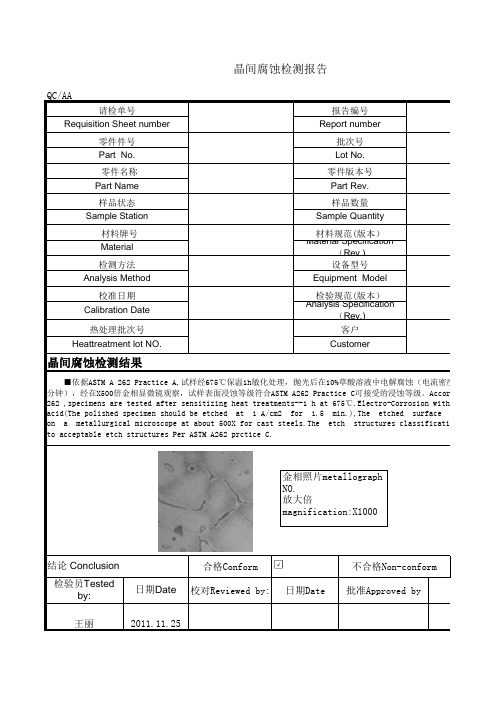
金相照片metallograph NO. 放大倍 magnification:X1000
结论 Conclusion
检验员Tested by:
合格Conform 日期Date 校对Reviewed by:
日期Date
王丽
2011.11.25
不合格Non-conform
批准Approved by
日期Date
晶间腐蚀检测结果
报告编号 Report number
பைடு நூலகம்批次号 Lot No.
零件版本号 Part Rev.
样品数量 Sample Quantity
材料规范(版本) Material Specification
(Rev.) 设备型号 Equipment Model
检验规范(版本) Analysis Specification
声明Statement:1.此分析结果仅对来样而言。Analysis results are only for requested sample.2.未经材料 验室书面批准,不得部分复制检验报告。The report shall not be reproduced except in full without the written approval of the MTL.
(Rev.) 客户
Customer
■依据ASTM A 262 Practice A,试样经675℃保温1h敏化处理,抛光后在10%草酸溶液中电解腐蚀(电流密度1A/cm2,时间 分钟),经在X500倍金相显微镜观察,试样表面浸蚀等级符合ASTM A262 Practice C可接受的浸蚀等级。According as AST 262 ,specimens are tested after sensitizing heat treatments--1 h at 675℃.Electro-Corrosion with 10% oxalic acid(The polished specimen should be etched at 1 A/cm2 for 1.5 min.),The etched surface is examine on a metallurgical microscope at about 500X for cast steels.The etch structures classification is compl to acceptable etch structures Per ASTM A262 prctice C.
ASTM G28-2002(R2015)锻制高镍铬轴承合金晶间腐蚀敏感性检测的标准试验方法(中文翻译版)

ASTM G28-2002(R2015)锻制高镍铬轴承合金晶间腐蚀敏感性检测的标准试验方法(中文翻译版)本标准以固定名称G28发布;紧跟在名称后面的数字表示最初采用的年份,如果是修订,则表示最后修订的年份。
括号中的数字表示上次重新批准的年份。
上标(ε)表示自上次修订或重新批准以来的编辑性修改。
本标准经美国国防部机构批准使用。
1.范围1.1试验方法包括下列两种方法:1.1.1 A法,硫酸-硫酸铁试验(第3-10节),这种试验方法描述了采用沸腾硫酸铁和50%硫酸试验测量某种镍基或铬轴承合金晶间腐蚀敏感性试验的工艺程序(请参阅术语G15),这种方法可能被遇到在某种腐蚀服务环境下。
通过这种方法获得相同的腐蚀速率,在合金成分方面是一个较小的变化函数,可能较容易掩盖全部的腐蚀速率的晶间腐蚀成分,比如N10276,N06020,N06059,N064455。
1.1.2方法B,氧化性盐、酸混合试验(第11-18节),这种试验方法描述了一种工艺,是指采用沸腾的含的23%硫酸+1.2%盐酸+1%氯化铁+1%氯化铜的试验,当晶界沉淀有高标准要求时,用于测量镍基材料和铬轴承合金的晶间腐蚀敏感性,显示阶梯函数提高腐蚀速率。
1.2这两种试验方法的目的是发现晶间腐蚀的敏感性在不同成分构成或不同程序中的影响,或者二者兼而有之。
显示有敏感性的材料在其他环境下可能或不可能被晶间腐蚀。
这必须单独的通过特殊的试验或服务经验予以确定。
1.3本标准主旨不在解决所有的安全问题,如果有,与使用本标准有关。
这是本标准使用者的责任,在使用之前建立适当的安全和健康实践,并确定控制局限性的适用性。
危险报告申明在章节5.1.1、5.1.3、5.1.9、13.1.1和13.1.11中讲述。
2.引用文件2.1 ASTM标准A262检测奥氏体不锈钢晶间腐蚀裂纹的敏感性D1193试验用水的规定G15与腐蚀及腐蚀试验有关的术语(2010年撤消)方法A硫酸铁—硫酸试验3.意义和用途3.1在合金锻造条件下的沸点硫酸铁-硫酸试验可适用于如下:合金试验时间(小时)N06007 120N06022 24N06030 120N06059 24N06200 24N06455 24N06600 24N06625 120N06686 24N06985 120N08020 120N08367 24N08800 120N08825A 120N10276 24A如果硫酸-硫酸铁腐蚀测试用于测试合金N008825的晶间腐蚀敏感性,如果在预定硝酸环境下,规程A262中的方法C的65%沸腾硝酸测试在测定不锈钢晶间腐蚀敏感性上具有较高的灵敏度。
铝合金晶间腐蚀报告范本

铝合金晶间腐蚀报告范本
报告背景:近期,我们的铝合金零件出现了晶间腐蚀现象,导致部分产品质量问题。
为了解决这一问题,我们进行了调查并制作了该报告,以便更好地了解问题根源并采取相应的措施。
调查方法:通过对受影响的铝合金零件进行实际观察及实验分析,我们发现晶间腐蚀主要发生在铝合金的晶界处。
同时,我们还分析了铝合金材料的成分、制造过程及使用环境等方面的因素。
调查结果:我们的调查结果表明,铝合金零件出现晶间腐蚀的原因主要是由于材料中含有较高的铜元素,这种元素会使得晶界处形成脆性相,从而导致晶间腐蚀的发生。
此外,制造过程中的热处理不当也会加重此类问题的发生。
另外,使用环境中的氯离子也是晶间腐蚀的加速因素。
解决方案:为了解决晶间腐蚀问题,我们需要采取以下措施:
1. 优化材料成分,减少铜等对晶间腐蚀的影响。
2. 改进铝合金的制造工艺,避免热处理不当引起的问题。
3. 在使用环境中注意去除氯离子等有害物质,从而减少晶间腐
蚀的发生。
结论:晶间腐蚀是铝合金零件质量问题的一个重要方面,需要我们在制造、使用等方面都密切注意。
通过本次调查,我们对该问题有了更深入的了解,并提出了相应的解决方案,以期更好地保障铝合金零件的质量和可靠性。
- 1 -。
晶间腐蚀试验报告1

评定结论
经16小时的硫酸-硫酸铜溶液腐蚀后,进行弯曲试验,试样未发现任何裂纹。评定结果为合格。
备注
检测说明
检测类别:委托检测
检测结果仅对来样负责
校核
主检
检测单位章
GB/T232-1999(弯曲)GB/T2975-1998(试样制备)
试样尺寸
生产厂家
检测日期
2014-03-09
试样重量
腐蚀前:g腐蚀后:g
敏化处理
温度:℃
冷却方式:
时间:
试验条件
溶液成分:硫酸-硫酸铜溶液
溶液状态:微沸状态
时间:16小时
评定方法
弯
曲
角度:180°
直径:
金
相
腐蚀液:硫酸-硫酸铜溶液
晶间腐蚀试验报告
委托位
首钢国际工程技术有限公司
报告编号
20140309
工程名称
莱钢焦化厂回收一车间二系统1#2#脱硫塔改造
试样编号
201403091
试样名称
焊接试板
试样状态
焊接试板
材料牌号
S3040S
试样表面积
检测项目
弯曲金相
规格
14mm
检测依据
GB/T4237-2007《不锈钢热轧钢板和钢带》
GB/T4334.5-2008《不锈钢硫酸-硫酸铜腐蚀试验方法》
环境腐蚀因素的电化学测定综合实验报告

实验 4.1: 环境腐蚀因素的电化学测定综合实验一、实验目的1.了解和掌握常用金属材料在不同环境条件中的腐蚀性强弱和主要腐蚀形态2.掌握影响材料环境失效的主要腐蚀因素3.掌握主要环境腐蚀性因素强弱的测试方法二、实验内容选取不同材料、不同介质分别进行以下实验:1.用酸度计测量所选介质的pH值;2.采用浸泡实验观察试验材料在不同介质中的腐蚀形态, 判断腐蚀类型;3.测量发生均匀腐蚀材料的失重或增重, 计算腐蚀速度;4.测量试验材料在不同介质中的φ-t曲线三、实验原理金属与周围环境之间发生化学或电化学作用而引起的破坏或变质, 称之为金属腐蚀。
也就是说, 金属腐蚀发生在金属与介质间的界面上。
材料究竟发生什么样的腐蚀、腐蚀的强弱主要取决于材料及其周围介质的性质。
不同的材料或不同设备工艺的同一种材料在同一介质中其腐蚀性不同;同一材料在不同环境中(如温度、pH值、浓度不同)其腐蚀性也会有很大的差别。
腐蚀类型很多, 也有多种分类方法。
如果按材料腐蚀后的外观特征分类: 当腐蚀均匀地发生在整个材料表面, 称为均匀腐蚀或全面腐蚀;当腐蚀集中在某些区域, 则称为局部腐蚀。
局部腐蚀又可分为电偶腐蚀、点蚀、缝隙腐蚀、晶间腐蚀、剥蚀、选择性腐蚀等。
金属腐蚀发生的根本原因是其热力学上的不稳定性造成的, 即金属及其合金较某些化合物原子处于自由能较高的状态, 这种倾向在条件具备时, 就会发生金属单质向金属化合物的转变, 即发生腐蚀。
发生化学腐蚀时, 被氧化的金属与介质中被还原的物质之间的电子是直接交换的。
发生电化学腐蚀时, 金属的氧化和介质中某物质的还原是在不同地点相对独立地进行的两个过程, 并且和流过金属内部的电子流和金属所处介质中的离子流形成回路, 即金属的电化学腐蚀是通过腐蚀电池进行的, 它是金属腐蚀中最常见最重要的类型。
在腐蚀过程中发生的腐蚀电池反应如下:阳极反应: M-ne- → M n+阴极反应: Ox+ne- → R总反应: M+Ox → Mn++R式中: Ox 为氧化剂, R为还原剂在大多数情况下, 氧化剂通常由水中溶解的氧或氢离子承担, 阴极反应为:1/2O2+H2O+2e → 2OH-或 H++e → 1/2H2金属与电解质接触时, 在金属与溶液界面将产生一电位差, 这一电位差值会随时间不断变化, 最后达到一稳定值, 通常称之为稳态自腐蚀电位Ecorr。
电化学再活化法(EPR)测量晶间腐蚀敏感性实验报告晶间腐蚀原理

电化学再活化法(EPR)测量晶间腐蚀敏感性电化学再活化法 (EPR) 测量晶间腐蚀敏感性( 一 ) 实验目的1. 用 EPR 法评价 308L 不锈钢的晶间腐蚀敏感性;2. 建立 EPR 法和草酸浸蚀法 (ASTM A 2622A) 评价 308L 不锈钢晶间腐蚀敏感性之间的关系;3. 了解不锈钢焊接接头产生晶间腐蚀的机理及晶间腐蚀区显微组织特征。
( 二 ) 晶间腐蚀原理绝大多数金属和合金是多晶体,在它们的表面上也显露出许多晶界。
晶界是原子排列较为疏松、紊乱的区域,容易产生杂质原子富集、晶界吸附、第二相的沉淀析出等现象,因此存在着显著的化学、物理不均匀性。
在腐蚀介质中,金属和合金的晶界的溶解速度和晶粒本身的溶解速度是不同的。
在某些环境中,晶界的溶解速度远大于晶粒本身的溶解速度时,会产生沿晶界进行的选择性局部腐蚀,称为晶间腐蚀 ( 图 1) 。
受热 ( 如敏化处理 ) 、受力 ( 冷加工形变 ) 而引起晶界组织结构的不均匀变化,对晶间腐蚀也有很大影响。
图 1. 晶间腐蚀的形貌特征晶间腐蚀发生后,金属和合金虽然表面仍保持一定的金属光泽,也看不出被破坏的迹象,但晶粒间的结合力已显著减弱,强度下降,因此设备和构件容易遭到破坏。
晶间腐蚀隐蔽性强,突发性破坏几率大,因此有严重的危害性。
不锈耐酸钢、镍基耐蚀合金、铝合金等金属材料都有可能产生晶间腐蚀;尤其在焊接时,焊缝附近的热影响区更容易发生晶间腐蚀。
( 三 ) 电化学再活化法 (EPR)EPR 方法最早由Cihal 等人提出,称为单环实验,现已列入美国标准ASTM G108292 ,但是这种单环实验方法对于现场检测晶间腐蚀敏感性有其不足之处:需要严格的表面处理和金相评定晶粒度。
后来,Akaski 等人提出了双环电化学动电位再活化实验方法,列入标准 J ISG 058021986 ,克服了单环实验法的缺点。
EPR 法提供了一种鉴别材料完全无敏化的判别标准,所以对于设备部件的质量控制是很有意义的,但是,无论是单环还是双环EPR 法对于有一定敏化程度的材料,都不能提供一个作为可接受的敏化程度的标准,所以必须建立起EPR 法和其它ASTM 标准实验方法之间的联系。
敏化态晶间腐蚀(竹本报告中提到的名词)
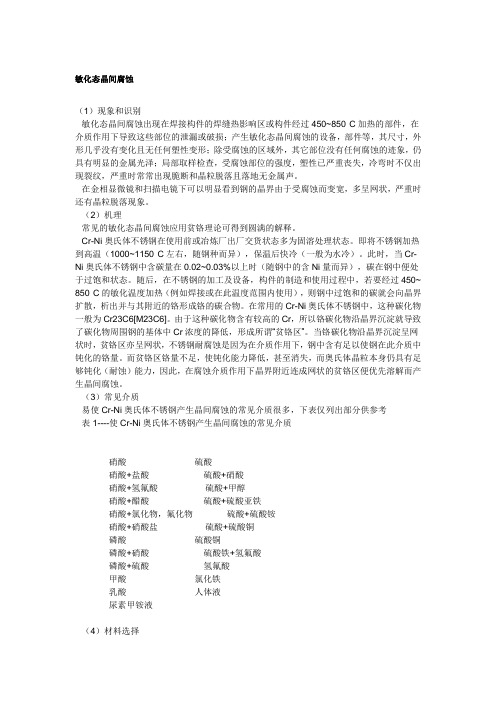
敏化态晶间腐蚀(1)现象和识别敏化态晶间腐蚀出现在焊接构件的焊缝热影响区或构件经过450~850°C加热的部件,在介质作用下导致这些部位的泄漏或破损;产生敏化态晶间腐蚀的设备,部件等,其尺寸,外形几乎没有变化且无任何塑性变形;除受腐蚀的区域外,其它部位没有任何腐蚀的迹象,仍具有明显的金属光泽;局部取样检查,受腐蚀部位的强度,塑性已严重丧失,冷弯时不仅出现裂纹,严重时常常出现脆断和晶粒脱落且落地无金属声。
在金相显微镜和扫描电镜下可以明显看到钢的晶界由于受腐蚀而变宽,多呈网状,严重时还有晶粒脱落现象。
(2)机理常见的敏化态晶间腐蚀应用贫铬理论可得到圆满的解释。
Cr-Ni奥氏体不锈钢在使用前或冶炼厂出厂交货状态多为固溶处理状态。
即将不锈钢加热到高温(1000~1150°C左右,随钢种而异),保温后快冷(一般为水冷)。
此时,当Cr-Ni奥氏体不锈钢中含碳量在0.02~0.03%以上时(随钢中的含Ni量而异),碳在钢中便处于过饱和状态。
随后,在不锈钢的加工及设备,构件的制造和使用过程中,若要经过450~ 850°C的敏化温度加热(例如焊接或在此温度范围内使用),则钢中过饱和的碳就会向晶界扩散,析出并与其附近的铬形成铬的碳合物。
在常用的Cr-Ni奥氏体不锈钢中,这种碳化物一般为Cr23C6[M23C6]。
由于这种碳化物含有较高的Cr,所以铬碳化物沿晶界沉淀就导致了碳化物周围钢的基体中Cr浓度的降低,形成所谓“贫铬区”。
当铬碳化物沿晶界沉淀呈网状时,贫铬区亦呈网状,不锈钢耐腐蚀是因为在介质作用下,钢中含有足以使钢在此介质中钝化的铬量。
而贫铬区铬量不足,使钝化能力降低,甚至消失,而奥氏体晶粒本身仍具有足够钝化(耐蚀)能力,因此,在腐蚀介质作用下晶界附近连成网状的贫铬区便优先溶解而产生晶间腐蚀。
(3)常见介质易使Cr-Ni奥氏体不锈钢产生晶间腐蚀的常见介质很多,下表仅列出部分供参考表1----使Cr-Ni奥氏体不锈钢产生晶间腐蚀的常见介质硝酸硫酸硝酸+盐酸硫酸+硝酸硝酸+氢氟酸硫酸+甲醇硝酸+醋酸硫酸+硫酸亚铁硝酸+氯化物,氟化物硫酸+硫酸铵硝酸+硝酸盐硫酸+硫酸铜磷酸硫酸铜磷酸+硝酸硫酸铁+氢氟酸磷酸+硫酸氢氟酸甲酸氯化铁乳酸人体液尿素甲铵液(4)材料选择长期以来,人们选用含稳定化元素Ti,Nb的Cr-Ni奥氏体不锈钢,例如1Cr18Ni9Ti, 0Cr 18Ni11Ti, 1Cr18Ni12Mo2Ti, 1Cr18Ni12Mo3Ti, 1Cr18Ni11Nb, 0Cr18Ni11Nb等以防止敏化态晶间腐蚀并取得了满意的结果。
铝合金晶间腐蚀报告范本
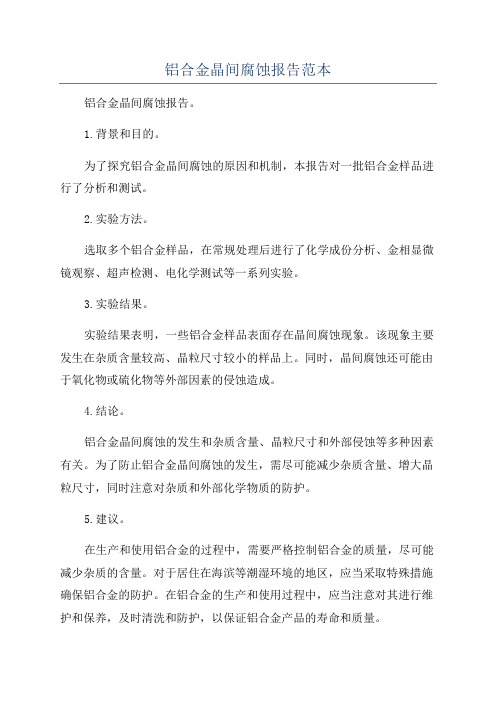
铝合金晶间腐蚀报告范本
铝合金晶间腐蚀报告。
1.背景和目的。
为了探究铝合金晶间腐蚀的原因和机制,本报告对一批铝合金样品进行了分析和测试。
2.实验方法。
选取多个铝合金样品,在常规处理后进行了化学成份分析、金相显微镜观察、超声检测、电化学测试等一系列实验。
3.实验结果。
实验结果表明,一些铝合金样品表面存在晶间腐蚀现象。
该现象主要发生在杂质含量较高、晶粒尺寸较小的样品上。
同时,晶间腐蚀还可能由于氧化物或硫化物等外部因素的侵蚀造成。
4.结论。
铝合金晶间腐蚀的发生和杂质含量、晶粒尺寸和外部侵蚀等多种因素有关。
为了防止铝合金晶间腐蚀的发生,需尽可能减少杂质含量、增大晶粒尺寸,同时注意对杂质和外部化学物质的防护。
5.建议。
在生产和使用铝合金的过程中,需要严格控制铝合金的质量,尽可能减少杂质的含量。
对于居住在海滨等潮湿环境的地区,应当采取特殊措施确保铝合金的防护。
在铝合金的生产和使用过程中,应当注意对其进行维护和保养,及时清洗和防护,以保证铝合金产品的寿命和质量。
10%草酸晶间腐蚀试验报告(各种腐蚀组织)

合格判定: Judgement
合格(Acceptable)
试验员
Inspector
审核
Check by
伍思遥 伍素仁
日期
Date
日期
Date
2012.3.26 2012 年.3.26
XXXX 不 锈 钢 管 有 限 公 司
XXXX Stainless Steel Pipe Co.,Ltd
晶间腐蚀试验报告
审核
Check
伍思遥 伍素仁
日期
Date
日期
Date
2012.3.26 2012 年.3.26
XXXX 不 锈 钢 管 有 限 公 司
XXXX Stainless Steel Pipe Co.,Ltd
晶间腐蚀试验报告
Testing Report of Intergranular Corrosion
试样尺寸
横截表面抛光,面积为
Sample Dimensions(mm)
25*25*5
试样处理 Sample condition
1.25cm2(≥ 1 cm2 ) Section polished,area is
1.25cm2
试验方法 Specimen Method.
10%草酸(H2C2O4·2H2O)浸蚀,电流密度 1 A/ cm2 ,浸蚀时间 1.5 分钟后,置于 250 倍~500 倍 显微镜下观测 Etched by 10%Oxalic Acid solution, The polished specimen should be etched at 1 A/cm2 for 1.5 min.
Testing Report of Intergranular Corrosion
ASTM_G_28探测高镍铬合金锻件晶间腐蚀敏感度的标准实施规程-中文

要求的腐蚀速率单位
密耳/年(mpy) 英寸/年(ipy) 英寸/月(ipm) 毫米/年(㎜/y) 微米/年(μm/y) 皮米/秒(pm/s) 每小时-克/米 2(g/㎡·h) 每天-克/分米 2(mdd) 每秒-微克/米 2(μg/㎡·45×106
3.45×103
-5-
7、试验程序
7.1 把试样放到玻璃支架上,移开冷凝器,将支架沉浸在沸腾的溶 液中,然后迅速的插上冷凝器。每次试验时应使用新配置的溶液。 7.2 用蜡笔对锥形瓶中溶液的水平面作记号,一旦发现溶液水平 面下降(0.5 ㎝或者更多),应立即重新配置新溶液,并使用新试 样或者重新抛光的试样,再进行试验。 7.3 按 3 中所规定的时间持续进行试验。结束后,取出试样,依 次用水和丙酮清洗、干燥。 7.4 称重,并计算出除去试样原重,试样的失重量。 7.5 通常情况下不需要中间称重,除非遇到了 7.7 所述的情况。 试 验 过 程 是 连 续 的 。然 而 ,若 试 验 中 间 需 要 得 到 初 步 的 结 果 ,可 以随时取出试样称量,然后继续试验。 7.6 试验期间不需要添加酸。 7.7 如果采用方法 A 进行试验时,腐蚀速速率极高,溶液颜色明 显 发 生 了 改 变( 绿 色 ),则 需 添 加 额 外 的 硫 酸 铁 。在 中 间 秤 重 时 , 发现试样总失重超过 2g 时,必须加入更多的硫酸铁,每溶解 1g 金属需添加硫酸铁 10g。这一款不适合方法 B。 7.8 采用方法 A 时,同一合金牌号的几个试样可同时进行试验, 大 约 一 个 锥 形 瓶 中 根 据 玻 璃 支 架( 应 与 锥 形 瓶 和 硫 酸 铁 的 含 量 相 配合)的数量一般可以放 3~4 个试样。在方法 B 中一个锥形瓶 中只能放置一个试样。 7.9 试验期间,在锥形瓶的上部会沉积一些氧化铁。试验完成后, 可在锥形瓶中加入沸腾的 10%HCL 溶液进行清洗。
M3304 用于1、2级和3级设备的奥氏体不锈钢钢管(热交换器管除外)

M3304产品采购技术标准用于1、2级和3级设备的奥氏体不锈钢钢管〔热交换器管除外〕0适用范围本标准适用于壁厚在1.0到50.0之间的奥氏体不锈钢无缝管,这些管用于辅助管路或其它用途的管路。
1熔炼必须采纳电炉或其它相当的熔炼工艺熔炼。
2化学成分要求2.1规定值熔炼分析和成品分析所确定的化学成分必须符合I规定的要求。
2.2化学分析钢厂须提供熔炼分析化学成分单,该单由厂长或厂长正式委派的代表签证。
成品检验在每批的一根钢管上进行这种分析。
一般情况下,仅检验C、Cr和Ni的含量,假如化学成分要求中对Mo、N的含量作出规定,也应对它们进行检验。
必须按MC1000的要求进行这些分析。
按照B2400、C2400和D2400的规定,有关CO含量的要求应在设备技术规格书或其它合同文件中规定。
2.3晶间腐蚀试验晶间腐蚀试验必须按B2300、C2300和D2300的规定进行。
试验按MC1000要求在浇注时制成的试验锭块上进行。
假如该试验不能在试验锭块上进行,那么必须在每批的一根钢管上进行。
表I给出了不同钢号的敏化处理条件,采纳的加热温度如下:A处理:——不含钼钢为:650±10℃;——含钼钢为:675±10℃。
腐蚀试验后,假如试样在声响中发出清脆的金属声,在弯曲曲折折试验中无裂纹和开裂现象,那么该腐蚀试验合格。
假设有疑点,可用金相法予以判定,以证实是否存在晶间腐蚀。
3制造3.1制造程序在开始制造前,钢管厂须制订制造程序。
该程序按时刻先后顺序列出不同的制造过程,所有的中间热处理、最终热处理、精加工和无损检验都应包括在制造程序中。
3.2钢管的制造用于制造钢管的圆钢或钢坯应取自头尾充分切除的钢锭。
总锻造比必须大于或等于3。
不管怎么样,必须保证按MC1000测定的成品管晶粒度指数至少为2。
另外,制造商应保证其所实施的制造工艺可不能改变钢的抗晶间腐蚀性能。
钢管应热加工成形,关于直径和壁厚不大的钢管也可采纳冷拔成型〔这种情况应在制造程序中明确规定——见3.1〕。
晶间腐蚀试验操作规程

晶间腐蚀试验操作规程总则1.1本公司采用的晶间腐蚀试验方法为GB/T4334.5-2000《不锈钢硫酸-硫酸铜腐蚀试验方法》。
1.2本守则对试样的提取、试验设备、试验条件和步骤、试验结果的评定及报告作了规定。
适用于检验奥氏体、奥氏体-铁素体不锈钢在加有紫铜屑的硫酸-硫酸铜溶液中的晶间腐蚀倾向。
2、试样的提取与制备2.1焊接件试样从与产品钢材相同且焊接工艺也相同的试板上提取,应包括母材、热影响区及焊接金属的表面,详见附件。
2.2试样用锯切取,如剪切则应通过切削或研磨方法除去剪切的影响部分。
2.3试样切取及表面研磨时,应防止表面过热。
试验试样表面粗糙度Ra值≯0.8μm,其他检验试样提取详见GB/T4334.5。
(见附件)3、试验仪器、设备、试验溶液3.1试验仪器为容量≥1L的带回流冷凝器的磨口锥形烧瓶。
3.2 600瓦的加热电炉配上一只可调变压器,通过后者调节加热电炉的功率,使本试验溶液能保持微沸状态。
3.3试验溶液配制方法如下:将100g符合GB/T665的分析纯硫酸铜(CuSO4·5H2O)溶解于700ml蒸馏水或去离子水中,再加入100ml符合GB/T625的优级纯硫酸,用蒸馏水或去离子水稀释至1000ml,即配成硫酸-硫酸铜溶液。
4、试验条件和步骤4.1试验前将试样用适当的溶剂或洗涤剂(非氯化物)去油污并干燥。
4.2在充入第3条配制的试验溶液的烧瓶底部铺一层符合GB/T466(纯度不小于99.5%)的紫铜屑或铜粒,然后放置试样。
保证每个试样与紫铜屑接触的情况下,同一烧瓶中允许放几层同一钢种的试样,但试样之间要用上述紫铜屑隔离而互不接触。
4.3试验溶液应高出最上层试样20mm以上。
每次试验都应使用新的试验溶液。
4.3.1仲裁试验时,试验溶液量按试样表面积计算,其量在8ml/Cm²以上。
4.4完成上述工作后,将烧瓶放在加热装置上,在回流冷凝器进水口要一直以冷却水(自来水)流入,出水口畅通放水。
TSGD0001-2019安装部分

焊缝的VT,硬度和NDT检查(82---87)
1.管道焊缝的检查,采用VT、RT、UT、 PT和MT等方法。
2.所有管道焊缝(除GC3对接环缝)应先进 行100%目视检查VT
3.焊缝处材料厚度超过30 mm时, 可采用 UT可代替RT;
4.厚度不超过30 mm时, 如采用UT代替RT, 应取得业主的批准 。
这些要求必须纳入焊接工艺评定的 附加要求。
管道焊接和热处理(管规62--72)
焊接工艺及焊工管理(62)
d.还应根据材料(包括焊接材料)、焊接工艺 和服役条件的具体(特殊)情况,重新审视 JB4708中的非重要因素及覆盖范围,必要时 应调正(缩小) 覆盖范围或将原JB4708中的 某些非重要因素添加为重要因素,
管道焊接和热处理(管规62--72)
1. GB/T20801.4-2019安装第7~9 章是对工业金属压力管道焊接和热处 理的基本要求:
2.焊接工艺评定;(管规62) 焊工技能评定;
管道焊接和热处理(管规62--72)
焊接工艺及焊工管理(62)
第六十二条 所有管道受压元件的焊接以及受压元 件与非受压元件之间的焊接,必须采用经评定合 格的焊接工艺,施焊单位必须严格对焊接工艺的 管理。
因素(有冲击韧性要求时)核定其适用的 范围。 对其中的不符合项应采取追加试验和评定 的方法,或重新进行焊接工艺评定。 b. JB4708仅将焊接接头的拉伸、冷弯和/或 冲击性能作为评定的依据;
管道焊接和热处理(管规62--72)
焊接工艺及焊工管理(62)
c. 管道材料和服役条件对焊接接头 提出其它要求时,如硬度限制、晶 间腐蚀试验、相比例、焊缝金属成 份、低温冲击、步冷及回火脆性试 验、铁素体数等要求时,
- 1、下载文档前请自行甄别文档内容的完整性,平台不提供额外的编辑、内容补充、找答案等附加服务。
- 2、"仅部分预览"的文档,不可在线预览部分如存在完整性等问题,可反馈申请退款(可完整预览的文档不适用该条件!)。
- 3、如文档侵犯您的权益,请联系客服反馈,我们会尽快为您处理(人工客服工作时间:9:00-18:30)。
晶间腐蚀试验报告
送样部门试样编号材料规格试验标准GB/T4334.5-2000产品名称材料牌号试样状态报告编号
试样尺寸试样表面积/ 报告日期
试样重量腐蚀前:/ g;腐蚀后:/ g 敏化处理
温度:/ ℃冷却方式:/
时间:/ h
试验条件溶液成份:硫酸-硫酸铜溶液
溶液状态:微沸状态
时间:16小时
评定方法
弯曲
角度:
直径:mm
金相
腐蚀剂:硫酸-硫酸铜溶液
放大倍数:10
评定结论备注/
试验员
审核
晶间腐蚀试验报告
送样部门试样编号材料规格试验标准GB/T4334.5-2000 产品名称材料牌号试样状态报告编号
试样尺寸100×20×4试样表面积/ 报告日期
试样重量腐蚀前:/ g;腐蚀后:/ g 敏化处理
温度:/ ℃冷却方式:/
时间:/ h
试验条件溶液成份:硫酸-硫酸铜溶液
溶液状态:微沸状态
时间:16小时
评定方法
弯曲
角度:
直径:mm
金相
腐蚀剂:硫酸-硫酸铜溶液
放大倍数:10
评定结论备注/
试验员
审核。