厂商来料批退率
供应商考核的六个指标

供应商考核的六个指标目录1 .前言 (1)2 .供应商考核的六个指标 (2)2.1.价格 (2)2.2.品质 (3)2.3.交货期 (5)2.4.服务水平 (6)2.5.信用度 (7)2.6.配合度 (8)1.刖百较先进的供应商考核系统则要进一步扩展到供应商的支持服务、供应商参与本公司产品开发的表现等,也就是把考核订单、订单实现过程延伸到产品开发过程。
采购人员通常从价格、品质、交货期和服务水平几个方面来考核供应商,并按百分制的形式来计算得分,至于如何分配,各公司可视具体情况自行决定。
不同企业生产规模不同,供应商供应的原材料也不同,因此针对供应商表现的考核要求也不相同,相应的考核指标设置也不一样。
一般来讲,最简单的办法就是衡量供应商的交货质量、及时性、价格和售后服务。
较先进的供应商考核系统则要进一步扩展到供应商的支持服务、供应商参与本公司产品开发的表现等,也就是把考核订单、订单实现过程延伸到产品开发过程。
采购人员通常从价格、品质、交货期和服务水平几个方面来考核供应商,并按百分制的形式来计算得分,至于如何分配,各公司可视具体情况自行决定。
欢迎关注供应商管理和开发公众号,交流学习更多供应商管理知识和经验。
这些评估指标可分为“定性”和“定量”两种类型,定量是指可以根据具体的公式或者算法得出准确的结果,而定性却需要人为进行判定。
传统企业使用的ERP,对以下的公式参数的条件,部分无法给出明确的值,而ISRM作为ERP的必要补充,可以提高公式算法的完整度,并且对很多需要定性判断的也可向定量判定转化,更客观,更准确。
2.供应商考核的六个指标2.1价格此处的价格是指供货的价格水平。
考核供应商的价格水平,可以和市场同档次产品的平均价和最低价进行比较,分别用市场平均价格比率和市场最低价格比率来表示。
平均价格比率二(供应商的供货价格-市场平均价)/市场平均价*100%最低价格比率=(供应商的供货价格■市场最低价)/市场最低价*100%长期从事招标代理工作的人都很清楚,招标活动中影响中标价格的因素很多。
进料检验合格率规定

编号:版本:
进料检验合格率规定
一、编制目的:
为防止供方进料不合格产品流入,加强供方质量管理工作。
二、职责划分:
质量部进料检验员每月完成统计并上报SQE和质量科长。
三、计算公式:
1.来料月批次合格率
2.计算公式=(1-发现不合格批次/检验批数)*100%
3.来料抽检合格率
4.计算公式=(1-发现不良数/来料总数)*100%
5.来料批次合格率
6.计算公式=(1-发现不良数/来料总数)*100%
四、日常规定:
1.供方月批次合格率低于95%的,则要求由供方展开自查与整改;
2.供方月批次合格率低于85%时,则需对供方准入资格进行审核;
3.单批次发现进料不合格的,则需第一时间反馈至供方并监督整
改;
4.每月1日完成上月供方进料合格率统计,并上报SQE和质量
科长;
5.每月5日前需将进料批次合格率及不良明细发至供方。
编制:XXX 审核:XXX 批准:XXX。
品质SQE绩效考核KPI
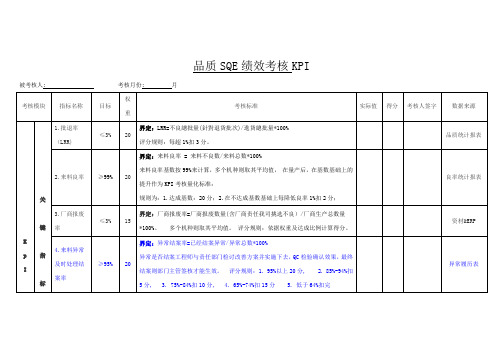
4.来料异常及时处理结案率
≥95%
20
界定:异常结案率=已经结案异常/异常总数*100%
异常是否结案工程师与责任部门检讨改善方案并实施下去,QC检验确认效果,最终结案则部门主管签核才能生效。评分规则:1. 95%以上20分, 2. 85%-94%扣5分,3. 75%-84%扣10分, 4. 65%-74%扣15分 5. 低于64%扣完
品质SQE绩效考核KPI
被考核人:考核月份:月
考核模块
指标名称
目标
权重
考核标准
实际值
得分
考核人签字
数据来源
K
p
I
关
键
指
标
1.批退率(LRR)
≤3%
20
界定:LRR=不良總批量(針對退貨批次)/進貨總批量*100%
评分规则:每超1%扣3分。
品质统计报表
2.来料良率
≥99%
20
界定:来料良率 = 来料不良数/来料总数*100%
来料良率基数按99%来计算,多个机种则取其平均值, 在量产后,在基数基础上的提升作为KPI考核量化标准:
规则为:1.达成基数:20分;2.在不达成基数基础上每降低良率1%扣2分;
良率统计报表
3.厂商报废率
≤3%
15
界定:厂商报废率=厂商报废数量(含厂商责任我司挑选不良)/厂商生产总数量*100%。多个机种则取其平均值。评分规则:依据权重及达成比例计算得分。
异常履历表
5.来料异常
是否明确注明此异常的原因及处理方法,少写或描述不清楚,每次扣3分
仓库
工作态度/服务承诺
工作态度
符合要求
5
包括工作失误、工作质量、工作心态(不积极、不主动)等相关事项, 每次扣2分,可以倒扣。
来料合格率定义
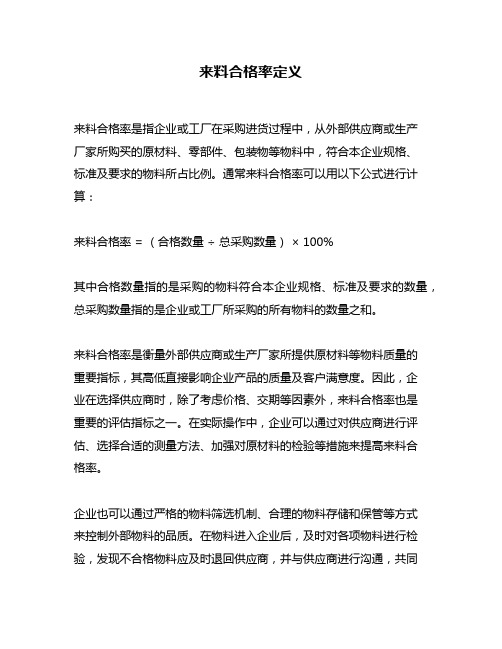
来料合格率定义
来料合格率是指企业或工厂在采购进货过程中,从外部供应商或生产
厂家所购买的原材料、零部件、包装物等物料中,符合本企业规格、
标准及要求的物料所占比例。
通常来料合格率可以用以下公式进行计算:
来料合格率 = (合格数量÷ 总采购数量)× 100%
其中合格数量指的是采购的物料符合本企业规格、标准及要求的数量,总采购数量指的是企业或工厂所采购的所有物料的数量之和。
来料合格率是衡量外部供应商或生产厂家所提供原材料等物料质量的
重要指标,其高低直接影响企业产品的质量及客户满意度。
因此,企
业在选择供应商时,除了考虑价格、交期等因素外,来料合格率也是
重要的评估指标之一。
在实际操作中,企业可以通过对供应商进行评估、选择合适的测量方法、加强对原材料的检验等措施来提高来料合
格率。
企业也可以通过严格的物料筛选机制、合理的物料存储和保管等方式
来控制外部物料的品质。
在物料进入企业后,及时对各项物料进行检验,发现不合格物料应及时退回供应商,并与供应商进行沟通,共同
解决问题。
如果出现大量不合格品,企业应及时找到原因,并采取相应措施,及时通报供应商,以达到共同提高品质的目的。
总之,来料合格率是企业质量管理的重要指标之一,关系到企业产品质量的好坏、客户满意度等问题。
企业应采取一系列措施,维护来料合格率的稳定和提高,以保证生产质量的稳定和持续发展。
供应商考核的KPI指标
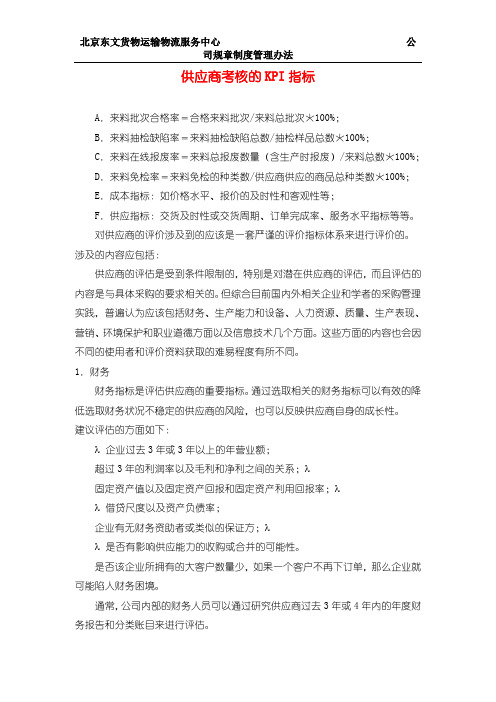
北京东文货物运输物流服务中心公司规章制度管理办法供应商考核的KPI指标A.来料批次合格率=合格来料批次/来料总批次*100%;B.来料抽检缺陷率=来料抽检缺陷总数/抽检样品总数*100%;C.来料在线报废率=来料总报废数量(含生产时报废)/来料总数*100%;D.来料免检率=来料免检的种类数/供应商供应的商品总种类数*100%;E.成本指标:如价格水平、报价的及时性和客观性等;F.供应指标:交货及时性或交货周期、订单完成率、服务水平指标等等。
对供应商的评价涉及到的应该是一套严谨的评价指标体系来进行评价的。
涉及的内容应包括:供应商的评估是受到条件限制的,特别是对潜在供应商的评估,而且评估的内容是与具体采购的要求相关的。
但综合目前国内外相关企业和学者的采购管理实践,普遍认为应该包括财务、生产能力和设备、人力资源、质量、生产表现、营销、环境保护和职业道德方面以及信息技术几个方面。
这些方面的内容也会因不同的使用者和评价资料获取的难易程度有所不同。
1.财务财务指标是评估供应商的重要指标。
通过选取相关的财务指标可以有效的降低选取财务状况不稳定的供应商的风险,也可以反映供应商自身的成长性。
建议评估的方面如下:λ企业过去3年或3年以上的年营业额;超过3年的利润率以及毛利和净利之间的关系;λ固定资产值以及固定资产回报和固定资产利用回报率;λλ借贷尺度以及资产负债率;企业有无财务资助者或类似的保证方;λλ是否有影响供应能力的收购或合并的可能性。
是否该企业所拥有的大客户数量少,如果一个客户不再下订单,那么企业就可能陷人财务困境。
通常,公司内部的财务人员可以通过研究供应商过去3年或4年内的年度财务报告和分类账目来进行评估。
供应商的信用报告也可以从银行提供的信用参考或者委托第三方机构获取相关财务状况评估。
2.生产能力生产能力的定义是:在指定时间内完成一个生产单位量的有限能力,通常以每单位时间输出的单位产量来表达。
能力是一个模糊的概念,因为它必须和生产部门如何使用这个概念相联系。
品质SQE岗位KPI绩效考核表

考核月份:
月
考核模块 指标名称
目标 权重
品质SQE KPI
考核标准
实际值 得分 考核人签字
数据来源
1.批退率 (LRR)
≤3%
20
界定:LRR=不良總批量(針對退貨批次)/進貨總批量*100% 评分规则:每超1%扣3分。
品质统计报表
2.来料良率
≥99%
界定:来料良率 = 来料不良数/来料总数*100%
键
评分规则:依据权重及达成比例计算得分。
K
p指
界定:异常结案率=已经结案异常/异常总数*100%
I
标
4.来料异常及 时处理结案率
≥95%
异常是否结案工程师与责任部门检讨改善方案并实施下去,QC检验确认效果,最 20 终结案则部门主管签核才能生效。
评分规则:1. 95%以上20分, 2. 85%-94%扣5分,
本部门直属领导打分
出勤率
由人事部统计 出勤率
0次
10
当月没有请假/迟到/早退/漏打卡10分, 扣1分。
当月有请假/迟到/早退/漏打卡每一次
此项由人事部统一填写
考核总分: 100
考核得分:
最终得分:
备注: 1. 90~100分, 优秀; 2. 80~90分, 良好; 3. 70~80分,一般; 4. 60~70分 待培养;5. 60分以下:不合格,每月绩效依据考核等级进行定义。 2. 因个人原因造成公司损失超过500元的, 取消当月个人绩效考核资格, 若造成严重后果, 公司保留追究法律责任的权利
20
来料良率基数按99%来计算,多个机种则取其平均值, 在量产后,在基数基础上 的提升作为KPI考核量化标准:
规则为:1.达成基数:20分;2.在不达成基数基础上每降低良率1%扣2分;
品质管理常见名词解释

品质指标名词解释1、CIT——Customer Incidents Tracking log,客诉追踪报告l CIT定义:CIT是为了有效地、系统地对客户端发生的质量异常进行追踪记录,而由CQS制作并更新维护的追踪报告。
(daily report)l CIT单位:件数。
CIT Qty:即客诉发生的件数。
l CIT的定义范围如下,共12条:1.1板子/零件烧毁1.2批量性不良(包括集中性高不良)1.3会引起重工的(包括厂内和厂外sorting & rework)1.4造成厂内hold货的客诉问题(即影响到厂内出货)1.5造成客户端停线/退货的客诉问题1.6 Workmanship issue和制程问题需100%提报(此问题可highlight给厂内改善)1.7属厂商来料不良的客诉问题1.8 Design 问题1.9客人Audit重大缺失项1.10客人发正式的异常通知单或者要求回复正式的改善报告1.11属CID的问题也需要报告CIT1.12厂商直接出货到客人端以及外包产品,在客户端出现问题均需要提报CITl CIT公式Weekly CIT Qty:当周提报的CIT Qty累加之和。
Monthly CIT Qty:当月提报的CIT Qty累加之和。
Yearly CIT Qty:整年度提报的CIT Qty累加之和。
2、AFR——Accumulated Failure Rate,累积不良率l AFR定义:AFR即产品在客户端的不良回归到产品制造月份的累积不良率。
从AFR 报告里面可以侦测到产品在客户端都发生了哪些不良以及这些不良在产品的整个生命周期发生的时机为何;还可以使用AFR对厂内外的良率做比对、分析和并寻求改善产品质量和信赖度的方向。
(weekly report)l AFR 单位:DPPM(每百万的不良数)l AFR公式3个月的AFR=(从生产当月算起3个月的所有返修数量/当月的生产总数)*10^66个月的AFR=(从生产当月算起6个月的所有返修数量/当月的生产总数)*10^61年的AFR=(从生产当月算起12个月的所有返修数量/当月的生产总数)*10^62年的AFR=(从生产当月算起24个月的所有返修数量/当月的生产总数)*10^63年的AFR=(从生产当月算起36个月的所有返修数量/当月的生产总数)*10^63、DOA&(客户端)LRR——Dead On Arrival,到货即损;(Customer) Line Reject Rate,(客户端)在线不良率l 定义:DOA&(客户端)LRR即客人收到货品后在进料检验时或在线投入使用时发现的不良,是工厂端为了监控产品到客户端的最及时的不良率报告。
来料合格率情况报告

来料品质状况报告本年度各供应商在品质上基本能满足我司的要求,尤其在后阶段,各供应商在品质上都有相应的提高;一、主料供应商相对比较稳定,如东宝,一年来的品质都比较稳定,在各供应商中表现比较突出;三圣在后阶段进步也很快,下面是各供应商近三个月的业绩:9月:总的合格率87.0%(来料批次654,不合格85批);10月:总的合格率91.8%(来料批次764,不合格63批);11月:总的合格率93.5%(来料批次675,不合格44批);平均合格率:90.77%各主料供应商来料合格率的详细情况如下:1.各供应商普遍存在材料厚度问题,基材在加工的过程中的厚度控制上没有完全控制住,有偏厚和偏薄的现象;2.倒角问题,主要是倒角不规则;3.强度的控制上,同一批有出现零星强度不良的现象,在强化过程中未能有效控制;4.混料现象也偶有出现,主要是新旧材料的变更未能彻底分开。
二、辅料供应商的品质情况各辅料供应商的品质相对要差些,主要的品质问题在:1.背胶的品质问题主要存在胶丝和线毛,各供应商也一直未能彻底解决,一年来因为这些问题多次遭到客户投诉或退货;2.保护膜问题主要是脏,储存一段时间后使镜片上存在白点;另一个方面是会产生水印;3.镭射纸问题,一个是镭射纸上的胶会溢出,这个问题的出现已导致批量退货;另一个是镭射纸打折和脏污,也导致客户多次投诉。
在各供应商中,未能有一家供应商能完全达到要求,相对来说,德晟和富源的供货在品质的配合上要好些,也能针对一些问题点去进行改善;强林的品质状况相对来说也还一般。
针对上述品质情况,对各供应商一方面通报04年的品质状况,另一方面要求各供应商在新的一年里彻彻实实地进行改善,同时能快速应对突发问题;做到及时反映,及时解决;其次,让所有供应商能及时理解市场的需求,并真正做到与供应商互利互惠的关系。
来料合格率情况报告

来料合格率情况报告尊敬的各位领导、同事:大家好!为了确保公司产品的质量和生产的顺利进行,现对近期的来料合格率情况进行详细报告。
本次报告旨在分析来料合格率的现状、存在的问题以及提出相应的改进措施,以便为公司的决策提供有力依据。
一、来料合格率的总体情况在过去的一段时间里,我们对公司所接收的各类原材料进行了严格的检验和统计。
总体来看,来料合格率呈现出一定的波动趋势。
经过详细的数据统计和分析,我们发现,在过去的具体时间段内,公司共接收了具体数量批次的原材料。
其中,合格批次为具体数量,不合格批次为具体数量,来料总体合格率为具体百分比。
从不同的原材料类别来看,原材料类别1的合格率为具体百分比1,原材料类别 2的合格率为具体百分比 2,原材料类别 3的合格率为具体百分比3……二、影响来料合格率的主要因素通过对不合格批次的深入分析,我们总结出了以下几个影响来料合格率的主要因素:1、供应商质量控制不足部分供应商在生产过程中未能严格按照质量标准进行操作,导致原材料存在缺陷。
例如,具体供应商名称供应的具体原材料名称在尺寸、性能等方面未能达到合同要求,从而影响了整体的合格率。
2、运输和储存环节的问题在原材料的运输和储存过程中,由于操作不当或环境因素的影响,也会导致原材料的质量受损。
例如,某些原材料在运输过程中受到碰撞和挤压,或者在储存过程中受潮、受热,从而影响了其性能和质量。
3、检验标准和方法的不完善我们现行的检验标准和方法可能存在一定的局限性,无法全面、准确地检测出原材料存在的问题。
例如,对于某些新型材料或复杂工艺的原材料,我们的检验手段可能不够先进和有效。
4、沟通协调不畅公司内部各部门之间以及与供应商之间的沟通协调不够顺畅,导致在原材料的采购、检验、使用等环节出现信息不对称和误解,从而影响了来料的合格率。
三、来料不合格对公司造成的影响来料不合格给公司带来了多方面的负面影响,主要包括以下几个方面:1、生产延误不合格的原材料无法直接投入生产,需要进行退货、换货或者重新采购,这必然会导致生产计划的延误,影响产品的按时交付。
批退率计算公式
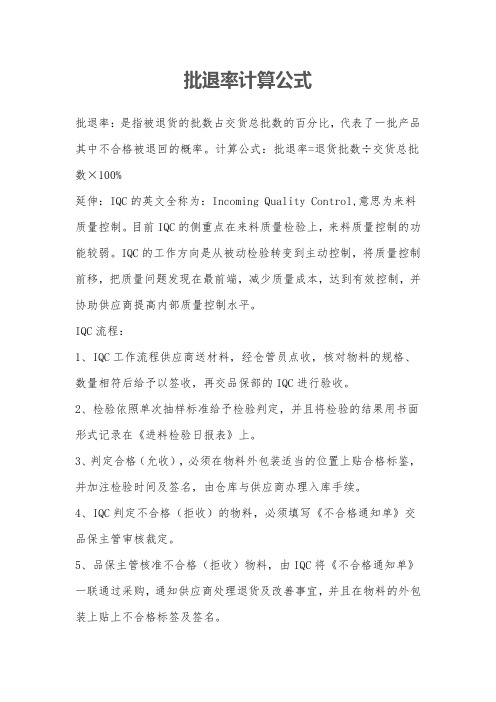
批退率计算公式
批退率:是指被退货的批数占交货总批数的百分比,代表了一批产品其中不合格被退回的概率。
计算公式:批退率=退货批数÷交货总批数×100%
延伸:IQC的英文全称为:Incoming Quality Control,意思为来料质量控制。
目前IQC的侧重点在来料质量检验上,来料质量控制的功能较弱。
IQC的工作方向是从被动检验转变到主动控制,将质量控制前移,把质量问题发现在最前端,减少质量成本,达到有效控制,并协助供应商提高内部质量控制水平。
IQC流程:
1、IQC工作流程供应商送材料,经仓管员点收,核对物料的规格、数量相符后给予以签收,再交品保部的IQC进行验收。
2、检验依照单次抽样标准给予检验判定,并且将检验的结果用书面形式记录在《进料检验日报表》上。
3、判定合格(允收),必须在物料外包装适当的位置上贴合格标鉴,并加注检验时间及签名,由仓库与供应商办理入库手续。
4、IQC判定不合格(拒收)的物料,必须填写《不合格通知单》交品保主管审核裁定。
5、品保主管核准不合格(拒收)物料,由IQC将《不合格通知单》一联通过采购,通知供应商处理退货及改善事宜,并且在物料的外包装上贴上不合格标签及签名。
6、品保部门判定不合格之物料,遇下列状况可由供应商或采购部向品保部提出予以特殊审核或提出特采申请。
a:供应商或采购部人员认定是IQC判定有误时;
b:该项符合物料生产急需使用时;
c:该项缺陷对后续加、生产影响甚微时;
d:其他特殊原因时。
制造行业品质控制常用KPI指标
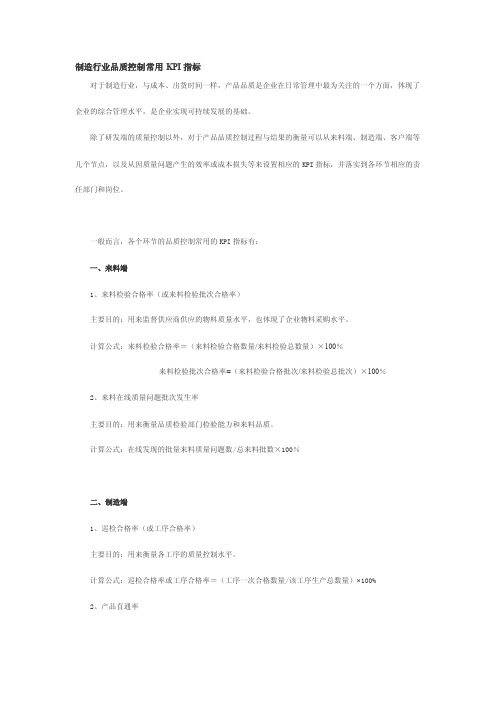
制造行业品质控制常用KPI指标对于制造行业,与成本、出货时间一样,产品品质是企业在日常管理中最为关注的一个方面,体现了企业的综合管理水平,是企业实现可持续发展的基础。
除了研发端的质量控制以外,对于产品品质控制过程与结果的衡量可以从来料端、制造端、客户端等几个节点,以及从因质量问题产生的效率或成本损失等来设置相应的KPI指标,并落实到各环节相应的责任部门和岗位。
一般而言,各个环节的品质控制常用的KPI指标有:一、来料端1、来料检验合格率(或来料检验批次合格率)主要目的:用来监督供应商供应的物料质量水平,也体现了企业物料采购水平。
计算公式:来料检验合格率=(来料检验合格数量/来料检验总数量)×100%来料检验批次合格率=(来料检验合格批次/来料检验总批次)×100%2、来料在线质量问题批次发生率主要目的:用来衡量品质检验部门检验能力和来料品质。
计算公式:在线发现的批量来料质量问题数/总来料批数×100%二、制造端1、巡检合格率(或工序合格率)主要目的:用来衡量各工序的质量控制水平。
计算公式:巡检合格率或工序合格率=(工序一次合格数量/该工序生产总数量)×100%2、产品直通率主要目的:用来衡量产品制造过程各个工序综合品质水平,指产品可以无缺损通过整个生产流程的概率值。
计算公式:产品直通率=工序1检验合格率×工序2检验合格率×…×工序N检验合格率3、产品出货检验合格率(或批次合格率)主要目的:用来衡量整个生产过程的最终产成质量水平。
计算公式:出货检验合格率=(出货检验合格数量/出货检验总数量)×100%出货检验批次合格率=(出货检验合格批次/出货检验总批次)×100%三、客户端1、客验合格率(或客验批次合格率)主要目的:用来衡量客户对企业提供的产品质量的要求。
计算公式:客验合格率=(客户检验产品合格数量/客户检验产品总数量)×100%客验批次合格率=(客户检验产品合格批次/客户检验产品总批次)×100%2、客户退货率主要目的:用来衡量客户对产品质量的接受程度。
供应商考核标准
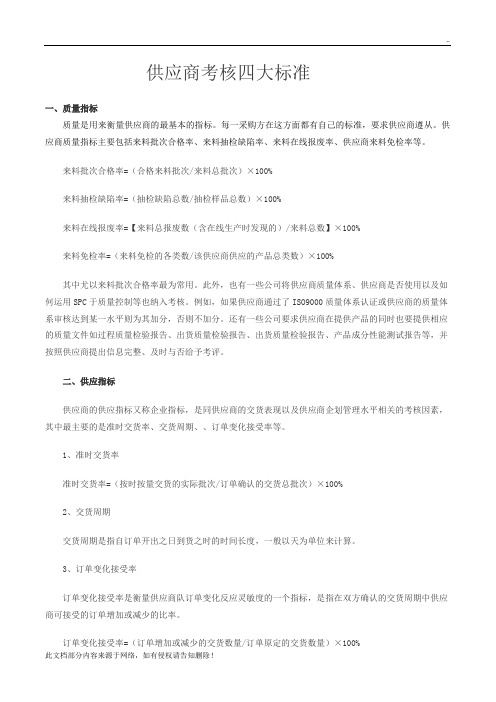
供应商考核四大标准一、质量指标质量是用来衡量供应商的最基本的指标。
每一采购方在这方面都有自己的标准,要求供应商遵从。
供应商质量指标主要包括来料批次合格率、来料抽检缺陷率、来料在线报废率、供应商来料免检率等。
来料批次合格率=(合格来料批次/来料总批次)×100%来料抽检缺陷率=(抽检缺陷总数/抽检样品总数)×100%来料在线报废率=【来料总报废数(含在线生产时发现的)/来料总数】×100%来料免检率=(来料免检的各类数/该供应商供应的产品总类数)×100%其中尤以来料批次合格率最为常用。
此外,也有一些公司将供应商质量体系、供应商是否使用以及如何运用SPC于质量控制等也纳入考核。
例如,如果供应商通过了ISO9000质量体系认证或供应商的质量体系审核达到某一水平则为其加分,否则不加分。
还有一些公司要求供应商在提供产品的同时也要提供相应的质量文件如过程质量检验报告、出货质量检验报告、出货质量检验报告、产品成分性能测试报告等,并按照供应商提出信息完整、及时与否给予考评。
二、供应指标供应商的供应指标又称企业指标,是同供应商的交货表现以及供应商企划管理水平相关的考核因素,其中最主要的是准时交货率、交货周期、、订单变化接受率等。
1、准时交货率准时交货率=(按时按量交货的实际批次/订单确认的交货总批次)×100%2、交货周期交货周期是指自订单开出之日到货之时的时间长度,一般以天为单位来计算。
3、订单变化接受率订单变化接受率是衡量供应商队订单变化反应灵敏度的一个指标,是指在双方确认的交货周期中供应商可接受的订单增加或减少的比率。
订单变化接受率=(订单增加或减少的交货数量/订单原定的交货数量)×100%值得注意的是,供应商能够接受的订单增加接受率与订单减少接受率往往并不相同。
其原因在于前者取决于供应商生产能力的弹性、生产计划安排与反应快慢、库存大小与状态(原材料、半成品或成品)等,而后者则主要取决于供应商的反应、库存(包括原材料与在制品)大小以及因减少订单带来可能损失的承受力。
KPI考核

指标名称 1.批退率(LRR)
考核月份 目标
≤3
权重 15%
SQE月度 KPI考核
2.来料良率
≥99% 15%
K
3.厂商报废率
≤3% 10%
P
I 关 键
4.来料异常及时 处理结案率
≥95%
10%
指 标
5.来料异常 SCAR单填写规
0次
10%
6.产线、客户投 诉次数
3≤
15%
7.报表执行
得分 考核人签字
数据来源 品质统计报表
良率统计报表
资材&ERP/MES
异常履历表
SCAR单描述 品质大会
Issue List 本部门主管
NA
最终得分
2.因个人原 因造成公司 损失超过500 元的,取消当 月个人绩效 考核资格,若 造成严重后 果的,公司保 留追究法律
SQE月度 KPI考核 月
考核标准 界定:LRR=不良总批量(针对退货批次)/进料总批量*100% 评分规则:每超1%扣3分 界定:来料良率=来料不良数/来料总数*100% 来料良率基数按99%来计算,多个机种则取其平均值,在量产后,在基数基础上的提升作为KPI考核化标准: 规则为:1,达成基数:15分,2.在不达成基数上每降低良率1%扣2分 界定:厂商报废率=厂商报废数量(含厂商责任我司挑选不良)/厂商生产总数量8100% 多个机种则取其平均值.评分规则:依据权重及达成比例计算得分 界定:异常结案率=已经结案异常数/异常总数*100% 异常是否结案,工程师与责任部门检讨改善方案并实施下去,QC检验确认效果,最终结案则部门主管签核 才能生效. 评分规则:1.95%以上10分,2.85%-94%扣3分.3.75%-84%扣6分,4.65%-74%扣7分,5.低于64%扣10分
供应商的绩效考核指标有哪些
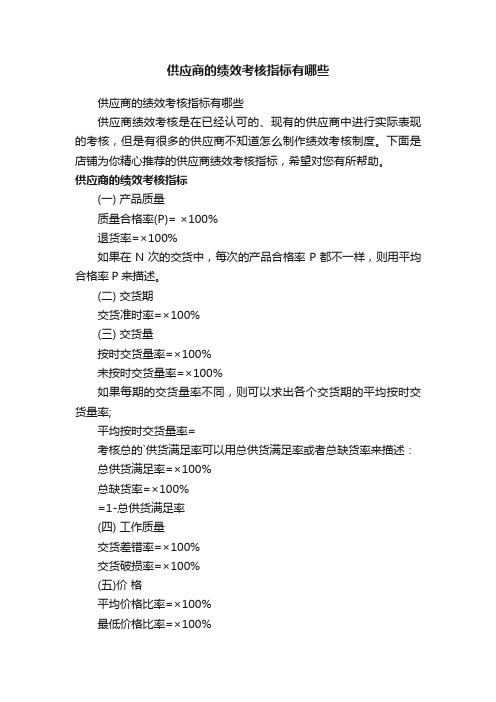
供应商的绩效考核指标有哪些供应商的绩效考核指标有哪些供应商绩效考核是在已经认可的、现有的供应商中进行实际表现的考核,但是有很多的供应商不知道怎么制作绩效考核制度。
下面是店铺为你精心推荐的供应商绩效考核指标,希望对您有所帮助。
供应商的绩效考核指标(一) 产品质量质量合格率(P)= ×100%退货率=×100%如果在N次的交货中,每次的产品合格率P都不一样,则用平均合格率P来描述。
(二) 交货期交货准时率=×100%(三) 交货量按时交货量率=×100%未按时交货量率=×100%如果每期的交货量率不同,则可以求出各个交货期的平均按时交货量率;平均按时交货量率=考核总的`供货满足率可以用总供货满足率或者总缺货率来描述:总供货满足率=×100%总缺货率=×100%=1-总供货满足率(四) 工作质量交货差错率=×100%交货破损率=×100%(五)价格平均价格比率=×100%最低价格比率=×100%(六)进货费用水平进货费用水平=×100%(七)信用度信用度主要考核供应商履行自己的承诺、以诚待人、不故意拖帐、欠帐的程度。
信用度可以用公式来描述:信用度= ×100%(八)配合度主要考核供应商的协调精神。
依靠人们的主管评分来考核。
供应商的绩效考核内容一、供应商绩效考核质量指标。
供应商绩效考核指标时供应商考核的最基本指标,包括来料批次合格率,来料抽检缺陷率、;来料在线报废率、供应商来叫免检率等。
二、供应商绩效考核供应指标。
供应指标又称企划指标,是与供应商的交货表现及其企划管理水平相关的因素,主要有准时交货率、交货周期、订单变化接受率等。
三、供应商绩效考核经济指标。
供应商绩效评估的方法在对供应商进行绩效评估时,一般分为四个步骤,包括建立供应商量化评估指标设计的原则,确定考核归口部门和量化指标权重,对供应商评估考核结果的应用,对供应商的分级管理。
供应商的考核标准总结
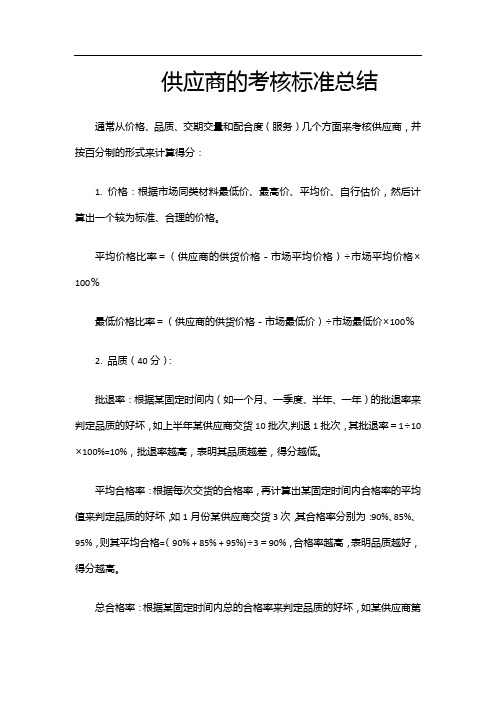
供应商的考核标准总结通常从价格、品质、交期交量和配合度(服务)几个方面来考核供应商,并按百分制的形式来计算得分:1. 价格:根据市场同类材料最低价、最高价、平均价、自行估价,然后计算出一个较为标准、合理的价格。
平均价格比率=(供应商的供货价格-市场平均价格)÷市场平均价格×100%最低价格比率=(供应商的供货价格-市场最低价)÷市场最低价×100%2. 品质(40分):批退率:根据某固定时间内(如一个月、一季度、半年、一年)的批退率来判定品质的好坏,如上半年某供应商交货10批次,判退1批次,其批退率=1÷10×100%=10%,批退率越高,表明其品质越差,得分越低。
平均合格率:根据每次交货的合格率,再计算出某固定时间内合格率的平均值来判定品质的好坏,如1月份某供应商交货3次,其合格率分别为:90%、85%、95%,则其平均合格=(90% + 85% + 95%)÷3=90%,合格率越高,表明品质越好,得分越高。
总合格率:根据某固定时间内总的合格率来判定品质的好坏,如某供应商第一季度分5批,共交货10000个,总合格数为9850个,则其合格率= 9850÷10000×100% = 98.5%,合格率越高,表明品质越好,得分更高。
3. 交期交量(20分):交货率:=送货数量÷订购数量×100%,交货率越高,得分就越多。
逾期率:=逾期批数÷交货批数×100%,逾期率越高,得分更少;逾期率越长,扣分越多;逾期造成停工待料,则加重扣分。
4. 配合度(服务)(10分):配合度上,应配备适当的分数,服务越好,得分越多。
5、进货费用水平(5分)进货费用水平=(本期进货费用-上期进货费用)÷上期进货费用×100%6、信用度(10分)信用度主要考核供应商履行自己的承诺、以诚待人、不故意拖帐、欠帐的程度。
品质管理常见名词解释
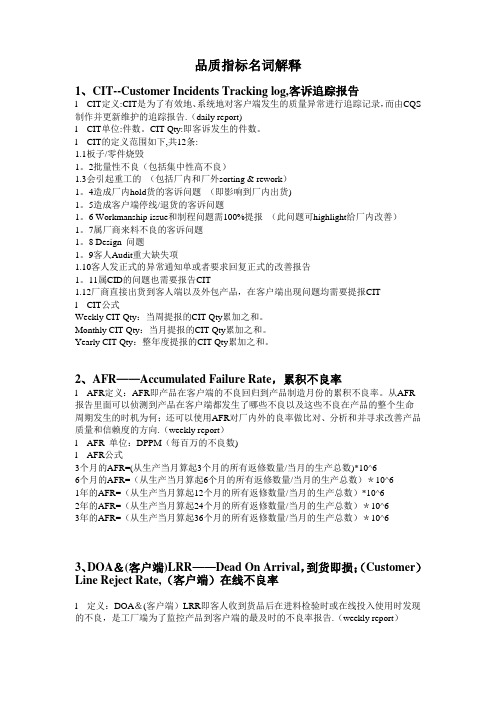
品质指标名词解释1、CIT--Customer Incidents Tracking log,客诉追踪报告l CIT定义:CIT是为了有效地、系统地对客户端发生的质量异常进行追踪记录,而由CQS 制作并更新维护的追踪报告.(daily report)l CIT单位:件数。
CIT Qty:即客诉发生的件数。
l CIT的定义范围如下,共12条:1.1板子/零件烧毁1。
2批量性不良(包括集中性高不良)1.3会引起重工的(包括厂内和厂外sorting & rework)1。
4造成厂内hold货的客诉问题(即影响到厂内出货)1。
5造成客户端停线/退货的客诉问题1。
6 Workmanship issue和制程问题需100%提报(此问题可highlight给厂内改善)1。
7属厂商来料不良的客诉问题1。
8 Design 问题1。
9客人Audit重大缺失项1.10客人发正式的异常通知单或者要求回复正式的改善报告1。
11属CID的问题也需要报告CIT1.12厂商直接出货到客人端以及外包产品,在客户端出现问题均需要提报CITl CIT公式Weekly CIT Qty:当周提报的CIT Qty累加之和。
Monthly CIT Qty:当月提报的CIT Qty累加之和。
Yearly CIT Qty:整年度提报的CIT Qty累加之和。
2、AFR——Accumulated Failure Rate,累积不良率l AFR定义:AFR即产品在客户端的不良回归到产品制造月份的累积不良率。
从AFR报告里面可以侦测到产品在客户端都发生了哪些不良以及这些不良在产品的整个生命周期发生的时机为何;还可以使用AFR对厂内外的良率做比对、分析和并寻求改善产品质量和信赖度的方向.(weekly report)l AFR 单位:DPPM(每百万的不良数)l AFR公式3个月的AFR=(从生产当月算起3个月的所有返修数量/当月的生产总数)*10^66个月的AFR=(从生产当月算起6个月的所有返修数量/当月的生产总数)*10^61年的AFR=(从生产当月算起12个月的所有返修数量/当月的生产总数)*10^62年的AFR=(从生产当月算起24个月的所有返修数量/当月的生产总数)*10^63年的AFR=(从生产当月算起36个月的所有返修数量/当月的生产总数)*10^63、DOA&(客户端)LRR——Dead On Arrival,到货即损;(Customer)Line Reject Rate,(客户端)在线不良率l 定义:DOA&(客户端)LRR即客人收到货品后在进料检验时或在线投入使用时发现的不良,是工厂端为了监控产品到客户端的最及时的不良率报告.(weekly report)l 单位:DPPM(每百万的不良数)l DOA&(客户端)LRR公式Weekly DOA&(客户端)LRR =(当周客户端上线发现的不良数/当周客户端上线的总投入数)*10^6Monthly DOA&(客户端)LRR =(当月客户端上线发现的不良数/当月客户端上线的总投入数)*10^64、(客户端)VLRR——Verified Line Reject Rate,(on—site FAE)确认后的客户端的在线不良率l (客户端)VLRR定义:(客户端)VLRR是经过本公司的人员(如on—site FAE)确认过的属于MSI责任的客户端的在线不良率。
- 1、下载文档前请自行甄别文档内容的完整性,平台不提供额外的编辑、内容补充、找答案等附加服务。
- 2、"仅部分预览"的文档,不可在线预览部分如存在完整性等问题,可反馈申请退款(可完整预览的文档不适用该条件!)。
- 3、如文档侵犯您的权益,请联系客服反馈,我们会尽快为您处理(人工客服工作时间:9:00-18:30)。
1.0 目的統一、規範本公司常用的品質指標的定義,包括中英文解釋、定義、公式、及其報告的格式。
以下按照從廠外到廠內(COPIS)的順序,把常見的品質指標加以說明,其中包括:CIT、AFR、DOA&客戶端LRR、客戶端VLRR、COQ、TAT、FPY(直通率)、制程不良率、制程來料不良率、MQA判退率、CAR結案率、SCAR 結案率、IQA LRR(進料批退率)、IQA VLRR(廠商來料批退率)2.0 範圍MSIS all QA Dept.3.0 組織與權責MSIS由Function QA定義制定; 由MSIS all QA Dept. 實施並執行。
4.0 流程圖無5.0 作業內容、規定、注意事項5.1 CIT5.1.1 CIT中英文對照中文:客訴追蹤報告English: Customer Incidents Tracking log5.1.2 CIT定義CIT是為了有效地、系統地對客戶端發生的品質異常進行追蹤紀錄,而由CQS製作並更新維護的追蹤報告。
(daily report)CIT單位:件數。
CIT Qty:即客訴發生的件數。
CIT的定義範圍如下,共12條:5.1.2.1板子/零件燒毀5.1.2.2批量性不良(包括集中性高不良)5.1.2.3會引起重工的(包括廠內和廠外sorting & rework)5.1.2.4造成廠內hold貨的客訴問題(即影響到廠內出貨)5.1.2.5造成客戶端停線/退貨的客訴問題5.1.2.6 Workmanship issue和制程問題需100%提報(此問題可highlight給廠內改善)5.1.2.7屬MSI的廠商來料不良的客訴問題5.1.2.8 Design 問題5.1.2.9客人Audit重大缺失項5.1.2.10客人發正式的異常通知單或者要求回復正式的改善報告5.1.2.11屬CID的問題也需要報告CIT(不會影響客訴減半的KPI)5.1.2.12廠商直接出貨到客人端以及外包產品,在客戶端出現問題均需要提報CITCIT Website address:首頁-2007>系統整合>未結案系統> Customer IncidentsTracking Log5.1.3 CIT公式Weekly CIT Qty:當周提報的CIT Qty累加之和。
Monthly CIT Qty:當月提報的CIT Qty累加之和。
Yearly CIT Qty:整年度提報的CIT Qty累加之和。
5.1.4 CIT報告格式5.2 AFR5.2.1 AFR中英文對照中文: 累積不良率English: Accumulated Failure Rate5.2.2 AFR定義AFR即產品在客戶端的不良回歸到產品製造月份的累積不良率。
從AFR報告裡面可以偵測到產品在客戶端都發生了哪些不良以及這些不良在產品的整個生命週期發生的時機為何;還可以使用AFR對廠內外的良率做比對、分析和並尋求改善產品品質和信賴度的方向。
(weekly report)AFR 單位:DPPM(每百萬的不良數)5.2.3 AFR公式3個月的AFR=(從生產當月算起3個月的所有返修數量/當月的生產總數)*10^66個月的AFR=(從生產當月算起6個月的所有返修數量/當月的生產總數)*10^61年的AFR=(從生產當月算起12個月的所有返修數量/當月的生產總數)*10^62年的AFR=(從生產當月算起24個月的所有返修數量/當月的生產總數)*10^63年的AFR=(從生產當月算起36個月的所有返修數量/當月的生產總數)*10^65.2.4 AFR報告格式5.3 DOA&(客戶端)LRR5.3.1 DOA&(客戶端)LRR中英文對照中文: DOA:到貨即損; LRR: (客戶端)線上不良率English: DOA: Dead On Arrival; LRR: (Customer) Line Reject Rate5.3.2 DOA&(客戶端)LRR定義DOA&(客戶端)LRR即客人收到貨品後在進料檢驗時或在線投入使用時發現的不良,包括客人的CND(誤判), PID(即MSI的CID)和VID(即MSI的VLRR)。
DOA&LRR是工廠端為了監控產品到客戶端的最及時的不良率報告。
(weekly report)DOA&(客戶端)LRR中屬於MSI責任的部分即VID部分是可以退貨、換貨或維修的,但退貨和換貨要在其DOA規定的期限內。
OEM客戶一般從7天到60天不等,而ODM客戶要久一些,如MSI Channel 客戶的DOA期限就是180天。
若超過DOA期限,就屬於RMA維修期限了,而RMA是不能退貨的。
DOA&(客戶端)LRR單位:DPPM(每百萬的不良數)5.3.3 DOA&(客戶端)LRR公式Weekly DOA&(客戶端)LRR =(當周客戶端上線發現的不良數/當周客戶端上線的總投入數)*10^6Monthly DOA&(客戶端)LRR =(當月客戶端上線發現的不良數/當月客戶端上線的總投入數)*10^65.3.4 DOA&(客戶端)LRR報告格式見附件6.35.4 (客戶端)VLRR5.4.1 (客戶端)VLRR中英文對照中文:(on-site FAE)確認後的客戶端的線上不良率English: Verified Line Reject Rate5.4.2 (客戶端)VLRR定義(客戶端)VLRR是經過本公司的人員(如on-site FAE)確認過的屬於MSI責任的客戶端的在線不良率。
(weekly report)單位:DPPM(每百萬的不良數)5.4.3 (客戶端)VLRR公式Weekly (客戶端)VLRR=(當周確認後的屬MSI責任的客戶端的在線不良數量/當周客戶端總投入數量)*10^6Monthly (客戶端)VLRR=(當月確認後的屬MSI責任的客戶端的在線不良數量/當月客戶端總投入數量)*10^65.4.4 (客戶端)VLRR報告格式見附件6.45.5 COQ5.5.1 COQ中英文對照中文:品質成本(或失敗成本)English: Cost of Quality5.5.2 COQ 定義COQ是為確保客戶得到高品質產品所耗之成本及為改善各種錯誤所投入的財力之總和。
不良之商業方法/程式,無效的品質體系,不良的製造方式,就會導致所謂的失敗成本。
較明顯的失敗有如停線,重工,維修,擔保,退款及其它類型的售後服務成本等;較不明顯的品質成本包括一些活動諸如IQA,ECN,SCAR跟蹤,及優秀員工的流失,潛在及現有客戶的流失等。
(weekly report)單位:美元通過計算品質成本可以達到以下目的:a. 將報廢及錯誤成本化以提高員工警覺。
b. 識別改善及降低失敗成本之機會。
c. 提供成本數據,以判斷改善方案選擇之正確性。
d. 通告周知激發改善。
e. 提供公司整體能力指標,將事情一次做好。
f. 用“管理語言”把品質成本量化為“錢”,將有利於引起管理上的注意。
g. 由於預算下降,有必要對改善方案做優先順序之選擇。
5.5.3 COQ公式COQ = 物料費用+搬運費用+人力費用+測試費用+場地費用+國家賦稅5.5.4 COQ 報告格式見附件6.55.6 TAT5.6.1 TAT中英文對照中文:返還時間English: Turn Around Time5.6.2 TAT 定義TAT定義為RMA從收到客人退回的不良品算起到維修ok寄出良品給客人之間的時段。
TAT單位:天5.6.3 TAT 公式TAT = 維修ok寄良品給客人的時間- 收到客人退回不良品的時間(daily report)5.6.4 TAT 報告格式見附件6.65.7 FPY(直通率)5.7.1 FPY(直通率)的中英文對照中文:直通率English: First Pass Yield (FPY),又稱go-straight-percentage5.7.2 FPY(直通率)定義FPY(直通率)是體現製造產出產品品質水準的一項指標﹐假如生產線投入100套材料﹐在製程中第一次就通過所有測試的產品的良品比率就是所謂的直通率。
經過生產線重工或維修才通過測試的產品不列入FPY的計算。
單位:%5.7.3 FPY(直通率)公式FPY = P1 x P2 x P3 x ... 其中P1, P2, P3,…等為產線上每一個站別的首次良率﹐同樣的對於重工或維修後的產品不列入計算。
透過這個計算式﹐我們可以知道及時的產線直通率﹐同時這個直通率有時比良率更能代表生產線真正的品質水準。
(weekly report)5.7.4 FPY(直通率)報告格式見附件6.75.8 制程不良率5.8.1制程不良率的中英文對照中文:制程不良率English: Process Failure Rate5.8.2制程不良率定義制程不良率是指產線在每個制程站別第一次產出的不良數與本站別的總投入數之比,例如F/T的不良率等。
(daily report)單位:DPPM(每百萬的不良數)5.8.3制程不良率公式制程不良率=(本制程站別的不良數/此制程站別的總投入數)*10^65.8.4制程不良率報告格式見附件6.85.9 制程來料不良率5.9.1制程來料不良率中英文對照中文:制程來料不良率English:Material Process Yield Rate Dell客戶也稱之為SVLRR,即Supplier Verified Lot Reject Rate5.9.2制程來料不良率定義制程來料不良率即在MSIS生產制程中發現的來料不良數與使用此物料的產品總投入數之比。
(weekly report)單位:DPPM(每百萬的不良數)5.9.3制程來料不良率公式制程來料不良率= (不良物料數/使用此物料的產品總投入數)*10^65.9.4制程來料不良率報告格式見附件6.95.10 MQA判退率5.10.1 MQA判退率中英文對照中文:MQA判退率English:Manufacture Quality Assurance Lot Reject Rate5.10.2 MQA判退率定義MQA判退率即MQA當日判退的批數與MQA當日總檢批數之比。
(daily report) MQA判退率單位:%具體判退標准請參考文件:“C-1-1-1-QW1001MSI HSF 產品外觀檢驗規範”5.10.3 MQA判退率公式MQA 判退率= MQA判退批數/ MQA總檢批數5.10.4 MQA判退率報告格式見附件6.105.11 CAR結案率5.11.1 CAR結案率中英文對照中文:矯正/預防措施報告結案率English: Corrective Action Report Close Rate5.11.2 CAR結案率定義CAR結案率定義即:CAR已結案數量占所發的CAR總數的比率。