基于DSP的电火花加工中抬刀过程的控制
微细电火花加工模糊抬刀控制系统的设计及实验研究

De i n a p r me t lS u y o z y J mpi g Co r lS se f r M i r — sg nd Ex e i n a t d fFu z u n nto y t m o c o EDM
Ab ta t sr c :Th s a e rsn s t o ffzyjmpn o to y tm ae nmie rg a i p p rp ee t meh do u z a u igc n r 1 se b s do x dpo rm— s
m i g o ATL n fM AB n a d VC + + .Th u z o t o y t m s d s n d b s d o t t t so h i e f z y c n r l s e i e i e a e n sa i i f t e d s s g sc —
《 电加工与模具》21 年第 1 02 期
关 的方 波信 号 ( 称放 电时 间 波 形 ) 就可 明显 区分 简 ,
出这两 种状 态 。 因此 , 用 放 电时 间 检测 法 检 测 微 采
时 如 以某 一 电压 为基 准 , 其 转 化 为与 放 电 时 间有 将
一
细电火 花加 工 间 隙大 小 的 灵敏 度很 高 , 于 微 细 电 适
—
编写 , 刀控 制 模 块 流 程 见 图 5 抬 。该 模 块 首 先 进 行 放 电状态 的辨 别 与 统计 , 设 计 的 放 电状 态 统 计 模 本 块是 基于 上述 放 电时 间检 测 法 、 脉 冲个 数 为 单 位 以 进行 放 电状态 统 计 的 。采用 累加 计 数 的方 法 , 软 在 件 中设 定 3个 变 量 c u t 、o n 、o n。l 分 别 o n. cu t c u t l S d a, 记 录短 路状 态数 、 花放 电状 态数 及总 放 电状态 数 , 火
抬刀高度和速度对电火花加工稳定性的影响机理研究

设 计 ・ 究 研
底 面加 工屑 浓度 的能 力 , 加工 变 得 稳定 。当 抬 刀 使 高度 大于 2mm 时 , 加工 已很 稳定 , 有效 放 电脉 冲数 保持 在较 高 的水 平上 。
35 O O
电状态 。图 4中 , a为 前 一 个 电极 加 工 时 间 刚 结 束
ge o lcr d u eg ta ds e d isfree to ejmp h ih n p e .Ho v r o d t ,t i me h ns wa o ul n eso d we e ,t ae hs c a im sn t l u d rto f y
2.Dain Unie st fTe hn lg Dain 11 02 Chia; la v r iy o c oo y, la 6 4, n
3.S z o a g a gS in e& Te h oo y C . t , u h u 2 5 2 Chn u h uS n u n ce c c n lg o ,L d S z o 1 1 9, ia) Ab ta t sr c :Th n e sa dn ft eme h ns h w h lcrd u eg ta d s e d afc eu d rtn ig o h c a im o t eee to ej mp h ih n p e f t e
《 电加工与模具》 02 2 1 年第 2 期
设 计 ・ 究 研
抬 刀高 度和速度对 电火花 加工稳定性 的影 响机 理研究
王 津 , 福 柱 卢 建 鸣。周 志 凯。赵 福 令 韩 , , ,
(1 .清华 大学精 密仪 器与机 械学 系 , 京 1 0 8 ; 北 0 0 4 2 大 连理 工大学 精密 与特种 加工 教育部 重点 实验 室 , 宁大 连 1 6 2 ; . 辽 1 0 4
用于电火花加工抬刀运动的速度规划算法

用于电火花加工抬刀运动的速度规划算法刘宏达;陈昊;陈默;奚学程;赵万生【摘要】电火花加工时,通过采用周期性的抬刀运动来降低放电间隙中的蚀除物浓度,能在改进有效放电率的同时提高加工的稳定性.目前用于电火花加工抬刀运动的速度规划算法,如常数加加速度S形曲线速度规划,其加加速度变化是不连续的,常数加加速度由于阶跃变化会引起机床的冲击和振动,使放电间隙状态变得不稳定,从而导致加工的不稳定.提出了一种用于抬刀运动的连续加加速度的速度规划算法,根据抬刀最大速度、抬刀高度及机床Z轴允许的最大加加速度进行基于连续加加速度的速度规划.通过对该速度规划算法进行的加工比较验证实验可知,运用该速度规划方法可在保证加工效率的基础上,更好地减少对机床的冲击和振动,使加工过程更稳定.%In order to improve the effective discharge ratio and the machining stability in electro-discharge machining (EDM),a periodic jump motion of the electrode can be adopted so as to reduce the debris concentration in the discharge gap. Velocity planning is an important part in the design of a jump motion. However,existing velocity planning algorithms,such as the S-shaped feedrate planning, do not address the discontinuities in jerks. With a possibility of invoking vibrations in a machine , discontinuities in jerks are harmful to a stable discharge status. A velocity planning algorithm with continuous jerks for jump motion is proposed ,which takes into considerations constraints on the maximum velocity,jump heights and jerks of the Z-axis of a machine. The experimental results show that this proposed velocity planning algorithm achieves a better performance witha smoother jump motion and the stability and reliability is verified through an EDM machining for a deep slot.【期刊名称】《电加工与模具》【年(卷),期】2016(000)003【总页数】5页(P1-5)【关键词】电火花加工;抬刀运动;S形曲线速度规划;连续加加速度【作者】刘宏达;陈昊;陈默;奚学程;赵万生【作者单位】上海交通大学机械与动力工程学院,机械系统与振动国家重点实验室,上海 200240;上海交通大学机械与动力工程学院,机械系统与振动国家重点实验室,上海 200240;上海交通大学机械与动力工程学院,机械系统与振动国家重点实验室,上海 200240;上海交通大学机械与动力工程学院,机械系统与振动国家重点实验室,上海 200240;上海交通大学机械与动力工程学院,机械系统与振动国家重点实验室,上海 200240【正文语种】中文【中图分类】TG661电火花加工材料去除是通过在电极与工件之间的绝缘通道中产生一系列放电完成的,放电产生的蚀除物不利于稳定加工[1]。
电火花成型加工操作规程及注意事项
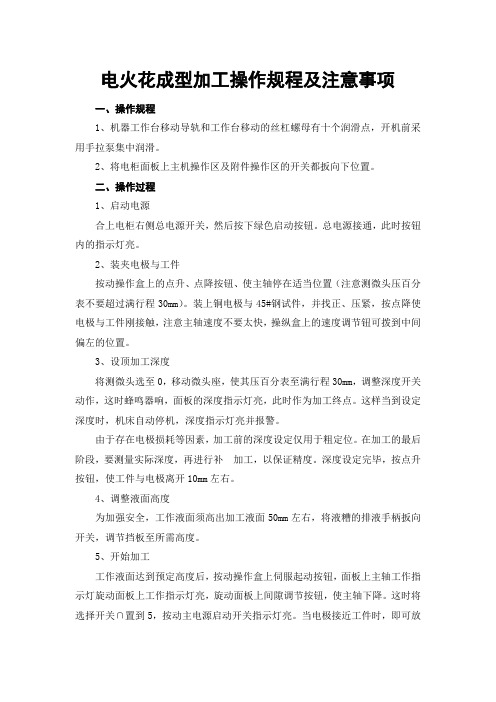
电火花成型加工操作规程及注意事项一、操作规程1、机器工作台移动导轨和工作台移动的丝杠螺母有十个润滑点,开机前采用手拉泵集中润滑。
2、将电柜面板上主机操作区及附件操作区的开关都扳向下位置。
二、操作过程1、启动电源合上电柜右侧总电源开关,然后按下绿色启动按钮。
总电源接通,此时按钮内的指示灯亮。
2、装夹电极与工件按动操作盒上的点升、点降按钮、使主轴停在适当位置(注意测微头压百分表不要超过满行程30mm)。
装上铜电极与45#钢试件,并找正、压紧,按点降使电极与工件刚接触,注意主轴速度不要太快,操纵盒上的速度调节钮可拨到中间偏左的位置。
3、设顶加工深度将测微头选至0,移动微头座,使其压百分表至满行程30mm,调整深度开关动作,这时蜂鸣器响,面板的深度指示灯亮,此时作为加工终点。
这样当到设定深度时,机床自动停机,深度指示灯亮并报警。
由于存在电极损耗等因素,加工前的深度设定仅用于粗定位。
在加工的最后阶段,要测量实际深度,再进行补加工,以保证精度。
深度设定完毕,按点升按钮,使工件与电极离开10mm左右。
4、调整液面高度为加强安全,工作液面须高出加工液面50mm左右,将液糟的排液手柄扳向开关,调节挡板至所需高度。
5、开始加工工作液面达到预定高度后,按动操作盒上伺服起动按钮,面板上主轴工作指示灯旋动面板上工作指示灯亮,旋动面板上间隙调节按钮,使主轴下降。
这时将选择开关∩置到5,按动主电源启动开关指示灯亮。
当电极接近工件时,即可放电加工。
6、加工调整为实现稳定加工,还需进行以下调节⑴调节间隙电压:旋动间隙电压调节钮,时面板上的电压指示表在50V左右,同时调节操纵盒上的速度调节钮大约在中间偏右位置,以加工稳定为准(百分表指针不抖动)。
⑵定时抬刀:要使加工稳定,有利排?,再加工盲孔时需定时抬刀。
拉出抬刀间隙旋钮,定时抬刀线路接通。
旋动此旋钮,调节到5秒钟抬一次,然后调节抬刀高度按钮,抬刀间隔时间缩短,抬刀高度适当增加。
7、故障报警如加工过程中液面降低或液温过高,液面指示灯亮并报警;如果产生积碳,积碳指示灯亮并报警,同时自动切断主电源并停机。
电火花成型加工机床操作规程范本

电火花成型加工机床操作规程范本第一章总则第一条为了保障电火花成型加工机床的安全操作,提高加工质量,根据相关法律法规及国家标准制定本规程。
第二章机床操作规范第二条操作人员必须经过专业培训,并持有相应的操作证书,方可操作电火花成型加工机床。
第三条操作人员必须熟悉电火花成型加工机床的结构、原理、性能及操作规程。
第四条操作人员必须检查机床的维护情况以及附件是否齐全,确保机床处于良好的工作状态。
第五条操作人员必须戴好防护用具,包括防护眼镜、口罩、耳塞、安全鞋等,保障个人安全。
第六条操作人员不得私自拆卸机床零部件或进行未经授权的维修。
第七条操作人员在操作机床前应对机床及周边进行查看,确保没有其他人员存在于危险区域。
第八条操作人员必须按照操作规程要求进行操作,不得随意更改参数和加工程序。
第九条加工前必须将工件夹固,确保稳定不松动。
第十条加工过程中严禁瞎操作,必须按照指令逐步进行。
第十一条操作人员在操作过程中要保持专注,不得与他人交谈或进行其他分散注意力的行为。
第十二条加工结束后,必须关闭机床电源,并及时清理工作区域,保持机床的清洁整洁。
第三章安全操作要点第十三条操作人员必须严格按照操作规程要求进行操作,不得进行超负荷操作。
第十四条加工过程中不得随意触摸机床运动部位,以免造成安全事故。
第十五条加工大型工件时,应根据工件的负载情况合理分配加工时间,以防过负荷导致机床故障。
第十六条操作人员应经常关注机床操作面板上的状态指示灯,一旦发现异常情况,应及时停车处理。
第十七条操作人员在操作机床时,严禁穿插其他任务,以免操作失误导致事故。
第十八条加工过程中不得私自修改程序或参数设置,必须按照规范进行调整。
第十九条操作人员在加工过程中发现异常声音、异味等情况时,应及时停车检查。
第二十条操作人员在加工小型零件时,应使用专用夹具,避免使用手持装置操作,以防伤手。
第四章操作事故处理第二十一条操作人员在操作过程中发生事故时,应立即停车,并及时报告给上级负责人。
电火花成型加工机床操作规程

电火花成型加工机床操作规程一、前言电火花成型加工机床是现代工业中常用的成形加工机器,它具有高精度、高效率、适用于各种材料等优点,被广泛应用于模具、航空航天、汽车、电子制造等行业。
但是,由于该机床操作过程中涉及高压电等安全隐患,在使用过程中必须严格遵守操作规程,以确保操作安全和加工质量。
二、操作规程1. 机床准备(1)检查机床各部件是否完好无损,如夹具、电极等是否合适且安装稳固。
(2)检查液压系统、冷却液系统是否正常运行,如压力、温度等是否在正常范围内。
(3)检查加工程序是否正确,并按照程序设定参数正确选取加工电极。
2. 操作流程(1)将加工工件夹紧在工作台上,并按照加工程序调整机床定位;(2)选择合适的电极,并安装好;(3)选取合适的工作流体,并启动冷却液系统;(4)将工作台移动至电极上方,拉开防护罩门;(5)根据加工程序输入正确参数,选择加工方式,启动机床;(6)监测加工过程中的参数,如电压、电流、钝化时间、脉冲时间等,根据需要适时调整;(7)加工结束后,将工作夹具固定在工作台上。
3. 安全操作(1)在操作过程中必须穿戴个人防护用具,如绝缘手套、护目镜、工作服、防静电鞋等。
(2)严禁在机床运行中操作机床,更不得在机床定位之前伸手进入工作区域。
(3)在机床运行过程中,严禁将金属或容易导电的材料放置在机床上或接近机床。
(4)加工过程中如发现异常情况,应立即停止机床,并进行检查排除故障。
(5)加工结束后,彻底清洁加工区域,并关闭机床电源、液压系统、冷却系统。
三、操作注意事项(1)严禁使用非正规厂家生产的电极或工作流体等配件;(2)加工过程中,电极的表面需要保持干净光滑,不得有氧化物、油渍等物质污染。
(3)在长时间连续加工时,需注意检查机床各部件是否易损耗,并及时更换维修。
(4)加工过程中,应按照加工程序和电极材料等信息设定参数,保证运行精度和工件质量。
四、总结电火花成型加工机床作为一种高先进的成形加工机器,应用范围广泛,但在操作中必须严格遵守操作规程,特别是在安全方面追求“安全、预防”的原则,以保障操作者的人身安全和机器的正常运行。
电火花线切割加工机床的安全操作规程

电火花线切割加工机床的安全操作规程电火花线切割加工机床是一种高精度加工设备,因其操作较为复杂,涉及到高压、高温等危险因素,所以需要遵守相关的安全操作规程,以确保工作人员的人身安全和设备的正常运行。
一、准备工作1.工作人员须备齐相关证件,经过安全培训,并严格按照标准程序操作。
2.检查机床灵敏度及限位开关的功能是否正常,杜绝可能出现的操作失误。
3.保证相关设备和周围环境清洁、干燥。
4.工作人员必须穿戴好防护服和防护手套,避免因接触高温部件产生烫伤。
5.检查控制系统和电气系统,确保电路线路完好,放电装置可靠及带电元件正确安装。
二、操作规程1.“三步操作法”是操作该设备的基本方法,即“确认工件位置-调整电极位置-操作掌机”。
必须坚决执行,遵守这个操作规则可以大大减少操作失误。
2.工作人员在进行操作前需认真检查工件的位置及尺寸,确认无误后方可进行下一步操作。
3.调整电极的位置时,应将掌机移出工件表面,在确保操作安全的前提下使用手轮或按键。
4.操作掌机时必须保持手部和脚部稳定,并注意观察放电脉冲频率,确保加工精度。
5.操作人员离开机床之前,须把掌机置放在预留位置,杜绝放置在机床内的可能,避免出现安全隐患。
6.当发生异常情况时,如出现工件与电极接触停滞、电极断电,应立刻切断电源,进行故障排查。
绝不能私自进行调试,避免因不当处理而给人身安全带来危害。
三、操作注意事项1.避免穿戴有宝石或其他金属饰物,避免发生意外触电事故。
2.严禁在机器运作状态下进行保养和维修,待停机后方可进行相关操作。
3.严禁对机器进行未经过授权的修改和维修,以免影响设备的正常运行和安全性。
4.加工较小的零件时,必须使用夹具固定,避免造成操作的危险。
5.定期检查机床的液压、气压系统,保证相关设备的正常工作。
6.每天结束工作时,应及时对设备进行清洗、保养和维护,保持机器的干净整洁。
以上为电火花线切割加工机床的安全操作规程,所有操作人员须严格遵守相关规程,从而确保设备的安全性和操作过程的顺畅。
基于可编程运动控制器的电火花加工高速抬刀控制系统

第46卷第9期 2012年9月上海交通大学学报JOURNAL OF SHANGHAI JIAOTONG UNIVERSITYVol.46No.9 Sep.2012 收稿日期:2011-10-14基金项目:国家科技重大专项基金资助项目(2009ZX04003-021)作者简介:梁 速(1983-),男,江西省南昌市人,主要研究方向为多轴联动电火花加工及微细电加工数控系统.赵万生(联系人),男,教授,博士生导师,电话(Tel.):021-34206949;E-mail:zws@sjtu.edu.cn. 文章编号:1006-2467(2012)09-1476-06基于可编程运动控制器的电火花加工高速抬刀控制系统梁 速, 赵万生, 康小明(上海交通大学机械与动力工程学院,上海200240)摘 要:针对电火花加工高速抬刀控制系统的设计要求,设计了基于可编程运动控制器的电火花加工高速抬刀控制系统,并将其应用于DK7140型商用电火花成形加工机床.结果表明,利用所设计的高速抬刀控制系统实现了主轴最高速度达200mm/s、最大加速度约9.68m/s2的稳定高速抬刀运动.进一步通过窄槽加工实验,取得了窄槽加工最大深度与加工效率的成倍提高,并验证了高速抬刀控制系统的控制与加工性能.关键词:高速抬刀;电火花加工;控制系统;可编程运动控制器中图分类号:TG 661 文献标志码:AHigh-Speed Jump Motion Control System for Electro-DischargeMachining Based on Programmable Multi-axis ControllerLIANG Su, ZHAO Wan-sheng, KANG Xiao-ming(School of Mechanical Engineering,Shanghai Jiaotong University,Shanghai 200240,China)Abstract:The requirements from designing high-speed jump motion control system for EDM(electro-dis-charge machining)were suggested in three terms:system capable of achieving high-speed motion control,system with good performance in responding and following the reference signal for axis and a jump motioncourse with high acceleration.A high-speed jump motion control system for EDM based on programmablemulti-axis controller(PMAC)was studied and designed to meet the requirements suggested.The controlsystem proposed was applied to type DK7140commercial EDM machine and achieved stable main axis jumpmotion with maximum speed of 200mm/s and maximum acceleration approximate to 9.68m/s2.Throughthe experiments of processing narrow slots,the control system obtains good results in terms of maximummachined depth and processing efficiency,and validates the good performance in control and machining.Key words:high-speed jump motion;electro-discharge machining(EDM);control system;programmablemulti-axis controller(PMAC) 在电火花加工(EDM)过程中,需要通过冲液、抬刀等方式而及时排除放电间隙中的电蚀产物,以避免加工屑滞留所导致的异常放电而使加工无法持续进行.抬刀的目的在于实现稳定加工,而通过智能控制抬刀的频率,有助于提高加工效率;同时,尽可能地提高抬刀速度,减少抬刀过程中往复运动所消耗的时间,已成为进一步提高其效率的有效途径[1-3].此外,高速抬刀使得加工液的流量和流速大幅提高,对加工屑的混合、带出作用更加充分有效,因而可以显著提高其排屑性能.在加工排屑条件恶劣的复杂或深窄型腔(如窄缝窄槽)时,高速抬刀可以大幅提高其最大加工深度与加工效率[4].本文分析了电火花加工高速抬刀控制系统的设计要求,设计了基于可编程运动控制器(Program-mable Multi-Axis Controller,PMAC)、全闭环速度指令模式的电火花加工高速抬刀控制系统,并将其应用于DK7140型商用电火花成形加工机床中,验证了该系统的稳定性与可靠性及优良的加工性能,以期为研究国内自主设计、抬刀速度最快的商用电火花成形加工机床提供依据.1 EDM高速抬刀控制系统的设计要求 高速抬刀要求运动轴具备高速运动性能,而电火花加工的伺服过程通常对运动轴的灵敏度要求较高,对进给和回退运动的速度要求较低,抬刀速度一般在3~5m/min左右,空走速度不超过10m/min.因此,国内主流的商用电火花成形加工机床在控制系统中大多采用脉冲+方向指令的位置闭环控制模式,在驱动执行机构中,采用伺服驱动器+旋转电机+滚珠丝杠平台的方案.这种体系无法满足运动轴的高速运动性能的要求,其原因在于:首先,运动控制系统输出的脉冲指令受到其软、硬件平台主频或时钟频率的限制而无法达到较高的触发频率,在保证电机控制精度的前提下限制了运动轴的高速运动;其次,位置指令半闭环模式完全依赖于驱动器的控制算子来实现位置闭环控制,而无法运用控制器(系统)更先进的控制算法来优化运动轴的瞬态性能,即使规划出理想的高速运动轨迹,也因为跟随性能不佳而无法实现其运动.因此,在设计高速抬刀控制系统的控制平台时,应将实现轴的高速运动放在首位,确定并构建满足高速运动要求的指令模式、控制系统与相应的伺服执行机构.同时,运动轴必须具备快速响应能力与优良的信号跟随性能,这是因为高速抬刀运动需要具备较高的加速度,以提高对加工屑的搅拌、混合与带出效果,减少抬刀运动所耗费的时间,从而提高加工效率[5].提高运动轴瞬态性能的策略为:①在执行机构中采用频响与灵敏度更高、驱动性能更好的驱动平台而实现轴的伺服控制;②基于先进控制策略或算法而实现闭环控制的控制器(系统),通过响应性能的测试而优化控制算法中的相关系数,以提高运动轴的瞬态性能.前者需要采用诸如大功率直线电机、精密直线平台等昂贵设备而成本较高;后者侧重于使用软件平台来改善性能,并基于现有硬件系统而实现运动轴瞬态性能的最优化.高的加速度,容易带来高速抬刀运动的速度不连续、过冲量大及机械冲击等问题,对伺服加工将产生负面影响,因而需要合理规划抬刀运动的加、减速过程.首先应确定抬刀过程加、减速曲线的类型.对比直线、抛物线及样条曲线等速度规划曲线发现,S形曲线具有峰值加速度高、加速初期与减速末期的加速度低、速度平滑连续等特点,能够保证较高加速度的同时抑制冲击,适用于优化高速抬刀的加、减速过程[6-9].此外,速度曲线的形状应结合系统的实际响应与指令跟随性能来设计.如果响应不够快,指令跟随误差较大,则在设计中降低速度曲线的平均曲率,以保证较好的跟随性能;如果机械冲击明显,则对“过渡阶段”(启动、加速变匀速、匀速变减速、停止)的速度连续性进行优化处理.鉴于此,本文设计了基于可编程运动控制器的电火花加工高速抬刀控制系统,并将其用于DK7140型商用电火花成形加工机床中.2 基于PMAC的EDM高速抬刀控制系统 高速抬刀功能是EDM数控系统的一部分,对其控制平台的设计即为对数控系统平台的设计.PMAC具备实现各类曲线插补、基于PID及其扩展算法的伺服控制、64个软可编程逻辑控制器(PLC)异步执行等各类运动与过程的控制功能,在数控机床、机器人及医疗设备等领域得到了广泛应用,并成为EDM数控系统理想的开发平台[10-11].PMAC不仅能够实现间隙电压检测、伺服进给与回退运动控制、多轴联动控制与加工电源控制等EDM关键技术[12-13],而且能够通过构建全闭环速度指令的控制体系,基于先进的PID控制算法优化运动轴动态性能,以及自行规划满足设计要求的加、减速曲线,从而实现运动轴的高速、高加速度运动.因此,本文EDM高速抬刀控制系统的硬件平台采用PMAC.2.1 全闭环速度指令的控制体系 PMAC可以通过PULSE/DIR、DAC和PWM等多种指令信号来控制各型号电机,并接收增量/绝对式编码器、直线/圆形光栅尺、激光干涉仪等反馈系统的位置反馈.基于DAC差分电压指令信号与7741 第9期梁 速,等:基于可编程运动控制器的电火花加工高速抬刀控制系统 光栅系统构建的全闭环速度指令的控制模式能够提高系统的定位精度;同时,由于将速度指令作为速度/扭矩参考信号输入伺服驱动器,使得理论上的运动轴最大速度或最大加速度达到伺服电机输出最大转速或最大扭矩时的水平,从而具备了高速运动的能力;此外,利用PMAC的PID控制算法,并借助于PEWIN32Pro软件来调节控制器参数,使得运动轴具备了优良的响应特性与信号跟随性能.PMAC的ACC-8P/D附件是用于输出DAC模拟量指令信号的外接端子板,以实现4/8通道(轴)的反馈信号输入、指令信号输出、电机使能、回零与限位信号接收等功能.其输出的DAC信号具有16位数模转换精度,幅值范围为-10~+10V,幅值分辨率为300μV/bit.反馈通道可接收单端/差分形式的编码器信号,通过参数设置而实现正、反方向4倍分频解码[14].本文以PMAC运动控制器及其ACC-8P/D附件为核心来构建控制系统的硬件体系,基于PMAC的EDM高速抬刀控制体系结构如图1所示.此外,还需要设置PMAC的相关变量,以实现全闭环速度指令的控制[10].2.2 运动轴伺服动态性能优化 基于PMAC系统设计了PID+速度前馈+加速度前馈的复合闭环控制算法,如图2所示.其中,引入前馈控制(1、2阶微分环节),可以在保证闭环图1 EDM高速抬刀控制体系结构图Fig.1 Scheme of high-speed jump motion controlsystem for EDM系统稳定性的前提下提高对指令信号的复现能力与精度[12].系统的比例增益Kp、积分增益Ki、微分增益Kd、速度前馈系数Kvff、加速度前馈系数Kaff以及积分模式可根据系统的实际响应性能进行优化调整.PMAC系统提供了PEWIN32Pro软件,以实现对PID参数的调节.PEWIN32Pro能够提供阶跃位置、抛物线速度等多类型目标指令输出,并根据实际反馈而测算系统的各项瞬态性能指标;同时,可直观地绘制出指令与响应信号的曲线图,以便于调试人员对控制器各参数的优化调整.图2 复合闭环控制算法Fig.2 Compound closed-loop control algorithm 结合商用DK7140型EDM机床的主轴系统,基于PID+速度前馈+加速度前馈的复合闭环控制算法,并借助于PEWIN32Pro软件进行了主轴动态性能的测试.实验分别采用阶跃位置与抛物线速度作为参考指令而测试系统的响应.其中:阶跃指令的单向位移为0.1mm,持续时间为500ms;抛物线指令的峰值速度分别为1.8mm/s(正向)、1.4mm/s(负向),持续时间为800ms.调试优化后,系统的各项瞬态性能指标分别为:上升时间10ms,调整时间33ms,最大超调量3.2%,自然频率32Hz,阻尼比0.7,跟随误差-6~5μm.经调试后,主轴的响应能力与指令的跟随性能均达到了理想的水平.2.3 抬刀运动S形曲线加减速规划 系统采用S形曲线设计抬刀运动的加、减速过程.PMAC提供了基于特征参数ts、ta与vmax而自行规划S曲线、加减速的插补器,其速度规划原理如图3所示.图中,ts为S曲线加、减速阶段所需的时间;ta为整个加、减速过程所需的时间,vmax为经过S曲线加速后所达到的最大速度.特征参数的优化设计需要结合系统的实际响应:一般而言,vmax较低时,应选择较小的ts与ta值;反之,则应选择较大的ts与ta值;同时,在保证高速性能的前提下,尽量缩小ts与ta值(增大加速度,减小加速行程),但ts与ta过小,又会带来机械冲击、跟随误差和过冲量大等8741上 海 交 通 大 学 学 报第46卷 问题.因此,需要结合系统实际的响应速度、跟随误差以及现场运动轴的冲击程度来设定ts、ta.本系统采用以下跟随误差约束设定方法来实现对特征参数的优化设计.图3 由ts、ta及vmax决定的S形加减速曲线Fig.3 S-shape acceleration/deceleration curvedefined by ts,taand vmax 跟随误差约束设定方法的原理如下:由于高速抬刀回复动作的减速过程将使运动轴产生一定程度的过冲,为了不使过冲影响加工区域(即防止进入放电间隙),在不同的vmax下,系统为过冲规划出相应行程的缓冲区.当减速规划曲线和实际跟随曲线(利用系统数据采集功能所绘)确定时,也确定了跟随误差曲线,过冲量则可以通过离散数值积分的方法粗略计算,因而可以确定跟随误差曲线(极大值)与过冲量粗略计算值的数值关系(比例系数);反之,通过预先设定缓冲区行程(过冲裕量)而确定减速过程跟随误差极大值的上限,并将其作为设定特征参数的约束条件.进一步通过反复调试运动轴的回复减速过程,以确定特征参数而得到较为理想的实际速度曲线.其具体方法为:首先,确定对应不同vmax的跟随误差极大值,在反复测试响应性能的过程中逐渐减小ts与ta,使得跟随误差极大值逐渐增大,直至接近于其上限.如果冲击不明显,则由此约束条件所确定的ts与ta既满足了较高的加速度,又具备了良好的跟随性能,且其过冲量也在设计范围内;如果出现较为明显的冲击,表明减速抛物线阶段的加速度变化过于剧烈,应适当增大ts值而缓解消除.基于上述原理和方法,结合DK7140型EDM机床实现了主轴高速抬刀运动,其抬刀回复减速运动的vmax与缓冲区行程及跟随误差极大值的对应关系如图4所示,vmax与所对应的ts、ta值的关系如图5所示.可以看出,当vmax=200mm/s时,所设计的ts=22ms,ta=50ms.为了检验其加速性能,利用系统的数据采集功能对抬刀加速过程的实际速度和跟随误差进行了采样分析(采样周期为2.5ms),其结果见图6.可见,主轴经加速后达到了200mm/s的运动速度,峰值加速度为9.68m/s2,最大跟随误差小于120μm,抬刀加速行程约5.3mm,抬刀回复减速运动的过冲量小于0.2mm,并无明显的冲击.由此可以看出,其主轴具备优良的高速、高加速度的运动性能.图4 缓冲区行程及跟随误差极大值与vmax的关系Fig.4 vmaxand the buffer distance and maximumvalue of following error图5 vmax及其对应的ts与taFig.5 vmaxand the corresponding tsand ta图6 主轴抬刀加速过程的指令速度和实际速度与跟随误差(vmax=200mm/s)Fig.6 Actual speed and following error in accelerationcourse of main axis jump motion(vmax=200mm/s)9741 第9期梁 速,等:基于可编程运动控制器的电火花加工高速抬刀控制系统 3 实验与结果 为了验证高速抬刀控制系统的实际加工性能,基于PMAC设计了包含定时抬刀功能的伺服进给回退运动程序,并结合商用DK7140型EDM机床而实现了高速抬刀EDM功能.同时,运用高速抬刀进行了窄槽加工实验,以检验其加工性能与效果. 窄槽是典型的高深宽比型腔,由于通道狭窄而使得加工时的排屑困难.通过窄槽加工实验,能够有效地检验抬刀运动的加工性能.实验采用尺寸为60mm×2mm×120mm(长×宽×深)、锥度为1°的石墨电极在45#钢工件表面加工窄槽,加工所采用的电参数如下:空载电压120V,最大加工电流12A,脉宽120μs,脉间60μs.同时,基于商用窄槽窄缝加工专用机床,采用相同的电极与工件并设置相同的电参数进行了窄槽加工实验.其实验性能的对比见表1.可见,与传统的中、低速抬刀系统相比,高速抬刀系统可使窄槽加工的最大深度与加工效率成倍提高.高速抬刀控制系统所加工的深100mm的窄槽样件及加工后的石墨电极如图7所示.表1 窄槽加工实验性能对比Tab.1 Performance comparison in narrow slot processing experiment机 床最大抬刀速度/(m·min-1)抬刀间隔/s抬刀高度/mm最大加工深度/mm加工效率/(mm·h-1)深度30~40mm深度50~100mm商用窄槽窄缝加工机床3 0.2~1.5 2~9 35~40 1.58-高速抬刀系统12 0.5~2.0 5~30≥100 7.50 4.62图7 深窄槽加工样件及加工后的石墨电极Fig.7 Image of the machined narrow slot and the graphiteelectrode after processing4 结 语 本文针对EDM高速抬刀功能控制系统的设计要求,构建了基于PMAC的全闭环速度指令模式的控制体系,通过设计PID+前馈控制的闭环控制算法、利用PEWIN32Pro调节控制器参数,得到了具有优良伺服动态性能的运动轴,并采用S形曲线规划了高速抬刀的加、减速过程.通过将控制系统应用于商用DK7140型EDM机床,实现了主轴最高速度达200mm/s、最大加速度约9.68m/s2的稳定高速抬刀运动.同时,进一步通过窄槽加工实验,验证了高速抬刀系统可使窄槽加工的最大加工深度与加工效率成倍提高,并具有良好的加工性能.参考文献:[1] 赵万生,刘晋春,袁哲俊,等.抬刀对电火花加工稳定性的影响及其自适应控制[J].电加工与模具,1990(1):3-8. ZHAO Wan-sheng,LIU Jin-chun,YUAN Zhe-jun,et al.Impact of tool-lifting on machining stability andits self-adaptive control[J].Electromachining andMould,1990(1):3-8.[2] 周明,韩福柱.电火花加工自适应控制系统的研究[J].电加工与模具,2008(6):16-20. ZHOU Ming,HAN Fu-zhu.Study of adaptive con-trol system for EDM process[J].Electromachiningand Mould,2008(6):16-20.[3] 刘晋春,白基成,郭永丰.特种加工[M].北京:机械工业出版社,2008:12-52.[4] Serkan C,Akira O,Yoshiyuki U.Effect of debrisdistribution on wall concavity in deep-hole EDM[J].JSME International Journal,2004,47(2):553-557.[5] 金子雄二.直线电动机驱动的电火花加工机床的性能[J].模具工业,2002(4):54-58. Kaneko Y.Performances of the EDM processingmachine driven by linear motor[J].Die and MouldIndustry,2002(4):54-58.[6] YAN Cun-liang,DU Dao-shan,LI Cong-xin.Designof a real-time adaptive interpolator with parametercompensation[J].International Journal of AdvancedManufacturing Technology,2007,35(1-2):169-178.[7] 赵巍,王太勇,万淑敏.基于NURBS曲线的加减速控制方法研究[J].中国机械工程,2006,17(1):1-3. ZHAO Wei,WANG Tai-yong,WAN Shu-min.Ac-celeration-deceleration control method based onNURBS curve[J].China Mechanical Engineering,0841上 海 交 通 大 学 学 报第46卷 2006,17(1):1-3.[8] 姚哲,冯景春,王宇晗.面向五轴加工的双NURBS曲线插补算法[J].上海交通大学学报,2008,42(2):235-238,244. YAO Zhe,FENG Jing-chun,WANG Yu-han.DualNURBS curve interpolation algorithm for 5-axis ma-chining[J].Journal of Shanghai Jiaotong University,2008,42(2):235-238,244.[9] WAN Da-ping,WANG Shi-long,ZHU Cai-chao,et al.Feedratescheduling and jerk control algorithmfor high-speed CNC machining[J].InternationalJournal of Manufacturing Technology and Manage-ment,2009,17(3):216-231.[10] Delta Tau Data Systems,Inc.PMAC user manual[M].USA:Delta Tau Data System Inc,1998.[11] 贾振元,任小涛,刘巍,等.大深径比微小孔快速电火花加工系统[J].光学精密工程,2009,17(12):3055-3061. JIA Zhen-yuan,REN Xiao-tao,LIU Wei,et al.Rapid EDM systems for micro and small holes withhigh-aspect-ratio[J].Optics and Precision Engineer-ing,2009,17(12):3055-3061.[12] 李论.基于实时Linux的六轴联动电火花加工数控系统[D].哈尔滨:哈尔滨工业大学机电工程学院,2004.[13] 郭锐,赵万生,李论,等.基于Linux的微细电火花加工数控系统的研究[J].计算机集成制造系统,2007,13(2):370-374. GUO Rui,ZHAO Wan-sheng,LI Lun,et al.Microelectrical discharge machining CNC system based onLinux[J].Computer Integrated Manufacturing Sys-tems,2007,13(2):370-374.[14] Delta Tau Data Systems,Inc.PMAC software refer-ence manual[M].USA:Delta Tau Data System Inc,1998. (上接第1470页)[11] Wang Wu-rong,He Chang-wei,Zhao Zhong-hua,etal.The limit drawing ratio and formability predictionof advanced high strength dual-phase steels[J].Materials and Design,2011,32(6):3320-3327.[12] 史刚,王武荣,羊军,等.1 000MPa级双相钢薄板极限成形性能研究[J].上海交通大学学报,2011,45(11):1653-1656.SHI Gang,WANG Wu-rong,YANG Jun,et al.Study on limit formability of 1 000MPa dual phasesteel[J].Journal of Shanghai Jiaotong University,2011,45(11):檿檿檿檿檿檿檿檿檿檿檿檿檿檿檿檿檿檿檿檿檿檿檿檿檿檿檿檿檿檿檿檿檿檿檿檿檿檿檿檿檿檿檿檿檿檿檿檿檿1653-1656. (上接第1475页)[6] 张彦,来新民,朱平,等.复合材料铺层板低速冲击作用下损伤的有限元分析[J].上海交通大学学报,2006,40(8):1348-1353. ZHANG Yan,LAI Xin-min,ZHU Ping,et al.Thefinite element analysis of low-velocity impact damagein composite laminated plates[J].Journal of Shang-hai Jiaotong University,2006,40(8):1348-1353.[7] Tita V,de Carvalho J,Vandepitte D.Failure analy-sis of low velocity impact on thin composite lami-nates:Experimental and numerical approaches[J].Composite Structure,2008,83(4):413-428.[8] Liu P F,Zheng J Y.Progressive failure analysis ofcarbon/epoxy composite laminates using continuumdamage mechanics[J].Material Science and Engi-neering A,2008,485(1-2):711-717.[9] Linde P,Pleitner J,de Boer H,et al.Modelling andsimulation of fibre metal laminates[C]//ABAQUSUsers Conference.Boston:Dassault Systemes Compa-ny,2004:421-439.[10] Lapczyk I,Hurtado J A.Progressive damage model-ing in fiber-reinforced materials[J].Composites PartA:Applied Science and Manufacturing,2007,38(11):2333-2341.1841 第9期梁 速,等:基于可编程运动控制器的电火花加工高速抬刀控制系统 。
电火花机床操作规程
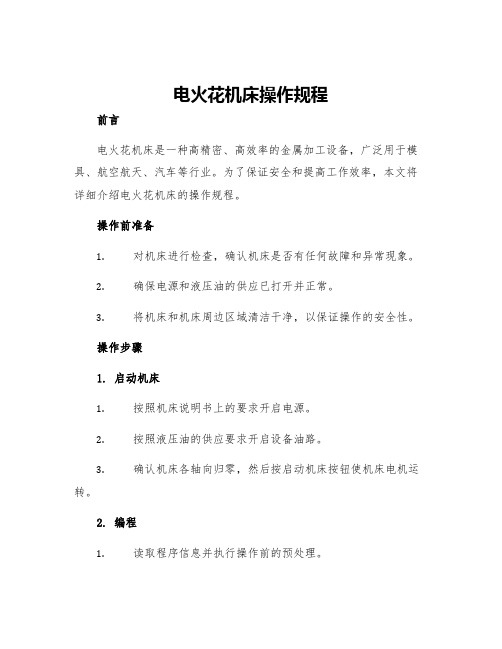
电火花机床操作规程前言电火花机床是一种高精密、高效率的金属加工设备,广泛用于模具、航空航天、汽车等行业。
为了保证安全和提高工作效率,本文将详细介绍电火花机床的操作规程。
操作前准备1.对机床进行检查,确认机床是否有任何故障和异常现象。
2.确保电源和液压油的供应已打开并正常。
3.将机床和机床周边区域清洁干净,以保证操作的安全性。
操作步骤1. 启动机床1.按照机床说明书上的要求开启电源。
2.按照液压油的供应要求开启设备油路。
3.确认机床各轴向归零,然后按启动机床按钮使机床电机运转。
2. 编程1.读取程序信息并执行操作前的预处理。
2.选择相应的程序,并进行必要的参数设置。
3.将工件夹紧在工作台上,将机床的刀具调整到适当的位置。
3. 加工操作1.运行程序,开始加工操作。
2.在加工过程中,随时观察刀具磨损和工件精度情况,及时修改程序或调整刀具位置。
3.遵循安全操作规程,禁止在加工时做其他事情,不要过度注视机床操作。
4. 关闭机床1.加工完成后,按停止按钮,停止机床电机运转。
2.清洁工件和机床上的剩余材料。
3.关闭液压油路和电源。
安全操作规程1.在操作机床过程中,禁止穿戴松散的衣物、首饰等物品,以免被卷入机床内部。
2.避免在机床运转时贴近机床,尤其是刀具运动轨迹处。
3.不要在操作机床时摆放手工工具或用手指直接接触刀具。
4.避免在机床换刀或刀具修整时操作,以免发生意外伤害。
结论以上即是电火花机床操作规程,希望可以为新手操作者提供参考,同时在操作机床时要格外注意安全。
电火花成型加工机床操作规程

电火花成型加工机床操作规程第一章:总则第一条这个操作规程是为了保证电火花成型加工机床的安全性、稳定性和生产效率,规范操作人员的行为。
第二条本操作规程适用于电火花成型加工机床的操作人员。
第三条操作人员必须具备相关的机械加工知识和技能,并且经过相应的培训和考核合格,方可上岗操作。
第四条操作人员必须严格按照本操作规程的要求执行操作,严禁违反操作规程进行操作。
第五条所有的操作必须在机械设备停止工作的情况下进行。
第二章:安全操作规程第六条操作人员必须佩戴个人防护装备,如安全帽、护目镜、防护手套等,并保持整洁。
第七条操作人员必须熟悉电火花成型加工机床的结构和工作原理,掌握操作技能。
第八条在操作过程中,必须确保电火花成型加工机床的稳定性,切勿乱动和撞击机床。
第九条操作人员在进行操作之前,必须检查机床的各项安全装置是否完好,如紧急停机按钮、轴向限位开关等。
第十条操作人员在清洗机床时,必须切断电源并等待所有运动部件停止运动之后,才能进行清洗。
第十一条操作人员在更换刀具或电极时,必须关闭电源并确保电极与工作件之间没有电气连接。
第三章:操作规程第十二条操作人员必须根据工艺要求选择合适的电极,并在装夹时保证紧固牢固。
第十三条操作人员必须根据工艺要求选择合适的加工参数,如放电电流、放电时间等,并设置在设备上。
第十四条操作人员在进行加工过程中,必须确保工作区域清洁,防止杂物影响加工质量。
第十五条操作人员在进行加工过程中,必须保持专注,密切观察加工过程中的任何异常情况,如放电不稳定、电极磨损等,并及时停机进行检修。
第十六条操作人员在加工过程中,必须按照设备的操作流程进行操作,如加工开始、加工暂停、加工停止等。
第十七条操作人员在加工完成后,必须关闭电源并注销操作记录。
第四章:维护保养规程第十八条操作人员在使用完毕后,必须对电火花成型加工机床进行清洁,清除加工过程中的废渣和杂物。
第十九条操作人员在使用完毕后,必须检查机床的润滑系统是否正常,并进行相应的维护保养。
电火花数控线切割机床操作规程

电火花数控线切割机床(jīchuáng)操作规程1.打开电脑及显示器,按HY编程操作要求(yāoqiú),输入加工程序。
2.打开驱动(qū dònɡ)电源开关,用鼠标点击“模拟(mónǐ)”键,机床(jīchuáng)X、Y、U、V四轴应按规定方向联动。
3.装夹好待切割工件,启动运丝按钮。
运丝电机转动加油润滑贮丝桶拖板导轨及贮丝桶齿轮组。
启动水泵按钮,线架下喷水嘴应有切削液喷出,切削液必须顺钼丝流动。
4.根据切割工件厚度计光洁度,速度要求,调节好高频电源参数,打开高频电源开关。
5.用鼠标点击“加工”按键。
机床系统进入加工状态。
6.先用较慢的速度进给,待钼丝进入工件后,对高频参数再次微调,直至加工电流、电压稳定为止。
7.工件加工完毕后,系统报警自动关机。
(切断机床电源)。
注意事项:1.开机前检查切削液液位、软管连接是否牢固。
摇动工件台纵横手轮是否灵活摇动贮丝桶是否灵活。
2.开启运丝检查换向是否可靠。
3.应及经常检查导轮、进电块、轴承是否磨损出沟槽等缺陷,如影响到加工稳定性和加工精度,应及时更换。
4.加工开始后半小时,时刻观察切削液是否偏离钼丝,如出现偏离现象须及时调整。
5.装夹工件必须在四周留有余地,避免运行过程中工作台与线架发生碰撞。
6.内容总结7.8.(1)电火花数控线切割机床操作规程9.打开电脑及显示器,按HY编程操作要求,输入加工程序10.(2)运丝电机转动加油润滑贮丝桶拖板导轨及贮丝桶齿轮组11.(3)启动水泵按钮,线架下喷水嘴应有切削液喷出,切削液必须顺钼丝流动12.(4)根据切割工件厚度计光洁度,速度要求,调节好高频电源参数,打开高频电源开关13.(5)先用较慢的速度进给,待钼丝进入工件后,对高频参数再次微调,直至加工电流、电压稳定为止14.。
电火花数控线切割机床工作原理
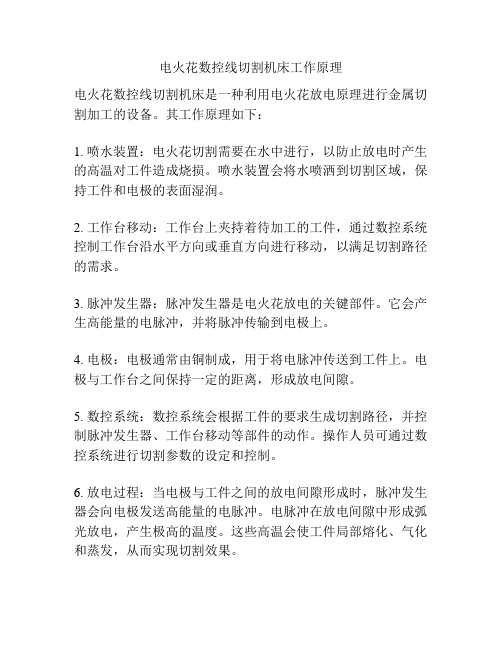
电火花数控线切割机床工作原理
电火花数控线切割机床是一种利用电火花放电原理进行金属切割加工的设备。
其工作原理如下:
1. 喷水装置:电火花切割需要在水中进行,以防止放电时产生的高温对工件造成烧损。
喷水装置会将水喷洒到切割区域,保持工件和电极的表面湿润。
2. 工作台移动:工作台上夹持着待加工的工件,通过数控系统控制工作台沿水平方向或垂直方向进行移动,以满足切割路径的需求。
3. 脉冲发生器:脉冲发生器是电火花放电的关键部件。
它会产生高能量的电脉冲,并将脉冲传输到电极上。
4. 电极:电极通常由铜制成,用于将电脉冲传送到工件上。
电极与工作台之间保持一定的距离,形成放电间隙。
5. 数控系统:数控系统会根据工件的要求生成切割路径,并控制脉冲发生器、工作台移动等部件的动作。
操作人员可通过数控系统进行切割参数的设定和控制。
6. 放电过程:当电极与工件之间的放电间隙形成时,脉冲发生器会向电极发送高能量的电脉冲。
电脉冲在放电间隙中形成弧光放电,产生极高的温度。
这些高温会使工件局部熔化、气化和蒸发,从而实现切割效果。
7. 加工过程控制:数控系统会根据设定的切割路径,控制工作台按照预定的速度和方向进行移动。
通过不断的放电,工件将逐渐被切割成设计好的形状。
8. 加工完成后:加工完成后,工作台停止移动,电极与工件之间的放电间隙关闭,切割过程结束。
操作人员可取下切割好的工件,并进行后续处理。
总而言之,电火花数控线切割机床利用电火花放电原理进行金属切割,通过数控系统控制脉冲发生器和工作台的动作,实现精确的加工过程。
基于嵌入式arm和dsp的电火花线切割机床控制系统设计

基于嵌入式ARM 和DSP 的电火花线切割机床控制系统设计Wire cut electrical discharge machining control systemdesign based on embedded ARM and DSP李 鸿,梁 荣LI Hong, LIANG Rong(宁波工程学院 杭州湾汽车学院,宁波 315336)摘 要:针对电火花线切割单CPU框架监控功能有限、线切割加工精度和效率低等问题,设计一种支持双CPU协作的高效率和高精度电火花线切割机床控制系统。
硬件上以ARM为上位机、DSP为下位机,由ARM集中处理线切割加工过程工艺参数,DSP实时控制工作台多轴联动和线电极加工节拍,通过扩展I/O全覆盖监控电火花线切割机床机电系统。
软件上植入多任务实时RT-Linux操作系统,通过多任务实时调度、人机交互和高速走丝线切割实时控制实现在线插补、齿隙补偿和多轴联动等多进程任务协调。
调试表明,双CPU协作系统运行可靠,能有效监测和反馈线切割加工过程机电系统运行状态,改善在线插补与多轴联动等协同控制性能。
关键词:电火花线切割;ARM;DSP;RT-Linux;控制系统中图分类号:TP23 文献标识码:B 文章编号:1009-0134(2019)11-0084-04收稿日期:2018-12-09基金项目:浙江省大学生科技创新活动计划(新苗人才计划)项目(2018R428030)作者简介:李鸿(1997 -),男,浙江宁波人,本科,主要从事材料成型及控制工程研究工作。
0 引言电火花线切割是利用钼丝电极与金属工件间脉冲放电产生的局部、瞬态高温以实现对导电材料的电蚀加工,在成型过程中电极不与工件直接接触,且无明显的切削力作用,加工性能也不受材料硬度、强度和韧性等因素影响,具有加工精度高、材料适用性强和应用范围广等优点[1~3]。
电火花线切割机床是影响工件电蚀加工精度和效率的关键,目前国外多采用慢走丝线切割机,其加工精度约2μm 、表面粗糙度Ra 可达0.8μm ,而我国普遍使用高速走丝线切割机,其工作原理不同,实际加工效果也与慢走丝线切割存在较大差距。
数控电火花加工的主要工艺指标及其提高途径
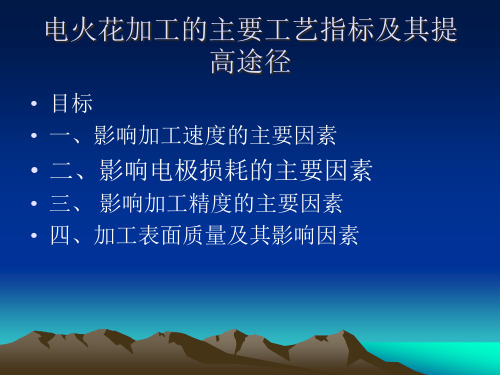
电规准的影响
所谓电规准,是指电火花加工时选用的电 加工参数,主要有脉冲宽度ti(μs)、脉冲间 隙to(μs)及峰值电流Ip等参数。
• 一. 脉冲宽度对加工速度
的影响
脉冲宽度增加,加工速度随 之增加,因为随着脉冲宽度的增加, 单个脉冲能量增大,使加工速度提 高。但若脉冲宽度过大,加工速度 反而下降(如图1)。这是因为单个脉 冲能量虽然增大,但转换的热能有
• 因素 脉冲宽度 峰值电流
表3-1 影响电极损耗的因素
说
明
脉宽愈大,损耗愈小,至一定数值后,损耗可降低至小 1%
峰值电流增大,电极损耗增加
减少损耗条件 脉宽足够大 减小峰值电流
加工面积
影响不大
大于最小加工面积
极性
影响很大。应根据不同电源、不同电规准、不同工作液、 不同电极材料、不同工件材料,选择合适的极性
/% 0.8 0.6 0.4 0.2
电 极 —铜 工 件 —T10A 加 工 极 性 —负
ti= 1200s
0 100 200 300 400 500 600 to / s
脉冲间隔对电极相对损耗的影响
• 4) 加工极性的影 响
一般情况下,采用石 墨电极和铜电极加工 钢时,粗加工用负极 性,精加工用正极性。 但在钢电极加工钢时, 无论粗加工或精加工 都要用负极性,否则 电极损耗将大大增加。
值电流,等于加大单个脉冲能
量,所以加工速度也就提高了。
但若峰值电流过大(即单个脉冲 放电能量很大),加工速度反而
下降。此外,峰值电流增大将
降低工件表面粗糙度和增加电
电火花加工机床操作说明

电火花加工机床操作说明
电火花加工机床是一种精密加工设备,通常用于加工硬质材料,如
金属和合金。
本文将详细介绍电火花加工机床的操作方法及注意事项。
一、准备工作
1. 确保电火花加工机床的所有安全装置处于正常工作状态。
2. 检查电火花加工机床的工作台面和夹持装置,确保固定工件的牢
固性。
3. 检查电火花加工机床的电源线路,确保接地良好。
二、操作步骤
1. 打开电火花加工机床的主电源开关,启动机床。
2. 将工件夹持在工作台面上,并调整工件的位置和姿态。
3. 根据加工要求选择合适的加工参数,如放电电流、放电时间等。
4. 启动电火花加工机床的加工程序,开始加工工件。
5. 观察加工过程中的电极磨损情况,及时调整电极位置。
6. 加工完成后,关闭电火花加工机床的加工程序,停止机床。
三、注意事项
1. 在操作电火花加工机床时,必须佩戴防护眼镜和手套,确保人身
安全。
2. 加工过程中严禁触碰电极和工件,以免发生意外。
3. 定期对电火花加工机床进行维护保养,保持设备的良好状态。
4. 加工结束后,及时清洁工作台面和加工区域,保持整洁。
通过本文的操作说明,相信您已经了解了如何正确操作电火花加工
机床,希望您能够按照以上步骤进行操作,确保加工效果和操作安全。
祝您工作顺利!。
menual DSP 控制双工序 操作步骤
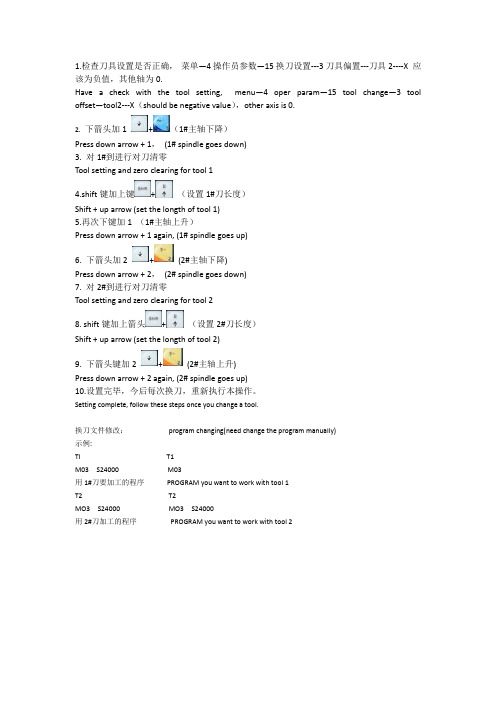
1.检查刀具设置是否正确,菜单—4操作员参数—15换刀设置---3刀具偏置---刀具2----X 应该为负值,其他轴为0.Have a check with the tool setting, menu—4 oper param—15 tool change—3 tool offset—tool2---X(should be negative value),other axis is 0.2.下箭头加1 +(1#主轴下降)Press down arrow + 1,(1# spindle goes down)3. 对1#到进行对刀清零Tool setting and zero clearing for tool 14.shift键加上键+(设置1#刀长度)Shift + up arrow (set the longth of tool 1)5.再次下键加1 (1#主轴上升)Press down arrow + 1 again, (1# spindle goes up)6. 下箭头加2 +(2#主轴下降)Press down arrow + 2,(2# spindle goes down)7. 对2#到进行对刀清零Tool setting and zero clearing for tool 28. shift键加上箭头+(设置2#刀长度)Shift + up arrow (set the longth of tool 2)9. 下箭头键加2 +(2#主轴上升)Press down arrow + 2 again, (2# spindle goes up)10.设置完毕,今后每次换刀,重新执行本操作。
Setting complete, follow these steps once you change a tool.换刀文件修改:program changing(need change the program manually)示例:TI T1M03 S24000 M03用1#刀要加工的程序PROGRAM you want to work with tool 1T2 T2MO3 S24000 MO3 S24000用2#刀加工的程序PROGRAM you want to work with tool 2。
抬刀运动对电火花加工电蚀产物浓度的影响_储召良

工件 脉冲 + 电源 工作台 工作液箱 数字示 波器 主 轴 片状电极 PC
ROGOWSKI 线圈
图1
试验系统示意图
1.2
抬刀运动对加工性能的影响 不同抬刀运动参数下的窄槽电火花加工试验
数据列于表 2。 从表 2 可以看出不同抬刀速度和高 度对窄槽加工性能的影响。
摘要:电极做周期性抬刀运动能够降低加工区域内的电蚀产物浓度,进而提高有效放电率和加工稳定性。为研究抬刀运动 对间隙中电蚀产物浓度等的影响, 选用不同的抬刀参数进行窄槽加工试验与分析; 采用计算流体动力学方法(Computational fluid dynamics, CFD)对高速抬刀和普通抬刀运动分别进行了仿真模拟,探讨二者对加工间隙中电蚀产物浓度的不同影响。 模拟结果为进一步理解抬刀运动对加工性能的影响提供了重要的参考。 关键词:电火花加工 高速抬刀 电蚀产物浓度 深窄槽加工 中图分类号:TG661
为进一步理解以上试验结果的内在本质, 下面 将通过有限元方法模拟分析抬刀运动对加工间隙 中电蚀产物浓度变化的影响。
图 4 不同抬刀速度条件下有效放电频率
2.1
加工间隙流场建模 设待加工窄槽的宽度为 2 mm, 长度为 20 mm,
(1) 当加工的深度达到 5 mm 以后,不论是高 速还是低速抬刀, 随着槽深的增加, 放电间隙中的 电蚀产物均变得较难排出, 极间有效放电频率均有 不同程度的下降。抬刀速度为 5 m/min 时,极间的 有效放电频率下降最为明显,从开始加工时的 2 816 次/s 降到了 1 643 次/s。 (2) 抬刀速度高,则极间的有效放电频率也 高。抬刀速度为 5 m/min 的情况下,加工 5 mm 时 的有效放电频率为 1 643 次/s。随着加工深度的增 加, 有效放电率持续降低。 当加工深度达到 20 mm 时,有效放电频率降低至 1 035 次/s,与加工开始 时相比降幅超过 63%;而采用高速抬刀条件,抬 刀速度为 36 m/min 情况下,加工深度从 5 mm 增 加至 20 mm 过程中,有效放电频率基本上可以维 持在 2 000 次/s 左右,且始终保持在较高水平,加 工可以稳定持续地进行。
数控电火花加工常见问题解决办法!

数控电火花加工常见问题的解决办法!在工作中,电火花加工经常会遇到一些常见问题,那么如何解决呢?看完本文相信您就都懂了!1、加工效率低1)起始放电加工效率低-----电极尺寸缩放量(火花位)要大,自动编程才能选出更大电流的条件号。
型腔要尽可能进行预铣加工。
2)程序中间的放电加工段效率低-----各段条件之间的余量过多,可以适当减少各段之间的加工余量。
3)程序最后的精细放电加工段效率低-----使用定时加工功能来有效控制精加工时间(需要设定加工时间)。
4)面积输入过小-----系统以面积作为限制门槛,即使电极尺寸缩放量再大,由于面积太小,也不会产生大的放电条件。
此类情况,可以适当人为增大输入的面积值。
5)应用类型选择不正确-----比如实际是大型腔的加工而选择了“微细”应用类型。
6)加工优先权-----选择低损耗优先权则效率低,选择高效率优先权则速度快,损耗偏大。
7)放电、抬刀组合不合理-----根据加工状态,调整抬刀高度、放电时间与之匹配。
8)优化参数-----减少脉冲间隙P,加大伺服基准COMP。
9)改进工艺-----使用石墨电极,大幅度提升整体生产效率。
2、电极损耗大1)使用参数不当-----应使用优先权为低损耗的加工参数。
小电极可选用微细加工应用类型。
2)放电条件号太强-----对于尖小电极,不能使用大电流加工。
3)放电能量太小,加工效率低下导致电极长时间的放电而损耗-----如果电极损耗大的同时伴随加工速度太慢的情况,请提高加工效率。
4)电极材料不好-----使用纯度高的紫铜,或者使用损耗更低的洛铜甚至是铜钨合金作为电极材料。
5)脉冲宽度太小-----加大条件号中的脉冲宽度T,可以显著降低电极损耗。
6)脉冲波形-----使用低损耗,带有斜度的放电波形模式。
3、分中不准确,位置偏差1)使用传统的“电极碰工件进行分中”的方法,由于分中属于面接触,电极与工件之间存在的诸多因素都会影响分中精度-----推荐使用“基准球点对点进行分中”的定方法。
- 1、下载文档前请自行甄别文档内容的完整性,平台不提供额外的编辑、内容补充、找答案等附加服务。
- 2、"仅部分预览"的文档,不可在线预览部分如存在完整性等问题,可反馈申请退款(可完整预览的文档不适用该条件!)。
- 3、如文档侵犯您的权益,请联系客服反馈,我们会尽快为您处理(人工客服工作时间:9:00-18:30)。
20 06年第 6 期
舰 船 电 子 工 程
ll 7
化 。从定性 的观 点 来 看 , h越 大 而 t越 小 , 抬 刀 ; 则
通 用 的异 步 串行 接 口 (C) 串行 ( 步 ) 设 接 口 S I、 同 外
的作用越显著, 但是这样加工过程中有效放电的时 问比例就会随之降低 , 对于排屑状况 良好的加工过 程来说会降低加工效率。所以 , 在本文中设计 了两
C n r lS he o o f n r c s i g i DM s d o P o to c me f r To l t g P o e sn E Li i n Ba e n DS
中图分类号
Xi a C a g Yu p n Z n  ̄iu L n S u n fn a Tin h n n ig ag ha i h a ge g
C a snl  ̄ r T 6 l s l n H1
也可以是变化的。在抬刀调节中, 一次抬刀过程通
1 前言
在电火 花加 工中 , 工过 程 的稳定 性 是保证 各 加
常用抬刀高度 h 和抬刀周期 t 来描述 , 也可以用上 升时间 t和下降与加工 时间 t来描述。对于一个 。 d 确定的系统来说 , 抬刀的上升与下降速度一般是确 定 的, 因此上升时 问 t 的大小 即表示 了抬刀 的高 。 度; 下降和加工时间 t的大小 , d n 即可 间接表示每个
g g
^
0
2 抬 刀过 程
有抬刀调节的加工过程可用图 1 中的抬刀过 程来描述 , 在加工过程 中, 将主轴抬起一定高度再
暨 星 呈 肇
落 回原来位置 , 加工一段时间后再将主轴抬起又落
下 , 复这样 的 过程 , 反 即形 成 了周 期性 的抬 刀 加 工
过程。
图 1 电火花加工抬 刀过程示意图
20 06年第 6 期
基 于 D P的 电 火 花 加 工 中抬 刀 过 程 的 控 制 S
夏 天 常 云萍 臧 义华 林 双凤
100 ) 50 1
( 哈尔滨工程大学 自动化学院
哈尔滨
摘
要
介绍电火花加工中的抬刀过程 及其所涉及到 的参 数 , 出一种广泛适用 的加工 过程 的数学模型 , 推导 在此基础
(col f u m tn H ri E nei n e i , a i 100 ) Sho o t ao , ab er gU i rt H r n 50 1 Ao i n n v sy b
A s at Tet l n r e i a f t tdcdi t ae. nt ai a ot lc e ebsdo S a pto- bt c h o 雠i po  ̄n wsi l ir ue epprO ebs ,ncno shm a nD Pws u fr r o g e g r y no s nh h s r e
采用步进电动机带动丝杠 , 使主轴运动 , 软 用
1 2 光 耦 隔 离 , 实 现控 制 部 分 和驱 动 部 分 的 7 1 25 以
Hale Waihona Puke 种抬刀周期 , 这样既可 以兼顾排屑状况良好时较高
的加工速度 , 又可以保证排屑状况变差时有较好 的 加工稳定性 , 从而实现整个加工过程 中加工效率和 加工稳定性整体 的优化。
3 实现 方 法
在整个加工过程中 , 抬刀剧期可以是 固定 的,
抬刀的凋节可以通过改变抬刀高度 h 和抬刀 周期 t j 两者中的任一个来实现 , 也可以两者同时变
收稿 日期 :06年 4月 2 20 0日, 回日期 :06 7月 2 修 20 6U
维普资讯
上设计 以 D P为核心 的抬 刀过程 的控制方案 。在 D S4 7 S C 20 A应用开发 平台上用汇编 和 c语言编写 软件并 给出部分硬 件电 路。实验证明 , 方案 切实可行 , 该 对进一步研 发有一定 的参 考价 值。 关键词 D P 电火花 ; S; 步进电机
Tt6 i l
抬 刀周 期 的长短 。
项加工性能指标 的前提。而抬刀调节是 提高加工 稳定性的较为简单 、 有效的措施 , 同时抬 刀调节与 电规准之间完全独立, 对加工结果指标不会造成任 何不利的影响。因此抬刀调节是电火花加工过程 控制中广泛采用 的一种方法。本文主要介绍 了用
D P控制抬 刀过 程 的方法及 其软硬 件实 现 。 S
w r . h n tecrut n orso dn rcd r eegv n I poe oh v rc c l au . ad T e , i ia dc r pn igpoe uew r i .t rvdt a ep t a le h c e e a i v
Ke o d D P E M ,tp ig moo yw rs S , D s pn tr e
(P) C N总线接 口。这些 丰富 的片上资源 使 SI和 A 得 T S2 L2 0A在工业控制 中尤其是在 电机控 M 30 I47 ; 制应用中比传统 的单 片机 有着无 与伦 比的优势 。 也正是 因为这 一点 ,M 30Y20A正在 被 越 来 越 T S2I 47 广泛地应用 在工业控制 和电机控 制 的不 同领域 。 32驱动部分设计及执行部件 . 驱动 部 分 的所 有 输 入 都 采 用 较 为 廉 价 的
维普资讯
总第 1 5 6期
眦 船 电 于1 二程
S i e t nc E gn e n hp El r i n ie r g co i
;== = == === != !!! !! — ! !一 = 。 === === = =
V 12 o 6 0.6 N . 10 7