熔融石英球形粉对陶瓷型芯高温收缩的影响
熔融石英的导热系数
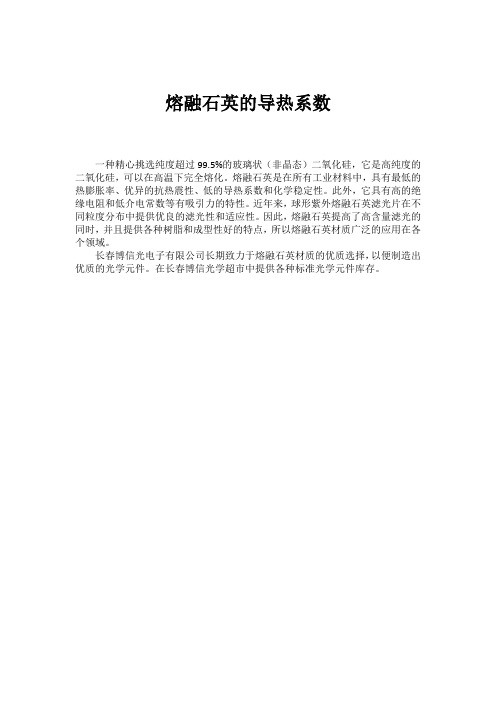
熔融石英的导热系数
一种精心挑选纯度超过99.5%的玻璃状(非晶态)二氧化硅,它是高纯度的二氧化硅,可以在高温下完全熔化。
熔融石英是在所有工业材料中,具有最低的热膨胀率、优异的抗热震性、低的导热系数和化学稳定性。
此外,它具有高的绝缘电阻和低介电常数等有吸引力的特性。
近年来,球形紫外熔融石英滤光片在不同粒度分布中提供优良的滤光性和适应性。
因此,熔融石英提高了高含量滤光的同时,并且提供各种树脂和成型性好的特点,所以熔融石英材质广泛的应用在各个领域。
长春博信光电子有限公司长期致力于熔融石英材质的优质选择,以便制造出优质的光学元件。
在长春博信光学超市中提供各种标准光学元件库存。
熔融石英的性能特点和使用..
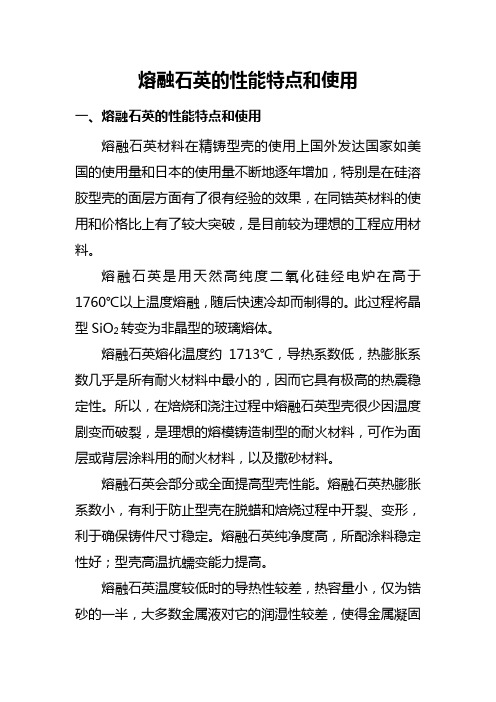
熔融石英的性能特点和使用一、熔融石英的性能特点和使用熔融石英材料在精铸型壳的使用上国外发达国家如美国的使用量和日本的使用量不断地逐年增加,特别是在硅溶胶型壳的面层方面有了很有经验的效果,在同锆英材料的使用和价格比上有了较大突破,是目前较为理想的工程应用材料。
熔融石英是用天然高纯度二氧化硅经电炉在高于1760℃以上温度熔融,随后快速冷却而制得的。
此过程将晶型SiO2转变为非晶型的玻璃熔体。
熔融石英熔化温度约1713℃,导热系数低,热膨胀系数几乎是所有耐火材料中最小的,因而它具有极高的热震稳定性。
所以,在焙烧和浇注过程中熔融石英型壳很少因温度剧变而破裂,是理想的熔模铸造制型的耐火材料,可作为面层或背层涂料用的耐火材料,以及撒砂材料。
熔融石英会部分或全面提高型壳性能。
熔融石英热膨胀系数小,有利于防止型壳在脱蜡和焙烧过程中开裂、变形,利于确保铸件尺寸稳定。
熔融石英纯净度高,所配涂料稳定性好;型壳高温抗蠕变能力提高。
熔融石英温度较低时的导热性较差,热容量小,仅为锆砂的一半,大多数金属液对它的润湿性较差,使得金属凝固层与型壳内表面间易产生间隙,热导率进一步减小,有利于壁薄铸件充型。
在高温下熔融石英的透明度高,能通过辐射传热,使其导热能力超过硅酸铝类壳。
而使铸件冷却较快,更易获得健全铸件。
铸件冷却时方石英又从高温型转变为低温型,同时体积产生骤变,使型壳出现无数裂纹,强度剧降,有利于脱壳进行。
熔融石英为酸性,能采用碱煮、碱爆等化学清砂方法去除型壳。
熔模铸造用熔融石英,其中SiO2所占的质量分数应为99.5%,配涂料用的粉料最好是270目或320目细粉占50%(质量分数),200目和120目粉各占25%(质量分数)。
①为0℃~1200℃间的膨胀系数平均值。
②400℃的热导率。
③1200℃热导率。
熔融石英及制品有三大特点:在所有耐火材料中,线膨胀系数最小(在1000℃的热胀率0.05);热导率最低,在1000℃热导率0.836W/(m·K)(0.02cal/cm·s·℃);抗热震性最好(在1200℃~水冷的抗震性),10次都不产生裂纹。
各类氧化物陶瓷烧结体积变化点

各类氧化物陶瓷烧结体积变化点一、概述氧化物陶瓷作为一种重要的结构材料,其烧结性能一直备受关注。
体积变化是认识氧化物陶瓷烧结行为的重要指标之一。
本文将对各类氧化物陶瓷在烧结过程中的体积变化点进行探讨。
二、硅酸盐陶瓷烧结体积变化点1. 石英陶瓷石英陶瓷在烧结过程中,通常在1200°C左右出现大小约0.2的体积收缩。
在1300°C左右会再次出现约0.5的体积收缩。
在1400°C以上,石英陶瓷的体积基本上稳定。
2. 镁铝硅酸盐陶瓷镁铝硅酸盐陶瓷在1000°C左右会出现约1的体积收缩。
在1100°C左右再度出现体积收缩,范围在0.5-1之间。
在1200°C以上,镁铝硅酸盐陶瓷的体积基本上保持稳定。
三、氧化物陶瓷烧结体积变化点1. 氧化铝陶瓷氧化铝陶瓷在1200°C左右会出现0.5-1的体积收缩。
在高温下,氧化铝陶瓷的体积基本上稳定,收缩的幅度不大。
2. 氧化锆陶瓷氧化锆陶瓷在1300°C左右会出现约0.5的体积收缩。
在1400°C以上,氧化锆陶瓷的体积基本上保持稳定。
四、复合氧化物陶瓷烧结体积变化点1. 氧化锆复合氧化钙陶瓷氧化锆复合氧化钙陶瓷在1300°C左右会出现约0.5的体积收缩。
在1400°C以上,氧化锆复合氧化钙陶瓷的体积基本上保持稳定。
2. 氧化锆复合氧化铝陶瓷氧化锆复合氧化铝陶瓷在1300°C左右会出现约1的体积收缩。
在1400°C以上,氧化锆复合氧化铝陶瓷的体积基本上保持稳定。
五、结论在烧结过程中,不同类型的氧化物陶瓷都会出现一定程度的体积收缩。
通过了解各类氧化物陶瓷在烧结过程中的体积变化点,可以更加深入地了解其烧结行为,为优化烧结工艺提供重要依据。
值得注意的是,以上数据仅供参考,实际应用中仍需根据具体情况进行调整。
希望本文对氧化物陶瓷烧结体积变化点的研究能够为相关领域的科研工作提供一定帮助。
熔融石英陶瓷的性能改进研究
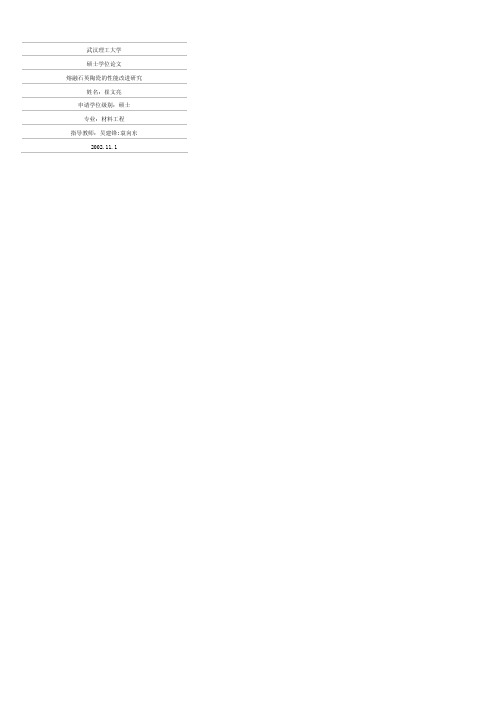
6.石英陶瓷坯体在干燥及烧成时收缩很小,一般小于5%,因此,石 英陶瓷易于制作大件制品。法国维苏威公司制作了长达5800ram的石英 陶瓷制品”1,国内山东中博先进材料股份有限公司制备的石英陶瓷制品 也达到4000ram以上。
7.石英陶瓷电性质很好。电阻很大,其介电常数与介电损耗角正切随 温度的变化都远远低于氧化铝等其他高温陶瓷,可用于绝缘材料,也是 导弹和雷达天线罩的良好材料‘61。
关键词:石英陶瓷,注凝成型,
Abstract
The preparation ofhigh strength high reliability fused silica ceramics formed bv
dynamic gel·casting process was studied.Factors influencing the procedures of
density is 1.96咖mj,tIle bending strength is 65.2MPa,the dielectric constant is
3.18,tg 5 is 5.3 x 10。4 with a difference ofless than 0.03 and scattering ofO.7%:the
石英陶瓷虽然有上述优良的特性,但与其他结构陶瓷相比,其强度 明显偏低,一般其抗弯强度为20.40MPa,抗压强度60.100MPa¨1,这个 强度作为耐火材料使用是足够了,但是作为工业陶瓷特别是结构陶瓷显 然是太低了,而且石英陶瓷材料与其他工业陶瓷材料如氧化铝、氮化硅 等相比,其强度要低很多,国内一般厂家制作的石英水口、坩埚等制品 的抗弯强度一般不足20MPa,山东中博先进材料股份有限责任公司生产 的石英陶瓷制品的强度较高,一般在25.35MPa之间。而氧化铝陶瓷、氮 化硅、氧化锆陶瓷的抗弯强度一般可分别达到380MPa、1200MPa、
熔融石英的性能特点和使用资料
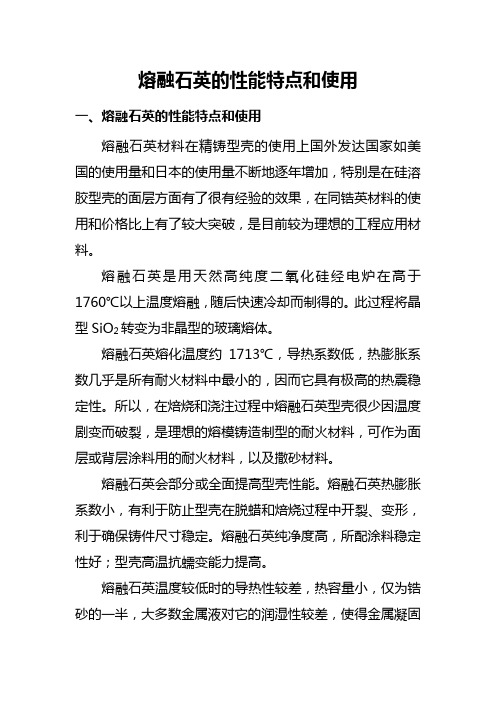
熔融石英的性能特点和使用一、熔融石英的性能特点和使用熔融石英材料在精铸型壳的使用上国外发达国家如美国的使用量和日本的使用量不断地逐年增加,特别是在硅溶胶型壳的面层方面有了很有经验的效果,在同锆英材料的使用和价格比上有了较大突破,是目前较为理想的工程应用材料。
熔融石英是用天然高纯度二氧化硅经电炉在高于1760℃以上温度熔融,随后快速冷却而制得的。
此过程将晶型SiO2转变为非晶型的玻璃熔体。
熔融石英熔化温度约1713℃,导热系数低,热膨胀系数几乎是所有耐火材料中最小的,因而它具有极高的热震稳定性。
所以,在焙烧和浇注过程中熔融石英型壳很少因温度剧变而破裂,是理想的熔模铸造制型的耐火材料,可作为面层或背层涂料用的耐火材料,以及撒砂材料。
熔融石英会部分或全面提高型壳性能。
熔融石英热膨胀系数小,有利于防止型壳在脱蜡和焙烧过程中开裂、变形,利于确保铸件尺寸稳定。
熔融石英纯净度高,所配涂料稳定性好;型壳高温抗蠕变能力提高。
熔融石英温度较低时的导热性较差,热容量小,仅为锆砂的一半,大多数金属液对它的润湿性较差,使得金属凝固层与型壳内表面间易产生间隙,热导率进一步减小,有利于壁薄铸件充型。
在高温下熔融石英的透明度高,能通过辐射传热,使其导热能力超过硅酸铝类壳。
而使铸件冷却较快,更易获得健全铸件。
铸件冷却时方石英又从高温型转变为低温型,同时体积产生骤变,使型壳出现无数裂纹,强度剧降,有利于脱壳进行。
熔融石英为酸性,能采用碱煮、碱爆等化学清砂方法去除型壳。
熔模铸造用熔融石英,其中SiO2所占的质量分数应为99.5%,配涂料用的粉料最好是270目或320目细粉占50%(质量分数),200目和120目粉各占25%(质量分数)。
①为0℃~1200℃间的膨胀系数平均值。
②400℃的热导率。
③1200℃热导率。
熔融石英及制品有三大特点:在所有耐火材料中,线膨胀系数最小(在1000℃的热胀率0.05);热导率最低,在1000℃热导率0.836W/(m·K)(0.02cal/cm·s·℃);抗热震性最好(在1200℃~水冷的抗震性),10次都不产生裂纹。
熔融石英的性能特点和使用解读

熔融石英的性能特点和使用一、熔融石英的性能特点和使用熔融石英材料在精铸型壳的使用上国外发达国家如美国的使用量和日本的使用量不断地逐年增加,特别是在硅溶胶型壳的面层方面有了很有经验的效果,在同锆英材料的使用和价格比上有了较大突破,是目前较为理想的工程应用材料。
熔融石英是用天然高纯度二氧化硅经电炉在高于1760℃以上温度熔融,随后快速冷却而制得的。
此过程将晶型SiO2转变为非晶型的玻璃熔体。
熔融石英熔化温度约1713℃,导热系数低,热膨胀系数几乎是所有耐火材料中最小的,因而它具有极高的热震稳定性。
所以,在焙烧和浇注过程中熔融石英型壳很少因温度剧变而破裂,是理想的熔模铸造制型的耐火材料,可作为面层或背层涂料用的耐火材料,以及撒砂材料。
熔融石英会部分或全面提高型壳性能。
熔融石英热膨胀系数小,有利于防止型壳在脱蜡和焙烧过程中开裂、变形,利于确保铸件尺寸稳定。
熔融石英纯净度高,所配涂料稳定性好;型壳高温抗蠕变能力提高。
熔融石英温度较低时的导热性较差,热容量小,仅为锆砂的一半,大多数金属液对它的润湿性较差,使得金属凝固层与型壳内表面间易产生间隙,热导率进一步减小,有利于壁薄铸件充型。
在高温下熔融石英的透明度高,能通过辐射传热,使其导热能力超过硅酸铝类壳。
而使铸件冷却较快,更易获得健全铸件。
铸件冷却时方石英又从高温型转变为低温型,同时体积产生骤变,使型壳出现无数裂纹,强度剧降,有利于脱壳进行。
熔融石英为酸性,能采用碱煮、碱爆等化学清砂方法去除型壳。
熔模铸造用熔融石英,其中SiO 2所占的质量分数应为99.5%,配涂料用的粉料最好是270目或320目细粉占50%(质量分数),200目和120目粉各占25%(质量分数)。
①为0℃~1200℃间的膨胀系数平均值。
耐火材料 化学组成 化学性质熔点/℃莫氏硬度 密度/(g/cm 3)膨胀系数①/×10-71/℃ 热导率/[W/(m 2.k)] 浸出性比较 颜色熔融石英 SiO 2 酸性 1713 7 2.251.951②在热浓碱和氢酸条件下有良好的可溶性 白色电熔刚玉 Al 2O 3 两性 2030 9 3.99~4.0 86 12.560②在热碱条件下反应很差 白色 莫来石 3Al 2O 3·2SiO 2 两性2030 6~72.7~2.9541.214② 在热碱条件下有轻微反应 灰色到棕黄色 高岭石 熟料 弱酸性 1700~1790 ~5 2.4~2.6 50- 在热碱条件下有轻微反应 灰色到棕黄色 锆砂 ZrSiO 4 弱酸性 <1948 7~8 4.5~4.9 46 2.094③在热碱条件下有中等反应 白色到棕黄色 氧化锆ZriO 2碱性26007~85.760-②400℃的热导率。
熔融石英的性能特点和使用
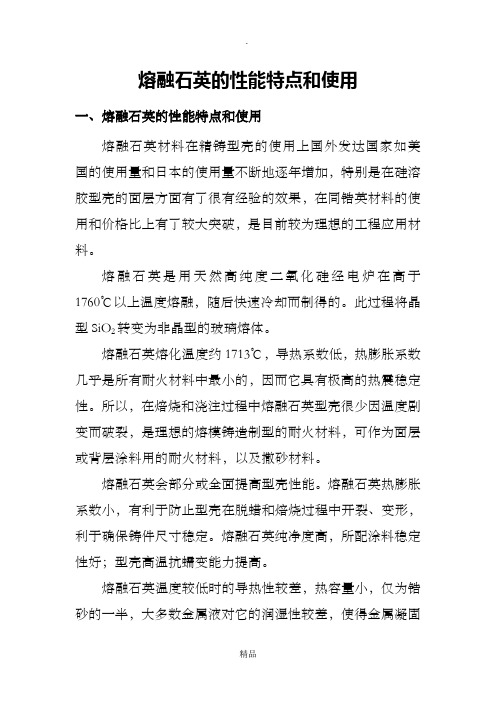
熔融石英的性能特点和使用一、熔融石英的性能特点和使用熔融石英材料在精铸型壳的使用上国外发达国家如美国的使用量和日本的使用量不断地逐年增加,特别是在硅溶胶型壳的面层方面有了很有经验的效果,在同锆英材料的使用和价格比上有了较大突破,是目前较为理想的工程应用材料。
熔融石英是用天然高纯度二氧化硅经电炉在高于1760℃以上温度熔融,随后快速冷却而制得的。
此过程将晶型SiO2转变为非晶型的玻璃熔体。
熔融石英熔化温度约1713℃,导热系数低,热膨胀系数几乎是所有耐火材料中最小的,因而它具有极高的热震稳定性。
所以,在焙烧和浇注过程中熔融石英型壳很少因温度剧变而破裂,是理想的熔模铸造制型的耐火材料,可作为面层或背层涂料用的耐火材料,以及撒砂材料。
熔融石英会部分或全面提高型壳性能。
熔融石英热膨胀系数小,有利于防止型壳在脱蜡和焙烧过程中开裂、变形,利于确保铸件尺寸稳定。
熔融石英纯净度高,所配涂料稳定性好;型壳高温抗蠕变能力提高。
熔融石英温度较低时的导热性较差,热容量小,仅为锆砂的一半,大多数金属液对它的润湿性较差,使得金属凝固层与型壳内表面间易产生间隙,热导率进一步减小,有利于壁薄铸件充型。
在高温下熔融石英的透明度高,能通过辐射传热,使其导热能力超过硅酸铝类壳。
而使铸件冷却较快,更易获得健全铸件。
铸件冷却时方石英又从高温型转变为低温型,同时体积产生骤变,使型壳出现无数裂纹,强度剧降,有利于脱壳进行。
熔融石英为酸性,能采用碱煮、碱爆等化学清砂方法去除型壳。
熔模铸造用熔融石英,其中SiO2所占的质量分数应为99.5%,配涂料用的粉料最好是270目或320目细粉占50%(质量分数),200目和120目粉各占25%(质量分数)。
①为0℃~1200℃间的膨胀系数平均值。
②400℃的热导率。
③1200℃热导率。
熔融石英及制品有三大特点:在所有耐火材料中,线膨胀系数最小(在1000℃的热胀率0.05);热导率最低,在1000℃热导率0.836W/(m·K)(0.02cal/cm·s·℃);抗热震性最好(在1200℃~水冷的抗震性),10次都不产生裂纹。
05 熔融石英

制壳耐火材料新秀——熔融石英—国外精铸技术进展述评(5)—原载《特种铸造及有色合金》,2005(5):294~298熔融石英在精铸中应用虽然已有相当长的历史,但以往主要用作陶瓷型芯,用作型壳则主要用于面层,背层很少使用。
这种状况近10 年来在美、欧各国有很大改变。
2001年美国著名耐火材料生产厂商Minco 公司,公布了对美国熔模铸造行业制壳耐火材料使用现况的调查统计数据,各种耐火材料消耗量所占比例的大致如下[1]:铝-硅系耐火材料55%、熔融石英30%、刚玉9%、锆石6%可见在美国精铸业中,熔融石英异军突起,在精铸制壳耐火材料的使用量中,已仅次于铝-硅系材料,远远超过锆石等其他耐火材料,迅速成为制壳耐火材料的一枝新秀。
一.熔融石英与铝-硅系材料的比较2000年美国Minco Inc.在美国第48 届精铸年会和INCAST 2001(3)发表的论文[1][2],对熔融石英和铝-硅系耐火材料进行了全面的分析对比。
主要结果如下:1)型壳重量熔融石英密度2.2g/cm3,铝-硅系材料约2.7g/cm3,故同样厚度型壳,前者重量明显轻于后者,有利于减轻工人劳动强度和机械手操作[1][2]。
2)热膨胀率图5-1 和图5-2 所示分别为脱蜡和焙烧过程中,这二种材料热膨胀率的比较[1][2]。
热膨胀系数小是熔融石英的一个很大的优点,有利于减小加热时,型壳内外因温度差造成的热应力,因而有利于防止脱蜡和焙烧过程中型壳开裂和变形。
同时,对提高铸件尺寸精度甚为有利。
所以,尺寸精度要求高的产品,就更适合采用熔融石英。
图5-1 脱蜡过程中二种材料热膨胀率的比较图5-2 焙烧过程中二种材料热膨胀率的比较3)力学性能和透气性表5-1所列为二种材料制得型壳的力学性能和透气性比较,结果显示,湿强度和断裂韧度,熔融石英型壳稍低于铝-硅系型壳,但透气性却远高于铝-硅系型壳[1][2]。
4)高温抗蠕变能力当采用熔融石英撒砂料代替硅酸铝时型壳高温抗蠕变能力提高(图5-3)[1][2] 。
熔融石英的性能特点和使用
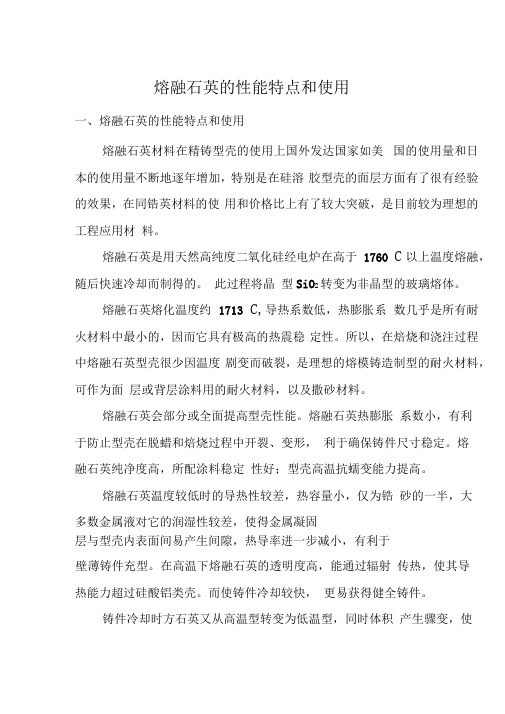
熔融石英的性能特点和使用一、熔融石英的性能特点和使用熔融石英材料在精铸型壳的使用上国外发达国家如美国的使用量和日本的使用量不断地逐年增加,特别是在硅溶胶型壳的面层方面有了很有经验的效果,在同锆英材料的使用和价格比上有了较大突破,是目前较为理想的工程应用材料。
熔融石英是用天然高纯度二氧化硅经电炉在高于1760 C以上温度熔融,随后快速冷却而制得的。
此过程将晶型SiO2转变为非晶型的玻璃熔体。
熔融石英熔化温度约1713 C,导热系数低,热膨胀系数几乎是所有耐火材料中最小的,因而它具有极高的热震稳定性。
所以,在焙烧和浇注过程中熔融石英型壳很少因温度剧变而破裂,是理想的熔模铸造制型的耐火材料,可作为面层或背层涂料用的耐火材料,以及撒砂材料。
熔融石英会部分或全面提高型壳性能。
熔融石英热膨胀系数小,有利于防止型壳在脱蜡和焙烧过程中开裂、变形,利于确保铸件尺寸稳定。
熔融石英纯净度高,所配涂料稳定性好;型壳高温抗蠕变能力提高。
熔融石英温度较低时的导热性较差,热容量小,仅为锆砂的一半,大多数金属液对它的润湿性较差,使得金属凝固层与型壳内表面间易产生间隙,热导率进一步减小,有利于壁薄铸件充型。
在高温下熔融石英的透明度高,能通过辐射传热,使其导热能力超过硅酸铝类壳。
而使铸件冷却较快,更易获得健全铸件。
铸件冷却时方石英又从高温型转变为低温型,同时体积产生骤变,使型壳出现无数裂纹,强度剧降,有利于脱壳进行。
熔融石英为酸性,能采用碱煮、碱爆等化学清砂方法去除型壳。
熔模铸造用熔融石英,其中SiO2所占的质量分数应为99.5%,配涂料用的粉料最好是270目或320目细粉占50%(质量分数),200目和120目粉各占25% (质量分数)。
①为0 C〜1200 C间的膨胀系数平均值。
②400 C的热导率。
③1200 C热导率。
熔融石英及制品有三大特点:在所有耐火材料中,线膨胀系数最小(在1000 C的热胀率0.05 );热导率最低,在1000 C热导率0.836W/ (m • K)(0.02cal/cm • s ・C);抗热震性最好(在1200 °C〜水冷的抗震性),10次都不产生裂纹。
石英坩埚中方石英的析晶与抑制简析

石英坩埚中方石英的析晶与抑制简析石英坩埚中方石英的析晶与抑制简析沈益顺10 前言熔融石英陶瓷具有高温荷重软化温度高、热膨胀系数小,热稳定性好、耐化学侵蚀性好等优良性能,广泛应用于太阳能、航天飞行器、半导体、电子通讯和光学器、器件等领域。
太阳能多晶硅铸锭用熔融石英坩埚就是其重要的应用领域之一,它是多晶硅铸锭生产中的必需品,用来装载、熔化硅料。
但熔融石英为热力学不稳定的高能态玻璃态物质,长时间在1200℃以上容易析晶产生方石英。
由于方石英的热膨胀系数不匹配和体积变化效应而在材料内部产生孔隙和应力,使得坩埚力学性能严重下降;再者,方石英本身的热学性能和电学性能差,因此,方石英的析出会使石英坩埚的综合性能下降,容易导致坩埚开裂损坏。
因此,在石英坩埚制备过程中必须保持石英的玻璃态,避免方石英析出。
1.石英坩埚中方石英析晶原理高纯石英坩埚的烧结机理主要为固相烧结,物料的传输是通过扩散(表面扩散和体扩散)进行的,即物质中原子或空位沿物质的表面、界面或体内进行。
烧结初期以表面扩散为主,随温度升高,体扩散饿活跃起来。
对非晶态石英颗粒而言,表面扩散的结果是在颗粒间形成“颈”部,不改变颗粒的非晶态,也不引起收缩;而体扩散则不同,它可以消除颗粒内部的结构缺陷和导致结构质点的有序化,即从非晶态转变晶体。
所以,在温度低于1200℃的石英陶瓷的烧结基本仍保持非晶态的结构组成,而在1200℃或略高一点的温度下方石英析出即将开始。
2.石英坩埚中方石英析晶影响因素分析2.1 颗粒表面形态的影响固相烧结的推动力是界面(粒子自由表面和相邻粒子接触面)自由能或化学势的差。
因此,不同形态的石英,由于表面状态和结构不同对方石英的析晶行为存在不同的影响。
温武广等人系统研究了石英块体、石英粉体和石英纤维的等温析晶行为及其动力学,结果表明:经相同热处理,石英块体、石英粉体和石英纤维在每个处理温度点的析晶都遵循以下规律:石英块体、石英粉体和石英纤维的析晶量依次增强、析晶能力依次变强。
熔融石英陶瓷的性能及其应用

% # ) 泥浆制备
一般采用 $ 种方式: 一步制浆和两
步制浆,一步制浆是将熔融石英料的细磨和配浆同时 进行,两步制浆是先将熔融石英原料磨成细粉然后再 配制泥浆。 影响泥浆性能的指标主要有: 泥浆的粒度组成, 泥 浆的密度, 流动性与 12 值等。 泥浆的粒度组成, 一般以 小于 &!3 的微粒在 !’4 - (’4 为宜,这是因为小于
要 * 介绍了石英陶瓷的性能特点、 制备过程及应用领域
关键词 * 石英陶瓷 + 性能 + 应用
熔融石英陶瓷是在 #,(! 年后才发展起来的一种 以石英玻璃为原料特种耐火材料,采用陶瓷的生产工 艺制造的,其成本要比透明石英玻璃制品低很多,甚 至低 #’ - #’’ 倍。它不但具备了石英玻璃的优良特 性, 如线胀系数小, 具有优良的热稳定性、 电性能、 核 性能以及耐化学侵蚀性。而且还具有一些石英玻璃制 品所缺乏的性质。如石英玻璃制品在使用时发生失 透,即损坏报废,而石英陶瓷制品即使发生析晶也仍 可使用。此外, 由于熔融石英陶瓷导热性差, 因此可应 用到宇宙飞船, 火箭, 导弹, 原子能工业, 电子工业, 以 及一般冶金,建材与化学工业,是一种很有前途的材 料
现 现 代 技 术 陶 瓷 现代 代技 技术 术陶 陶瓷 瓷 !""# 年第 $ 期 % 总第 &"# 期 ’
其它高温陶瓷,可用于绝缘材料,也是导弹和雷达天 线罩的良好材料。
熔融石英陶瓷的制备及其增强性的研究(可编辑)

熔融石英陶瓷的制备及其增强性的研究桂林理工大学硕士学位论文熔融石英陶瓷的制备及其增强性研究姓名:刘恒波申请学位级别:硕士专业:材料加工工程指导教师:蒋述兴20090401桂林理工大学硕士学位论文摘要熔融石英陶瓷是一种以熔融石英或石英玻璃边角料为原料经特殊生产工艺再经高温烧结而成的特种耐火陶瓷材料,又称为石英陶瓷、石英玻璃陶瓷、石英玻璃烧结制品。
熔融石英陶瓷不仅具备了石英玻璃的许多优良性质,如热膨胀系数小、热震稳定性好、电性能好、核性能好、耐化学侵蚀性好等特点,干燥及烧成收缩小,易于成型复杂形状及大件制品等。
目前熔融石英陶瓷材料广泛应用于太阳能电池用多晶硅铸锭冶炼坩埚、玻璃窑炉匝板砖、导弹天线罩,电子类产品等高科技行业。
但熔融石英陶瓷也存在着一些致命问题,如力学强度较低、结晶化、成型困难等问题。
因此本文重点解决此类问题。
由于熔融石英属脊性粉料,塑性极低,而采用先进的初凝成型技术,可以有效地解决熔融石英陶瓷成型困难问题。
论文在前人研究的基础上,制备的熔融石英浆料体系中加入有机单丙烯酰胺%、引发剂过硫酸铵.%、固相含量%,且浆料中调节在之间。
成型后的生坯密度达./,强度达。
于℃~℃烧结,保温时间.~。
研究结果表明:利用注凝成型技术能够制备高强度、高密度、高耐酸性、高抗热震性的熔融石英陶瓷材料。
此外还分别加入、、这三种不同添加剂,以研究对熔融石英陶瓷的增%、 %强作用,并初步探讨了增强机理。
结果表明:当加入量分别为%、时,其增强效果为最佳,借助于、和力学性能测试等手段,发现其增强机理应该是第二相杂质与基体反应形成液相补强和颗粒弥散两种机制。
本文研究了影响生坯、和熟坯性能的因素;通过比较其体积密度、抗弯强度、耐酸腐蚀性和抗热震性能,以及和分析,初步探讨了影响熔融石英陶瓷析晶的因素和析晶过程。
关键词:熔融石英陶瓷;注凝成型;析晶;增强剂;耐酸腐蚀;抗热震性桂林理工大学硕士学位论文.,, . ,,, ,,., ,. ,, ,,, ,.,. , .%. ,.聊 % , .%, ℃~℃./.., .,曲豇,曲 .曲,, , :..%、砒%、叭%,,. , ,, ,.:;删;;;;研究生学位论文独创性声明和版权使用授权书独创性声明本人声明:所呈交的论文是本人在导师指导下进行的研究工作及取得的研究成果。
《金属精密液态成形技术》复习题答案

《金属精密液态成形技术》复习题答案第1章绪论一、简答题1.常用金属精密液态成形方法有哪些?答:熔模精密铸造、石膏型精密铸造、陶瓷型精密铸造、消失模铸造、金属型铸造、压力铸造、低压铸造、差压铸造、真空铸造、调压铸造、挤压铸造、离心铸造、壳型铸造、连续铸造、半固态铸造、喷射成行技术、石墨型铸造、电渣熔铸、电磁铸造2.金属精密液态成形技术的特点是什么?对铸件生产有哪些影响?答:(1)特点:特殊的铸型制造工艺与材料;特殊的液态金属充填方式与铸件冷凝条件。
(2)对铸件生产的影响:由于铸型材料与铸型制作工艺的改变,对铸件表面粗糙度产生很大影响,不但尺寸精度很高,还可使铸件表面粗糙度降低,从而可实现近净成形。
在某些精密液态成形过程中,金属液是在外力(如离心力、电磁力、压力等)作用下完成充型和凝固的,因此提高了金属液的充型能力,有利于薄壁铸件的成形;液态金属在压力下凝固,有利于获得细晶组织,减少缩松缺陷,提高力学性能。
第2章熔模铸造成形一、名词解释1.硅溶胶:是由无定形二氧化硅的微小颗粒分散在水中而形成的稳定胶体溶液。
2.水玻璃模数:水玻璃中的二氧化硅与氧化钠摩尔数之比。
3.树脂模料:以树脂及改性树脂为主要组分的模料。
4.压型温度:熔模压制时压型的工作温度。
5.涂料的粉液比:涂料配置中粉料和液体的比例。
6.析晶:是当物体在处于非平衡态时,会析出另外的相,该相以晶体的形式被析出。
7.硅酸乙酯水解:硅酸乙酯通过熔剂(乙醇)和催化剂(盐酸)的作用与水发生反应的全过程。
8.皂化物:油脂等样品中能与氢氧化钠或氢氧化钾起皂化反应的物质。
二、填空题1.熔模铸造的模料强度通常以抗弯强度来衡量。
2.硅溶胶型壳的干燥过程实质上就是硅溶胶的胶凝过程。
3.一般说来说:硅溶胶中SiO2含量越高、密度越大,则型壳强度越大。
4.涂料中最基本的两个组成粘结剂和耐火粉料之间的比例,即为涂料的粉液比。
5.通常按模料熔点的高低将其分为高温、中温和低温模料。
温度对陶瓷材料性能的影响
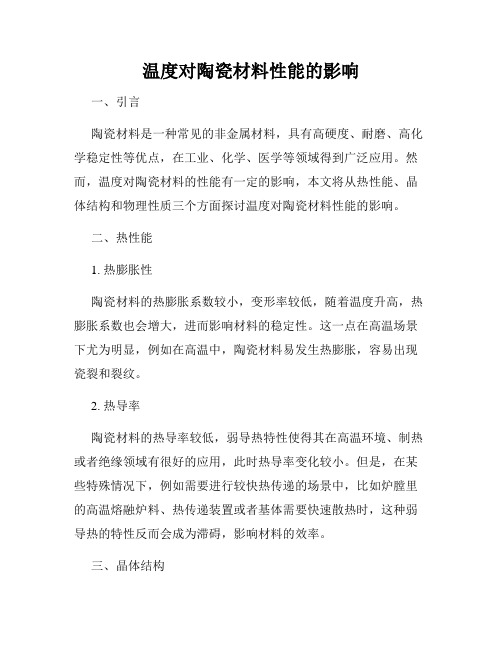
温度对陶瓷材料性能的影响一、引言陶瓷材料是一种常见的非金属材料,具有高硬度、耐磨、高化学稳定性等优点,在工业、化学、医学等领域得到广泛应用。
然而,温度对陶瓷材料的性能有一定的影响,本文将从热性能、晶体结构和物理性质三个方面探讨温度对陶瓷材料性能的影响。
二、热性能1. 热膨胀性陶瓷材料的热膨胀系数较小,变形率较低,随着温度升高,热膨胀系数也会增大,进而影响材料的稳定性。
这一点在高温场景下尤为明显,例如在高温中,陶瓷材料易发生热膨胀,容易出现瓷裂和裂纹。
2. 热导率陶瓷材料的热导率较低,弱导热特性使得其在高温环境、制热或者绝缘领域有很好的应用,此时热导率变化较小。
但是,在某些特殊情况下,例如需要进行较快热传递的场景中,比如炉膛里的高温熔融炉料、热传递装置或者基体需要快速散热时,这种弱导热的特性反而会成为滞碍,影响材料的效率。
三、晶体结构1. 晶体缺陷陶瓷材料由于其独特的晶体结构具有极好的高温稳定性,在高温中仍可以保持其结构的完整性,因此被广泛应用于高温环境中。
但是,随着温度升高,材料结构中存在的晶体缺陷会逐渐增多,导致其性能降低甚至破坏。
2. 晶粒长大另一方面,随着温度升高,晶格中的原子振动幅度相对增加,也使得晶粒长大。
晶粒的长大会影响材料的性能,例如硬度下降、韧性降低等,热加工陶瓷材料时需要考虑到晶粒长大的影响。
四、物理性质1. 电学性能陶瓷材料的电性能随着温度升高会降低,这种电性能的变化与材料表面导体自由电子数量的变化有关,同时也会影响材料的介电常数、电耗等物理性质,判断材料性能时应注意这种变化。
2. 磁学性能具有磁学性能的陶瓷材料在磁场中具有一定的磁化率,然而随着温度升高,其磁性会下降,这主要是由于材料中电子激发方式的变化导致磁矩的变化,磁学性能随温度变化的特性可以作为判断材料特性的重要指标之一。
五、总结总的来说,温度对陶瓷材料的性能会产生一定的影响,需要在生产或者使用过程中谨慎考虑,并根据实际情况定制合理的加工和使用环境,保证其材料的性能表现。
熔融石英的性能特点和使用
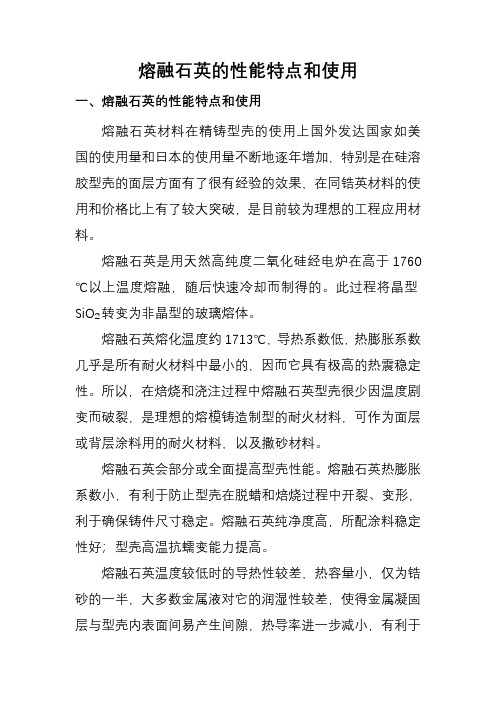
熔融石英的性能特点和使用一、熔融石英的性能特点和使用熔融石英材料在精铸型壳的使用上国外发达国家如美国的使用量和日本的使用量不断地逐年增加,特别是在硅溶胶型壳的面层方面有了很有经验的效果,在同锆英材料的使用和价格比上有了较大突破,是目前较为理想的工程应用材料。
熔融石英是用天然高纯度二氧化硅经电炉在高于1760℃以上温度熔融,随后快速冷却而制得的。
此过程将晶型SiO2转变为非晶型的玻璃熔体。
熔融石英熔化温度约1713℃,导热系数低,热膨胀系数几乎是所有耐火材料中最小的,因而它具有极高的热震稳定性。
所以,在焙烧和浇注过程中熔融石英型壳很少因温度剧变而破裂,是理想的熔模铸造制型的耐火材料,可作为面层或背层涂料用的耐火材料,以及撒砂材料。
熔融石英会部分或全面提高型壳性能。
熔融石英热膨胀系数小,有利于防止型壳在脱蜡和焙烧过程中开裂、变形,利于确保铸件尺寸稳定。
熔融石英纯净度高,所配涂料稳定性好;型壳高温抗蠕变能力提高。
熔融石英温度较低时的导热性较差,热容量小,仅为锆砂的一半,大多数金属液对它的润湿性较差,使得金属凝固层与型壳内表面间易产生间隙,热导率进一步减小,有利于②400℃的热导率。
③1200℃热导率。
熔融石英及制品有三大特点:在所有耐火材料中,线膨胀系数最小(在1000℃的热胀率0.05);热导率最低,在1000℃热导率0.836W/(m·K)(0.02cal/cm·s·℃);抗热震性最好(在1200℃~水冷的抗震性),10次都不产生裂纹。
二、熔融石英涂料配制使用操作工艺(一)本操作工艺适用于硅溶胶,制壳的表面层或过渡层。
(二)本工艺使用的硅溶胶同锆英粉涂料即SiO230%。
(三)本工艺操作中的润湿剂,消泡剂同锆英粉涂料。
(四)本操作中使用的流杯粘度计为詹氏(Zahn)5#杯,出口孔径为Φ5.28mm。
(五)涂料配制:1、熔融石英粉的配制,320目(网号:0.044)275目(网号:0.052)200目(网号:0.076)120目(网号:0.125)熔融石英粉中的SiO2的质量分数为99.5%以上。
熔融石英球形粉对陶瓷型芯高温收缩的影响
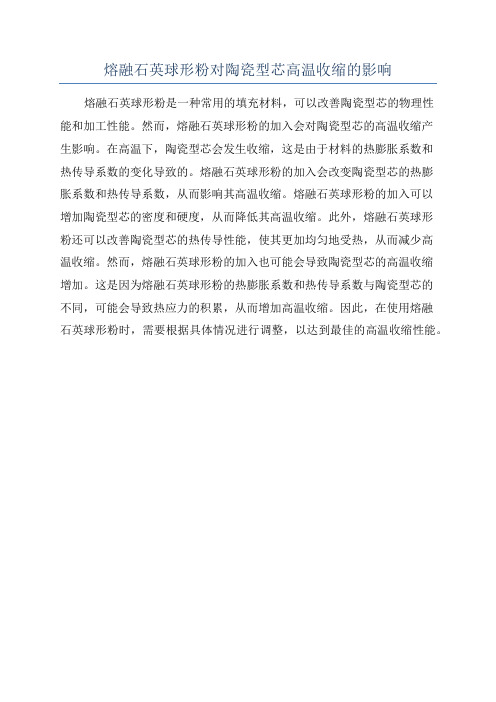
熔融石英球形粉对陶瓷型芯高温收缩的影响熔融石英球形粉是一种常用的填充材料,可以改善陶瓷型芯的物理性
能和加工性能。
然而,熔融石英球形粉的加入会对陶瓷型芯的高温收缩产
生影响。
在高温下,陶瓷型芯会发生收缩,这是由于材料的热膨胀系数和
热传导系数的变化导致的。
熔融石英球形粉的加入会改变陶瓷型芯的热膨
胀系数和热传导系数,从而影响其高温收缩。
熔融石英球形粉的加入可以
增加陶瓷型芯的密度和硬度,从而降低其高温收缩。
此外,熔融石英球形
粉还可以改善陶瓷型芯的热传导性能,使其更加均匀地受热,从而减少高
温收缩。
然而,熔融石英球形粉的加入也可能会导致陶瓷型芯的高温收缩
增加。
这是因为熔融石英球形粉的热膨胀系数和热传导系数与陶瓷型芯的
不同,可能会导致热应力的积累,从而增加高温收缩。
因此,在使用熔融
石英球形粉时,需要根据具体情况进行调整,以达到最佳的高温收缩性能。
熔融石英膨胀系数
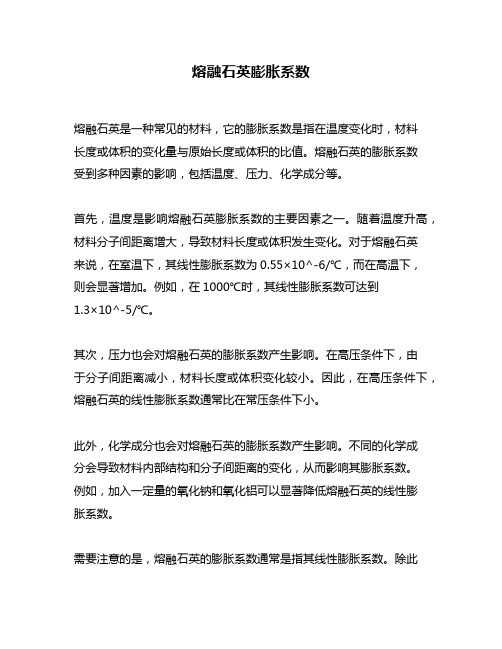
熔融石英膨胀系数
熔融石英是一种常见的材料,它的膨胀系数是指在温度变化时,材料
长度或体积的变化量与原始长度或体积的比值。
熔融石英的膨胀系数
受到多种因素的影响,包括温度、压力、化学成分等。
首先,温度是影响熔融石英膨胀系数的主要因素之一。
随着温度升高,材料分子间距离增大,导致材料长度或体积发生变化。
对于熔融石英
来说,在室温下,其线性膨胀系数为0.55×10^-6/℃,而在高温下,
则会显著增加。
例如,在1000℃时,其线性膨胀系数可达到
1.3×10^-5/℃。
其次,压力也会对熔融石英的膨胀系数产生影响。
在高压条件下,由
于分子间距离减小,材料长度或体积变化较小。
因此,在高压条件下,熔融石英的线性膨胀系数通常比在常压条件下小。
此外,化学成分也会对熔融石英的膨胀系数产生影响。
不同的化学成
分会导致材料内部结构和分子间距离的变化,从而影响其膨胀系数。
例如,加入一定量的氧化钠和氧化铝可以显著降低熔融石英的线性膨
胀系数。
需要注意的是,熔融石英的膨胀系数通常是指其线性膨胀系数。
除此
之外,还有体积膨胀系数、表观体积膨胀系数等不同类型的膨胀系数。
其中,体积膨胀系数是指材料体积变化与原始体积之比,表观体积膨
胀系数则是指材料密度变化与原始密度之比。
总之,熔融石英的膨胀系数受到多种因素的影响,包括温度、压力、
化学成分等。
在实际应用中,需要根据具体情况选择合适的材料,并
考虑其在不同条件下的性能表现。
熔融石英热膨胀系数

熔融石英热膨胀系数
熔融石英的热膨胀系数很小,几乎是所有耐火材料中热膨胀系数最小的。
根据相关资料,熔融石英的热膨胀系数约为(0.5±0.5)×10^-6/K。
熔融石英的热膨胀系数之所以如此低,是因为其内部结构非常稳定,晶体结构不易受热膨胀的影响。
此外,熔融石英的成分单一,不含其他杂质,也减少了外部因素对热膨胀系数的影响。
在实际应用中,熔融石英的热膨胀系数与许多材料都不匹配,但它在一些特定领域中具有重要作用。
例如,在电子封装材料中,熔融石英由于其热膨胀系数与某些金属不匹配,可以在高温下防止开裂。
此外,在光学领域中,熔融石英的热膨胀系数也非常低,可以用于制造高精度的光学元
件。
总之,熔融石英的热膨胀系数虽然很小,但在一些特定领域中具有非常重要的应用价值。
- 1、下载文档前请自行甄别文档内容的完整性,平台不提供额外的编辑、内容补充、找答案等附加服务。
- 2、"仅部分预览"的文档,不可在线预览部分如存在完整性等问题,可反馈申请退款(可完整预览的文档不适用该条件!)。
- 3、如文档侵犯您的权益,请联系客服反馈,我们会尽快为您处理(人工客服工作时间:9:00-18:30)。
0摇 引言
随着高性能航空发动机的不断发展,航空发动机涡轮叶 片逐渐由简单实心结构发展到复杂气冷的空心结构。 陶瓷 型芯是形成涡轮叶片空心结构的转接件,型芯尺寸及变形量 直接关系到涡轮叶片空心结构的尺寸精度,而高温收缩是影 响陶瓷型芯尺寸准确性的重要因素,因此,如何控制陶瓷型 芯的高温收缩以获得符合尺寸与几何公差要求的空心涡轮 叶片一直深受关注。
Effect of Fused Silica Spherical cles on Shrinkage Properties of Ceramic Cores
WANG Lili , YAO Jiansheng, XU Liang, YANG Xiaowei, GU Guohong, LI Xin, NIU Shuxin
2019,Vol郾 33,No郾 7摇 www. mater鄄rep. com
熔融石英球形粉对陶瓷型芯高温收缩的影响
王丽丽 , 姚建省,许摇 亮,杨小薇,顾国红, 李摇 鑫, 牛书鑫
北京航空材料研究院先进高温结构材料重点实验室,北京 100095
分别以熔融石英球形粉、角形粉为原料,采用注射成型工艺制备陶瓷型芯,对比型芯的烧结收缩和二次烧结收缩,并结合 SEM 和 XRD 分析,探 讨了添加熔融石英球形粉对陶瓷型芯高温收缩的影响。 研究结果表明:当混合粉粒度级配相近时,由 100% 熔融石英球形粉制备的型芯在 1 200 益的烧 结收缩率远小于由角形粉制备的型芯;在 SiO2 鄄ZrSiO4 和 SiO2 鄄Al2 O3 型芯原料配比不变时,添加熔融石英球形粉可起到抑制原有型芯料烧结收缩 的作用;随着球形粉添加量的增大,型芯的烧结收缩率有不同程度的降低。 熔融石英球形粉对型芯烧结收缩的抑制作用与球形粉中残留的石英晶相 含量高及其高温方石英化有关。 添加熔融石英球形粉对型芯 1 500 益二次烧结收缩的影响不大。 关键词摇 摇 球形粉摇 氧化硅基陶瓷型芯摇 烧结收缩摇 二次烧结收缩 中图分类号:TQ174郾 7;V254郾 2摇 摇 文献标识码:A
硅基陶瓷型芯易脱芯、抗热震性好,是目前制备空心涡 轮叶片用铸型的首选材料[1鄄3] 。 根据矿化剂类型的不同,硅 基陶瓷型芯可 分 为 SiO2 型 芯、 SiO2 鄄ZrSiO4 型 芯、 SiO2 鄄Al2 O3 型芯、SiO2 鄄ZrO2 型芯和 SiO2 鄄莫来石型芯等[4] 。 型芯材料物 性( 包括矿化剂种类、 粉 体 配 比、 粉 体 形 貌、 粒 度 级 配 等) 、 工 艺条件( 包括注射速 度、保 压 压 力、保 压 时 间、烧 结 工 艺 等) 、 型芯结构和模具设计等都会影响陶瓷型芯的高温收缩行为。 在型芯原料配比不宜变动的情况下,一般通过调整烧结工艺 来调节型芯的烧结收缩,但该方法的调节效果有限。 烧结程 度降低,型芯的烧结收缩率减小、型面尺寸变化降低,可暂时 满足蜡模对型芯尺寸和形状公差的要求,但这会引起型芯二 次烧结收缩率的增大,严重时将导致型芯在合金浇注过程中 发生偏芯或断芯。 韩绍娟等[5] 在型芯中引入质量 分 数 为 0郾 5% ~ 3% 的石英玻璃纤维或氧化锆纤维,获得了烧结收缩 率低于 0郾 4% 、室温抗弯强度大于 10 MPa 的型芯材料,但无 机纤维的引入会导致型芯浆料的流动性严重降低。 Manns鄄
Science and Technology on Advanced High Temperature Structural Materials Laboratory, Beijing Institute of Aeronautical Materials, Beijing 100095
Ceramic cores with fused silica spherical particles were prepared by injection molding. Compared with the comminuted particles, the effects of fused silica spherical particles on sintering shrinkage at 1 200 益 and 1 500 益 were investigated by SEM and XRD. The results showed that the ceramic cores with 100% fused silica spherical particles had a smaller sintering shrinkage at 1 200 益 than cores with 100% fused silica com鄄 minuted particles when the particle size distributions of fused silica were similar. When the proportion of raw materials ( not include spherical parti鄄 cles) was constant, adding spherical particles could inhibit the sintering at 1 200 益 of SiO2 鄄ZrSiO4 and SiO2 鄄Al2 O3 ceramic cores, and the de鄄 creases of sintering shrinkage varied with the increasing amount of spherical particles. The native reaction of spherical particles on ceramic sinte鄄 ring is likely to relate to the residual quartz phase in spherical particles and the transformation to cristoballite phase. The additive of spherical parti鄄 cles had no significant influence with the further shrinkage at 1 500 益 of silica based ceramic cores.