Seven_Waste_七大浪废
7大浪费是什么

7大浪费是什么
七种浪费被称为:等待浪费、处理浪费、次品浪费、行动浪费、加工浪费、库存浪费、过度(早期)制造浪费。
1.等待浪费:等待就是什么都不做,等待下一个动作。
这种浪费是毋庸置疑的。
2.搬运浪费:包括放置、堆放、移动、分类和其他行为的废物。
3.不良品浪费:在产品制造过程中,任何不良品都会造成材料、机器、人工等的浪费。
4.动作浪费:达到同一个目的,会有不同的动作,很多动作都有。
5.加工浪费:有些加工工序可以省略、替换、重组或合并。
6.库存浪费:难怪精益生产称库存为万恶之源,减少库存,争取零库存。
7.制造过度(早期)浪费:真正消除行动中的“浪费”,降低成本,提高效率,增加效益。
精益生产之七大浪费

精益生产之七大浪费精益生产是一种以最小化浪费为目标,通过优化流程和提高效率来提高产品质量和客户满意度的管理方法。
在精益生产中,有七大浪费被认为是造成资源浪费和低效率的主要原因,它们是:过产、等待、运输、不合格、运动、库存和过程错误。
1. 过产(Overproduction):过产是指在没有实际需求的情况下进行生产活动,导致产品过度积压和资源浪费。
这不仅会给企业带来高成本,还会增加库存量和缩短产品寿命。
2. 等待(Waiting):等待是指生产过程中出现的不必要的停顿和延迟。
这可能是由于设备故障、物料不足、工人缺席等原因导致的。
等待会降低生产效率,增加生产周期,延迟产品交付。
3. 运输(Transportation):运输是指不必要的材料和产品的长距离运输。
这使得运输成为了一个独立的过程,需要额外的时间和资源。
这些额外的步骤可能会导致物料的损坏、遗失和延迟,进一步增加了生产成本。
4. 不合格(Defects):不合格是指生产中出现的错误、缺陷和质量问题。
不合格的产品需要进行修正、重新制造或报废,这增加了不必要的时间和资源。
这不仅会导致生产延误,还会降低产品质量和客户满意度。
5. 运动(Motion):运动是指工人在生产过程中进行不必要的移动和动作。
这可能是由于生产线布局不合理、工具和设备摆放不当等原因导致的。
这增加了工人的体力消耗,降低了生产效率,也增加了人为错误的可能性。
6. 库存(Inventory):库存是指未经加工的原材料和半成品的储存量。
过多的库存可能会导致资金占用、过期损失、储存空间浪费等问题。
此外,库存过多也会隐藏潜在的问题,如质量问题和需求变化的风险。
7. 过程错误(Processing):过程错误是指生产过程中出现的不必要的重复、增补和调整。
这可能是由于不合理的工艺流程、工具和设备的不良设计等原因导致的。
这会增加生产成本和时间,降低生产效率和产品质量。
有效管理和消除以上七大浪费是精益生产的关键。
七大浪费Seven Waste

定义:
过程(操作/步骤)与顾客的价值或满意度无关, 是不必要的。
2003,10,23
CHANGAN-FORD
CHEN JIACHUN
16
七大浪费-多余的过程(续)
Seven Forms Of Waste – Over Process
观察的征兆:
产品需求已经发生了变化但过程仍停留在原来的状态 上 对顾客的需求不明确、不清楚 多余的步骤或过程 操作者缺乏训练或缺乏指导书 操作者在顾客不关心的方面花费过多的工作
Seven Forms Of Waste – Waiting
消除浪费的方法与思路:
进行工作平衡(WBB:work balance board) 改进FTPM 使用WES改进质量 推行快速转换QCO 运用拉动系统 按OIS的标准化要求进行操作 开展多技能培训
2003,10,23
CHANGAN-FORD
CHEN JIACHUN
12
七大浪费-库存
Seven Forms Of Waste – Inventory
定义:在工序间超出一个流原则的额外零件
库存的是金钱
库存会贬值
2003,10,23
CHANGAN-FORD
CHEN JIACHUN
13
七大浪费-库存(续)
观察的征兆:
生产计划缺乏均衡 未使用拉动系统 正常运转时间不足 质量低劣 生产顺序缺乏沟通 换型时间过长
Seven Forms Of Waste – Inventory
并不总是能真正消除掉库存或达 到一个流,关键是要管理库存并知道 为什么会有库存。 应尽可能的消除库存
2003,10,23CHANGAN-FORDCHEN JIACHUN
15
精益生产管理中的7大浪费

生产管理中的“七大浪费”定义与说明生产管理中的“七大浪费”,懂精益生产的人都知道,就是不良品,超量生产,库存,搬运,多余的工序,不必要的调动,等待。
一、库存浪费◆精益生产认为:“库存是万恶之源”,所有改善行动皆会与直接或间接地和消除库存有关①产生不必要的搬运、堆积、放置、防护处理、找寻等浪费②使先进先出的作业困难③损失利息及管理费用④物品的价值会减低,变成呆滞品⑤占用厂房空间、造成多余工场、仓库建设等⑥设备能力及人员需求的误判◆因库存造成无形损失,绝不亚于上述有形损失,精益生产者认为库存会隐藏问题,而“问题”在精益生产者被认为是宝藏,问题如果能不断地被发现解决,则利益便会不断地产生1、没有管理的紧张感,阻碍改进2、库存量一多,因机械故障、不良产品所带来的不利后果不能马上显现出来,因而也不会产生对策3、由于有了充足的库存,出现问题时可以用库存先顶上,问题就可以慢慢解决甚至不用解决,最起码是被掩盖住了,不急迫了,不会被上级追究了,于是乎本部门的工作成绩就出来了二、过渡生产(制造过多或过早浪费)◆TPS强调的是“适时生产”◆多做能提高效率,提早做好能减少产能损失(不做白不做,机器还不是一样停着?)1、提早用掉了材料费、人工费而已,并不能得到什么好处2、把“等待浪费”隐藏,使管理人员漠视等待的发生和存在3、积压在制品,使生产周期L/T变长(无形的),而且会使现场工作空间变大,不知不觉吞蚀我们的利润4、产生搬运、堆积浪费,先进先出变得困难三、品质缺陷(不良品浪费)◆任何的不良品产生,皆会造成材料、机器、人工等的浪费◆及早发现不良品,容易确定不良来源,进而减少不良品的产生◆关键是第一次要把事情做对,“零缺陷”四、运输(搬运浪费)◆大部分人皆认同搬运是一种无效的动作,也有人认为搬运是必须的◆用“输送带”的方式来克服,行吗?1、取放浪费;2、等待浪费;3、在制品过多浪费;4、空间浪费◆搬运浪费又包含放置、堆积、移动、整理等动作的浪费五、处理(加工浪费)◆定义:指的是与工程进度及加工精度无关的不必要的加工◆有一些加工程序是可以省略、替代、重组或合并◆很多时候会习惯并认为现在的做法较好六、动作浪费12种动作浪费:◆两手空闲◆单手空闲◆不连贯停顿◆幅度太大◆左右手交换◆步行多◆转身角度大◆移动中变换状态◆不明技巧◆伸背动作◆弯腰动作◆重复不必要动作七、等待浪费◆生产线的品种切换◆工作量少时,便无所事事◆时常缺料,设备闲置◆上工序延误,下游无事可做◆设备发生故障◆生产线工序不平衡◆有劳逸不均的现象◆制造通知或设计图未送达。
7大浪费(漫画图示版)

一、制造过多(早)的浪费
必要的东西在必要的时候做出必要的数量,此外都是浪费。
七 大 浪 费
最坏的浪费
二、库存的浪费
七 大 浪 费
最大的浪费
三、搬运的浪费
物流搬运路径设置不合理-----太远,取、放、运、还 有点数后重新装货等重复
七 大 浪 费
最长的浪费
四、等待的浪费
材料供应不足或设备故障,员工空手等待,或者设备空转 的等待-----等待的这些时间都付费了的时间(人工费、设备 折旧费,但是没有产品产出也就是没有产生效益)
七 大 浪 费
最深的浪费
七、动作的浪费(十二种)
两手空闲的浪费 单手空闲的浪费 作业动作停止的浪费 作业动作太大的浪费 拿的动作交替的浪费 步行的浪费 转身角度太大的浪费 动作之间没有配合好的浪费 不了解作业技巧的浪费 伸背动作的浪费 弯腰动作的浪费 重复动作的浪费
七 大 浪 费
最多的浪费
七 大 浪 费
最迟的浪费
五不良品的浪费
是指在工厂内发生不良品,本身生产的不良品也是需要 原材料的,耗费原材料成本,直接报废总觉得可惜,如果 返修,需要消耗时间和人力、物力上的浪费。
七 大 浪 费
最差的浪费
六、加工的浪费
是指加工过程中存在的一些多余的加工,没必要的加工工 序多,如机械行程过长、检查标准不明确或过高等
精益生产之七大浪费
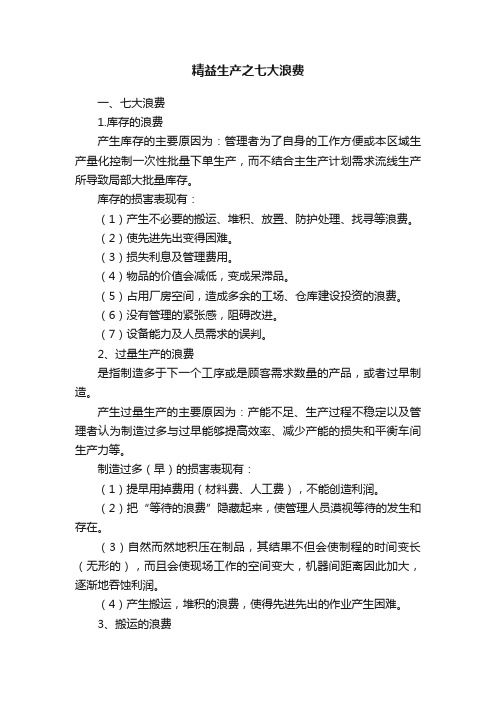
精益生产之七大浪费一、七大浪费1.库存的浪费产生库存的主要原因为:管理者为了自身的工作方便或本区域生产量化控制一次性批量下单生产,而不结合主生产计划需求流线生产所导致局部大批量库存。
库存的损害表现有:(1)产生不必要的搬运、堆积、放置、防护处理、找寻等浪费。
(2)使先进先出变得困难。
(3)损失利息及管理费用。
(4)物品的价值会减低,变成呆滞品。
(5)占用厂房空间,造成多余的工场、仓库建设投资的浪费。
(6)没有管理的紧张感,阻碍改进。
(7)设备能力及人员需求的误判。
2、过量生产的浪费是指制造多于下一个工序或是顾客需求数量的产品,或者过早制造。
产生过量生产的主要原因为:产能不足、生产过程不稳定以及管理者认为制造过多与过早能够提高效率、减少产能的损失和平衡车间生产力等。
制造过多(早)的损害表现有:(1)提早用掉费用(材料费、人工费),不能创造利润。
(2)把“等待的浪费”隐藏起来,使管理人员漠视等待的发生和存在。
(3)自然而然地积压在制品,其结果不但会使制程的时间变长(无形的),而且会使现场工作的空间变大,机器间距离因此加大,逐渐地吞蚀利润。
(4)产生搬运,堆积的浪费,使得先进先出的作业产生困难。
3、搬运的浪费不必要的搬运零件和产品,例如两个连续的生产工序,将产品在完成一个工序后,先运到仓库,然后再运到下一个工序。
较理想的情况是让两个工序的位置相邻,以便使产品能够从一个工序立即转到下一个工序。
产生搬运的主要原因为:车间布置采用批量生产,依工作站为区别的集中的水平式布置(也就是分工艺流程批量生产),无连续流生产的观念。
4、等待的浪费在生产过程中,操作员或者设备空闲。
产生等待的主要原因为:作业不平衡,安排作业不当、待料、品质不良等。
5、多余动作的浪费操作员所作的没有增值的动作,例如找零件,找工具、文件等。
产生多余动作的主要原因为:生产场地规划不好,生产模式设计不周全,生产动作不规范统一。
6、缺陷的浪费不良品和废品。
七大浪费——精选推荐

七⼤浪费七⼤浪费1.1 浪费的认识——是只增加成本及⼯时未增加任何附加价值的活动;——尽管是增加价值的活动,所⽤的资源超过了“绝对最少”的界限,也是浪费;1.2等待的浪费——等待就是闲着没事,等着下⼀个动作的来临。
另⼀种“监视机器”的浪费。
结果:会造成⼈员、作业、时间、机器的浪费及库存、在制品的增加。
分析:⼯序间作业不平衡、计划不周全、⼤批量⽣产、停⼯待料、品质不良、机器配置不当等、排除⼩故障、补充材料。
对策:平准化⽣产⽅式、⾃働化、防错裝置、快速換模、产品別配置。
1.3搬运的浪费——⼤多数⼈都会认为搬运是必需的动作,因为没有搬运,如何做下⼀个动作。
正因为如此,便有很多⼈默许它的存在,⽽不去设法消除它。
更有甚者,做了很长的传送带来代替这种搬运。
这种⽅式只能称为花⼤钱减少体⼒的消耗,但搬运本⾝的浪费并没有消除,反⽽被隐藏起来。
其中搬运浪费若分解开来看,⼜包含放置、堆积、移动、整理等动作的浪费。
结果:空间使⽤的浪费、⽣产⼒降低、搬运⼯时增加、搬运设备增加、不良的发⽣。
分析:⼯程别集中的⽔平式布置、Layout不合理、⼤批量⽣产、单能⼯、坐式作业、低活性度。
对策: U形线配置、流程式⽣產、多能⼯化、站⽴式作業、活性系数的改善、混载搬运。
1.4不良品的浪费——产品制造过程中,任何不良品产⽣,都会造成材料、机器、⼈⼯等,任何返修都是额外的成本⽀出。
若不良品⼀量成为报废品,更造成材料、⼈⼯等各种浪费,甚⾄增加处理报废的善后费⽤。
因此公司在推⾏精益⽣产时要强调第⼀次就把事情做好,前⼯程绝不把不良品流到后⼯程,彻底避免不良品的浪费。
结果:材料费的增加、⽣产⼒降低、检查⼈员、制程增加、不良、顾客抱怨增加。
分析:重视下游的作业、检查⽅法、检查基准不全、品质过剩、标准作业的不全。
对策:⾃働化、标准作业、防错裝置、全数检查、品保制度的健全。
1.5动作的浪费——不必要的动作,不产⽣附加价值的动作,过快或过慢的动作。
是不是要拿上、拿下如此频繁?有没有步⾏的动作、弯腰的动作、对准的动作、直⾓转弯的动作等?若⼯位设计的好,有很多动作都可被省掉。
七大浪费

丰田生产方式认为:“不产生附加价值的一切作业都是浪费”。
它把生产过程中的浪费问为以下七种(见下表):
1、生产过程的浪费。
一心想要多销售而大量生产,结果是人员、设备、材料、能源等方面都产生了浪费。
在没有需求的时候提前生产而产生浪费。
2、产生不合格品的浪费。
在生产过程中出现不合格品(次品、废品),会在原材料、零部件、返工或返修所需工时等生产不合格品所消耗的资源方面而产生浪费。
3、停工待产的浪费。
在进行机械加工时,机器发生故障不能正常作业,或因缺少零部件而停工等活等,在这样的状态下所产生的浪费都是停工待产的浪费。
4、动作的浪费。
不产生附加价值的动作、不合理的操作、效率低下的姿势和动作都是浪费。
5、搬运的浪费。
除去准时化生产所必须的搬运,其他任何搬运都是一种浪费。
如在不同仓库间移动、转运、长距离运输、运输次数过多和运输方法不档等。
6、加工本身的浪费。
把与工程的进展情况和产品质量没有任何关系的加工当作必要的加工而进行操作所产生的浪费。
7、库存的浪费。
因原材料、零部件、各道工序的半成品过多而产生的浪费。
这些产品过度积压还会引起库存管理费用的增加。
丰田七种浪费对策表。
七种浪费

七没事,等着下一个动作的来临, 这种浪费是无庸置疑的——很平常。造成等 这种浪费是无庸置疑的——很平常。造成等 待的原因通常有: 1.作业不平衡、 1.作业不平衡、 2.安排作业不当、 2.安排作业不当、 3.停工待料、 3.停工待料、 4.品质不良等 4.品质不良等
增加工序-现场 增加工序 现场 混乱
异地装箱-不必 异地装箱 不必 要造成
七种浪费之四:动作的浪费 七种浪费之四:
要达到同样作业的目的,会有不同的动作,哪些 动作是不必要的呢?是不是要拿上、拿下如此频繁? 动作是不必要的呢?是不是要拿上、拿下如此频繁? 有没有必要有反转的动作、步行的动作、弯腰的 动作、对准的动作、直角转弯的动作等? 设计得 动作、对准的动作、直角转弯的动作等?若设计得 好,有很多动作皆可被省掉!在管理理论 好,有很多动作皆可被省掉!在管理理论 >管理 理论中,专门有一种“动作研究” 理论中,专门有一种“动作研究”,但实施起来 比较复杂,我们完全可以用上述的基本思想,反 思一下日常工作中有哪些动作不合理?如何改进? 思一下日常工作中有哪些动作不合理?如何改进?
B51后背门呆滞及原辅库纸箱 B51后背门呆滞及原辅库纸箱
5、占用厂房空间、造成多馀的工场、仓库建设投资 、占用厂房空间、造成多馀的工场、仓库建设投资 的浪费。
6、设备能力及人员需求的误判:由於库存量的存在, 设备能力不平衡时也看不出(库存越多,越不容易 看出来)。人员是否过剩,也无法了解。由於有较 多的库存,供应部门需要增加人员,制造一线需要 更多的人员来生産産品用於补充库存,需要增添设 备来保证生産库存所需要的设备能力,从而形成新 一轮的浪费。
七种浪费之一:等待的浪 七种浪费之一: 费
等待的浪 费在我们 现场比比 皆是,像 右图中取 完件后等 待的情况 太多了。
Seven MODAS七种浪费
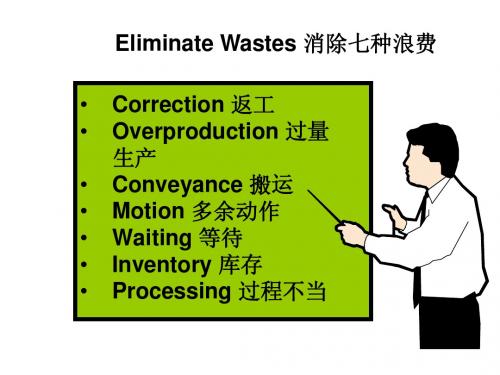
Eliminate Wastes 消除七种浪费 • • • • • • • Correction 返工 Overproduction 过量 生产 Conveyance 搬运 Motion 多余动作 Waiting 等待 Inventory 库存 Processing 过程不当
Definition of Wastes 什么是浪 费?
一切物料搬运
活动
Waste of Material Movement Conveyance 物料搬运
Characteristics特征:
• • • • • Extra Fork Trucks Multiple Storage Locations Extra Facility Space Incorrect Inventory Counts Opportunity for Damage 多余的叉车,空间,物品损坏
• Incapable Processes / 能力不足 • Operator Control Error / 操作不当 • Insufficient Training / 培训不足
企业七大浪费(7 Waste)概述

生產過剩產生的原因:
1. 大量生產 2. 投入過多人力與設備 3. 生產計劃預測錯誤 4. 設備稼動率過剩 5. 生產線停線是罪惡的想法
5
生產過剩的浪費
案例解析
10 人 / hr 作業,可生產 100 台
“ KAIZEN ”
10 人 / hr 作業,可生產 120 台
客戶需求只有 100 台,仍生產 120 台
產生支流搬運
庫存浪費產生的原因: 1. 生產線 Layout 不合理 2. 線平衡差導致WIP堆積 3. 生產過剩產生的WIP頻繁搬運
11
案解析
搬運的浪費
12
加工的浪費
定義:零件或半成品要送到下一個流程前,
在作業過程因技術(設計,加工)不足造成加工上的浪費。
表現形式: 1. 品質過剩 2. 二次修補 3. 重複測試 4. 加工方式錯誤 5. 總檢的存在
產品製作過程中作
2
業員的疏忽
3
沒有嚴格品管標準
18
案例解析
等待的浪費
鎖PCB板螺絲無防護罩,作業中螺絲打 滑,將PCB板銅箔打斷,板子報廢.
製作鎖螺絲保護治具,降低製程報廢率, 提高品質.
不良產生待修補或報廢,增加人工檢查與維修治具成本
19
浪費分類
生產過剩
加工
庫存
等待
搬運
物品的浪費
動作
人為的浪費
庫存浪費產生的原因: 1. 設計能力不足 2. 治具不當 3. 標準不明確 4. 人為疏忽
13
案例解析
加工的浪費
來料或包裝方式不方便作業
反饋客戶、廠商,改善來料、包裝方式, 方便作業
14
動作的浪費
定義:是指作業員沒有效率的動作所引發的浪費。
精益生产概述之七大浪费

精益生产概述之七大浪费精益生产是一种以消除浪费为核心的生产管理方法,旨在提高生产效率和质量。
七大浪费是精益生产的基本概念之一,它们是指在生产过程中存在的七种浪费现象,并且这些浪费都可以避免或减少。
以下是对七大浪费的简要概述。
1. 运输浪费:指在生产过程中不必要的物料运输或移动,例如将产品从一个车间搬到另一个车间,或者将材料从仓库搬到生产线。
运输浪费会增加生产时间和成本,并容易引起损坏或丢失。
2. 库存浪费:指生产过程中积压的过多原材料、半成品或成品库存。
库存浪费会增加库房和仓储成本,还可能导致过期、损坏或过时的物料。
3. 过程中的等待浪费:指在生产过程中由于机器故障、零部件不足或工人等待等原因导致的停工或非生产时间。
等待浪费会降低生产效率,增加生产周期,并导致交货延迟。
4. 过度加工浪费:指在生产过程中对产品进行过多或不必要的加工。
过度加工浪费会增加生产成本,并可能导致质量问题或产品过度精细化。
5. 度量浪费:指在生产过程中由于测量、追踪或监控不足导致的效率低下或质量问题。
度量浪费会增加错误率和修复成本,并且可能导致产品不符合客户要求。
6. 过剩生产浪费:指生产过程中超出客户需求的产品或数量。
过剩生产浪费会增加库存和仓储成本,并降低资金周转率。
7. 动作浪费:指生产过程中不必要的动作或无效的动作,包括重复、走动、等待、纠正错误等。
动作浪费会降低工人的效率和舒适度,增加生产时间和成本。
精益生产的目标是通过识别和消除这些浪费,提高生产效率和质量,实现产品的快速交付和客户满意度的提升。
通过精益生产的实施,企业可以提高生产线的流程,优化生产方式,减少生产成本,并最大限度地提高企业的竞争力和盈利能力。
精益生产的实施需要从各个方面入手,包括流程优化、员工参与和培训、设备改进等。
下面将进一步探讨精益生产的相关内容,以及其对企业的影响和益处。
首先,要实施精益生产,必须对生产流程进行优化。
通过识别和消除七大浪费,可以简化生产流程,降低生产周期,并提高产品的质量和交货效率。
精益七大浪费7waste
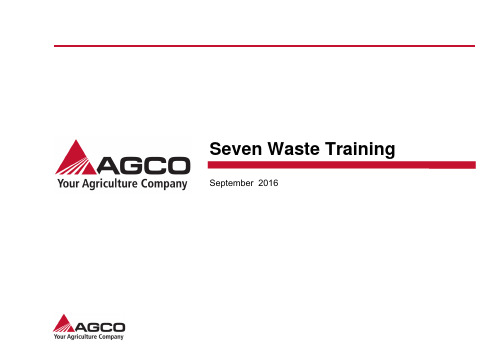
需要多余的人工和设备,
需要多余的水,电,气等能源
增加了设备的损耗
增加管理等成本
23
七大浪费:过度加工的浪费 过度加工的浪费一般有: 提供较高品质的产品,例如超过客户要求的标准 不必要的工艺步骤 (普通车削三遍才能完成的工作改良后车两遍就能符
合要求 )
习惯性的零件的全检(可以是每隔几天做一次检查) 过度的包装等等 改善方法: 正确理解客户的技术要求,严格按照技术要求加工零件
25
七大浪费:返工的浪费 返工的浪费一般有: 作业者作业不熟练造成缺陷 产品包装,保护不到位造成的缺陷
没有标准作业,产品质量不稳定
改善方法: 提升OJT培训 推行PFEP,对每颗物料,采用什么样的包装都具体化 实施标准作业,对产品质量偏差进行管控
26
目录
1 2 3
9
七大浪费:运输浪费 运输浪费的表现: 物料及零部件的运输不能增加价值,而且还占用: 额外的资源 (包括人力,物料,运输设备)
管理
临时库存区域 (空间) 零件转运的次数越多,受损的可 能性就越大 缩短了搬运工具的使用寿命
10
七大浪费:运输浪费 运输的产生 不合理的布局,过长,迂回的运输路线 不合理的搬运工具 不科学的搬运方法 改善方法: 重新调整,改善生产线布局,减少搬运距离,提升搬运效率 改善搬运工具,选择合适的搬运工具 制定标准化的搬运路线,对搬运路线进行距离分析,采用精益的 方案。(Milk Run)
17
七大浪费:动作浪费 动作的浪费: 动作的浪费有: 寻找工具 弯腰侧身取料 登高,爬梯 走动 改善方法: 物料补放到线边,遵循使用点物料(POU)原则 工具箱使用行迹管理,并且工具靠近员工使用点 5S 改善
七大浪费(不含管理的浪费)
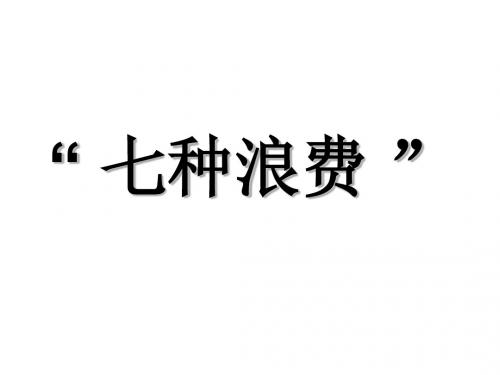
四:动作的浪费
• 反思一下日常工作中有哪些动作不合理? 如何改进?
五:加工的浪费
• 在制造过程中,为了达到作业的目的, 有一些加工程序是可以省略、替代、重组 或合并的,若是仔细地加以检查,你将可 发现,又有不少的浪费等着你去改善。
六:库存的浪费
• " 库存是万恶之源 " 。因为: • 1 、产生不必要的搬运、堆积、放置、防护 处理、找寻等浪费。 • 2 、使先进先出的作业困难。 • 3 、损失利息及管理费用。 • 4 、物品的价值会减低,变成呆滞品。 • 5 、占用厂房空间,造成多余的工场、仓库 建设投资的浪费。 • 6 、设备能力及人员需求的误判:
把无序变有序
• • • • • • 企业的管理混乱的原因: “没有规矩,不成方圆” 。 职责不清造成的无序。 业务能力低下造成的无序。 有章不循造成的无序 。 业务流程的无。
三:不良品的浪费
• 要用一切办法来消 除、减少一切非增 值活动,例如检验、搬运和等待等造成的 浪费,具体方法就是推行 " 零返修率 " ,。
一:等待的浪费
• • • • • • 造成等待的原因通常有: 作业不平衡、 安排作业不当、 停工待料、 品质不良等。 " 监视机器 " —— " 闲视 " 的浪费。 • • • • 等待上级的指示。 等待下级的汇报。 等待对方的
30000 40000 50000 60000 75000 100000
“ 七种浪费 ”
提案改善的內容
1 2 3 4 5 6 品質 成本 機器 失誤 效率 管理 降低不良、提高品質、防止訴怨、減少異常、減少變異、維持管 制狀態 刪減費用、減少工時、縮短時間、減少材料 防止故障、自動化、改良夾具與工具、改善佈置 疏忽失誤、事故、檢驗失誤、資訊失誤 生產量、時間、及時性、生產管制、交期改善 標準化、對策、管理點、防止再發、切實管理
7 Waste七大浪费

精益生产培训课程系列—— 认识浪费
以最节省人力的状态取得岗位需要的零件或工具,避免所有的动作浪费
Lean Manufacturing
35
精益生产培训课程系列—— 认识浪费
大家一起来谈谈常见的12种动作浪费 • 两手空闲 • 单手空闲 • 作业动作不连贯停顿
• 动作太大
Lean Manufacturing
=
=
Lean Manufacturing
43
精益生产培训课程系列—— 认识浪费
企业中的各个环节的生产能力普遍不均衡的原因,总 会出现“瓶颈”存在。 非瓶颈生产过快,瓶颈流不出去,必然会有库存产生。
Lean Manufacturing
44
精益生产培训课程系列—— 认识浪费
总结以上,有七种浪费:
1. 等待的浪费 2. 搬运的浪费 3. 不良品的浪费 4. 动作的浪费 5. 过量加工的浪费 6. 库存的浪费 7. 过量生产的浪费 Lean Manufacturing
过量加工的浪费
与产品价值核心不相关的加工与作业都是浪费
Lean Manufacturing
32
精益生产培训课程系列—— 认识浪费
避免了不必要的加工动作
排除
减小
物品加工时的不顺利
工作时间的浪费
Lean Manufacturing
33
精益生产培训课程系列—— 认识浪费
动 作 的 浪 费
Lean Manufacturing
45
这些都不 能存在
精益生产培训课程系列—— 认识浪费
第一节 如何发现浪费
Lean Manufacturing
46
精益生产培训课程系列—— 认识浪费
精益生产名词解释:七大浪费与意大利面条图

精益生产名词解释:七大浪费与意大利面条图SevenWastes(七种浪费)
精益生产里把大规模制造方法的浪费划分成七个主要类别:
1.过量生产:制造多于下一个工序,或是顾客需求的产品。
这是浪费形式中最严重的一种,因为它会导致其它六种浪费
2.等待:在生产周期中,操作员空闲的站在一旁;或是设备失效;或是需要的零部件没有运到等
3.搬运:不必要的搬运零件和产品,例如两个连续的生产工序,将产品在完成一个工序后,先运到仓库,然后再运到下一个工序。
较理想的情况是让两个工序的位置相邻,以便使产品能够从一个工序立即转到下一个工序
4.返工:进行不必要的修正加工,通常是由于选用了较差的工具或产品缺陷而导致
5.库存:现有的库存多于拉动系统所规定的最小数量
6.操作:操作员所作的没有增值的动作,例如找零件,找工具、文件等
7.改正:检查,返工,和废品
参见:Changeover(换模),Set-UpReduction(减少转换时间)
SpaghettiChart(意大利面条图)
按照一件产品沿着价值流各生产步骤路径的所绘制的图。
之所以叫这个名字,是因为大批量制造路径非常复杂通常看起来像一盘意大利面条。
参见:MaterialFlow(物料流)。
精益生产管理中的7大浪费1完整篇.doc
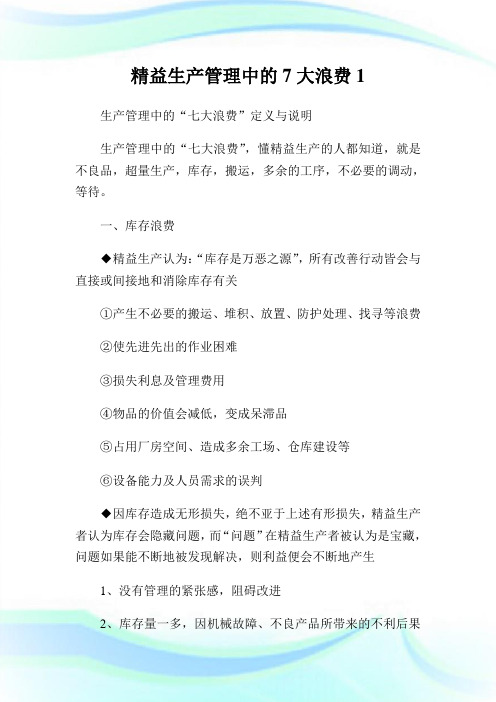
精益生产管理中的7大浪费1 生产管理中的“七大浪费”定义与说明生产管理中的“七大浪费”,懂精益生产的人都知道,就是不良品,超量生产,库存,搬运,多余的工序,不必要的调动,等待。
一、库存浪费◆精益生产认为:“库存是万恶之源”,所有改善行动皆会与直接或间接地和消除库存有关①产生不必要的搬运、堆积、放置、防护处理、找寻等浪费②使先进先出的作业困难③损失利息及管理费用④物品的价值会减低,变成呆滞品⑤占用厂房空间、造成多余工场、仓库建设等⑥设备能力及人员需求的误判◆因库存造成无形损失,绝不亚于上述有形损失,精益生产者认为库存会隐藏问题,而“问题”在精益生产者被认为是宝藏,问题如果能不断地被发现解决,则利益便会不断地产生1、没有管理的紧张感,阻碍改进2、库存量一多,因机械故障、不良产品所带来的不利后果不能马上显现出来,因而也不会产生对策3、由于有了充足的库存,出现问题时可以用库存先顶上,问题就可以慢慢解决甚至不用解决,最起码是被掩盖住了,不急迫了,不会被上级追究了,于是乎本部门的工作成绩就出来了二、过渡生产(制造过多或过早浪费)◆TPS强调的是“适时生产”◆多做能提高效率,提早做好能减少产能损失(不做白不做,机器还不是一样停着?)1、提早用掉了材料费、人工费而已,并不能得到什么好处2、把“等待浪费”隐藏,使管理人员漠视等待的发生和存在3、积压在制品,使生产周期L/T变长(无形的),而且会使现场工作空间变大,不知不觉吞蚀我们的利润4、产生搬运、堆积浪费,先进先出变得困难三、品质缺陷(不良品浪费)◆任何的不良品产生,皆会造成材料、机器、人工等的浪费◆及早发现不良品,容易确定不良来源,进而减少不良品的产生◆关键是第一次要把事情做对,“零缺陷”四、运输(搬运浪费)◆大部分人皆认同搬运是一种无效的动作,也有人认为搬运是必须的◆用“输送带”的方式来克服,行吗?1、取放浪费;2、等待浪费;3、在制品过多浪费;4、空间浪费◆搬运浪费又包含放置、堆积、移动、整理等动作的浪费五、处理(加工浪费)◆定义:指的是与工程进度及加工精度无关的不必要的加工◆有一些加工程序是可以省略、替代、重组或合并◆很多时候会习惯并认为现在的做法较好六、动作浪费12种动作浪费:◆两手空闲◆单手空闲◆不连贯停顿◆幅度太大◆左右手交换◆步行多◆转身角度大◆移动中变换状态◆不明技巧◆伸背动作◆弯腰动作◆重复不必要动作七、等待浪费◆生产线的品种切换◆工作量少时,便无所事事◆时常缺料,设备闲置◆上工序延误,下游无事可做◆设备发生故障◆生产线工序不平衡◆有劳逸不均的现象◆制造通知或设计图未送达精益生产管理中的七大浪费7 精益生产管理中的七大浪费精益生产管理方式是企业在适应社会生产模式由简单生产方式――大生产方式――小批量多品种生产方式的转变过程中而发展起来的,在贴近客户需求及企业生产效益两方面同时达成最优化的生产方式。
7种浪费
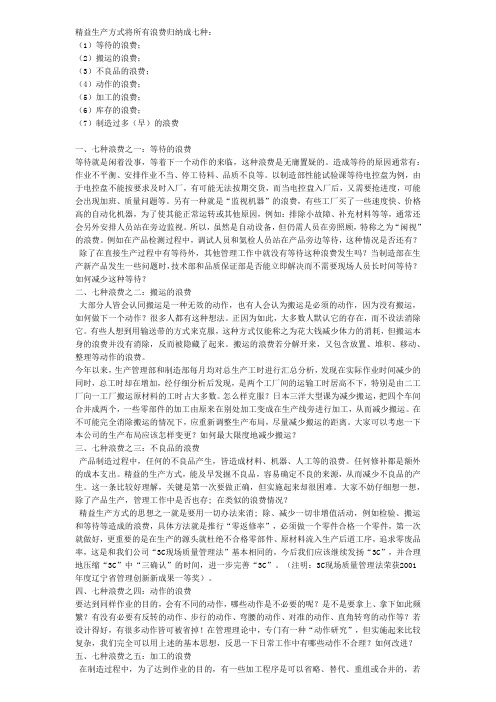
精益生产方式将所有浪费归纳成七种:(1)等待的浪费;(2)搬运的浪费;(3)不良品的浪费;(4)动作的浪费;(5)加工的浪费;(6)库存的浪费;(7)制造过多(早)的浪费一、七种浪费之一:等待的浪费等待就是闲着没事,等着下一个动作的来临,这种浪费是无庸置疑的。
造成等待的原因通常有:作业不平衡、安排作业不当、停工待料、品质不良等。
以制造部性能试验课等待电控盘为例,由于电控盘不能按要求及时入厂,有可能无法按期交货,而当电控盘入厂后,又需要抢进度,可能会出现加班、质量问题等。
另有一种就是“监视机器”的浪费,有些工厂买了一些速度快、价格高的自动化机器,为了使其能正常运转或其他原因,例如:排除小故障、补充材料等等,通常还会另外安排人员站在旁边监视。
所以,虽然是自动设备,但仍需人员在旁照顾,特称之为“闲视”的浪费。
例如在产品检测过程中,调试人员和氦检人员站在产品旁边等待,这种情况是否还有?除了在直接生产过程中有等待外,其他管理工作中就没有等待这种浪费发生吗?当制造部在生产新产品发生一些问题时,技术部和品质保证部是否能立即解决而不需要现场人员长时间等待?如何减少这种等待?二、七种浪费之二:搬运的浪费大部分人皆会认同搬运是一种无效的动作,也有人会认为搬运是必须的动作,因为没有搬运,如何做下一个动作?很多人都有这种想法。
正因为如此,大多数人默认它的存在,而不设法消除它。
有些人想到用输送带的方式来克服,这种方式仅能称之为花大钱减少体力的消耗,但搬运本身的浪费并没有消除,反而被隐藏了起来。
搬运的浪费若分解开来,又包含放置、堆积、移动、整理等动作的浪费。
今年以来,生产管理部和制造部每月均对总生产工时进行汇总分析,发现在实际作业时间减少的同时,总工时却在增加,经仔细分析后发现,是两个工厂间的运输工时居高不下,特别是由二工厂向一工厂搬运原材料的工时占大多数。
怎么样克服?日本三洋大型课为减少搬运,把四个车间合并成两个,一些零部件的加工由原来在别处加工变成在生产线旁进行加工,从而减少搬运。
- 1、下载文档前请自行甄别文档内容的完整性,平台不提供额外的编辑、内容补充、找答案等附加服务。
- 2、"仅部分预览"的文档,不可在线预览部分如存在完整性等问题,可反馈申请退款(可完整预览的文档不适用该条件!)。
- 3、如文档侵犯您的权益,请联系客服反馈,我们会尽快为您处理(人工客服工作时间:9:00-18:30)。
Seven Wastes
13
Example
搬运的浪费
物料储存区距离使用单位非常远
( 仓库到针车19线有 100 米的距离 )
仓库
结果: 我们必须通知搬运员去哪里取料 我们需要额外的库存区 我们需要额外的物料搬运员和设备
Seven Wastes 14
等待的浪费
定义: 人、机器或产品在 “睡觉” 影响:时间、空间、劳力、潜在的报废、 $$$ 原因:不清楚或没有标准,布置等 • 范例 …………..?
Seven Wastes
15
Waste of Waiting (People) 人的等待
In the above photo, why was this waste generated? 在这个例子中,为什么浪费会产生呢?
Seven Wastes 16
Waste of waiting (machine) 机器的等待
Seven Wastes
29
多余制程的浪费
定义: 在加工或组装产品中,做一些对顾客品质期望不必要的操作工序 • 影响:时间、成本、劳力、$$$ • 原因:不清楚或没有标准 范例 …………..?
Seven Wastes
30
Waste of Over-Process 多余制程的浪费
What causes this waste? 计算半成品的数量. 为什么会产生这样的浪费呢 ?
•
不可避免的不增加价值活动 Incidental 没有增加价值,但在当前的技术及生产条件下无法避免的 生产活动。
•
浪费(不增加价值) Non Value Added – 没有增加价值(改变材料的形状、形式或 功能),且可以立刻消除的活动。
Seven Wastes
7
三种活动的分类
增加价值
不增加价值
不必要
•
•
Seven Wastes
33
现场练习
浪费的种类 1) 提前/过量生 产 2) 等待 现场实例 影响? 如何改善? 改善前后的对比,附图片
3) 搬运
4) 多余制程
5) 库存
6) 动作
7) 不良
Seven Wastes
34
生产排程 停机 长距离 搬运 品质 生产线 不平衡 厂商的 交期问题 沟通 问题 旷工
换模 时间长
工作 环境
通过问题解决活动可以使生产航行顺利,同时减少库存。
Seven Wastes
成
品
原 材 料
27
动作的浪费
定义: 人或机器因素造成不符人因工程或额外的移动
影响:时间、人因问题、劳力、 $$$ 原因:作业流程, 布局、机台设定 ? 范例…………………… ……………………?
Seven Wastes 31
多余制程的浪费
裁斷
點料 在裁斷 檢驗 包裝 點料 半成品 倉庫 點料 在針車
針車
Seven Wastes
32
丰田公司与“消除浪费”
•
Muda – 浪费 – 七大浪费,即本课程所讨论的内容。 Muri – 超负载 – 员工或机器的工作负荷或压力超出其正常负荷水平。 Mura – 不平衡 – 员工之间的工作负荷不平衡。
Seven Wastes
成
品
原 料 材
25
库存的海洋 -
“海水与礁石"
库存的海洋
生产排程 停机 长距离 搬运 品质 生产线 不平衡 厂商的 交期问题 换模 时间长 旷工 沟通 问题
工作 环境
减少库存,暴露库存所掩盖的问题。
Seven Wastes
成
品
原 材 料
26
库存的海洋 -
“海水与礁石"
库存的海洋
Seven Wastes
9
客户需要更短的交期
客户订单
浪费
时间
X
产品出货
X
客户订单
WASTE
产品出货
精益生产协助缩短从接单到产品 出货的整个交期.
时间
Seven Wastes
10
七大浪费
过量生产 提前生产或生产了多于客户需求的产品。通常这种浪费会产生其他形 式的浪费,比如由于处理过多的库存而引起的冗员、存储空间、及搬 运的成本。 员工唯一能做的事情就是监视机器的运转,或者等待着去进行下一道 工序,等待工具、零件、材料,等等。 在一道工序内需要将在制品(WIP)搬运到另一个地点,或者需要把 材料、部件或成品在仓库(及在工序间)搬进搬出。 在加工部件的生产过程中需要采取不必要的工序。这些导致效率低下 的工序是由于产品设计、有瑕疵的工具及流程设计而引起;同时还会 造成不必要的动作浪费及不良品的浪费。 多余的原材料、在制品或成品库存会引起较长的生产交期、仓储呆料、 物料损坏、搬运以及增加仓储的成本和交货的延期。 在工作过程中,除了对部件进行的增加价值的活动外,其他的非增加 价值活动,如站起来拿物料、起身寻找材料、堆叠材料、工具,等等。 生产不良品及对不良品进行修正的生产活动,如返修不良品、报废、 修复不良品所进行的补足生产。
Deep well pressing machine
Why was this waste generated?
Seven Wastes
为什么浪费会产生呢?
17
过量生产的浪费
• 定义:制造超过顾客需求或提前生产 • 影响:时间、搬运、空间、劳力、 $$$ 、潜在的品质问题, 导致其它形式的浪费 • 原因:不稳定的工作环境(停机时间、品质问题、工会等 ) • 范例: …………..?
Seven Wastes
28
Waste of Motion
动作的浪费
Pick up the below box to make FITwist and pick up parts from flo FO w rack 根据先进先出的原则, 需要拿起底下的箱子 转动身体从物架取料
What is causing this waste? 什么原因造成浪费?
Seven Wastes
18
Waste of Overproduction
过量生产的浪费
Why is it generated? 为什么会产生这 样的浪费呢?
Seven Wastes
19
过量生产的浪费
倉庫
更多库存 = 更多资金 進 5500prs 出 1500prs
• 更多不良 • 額外處理 • 額外空間
结果
• 額外機器 • 額外文件作業 • 多人 • 額外費用
Seven Wastes
20
不良的浪费
定义: 制造必须补修、重工或报废的不良品 影响:时间,劳力,$$$ 原因:不清楚或没有标准,不正确的机台设定 ..? 范例 ………… …………..?
Seven Wastes
21
Defect Examples
Seven Wastes
3
你会这些付钱吗?
面饼? 酱料? 面馅? 盒子? 掉在地上的馅料? 烤炉的电? 一夜没关烤炉耗用的电? 电话费? 没事干的员工?
Seven Wastes
4
NOS Focuses on the Customer 关注客户
The Customer is the ONLY one who defines the VALUE of the product. 客户是唯一定义产品价值的人。 Anything not adding Value to the product is WASTE. 任何不增加价值的活动就是浪费
23
Waste of Inventory 库存的浪费
In process Inventory 在制品库存
是否可以减少在制品, 建立超市概念和运作 Component W/H 半成品库存
Seven Wastes 24
库存的海洋 - “海水与礁石"
库存的海洋
生产排程 停机 长距离 搬运 品质 生产线 不平衡 厂商的 交期问题 换模 时间长 旷工 沟通 问题 工作 环境
必要
保持
减少
尚不存在
消除!
Seven Wastes
8
Why Remove Wastes?
• If you want to lose weight or train to run a marathon, would you eat the following foods?
•
Why is it essential that we focus on eliminating waste?
Seven Wastes 七大浪费
03F 7Waste.ppt.ppt
NOS House Foundations
消除浪费
5S/目视管理
TPM
平准化
Seven Wastes2学习目标Understand Waste Definition 理解浪费的定义 e 理解浪费的七 � Understand the Seven forms of Wast Waste 种形式 � Identify examples of each 识别每种浪费的例子 � Understand steps to eliminate waste 理解消除浪费 的步骤
Bond Gap
Paint Touch-up
Seven Wastes
22
库存的浪费
• 定义: 耗用更多材料 (原物料、在线在制品、成品) • 影响:等待时间、资金紧张、劳力、搬运、 $$$ 、潜在的品质 问题、掩盖住问题 • 原因:过量生产, 某些流程需要的时间比较少 范例……………….?
Seven Wastes
Seven Wastes 12
两个一角硬币
搬运的浪费
定义:从一个地方到另一地产品的移动 (靠手拿、推车、输送带、 卡车等) 影响:时间、成本、设备、劳力、潜在的品质问题 原因:工厂布置、单元设计 ..? 范例 ………… …………..?