管道焊缝射线探伤数量和合格年级别
工艺管线焊缝探伤等级及合格标准

25
2、VT=外观检测
RT=X射线检测
MT=磁粉检测
PT=着色渗透检测
UT=超声波检测
3、焊接接头的无损检测应执行JB4730-94
RT检测时: ①、检测比例大于5% Ⅱ级合格 ②、检测比例5%
Ⅲ级合格
UT检测时: ①、检测比例100% Ⅰ级合格 ②、检测比例为局部 Ⅱ级合格
MT/PT检测时:Ⅰ级合格
4、在被检测的焊接接头中,固定焊的焊接接头不得少于40%,且不少于1个焊接接头。
承插焊缝 VT MT或PT
100% 100%
P<10.0MPa且-29℃≤T<400℃
介质:毒性程度为极度危害介质的苯
、毒性程度为高度危害介质(丙烯腈 20%
20%
、光气、二硫化碳和氟化氢除外)和
A1D、A1E、A1F、A1J、A1K
甲A类液化烃
、A1NR、A1P、A1PA、A1WR
P<4.0MPa且T≥400℃ 介质:毒
2 B1A、B21D、D1A、D54A、
B
H1A、H1D、H3A、H3B
5%
5%
不要求 5%
5%
5%
5% 不要求
A1DA、A1DB、A1DC、A21BB
3 、B1DA、B1DB、D25B、
C
D55B、B1DC
4 F1A、F1D、F21B、G54A、
D
10%
20%
不要求 10%
20%
20% 10% 20%
10%
、乙A类可燃气体
P<4.0MPa且T≥400℃ 介质:甲类
、乙类可燃气体和甲B类、乙A类可 10%
10%
燃气体
20% 20%
20%
20% 20%
焊缝质量标准及等级

管道类别Ⅰ(1)毒性程度为极度危害的流体管道;(2)设计压力大于或等于10MPa的可燃流体、有毒流体的管道;(3)设计压力大于或等于4MPa、小于10MPa,且设计温度大于等于400℃的可燃流体、有毒流体的管道;(4)设计压力大于或等于10MPa,且设计温度大于或等于400℃的非可燃流体、无毒流体的管道;(5)设计文件注明为剧烈循环工况的管道;(6)设计温度低于-20℃的所有流体管道;(7)夹套管的内管;(8)按本规范第8.5.6条规定做替代性试验的管道;(9)设计文件要求进行焊缝100%无损检测的其他管道。
Ⅱ(1)设计压力大于或等于4MPa、小于10MPa,设计温度低于400℃,毒性程度为高度危害的流体管道;(2)设计压力小于4MPa,毒性程度为高度危害的流体管道;(3)设计压力大于或等于4MPa、小于10MPa,设计温度低于400℃的甲、乙类可燃气体和甲类可燃液体的管道;(4)设计压力大于或等于10MPa,且设计温度小于400℃的非可燃流体、无毒流体的管道;(5)设计压力大于或等于4MPa、小于10MPa,且设计温度大于等于400℃的非可燃流体、无毒流体的管道;(6)设计文件要求进行焊缝20%无损检测的其他管道。
Ⅲ(1)设计压力大于或等于4MPa、小于10MPa,设计温度低于400℃,毒性程度为中毒和轻度危害的流体管道;(2)设计压力小于4MPa的甲、乙类可燃气体和甲类可燃液体管道;(3)设计压力大于或等于4MPa、小于10MPa,设计温度低于400℃的乙、丙类可燃液体管道;(4)设计压力大于或等于4MPa、小于10MPa,设计温度低于400℃的非可燃流体、无毒流体的管道;(5)设计压力大于1MPa小于4MPa,设计温度高于或等于400℃的非可燃流体、无毒流体的管道;(6)设计文件要求进行焊缝10%无损检测的其他管道。
Ⅳ(1)设计压力小于4MPa,毒性程度为中毒和轻度危害的流体管道;(2)设计压力小于4MPa的乙、丙类可燃液体管道;(3)设计压力大于1MPa小于4MPa,设计温度低于400℃的非可燃流体、无毒流体的管道;(4)设计压力小于或等于1MPa,且设计温度大于185℃的非可燃流体、无毒流体的管道;(5)设计文件要求进行焊缝5%无损检测的其他管道。
焊缝质量标准及等级

管道类别Ⅰ(1)毒性程度为极度危害的流体管道;(2)设计压力大于或等于10MPa的可燃流体、有毒流体的管道;(3)设计压力大于或等于4MPa、小于10MPa,且设计温度大于等于400℃的可燃流体、有毒流体的管道;(4)设计压力大于或等于10MPa,且设计温度大于或等于400℃的非可燃流体、无毒流体的管道;(5)设计文件注明为剧烈循环工况的管道;(6)设计温度低于-20℃的所有流体管道;(7)夹套管的内管;(8)按本规范第8.5.6条规定做替代性试验的管道;(9)设计文件要求进行焊缝100%无损检测的其他管道。
Ⅱ(1)设计压力大于或等于4MPa、小于10MPa,设计温度低于400℃,毒性程度为高度危害的流体管道;(2)设计压力小于4MPa,毒性程度为高度危害的流体管道;(3)设计压力大于或等于4MPa、小于10MPa,设计温度低于400℃的甲、乙类可燃气体和甲类可燃液体的管道;(4)设计压力大于或等于10MPa,且设计温度小于400℃的非可燃流体、无毒流体的管道;(5)设计压力大于或等于4MPa、小于10MPa,且设计温度大于等于400℃的非可燃流体、无毒流体的管道;(6)设计文件要求进行焊缝20%无损检测的其他管道。
Ⅲ(1)设计压力大于或等于4MPa、小于10MPa,设计温度低于400℃,毒性程度为中毒和轻度危害的流体管道;(2)设计压力小于4MPa的甲、乙类可燃气体和甲类可燃液体管道;(3)设计压力大于或等于4MPa、小于10MPa,设计温度低于400℃的乙、丙类可燃液体管道;(4)设计压力大于或等于4MPa、小于10MPa,设计温度低于400℃的非可燃流体、无毒流体的管道;(5)设计压力大于1MPa小于4MPa,设计温度高于或等于400℃的非可燃流体、无毒流体的管道;(6)设计文件要求进行焊缝10%无损检测的其他管道。
Ⅳ(1)设计压力小于4MPa,毒性程度为中毒和轻度危害的流体管道;(2)设计压力小于4MPa的乙、丙类可燃液体管道;(3)设计压力大于1MPa小于4MPa,设计温度低于400℃的非可燃流体、无毒流体的管道;(4)设计压力小于或等于1MPa,且设计温度大于185℃的非可燃流体、无毒流体的管道;(5)设计文件要求进行焊缝5%无损检测的其他管道。
管道焊接检验标准

管道焊接对焊接方式和焊接质量,应按设计规定套用相应定额。
如设计无规定时,可参考以下规定套用相应定额项目。
1.Ⅰ、Ⅱ级焊缝以及管内壁清洁度要求严格,且焊后不易清理的管道(如透平机入口管、锅炉给水管、机组的循环油、控制油、密封油管道等)单面焊缝、宜采用氩电联焊。
合金钢管焊缝采用氩弧焊打底时,焊缝内侧宜充氩气保护。
2.奥氏体不锈钢管单面焊的焊缝,宜采用手工钨极氩弧焊打底,手工电弧焊填充盖面(氩电联焊)。
公称直径在50毫米以下的采用氩弧焊。
3.Ⅲ级以下焊缝碳钢管,公称直径在50毫米以下的(壁厚在3.5毫米以下)采用氧炔焊。
4.管道分类见表1注:⑴剧毒介质的管道按Ⅰ类管道。
⑵有毒介质,甲、乙类火灾危险物质的管道均升一类。
⑶“工作压力”项内任意为不分压力均为一级管道。
5.管口焊前预热和焊后热处理要求见表2。
注:⑴当焊接环境温度低于零度时,除规定壁厚必须作预热要求的金属外,其余金属壁厚也均应作适当的预热,使被焊接母材有手温感。
规定必须作预热要求的金属,定额项目内的预热消耗已考虑了温度变化因素,故不再增加预热。
⑵有应力腐蚀的碳素钢、合金钢,不论其壁厚条件,均应进行焊后热处理。
6.管口焊缝无损探伤计算规定数据:(1)管口焊接含量取定见表3。
表3(2)每个管口焊缝X光拍片张数,如无规定者可按表4计算。
表4注:⑴公称直径80毫米以下的管道焊缝X光透视检查拍片,一个焊口要求至少拍两张片。
定额中采用的胶片为85×300毫米的,实际上可用85×150毫米的胶片,执行定额时,人工和机械使用费壁变,材料费乘0.5系数。
⑵片子有效长度按片长减去搭接每边25毫米计算。
⑶管道焊口透视拍片的张数=管道等级规定的探伤百分比×焊口数量×张数(见表4)(3)管道各级焊缝射线探伤数量,应按设计规定计算。
如设计无规定时,按表5规定计算。
注:每条管线上最低探伤不得少于一个焊口。
焊缝质量规范标准及其等级

管道类别Ⅰ(1)毒性程度为极度危害的流体管道;(2)设计压力大于或等于10MPa的可燃流体、有毒流体的管道;(3)设计压力大于或等于4MPa、小于10MPa,且设计温度大于等于400℃的可燃流体、有毒流体的管道;(4)设计压力大于或等于10MPa,且设计温度大于或等于400℃的非可燃流体、无毒流体的管道;(5)设计文件注明为剧烈循环工况的管道;(6)设计温度低于-20℃的所有流体管道;(7)夹套管的内管;(8)按本规范第8.5.6条规定做替代性试验的管道;(9)设计文件要求进行焊缝100%无损检测的其他管道。
Ⅱ(1)设计压力大于或等于4MPa、小于10MPa,设计温度低于400℃,毒性程度为高度危害的流体管道;(2)设计压力小于4MPa,毒性程度为高度危害的流体管道;(3)设计压力大于或等于4MPa、小于10MPa,设计温度低于400℃的甲、乙类可燃气体和甲类可燃液体的管道;(4)设计压力大于或等于10MPa,且设计温度小于400℃的非可燃流体、无毒流体的管道;(5)设计压力大于或等于4MPa、小于10MPa,且设计温度大于等于400℃的非可燃流体、无毒流体的管道;(6)设计文件要求进行焊缝20%无损检测的其他管道。
Ⅲ(1)设计压力大于或等于4MPa、小于10MPa,设计温度低于400℃,毒性程度为中毒和轻度危害的流体管道;(2)设计压力小于4MPa的甲、乙类可燃气体和甲类可燃液体管道;(3)设计压力大于或等于4MPa、小于10MPa,设计温度低于400℃的乙、丙类可燃液体管道;(4)设计压力大于或等于4MPa、小于10MPa,设计温度低于400℃的非可燃流体、无毒流体的管道;(5)设计压力大于1MPa小于4MPa,设计温度高于或等于400℃的非可燃流体、无毒流体的管道;(6)设计文件要求进行焊缝10%无损检测的其他管道。
Ⅳ(1)设计压力小于4MPa,毒性程度为中毒和轻度危害的流体管道;(2)设计压力小于4MPa的乙、丙类可燃液体管道;(3)设计压力大于1MPa小于4MPa,设计温度低于400℃的非可燃流体、无毒流体的管道;(4)设计压力小于或等于1MPa,且设计温度大于185℃的非可燃流体、无毒流体的管道;(5)设计文件要求进行焊缝5%无损检测的其他管道。
压力管道安装施工有关无损检测的规定
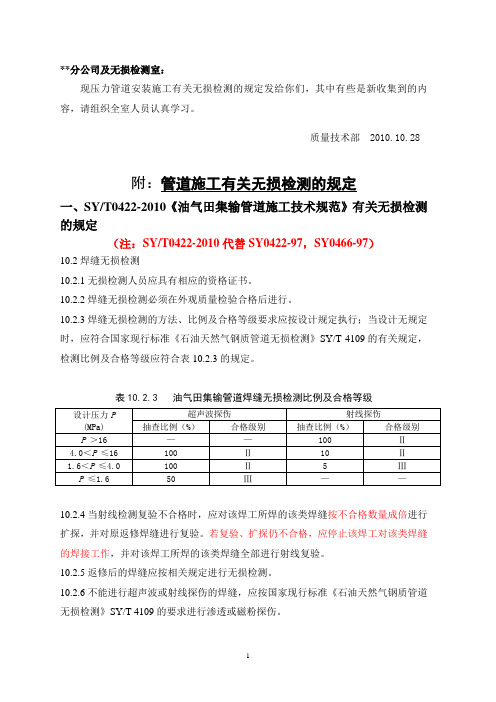
**分公司及无损检测室:现压力管道安装施工有关无损检测的规定发给你们,其中有些是新收集到的内容,请组织全室人员认真学习。
质量技术部 2010.10.28附:管道施工有关无损检测的规定一、SY/T0422-2010《油气田集输管道施工技术规范》有关无损检测的规定(注:SY/T0422-2010代替SY0422-97,SY0466-97)10.2焊缝无损检测10.2.1无损检测人员应具有相应的资格证书。
10.2.2焊缝无损检测必须在外观质量检验合格后进行。
10.2.3焊缝无损检测的方法、比例及合格等级要求应按设计规定执行;当设计无规定时,应符合国家现行标准《石油天然气钢质管道无损检测》SY/T 4109的有关规定,检测比例及合格等级应符合表10.2.3的规定。
表10.2.3 油气田集输管道焊缝无损检测比例及合格等级10.2.4当射线检测复验不合格时,应对该焊工所焊的该类焊缝按不合格数量成倍进行扩探,并对原返修焊缝进行复验。
若复验、扩探仍不合格,应停止该焊工对该类焊缝的焊接工作,并对该焊工所焊的该类焊缝全部进行射线复验。
10.2.5返修后的焊缝应按相关规定进行无损检测。
10.2.6不能进行超声波或射线探伤的焊缝,应按国家现行标准《石油天然气钢质管道无损检测》SY/T 4109的要求进行渗透或磁粉探伤。
二、《石油天然气建设工程施工质量验收规范站内工艺管道工程》SY/T 4203-2007有关无损检测的规定8.1.27 焊缝无损检测应由GB/T9445考试合格并取得相应资格证书的检测人员承担,评片应由取得Ⅱ级资格证书及以上的检测人员承担。
8.1.28 焊缝外观检查合格后应对其进行无损检测。
无损检测应按SY/T4109的管道执行。
8.1.29无损检测的比例及验收合格等级应符合设计要求。
如没有规定时,应按下列管道执行:a) 管道对接焊缝无损检测数量及合格等级应符合表8的规定。
b) 穿越站场道路的管道焊缝、试压后连头的焊缝应进行100%射线照相检查。
管道焊缝射线探伤数量和合格级别

SY4056<<石油天然
气钢制管道对接焊缝射线照相及质量
分级>>
SY4065<<石油天然
气钢制管道对接焊缝超声波探伤及质量分级>>
焊缝的射线探伤可用超声波代替,合格级别与射线探伤相同,超声波探伤数量不少于射线探伤数量。
当选用超声波探伤时,应对超声波探伤部位作射线复验,复验数量为规定探伤数量5%,且不得少于一条焊缝。
设计压力大于1.6Mpa 的管道环焊缝宜选用射线探伤。
注汽管道的焊缝的无损探伤除符合上述规定外,合格级别为Ⅱ级的焊缝不得有未焊透缺陷,当选用超生探伤时,应对超生探伤的部位作20%的射线复验。
油田集输管道类别和等级划分方法
管道焊缝射线探伤数量和合格级别
焊接层数及焊条直径
焊道焊接应采用多层焊,焊道熔渣应清除干净,并进行外观检查,合格后可进行下道焊接。
低氢焊条在常温下4h应重新烘干,重复烘干次数不得超过两次。
管道焊接探伤比例
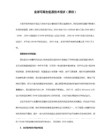
(1)输送剧毒流体的管道;
( 2 )输送设计压力大于等于 10MPa 或设计压力大于等于 4MPa
且设计温度大于等于400℃的可燃流体、有毒流体的管道;
( 3 )输送设计压力大于等于 10MPa 且设计温度大于等于 400 ℃
的非可燃流体、无毒流体的管道;
(4)设计温度小于-29℃的低温管道。
(5)设计文件要求进行100%射线照相检验的其他管道。
7.4.3.2输送设计压力小于等于1MPa且设计温度小于400℃的非可燃流体管道、无毒流体管道的焊缝,可不进行射线照相检验。
7.4.3.3其他管道应进行抽样射线照相检验,抽检比例不得低于5%,
其质量不得低于III级。抽检比例和质量等级应符合设计文件的要求。
管道焊接探伤比例
100%和5%就两种
规范是这样规定的:
7.4.2管道焊缝的射线照相检验或超声波检验应及时进行。当抽样检验
时,应对每一焊工所焊焊缝按规定的比例进行抽查,检验位置应由施
工单位和建设单位的验数量应符合下列规定:
7.4.3.1下列管道焊缝应进行100%射线照相检验,其质量不得低于
焊缝合格标准

焊缝合格级别及无损检测要点一、长输管道:1.SY0410—98《输油输气管道线路工程施工及验收规范》第7.3.2条:RT执行SY4056—93;UT执行SY4065—93合格级别:输油:P设≤6.4MPa Ⅲ级P设>6.4MPa Ⅱ级输气:P设≤4MPa 一、二级地区Ⅲ级;三、四级地区Ⅱ级P设>4MPa Ⅱ级第7.3.4条:输油管道的探伤比例可任选下面其中之一:100%UT后,对每个焊工或机组每天完成数量的5%作射线复验只进行RT抽查,抽查比例为每个焊工或作业机组每天完成数量的15% 。
第7.3.5条:输气管道的探伤比例:100%UT后,对每个焊工或作业机组每天完成数量的抽查比例:一级地区5%二级地区10%三级地区15%四级地区20%只进行RT抽查,对每个焊工或作业机组每天完成数量的抽查比例:一级地区10%二级地区15%三级地区40%四级地区75%第7.3.6条:抽查时,如每天的焊口数量比例达不到比例要求时,可以每公里为一个检验段,并按规定的比例数随焊随查,均匀的复验、抽查。
第7.3.7条:射线探伤复验,抽查中,有一个焊口不合格,应对该焊工或机组段焊接焊口加倍检查,再不合格,则其余焊口逐个RT探伤第7.3.8条:穿越焊口,钢管与弯头连接的焊口,试压后连头的碰口应进行100%RT。
第7.3.9条:×60及以上级别管材,返修后应按《常压钢制焊接储罐及管道渗透检测技术标准》SY/T0443进行渗透检查。
第7.3.10条:探伤人员应取得相关主管部门颁发的证书。
2.SY0470—2000《石油天然气跨越工程施工及验收规范》第5.3.2条:焊缝外观检查合格之后,应进行无损探伤。
焊缝无损探伤应符合下列规定:跨越管道环向焊缝应进行100%射线探伤。
对射线探伤难度大的个别环向焊缝部位,经有关部门共同商定可用超声波探伤代替射线探伤,但其数量不准超过总数10%。
RT符合SY4056 Ⅱ级合格;UT符合SY4065 Ⅱ级合格二、集输管道:1.SY0466—97《天然气集输管道施工及验收规范》第5.2条无损探伤:第5.2.1条:无损探伤人员必须具备劳动部门颁发的Ⅰ级以上资格证,评片人员具有Ⅱ级及其以上资格;第5.2.2条:焊缝无损探伤必须在外观质量检验合格后进行;第5.2.3条:设计无规定时,管道环缝100%UT,每个焊工所焊的各类焊缝应第5.2.5条:当RT复验不合格,应对该焊工所焊该类焊缝按原射线探伤复验数量补充探伤,仍不合格,停止其工作,并对其于焊工所焊焊缝进行100%RT 复验。
焊缝的无损检测要求及等级分类解释
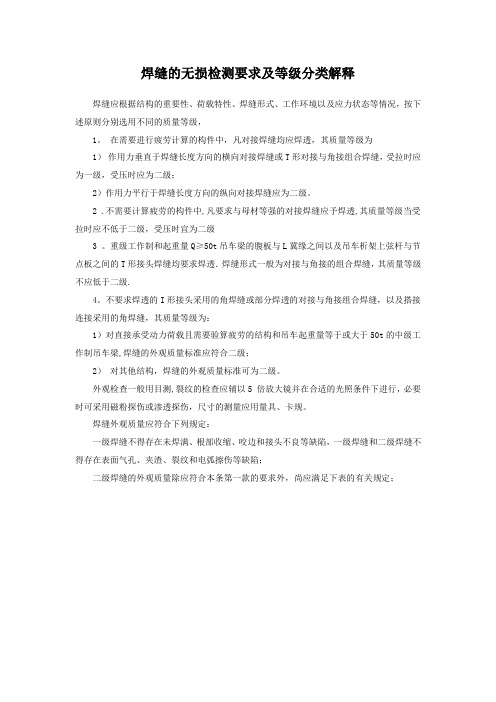
焊缝的无损检测要求及等级分类解释焊缝应根据结构的重要性、荷载特性、焊缝形式、工作环境以及应力状态等情况,按下述原则分别选用不同的质量等级,1。
在需要进行疲劳计算的构件中,凡对接焊缝均应焊透,其质量等级为1)作用力垂直于焊缝长度方向的横向对接焊缝或T形对接与角接组合焊缝,受拉时应为一级,受压时应为二级;2)作用力平行于焊缝长度方向的纵向对接焊缝应为二级。
2 .不需要计算疲劳的构件中,凡要求与母材等强的对接焊缝应予焊透,其质量等级当受拉时应不低于二级,受压时宜为二级3 。
重级工作制和起重量Q≥50t吊车梁的腹板与L冀缘之间以及吊车析架上弦杆与节点板之间的T形接头焊缝均要求焊透.焊缝形式一般为对接与角接的组合焊缝,其质量等级不应低于二级.4。
不要求焊透的I形接头采用的角焊缝或部分焊透的对接与角接组合焊缝,以及搭接连接采用的角焊缝,其质量等级为:1)对直接承受动力荷载且需要验算疲劳的结构和吊车起重量等于或大于50t的中级工作制吊车梁,焊缝的外观质量标准应符合二级;2)对其他结构,焊缝的外观质量标准可为二级。
外观检查一般用目测,裂纹的检查应辅以5 倍放大镜并在合适的光照条件下进行,必要时可采用磁粉探伤或渗透探伤,尺寸的测量应用量具、卡规。
焊缝外观质量应符合下列规定:一级焊缝不得存在未焊满、根部收缩、咬边和接头不良等缺陷,一级焊缝和二级焊缝不得存在表面气孔、夹渣、裂纹和电弧擦伤等缺陷;二级焊缝的外观质量除应符合本条第一款的要求外,尚应满足下表的有关规定;设计要求全焊透的焊缝,其内部缺陷的检验应符合下列要求:1 一级焊缝应进行100%的检验,其合格等级应为现行国家标准GB/T 11345—2013《钢焊缝手工超声波探伤方法及质量分级法》B 级检验的Ⅱ级及Ⅱ级以上;2 二级焊缝应进行抽检,抽检比例应不小于20%,其合格等级应为现行国家标准GB/T 11345—2013《钢焊缝手工超声波探伤方法及质量分级法》B级检验的Ⅲ级及Ⅲ级以上;3 全焊透的三级焊缝可不进行无损检测。
管道焊缝射线探伤数量和合格年级别
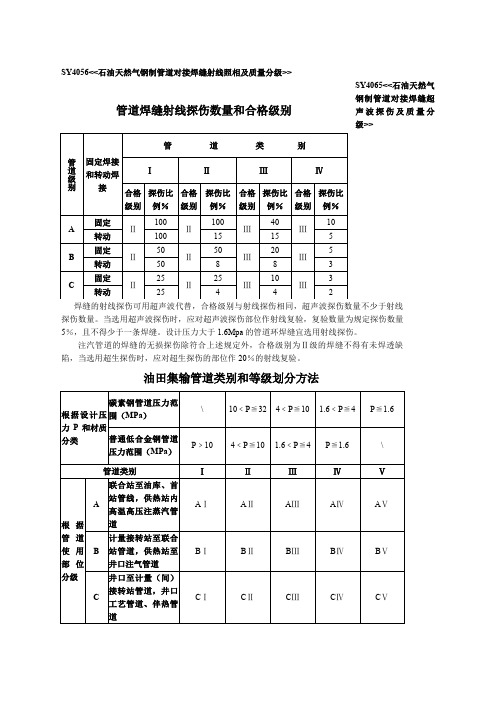
SY4056<<石油天然气钢制管道对接焊缝射线照相及质量分级>>
SY4065<<石油天然气钢制管道对接焊缝超
声波探伤及质量分级>>
焊缝的射线探伤可用超声波代替,合格级别与射线探伤相同,超声波探伤数量不少于射线探伤数量。
当选用超声波探伤时,应对超声波探伤部位作射线复验,复验数量为规定探伤数量5%,且不得少于一条焊缝。
设计压力大于1.6Mpa 的管道环焊缝宜选用射线探伤。
注汽管道的焊缝的无损探伤除符合上述规定外,合格级别为Ⅱ级的焊缝不得有未焊透缺陷,当选用超生探伤时,应对超生探伤的部位作20%的射线复验。
油田集输管道类别和等级划分方法
管道焊缝射线探伤数量和合格级别
焊接层数及焊条直径
焊道焊接应采用多层焊,焊道熔渣应清除干净,并进行外观检查,合格后可进行下道焊接。
低氢焊条在常温下4h应重新烘干,重复烘干次数不得超过两次。
射线探伤标准

射线探伤标准5.1.1 范围本条规定适用于厚度为2mm至400mm的碳素钢、低合金钢、奥氏体不锈钢、镍及镍合金制承压设备,以及厚度为2mm至80mm的铜及铜合金制承压设备的熔化焊对接焊接接头射线检测的质量分级。
管子和压力管道环向对接焊接接头射线检测质量分级按照第6章规定执行。
5.1.2 缺陷类型对接焊接接头中的缺陷按性质可分为裂纹、未熔合、未焊透、条形缺陷和圆形缺陷共五类。
5.1.3 质量分级依据根据对接接头中存在的缺陷性质、数量和密集程度,其质量等级可划分为Ⅰ、Ⅱ、Ⅲ、Ⅳ级。
5.1.4 质量分级一般规定5.1.4.1 I级对接焊接接头内不允许存在裂纹、未熔合、未焊透和条形缺陷。
5.1.4.2Ⅱ级和Ⅲ级对接焊接接头内不允许存在裂纹、未熔合和未焊透。
5.1.4.3对接焊接接头中缺陷超过Ⅲ级者为Ⅳ级。
5.1.4.4当各类缺陷评定的质量级别不同时,以质量最差的级别作为对接焊接接头的质量级别。
5.1.5 圆形缺陷的质量分级5.1.5.1圆形缺陷用圆形缺陷评定区进行质量分级评定,圆形缺陷评定区为一个与焊缝平行的矩形,其尺寸见表8.圆形缺陷评定区应选在缺陷最严重的区域。
表8 缺陷评定区(mm)母材公称厚度T 评定区尺寸25 10×1025~100 10×20100 10×305.1.5.2在圆形缺陷评定区内或与圆形缺陷评定区边界线相割的缺陷均应划入评定区内。
将评定区内的缺陷按表9的规定换算为点数,按表10的规定评定对接焊接接头的质量级别。
表9 缺陷点数换算表缺陷长径,mm 缺陷点数1 l1~2 22~3 33~4 64~6 106~8 158 25表10 各级别允许的圆形缺陷点数评定区(mm×mm) 母材公称厚度T,mmI级 II级 UI级10 1 3 610~15 2 6 1215~25 3 9 1825~50 4 12 2450~100 5 15 3010×30 6 18 36100 6 18 36 Ⅳ级注:当母材公称厚度不同时,取较薄板的厚度。
管道焊缝无损探伤拍片数量的确定

管道焊缝无损应按设计文件或规范要求进行,工程量按现场实际拍片数量计算。拍片数量如设 计有要求时,按设计规定计算,如无规定,参照下表执行: 每一管口焊缝拍片规格及数量参考表 管外径(mm) ≤89 102 108 133 159 219 273 325 377 426 478 529 片子规格(mm) 150 150 150 150 300 300 300 300 300 300 300 300 X射线拍片(张/口) 低、中压管 2 4 6 6 6 6 6 6 6 6 6 7 高压管 2 4 8 8 8 8 8 8 8 7 7 7 γ 射线拍片(张/口) 高压管 2 4 6 6 6 6 6 6 6 6 6 7
注:1、DN600以上的管道焊缝无损探伤按管口周长计算工程量,片子的有效长度按片长减去搭 接每边25mm计算。 2、当管道外径小于或等于φ 89mm时,采用双壁双投影法透照;管道外径大于φ 108mm时, 其焊缝采用双壁单投影法透照。
片数量如设ຫໍສະໝຸດ
焊缝质量分级
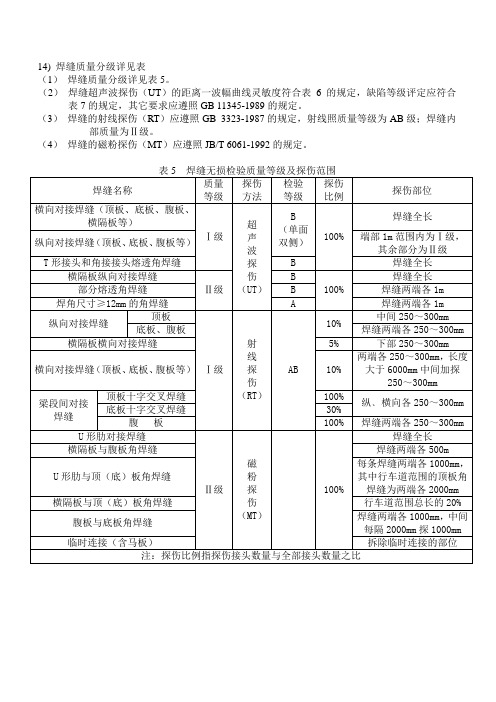
U形肋与顶(底)板角焊缝
每条焊缝两端各1000mm,其中行车道范围的顶板角焊缝为两端各2000mm
横隔板与顶(底)板角焊缝
行车道范围总长的20%
腹板与底板角焊缝
焊缝两端各1000mm,中间每隔2000mm探1000mm
临时连接(含马板)
拆除临时连接的部位
注:探伤比例指探伤接头数量与全部接头数量之比
注3:如果超声波探伤已可准确认定焊缝存在裂纹,则应判定焊缝质量不合格;
注4:Φ6﹑Φ3﹑Φ2表示纵波探伤的平底孔参考反射体尺寸。
表7缺陷等级评定
评定等级
板厚
单个缺陷指示长度
对接焊缝Ⅰ级
8~100
t/3,最小可为10,最大不超过30
对接焊缝Ⅱ级
2t/3,最小可为12,最大不超过30
全熔透角焊缝Ⅰ级
t/3,最小可为10,最大不超过30
(4)焊缝的磁粉探伤(MT)应遵照JB/T 6061-1992的规定。
表5焊缝无损检验质量等级及探伤范围
焊缝名称
质量等级
探伤
方法
检验
等级
探伤
比例
探伤部位
横向对接焊缝(顶板、底板、腹板、横隔板等)
Ⅰ级
超
声
波
探
伤
(UT)
B
(单面双侧)
100%
焊缝全长
纵向对接焊缝(顶板、底板、腹板等)
端部1m范围内为Ⅰ级,
横向对接焊缝(顶板、底板、腹板等)
10%
两端各250~300mm,长度大于6000mm中间加探250~300mm
梁段间对接焊缝
顶板十字交叉焊缝
100%
纵﹑横向各250~300mm
射线探伤标准

5.1.1范围
本条规定适用于厚度为2mm~400mm的碳素钢、低合金钢、奥氏体不锈钢、镍及镍合金制承压设
备,以及厚度为2mm~80mm的铜及铜合金制承压设备的熔化焊对接焊接接头射线检测的质量分级。
管子和压力管道环向对接焊接接头射线检测质量分级按照第6章规定执行。
5.1.2缺陷类型
对接焊接接头中的缺陷按性质可分为裂纹、未熔合、未焊透、条形缺陷和圆形缺陷共五类。
5.1.3质量分级依据
根据对接接头中存在的缺陷性质、数量和密集程度,其质量等级可划分为Ⅰ、Ⅱ、Ⅲ、Ⅳ级。
5.1.4 质量分级一般规定
5.1.4.1 I级对接焊接接头内不允许存在裂纹、未熔合、未焊透和条形缺陷。
5.1.4.2Ⅱ级和Ⅲ级对接焊接接头内不允许存在裂纹、未熔合和未焊透。
5.1.4.3对接焊接接头中缺陷超过Ⅲ级者为Ⅳ级。
5.1.4.4 当各类缺陷评定的质量级别不同时,以质量最差的级别作为对接焊接接头的质量级别。
5.1.5圆形缺陷的质量分级
5.1.5.1 圆形缺陷用圆形缺陷评定区进行质量分级评定,圆形缺陷评定区为一个与焊缝平行的矩形,其尺寸见表8。
圆形缺陷评定区应选在缺陷最严重的区域。
表8 缺陷评定区 mm
5.1.5.2 在圆形缺陷评定区内或与圆形缺陷评定区边界线相割的缺陷均应划入评定区内。
将评定区内的缺陷按表9的规定换算为点数,按表10的规定评定对接焊接接头的质量级别。
表9 缺陷点数换算表
表10 各级别允许的圆形缺陷点数。
管道焊缝等级探伤比例
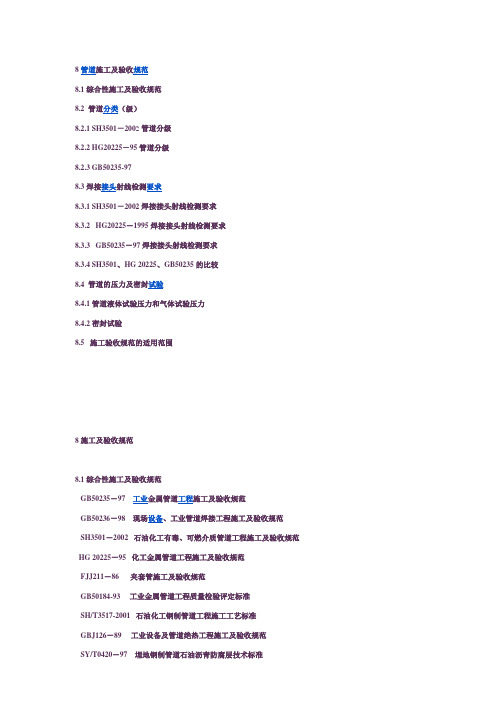
8管道施工及验收规范8.1综合性施工及验收规范8.2 管道分类(级)8.2.1 SH3501-2002管道分级8.2.2 HG20225-95管道分级8.2.3 GB50235-978.3焊接接头射线检测要求8.3.1 SH3501-2002焊接接头射线检测要求8.3.2 HG20225-1995焊接接头射线检测要求8.3.3 GB50235-97焊接接头射线检测要求8.3.4 SH3501、HG 20225、GB50235的比较8.4 管道的压力及密封试验8.4.1管道液体试验压力和气体试验压力8.4.2密封试验8.5 施工验收规范的适用范围8施工及验收规范8.1综合性施工及验收规范GB50235-97 工业金属管道工程施工及验收规范GB50236-98 现场设备、工业管道焊接工程施工及验收规范SH3501-2002 石油化工有毒、可燃介质管道工程施工及验收规范 HG 20225-95化工金属管道工程施工及验收规范FJJ211-86 夹套管施工及验收规范GB50184-93 工业金属管道工程质量检验评定标准SH/T3517-2001 石油化工钢制管道工程施工工艺标准GBJ126-89 工业设备及管道绝热工程施工及验收规范SY/T0420-97 埋地钢制管道石油沥青防腐层技术标准HGJ229-91 工业设备、管道防腐蚀工程施工及验收规范SH3022-1999 石油化工设备和管道涂料防腐蚀技术规范SH3010-2000 石油化工设备和管道隔热技术规范CCJ28-89 城市供热网工程施工及验收规范CJJ/T81-98 城镇直埋供热管道工程技术规程CJJ33-89 城镇燃气输配工程施工及验收规范8.2 管道分类(级)在施工验收规范中,不同的介质、不同的操作条件的管道其检测要求是不同的。
8.2.1 SH3501-2002管道分级SH3501将管道分为SHA、SHB、SHC、SHD四个等级。
表8-1 SH3501-2002管道分级8.2.2 HG20225-95管道分级HG20225-95将管道分为A、B、C、D四个等级表8-2 HG20225-95管道分级8.2.3 GB50235-97取消了管道分类,按照设计温度、设计压力和介质类别来区分1) 设计温度分为:t ≥400℃、-29≤t<400℃、t<-29;2) 设计压力分为:P≥10.0MPa(≤42.0)、P<10.0 MPa、4.0≤P<10.0 MPa、P<4.0 MPa、3) 介质: 剧毒、有毒、可燃介质、无毒、非可燃介质(GB5044、)注:剧毒介质即GB5044《职业性接触毒物危害程度分级》中I级危害程度的介质;有毒介质按GB5044《职业性接触毒物危害程度分级》中II级及以下危害程度的介质;可燃介质按GB50160《石油化工企业设计防火规范》分类8.3焊接接头射线检测要求8.3.1 SH3501-2002焊接接头射线检测要求表8-3 SH3501-2002焊接接头射线检测要求※SH3501考虑了石油化工的特点,对有毒、可燃介质管道做了详细的规定。
焊缝 无损检测标准
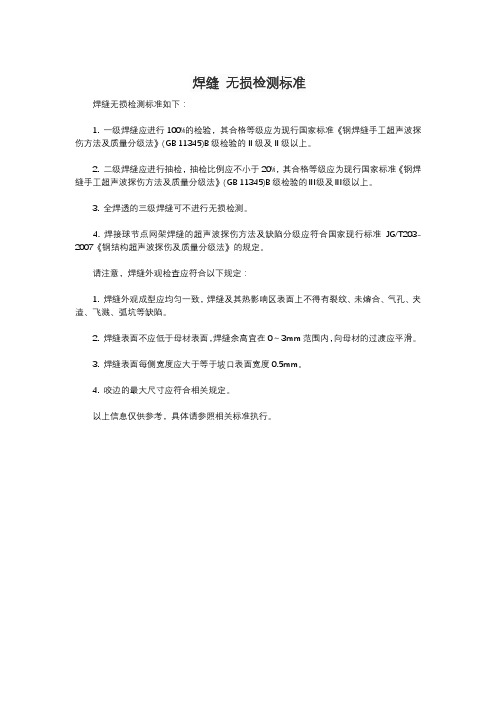
焊缝无损检测标准
焊缝无损检测标准如下:
1. 一级焊缝应进行100%的检验,其合格等级应为现行国家标准《钢焊缝手工超声波探伤方法及质量分级法》(GB 11345)B级检验的Ⅱ级及Ⅱ级以上。
2. 二级焊缝应进行抽检,抽检比例应不小于20%,其合格等级应为现行国家标准《钢焊缝手工超声波探伤方法及质量分级法》(GB 11345)B级检验的Ⅲ级及Ⅲ级以上。
3. 全焊透的三级焊缝可不进行无损检测。
4. 焊接球节点网架焊缝的超声波探伤方法及缺陷分级应符合国家现行标准JG/T203-2007《钢结构超声波探伤及质量分级法》的规定。
请注意,焊缝外观检查应符合以下规定:
1. 焊缝外观成型应均匀一致,焊缝及其热影响区表面上不得有裂纹、未熔合、气孔、夹渣、飞溅、弧坑等缺陷。
2. 焊缝表面不应低于母材表面,焊缝余高宜在0~3mm范围内,向母材的过渡应平滑。
3. 焊缝表面每侧宽度应大于等于坡口表面宽度0.5mm。
4. 咬边的最大尺寸应符合相关规定。
以上信息仅供参考,具体请参照相关标准执行。
工业管道的焊接

工业管道的焊接第一节材料要求第1.1.1 条管道组成件必须具有制造厂的合格证明书,否则应补所缺项目的检验。
第 1.1.2 条焊接工程中所用的母材和焊接材料应具备出厂质量合格证明书或质量复验报告。
第 1.1.3 条焊接工程中应优先选用已列入国家标准或部颁标准的母材和焊接材料。
第 1.1.4 条如设计选用未列入标准的母材和焊接材料,应说明该材料的可焊性,并提出满足设计要求的焊接工艺试验资料。
第二节主要机具第1.2.1 条焊接设备:包括交流电焊机、直流电焊机、氩弧焊机。
第 1.2.2 条机具包括:坡口加工机、切割机、角向磨光机、台式钻诃、等离子弧切割机、焊矩。
第 1.2.3 条计量器具包括:柜式水平仪、焊接检验尺,内外径千分尺、内外径卡尺、深度游标尺、高度游标尺、万能角度尺、光学水准仪、光学经纬仪。
第1.2.4 条液压千斤顶、液压式万能材料试验机、热处理设备、微控电子式拉力试验机、便携式数显里氏硬度计、光谱分析仪。
第1.2.5 条探伤设备及其它:X 射线擦伤机、超声波探伤仪、梯粉探伤机、智能化X 射线探伤机、远红外线干燥机。
第三节作业条件第1.3.1 条与管道有关的土建工程、金属结构工程检验合格,满足管道安装要求。
第1.3.2 条与管道连接的机械设备,容器已找正固定,或已确定管口方位及标高。
第1.3.3 条管道组成件已清理完毕,并满足设计规定的特殊清理要求。
第1.3.4 条管道加工及预制完成,并编号。
第1.3.5 条焊接平台按工程要求制作完成。
第四节操作工艺第 1.4.1 条工艺流程:备料→焊工资格认可→坡口制备→焊接工艺评定→夹具准备→装配定位→施焊→焊后处理→焊接检验第 1.4.2 条焊工1.压力管道所用焊工必须取得由长沙市技术监督局批准颁发的《锅炉压力容器焊工合格证》,且只限于焊接《合格证》内规定的项目。
2.“压力容器焊工合格证”有效期为三年,超过有效期后必须重新办理,否则视为无效。
3.焊工累计合格项目满足GB235-82 中表4.4.1 规定的所有材质的焊接。
管道焊缝射线探伤数量和合格级别

SY4056<<石油天然气钢制管道对接焊缝射线照相及质量分
级>>
SY4065<<石油天然气钢制管道对接焊缝超声波探伤及质量分级>>
焊缝的射线探伤可用超声波代替,合格级别与射线探伤相同,超声波探伤数量不少于射线探伤数量。
当选用超声波探伤时,应对超声波探伤部位作射线复验,复验数量为规定探伤数量5%,且不得少于一条焊缝。
设计压力大于1.6Mpa 的管道环焊缝宜选用射线探伤。
注汽管道的焊缝的无损探伤除符合上述规定外,合格级别为Ⅱ级的焊缝不得有未焊透缺陷,当选用超生探伤时,应对超生探伤的部位作20%的射线复验。
油田集输管道类别和等级划分方法
管道焊缝射线探伤数量和合格级别
焊接层数及焊条直径
焊道焊接应采用多层焊,焊道熔渣应清除干净,并进行外观检查,合格后可进行下道焊接。
低氢焊条在常温下4h应重新烘干,重复烘干次数不得超过两次。
- 1、下载文档前请自行甄别文档内容的完整性,平台不提供额外的编辑、内容补充、找答案等附加服务。
- 2、"仅部分预览"的文档,不可在线预览部分如存在完整性等问题,可反馈申请退款(可完整预览的文档不适用该条件!)。
- 3、如文档侵犯您的权益,请联系客服反馈,我们会尽快为您处理(人工客服工作时间:9:00-18:30)。
SY4056<<石油天然
气钢制管道对接焊缝射线照相及质量分
级>>
SY4065<<石油天然气钢制管道对接焊缝超声波探伤及质量分级>>
焊缝的射线探伤可用超声波代替,合格级别与射线探伤相同,超声波探伤数量不少于射线探伤数量。
当选用超声波探伤时,应对超声波探伤部位作射线复验,复验数量为规定探伤数量5%,且不得少于一条焊缝。
设计压力大于1.6Mpa 的管道环焊缝宜选用射线探伤。
注汽管道的焊缝的无损探伤除符合上述规定外,合格级别为Ⅱ级的焊缝不得有未焊透缺陷,当选用超生探伤时,应对超生探伤的部位作20%的射线复验。
油田集输管道类别和等级划分方法
管道焊缝射线探伤数量和合格级别
焊接层数及焊条直径
焊道焊接应采用多层焊,焊道熔渣应清除干净,并进行外观检查,合格后可进行下道焊接。
低氢焊条在常温下4h应重新烘干,重复烘干次数不得超过两次。