回转窑煅烧冶金石灰工艺研究与实践
石灰回转窑煅烧技术

石灰回转窑煅烧技术石灰回转窑煅烧技术是一种常用于石灰生产的工艺。
通过将石灰石放入回转窑中进行煅烧,可以将其转化为高活性的石灰,广泛应用于建筑材料、冶金、化工等行业。
一、石灰回转窑的结构和原理石灰回转窑是一种圆筒形的设备,通常由筒体、支撑装置、传动装置、焚化装置、气体进出口等部分组成。
在石灰石进入回转窑后,通过传动装置将其慢慢旋转,使石灰石在高温下进行煅烧。
石灰石煅烧的过程中,主要经历以下几个阶段:预热阶段、分解阶段、石灰化阶段和冷却阶段。
在预热阶段,石灰石中的水分和部分游离二氧化碳会被释放出来。
随着温度的升高,石灰石会进入分解阶段,二氧化碳会被彻底释放出来。
接下来是石灰化阶段,石灰石中的钙氧化物会与二氧化碳反应生成石灰。
最后是冷却阶段,石灰会被冷却至合适的温度后取出。
二、石灰回转窑煅烧技术的优势石灰回转窑煅烧技术相比于其他石灰生产工艺具有以下优势:1. 温度控制精准:石灰回转窑可以通过控制回转速度和燃烧器的热量输出来控制煅烧温度,使其达到最佳值,从而保证石灰的质量稳定。
2. 热能利用高效:石灰回转窑的结构设计使得煅烧过程中产生的余热可以被充分利用,用于预热石灰石和干燥原料,提高能源利用效率。
3. 适应性强:石灰回转窑可以适应不同种类的石灰石,且处理能力大,可以满足大规模生产的需求。
同时,还可以处理含有杂质的石灰石,提高了原料利用率。
4. 环境友好:石灰回转窑采用闭路燃烧方式,减少了烟气排放,对环境影响较小。
并且通过煅烧过程中产生的高温燃烧,可以将有害物质完全破坏,减少了对环境的污染。
三、石灰回转窑煅烧技术的应用石灰回转窑煅烧技术在建筑材料、冶金、化工等行业有着广泛的应用。
1. 建筑材料行业:石灰是制作砂浆、砖块、混凝土等建筑材料的重要原料,石灰回转窑煅烧技术可以生产出高活性的石灰,提高建筑材料的质量。
2. 冶金行业:石灰在冶金过程中有着重要的作用,可以用于炼钢、脱硫等工艺。
石灰回转窑煅烧技术可以生产出高纯度的石灰,满足冶金行业的需求。
回转窑烧石灰工艺

回转窑烧石灰工艺回转窑烧石灰工艺是一种常见的生产石灰的方法。
这种工艺的原理是将石灰石放入回转窑中,通过高温烧制,使其分解成氧化钙和二氧化碳。
这种工艺具有高效、节能、环保等优点,因此在石灰生产中得到了广泛应用。
回转窑烧石灰工艺的主要流程包括石灰石的破碎、预热、烧结和冷却等环节。
首先,将石灰石经过破碎后送入预热器中进行预热,使其达到一定温度。
然后将预热后的石灰石送入回转窑中进行烧结,烧结过程中需要控制炉内温度和氧气含量,以保证石灰石的分解反应能够顺利进行。
最后,将烧结后的石灰石送入冷却器中进行冷却,使其达到室温后即可包装出售。
回转窑烧石灰工艺具有以下优点:1.高效:回转窑烧石灰工艺可以实现连续生产,生产效率高,生产能力大。
2.节能:回转窑烧石灰工艺采用了预热器和冷却器,可以充分利用热能,减少能源消耗。
3.环保:回转窑烧石灰工艺可以减少二氧化碳的排放,对环境污染较小。
4.质量稳定:回转窑烧石灰工艺可以控制炉内温度和氧气含量,保证石灰石的分解反应能够顺利进行,从而保证产品质量稳定。
回转窑烧石灰工艺也存在一些缺点:1.设备投资大:回转窑烧石灰工艺需要大型设备,设备投资较大。
2.炉内温度难以控制:回转窑烧石灰工艺中,炉内温度难以精确控制,容易影响产品质量。
3.烟气处理难度大:回转窑烧石灰工艺中,烟气中含有大量的二氧化碳和氮氧化物等有害物质,需要进行处理。
总的来说,回转窑烧石灰工艺是一种高效、节能、环保的石灰生产方法,具有广泛的应用前景。
随着科技的不断发展,回转窑烧石灰工艺也将不断改进和完善,为石灰生产带来更多的便利和效益。
煅烧冶金石灰活性度分析

分, 随着煅烧 温度 的不断升高 , 生成 C O・i2由 首先 a So ,
于有过量 的 C O气 氛 ,反应 向硅酸 钙最大饱 和量进 a 行, 直到生成 3 a SO 。 i2 A23 F 23 C O反 C O・i2 S 、 1 、 e 与 a O 0 0
依 据石 灰石煅烧机理 和上述 ( ) ( ) 学反应式 1 、2 化
22 冶金 石灰 活性度 理论 计算 公 式的推 导 .
石灰 中的化学 成分为 :a 、 O、i 2 I 3F23 C O Mg S 、 2 、e O Ao o
采用现代化 的煅 烧工艺技术 , 制定科学合理 的石灰窑 工 艺技术操 作参数 , 才能 煅烧 出高质 量 、 活性 度 的 高 冶金石灰 , 满足现代化炼钢生产要 求。实 践证 明 , 断 判 石灰 石原料 是否合 适 , 类石灰 竖窑 的设计 , 化制 各 优 定工艺技术参 数 , 往往有一 定的技术难 度 。其理论计 算是科学 的重 要论证方法 。资料显示 , 计算 活性度公
式较多 . 观点不 一致 , 不规 范。经实践检验 , 有些公式
及其它微 量元素 . 仅有 C O水解消耗 H 1 a C 。石灰活性 度( 生石灰 在水 中的消化 速度 ) 的测试 原理 , 以找 出 可
H1 C 消耗量 与 C O 的理论关系 。 a
C O H(一C ( H) a + 2_ aO 2 ) C ( H22 C- C C + 2 aO ) H 1- a h H 0 + -  ̄ C O 2 C- ̄a 1 H 0 a + H 1 C C2 2 - + () 5 () 6 () 7
在石灰石原料煅烧过程 中, 由于 C O和 SO 具有 a i: 亲和力 强 的化学特性 ,并受石灰窑煅 烧工艺 的制约 ,
回转窑煅烧活性石灰的工艺

1 引 言
最 近几 十年 ,随着 冶金 行业 的迅 猛发 展 ,与之 配 套 的活性 石灰 生产 技 术 也 日新 月 异 ,我 国虽 在 此方 面有 巨大 的产 能 ,但生 产技 术普 遍落 后 ,能耗 大且 污 染严 重 。近年 来 ,一 些 钢铁 企 业 相 继 建 起 技 术 比较 先进 的 回转窑 ,用 焦 炉 煤气 、高 炉 煤气 、转 炉 煤气 等 附属 产物 作为 燃料 ,在 节 能 的 同时 也 解 决 了环保 的 问题 。本 文所 要论 述 的就是 煅烧 活性 石灰 回转 窑 的 工艺 。
2 活 性 石 灰 形成 机 理
石灰 是炼 钢生 产 中最 重要 的辅 助 原 料 ,其 质 量 直接 影 响炼钢 过程 、精炼 阶段 的成 渣速 度 、能量 消耗 及 渣 的反应 性 能 ,也 就是 脱磷 、脱 硫 的能力 。炼 钢过 程 中必 须使 用 活 性 度 高 、成 分 稳 定 、含 杂 质 少 的 石 灰 。石 灰 活性 度 是 炼 钢 用 石 灰 的 最 重 要 的性 能 指 标 。
Process of active lim e calcination with rotary kiln
Niu Jie (Xiqu Mine of Shanxi Coal and Electric Power Group Co.,Ltd.,Taiyuan 030200,China)
Abstract: This paper studies the process of active lime calcined with rotary kiln based on the pro- duction experience and experiment results,and analyses the effects of calcination tem perature,hold— ing time,combustion—supporting air volume and rotation speed of kiln proper etc. on the activity of lime. In addition,some viewpoints about the production process of superior quality active lime cal— cined with rotary kiln are proposed in this paper. K ey words: Rotary kiln;Active lime;Calcination
石灰回转窑生产工艺

石灰回转窑生产工艺
石灰回转窑是一种重要的石灰生产设备,广泛应用于建筑、冶金、化工等行业。
它采用了先进的生产工艺,能够高效地生产出优质的石灰产品。
石灰回转窑的生产工艺非常独特。
首先,将石灰石和燃料送入窑体,窑体内部设置有一系列的提升板,它们将石灰石和燃料均匀地分布在窑体内。
然后,点燃燃料,使其产生高温燃烧。
这样,窑体内部的温度就会迅速升高。
随着燃料的燃烧,窑体内部的温度逐渐升高。
当温度达到一定程度后,石灰石开始分解,产生二氧化碳和石灰。
二氧化碳从窑体顶部排出,而石灰则沿着窑体内壁滑下,最终从窑体底部排出。
在整个生产过程中,石灰石的分解和石灰的产生是同时进行的。
石灰石在窑体内部逐渐转动,使得它能够充分与燃料接触,从而实现高效的分解和产生石灰。
同时,窑体内部的提升板能够帮助石灰石和燃料充分混合,进一步提高产量和质量。
石灰回转窑生产工艺具有许多优点。
首先,它能够高效地生产出优质的石灰产品。
石灰的分解和产生是在高温环境下进行的,能够充分利用燃料的热能,提高石灰的产量和质量。
其次,石灰回转窑具有良好的适应性。
它可以适应不同种类的石灰石和燃料,能够灵活地调整生产工艺,以满足不同用户的需求。
此外,石灰回转窑还具
有节能环保的特点。
它采用了闭式生产,能够有效地控制废气的排放,减少对环境的污染。
石灰回转窑是一种高效、适应性强、节能环保的石灰生产设备。
它的生产工艺独特,能够高效地生产出优质的石灰产品。
随着科技的不断进步,石灰回转窑的生产工艺也在不断创新和完善,为各行各业提供更好的石灰产品。
石灰回转窑煅烧技术

石灰回转窑煅烧技术石灰回转窑煅烧技术是一种重要的石灰生产工艺,广泛应用于水泥、冶金、化工等行业。
本文将从原理、工艺流程、优势和应用领域等方面介绍石灰回转窑煅烧技术。
一、原理石灰回转窑煅烧技术是通过将石灰石或石灰石粉末放入回转窑中,利用高温和氧化条件下的化学反应,使石灰石中的钙和镁等金属氧化物转化为石灰石中的金属氧化物,从而实现石灰的煅烧和生产。
回转窑是一种圆筒形的设备,具有一定的倾斜角度,通过回转和倾斜运动使石灰石在窑内充分接触高温气流,从而达到高效煅烧的目的。
二、工艺流程石灰回转窑煅烧技术的工艺流程主要包括进料、预热、煅烧和冷却等几个阶段。
1. 进料阶段:将石灰石或石灰石粉末通过给料器均匀地投入回转窑中。
进料的均匀性对煅烧效果具有重要影响。
2. 预热阶段:在回转窑的前部,石灰石在与高温气流接触的过程中逐渐升温,水分和一部分二氧化碳开始释放。
3. 煅烧阶段:石灰石进入窑体的中部和后部,经过高温区域的煅烧。
在高温下,石灰石中的钙和镁等金属氧化物发生分解和氧化反应,生成石灰石中的金属氧化物。
4. 冷却阶段:煅烧后的石灰石经过窑体后部的冷却区域,与较低温度的气流接触,逐渐冷却,并最终排出窑外。
三、优势石灰回转窑煅烧技术相比于其他石灰煅烧技术具有以下优势:1. 高热效率:回转窑煅烧过程中,窑体内部高温气流能够充分与石灰石接触,从而实现石灰石的高效煅烧,提高热效率。
2. 适应性强:石灰回转窑煅烧技术适用于多种石灰石原料,包括石灰石矿石、石灰石粉末等,具有较强的适应性。
3. 产品质量稳定:由于回转窑煅烧过程中的高温和氧化条件,可以使石灰石中的杂质和有害物质得到有效去除,从而提高产品的质量稳定性。
4. 节能环保:回转窑煅烧技术采用闭路循环运行,可以有效回收和利用窑尾气中的热能和粉尘等,降低能耗和污染物排放。
四、应用领域石灰回转窑煅烧技术广泛应用于水泥、冶金、化工等行业。
在水泥生产中,石灰回转窑煅烧技术可用于生产高质量的石灰石熟料,作为水泥生产的重要原料。
论竖窑煅烧冶金石灰工艺

论竖窑煅烧冶金石灰工艺
是的,竖窑煅烧冶金石灰工艺是一种非常古老和有效率的是非技术。
泥坯用竖窑煅烧,可以快速地获得高品质的冶金石灰。
这种技术
通常被称为“砖窑烧”,像砖一样从挤压机挤出,然后烧制在窑炉内,形成冶金石灰。
砖窑烧的主要优点是可以一次完成一系列运行步骤,
从而减少原材料的损失,该技术也使用较少的能量和生产工艺,因此
能够实现较高的产量和质量。
此外,该技术还可以在更短的时间内完
成煅烧,因此减少了使用石灰的浪费。
回转窑生产转炉炼钢用高质量石灰的研究

回转窑生产转炉炼钢用高质量石灰的研究摘要:随着钢铁质量和产量的持续提升,炼钢过程中对于石灰质量的要求也在持续提升,在这种情况下,活性石灰被广泛应用于炼铁过程中。
基于此,本文对活性石灰特性及在炼钢中的作用进行了分析,阐述了活性石灰的煅烧机理,总结了国内外先进石灰窑型的生产特点及炼钢用石灰质量的提高途径,加深企业对“活性石灰”的认识,为冶金企业建设“活性石灰”生产线起到良好的借鉴和参考作用。
关键词:活性石灰;特性及作用;煅烧机理;石灰窑引言冶金石灰作为炼钢用的“造渣剂”,它的重要性已逐步得到人们的重视和认知。
它不仅影响着钢水的冶炼过程,还直接影响钢水的最终质量。
国际上已广泛采用品质好、反应快、造渣彻底的优质“活性石灰”取代过去使用的“普通石灰”为冶炼优质钢水奠定了基础。
活性石灰的应用,加快了冶炼造渣速度、缩短了冶炼时间、降低了吨钢石灰消耗、减少了杂质带入、大大提高了钢水的质量,给企业带来了显著的综合效益,在钢铁行业已形成共识。
20年代末至今,国内各大钢铁企业,纷纷建设一流活性石灰生产线,石灰窑配套的主体设施均采用引进或消化外来技术自行建造,石灰产品质量明显优于传统式窑生产的产品。
所以活性石灰的应用正成为大趋势在飞速普及发展。
1.活性石灰特性及在炼钢中的作用1.1活性石灰的特性活性石灰是一种化学性能活泼、反应能力强,在炼钢造渣过程中熔解速度快,含 S、P 等有害元素少的优质软烧石灰。
它的质量优劣主要采用“活性度”这一指标来衡量。
活性度体现了石灰在熔渣中与其它物质的反应能力,表观现象为石灰在熔渣中的熔化速度。
由于直接在钢水中测定较困难,所以一般以测试石灰在水中的反应速度来代替,即以石灰水活性来表示。
活性度的测试方法为:取50g 试样,与水混匀成饱和溶液再加入酚酞试剂后呈粉红色,再用浓度为4N( 摩尔) 的 HCl( 盐酸) 在40℃±1℃的环境温度下,连续10min( 分钟) 滴定,彻底中和后滴入HCl 的毫升数( 滴定值) 即为“活性度”值。
浅谈预热器/回转窑煅烧白云石制取煅白技术

灼减量的测量方法为称取一定质量的煅白 (nl,),在马弗炉中灼烧(灼烧温度应与白云
石煅烧温度相同)1—1.5h,然后称量灼烧好
白云石中的CaCO,与Ms'C03分解分两 个阶段进行,第一阶段是MgCO,的分解,分 一76一
的煅白(in:)。煅白的灼减量按下式计算:
灼减量%=(ml—m2)/ml×100%
项目
烧损率(%)
2 3 1
灼减量(%)
2 3 1
水化活性度(%)
2 3
从表4中可知,白云石在1150~1200℃ 温度下煅烧2—3h后(生产实践中指在高温 带停留的时间),所获得的煅白才能满足硅 热法炼镁的要求。 (3)煅烧时间的影响 白云石在煅烧时间与煅烧温度和白云石 的块度有关。在一定的块度与一定的温度下 煅烧白云石,如果高温下煅烧时间过长,氧化 物(CaO・Mgo)的晶粒长大,而且表面会老 化失去活性。因此生产上对于白云石的煅 烧,不管是采用回转窑、竖窑或隧道窑,都应 采用缓慢升温、高温快速煅烧的方法来煅烧。 (4)白云石的粒度 不同的煅烧设备,白云石的入窑粒度是 不同的,过大与过小粒度的白云石在一定温 度下(1150—1200℃)煅烧,烧制出来的白云 石不是过烧就是生烧。过烧的煅白其灼减量 低,水化活性度也极低;欠烧的煅白其灼减量
白云石的烧损率指白云石在煅烧过程可 以烧去的质量分数(如白云石中的水分、CO: 及有机物等)。白云石的烧损率可用下列公 式计算:
烧损率%=(Wl—W2)/W1×100%
式中:w1——白云石的质量,g;
1煅烧白云石制取煅白的质量
因素
1.1
W2——煅烧后煅白的质量,g。 白云石在1200℃温度下煅烧,其烧损率
灼减度
≤0.5
表2 等 煅34
原料性能对石灰回转窑煅烧及结圈影响的研究

些碎料的加入 ,增加了入窑石灰石的体积密度 ,降 低了透气性 ,形成生过烧石灰 ,也可以产生结瘤 、 挂窑皮等现象 。一般来说 ,石灰石的冷强度对结 圈问题影响不大 。
热强度是指石灰石在进入烧成带之前的热爆 裂或粉化性能 。很显然 ,如果热强度太差 ,那么在 窑内将形成大量的碎料和粉末 ,严重影响料层透 气性 ,也将导致结圈的发生 。为了考察田湖铁矿 石灰石原料的热强度 ,我们对其进行热爆裂与预 热后转动粉化性能的测试 ,结果见表 5 、表 6 。
另一方面 ,提高煅烧温度的范围是有限的 。 通过实验发现 ,当温度超高一定值后 ,CaO 及活性 度反而下降 ,特别是活性度 ,对煅烧温度非常敏 感 ,因为煅烧温度增加 ,将使石灰孔隙度降低 ,氧 化钙晶粒长大 ,活性度降低 ,因此煅烧温度一般不 应超过 1 200 ℃。
至于实际生产中小颗粒石灰石反而生烧的原 因 ,我们认为 ,一方面缘于料层透气性的影响 ,虽 然外部温度高 ,但由于细粒物料对透气性的影响 , 使得料柱的传热效果变差 ,因而造成生烧 ;另一方 面也可能缘于煅烧温度过高 ,石灰石表面生成的 氧化钙晶粒很快长大 ,迅速形成致密的覆盖层 ,从 而影响料层中心 CaCO3 的分解 ,而导致料块中心 生烧 ;第 3 个原因 ,石灰石中泥土多 , w ( SiO2 ) 增 多 ,SiO2 不参与分解反应 ,但与 CaO 发生化合反 应生成 CaSiO3 ,而使整个化学组成中的 w ( CaO) 降低 ,同时窑内料柱的透气性也降低 ,阻止石灰石 分解反应的顺利进行 ,这样也将使生烧率增加 。
对于冶金活性石灰的煅烧 ,实际上就是在一 定炉子保证其产量质量条件下 ,研究石灰石分解 的热力学条件和动力学条件问题 。当碳酸盐加热 到分解温度时 ,碳酸盐分解时气相产物二氧化碳 的体积较大 ,一般很难由致密的碳酸盐晶体石灰 石料块中心扩散出来 。石灰石的热分解首先在料 块表面进行 。随着时间的推移 ,料块的热分解由 表面向料块深处推进 ,这时石灰石的热分解在氧 化钙与 CaCO3 两相界面上进行 ,最终达到料块中
回转窑焙烧优质活性冶金石灰的质量研究

西安建筑科技大学硕士学位论文We not only analyse calcinations mechanism, decomposition of thermodynamicsand thermodynamics of calcite, but also conduct study on the influence of raw material particle size, temperature, time and other factors on the quality of lime under laboratory conditions. Results showed that the lime activity is the highest when the limestone of which particle size is in about 20 to 40 mm has been calcined at 1200 ° C for 60min, and the maximum can reach 398ml.Based on the above research, the industrial-scale tests of calcining technology for activating lime were performed in the rotary kiln. The effects of raw materials, fuel, rotary equipment and thermal system on activity of lime were examined in the production practice, and the problems that exist in the production were improved. After the improvement ,the rotary kiln conditions becomes more stability, quality of lime is in smaller fluctuations, and the content of CaO reached 93.10% and the mean activity is lime more than 385 ml, meaning products have achieved high level in the country.key words: rotary kiln; metallurgical lime; activity; roasted; researchI 目 录第一章 绪论 (1)1.1石灰概述 (1)1.2 冶金活性石灰在国内的发展现状 (1)1.3冶金活性石灰在国外的发展现状 (4)1.4 生产石灰的主要窑炉分析 (5)1.4.1并流蓄热式双膛竖窑 (6)1.4.2双D 窑 (8)1.4.3套筒式竖窑 (10)1.4.4梁式烧嘴竖窑 (11)1.4.5回转窑 (13)1.5课题的提出和主要研究内容 (16)1.5.1 课题提出的背景 (16)1.5.2 课题研究的目的和意义 (17)1.5.3 课题研究的主要内容 (17)第二章 新钢回转窑生产活性石灰的生产实践分析 (19)2.1 新钢回转窑焙烧石灰工艺流程 (19)2.1.1 原料系统 (20)2.1.2 焙烧系统 (21)2.1.3 燃烧系统 (22)2.1.4 窑尾除尘系统 (23)2.1.5 余热发电系统 (23)2.2回转窑设备常见故障及分析 (23)2.2.1 燃烧器 (24)2.2.2 预热器 (25)2.2.3 出料系统 (26)2.2.4 回转窑窑体 (26)2.3 本章小结 (30)第三章 影响活性石灰质量的实验研究 (32)II3.1石灰石焙烧机理 (32)3.1.1 石灰石分解的热力学分析 (32)3.1.2 石灰石分解的动力学分析 (33)3.2试验方法与研究内容 (34)3.2.1 实验设备 (35)3.2.2 试验材料与方法 (35)3.3实验结果及分析 (36)3.3.1 焙烧温度对石灰活性的影响 (36)3.3.2 焙烧时间对石灰活性的影响 (37)3.3.3 粒度对石灰活性的影响 (39)3.4本章小结 (40)第四章 石灰石焙烧工业试验 (41)4.1试验原料 (41)4.2试验结果及分析 (42)4.2.1 石灰石原料对石灰质量的影响 (43)4.2.2 燃料对石灰质量的影响 (43)4.2.3 转速及风量对石灰质量的影响 (44)4.3短时设备故障时工艺参数优化 (46)4.3.1停窑前焙烧参数调整操作 (46)4.3.2 留火保温操作 (47)4.3.3 检修后开窑操作 (47)4.4现行的工艺参数及技术指标 (48)4.5本章小结 (50)第五章 结论 (51)参考文献 (52)致谢 (55)攻读硕士学位期间发表的论文 (55)1第一章 绪论1.1石灰概述石灰是炼钢过程中的造渣材料,主要成分为CaO ,是脱硫、脱氧、脱磷提高钢液纯净度和减少热损失不可或缺的材料。
高温煅烧石灰石设备 智能化控制冶金回转窑焙烧工艺原理

高温煅烧石灰石设备智能化控制冶金回转窑焙烧工艺原理高温煅烧石灰石设备是一种用于生产石灰石的设备,通过高温煅烧工艺将石灰石转化为石灰,并且可以通过智能化控制系统来控制和监测整个煅烧过程。
智能化控制冶金回转窑焙烧工艺原理是基于冶金回转窑的热学原理以及控制系统的工作方式。
冶金回转窑是一种高效的热处理设备,常用于煅烧、焙烧和烧结等工艺过程中。
通过智能化控制系统,可以实现对冶金回转窑的温度、气体流量、转速等参数的自动控制和监测,从而实现工艺参数的优化调整,提高生产效率和产品质量。
在高温煅烧石灰石设备中,石灰石首先被送入回转窑的入口处,随着回转窑的旋转,石灰石慢慢向前移动。
在煅烧过程中,石灰石经历了一系列化学和物理变化。
其中最主要的变化是石灰石中的碳酸钙分解成氧化钙和二氧化碳。
煅烧过程中,需要加入一定量的燃料,例如煤粉或天然气,以提供充足的热量。
同时,还需要加入适量的空气,以保证石灰石中的碳酸钙能够充分分解。
智能化控制系统可以根据石灰石的性质和煅烧所需的温度、时间等参数,自动调整燃料和空气的供应量,以实现最佳的煅烧效果。
在整个煅烧过程中,智能化控制系统可以实时监测煅烧窑内的温度、燃料和空气供应量、石灰石的流动状况等参数,并将这些数据反馈给操作人员。
操作人员可以通过控制系统对煅烧过程进行实时调整,并进行必要的故障排除。
智能化控制冶金回转窑焙烧工艺原理的优势在于提高了生产效率和产品质量。
通过自动调整工艺参数,可以最大限度地提高石灰石的煅烧效果,减少能源的浪费,降低生产成本。
同时,智能化控制系统还可以实现对煅烧过程的准确监测,提高了生产过程的可控性和稳定性。
总之,高温煅烧石灰石设备的智能化控制冶金回转窑焙烧工艺原理是一种优化生产过程的方法。
通过自动调整工艺参数和实时监测,可以提高生产效率和产品质量,同时减少能源的消耗和生产成本。
这种智能化控制技术在石灰石及其他矿石的煅烧过程中有着广泛的应用前景。
炼钢用冶金活性石灰的生产及质量控制

炼钢用冶金活性石灰的生产及质量控制炼钢用冶金活性石灰是冶金行业的重要原料,用于钢铁生产中的炼钢过程。
它具有降温、还原、脱硫、固定非金属夹杂物等作用,在钢铁生产中起着至关重要的作用。
炼钢用冶金活性石灰的生产及质量控制显得尤为重要。
本文将探讨炼钢用冶金活性石灰的生产工艺及质量控制措施。
一、炼钢用冶金活性石灰的生产工艺1. 原料准备:炼钢用冶金活性石灰的主要原料是石灰石,石灰石是一种含钙的矿石,通常含有一定量的杂质。
在生产过程中,首先要对原料进行粉碎,以达到所需的颗粒度。
2. 预处理:经过粉碎后的原料还需要进行预处理,主要包括干燥和分级,以确保原料中的水分和杂质得到有效的去除。
3. 煅烧反应:预处理后的原料进入煅烧炉,进行高温煅烧反应。
在煅烧的过程中,原料中的氧化钙变成活性石灰,释放二氧化碳气体并形成石灰石。
这一步骤是炼钢用冶金活性石灰生产中最为关键的环节。
4. 粉磨:经过煅烧后的产品需要进行粉磨处理,以获得所需的颗粒度和表面积。
石灰和石灰石通常需要经过多级磨研系统,以确保产品的质量。
5. 包装:经过粉磨处理后的产品需要进行包装,以便于储运和使用。
在包装的过程中,需要对产品进行质量检验,确保产品符合相关标准。
以上就是炼钢用冶金活性石灰的生产工艺的基本步骤,而下面我们将重点介绍炼钢用冶金活性石灰的质量控制措施。
1. 原料的质量控制:原料的质量直接影响到最终产品的质量,因此在生产中需要对原料进行严格的质量控制。
包括对原料的化学成分、颗粒度、含水量等进行检测,并根据检测结果进行相应的调整。
2. 煅烧反应的控制:煅烧反应是影响产品质量的关键环节,需要对炉温、停留时间、气氛等进行严格控制,以确保煅烧的效果和产品的稳定性。
3. 产品的颗粒度和表面积控制:活性石灰的颗粒度和表面积对其活性起着至关重要的作用,需要通过粉磨系统对产品进行精细控制,以获得所需的颗粒度和表面积。
4. 包装及贮存控制:产品在包装和贮存过程中容易受到潮气和灰尘的污染,因此需要对包装材料和储存条件进行严格控制,确保产品不受污染。
[笔记]回转窑煅烧冶金石灰工艺研究与实践
![[笔记]回转窑煅烧冶金石灰工艺研究与实践](https://img.taocdn.com/s3/m/aa0fc5406bec0975f565e226.png)
[笔记]回转窑煅烧冶金石灰工艺研究与实践回转窑煅烧冶金石灰工艺研究与实践摘要: 由原料、燃料条件、设备及生产实际确定合理的预热温度、煅烧温度与煅烧时间得到有效CaO高、活性高的冶金石灰关键词:活性度;回转窑;煅烧温度;煅烧时间;预热温度前言:随着钢铁行业的不断发展对作为转炉炼钢造渣剂的冶金石灰要求也越来越高,要求冶金石灰在保证有效CaO的前提下还必须具有很高的活性。
提高冶金石灰的活性,可以减少炼钢时石灰的用量、提高钢水收得率、废钢比和炉衬寿命,做到快速造渣,少渣吹炼,减少吹炼喷溅,提高生产节奏等效果,这直接关系到企业的技术经济效益和节能降耗。
1. 生成冶金石灰的机理石灰组成中有游离氧化钙和结合氧化钙,游离氧化钙中又分活性氧化钙和非活性氧化钙。
非活性氧化钙在普通消解条件下,不能同水发生反应,但有可能转化为活性氧化钙(如磨细后)。
活性氧化钙则是在普通消解条件下,能同水发生反应的那部分游离氧化钙,结合氧化钙是不可回复的,故不能称为非活性氧化钙。
氧化钙在石灰中存在形式可以用图1.1表示。
石灰的反应能力实际上可以看成是游离氧化钙总量中活性氧化钙的数量。
石灰石的锻烧是石灰石菱形晶格重新结晶转化为石灰的立方晶格的变化过程。
其变化所得晶体结构与形成新相晶核的速度和它的生长速度有关。
当前者大于后者时,所得到的为细粒晶体,其活性氧化钙分子数量多,具有高的表面能;反之,所得为低表面能的粗粒晶体,其活性氧化钙分子数量少。
在石灰石快速加热锻烧下,所得到的为细粒晶体结构的石灰,活 [1]性度就高;缓慢加热锻烧时,所得为粗晶体结构的石灰,活性就低。
2.燃料和燃烧设备及原料要求2.1燃料和燃烧设备根据所用窑型和生产实际情况的不同,生产冶金石灰常用的燃料有焦炭、煤、重油和各种煤气。
本厂采用的是转炉煤气和高炉煤气混烧,转炉煤气和高炉煤气作为燃料的优点是烧出的石灰S含量比起其它燃料要低,窑内结圈现象较其它燃料要轻微;缺点是转炉煤气和高炉煤气的主要成分为CO其发热值较含碳氢化合物的燃料低,这在一定程度上制约了产量的进一步提高。
回转窑生产转炉炼钢用高质量石灰的研究

表示[1]。 提高有效 CaO 含量, 可达到满意的冶金效果 和降低石灰消耗。 CaO 有效% = CaO 石灰%-SiO2 石灰%×R 式中: R-炉渣碱度。 (1 )
选择 CaO 含量高、 SiO2 含量低的石灰石和合适 的煅烧工艺制度,可生产出有效 CaO 含量高的石 灰。 1.2 灼烧减量的影响 灼烧减量越低, 说明矿石煅烧过程中残留未分 解的 CaCO3 越少,可参与炉渣反应的 CaO 量越多, 可减少炼钢热量损失, 有利于钢渣物理化学反应进 可使 行。合适的煅烧工艺制度及入窑石灰石粒度, 石灰石分解更加充分, 降低灼烧减量。 1.3 硫含量的影响 石灰中硫多以 CaS 形式存在, 在炼钢时自身消 耗石灰, 在氧化性气氛炼钢中显著降低脱硫 、 脱磷 能力。选择 S 含量低的石灰石及燃料,可生产出 S 含量低的石灰。本钢回转窑燃料采用焦炉煤气, 热 3 -6 值在 16800~17640kJ/m , 含 S≤150×10 。 1.4 活性度的影响 活性度高的石灰, 气孔率高, 比表面积大, 炼钢 时参加反应充分, 成渣速度快。合适的煅烧工艺制 度及杂质含量低的石灰石可生产出较高活性度的 石灰 。 石灰杂质一般是指石灰石中的 SiO2、 Al2O3、 Fe2O3、 Na2O、 K2O 等成份, 这部分杂质随煅烧温度升 高而渣化, 石灰气孔被堵塞, 降低石灰气孔率及活 性度。
2 基本工艺流程及装备
2.1 工艺流程 本钢回转窑基本工艺流程示意图见图 1。
2.2 主要装备 本钢回转窑主要装备见表 1。
18
2010 年第 2 期
石, 才能满足生产活性石灰产量和质量的需求 。各 家小矿点质量不尽相同, 在选择矿点时要进行质量
认证来优化矿点, 满足石灰石技术条件的要求 。入 窑前进行合理配矿来稳定质量, 并合理利用有限的 资源。部分矿点质量见表 3。
石灰回转窑煅烧技术
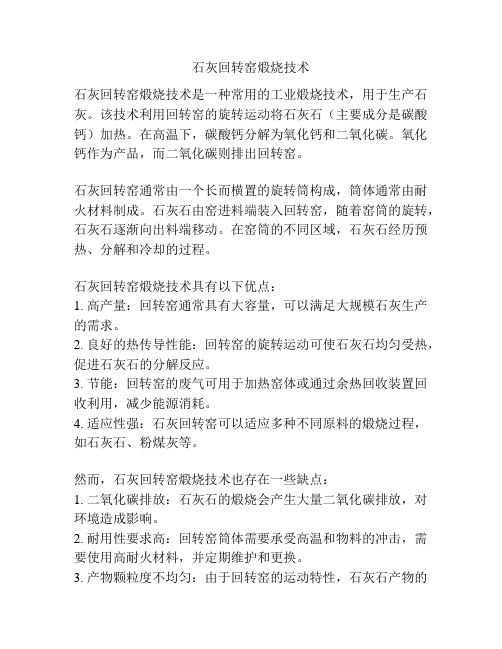
石灰回转窑煅烧技术
石灰回转窑煅烧技术是一种常用的工业煅烧技术,用于生产石灰。
该技术利用回转窑的旋转运动将石灰石(主要成分是碳酸钙)加热。
在高温下,碳酸钙分解为氧化钙和二氧化碳。
氧化钙作为产品,而二氧化碳则排出回转窑。
石灰回转窑通常由一个长而横置的旋转筒构成,筒体通常由耐火材料制成。
石灰石由窑进料端装入回转窑,随着窑筒的旋转,石灰石逐渐向出料端移动。
在窑筒的不同区域,石灰石经历预热、分解和冷却的过程。
石灰回转窑煅烧技术具有以下优点:
1. 高产量:回转窑通常具有大容量,可以满足大规模石灰生产的需求。
2. 良好的热传导性能:回转窑的旋转运动可使石灰石均匀受热,促进石灰石的分解反应。
3. 节能:回转窑的废气可用于加热窑体或通过余热回收装置回收利用,减少能源消耗。
4. 适应性强:石灰回转窑可以适应多种不同原料的煅烧过程,如石灰石、粉煤灰等。
然而,石灰回转窑煅烧技术也存在一些缺点:
1. 二氧化碳排放:石灰石的煅烧会产生大量二氧化碳排放,对环境造成影响。
2. 耐用性要求高:回转窑筒体需要承受高温和物料的冲击,需要使用高耐火材料,并定期维护和更换。
3. 产物颗粒度不均匀:由于回转窑的运动特性,石灰石产物的
颗粒度分布可能不均匀,需要进行后续的分级和篩分处理。
尽管存在一些缺点,石灰回转窑煅烧技术仍然是一种广泛应用的石灰生产技术,因为其具有高效、大容量和适应性强等特点。
随着环保要求的提高,为了减少二氧化碳排放,一些改进的石灰石煅烧技术也逐渐得到应用,如高温回转窑(HTTR)和高
氧煅烧(GOC)技术。
冶金回转窑煅烧工艺流程

冶金回转窑煅烧工艺流程
回转窑是冶金行业中常用的熔炼、烧结设备之一。
回转窑煅烧工艺流程主要包括以下步骤:
1. 原料准备
根据生产需要,按照一定比例称量和混合各种原料,如矿石、焦炭等。
要确保原料的成分和比例符合工艺要求,并达到供料的粒度分布。
2. 供料
将混合均匀的原料从回转窑供料端连续、稳定地供入。
需要控制好供料量,保证回转窑内原料的填充高度。
3. 加热
沿窑轴方向顺序布置多组燃烧器,可采用煤气或油为燃料,燃烧产生的高温烟气使回转窑内原料加热。
要精确控制每个燃烧区的温度,实现原料的分步加热。
4. 煅烧
在高温条件下,原料中矿石发生化学变化,释放出金属、挥发分等,同时发生烧结。
要控制好回转窑转速和温度,保证原料得到充分反应。
5. 排出
经过煅烧的产物在窑尾连续排出。
需要用水冷却固化,然后进行分类。
产物中含有目标金属,还可能含有烧结块、灰等。
6. 尾气处理
对回转窑尾气中含有的粉尘、有害气体等进行收集处理,确保达到排放标准。
在整个工艺中,要严格控制各个参数,实时检测生产情况,以保证冶金回转窑的平稳、高效运行。
冶金工艺认识实习报告

冶金工艺认识实习报告一、实习单位简介本次实习单位为我所在的学校实习基地,基地拥有较为完善的冶金工艺设备,包括炼铁、炼钢、轧钢等生产线。
通过实习,我对冶金工艺有了更深入的了解和认识。
二、实习过程、收获总结1. 炼铁工艺在炼铁工艺中,我了解了铁矿石的烧结、高炉炼铁等过程。
烧结是将铁矿粉与焦炭混合后,通过高温加热使其形成块状烧结矿。
高炉炼铁是将烧结矿、焦炭、石灰石等原料放入高炉中,通过高温还原反应,将铁从铁矿石中还原出来。
2. 炼钢工艺在炼钢工艺中,我了解了转炉炼钢、电弧炉炼钢等过程。
转炉炼钢是将铁水与氧气反应,生成氧化铁,然后通过加入合金元素,调整钢水成分。
电弧炉炼钢是利用电弧加热将铁水熔化,然后加入合金元素,调整钢水成分。
3. 轧钢工艺在轧钢工艺中,我了解了热轧、冷轧等过程。
热轧是将高温熔化的钢水通过轧机轧制成型,冷轧是在室温下将热轧钢材通过轧机轧制成型。
通过实习,我收获如下:(1)了解了冶金工艺的基本流程,包括炼铁、炼钢、轧钢等过程。
(2)掌握了各种冶金设备的操作方法,如炼铁炉、炼钢炉、轧机等。
(3)了解了冶金工艺中的环保措施,如废气处理、废水处理等。
(4)加深了对冶金工艺的理论认识,如炼铁原理、炼钢原理等。
三、实习体会通过本次实习,我对冶金工艺有了更深入的了解和认识。
实习过程中,我积极参与各项实践活动,掌握了冶金设备的操作方法,提高了自己的实践能力。
同时,我也认识到冶金工艺在环保方面的重要性,将在以后的学习和工作中注重环保意识的培养。
总之,本次实习使我受益匪浅,对我今后的学习和工作具有积极的推动作用。
在今后的学习和工作中,我将继续努力,不断提高自己的理论水平和实践能力,为我国冶金事业的发展贡献自己的力量。
石灰窑实习报告

石灰窑实习报告一、引言本实习报告旨在总结和分享我在石灰窑实习期间的经验和收获。
石灰窑是一种用于生产石灰的设备,广泛应用于建筑、冶金和环保等领域。
在实习期间,我有幸参与了石灰窑的操作与维护工作,亲身体验到了石灰生产的过程和技术。
本报告将围绕以下几个方面展开:1.石灰窑的工作原理和生产流程2.实习期间的实际工作内容3.所遇到的问题及解决方法4.对石灰窑的个人认识和体会5.实习期间的收获和感悟二、石灰窑的工作原理和生产流程石灰窑是利用石灰石在高温下分解产生石灰的设备。
其工作原理主要包括石灰石预热、分解、石灰烧成和冷却四个过程。
1.石灰石预热:在石灰窑的上部装有预热器,将石灰石加热至一定温度,以提高分解过程的效率。
2.石灰石分解:经过预热后的石灰石进入窑体,在高温下发生分解反应,产生二氧化碳和石灰。
3.石灰烧成:石灰窑中的石灰经过一定时间的烧成,达到所需的石灰质量和活性。
4.冷却:从石灰窑中取出的石灰需要进行冷却,以降低温度并避免进一步反应。
三、实习期间的实际工作内容在实习期间,我主要从事以下几项工作:1.准备工作:每天开始工作前,我需要检查石灰窑设备的运行状况,并及时清理窑壁和窑底的积灰。
2.石灰石供应:我需要负责将石灰石送至石灰窑预热器,并确保供给的稳定性和均匀性。
3.操作控制:在石灰烧成过程中,我需要控制石灰窑的温度、通风和进料速度,以确保生产的石灰质量满足要求。
4.故障处理:当石灰窑出现故障或异常情况时,我需要快速判断问题,并采取相应的措施进行处理,以确保生产的连续性和稳定性。
四、所遇到的问题及解决方法在实习期间,我遇到了一些常见的问题,如窑温控制不准确、石灰石供给不均匀等。
针对这些问题,我采取了以下解决方法:1.窑温控制不准确:通过调整燃料供给和通风情况,我成功提高了窑内的温度稳定性和控制精度。
2.石灰石供给不均匀:我对供给系统进行了调整和优化,以确保石灰石的均匀供给,提高了石灰窑的生产效率和石灰质量。
- 1、下载文档前请自行甄别文档内容的完整性,平台不提供额外的编辑、内容补充、找答案等附加服务。
- 2、"仅部分预览"的文档,不可在线预览部分如存在完整性等问题,可反馈申请退款(可完整预览的文档不适用该条件!)。
- 3、如文档侵犯您的权益,请联系客服反馈,我们会尽快为您处理(人工客服工作时间:9:00-18:30)。
回转窑煅烧冶金石灰工艺研究与实践摘要:由原料、燃料条件、设备及生产实际确定合理的预热温度、煅烧温度与煅烧时间得到有效CaO高、活性高的冶金石灰关键词:活性度;回转窑;煅烧温度;煅烧时间;预热温度前言:随着钢铁行业的不断发展对作为转炉炼钢造渣剂的冶金石灰要求也越来越高,要求冶金石灰在保证有效CaO的前提下还必须具有很高的活性。
提高冶金石灰的活性,可以减少炼钢时石灰的用量、提高钢水收得率、废钢比和炉衬寿命,做到快速造渣,少渣吹炼,减少吹炼喷溅,提高生产节奏等效果,这直接关系到企业的技术经济效益和节能降耗。
1. 生成冶金石灰的机理石灰组成中有游离氧化钙和结合氧化钙,游离氧化钙中又分活性氧化钙和非活性氧化钙。
非活性氧化钙在普通消解条件下,不能同水发生反应,但有可能转化为活性氧化钙(如磨细后)。
活性氧化钙则是在普通消解条件下,能同水发生反应的那部分游离氧化钙,结合氧化钙是不可回复的,故不能称为非活性氧化钙。
氧化钙在石灰中存在形式可以用图1.1表示。
石灰的反应能力实际上可以看成是游离氧化钙总量中活性氧化钙的数量。
石灰石的锻烧是石灰石菱形晶格重新结晶转化为石灰的立方晶格的变化过程。
其变化所得晶体结构与形成新相晶核的速度和它的生长速度有关。
当前者大于后者时,所得到的为细粒晶体,其活性氧化钙分子数量多,具有高的表面能;反之,所得为低表面能的粗粒晶体,其活性氧化钙分子数量少。
在石灰石快速加热锻烧下,所得到的为细粒晶体结构的石灰,活性度就高;缓慢加热锻烧时,所得为粗晶体结构的石灰,活性就低[1]。
2.燃料和燃烧设备及原料要求2.1燃料和燃烧设备根据所用窑型和生产实际情况的不同,生产冶金石灰常用的燃料有焦炭、煤、重油和各种煤气。
本厂采用的是转炉煤气和高炉煤气混烧,转炉煤气和高炉煤气作为燃料的优点是烧出的石灰S含量比起其它燃料要低,窑内结圈现象较其它燃料要轻微;缺点是转炉煤气和高炉煤气的主要成分为CO其发热值较含碳氢化合物的燃料低,这在一定程度上制约了产量的进一步提高。
燃烧设备在实际生产中起到非常关键的作用。
本厂采用的燃烧设备(及烧嘴)是一种煤气与空气预先不进行混合,二者在燃烧空间内边混合边燃烧的的设备,此时燃烧速度受到混合速度的限制,燃烧缓慢且有明显的火焰,此时燃烧产物与周围物体之间所进行的热交换属于火焰辐射它比起单纯的气体辐射具有更强的辐射力[4]。
对于本厂使用的煤气燃烧过程其本上可以归纳为:煤气与空气的混合;将混合物加热到着火温度;煤气中的可燃组分与空气中的氧发生激烈的化学反应进行燃烧。
在上述过程中,煤气中的可燃组分与空气中的氧在高温下进行燃烧反应是非常快的,可以认为是在一瞬间完成的。
将煤气预热到着火温度在煤气预热室进行,唯有煤气和空气的混合过程是一种物理扩散过程,需要一定的时间,因此它是决定燃烧速度的主要因素。
对比我厂的1#窑和2#窑的烧嘴可以看出1#的燃烧速度比2#更快、更充分,在煤气条件基本一致的情况下考虑可能是烧嘴、管路差异、风煤的配比、压力等方面造成的。
2.2原料要求工业用石灰对石灰石的质量要求主要有两个方面:一个是要求含碳酸钙成分要高,一般要求要在97%以上,二是它的结构晶粒要小,因为晶粒小的石灰石晶间不严实,且在含有机物的情况下,有机物燃烧形成的多孔状,CO 2容易分离,故便于煅烧,三是杂质少,特别是有害成分如二氧化硅,氧化镁,氧化铝,硫和磷等。
2.2.1粒度要求在冶金石灰生产中,原料石灰石的粒度应控制在一定范围。
如果粒度差别大,小粒石灰石在短时间内就可完全分解,而大粒度的则需要较长时间。
若大粒度的石灰石已完全分解,而小粒的因在煅烧区停留时间过长造成过烧而失去活性,反之大粒度的会形成夹心生烧而使活性度偏低。
因此要求石灰石粒度尽可能均匀, 一般要求大小粒度之比不超过二分之一[2]。
表1为我厂与其它厂的对比:石灰 CaO (活性) CaO (非活性) CaCO 3,CaSO 4,2CaO ·SiO 2 CaO ·Al 2O 3,3CaO ·Al 2O 32CaO ·Fe 2O 3,CaO ·Fe 2O 3细磨 图1.1 石灰中氧化钙的存在形式表1 为几个冶金厂石灰生产的统计2.2.2成分条件石灰石的主要成分是CaCO3,还含有一定量的MgCO3、SiO2、Al2O3、Fe2O3 等杂质。
CaCO3的含量表示石灰石的纯度,它直接影响着石灰中CaO的含量,是决定石灰活性度的主要指标,因此CaCO3的含量越高越好,生产中认为大于96%的石灰石较好。
石灰石中的杂质是有害成分,煅烧过程中分别与CaO反应:SiO2 + 3CaO = 3CaO·SiO2Al2O3 + 3CaO = 3CaO·Al2O 32CaO + Fe2O 3 = 2CaO·Fe2O 3Al2O 3 + Fe2O 3 + 4CaO =4CaO·Al2O3·Fe2O 3生成的盐类大部分熔点低,在煅烧带常以液相存在,促进了CaO颗粒间的融合,使石灰结构紧缩,气孔率下降,活性度较低。
冶金石灰生产要求原料中杂质含量尽可能少,根据原料所含成分不同,国家统一把石灰石划分为不同的等级,见表2。
表2 冶金石灰石工业标准(%)3.工艺技术要求3.1预热温度与操作负压本厂的预热器属于竖式预热器。
利用转窑中废气温度来预热石灰石优点是可以节约能源、降低成本;缺点是废气中有大量的粉尘可能夹杂到石灰石中影响预热效果,废气温度与锻烧制度关系密切很难既达到理想的预热温度又达到理想的煅烧温度,两者间存在矛盾。
回转窑的负压操作有利于石灰石的快速分解同时对预热温度也有直接的影响,负压的大小应该以窑中石灰石的量为主要标准而不要把其用作调整预热温度的主要手段。
3.2冶金石灰(活性石灰)煅烧特点活性石灰,除要求原料(石灰石)化学成分和块度合适外,还要有一定的煅烧制度,其煅烧特点:(1) 锻烧时,石灰石表面温度不能超过1150℃,温度过高,表面形成致密过烧层,使活性度降低。
(2) 供热强度要合理,石灰石分解初期允许较大的供热强度,可达10000~25000Kcal/m2。
待基本分解完时,应逐渐降到<5000 Kcal/m2以保证石灰石晶粒细、活性高。
(3) 一旦分解结束,要立即降温冷却,以防石灰持续结晶致使晶粒过大,活性降低[3]。
3.3煅烧温度煅烧温度不仅决定了石灰石的分解反应速度,而且也影响石灰晶体粒度大小。
如果温度偏低,分解慢,在有效煅烧时间内石灰石不能完全分解,造成生烧,活性度偏低;温度较高时,石灰石分解速度快,但随着温度的升高,CaO晶粒长大,体积密度增大,比表面积和气孔率减小,使石灰反应能力下降,活性度降低。
因此,生产要求煅烧温度要控制在合适的范围。
不同的石灰石在理论上都存在一个理想的煅烧温度,而在950~1150℃时,大部分石灰石都能烧成较高活性度的℃CaO含量高的时候石灰活性度反而低。
在双色温度高、CaO含量高时CaO晶粒长大,体积密度增大,比表面积和气孔率减小使活性降低;双色温度低时CaO含量降低使得石灰活性度降低。
3.4煅烧时间生产中原料粒度和成分稳定后,煅烧温度一定,煅烧时间也就基本确定,不可偏差过大,否则,若煅烧时间过短,较大粒度的石灰石分解不完,反之,因煅烧时间过长,已完全分解的石灰在高温下晶体长大,使体积密度增大,两者都会引起石灰活性度降低。
有关资料指出:同类石灰石在1093℃下煅烧2h所形成的气孔表面积若在927℃下则需要煅烧8h[3]。
可见,煅烧时间与煅烧温度相关。
3.5煅烧温度与煅烧时间的关系从理论上说,煅烧优质石灰,应先根据石灰石质量,确定最佳煅烧温度,而煅烧时间在煅烧温度确定时也就一定了。
实际生产中,根据需要,产量经常波动,为了保证石灰质量的稳定,应由产量确定煅烧时间,再由煅烧时间确定煅烧温度,所以实际煅烧温度不仅与理论最佳煅烧温度有一定偏差,而且也应随原料粒度,产量等的波动而变化,但原料粒度、产量等的波动应控制在一定的范围内,否则,将影响正常操作,引起质量波动。
用本厂使用的石灰石在实验室条件下做石灰石热稳定性实验,实验步骤:石灰石水洗→烘干1小时→称量→马弗炉加热→称量→水化→烘干1小时→称量由实验得出的数据我们可以得出石灰石在加热30分钟的情况下只需1100℃—1150℃即可生产出合格石灰。
考虑到实际生产和实验室条件的差异根据本厂生产实际经验在1170℃,保温40分钟,8小时产量170t的条件下即可生产出CaO 含量在84%以上,活性度在350以上的石灰。
4.结论(1)加强对石灰石质量的监督,降低入窑低熔点杂质量从而控制结圈和预热室被堵现象,从而减少非计划停机。
(2)石灰石在实验条件下800℃左右开始分解,预热器连续出料且受热不均预热温度应该适当提高,预热时间变短(推速加快)也应该适当提高预热温度。
(3)石灰的CaO含量和活性度之间存在一定的矛盾,在双色温度高、CaO含量高时CaO晶粒长大,体积密度增大,比表面积和气孔率减小使活性降低;双色温度低时CaO含量降低使得石灰活性度降低。
(4)煅烧活性石灰工艺制度为:在煅烧温度为1170℃,保温40分钟,8小时产量170t,然后迅速冷却,即可得到高活高CaO石灰。
参考文献[1]唐亚新,影响石灰活性的因素分析[J].炼钢,2001,17(3):50.[2] 刘世洲, 詹庆林, 张树勋等.冶金石灰[M].沈阳:东北工学院出版社,1992.[3] 贾玉红,生产优质冶金石灰的条件[J].钢铁,2000,35(11):34-35.[4] 姜金宁,硅酸盐工业热工过程及设备.冶金工业出版社。