最新橡胶工艺原理(二十四)
橡胶 工艺 原理

橡胶工艺原理
橡胶是一种由橡胶树的乳液经过加工制成的具有弹性的材料。
橡胶的工艺原理主要包括以下几个方面。
1. 采集橡胶乳液:橡胶树的树干被割开后,乳液会自然流出。
采集工人使用刮刀将乳液慢慢刮下,收集到容器中。
2. 乳液稳定化:采集到的橡胶乳液中含有大量的水分和其他杂质,需要经过稳定化处理。
常用的稳定化剂包括氨水和醋酸,它们可以使乳液保持稳定状态,并防止乳液中的橡胶团聚。
3. 合成橡胶:乳液经过稳定化处理后,需要加入硫化剂、填充剂和加工助剂等多种化学物质进行合成橡胶的加工。
其中,硫化剂可以使橡胶分子之间的交联结构更加牢固,增加橡胶材料的强度和耐磨性;填充剂可以提高橡胶材料的硬度和耐磨性;加工助剂则可以调整橡胶材料的流动性和加工性能。
4. 橡胶成型:合成橡胶经过调配后,可以通过各种成型方法将其制成不同形状的橡胶制品。
常见的成型方法包括压延、压缩模压、浇注和挤出等。
5. 硫化和固化:成型后的橡胶制品需要进行硫化或固化处理,使其获得所需的弹性和耐磨性。
硫化是将成型的橡胶制品置于加热的硫化炉中,在一定温度下与硫化剂反应,形成较为稳定的交联结构;固化则是使用特定的固化剂或光线照射,使成型的橡胶制品的分子链交联,增加其硬度和强度。
通过以上的工艺原理,橡胶可以被制备成各种应用于工业、交通、建筑和日常生活中的橡胶制品,如轮胎、密封件、橡胶管、橡胶鞋等。
橡胶加工工艺
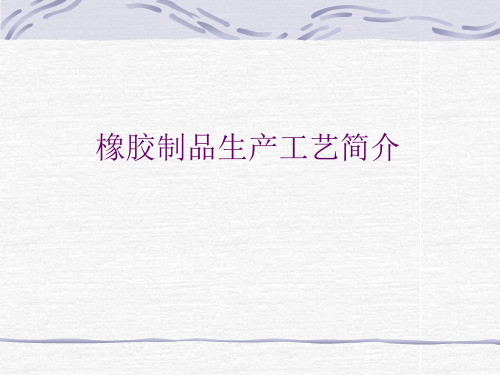
➢ 化学塑解剂:塑解剂的用量,在NR中一般为生胶重量的0.1~0.3%,合 成橡胶则应增大到2~3%。
橡胶制品生产工艺简介-塑炼工艺塑炼工艺
不同胶料开炼机混炼时辊筒温度
胶种
天然胶 丁苯胶 氯丁胶 丁基胶 丁腈胶 顺丁胶 三元乙丙胶 氯磺化聚乙烯 氟橡胶23—27 丙烯酸酯橡胶
橡胶制品生产工艺简介-塑炼工艺塑炼工艺
常用橡胶的塑炼特性
2. SBR ➢ 软SBR的初始门尼粘度一般在54~64之间,不需进行塑炼。 ➢ SBR采用机械塑炼效果不大,比较有效的方法时采用高温
塑炼法,以130~140℃温度最好,温度过高易生成凝胶。 3.BR ➢ BR一般不需要进行塑炼。 4.CR ➢ CR的初始门尼粘度都较低,一般不需要进行塑炼。但在储
➢ 物料在密炼室中主要受到几种作用: 转子间及转子与混炼室内壁间的作用;
转子棱间的搅拌作用;
转子轴向的往复切割作用。
➢ 优点:自动化程度高,生产效率高,节能,劳动强度低
➢ 缺点:温度高,冷却困难,易过炼,出料为无定形状
橡胶制品生产工艺简介-塑炼工艺塑炼工艺
密炼机
橡胶制品生产工艺简介-塑炼工艺塑炼工艺
存过程中其可塑性会下降,因此CR仍需经过塑炼加工,才 能获得所要求的可塑性。 ➢ CR宜采用开炼机进行塑炼,低温薄通塑炼效果最好。
橡胶制品生产工艺简介-塑炼工艺塑炼工艺
常用橡胶的塑炼特性
5.IIR ➢ 门尼粘度在38~75之间的品种一般不需要塑炼。 ➢ IIR采用机械塑炼效果不大,但用密炼机在120℃以上,并
且加入塑解剂进行高温塑炼则可取得较好的塑炼效果。 6.NBR ➢ NBR的塑炼应采用开炼机在低温(40℃以下)、小辊距
橡胶的压延工艺
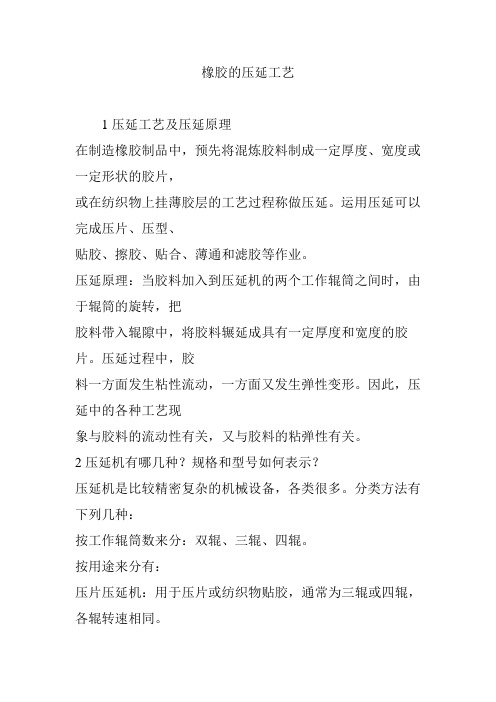
橡胶的压延工艺1压延工艺及压延原理在制造橡胶制品中,预先将混炼胶料制成一定厚度、宽度或一定形状的胶片,或在纺织物上挂薄胶层的工艺过程称做压延。
运用压延可以完成压片、压型、贴胶、擦胶、贴合、薄通和滤胶等作业。
压延原理:当胶料加入到压延机的两个工作辊筒之间时,由于辊筒的旋转,把胶料带入辊隙中,将胶料辗延成具有一定厚度和宽度的胶片。
压延过程中,胶料一方面发生粘性流动,一方面又发生弹性变形。
因此,压延中的各种工艺现象与胶料的流动性有关,又与胶料的粘弹性有关。
2压延机有哪几种?规格和型号如何表示?压延机是比较精密复杂的机械设备,各类很多。
分类方法有下列几种:按工作辊筒数来分:双辊、三辊、四辊。
按用途来分有:压片压延机:用于压片或纺织物贴胶,通常为三辊或四辊,各辊转速相同。
擦胶压延机:用于纺织物擦胶,通常为三辊,各辊之间有一定速比。
通用(万能)压延机:这种压延机兼有上述两种压延机的功能,通常为三辊或四辊,各辊的速比可借辅助齿轮调节。
压型压延机:用于制造表面带有花纹或有一定形状的胶片,其中有一个辊筒刻有花纹。
钢丝压延机:用于钢丝帘布的贴胶,由四个辊筒组成。
按辊筒的排列形式有:I型、△型、T型、L型、Z型、S型等。
压延机规格可用辊筒外直径×辊筒工作部分长度来表示,如压延机规格Φ610×1730。
我国压延机型号可表示为XY —4T—1730。
其中XY 表示橡胶胶压延机,4T表示四辊筒型排列。
1730表示辊筒工作部分的长度(mm)。
3在设计压延机时为什么需采用补偿措施在压延机加工过程中,当胶料通过辊距时,给予辊筒的横压力很高,加上辊筒自身的重量,致使辊筒会产生一定的弹性弯曲(其弯曲度称为挠度)结果使压延胶片出现中间厚两边薄的现象。
为了克服为种弊病,通常在设计压延机时,都采取一些补偿措施,以确保压延的精密度,常用的补偿方法有;凹凸系数法(中高法);轴交叉法和反弯曲法(予负荷法)等。
4什么叫压延效应,它对制品的性能有何影响?压延后的制品在纵横方向性能差异的现象叫做压延效应,即沿胶片纵方向(压延方向)的扯断强度大,伸长率小,收缩率大;而沿胶片横向的扯断强度小,伸长率大,收缩率小。
橡胶加工工艺—橡胶压出工艺(高分子成型课件)
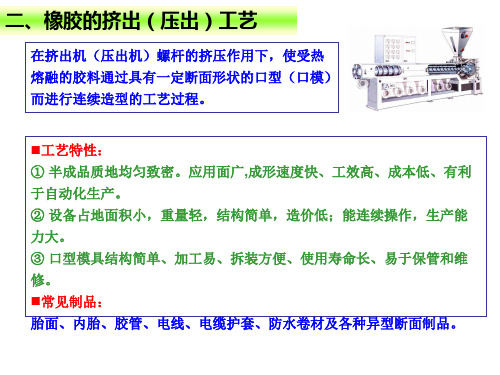
二、橡胶的挤出(压出)工艺
(一)压出机工作原理及胶料的运动状态 3 物料在口型中的流动状体和挤出变形 胶料经机头进入口型后,由于口型形状不同及内表 面对物料流动的阻碍,物料流动速度也存在有与机 头类似的速度分布。中间流速大,越接近口型壁流 速越小 。 一般粘弹性的物料,从口型挤出后就不可避免地存 在松弛现象,即:胶条的长度会沿挤出方向缩短, 厚度沿垂直挤出方向增加(离模膨胀现象或称作挤 出变形现象)。挤出后的变形(收缩和膨胀)可以控制 在一定范围,但不可能完全消除。要求收缩率为 2~5%。 物料可塑性小、含胶率大,填充剂用量小,物料挤 出快,机头和口型温度低,膨胀和收缩率就大。
二、橡胶的挤出(压出)工艺
在挤出机(压出机)螺杆的挤压作用下,使受热 熔融的胶料通过具有一定断面形状的口型(口模) 而进行连续造型的工艺过程。
工艺特性: ① 半成品质地均匀致密。应用面广,成形速度快、工效高、成本低、有利 于自动化生产。 ② 设备占地面积小,重量轻,结构简单,造价低;能连续操作,生产能 力大。 ③ 口型模具结构简单、加工易、拆装方便、使用寿命长、易于保管和维 修。 常见制品: 胎面、内胎、胶管、电线、电缆护套、防水卷材及各种异型断面制品。
二、橡胶的挤出(压出)工艺
(一)压出机工作原理及胶料的运动状态
1 胶料在挤出机中的运动状态
加料段:加入的条状胶料,受到旋转螺杆的推挤作用形成连续的胶 团,并沿着螺槽的空间一边旋转,一边不断前进。 压缩段:加料段输送过来的松散胶团在压缩段被逐渐压实、软化, 并把夹带的空气向加料段排出。同时胶团间间隙缩小,密度增高, 进而粘在一起,再加上受到剪切和搅拌作用,因而胶团逐渐被加热 塑化形成连续的粘流体。 挤出段:在挤出段,压缩段输送过来的物料进一步塑化均匀,并输 送到机头和口模处挤出成型。
HCR工艺原理及特点
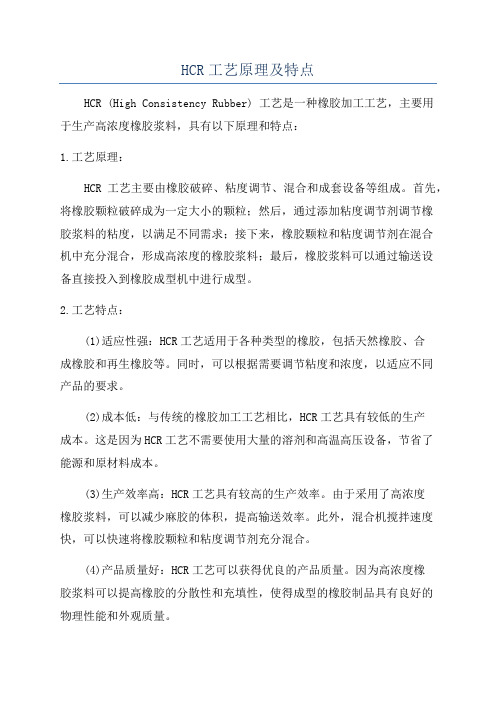
HCR工艺原理及特点HCR (High Consistency Rubber) 工艺是一种橡胶加工工艺,主要用于生产高浓度橡胶浆料,具有以下原理和特点:1.工艺原理:HCR工艺主要由橡胶破碎、粘度调节、混合和成套设备等组成。
首先,将橡胶颗粒破碎成为一定大小的颗粒;然后,通过添加粘度调节剂调节橡胶浆料的粘度,以满足不同需求;接下来,橡胶颗粒和粘度调节剂在混合机中充分混合,形成高浓度的橡胶浆料;最后,橡胶浆料可以通过输送设备直接投入到橡胶成型机中进行成型。
2.工艺特点:(1)适应性强:HCR工艺适用于各种类型的橡胶,包括天然橡胶、合成橡胶和再生橡胶等。
同时,可以根据需要调节粘度和浓度,以适应不同产品的要求。
(2)成本低:与传统的橡胶加工工艺相比,HCR工艺具有较低的生产成本。
这是因为HCR工艺不需要使用大量的溶剂和高温高压设备,节省了能源和原材料成本。
(3)生产效率高:HCR工艺具有较高的生产效率。
由于采用了高浓度橡胶浆料,可以减少麻胶的体积,提高输送效率。
此外,混合机搅拌速度快,可以快速将橡胶颗粒和粘度调节剂充分混合。
(4)产品质量好:HCR工艺可以获得优良的产品质量。
因为高浓度橡胶浆料可以提高橡胶的分散性和充填性,使得成型的橡胶制品具有良好的物理性能和外观质量。
(5)环保性好:HCR工艺对环境的影响较小。
与传统的橡胶加工工艺相比,HCR工艺不需要使用大量的溶剂和污水处理设备,减少了废物的排放和处理成本。
(6)工艺控制精度高:HCR工艺可以精确控制橡胶浆料的粘度、浓度和颗粒大小。
通过调节粘度调节剂的添加量和搅拌时间等参数,可以满足不同产品的要求。
总结起来,HCR工艺是一种适应性强、成本低、生产效率高、产品质量好、环保性好且工艺控制精度高的橡胶加工工艺。
该工艺在橡胶制品行业具有广泛应用前景。
橡胶工艺原理
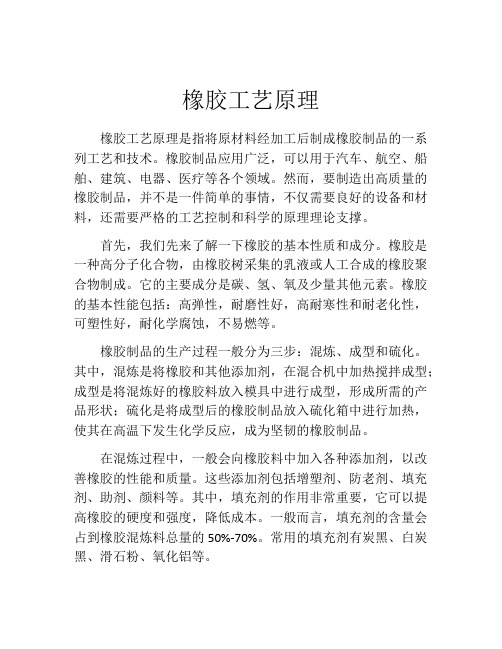
橡胶工艺原理橡胶工艺原理是指将原材料经加工后制成橡胶制品的一系列工艺和技术。
橡胶制品应用广泛,可以用于汽车、航空、船舶、建筑、电器、医疗等各个领域。
然而,要制造出高质量的橡胶制品,并不是一件简单的事情,不仅需要良好的设备和材料,还需要严格的工艺控制和科学的原理理论支撑。
首先,我们先来了解一下橡胶的基本性质和成分。
橡胶是一种高分子化合物,由橡胶树采集的乳液或人工合成的橡胶聚合物制成。
它的主要成分是碳、氢、氧及少量其他元素。
橡胶的基本性能包括:高弹性,耐磨性好,高耐寒性和耐老化性,可塑性好,耐化学腐蚀,不易燃等。
橡胶制品的生产过程一般分为三步:混炼、成型和硫化。
其中,混炼是将橡胶和其他添加剂,在混合机中加热搅拌成型;成型是将混炼好的橡胶料放入模具中进行成型,形成所需的产品形状;硫化是将成型后的橡胶制品放入硫化箱中进行加热,使其在高温下发生化学反应,成为坚韧的橡胶制品。
在混炼过程中,一般会向橡胶料中加入各种添加剂,以改善橡胶的性能和质量。
这些添加剂包括增塑剂、防老剂、填充剂、助剂、颜料等。
其中,填充剂的作用非常重要,它可以提高橡胶的硬度和强度,降低成本。
一般而言,填充剂的含量会占到橡胶混炼料总量的50%-70%。
常用的填充剂有炭黑、白炭黑、滑石粉、氧化铝等。
成型过程则包括挤出、压缩成型、注塑、挤压等多种方式。
其中,挤出是指将热压橡胶料挤出成型,常用于制造板材、管材和带材等;压缩成型是将混炼好的橡胶料放到压力机模具中压缩成型,常用于制造密封件、垫片和橡胶板等;注塑是将热熔态的橡胶料注入模具中成型,常用于制造零件、机械件等;挤压是将橡胶料通过挤压机制成所需的形状,常用于制造密封圈、管子等产品。
硫化则是通过加热使橡胶聚合物中的硫和碳原子相互交联,从而增加橡胶制品的硬度和强度,提高耐磨性和耐寒性。
硫化温度和时间是影响橡胶制品性能的关键因素,硫化温度过高或时间过长会导致橡胶制品变质、失去弹性等问题。
总的来说,橡胶工艺原理的核心问题在于如何在制造过程中控制好各种参数,确保所制造的橡胶制品具有优异的性能和质量。
橡胶模压成型工艺原理
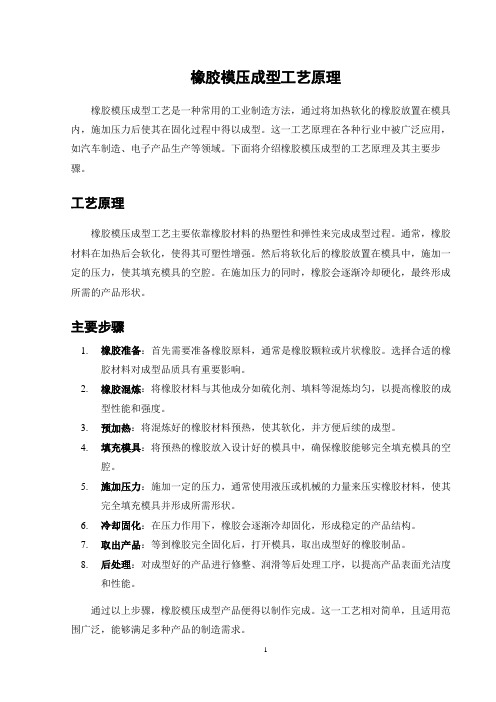
橡胶模压成型工艺原理橡胶模压成型工艺是一种常用的工业制造方法,通过将加热软化的橡胶放置在模具内,施加压力后使其在固化过程中得以成型。
这一工艺原理在各种行业中被广泛应用,如汽车制造、电子产品生产等领域。
下面将介绍橡胶模压成型的工艺原理及其主要步骤。
工艺原理橡胶模压成型工艺主要依靠橡胶材料的热塑性和弹性来完成成型过程。
通常,橡胶材料在加热后会软化,使得其可塑性增强。
然后将软化后的橡胶放置在模具中,施加一定的压力,使其填充模具的空腔。
在施加压力的同时,橡胶会逐渐冷却硬化,最终形成所需的产品形状。
主要步骤1.橡胶准备:首先需要准备橡胶原料,通常是橡胶颗粒或片状橡胶。
选择合适的橡胶材料对成型品质具有重要影响。
2.橡胶混炼:将橡胶材料与其他成分如硫化剂、填料等混炼均匀,以提高橡胶的成型性能和强度。
3.预加热:将混炼好的橡胶材料预热,使其软化,并方便后续的成型。
4.填充模具:将预热的橡胶放入设计好的模具中,确保橡胶能够完全填充模具的空腔。
5.施加压力:施加一定的压力,通常使用液压或机械的力量来压实橡胶材料,使其完全填充模具并形成所需形状。
6.冷却固化:在压力作用下,橡胶会逐渐冷却固化,形成稳定的产品结构。
7.取出产品:等到橡胶完全固化后,打开模具,取出成型好的橡胶制品。
8.后处理:对成型好的产品进行修整、润滑等后处理工序,以提高产品表面光洁度和性能。
通过以上步骤,橡胶模压成型产品便得以制作完成。
这一工艺相对简单,且适用范围广泛,能够满足多种产品的制造需求。
总的来说,橡胶模压成型工艺依靠橡胶材料的特性和适当施加的压力,实现了橡胶制品的高效成型。
它在现代工业生产中扮演着重要角色,为各行业提供了高品质、高性能的橡胶制品,推动了工业的发展与进步。
橡胶工艺原理
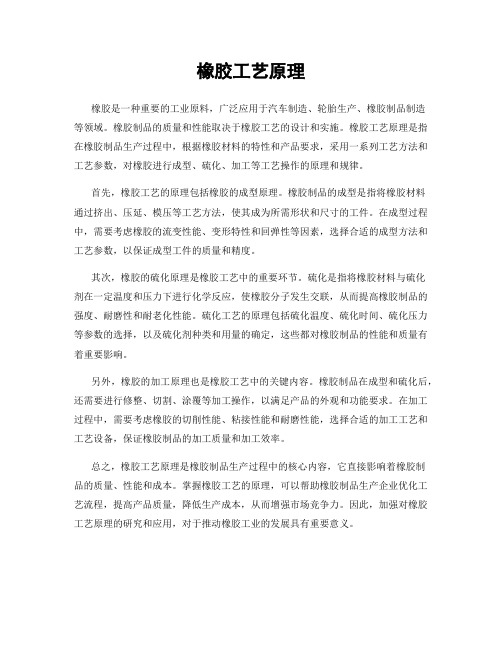
橡胶工艺原理
橡胶是一种重要的工业原料,广泛应用于汽车制造、轮胎生产、橡胶制品制造
等领域。
橡胶制品的质量和性能取决于橡胶工艺的设计和实施。
橡胶工艺原理是指在橡胶制品生产过程中,根据橡胶材料的特性和产品要求,采用一系列工艺方法和工艺参数,对橡胶进行成型、硫化、加工等工艺操作的原理和规律。
首先,橡胶工艺的原理包括橡胶的成型原理。
橡胶制品的成型是指将橡胶材料
通过挤出、压延、模压等工艺方法,使其成为所需形状和尺寸的工件。
在成型过程中,需要考虑橡胶的流变性能、变形特性和回弹性等因素,选择合适的成型方法和工艺参数,以保证成型工件的质量和精度。
其次,橡胶的硫化原理是橡胶工艺中的重要环节。
硫化是指将橡胶材料与硫化
剂在一定温度和压力下进行化学反应,使橡胶分子发生交联,从而提高橡胶制品的强度、耐磨性和耐老化性能。
硫化工艺的原理包括硫化温度、硫化时间、硫化压力等参数的选择,以及硫化剂种类和用量的确定,这些都对橡胶制品的性能和质量有着重要影响。
另外,橡胶的加工原理也是橡胶工艺中的关键内容。
橡胶制品在成型和硫化后,还需要进行修整、切割、涂覆等加工操作,以满足产品的外观和功能要求。
在加工过程中,需要考虑橡胶的切削性能、粘接性能和耐磨性能,选择合适的加工工艺和工艺设备,保证橡胶制品的加工质量和加工效率。
总之,橡胶工艺原理是橡胶制品生产过程中的核心内容,它直接影响着橡胶制
品的质量、性能和成本。
掌握橡胶工艺的原理,可以帮助橡胶制品生产企业优化工艺流程,提高产品质量,降低生产成本,从而增强市场竞争力。
因此,加强对橡胶工艺原理的研究和应用,对于推动橡胶工业的发展具有重要意义。
橡胶制品的成型工艺介绍

橡胶制品的成型工艺介绍橡胶制品种类繁多,但其生产工艺过程,却基本相同。
以一般固体橡胶(生胶)为原料的制品,它的生产工艺过程主要包括:原材料准备塑炼混炼成型硫化修整检验(1)生胶的塑炼使弹性生胶转变为可埋状态的加工过程称为塑炼。
塑炼的目的是降低生胶的弹性、增加其可塑性,并且获得适当的流动性,以满足混炼,压延或压出成型、硫化以及胶浆制造、海绵胶制造等各种加工过程的要求。
塑炼有机械塑炼法和化学塑炼法。
前者通过塑炼机的机械破坏作用,降低生胶的弹性,获得一定的可塑性。
后者通过化学药品的化学作用,使生胶达到塑化的目的。
塑炼过程的实质是橡胶的大分子断裂成相对分子质量较小的分子,从而使黏度下降,可塑性增大。
(2)胶料的混炼将各种配合剂混入生胶中制成质量均匀的混炼胶的过程称为混炼。
其基本任务是制造出符合性能要求的混炼胶,使压延或压出成型、涂胶及硫化等后续工序得以正常进行。
混炼过程就是炭黑等配合剂在生胶中均匀分散的过程,配合剂每一颗粒的表面必须完全被橡胶包围和湿润。
用来制备塑炼胶、混炼胶的设备有开放式炼胶机(简称开炼机)、密闭式炼胶机(简称密炼机)。
开炼机的工作原理是两个异向向内旋转的中空辊筒以不同速度相对回转,两辊筒大小相同。
生胶或胶料随着辊筒的转动在摩擦力作用下被卷入两辊间隙。
由于两辊筒的转速不同而产生速度梯度作用,生胶或胶料受到强烈的摩擦剪切,橡胶的分子链断裂,在周围氧气或塑解剂的作用下生成相对分子质量较小的稳定分子,塑炼后橡胶的可塑性得到提高,混炼后可获得质量均匀的混炼胶。
橡胶制品的成形方法有哪些?一、模压成型常用模压方法来制造某些形状复杂如皮碗、密封圈的橡胶制品,借助成型的阴、阳模具将胶料放置在模具中加热成型。
阅读:橡胶模压制品的废次品的特征及产生原因二、挤出成型压出成型又称挤出成型,压出成型常用设备是橡胶挤出机,工作原理与塑料挤出机相似。
物料经过挤出机料斗进入料筒,通过料筒和旋转螺杆之间的作用,胶料边受热塑化,边被螺杆向前推送,连续通过机头并借助于口型模而制成各种复杂截面形状的制品或半制品,如轮胎的胎面胶、内胎胎筒、纯胶管、胶管内外层胶及电线和电缆的外皮等。
(完整版)橡胶生产工艺

橡胶制品的基本生产工艺过程4.1 基本工艺流程伴随现代工业尤其是化学工业的迅猛发展,橡胶制品种类繁多,但其生产工艺过程,却基本相同。
以一般固体橡胶(生胶)为原料的制品,它的生产工艺过程主要包括:原材料准备→塑炼→混炼→成型→硫化→休整→检验4.2 原材料准备橡胶制品的主要材料有生胶、配合剂、纤维材料和金属材料。
其中生胶为基本材料;配合剂是为了改善橡胶制品的某些性能而加入的辅助材料;纤维材料(棉、麻、毛及各种人造纤维、合成纤维)和金属材料(钢丝、铜丝)是作为橡胶制品的骨架材料,以增强机械强度、限制制品变型。
在原材料准备过程中,配料必须按照配方称量准确。
为了使生胶和配合剂能相互均匀混合,需要对某些材料进行加工:生胶要在60--70℃烘房内烘软后,再切胶、破胶成小块;块状配合剂如石蜡、硬脂酸、松香等要粉碎;粉状配合剂若含有机械杂质或粗粒时需要筛选除去;液态配合剂(松焦油、古马隆)需要加热、熔化、蒸发水分、过滤杂质;配合剂要进行干燥,不然容易结块、混炼时旧不能分散均匀,硫化时产生气泡,从而影响产品质量;4.3 塑炼生胶富有弹性,缺乏加工时的必需性能(可塑性),因此不便于加工。
为了提高其可塑性,所以要对生胶进行塑炼;这样,在混炼时配合剂就容易均匀分散在生胶中;同时,在压延、成型过程中也有助于提高胶料的渗透性(渗入纤维织品内)和成型流动性。
将生胶的长链分子降解,形成可塑性的过程叫做塑炼。
生胶塑炼的方法有机械塑炼和热塑炼两种。
机械塑炼是在不太高的温度下,通过塑炼机的机械挤压和摩擦力的作用,使长链橡胶分子降解变短,由高弹性状态转变为可塑状态。
热塑炼是向生胶中通入灼热的压缩空气,在热和氧的作用下,使长链分子降解变短,从而获得可塑性。
4.4 混炼为了适应各种不同的使用条件、获得各种不同的性能,也为了提高橡胶制品的性能和降低成本,必须在生胶中加入不同的配合剂。
混炼就是将塑炼后的生胶与配合剂混合、放在炼胶机中,通过机械拌合作用,使配合剂完全、均匀地分散在生胶中的一种过程。
橡胶的塑炼与混炼原理工艺24页PPT

41、实际上,我们想要的不是针对犯 罪的法 律,而 是针对 疯狂的 法律。 ——马 克·吐温 42、法律的力量应当跟随着公民,就 像影子 跟随着 身体一 样。— —贝卡 利亚 43、法律和制度必须跟上人类思想进 步。— —杰弗 逊 44、人类受制于法律,法律受制于情 理。—敢地 走到底 ,决不 回头。 ——左
45、法律的制定是为了保证每一个人 自由发 挥自己 的才能 ,而不 是为了 束缚他 的才能 。—— 罗伯斯 庇尔
56、书不仅是生活,而且是现在、过 去和未 来文化 生活的 源泉。 ——库 法耶夫 57、生命不可能有两次,但许多人连一 次也不 善于度 过。— —吕凯 特 58、问渠哪得清如许,为有源头活水来 。—— 朱熹 59、我的努力求学没有得到别的好处, 只不过 是愈来 愈发觉 自己的 无知。 ——笛 卡儿
橡胶浇注工艺
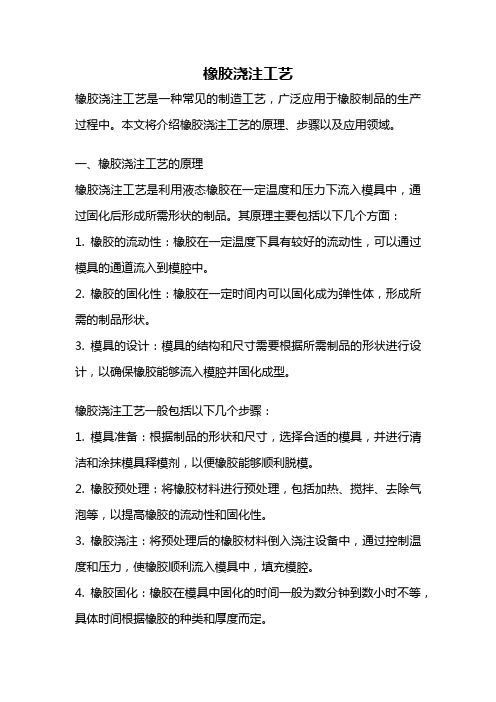
橡胶浇注工艺橡胶浇注工艺是一种常见的制造工艺,广泛应用于橡胶制品的生产过程中。
本文将介绍橡胶浇注工艺的原理、步骤以及应用领域。
一、橡胶浇注工艺的原理橡胶浇注工艺是利用液态橡胶在一定温度和压力下流入模具中,通过固化后形成所需形状的制品。
其原理主要包括以下几个方面:1. 橡胶的流动性:橡胶在一定温度下具有较好的流动性,可以通过模具的通道流入到模腔中。
2. 橡胶的固化性:橡胶在一定时间内可以固化成为弹性体,形成所需的制品形状。
3. 模具的设计:模具的结构和尺寸需要根据所需制品的形状进行设计,以确保橡胶能够流入模腔并固化成型。
橡胶浇注工艺一般包括以下几个步骤:1. 模具准备:根据制品的形状和尺寸,选择合适的模具,并进行清洁和涂抹模具释模剂,以便橡胶能够顺利脱模。
2. 橡胶预处理:将橡胶材料进行预处理,包括加热、搅拌、去除气泡等,以提高橡胶的流动性和固化性。
3. 橡胶浇注:将预处理后的橡胶材料倒入浇注设备中,通过控制温度和压力,使橡胶顺利流入模具中,填充模腔。
4. 橡胶固化:橡胶在模具中固化的时间一般为数分钟到数小时不等,具体时间根据橡胶的种类和厚度而定。
5. 脱模和后处理:橡胶固化后,将制品从模具中取出,进行脱模。
然后根据需要进行修整、清洁、检验等后处理工序。
三、橡胶浇注工艺的应用领域橡胶浇注工艺广泛应用于橡胶制品的生产中,主要包括以下几个领域:1. 汽车工业:橡胶浇注工艺可以用于汽车零部件的制造,如橡胶密封件、橡胶管件等。
2. 电子工业:橡胶浇注工艺可以用于电子产品的制造中,如橡胶按键、橡胶密封圈等。
3. 医疗器械:橡胶浇注工艺可以用于医疗器械的制造,如橡胶导管、橡胶垫片等。
4. 工程机械:橡胶浇注工艺可以用于工程机械的制造,如橡胶履带、橡胶振动器等。
5. 日用品:橡胶浇注工艺可以用于日用品的制造,如橡胶手柄、橡胶垫等。
橡胶浇注工艺是一种常见且重要的制造工艺,通过控制橡胶的流动性和固化性,以及合理设计模具,可以制造出各种形状的橡胶制品。
橡胶工艺原理-复习思考题-+答案

橡胶工艺原理-复习思考题-+答案(总12页)--本页仅作为文档封面,使用时请直接删除即可----内页可以根据需求调整合适字体及大小--《橡胶工艺原理》复习思考题名词解释碳链橡胶、硬质橡胶、杂链橡胶、混炼胶、硫化胶、冷冻结晶、拉伸结晶、极性橡胶杂链橡胶:碳-杂链橡胶: 主链由碳原子和其它原子组成全杂链橡胶:主链中完全排除了碳原子的存在,又称为“无机橡胶”,硅橡胶的主链由硅、氧原子交替构成。
混炼胶:所谓混炼胶是指将配合剂混合于块状、粒状和粉末状生胶中的未交联状态,且具有流动性的胶料硫化胶 : 配合胶料在一定条件下(如加硫化剂、一定温度和压力、辐射线照射等)经硫化所得网状结构橡胶谓硫化胶,硫化胶是具有弹性而不再具有可塑性的橡胶,这种橡胶具有一系列宝贵使用性能。
硬质橡胶:玻璃化温度在室温以上、简直不能拉伸的橡胶称为硬质橡胶一般来说,塑料、橡胶、纤维的分子结构各有什么特点影响橡胶材料性能的主要因素有哪些?橡胶性能主要取决于它的结构,此外还受到添加剂的种类和用量、外界条件的影响。
(1) 化学组成:单体,具有何种官能团(2) 分子量及分子量分布(3) 大分子聚集状况:空间结构和结晶(4) 添加剂的种类和用量(5) 外部条件:力学条件、温度条件、介质简述橡胶分子的组成和分子链结构对橡胶的物理机械性能和加工性能的影响。
答:各种生胶的MWD曲线的特征不同,如NR一般宽峰所对应的分子量值为30~40万,有较多的低分子部分。
低分子部分可以起内润滑的作用,提供较好的流动性、可塑性及加工性,具体表现为混炼速率快、收缩率小、挤出膨胀率小。
分子量高部分则有利于机械强度、耐磨、弹性等性能。
简述橡胶的分类方法。
答:按照来源用途分为天然胶和合成胶,合成胶又分为通用橡胶和特种橡胶;按照化学结构分为碳链橡胶、杂链橡胶和元素有机橡胶;按照交联方式分为传统热硫化橡胶和热塑性弹性体。
简述橡胶的分子量和分子量分布对其物理机械性能和加工性能的影响。
橡胶工艺原理

橡胶工艺原理绪论一.橡胶材料的特点1.高弹性:弹性模量低,伸长变形大,有可恢复的变形,并能在很宽的温度(-50~150℃)范围内保持弹性。
2.粘弹性:橡胶材料在产生形变和恢复形变时受温度和时间的影响,表现有明显的应力松弛和蠕变现象,在震动或交变应力作用下,产生滞后损失。
3.电绝缘性:橡胶和塑料一样是电绝缘材料。
4.有老化现象:如金属腐蚀、木材腐朽、岩石风化一样,橡胶也会因为环境条件的变化而产生老化现象,使性能变坏,寿命下降。
5.必须进行硫化才能使用,热塑性弹性体除外。
6.必须加入配合剂。
其它如比重小、硬度低、柔软性好、气密性好等特点,都属于橡胶的宝贵性能。
表征橡胶物理机械性能的指标:1.拉伸强度:又称扯断强度、抗张强度,指试片拉伸至断裂时单位断面上所承受的负荷,单位为兆帕(MPa),以往为公斤力/平方厘米(kgf/cm2)。
2.定伸应力:旧称定伸强度,指试样被拉伸到一定长度时单位面积所承受的负荷。
计量单位同拉伸强度。
常用的有100%、300%和500%定伸应力。
它反映的是橡胶抵抗外力变形能力的高低。
3.撕裂强度:将特殊试片(带有割口或直角形)撕裂时单位厚度所承受的负荷,表示材料的抗撕裂性,单位为kN/m。
4.伸长率:试片拉断时,伸长部分与原长度之比叫作伸长率;用百分比表示。
5.永久变形:试样拉伸至断裂后,标距伸长变形不可恢复部分占原始长度的百分比。
在解除了外力作用并放置一定时间(一般为3分钟),以%表示。
6.回弹性:又称冲击弹性,指橡胶受冲击之后恢复原状的能力,以%表示。
7.硬度:表示橡胶抵抗外力压入的能力,常用邵尔硬度计测定。
橡胶的硬度范围一般在2 0~100之间,单位为邵氏A。
二.关于橡胶的几个概念1.橡胶:世界上通用的橡胶的定义引自美国的国家标准ASTM-D1566。
定义如下:橡胶是一种材料,它在大的变形下能迅速而有力地恢复其变形,能够被改性(硫化)。
改性的橡胶实质上不溶于(但能溶脹于)沸腾的苯、甲乙酮、乙醇—甲苯混合物等溶剂中。
- 1、下载文档前请自行甄别文档内容的完整性,平台不提供额外的编辑、内容补充、找答案等附加服务。
- 2、"仅部分预览"的文档,不可在线预览部分如存在完整性等问题,可反馈申请退款(可完整预览的文档不适用该条件!)。
- 3、如文档侵犯您的权益,请联系客服反馈,我们会尽快为您处理(人工客服工作时间:9:00-18:30)。
最新橡胶工艺原理(二十四)王作龄 编译中图分类号:T Q 330.1 文献标识码:E 文章编号:167128232(2005)032005220410.4.2 流动与弹性效应(挤出膨胀)对于粘弹性流体来说,除剪切应力外还存在着由弹性效应引起的法向应力(韦森堡效应),因此,它显示出在牛顿流体中看不到的特异现象。
将溶融高分子材料从毛细管中挤出时,该高分子材料在毛细管出口处不变细反而变粗的现象(见图10-21)也是粘弹性流体的一种特性。
图10-21 粘弹性液体的韦森堡效应(上)与巴勒斯效应(下) 橡胶和塑料在挤出等加工过程中也会出现这种现象,即胶料由口型挤出时,挤出物的直径大于口型直径。
因此,在确定胶坯形状等时,有必要预先调整好口型的形状。
这种现象称为挤出膨胀(巴勒斯效应)。
因此,用挤出机加工高分子材料时,要预测口型直径与制品截面形状之间的差异以及制品截面积,而后再确定口型的形状。
此外,口型直径与挤出物直径的比值称为挤出膨胀率。
挤出膨胀率以前采用挤出物截面积对毛细管和口型截面积的比值,而近年因测定装置等原因多采用挤出物直径对毛细管直径的比值。
在此,设定D j 为挤出物直径,W 为挤出物质量,l 为挤出物长度,ρ为挤出物密度,则挤出膨胀率Ds 可由下式表示:D j =4Wπlρ(10-28)当设口型直径为D 时,挤出膨胀率如式(10-29)所示:Ds =D j D(10-29)挤出物直径的测定除上述方法外,还有用测微计等测定的方法,最近还有人在口型出口附近用激光等光学方法进行测定。
对于前者,可认为试样系通过自重伸长变细,或因试片的测定装置引起变形等。
对于后者,即使用激光测定的方法,试样在出口处因流动不稳定引起旋转,而且会因进一步旋转和暂时性熔体遭破坏等因素致使测定值增大。
因此,无论采用哪一种测定方法都要加以注意。
作为测定例,是在S BR (1512)中加入炭黑(H AF ,B334)、芳烃油、氧化锌和硬脂酸的配合胶料,而且对炭黑和芳烃油进行变量测定。
此外,用重量法测定挤出膨胀。
图10-22是于100°C 下各种材料的挤出膨胀率与剪切速率的关系。
由该图可见,挤出膨胀率表现出随剪切速率提高而增大的倾向。
图10-22 挤出膨胀率与剪切速率的关系10.4.3 紊流与剪切破坏(熔体破坏)将未硫化胶从口型等狭小的部位挤出时,如果加工速度(剪切速率)提高,则挤出物的表面上会出现粗糙或扭曲现象。
这种现象被称为熔体破坏,是粘弹性体具有的特征之一。
关于熔体破坏现象有各种学说,其中有,如同弹性体因变形引起破坏一样,在流动场中施加极限以上的力时,熔体同样也产生破坏的弹性破坏学说,以及口型壁面与胶料之间的不稳定滑动(蠕动)学说。
图10-23 用流痕法观察挤出物的结果(a)-稳流;(b)-粗糟表面;(c)-熔体流动破坏 与图10-23所示的稳流相比,熔体破坏是在增加剪切速率时表面出现粗糙,而后,整体变形为扭曲的状态,此系常见现象。
挤出物扭曲现象有时称为螺旋形流出。
此外,图10-24为日本学者大柳康提出的例子。
他难以解决的是不能正确限定引起熔体破坏的条件。
大柳康等学者提出,发生螺旋形流出和熔体破坏的极限条件用剪切应力表示,规定发生螺旋形流出的极限剪切力为2~3kg f Πcm 2,发生熔体破坏的极限剪切应力为3~5kg f Πcm2。
此外,产生这些不良现象的机理是,在毛细管的树脂流入端附近产生的应力平衡因流速增大而被破坏,所以在一处或几处发生弹性破坏。
表10-13和表10-14是关于S BR (1512)配合胶料挤出后将表面状态分4个等级进行评价的实例。
由表得知,在温度和剪切速率较高的区域产生了熔体破坏。
图10-24 HIZEX 27000H 的流出树脂的内部和表面的流动花纹表10-13 挤出物表面状态等级等级流动种类挤出物表面状态1正常流动表面光滑直径无变化2正常流动表面无光泽不稳定流动表面粗糙初始3异常流动表面粗糙显著4异常流动熔体破坏初始表10-14 挤出物表面状态等级与L ΠD 、温度和剪切速率的关系L ΠD 温度°C剪切速率 r ,秒-112.1624.3260.80121.6143.2608.012169022233442Π1100222223311022222339022223345Π1100222233311022223339022344447.5Π11002223444110222223490223444410Π110022234441102222334注:挤出物为S BR (1512)配合胶料10.4.4 流痕(weld line )流痕是在挤出成型和注射成型过程中,胶料在模型内等会合的部位形成的一种缺陷,即挤出物表面呈现线状。
此外,该缺陷在挤出物内部也以断面状扩大,成为制品强度降低和产生裂纹的原因。
图10-25的下图是关于简单流痕产生的机理。
由图可知,从两侧注胶口流入的胶料在中央位置会合,产出了流痕。
此时,向模型内部流动的胶料,其顶端被称为熔体流动顶端(图10-25的上图)。
图10-25 流痕部分强度试验用试样 形状复杂的制成品,难以了解其流痕产生的位置。
此外,对于有厚度的橡胶材料,因在内部形成了流痕,所以更难了解其产生的位置。
此时,若减少胶料填充量(缺胶),则在熔接部分出现了许多空穴。
下文将要介绍的模拟解析加工过程引人注目。
因此,对产生流痕的部分进行预测,对模型进行改进,以便降低流痕对制成品的影响。
10.5 用计算机模拟加工过程上文讨论的有关流动的各种现象是很费时间的。
最近,正盛行利用C AF (计算机辅助工程软件)技术解析橡胶加工过程。
随着计算机应用范围的拓展,人们开发了多种用于橡胶加工业的软件。
早期计算机主要用于解析填充过程中熔体流动顶端的计算等,最近还将它用于解析注射成型硫化过程中的保压、冷却过程、制品歪曲现象等,以及用于解析胶料流动、硫化和模型设计等。
10.5.1 关于流动解析程序在求取注射成型中的填充压力时,计算注胶口主流道和模腔等的压力损失,研究流动的顶端是不到达模型末端是必要的。
但是,在研究该问题时必须考虑胶料的物理性能和模型的形状。
如上所述,胶料粘度随剪切速率不同而各异。
此外,最近使用的模型多数比较复杂,增加这些因素进行计算就比较困难。
因此,用计算机解析流动引人注目。
C AE 的研究始于1970年左右,从开始的一维流动的解析进展到二维流动的解析。
最近,随着计算机的发展,还在进行三维流动的解析。
下文将介绍杉浦弘等学者提出的一元流动解析例。
该例是将图10-26所示平板形状模型的单元因素应用于图10-27中,根据各因素的计算结果再计算整体状态的方法。
在应用单元因素的方法时,流动一般如图10-27所示,从注胶口向主流道扩大和分流,所以要将圆锥形、圆柱形和圆板形单元因素精细地组合起来。
图10-26 实验用模型的典型单元因素 此外,线性主流道部分因流动比较简单,所以可用一个单元因素表示。
再者,对于主流道有弯曲的部分,对单元因素进行细致的组合是必要的。
由图10-28可见,实验值与计算值几乎一致。
对于一维流动的解析来说,形状简单的模型容易操作,而形状复杂的模型则难以操作。
因此,二维流动解析引人注目。
挤出物的形状多为平板状,因此可使用下列计算式。
图10-27 实验用模型的单元因素分割图图10-28 整体压力降低的实验值与计算值的比较 在解析流动的,一般将制品看作为在薄平行板之间的流动的非压缩性流体,基础理论式采用正交座标系以下简化的连续式,用运动量式和能量式表示,即:5Vx 5x +5Vy5y=0(10.30)-5P 5x +5τzx 5z=0(10.31)-5P 5y +5τzy 5z=0(10.32)ρc 5T 5t =λ52T 5x 2+λ52T 5y 2λ52T 5z2(10.33)式中,Vx 和Vy 分别为x 方向和y 方向的速度;τzx 和τzy 分别为Z x 平面方向的Z y 平面方向的剪切应力;ρ为密度;c 为比热;λ为导热系数;T 为温度;t 为时间。
作为解析例,图10-29为未硫化胶填充时的流动速度;图10-30为使用1Π4圆平板状模图10-29 未硫化胶填充模型时的流动速度状态图10-30 壁厚中心硫化度的分布(单位:%)型从未硫化胶充模到硫化的解析例。
由图可知,未硫化胶的填充状态和硫化状态良好,对成型条件的设定和硫化条件的确定有很大好处。
10.5.2 未硫化胶的流动解析M.D.H.托马斯提出了未硫化胶流动解析例。
数学模型系使用由质量、能量和运动量的各方程式得出的联立方程。
该联立方程考虑了粘度与温度的关系。
此外,采用Hele 2Shaw 流动,对模型内未硫化胶的流动进行模拟。
此时的解析条件如下: ①流动为斯托克斯流动,惯性项可省略;②截面薄,厚度方向的流动可忽略不计;③热移动设定为流动方向的热平流和厚度方向的热传导;④材料为非压缩性材料;⑤流动假定为通常的粘性流动,壁表面假(下转第56页)橡胶小知识比表面积 比表面积是衡量粉体材料粒子粗细(或粒径大小)的指标,用m 2Πg 表示。
材料的粒径越小,则比表面积越大。
粉体粒子的粗细不仅影响加工难易程度(粒子越细,分散越难),且对橡胶的力学性能也有决定性的作用。
比表面积越大,补强效果越好,这就意味着橡胶与粒子间接触和反应的机会越多。
以炭黑为例,比表面积与粒径之间存在着对应关系,如下表所示。
几种常用炭黑的粒径和比表面积品种平均粒径nm 比表面积m 2Πg电镜法氮吸附法(BET )大分子吸附法(CT AB )中超耐磨炉黑23111.0107.994.4高耐磨炭黑2977.266.963.2通用炉黑5029.325.225.5半补强炭黑6020.617.916.6中粒子热裂炭黑4709.811.311.1 这种对应关系也存在于其它粉体材料中,如白炭黑、氧化锌等。
测定比表面积的方法有电镜法、氮吸附法(又称BET 法)、碘吸附法及大分子吸附法。
其中除电镜法外,其他均属吸附法。
电镜法用测得之平均粒径,按球面积计算出比表面积,而其它方法则根据被炭黑吸附的物料量的多少来计算比表面积。
它们的不同点在于,由电镜法计算得到的比表面积仅为外表面积,而表面粗糙的粉体材料(如炭黑),其微孔所吸附的物料无法换算并一起计入比表面积,即外表面积和内表面积之和。
因此,电镜法所得之数值最小。
氮分子的体积最小(仅4mm ),所以,进入微孔后被吸附的量也多,所测得的比表面积接近于实际状况。
而CT AB 法所用的吸附物为溴化十六烷基三甲酸,其粒径比氮分子大得多,因此只能进入较大的微孔。
这样,所测得的比表面积比氮吸附法测得的要低。
(君轩)(上接55页)图10-31 未硫化胶填充图形定无滑动;⑥模型温度为定值。