制程品质管控注意事项
制程品质管控作业办法
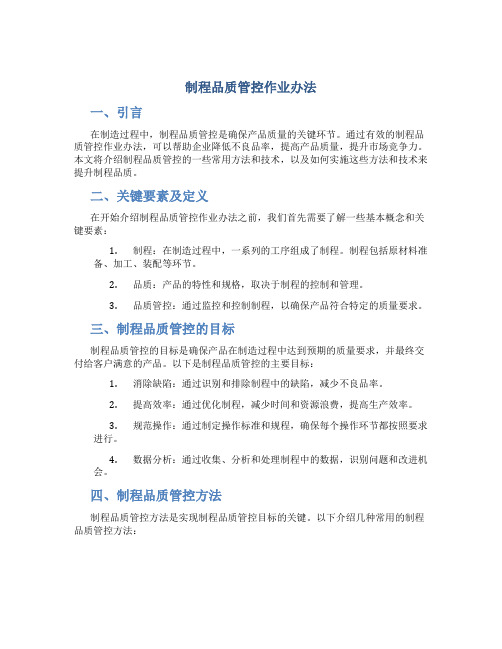
制程品质管控作业办法一、引言在制造过程中,制程品质管控是确保产品质量的关键环节。
通过有效的制程品质管控作业办法,可以帮助企业降低不良品率,提高产品质量,提升市场竞争力。
本文将介绍制程品质管控的一些常用方法和技术,以及如何实施这些方法和技术来提升制程品质。
二、关键要素及定义在开始介绍制程品质管控作业办法之前,我们首先需要了解一些基本概念和关键要素:1.制程:在制造过程中,一系列的工序组成了制程。
制程包括原材料准备、加工、装配等环节。
2.品质:产品的特性和规格,取决于制程的控制和管理。
3.品质管控:通过监控和控制制程,以确保产品符合特定的质量要求。
三、制程品质管控的目标制程品质管控的目标是确保产品在制造过程中达到预期的质量要求,并最终交付给客户满意的产品。
以下是制程品质管控的主要目标:1.消除缺陷:通过识别和排除制程中的缺陷,减少不良品率。
2.提高效率:通过优化制程,减少时间和资源浪费,提高生产效率。
3.规范操作:通过制定操作标准和规程,确保每个操作环节都按照要求进行。
4.数据分析:通过收集、分析和处理制程中的数据,识别问题和改进机会。
四、制程品质管控方法制程品质管控方法是实现制程品质管控目标的关键。
以下介绍几种常用的制程品质管控方法:1. 过程控制图过程控制图是一种统计工具,用于监控和控制制程的稳定性和能力。
它可以帮助我们了解制程的变化趋势和偏差,并及时采取措施进行调整。
过程控制图应用广泛,常见的类型包括控制图、直方图和散点图等。
使用过程控制图的步骤如下:1.收集并整理制程的相关数据。
2.绘制过程控制图,包括控制线和数据点。
3.分析过程控制图,判断制程是否稳定,并识别任何潜在问题。
4.根据分析结果,采取措施对制程进行调整和改进。
2. 核对表核对表是一种用于记录和跟踪制程执行情况的工具。
它可以帮助我们确认每个操作步骤是否按照预期进行,并及时发现问题。
核对表通常包括操作步骤、检查项和结果等。
使用核对表的步骤如下:1.根据操作标准和规程,制定核对表。
制程品质管理

制程品质管理制程品质管理是现代企业生产过程中的一个重要环节。
它涉及到从产品设计、原材料采购到生产流程的各个环节,旨在确保产品质量的稳定和满足客户需求。
有效的制程品质管理不仅可以提高产品的可靠性和性能,还能提高企业的竞争力和口碑。
一、品质观念与意识制程品质管理的核心是建立企业内部员工的品质观念与意识。
这包括将品质视为企业生产和经营的首要目标,要求每个员工在工作中都注重品质,关注每一个环节。
只有通过全员参与,才能确保每个生产细节都符合高品质的标准。
二、流程管理流程是制程品质管理的重要部分。
通过建立并持续改进生产流程,可以减少错误和事故的发生,提高制程效率和品质稳定性。
流程管理的关键是标准化,即确保所有员工都按照统一的规范进行操作,从而避免由于个体操作引起的品质问题。
三、供应链管理制程品质管理不仅要关注内部流程,还要关注外部供应链的质量控制。
在选择供应商时,企业应充分考虑其品质管理能力,并与之建立长期、密切的合作关系。
通过与供应商的合作,不仅可以实现共赢,还可以共同提升产品的质量水平。
四、数据分析与决策数据分析是制程品质管理的重要手段。
通过对生产数据进行收集、整理和分析,可以发现潜在的问题和趋势,及时采取纠正措施,防止品质问题扩大。
数据还可以为企业提供决策支持,帮助企业优化生产流程,提高生产效率和品质水平。
五、员工培训与激励员工培训是制程品质管理的基础保障。
通过定期培训,提高员工的工作技能、品质意识和质量控制知识,可以使员工更加熟悉操作规程,减少误操作的发生。
此外,通过激励机制,如奖励制度和晋升机制,可以激发员工的积极性,提高工作质量和效率。
六、持续改进制程品质管理是一个不断改进的过程。
企业要有持续改进的意识,不断寻找提高品质的方法和途径。
这涉及到流程的改进、设备的更新、技术的创新等方面。
只有不断追求卓越,才能在激烈的市场竞争中立于不败之地。
总结制程品质管理对于企业来说非常重要。
它涉及到企业内外多个环节,需要全员参与,强调标准化和流程优化。
FPC制程要点2
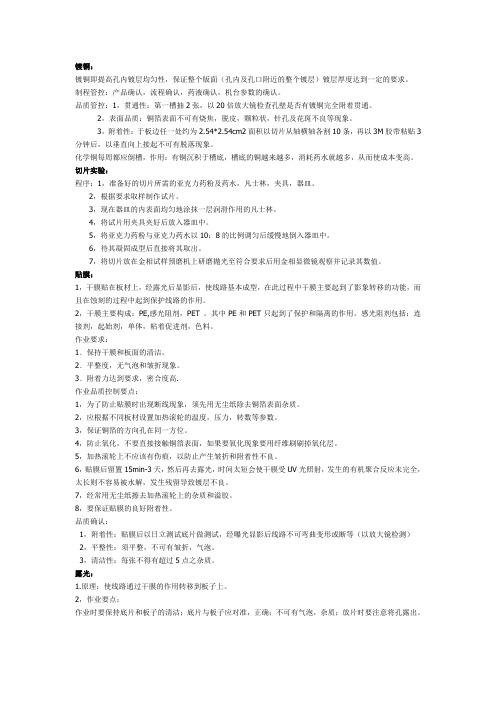
镀铜:镀铜即提高孔内镀层均匀性,保证整个版面(孔内及孔口附近的整个镀层)镀层厚度达到一定的要求。
制程管控:产品确认,流程确认,药液确认,机台参数的确认。
品质管控:1,贯通性:第一槽抽2张,以20倍放大镜检查孔壁是否有镀铜完全附着贯通。
2,表面品质:铜箔表面不可有烧焦,脱皮,颗粒状,针孔及花斑不良等现象。
3,附着性:于板边任一处约为2.54*2.54cm2面积以切片从轴横轴各割10条,再以3M胶带粘贴3分钟后,以垂直向上接起不可有脱落现象。
化学铜每周都应倒槽,作用:有铜沉积于槽底,槽底的铜越来越多,消耗药水就越多,从而使成本变高。
切片实验:程序:1,准备好的切片所需的亚克力药粉及药水,凡士林,夹具,器皿。
2,根据要求取样制作试片。
3,现在器皿的内表面均匀地涂抹一层润滑作用的凡士林。
4,将试片用夹具夹好后放入器皿中。
5,将亚克力药粉与亚克力药水以10:8的比例调匀后缓慢地倒入器皿中。
6,待其凝固成型后直接将其取出。
7,将切片放在金相试样预磨机上研磨抛光至符合要求后用金相显微镜观察并记录其数值。
贴膜:1,干膜贴在板材上,经露光后显影后,使线路基本成型,在此过程中干膜主要起到了影象转移的功能,而且在蚀刻的过程中起到保护线路的作用。
2,干膜主要构成:PE,感光阻剂,PET 。
其中PE和PET只起到了保护和隔离的作用。
感光阻剂包括:连接剂,起始剂,单体,粘着促进剂,色料。
作业要求:1﹑保持干膜和板面的清洁。
2﹑平整度,无气泡和皱折现象。
3﹑附着力达到要求,密合度高.作业品质控制要点:1,为了防止贴膜时出现断线现象,须先用无尘纸除去铜箔表面杂质。
2,应根据不同板材设置加热滚轮的温度,压力,转数等参数。
3,保证铜箔的方向孔在同一方位。
4,防止氧化,不要直接接触铜箔表面,如果要氧化现象要用纤维刷刷掉氧化层。
5,加热滚轮上不应该有伤痕,以防止产生皱折和附着性不良。
6,贴膜后留置15min-3天,然后再去露光,时间太短会使干膜受UV光照射,发生的有机聚合反应未完全,太长则不容易被水解,发生残留导致镀层不良。
制程品质管制

制程品质管制制程品质管制是指在生产过程中,通过各种控制措施,确保产品符合规定要求和标准。
制程品质管理的目的是为了保障产品品质,提高生产效率,降低生产成本,提高企业竞争力。
制程品质管制的意义制程品质管制是制造业企业在生产过程中采取的一种重要管理方式。
其重要性表现在以下几个方面:一、提高产品质量制程品质管制是对产品品质进行有效控制的手段,可以较好地控制产品的各项指标,保障产品质量得到控制和提高。
二、提高生产效率制程品质管制可以通过控制生产过程,使生产过程中发现的问题及时解决,减少生产过程中的损失,提高生产效率。
三、降低制造成本通过制程品质管制,可以降低制造成本,提高企业竞争力。
制程品质管制的方法制程品质管制的方法包括两部分:一、质量规划1.划分控制点根据制造过程的特征和具体需求,确定合适的尺寸、质量参数,将控制点进行划分,对不同的控制点进行不同程度的管理和控制。
2.制定标准根据产品的使用要求制定适应的标准和质量要求,从而防止不同制造批次的产品出现质量异同的问题。
3.制定检查方案在质量规划过程中,要制定出符合产品标准的检查方案,对产品的各项指标进行标准化的检测。
二、质量控制1.过程控制制造企业需要在制造流程中进行严格的过程控制。
設計機械制造工藝時,要合理安排工艺流程,对每一步操作时间、过渡、切换等设施进行合理管理,以确保制品在每个环节的质量都可以得到保障。
2.品质检测对产品的质量要求,要严格执行符合标准的检验方案与检验标准,保证产品的所有指标能够得到合格的检测。
制程品质管控的重要性制程品质管控在整个企业的生产管理中,扮演了不可替代的角色。
只有降低生产成本,提高产品质量,增强企业市场竞争力,才能在日益激烈的竞争环境中立于不败之地。
制程品质管控不仅仅是一种企业管理手段,更是一种追求卓越品质的企业宗旨,不断优化完善制程管控,是企业长期稳定发展的关键。
如何做好制程品质管制
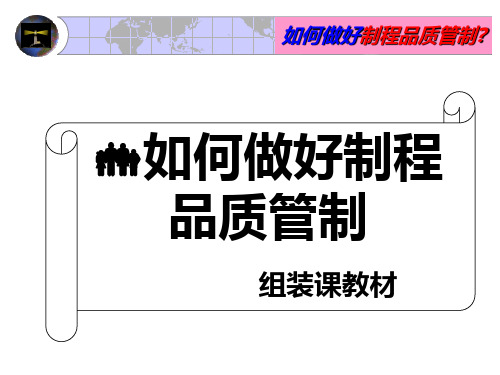
如何做好制程品质管制?
针对人为操作不良常用的改善对策
如何做好制程品质管制?
1.利用早会,将实际不良品拿出来示范,向员工说明不良原因与对策; 2.将不良品的损失金额化,并公布于现场,向员工说明; 3.按照个别不良品状况,分别教育; 4.加强作业员工责任心之教育; 5.员工技术性指导及品质观念灌输; 6.将良品、不良品分别用实物或照片列出,教育相关人员; 7.将正确与错误的动作照片列出,教育员工; 8.标准操作规范之要求、查核; 9.确实传达各工序品质需要之目标; 10.加强各工序间自检、互检,互相纠正、提醒; 11.新进员工或工作轮调时特别加强该站巡视; 12.将个别不良数予以公布,利用看板,达到警示效果.
4
不愿
1.管理问题; 2.组织问题; 3.缺乏压力; 4.缺乏激励.
1.开展品质评比活动; 2.推行QCC活动; 3.强化基层干部训练; 4.公司制度定期检讨修订,具激励性; 5.强调“对事不对人”的原则; 6.建立适当的责任归属.
如何做好制程品质管制?
二、强化人员的管理以提升品质
如何做好制程品质管制?
如何做好制程品质管制?
三、制度化、标准化、简单化、愚巧化
如何做好制程品质管制?
1.流程制度化:
任何作业流程都应该予以规范化、制度化,使 员工有据可循,使每一次作业可以预先得以教导、 安排,事中得到控制,事后便于追查.
如何做好制程品质管制?
2.工作标准化:
将工作方法、步骤、注意事项予以标准化, 易于操作,不易出错,便于查核,对品质稳定有 关键作用.
如何做好制程品质管制?
如何做好制程 品质管制
组装课教材
如何做好制程品质管制?
一、产生品质不良的原因及对策
制程管控------制程之三大纪律八项注意
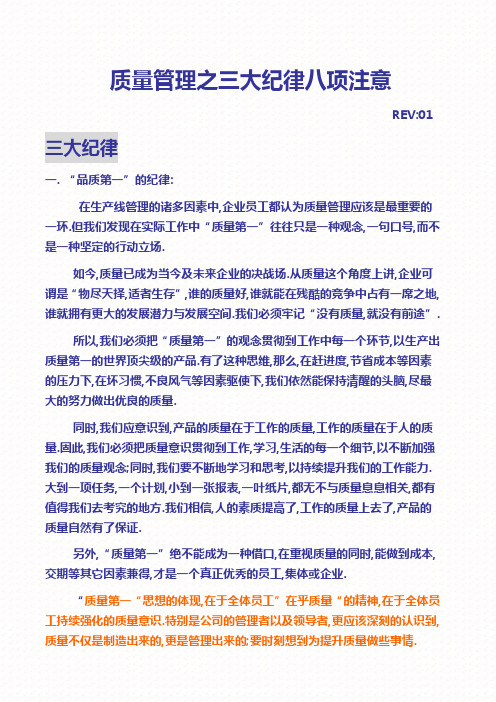
质量管理之三大纪律八项注意REV:01 三大纪律一.“品质第一”的纪律:在生产线管理的诸多因素中,企业员工都认为质量管理应该是最重要的一环.但我们发现在实际工作中“质量第一”往往只是一种观念,一句口号,而不是一种坚定的行动立场.如今,质量已成为当今及未来企业的决战场.从质量这个角度上讲,企业可谓是“物尽天择,适者生存”,谁的质量好,谁就能在残酷的竞争中占有一席之地,谁就拥有更大的发展潜力与发展空间.我们必须牢记“没有质量,就没有前途”.所以,我们必须把“质量第一”的观念贯彻到工作中每一个环节,以生产出质量第一的世界顶尖级的产品.有了这种思维,那么,在赶进度,节省成本等因素的压力下,在坏习惯,不良风气等因素驱使下,我们依然能保持清醒的头脑,尽最大的努力做出优良的质量.同时,我们应意识到,产品的质量在于工作的质量,工作的质量在于人的质量.固此,我们必须把质量意识贯彻到工作,学习,生活的每一个细节,以不断加强我们的质量观念;同时,我们要不断地学习和思考,以持续提升我们的工作能力.大到一项任务,一个计划,小到一张报表,一叶纸片,都无不与质量息息相关,都有值得我们去考究的地方.我们相信,人的素质提高了,工作的质量上去了,产品的质量自然有了保证.另外,“质量第一”绝不能成为一种借口,在重视质量的同时,能做到成本,交期等其它因素兼得,才是一个真正优秀的员工,集体或企业.“质量第一“思想的体现,在于全体员工”在乎质量“的精神,在于全体员工持续强化的质量意识.特别是公司的管理者以及领导者,更应该深刻的认识到,质量不仅是制造出来的,更是管理出来的;要时刻想到为提升质量做些事情.二.“按SOP作业”的纪律作业指导书是员工依照标准进行作业的唯一的正式的行动指南,是生产规格在产品生产过程中全面的真实的符合实际需要的反映与要求,任何个人之言论或会议之结论均无法替代SOP之职能,除非给标准化后成为临时或正式SOP.所以,员工唯有严格严格按照SOP作业,才能最大限度体现SOP之作用,才能生产出符合规格并让客户满意之产品.按SOP作业,首先,必须将SOP看懂.怎样才算懂了呢?我认为员工若能回答以下几个问题,便算通晓SOP了:1.SOP让我做什么?怎么做?2.这样做的目的是什么?3.按我这样做,达到了目的,并符合质量标准吗4.这样做了有其它不良影响吗?(如零件干涉,伤及零件,影响组立,空间不足等等)5.有更好的做法吗?(如节省时间,增强舒适性,提升质量等等)当以上任何一点存在疑问时,必须及时向组长,生产主管/IE工程师,品管或IE反映,必要时,须停线处理.当然,我们强调忠实地按照SOP作业,但并不宣扬迷信SOP, SOP是人作的,SOP也会存在问题.只有发现SOP存在的问题,并加以改善,才是按SOP作业的最高境界.目前,SOP一般存在以下问题:1.不符合生产规格.2.排站不合理,造成质量隐患或生产线不平衡.3.未及时按规定更新.4.描述不清,让人看不懂.5.明显与实际不符,做不到.所以,作为生产线人员,必须养成换线前核对生产规格的好习惯,并在生产过程中不断发现问题,反映问题,并锲而不舍地跟催,直到问题得到彻底的解决.但在任何变更之前,我们必须无条件地坚决按SOP作业,绝不允许私调制程,私改动作之行为发生.作业员的不良习惯是造成作业员不按SOP作业的主要原因,这些不良习惯主要是:1.依赖,被动,没人教则不看:坐等着别人来教,不教好像就不知道自己怎样动手,不主动去学去问.2.管中窥豹:没有全面地检视SOP,只是随便或选择性的看一部分,造成关键部分可能漏失..3.因循守旧:自以为本站工作千篇一律,内容变异后也浑然不知,还按旧的作业方式工作.4.自以为是,不懂装懂:即使有不懂的地方,也不反映,想当然地把产品作下去.这些都为管理者教导员工按SOP作业提出了更高的要求,一般教导分为八步完成:(1)解释OI含义,(2)倡导OI目的,(3)指出OI位置,(4)演示作业方法,(5)作出标准样品,(6)检查作业动作,(7)纠正不良动作,(8)赞美员工表现.三.“顺检”的纪律:关于NOAC的教育训练已经进行,其根本观念是把下一站当作自己的客户,其基本作法是加强顺检(顺检确实执行的判断依据是作业员能用手指出顺检的位置及顺检的位置没有不良品流到下一站),其最终目的是人人都不制造不良品,不接受不良品及不把不良品流到下一站.统计数据表明,顺检执行力度高的线别,质量状况(尤指A类不良)良好,顺检执行力度差的线别,质量状况则让人担忧(请参阅QA每日顺检执行力度稽核报告及生产线不良报表).所以说,顺检执行力度是反映一条生产线整体作业水准高低及集体作战能力强弱的重要因素.目前,对SOP上有备注顺检的站别我们虽要求必须顺检,但顺检执行力度并未完全达到100%,至于那些SOP未备注顺检的站别我们显然要求还不够,这与“NOAC”的精神是不符合的.我认为每一站别之都须对该站的产品作出检查以保证流下去的产品是良品,如点胶站的人员,就可以顺检正面的零件有无反向,相踫,错件及有无溢锡,铁芯有无破裂等等.当然,我们不仅要强调顺检,还要注意作业员能够顺检出不良品,就像让一个从未抽烟的人谈戒烟的体会无疑是茺谬的一样,那么,让一个从未拿过烙铁的人顺检焊锡质量显然也是错误的,所以说必须培养每个作业员须懂三站或三站以上的工作,顺检才会有实质性的改善,这是每个管理者应该重视的问题.最后,我们要说的是顺检的真正意义在于培养大家“我损俱损,我荣俱荣”的集体荣誉感,在于培养大家互相监督,互相促进的团队协作的精神.一个人作错了,而大家又顺检不出来,就等于整条线作不好,因为流下去的是不良品,而一个人作错了, 马上有人发现并指出来,作下去的就是良品.所以只有大家都作好了,质量才会有根本的保障,而作好的标准就是不仅把本站工作作好,还能顺检并修正别人的错误以保证产品最终质量.八项注意一.良品,不良品的管理须做到细致,合理1.良品及不良品之定义:根据产品目前所处之状态,或达到了制程要求,或合乎产品规格及或符合外观检验标准之产品方可视为良品,否则的话则可视为不良品.2.输送带上产品之摆放:一条平衡的生产线,输送带上的产品必须合理摆放,以达到质量及“5S”之要求.一般说来产品摆放须遵循四点原则:(1)按格摆放,间隔均匀,整齐划一.(2)方便下一站的作业.(3)便于制程辨视(站与站之间产品之区分)(4)不伤及产品(如P/C露在输送带外被刮伤压伤)3.良品,不良品之管制:(1)良品与不良品绝对不允许混放在一起.(2)任何不良品在处理之前须有明确之标示,标示的基本要求是让任何人看了都知道该产品目前所处状态.(3)外观不良品不允许与电气不良品放在一起.(4)Hi-Pot不良须立即分析,在修护OK前不可与其它任何不良品放在一起.(5)不同机种之产品禁止摆放在一起,在投A机种时,在线不可看到外观类似B机种产品.(6)正检盒内的不良品均须标示电气不良挂红卡,外观不良挂外观不良卡(可以自制不良卡),正检不良注明不良位置于板边.(书写清楚明了,背检也一样)(7)外观不良的处理:除CASE不良且经过内观检查之产品外,其它产品须从正检流入正常制程.(8)除免B/I机种外,任何电气不良之产品须经过B/I后才可流出货段.(9)未经本站处理的产品(良品或不良品)不可放到下一站.4.WIP的处理:根据定义, WIP属于一种特殊的不良品,WIP的数量插件流到二次不可超过十五台,所有Open CASE之WIP均应套上P/C胶带,并用防静电料盒放置,摆放整齐.最终按正常流程流线.原材料 IPQC PASS>=30pcs, 正常O/I&人員, 一人一張O/I, 按正常流程作業經加工站加工的材料 P QC P AS S<30pcs, 正常O/I, 人力安排由MF G決定.處理WIP品時,MF G通知IP QC, 所有產品在組立前, 須由IP QC100% 作內觀檢查.未經B/I過的WIP產品, 須按正常流程B/I;已B/I過的WIP產品, 更換CAS E,P/C,S/C, 背板,絕緣片, 膠布,套管這些机构件,無須B/I;已B/I過的WIP產品, 更換電子零件, 須全部 B/I2H.5.堆货之管理:一般情况下,禁止生产线堆货超过3台,特别是二次,可谓“二次流得顺,质量有保证”但特殊情况下,如测试仪器突然故障,输送带突然停走,换胶筒,超音波故障,换人作业,缺包材等等,视情况允许堆一定数量产品,但堆货:(1)不能与其它非堆货产品放在一起,(2)不能无明确标示.(生产线相关人员都要知道堆货产品目前所处之状态)(3)不能乱摆乱放(如摆放不整齐,放到下一工作站或到处乱挂,乱搁)(4)不能不及时处理.6. 产品拿取规范产品形态拿取位置拿取方式注意事项PWB PWB板边一手一片,轻拿轻放戴手套,不可污染零件及焊垫无CASE之半成品,成品产品板边一手一台,合理摆放不可挤压或碰撞零件有CASE之半成品,成品产品本体一手一台或两台,平稳不可摩擦刮伤或掉在地上二.对策的执行要做到坚决确实当问题发生后,如电气,外观高不良,FQC/QA抽验不良,客诉等等,各部门往往会一起检讨问题发生之原因,并提出有效可行之对策,以提防问题的再次发生,但在实际工作中,由于对对策的倡导不够,或由于工作人员执行力度不够,往往对策得不到很好的落实,造成问题的重复发生,让人痛心疾首.典型案例分析:某机种A,客户要求记录每箱报废Label序号及增补Label 序号.为方便操作,生产线起先将报废之Label贴于产品胶袋上随线流下,以便封箱人员记录.不久,客诉有报废Label未从胶袋上清理掉.生产线即将报废Label 改贴在一纸板上随产品流下,但操作困难.生产线便又将报废Label改贴在一个白色小方形泡棉上,随产品流下,但依然被客诉报废Label贴在胶袋上之事,原因为E段人员未严格执行对策,造成缺失,为此出货段开除8人.由以上事件可知,对策的执行必须完善三点:1.严格执行对策要求之内容.2.不断追踪对策实施之成效.3.评估对策之缺失,以不断改善.三.严格按照流程作业:在现代企业中,组织分工愈加细化,大家既要分工又要合作,为减少小疏失,提高效率及完善系统,各种流程被相继提出并改善,我们必须按照流程作业,就像作业员必须按照SOP作业一样.目前按流程作业存在以下问题:1.对作业流程一知半解,缺乏足够认识,甚至根本不了解什么流程.2.存在侥幸心理,漠视不按流程作业的严重后果.3.擅自改流程或跳流程,忽视正确流程的合理性与严密性.作为生产线基层管理者,必须掌握的流程有:不良反馈流程,WIP的处理流程,FQC/QA抽验不良处理流程,物料作业流程,材料加工流程,包装作业与出货流程等等.典型案例:某线应工程变更要求,须在入库成品外箱上增列一C a r t o n l a b e l.生产线在领出成品后,在未召开任何会议,参照任何规格的情况下,将准备好之L a b e l贴在外箱后入库,结果再次遭批退,原因为Label贴错位置.由此我们不难看出:1.作业者首先必须了解作业流程,并一步一步按照流程去作业.2.必须留下按流程作业的凭据,如测试流程记号,批退单的填写,重工flow chart的发行等等.在按流程作业方面,重工是最值得考究的.一般说来,每一次重工,都应该明确以下内容:重工的原因,重工的内容,重工的安排(材料,人员,治工具设备,方法,出货时间,是否B/I),重工的流程;如果是客退品重工,还要考虑产品有哪些变更,客户有哪些要求等等.在实际重工的现场,还要把以上内容倡导给每一个人,特别是作业员.四.作好不良反馈:一条生产线,不良反馈的好坏,直接反映了技术人员与管理人员警惕性的高低与质量意识的强弱.不良反馈做得好,不仅可以改善质量,还可以尽可能地减少损失,那么不良反馈怎样才算作好了呢?我以为须满足三点要求:1.及时.当不良发生并被确认时,要马上反馈,切不可麻痹大意或无动于衷;特别是人为不良存在信赖性,隐患性甚至影响安规的不良,要在5分钟内反馈给负责人.这可以大大提高解决问题的时效性和针对性.如有必要,则须立即对对策前后的产品作管制.2.确实.不良发生后要认真分析,信息(5WIH)的提供一定要准确,特别是数据的收集要一丝不苟,切不可出现有偏差甚至错误的信息.这可以大大提高解决问题的可靠性和完整性.3.改善.如果不良反馈仅停留在反映问题的层面上,而没有人去解决与追踪,不良反馈就没有任何意义.当不良发生后,大家只有经过认真分析,找出不良发生的原因,提出相应的改善对策,追踪以评估对策实施之成效,才算把不良反馈真正完成.这可以大大提高解决问题的可持续性.但我们看到的情况却经常是报表记录反映出的高不良无人问津,测试日报表与修护报表互相矛盾,主要的检查报表或测试报表无人签名,或干脆走过场式签名,A类不良在作业成绩表上得不到反映,一些完全可以避免的问题却持续发生,对生产线发生不良司空见惯.麻木不仁等等.五.“异常时期”的管理:同一班人,同一线体在不同时间制造出的质量往往不一样,我们把目前这种状况下质量出现异常的时期称为异常时期.异常时期一般会是a.上,下班时或换线时, b.逢年过节,盘点前后或周末加班, c.生产主管/IE工程师,组长上课开会或因其它原因不在生产线.异常时期的一般特点是:1.作业人员未准备好或场面比较混乱.2.工作人员心情过于放松或身在曹营心在汉.3.生产线没有管理人员或负责人.由此对应之对策是:1.作业人员必须在开线前2分钟已坐在自己的位置上准备就绪,若有不未准备好则不准开线,并追究其拖延之责任;停线时若线未停稳,则任何人不可以离开自己的位置,且未完成卡必须放在第一台未完成品之上,生产在线不可有标示不清之产品或堆货留给下一班次,或“半成品”或不良品.2.换线前所有之材料及治工具都应准备妥当,所有作业人员也应安排有序,换线时,所有人员须按安排坐在自己位置,禁止喧哗,且换线机种与上一机种之间至少保留5米以上安全距离.3.逢年过节或周未加班生产线管理人员必须亲临现场,并且工作前须向作业人员灌输质量观念.严肃纪律.并对此期间出现的质量问题加倍重视,同时对责任者严惩不怠,加严处罚.4.当组长或生产主管/IE工程师均不在在线时,应物色一名严肃认真的员工充当临时负责人,以负责生产线纪律.同时,平日应加强教育训练和奖惩力度以持续培养员工责任感和自觉性,以实现有效的管理.六.准确及时的咨讯收集对工作如果仅停留在“做”上,那叫上班;如果一定要把工作“做完”,叫责任,如果能把工作“做好”那才叫境界.那怎样才算做好了呢?当然首先得符合质量标准,那怎么样做才符合标准呢?这就靠信息.信息的来源是多种多样的,但作为一些基层管理者,主要有四个方面:1.人与人之间的交接.2.生产规格的阅读.3.历史记录查阅.4.生产线报表.而目前存在很多不正常的现象,如交接不清,生产规格无人问津,历史问题点不清楚,生产线报表徒具形式,这些不良现象直接导致了问题不能得到及时发现和解决,或问题重复发生,或未按FN要求生产等等.因此,针对以上四点,要求如下:1.针对问题点,人与人之间必须作详细而准确的交接,可以书面交接,可以面对面沟通,甚至可以打个电话或捎个口信,但必须把问题讲清楚.在交接出现岐义而导致问题发生时,一切以书面交接为证据,对责任者进行处罚.2.FN发下来后,生产线生产主管/IE工程师必须在规定时间内(2天)签核完毕,换线前2小时组长必须查看生产规格,主要是核对FN.3.历史纪录a.针对ADP各机种之质量问题,生产线之组长或生产主管/IE工程师均应作详细记录并分析.b.生产线投本线从未生产过之机种,须向曾经生产过该机种的线别组长询问问题点甚至请其指导,若为首批量产机种,则必须开量产前会议.c.借阅品管部生产规格查看历史记录.4.针对生产线检查报表,测试报表及修护报表,生产主管/IE工程师及组长都必须2小时签核一次,并就前三项不良提出改善对策.七.新人作业之管理追查各类质量事件,因新人作业而引起的就超过10%,怎样对新人作业进行管理是每一个基层管理者应该认真思考的问题.新人的再定义:1.进厂时间未满一月者.2.进厂时间虽超过三个月但从事新站别的工作者.3.从事专技站别工作但从无上岗证或专技证者.新人作业之管理:1.对进厂时间未满一周者,挂新人实习卡,除组长对作业员讲解作业方法并示范外,制造生产主管/IE工程师,QC工程师,IE工程师都有责任先对新人进行教导与确认后在新人实习卡上签名.2.对老员工从事新站别,该段组长须耐心讲解该站别之工作内容与注意事项,直到该员工可以胜任该站工作为止.并出示“老人新站别”卡,以便巡线人员稽核其工作质量.3.原则上禁止无证上岗,若因生产需要,须经MFG;IE,或ME;QC共同主动确认才可上岗,同时以上部门人员须在该员工作业成绩表上填上“M,Q,I,ME或T”字样.同时要强调以下几点:a.新人作业之站别不论在任何情况下,都禁止堆货,一旦堆货超过3台,则立即停线.b.若新人作业而导致质量事件,除对作业者进行必要处罚外,对管理者进行加倍处罚.c.新人在作业过程中若存在问题,应主动及时提出,以免酿成大错,后则对该员工加倍处罚.d.对新人表现优秀者,当月生产奖金评审一律在B等以上,甚至可以申请其它奖励.e.新人实习必须写新人实习报告,生产主管/IE工程师须根据报告反映之问题对该名员工进行面谈.八.线脚,锡渣,锡珠等引起的异音:在FQC/QA批退的记录中,因异音造成的批退一直占很大比例,以2001年11月份为例,FQC共批退6次,其中5次为异音,不良率为83.3%,而4次为线脚,锡渣,锡珠等造成(另一次是点胶不到位)不良率为66.7%.可以说怎样防止这个问题的再三发生,是让生产线非常头痛却是非常重要的#问题.目前,在大环境(如免剪脚,波焊质量)不能有大的改善的情况上,只能靠生产线防止,主要有以下几个方面:1.线脚部分:a.插件段,加工站零件是否有混放少量线脚,若有则立即清理干净,否则不准上线.b.气剪或斜口钳必须准时经过点检,若点检不合格,要及时更新.c.压克力罩要完好无损,不可有裂缝,破洞.d.作业时产品须伸进压克力罩内且与水平成450角以上,最好推行线外剪脚.剪脚作业员自检有无线脚从PCB孔流入产品,若有,则作不良品处理,清理出线脚.2.锡渣,锡珠部分:a.所有焊锡人员必须经过严格训练,拥有上岗证或专技证.b.流线作业时,作业员动作必须规范(如严格按焊锡五大步骤作业,泡棉的湿度,符合标准,锡渣盒时清理,动五次烙铁至少擦拭一次等等).c.焊锡人员在作业完毕后必须对自己的作业质量100%自检.d.输送带上的锡珠,锡渣,线脚等落在谁面前谁立即清理,不可流至下一站.e.锡面有人刷,且正面必须检查(正面往往有溢锡,零件沾锡珠,线脚,锡渣等,或有线脚从正面落入产品等等不良)f.生产线挡板是否起到应有作用,若否,则立即改善.g.所有的半成品是否有合理摆放.h.CASE若经过加工站加工,是否有经过顺检.i.出货段人员是否有100%听异音,听的方式是否正确(A面,B面皆听,摆动有节奏等等)当然以上仅能算生产线的权宜之计,要想长治久安,还得的大家齐心协力,从根本上解决问题,如推行免剪脚,减少二次焊锡动作等等.本<<三大纪律.八项注意>>未参考其它任何正式文件,仅为作者经验积累,难免有所谬误,不作正式文件发行. 解释权属胡楚明生产线各段(站)之注意事项在强调注意事项之前,先必须说明,对于已经标准化,规范化的东西,各线应该严格执行,并保持统一,避免差异.生产线各站别之工作内容主要以遵循SOP作业为主,但为适生产线质量及平衡之要求,部分站别之工作内容,须加强甚至推展,主要是加强一些顺检动作,具体说明如下:1插件段:(核心内容:顺检)1.1插件第一站(基本工作内容一般有:放框架,拿PWB或切PWB,压。
PCB制程品质预防重要监控点
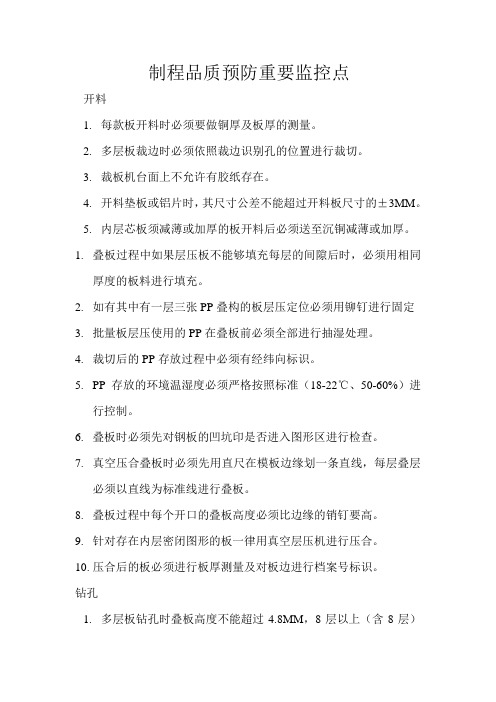
制程品质预防重要监控点开料1.每款板开料时必须要做铜厚及板厚的测量。
2.多层板裁边时必须依照裁边识别孔的位置进行裁切。
3.裁板机台面上不允许有胶纸存在。
4.开料垫板或铝片时,其尺寸公差不能超过开料板尺寸的±3MM。
5.内层芯板须减薄或加厚的板开料后必须送至沉铜减薄或加厚。
1.叠板过程中如果层压板不能够填充每层的间隙后时,必须用相同厚度的板料进行填充。
2.如有其中有一层三张PP叠构的板层压定位必须用铆钉进行固定3.批量板层压使用的PP在叠板前必须全部进行抽湿处理。
4.裁切后的PP存放过程中必须有经纬向标识。
5.PP存放的环境温湿度必须严格按照标准(18-22℃、50-60%)进行控制。
6.叠板时必须先对钢板的凹坑印是否进入图形区进行检查。
7.真空压合叠板时必须先用直尺在模板边缘划一条直线,每层叠层必须以直线为标准线进行叠板。
8.叠板过程中每个开口的叠板高度必须比边缘的销钉要高。
9.针对存在内层密闭图形的板一律用真空层压机进行压合。
10.压合后的板必须进行板厚测量及对板边进行档案号标识。
钻孔1.多层板钻孔时叠板高度不能超过4.8MM,8层以上(含8层)的多层板钻孔时每次只能叠一PNL。
2.钻孔过程中如出现断刀的现象,补孔时必须上调2个孔位进行补孔,并且本次钻孔完成后必须用红胶片对板的方式进行检查。
3.ROGERS系列板及聚四氟乙烯板在钻孔后一率用1200目以上的砂纸进行打磨。
4.钻孔后的板必须进行磨边倒角后方可转入下工序。
5.板厚≦3MM的板钻完内层定位孔后必须进行打披锋,6.光电产品钻孔后不允许进行打磨,外发钻孔时必须在外协单上注明不能打磨字样。
外型1.具有大金面外露的板外型前必须将板送丝印贴保护膜后方可进行外型作业。
2.作业员进行外型首件作业时,必须先铣出1PCS或1SET进行首件确认,不允许一次铣出一首板后进行首件确认。
批量≧10PNL 的板首件必须送IPQC进行确认。
3.V-CUT板批量10SET以上的板每调一次刀必须对首板送IPQC进行确认。
制程品质控制
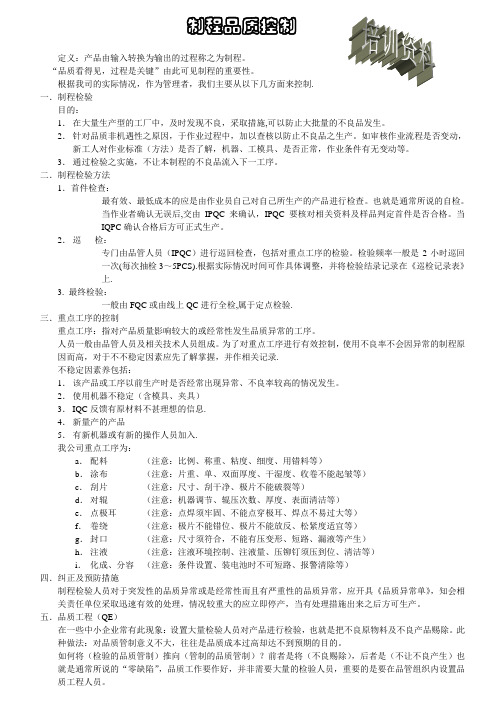
制程品质控制定义:产品由输入转换为输出的过程称之为制程。
“品质看得见,过程是关键”由此可见制程的重要性。
根据我司的实际情况,作为管理者,我们主要从以下几方面来控制.一.制程检验目的:1.在大量生产型的工厂中,及时发现不良,采取措施,可以防止大批量的不良品发生。
2.针对品质非机遇性之原因,于作业过程中,加以查核以防止不良品之生产。
如审核作业流程是否变动,新工人对作业标准(方法)是否了解,机器、工模具、是否正常,作业条件有无变动等。
3.通过检验之实施,不让本制程的不良品流入下一工序。
二.制程检验方法1.首件检查:最有效、最低成本的应是由作业员自己对自己所生产的产品进行检查。
也就是通常所说的自检。
当作业者确认无误后,交由IPQC来确认,IPQC要核对相关资料及样品判定首件是否合格。
当IQPC确认合格后方可正式生产。
2.巡检:专门由品管人员(IPQC)进行巡回检查,包括对重点工序的检验。
检验频率一般是2小时巡回一次(每次抽检3~5PCS).根据实际情况时间可作具体调整,并将检验结录记录在《巡检记录表》上.3. 最终检验:一般由FQC或由线上QC进行全检,属于定点检验.三.重点工序的控制重点工序:指对产品质量影响较大的或经常性发生品质异常的工序。
人员一般由品管人员及相关技术人员组成。
为了对重点工序进行有效控制,使用不良率不会因异常的制程原因而高,对于不不稳定因素应先了解掌握,并作相关记录.不稳定因素养包括:1.该产品或工序以前生产时是否经常出现异常、不良率较高的情况发生。
2.使用机器不稳定(含模具、夹具)3.IQC反馈有原材料不甚理想的信息.4.新量产的产品5.有新机器或有新的操作人员加入.我公司重点工序为:a.配料(注意:比例、称重、粘度、细度、用错料等)b.涂布(注意:片重、单、双面厚度、干湿度、收卷不能起皱等)c.刮片(注意:尺寸、刮干净、极片不能破裂等)d.对辊(注意:机器调节、辊压次数、厚度、表面清洁等)e.点极耳(注意:点焊须牢固、不能点穿极耳、焊点不易过大等)f.卷绕(注意:极片不能错位、极片不能放反、松紧度适宜等)g.封口(注意:尺寸须符合,不能有压变形、短路、漏液等产生)h.注液(注意:注液环境控制、注液量、压铆钉须压到位、清洁等)i.化成、分容(注意:条件设置、装电池时不可短路、报警清除等)四.纠正及预防措施制程检验人员对于突发性的品质异常或是经常性而且有严重性的品质异常,应开具《品质异常单》,知会相关责任单位采取迅速有效的处理,情况较重大的应立即停产,当有处理措施出来之后方可生产。
制程品质管理制度

制程品质管理制度第一章总则第一条为加强公司对制程品质的管理,确保产品品质的稳定和可靠性,根据《质量管理制度》的要求,制定本制度。
第二条本制度适用于公司生产制程的品质管理,规范公司的制程操作和控制,确保产品品质符合相关标准和客户要求。
第三条公司生产制程品质管理的责任主体为生产制程管理部门,具体负责品质检验、控制和改进工作。
第四条公司各生产制程部门应依据本制度,在生产过程中开展制程品质管理工作,确保生产过程符合质量要求。
第二章制程品质管理体系第五条公司应建立起严格的制程品质管理体系,包括质量方针、质量目标、质量管理程序和相关文件。
第六条质量方针是公司品质管理工作的总体指导思想,必须贯彻于公司全体员工的工作实践之中。
第七条公司应制定制程品质管理相关的目标,并将其具体化为具体的管理措施和要求。
第八条公司应建立完善的质量管理程序和相关文件,确保生产过程的品质管理工作得以规范和执行。
第九条公司应对制程品质管理体系进行定期的评审和监控,确保其持续有效。
第十条公司应建立起完善的品质管理档案和记录,对制程品质的改进起到辅助作用。
第三章制程品质管理责任第十一条公司生产制程部门是制程品质管理的直接责任主体,应具体负责制程的品质管理工作,并实施相关的品质管理措施。
第十二条公司生产制程部门应建立起完善的品质管理团队,对各制程进行全方位的品质管理工作。
第十三条公司生产制程部门应建立起职责明确的制程品质管理岗位,并确保相关人员具备相应的专业知识和技能。
第十四条公司生产制程部门应建立起健全的品质管理机构,明确各级主管人员的品质管理责任和权限。
第四章制程品质管理的基本要求第十五条公司生产制程部门应依据相关标准和要求,制定具体的制程品质管理计划,并贯彻执行。
第十六条公司生产制程部门应确保人员的技能与素质达标,并对其进行相应的培训和考核。
第十七条公司生产制程部门应建立起完善的制程品质管理流程和程序,确保生产过程的可控性。
第十八条公司生产制程部门应建立起严格的品质检验制度,并依据相关标准和要求对产品进行检验。
制程品质管控作业规定

制程品质管控作业规定1. 质量标准1.1. 零件标准•每个零件应符合设计图纸规格,材料品质符合标准要求。
•部件外观应符合设计图纸和质量要求,不得有明显缺陷。
•壳体、机壳等外壳需要进行防腐蚀处理,保证外形美观,否则需进行修复或更换。
1.2. 工艺标准•电器焊接应符合公司标准,不得出现未焊透、焊点接触面积不足等缺陷。
•焊接操作人员需持有证书,并进行定期培训。
•机器的零部件及配件采购须从正规渠道采购,补件源要求明确。
2. 品质管控2.1. 检验流程•零件检验:每个零件从生产出来到组成完成,均需要进行检验,检验合格后方可进入下一道工序。
•一次检验:零件组成完成后,进行一次全面检验,检验合格后方可进行下一个环节。
•精度检验:在机器组装完成后,岗位需要进行精度检验,检验过程中应严格按照检验标准操作。
2.2. 品质责任人•品质责任人应根据制程要求并结合实际情况,与工艺人员一起制定实施方案和作业规定,确保制程品质控制有力有效。
•品质责任人负责制定制程品质控制标准及检验标准,并进行培训。
•品质责任人必须具备相关工程、品质知识,要求检验员必须进行相关证书持有及定期培训。
2.3. 纪录与报告•制程品质控制要有严密的记录,以备案,便于追溯。
•对于不合格产品,要及时上报及时处理,同时组织相关人员进行分析,确定原因并采取措施以防止同类问题的再次发生。
•质量日报记录、质量月报分析、质量年度是公司制程品质控制的重要记录。
3. 盲点避免1.产品组装时应谨慎,防止安装过程中的误伤、碰撞及毁坏。
2.在运输过程中,产品应妥善包装,避免震荡、碰撞等,以防止损坏。
3.产品使用中,需注意机器的调试,使用前对产品性能进行一次全面检查,防止因机器性能因素造成的客户投诉。
4. 责任分工•制程品质管控分为产品质量管控和生产工艺管控。
产品质量管控主要负责对产品零部件质量进行管控,生产工艺管控主要负责对生产工艺执行情况进行管控。
5. 附则1.对于任何制程品质控制出现的问题,应及时报告公司领导并由制程品质管控人员及时处理。
制程品质管控作业办法

制程品质管控作业办法简介制程品质管控是制造企业重要的品质保障手段之一,可以帮助企业保证产品的稳定和一致性,并且在生产过程中及时发现和解决问题。
制程品质管控作业办法是描述制程品质管控操作流程和方法的文档。
制程品质管控作业流程制程品质管控作业流程是实施制程品质管控的关键,下面是流程的详细解释:1.初步检查:在制造生产的初期,需要进行初步检查,包括工艺和设备的确认,生产操作流程的合理性等基本检查。
2.设定关键控制点:分析全过程,将制造中最为重要的关键点确定下来,这些关键点是后续制程品质管控的依据。
3.设定检查标准:在关键控制点设定完成后,需要对这些关键点详细制定检查标准,判定和执行的依据。
4.样本抽取检验:在生产制造过程中需要抽样品进行检查,时间和样本数量需要再次确认,确保检验的全面性和准确性。
在检验时需要依据之前设定的检查标准进行操作。
5.记录结果分析:将抽样检查到的品质信息进行记录和分析,确保数据精确可靠,同时在发现异常情况时能够及时反馈。
6.品质问题解决:在发现品质异常问题及时进行解决处理,以确保产品符合质量要求。
7.经验总结:在制程品质管控的全过程中,需要及时总结经验,分析成功和不足之处,不断完善操作流程。
制程品质管控方法制程品质管控方法是具体实施制程品质管控的操作方法,下面是具体的制程品质管控方法:SOP规程的预设制定SOP规程,以确保所有人都对操作规程有清晰的认识和理解。
SOP规程包括规程的类型、制定标准、制定原则及其编制的要求等。
程序管理1.相关人员评审制程问题2.确认检查点3.解决问题4.业务流程的维护维护设备设备维护应包括预防性维护、校正和维护计划,以保持设备的正常运行状态。
同时,维护工作应是计划及合规的,工作记录要详细,并由经验丰富人员检查确保维护计划得到完整、有效的实施。
数据分析数据分析是制程品质管控的重要环节,通过对数据的分析,可以在制造的各个环节及时发现和预防问题,减少资源损失和不必要的工作量。
工厂制程品质控制
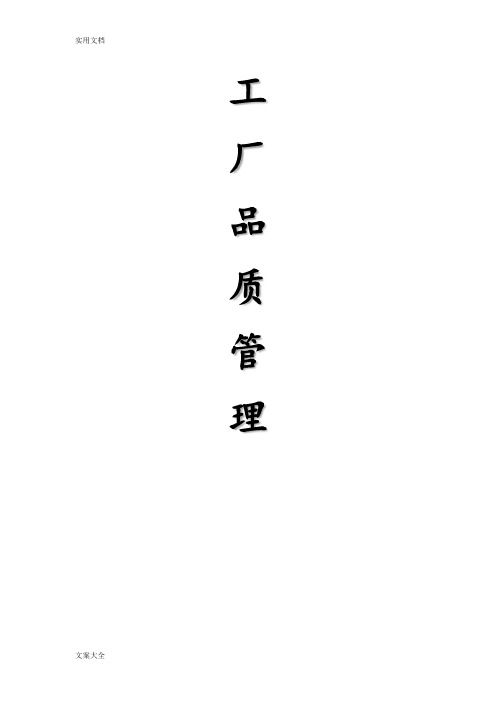
工厂品质管理工厂制程品质控制3.3.2 首件检验内容解读首件是指每个生产班次加工的第一个工件,或加工过程中因换人、换料、换岗以及换工装、调整设备等改变工序条件后加工的第一个工件。
对于大批量生产,“首件”往往是指一定数量的样品。
1.首件检验的操作者首件检验一般采用“三检制”的办法,即先由操作者自检,再由班组长复检,最后由检验员专检。
2.首件检验的条件(1)符合下列条件的产品才可以进行首件三检。
①有经正式批准的图样、技术条件、工艺规程。
②具有符合工艺规程规定的工装、量具,并经检定合格。
(2)下列情况经首件三检合格后方能继续生产。
①每个班开始时。
②每个工人每道工序第一件加工后。
③生产中更换操作人员。
④生产中更换或重调工装、机床设备。
⑤更改、调整工艺。
3.首件检验的主要项目(1)图号与工作单是否符合。
(2)材料、毛坯或半成品和工作任务单是否相符。
(3)材料、毛坯的表面处理和安装定位是否相符。
(4)配方配料是否符合规定要求。
(5)首件产品加工出来后的实际质量特征是否符合图纸或技术文件所规定的要求。
4.首件检验的要求进行产品首件检验时,必须注意以下事项。
(1)首件三检需由操作人员办理交验手续,经首件三检合格的零件、产品,要在交验单上签字盖章,并做好首件检验的记录。
(2)首件三检发生错检时,由参加三检者负责。
(3)不执行首件三检盲目生产、不听劝告者,检验员有权拒绝验收其产品,由此而造成的废品由直接责任者负责,视情节轻重程度赔偿废品损失。
(4)首件三检不合格,需查明原因,采取措施排除故障后重新进行首件三检。
(5)首件三检合格后,生产人员在生产过程中还要勤看、勤量、勤检查,检验员需要加强巡回检验,预防不合格品产生。
(6)对于重要零部件的关键工序和尺寸,应建立质量控制点,加强首件三检,增加巡回抽检的次数。
(7)检验员应按规定在检验合格的首件上作出标识,并保留到该批产品完工。
(8)首件检验必须及时,以免造成不必要的浪费。
制程品质管控作业办法

制程品质管控作业办法前言制程品质管控是保障产品质量的关键,一定要对其进行全面、系统的管控,使得产品的制造过程稳定,并达到最终的品质要求。
本文将介绍一些制程品质管控的作业办法,旨在为企业制造管理部门提供参考。
制程品质管控作业办法1. 设定品质标准首先,制程品质管控的前提是要设定品质标准,明确产品的品质要求。
品质标准包括外观、尺寸、性能、可靠性等各个方面,要根据不同的产品确定不同的标准。
必要时,还要进行实验验证、样品检验等,保证标准的准确性和可操作性。
2. 制定工艺流程表依据产品的制造工艺,制定工艺流程表,将加工工位、工序、检验点等都列入其中。
要特别注意的是,工艺流程表需根据品质标准调整和改进,持续优化工艺流程,以确保产品的制造过程稳定和质量可控。
3. 预防性控制在产品制造的每个环节中,都需要注意预防性控制。
对于可能出现的问题,要提前进行预防,及时采取控制措施,以避免品质问题的产生。
例如,在原材料采购中,要审核供应商的质量体系、技术设备等,确保原材料的质量符合标准。
4. 过程控制过程控制是制程品质管控的关键。
通过对制造过程进行全面、系统的管控,可以最大程度地避免制造过程中的质量问题。
具体来说,过程控制要包括以下几个方面:•操作规程制定:针对每个操作,都要建立详细的操作规程,确保操作的规范化、标准化。
•工艺参数控制:要针对每个工艺参数,建立相应的控制标准,确保参数在标准范围内。
•检测方法、仪器控制:要建立检测方法和仪器的控制标准,以保证检测结果的准确性。
5. 数据分析制程品质管控要高度重视数据分析。
通过对生产数据的分析,可以了解制造过程中的变化和趋势,及时调整制造过程,保证产品的品质稳定。
具体来说,要进行以下几个方面的数据分析:•制程能力分析:通过对制程数据的分析,计算出制程的能力,以了解制程能否稳定、满足品质标准。
•质量问题分析:对出现的各种质量问题,要进行详细的分析,找出根本原因,并给出相应的改进措施。
制程各工序间品质控制要点
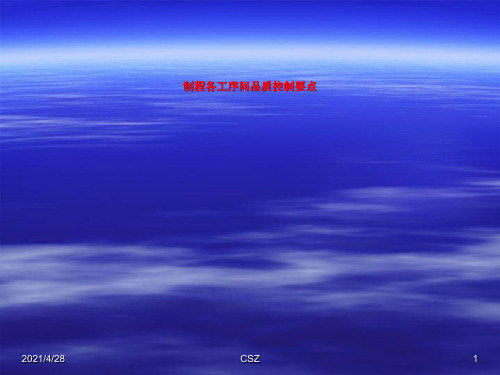
2021/4/28
CSZ
1
为了更好的控制产品质量,提高效率、 降低品质成本,现将生产中各工序间 易出的品质异常总结如下;大家都知 道在对产品进行检测时,必须注意六 大要素;材质、料厚、位置、方向、 数量、尺寸 、只有严格控制这几点才
能保证产品品质。
第一工序剪口;在进行剪口检验时必须具备展开的计 算能力,常出现用错材料,包括料厚、材质;此工序 为加工中首工序,常出现程式有误导致剪口错,在计 算展开时须注意确认外形是否有误,注意图纸尺寸; 在剪口检验时注意孔径尺寸的大小,因作业员在生产 时常出现装错刀的情况;在生产中常出现压印,须多 巡检,压印常为刀具带料没有及时清理产生的,有时 出现刀具带料和撞料的现象导致产品变形;还须注意 生产时走位导致剪口边不平齐;在剪口生产时须要求 将毛剌去除干净,在锉毛剌时作业员方法不当常将毛 剌锉到正面,巡检时须多注意。在生产时产品有不切
剪口程式有误,作业员少装刀具
按照图纸要求生产,在签单时将材料要 求标注清楚 在签单时须按照图纸进行全尺寸检测、 保留合格样板 在发现有此现象时须要求作业员及时清 理刀具 对刀盘加以清理消除不良隐患,对变形 材料是否停用
注意刀具的选择,剪口时速度不可过快,
参照图纸和样板认真核对
接刀不齐 剪口时走位
速度不可过快,增加夹爪的力量,
边的情况,注意夹爪印。
剪口
不良内容
不良的主要原因
控制方法
材料用错
作业员没按照图纸要求生产,生产 单有误
剪口展开 工程程式有误,作业员改程式错,
错
IPQC签单失误
产品表面 压印
刀具带料没有清理刀具
划伤
刀盘上的下模高出刀盘面致模具划 伤材料,材料变形
制程品质管控
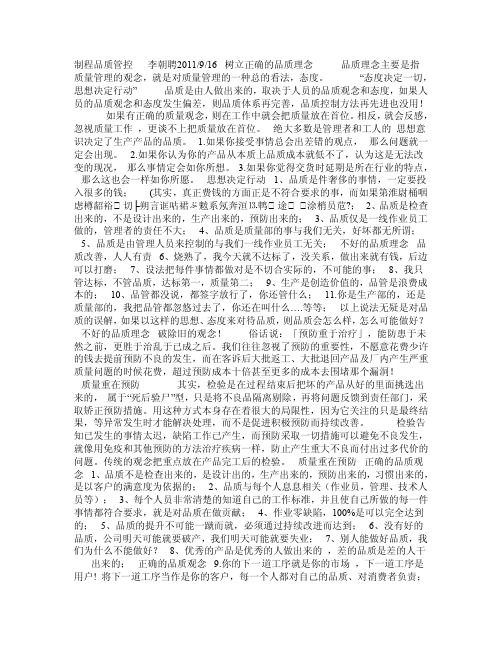
制程品质管控李朝聘2011/9/16树立正确的品质理念品质理念主要是指质量管理的观念,就是对质量管理的一种总的看法,态度。
“态度决定一切,思想决定行动”品质是由人做出来的,取决于人员的品质观念和态度,如果人员的品质观念和态度发生偏差,则品质体系再完善,品质控制方法再先进也没用!如果有正确的质量观念,则在工作中就会把质量放在首位。
相反,就会反感,忽视质量工作,更谈不上把质量放在首位。
绝大多数是管理者和工人的思想意识决定了生产产品的品质。
1.如果你接受事情总会出差错的观点,那么问题就一定会出现。
2.如果你认为你的产品从本质上品质成本就低不了,认为这是无法改变的现况,那么事情定会如你所想。
3.如果你觉得交货时延期是所在行业的特点,那么这也会一样如你所愿。
思想决定行动1、品质是件奢侈的事情,一定要投入很多的钱;(其实,真正费钱的方面正是不符合要求的事,而如果第淮尉桶咽虑樽龆裕 切├朔言诓咕裙ぷ魃系氖奔洹⒔鹎 途 涂梢员苊?;2、品质是检查出来的,不是设计出来的,生产出来的,预防出来的;3、品质仅是一线作业员工做的,管理者的责任不大;4、品质是质量部的事与我们无关,好坏都无所谓;5、品质是由管理人员来控制的与我们一线作业员工无关;不好的品质理念品质改善,人人有责6、烧熟了,我今天就不达标了,没关系,做出来就有钱,后边可以打磨;7、设法把每件事情都做对是不切合实际的,不可能的事;8、我只管达标,不管品质,达标第一,质量第二;9、生产是创造价值的,品管是浪费成本的;10、品管都没说,都签字放行了,你还管什么;11.你是生产部的,还是质量部的,我把品管都忽悠过去了,你还在叫什么….等等;以上说法无疑是对品质的误解,如果以这样的思想、态度来对待品质,则品质会怎么样,怎么可能做好?不好的品质理念破除旧的观念!俗话说:「预防重于治疗」,能防患于未然之前,更胜于治乱于已成之后。
我们往往忽视了预防的重要性,不愿意花费少许的钱去提前预防不良的发生,而在客诉后大批返工、大批退回产品及厂内产生严重质量问题的时候花费,超过预防成本十倍甚至更多的成本去围堵那个漏洞!质量重在预防其实,检验是在过程结束后把坏的产品从好的里面挑选出来的,属于“死后验尸”型,只是将不良品隔离剔除,再将问题反馈到责任部门,采取矫正预防措施。
如何控制制程品质
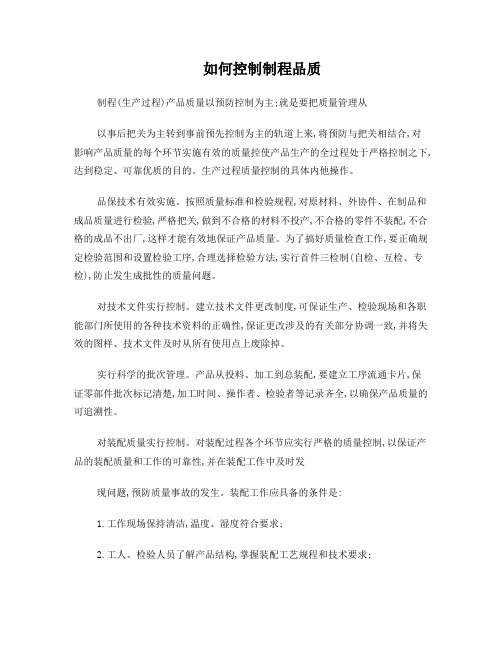
如何控制制程品质制程(生产过程)产品质量以预防控制为主;就是要把质量管理从以事后把关为主转到事前预先控制为主的轨道上来,将预防与把关相结合,对影响产品质量的每个环节实施有效的质量控使产品生产的全过程处于严格控制之下,达到稳定、可靠优质的目的。
生产过程质量控制的具体内他操作。
品保技术有效实施。
按照质量标准和检验规程,对原材料、外协件、在制品和成品质量进行检验,严格把关,做到不合格的材料不投产,不合格的零件不装配,不合格的成品不出厂,这样才能有效地保证产品质量。
为了搞好质量检查工作,要正确规定检验范围和设置检验工序,合理选择检验方法,实行首件三检制(自检、互检、专检),防止发生成批性的质量问题。
对技术文件实行控制。
建立技术文件更改制度,可保证生产、检验现场和各职能部门所使用的各种技术资料的正确性,保证更改涉及的有关部分协调一致,并将失效的图样、技术文件及时从所有使用点上废除掉。
实行科学的批次管理。
产品从投料、加工到总装配,要建立工序流通卡片,保证零部件批次标记清楚,加工时间、操作者、检验者等记录齐全,以确保产品质量的可追溯性。
对装配质量实行控制。
对装配过程各个环节应实行严格的质量控制,以保证产品的装配质量和工作的可靠性,并在装配工作中及时发现问题,预防质量事故的发生。
装配工作应具备的条件是:1.工作现场保持清洁,温度、湿度符合要求;2.工人、检验人员了解产品结构,掌握装配工艺规程和技术要求;3.检验人员经过考试合格后上岗操作;4.车间应将对装配质量(如产品性能、安全性、可靠性)有重大影响的工序以及工艺复杂的工序确定为重点工序,对执行重点工序的班组或个人设立控制点,以便对这些工序进行重点质量控制;掌握好质量动态。
要搞好产品生产过程的质量控制,就必须掌握产品质量的现状和动态,而综合统计与分析,是掌握质量动态的工具,如通过统计和分析产品的不合格率等指标,可及时掌握有关情况,以便采用相应的措施。
实施生产全过程的质量控制,除了以上几方面还要充分依靠群众,广泛开展质量管理小组活动,运用数理统计等科学方法进行质量控制。
制程品质管制的五要素

制程品质管制的五要素制程品质管制是一种重要的管理方法,用于确保产品在制造过程中的质量稳定性和一致性。
为了有效地进行制程品质管制,我们需要关注五个重要的要素,分别是目标设定、数据收集、数据分析、过程改进和持续改进。
下面将对这五个要素进行详细的介绍。
一、目标设定目标设定是制程品质管制的第一步,也是最关键的一步。
通过设定明确的目标,我们可以明确制程的要求和标准,以便于后续的数据收集和分析。
目标可以包括产品质量指标、制程能力要求等。
在设定目标时,我们需要考虑制程的特点和要求,合理地制定可实现的目标。
二、数据收集数据收集是制程品质管制的基础,通过收集制程过程中的各类数据,我们可以了解制程的状态和性能。
数据收集可以通过直接观测、抽样、检测等方式进行。
在数据收集过程中,需要确保数据的准确性和可靠性,避免数据的误差和偏差。
三、数据分析数据分析是制程品质管制的核心环节,通过对收集到的数据进行统计和分析,我们可以了解制程的变化规律和特点。
数据分析可以采用各种方法,如统计分析、图表分析、趋势分析等。
通过数据分析,我们可以找出制程中存在的问题和不稳定因素,并对其进行改进和调整。
四、过程改进过程改进是制程品质管制的重要环节,通过对制程中存在的问题和不稳定因素进行改进,我们可以提高制程的质量稳定性和一致性。
过程改进可以包括改进设备、改进工艺、改进操作等方面。
在过程改进过程中,需要确保改进措施的有效性和可行性,避免引入新的问题和风险。
五、持续改进持续改进是制程品质管制的基本原则,通过持续地对制程进行改进和优化,我们可以不断提高制程的质量水平和竞争力。
持续改进需要建立良好的反馈机制和改进体系,及时收集和分析制程的问题和改进需求。
在持续改进过程中,需要注重团队合作和知识共享,不断推动制程的改进和创新。
制程品质管制的五要素是目标设定、数据收集、数据分析、过程改进和持续改进。
通过合理地运用这五个要素,我们可以有效地进行制程品质管制,提高制程的质量稳定性和一致性,为产品的优化和升级奠定基础。
如何做好制程品质控制
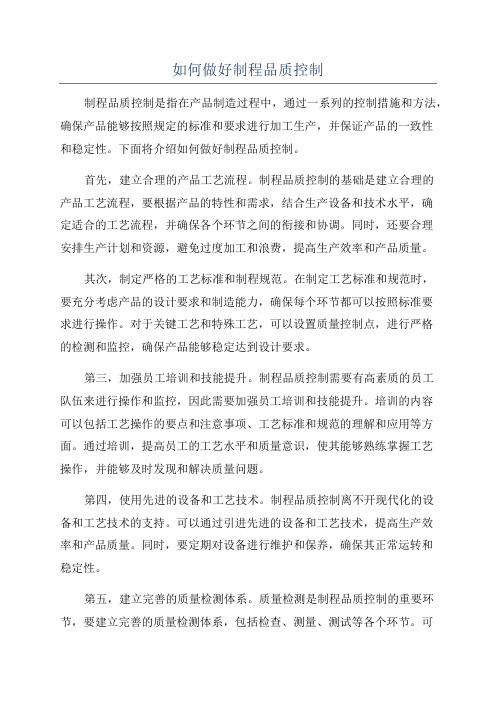
如何做好制程品质控制制程品质控制是指在产品制造过程中,通过一系列的控制措施和方法,确保产品能够按照规定的标准和要求进行加工生产,并保证产品的一致性和稳定性。
下面将介绍如何做好制程品质控制。
首先,建立合理的产品工艺流程。
制程品质控制的基础是建立合理的产品工艺流程,要根据产品的特性和需求,结合生产设备和技术水平,确定适合的工艺流程,并确保各个环节之间的衔接和协调。
同时,还要合理安排生产计划和资源,避免过度加工和浪费,提高生产效率和产品质量。
其次,制定严格的工艺标准和制程规范。
在制定工艺标准和规范时,要充分考虑产品的设计要求和制造能力,确保每个环节都可以按照标准要求进行操作。
对于关键工艺和特殊工艺,可以设置质量控制点,进行严格的检测和监控,确保产品能够稳定达到设计要求。
第三,加强员工培训和技能提升。
制程品质控制需要有高素质的员工队伍来进行操作和监控,因此需要加强员工培训和技能提升。
培训的内容可以包括工艺操作的要点和注意事项、工艺标准和规范的理解和应用等方面。
通过培训,提高员工的工艺水平和质量意识,使其能够熟练掌握工艺操作,并能够及时发现和解决质量问题。
第四,使用先进的设备和工艺技术。
制程品质控制离不开现代化的设备和工艺技术的支持。
可以通过引进先进的设备和工艺技术,提高生产效率和产品质量。
同时,要定期对设备进行维护和保养,确保其正常运转和稳定性。
第五,建立完善的质量检测体系。
质量检测是制程品质控制的重要环节,要建立完善的质量检测体系,包括检查、测量、测试等各个环节。
可以使用现代化的检测设备和方法,对产品进行严格的检测和评估,确保产品的质量达到标准要求。
第六,实施全员参与的品质管理。
制程品质控制是一项系统工程,需要全员参与和共同努力。
可以通过制定相关的品质目标和绩效评估指标,激励员工积极参与品质管理,形成全员质量意识和责任感。
同时,还要建立有效的沟通渠道和反馈机制,及时了解员工的意见和建议,进行问题分析和改进。
制程中调机品,不良品与良品分开隔离的管控措施
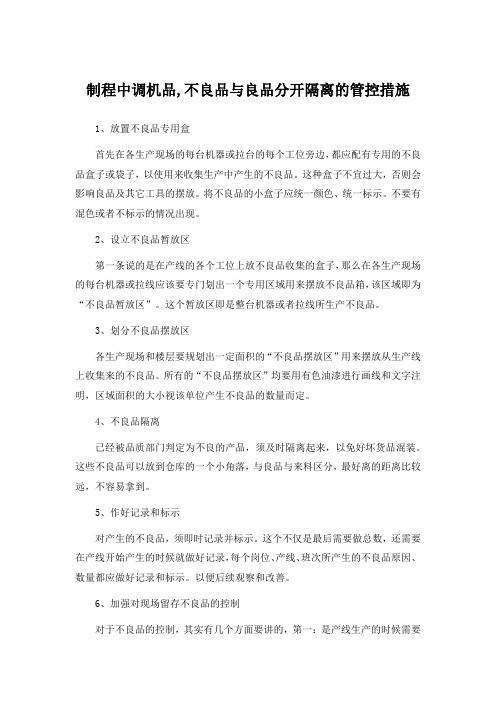
制程中调机品,不良品与良品分开隔离的管控措施1、放置不良品专用盒首先在各生产现场的每台机器或拉台的每个工位旁边,都应配有专用的不良品盒子或袋子,以使用来收集生产中产生的不良品。
这种盒子不宜过大,否则会影响良品及其它工具的摆放。
将不良品的小盒子应统一颜色、统一标示。
不要有混色或者不标示的情况出现。
2、设立不良品暂放区第一条说的是在产线的各个工位上放不良品收集的盒子,那么在各生产现场的每台机器或拉线应该要专门划出一个专用区域用来摆放不良品箱,该区域即为“不良品暂放区”。
这个暂放区即是整台机器或者拉线所生产不良品。
3、划分不良品摆放区各生产现场和楼层要规划出一定面积的“不良品摆放区”用来摆放从生产线上收集来的不良品。
所有的“不良品摆放区”均要用有色油漆进行画线和文字注明,区域面积的大小视该单位产生不良品的数量而定。
4、不良品隔离已经被品质部门判定为不良的产品,须及时隔离起来,以免好坏货品混装。
这些不良品可以放到仓库的一个小角落,与良品与来料区分,最好离的距离比较远,不容易拿到。
5、作好记录和标示对产生的不良品,须即时记录并标示。
这个不仅是最后需要做总数,还需要在产线开始产生的时候就做好记录,每个岗位、产线、班次所产生的不良品原因、数量都应做好记录和标示。
以便后续观察和改善。
6、加强对现场留存不良品的控制对于不良品的控制,其实有几个方面要讲的,第一:是产线生产的时候需要做到控制,第二:是因搬运过程中所导致的。
第三、在仓库存放的时候所产生的。
对于以上所产生的不良,应该做好控制工作。
不可流出或再次回产线。
7、保证不良品在手动过程中标志物的维护标示可能会被移动、或者损坏。
因此要做好不良品手动过程中标志物的维护。
若标志物没有了,很容易混淆。
这也是5S中严格要求做到的,如果是有做体系的公司,这一项也是必做的项目。
8、明确不良品的处置部门和权限、有了明确的责任,必然事情处理急时。
不良品的产生不只有生产线上才会制造出来,也可能是开发部门设计不合理,或者仓库搬运时所产生的不良,或者检验部门在检查过程中造成的。
制程品质控制制度

制程品质控制制度摘要制程品质控制制度在现代制造业中扮演着至关重要的角色。
它是确保产品符合规格要求、优化生产过程、提高生产效率和降低成本的关键之一。
本文将探讨制程品质控制制度的重要性、主要内容、实施步骤以及效益。
一、制程品质控制制度的重要性制程品质控制制度是组织内部规范、定量的控制制度,通过严格执行,可以有效地降低产品变异性,提高产品品质一致性,确保产品符合客户需求。
同时,制程品质控制制度还可以帮助企业不断改进生产工艺,提高生产效率和降低生产成本。
二、制程品质控制制度的主要内容1.制程品质控制计划:确定控制的范围、目标和方法。
2.控制参数的设定:确定影响产品质量的关键参数。
3.制程控制图的绘制:监控制程参数的变化趋势。
4.控制限的设定:设定上下限,及时发现制程异常。
5.制程改进措施:对不良制程进行改进,确保品质可控。
三、制程品质控制制度的实施步骤1.制程分析:对生产过程进行分析,确定关键控制点。
2.制程测量:测量关键参数,建立数据集合。
3.制程监控:利用制程控制图监控制程状态。
4.制程改进:根据监控结果,采取改进措施。
5.制程稳定:确保制程持续稳定,达到预期效果。
四、制程品质控制制度的效益1.降低制程变异性:提高产品品质一致性。
2.提高生产效率:减少废品,加快生产速度。
3.降低生产成本:通过制程改进,减少废品和报废率。
4.提升客户满意度:确保产品符合客户需求,提升品牌形象。
结论制程品质控制制度是现代制造业中不可或缺的重要环节,它通过规范和优化生产过程,实现产品质量的持续提升和生产效率的不断改进。
企业应该重视制程品质控制制度的建立和执行,将其作为提高竞争力、降低成本、提升客户满意度的重要手段。
- 1、下载文档前请自行甄别文档内容的完整性,平台不提供额外的编辑、内容补充、找答案等附加服务。
- 2、"仅部分预览"的文档,不可在线预览部分如存在完整性等问题,可反馈申请退款(可完整预览的文档不适用该条件!)。
- 3、如文档侵犯您的权益,请联系客服反馈,我们会尽快为您处理(人工客服工作时间:9:00-18:30)。
d.當制程中全檢員在查貨時或代班在抽檢成品時發現重缺失不良時,應告知班長對相應之QC人員進行教育訓練,并將此批貨進行重工。對制程中常見的不良及品保或客戶有投訴過的不良班長應負責制作瑕疵樣品,懸挂于拉頭,以利后續生產時作教育訓練用。
b.當制程中作業員有發現不良而無法判定有詢問班長或代班時,班長或代班應引起重視,如屬突發性、偶發性不良,也應按上面的方法,召集本班所有人員進行宣導,引起全員重視。對制程中各工位之良品與不良品要進行明顯的區分,嚴禁將不良品與良品混放在台面上,需放在指定的區域內,良品放在良品盒內,不良品放在不良品盒內。
2.首件:為確定物料的品質狀況及機器設備的運行狀況是否良好,代班需對首件的結果進行跟蹤,
確認OK后,再告知班長排線生產,當機器因不穩定而導致產品品質變異較大時,代班需對此產品多次制作首件,以確保產品品質。
3.機器: a每個操作員均需熟練掌握機器的基本操作方法,并需經過班長、組長、課長、培訓考核
合格后方可正式上崗操作,以防因人員不熟練而產生大批量不良。
7.重視查核的動作:班長及代班工作職責不是在拉線上做工位,而是要不斷的巡拉,去發現問題,處理問題,查核各工位是否有按照規定的要求去做,對車間的各種規定及制程中出現的品質異常擬定的改善對策等都需要進行查核并了解其成效。
d.當機器因異常需修機時,應將機台旁所有的良品全部移至良,修機產生之產品需安排專人進行處理。
4.制程: a.因品質的好壞是與制程息息相關,所以在制程中應嚴格把好質量關,班長一定要按照作業指導書上的工藝流程進行編排,不可自行更改流程。要求各工位落實執行自檢之動作,班長及代班應隨時對各工位之產出品予以查看,當有發現重缺失不良及其它異常時,應立即召集本班人員開會講解此不良,防止不良流入下一工位。
進行原因分析,并擬定改善對策,對當天生產的產品要重點宣導品質管控重點。
b.對品保要求返工的產品班長在取得不良樣品的第一時間內應召集相關責任人進行檢討,分析原因,后續生產如何管控,并安排人員進行重工。其相關責任人應在三天內提交改善對策。
c.在新產品進行試做與量產前,應集合本班人員召開產前會義,主要對新產品的工藝流程,外觀、尺寸、瑕疵等方面進行講解,對員工進行培訓。
文件編碼
廣晉電子廠
發行日期
2004/11/24
適用范圍
組立課
組立課制程品質管控注意事項
版本
AO
擬稿單位
組立課
頁次
1-2
核准
審核
擬稿
王躍杰
一、目的:
為降低制程品質不良,以提升產品品質效率
二、范圍:
組立課各班
三、內容:
1.物料:代班對本班產線之物料需不定時進行抽檢,發現不良,立即告知班長進行處理,安排人員挑選,并將不良品標示區隔,防止員工誤用而產生不良,當來料不良有超過不良目標3%時,應立即對不良物料予以區分、標示或派專人處理,且開立異常單呈報,并召集本班人員開會對不良現象予以講解,在生產中作重點管制。
b機器的日常保養工作要落實執行,操作者除了需保持機台干淨整潔外,還需定期給機器加防鏽油、潤化劑等。使機台能夠正常運行。
..c操作員除了每兩小時對產品進行尺寸的量測填寫一次首件檢驗表外,還需對本工位常見不良進行自主檢查,以防因機器異常而產生大批量不良。當有發現不良時,除了通知生技人員修機外還應立即告知班長召集QC、全檢進行宣導,防止此不良外流。
e.制程不良超過0.3%時,應立即就問題點進行分析、改善。并及時呈報上級領導。
5.重視“5S”工作:因為好的品質來源于干淨整潔的工作場所,所以要嚴格遵守車間5S管理要求,落實整理整頓的工作,認真做到對拉線所有物品都有標示定位,消除尋找的浪費,防止員工因誤用、誤送而產生不良。
6.重視教育訓練:a.班長可利用早會的時間對員工進行品質觀念的灌輸,對前一天發生的品質異常