某型火箭炮液压泄漏的检测与控制
液压油缸泄露实验标准

公称压力×2.5%
2、活塞式单作用油缸最低启动压力不得大于下表:
公称压力
活塞密封形式
活塞杆密封形式
除V型外
V型
≤16MPa
V型
0.5
0.75
除V型外
0.35
0.5
>16MPa
V型
公称压力×3.5%
公称压力×9%
除V型外
公称压力×3.4%
公称压力×6%
3、柱塞式单作用油缸最低启动压力不得大于下表:
液压油缸泄漏实验检测标准
1、双作用油缸最低启动压力不得大于下表:
公称压力
活塞密封形式
活塞杆密封形式
除V型外
V型
≤16MPa
V型
0.5
0.75
O、U、Y、X、组合密封
0.3
0.45
活塞环
0.1
0.15
>16MPa
V型
公称压力×6%
公称压力×9%
O、U、Y、X、组合密封
公称压力×4%
公称压力×6%
活塞环
内泄漏量mL/min
缸内径D mm
内泄漏量mL/min
40
0.03
125
0.28
50
0.05
140
0.30
63
0.08
160
0.50
80
0.13
180
0.63
90
0.15
200
0.70
100
0.20
220
1.00
110
0.22
250
1.10
注:使用组合密封时,允许内泄漏量为规定值的2倍
6、单作用油缸内泄漏量不得大于:
航天产品常用泄漏检测方法

书山有路勤为径,学海无涯苦作舟
航天产品常用泄漏检测方法
介绍了航天产品研制过程中的常用泄漏检测方法。
按照检漏的原理,将航天产品泄漏检测方法归纳为氦质谱检漏法、压力变化检漏法和原工质检漏法三大类,每一大类根据测量系统结构的不同又分为若干小类。
详细介绍了每种泄漏检测方法的测量原理,以及在航天产品中的应用。
未来航天产品泄漏检测技术的发展趋势,是不同密封结构检漏技术、极小漏率检漏技术和原工质泄漏检测技术等。
1、引言
航天产品研制过程涉及到大量有密封性能要求的组件或部件、甚至整机
产品,如载人航天器的密封舱、卫星推进剂燃料贮箱、星载一次电源用氢- 镍蓄电池、卫星通信用天线、记时用频标光源以及其它各种星载仪器等。
航天产品密封性能直接关系到航天器的发射成功率和在轨使用寿命。
泄漏检测贯穿航天产品设计、制造、关键工艺点控制、部件性能、整星出场、发射及运行全过程,是确保航天产品密封性能的重要手段。
航天领域使用的泄漏检测方法多种多样,从检测精度上可以分为粗检和
细检两种,粗检主要用于较大漏孔的检测工作,适用于产品研制过程中的密封性能定性分析。
细检主要用于微小漏孔的测量和定位,适用于产品密封性能的定量检测,主要介绍细检漏方法。
细检从测量原理上可以分为氦质谱检漏法、压力变化检漏法和原工质检漏法。
在检测方法选择上需要从被检测对象的密封性能指标要求、体积大小和结构复杂性、检测工作安全性、检测成本等方面综合考虑。
真空技术网(chvcuum)的专家认为氦质谱检漏方法在航天产品的泄漏检测工作中应优先选择。
液压系统中液体泄漏的检测与控制

液压系统中液体泄漏的检测与控制液压系统是一种广泛应用于工业领域的动力传动和控制系统,它通过液体在封闭的管路中传递力量来实现机械的运动。
然而,液压系统中常常会出现液体泄漏的情况,这不仅导致能量的浪费,还可能引发系统故障和环境污染。
因此,检测和控制液体泄漏成为液压系统运行中的一项重要任务。
液体泄漏的检测方法有多种,其中最常用的方法是通过观察液体泄漏现象来判断。
当液压系统中存在泄漏时,液体会从管路连接点、密封件处或者管路破损处泄漏出来,形成一滴滴或流淌的液体。
在检测过程中,我们可以检查管路连接点是否松动或存在渗漏痕迹,观察密封件是否存在磨损或变形,以及检查管路是否存在明显的破损等。
此外,还可以借助红外热像仪来检测液体泄漏,因为液体泄漏会引起局部热量变化,红外热像仪可以准确地检测出这些变化并进行定位。
除了直接观察外,液体泄漏的检测还可以借助仪器设备进行。
例如,压力传感器可以用来检测液压系统中的压力变化,当液体泄漏时,压力传感器会通过监测管路压力的下降来判断是否存在泄漏。
另外,流量计也是一种常用的液体泄漏检测设备,它可以通过测量液体在管路中的流速来间接判断是否存在泄漏。
此外,还有一些更高级的泄漏检测技术,如声学泄漏检测技术和光学泄漏检测技术,它们可以通过对液体泄漏产生的声音或光信号进行分析来判断泄漏的位置和程度。
液体泄漏的控制是液压系统中的另一个关键问题。
一旦液体泄漏发生,首先需要迅速维修或更换泄漏点的密封件或管路,以避免进一步的泄漏。
此外,可以采取一些预防措施来降低液体泄漏的发生概率。
例如,定期检查和维护液压系统,确保管路连接牢固,密封件完好,并且注意避免管路的磨损和破损。
此外,合适的液压油的选择和使用也是防止液体泄漏的重要因素。
选择合适的液压油可以提高密封件的工作寿命,并减少泄漏的风险。
液体泄漏的发生不仅对液压系统的正常运行造成影响,还可能对环境产生不良影响。
因此,在设计和使用液压系统时,需要充分考虑减少液体泄漏的措施。
检测与监管油气管道泄漏的方法

检测与监管油气管道泄漏的方法油气管道泄漏是一种非常严重的环境问题,如果不能及时发现并处理,那么会对人类的生活和环境造成不可逆转的损害。
为了预防和解决这种问题,需要有一些专业的检测和监管方法。
下面,我们就来探讨一下这方面的内容。
一、泄漏的检测方法在检测油气管道泄漏的时候,需要采用一些专业的方法,通过分析、测试和检测来判断管道是否存在泄漏问题。
现在常见的检测方法主要有以下几种。
1、气体检测法气体检测法是一种非常常见的检测方法,它可以通过检测气体成分来判断管道是否泄漏。
在使用这种方法的时候,需要在查漏的地方放置一些探测器,然后对管道中的气体进行测试和分析。
如果管道中的气体呈现出了异常的成分,那么就可以判断管道存在泄漏问题。
2、超声波检测法超声波检测法是一种高精度、高敏感度的检测方法。
它可以通过检测管道泄漏时产生的音波来判断管道是否存在泄漏问题。
这种方法不但可以检测常温下的管道泄漏,还可以检测高温状态下的泄漏问题。
同时,它的检测效果也比较可靠。
3、红外线检测法红外线检测法主要是通过检测管道泄漏时产生的热量变化来判断管道是否存在泄漏问题。
它利用了红外线热像仪来检测管道的温度变化,如果发现温度变化过大,那么就可以判断管道存在泄漏问题。
这种方法的优点是非侵入性强,检测效果也比较可靠。
二、泄漏的监管方法除了检测泄漏之外,还需要有一些专业的监管方法。
这些方法主要是通过在管道中安装一些监测装置来实现的,通过这些装置可以对管道进行全方位的监控,及时发现并处理管道泄漏问题。
1、压力监测系统压力监测系统是一种非常常见的监管方法。
它主要通过安装压力传感器等监测装置来实现对管道压力的实时监控,当管道中的压力发生异常的变化时,系统就会自动报警,并提示工作人员对管道进行检修和维护。
2、温度监测系统温度监测系统也是一种比较常用的监管方法。
它主要通过安装温度传感器等监测装置,对管道中的温度参数进行实时监控。
当管道中温度异常变化时,系统就会自动报警,提示工作人员注意管道的安全问题。
某火箭炮调炮过程中液压系统故障仿真研究

2018年9月第46卷第17期机床与液压MACHINETOOL&HYDRAULICSSep 2018Vol 46No 17DOI:10.3969/j issn 1001-3881 2018 17 040收稿日期:2017-04-14作者简介:马万鹏(1992 ),男,硕士研究生,主要从事武器系统仿真与虚拟样机技术研究㊂E-mail:mawanpengyjs@163 com㊂某火箭炮调炮过程中液压系统故障仿真研究马万鹏,马吉胜,曹立军,邓世杰(军械工程学院火炮工程系,河北石家庄050000)摘要:为解决某火箭炮在调炮过程中,液压系统故障诊断样本较少㊁故障知识获取较难等问题,以某火箭炮高低随动液压系统为研究对象,利用ADAMS与EASY5软件建立其虚拟样机模型,并通过高低调炮过程的仿真结果与实测数据对比,完成模型准确度校核㊂在此基础上,分析液压故障原理,通过修改模型参数或等效建模,完成液压泵泄漏㊁油液夹带空气以及过滤器堵塞等故障的注入,并仿真计算了不同故障情况对系统性能的影响,仿真结果符合理论分析㊂因此可以通过故障仿真获取故障知识和样本,为液压系统故障诊断提供参考,对装备的维修保障具有指导意义㊂关键词:随动系统;液压故障;联合仿真;故障仿真中图分类号:TP391 9㊀㊀文献标志码:A㊀㊀文章编号:1001-3881(2018)17-180-5ResearchonFaultSimulationofHydraulicSysteminaRocketGunAdjustmentProcessMAWanpeng,MAJisheng,CAOLijun,DENGShijie(ArtilleryEngineeringDepartment,OrdnanceEngineeringCollege,ShijiazhuangHebei050000,China)Abstract:Inordertosolvetheproblemthatthefaultdiagnosisofarocketlauncherhydraulicsystemwaslessandthefaultknowl⁃edgewasdifficulttoget,therocketlauncherhydraulicsystemwasusedastheresearchobject,ADAMSandEASY5softwarewereusedtobuildthevirtualprototypemodel,theaccuracyofthemodelwascheckedbycomparingthesimulationresultsandtestingresults.Onthebasis,theprincipleofhydraulicfailurewasanalyzed,andthefailuremodesofhydraulicpumpleakage,oilentrainedairandfiltercloggingwerecompletedbymodifyingthemodelparametersorequivalentmodeling.Theeffectsofdifferentfaultconditionsontheperformanceofthesystemwerecalculated.Thesimulationresultsareinagreementwiththetheoreticalanalysis.Theresultsshowthatfaultknowledgeandsamplescanbeobtainedthroughfaultsimulation,whichcanprovidereferenceforhydraulicsystemfaultdiag⁃nosisandhaveguidingsignificanceformaintenanceoftheequipment.Keywords:Servosystem;Hydraulicfault;Jointsimulation;Faultsimulation0㊀前言调炮过程是由随动系统控制并完成的,调炮的范围㊁速度以及精度是火箭炮十分重要的战斗性能指标,随动系统性能的优劣直接决定了火箭炮射击密集度与准确度㊂随动系统由机械装置㊁液压回路和控制单元3个子系统组成㊂在装备实际使用中发现,液压系统故障具有形式隐蔽㊁发生率高㊁危害性强㊁维修困难等特点,因而获取其故障知识和识别其故障特征是液压系统故障研究的重点和难点㊂若仅凭经验和物理实验建立有效的故障知识库,必然会消耗大量的人力㊁物力㊁财力,增加了故障识别诊断与维修保障的难度㊂所以为了减少故障研究成本,提高可靠性,可以利用虚拟样机进行故障仿真,得到各种故障模式下系统的动态特性,分析故障特征获取故障知识㊂文献[1]中分析了某火箭炮高低随动系统的数学模型㊁主要故障以及可靠性问题;文献[2]中以飞机起落架收放系统为研究对象,利用液压仿真软件AMESim进行系统建模和故障仿真,其研究方法较为标准,可以应用到其他工程实践问题;文献[3]中以某型发射车起落系统为研究对象,建立液压系统故障模型,确定系统异常表现与故障之间关系;文献[4]中利用键合图对液压元件进行原理分析㊁搭建模型与故障数值仿真,实现故障探测和诊断㊂前人对某型火箭炮的结构原理有了较为深入的研究,对各类液压工程系统实际故障的原理分析也十分具体,积累了大量的故障仿真经验和故障样本㊂不过文中所研究的某型火箭炮是较新型的武器装备,在其完整的虚拟样机建模和故障仿真研究方面还不够深入,而且调炮过程是机电液全系统作动过程,单独考虑故障对液压系统影响显然无法全面准确地反映故障特征和对整体系统的影响㊂所以文中以火箭炮高低随动系统为研究对象,建立包括机械㊁液压和控制子系统在内的机电液耦合全系统虚拟样机模型,在校核模型准确度的基础上,对液压子系统采用等效和模型化方式[5-6]完成故障注入,分析液压故障在火箭炮调炮过程中对系统的影响以及相关参数的变化规律,获取了液压系统故障知识与特征,为后续故障诊断研究提供参考依据,对实际装备的故障排除与维修保障具有指导意义㊂1 高低随动调炮原理与常见故障1 1㊀高低随动系统组成与工作原理高低随动系统根据射击诸元快速准确地确定火箭炮射角,进行自动调炮,是提高火箭炮操瞄自动化水平的关键部分㊂系统包括机械㊁液压和控制3个子系统,其中机械装置主要是高低机㊁平衡机㊁起落架体㊁定向器束㊁夹板组等;液压系统包括油箱㊁过滤器㊁伺服泵总成㊁手动泵㊁控制阀组㊁锁紧阀组以及蓄能器和高低机液压筒;控制系统有火控计算机㊁数字控制器㊁速度调节器㊁旋转变压器㊁功率放大器㊁PID控制器㊁数模转换器等㊂高低随动系统原理如图1所示㊂图1㊀高低随动系统原理图高低随动调炮时通过RS232⁃C串行通信接口接收火控计算机指令,自动计算出实际俯仰位置与射击诸元之间误差,通过功率放大器驱动电液伺服阀进而控制双杆液压缸,改变柱塞泵斜盘角度与方向,控制伺服泵输出液压油的流量与方向,实现火箭炮高精度俯仰自动调炮㊂通过随动系统调炮的原理,可以看出该系统采用的是泵控位置伺服闭环系统,与阀控伺服系统相比,该系统更为大型㊁更为复杂,适用于对大功率㊁大负载的控制㊂根据系统结构原理,对系统进行数学建模㊂首先根据流量特性,列写泵控缸流量连续性方程:φkbωb-λp=Adxdt+VEdpdt(1)式中:φ为柱塞泵斜盘转角;kb为柱塞泵排量梯度;ωb为泵转速;λ为泵泄漏系数;A为高低机液压筒有效面积;x为活塞杆伸长量;V为液压腔室容积;E为弹性模量㊂因为射击诸元和系统控制信号的输入量为高低射角,并非活塞杆位移量,所以令:dxdt=K(θ)dθdt(2)式中:θ为高低角;K(θ)为活塞杆线位移与起落架角位移转换系数㊂再根据系统动力学和系统几何关系,列写高低机与负载的力矩平衡方程为:Jd2θdt2+Bdθdt+Gθ+ML=pAl(θ)(3)式中:J为转动惯量;B为阻尼系数;G为弹性刚度;ML为不平衡力矩;l(θ)为高低机作用力臂㊂将公式(2)代入公式(1)后,分别对其和公式(3)进行拉普拉斯变换,之后消除中间量p,就可得到高低位置随动系统的传递函数:θ(s)=φkbωbAl(θ)-VEs+λæèçöø÷ML(s)VJEs3+VBE+CJæèçöø÷s2+VGE+CB+A2K(θ)l(θ)éëêêùûúús+GC(4)以上随动系统传递函数和数学模型的建立,为后续虚拟样机建模和故障仿真分析提供了严谨的理论支撑[7]㊂1 2㊀液压子系统常见故障分析某型火箭炮高低调炮过程主要的故障现象是调炮过程缓慢㊁机构运动不平稳㊁调炮出现爬行㊁无法调到指定射角等㊂虽然这些故障形式和症状比较宏观,但是由于液压系统的复杂性,一个故障形式会对应一系列故障因素,因此以液压系统为研究对象,总结装备使用过程中产生的实际故障,采用故障树分析法对上述故障进行分析㊂其故障树分析图如图2所示㊂图2㊀液压系统故障树分析其中液压油质故障会导致液压油特性不佳,降低系统效能;伺服泵故障会使系统动力输入受损,降低系统供压,甚至无法实现泵控缸伺服作动;锁紧阀组故障会直接导致系统无法调炮或者作动不平稳;蓄能器故障会降低平衡负载的能力,影响调炮平稳性;高低机泄漏故障会导致调炮速度达不到要求指标㊂通过对液压系统故障树分析可以看出,液压系统故障隐蔽性高㊁危害性强㊂为了充分获取故障样本和知识,采㊃181㊃第17期马万鹏等:某火箭炮调炮过程中液压系统故障仿真研究㊀㊀㊀用建立系统虚拟样机模型的方法,进行故障仿真模拟㊂2㊀高低随动系统虚拟样机建模与校核2 1㊀基于ADAMS-EASY5的机电液一体化建模为更全面准确研究液压故障对全系统性能的影响,使用ADAMS-EASY5软件实现机电液一体化虚拟样机建模㊂首先通过三维实体建模软件,按照装备实际尺寸绘制高低随动机构的实体模型,将其导入ADAMS软件中定义模型材料㊁重力方向,自动获取各零部件质心位置㊁质量以及转动惯量,由拓扑关系添加零部件间约束,实现随动机械子系统建模㊂其次根据随动调炮液压系统原理图,在EASY5平台上使用高级液压库中规范元件模型和原理模型,搭建液压子系统模型,设置相关元件的参数与系统环境条件㊂根据随动调炮控制原理以及高低伺服系统传递函数,在EASY5中建立控制子系统模型,并通过整定PID控制器参数实现快速㊁准确㊁稳定响应㊂最后根据系统机电液参数耦合关系(如图3所示),在ADAMS和EASY5中建立输入输出变量,利用软件接口和拓展库AD模块使模型互联,最终建立高低随动系统机电液一体化虚拟样机模型㊂图3㊀随动系统机电液参数耦合关系2 2㊀模型准确度校核基于以上建立的虚拟样机模型,只有对其进行准确度的校核与验证(Verification&Validation),才能确认模型具有可信度,在此基础上进行的故障仿真分析才有研究价值与实际意义㊂对于复杂系统仿真模型验证方法的研究已较为深入,最直接有效的校核方式是将系统动力学响应的仿真试验结果与实际测试结果进行对比,用结果的一致性对模型的可信度和准确度做出评价㊂对于高低随动系统模型的校核,以完成调炮的作动时间和调炮过程中最大角速度为对比项,其中由于实际装备测试具有个体差异以及偶然误差,所以对技术状态良好的装备系统进行多次调炮测试,得到多角度调炮时间与最大角速度平均值后,再与仿真结果进行对比,如表1所示㊂表1㊀仿真与实测数据对比射角/mil㊀㊀㊀时间㊀㊀㊀㊀㊀㊀最大角速度㊀㊀㊀实测平均值/s仿真值/s误差/%实测平均值/(mil㊃s-1)仿真值/(mil㊃s-1)误差/%3006.946.634.546.6448.433.760012.4512.152.555.7957.573.190017.2516.564.270.0673.444.6备注:360ʎ等价于6000mil㊂可以看到:仿真结果与实测结果很好地吻合,误差均低于5%㊂说明所建立的随动系统虚拟样机模型具有较高的准确度和可信度,仿真结果具有实际意义和研究价值,该模型可以成为故障研究的仿真平台㊂3㊀液压系统故障仿真分析故障仿真是对实际系统进行原理分析,利用计算机仿真软件在数学模型的基础上建立虚拟样机模型,经过数值仿真和计算求解,重现虚拟故障的过程㊂研究的难点在于对不同故障的注入是否准确有效,故采用等效和模型化的方法注入故障:(1)分析故障模式找到故障内部的等效关系,建立等效故障模型,实现对某类故障的等效注入;(2)分析液压系统数学模型,确定相关参数对系统的影响,对相应元件参数变量化处理,完成故障注入㊂基于前文对液压系统原理和故障树的分析,以及装备实际使用和维修情况,借助所建立的高低随动系统虚拟样机模型,主要针对伺服泵泄漏㊁液压油夹杂空气㊁过滤器堵塞3个故障进行仿真计算,分析故障对调炮位移㊁速度和系统压力㊁流量等关键参数的影响,确定故障特征和原因㊂3 1㊀伺服泵泄漏故障伺服泵作为液压系统动力元件,其容积效率与流量之间关系为:ηV=Q0Qe=Qe-QxQe(5)式中:ηV为容积效率;Qe为额定流量;Q0为实际流量;Qx为泄漏量㊂由于各零件较长时间运行产生的磨损,液压泵会出现油液泄漏,即Qx值增大,减少泵实际出口流量,降低了泵容积效率㊂对此故障采用等效法实现故障注入:在液压子系统模型中,将含孔分流器(ST模块)串接至伺服泵与过滤器之间,通过设定分流器泄漏流口孔径大小来等效泵发生不同程度的泄漏故障㊂等效孔径分别设定为0㊁0 5㊁0 7㊁1mm,系统模型其他参数不变,分别进行600mil高低调炮仿真模拟,计算出调炮角位移㊁角速度㊁泵出口压力以及流量随时间变化曲线,分别如图4㊁5㊁6㊁7所示㊂图4㊀泵不同程度泄漏时调炮角位移曲线㊀㊀图5㊀泵不同程度泄漏时调炮角速度曲线㊃281㊃机床与液压第46卷图6㊀泵不同程度泄漏时出口压力曲线㊀㊀图7㊀泵不同程度泄漏时出口流量曲线可以看出:随着流口孔径的增大,即泵泄漏量增大,泵出口压力与流量输出逐渐减小,直接导致了调炮速度降低,调炮到位时间延长㊂仿真结果与理论分析十分相符㊂3 2㊀液压油夹杂空气故障液压油是系统动力与能量的传递介质,由于泵转速较高㊁系统油管较长等原因,泵在运行时吸油不完全,使空气混入油液产生 气穴 ,降低了液压油体积弹性模量,导致管路中油液流动不稳定,作动元件会产生振动或者爬行,系统的流量与压力也会出现不同程度的振荡与冲击㊂油液中夹杂空气对系统性能与寿命有直接影响㊂对此故障采用模型化方式完成注入:在液压子系统模型中,通过修改全局环境模块中的油液含气比这一参数实现故障模拟㊂设定参数分别为0 1%㊁1%㊁10%,系统模型其他参数不变,分别进行600mil高低调炮仿真模拟,计算出调炮角位移㊁角速度㊁泵出口压力以及流量随时间变化曲线,分别如图8㊁9㊁10㊁11所示㊂可以看到:油液含气量在0 1%和1%时,系统动力学响应以及泵出口压力与流量差异均不明显,均满足装备性能设计指标;但是在含气量为10%时,调炮到位时间明显增长,角速度增速出现迟滞,在调炮初始和停止阶段泵出口压力和流量产生了较长时间的波动㊂所以油液含气量较大,对系统动力学和液压特性都有严重的影响,使装备无法达到设计性能标准,故障仿真计算结果与故障理论分析结果一致㊂图8㊀不同含气量调炮位移曲线㊀㊀㊀㊀㊀图9㊀不同含气量调炮角速度曲线图10㊀不同含气量泵出口压力曲线㊀㊀图11㊀不同含气量泵出口流量曲线3 3㊀过滤器堵塞故障液压系统使用过程中,由于液压油污染造成的系统故障十分常见㊂因此,需要安装过滤器滤掉液压油杂质,防止油液污染,保障装备无故障运行㊂过滤器在液压系统中为阻性元件,当加压的油液通过重叠小孔通路构成的屏蔽层时,污染颗粒则被阻留在屏蔽层内,从而实现排除污染物的任务㊂同时油液通过过滤器时必然将产生压力降,其数学表达式为:Δp=μqαA(6)式中:μ为油液动力黏度;q为过滤器通流能力;α为过滤器单位面积通流能力;A为有效过滤面积㊂在较长时间的使用后,污染颗粒会使小孔通路堵塞,降低有效过滤面积,进而过滤器出入两端的压力降会增大,降低了系统工作效能[8]㊂对此故障采用模型化方式完成注入:在液压系统模型中,通过修改过滤器通流孔径这一参数模拟堵塞故障㊂设定参数分别为6㊁3㊁2mm,系统模型其他参数不变,分别进行600mil高低调炮仿真模拟,计算出过滤器入口与出口压力随时间变化曲线如图12㊁13所示㊂可发现:过滤器未堵塞(即通流孔径6mm)和堵塞(通流孔径3㊁2mm)比较,过滤器出口压力基本未产生差异,说明过滤器堵塞对调炮速度和位移无明显影响;但是过滤器入口压力随着通流孔径的减小㊁有效面积的降低而不断增大㊂在通流孔径分别为6㊁3㊁2mm时,过滤器产生的压力降值分别为0 04㊁0 12㊁0 36MPa,压降最大增加9倍,大大增加了系统的液压阻力,从而使泵出口压力增大以克服额外的阻力,系统效能降低,故障仿真结果与理论分析结果较吻合㊂图12㊀过滤器不同程度堵塞时入口压力曲线㊀㊀图13㊀过滤器不同程度堵塞时出口压力曲线㊃381㊃第17期马万鹏等:某火箭炮调炮过程中液压系统故障仿真研究㊀㊀㊀4㊀结论(1)通过分析某型火箭炮高低随动系统组成和工作原理,利用ADAMS-EASY5软件建立全系统机电液耦合虚拟样机模型,将仿真正常调炮过程与装备实测对比,校核并验证了模型准确度㊂(2)对液压子系统进行故障树分析,采用等效和模型化的方法向所建模型注入典型故障,对伺服泵泄漏㊁油液夹杂空气和过滤器堵塞3个常见故障进行理论分析和仿真模拟㊂结果表明:伺服泵泄漏降低了容积效率,延长了调炮到位时间,降低了系统流量和压力;油液含气量大导致压力和流量产生剧烈波动;过滤器堵塞大幅增加了液阻和压力损失,降低系统效能㊂仿真结果与理论分析及实际反映情况较一致㊂(3)利用虚拟样机模型进行故障仿真,获取了液压系统故障知识与特征,为进一步故障诊断研究与知识库建立提供参考,对实际装备的维修保障工作具有指导意义㊂参考文献:[1]冯广斌.远程火箭炮武器系统可靠性研究[D].南京:南京理工大学,2004:59-63.[2]胡晓青,马存宝,和麟,等.飞机起落架收放系统建模与故障仿真[J].计算机工程与科学,2016,38(6):1286-1293.HUXQ,MACB,HEL,etal.ModelingandFaultSimula⁃tionoftheLandingGearExtensionandRetractionSystem[J].ComputerEngineeringandScience,2016,38(6):1286-1293.[3]李田科,李建华,于仕财,等.基于AMESim的发射车液压系统故障仿真研究[J].机床与液压,2013,41(5):156-160.LITK,LIJH,YUSC,etal.FaultSimulationoftheLaunchVehicleHydraulicSystemBasedonAMESim[J].MachineTool&Hydraulics,2013,41(5):156-160.[4]ATHANASATOSP,COSTOPOULOST.ProactiveFaultFandingina4/3-wayDirectionControlValveofaHighPressureHydraulicSystemUsingtheBondGraphMethodwithDigitalSimulation[J].MechanismandMachineTheo⁃ry,2012,50:64-89.[5]彭国朋,黄海涛.雷达天线车液压故障分析及其动态仿真[J].火控雷达技术,2009,38(2):43-47.PENGGP,HUANGHT.HydraulicFaultAnalysisofaRadarAntennaVehicleandItsDynamicSimulation[J].FireControlRadarTechnology,2009,38(2):43-47.[6]李伟.供输弹系统机电液耦合动力学及动作可靠性仿真研究[D].石家庄:军械工程学院,2010:84-85.[7]高强.远程多管火箭炮电液位置伺服系统辨识与控制策略研究[D].南京:南京理工大学,2008:20-26.[8]王森.调距浆液压系统故障仿真与诊断技术研究[D].哈尔滨:哈尔滨工程大学,2013:47-49.(责任编辑:张艳君)(上接第176页)[6]李有平,陈启卷.基于灰色理论与不变矩的水电机组轴心轨迹自动识别[J].电力系统自动化,2001,25(9):19-22.LIYP,CHENQJ.AutomaticIdentificationofAxisOrbitofHydroelectricGeneratingsetBasedonGreyTheoryandMomentInvariants[J].AutomationofElectricPowerSys⁃tems,2001,25(9):19-22.[7]丁克北.基于图像处理方法的轴心轨迹识别方法[J].风机技术,2006(5):35-37.DINGKB.AMethodtoIdentifyAxisPathBasedonImageProcessingMethod[J].Compressor,Blower&FanTechnol⁃ogy,2006(5):35-27.[8]VOLDH,LEURIDANH.HighResolutionOrderTrackingatExtremeSlewRates,UsingKalmanTrackingFilters[R].SAEPaperNumber931288,1993.[9]VOLDH,MAINSM,BLOUGHJ.TheoreticalFoundationsforHighPerformanceOrderTrackingwiththeVold-Kal⁃manTrackingFilter[R].SAEPaperNumber972007,1997.[10]傅炜娜.基于Vold-Kalman跟踪滤波的旋转机械阶比分析方法与研究[D].重庆:重庆大学,2010.[11]史东锋,屈梁生.轴心轨迹定量特征提取技术在回转机械诊断中的应用[J].化工机械,1999(1):27-30.SHIDF,QULS.ApplicationofExtractionTechnologyoftheQuantitativeCharacteristicsofanAxisCenterTrailintheDiagnosisofRotatingMachinery[J].ChemicalEngi⁃neering&Machinery,1999(1):27-30.[12]HUM.VisualPatternRecognitionbyMomentInvariants[J].IRETransactionsonInformationTheory,1962,8(2):179-187.[13]马朝永,黄攀,胥永刚,等.基于MDS和神经网络的滚动轴承故障诊断方法[J].噪声与振动控制,2017,37(4):171-174.MACY,HUANGP,XUYG,etal.RollingBearingFaultDiagnosisMethodBasedonMDSandNeuralNetwork[J].NoiseandVibrationControl,2017,37(4):171-174.(责任编辑:张艳君)㊃481㊃机床与液压第46卷。
3-泄漏的诊断与治理

泄漏的诊断与防治泄漏是液压系统的老大难问题。
现场液压故障诊断与处理工作的很大一部分就是分析与排除各类密封失效故障。
设备的泄漏,从理论上说,凡是要求密封的部位,介质泄漏量不为零的都应认为是泄漏。
通常根据生产工艺流程、设备结构特点和密封技术水平,允许设备某些部位有一定的泄漏量。
正在使用的设备,如果不允许泄漏的部位有了泄漏,或允许有一定泄漏量的部位超过了规定值,那就是泄漏。
第1节液压系统泄漏及其防治概述4.1.1 液压系统的内泄与外泄液压系统的泄漏分为两类,一种是内部泄漏,一种是外部泄漏。
(1)外部泄漏压力管道的泄漏可被很容易地发现,因为可以看到泄漏出的液压油。
维护人员和操作者应当经常检查整个液压系统的每个元件,及时发现泄漏点并立即着手解决泄漏问题。
但外部泄漏发生在泵的吸油口时则很难检测到,如果出现以下5条之一的现象,可以怀疑发生了系统吸油管泄漏:1)液压油中有空气气泡;2)液压系统动作不稳定,有爬行现象;3)液压系统过热;4)油箱压力增高;5)泵噪声增大。
假如以上任何一现象存在,就应当首先检查所有的吸油管接头和连接处以寻找泄漏点。
对于软管接头不要过度地旋紧,因为过度的旋紧会使管接头变形,反而会增加泄漏,应当使用设备制造商推荐的旋紧转矩值,这将保证可靠的密封并且不会使管接头和密封圈产生扭曲变形造成密封圈表面的损坏。
(2)内部泄漏由于液压系统中元件的磨损,随着时间的推移,在元件内部产生的泄漏会越来越明显,轻微的内部泄漏可能察觉不到,但是,随着内漏的增加,系统过热将成为问题。
当这种情况发生时,系统的其他元件将开始失效。
鉴别内部泄漏的简单办法是测试系统满载和空载时的工作周期,假如花了比空载时长很多的时间才完成有载时的动作,那么可以怀疑泵可能失效了。
液压系统中的液压元件一旦发生泄漏,不仅会造成介质的浪费和环境的污染,而更严重的会使整个液压系统发生故障,中止工作,以致发生安全、质量事故。
为了减少液压系统的故障,提高液压系统的效率,防止环境污染和减少液压介质的损耗,必须注意泄漏问题,并分析造成泄漏的原因,采取相应的措施,达到减少泄漏以至避免泄漏的目的。
液压系统漏气检测技术研究及应用

液压系统漏气检测技术研究及应用液压系统是工业、机械等领域中不可或缺的重要元件,其稳定的、高效的性能一直受到广泛关注。
然而,由于液压系统工作的特性,易被机械振动、气压变化、机械磨损等因素影响而发生漏气,导致系统性能下降、工作效率降低、甚至系统损坏。
因此,液压系统漏气检测技术的研究和应用具有非常重要的实际意义。
液压系统漏气检测技术的研究,可以分为三个方面:检测原理、检测方法和检测设备。
一、检测原理漏气检测的原理是利用不同的能量转换实现对漏气的检测。
其原理主要有两种:一种是基于液压系统的压力变化来进行检测,一种是基于液压系统内部振动变化来进行检测。
(一)压力变化法压力变化法是最常见的漏气检测原理,其原理是利用压力变化检测系统中是否存在漏气点。
即在充满油液时,应将系统压力进行调整至一定值,并且记录下此压力值。
然后,关闭主阀,停止液压系统的运动,记录下固定时间内的压力值,如果压力值变化,则可判断系统中是否存在漏气点。
此种方法检测精度较高,但容易对检测对象造成短暂压力变化和气泡的产生。
(二)振动变化法振动变化法是另一种较为常见的漏气检测原理,其原理是利用液压系统内部的振动变化来检测漏气。
在液压系统运行时,由于系统内部流体的冲击和摩擦,会发生一系列的振动变化,当系统内存在漏气点时,流体的压力和流量会发生变化,进而产生一定的振动,因此可以通过检测振动信号的变化,来判断系统中存在的漏气问题。
二、检测方法目前,液压系统漏气检测方法主要包括:无压检测法、负压检测法、正压检测法和氦气检测法等。
(一)无压检测法无压检测法通常通过对待检对象进行抽真空处理,在真空状态下检测漏气点。
在真空状态下,抽出系统内所有气体,充满为真空,然后关闭系统,确认是否有损坏或者是松弛的部件,将其修复或更换,来达到检测系统漏气的目的。
该方法简单易行,但存在漏气点无法检测的情况。
(二)负压检测法负压检测法是在系统运行后,将其运作环境压力降低,如通过负压泵对系统进行抽真空处理,检测是否存在漏气点。
工程机械液压系统泄漏分析及预防措施
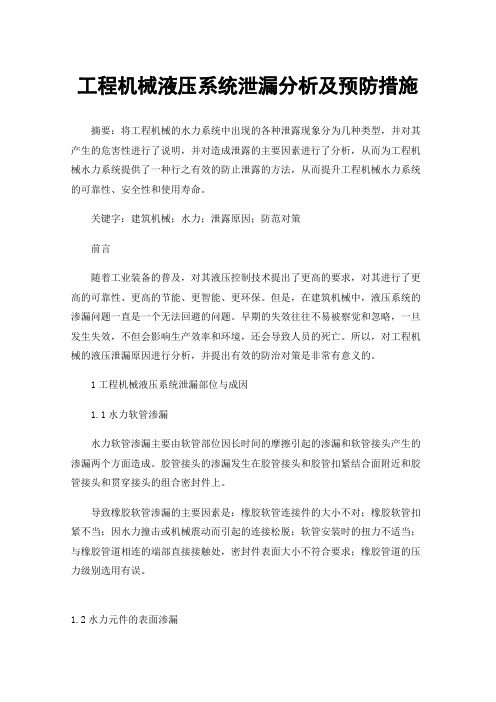
工程机械液压系统泄漏分析及预防措施摘要:将工程机械的水力系统中出现的各种泄露现象分为几种类型,并对其产生的危害性进行了说明,并对造成泄露的主要因素进行了分析,从而为工程机械水力系统提供了一种行之有效的防止泄露的方法,从而提升工程机械水力系统的可靠性、安全性和使用寿命。
关键字:建筑机械;水力;泄露原因;防范对策前言随着工业装备的普及,对其液压控制技术提出了更高的要求,对其进行了更高的可靠性、更高的节能、更智能、更环保。
但是,在建筑机械中,液压系统的渗漏问题一直是一个无法回避的问题。
早期的失效往往不易被察觉和忽略,一旦发生失效,不但会影响生产效率和环境,还会导致人员的死亡。
所以,对工程机械的液压泄漏原因进行分析,并提出有效的防治对策是非常有意义的。
1工程机械液压系统泄漏部位与成因1.1水力软管渗漏水力软管渗漏主要由软管部位因长时间的摩擦引起的渗漏和软管接头产生的渗漏两个方面造成。
胶管接头的渗漏发生在胶管接头和胶管扣紧结合面附近和胶管接头和贯穿接头的组合密封件上。
导致橡胶软管渗漏的主要因素是:橡胶软管连接件的大小不对;橡胶软管扣紧不当;因水力撞击或机械震动而引起的连接松脱;软管安装时的扭力不适当;与橡胶管道相连的端部直接接触处,密封件表面大小不符合要求;橡胶管道的压力级别选用有误。
1.2水力元件的表面渗漏水工零件的表层渗漏主要是由于零件设计缺陷、制造缺陷在水工零件的水工零件中,在水工零件的压力波动或冲击振动等因素的影响下,逐步增大而造成的。
(1)造成铸件表面渗漏的因素包括:零件出现缩孔、缩松等铸件质量问题;铸件的厚度设计不当;铸件的材质选用不当和工艺不当等。
(2)造成熔池内气体泄露的因素:熔池结构不合理,熔池内没有填满,熔池中有空洞及其它不良现象;由于过长的焊缝连接不够牢固等因素。
1.3在水力部件接合面上产生渗漏在工程机械液压系统中,元件的结合面主要有:各个元件的油口与液压接头、液压合流块的连接面、焊接钢管与软管的连接面、主阀片间的密封面、部件间的安装面等。
液压油缸泄露实验标准

液压油缸泄露实验标准液压油缸泄漏实验检测标准1、双作用油缸最低启动压力不得大于下表:公称压力活塞密封形式活塞杆密封形式除V型外V型≤16MPaV型0.5 0.75O、U、Y、X、组合密封0.3 0.45 活塞环0.1 0.15>16MPaV型公称压力×6% 公称压力×9% O、U、Y、X、组合密封公称压力×4% 公称压力×6% 活塞环公称压力×1.5% 公称压力×2.5%2、活塞式单作用油缸最低启动压力不得大于下表:公称压力活塞密封形式活塞杆密封形式除V型外V型≤16MPaV型0.5 0.75除V型外0.35 0.5>16MPaV型公称压力×3.5% 公称压力×9% 除V型外公称压力×3.4% 公称压力×6%3、柱塞式单作用油缸最低启动压力不得大于下表:公称压力柱塞杆密封形式O、Y型V型≤10MPa 0.4 0.516 公称压力×3.5% 公称压力×6% 4、多级套筒式单作用油缸最低启动压力不得大于下表:公称压力柱塞杆密封形式O、Y型V型≤16MPa公称压力×3.5% 公称压力×5%20 公称压力×4% 公称压力×6%5、双作用油缸内泄漏量不得大于:缸内径D mm 内泄漏量 mL/min 缸内径D mm 内泄漏量 mL/min 40 0.03 125 0.2850 0.05 140 0.3063 0.08 160 0.5080 0.13 180 0.6390 0.15 200 0.70100 0.20 220 1.00110 0.22 250 1.10注:使用组合密封时,允许内泄漏量为规定值的2倍6、单作用油缸内泄漏量不得大于:缸内径D mm 内泄漏量 mL/min 缸内径D mm 内泄漏量 mL/min 40 0.06 110 0.5050 0.10 125 0.6463 0.18 140 0.8480 0.26 160 1.2090 0.32 180 1.40100 0.40 200 1.80注:1、使用组合密封时,允许内泄漏量为规定值的2倍;2、采用沉降量检查内泄漏量,沉降量不超过0.05mm/min;3、本规定仅适用活塞式单作用液压缸。
浅谈液体火箭增压输送系统泄漏与检测

浅谈液体火箭增压输送系统泄漏与检测发布时间:2021-04-02T11:32:03.060Z 来源:《基层建设》2020年第29期作者:刘磊刘乐威石鸿广[导读] 摘要:近些年,我国航天事业蓬勃发展,正处于由航天大国迈向航天强国的关键阶段,而火箭正是航天的一项重要工程,增压输送系统又是火箭动力系统重要的组成部分,且是影响火箭以及有效载荷性能、安全性、可靠性的一个极其重要的分系统。
天津航天长征火箭制造有限公司天津 300000摘要:近些年,我国航天事业蓬勃发展,正处于由航天大国迈向航天强国的关键阶段,而火箭正是航天的一项重要工程,增压输送系统又是火箭动力系统重要的组成部分,且是影响火箭以及有效载荷性能、安全性、可靠性的一个极其重要的分系统。
增压输送系统的质量直接影响产品的成败。
若某些产品的增压输送系统在使用过程中出现泄漏,将直接影响火箭的顺利发射。
本文结合火箭增压输送系统泄漏原因进行分析,学习前人的经验,并加以总结,以供参考。
关键词:火箭增压输送系统;焊接;检漏;气密引言火箭增压输送系统被称为火箭运行中的重要“器官”,其质量直接影响着火箭的应用效果。
下文将结合火箭增压输送系统泄漏的多种原因进行探讨,分析火箭增压输送系统在使用过程中出现的泄漏问题,总结一些火箭增压输送系统常见检漏方法。
1火箭增压输送系统及结构设计火箭增压输送系统包含贮箱、增压相关管路、活门(含电磁阀)、气瓶、手阀等。
1.1贮箱以及管路焊接贮箱箱底的瓜瓣之间、箱体的筒段之间、过渡环与筒段之间等都需要焊接,然后才能拼接成整个箱体;导管的接头、三通等与管材也需要焊接。
1.2法兰接口箭体上一些通经大的接口、增压输送管路以及发动机部分气液接口都使用法兰加密封圈结构实现连接密封。
1.3球头球窝或者台阶式双道密封测压、吹除、气封、阀门控制、部分增压管路等大多使用通经较小的导管,这些导管依靠外套螺母连接,密封形式分为球头球窝、台阶配合密封圈等。
2火箭增压输送系统泄漏原因 2.1装配及焊接因素:对中性不好、焊接加工、施加力矩过大导致密封面损伤、多余物混入密封圈或者密封面等。
NG 液压渗漏标准——机务经验交流

液压系统渗漏检查(27、29 、32 、78章)一.液压系统外部渗漏检查★依据AMM PART II TASK29-00-00-790-8011.概述1)一给出了不同部件的最大可允许的外部渗漏率。
但你必须对多个渗漏的部件的渗漏总量进行判断,以确定飞机是否放行。
2)态封严壳的裂纹可能会引起渗漏,而且随着压力的增加,渗漏会加剧。
2.检查程序1)接近渗漏的部件;2)清洁部件上的液压油;3)液压系统增压;4)计算渗漏率,叁照表一,以确定是否放行。
注:如有可能,作动部件大约三个循环,以便得到真实的渗漏率;对于动态封严,如果可能应检查部件运动时的渗漏量和部件停止时的渗漏量。
5)若渗漏超过限制值,应修理;16) 断开液压压力。
3. 液压系统外部渗漏标准表2*⑴每立方厘米大约有20滴,每加仑大约有75600滴。
*⑵确保接头力矩拧紧到正确值。
*⑶静态封严是指两部件间没有相对运动的封严。
(例如:总管的盖子,泵壳体的盖子)。
注:对于转接头(UNION),与管子连接一端漏油应按管接头渗漏的标准检查;与部件壳体连接的一端有封圈封严,应按静态封严的渗漏标准,但应注意检查是封严渗漏还是部件壳体裂纹造成的渗漏。
*⑷动态封严是指两部件间有相对运动的封严。
(例如:作动器活塞杆的封严,泵轴的封严,旋转封严)。
*⑸方向舵PCU的中间通气口实际是两个动态封严的余油口。
所以,评估方向舵PCU3中间通气口的渗漏时,其渗漏标准可加倍。
注:“ABEX”“VICKERS”分别为两个厂家名称,目前我司同时使用“ABEX”、“VICKERS”两家公司电动泵。
二. 飞行控制系统部分部件外部渗漏检查(27章)1. 后缘襟翼电动马达里面加注红油(MIL-H-5606),起润滑作用。
如放油堵头处漏油,更换封圈,并重新加油直到油面到加油口处(叁照AMM PART II TASK12-22-51-601-805)。
42. 后缘襟翼动力驱动组件(PDU)里面加注黄褐色液压油(BMS3-32 TYPE II),起润滑作用。
- 1、下载文档前请自行甄别文档内容的完整性,平台不提供额外的编辑、内容补充、找答案等附加服务。
- 2、"仅部分预览"的文档,不可在线预览部分如存在完整性等问题,可反馈申请退款(可完整预览的文档不适用该条件!)。
- 3、如文档侵犯您的权益,请联系客服反馈,我们会尽快为您处理(人工客服工作时间:9:00-18:30)。
Ab ta t n lne t he c r c e itc he r c tc n n hy a lc s s e n he i l nc s r c :I i o t ha a t rs i soft o ke a no dr u i y t m a d t nfue eof
Vo1 1 N O 3 .9 .
期 第 1 卷 第 3 9
某 型 火 箭 炮 液 压 泄 漏 的 检 测 与 控 制
程 荃 ,
摘
王 强
( 放 军 理 工 大 学 工程 兵 工程 学 院 , 苏 南 京 2 0 0 ) 解 江 1 0 7
要 :针 对某 型火 箭 炮 液 压 系统 的特 点 和 战 场环 境 的影 响 , 析 了火 箭 分
文 献 标 识 码 :A
文 章 编 号 :1 7 —1 7 2 0 ) 30 0 —4 6 30 2 ( 0 8 0 — 1 90
DOI 0 3 8 /.s n 1 7 — 1 7 2 0 . 3 0 3 :1 . 7 3 jis . 6 3 0 2 . 0 8 0 . 2
Hy r u i ak Det to n n r fa Ro k tCa n n d a I Le C ec i n a d , 箭炮 的很 多 机 构 采 用 了液 压 传 动 控 火 制 系统 , 方 面 大大 提 高 了武 器 系 统 的 综 合 战 技 一
指标; 另一 方 面 , 由于 火 箭炮 液压 系 统 压 力 高 、 流 量大、 液压 元 件 密 集度 和元 件 精 度 高 、 构 复 杂 、 结 拆 卸 困难 , 时 由于连续 作业 时 间长 、 同 战场 环境 恶 劣 等原 因 , 得火 箭炮 液 压 系 统故 障 复杂 且 排 除 使 困难 。在实 际工 作 中 , 压泄 漏 是最 常见 、 是最 液 也 难 根治 的液 压 系统 故 障之 一 , 战 时武 器装 备 的 给
CH ENG a W ANG a g Qu n, Qin
( n i e r g I si t fE gn eig C r s P A i. fS i & T c . E gn e i n t u eo n ie r o p , L Un v o e n t n . e h ,Na j g J n s 1 0 7 hn ) ni i g u 2 0 0 ,C ia n a
Ac or i o t e hy a i e k i iy t a n ng,a s ca i g wih t e e ton s r i i a i te h t c d ng t h dr ulcl a n da l r i i s o i tn t he d t c i e v cng f cl is t a i a c ut r f he r c t c nn c o e or t o ke a on,p a tc lf a i l e e to t od nd ma n e a e s he e a e put r c ia e s b e d t c i n me h s a i t n nc c m r
t eb tlf l n io me to t h j rra o so h o k tc n o y r ui e k a ea ay e . h a tei d e v r n n n i,t e mao e s n ft er c e a n n h d a l la r n lz d e c
维普资讯
2 08正 0
6月
装 备 指 挥 技 术 学 院 学 报
J u n l ft eAc d myo up n mma d & Te h oo y o r a h a e fEq ime tCo o n c n lg
J n 2 0 ue 08
十分必 要 。
1 液 压 油 泄 漏 原 因及 分 类
在 液 压系 统 中 , 压 油 从 油 箱 出 来 , 过 油 液 经 泵 、 压 阀组 、 路 、 头 、 能 器 、 滤 器 、 却 液 管 接 蓄 过 冷 器、 油缸 等再 流 回到 油箱 的各 个 环 节 都 有 可 能产
生泄 漏 。 1 1 液 压 油 泄 漏 的 原 因 .
维修 保 障工 作 带 来 了 巨大 挑 战 。 因此 , 分析 火 箭 炮 液压控 制 系统 泄 漏 故 障机 理 及 其 原 因 , 时 有 及 效地 监测 到故 障 源 , 由此 进 行 有 效 的维 修 控 制 并
炮 液压 系统 泄 漏 的主要 原 因; 据 日常 训练 中液 压 系统遇 到 的泄 漏 问题 , 根 结合 火箭 炮
所 配备 的检 测 维修设 备 , 出 了可行 的检 测 方法 和维 修控 制方 案 ; 提 对使 用 单位 的保养
和 维 护 工 作 提 出 了建 议 。 关 键 词 :火 箭 炮 ; 压 油 ; 漏 液 泄 中图分 类号 : TH 3 17
f r a d Postv ug s i s r ve t t e e a hm e nd n v d l de t ki t e ow r. ii e s ge ton a e gi n o h d t c nt a i di i ua s un r a ng h m a n e it — na e w o k or u i g t e po y t m . nc r s n he w a n s s e Ke y wor ds:r ke a on;hyd a i i; la oc t c nn r ulc o l e k