L503IDT中文资料
R12I05资料

Electrical Specifications (measured at TA = 25°C, at nominal input voltage and rated output current unless otherwise specified)
Input Voltage Range VIN (continuous operation) Reflected Ripple Current (depending on the type) Voltage Set Point Accuracy Line Regulation (high VIN to low VIN) Load regulation (depending on the type) Ripple and Noise (BW=DC to 20MHz) (depending on the type) Isolation Voltage (flash tested for 1 second) Test Voltage (50Hz, 10 seconds) Resistance (Viso = 500V) Switching Frequency Package Weight Storage Temperature Range Operating Temperature Range (all output types) Case Temperature Above Ambient (depending on the type) MTTF 1) (depending on the type) –40°C +25°C +85°C SIP types 5V types 12V types 4.5VDC min. / 5.5VDC max. 10.8VDC min. / 13.2VDC max. 23 mA p-p min. to 38 mA p-p max. see Tolerance Envelope 1.0% min. / 1.2% max. of VIN 3.7% min. / 8.5% max. 45mVp-p min. / 200mVp-p max. 1000VDC min. 1000 Vpk min. 10 GΩ min. 90kHz typ. 2.0 g –50°C to +130°C –40°C min. to +85°C max. (see graph) +36°C min. / +45°C max. 417kHrs min. / 3970kHrs max. 328kHrs min. / 2327kHrs max. 222kHrs min. / 934kHrs max.
ZL50112中文资料(Zarlink Semiconductor)中文数据手册「EasyDatasheet - 矽搜」
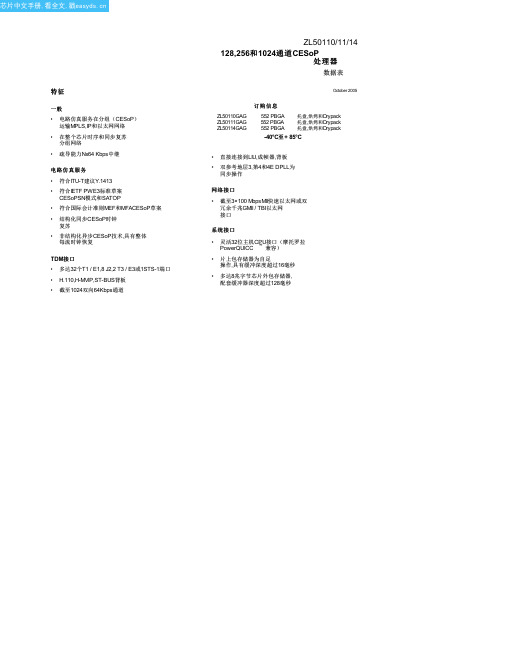
芯片中文手册,看全文,戳
ZL50110/11/14
数据包处理功能
• 灵活多协议数据包封装包括IPv4,IPv6RTP,MPLS,L2TPv3ITU-T Y.1413,IETF CESoPSN模式,IETF SATOP和用户可编程
• 包重测序,允许丢失数据包检测 • 利用出口队列四大类服务优先级可编程机制(WFQ和SP) • 传入分组层2,3,4灵活分类,和5 • 最多支持通过分组交换网络128单独CESoP连接
• 结构感知TDM电路仿真服务在分组交换网络(CESoPSN模式) - 选秀ietfpwe3-cesopsn
该ZL50110/11/14提供高达三倍100 MbpsMII端口或双冗余1000 MbpsGMII / TBI端口.
所述ZL50110/11/14包含一系列每个TDM流强大时钟恢复机制,允许在源时钟频率,可以忠实在目地产生 ,实现更高系统性能和质量.定时使用RTP或类似协议进行,双方自适应和差分时钟恢复方案包括,允许客户选择 正确方案应用.一个外部提供时钟,也可以用于驱动ZL50110/11/14TDM接口.
设备
ZL50114 ZL50110
ZL50111
TDM接口
4 T1,4 E1或1 J 2流或 4 MVIP / ST-BUS流以2.048 Mbps或 1 H.110 / H-MVIP / ST-BUS流在8.192 Mbps
8 T1,8个E1或2 J2流或 8 MVIP / ST-BUS流以2.048 Mbps或 2 H.110 / H-MVIP / ST-BUS流在8.192 Mbps
2.0物理规格. . . . . . . . . . . . . . . . . . . . . . . . . . . . . . . . . . . . . . . . . . . . . . . . . . . . . . . . . . . . . . . . . . 12
VLA503-01;中文规格书,Datasheet资料

Powerex, Inc., 173 Pavilion Lane, Youngwood, Pennsylvania 15697-1800 (724) 925-7272Hybrid ICIGBT Gate DriverVLA503-01Rev. 04/07Description:The VLA503-01 is a hybrid integrated circuit designed to provide optimum gate drive for IGBT modules. This device provides high current optically isolated gate drive with a large output voltage swing. The driver also provides short circuitprotection based on desaturation detection.Features:£ Electrical Isolation Voltage Between Input and Output with Opto-coupler(2500 V rms for 1 Minute)£ Two Supply Driver Topology £ Built-in Short-Circuit Protection (With a Pin for Fault Output)£ TTL Compatible Input Interface Application:To drive IGBT modules for inverter or AC servo systems applications Recommended IGBT Modules:600V module up to 600A 1200V module up to 400ADimensions Inches Millimeters A 2.0 51.0 B 1.02 26.0 C 0.4 10.0 D 0.45 11.5 E 0.12 3.0 F 0.3 7.5 G 0.25 6.5 H 0.10 2.54 J 0.02+0.006/-0.004 0.5+0.15/-0.1 K 0.18±0.06 4.5±1.5 L 0.01+0.01/-0.004 0.25+0.2/-0.1Note: All dimensions listed are maximums except H, J, K, and L./Powerex, Inc., 173 Pavilion Lane, Youngwood, Pennsylvania 15697-1800 (724) 925-7272VLA503-01Hybrid IC IGBT Gate DriverAbsolute Maximum Ratings, T a = 25°C unless otherwise specifiedCharacteristics Symbol VLA503-01 Units Supply Voltage, DC V CC 18 VoltsV EE-15 Volts Input Signal Voltage (Applied between Pin 13 - 14, 50% Duty Cycle, Pulse Width 1ms) V i -1 ~ +7 Volts Output Voltage (When the Output Voltage is "H") V O V CC Volts Output Current I OHP-5 Amperes (Pulse Width 2µs, f ≤ 20kHz) I OLP 5 Amperes Isolation Voltage (Sine Wave Voltage 60Hz, for 1 Minute) V ISO2500 V rms Case Temperature T C85 °C Operating Temperature (No Condensation Allowable) T opr-20 ~ +60 °C Storage Temperature (No Condensation Allowable) T stg-25 ~ +100* °C Fault Output Current (Applied Pin 8) I FO 20 mA Input Voltage at Pin 1 (Applied Pin 1) V R1 50 Volts *Differs from H/C condition.Electrical and Mechanical Characteristics, T a = 25°C unless otherwise specified, V CC = 15V, V EE = -10V) Characteristics Symbol Test Conditions Min. Typ. Max. Units Supply Voltage V CC Recommended Range 14 15 — VoltsV EE Recommended Range -7 — -10 Volts Pull-up Voltage on Primary Side V IN Recommended Range 4.75 5 5.25 Volts "H" Input Current I IH Recommended Range 15.2 16 19 mA Switching Frequency f Recommended Range — — 20 kHz Gate Resistance R G Recommended Range 2 — — W "H" Input Current I IH V IN = 5V — 16 — mA "H" Output Voltage V OH13 14 — Volts "L" Output Voltage V OL-8 -9 — Volts "L-H" Propagation Time t PLH I IH = 16mA — 0.5 1 µs "L-H" Rise Time t r I IH = 16mA — 0.3 1 µs "H-L" Propagation Time t PHL I IH = 16mA — 1 1.3 µs "H-L" Fall Time t f I IH = 16mA — 0.3 1 µs Timer t timer Between Start and Cancel 1 — 2 ms(Under Input Sign "L")Fault Output Current I FO Applied 8 Pin, R = 4.7k W— 5 — mA Controlled Time Detect Short-Circuit 1 t trip1Pin 1: 15V and More, Pin 2: Open — 2.6 — µs Controlled Time Detect Short-Circuit 2** t trip2Pin 1: 15V and More, Pins 2-4: 10pF — 3 — µs(Connective Capacitance)SC Detect Voltage V SC Collector Voltage of Module 15 — — Volts **Length of wiring capacitor controlled time detect short-circuit is within 5cm from Pin 2 and Pin 4 coming and going.Rev. 04/07 /VLA503-01Hybrid IC IGBT Gate DriverPowerex, Inc., 173 Pavilion Lane, Youngwood, Pennsylvania 15697-1800 (724) 925-7272Rev. 04/07FAULTFAULTApplication Circuit/VLA503-01Hybrid IC IGBT Gate DriverPowerex, Inc., 173 Pavilion Lane, Youngwood, Pennsylvania 15697-1800 (724) 925-72724Rev. 04/07020604080AMBIENT TEMPERATURE, T a , (°C)010302040SUPPL Y VOLTAGE, V CC , (VOLTS)(PIN: 4 – 6)1.01.61.41.20.80.60.20.4P R O P A G A T I O N D E L A Y T I M E “L -H ”, t P L H , (µs )P R O P A G A T I O N D E L A Y T I M E “H -L ”, t P H L , (µs )0956784320257510012550150CONNECTIVE CAPACITANCE, C trip , (p F )(PIN: 2 – 4)C O N T R O L L ED T I ME S H O R T -C I R C U I T D E T E C T , t t r i p , (µs )01PROPAGATION DELAY TIME VS. AMBIENT CHARACTERISTICS(TYPICAL)PROPAGATION DELAY TIME VS. INPUT VOLTAGE CHARACTERISTICS(TYPICAL)PROPAGATION DELAY TIME VS.AMBIENT TEMPERATURE CHARACTERISTICS(TYPICAL)SWITCHING TIME DEFINITIONSV IN(PIN 14 TO 13)V O(PIN 5 TO 6)/VLA503-01Hybrid IC IGBT Gate DriverPowerex, Inc., 173 Pavilion Lane, Youngwood, Pennsylvania 15697-1800 (724) 925-7272Rev. 04/07General DescriptionThe VLA503-01 is a hybrid integrated circuit designed to provide gate drive for high power IGBT modules. This circuit has been optimized for use with Powerex NF-Series and A-Series IGBT modules. However, the output characteristics are compatible with most MOS gated power devices. The VLA503-01 features a compact single-in-line package design. The upright mounting minimizes required printed circuit board space to allow efficient and flexible layout. The VLA503-01 converts logic level control signals into fully isolated +15V/-8V gate drive with up to 5A of peak drive current. Control signal isolation is provided by an integrated high speed opto-coupler. Short circuit protection is provided by means of destauration detection. Short Circuit ProtectionFigure 1 shows a block diagram of a typical desatura-tion detector. In this circuit, a high voltage fast recovery diode (D1) is connected to the IGBT’s collector to moni-tor the collector to emitter voltage. When the IGBT is in the off state, V CE is high and D1 is reverse biased. With D1 off the (+) input of the comparator is pulled up to the positive gate drive power supply (V+) which is normally +15V . When the IGBT turns on, the compara-tors (+) input is pulled down by D1 to the IGBT’s V CE(sat). The (-) input of the comparator is supplied with a fixed voltage (V TRIP ). During a normal on-state condition the comparator’s (+) input will be less than V TRIP and it’s output will be low. During a normal off-state condi-tion the comparator’s (+) input will be larger than V TRIPand it’s output will be high. If the IGBT turns on into a short circuit, the high current will cause the IGBT’s col-lector-emitter voltage to rise above V TRIP even though the gate of the IGBT is being driven on. This abnormal presence of high V CE when the IGBT is supposed to be on is often called desaturation . Desaturation can be detected by a logical AND of the driver’s input signal and the comparator output. When the output of the AND goes high a short circuit is indicated. The output of the AND can be used to command the IGBT to shut down in order to protect it from the short circuit. A delay (t TRIP ) must be provided after the comparator output to allow for the normal turn on time of the IGBT. The t TRIP delay is set so that the IGBTs V CE has enough time to fall below V TRIP during normal turn on switching. If t TRIP is set too short, erroneous desaturation detection will occur. The maximum allowable t TRIP delay is limited by the IGBT’s short circuit withstanding capability. In typical applications using Powerex IGBT modules the recom-mended limit is 10µs.Operation of the VLA503-01 Desaturation Detector The Powerex VLA503-01 incorporates short circuit protection using desaturation detection as described above. A flow chart for the logical operation of the short-circuit protection is shown in Figure 2. When a desaturation is detected the hybrid gate driver performs a soft shut down of the IGBT and starts a timed (t timer ) 1.5ms lock out. The soft turn-off helps to limit the tran-sient voltage that may be generated while interrupting the large short circuit current flowing in the IGBT . During the lock out the driver pulls Pin 8 low to indicate the fault status. Normal operation of the driver will resume after the lock-out time has expired and the control input signal returns to its off state.Adjustment of Trip TimeThe VLA503-01 has a default short-circuit detection time delay (t TRIP ) of approximately 2.5µs. This will prevent erroneous detection of short-circuit conditions as long as the series gate resistance (R G ) is near the minimum recommended value for the module being used. The 2.5µs delay is appropriate for most applica-tions so adjustment will not be necessary. However, in some low frequency applications it may be desirable to use a larger series gate resistor to slow the switching of the IGBT, reduce noise, and limit turn-off transient volt-ages. When R G is increased, the switching delay time of the IGBT will also increase. If the delay becomesINPUTFigure 1. Desaturation Detector/VLA503-01Hybrid IC IGBT Gate DriverPowerex, Inc., 173 Pavilion Lane, Youngwood, Pennsylvania 15697-1800 (724) 925-7272 Rev. 04/07Figure 2. VLA503-01 Desaturation DetectorV Figure 3. Adjustment of t triplong enough so that the voltage on the detect Pin 1 is greater than V SC at the end of the t TRIP delay the driver will erroneously indicate that a short circuit has occurred. T o avoid this condition the VLA503-01 has provisions for extending the t TRIP delay by connecting a capacitor (C TRIP ) between Pin 2 and V CC (Pins 4). The effect of adding C TRIP on trip time is shown in Figure 3. If t TRIP is extended care must be exercised not to exceed the short-circuit withstanding capability of the IGBT mod-ule. Normally this will be satisfied for Powerex NF and A-Series IGBT modules as long as the total shut-down time does not exceed 10µs./分销商库存信息: POWEREXVLA503-01。
二路达林顿管 型号

二路达林顿管型号一、引言二路达林顿管是一种常见的电子元件,广泛应用于各种电路中。
它具有高性能、可靠性强的特点,被广泛应用于功放、电源等领域。
本文将对二路达林顿管的型号进行详细介绍,并探讨其在电子领域中的应用。
二、二路达林顿管的基本原理二路达林顿管是由两个晶体管级联组成的,其中一个晶体管的发射极与另一个晶体管的基极相连。
这种结构使得二路达林顿管具有较高的放大倍数和较低的输入阻抗,能够在放大信号的同时提供较大的电流输出。
三、常见的二路达林顿管型号1. BC517BC517是一种常见的二路达林顿管型号,它具有较高的电流放大倍数和较低的饱和压降。
BC517广泛应用于功放电路、开关电源等场合,能够提供稳定可靠的放大和开关功能。
2. TIP122TIP122是一种高功率的二路达林顿管型号,它能够承受较大的电流和功率。
TIP122常用于高功率放大器、电源控制等领域,具有较好的热稳定性和可靠性。
3. BD139BD139是一种常见的二路达林顿管型号,它具有较低的饱和压降和较高的电流放大倍数。
BD139广泛应用于音频功放、开关电源等领域,能够提供稳定的放大和开关功能。
四、二路达林顿管的应用1. 功放电路二路达林顿管在功放电路中起到放大信号的作用。
通过合理的电路设计和选用合适的型号,可以实现高保真、低噪声的音频放大效果。
在功放电路中,BC517、TIP122等型号常被使用。
2. 电源控制二路达林顿管在电源控制中用于开关电路的驱动。
通过控制二路达林顿管的导通和截止,可以实现电源的开关控制,提供稳定的电源输出。
在电源控制中,TIP122、BD139等型号常被使用。
3. 电机驱动二路达林顿管能够提供较大的电流输出,因此常被用于电机驱动电路中。
通过合理的电路设计和选用合适的型号,可以实现电机的高效驱动和控制。
在电机驱动中,TIP122等型号常被使用。
4. 其他应用除了上述应用,二路达林顿管还可以用于锁相环电路、电压调节等领域。
LM5030中文资料

LM5030100V Push-Pull Current Mode PWM ControllerGeneral DescriptionThe LM5030High Voltage PWM controller contains all of the features needed to implement Push-Pull and Bridge topolo-gies,using current-mode control in a small 10pin package.This device provides two alternating gate driver outputs.The LM5030includes a high-voltage start-up regulator that oper-ates over a wide input range of 14V to 100V.Additional features include:error amplifier,precision reference,dual mode current limit,slope compensation,softstart,sync ca-pability and thermal shutdown.This high speed IC has total propagation delays less than 100ns and a 1MHz capable single resistor adjustable oscillator.Package:MSOP-10(Contact factory for thermally enhanced LLP availability).Featuresn Internal High Voltage Start-up Regulator n Single Resistor Oscillator Setting n Synchronizable n Error Amplifiern Precision Reference n Adjustable Softstartn Dual Mode Over-Current Protection n Slope Compensationn Direct Optocoupler Interface n 1.5A Peak Gate Drivers nThermal ShutdownApplicationsn Telecommunication Power Converters n Industrial Power Converters n +42V Automotive SystemsConnection DiagramTop View2005811210-Lead MSOPOrdering InformationOrder Number Package MarkingNSC Package DrawingSupplies AsLM5030MM S73B MUB10A 1000Units on Tape and Reel LM5030MMXS73BMUB10A3500Units on Tape and ReelAugust 2003LM5030100V Push-Pull Current Mode PWM Controller©2003National Semiconductor Corporation Block Diagram20058101FIGURE 1.L M 5030 2Pin DescriptionPin Name PinNumberDescription Application Information V IN1Source Input Voltage Input to start-up regulator.Input range14to100Volts.V FB2Inverting input to the error amplifier The non-inverting input is internally connected to a1.25Voltreference.COMP3Output to the error amplifier There is an internal5K resistor pull-up on this pin.The erroramplifier provides an active sink.Vcc4Output from the internal highvoltage series pass regulator.Theregulation setpoint is7.7Volts.If an auxiliary winding raises the voltage on this pin above the regulation setpoint the internal series pass regulator will shutdown,reducing the IC power dissipation.OUT15Output of the PWM controller Alternating PWM output gate driver.OUT26Output of the PWM controller Alternating PWM output gate driver.GND7Return GroundCS8Current sense input Current sense input for current mode control and current limiting separate dedicated comparators,if CS exceeds0.5Volt the outputs will go into Cycle by Cycle current limit.If CSexceeds0.625V the outputs will be disabled and a softstartcommenced.RT9Oscillator timing resistor pin andsynchronization input.An external resistor sets the oscillator frequency.This pin will also accept synchronization pulses from an external oscillator.SS10Dual purpose Softstart andShutdown pin A10µA current source and an external capacitor set the softstart timing length.The controller will enter a low power state if the SSpin is pulled below the typical shutdown threshold of0.45V.LM50303Absolute Maximum Ratings(Note 1)If Military/Aerospace specified devices are required,please contact the National Semiconductor Sales Office/Distributors for availability and specifications.V IN to GND (Survival)-0.3V to 100V V CC to GND (Survival)-0.3V to 16V RT to GND (Survival)-0.3V to 5.5V All other pins to GND (Survival)-0.3V to 7V Power Dissipation (Note 2)Internally LimitedESD Rating (Note 3)Human Body Model Machine Model2kV 200VLead Temperature(Soldering 4seconds)260˚CStorage Temperature Range -55˚C to +150˚CJunction Temperature150˚COperating RatingsJunction Temperature -40˚C to +105˚CV IN14V to 90VElectrical CharacteristicsSpecifications in standard type face are for T J =+25˚C and those in boldface type apply over the full operating junction tem-perature range.Unless otherwise specified:V IN =48V,V CC =10V,and RT =26.7K ΩSymbol ParameterConditionsMin (Note 4)Typ (Note 5)Max (Note 4)UnitsStartup Regulator V CC Reg V CC Regulation open ckt 7.47.78.0V V CC Current Limit(Note 2)1017mA I-V IN Startup Regulator Leakage (external Vcc Supply)V IN =90V150500µA I INShutdown CurrentSS =0V,V CC =open250350µAV CC SupplyV CC undervoltage Lockout VoltageVccReg -300mV VccReg -100mV V Undervoltage Hysteresis1.21.62.1V I CC Supply Current Cload =023mAError AmplifierGBWGain Bandwidth 4MHz DC Gain 75dB Input VoltageV FB =COMP1.220 1.245 1.270V COMP Sink CapabilityV FB =1.5V COMP=1V513mACurrent Limit CS1Cycle by Cycle CS Threshold Voltage0.450.50.55V CS2Restart CS Threshold Voltage Resets SS capacitor;auto restart0.5750.6250.675V ILIM Delay to OutputCS step from 0to 0.6V Time to onset of OUT Transition (90%)Cload =030nsCS Sink Current (clocked)CS =0.3V36mA Soft Start/ShutdownSoftstart Current Source 71013µA Softstart to COMP Offset 0.250.50.75V Shutdown Threshold0.20.450.7VL M 5030 4Electrical Characteristics(Continued)Specifications in standard type face are for T J=+25˚C and those in boldface type apply over the full operating junction tem-perature range.Unless otherwise specified:V IN=48V,V CC=10V,and RT=26.7KΩSymbol Parameter Conditions Min(Note4)Typ(Note5)Max(Note4)UnitsOscillatorFrequency1(RT=26.7K)175200225kHzFrequency2(RT=8.2K)510600690kHzSync threshold 3.2 3.8VPWM ComparatorDelay to Output COMP set to2V CSstepped0to0.4V,Timeto onset of OUT transitionlow30nsMax Duty Cycle Inferred from deadtime47.54950%Min Duty Cycle COMP=0V0%COMP to PWM ComparatorGain0.34COMP Open Circuit Voltage V FB=0V 4.3 5.2 6.1VCOMP Short Circuit Current V FB=0V,COMP=0V0.6 1.1 1.5mASlope CompensationSlope Comp Amplitude Delta increase at PWMComparator to CS80105130mVOutput SectionDeadtime Cload=0,10%to10%85135185nsOutput High Saturation Iout=50mA,V CC-V OUT0.250.75VOutput Low Saturation I OUT=100mA0.250.75VRise Time Cload=1nF16nsFall Time Cload=1nF16nsThermal ShutdownTsd Thermal Shutdown Temp.165˚C Thermal Shutdown Hysteresis15˚C Note1:Absolute Maximum Ratings are limits beyond which damage to the device may occur.Operating Ratings are conditions under which operation of the device is intended to be functional.For guaranteed specifications and test conditions,see the Electrical Characteristics.Note2:The maximum allowable power dissipation is a function of the maximum junction temperature,T J(MAX),the junction-to-ambient thermal resistance,θJA,and the ambient temperature,T A.The maximum allowable power dissipation at any ambient temperture is calculated using:Where the value ofθJA for the mini SO-10(MM)package is200˚C/W.Exceeding the maximum allowable dissipation will cause excessive die temperature,and the device will go into thermal shutdown.Note3:The human body model is a100pF capacitor discharged through a1.5kΩresistor into each pin.The machine model is a200pF capacitor discharged directly into each pin.The machine model ESD rating for pin5and pin6is150V.Note4:Limits are100%production tested at25˚C.Limits over the operating temperature range are guaranteed through correlation using Statistical Quality Control (SQC)methods.The limits are used to calculate National’s Average Outgoing Quality Level(AOQL).Note5:Typical numbers represent the most likely parametric norm for25˚C operation.LM50305Typical Performance CharacteristicsUnless otherwise specified:T J =25˚C.V CC vs V INV CC vs I CC (V IN =48V)2005810520058107Oscillator Frequency vs RTOscillator Frequency vs TemperatureRT =26.7k Ω2005810820058109Soft Start Current vs Temperature Deadtime vs Temperature2005811020058111L M 5030 6Typical Performance Characteristics Unless otherwise specified:TJ=25˚C.(Continued) Feedback Amplifier Gainphase20058115Detailed Operating DescriptionThe LM5030High Voltage PWM controller contains all of the features needed to implement Push-Pull and Bridge topolo-gies,using current-mode control in a small10pin package. Features included are,startup regulator,dual mode current limit,dual alternating gate drivers,thermal shutdown,soft-start and slope compensation.This high speed IC has total propagation delays<100nS.The Functional Block Diagram of the LM5030is shown in Figure1.The LM5030is designed for Current-Mode Control convert-ers which require alternating outputs,such as Push-Pull and Half/Full Bridge topologies.The features included in the LM5030enable all of the advantages of Current-Mode Con-trol,line feed-forward,cycle by cycle current limit and sim-plified loop compensation.The oscillator ramp is internally buffered and added to the PWM comparator input to provide slope compensation necessary for current mode control at higher duty cycles.High Voltage Start-Up RegulatorThe LM5030contains an internal high voltage startup regu-lator.The input pin(Vin)can be connected directly to line voltages as high as100V.The regulator output is internally current limited to10mA.Upon power up,the regulator is enabled and sources current into an external capacitor con-nected to the V CC pin.The recommended capacitance range for the V CC regulator is0.1µF to50µF.When the voltage on the V CC pin reaches the regulation point of7.7V,the control-ler outputs are enabled.The outputs will remain enabled unless,V CC falls below6.1V or if the SS/SHUTDOWN pin is pulled to ground or an over temperature condition occurs.In typical applications,an auxiliary transformer winding is diode connected to the V CC pin.This winding raises the V CC voltage greater than8V,effectively shutting off the internal startup regulator and saving power while reducing the con-troller dissipation.The external V CC capacitor must be sized such that the self-bias will maintain a V CC voltage greater than6.1V during the initial start-up.During a fault mode when the converter self bias winding is inactive,external current draw on the V CC line should be limited as to not exceed the maximum power dissipation of the controller.An external start-up or other bias rail can be used instead of the internal start-up regulator by connecting the V CC and the Vin pins and feeding the external bias voltage(8-15V)to that node.Error AmplifierAn internal high gain error amplifier is provided within theLM5030.The amplifier’s non-inverting reference is tied to1.25V.In non-isolated applications the power converter out-put is connected to the VFB pin via the voltage settingresistors and loop compensation is connected between theCOMP and VFB pins.For most isolated applications the error amplifier function isimplemented on the secondary side ground.Since the inter-nal error amplifier is configured as an open drain output itcan be disabled by connecting VFB to ground.The internal5K pull-up resistor,connected between the5V reference andCOMP,can be used as the pull-up for an optocoupler orother isolation device.PWM ComparatorThe PWM comparator compares the compensated currentramp signal to the loop error voltage from the internal erroramplifier(COMP pin).This comparator is optimized forspeed in order to achieve minimum discernable duty cycles.The comparator polarity is such that zero Volts on the COMPpin will cause a zero duty cycle.Current Limit/Current SenseThe LM5030contains two levels of over-current protection.Ifthe voltage on the current sense comparator exceeds0.5Volts the present cycle is terminated(cycle by cycle currentlimit).If the voltage on the current sense comparator ex-ceeds0.625Volts,the controller will terminate the presentcycle and discharge the softstart capacitor.A small RC filter,located near the controller,is recommended for the CS pin.An internal MOSFET discharges the current sense filtercapacitor at the conclusion of every cycle,to improve dy-namic performance.The LM5030CS and PWM comparators are very fast,andas such will respond to short duration noise youtconsiderations are critical for the current sense filter andsense resistor.The capacitor associated with the CS filtermust be placed very close to the device and connecteddirectly to the pins of the IC(CS and RTN).Also if a currentsense transformer is used,both leads of the transformersecondary should be routed to the sense resistor,whichshould also be located close to the IC.If a current senseresistor located in the drive transistor sources is used,forcurrent sense,a low inductance resistor should be chosen.LM50307Current Limit/Current Sense(Continued)In this case all of the noise sensitive low power grounds should be commoned together around the IC and then a single connection should be made to the power ground (sense resistor ground point).The second level threshold is intended to protect the power converter by initiating a low duty cycle hiccup mode when abnormally high,fast rising currents occur.During excessive loading,the first level threshold will always be reached and the output characteristic of the converter will be that of a current source but this sustained current level can cause excessive temperatures in the power train especially the output rectifiers.If the second level threshold is reached,the softstart capacitor will be fully discharged,a retry will com-mence following the discharge detection.The second level threshold will only be reached when a high dV/dt is present at the current sense pin.The signal must be fast enough to reach the second level threshold before the first threshold detector turns off the driver.This can usually happen for a saturated power inductor or shorted load.Excessive filtering on the CS pin,extremely low value current sense resistor or an inductor that does not saturate with excessive loading may prevent the second level threshold from ever being reached.Oscillator,Shutdown and Sync CapabilityThe LM5030oscillator is set by a single external resistor connected between the RT pin and return.To set a desired oscillator frequency the necessary RT resistor can be calcu-lated as:Each output switches at half the oscillator frequency in a Push-Pull configuration.The LM5030can also be synchro-nized to an external clock.The external clock must be of higher frequency than the free running frequency set by the RT resistor.The clock signal should be capacitively coupled into the RT pin with a 100pF capacitor.A peak voltage level greater than 3Volts with respect to ground is required for detection of the sync pulse.The sync pulse width should be set in the 15to 150nS range by the external components.The RT resistor is always required,whether the oscillator is free running or externally synchronized.The voltage at the RT pin is internally regulated to a nominal 2Volts.The RT resistor should be located very close to the device and connected directly to the pins of the IC (RT and GND).Slope CompensationThe PWM comparator compares the current sense signal to the voltage derived from the COMP pin.The COMP voltage is set by either the internal error amplifier or an external error amplifier through an optocoupler.At duty cycles greater than 50%(composite of alternating outputs)current mode control circuits are prone to subharmonic oscillation.By adding an additional ramp signal to the current sense ramp signal this condition can be avoided.The LM5030integrates this slope compensation by buffering the internal oscillator ramp and summing it internally to the current sense (CS)signal.Addi-tional slope compensation may be added by increasing the source impedance of the current sense signal.Soft Start/ShutdownThe softstart feature allows the converter to gradually reach the initial steady state operating point,thus reducing start-up stresses and surges.An internal 10uA current source and an external capacitor generate a ramping voltage signal which limits the error amplifier output during start-up.In the event of a second level current limit fault,the softstart capacitor will be fully discharged which disables the output drivers.When the fault condition is no longer present,the softstart capaci-tor is released to ramp and gradually restart the converter.The SS pin can also be used to disable the controller.If the SS pin voltage is pulled down below 0.45V (nominal)the controller will disable the outputs and enter a low power state.OUT1,OUT2and Time DelayThe LM5030provides two alternating outputs,OUT1and OUT2.The internal gate drivers can each sink 1.5A peak each.The maximum duty cycle for each output is inherently limited to less than 50%.The typical deadtime between the falling edge of one gate driver output and the rising edge of the other gate driver output is 135ns.Thermal ProtectionInternal Thermal Shutdown circuitry is provided to protect the integrated circuit in the event the excessive junction tem-perature.When activated,typically at 165degrees Celsius,the controller is forced into a low power reset state,disabling the output drivers and the bias regulator.This feature is provided to prevent catastrophic failures from accidental device overheating.L M 5030 8T y p i c a l A p p l i c a t i o n C i r c u i tT y p i c a l A p p l i c a t i o n C i r c u i t ,36V -75V I N a n d 3.3V ,10A O U T20058103LM50309ITEM PART NUMBERDESCRIPTIONVALUE C 1C0805C472K5RAC Capacitor,CER,KEMET 4700p,50V C 2C0805C103K5RAC Capacitor,CER,KEMET 0.01µ,50V C 3C4532X7S0G686M Capacitor,CER,TDK 68µ,4V C 4T520D337M006AS4350Capacitor,TANT,KEMET 330µ,6.3V C 5T520D337M006AS4350Capacitor,TANT,KEMET 330µ,6.3V C 6C4532X7R3A103K Capacitor,CER,TDK 0.01µ,1000V C 7C3216X7R2A104K Capacitor,CER,TDK 0.1µ,100V C 8C4532X7R2A105M Capacitor,CER,TDK 1µ,100V C 9C4532X7R2A105M Capacitor,CER,TDK 1µ,100V C 10C0805C102K1RAC Capacitor,CER,KEMET 1000p,100V C 11C1206C223K5RAC Capacitor,CER,KEMET 0.022µ,50V C 12C3216X7R1E105M Capacitor,CER,TDK 1µ,25V C 13C3216COG2J221J Capacitor,CER,TDK 220p,630V C 14C3216COG2J221J Capacitor,CER,TDK 220p,630V C 15C1206C104K5RAC Capacitor,CER,KEMET 0.1µ,50V C 16C0805C101J1GAC Capacitor,CER,KEMET 100p,100V C 17C0805C101J1GAC Capacitor,CER,KEMET 100p,100V C 18C3216X7R1H334K Capacitor,CER,TDK 0.33µ,50µD 1MBRB3030CTL Diode,Schottky,ON D 2CMPD2838-NSA Diode,Signal,Central D 3CMPD2838-NSA Diode,Signal,Central D 4CMPD2838-NSA Diode,Signal,Central D 5CMPD2838-NSA Diode,Signal,Central L 1MSS6132-103Input Choke,Coilcraft 10µH,1.5A L 2A9785-BOutput Choke,Coilcraft 7µH R 1CRCW12061R00F Resistor 1R 2CRCW12064990F Resistor 499R 3CRCW2512101J Resistor 100,1W R 4CRCW2512101J Resistor 100,1W R 5CRCW12064022F Resistor 40.2K R 6CRCW120610R0F Resistor 10R 7CRCW120610R0F Resistor 10R 8CRCW12061002F Resistor 10K R 9CRCW120623R7F Resistor 23.7R 10CRCW12062002F Resistor 20K R 11CRCW120610R0F Resistor 10R 12CRCW12063010F Resistor 301R 13CRCW120610R0F Resistor 10R 14CRCW12061001F Resistor1KTX 1A9784-B POWER XFR,COILCRAFT TX 2P8208T CURRENT XFR,Pulse 100:1U11LM5030REGULATOR,NATIONAL U22MOCD207M OPTO-COUPLER,QT OPTOELECTRONICS U33LM3411AM5-3.3REFERENCE,NATIONAL 651-1727010DUAL TERMINALS,MOUSER 3per ASSY X 1SUD19N20-90FET,N,200V,SILICONIX X2SUD19N20-90FET,N,200V,SILICONIXL M 5030 10Physical Dimensionsinches (millimeters)unless otherwise noted10Lead MSOP Package NS Package Number MUB10ALIFE SUPPORT POLICYNATIONAL’S PRODUCTS ARE NOT AUTHORIZED FOR USE AS CRITICAL COMPONENTS IN LIFE SUPPORT DEVICES OR SYSTEMS WITHOUT THE EXPRESS WRITTEN APPROVAL OF THE PRESIDENT AND GENERAL COUNSEL OF NATIONAL SEMICONDUCTOR CORPORATION.As used herein:1.Life support devices or systems are devices or systems which,(a)are intended for surgical implant into the body,or (b)support or sustain life,and whose failure to perform when properly used in accordance with instructions for use provided in the labeling,can be reasonably expected to result in a significant injury to the user.2.A critical component is any component of a life support device or system whose failure to perform can be reasonably expected to cause the failure of the life support device or system,or to affect its safety or effectiveness.National Semiconductor Americas Customer Support CenterEmail:new.feedback@ Tel:1-800-272-9959National SemiconductorEurope Customer Support CenterFax:+49(0)180-5308586Email:europe.support@Deutsch Tel:+49(0)6995086208English Tel:+44(0)8702402171Français Tel:+33(0)141918790National Semiconductor Asia Pacific Customer Support CenterEmail:ap.support@National SemiconductorJapan Customer Support Center Fax:81-3-5639-7507Email:jpn.feedback@ Tel:81-3-5639-7560LM5030100V Push-Pull Current Mode PWM ControllerNational does not assume any responsibility for use of any circuitry described,no circuit patent licenses are implied and National reserves the right at any time without notice to change said circuitry and specifications.元器件交易网。
REF5030IDR中文资料

FEATURESDESCRIPTION APPLICATIONSInput Signal 0V to 4V12348765DNC(1)NC(2)TRIMDNC(1)V INTEMPGNDV OUTREF50xxSO-8, MSOP-8(3)(1) DNC = Do not connect.(2) NC = No internal connection.(3) MSOP-8 package available Q3, 2007.NOTES:REF5020,,REF5025REF5030,REF5040 REF5045,REF5050SBOS410–JUNE2007 Low-Noise,Very Low Drift,PrecisionVOLTAGE REFERENCE•LOW TEMPERATURE DRIFT:–High-Grade:3ppm/°C(max)The REF50xx is a family of low-noise,low-drift,veryhigh precision voltage references.These references –Standard-Grade:8ppm/°C(max)are capable of both sinking and sourcing,and are •HIGH ACCURACY:very robust with regard to line and load changes.–High-Grade:0.05%(max)Excellent temperature drift(3ppm/°C)and high –Standard-Grade:0.1%(max)accuracy(0.05%)are achieved using proprietary •LOW NOISE:3μV PP/V design techniques.These features,combined withvery-low noise make the REF50xx family ideal for use •HIGH OUTPUT CURRENT:±10mAin high-precision data acquisition systems.•TEMPERATURE RANGE:–40°C to+125°CEach reference voltage is available in both standard-and high-grade versions.They are offered in MSOP-8(available Q3,2007)and SO-8packages,and are •16-BIT DATA ACQUISITION SYSTEMSspecified from–40°C to+125°C.•ATE EQUIPMENT•INDUSTRIAL PROCESS CONTROL REF50xx Family•MEDICAL INSTRUMENTATION MODEL OUTPUT VOLTAGE •OPTICAL CONTROL SYSTEMS REF5020 2.048V •PRECISION INSTRUMENTATION REF5025 2.5VREF5030 3.0VREF5040 4.096VREF5045 4.5VREF5050 5.0VPlease be aware that an important notice concerning availability,standard warranty,and use in critical applications ofTexas Instruments semiconductor products and disclaimers thereto appears at the end of this data sheet.All trademarks are the property of their respective owners.ABSOLUTE MAXIMUM RATINGS (1)REF5020,,REF5025REF5030,REF5040REF5045,REF5050SBOS410–JUNE 2007This integrated circuit can be damaged by ESD.Texas Instruments recommends that all integrated circuits be handled with appropriate precautions.Failure to observe proper handling and installation procedures can cause damage.ESD damage can range from subtle performance degradation to complete device failure.Precision integrated circuits may be more susceptible to damage because very small parametric changes could cause the device not to meet its published specifications.PACKAGE/ORDERING INFORMATION (1)(1)For the most current package and ordering information see the Package Option Addendum at the end of this document,or see the TI web site at .(2)MSOP-8(DGK)package available Q3,2007.PARAMETER REF50xx UNIT Input Voltage +18V Output Short-Circuit30mA Operating Temperature Range –55to +125°C Storage Temperature Range –55to +150°C Junction Temperature (T J max)+150°C Human Body Model (HBM)3000V ESD Rating Charged Device Model (CDM)1000V(1)Stresses above these ratings may cause permanent damage.Exposure to absolute maximum conditions for extended periods may degrade device reliability.These are stress ratings only,and functional operation of the device at these or any other conditions beyond those specified is not implied.ELECTRICAL CHARACTERISTICS:PER DEVICE REF5020,,REF5025 REF5030,REF5040 REF5045,REF5050SBOS410–JUNE2007Boldface limits apply over the specified temperature range,T A=–40°C to+125°C.At T A=+25°C,I LOAD=0,C L=1μF,and V IN=(V OUT+0.2V)to18V,unless otherwise noted.PER DEVICE PARAMETER CONDITIONS MIN TYP MAX UNITREF5020(V OUT=2.048V)(1)OUTPUT VOLTAGEOutput Voltage V OUT 2.7V<V IN<18V 2.048V Initial Accuracy:High-Grade–0.050.05% Standard-Grade–0.10.1% NOISEOutput Voltage Noise f=0.1Hz to10Hz6μV PPREF5025(V OUT=2.5V)OUTPUT VOLTAGEOutput Voltage V OUT 2.5V Initial Accuracy:High-Grade–0.050.05% Standard-Grade–0.10.1% NOISEOutput Voltage Noise f=0.1Hz to10Hz7.5μV PPREF5030(V OUT=3.0V)OUTPUT VOLTAGEOutput Voltage V OUT 3.0V Initial Accuracy:High-Grade–0.050.05% Standard-Grade–0.10.1% NOISEOutput Voltage Noise f=0.1Hz to10Hz9μV PPREF5040(V OUT=4.096V)OUTPUT VOLTAGEOutput Voltage V OUT 4.096V Initial Accuracy:High-Grade–0.050.05% Standard-Grade–0.10.1% NOISEOutput Voltage Noise f=0.1Hz to10Hz12μV PPREF5045(V OUT=4.5V)OUTPUT VOLTAGEOutput Voltage V OUT 4.5V Initial Accuracy:High-Grade–0.050.05% Standard-Grade–0.10.1% NOISEOutput Voltage Noise f=0.1Hz to10Hz13.5μV PPREF5050(V OUT=5.0V)OUTPUT VOLTAGEOutput Voltage V OUT 5.0V Initial Accuracy:High-Grade–0.050.05% Standard-Grade–0.10.1% NOISEOutput Voltage Noise f=0.1Hz to10Hz15μV PP (1)For V OUT≤2.5V,the minimum supply voltage is2.7V.ELECTRICAL CHARACTERISTICS:ALL DEVICESREF5020,,REF5025REF5030,REF5040REF5045,REF5050SBOS410–JUNE 2007Boldface limits apply over the specified temperature range,T A =–40°C to +125°C.At T A =+25°C,I LOAD =0,C L =1μF,and V IN =(V OUT +0.2V)to 18V,unless otherwise noted.REF50xxPARAMETERCONDITIONSMIN TYP MAX UNITOUTPUT VOLTAGE TEMPERATURE DRIFT Output Voltage Temperature Drift dV OUT /dTHigh-Grade 2.53ppm/°C Standard-Grade 38ppm/°CLINE REGULATION Line Regulation dV OUT /dV INREF5020(1)Only V IN =2.7V to 18V0.11ppm/V All Other Devices 0.11ppm/V Over Temperature 0.21ppm/V LOAD REGULATION Load Regulation dV OUT /d ILOAD–10mA <I LOAD <+10mA,V IN =V OUT +0.75V2030ppm/mA Over Temperature 50ppm/mA SHORT-CIRCUIT CURRENT Short-Circuit Current I SC V OUT =025mA TEMP PIN Voltage OutputAt T A =+25°C575mV Temperature Sensitivity 2.64mV/°C TURN-ON SETTLING TIME Turn-On Settling Time To 0.1%with C L =1μF200μsPOWER SUPPLY Supply Voltage V SSee Note(1)V OUT +0.2(1)18V Quiescent Current 0.81mA Over Temperature 1.2mATEMPERATURE RANGE Specified Range –40+125°C Operating Range –55+125°CThermal Resistance θJAMSOP-8150°C/W SO-8150°C/W(1)For V OUT ≤2.5V,the minimal supply voltage is 2.7V.TYPICAL CHARACTERISTICS0.20.50.71.01.21.51.72.02.22.52.73.03.23.53.74.04.24.54.75.0Drift (ppm/C)°P o p u l a t i o n (%)0.51.01.52.02.53.03.54.04.55.05.56.06.57.07.58.0Drift (ppm/C)°P o p u l a t i o n (%)-50-25T emperature (C)°0.050.040.030.020.010-0.01-0.02-0.03-0.04-0.05O u t p u tV o l t a g e A c c u r a c y (%)125255075100-0.0-0.0-0.0-0.0-0.00.00.00.00.00.0Drift (ppm/C)°P o p u l a t i o n (%)10Frequency (Hz)160140120100806040200P S R R (d B )100k1001k10k-15-10-5Load Current (mA)0.80.70.60.50.40.30.20.10D r o p o u t V o l t a g e (V )150510+125C°+25C °-°40CREF5020,,REF5025REF5030,REF5040REF5045,REF5050SBOS410–JUNE 2007At T A =+25°C,I LOAD =0,and V S =V OUT +0.2V,unless otherwise noted.For V OUT ≤2.5V,the minimum supply voltage is 2.7V.TEMPERATURE DRIFTTEMPERATURE DRIFT (0°C to +85°C)(–40°C to +125°C)Figure 1.Figure 2.OUTPUT VOLTAGE OUTPUT VOLTAGE ACCURACYINITIAL ACCURACYvs TEMPERATUREFigure 3.Figure 4.POWER-SUPPLY REJECTION RATIOvs FREQUENCYDROPOUT VOLTAGE vs LOAD CURRENTFigure 5.Figure 6.-10-5Load Current (mA)2.501252.501002.500752.500502.500252.500002.499752.499502.499252.499002.49875O u t p u t V o l t a g e (V )105+125C°+25C°-°40C -50-25T emperature (C)°0.90.80.70.60.50.40.3T E M P P i n O u t p u t V o l t a g e (V )125255075100-50-25T emperature (C)°10501000950900850800750700650600Q u i e s c e n t C u r r e n t (m A )125255075100-50-25T emperature (C)°0.50.40.30.20.10-0.1-0.2-0.3-0.4-0.5L i n e R e g u l a t i o n (p p m /V )1252550751001s/div1V /d i vm -50-25T emperature (C)°35302520151050S h o r t -C i r c u i t C u r r e n t (m A )125255075100REF5020,,REF5025REF5030,REF5040REF5045,REF5050SBOS410–JUNE 2007TYPICAL CHARACTERISTICS (continued)At T A =+25°C,I LOAD =0,and V S =V OUT +0.2V,unless otherwise noted.For V OUT ≤2.5V,the minimum supply voltage is 2.7V.REF5025OUTPUT VOLTAGETEMP PIN OUTPUT VOLTAGEvs LOAD CURRENTvs TEMPERATUREFigure 7.Figure 8.QUIESCENT CURRENT LINE REGULATION vs TEMPERATUREvs TEMPERATUREFigure 9.Figure 10.SHORT-CIRCUIT CURRENTvs TEMPERATURENOISEFigure 11.Figure 12.40s/div m 2V/div1V/divV OUTV IN400s/divm 5V/div1V/divV OUTV IN20s/div m -1mA-1mA+1mAI LOADV OUT5mV/div1mA/div20s/divm -10mA+10mA+10mAI LOAD V OUT2mV/div10mA/div100s/div m -1mA-1mA+1mAI LOAD V OUT5mV/div1mA/div100s/divm -10mA-10mA+10mAI LOAD V OUT2mV/div10mA/divREF5020,,REF5025REF5030,REF5040REF5045,REF5050SBOS410–JUNE 2007TYPICAL CHARACTERISTICS (continued)At T A =+25°C,I LOAD =0,and V S =V OUT +0.2V,unless otherwise noted.For V OUT ≤2.5V,the minimum supply voltage is 2.7V.STARTUPSTARTUP(REF5025,C =1μF)(REF5025,C =10μF)Figure 13.Figure 14.LOAD TRANSIENT LOAD TRANSIENT (C L =1μF,I OUT =1mA)(C L =1μF,I OUT =10mA)Figure 15.Figure 16.LOAD TRANSIENT LOAD TRANSIENT (C L =10μF,I OUT =1mA)(C L =10μF,I OUT =10mA)Figure 17.Figure 18.20m s/div V OUTV IN5mV/div500mV/div100s/divm V OUTV IN5mV/div500mV/divREF5020,,REF5025REF5030,REF5040REF5045,REF5050SBOS410–JUNE 2007TYPICAL CHARACTERISTICS (continued)At T A =+25°C,I LOAD =0,and V S =V OUT +0.2V,unless otherwise noted.For V OUT ≤2.5V,the minimum supply voltage is 2.7V.LINE TRANSIENTLINE TRANSIENT (C L =1μF)(C L =10μF)Figure 19.Figure 20.APPLICATION INFORMATIONSUPPLY VOLTAGEOUTPUT ADJUSTMENT (TRIM Pin)BASIC CONNECTIONSTEMPERATURE DRIFTDrift +ǒVOUTMAX*V OUTMINV OUT Temp RangeǓ106(ppm)(1)REF5020,,REF5025REF5030,REF5040REF5045,REF5050SBOS410–JUNE 2007The REF50xx is family of low-noise,precision bandgap voltage references that are specifically designed for excellent initial voltage accuracy and The REF50xx family of voltage references features drift.Figure 21shows a simplified block diagram of extremely low dropout voltage.With the exception of the REF50xx.the REF5020,which has a minimum supply requirement of 2.7V,these references can be operated with a supply of 200mV above the output voltage in an unloaded condition.For loaded conditions,a typical dropout voltage versus load plot is shown in Figure 6of the Typical Characteristics.The REF50xx provides a very accurate voltage output.However,V OUT can be adjusted from the nominal value for the purpose of trimming system errors by configuring the TRIM pin (pin 5).The TRIM pin provides for adjustment of the voltage at V OUT over a ±15mV range.Figure 23shows a typical circuit using the TRIM pin to adjust V OUT .When using this technique,the temperature coefficients of the resistors can degrade the temperature drift at the output.Figure 21.REF50xx Simplified Block DiagramFigure 22shows the typical connections for the REF50xx.A supply bypass capacitor ranging between 1μF to 10μF is recommended.A 1μF to 50μF,low-ESR output capacitor (C L )must be connected to V OUT .Figure 23.V OUT Adjustment Using the TRIM PinThe REF50xx is designed for minimal drift error,which is defined as the change in output voltage over temperature.The drift is calculated using the box method,as described by the following equation:Figure 22.Basic ConnectionsThe REF50xx features a maximum drift coefficient of 3ppm/°C for the high-grade version,and 8ppm/°C for the standard-grade.TEMPERATURE MONITORINGPOWER DISSIPATIONNOISE PERFORMANCEREF5020,,REF5025REF5030,REF5040REF5045,REF5050SBOS410–JUNE 2007The temperature output terminal (TEMP,pin 3)The REF50xx family is specified to deliver current provides a temperature-dependent voltage output loads of ±10mA over the specified input voltage with approximately 60k Ωsource impedance.As seen range.The temperature of the device increases in Figure 8,the output voltage follows the nominal according to the equation:relationship:T J =T A +P D ×θJAV TEMPPIN=509mV +2.64×T(°C)Where:T J =Junction temperature (°C)This pin indicates general chip temperature,accurate to approximately ±15°C.Although it is not generally T A =Ambient temperature (°C)suitable for accurate temperature measurements,it P D =Power dissipated (W)can be used to indicate temperature changes or for θJA =Junction-to-ambient thermal resistance temperature compensation of analog circuitry.A (°C/W)temperature change of 30°C corresponds to an approximate 79mV change in voltage at the TEMP The REF50xx junction temperature must not exceed pin.the absolute maximum rating of +150°C.The TEMP pin has high output impedance (see Figure 21).Loading this pin with a low-impedance circuit induces a measurement error;however,it does Typical 0.1Hz to 10Hz voltage noise for each member not have any effect on V OUT accuracy.To avoid of the REF50xx family is specified in the Electrical errors caused by low-impedance loading,buffer the Characteristics:Per Device table.The noise voltage TEMP pin output with a suitable low-temperature drift increases with output voltage and operating op amp,such as the OPA333,OPA335,or OPA376,temperature.Additional filtering can be used to as shown in Figure 24.improve output noise levels,although care should be taken to ensure the output impedance does not degrade performance.Figure 24.Buffering the TEMP Pin OutputAPPLICATION CIRCUITSDATA ACQUISITIONNEGATIVE REFERENCE VOLTAGEREF5020,,REF5025REF5030,REF5040REF5045,REF5050SBOS410–JUNE 2007Data acquisition systems often require stable voltage For applications requiring a negative and positive references to maintain accuracy.The REF50xx family reference voltage,the REF50xx and OPA735can be features low noise,very low drift,and high initial used to provide a dual-supply reference from a 5V accuracy for high-performance data converters.supply.Figure 25shows the REF5025used to Figure 26shows the REF5040in a basic data provide a 2.5V supply reference voltage.The low drift acquisition system.performance of the REF50xx complements the low offset voltage and zero drift of the OPA735to provide an accurate solution for split-supply applications.Care must be taken to match the temperature coefficients of R 1and R 2.Figure 26.Basic Data Acquisition SystemFigure 25.The REF5025and OPA735Create Positive and Negative Reference VoltagesPACKAGING INFORMATIONOrderableDevice Status (1)Package Type Package DrawingPins Package Qty Eco Plan (2)Lead/Ball Finish MSL Peak Temp (3)REF5020AID ACTIVE SOIC D 875Green (RoHS &no Sb/Br)CU NIPDAU Level-2-260C-1YEAR REF5020AIDG4ACTIVE SOIC D 875Green (RoHS &no Sb/Br)CU NIPDAU Level-2-260C-1YEAR REF5020AIDR ACTIVE SOIC D 82500Green (RoHS &no Sb/Br)Call TI Level-2-260C-1YEAR REF5020AIDRG4ACTIVE SOIC D 82500Green (RoHS &no Sb/Br)Call TI Level-2-260C-1YEAR REF5020ID ACTIVE SOIC D 875Green (RoHS &no Sb/Br)CU NIPDAU Level-2-260C-1YEAR REF5020IDG4ACTIVE SOIC D 875Green (RoHS &no Sb/Br)CU NIPDAU Level-2-260C-1YEAR REF5020IDR ACTIVE SOIC D 82500Green (RoHS &no Sb/Br)CU NIPDAU Level-2-260C-1YEAR REF5020IDRG4ACTIVE SOIC D 82500Green (RoHS &no Sb/Br)CU NIPDAU Level-2-260C-1YEAR REF5025AID ACTIVE SOIC D 875Green (RoHS &no Sb/Br)CU NIPDAU Level-2-260C-1YEAR REF5025AIDG4ACTIVE SOIC D 875Green (RoHS &no Sb/Br)CU NIPDAU Level-2-260C-1YEAR REF5025AIDR ACTIVE SOIC D 82500Green (RoHS &no Sb/Br)Call TI Level-2-260C-1YEAR REF5025AIDRG4ACTIVE SOIC D 82500Green (RoHS &no Sb/Br)Call TI Level-2-260C-1YEAR REF5025ID ACTIVE SOIC D 875Green (RoHS &no Sb/Br)CU NIPDAU Level-2-260C-1YEAR REF5025IDG4ACTIVE SOIC D 875Green (RoHS &no Sb/Br)CU NIPDAU Level-2-260C-1YEAR REF5025IDR ACTIVE SOIC D 82500Green (RoHS &no Sb/Br)CU NIPDAU Level-2-260C-1YEAR REF5025IDRG4ACTIVE SOIC D 82500Green (RoHS &no Sb/Br)CU NIPDAU Level-2-260C-1YEAR REF5030AID ACTIVE SOIC D 875Green (RoHS &no Sb/Br)CU NIPDAU Level-2-260C-1YEAR REF5030AIDG4ACTIVE SOIC D 875Green (RoHS &no Sb/Br)CU NIPDAU Level-2-260C-1YEAR REF5030AIDR ACTIVE SOIC D 82500Green (RoHS &no Sb/Br)Call TI Level-2-260C-1YEAR REF5030AIDRG4ACTIVE SOIC D 82500Green (RoHS &no Sb/Br)Call TI Level-2-260C-1YEAR REF5030ID ACTIVE SOIC D 875Green (RoHS &no Sb/Br)CU NIPDAU Level-2-260C-1YEAR REF5030IDG4ACTIVE SOIC D 875Green (RoHS &no Sb/Br)CU NIPDAU Level-2-260C-1YEAR REF5030IDR ACTIVE SOIC D 82500Green (RoHS &no Sb/Br)CU NIPDAU Level-2-260C-1YEAR REF5030IDRG4ACTIVE SOIC D 82500Green (RoHS &no Sb/Br)CU NIPDAU Level-2-260C-1YEAR REF5040AIDACTIVESOICD875Green (RoHS &no Sb/Br)CU NIPDAULevel-2-260C-1YEAR12-Oct-2007Orderable Device Status (1)Package Type Package DrawingPins Package Qty Eco Plan (2)Lead/Ball Finish MSL Peak Temp (3)REF5040AIDG4ACTIVE SOIC D 875Green (RoHS &no Sb/Br)CU NIPDAU Level-2-260C-1YEAR REF5040AIDR ACTIVE SOIC D 82500Green (RoHS &no Sb/Br)Call TI Level-2-260C-1YEAR REF5040AIDRG4ACTIVE SOIC D 82500Green (RoHS &no Sb/Br)Call TI Level-2-260C-1YEAR REF5040ID ACTIVE SOIC D 875Green (RoHS &no Sb/Br)CU NIPDAU Level-2-260C-1YEAR REF5040IDG4ACTIVE SOIC D 875Green (RoHS &no Sb/Br)CU NIPDAU Level-2-260C-1YEAR REF5040IDR ACTIVE SOIC D 82500Green (RoHS &no Sb/Br)CU NIPDAU Level-2-260C-1YEAR REF5040IDRG4ACTIVE SOIC D 82500Green (RoHS &no Sb/Br)CU NIPDAU Level-2-260C-1YEAR REF5045AID ACTIVE SOIC D 875Green (RoHS &no Sb/Br)CU NIPDAU Level-2-260C-1YEAR REF5045AIDG4ACTIVE SOIC D 875Green (RoHS &no Sb/Br)CU NIPDAU Level-2-260C-1YEAR REF5045AIDR ACTIVE SOIC D 82500Green (RoHS &no Sb/Br)Call TI Level-2-260C-1YEAR REF5045AIDRG4ACTIVE SOIC D 82500Green (RoHS &no Sb/Br)Call TI Level-2-260C-1YEAR REF5045ID ACTIVE SOIC D 875Green (RoHS &no Sb/Br)CU NIPDAU Level-2-260C-1YEAR REF5045IDG4ACTIVE SOIC D 875Green (RoHS &no Sb/Br)CU NIPDAU Level-2-260C-1YEAR REF5045IDR ACTIVE SOIC D 82500Green (RoHS &no Sb/Br)CU NIPDAU Level-2-260C-1YEAR REF5045IDRG4ACTIVE SOIC D 82500Green (RoHS &no Sb/Br)CU NIPDAU Level-2-260C-1YEAR REF5050AID ACTIVE SOIC D 875Green (RoHS &no Sb/Br)CU NIPDAU Level-2-260C-1YEAR REF5050AIDG4ACTIVE SOIC D 875Green (RoHS &no Sb/Br)CU NIPDAU Level-2-260C-1YEAR REF5050AIDR ACTIVE SOIC D 82500Green (RoHS &no Sb/Br)Call TI Level-2-260C-1YEAR REF5050AIDRG4ACTIVE SOIC D 82500Green (RoHS &no Sb/Br)Call TI Level-2-260C-1YEAR REF5050ID ACTIVE SOIC D 875Green (RoHS &no Sb/Br)CU NIPDAU Level-2-260C-1YEAR REF5050IDG4ACTIVE SOIC D 875Green (RoHS &no Sb/Br)CU NIPDAU Level-2-260C-1YEAR REF5050IDR ACTIVE SOIC D 82500Green (RoHS &no Sb/Br)CU NIPDAU Level-2-260C-1YEAR REF5050IDRG4ACTIVESOICD82500Green (RoHS &no Sb/Br)CU NIPDAULevel-2-260C-1YEAR(1)The marketing status values are defined as follows:ACTIVE:Product device recommended for new designs.LIFEBUY:TI has announced that the device will be discontinued,and a lifetime-buy period is in effect.NRND:Not recommended for new designs.Device is in production to support existing customers,but TI does not recommend using this part in a new design.PREVIEW:Device has been announced but is not in production.Samples may or may not be available.12-Oct-2007OBSOLETE:TI has discontinued the production of the device.(2)Eco Plan -The planned eco-friendly classification:Pb-Free (RoHS),Pb-Free (RoHS Exempt),or Green (RoHS &no Sb/Br)-please check /productcontent for the latest availability information and additional product content details.TBD:The Pb-Free/Green conversion plan has not been defined.Pb-Free (RoHS):TI's terms "Lead-Free"or "Pb-Free"mean semiconductor products that are compatible with the current RoHS requirements for all 6substances,including the requirement that lead not exceed 0.1%by weight in homogeneous materials.Where designed to be soldered at high temperatures,TI Pb-Free products are suitable for use in specified lead-free processes.Pb-Free (RoHS Exempt):This component has a RoHS exemption for either 1)lead-based flip-chip solder bumps used between the die and package,or 2)lead-based die adhesive used between the die and leadframe.The component is otherwise considered Pb-Free (RoHS compatible)as defined above.Green (RoHS &no Sb/Br):TI defines "Green"to mean Pb-Free (RoHS compatible),and free of Bromine (Br)and Antimony (Sb)based flame retardants (Br or Sb do not exceed 0.1%by weight in homogeneous material)(3)MSL,Peak Temp.--The Moisture Sensitivity Level rating according to the JEDEC industry standard classifications,and peak solder temperature.Important Information and Disclaimer:The information provided on this page represents TI's knowledge and belief as of the date that it is provided.TI bases its knowledge and belief on information provided by third parties,and makes no representation or warranty as to the accuracy of such information.Efforts are underway to better integrate information from third parties.TI has taken and continues to take reasonable steps to provide representative and accurate information but may not have conducted destructive testing or chemical analysis on incoming materials and chemicals.TI and TI suppliers consider certain information to be proprietary,and thus CAS numbers and other limited information may not be available for release.In no event shall TI's liability arising out of such information exceed the total purchase price of the TI part(s)at issue in this document sold by TI to Customer on an annualbasis.12-Oct-2007TAPE AND REEL BOXINFORMATIONDevicePackage Pins SiteReel Diameter (mm)Reel Width (mm)A0(mm)B0(mm)K0(mm)P1(mm)W (mm)Pin1Quadrant REF5020AIDR D 8SITE 4133012 6.4 5.2 2.1812Q1REF5020IDR D 8SITE 4133012 6.4 5.2 2.1812Q1REF5025AIDR D 8SITE 4133012 6.4 5.2 2.1812Q1REF5025IDR D 8SITE 4133012 6.4 5.2 2.1812Q1REF5030AIDR D 8SITE 4133012 6.4 5.2 2.1812Q1REF5030IDR D 8SITE 4133012 6.4 5.2 2.1812Q1REF5040AIDR D 8SITE 4133012 6.4 5.2 2.1812Q1REF5040IDR D 8SITE 4133012 6.4 5.2 2.1812Q1REF5045AIDR D 8SITE 4133012 6.4 5.2 2.1812Q1REF5045IDR D 8SITE 4133012 6.4 5.2 2.1812Q1REF5050AIDR D 8SITE 4133012 6.4 5.2 2.1812Q1REF5050IDRD8SITE 41330126.45.22.1812Q17-Nov-2007DevicePackagePins Site Length (mm)Width (mm)Height (mm)REF5020AIDR D 8SITE 41346.0346.029.0REF5020IDR D 8SITE 41346.0346.029.0REF5025AIDR D 8SITE 41346.0346.029.0REF5025IDR D 8SITE 41346.0346.029.0REF5030AIDR D 8SITE 41346.0346.029.0REF5030IDR D 8SITE 41346.0346.029.0REF5040AIDR D 8SITE 41346.0346.029.0REF5040IDR D 8SITE 41346.0346.029.0REF5045AIDR D 8SITE 41346.0346.029.0REF5045IDR D 8SITE 41346.0346.029.0REF5050AIDR D 8SITE 41346.0346.029.0REF5050IDRD8SITE 41346.0346.029.07-Nov-2007IMPORTANT NOTICETexas Instruments Incorporated and its subsidiaries(TI)reserve the right to make corrections,modifications,enhancements, improvements,and other changes to its products and services at any time and to discontinue any product or service without notice. Customers should obtain the latest relevant information before placing orders and should verify that such information is current and complete.All products are sold subject to TI’s terms and conditions of sale supplied at the time of order acknowledgment.TI warrants performance of its hardware products to the specifications applicable at the time of sale in accordance with TI’s standard warranty.Testing and other quality control techniques are used to the extent TI deems necessary to support this warranty.Except where mandated by government requirements,testing of all parameters of each product is not necessarily performed.TI assumes no liability for applications assistance or customer product design.Customers are responsible for their products and applications using TI components.To minimize the risks associated with customer products and applications,customers should provide adequate design and operating safeguards.TI does not warrant or represent that any license,either express or implied,is granted under any TI patent right,copyright,mask work right,or other TI intellectual property right relating to any combination,machine,or process in which TI products or services are rmation published by TI regarding third-party products or services does not constitute a license from TI to use such products or services or a warranty or endorsement e of such information may require a license from a third party under the patents or other intellectual property of the third party,or a license from TI under the patents or other intellectual property of TI. Reproduction of TI information in TI data books or data sheets is permissible only if reproduction is without alteration and is accompanied by all associated warranties,conditions,limitations,and notices.Reproduction of this information with alteration is an unfair and deceptive business practice.TI is not responsible or liable for such altered rmation of third parties may be subject to additional restrictions.Resale of TI products or services with statements different from or beyond the parameters stated by TI for that product or service voids all express and any implied warranties for the associated TI product or service and is an unfair and deceptive business practice.TI is not responsible or liable for any such statements.TI products are not authorized for use in safety-critical applications(such as life support)where a failure of the TI product would reasonably be expected to cause severe personal injury or death,unless officers of the parties have executed an agreement specifically governing such use.Buyers represent that they have all necessary expertise in the safety and regulatory ramifications of their applications,and acknowledge and agree that they are solely responsible for all legal,regulatory and safety-related requirements concerning their products and any use of TI products in such safety-critical applications,notwithstanding any applications-related information or support that may be provided by TI.Further,Buyers must fully indemnify TI and its representatives against any damages arising out of the use of TI products in such safety-critical applications.TI products are neither designed nor intended for use in military/aerospace applications or environments unless the TI products are specifically designated by TI as military-grade or"enhanced plastic."Only products designated by TI as military-grade meet military specifications.Buyers acknowledge and agree that any such use of TI products which TI has not designated as military-grade is solely at the Buyer's risk,and that they are solely responsible for compliance with all legal and regulatory requirements in connection with such use.TI products are neither designed nor intended for use in automotive applications or environments unless the specific TI products are designated by TI as compliant with ISO/TS16949requirements.Buyers acknowledge and agree that,if they use anynon-designated products in automotive applications,TI will not be responsible for any failure to meet such requirements. Following are URLs where you can obtain information on other Texas Instruments products and application solutions:Products ApplicationsAmplifiers Audio /audioData Converters Automotive /automotiveDSP Broadband /broadbandInterface Digital Control /digitalcontrolLogic Military /militaryPower Mgmt Optical Networking /opticalnetworkMicrocontrollers Security /securityRFID Telephony /telephonyLow Power /lpw Video&Imaging /videoWirelessWireless /wirelessMailing Address:Texas Instruments,Post Office Box655303,Dallas,Texas75265Copyright©2007,Texas Instruments Incorporated。
IDT72801L10PF中文资料

FFB). Two programmable flags, Almost-Empty (PAEA, PAEB) and Almost-Full (PAFA, PAFB), are provided for each FIFO bank to improve memory utilization. If not programmed, the programmable flags default to empty+7 for PAEA and PAEB, and full-7 for PAFA and PAFB.
input port is controlled by a free-running clock (WCLKA, WCLKB), and two Write Enable pins (WENA1, WENA2, WENB1, WENB2). Data is written into each of
the two arrays on every rising clock edge of the Write Clock (WCLKA, WCLKB)
IDT72801/728211/72821/72831/72841/72851
Commercial And Industrial Temperature Range
PIN DESCRIPTIONS
The IDT72801/72811/72821/72831/72841/72851s two FIFOs, referred description defines the input and output signals for FIFO A. The correspondto as FIFO A and FIFO B, are identical in every respect. The following ing signal names for FIFO B are provided in parentheses.
HLMP-KW50 T-1 高精度白LED数据表说明书
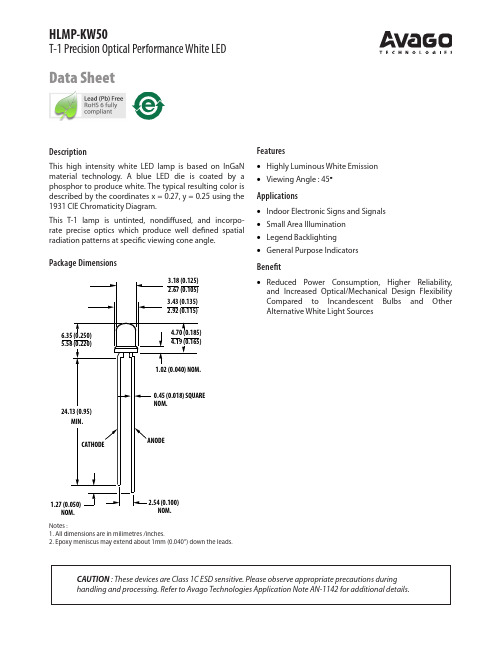
HLMP-KW50T-1 Precision Optical Performance White LEDData SheetPackage DimensionsNotes :1. All dimensions are in milimetres /inches.2. Epoxy meniscus may extend about 1mm (0.040”) down the leads.CAUTION : These devices are Class 1C ESD sensitive. Please observe appropriate precautions during handling and processing. Refer to Avago Technologies Application Note AN-1142 for additional details.NOM.DescriptionThis high intensity white LED lamp is based on InGaN material technology. A blue LED die is coated by a phosphor to produce white. The typical resulting color is described by the coordinates x = 0.27, y = 0.25 using the 1931 CIE Chromaticity Diagram.This T-1 lamp is untinted, nondiffused, and incorpo-rate precise optics which produce well defined spatial radiation patterns at specific viewing cone angle.Features• Highly Luminous White Emission • Viewing Angle : 45°Applications• Indoor Electronic Signs and Signals • Small Area Illumination • Legend Backlighting • General Purpose IndicatorsBenefit• Reduced Power Consumption, Higher Reliability, and Increased Optical/Mechanical Design Flexibility Compared to Incandescent Bulbs and Other Alternative White Light SourcesDevice Selection GuidePart Number Typical Viewing Angle Min Iv (mcd) @ 20mA Max Iv (mcd) @ 20mA Typical Chromaticity Coordinates (x,y)HLMP-KW50-QS00045°115025000.27, 0.25 Notes:1. The chromaticity coordinates are derived from the CIE 1931 Chromaticity Diagram and represent the perceived color of the device.2. θ1/2 is the off-axis angle where the luminous intensity is ½ the peak intensity.3. Tolerance for intensity bin limit is +/- 15%Absolute Maximum Ratings (T A = 25°C)Parameter Value UnitsDC Forward Current [1]30mAPeak Forward Current [2]100mAPower Dissipation111mWReverse Voltage (I R = 10μA)5VLED Junction Temperature110°COperating Temperature Range-40 to +85°CStorage Temperature Range-40 to +100°CNotes:1. Derate linearly as shown in Figure 5.2. Duty factor 10%, Frequency = 1KHz.Electrical Characteristics (T A = 25°C)Forward Voltage, V F (V) @ I F = 20 mA Reverse Breakdown,VR (V) @ I R = 10μACapacitance,C (pF), V F = 0,f = 1 MHzThermal ResistanceRθJ-PIN (°C/W)Typ.Max.Min.Typ.Typ.3.2 3.7570290WAVELENGTH –nmR E L A T I V E L U M I N O U S I N T E N S I T Y3807801.00.606805804800.40.80.201.50.3R E L A T I V E L U M I N O U S I N T EN S I T YFORWARD CURRENT -mA1.20.90.6-0.0100.02500.005-0.005Y -C O O R D I N A T E SX-COORDINATES(X,Y)VALUES @20mA REFERENCE TO (0,0)0.0150.0100.020F O R W A R D C U R R E N T -m A0FORWARD VOLTAGE -V2015353051025I F M A X .-M A X I M U M F O R W A R D C U R R E N T -m AT A -AMBIENT TEMPERATURE -C4080353010206010015255200302010Figure 1. Relative Intensity vs Wavelength Figure 2. Forward Current vs Forward VoltageFigure 3. Relative Iv vs. Forward Current Figure 4. Chromaticity shift vs. currentFigure 5. Maximum Fwd. Current vs TemperatureFigure 6. Spatial Radiation Pattern00.20.40.60.81.0SPATIAL DISPLACEMENT -DEG.R E L A T I V E I N T E N S I T YIntensity Bin Limits (mcd at 20 mA) Bin Min.Max.Q11501500R15001900S1******* Tolerance for each bin limit is ± 15%.Color Bin Limit TablesRank Limits(Chromaticity Coordinates)1xy0.3300.3600.3300.3180.3560.3510.3610.3852xy0.2870. 2950.2960.2760.3300.3180.3300.3393xy0.2640.2670.2800.2480.2960.2760.2830.3054 xy0.2830.3050.2870.2950.3300.3390.3300.360Tolerance for each color bin limit is ± 0.01Color Bin Limits with Respect to CIE 1931 Chromaticity Diagram0.260.30.340.38X-COORDINATEY-COORDINATENote:1. Bin categories are established for classification of products. Products may not be available in allbin categories. Please contact your Avago representative for information on currently availableRelative Light Output vs. Junction Temperature0.1110T J-JUNCTION TEMPERATURE-°CRELATIVELIGHTOUTPUT(NORMALIZEDATTJ=25ºC)InGaN DevicePrecautions:Lead Forming:• The leads of an LED lamp may be preformed or cut to length prior to insertion and soldering on PC board.• For better control, it is recommended to use proper tool to precisely form and cut the leads to applicable length rather than doing it manually.• If manual lead cutting is necessary, cut the leads after the soldering process. The solder connection forms a mechanical ground which prevents mechanical stress due to lead cutting from traveling into LED package. This is highly recommended for hand solder operation, as the excess lead length also acts as small heat sink.Soldering and Handling:• Care must be taken during PCB assembly and soldering process to prevent damage to the LED component. • LED component may be effectively hand soldered to PCB. However, it is only recommended under unavoidable circumstances such as rework. The closest manual soldering distance of the soldering heat source (soldering iron’s tip) to the body is 1.59mm. Soldering the LED using soldering iron tip closer than1.59mm might damage the LED.• ESD precaution must be properly applied on the soldering station and personnel to prevent ESD damage to the LED component that is ESD sensitive. Do refer to Avago application note AN 1142 for details. The soldering iron used should have grounded tip to ensure electrostatic charge is properly grounded.• Recommended soldering condition:WaveSoldering [1, 2]Manual Solder DippingPre-heat temperature 105 °C Max.-Preheat time 60 sec Max -Peak temperature 250 °C Max.260 °C Max.Dwell time3 sec Max.5 sec MaxNote:1) Above conditions refers to measurement with thermocouple mounted at the bottom of PCB.2) It is recommended to use only bottom preheaters in order to reduce thermal stress experienced by LED.• Wave soldering parameters must be set and maintained according to the recommended temperature and dwell time. Customer is advised to perform daily check on the soldering profile to ensure that it is always conforming to recommended soldering conditions.Note: Electrical connection between bottom surface of LED die and the lead frame is achieved through conductive paste.• Any alignment fixture that is being applied during wave soldering should be loosely fitted and should not apply weight or force on LED. Non metal material is recommended as it will absorb less heat during wave soldering process.• At elevated temperature, LED is more susceptible to mechanical stress. Therefore, PCB must allowed to cool down to room temperature prior to handling, which includes removal of alignment fixture or pallet.• If PCB board contains both through hole (TH) LED and other surface mount components, it is recommended that surface mount components be soldered on the top side of the PCB. If surface mount need to be on the bottom side, these components should be soldered using reflow soldering prior to insertion the TH LED.• Recommended PC board plated through holes (PTH) size for LED component leads.LED component lead sizeDiagonalPlated through hole diameter0.45 x 0.45 mm (0.018x 0.018 inch)0.636 mm (0.025 inch)0.98 to 1.08 mm (0.039 to 0.043 inch)0.50 x 0.50 mm (0.020x 0.020 inch)0.707 mm (0.028 inch)1.05 to 1.15 mm (0.041 to 0.045 inch)• Over-sizing the PTH can lead to twisted LED after clinching. On the other hand under sizing the PTH can cause difficulty inserting the TH LED.Note:1. PCB with different size and design (component density) will have different heat mass (heat capacity). This might cause a change in temperature experienced by the board if same wave soldering setting is used. So, it is recommended to re-calibrate the soldering profile again before loading a new type of PCB.2. Avago Technologies’ high brightness LED are using high efficiency LED die with single wire bond as shown below. Customer is advised to take extra precaution during wave soldering to ensure that the maximum wave temperature does not exceed 250°C and the solder contact time does not exceeding 3sec. Over-stressing the LED during soldering process might cause premature failure to the LED due to delamination.Avago Technologies LED configurationExample of Wave Soldering Temperature Profile for TH LED25020015050TIME (MINUTES)Recommended solder:Sn63(Leaded solder alloy)SAC305(Lead free solder alloy)Flux:Rosin fluxSolder bath temperature:245°C±5°C (maximum peak temperature =250°C)Dwell time:1.5sec -3.0sec (maximum =3sec)Note:Allow for board to be sufficiently cooled to room temperature before exerting mechanical force.T E M P E R A T U R E (°C )Packaging Box for Ammo PacksNote: For InGaN device, the ammo pack packaging box contains ESD logo.Packaging Label(i) Avago Mother Label: (Available on packaging box of ammo pack and shipping box)Acronyms and Definition:BIN:(i) Color bin only or VF bin only(Applicable for part number with color bins but without VF bin OR part number with VF bins and no color bin)OR(ii) Color bin incorporated with VF Bin(Applicable for part number that have both color bin and VF bin)(ii) Avago Baby Label (Only available on bulk packaging)Example:(i) Color bin only or VF bin only BIN: 2 (represent color bin 2 only) BIN: VB (represent VF bin “VB” only)(ii) Color bin incorporate with VF BinVB: VF bin “VB”2: Color bin 2 onlyDISCLAIMER: AVAGO’S PRODUCTS AND SOFTWARE ARE NOT SPECIFICALLY DESIGNED, MANUFAC-TURED OR AUTHORIZED FOR SALE AS PARTS, COMPONENTS OR ASSEMBLIES FOR THE PLANNING, CON-STRUCTION, MAINTENANCE OR DIRECT OPERATION OF A NUCLEAR FACILITY OR FOR USE IN MEDICAL DEVICES OR APPLICATIONS. CUSTOMER IS SOLELY RESPONSIBLE, AND WAIVES ALL RIGHTS TO MAKE CLAIMS AGAINST AVAGO OR ITS SUPPLIERS, FOR ALL LOSS, DAMAGE, EXPENSE OR LIABILITY IN CONNEC-TION WITH SUCH USE.For product information and a complete list of distributors, please go to our web site: Avago, Avago Technologies, and the A logo are trademarks of Avago Technologies Limited in the United States and other countries.Data subject to change. Copyright © 00 - 008 Avago Technologies Limited. All rights reserved. Obsoletes 989- 1 EN AV0 -0 EN - April 8, 008。
L-513中文资料

Electrical / Optical Characteristics at T)=25°C °
Sy m b o l Par am et er D ev i c e Bright Red High Efficiency Red Orange Green Yellow Super Bright Green Bright Red High Efficiency Red Orange Green Yellow Super Bright Green Ty p . 700 627 627 565 590 565 660 625 625 568 588 568 45 45 45 30 35 30 40 15 15 15 20 15 2.25 2.0 2.0 2.2 2.1 2.2 2.5 2.5 2.5 2.5 2.5 2.5 10 Max . Un it s Tes t Co n d it io n s
REV NO: V.1 CHECKED:
DATE: SEP/15/2001 DRAWN: J.X.FU
PAGE: 3 OF 6
元器件交易网
High Efficiency Red L-513IDT
Orange L-513EDT
SPEC NO: KDA0291 APPROVED: J.LU
P ar t N o .
Dic e
L en s Ty p e
Notes: 1. θ1/2 is the angle from optical centerline where the luminous intensity is 1/2 the optical centerline value. 2. * Luminous intensity with asterisk is measured at 20mA.
STM32L053C8 MCU用户手册

UM1775User manual Discovery kit for STM32L0 series with STM32L053C8 MCUIntroductionThe STM32L053 discovery kit (32L0358DISCOVERY) helps you to discover the full featuresof the STM32L0 series and to develop your applications. It is based on an STM32L053C8T6and includes an ST-LINK/V2-1 embedded debug tool interface, linear touch sensor, touchkeys, IDD current measurement, 2.04” E-paper display, NFC connector for PLUG-CR95HF-B board, LEDs, pushbuttons and an USB mini-B connector.Figure 1. STM32L053 discovery boardJune 2014DocID026429 Rev 21/39Contents UM1775Contents1Conventions . . . . . . . . . . . . . . . . . . . . . . . . . . . . . . . . . . . . . . . . . . . . . . . . 62Ordering and product information . . . . . . . . . . . . . . . . . . . . . . . . . . . . . . 72.1Order code . . . . . . . . . . . . . . . . . . . . . . . . . . . . . . . . . . . . . . . . . . . . . . . . . 7 3Features . . . . . . . . . . . . . . . . . . . . . . . . . . . . . . . . . . . . . . . . . . . . . . . . . . . 84Hardware layout . . . . . . . . . . . . . . . . . . . . . . . . . . . . . . . . . . . . . . . . . . . . 94.1Embedded ST-LINK/V2-1 . . . . . . . . . . . . . . . . . . . . . . . . . . . . . . . . . . . . . 124.1.1Drivers . . . . . . . . . . . . . . . . . . . . . . . . . . . . . . . . . . . . . . . . . . . . . . . . . . 124.1.2ST-LINK/V2-1 firmware upgrade . . . . . . . . . . . . . . . . . . . . . . . . . . . . . . 134.1.3Using ST-LINK/V2-1 to program/debug the STM32L053 on board . . . 144.1.4Using ST-LINK/V2-1 to program/debug an external STM32 application 154.2Power supply and power selection . . . . . . . . . . . . . . . . . . . . . . . . . . . . . . 164.2.1Power supply input from the USB connector . . . . . . . . . . . . . . . . . . . . . 174.2.2External power supply inputs: 5V_IN or USB USER CN3 . . . . . . . . . . . 174.3LEDs . . . . . . . . . . . . . . . . . . . . . . . . . . . . . . . . . . . . . . . . . . . . . . . . . . . . 184.4Pushbuttons . . . . . . . . . . . . . . . . . . . . . . . . . . . . . . . . . . . . . . . . . . . . . . . 184.5NFC connector for PLUG-CR95HF-B board . . . . . . . . . . . . . . . . . . . . . . 194.6Electronic Paper Display (EPD) . . . . . . . . . . . . . . . . . . . . . . . . . . . . . . . . 204.7JP4 (Idd) . . . . . . . . . . . . . . . . . . . . . . . . . . . . . . . . . . . . . . . . . . . . . . . . . . 204.8BOOT0 configuration . . . . . . . . . . . . . . . . . . . . . . . . . . . . . . . . . . . . . . . . 214.9Linear touch sensor / touch keys . . . . . . . . . . . . . . . . . . . . . . . . . . . . . . . 214.10USB device support . . . . . . . . . . . . . . . . . . . . . . . . . . . . . . . . . . . . . . . . . 224.11USART configuration . . . . . . . . . . . . . . . . . . . . . . . . . . . . . . . . . . . . . . . . 224.12OSC clock supply . . . . . . . . . . . . . . . . . . . . . . . . . . . . . . . . . . . . . . . . . . . 224.13OSC 32 kHz clock supply . . . . . . . . . . . . . . . . . . . . . . . . . . . . . . . . . . . . . 234.14Solder bridges . . . . . . . . . . . . . . . . . . . . . . . . . . . . . . . . . . . . . . . . . . . . . 244.15Extension connectors . . . . . . . . . . . . . . . . . . . . . . . . . . . . . . . . . . . . . . . . 25 5Mechanical drawing . . . . . . . . . . . . . . . . . . . . . . . . . . . . . . . . . . . . . . . . 31 6Electrical schematics . . . . . . . . . . . . . . . . . . . . . . . . . . . . . . . . . . . . . . . 32 2/39DocID026429 Rev 2UM1775Contents 7Revision history . . . . . . . . . . . . . . . . . . . . . . . . . . . . . . . . . . . . . . . . . . . 38DocID026429 Rev 23/39List of tables UM1775 List of tablesTable 1.ON/OFF conventions . . . . . . . . . . . . . . . . . . . . . . . . . . . . . . . . . . . . . . . . . . . . . . . . . . . . . . 6 Table 2.Jumper states. . . . . . . . . . . . . . . . . . . . . . . . . . . . . . . . . . . . . . . . . . . . . . . . . . . . . . . . . . . 12 Table 3.Debug connector CN5 (SWD) . . . . . . . . . . . . . . . . . . . . . . . . . . . . . . . . . . . . . . . . . . . . . . 15 Table 4.NFC connector pin-out . . . . . . . . . . . . . . . . . . . . . . . . . . . . . . . . . . . . . . . . . . . . . . . . . . . . 20 Table 5.Solder bridges. . . . . . . . . . . . . . . . . . . . . . . . . . . . . . . . . . . . . . . . . . . . . . . . . . . . . . . . . . . 24 Table 6.Extension connectors. . . . . . . . . . . . . . . . . . . . . . . . . . . . . . . . . . . . . . . . . . . . . . . . . . . . . 25 Table 7.Document revision history . . . . . . . . . . . . . . . . . . . . . . . . . . . . . . . . . . . . . . . . . . . . . . . . . 38 4/39DocID026429 Rev 2UM1775List of figures List of figuresFigure 1.STM32L053 discovery board . . . . . . . . . . . . . . . . . . . . . . . . . . . . . . . . . . . . . . . . . . . . . . . . 1 Figure 2.STM32L053 discovery hardware block diagram. . . . . . . . . . . . . . . . . . . . . . . . . . . . . . . . . . 9 Figure 3.Top layout. . . . . . . . . . . . . . . . . . . . . . . . . . . . . . . . . . . . . . . . . . . . . . . . . . . . . . . . . . . . . . 10 Figure 4.Bottom layout . . . . . . . . . . . . . . . . . . . . . . . . . . . . . . . . . . . . . . . . . . . . . . . . . . . . . . . . . . . 11 Figure 5.Updating the list of drivers in device manager . . . . . . . . . . . . . . . . . . . . . . . . . . . . . . . . . . 13 Figure 6.STM32L053 discovery board connections . . . . . . . . . . . . . . . . . . . . . . . . . . . . . . . . . . . . . 14 Figure 7.ST-LINK connections . . . . . . . . . . . . . . . . . . . . . . . . . . . . . . . . . . . . . . . . . . . . . . . . . . . . . 16 Figure 8.NFC board plugged on STM32L053 discovery. . . . . . . . . . . . . . . . . . . . . . . . . . . . . . . . . . 19 Figure 9.Jumper on position OFF. . . . . . . . . . . . . . . . . . . . . . . . . . . . . . . . . . . . . . . . . . . . . . . . . . . 20 Figure 10.Jumper on position ON. . . . . . . . . . . . . . . . . . . . . . . . . . . . . . . . . . . . . . . . . . . . . . . . . . . . 21 Figure 11.No Jumper . . . . . . . . . . . . . . . . . . . . . . . . . . . . . . . . . . . . . . . . . . . . . . . . . . . . . . . . . . . . . 21 Figure 12.STM32L053 discovery board mechanical drawing. . . . . . . . . . . . . . . . . . . . . . . . . . . . . . . 31 Figure 13.STM32L053 discovery . . . . . . . . . . . . . . . . . . . . . . . . . . . . . . . . . . . . . . . . . . . . . . . . . . . . 32 Figure 14.ST-LINK/V2-1 (SWD only) . . . . . . . . . . . . . . . . . . . . . . . . . . . . . . . . . . . . . . . . . . . . . . . . . 33 Figure 15.STM32L053C8T6 MCU . . . . . . . . . . . . . . . . . . . . . . . . . . . . . . . . . . . . . . . . . . . . . . . . . . . 34 Figure 16.Electronic paper display . . . . . . . . . . . . . . . . . . . . . . . . . . . . . . . . . . . . . . . . . . . . . . . . . . . 35 Figure 17.Linear touch sensor, NFC, USB and pushbutton . . . . . . . . . . . . . . . . . . . . . . . . . . . . . . . . 36 Figure 18.IDD measurement / MFX (Multi Function eXpander) . . . . . . . . . . . . . . . . . . . . . . . . . . . . . 37DocID026429 Rev 25/39Conventions UM1775 1 ConventionsTable 1 provides the definition of some conventions used in the present document.Table 1. ON/OFF conventionsConvention DefinitionJumper JPx ON Jumper fittedJumper JPx OFF Jumper not fittedSolder bridge SBx ON SBx connections closed by SolderSolder bridge SBx OFF SBx connections left open6/39DocID026429 Rev 2UM1775Ordering and product information 2 Ordering and product informationThe STM32L053 discovery is a low-cost and easy-to-use development kit to quicklyevaluate and start a development with an STM32L0 series microcontroller.Before installing and using the product, please accept the Evaluation Product LicenseAgreement from /stm32l0-discovery.For more information on the STM32L053 discovery board and for demonstration software,visit /stm32l0-discovery.code2.1 OrderTo order the STM32L053 discovery kit, use the order code: STM32L0538-DISCO.DocID026429 Rev 27/39Features UM17758/39DocID026429 Rev 23 FeaturesThe STM32L053 discovery board offers the following features: •STM32L053C8T6 microcontroller featuring 64 KB of flash memory, 8 KB of RAM in an LQFP48 package•On-board ST-LINK/V2-1 with selection mode switch to use the kit as a standalone ST-LINK/V2-1 (with SWD connector for programming and debugging)•USB re-enumeration capability: three different interfaces supported on USB –Virtual com port –Mass storage –Debug port•Board power supply: through USB bus or from an external 5 V supply voltage •External application power supply: 3 V and 5 V •One linear touch sensor or four touch keys.•IDD current measurement.• 2.04” E-paper Display, 172x72 pixels.•NFC connector for PLUG-CR95HF-B board.•USB USER with Mini-B connector.•Four LEDs:–LD1 (red/green) for USB communication –LD2 (red) for 3.3 V power on–Two user LEDs: LD3 (green), LD4 (red)•Two pushbuttons (user and reset)•Extension header for LQFP48 I/Os for a quick connection to the prototyping board and easy probing.UM1775Hardware layoutlayout4 HardwareThe STM32L053 discovery board has been designed around the STM32L053C8T6microcontroller in a 48-pin LQFP package.Figure 2 illustrates the connections between the STM32L053C8T6 and its peripherals (ST-LINK/V2-1, linear touch sensor, touch keys, IDD current measurement, 2.04” E-paperdisplay, NFC connector for PLUG-CR95HF-B board, LEDs, pushbuttons and an USB mini-Bconnector).Figure 3 and Figure 4 help you to locate these features on the STM32L053 discovery board.DocID026429 Rev 29/39Hardware layout UM177510/39DocID026429 Rev 2DocID026429 Rev 211/3912/39DocID026429 Rev 24.1 Embedded ST-LINK/V2-1The ST-LINK/V2-1 programming and debugging tool is integrated on the STM32L053discovery board.The embedded ST-LINK/V2-1 supports only SWD for STM32 devices. For information aboutdebugging and programming features, refer to user manual UM1075 (ST-LINK/V2 in-circuitdebugger/programmer for STM8 and STM32) which describes in detail all the ST-LINK/V2features.The changes versus ST-LINK/V2 version are listed below.•New features supported on ST-LINK/V2-1:–USB software re-enumeration –Virtual com port interface on USB –Mass storage interface on USB –USB power management request for more than 100 mA power on USB •Features not supported on ST-LINK/V2-1:–SWIM interface –Minimum supported application voltage limited to 3 V There are two different ways to use the embedded ST-LINK/V2-1 depending on the jumperstates (see Table 2):•Program/debug the MCU on board (Section 4.1.3).•Program/debug an MCU in an external application board using a cable connected to SWD connector CN5 (Section 4.1.4). 4.1.1 DriversThe ST-LINK/V2-1 requires a dedicated USB driver, which can be found on forWindows Vista, 7 and 8. On Windows XP the ST-LINK/V2-1 driver requires WinUsb to beinstalled before using the ST-LINK/V2-1 (either available from Microsoft website or includedin the USB driver for ST-LINK/V2 for XP).In case the STM32L053 discovery board is connected to the PC before the driver isinstalled, some discovery interfaces may be declared as “Unknown” in the PC devicemanager. In this case the user must install the driver files (Figure 5), and from the devicemanager update the driver of the connected device.Note:Prefer using the “USB Composite Device” handle for a full recovery.Table 2. Jumper statesJumper state DescriptionBoth CN4 jumpers ON ST-LINK/V2-1 functions enabled for on board programming (default)Both CN4 jumpers OFFST-LINK/V2-1 functions enabled for application through external CN5connector (SWD supported)Figure 5. Updating the list of drivers in device manager4.1.2 ST-LINK/V2-1 firmware upgradeThe ST-LINK/V2-1 embeds a firmware upgrade mechanism for in-situ upgrade through theUSB port. As the firmware may evolve during the life time of the ST-LINK/V2-1 product (forexample new functionality, bug fixes, support for new microcontroller families), it isrecommended to visit at the board delivery, then periodically in order to stay up-to-date with the latest firmware version.DocID026429 Rev 213/3914/39DocID026429 Rev 24.1.3 Using ST-LINK/V2-1 to program/debug the STM32L053 on boardTo program the STM32L053 on board, simply plug in the two jumpers on CN4, as shown inFigure 6 in red, but do not use the CN5 connector as that could disturb communication withthe STM32L053C8T6 of the STM32L053 discovery board.Figure 6. STM32L053 discovery board connections4.1.4 Using ST-LINK/V2-1 to program/debug an external STM32 applicationIt is very easy to use the ST-LINK/V2-1 to program the STM32 on an external application.Simply remove the 2 jumpers from CN4 as shown in Figure 7 and connect your applicationto the CN5 debug connector according to Table 3.Note:SB13, must be OFF if you use CN5 pin 5 (NRST) in your external application.Table 3. Debug connector CN5 (SWD)Pïn CN5Designation1VDD_TARGET VDD from application2SWLCK SWD clock3GND Ground4SWDIO SWD data input/output5NRST RESET of target MCU6SWO ReservedDocID026429 Rev 215/39Figure 7. ST-LINK connections4.2 Power supply and power selectionThe power supply is provided either by the host PC through the USB cable, or by anexternal 5 V power supply.The STM32L053 discovery board requires to the Host PC 300mA, but around 90mA isneeded for its demo, 100mA for an extension board and a safety margin of 100mA.The D3, D4 and D6 diodes protect the 5 V pins from external power supplies:• 5 V and 3 V can be used as output power supplies when an extension board isconnected to pins P2 and P3.16/39DocID026429 Rev 2In this case, the 5V_O and 3V_O pins deliver a 5 V or 3.3 V power supply and thepower consumption of the extension board must be lower than 100 mA.• 5 V can also be used as input power supplies, e.g. when the USB connector is not connected to the PC. (5V_I pin of P3 Header)In this case, the STM32L053 discovery board must be powered by a power supply unitor by auxiliary equipment complying with standard EN-60950-1: 2006+A11/2009, andmust be Safety Extra Low Voltage (SELV) with limited power capability.4.2.1 Power supply input from the USB connectorThe ST-LINK/V2-1 supports USB power management allowing to request more than 100mA current to the host PC.All parts of the STM32L053 discovery board and extension board can be powered from theST-LINK USB connector CN2 (U5V or VBUS). Note that only the ST-LINK part is powersupplied before the USB enumeration as the host PC only provides 100 mA to the board atthat time. During the USB enumeration, the STM32L053 discovery board requires 300 mAof current to the Host PC. If the host is able to provide the required power, the targetedSTM32 microcontroller is powered and the red LED LD2 is turned ON, thus the STM32L053discovery board and its extension board can consume a maximum of 300 mA current, notmore. If the host is not able to provide the required current, the targeted STM32microcontroller and the MCU part including the extension board are not power supplied. Asa consequence the red LED LD2 remains turned OFF. In such case it is mandatory to usean external power supply as explained in the next chapter.Warning: If the maximum current consumption of the STM32L053 discovery and itsextension boards exceeds 300 mA, it is mandatory to power the STM32L053 discoveryusing an external power supply connected to 5V_IN.Note:In case of this board is powered by an USB charger or USB battery then there is no USB enumeration so the led LD1 remains OFF permanently and the target MCU is not powered.In this specific case the jumper JP2 needs to be ON to allow target MCU to be poweredanyway. This is a special use without enumeration and JP2 is not soldered. To use thisoptional power supply, solder a 2 pins header in JP2 and set a jumper.4.2.2 External power supply inputs: 5V_IN or USB USER CN3The external power source 5V_IN or USB USER CN3 is automatically detected, in this casethe current consumption of STM32L053 discovery board and extension board may exceedthe allowed current on USB. In this condition it is still possible to use the USB forcommunication, for programming or debugging only, but it is mandatory to power supply theboard first using 5V_IN or USB USER CN3 then connect the USB cable to the PC.Proceeding this way ensures that the enumeration occurs thanks to the external powersource.The following power sequence procedure must be respected:1.Connect the external power source to 5V_IN or USB USER CN3.2. Power on the external power supply 5V_IN or USB USER CN3.3. Check that LD2 is turned ON.4. Connect the PC to USB connector CN2.If this order is not respected, the board may be supplied by VBUS first then by 5V_IN orUSB USER CN3, and the following risks may be encountered:DocID026429 Rev 217/391.If more than 300 mA current is needed by the board, the PC may be damaged or thecurrent supply can be limited by the PC. As a consequence the board is not poweredcorrectly.2. 300 mA is requested at enumeration (since JP2 must be OFF) so there is a risk that therequest is rejected and the enumeration does not succeed if the PC cannot providesuch current. Consequently the board is not power supplied (LED LD2 remains OFF).4.3 LEDs•LD1 COM:LD1 default status is red. LD1 turns to green to indicate that communications are inprogress between the PC and the ST-LINK/V2-1.•LD2 PWR:The red LED indicates that the board is powered.•User LD3:The green LED is a user LED connected to the I/O PB4 of the STM32L053C8T6.•User LD4:The red LED is a user LED connected to the I/O PA5 of the STM32L053C8T6.4.4 Pushbuttons•B1 USER:User and Wake-Up button connected to the I/O PA0 of the STM32L053C8T6.•B2 RESET:The pushbutton connected to NRST is used to RESET the STM32L053C8T6.18/39DocID026429 Rev 2DocID026429 Rev 219/394.5 NFC connector for PLUG-CR95HF-B boardA NFC (Near Field Communication) transceiver board can be connected to the STM32L053Discovery board, for example the PLUG-CR95HF-B board.The NFC board is plugged in connector CN1 of STM32L053 Discovery board as following:Figure 8. NFC board plugged on STM32L053 discovery20/39DocID026429 Rev 2The NFC board can be accessed in SPI or UART mode.4.6 Electronic Paper Display (EPD)The STM32L053 Discovery includes an E-Paper PD with High contrast, High reflectance and Ultra wide viewing angle.This display is a TFT active matrix electrophoretic display. The 2.04" active area contains 172x72 pixels, and has 1-bit and 2-bit full display capabilities. An integrated circuit contains buffers, interface, control logic, oscillator, DC-DC, Etc... (For more information on E-Paper GDE021A1, see )The STM32L053C8T6 controls this peripheral and is able to switch off its power supply. (See Section 6: Electrical schematics )4.7 JP4 (Idd)Jumper JP4, labeled Idd, allows the consumption of STM32L053C8T6 to be measured directly by a module onboard able to measure from 100 nA to 50 mA or by removing the jumper and connecting an ammeter.•Jumper on position OFF: STM32L053C8T6 is powered (default).Figure 9. Jumper on position OFFTable 4. NFC connector pin-outCN1 pinNFC signals STM32L053C8T6Description 1NFC_IRQOUTN or UART1_TX PB7Interrupt output for NFC connected to STM32L053C8T6 UART1 RX 2NFC_IRQINN or UART1_RX PB6Interrupt input for CR95HF connected to STM32L053C8T6 UART1 TX 3NFC_NSS PB12SPI slave select 4NFC_MISO PB14SPI data, slave output 5NFC_MOSI PB15SPI data, slave input 6NFC_SCK PB13SPI serial clock 7+3V3Main power supply/power supply for RF drivers 8GND GroundDocID026429 Rev 221/39•Jumper on position ON: a module onboard is designed to measure from 100 nA to 50 mA by using several MOSFET and switching automatically depending the read value.Figure 10. Jumper on position ON•NO Jumper on JP4: an ammeter must be connected to measure the STM32L053C8T6current through pin 1 and 2 (if there is no ammeter, the STM32L053C8T6 is not powered).Figure 11. No Jumper4.8 BOOT0 configurationBOOT0 is at level “0” through a pull-down R65. If you want to set BOOT0 at level “1”, it canbe configured by setting a jumper between P2.6 (BOOT0) and P2.5 (VDD).Note:If you need to set BOOT0 at level "1" continuously, then unsolder the resistor R65 to avoid a consumption of 6 mA while connecting pin P2.6 (BOOT0) and P2.5 (VDD) with a jumper or with a wire.4.9 Linear touch sensor / touch keysTo demonstrate touch sensing capabilities, the STM32L053 discovery includes a linear touch sensor which can be used either as a 3-position linear touch sensor or as 4 touch keys. Both functions are illustrated in the demonstration software.3 pairs of I/O ports are assigned to the linear touch sensor / touch keys. Each pair mustbelong to the same analog switch group:•PA2, PA3 (group 1)•PA6, PA7 (group 2)•PB0, PB1 (group 3)To minimize the noise, these pairs are dedicated to the linear touch sensor and the touchkeys and are not connected to external headers. To design a touch sensing application,refer to the following documentation and firmware:•For details concerning I/O ports, refer to the STM32L053C8T6 datasheet.•For information on software development, see DISCOVER application software on /stm32l0-discovery.•For more detail concerning touch sensing application design and layout, refer to AN2869 -Guidelines for designing touch sensing applications.•STM32 touch sensing library available from /stm32l0-discovery.The STM32L053C8T6 MCU controls the linear touch sensor and the touch keys.4.10 USB device supportThe STM32L053C8T6 MCU is also used to drive the second USB mini-B connector (USBUSER) which allows the board to be used as a USB Device. The STM32L053 discovery canthen act as a USB joystick, mouse, or other similar device. If both USBs are connected,diodes D3 and D4 protect the board and use the power from the USB ST-LINK or USBUSER. Section 4.2.2: External power supply inputs: 5V_IN or USB USER CN3.The board can be powered through this USB USER connector, in which case LED2 PWRlights up, LED1 COM blinks and it can run an application in standalone mode.The STM32L053C8T6 MCU controls the USB USER through PA11 and PA12.configuration4.11 USARTThe USART1 interface available on PA9 and PA10 of the STM32L053C8T6 can beconnected to ST-LINK MCU to use the Virtual Com Port function.By default the USART1 communication between the target STM32L053C8T6 and ST-LINKMCU is not enabled.To use the Virtual Com Port function with:•The onboard STM32L053C8T6, then set SB2 and SB3 ON. (SB14,15 must be OFF)•An external MCU then remove solder from SB2 and SB3, solder a 2 pins header on JP3, then you can connect RX and TX of the external MCU directly to RX and TX ofJP3. (for more details see Section 6: Electrical schematics)4.12 OSC clock supplyIf PH0 is only used as GPIOs instead of as a clock, then SB21 is closed. (SB20 must beopen)22/39DocID026429 Rev 2MCO from ST-LINK (from MCO of the STM32F103CBT6)This frequency cannot be changed, it is fixed at 8 MHz and connected to PH0-OSC_IN ofthe STM32L053C8T6. The configuration needed is:–SB20 closed and SB21 openOscillator from external PH0 (from external oscillator through pin 7 of the P3 connector)The configuration needed is:–SB21 closed and SB20 openNote:Please refer to the AN2867 for oscillator design guide for STM32 microcontrollers.4.13 OSC 32 kHz clock supplyIf PC14 and PC15 are only used as GPIOs instead of as a clock, then SB18 and SB19 areclosed and R70 and R71 are removed.HSE Oscillator onboard from X2 crystal (not provided)For typical frequencies and its capacitors and resistors, please refer to the STM32L053C8T6Datasheet. The configuration needed is:–SB18, SB19 open–X2, R70, R71, C47, C50 solderedOscillator from external PC14 (from external oscillator through pin 5 of the P3 connector)the configuration needed is:–SB18 closed–SB19 open–R70 removedNote:Please refer to the AN2867 for oscillator design guide for STM32 microcontrollers.DocID026429 Rev 223/394.14 SolderbridgesTable 5. Solder bridges Bridge State(1)DescriptionSB18, 19 (X2 crystal)OFFX2, C47, C50, R70 and R71 provide a clock. PC14, PC15 are disconnectedfrom P3.ON PC14, PC15 are connected from P3. Remove only R70 and R71SB7,8,9,12 (default)ON Reserved, do not modify SB4,5,6,11 (reserved)OFF Reserved, do not modify SB2,3 (reserved)OFF Reserved, do not modifySB29 (B2-RESET)ON B2 Push Button is connected to NRST of STM32L053C8T6 OFF B2 Push Button is not connected to NRST of STM32L053C8T6SB22 (B1-USER)ON B1 Push Button is connected to PA0 OFF B1 Push Button is not connected to PA0SB14, 15 (RX, TX)OFFPA2, PA3 of STM32F103CBT6 are not connected to PB4, PB3 ofSTM32L053C8T6ON PA2, PA3 of STM32F103CBT6 are connected to PB4, PB3 of STM32L053C8T6SB16, 17 (USB_USER)OFF USB1_DP and USB1_DM are dedicated to the USB USER connector CN3ONUSB1_DP is connected to PA12 and USB1_DM is connected to PA11. Both areavailable as GPIO on P2, P3 headers.SB23,24,25,26,27,28 (touch sensor)OFF PA2, PA3, PA6, PA7, PB0, PB1 are dedicated to touch sensor.ON PA2, PA3, PA6, PA7, PB0, PB1 are available as GPIO on P2, P3 headers.SB1 (ST-LINK PWR)ON ST-LINK module is powered OFF ST-LINK module is not poweredSB21 (OSC_IN)OFFClock signal from header P3.7 is connected to OSC_IN of STM32L053C8T6 orPH0 is available as GPIO. SB20 must be OFFON No connection between header P3.7 and PH0 of STM32L053C8T6SB13 (NRST)ONT_NRST signal from connector CN5 and STM32F103CBT6, is connected toNRST of STM32L053C8T6OFF T_NRST signal is not connectedSB10 (STM_RST)OFF No incidence on NRST signal of STM32F103CBT6ON NRST signal of STM32F103CBT6 is connected to GNDSB20 (MCO)ON MCO clock signal from STM32F103CBT6 is connected to OSC_IN of STM32L053C8T6. SB21 must be OFFOFF MCO signal of STM32F103CBT6 is not used.1.Default value is in bold.24/39DocID026429 Rev 2DocID026429 Rev 225/394.15 Extension connectorsThe male headers P2 and P3 can connect the STM32L053 discovery board to a standard prototyping/wrapping board. STM32L053C8T6 GPI/Os are available on these connectors. P2 and P3 can also be probed by an oscilloscope, logical analyzer or voltmeter.Table 6. Extension connectorsMCU pinBoard function M a i n f u n c t i o nL Q F P 48 p i n n u m .S Y S T E MV C PP u s h B u t t o n sL E DN F C C R 95H F -BU S B U S E RL i n e a r t o u c h s e n s o rE -p a p e r D i s p l a yI d d M e a s u r eF r e e I /OP o w e r S u p p l yP 2P 3C N 1C N 3S B x (1)BOOT044B O O T 0----------6----NRST 7N R S T -----------9---PA010--B P _U S E R---------11---PA111--------M F X _W A K E U P---12---PA212------T S _G 1_I O 3-----13--S B 28PA313------T S _G 1_I O 4-----14--S B 27PA414---------P A 4--15---PA515----R E D-------16---PA616------T S _G 2_I O 3-----17--S B 26。
二路达林顿管 型号

二路达林顿管型号
【原创版】
目录
1.二路达林顿管简介
2.二路达林顿管型号分类
3.二路达林顿管的特点与应用
4.市场上主要的二路达林顿管品牌
正文
一、二路达林顿管简介
二路达林顿管,又称为双路达林顿管,是一种电子元器件,主要用于音频放大器的输出级。
它的特点是具有较高的电压放大系数和较低的输出阻抗,可以提供较大的电流输出,使音频信号在负载电阻上得到充分放大。
由于其性能优良,二路达林顿管在音响设备、通信设备等领域具有广泛的应用。
二、二路达林顿管型号分类
根据不同的品牌和性能要求,二路达林顿管有多种型号。
常见的型号有:
1.6CW7
2.6CA7
3.6SL7
4.6SN7
5.6BQ7
6.6V6
7.EL34
这些型号的二路达林顿管在结构、尺寸、性能参数等方面存在差异,用户需要根据具体应用场景和设备要求选择合适的型号。
三、二路达林顿管的特点与应用
二路达林顿管具有以下特点:
1.高电压放大系数:二路达林顿管具有较高的电压放大系数,可以提供较大的电压增益。
2.低输出阻抗:二路达林顿管的输出阻抗较低,可以提供较大的电流输出,使音频信号在负载电阻上得到充分放大。
3.宽频带:二路达林顿管具有较宽的工作频带,可以满足不同音频信号的放大需求。
4.良好的线性特性:二路达林顿管具有较好的线性特性,可以保证音频信号在放大过程中不失真。
基于以上特点,二路达林顿管广泛应用于音响设备、通信设备、广播设备等领域。
L5030中文资料

0.8
Drive Voltage
High Low
VVDRIVE
VISENSE = 0V, IVDRIVE =-0.5mA VCC-0.3
VISENSE = 50mV, IVDRIVE = 5mA
0
ISENSE Threshold Voltaห้องสมุดไป่ตู้e
VISENSE
14 19
Efficiency(Note 1)
元器件交易网
L5030
LINEAR INTEGRATED CIRCUIT
ABSOLUTE MAXIMUM RATINGS (Ta = 25Ċ)
PARAMETER
SYMBOL
RATINGS
UNIT
Supply Voltage
VCC
-0.3 ~ 10
V
Input Voltage
MAX UNITS
8 0.92 VCC 0.2 24 92
3.6 4
-65
V V V V mV % mA mA mA %/°C µA
3.2 µs 200 kHz
UNISONIC TECHNOLOGIES CO., LTD
5 of 7
QW-R125-001.#
元器件交易网
UNISONIC TECHNOLOGIES CO., LTD
L5030
LINEAR INTEGRATED CIRCUIT
BOOST-UP VOLTAGE CONVERTER FOR LED DRIVER
DESCRIPTION
The L5030 is a high efficiency boost converter operating in current loop, based on a PFM mode to drive LEDs. The current mode regulation allows the uniform brightness of LEDs. The wide application of L5030 makes it suitable for many types of battery applications such as Li-ions, Alkaline, or Sealed Lead Acid battery. The combination of few external components and small package size keeps the converter board area to a minimum in space-restricted applications.
NT503 中文规格书
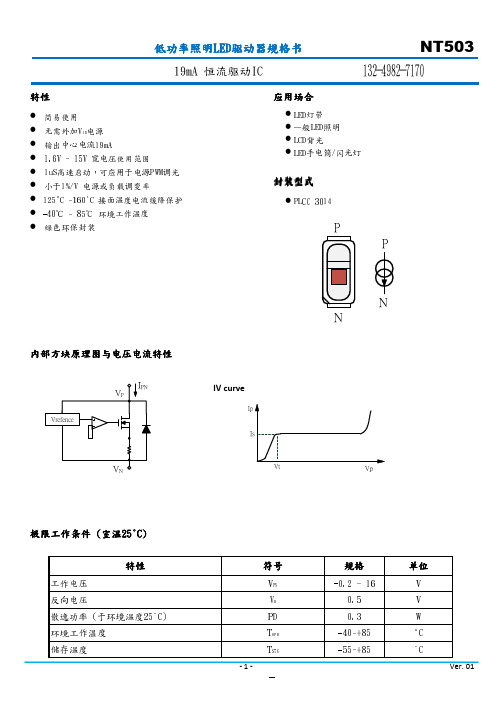
NT503
19mA 恒流驱动IC
132-4982-7170
特性
简易使用 无需外加VDD电源 输出中心电流19mA 1.6V ~ 15V 宽电压使用范围 1uS高速启动,可应用于电源PWM调光 小于1%/V 电源或负载调变率 125°C ~160°C 接面温度电流缓降保护 -40℃ ~ 85℃ 环境工作温度 绿色环保封装
IS %/VP
符号Leabharlann tRise tFallNT503
工作条件
IPN = IS IPN = IS Spec. 10V > VPN > 1.6V
最小
-
典型
1.5 19 -
最大
1.6 15 ±1
单位
V V mA %/V
工作条件
VPN = 0V → 3V VPN = 3V → 0V
最小
-
典型
0.25 0.1
最大
应用场合
LED灯带 一般LED照明 LCD背光 LED手电筒/闪光灯
封装型式
PLCC 3014
内部方块原理图与电压电流特性
IV curve
极限工作条件 (室温25°C)
特性 工作电压 反向电压 散逸功率 (于环境温度25°C) 环境工作温度 储存温度
符号 VPN VR PD TOPR TSTG
- - 1 -
1 0.5
单位
uS uS
温度保护特性
-2-
Ver. 01
应用线路
一般照明应用
LED调光照明应用
NT503
封装尺寸
PLCC 3014
底视图
-
- - 3 -
焊盘尺寸
Ver. 01
IDT IDT23S05 数据手册

The IDT logo is a registered trademark of Integrated Device Technology, Inc.FEATURES:•Phase-Lock Loop Clock Distribution •10MHz to 133MHz operating frequency•Distributes one clock input to one bank of five outputs •Zero Input-Output Delay •Output Skew < 250ps•Low jitter <200 ps cycle-to-cycle •IDT23S05-1 for Standard Drive •IDT23S05-1H for High Drive•No external RC network required •Operates at 3.3V V DD •Power down mode•Spread spectrum compatible •Available in SOIC packageFUNCTIONAL BLOCK DIAGRAMIDT23S053.3V ZERO DELAY CLOCKBUFFER, SPREAD SPECTRUM COMPATIBLEPLL8CLK1CLK2CLK3CLK4Control LogicREFCLKOUT13257DESCRIPTION:The IDT23S05 is a high-speed phase-lock loop (PLL) clock buffer,designed to address high-speed clock distribution applications. The zero delay is achieved by aligning the phase between the incoming clock and the output clock, operable within the range of 10 to 133MHz.The IDT23S05 is an 8-pin version of the IDT23S09. IDT23S05 accepts one reference input, and drives out five low skew clocks. The -1H version of this device operates up to 133MHz frequency and has a higher drive than the -1 device. All parts have on-chip PLLs which lock to an input clock on the REF pin. The PLL feedback is on-chip and is obtained from the CLKOUT pad. In the absence of an input clock, the IDT23S05 enters power down.In this mode, the device will draw less than 12µA for Commercial Tempera-ture range and less than 25µA for Industrial temperature range , the outputs are tri-stated, and the PLL is not running, resulting in a significant reduction of power.The IDT23S05 is characterized for both Industrial and Commercial operation.查询IDT23S05供应商(1)NOTES:1.Stresses greater than those listed under ABSOLUTE MAXIMUM RATINGS may causepermanent damage to the device. This is a stress rating only and functional operationof the device at these or any other conditions above those indicated in the operationalsections of this specification is not implied. Exposure to absolute maximum ratingconditions for extended periods may affect reliability.2.The input and output negative-voltage ratings may be exceeded if the input and outputclamp-current ratings are observed.3.The maximum package power dissipation is calculated using a junction temperatureof 150°C and a board trace length of 750 mils. APPLICATIONS:•SDRAM•Telecom•Datacom•PC Motherboards/Workstations•Critical Path Delay DesignsPIN DESCRIPTIONPin Name Pin Number Type Functional DescriptionREF(1)1IN Input reference clock, 5 Volt tolerant inputCLK2(2)2Out Output clockCLK1(2)3Out Output clockGND4Ground GroundCLK3(2)5Out Output clockV DD6PWR 3.3V SupplyCLK4(2)7Out Output clockCLKOUT(2)8Out Output clock, internal feedback on this pinNOTES:1.Weak pull down.2.Weak pull down on all outputs.OPERATING CONDITIONS - COMMERCIALSymbol Parameter Min.Max.Unit V DD Supply Voltage3 3.6V T A Operating T emperature (Ambient T emperature)070°CC L Load Capacitance < 100MHz—30pFLoad Capacitance 100MHz - 133MHz—10C IN Input Capacitance—7pF DC ELECTRICAL CHARACTERISTICS - COMMERCIALSymbol Parameter Conditions Min.Max.Unit V IL Input LOW Voltage Level—0.8V V IH Input HIGH Voltage Level2—VI IL Input LOW Current V IN= 0V—50µAI IH Input HIGH Current V IN= V DD—100µAV OL Output LOW Voltage Standard Drive I OL= 8mA—0.4VHigh Drive I OL= 12mA (-1H)V OH Output HIGH Voltage Standard Drive I OH= -8mA 2.4—VHigh Drive I OH= -12mA (-1H)I DD_PD Power Down Current REF = 0MHz—12µAI DD Supply Current Unloaded Outputs at66.66MHz—32mASWITCHING CHARACTERISTICS (23S05-1) - COMMERCIAL(1,2)Symbol Parameter Conditions Min.Typ.Max.Unit t1Output Frequency10pF Load10—133MHz30pF Load10—100 Duty Cycle = t2÷ t1Measured at 1.4V, F OUT = 66.66MHz405060% t3Rise Time Measured between 0.8V and 2V—— 2.5ns t4Fall Time Measured between 0.8V and 2V—— 2.5ns t5Output to Output Skew All outputs equally loaded——250ps t6Delay, REF Rising Edge to CLKOUT Rising Edge Measured at V DD/2—0±350ps t7Device-to-Device Skew Measured at V DD/2 on the CLKOUT pins of devices—0700ps t J Cycle-to-Cycle Jitter, pk - pk Measured at 66.66MHz, loaded outputs——200ps t LOCK PLL Lock Time Stable power supply, valid clock presented on REF pin——1msNOTES:1.REF Input has a threshold voltage of V DD/2.2.All parameters specified with loaded outputs.SWITCHING CHARACTERISTICS (23S05-1H) - COMMERCIAL(1,2)Symbol Parameter Conditions Min.Typ.Max.Unit t1Output Frequency10pF Load10—133MHz30pF Load10—100 Duty Cycle = t2÷ t1Measured at 1.4V, F OUT = 66.66MHz405060%Duty Cycle = t2÷ t1Measured at 1.4V, F OUT <50MHz455055% t3Rise Time Measured between 0.8V and 2V—— 1.5ns t4Fall Time Measured between 0.8V and 2V—— 1.5ns t5Output to Output Skew All outputs equally loaded——250ps t6Delay, REF Rising Edge to CLKOUT Rising Edge Measured at V DD/2—0±350ps t7Device-to-Device Skew Measured at V DD/2 on the CLKOUT pins of devices—0700ps t8Output Slew Rate Measured between 0.8V and 2V using Test Circuit #21——V/ns t J Cycle-to-Cycle Jitter, pk - pk Measured at 66.66MHz, loaded outputs——200ps t LOCK PLL Lock Time Stable power supply, valid clock presented on REF pin——1ms NOTES:1.REF Input has a threshold voltage of V DD/2.2.All parameters specified with loaded outputs.OPERATING CONDITIONS - INDUSTRIALSymbol Parameter Min.Max.Unit V DD Supply Voltage3 3.6V T A Operating T emperature (Ambient T emperature)-40+85°CC L Load Capacitance < 100MHz—30pFLoad Capacitance 100MHz - 133MHz—10C IN Input Capacitance—7pF DC ELECTRICAL CHARACTERISTICS - INDUSTRIALSymbol Parameter Conditions Min.Max.Unit V IL Input LOW Voltage Level—0.8V V IH Input HIGH Voltage Level2—VI IL Input LOW Current V IN= 0V—50µAI IH Input HIGH Current V IN= V DD—100µAV OL Output LOW Voltage Standard Drive I OL= 8mA—0.4VHigh Drive I OL= 12mA (-1H)V OH Output HIGH Voltage Standard Drive I OH= -8mA 2.4—VHigh Drive I OH= -12mA (-1H)I DD_PD Power Down Current REF = 0MHz—25µAI DD Supply Current Unloaded Outputs at66.66MHz—35mASWITCHING CHARACTERISTICS (23S05-1) - INDUSTRIAL(1,2)Symbol Parameter Conditions Min.Typ.Max.Unit t1Output Frequency10pF Load10—133MHz30pF Load10—100 Duty Cycle = t2÷ t1Measured at 1.4V, F OUT = 66.66MHz405060% t3Rise Time Measured between 0.8V and 2V—— 2.5ns t4Fall Time Measured between 0.8V and 2V—— 2.5ns t5Output to Output Skew All outputs equally loaded——250ps t6Delay, REF Rising Edge to CLKOUT Rising Edge Measured at V DD/2—0±350ps t7Device-to-Device Skew Measured at V DD/2 on the CLKOUT pins of devices—0700ps t J Cycle-to-Cycle Jitter, pk - pk Measured at 66.66MHz, loaded outputs——200ps t LOCK PLL Lock Time Stable power supply, valid clock presented on REF pin——1msNOTES:1.REF Input has a threshold voltage of V DD/2.2.All parameters specified with loaded outputs.SWITCHING CHARACTERISTICS (23S05-1H) - INDUSTRIAL(1,2)Symbol Parameter Conditions Min.Typ.Max.Unit t1Output Frequency10pF Load10—133MHz30pF Load10—100 Duty Cycle = t2÷ t1Measured at 1.4V, F OUT = 66.66MHz405060%Duty Cycle = t2÷ t1Measured at 1.4V, F OUT <50MHz455055% t3Rise Time Measured between 0.8V and 2V—— 1.5ns t4Fall Time Measured between 0.8V and 2V—— 1.5ns t5Output to Output Skew All outputs equally loaded——250ps t6Delay, REF Rising Edge to CLKOUT Rising Edge Measured at V DD/2—0±350ps t7Device-to-Device Skew Measured at V DD/2 on the CLKOUT pins of devices—0700ps t8Output Slew Rate Measured between 0.8V and 2V using Test Circuit #21——V/ns t J Cycle-to-Cycle Jitter, pk - pk Measured at 66.66MHz, loaded outputs——200ps t LOCK PLL Lock Time Stable power supply, valid clock presented on REF pin——1ms NOTES:1.REF Input has a threshold voltage of V DD/2.2.All parameters specified with loaded outputs.ZERO DELAY AND SKEW CONTROLAll outputs should be uniformly loaded in order to achieve Zero I/O Delay. Since the CLKOUT pin is the internal feedback for the PLL, its relative loading can affect and adjust the input/output delay.For designs utilizing zero I/O Delay, all outputs including CLKOUT must be equally loaded. Even if the output is not used, it must have a capacitive load equal to that on the other outputs in order to obtain true zero I/O Delay. If I/O Delay adjustments are needed, use the Output Load Difference diagram to calculate loading differences between the CLKOUT pin and other outputs. For zero output-to-output skew, all outputs must be loaded equally.SPREAD SPECTRUM COMPATIBLEMany systems being designed now use a technology called Spread Spectrum Frequency Timing Generation. This product is designed not to filter off the Spread Spectrum feature of the reference input, assuming it exists. When a zero delay buffer is not designed to pass the Spread Spectrum feature through, the result is a significant amount of tracking skew, which may cause problems in systems requiring synchronization.V DDOUTPUTSV DDGNDGND0.1µF0.1µFV DDOUTPUTS10pFV DDGNDGND0.1µF0.1µF1K Ω1K ΩC LOADCLK OUTCLK OUTOutput 1.4V1.4Vt5OutputREF V DD/2t6OutputCLK OUT Device 1t7CLK OUT Device 2V DD/2V DD /2V DD /21.4V1.4Vt2t11.4V2V 0.8V t3t40.8V 3.3V 0V2V OutputAll Outputs Rise/Fall Time Input to Output Propagation DelayDevice to Device SkewOutput to Output SkewDuty Cycle TimingSWITCHING WAVEFORMSTest Circuit 1 (all Parameters Except t8)Test Circuit 2 (t8, Output Slew Rate On -1H Devices)TEST CIRCUITSORDERING INFORMATIONOrdering Code Package Type Operating RangeIDT23S05-1DC8-Pin SOIC CommercialIDT23S05-1DCG8-Pin SOIC CommercialIDT23S05-1DCI8-Pin SOIC IndustrialIDT23S05-1HDC8-Pin SOIC CommercialIDT23S05-1HDCG8-Pin SOIC CommercialIDT23S05-1HDCGI8-Pin SOIC IndustrialIDT23S05-1HDCI8-Pin SOIC IndustrialCORPORATE HEADQUARTERS for SALES:for Tech Support:2975 Stender Way800-345-7015 or 408-727-6116*****************Santa Clara, CA 95054fax: 408-492-8674(408) 654-6459IDT XXXXX XX XPackage ProcessDevice Type23S05-123S05-1HZero Delay Clock Buffer withHigh Drive, Spread Spectrum CompatibleDCDCGSmall OutlineSOIC - GreenBlankICommercial (0o C to +70o C)Industrial (-40o C to +85o C)。
Statox 503控制模块说明书
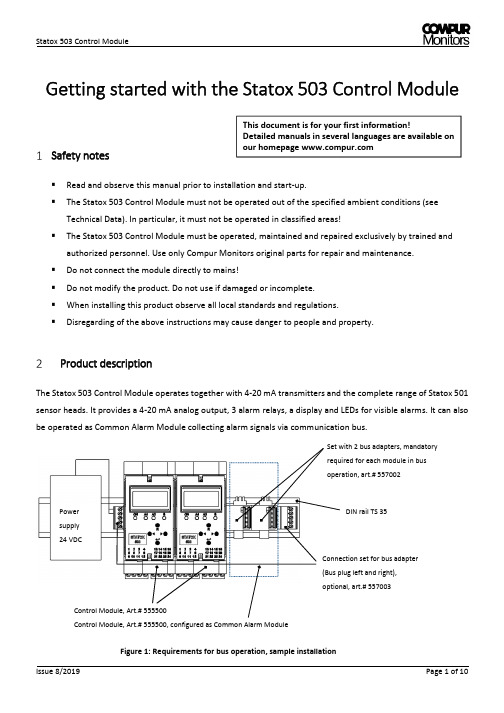
Getting started with the Statox 503 Control ModuleSafety notes▪Read and observe this manual prior to installation and start-up.▪The Statox 503 Control Module must not be operated out of the specified ambient conditions (see Technical Data). In particular, it must not be operated in classified areas!▪The Statox 503 Control Module must be operated, maintained and repaired exclusively by trained and authorized personnel. Use only Compur Monitors original parts for repair and maintenance.▪Do not connect the module directly to mains!▪Do not modify the product. Do not use if damaged or incomplete.▪When installing this product observe all local standards and regulations.▪Disregarding of the above instructions may cause danger to people and property.Product descriptionThe Statox 503 Control Module operates together with 4-20 mA transmitters and the complete range of Statox 501 sensor heads. It provides a 4-20 mA analog output, 3 alarm relays, a display and LEDs for visible alarms. It can also be operated as Common Alarm Module collecting alarm signals via communication bus.Set with 2 bus adapters, mandatoryrequired for each module in busoperation, art.# 557002Connection set for bus adapter(Bus plug left and right),optional, art.# 557003DIN rail TS 35Figure 1: Requirements for bus operation, sample installationControl Module, Art.# 555500Control Module, Art.# 555500, configured as Common Alarm ModulePowersupply24 VDCThis document is for your first information!Detailed manuals in several languages are available onour homepage Figure 2: Mounting to DIN railMounting and DismountingThe Control Modules can be operated without bus adapter, in this case they are clipped onto the DIN rail as shown in figure 2. In this case every single module must be powered with 24 VDC.Connecting to power supplyDo not connect the module directly to mains! Do not short circuit terminals! Both can destroy the module! Observe 24 ± 2 VDC power supply tolerance!There are two options connecting the 24 VDC power supply: via bus plug to the communication bus or directly to the relevant Statox 503 Control Module terminal. In both cases all subsequent modules are automatically connected to the power supply via bus. The terminals are rated to accept a max. diameter of 2,5 mm 2.After connection to power, the green LED is on. During the starting process the module displays the firmware version, then the actual measuring program, then “PLEASE WAIT”.!1314 15 16+24 VDC17 18 19 20421 0 V +24 VDC12!Figure 3: Dismounting from DIN railFigure 4: Connecting the power supplySFMain menu structurePush ◄- and ► -button together for 2 s. Select each digit of the password 1994 with the arrow keys and confirm with ENTER. Correct false inputs with the R key.General time-out: if no button is pushed within 30 seconds, the module returns to measuring mode.Selecting the measuring programPrior to connecting a sensor head the first step is always to select the appropriate program. Thismust be done before the sensor head is connected, otherwise the sensor can be damaged! If a new program is selected, the default alarm settings and relay configurations according to the program listing are valid and the calibration data for the sensor heads for combustible gases, type HRC, ARE, LCIR, MCIR, CO 2 and PID will be lost. A new calibration is necessary (the display shows CALIB. REQUIRED).!Figure 5: Main menu structureIn this menu the appropriate measuring program can be selected. The program defines the target gas, the measuring range, the concentration window for span gas and the ex - works settings of the relays. See an overview of all available programs in the program listing enclosed with each module.Starting with menu SEL PROG the time-out is not active. In this menu a new program can be selected with the arrow keys.After STORE the new program is displayed, push ENTER to start the new program.Figure 6: Program selection diagramMEASURING MODEnCalibrationAfter connecting the sensor heads type Statox 501 HRC, ARE, LCIR, MCIR, CO 2 and PID to the Control Module a calibration is mandatory. Exception: a line calibration has been done ex works. The test gas concentration must be within the permitted range, see program listing.RFigure 7: Calibration menu diagramChange menu itemFlashing, searching zero point.Flashing, turn test gas on.Displayed if zero point is adjusted.Signal is stable, turn test gas off.Input: gas concentration (value) Start zeroingInput: reference factor (value) Correction with RConfirmation with ENTER Displayed for 2 s after successful calibration.Actual measuring value and unitSpan gas has been recognized.Programming the alarm relaysIn this menu you can set parameters of the alarm relays A1 and A2:▪Alarm thresholds▪High or low alarm▪Latching (HOLD) or not latching (AUTO RESET)▪Coil active (ACTIVE) or not active (PASSIVE) in case of alarmFigure 8: Alarm relay settingCurrent output in Service ModeIf you operate the module as a SIL device EN 50402 or IEC 61508, 2 mA output in theservice mode is mandatory.Changing the operation mode - Control Module or Common Alarm ModuleReading the bridge voltageSwitching the sensor power supply offNo changeof operationmodeMEASURING MODEChange of operation mode: start-upIn this menu the operation mode of theStatox 503 can be selected.The ex - works setting of the Statox 503is Control Module.Please find detailed information forrunning the Statox 503 in CommonAlarm mode in the detailed manual onour homepage !Active in the programs for Statox 501HRC, ARE, LCIR, MCIR, CO2 and PIDsensor heads.Displays either the actual bridge voltageor the actual concentration.Time-out 60 minutes!Active in the programs for Statox 501HRC, ARE, LCIR, MCIR, CO2 and PIDsensor heads.It disconnects the sensor head for servicepurposes.In this menu the time-out is not active!MEASURING MODEConnecting the sensor headThe sensor head power supply must be OFF before connecting a sensor head!Short circuits on the terminals or selection of a wrong program may destroy the sensor head.!Figure 10: Connections sensor heads Statox 501/Sand Statox 505/5065 6 7 8 9 10 11 12 5 6 7 89 10 11 123 4 5 o. 4 1 o. 2Figure 12: Connections sensor heads Statox 501 HRC, ARE, LCIR, MCIR, CO 2 and PID2 wire mode9 10 11 12INP 5 6 78 910 1112I INP5 6 783 wire mode Statox 505/506Figure 11: Connections sensor head Statox 501 Infratox /Infratox HS5 wire mode 3 wire modeThe sensor heads Statox 501/S and Statox 505/506 for toxic gases and oxygen are operated as 4 – 20 mA transmitters in 2 wire mode. The Statox 505/506 sensor heads can alternatively be operated in 3 wire mode. This way you can differentiate between service mode (2 mA) and system failure (0 mA). The standard application of sensor heads running in voltage mode is 3 wire mode. Starting with 750 m length of cable, Compur recommends to generally operate in the 5 wire mode. The two additional “sense” lines measure the sensor supply voltage and compensate for voltage drops due to long cable or extreme temperatures.The sensor head Statox 501 Infratox/ Infratox HS for combustible gases and CO 2 requires 3 or 4 wires (2 ground wires) for proper operation. 9 10 11 12 21 22 23 24The sensor heads Statox 501/S and Statox 505/506must be operated in connection with an intrinsically safe repeater if they are installed in classified area, zone 1 or zone 2. Detailed information regarding the operation with an intrinsically safe repeater can be found in the manuals of the corresponding sensor heads. Connect the shield of the sensor head cable to the grounding bar. Both, grounding bar and DIN Rail must be grounded.Please find more information for connecting other sensor heads in the detailed manual on !Control Module – Status diagramInput from Sensor or transmitter SystemStatusCurrentoutputBussignalDisplayLEDs RelaysA1 A2 S ON A1 1)A2 1)SF4-20 mA orbridge voltageNormal 4 – 20 mA --- Measuring value OFF OFF OFF ON active active active 4-20 mA orbridge voltageAlarm 1 4 - 20 mA A1 Measuring value ON OFF 2)OFF ON passive active 2)active 4-20 mA orbridge voltageAlarm 2 4 - 20 mA A2 Measuring value OFF 2)ON OFF ON active 2)passive active22 mA or mV over range Over Range 22 mA 2)Full scaleflashing2) 2) OFF ON 2) 2) active0 mA orError statusSystem failure 0 mA SF Error code OFF OFF ON ON active active passive2 mA or Service ModeServiceMode 3)2 mA 1)---SERVICE MODEor menuOFF OFF flashing ON active active active1)Ex-works setting, can be changed by user.2)Depending on actual alarm status.3)Priority ranking: Service Mode > SF > (A1 / A2 / Over range)Common Alarm Module – Status diagramBus input SystemstatusCurrentoutputDisplayLEDs 4)Relays 4)A1 A2 S ON A1 1)A2 1)SF--- Normal 4 mA COMMONOKOFF OFF OFF ON active active activeA1 Alarm 1 12 mA COMMONALARM 1ON OFF OFF ON passive active activeA2 Alarm 2 16 mA COMMONALARM 2OFF ON OFF ON active passive activeSF Systemfailure 0 mACOMMONFAILUREOFF OFF ON ON active active passive--- Service 4) 2 mA 1)Menu OFF OFF flashing ON active active active1)Ex-works setting, can be changed by user.4)The listed LED and relay status describes an isolated alarm event. In case of multiple alarm eventscombinations are possible.The priority ranking for display and current output is: Service Mode > A2 > A1 > SFError messagesIn case the display stays dark, check the polarity and the voltage of the power supply. The internal fuse may be damaged. In any case critical errors lead to system failure.Display Nature Description MeasuresERROR 1 Critical Short circuit in the sensor head cable. Check wiring and connections. Push R button.ERROR 2 Critical Cable interruption (in current mode) or aconnected sensor head transmits 0 mA.Check wiring and connections.Automatic reset after error correction.ERROR 3 Critical Cable too long(only in voltage mode)Check wiring and connections.Check selected program.Connect sensor head and push R button. Eventuallychange to 5 wire installation.ERROR 4 Critical Sensor power supply voltagecannot be controlled.Push the R button. If error persists contact yourCompur service partner.ERROR 5 Critical Cable interruption (only in voltage mode)or sensor defective.As a precaution the sensor has beenpowered off.Jumper mounted in 3 wire mode?Check connections, connect sensor head and pushReset button to restart.Check power supply and voltage.Eventually change the sensor.ERROR 6NoncriticalZero not found during time limit.Check connections.If gas is present use zero gas.Push the Enter button and try again.The old zero value remains valid.ERROR 7NoncriticalZero shift out of specifications.Check if gas is present.Push the Enter button and try again.The old zero value remains valid.Eventually replace the sensor.ERROR 8NoncriticalSensor sensitivity too low.No gas or no plateau found duringcalibration.Check if gas is on and gas adapter tightly connected.Push ENTER and try again.The old gain value remains valid.Eventually replace the sensor.ERROR 9-12 Critical Hardware error Contact your Compur service partner.ERROR 13 Critical Output current out of specifications. Check connections.Terminals 3/4: evaluation unit or jumper mounted? Jumper mounted in 3 wire mode?If error persists contact your Compur service partner.ERROR 14-15 Critical Hardware error Contact your Compur service partner.GAS CONC ERRORNonCriticalThe result ofgas concentration x response factoris out of range.Check gas concentration and response factor entry.Eventually select another span gas concentration.Push the Enter button and try again.The old gain value remains valid.Eventually replace the sensor.CALIB. FAILEDNonCriticalThe result ofsensor signalgas concentration response factoris too low.Check gas concentration and response factor entry.Eventually select higher span gas concentration.Push the Enter button and try again.The old gain value remains valid.Eventually replace the sensor.CALIB. REQUIREDNoncriticalNo valid calibration data, measurementwith default sensor parameters (at start-up or after change of program).Blanket with ENTER. “NO VALID CAL.DATA“ appearsfor 5 s. Calibrate with span gas!Technical DataProduct name: Statox 503 Control ModuleManufacturer: COMPUR Monitors GmbH & Co. KG, D-81539 Munich Power supply: 24 ± 2 VDC, max. 200 mA Power consumption: max. 5 WCurrent rating: max. 8 A on communication bus Operating temperature: -10° C to +60° C (14°F to 140°F) Storage temperature: -30°C to +60°C (-22°F to 140°F) Pressure: 900 to 1100 hPaHumidity: 0% to 99% r. H. (non-condensing) Display: 2 x 8 digit LCD with backlightHousing: Polyamide, protection class IP 20Connections: 24 terminals, can take cable diameters up to 2.5 mm 2 Relays: 2 x alarm, 1 x system failure Relays contact: 250 VAC, 8Amin. burden ≥ 12V, 10 mA (contact material: silver-nickel 90/10) System failure relay: In normal operation active (coil active), make contact (NO) is closed Analog output: 0 mA in case of system failure2 or 4 mA in service mode, programmable4 - 20 mA in measuring mode, tolerance ± 2 % at -10°C to + 50°C22 mA at over range Max. Burdon: 700 Ohm Installation: 35 mm DIN-Rail CE-Marking: EN 61326-1:2013Functional safety: SIL 2 capable according to IEC 61508 Dimension: 45 x 103 x 115 mm (1.77 x 4.06 x 4.52 “) Weight: 275 gSpecifications are subject to change without notice, and are provided only for comparison of products. The conditions, under which our products are used, are beyond our control. Therefore, the user must fully test our products and/or information to determine suitability for any intended use, application, condition or situation. All information is given without warranty or guarantee. Compur Monitors disclaims any liability, negligence or otherwise, incurred in connection with the use of the products and information. Any statement or recommendation not contained herein is unauthorized and shall not bind Compur Monitors. Nothing herein shall be construed as a recommendation to use any product in conflict with patents covering any material or device or its use. No license is implied or in fact granted under the claims of any patent. Instruments are manufactured by Compur Monitors GmbH & Co. KG, Munich. The General Conditions of Supply and Service of Compur Monitors GmbH & Co. KG are applicable.45 mm (1.77 ")103 m m (4.06 ")。
利海尔轨道受力推挽机商品说明书
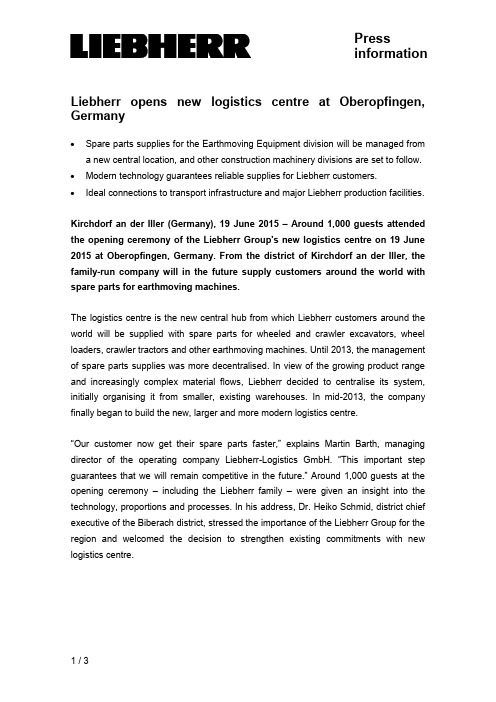
Pressinformation Liebherr opens new logistics centre at Oberopfingen, Germany∙Spare parts supplies for the Earthmoving Equipment division will be managed froma new central location, and other construction machinery divisions are set to follow. ∙Modern technology guarantees reliable supplies for Liebherr customers.∙Ideal connections to transport infrastructure and major Liebherr production facilities.Kirchdorf an der Iller (Germany), 19 June 2015 –Around 1,000 guests attended the opening ceremony of the Liebherr Group's new logistics centre on 19 June 2015 at Oberopfingen, Germany. From the district of Kirchdorf an der Iller, the family-run company will in the future supply customers around the world with spare parts for earthmoving machines.The logistics centre is the new central hub from which Liebherr customers around the world will be supplied with spare parts for wheeled and crawler excavators, wheel loaders, crawler tractors and other earthmoving machines. Until 2013, the management of spare parts supplies was more decentralised. In view of the growing product range and increasingly complex material flows, Liebherr decided to centralise its system, initially organising it from smaller, existing warehouses. In mid-2013, the company finally began to build the new, larger and more modern logistics centre.“Our customer now get their spare parts faster,” explains Martin Barth, managing director of the operating company Liebherr-Logistics GmbH. “This important step guarantees that we will remain competitive in the future.” Around 1,000 guests at the opening ceremony –including the Liebherr family –were given an insight into the technology, proportions and processes. In his address, Dr. Heiko Schmid, district chief executive of the Biberach district, stressed the importance of the Liebherr Group for the region and welcomed the decision to strengthen existing commitments with new logistics centre.Fully automated material flow and maximum supply reliabilityThe new central warehouse has an area of 47,000 m² – about the size of six football pitches – space for about 100,000 different spare parts for the Earthmoving Equipment division. Parts are taken into and out of stock in the automatic warehouse areas - which can be up to 36 m high - by energy-efficient operating machines. The responsible persons at Liebherr-Logistics GmbH employ extremely short throughput times: “Our modern warehouse technology and order picking systems make it possible to ship 1,600 individual orders to many European countries – almost all of them on the day the order is received,” explains Martin Barth. Redundant IT systems, the ability to conduct preventative maintenance work during ongoing operations and modern fire prevention measures guarantee maximum supply reliability.Strategically important location, best transportation connections and future potentialThe location at Oberopfingen was chosen deliberately. Not only is the site directly next to the A7 autobahn, it is also in the immediate neighbourhood of the major production site for Liebherr earthmoving machines at Kirchdorf an der Iller. Other plants from the construction machinery and components divisions in France, Austria and Switzerland are also not far away. “We consi dered, analysed and evaluated various locations for the warehouse,” Martin Barth continues. “In the end, Oberopfingen was the favourite.” In the final expansion phase in a few years time, the site should grow to a total of 360,000 m², or more than 50 football pitches, and hall space will be created to secure the logistics processes for the decades ahead. In the long term, the Liebherr Group is planning to merge the spare parts logistics of other construction machinery divisions in Oberopfingen.Captionsliebherr-logistics-centre-1-300dpi.jpgThe new Liebherr logistics centre at Oberopfingen near Kirchdorf an der Illerliebherr-logistics-centre-2-300dpi.jpgMartin Barth, managing director of Liebherr-Logistics GmbH (right), and logistics manager Kilian Ribheggeliebherr-logistics-centre-3-300dpi.jpgManual warehouse area and shipping at the new Liebherr logistics centre at Oberopfingenliebherr-logistics-centre-4-300dpi.jpgSpare parts are automatically moved on roller conveyors.Contact personKristian KüppersCorporate CommunicationPhone: +49 7351 41-2708E-mail:******************************Published byLiebherr-International Deutschland GmbHBiberach / Riss, Germany。
IDT 高精度宽量程单相电能计量芯片 90E21 22 23 24 数据手册

高精度宽量程单相电能计量芯片90E21/22/23/24数据手册版本:32010年12月13日6024 Silver Creek Valley Road, San Jose, CA 95138© 2010 Integrated Device Technology, Inc.免责声明艾迪悌有限公司(IDT)保留无需事先通知,可随时更改其产品或规格的权利,以改进设计或性能,提供最好的产品。
IDT公司对使用所述任何非IDT公司产品所包含的电路不承担任何责任。
IDT公司对使用所述电路不会侵犯第三方专利权或其它权利不作任何陈述。
IDT公司不对任何受专利或其它权利保护的许可作任何明示或暗示。
生命支持政策除非与IDT公司签订明确的书面协议,否则不得将IDT公司产品用作生命支持设备或系统的关键部件。
1.生命支持设备或系统是指此种设备或系统(a) 拟外科植入人体,或者(b)用于生命支持或维持,其正常使用时发生的故障可能会给用户带来严重伤害。
2.关键部件是指生命支持设备或系统中任何发生故障时,可能导致生命支持设备或系统故障,或影响其安全性或有效性的部件。
目录产品特性 (6)应用 (6)产品说明 (6)功能模块图 (7)1引脚分布 (9)2引脚说明 (10)3功能描述 (12)3.1计量动态范围 (12)3.2起动与潜动功率 (12)3.3电能寄存器 (12)3.4N线计量与防窃电功能 (13)3.4.1计量模式与L、N线电流采样增益配置 (13)3.4.2防窃电模式 (13)3.5测量与过零输出功能 (14)3.5.1测量功能 (14)3.5.2过零输出 (14)3.6校表方法 (15)3.7复位 (15)4芯片接口 (16)4.1SPI接口 (16)4.1.1四线模式 (16)4.1.2三线模式 (17)4.1.3超时和保护 (18)4.2严重报警WARNOUT引脚 (18)4.3芯片与MCU隔离情况下的低成本功能实现 (18)5寄存器 (19)5.1寄存器列表 (19)5.2状态和特殊寄存器 (20)5.3计量/测量的校准和配置 (24)5.3.1计量校准和配置寄存器 (24)5.3.2测量校准寄存器 (31)5.4电能寄存器 (36)5.5测量量寄存器 (40)6电气参数 (46)6.1技术指标 (46)6.2SPI接口时序 (48)6.3上电复位时序 (49)6.4过零信号时序 (50)6.5失压时序 (51)6.6脉冲输出 (51)6.7极限参数和热特性 (52)订货信息 (53)表格列表表-1 芯片功能列表 (6)表-2 引脚说明 (10)表-3 有功计量的误差 (12)表-4 无功计量的误差 (12)表-5 起动与潜动阈值设置 (12)表-6 电能寄存器 (12)表-7 计量模式 (13)表-8 芯片的测量格式 (14)表-9 四线模式的读写结果 (18)表-10 三线模式的读写结果 (18)表-11 寄存器列表 (19)表-12 SPI时序特征 (48)表-13 上电复位参数 (49)表-14 过零信号参数 (50)表-15 失压参数 (51)图形列表图-1 90E21功能模块图 (7)图-2 90E22功能模块图 (7)图-3 90E23功能模块图 (8)图-4 90E24功能模块图 (8)图-5 产品引脚分布 (顶视图) (9)图-6 四线模式的读序列 (16)图-7 四线模式的写序列 (16)图-8 三线模式的读序列 (17)图-9 三线模式的写序列 (17)图-10 4线SPI时序图 (48)图-11 3线SPI时序图 (48)图-12 上电复位时序图 (49)图-13 过零时序图 (50)图-14 失压时序图 (51)图-15 脉冲输出宽度 (51)90E21/22/23/24高精度宽量程单相电能计量芯片IDT 和IDT 标识是IDT公司的注册商标产品特性计量特性·芯片计量特性完全符合中国国家标准GB/T17215.211-2006 (idt IEC62052-11)、GB/T17215.321-2008 (idt IEC62053-21)、GB/T 17215.323-2008 (idt IEC62053-23)的要求;芯片可应用于1级或2级单相有功电能表和2级单相无功电能表;·计量动态范围5000:1 (典型值)内,有功电能准确度优于0.1%,无功电能准确度优于0.2%;·片上电压基准源的温度系数为15ppm/℃(典型值);·在5000:1的动态范围内只需单点校准有功电能,无功电能不需要校准;·小电流情况下支持仪表常数加倍校验以节省校验时间;·电参量测量功能:电压/电流有效值、平均有功/无功/视在功率、频率、功率因数和相角的引用误差都小于±0.5%;·正反向有功/无功电能均具有独立的电能寄存器,有功/无功电能可由脉冲输出,亦可由电能寄存器读出以适应不同的应用场合;·可编程的起动和潜动功率阈值;·L 线和N 线电流采样回路采用独立的ADC,并具有不同的回路增益;电流回路可选用锰铜或电流互感器(CT)进行采样,电压回路可选用电阻分压网络或电压互感器(PT)进行采样;·L 线和N 线的计量方式可配置:防窃电模式(较大功率)、L 模式(固定L 线)、L+N 模式(单相三线适用)和灵活模式(通过寄存器指定);·防窃电模式下,L 和N 线功率比较阈值可编程设置;其它特性·3.3V 单电源供电,工作电压范围:2.8~3.6V ;3.0~3.6V 电压范围内保证芯片的计量准确度;芯片数字输入引脚可兼容5V 系统;·内置滞回型上电复位电路;·标准的SPI 接口或简化的三线准SPI 接口,对所有寄存器的操作均为24个周期;·具有参数校验功能和可编程中断输出功能,能输出IRQ 中断信号和WarnOut 报警信号;·具有可配置的失压检测和过零输出功能;·各通道输入范围:-电压通道(增益为1倍时):120µVrms ~600mVrms ;-L 线电流通道(增益为24倍时):5µVrms ~25mVrms ;-N 线电流通道(增益为1倍时):120µVrms ~600mVrms ;·可编程的L 线电流通道增益:1, 4, 8, 16, 24倍; 可编程的N 线电流通道增益:1, 2, 4倍;·提供L 线和N 线的失调补偿;·CF1和CF2分别输出有功和无功电能脉冲,可用于校表或电能累计;·晶振频率:8.192MHz ;芯片内置10pF 电容,无需外置电容;·绿色SSOP28 封装;·工作温度范围:-40℃~+85℃。
CITILED LED lamp 503系列产品说明书

1. Scope of Application
These specifications apply to chip type LED lamp, CITILED, model CL-503T-SD-T.
2. Part code CL-503 T -SD-T Series 503:Multi-color Ultra small size Lighting color T type R: High brightness Red G : High brightness Green B: High brightness Blue Diffusion SD: Diffused Shipping mode T Taping (stan
260°C Max 220°C
60~70sec
Reference
3) Use a soldering iron of 25W or smaller. Adjust the temperature of the soldering iron below 350°C.
4) Force or stress must not be applied to the resin portion while soldering. 5) Finish soldering within 3 seconds.
2) The temperature profile at the top surface of the parts is recommended as shown below.
3) It is requested that products should be handled after their temperature has dropped down to the normal room temperature.
AIG-501 系列 4 埠 Modbus 到 Azure 進階 IIoT 閘道器说明书

AIG-501系列4埠Modbus到Azure進階IIoT閘道器,配備Intel Atom®四核1.91GHz處理器,Azure IoT Edge特色與優點•支援通用MQTT用戶端•支援Azure/AWS cloud使用內建裝置SDK的MQTT連接•支援Modbus RTU/ASCII/TCP主控裝置/用戶端•支援Azure IoT Edge•支援使用ThingsPro Proxy實用程序輕鬆裝置開通•提供堅固的OTA功能,以預防軟體升級時出現系統故障•配備安全啟動以防止惡意軟體注入攻擊•-40°C至70°C操作溫度範圍•LTE Cat.提供4種美國、歐盟和亞太地區型號認證簡介AIG-501系列進階IIoT閘道器專為工業IoT應用設計,尤其適用在艱困的操作環境中分散式和無人值守的站點。
閘道器實施Modbus RTU/TCP主控裝置/用戶端通訊協定,可有助您輕鬆從Modbus裝置收集資料。
此外,Azure IoT Edge軟體已預先下載並與AIG-501完全整合,藉由使用Azure雲端解決方案達到輕鬆、可靠且安全的感測器到雲端連接,以完成資料擷取和裝置管理。
通過使用ThingsPro Proxy實用程序,裝置開通過程比過往都更為容易。
多虧於強大的OTA功能,再也無須擔心軟體升級過程中出現系統故障。
啟用安全啟動功能,尤其是在啟動過程,您可預防惡意軟體攻擊。
外觀規格ComputerCPU Intel Atom®Processor E3845(2M Cache,1.91GHz) Graphics Controller Intel®HD GraphicsDRAM4GB DDR3LStorage Pre-installed32GB CFast eMMCPre-installed OS Linux Debian9,Kernel4.9No.of Tags Supported2048Computer InterfaceTPM TPM v2.0USB2.0USB2.0hosts x2,type-A connectorsWi-Fi Antenna Connector RP-SMA x2(AIG-501-T-AZU-LX)Cellular Antenna Connector SMA x2(excluding AIG-501-T-AZU-LX)GPS Antenna Connector SMA x1(excluding AIG-501-T-AZU-LX) Expansion Slots mPCIe slots x1(AIG-501-T-AZU-LX)Buttons RebootReset to factory defaultDigital Input DIs x4Digital Output DOs x4Number of SIMs1SIM Format MiniVideo Output VGA x1,15-pin D-sub connector(female) Ethernet InterfaceMagnetic Isolation Protection 1.5kV(built-in)10/100/1000BaseT(X)Ports(RJ45connector)4Ethernet Software FeaturesIndustrial Protocols Modbus TCP Client(Master)Generic MQTTAzure IoT DeviceAWS IoT CoreAzure IoT EdgeOPC UA ServerSparkplug B ClientConfiguration Options Web Console(HTTP/HTTPS)ThingsPro Proxy UtilityTime Management NTP Server/ClientGPSSerial InterfaceConsole Port1x4-pin headerNo.of Ports4Connector DB9maleBaudrate300bps to921.6kbpsData Bits7,8Flow Control ADDC(automatic data direction control)for RS-485 Parity NoneEvenOddSpaceMarkStop Bits1,2Serial SignalsRS-232TxD,RxD,RTS,CTS,DTR,DSR,DCD,GNDRS-422Tx+,Tx-,Rx+,Rx-,GNDRS-485-2w Data+,Data-,GNDRS-485-4w Tx+,Tx-,Rx+,Rx-,GNDSerial Software FeaturesIndustrial Protocols Modbus RTU/ASCII MasterDigital InputsConnector Spring-type Euroblock terminalSensor Type Dry contactDry Contact Off:openOn:short to GNDIsolation NoneDigital OutputsConnector Spring-type Euroblock terminalCurrent Rating10mA(max.)total for all channelsI/O Type SinkIsolation NoneCellular InterfaceCellular Standards LTE Cat.4Band Options(US)LTE Band2(1900MHz)/LTE Band4(1700MHz)/LTE Band5(850MHz)/LTE Band12(700MHz)/LTE Band13(700MHz)/LTE Band14(700MHz)/LTE Band66(1700MHz)/LTE Band71(600MHz)1UMTS/HSPA Band2(1900MHz)/Band4(1700MHz)/Band5(850MHz)Carrier Approval:Verizon,AT&TBand Options(EU)LTE Band1(2100MHz)/LTE Band3(1800MHz)/LTE Band7(2600MHz)/LTE Band8(900MHz)/LTE Band20(800MHz)/LTE Band28A(700MHz)UMTS/HSPA Band1(2100MHz)/Band3(1900MHz)/Band8(900MHz)Band Option(APAC)LTE Band1(2100MHz)/LTE Band3(1800MHz)/LTE Band5(850MHz)/LTE Band8(900MHz)/LTE Band9(1700MHz)/LTE Band18(850MHz)/LTE Band19(850MHz)/LTE Band26(850MHz)/LTE Band28(700MHz)UMTS/HSPA Band1(2100MHz)/Band5(850MHz)/Band6(800MHz)/Band8(900MHz)/Band19(800MHz)GPS InterfaceReceiver Types GPS/GLONASS/BeiDou/Galileo/QZSSAccuracy0.8mAcquisition-147dBmSensitivity Cold starts:-145dBmTracking:-160dBmLED IndicatorsSystem Power x1Storage x1LAN2per port(10/100/1000Mbps)Serial2per port(Tx,Rx)Azure IoT EdgeVersions Supported v1.4.8Authentication Methods Manual/Connection StringDPS/TPMDPS/Symmetric EncryptionDPS/X.509Certificate1.此波段不在可選的天線支援範圍。
- 1、下载文档前请自行甄别文档内容的完整性,平台不提供额外的编辑、内容补充、找答案等附加服务。
- 2、"仅部分预览"的文档,不可在线预览部分如存在完整性等问题,可反馈申请退款(可完整预览的文档不适用该条件!)。
- 3、如文档侵犯您的权益,请联系客服反馈,我们会尽快为您处理(人工客服工作时间:9:00-18:30)。
Notes: 1. All dimensions are in millimeters (inches). 2. Tolerance is ±0.25(0.01") unless otherwise noted. 3. Lead spacing is measured where the leads emerge from the package. 4. Specifications are subject to change without notice.
Description
The High Efficiency Red source color devices are made with Gallium Arsenide Phosphide on Gallium Phosphide Orange Light Emitting Diode.
Package Dimensions
High Efficiency Red
L-503IDT
SPEC NO: DSAD0525 APPROVED: WYNEC
REV NO: V.6 CHECKED: Allen Liu
DATE: JUL/06/2007 DRAWN: Y.H.CHEN
PAGE: 3 OF 5 ERP: 1101009432
Electrical / Optical Characteristics at TA=25°C
Symbol λpeak λD [1] Δλ1/2 C VF [2] IR Parameter Peak Wavelength Dominant Wavelength Spectral Line Half-width Capacitance Forward Voltage Reverse Current Device High Efficiency Red High Efficiency Red High Efficiency Red High Efficiency Red High Efficiency Red High Efficiency Red Typ. 627 625 45 15 2 2.5 10 Max. Units nm nm nm pF V uA Test Conditions IF=20mA IF=20mA IF=20mA VF=0V;f=1MHz IF=20mA VR = 5V
Part No. Dice Lens Type Iv (mcd) [2] @ 10mA Min. L-503IDT High Efficiency Red (GaAsP/GaP) RED DIFFUSED 3 Typ. 6 Viewing Angle [1] 2θ1/2 110°
Notes: 1. θ1/2 is the angle from optical centerline where the luminous intensity is 1/2 the optical centerline value. 2. Luminous intensity/ luminous Flux: +/-15%.
Units mW mA mA V
SPEC NO: DSAD0525 APPROVED: WYNEC
REV NO: V.6 CHECKED: Allen Liu
DATE: JUL/06/2007 DRAWN: Y.H.CHEN
PAGE: 2 OF 5 ERP: 1101009432
元器件交易网
SPEC NO: DSAD0525 APPROVED: WYNEC
REV NO: V.6 CHECKED: Allen Liu
DATE: JUL/06/2007 DRAWN: Y.H.CHEN
PAGE: 1 OF 5 ERP: 1101009432
元器件交易网
Selection Guide
Notes: 1. 1/10 Duty Cycle, 0.1ms Pulse Width. 2. 2mm below package base. 3. 5mm below package base.
High Efficiency Red 75 30 160 5 -40°C To +85°C 260°C For 3 Seconds 260°C For 5 Seconds
元器件交易网
SPEC NO: DSAD0525 APPROVED: WYNEC
REV NO: V.6 CHECKED: Allen Liu
DATE: JUL/06/2007 DRAWN: Y.H.CHEN
PAGE: 4 OF 5 ERP: 1101009432
元器件交易网
SPEC NO: DSAD0525 APPROVED: WYNEC
REV NO: V.6 CHECKED: Allen Liu
DATE: JUL/06/2007 DRAWN: Y.H.CHEN
PAGE: 5 OF 5 ERP: 1101009432
元器件交易网
5x5mm SQUARE TOP LED LAMP
Part Number: L-503IDT High Efficiency Red
Features
LOW POWER CONSUMPTION. ULTRA BRIGHTNESS IS AVAILABLE. WIDE VIEWING ANGLE. RELIABLE AND RUGGED. EXCELLENT UNIFORMITY OF LIGHT OUTPUT. IDEAL AS FLUSH MOUNTED PANEL INDICATORS. LONG LIFE - SOLID STATE RELIABILITY. RoHS COMPLIANT.
Notes: 1.Wavelength: +/-1nm. 2. Forward Voltage: +/-0.1V.
Absolute Maximum Ratings at TA=25°C
Parameter Power dissipation DC Forward Current Peak Forward Current [1] Reverse Voltage Operating/Storage Temperature Lead Solder Temperature [2] Lead Solder Temperature [3]