金属切削过程中地三个变形区
机械制造技术基础课后部分习题及答案

2-2切削过程的三个变形区各有何特点?它们之间有什么关联?答:切削塑性金属材料时,刀具与工件接触的区域可分为3个变形区:①第一变形区(基本变形区):是切削层的塑性变形区,其变形量最大,常用它来说明切削过程的变形情况;②第二变形区(摩擦变形区):是切屑与前面摩擦的区域;③第三变形区(表面变形区):是工件已加工表面与后面接触的区域。
它们之间的关联是:这三个变形区汇集在切削刃附近,此处的应力比较集中而且复杂,金属的被切削层就在此处与工件基体发生分离,大部分变成切屑,很小的一部分留在已加工表面上。
2-3分析积屑瘤产生的原因及其对加工的影响,生产中最有效的控制积屑瘤的手段是什么?答:在中低速切削塑性金属材料时,刀—屑接触表面由于强烈的挤压和摩擦而成为新鲜表面,两接触表面的金属原子产生强大的吸引力,使少量切屑金属粘结在前刀面上,产生了冷焊,并加工硬化,形成瘤核。
瘤核逐渐长大成为积屑瘤,且周期性地成长与脱落。
积屑瘤粘结在前刀面上,减少了刀具的磨损;积屑瘤使刀具的实际工作前角大,有利于减小切削力;积屑瘤伸出刀刃之外,使切削厚度增加,降低了工件的加工精度;积屑瘤使工件已加工表面变得较为粗糙。
由此可见:积屑瘤对粗加工有利,生产中应加以利用;而对精加工不利,应以避免。
消除措施:采用高速切削或低速切削,避免中低速切削;增大刀具前角,降低切削力;采用切削液。
2-7车削时切削合力为什么常分解为三个相互垂直的分力来分析?分力作用是什么?答:(1)车削时的切削运动为三个相互垂直的运动:主运动(切削速度)、进给运动(进给量)、切深运动(背吃刀量),为了实际应用和方便计算,在实际切削时将切削合力分解成沿三个运动方向、相互垂直的分力。
(2)各分力作用:切削力是计算车刀强度、设计机床主轴系统、确定机床功率所必须的;进给力是设计进给机构、计算车刀进给功率所必需的;背向力是计算工件挠度、机床零件和车刀强度的依据,与切削过程中的振动有关。
2-11背吃刀量和进给量对切削力和切削温度的影响是否一样?为什么?如何运用这一定律知道生产实践?答:不一样。
机械制造知识

8、CA6140型卧式车床。C类别代号、A结构特性代号(结构不同)、6组别代号(落地及卧式车床组)、1系别代号(卧式车床系)、40主参数(最大车削直径400mm)。MG1432A型高精度万能外圆磨床。 M类别代号(磨床类)、G通用特性(高精度)、1组别代号(外圆磨床组)4系别代号(万能外圆磨床系)、32主参数(最大磨削直径320mm)、A重大改进顺序号(第一次重大改进)。
11、六点定位原理:用六个定位支撑点与工件接触,并保证支撑点合理分布,每个定位支撑点限制工件的一个自由度,便可将工件六个自由度完全限制,工件在空间的位置也就唯一地被确定。完全定位:限制工件全部六个自由度。不完全定位:允许少于六点的定位。过定位:工件的某一个自由度同时被一个以上的定位支撑点重复限制。欠定位:工件的定位支撑点数少于应限制的自由度数。
3、车刀角度的定义:前角(正交平面内测量的前面与基面之间的夹角)、后角(正交平面内测量的主后面与切削平面的夹角,表示主后面的倾斜程度,一般为正值)、主偏角(基面内测量的主切削刃在基面上的投影与进给运动方向的夹角,一般为正值)、副偏角(基面内测量的副切削刃在基面上的投影与进给反方向的夹角,一般为正值)、刃倾角(切削平面内测量的主切削刃与基面的夹角)。
9、机床常用技术性能指标:机床工艺范围、机床技术参数(尺寸参数、运动参数、动力参数)。
10Байду номын сангаас选用加工中心需考虑的因素:加工中心种类、根据加工表面及曲面复杂程度决定其联动轴数、根据工件尺寸范围考虑其主要尺寸以及型号、其他功能(检测加工表面粗糙度、自适应控制功能)。工件在机床上的装夹方法:找正法装夹工件(根据工件的一个或几个表面用划针或指示表找正工件准确位置后再进行夹紧)、夹具装夹工件(工件装在夹具上,不再进行找正,便能直接得到准确加工位置的装夹方法)。
第十七章 金属切削加工基础知识

图17-17 刀具磨损的三个阶段
• 第五节
工件材料的切削加工性
• 一、 衡量工件材料切削加工性的指标 • 由于切削加工性是对材料多方面的综合评价,所以很难用一个简单的 物理量来精确规定和测量。在生产和实验中,常取某一项指标来反映 材料切削加工性的某一具体方面,最常用的是vT和Kr。 • vT——指在一定的切削条件下,当刀具的寿命为T分钟时,切削某种材 料所允许的最大的切削速度。vT越高,表示材料的切削加工性越好。 通常取T=60min,则vT可写作v60。 • Kr——称为相对加工性,一般以正火状态45钢的v60为基准,写作 (v60),然后将其它各种材料的v60与之相比所得的比值。当Kr>1时, 表示该材料比45钢容易切削。反之,则比45钢难切削。常用工件材料 的相对加工性可分为八级,见表17-2。
• 五、切削热与切削温度 • 1.切削热的来源: • ⑴是正在加工和已加工表面所发生的弹性和塑性变形而产生的大量的热, 是切削热的主要来源; • ⑵是切屑与刀具前刀面之间的摩擦产生的热; • ⑶是工件与刀具后刀面之间的摩擦产生的热。切削时所消耗的功约有98% -99%转换为切削热。 • 2.切削温度 • 切削温度过高,会使刀头软化,磨损加剧,寿命下降;工件和刀具受热膨 胀,会导致工件精度超差影响加工精度,特别是在加工细长轴、薄壁套时, 更应注意热变形的影响。 ⑴ • 在生产实践中,为了有效地降低切削温度,常应用切削液,切削液能带走 大量的热,对降低切削温度的效果显著,同时还能起到润滑、清洗和防锈的 作用。常见的切削液有: • ⑴切削油 主要是各种矿物油、动植物油和加入油性、极压添加剂的混 合油。其润滑性能好,但冷却性能较差,主要用来减少磨损和降低工件的表 面粗糙度,一般用于低速精加工,如铣削加工和齿轮加工等。 • ⑵水溶液 主要成分是水并加入防锈剂、表面活性剂或油性添加剂。其 热导率高、流动性好,主要起冷却作用,同时还具有防锈、清洗等作用。 • ⑶乳化液 由乳化油加水稀释而成,呈乳白色或半透明状,有良好的流 动性和冷却作用,是应用最广泛的切削液。低浓度的乳化液用于粗车、磨削。 高浓度乳化液用于精车、钻孔和铣削等。在乳化液中加入硫、磷等有机化合 物,可提高润滑性。适用于螺纹、齿轮等精加工。
机械制造技术基础-卢秉恒 答案 第二章

变,而切削宽度aw则随ap的增大正比增大,由于
aw的变化差不多与M和ξ无关,所以ap对Fz的影响
成正比关系。
2-8背吃刀量和进给量对切削力的影响有何不 同? (2)
而f增大一倍,Fz约增大0.8倍,因为f增大,切 削功增大,切削力也相应增大,而f增大,切削厚度 也成正比增大,ac增大,ξ减小,μ减小,又会使切 削力减小,这正反两方面的作用,使切削力的增大 与f不成正比。
磨钝标准决定刀具寿命的长短(正常磨损情况下)。
但是受切削速度,工件材料,刀具材料和刀具几何形状
影响,同一磨钝标准下,刀具寿命是不相同的。
2-16简述车刀、铣刀、钻头的特点。(1)
答:1.车刀是金属切削中使用最广泛的刀具,可完
成工作的外圆,端面,切槽或切断等不同的加工工序。
一般情况下车刀都只有一条主切削刃的单刃刀具,加工 时工作的主运动是工件的旋转运动,进给运动为车刀的 直线运动。
答:粗加工时进给量的选择应考虑机床进给机构的强 度、车刀刀杆的强度和刚度、硬质合金或陶瓷刀片的
强度和工件的装夹刚度等。上述情况可以采用增大刀
尖圆弧半径,提高切削速度的方法来保证粗糙度的前
提下选择较大的进给量。
2-20 如果选定切削用量后,发现所需的功率 超过机床功率时,应如何解决?
答:要么调换较大功率的机床、要么根据所选定的
取
(3)确定切削速度:切削速度可通过 计算,也可查表,本题
查表取
主轴转速 按机床书说明书取 ,实际切削速度为
2、半精工步 (1)确定背吃刀量 : 。
(2)确定进给量 :根据表面粗糙度和刃口圆角半径,并预估
切削速度 ,从表中查出 。按机床说明书中实有的进给量,
机械制造技术基础期末试题及答案

1.机床误差是由机床的制造误差、安装误差和使用中的磨损引起的,其中对加工精度影响最大的三种几何误差是主轴回转误差、导轨误差和传动误差。
2.典型的刀具磨损过程分为初期磨损、正常磨损和急剧磨损阶段。
3.精加工基准的选择原则应遵循如下原则:统一基准、基准重合、互为基准和自为基准等原则。
4.工件的装夹过程就是定位和夹紧的综合过程。
5.在切削加工中,用于描述切削机理的指标是切削层及切削层参数,切削层参数包括切削层公称厚度h D、切削层公称宽度b D和切削面积,其中切削面积=h D× b D。
6.由于工件材料以及切削条件的不同,切削的变形程度也不同,因而所产生的切屑也不同,切屑的可分为带状切屑、节状切屑、粒状切屑和崩碎切屑四大类。
其中当切削塑性材料,切削速度极低,刀具前角较小时,往往产生节状切屑。
7.切削变形程度有三种不同的表示方法,即变形系数、相对滑移和剪切角。
8.在车削外圆时,切削力可以分解为三个垂直方向的分力,即主切削力,进给力抗力和切深抗力,其中在切削过程中不作功的是切深抗力。
1. 从形态上看,切屑可以分为带状切屑、挤裂切屑、单元切屑和崩碎切屑2. 切削过程中金属的变形主要是剪切滑移,所以用相对滑移(剪应变)的大小来衡量变形程度要比变形系数精确些。
3. 利用自然热电偶法可测得的温度是切削区的平均温度。
4. 刀具一次刃磨之后,进行切削,后刀面允许的最大磨损量(VB),称为磨钝标准。
5. 工件经一次装夹后所完成的那一部分工艺过程称为安装。
6. 靠前刀面处的变形区域称为第二变形区,这个变形区主要集中在和前刀面接触的切屑底面一薄层金属内。
7. 系统性误差可以分为常值性系统性误差和变值性系统性误差两种1.刀具后角是后刀面与切削平面间的夹角2.衡量切削变形的方法有变形系数与滑移系数两种,当切削速度提高时,切削变形(减少)。
3.精车铸铁时应选用(YG3);粗车钢时,应选用(YT5)。
4.当进给量增加时,切削力(增加),切削温度(增加)。
第十七章 金属切削加工基础知识

图17-15 切削合力与分力
(1)主切削力Fc 垂直于基面且与切削主运动速度方向一致。机床动 力的主要依据。消耗功率95%以上。 (2)背向力Fp 在基面内,与切削进给速度方向垂直。易使工件变 2 形,同时还会引起振动,使工件的表面粗糙度值增大。 (3)进给力Ff 在基面内,与进给速度方向平行。是验证进给系统 零件强度和刚度的依据。 (17-6) 由图17-15可知 F2=F2c+ F2p+ F2f 2. 影响切削力的大小的因素: 影响切削力的大小的因素: (1)工件材料的影响 )工件材料的影响:一般材料的强度、硬度愈高,韧性、塑性愈好, 愈难切削,切削力也愈大。 (2)切削用量的影响:当ap和f增加时,切削力也增大。在车削加工时, )切削用量的影响: 当ap加大一倍,Fc也增大一倍;而f加大一倍,Fc只增大68%~86%,因 此,从切削力角度考虑,加大进给量比加大背吃刀量有利。 (3)刀具几何参数的影响 前角和后角对切削力的影响最大。 ) 前角愈大切屑变形小,切削力也小。 后角愈大,刀具后刀面与工件加工表面间的摩擦愈小。 改变主偏角的大小,可以改变轴向力与径向力的比例(特别是加工细长工 件时,经常采用较大的主偏角以使径向力减小)
• 二、影响材料切削加工性的因素 • 1.影响工件材料切削性能的主要因素 • (1)硬度、强度 一般来讲,材料的硬度、强度愈高,则切削力愈大, 消耗切削功率愈多,切削温度愈高,刀具磨损愈快,因此,其切削加 工性差。 • (2)塑性 材料的塑性愈大,则切削变形愈大,刀具容易发生磨损。 在较低的切削速度下加工塑性材料还容易出现积屑瘤使加工表面粗糙 度值增大,且断屑困难,故切削加工性不好。但材料塑性太差时,得 到崩碎切屑,切削力和切削热集中在切削刃附近,刀具易产生崩刃, 加工性也较差。 • (3)另外,材料的热导率、化学成分、金相组织等都对材料的切削加 工性有一定的影响。 • 2.改善材料切削加工性的主要措施 • (1)调整材料的化学成分 在钢中加入S、P、Pb、Ca等元素能起 到一定的润滑作用并增加材料的热脆性,从而改善其切削加工性。 • (2)对工件材料进行适当的热处理 利用热处理可改善低碳钢和高 碳钢的切削加工性。例如,对低碳钢和进行正火处理,或降低塑性, 提高硬度,使其切削加工性得到改善。对高碳钢和工具钢进行球化退 火,使网状、片状的渗碳体组织球状渗碳体,降低了材料的硬度,使 切削加工较易进行。对于出现白口组织的铸件,可在950~1000℃下 进行长时间退火,降低硬度, 达到改善切削加工性的目的。
金属切削过程中地三个变形区
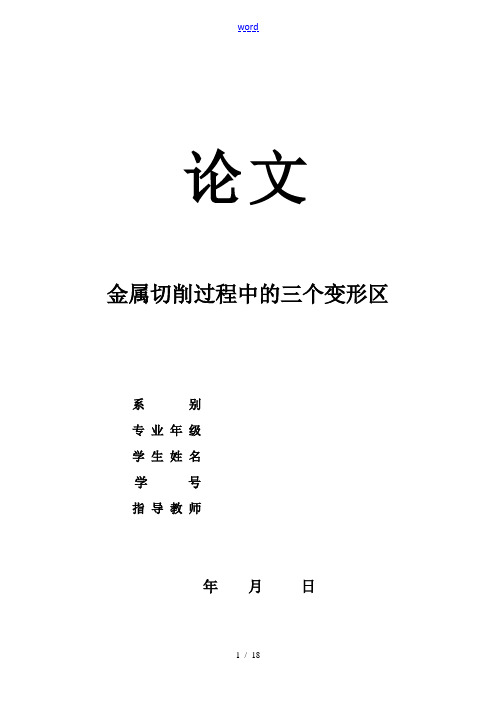
论文金属切削过程中的三个变形区系别专业年级学生姓名学号指导教师年月日金属切削过程中的三个变形区摘要:金属切削过程是指道具与工件相互作用形成切屑的过程,本文主要表示了金属切削加工过程中的三个变形区的形成与相互联系,并分析了与这三个变形区有关的反映金属变形程度的相关参数,同时加以总结。
关键词:金属切削,三个变形区,金属变形程度Abstract: the process of metal cutting refers to tools and the workpiece interact to form a cutting process, this paper mainly describes the process of metal machining three deformation zone was formed and interconnected, and analyzed and the three deformation zone related to reflect the extent of metal distortion of the relevant parameters, at the same time to sum up.Keywords:metal cutting, three deformation zone, extent of metal distortion引言金属切削过程是机械制造过程的一个重要组成局部。
金属切削过程是指将工件上多余的金属层,通过切削加工被刀具切除而形成切屑并获得几何形状、尺寸精度和外表粗糙度都符合要求的零件的过程。
在这一过程中,始终存在着刀具切削工件和工件材料抵抗切削的矛盾,从而产生一系列现象,如切削变形、切削力、切削热与切削温度以与有关刀具的磨损与刀具寿命、卷屑与断屑等。
对这些现象进展研究,揭示其在的机理,探索和掌握金属切削过程的根本规律,从而主动地加以有效的控制,对保证加工精度和外表质量,提高切削效率,降低生产本钱和劳动强度具有十分重大的意义。
金属切削过程中的三个变形区
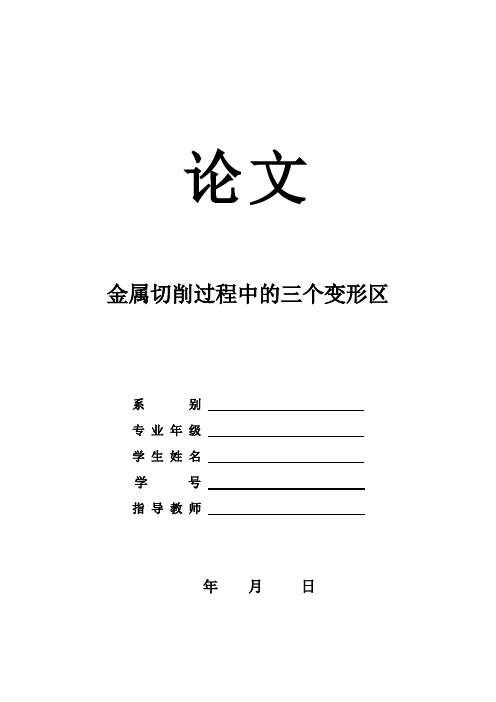
论文金属切削过程中的三个变形区系别专业年级学生姓名学号指导教师年月日金属切削过程中的三个变形区摘要:金属切削过程是指道具与工件相互作用形成切屑的过程,本文主要叙述了金属切削加工过程中的三个变形区的形成及相互联系,并分析了与这三个变形区有关的反映金属变形程度的相关参数,同时加以总结。
关键词:金属切削,三个变形区,金属变形程度Abstract: the process of metal cutting refers to tools and the workpiece interact to form a cutting process, this paper mainly describes the process of metal machining three deformation zone was formed and interconnected, and analyzed and the three deformation zone related to reflect the extent of metal distortion of the relevant parameters, at the same time to sum up.Keywords:metal cutting, three deformation zone, extent of metal distortion引言金属切削过程是机械制造过程的一个重要组成部分。
金属切削过程是指将工件上多余的金属层,通过切削加工被刀具切除而形成切屑并获得几何形状、尺寸精度和表面粗糙度都符合要求的零件的过程。
在这一过程中,始终存在着刀具切削工件和工件材料抵抗切削的矛盾,从而产生一系列现象,如切削变形、切削力、切削热与切削温度以及有关刀具的磨损与刀具寿命、卷屑与断屑等。
对这些现象进行研究,揭示其内在的机理,探索和掌握金属切削过程的基本规律,从而主动地加以有效的控制,对保证加工精度和表面质量,提高切削效率,降低生产成本和劳动强度具有十分重大的意义。
- 1、下载文档前请自行甄别文档内容的完整性,平台不提供额外的编辑、内容补充、找答案等附加服务。
- 2、"仅部分预览"的文档,不可在线预览部分如存在完整性等问题,可反馈申请退款(可完整预览的文档不适用该条件!)。
- 3、如文档侵犯您的权益,请联系客服反馈,我们会尽快为您处理(人工客服工作时间:9:00-18:30)。
论文金属切削过程中的三个变形区系别专业年级学生姓名学号指导教师年月日金属切削过程中的三个变形区摘要:金属切削过程是指道具与工件相互作用形成切屑的过程,本文主要叙述了金属切削加工过程中的三个变形区的形成及相互联系,并分析了与这三个变形区有关的反映金属变形程度的相关参数,同时加以总结。
关键词:金属切削,三个变形区,金属变形程度Abstract: the process of metal cutting refers to tools and the workpiece interact to form a cutting process, this paper mainly describes the process of metal machining three deformation zone was formed and interconnected, and analyzed and the three deformation zone related to reflect the extent of metal distortion of the relevant parameters, at the same time to sum up.Keywords:metal cutting, three deformation zone, extent of metal distortion引言金属切削过程是机械制造过程的一个重要组成部分。
金属切削过程是指将工件上多余的金属层,通过切削加工被刀具切除而形成切屑并获得几何形状、尺寸精度和表面粗糙度都符合要求的零件的过程。
在这一过程中,始终存在着刀具切削工件和工件材料抵抗切削的矛盾,从而产生一系列现象,如切削变形、切削力、切削热与切削温度以及有关刀具的磨损与刀具寿命、卷屑与断屑等。
对这些现象进行研究,揭示其在的机理,探索和掌握金属切削过程的基本规律,从而主动地加以有效的控制,对保证加工精度和表面质量,提高切削效率,降低生产成本和劳动强度具有十分重大的意义。
总之,金属切削过程的优劣,直接影响机械加工的质量、生产率与生产成本。
因此,必须进行深入的研究。
一、切屑形成过程及变形区的划分1、切削变形金属的切削过程与金属的挤压过程很相似。
金属材料受到刀具的作用以后,开始产生弹性变形;虽着刀具继续切入,金属部的应力、应变继续加大,当达到材料的屈服点时,开始产生塑性变形,并使金属晶格产生滑移;刀具再继续前进,应力进而达到材料的断裂强度,便会产生挤裂。
2、变形区的划分大量的实验和理论分析证明,塑性金属切削过程中切屑的形成过程就是切削层金属的变形过程。
切削层的金属变形大致划分为三个变形区:第一变形区(剪切滑移)、第二变形区(纤维化)、第三变形区(纤维化与加工硬化)。
3、切屑的形成及变形特点1)第一变形区(近切削刃处切削层产生的塑性变形区)金属的剪切滑移变形切削层受刀具的作用,经过第一变形区的塑性变形后形成切屑。
切削层受刀具前刀面与切削刃的挤压作用,使近切削刃处的金属先产生弹性变形,继而塑性变形,并同时使金属晶格产生滑移。
在下图中,切削层上各点移动至AC线均开始滑移、离开AE线终止滑移,在沿切削宽度围,称AC是始滑移面,AE是终滑移面。
AC、AE之间为第—变形区。
由于切屑形成时应变速度很快、时间极短,故AC、AE面相距很近,一般约为0.02一0.2mm,所以常用AB滑移面来表示第—变形区,AB面亦称为剪切面。
剪切面AB与切削速度Vc之间的夹角称为剪切角。
作用力Fr与切削速度Vc之间的夹角ω称为作用角。
第一变形区就是形成切屑的变形区,其变形特点是切削层产生剪切滑移变形。
2)第二变形区(与前刀面接触的切屑层产生的变形区)金属的挤压磨擦变形经过第一变形区后,形成的切屑要沿前刀面方向排出,还必须克服刀具前刀面对切屑挤压而产生的摩擦力。
此时将产生挤压摩擦变形。
应该指出,第一变形区与第二变形区是相互关联的。
前刀面上的摩擦力大时,切屑排出不顺,挤压变形加剧,以致第一变形区的剪切滑移变形增大。
3)第三变形区(近切削刃处已加工表面产生的变形区)金属的挤压磨擦变形已加工表面受到切削刃钝圆部分和后刀面的挤压摩擦,造成纤维化和加工硬化。
需要指出的是,由于刀刃有钝圆半径rb,整个切削层厚度ac中,将有一层金属 a无法沿OM方向滑移,而是从刀刃钝园部分O点下面挤压过去,即切削层金属在O点处分离为两部分。
已加工表面的形成过程二、切削变形程度的度量方法1、相对滑移ε相对滑移ε是用来量度第1变形区滑移变形的程度。
如下图,设切削层中A'B'线沿剪切面滑移至A"B"时的距离为△y,事实上△y很小,故可认为滑移是在剪切面上进行,其滑移量为△s。
则相对滑移ε表示为:ε=△s△y=cotφ+tan(φ-γ0)2、变形系数∧h变形系数∧h是表示切屑的外形尺寸变化大小的一个参数。
如下图所示,切屑经过剪切变形、又受到前刀面摩擦后,与切削层比较,它的长度缩短、厚度增加,这种切屑外形尺寸变化的变形现象称为切屑的收缩。
变形系数∧h表示切屑收缩的程度,即∧h=lclch =hchhD>1lc\hD————切削层长度和厚度;lch\hch————切屑长度和厚度。
从上图可知,剪切角 变化对切屑收缩的影响, 增大剪切面AB 减短,切屑厚度hch 减小,故∧h 变小。
它们之间的关系如下:∧h=hch hD=cot φcos γ0+sin γ0从上面两个公式可知,剪切角与前角γ0是影响切削变形的两个主要因素。
如果增大前角γ0和剪切角,使相对滑移ε、变形系数∧h 减小,则切削变形减小。
注意:由于切削过程是一个非常复杂的物理过程,切削变形除了产生滑移变形外,还有挤压、摩擦等作用,而ε值主要从剪切变形考虑;而∧h 主要从塑性压缩方面分析。
所以,ε与∧h 都只能近似地表示切削变形程度。
三、剪切角的确定剪切角是影响切削变形的一个重要因素。
若能预测剪切角的值,则对了解与控制切削变形具有重要意义。
为此,许多学者进行了大量研究,并推荐了若干剪切角的计算式。
按最少能量原则来确定剪切角φ的计算式为:φ=450+γ02 -β2按最大剪应力的理论,求出剪切角φ的计算式为:φ=π4+γ0-β0从上面公式可看出:与γ0、β有关。
增大前角γ0、减小摩擦角β,使剪切角增大,切削变形减小,这一规律已被普遍用于生产实践中。
从上面公式也可看出:第2变形区产生的摩擦对第1变形区剪切变形的影响规律。
四、总结切削加工过程中刀具与工件之间的关系十分复杂,如果将三个变形区联系起来,当切削层金属进入第一变形区时,晶粒因压缩而变长,因剪切滑移而倾斜。
当切削层金属逐渐接近刀刃时,晶粒更伸长,成为包围刀刃周围的纤维层,最后在O 点断裂,一部分金属成为切屑沿前刀面流出,另一部分金属绕过刀刃沿后刀面流出,并继续经受变形而成为已加工表面的表层。
因此,已加工表面表层的金属纤维被拉伸得更长更细,其纤维方向平行于已加工表面。
这个表层的金属具有与基体组织不同的性质,所以称为加工变质层。
由此可见,三个变形区是要联系地去进行分析的,只单独研究其中一个区是无法了解它们在金属切削过程中所体现出来的研究价值的。
一、切屑形成过程及变形区的划分1、切削变形金属的切削过程与金属的挤压过程很相似。
金属材料受到刀具的作用以后,开始产生弹性变形;虽着刀具继续切入,金属部的应力、应变继续加大,当达到材料的屈服点时,开始产生塑性变形,并使金属晶格产生滑移;刀具再继续前进,应力进而达到材料的断裂强度,便会产生挤裂。
2、变形区的划分大量的实验和理论分析证明,塑性金属切削过程中切屑的形成过程就是切削层金属的变形过程。
切削层的一、切屑形成过程及变形区的划分1、切削变形 金属的切削过程与金属的挤压过程很相似。
金属材料受到刀具的作用以后,开始产生弹性变形;虽着刀具继续切入,金属部的应力、应变继续加大,当达到材料的屈服点时,开始产生塑性变形,并使金属晶格产生滑移;刀具再继续前进,应力进而达到材料的断裂强度,便会产生挤裂。
2、变形区的划分 大量的实验和理论分析证明,塑性金属切削过程中切屑的形成过程就是切削层金属的变形过程。
切削层的金属变形大致划分为三个变形区:第一变形区(剪切滑移)、第二变形区(纤维化)、第三变形区(纤维化与加工硬化)。
三个变形区3、切屑的形成及变形特点1)第一变形区(近切削刃处切削层产生的塑性变形区)金属的剪切滑移变形切削层受刀具的作用,经过第一变形区的塑性变形后形成切屑。
切削层受刀具前刀面与切削刃的挤压作用,使近切削刃处的金属先产生弹性变形,继而塑性变形,并同时使金属晶格产生滑移。
切屑形成过程在图(a)中,切削层上各点移动至AC线均开始滑移、离开AE线终止滑移,在沿切削宽度围,称AC是始滑移面,AE是终滑移面。
AC、AE之间为第一变形区。
由于切屑形成时应变速度很快、时间极短,故AC、AE面相距很近,一般约为0.02-0.2mm,所以常用AB滑移面来表示第一变形区,AB面亦称为剪切面。
nextpage剪切面AB与切削速度Vc之间的夹角φ称为剪切角。
作用力Fr与切削速度Vc之间的夹角ω称为作用角。
第一变形区就是形成切屑的变形区,其变形特点是切削层产生剪切滑移变形。
2)第二变形区(与前刀面接触的切屑层产生的变形区)金属的挤压磨擦变形经过第一变形区后,形成的切屑要沿前刀面方向排出,还必须克服刀具前刀面对切屑挤压而产生的摩擦力。
此时将产生挤压摩擦变形。
应该指出,第一变形区与第二变形区是相互关联的。
前刀面上的摩擦力大时,切屑排出不顺,挤压变形加剧,以致第一变形区的剪切滑移变形增大。
3)第三变形区(近切削刃处已加工表面产生的变形区)金属的挤压磨擦变形已加工表面受到切削刃钝圆部分和后刀面的挤压摩擦,造成纤维化和加工硬化。
二、切削变形程度的度量方法相对滑移1、相对滑移ε相对滑移ε是用来量度第1变形区滑移变形的程度。
如上图,设切削层中A'B'线沿剪切面滑移至A"B"时的距离为△y,事实上△y很小,故可认为滑移是在剪切面上进行,其滑移量为△s。
则相对滑移ε表示为:2、变形系数∧h变形系数∧h是表示切屑的外形尺寸变化大小的一个参数。
如下图所示,切屑经过剪切变形、又受到前刀面摩擦后,与切削层比较,它的长度缩短、厚度增加,这种切屑外形尺寸变化的变形现象称为切屑的收缩。
变形系数∧h表示切屑收缩的程度,即nextpage从上图可知,剪切角φ变化对切屑收缩的影响,φ增大剪切面AB减短,切屑厚度h ch 减小,故∧h变小。
它们之间的关系如下:从上面两个公式可知,剪切角φ与前角γ0是影响切削变形的两个主要因素。
如果增大前角γ0和剪切角φ,使相对滑移ε、变形系数∧h减小,则切削变形减小。