基于Deform3D的高速车削加工仿真研究
基于deform—3d车削TC4加工过程仿真

基于deform—3d车削TC4加工过程仿真作者:陈卓来源:《科技视界》2016年第19期[摘要]Deform-3D是一套基于工艺模拟系统的有限元仿真(FEM)软件,是模拟3D材料流动的理想工具。
它不仅鲁棒性好,而且易于使用。
借助于该模拟分析环境,能够对切削过程中切削条件以及加工过程中的其他因素产生的影响进行研究。
应用DEFORM-3D自带的切削仿真模型,分析加工过程中工件对不同刀具的影响,以及对切削力、切削温度、切削应力结果进行分析。
模拟结果对减少产品试验、降低开发成本、缩短开发新产品及新工艺的时间等方面都具有重大意义。
[关键词]车削;Deform-3D;切削力;切削温度;切削参数0引言金属切削过程是一个非常复杂的工艺过程,它涉及到弹性力学、塑性力学、断裂力学、热力学、摩擦学等多个学科,刀具形状,温度分布、刀具磨损等因素都会对切削过程产生重要影响。
因此利用传统的解析方法,很难对切削过程进行分析和研究,但随着现代制造技术和计算机软件技术的不断进步,出现了很多针对金属切削过程进行数值模拟和仿真的软件,如DEFORM、ANSYS、ABAQUS等等,为金属切削过程仿真提供了非常有效的方法和技术手段。
本文选择三维有限元软件DEFORM,以硬质合金刀具切削钛合金TC4作为研究对象,对切削过程进行仿真,利用控制变量的方法得出了刀片在不同切削参数下的切削力、切削温度、以及切削应力的影响。
1有限元模型的建立1.1几何模型及仿真参数设置使用有限元分析软件DEFORM-3D模拟分析车削钛合金的加工过程,应用DEFORM-3D 中的Machining(Cutting)模块进行建模。
建立的切削模型如图1所示。
本分析中是直接从Deform封装的刀片库中选取刀片,所选取的刀片代号是CNMA432。
模拟过程中关于网格划分方面,DEFORM-3D提供了两种网格划分方式,分别为相对网格划分方式和绝对网格划分方式。
本文中工件采用的是绝对网格类型,最大网格单元尺寸和最小网格单元尺寸之比为7。
DEFORM的车削仿真案例
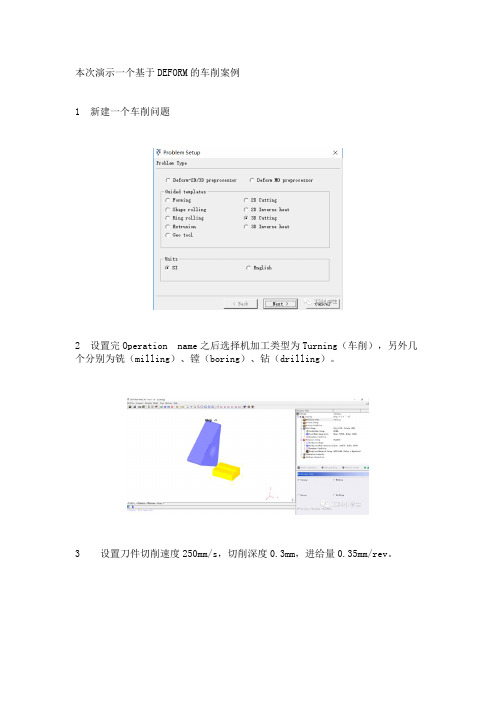
本次演示一个基于DEFORM的车削案例1 新建一个车削问题2 设置完Operation name之后选择机加工类型为Turning(车削),另外几个分别为铣(milling)、镗(boring)、钻(drilling)。
3 设置刀件切削速度250mm/s,切削深度0.3mm,进给量0.35mm/rev。
4 设置环境温度为20℃,空气对流传热系数保持默认,摩擦系数设为剪切摩擦0.5,刀件与工件的传热系数设为45.5 选择系统内置的TNMA332刀具,当然用户也可以通过Define a new tool来导入自己的刀具模型,支持STL格式。
通过Edit position来调整刀具的位置。
6 选择车刀角度,Side cutting Angle(主偏角)back rake angle 前角side rake angle副前角,除了导入自带的参数,用户可以通过Create a new toolholder自己设置对应参数。
具体这些参数修改会有什么变化如下图所示:7 给车刀划分网格8 设置工件基本参数。
9 设置工件长度为7mm。
Curved model可以生成一个圆环。
当然也可以通过Import Geometry来自己导入工件模型。
10 给工件划分网格,设置最小单元尺寸为0.06mm,尺寸比例为7。
11 给工件赋予材料,通过Import material from liabrary从材料库中导入相应材料。
12 设置模拟步数为10000,每25步存储一次,规定切削长度为3.5mm,也就是工件的一半长度。
注意,当设置了切削长度,那么步数就无效了,可以尽可能往大了设,当满足切削长度之后程序自动停止。
下面的刀具磨损模型采用的Usui模型,具体参数需要参照实验校准,其与所使用的材料和车削工艺有关。
13 查看结果后处理可以查看切削过程中,应力,应变,温度等的变化以及切屑的形态。
等效应力的变化等效应变的变化温度的变化。
基于DEFORM-3D的钛合金车削加工过程分析-毕业论文
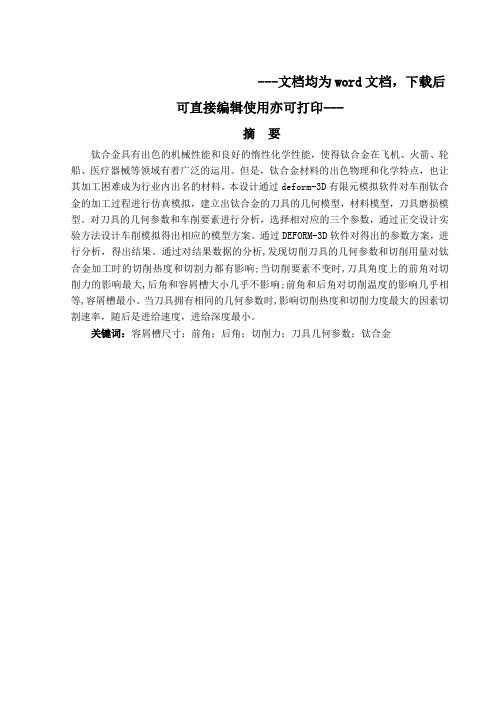
---文档均为word文档,下载后可直接编辑使用亦可打印---摘要钛合金具有出色的机械性能和良好的惰性化学性能,使得钛合金在飞机、火箭、轮船、医疗器械等领域有着广泛的运用。
但是,钛合金材料的出色物理和化学特点,也让其加工困难成为行业内出名的材料。
本设计通过deform-3D有限元模拟软件对车削钛合金的加工过程进行仿真模拟,建立出钛合金的刀具的几何模型,材料模型,刀具磨损模型。
对刀具的几何参数和车削要素进行分析,选择相对应的三个参数,通过正交设计实验方法设计车削模拟得出相应的模型方案。
通过DEFORM-3D软件对得出的参数方案,进行分析,得出结果。
通过对结果数据的分析,发现切削刀具的几何参数和切削用量对钛合金加工时的切削热度和切割力都有影响;当切削要素不变时,刀具角度上的前角对切削力的影响最大,后角和容屑槽大小几乎不影响;前角和后角对切削温度的影响几乎相等,容屑槽最小。
当刀具拥有相同的几何参数时,影响切削热度和切削力度最大的因素切割速率,随后是进给速度,进给深度最小。
关键词:容屑槽尺寸;前角;后角;切削力;刀具几何参数;钛合金目录1 绪论 (1)1.1本设计的目的、意义 (1)1.2本设计在国内外的发展概况及存在的问题 (2)1.3本设计应解决的主要问题 (3)2基于DEFORM-3D的钛合金车削加工过程分析 (3)2.1有限元模型的建立 (4)2.2刀具几何参数对切削力,切削温度影响的三维正交实验设计 (8)2.2.1 钛合金的车削参数选择 (8)2.2.2 正交设计变量的确定 (9)2.2.3正交试验设计方案 (9)2.2.4后处理结果对比分析 (10)2.2.5数据分析处理 (13)2.3切削用量对切削温度和切削力影响的三维正交试验分析 (15)2.3.1 钛合金的车削参数选择 (15)2.3.2 正交设计变量的确定 (15)2.3.3正交实验安排 (16)2.3.4后处理结果对比分析 (16)2.3.5数据分析处理 (20)3结论 (22)参考文献 (23)谢辞 (24)1 绪论在上世纪50年代初,钛合金被开发成为一种结构重要的金属,是具有出色的机械性能和良好的惰性化学性能的金属。
基于Deform3D加工中心钻削加工仿真研究

削 力 大 小 、 削 温度 的 分 布情 况 , 切 该仿 真 结 果 对 钻 削 . 艺效 果 的预 测和 优 化 具 有 现 实 的指 导 意 义 。 y -
关键 词 : e r D 高速 钻 削 D f m3 o
中 图分 类 号 :G 2 T 3 T 5 ;P 1
文 献 标 识码 : A
成 形 、 处 理 工 艺 , 加 工 过 程 中 因 工 件 材 料 、 具 材 热 对 刀 料 、 具 角 度 、 削 速 度 不 同 引 起 的 被 加 工 工 件 的 剪 切 刀 切
设 定 工 作 环 境 和 接 触 面 属 性 , 定 环 境 温 度 2 ℃ , 件 设 O 工 接 触 属 性 : 擦 因 数 0 5 导 热 系 数 4 /( ・K)3。 摩 .和 5W m [ 1 ( 工 件 的 设 定 : 件 属 性 为 塑 性 , 能 够 满 足 模 2) 工 在 拟 条 件 下 , 量 选 择 较 小 模 型 。 择 4 钢 作 为 工 件 的 材 尽 选 5
料Hale Waihona Puke 变形 、 削温 度 、 应力 等 因 素进行 分 析 , 正确 选择 切 内 是
刀具材 料 、 具 角度 和 切 削用 量 以及进 行 材料 加 工性 刀 分 析 的依 据 。
( ) 拟 条 件 设 定 : 共 运 算 步 数 15 0 , 储 增 3模 总 o 步 存 量 为每2 步存 一次 。 5 () 成 数据 库并完 成模 拟运算 。 4生
文 章 编号 :0 0— 9 82 1 )5— 0 8— 2 10 4 9 (0 0 0 0 1 0
钻 削 加 工 是 机 械 制 造 行 业 中 应 用 较 广 泛 的金 属 切
基于遗传算法BP神经网络的DEFORM-3D车削加工模拟优化

机床与液压
M ACHI NE T00L & HYDRAUL CS I
Ap . 2 2 r 01
Vo. 0 No 7 14 .
D I 1 .9 9 ji n 10 — 8 12 1.7 0 0 O : 0 3 6/. s.0 1 3 8 .0 20 .5 s
中图分类 号 :T 3 9 1 P 8 . 文献标 识码 :A 文章编号 :10 3 8 2 1 )7—13— 0 1— 8 1(0 2 6 4
Optm i a i n o i z to fDEFO RM - Tur i g M a h n n m u a i n s d o 3D nn c i i g Si l to Ba e n Ge tc Al o ih ne i g r t m BP ur lNe wo k Ne a t r
.
1 1 刀具和 工件 的建 立 以及 网格 划分 .
车削细长轴时 ,由于工件刚性 差 ,车刀的几何形 状对减小作用在工件上 的车削力 、减小工件弯曲变形
和振动 、减小车削热 的产生等均有 明显的影响。选择 时主要考 虑以下几点 : ( ) 由于 细 长轴 刚性 差 ,为 减 少 细长 轴 弯 曲, 1 要求径 向车削力越小越好 ,而刀具 的主偏 角是影 响径 向车削力 的主要 因素 ,在不影响刀具强度情况下 ,应 尽量增大车刀主偏角 。车刀 的主偏角取 8 。 9 。 0 ~ 3。 ( ) 为减少 径 向车削 分力 和车 削热 ,应 该选 择 2 较大 的前角 ,一般取 1 。 3 。 5 ~0。 ( )选择正刃倾 角 ,取 3 ~1 。 3 。 0 ,使车削 屑流 向 待加工表面 ,并使卷屑效果 良好 ,车刀也容易切人工
基于Deform3D的齿轮高速干式滚切过程模型及性能分析

基于D e f o r m 3D 的齿轮高速干式滚切过程模型及性能分析周 力 曹华军 陈永鹏 杨 潇重庆大学机械传动国家重点实验室,重庆,400044摘要:齿轮高速干式滚切工艺取消了切削油/液的使用,是一种绿色高效的齿轮制造工艺,其成形过程分析是提升该滚齿工艺性能的有效途径㊂基于金属切削工艺仿真软件D e f o r m 3D 建立了齿轮高速干式滚切过程的有限元仿真模型;进行了齿轮高速干式滚切材料去除过程的数值仿真分析,获得了不同参数条件下齿轮高速干式滚切过程中切屑的变形规律,以及切削力与切削温度的分布规律,分析并确定了影响滚切性能的主要参数㊂研究结果为齿轮高速干式滚切工艺参数优化提供了理论和方法支撑㊂关键词:高速干式滚切;仿真;过程模型;性能分析中图分类号:T G 61 D O I :10.3969/j.i s s n .1004‐132X.2015.20.002P r o c e s s S i m u l a t i o n M o d e l a n dP e r f o r m a n c eA n a l y s i s o fH i g h ‐s p e e dD r y G e a rH o b b i n g B a s e do nD e f o r m3D Z h o uL i C a oH u a j u n C h e nY o n g p e n g Y a n g Xi a o S t a t eK e y L a b o r a t o r y o fM e c h a n i c a lT r a n s m i s s i o n ,C h o n g q i n g U n i v e r s i t y ,C h o n g q i n g,400044A b s t r a c t :H i g h ‐s p e e d d r y g e a rh o b b i n g i sa k i n d o f g r e e n a n d e f f i c i e n t g e a r m a n u f a c t u r i n g p r o c e s s ,w h i c he l i m i n a t e d t h eu s eo f c u t t i n g o i l /l i q u i d .A n a l y z i n g t h e c u t t i n gp r o c e s so f g e a rh o b b i n gw a s a n e f f e c t i v ew a y t o i m p r o v e i t s p e r f o r m a n c e .B a s e d o n a p r o f e s s i o n a l F E Ms i m u l a t i o n s o f t w a r eD e -f o r m3D ,af i n i t ee l e m e n ts i m u l a t i o n m o d e lo f t h eh igh ‐s p e e dd r yg e a rh o b bi n gp r o c e s sw a se s t a b -l i s h e d ,an u m e r i c a l s i m u l a t i o no fm a t e r i a l r e m o v a l p r o c e s sw a s a c h i e v e d ,a n d t h e l a wo f c h i p d e f o r m a -t i o na n d t h e d i s t r i b u t i o no f c u t t i n g f o r c e a n d t e m p e r a t u r ew e r e g o t t e n ,t h em a i n p a r a m e t e r s a f f e c t i n gg e a rh o b b i n gp e r f o r m a n c ew e r e c o n f i r m e d .T h e a n a l y s e s p r o v i d e a n e f f e c t i v e s u p p o r t f o r t h e o p t i m i z a -t i o no f h i g h ‐s p e e dd r yg e a r h o b b i n gpa r a m e t e r s .K e y w o r d s :h i g h ‐s p e e dd r yg e a r h ob b i n g ;s i m u l a t i o n ;D e f o r m 3D p r oc e s sm ode l ;p e rf o r m a n c e a n a l -ys i s 收稿日期:20141022基金项目:国家高技术研究发展计划(863计划)资助项目(2012A A 040107);教育部新世纪优秀人才支持计划资助项目(N C E T ‐13‐0628);国家自然科学基金资助项目(51475058);机械传动国家重点实验室科研业务费专项(S K L MT ‐Z Z K T ‐2012M S 01)0 引言齿轮高速干式滚切工艺是滚齿加工工艺的发展方向,相比于传统湿式滚切工艺,它消除了切削油/液使用导致的生态环境污染和工人职业健康危害等问题,同时具有高效率㊁低能耗的特点,是一种绿色环保的齿轮制造工艺[1‐2]㊂但是,由于对齿轮高速干式滚切过程及性能特征研究的不足导致企业在实际生产过程中面临诸多问题,从而未能充分发挥齿轮高速干式滚切工艺的优势,因而亟需对该问题展开研究㊂齿轮高速干式滚切基于展成原理,由一系列切削刃断续切削成形,成形过程复杂㊂传统车间实验和数学解析方法成本高㊁实施难度大㊁周期长㊁计算复杂且研究目标单一,而有限元仿真分析方法具有成本低㊁耗时短㊁精确直观和条件可控的特点,在工程实践中获得了广泛的应用㊂针对金属切削加工过程及性能分析,国内外专家学者利用有限元分析软件D e f o r m 3D 开展了广泛研究,并在金属切削规律和工艺参数优化等方面取得了成果㊂B o u z a k i s 等[3]进行了滚齿仿真研究,对滚切工艺参数进行了优化㊂F r i d e r i k o s 等[4]研究了滚切过程中切屑冲击对刀刃边缘崩刃现象的影响,建立了滚齿切屑冲击理论㊂A t t a n a -s i o 等[5]研究了车削加工过程中刀具的磨损,并建立了刀具磨损量的预测方法㊂黄美霞等[6]开展了高速车削加工过程仿真研究,其研究结果对车削工艺效果的预测和优化具有现实的指导意义㊂高兴军等[7]研究了麻花钻钻削过程中切屑形成过程㊁钻削力大小和钻削温度的分布情况以及麻花钻主要几何参数对不锈钢钻削性能的影响规律,分析了切削用量对不锈钢钻削轴向力的影响规律,得到了钻削温度场和钻头磨损情况㊂宋健[8]开展了发动机缸体钻削仿真研究,并对发动机缸体钻削工艺和参数进行了优化㊂与一般切削加工相比较,齿轮高速干式滚切工艺涉及复杂的成形运动关系及几何成形过程㊂㊃5072㊃基于D e f o r m 3D 的齿轮高速干式滚切过程模型及性能分析周 力 曹华军 陈永鹏等Copyright ©博看网. All Rights Reserved.本文基于齿轮滚切原理,利用数学计算软件M a t h e m a t i c a 和三维建模软件P r o /E 建立齿轮高速干式滚切的运动关系和实体模型,并使用金属切削工艺仿真软件D e f o r m 3D 开展齿轮高速干式滚切过程模型及性能分析研究,通过结合工艺仿真实验和车间实验研究齿轮高速干式滚切过程中的切屑变形规律㊁切削力与应力分布和温度分布,对比研究分析干/湿式滚切下工件和刀具的温度变化规律㊂该研究可为高速干切滚齿机床热变形和工艺参数优化等提供支撑㊂1 齿轮高速干式滚切过程仿真模型1.1 滚切模型及运动关系齿轮滚切过程等效于一对相错轴渐开线圆柱齿轮啮合过程㊂基于展成原理,滚刀与工件齿轮按一定传动比回转过程中,由分布在滚刀基本蜗杆曲面上的一系列切削刃切除材料最终包络出渐开线齿形㊂同时,滚刀沿齿轮轴向进给加工出齿轮全齿宽㊂齿轮滚切属于多刃断续非自由斜角切削,其成形过程与滚刀刀齿的几何结构㊁滚切运动关系相关,且每一个刀齿都将在已形成的齿槽实体上切除一部分材料形成新的齿槽实体㊂根据上述分析,基于D e f o r m 3D 的齿轮高速干式滚切仿真实体模型和运动关系模型的建立过程如图1所示㊂(a )齿轮滚切(b)刀齿建模 (c)齿槽建模(d )D e f o r m 3D滚齿仿真图1 基于D e f o r m 3D 的齿轮高速干式滚切仿真实体模型及运动关系模型的建立1.1.1 滚刀单齿建模滚刀由形状相同的一系列刀齿按规律分布在其基本蜗杆螺旋面上形成㊂滚切过程中,各刀齿根据滚切原理相继从齿坯上断续切除材料,最终包络形成齿轮齿面,如图1a 所示㊂对齿轮高速干式滚切过程的研究可以针对各个刀齿进行仿真分析,由于各刀齿几何形状一致,因此滚刀建模可以简化为滚刀单齿建模㊂基于P r o /E 三维建模软件,根据滚刀轴向齿形建立前刀面轮廓,并结合滚刀后面与前面的角度关系通过混合拉伸可得到滚刀单齿的三维实体模型,如图1b 所示㊂1.1.2 齿槽建模当滚刀沿工件轴向进给到某一位置时,随着滚刀与齿轮工件相对回转,分布在滚刀基本蜗杆螺纹上的刀齿包络出齿轮齿形并形成齿槽㊂根据滚刀的进给位置,将齿槽的形成过程分为三个阶段,如图2所示:第一阶段为切入过程,指滚刀接触齿坯开始切削,直到齿坯顶部被切出完整的齿槽轮廓(图2);第二阶段为完整切削过程,指第一阶段结束直到滚切形成齿轮全齿宽的阶段;第三阶段为切出过程,指第二阶段结束直到滚刀脱离与齿坯接触㊂本文主要研究切削刃轨迹和工件接触长度保持不变的完整切削状态,该状态下齿槽形状特征为:已经出现一段完整的齿槽轮廓,但还未切到齿坯底部,如图2所示㊂图2 齿槽成形三阶段在完整切削过程中,不同刀齿对应的齿槽形状各不相同㊂根据滚刀和齿轮几何参数及其相对运动关系,利用数学计算工具M a t h e m a t i c a 编写滚切加工运动关系计算程序,获取了滚刀切削刃的滚切运动空间轨迹曲面簇㊂该曲面簇确定了被去除材料实体(未变形切屑)和成形齿槽的分割界面㊂与三维建模工具P r o /E 相结合,得到了滚刀不同单齿的切屑几何模型(图3)及切除相应材料后形成的齿槽实体模型(图1c)㊂滚刀上每个刀齿与对应齿槽都有一个相对的空间位置和运动关系,建立滚刀单齿和齿槽的滚切运动模型,将其在D e f o r m 3D 软件中实现,可得㊃6072㊃中国机械工程第26卷第20期2015年10月下半月Copyright ©博看网. All Rights Reserved.图3 不同刀齿切除材料的几何形状到基于D e f o r m3D的滚切过程仿真模型,见图1d㊂1.2 仿真理论1.2.1 材料的本构关系模型在利用D e f o r m3D进行金属切削加工工艺仿真的应用过程中,工件材料与断裂准则密切相关,考虑到齿轮材料为25C r M o4,其对应断裂准则选择J o h n s o n‐C o o k模型:σ=(A+Bεn)(1+C l n(ε㊃/ε㊃0))㊃(ε㊃/ε㊃0)α0(1-E(T*)m c)(1)T*=T-T r o o mT m e l t-T r o o m式中,σ为流动应力;ε为有效塑性应变;n为加工硬化指数;A为准静态条件下的屈服强度;B为应变硬化参数;C 为应变率强化参数;m c为热软化参数;E㊁α0为常数;T r o o m 为室温(一般取298K);T m e l t为熔点;ε㊃为有效应变率;ε/ε0为标准有效属性应变率㊂1.2.2 滚刀切屑之间的摩擦特性模型在滚切加工过程中,滚刀切屑之间的高压高温特性使得传统的库仑摩擦模型不再适用于描述滚刀与切屑之间的摩擦特性㊂S t i c k‐S l i p摩擦模型认为滚刀切屑之间的摩擦特性与切屑速度有关,在黏滞阶段产生较大的摩擦力㊂工艺仿真实验选择D e f o r m3D提供的剪切摩擦模型:f s=μk(2)式中,f s为摩擦力;k为剪切屈服应力;μ为摩擦因数㊂1.2.3 分离准则在进行金属切削工艺仿真时,分离准则是决定切削所产生的力和切削温度的基本准则㊂分离准则是指当张力作用在结合点上的节点时,节点的变化情况㊂D e f o r m3D切削仿真用到的分离准则为:当接触节点受到的张力或者压力大于0.1时接触点就会产生分离㊂2 实验结果与分析在对齿轮高速干式滚切工艺进行工艺仿真分析时,由于工件材料的塑性变形大,切削区发生流动,导致网格单元退化㊁畸变,需要在仿真过程中不断地对网格重新进行划分㊂完成前处理后,进入数值计算阶段,该过程由计算机依据D e-f o r m3D既定算法自动求解完成,通过后处理获得切屑变形㊁切削力和应力分布㊁刀具与工件接触区域温度场分布等结果㊂本研究分别对典型工况下的车间加工齿轮高速干式滚切和传统湿式滚切进行了仿真和对比分析㊂2.1 切屑变形在1.1节中基于数学计算工具M a t h e m a t i c a 与三维建模软件P r o/E建立了各刀齿切除材料(未变形切屑)的实体模型(图3),在实际滚切过程中,由于受热力耦合作用,材料将产生塑性变形㊂通过整理车间实验产生的切屑发现,大量相似形状的切屑重复出现,其主要原因是在完整滚切过程中滚刀在各个进给位置包络齿形时切除的材料(图3)一致㊂图4所示为仿真结果和实际滚切形成的切屑形态对比,两种方式得到的切屑形态十分相似,有效验证了仿真结果的可靠性㊂图4中,模数m=4mm,压力角α=20°,螺旋角β=0°,槽数n i=9,齿数比Z1∶Z2=1∶36,进给速度f= 100mm/m i n,滚刀转速n=600r/m i n,刀具材料为M35/T i C N,工件材料为25C r M o4㊂图4 D e f o r m3D仿真-7号刀齿切屑形成过程及切屑对比2.2 滚切过程切削力与切削应力由D e f o r m3D工艺仿真实验结果可以获得滚切过程中的载荷图㊂图5所示为工件z方向的切削力载荷,图5中,各项参数及材料同图4,可以看出,在进入切削的瞬间滚刀单齿的切削力急剧增大,这表现为滚切过程中的切削力冲击㊂此外,㊃7072㊃基于D e f o r m3D的齿轮高速干式滚切过程模型及性能分析 周 力 曹华军 陈永鹏等Copyright©博看网. All Rights Reserved.滚切过程中切削力曲线并不光滑,而是在一定振幅范围内高频波动的曲线,这是因为高速滚切过程中材料软化不均匀和变形不均匀㊂图5 z 方向的切削力载荷(-4号刀齿)图6为应力分布图,图6中,除滚刀转速㊁工件材料外,其他各项参数及刀具材料与图4相同㊂图6a 说明应力主要集中在刀刃与工件接触的位置,(a)应力分布云图(b)刀具接触区瞬时最大等效应力(n =600r /m i n ,工件材料25C r M o 4)(c)刀具接触区瞬时最大等效应力(n =900r /m i n ,工件材料25C r M o 4)(d)刀具接触区瞬时最大等效应力(n =900r /m i n ,工件材料45钢)图6 应力分布(-4号刀齿)图6b 说明应力与切削力一样呈现高频振动现象㊂在整个滚切过程中应力值在相对较小幅度内变化,趋势平缓㊂改变滚切速度后,应力值基本保持不变(图6b ㊁图6c ),但是在改变工件齿轮材料后应力值发生变化(图6d ),说明滚切速度对应力的影响较小,影响切削应力的主要因素是工件的材料㊂在干/湿式滚切实验中,两者的瞬时最大应力值基本一致,说明在齿轮材料相同的情况下,滚切过程中其他滚切参数不影响滚切应力值的大小㊂切削力的大小主要与切屑厚度即刀具与工件的接触面积相关㊂在切削相同材料㊁切下相同厚度的切屑时,切削力做功(P =F v c ,F 为切削力,v c为切削力方向的切削速度)与速度相关,在相同的切削时间内,高速干式滚切做功大于传统滚切做功,使得高速干式滚切中切屑和工件的温度上升较快㊂2.3 切削区温度场图7为工艺仿真实验获得的切削区温度分布云图,图7中,m =2mm ,α=20°,β=20°,n i =17,Z 1︰Z 2=3︰35,f =2mm/r ,n =900r /m i n ,刀具材料为M 35/T i C N ,工件材料为25C r M o 4㊂在不同区域切屑平均温度比工件平均温度高,尤其是在切削第二变形区域,切屑温度远高于工件上与其对应分离位置的温度,这是由于第二变形区域内工件材料变形量和滚刀工件间的摩擦力都很大,是发热最集中的区域㊂由图7可知,切屑是切削热的主要载体,高载热的切屑在重力作用下脱离切削区域进入机床并由排屑系统带出机床,将直接影响机床床身的温升,因此,合理的排屑系统对于高速干式滚切加工机床的设计十分必要㊂(a)切削区域温度分布云图(b)剪切变形区温度图7 切削区温度分布云图(-2号刀齿)对仿真结果进行后处理后获得切屑瞬时最高温度曲线(图8a)和滚刀刀刃瞬时最高温度曲线(图8b ),图8中的切削参数㊁齿轮参数㊁刀具材料和工件材料同图4㊂对比切屑和滚刀刀刃瞬时最高温度可知,滚刀刀刃温度远低于切屑温度,其主㊃8072㊃中国机械工程第26卷第20期2015年10月下半月Copyright ©博看网. All Rights Reserved.要原因是滚刀T i C N 涂层材料的传热系数小㊁摩擦因数小,由第二变形区塑性变形和刀齿前刀面与材料摩擦产生的热量不能及时传递到刀齿上㊂此外,工件接触变形区域在很短的时间内就达到了较高的温度,局部最高温度接近材料的熔点,此时材料不能保证其红硬性,很容易被切掉,而滚齿刀刃由于涂层传热系数小和摩擦因数小的特性,温度上升很慢,故依旧能够保证刀具的红硬性而具有良好的切削性能,这也是能够实现齿轮高速干式滚切的一个重要条件㊂(a)切屑瞬时最高温度曲线(b)刀刃瞬时最高温度曲线图8 温度曲线图9为干/湿式滚切下工件和刀具在切削区域的温度分布云图和瞬时最高温度曲线㊂图9中,干切条件为:m =2mm ,α=20°,β=20°,n i =17,Z 1∶Z 2=3∶35,f =2mm/r ,n =900r /m i n ,M 35/T i C N ,25C r M o 4,-2号齿;湿切条件为:m =2mm ,α=20°,β=20°,n i =14,Z 1︰Z 2=3︰35,f =1.6mm /r ,n =100r /m i n ,M 35/T i C N ,25C r M o 4,-1号刀齿㊂高速干式滚切和传统湿切都是在刀刃和工件的接触区域即切屑变形区域温度最高,但由于切削液的冷却作用,传统湿切的温度明显要低于高速干式滚切的温度㊂同理,由于缺少切削液的冷却作用且处于高速条件下,切削热易短时间内在切削区聚集,造成高速干式滚切下滚刀刀刃上瞬时最高温度也比传统湿切滚刀刀刃瞬时最高温高出2~3倍㊂通过对齿轮高速干式滚切和湿式滚切的切削性能对比,并结合前面对切削力的研究,发现齿轮实验高速干式滚切工艺对床身稳定性㊁排屑性能和刀具涂层性能的要求都远远超过了传统湿切滚齿㊂(a)湿切温度场(b)干切温度场(c)工件切削区域瞬时最高温度对比(d)刀刃瞬时最高温度对比图9 干/湿式滚切温度曲线对比3 结论(1)面向绿色高效的齿轮高速干式滚切工艺,建立了基于M a t h e m a t i c s ㊁三维实体建模和D e -f o r m 3D 的齿轮高速干式滚切过程仿真模型,该模型可以为齿轮高速干式滚切工艺分析提供有效的方法支持,从而为工艺参数优化提供理论和方法支撑㊂(2)进行了实验和仿真分析,仿真得到的切屑形态与实际滚切形成的切屑形态十分相似,从侧面验证了仿真实验方法的可靠性㊂(3)不同切削速度条件下,滚切相同工件材料产生的滚切力相近,因此工件材料的力学性能是影响滚切力的主要因素㊂(4)由于缺少切削油/液的冷却作用,高速干式滚切条件下滚刀刀齿最高温度为传统湿式滚切的2~3倍,该结果说明高速干切滚刀的热学性能是保证该工艺实现的重要条件㊂参考文献:[1] 陈永鹏,曹华军,李先广,等.高速干切滚齿机床热㊃9072㊃基于D e f o r m 3D 的齿轮高速干式滚切过程模型及性能分析周 力 曹华军 陈永鹏等Copyright ©博看网. All Rights Reserved.变形误差模型及试验研究[J ].机械工程学报,2013,49(7):36‐42.C h e nY o n g p e n g ,C a o H u a j u n ,L iX i a n g u a n g,e ta l .S t u d y o n M o d e l i n g a n dE x p e r i m e n t o fT h e r m a lD e -f o r m a t i o nE r r o r f o r H igh ‐s p e e dD r y H o b bi n g M a -c h i n e [J ].J o u r n a l o fM e c h a n i c a lE n g i n e e r i n g,2013,49(7):36‐42.[2] 李先广,刘飞,曹华军.齿轮加工机床的绿色设计与制造技术[J ].机械工程学报,2009,45(11):140‐145.L iX i a n g u a n g ,L i u F e i ,C a o H u a j u n .G r e e n D e s i g n a n d M a n u f a c t u r i n g T e c h n o l o g y o fG e a rC u t t i n g M a -c h i n e [J ].J o u r n a l o fM e c h a n i c a lE n g i n e e r i n g ,2009,45(11):140‐145.[3] B o u z a k i sK D ,F r i d e r i k o sO ,T s i a f i s I .F E M ‐s u p p o r -t e dS i m u l a t i o no fC h i p Fo r m a t i o na n dF l o wi nG e a r H o b b i n g o fS pu ra n d H e l i c a lG e a r s [J ].J o u r n a lo f M a n u f a c t u r i n g S c i e n c ea n d T e c h n o l o g y,2008(1):18‐26.[4] F r i d e r i k o sO ,M a l i a r i sG ,D a v i dCN ,e t a l .A n I n v e s -t i g a t i o no fC u t t i n g E d g eF a i l u r ed u e t oC h i p Cr u s h i nC a r b i d eD r y H o b b i n g U s i n g t h eF i n i t eE l e m e n t M e t h o d [J ].A d v a n c e d M a n u f a c t u r i n g T e c h n o l o g y,2011,57:297‐306.[5] A t t a n a s i oA ,C e r e t t i E ,R i z z u t i S ,e t a l .3DF i n i t eE l -e m e n tA n a l y s i sof T o o l W e a ri n M a c h i n i ng [J ].M a n u f a c t u r i n g T e c h n o l o g y ,2008,57:61‐64.[6] 黄美霞,武文革.基于D e f o r m 3D 的高速车削加工仿真研究[J ].工具技术,2008,42(10):70‐73.H u a n g M e i x i a ,W uW e n g e .F E MS i m u l a t i o n o fH i gh ‐s p e e dT u r n i n g B a s e do nD e f o r m ‐3D [J ].T o o lE n g i -n e e r i n g,2008,42(10):70‐73.[7] 高兴军,李萍,闫鹏飞,等.基于D e f o r m 3D 不锈钢钻削机理的仿真研究[J ].工具技术,2011,45(4):17‐20.G a oX i n g j u n ,L i P i n g ,Y a nP e n g f e i ,e t a l .S i m u l a t i o n o fS t a i n l e s sS t e e lD r i l l i n g M e c h a n i s m B a s e do nD e -f o r m ‐3D [J ].T o o l E ng i n e e r i n g,2011,45(4):17‐20.[8] 宋健.基于D E F O R M 3D 的发动机缸体钻削仿真及切削参数优化[D ].大连:大连理工大学,2012.(编辑 苏卫国)作者简介:周 力,男,1989年生㊂重庆大学机械工程学院硕士研究生㊂主要研究方向为齿轮高速干式滚切工艺与装备㊂曹华军(通信作者),男,1978年生㊂重庆大学机械工程学院教授㊁博士研究生导师㊂陈永鹏,男,1987年生㊂重庆大学机械工程学院博士研究生㊂杨 潇,男,1987年生㊂重庆大学机械工程学院博士研究生㊂(上接第2704页)[5] 孟文俊,沈东凯,王占林,等.基于矢量控制的航空液压泵源测试系统转速控制方案[J ].机械工程学报,2009,45(3):311‐316.M e n g W e n j u n ,S h e nD o n g k a i ,W a n g Zh a n l i n ,e ta l .V e c t o rC o n t r o l B a s e dR o t a t i n g S p e e dC o n t r o l S t r a t -e g i e si n A e r o H y d r a u l i c P u m p T e s tS ys t e m [J ].J o u r n a lo f M e c h a n i c a lE n g i n e e r i n g ,2009,45(3):311‐316.[6] 毛君,汪涛,卢进南.滑油泵试验器流量修正参数确定方法研究[J ].测控技术,2014,33(11):118‐125.M a o J u n ,W a n g T a o ,L u J i n n a n .R e s e a r c h o n t h eD e -t e r m i n a t i o n M e t h o d f o rC o r r e c t e dP a r a m e t e r o fL u -b r i c a t i n g P u m p B e n c h ’sF l o w [J ].M e a s u r e m e n t &C o n t r o lT e c h n o l o g y,2014,33(11):118‐125.[7] 李昂.航空发动机滑油供油系统性能分析与试验技术研究[D ].沈阳:沈阳航空航天大学,2013.[8] 李丛珊,姜印平.一种磁致伸缩位移传感器的优化设计方法[J ].传感技术学报,2014,27(9):1202‐1207.L iC o n g s h a n ,J i a n g Y i n p i n g .A n O p t i m i z a t i o n D e -s i g n M e t h o do fM a g n e t o s t r i c t i v eD i s p l a c e m e n tS e n -s o r [J ].C h i n e s eJ o u r n a lo fS e n s o r sa n d A c t u a t o r s ,2014,27(9):1202‐1207.[9] W e n g L i n g ,W a n g B o w e n ,S u n Y i n g,e ta l .M o d e l a n dE x p e r i m e n t o fG i a n tM a g n e t o s t r i c t i v eV i b r a t i o n S e n s o r [C ]//11t hI n t e r n a t i o n a lC o n f e r e n c eo nE l e c -t r i c a l M a c h i n e sa n d S y s t e m s .W u h a n ,2008:4092‐4095.[10] 李永波,胡旭东,曾宗云.温度对磁致伸缩液位传感器测量精度的影响[J ].工业仪表与自动化装置,2007(6):11‐13.L iY o n g b o ,H u X u d o n g ,Z e n g Z o n g y u n .T h eE m -p e r a t u r eE f f e c to nt h e M e a s u r i n g A c c u r a c y ofa M a g n e t o s t r i c t i v eL i q u i dL e v e r S e n s o r [J ].I n d u s t r i -a l I n s t r u m e n t a t i o n&A u t o m a t i o n ,2007(6):11‐13.[11] 李建藩.气压传动系统动力学[M ].广州:华南理工大学出版社,1991.[12] 罗艳蕾,李渊,李蒙,等.基于AM E S i m 的两位三通阀动态仿真研究[J ].科技广场,2010(6):99‐101.L u oY a n l e i ,L iY u a n ,L iM e n g ,e t a l .D y n a m i cS i m -u l a t i o nR e s e a r c ho nB i ‐p o s i t i o n T h r e e ‐w a y V a l v e B a s e do n AM E S i m [J ].S c i e n c e M o s a i c ,2009(6):99‐101.(编辑 陈 勇)作者简介:谢 苗,女,1980年生㊂辽宁工程技术大学机械工程学院副教授㊁博士研究生导师㊂主要研究方向为机械动力学分析及控制㊂刘治翔,男,1988年生㊂辽宁工程技术大学机械工程学院博士研究生㊂鲁启通,男,1988年生㊂大连东方工程建设项目管理有限公司助理工程师㊂田丰旭,男,1984年生㊂大连东方工程建设项目管理有限公司助理工程师㊂毛 君,男,1960年生㊂辽宁工程技术大学机械工程学院教授㊁博士研究生导师㊂黄增平,男,1986年生㊂辽宁工程技术大学机械工程学院硕士㊂㊃0172㊃中国机械工程第26卷第20期2015年10月下半月Copyright ©博看网. All Rights Reserved.。
基于DDFORM3D的高速车削有限元模拟

自动化与控制69基于DDFORM一3D的高速车削有限元模拟赵雷t邓远超,王军z陈友平1(1.西华大学机械j二程及其自动化学院,成都610039;2.淄博市计量测试所,淄博255033)摘要:基于有限元分析软件DEFORM一3D建立高速切削的切削力预报模型,并对车削力和工件、刀具及切屑的温度分布进行模拟。
该模拟结果对实际工作有现实的作用。
关键词:有限元高速切削切削力切削加工是机械制造行业中应用最广泛的金属成形]二艺,而目前由于高速主轴技术、直线电机技术、高速控制技术以及刀具技术的发展和进步,以加工的高速化实现加工的高品质、高效率已成为切削加工技术发展的重要特征。
而车削加工是各种切削方法的基础,因此本文就以高速车削加工进行具体分析。
对加工过程中,被加工金属材料的表面温度、切削力进行分析,为选择正确的刀具角度、刀具材料、切削用量和制定合适的加工工艺提供主要依据。
DEFORM一3D是由美国的SFFC公司1998年推出的基于有限元的工艺仿真系统,用于分析金属成形及其相关工业的各种成形工艺和热处理工艺三维软件。
设计人员和工程师通过仿真金属的变形过程,来预测变形过程中的金属流动,确定零件在变形过程中是否产生缺陷,预测设备压力和加工应力。
在要求精度较高的区域,可以划分较细密的网格,从而降低题目的规模,并显著提高计算效率。
Deform一3D的计算精度和结果的可靠性,被公认为国际成形过程模拟最理想的软件工具之一。
1用Deform软件分析工程实际问题(31Deform3D包含前处理器(PreProcessor)、工具(t001)、模拟(Simulator)和后处理器(PostProcessor)四个子模块,分别承担建模、计算与仿真和数据处理i大功能。
通常Deform分析制造工程实际问题的顺序如下:(1)定义工程实际问题;收集所需的数据;(2)生成FEM网格;生成一个DEFORM数据库;(3)进行仿真;处理仿真结果。
DEFORM3D—V5.0版中包含了切削分析模块Machin—ing。
基于DEFORM-3D对300M切削烧伤进行分析及加工过程改善

1 序言在国内外先进民航飞机的结构设计中,为满足飞机长寿命、易维护、轻量化等需求,飞机零件结构向整体化、复杂化、薄壁化等方向发展,因此越来越多地采用整体结构设计,使用新型材料,提高飞机结构的强度。
随着材料技术、锻造技术、制造技术的不断发展,使用超高强度合金钢制造大型飞机起落架主承力结构件成为必然的选择。
300M材料具有良好的力学性能,因此广泛应用于飞机关键零部件。
2 300M的材料特性2.1 金属特性超高强度合金钢300M是美国航空工业一种重要的合金钢,在化学、物理方面具有独特的性能,概括如下。
300M是一种低碳、低合金含量的钢,与非合金钢相比,具有较高的强度,固有“低合金超高强度钢”之称。
其屈服点高,因此在相同载荷下,工件的质量可以减轻20%~30%,具有良好的塑性和韧性,合金材料中含有Ni、Cr、Mo等元素,使钢的过冷奥氏体相当稳定,空淬即可获得马氏体和贝氏体组织。
2.2 加工特性该材料具有良好的硬度,同时抗拉强度也非常高,正是因此,使得其非常难加工,属于难加工材料,主要表现如下。
由于材料具有高的硬度和强度,原子密度和结合力大,断裂韧度和持久塑性高,在切削过程中切削力大,而且切削力的波动也比较大。
加工过程中产生的热量多,在切削区集中了大量的切削热,形成很高的切削温度。
再加上强化系数高,在切削力和切削热的作用下产生巨大的塑性变形,造成加工硬化。
由于切削时切削力大,切削热高,刀具与切屑的直接摩擦加剧,所以导致刀具材料与工件材料产生亲和作用,加上材料硬质点的存在和严重的加工硬化现象,刀具在切削过程中易产生黏结磨损、扩散磨损、磨料磨损和沟纹磨损,使刀具丧失切削的能力。
切削时的切屑为带状的缠绕屑,既不安全,又影响切削过程的顺利进行,也不便于处理。
在加工中容易产生热变形,因而一些精密尺寸和形状不易保证。
从300M的材料特性和加工特性来看,此材料在加工过程中极易产生大量的切削热,过多的切削热会导致工件出现烧伤现象。
车削加工工艺参数对切削力的影响

基于DEFORM3D的车削有限元模拟摘要:本文在建立了车削三维有限元模型基础上,运用有限元法对45钢的车削过程中切削用量对切削力影响进行了模拟,并对结果进行了分析讨论。
该模拟对现实工程应用有较大的作用。
关键字:车削模拟 DEFORM3D1 引言金属零件的加工方式可分为塑性加工、热成形或压力成形加工、机械加工、高能加工、电及化学加工等几大类。
在上述各种加工方法中,在机械制造过程所占比重最大的是机械加工中的切削加工和磨削加工;而车削加工作为切削加工中应用最广泛的加工形式,其加工过程中的工艺参数一直成为研究的对象。
本文利用STFC公司的DEFORM3D软件对车削过程进行模拟,并分析了不同的切削用量对切削力的影响。
1.1 车削加工过程中切削力的来源与分解1.1.1 切削力的来源刀具总切削力是刀具上所有参与切削的各切削部分所产生的总切削力的合力。
而一个切削部分的总切削力F是一个切削部分切削工件时所产生的全部切削力。
它来源于两个方面:三个变形区(剪切区、摩擦区、挤压区)内产生的弹、塑性变形抗力和切屑、工件与刀具之间的摩擦力。
切削时金属的塑性变形如图1所示,其中第Ⅰ变形区为剪切区,第Ⅱ变形区为摩擦区,第Ⅲ变形区为挤压区。
图1 切削时金属的塑性变形1.1.2 总切削力的几何分力刀具切削部分的总切削力是个大小、方向不易测量的力。
为方便分析,常将总切削力沿选定轴系作矢量分解来推导出各分力,即总切削力的几何分力。
图2 外圆车削时力的分解(1) 切削力F。
CF是F在主运动方向上的正投影。
在各分力中它最大,要消耗机床功率的C95%以上。
它是计算机床功率和主传动系统零件强度和刚度的主要依据。
F。
(2) 进给力fF是F在进给运动方向上的正投影,是设计或校核进给系统零件强度和刚f度的依据。
F(3) 背向力pF是F在垂直于工作平面上的分力。
背向力不做功,具有将工件顶弯的趋pF。
势,并引起振动,从而影响工件加工质量。
用增大车刀主偏角的方法可以减小p F与各分力之间的关系为:F=1.2 切削热和切削温度1.2.1 切削热的来源切削过程中所消耗的切削功绝大部分转变为切削热。
毕业论文-基于DEFORM-3D的切削温度仿真
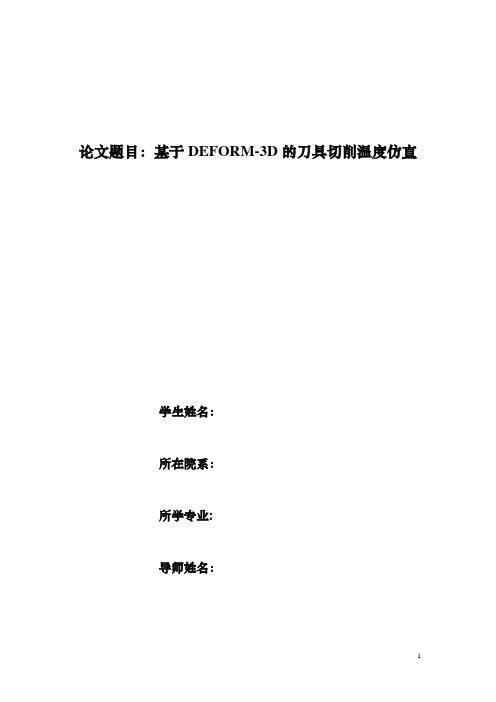
论文题目:基于DEFORM-3D的刀具切削温度仿真学生姓名:所在院系:所学专业:导师姓名:目录摘要 (1)第一章绪论……………………………………………………错误!未定义书签。
第二章仿真软件介绍 (6)第三章Deform—3D软件简介 (9)3。
1软件模块结构分析 (9)3。
2 前处理器及其设置 (9)3.3 模拟器 (9)3。
4 后处理器 (11)第四章有限元模型的建立 (13)4。
1 切削加工模型 (13)4。
2 切削模型建立 (14)第五章 DEFORM-3D对切削温度的仿真 (17)5。
1刀具和工件的温度场分析 (17)5.2 切削速度对切削温度的影响 (17)5.3切削过程中总体温度分布 (19)5。
4 切削厚度对切削温度的影响 (20)第六章结论 (22)第七章参考文献 (23)摘要在金属切削加工中,切削温度对切削加工过程有着非常重要的意义。
为了更好的研究金属材料的切削加工过程中切削温度的分布,本文以Deform—3D软件为平台,利用有限元方法对45号钢的切削过程中的温度进行了建模与仿真,分别分析了切削过程中刀具和工件的切削温度场分布,以及切削速度变化时对切削温度的影响。
仿真结果表明:刀-屑接触区及工件上的最高温度随切削速度的增加而升高,但工件上温度升高的趋势较平缓;无论切削条件怎么变化,切削温度的最高点总不在刀刃处,而是位于前后刀面上距离刀刃不远的地方;剪切面上各点的温度几乎相同.仿真结果表明,Deform—3D软件所得的仿真结果和理论依据的吻合度较高,说明仿真具有较高的可信度,为生产实践中切削速度的优化选择,刀具及工件材料的选择提供理论依据关键词:Deform-3D,有限元仿真,切削温度AbstractIn the process of metal cutting, the cutting temperature of the cutting process has very important significance. In order to better study the metal material cutting process of cutting temperature distribution,Based on the Deform -3D software as the platform,using the finite element method for45 steel cutting temperature by modeling and simulation,Analysis of the cutting process, the cutting tool and the workpiece cutting temperature field distribution,as well as the cutting speed change on cutting temperature effect.The simulation results show that:the tool-chip contact area and the workpiece on the maximum speed with cutting speed increases, but the workpiece temperature increased more gentle; No matter how the change of cutting temperature cutting conditions,highest point total in the blade,but are located before and after the knife surface distance edge not far place;Shear plane of each point on the temperature is almost the same. The simulation results show that,the Deform - 3D software the simulation results and the theoretical basis of the anastomosis of a higher degree, a description of the simulation has high reliability,Production practice of cutting speed optimization,tool and workpiece material selection and provide a theoretical basisKey word:Deform—3D,Finite element simulation, Cutting temperature第一章绪论金属切削是机械制造中使用最广泛的加工方法,金属切削加工时在机床上利用个切削工具从工件上切除多余材料,从而获得具有一定形状精度、尺寸精度、位置精度和表面质量的机械零件,是机械加工的基本方法。
基于Deform+3D的高速超高速磨削温度的仿真研究
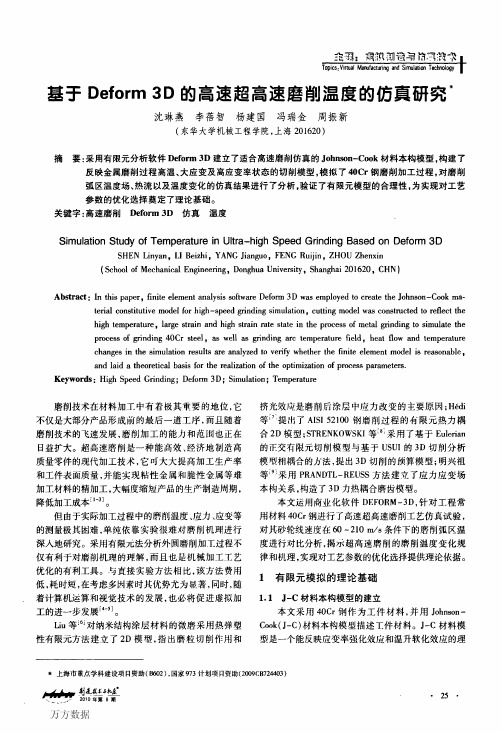
图2单颗磨粒仿真的有限元模型
2.2预处理设置 预处理设置作为加工仿真分析的准备工作,主要
完成前处理设置、生成数据库和模拟运算三个步 骤㈨。
在仿真控制(Simulation Contr01)中设置仿真步数 为80步,时间增量为1x10~S,存储增鼍为每2步保 存一次,时间步长设置不能太大,否则会降低求解精 度,导致网格严重畸变甚至不收敛。采用国标单位标 准sI,仿真模式为热传递(Heat Transfer)和变形(De. form);迭代方法(Iteration Method)采用Direct itera. tion;求解器(Deformation Solver)采用共轭梯度法 (Conjugate-Gradient Solver),C—G法为DEFORM 3D
图3单个周期蘑削弧区温度
鼍≥象怂三磐
万方数据
3.2磨削弧区热流分析 图4为磨削弧区热流的分布情况。可以发现沿着
磨削弧区的热流并不是逐渐增加的,而是随着砂轮的 旋转,单颗磨粒从开始接触工件到磨粒切出工件,产生 的热流呈现出非线性的先上升后下降的规律。这是由 于在磨削加工过程中,随着磨粒的切入,切深逐渐变 大,随之产生大量的磨削热,大约在弧区中心位置产生 最大热流,且热流分布形状可近似的看成二次曲线分 布。
脚象羔笔等
三毫习:司飘铷铅与诗j敖木l
中最常用的求解器,这种方法考虑了刀一屑之间的摩 擦及工件材料流动应力受应变、应变速率和温度的影 响。该方法对多数FEM问题都具有优势,但对于有些 问题,如接触点较少的情况,收敛较慢甚至不收敛,此 时,软件会自动识别转为Sparse法求解。因此,可有 效的保证较少的迭代次数和迭代收敛性。
Cook(J-C)材料本构模型描述T件材料。J—C材料模 型是一个能反映应变率强化效应和温升软化效应的理
DEFORM的车削仿真案例
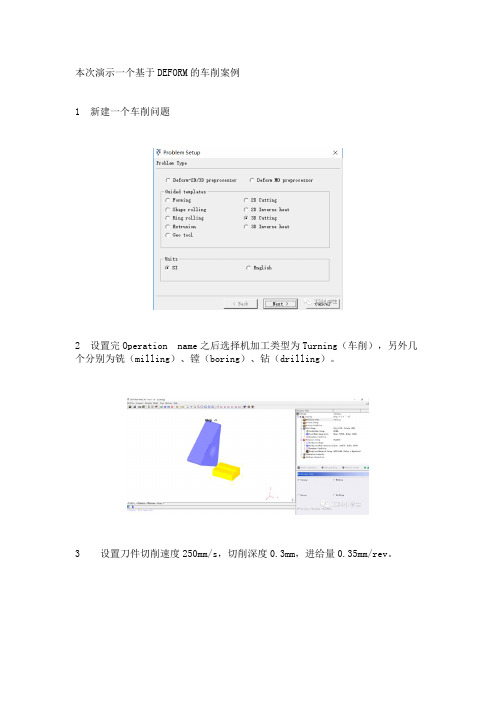
本次演示一个基于DEFORM的车削案例1 新建一个车削问题2 设置完Operation name之后选择机加工类型为Turning(车削),另外几个分别为铣(milling)、镗(boring)、钻(drilling)。
3 设置刀件切削速度250mm/s,切削深度0.3mm,进给量0.35mm/rev。
4 设置环境温度为20℃,空气对流传热系数保持默认,摩擦系数设为剪切摩擦0.5,刀件与工件的传热系数设为45.5 选择系统内置的TNMA332刀具,当然用户也可以通过Define a new tool来导入自己的刀具模型,支持STL格式。
通过Edit position来调整刀具的位置。
6 选择车刀角度,Side cutting Angle(主偏角)back rake angle 前角side rake angle副前角,除了导入自带的参数,用户可以通过Create a new toolholder自己设置对应参数。
具体这些参数修改会有什么变化如下图所示:7 给车刀划分网格8 设置工件基本参数。
9 设置工件长度为7mm。
Curved model可以生成一个圆环。
当然也可以通过Import Geometry来自己导入工件模型。
10 给工件划分网格,设置最小单元尺寸为0.06mm,尺寸比例为7。
11 给工件赋予材料,通过Import material from liabrary从材料库中导入相应材料。
12 设置模拟步数为10000,每25步存储一次,规定切削长度为3.5mm,也就是工件的一半长度。
注意,当设置了切削长度,那么步数就无效了,可以尽可能往大了设,当满足切削长度之后程序自动停止。
下面的刀具磨损模型采用的Usui模型,具体参数需要参照实验校准,其与所使用的材料和车削工艺有关。
13 查看结果后处理可以查看切削过程中,应力,应变,温度等的变化以及切屑的形态。
等效应力的变化等效应变的变化温度的变化。
基于Deform 3D的不锈钢车削加工仿真研究
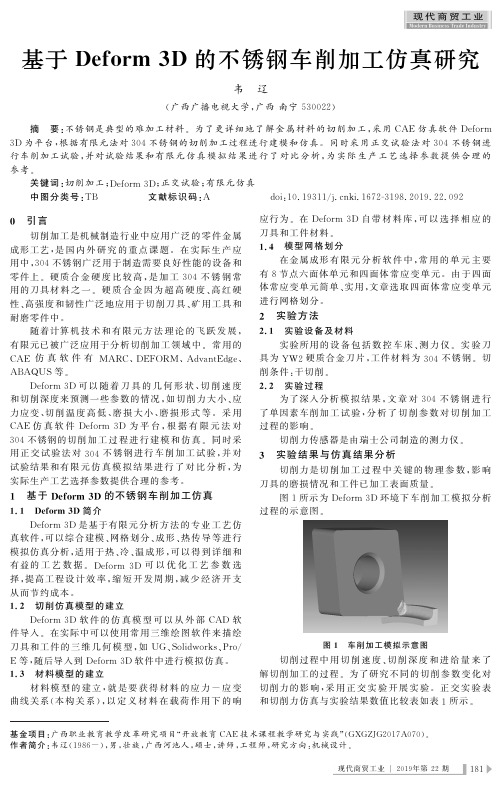
现代商贸工业2019年第22期181㊀基金项目:广西职业教育教学改革研究项目 开放教育C A E 技术课程教学研究与实践 (G X G Z J G 2017A 070).作者简介:韦辽(1986-),男,壮族,广西河池人,硕士,讲师,工程师,研究方向:机械设计.基于D e f o r m3D 的不锈钢车削加工仿真研究韦㊀辽(广西广播电视大学,广西南宁530022)摘㊀要:不锈钢是典型的难加工材料.为了更详细地了解金属材料的切削加工,采用C A E 仿真软件D e f o r m3D 为平台,根据有限元法对304不锈钢的切削加工过程进行建模和仿真.同时采用正交试验法对304不锈钢进行车削加工试验,并对试验结果和有限元仿真模拟结果进行了对比分析,为实际生产工艺选择参数提供合理的参考.关键词:切削加工;D e f o r m3D ;正交试验;有限元仿真中图分类号:T B ㊀㊀㊀㊀㊀文献标识码:A㊀㊀㊀㊀㊀㊀d o i :10.19311/j.c n k i .1672G3198.2019.22.0920㊀引言切削加工是机械制造行业中应用广泛的零件金属成形工艺,是国内外研究的重点课题.在实际生产应用中,304不锈钢广泛用于制造需要良好性能的设备和零件上.硬质合金硬度比较高,是加工304不锈钢常用的刀具材料之一.硬质合金因为超高硬度㊁高红硬性㊁高强度和韧性广泛地应用于切削刀具㊁矿用工具和耐磨零件中.随着计算机技术和有限元方法理论的飞跃发展,有限元已被广泛应用于分析切削加工领域中.常用的C A E 仿真软件有MA R C ㊁DEF O R M ㊁A d v a n t E d ge ㊁A B A Q U S 等.D e f o r m3D 可以随着刀具的几何形状㊁切削速度和切削深度来预测一些参数的情况,如切削力大小㊁应力应变㊁切削温度高低㊁磨损大小㊁磨损形式等.采用C A E 仿真软件D e f o r m 3D 为平台,根据有限元法对304不锈钢的切削加工过程进行建模和仿真.同时采用正交试验法对304不锈钢进行车削加工试验,并对试验结果和有限元仿真模拟结果进行了对比分析,为实际生产工艺选择参数提供合理的参考.1㊀基于D e f o r m3D 的不锈钢车削加工仿真1.1㊀D e f o r m3D 简介D e f o r m3D 是基于有限元分析方法的专业工艺仿真软件,可以综合建模㊁网格划分㊁成形㊁热传导等进行模拟仿真分析,适用于热㊁冷㊁温成形,可以得到详细和有益的工艺数据.D e f o r m 3D 可以优化工艺参数选择,提高工程设计效率,缩短开发周期,减少经济开支从而节约成本.1.2㊀切削仿真模型的建立D e f o r m3D 软件的仿真模型可以从外部C A D 软件导入.在实际中可以使用常用三维绘图软件来描绘刀具和工件的三维几何模型,如U G ㊁S o l i d w o r k s ㊁P r o/E 等,随后导入到D e f o r m3D 软件中进行模拟仿真.1.3㊀材料模型的建立材料模型的建立,就是要获得材料的应力-应变曲线关系(本构关系),以定义材料在载荷作用下的响应行为.在D e f o r m3D 自带材料库,可以选择相应的刀具和工件材料.1.4㊀模型网格划分在金属成形有限元分析软件中,常用的单元主要有8节点六面体单元和四面体常应变单元.由于四面体常应变单元简单㊁实用,文章选取四面体常应变单元进行网格划分.2㊀实验方法2.1㊀实验设备及材料实验所用的设备包括数控车床㊁测力仪.实验刀具为YW 2硬质合金刀片,工件材料为304不锈钢.切削条件:干切削.2.2㊀实验过程为了深入分析模拟结果,文章对304不锈钢进行了单因素车削加工试验,分析了切削参数对切削加工过程的影响.切削力传感器是由瑞士公司制造的测力仪.3㊀实验结果与仿真结果分析切削力是切削加工过程中关键的物理参数,影响刀具的磨损情况和工件已加工表面质量.图1所示为D e f o r m3D 环境下车削加工模拟分析过程的示意图.图1㊀车削加工模拟示意图切削过程中用切削速度㊁切削深度和进给量来了解切削加工的过程.为了研究不同的切削参数变化对切削力的影响,采用正交实验开展实验.正交实验表和切削力仿真与实验结果数值比较表如表1所示.工程管理与技术现代商贸工业2019年第22期182㊀㊀图2㊀切削力仿真曲线表1㊀正交实验表和切削力仿真与实验结果数值比较表序号切削深度(a p )进给量(f)切削速度(V c )仿真值(N )实验值(N )误差(%)10.40.2060706763.48.120.40.2365745789.35.930.40.2670772802.84.040.60.2065796824.53.650.60.2370823806.2-2.060.60.2660836847.71.470.80.2070872897.32.980.80.2360841875.14.190.80.2665862873.61.3㊀㊀在实际加工过程中,由于环境温度变化㊁刀具磨损状况㊁加工参数对排屑情况等因素的影响,可能会导致实际数值与模拟数值产生一定的误差.同时,因为金属切削过程是一个非线性问题,具有连续性和动态性特征,在D e f o r m3D 中对于刀具和工件的网格划分不同也将会导致误差产生,在仿真切削过程中一些单元可能被挤压或变形,严重影响切削精度,导致计算过程不收敛,也会产生误差.从表1可以看出,考虑到实际切割中材料的失效和摩擦条件非常复杂,误差在8%以内,所以模拟结果是可以接受的.D e f o r m3D 模拟在理想条件下,实际加工过程中存在各种影响因素,可以看出实验值和切削力模拟值存在一定的误差.但总体误差很小,在可接受的范围内.㊀㊀从图2可以看出,当刀具开始切削工件后,切削力开始比较小,随着时间的增加不断增加,到了一定时间后才会达到稳定值,数值在一定范围内也存在不断波动情况,这与在实际试验中利用测力仪所获取的图表变化趋势是一致的.4㊀结语文章以C A E 仿真软件D e f o r m3D 为研究平台,根据有限元法对304不锈钢的切削加工过程进行建模和仿真.同时采用正交试验法对304不锈钢进行车削加工试验,并对试验结果和有限元仿真模拟结果进行了对比分析,为实际生产工艺选择参数提供合理的参考和理论指导.参考文献[1]VB o u n h o u r e a ,SL a ya ,SC o i n d e a u ab ,e t a l .E f f ec t o f C r ad d i t i o n o n s o l i d s t a te s i n t e r i n g o fW C -C o a l l o y s [J ].I n t e r n a t i o n a l J o u r Gn a l o fR ef r a c t o r y Me t a l s a n dH a r d M a t e r i a l s ,2015,52:21G28.[2]S u W e i ,S u nY e x i ,J i a oF e n g ,e t a l .I nf l u e n c e so f t h e p r e pa r a Gt i o nm e t h o d so f W C-C o p o w d e r so nt h es i n t e r i n g an d m i c r o Gs t r u c t u r e o fc o a r s e g r a i n e d W C-8C oh a r d m e t a l s [J ].I n t e r n a Gt i o n a l J o u r n a lo fR e f r a c t o r y Me t a l sa n d H a r d M a t e r i a l s ,2015,48:369G375.[3]R u m m a n M R ,X i eZ ,H o n g SJ ,e t a l .Ef f e c t o f s pa r k p l a s m a s i n t e r i n gp r e s s u r eo n m e c h a n i c a l p r o pe r t i e sof W C-7.5w t %N a n oC o [J ].M a t e r i a l s&D e s i gn ,2015,68:221G227.[4]温效朔,王克琦.切削加工有限元仿真与应力分析[J ].工具技术,2006,40(7):30G32.[5]方刚.切削加工过程数值模拟的研究进展[J ].力学进展,2001,31(3):394G404.[6]张磊光.三维金属切削过程的有限元模拟[D ].北京:华北电力大学,2008.[7]于贻鹂.金属切削过程有限元法仿真研究[D ].大连:大连理工大学,2005.[8]章振翔,张金明,王来钱等.基于D e f o r m-3D 的不锈钢切削力有限元仿真[J ].轻工机械,2011,29(4):40G42.[9]聂闻,李成让,张伟等.基于D e f o r m 的304不锈钢的车削仿真与实验研究的影响[J ].装备制造技术,2014,(5):55G57.建筑工程项目管理的重要性与创新方法探析张海波(吉林省辽源市人防办工程管理处,吉林辽源136200)摘㊀要:随着我国经济建设的高速发展,我国的建筑工程建设也取得了令人瞩目的成绩.建筑工程的发展,满足了人民群众对生活水平的日益增长的要求,也满足了我国国际竞争力的不断增强的目标.为了保证我国在建筑工程领域能够不断的取得进步和发展,就必须认识到建筑工程管理的重要性.只有采取了行之有效的管理方法,建筑工程水平才能够不断提高,我国的建筑工程事业才能得到健康有序的发展与进步.关键词:建筑工程;项目管理;重要性;创新方法中图分类号:T B ㊀㊀㊀㊀㊀文献标识码:A㊀㊀㊀㊀㊀㊀d o i :10.19311/j .c n k i .1672G3198.2019.22.093㊀㊀在当今社会的新的发展阶段,建筑工程的质量和效率,影响着我们社会的进步和人民的满意程度.在当代经济高速发展的大环境下,如何促进建筑工程项目管理水平的进步,也是我们现阶段要重点要研究的问题.只有改变现有的建筑工程管理方法,才能使建筑工程管理水平的提高得以实现.通过建筑工程项目管理方法的研究,可以对我国建筑工程管理方法创新的目标提供有效的途径.1㊀建筑工程项目管理的现状在我国改革开放以后,为了满足社会进步的需求。
基于Deform 3D的30CrNiMo8干硬车削温度仿真模拟研究

口 黄 建龙 口 岳
兰州
芸
705 30 0
兰州 理 工 大 学 机 电工 程 学 院
摘
要 : 于材 料 变 形 的 弹 塑 性 理 论 、 力耦 合 理 论 以及 U u 磨 损 模 型, 用有 限 元 分 析 软 件 D F R 3 建 立 了 基 热 si 采 E O M一 D
其 中 = ; D= e p k( - b ̄ Dox [ T T )]
( a r n fr 和 变 形 ( —o m) 求 解 器 ( fr t n He tT a se ) De fr ; Deo mai o S le );用 S a s ov r 3:  ̄ p re法 求 解 。 S as p re解 法 是 一 种 利 用 极 式 中 : 、 C、 、 m 分 别 为 材 料 参 数 ; 为 有 效 塑 性 A 曰、 D n、 善
12 Us i磨 损 模 型 . u
=
v lp e a
£
() 2
工 件 材 料 、 具 材 料 、 具 角 度 和 切 削 速 度 不 同 引 刀 刀 起 的 被 加 工 工 件 的 切 削 温 度 和 热 流 分 析 是 加 工 技 术 的
式 中 : 为 磨 损 深 度 ; 为 接 触 压 力 ; 为滑 移 速 度 ; p T
文 章编 号 :00 4 9 f l)9 o 5 — 5 10 — 9 82 1o 一 o 6 0 0
金 属 切 削 过 程 是 一 个 非 常 复 杂 的 工 艺 过 程 它 涉
L ga g a r n e公 式 和 增 量 变 分 原 理 导 出 热 弹 塑 性 大 变 形 耦 合 方程 [ :
基于Deform 3D的高速超高速磨削温度的仿真研究

毫 司 :帚嬲 铷 趋 习 翰 马藏 I 丽 而 .- t
基 于 D fr 3 eo m 高 速 超 高 速 磨 削温 度 的 仿 真 研 究 D的
沈琳 燕 李蓓智 杨 建 国 冯瑞金 周振 新
( 华 大学机 械 工程 学 院 , 海 2 1 2 ) 东 上 0 6 0 摘 要: 采用 有 限元分 析 软件 D fr 3 建 立 了适合 高速 磨 削仿 真 的 J h sn C o eo m D o no - o k材 料本 构模 型 。 构建 了 反 映 金属磨 削 过 程 高温 、 应变 及 高应 变 率 状态 的切 削 模 型 , 拟 了 4 C 大 模 0 r钢磨 削 加工 过 程 , 磨 削 对 弧 区温度 场 、 热流 以及 温 度变 化 的仿真 结 果进 行 了分 析 , 证 了有 限元模 型 的合 理 性 , 实现 对工 艺 验 为
基于Deform3D的高速车削加工仿真研究
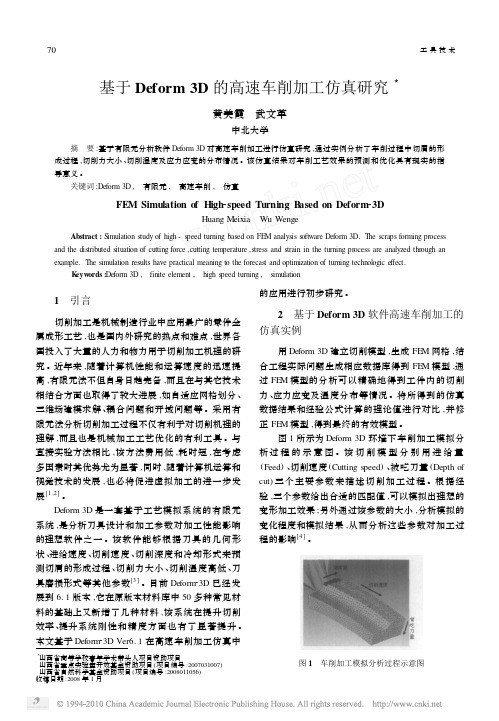
图 4 为试件等效应力的分布 。图 5 为切削区最
大主应力的分布 ,无论从图中的等效应力还是最大
主应力分布状态的等高线都可看出刃前区应力分布
状态最为复杂 ,在第一变形区等效应力数值最大并
有较大变化梯度 ; 第二变形区应力的分布较为均
匀[6] 。
图 6 为刀具的等效应力等值线图 。图 7 为刀具
的位移变化分布云图 。从两图中可以看出刀具的应
图 2 切削力 Fc 随着切削距离的变化
图
3a
和图
3b
分别为工件转过 1 后工件和刀具 12
的切削温度分布图 ,从两图中看出切削温度最高点
不在刀尖处 ,而是离开刀尖一段距离 。整个切削过
程中工件切削温度的峰值可达 1030 ℃℃以上 407 ℃以下 。
1030
3 结语
采用有限元法模拟切削加工可获得切削试验法 或难以直接测量的状态变量 ,如工件和刀具的切削 力分布 、切削温度等 ,有利于更好地理解切削加工机 理 、评价和优化切削加工过程 。而采用有限元法分 析和评价各种切削条件下的刀具磨损状况 ,费用低 耗时短 。但是由于车削加工尤其是高速车削加工过 程极其复杂 ,有关其切削机理的许多问题仍未得到 解决[7] 。如车削过程中积屑瘤 、分流等各种特定现 象的研究 ;车床振动 、冷却液等实际切削过程的工艺 因素对车削模拟的影响 ;刀具材料的磨损机制 、切削 力 、切屑变形和加工表面质量随实际加工过程中工 件材料的相变而发生相应变化的研究 ;其模拟运算 时间过长对制造车间在线控制的障碍 ;网格划分的 疏密和步长设置的大小都会影响仿真的精度 ,如何 设置才能实现最合理化等都有待进一步研究 。
力和变形区域主要集中在刀尖处 ,向外沿区域呈逐
渐减弱的趋势 。
基于Deform—3D车削钛合金Ti—6Al—4V的加工过程仿真

基于Deform—3D车削钛合金Ti—6Al—4V 的加工过程仿真作者:陈卓来源:《科技视界》2016年第20期【摘要】通过Deform-3D软件,进行了钛合金Ti-6Al-4V车削过程的仿真,预测了切削力和切削温度,为提高刀具耐用度和加工质量提供了有效方法,为改善难加工材料的切削加工性提供了参考依据。
【关键词】车削;Deform-3D;切削力;切削温度;仿真0 引言钛合金作为航空、航天、航海、医疗等领域应用较为广泛的一种难加工材料,其加工过程中一直存在切削温度高、刀具耐用度低、加工质量难以保证等问题。
预测切削过程从而优化切削参数进而达到提高刀具耐用度和加工质量是现实钛合金加工优化最有效的方法之一,由于实际切削实验需要耗费价格不菲的刀具和材料且实验时间较长,因此通过计算机仿真技术预测切削过程已成为目前常见的方法。
现阶段,Deform、Ansys、Abaqus、AdvantEdge等软件已普遍应用于金属切削过程的仿真[1-3]。
本文选择三维有限元软件Deform-3D作为仿真实验平台,以车削钛合金TC4作为研究对象,采用硬质合金刀具,预测了不同切削参数对切削力和切削温度的影响规律,为切削参数的优化提供了参考。
1 仿真步骤Ddeform-3D软件可以分析车削、铣削、钻削等加工过程,本文以车削加工为研究对象。
首先,建立切削模型和设置参数。
Deform-3D软件可以导入其他三维建模软件创建的模型,导入的格式有STL、UNV、IGS等。
此外,Deform-3D也自带建模功能。
本文采用Deform-3D自带建模功能,创建车削模型如图1所示。
参数的设置分别为:切削速度v为别为80、100、120m/min,进给量f分别为0.05、0.1、0.15 mm/r,切削深度ap分别为0.3、0.6、1mm。
图1 车削模型第二步,进行网格划分。
Deform-3D有两种划分方法——相对和绝对网格划分。
本文中工件采用绝对网格划分方法,最大和最小网格单元尺寸之比为7;刀具采用的是相对网格划分,其单元数为36000。
基于DEFORM-3D的高速车削加工仿真

基于DEFORM-3D的高速车削加工仿真
武文革;黄美霞
【期刊名称】《现代制造工程》
【年(卷),期】2009(000)011
【摘要】DEFORM-3D是应用有限元方法(FEM)分析三维复杂加工过程的模拟工具,它不仅鲁棒性好,而且易于使用.借助于该模拟分析环境,能够对切削过程中刀具几何参数、切削条件以及加工过程中的其他因素产生的影响进行研究.应用DEFORM 自带的切削仿真模型,模拟高速车削加工中工件及刀具的温度分布、切屑流动、应力、应变和切削力等.模拟结果对减少产品试验、降低开发成本、缩短开发新产品及新工艺的时间等方面都具有重大意义.DEFORM-3D对于研究刀具几何模型、切屑形成以及切削参数控制的刀具制造者和使用者来说,是一个较理想的工具.
【总页数】5页(P91-94,24)
【作者】武文革;黄美霞
【作者单位】中北大学机械工程与自动化学院,太原,030051;中北大学机械工程与自动化学院,太原,030051
【正文语种】中文
【中图分类】TP391
【相关文献】
1.基于Deform-3D的铝合金2A12车削加工有限元模拟 [J], 黄勇;狄欧;李亚非
2.基于DEFORM-3D的镍基合金钢的车削加工仿真 [J], 陈立;张智栋;衡婷;管小燕
3.三维车削加工的Deform-3D有限元模拟 [J], 刘伟;李家春
4.基于遗传算法BP神经网络的DEFORM-3D车削加工模拟优化 [J], 江平;邓志平
5.基于Deform 3D的高速车削加工仿真研究 [J], 黄美霞;武文革
因版权原因,仅展示原文概要,查看原文内容请购买。
基于Deform-3D轴向超声辅助磨削仿真试验

基于Deform-3D轴向超声辅助磨削仿真试验
王艳;张省;王帅;杨林;谢建华
【期刊名称】《系统仿真学报》
【年(卷),期】2015(0)1
【摘要】磨削过程可视为大量随机分布磨粒切削形成的累积效应,因此可以把复杂的磨削过程简化为单颗磨粒的切削过程。
提出了一种新的超声辅助单颗磨粒磨削的仿真方法:利用Deform-3D软件,对轴向超声振动辅助磨削时单颗磨粒的速度进行加载,完成磨削力和磨削温度的仿真。
仿真结果表明:在相同磨削条件,超声振动辅助磨削弧区最高温度值低于普通磨削最高温度值;超声振动辅助磨削磨粒的法向磨削力及切向磨削力均小于普通磨削条件下所得到的磨削力;随着磨粒速度增加,磨削弧区温度升高,法向磨削力与切向磨削力下降,而其磨削力比增大;随着磨粒切削深度的增加,磨削弧区温度升高,法向磨削力与切向磨削力上升,而其磨削力比下降。
【总页数】8页(P104-111)
【作者】王艳;张省;王帅;杨林;谢建华
【作者单位】上海理工大学
【正文语种】中文
【中图分类】TG580.6;TG663
【相关文献】
1.轴向超声振动辅助磨削的磨削力研究
2.轴向超声辅助磨削陶瓷的磨削力模型
3.基于光滑粒子流体动力学法单颗磨粒超声辅助磨削陶瓷材料的磨削力仿真研究
4.颗
粒增强钛基复材轴向超声振动辅助磨削试验研究5.轴向超声振动辅助磨削的磨削力建模
因版权原因,仅展示原文概要,查看原文内容请购买。
基于DEFORM的高速切削加工分析及切削参数优化中期报告

基于DEFORM的高速切削加工分析及切削参数优化中期报告一、研究背景随着制造业的快速发展,高速切削加工技术在零件制造中得到广泛应用。
高速切削技术具有高效、高质、高精、高稳定性等优点,可以大幅提高零件的加工效率和质量。
但是,切削加工过程中涉及多个关键参数,如刀具类型、切削速度、进给速度等,对切削过程进行优化和调整非常困难。
因此,需要通过数值模拟分析,优化切削参数,提高加工效率和质量,降低生产成本。
DEFORM是一种广泛应用的数值模拟软件,可以模拟金属成形加工过程中的应力、应变、变形、温度等关键参数,并进行工艺分析和优化。
通过DEFORM软件模拟切削加工过程,可以深入了解切削加工过程中的各种关键参数,优化加工工艺,提高加工效率和质量。
二、研究目的和内容本文旨在基于DEFORM软件进行高速切削加工过程数值模拟,并分析切削参数对切削过程的影响。
具体研究内容包括:1. 建立高速切削加工数值模拟模型;2. 模拟分析不同切削参数对加工质量的影响,如工件表面粗糙度、加工强度等;3. 进行切削参数优化,使切削加工效率最大化;4. 验证数值模拟结果的准确性,与实验数据进行对比和分析。
三、研究方法和步骤本研究采用数值模拟方法研究高速切削加工过程。
具体步骤如下:1. 建立数值模拟模型。
首先,根据切削加工的基本原理,建立切削过程的有限元模型。
模型中包含工件、刀具、夹具等物理实体的几何形状、材料性质、边界条件等信息。
2. 设定切削参数和加载条件。
在模型中设置切削参数,如切削速度、进给速度、刀具半径、角度等,以及加载条件,如初始应力、初始温度等。
3. 进行数值模拟。
在DEFORM软件中进行数值模拟,计算出加工过程中的关键参数,如应力、应变、温度、位移等。
4. 分析切削参数对加工质量的影响。
根据数值模拟结果,分析不同切削参数对加工质量的影响,如工件表面粗糙度、加工强度等。
5. 进行切削参数优化。
根据分析结果,对切削参数进行优化,使切削加工效率最大化。
- 1、下载文档前请自行甄别文档内容的完整性,平台不提供额外的编辑、内容补充、找答案等附加服务。
- 2、"仅部分预览"的文档,不可在线预览部分如存在完整性等问题,可反馈申请退款(可完整预览的文档不适用该条件!)。
- 3、如文档侵犯您的权益,请联系客服反馈,我们会尽快为您处理(人工客服工作时间:9:00-18:30)。
3山西省高等学校青年学术带头人项目资助项目山西省重点实验室开放基金资助项目(项目编号:2007031007)山西省自然科学基金资助项目(项目编号:2008011056)收稿日期:2008年1月基于Deform 3D 的高速车削加工仿真研究3黄美霞 武文革中北大学摘 要:基于有限元分析软件Deform 3D 对高速车削加工进行仿真研究,通过实例分析了车削过程中切屑的形成过程,切削力大小、切削温度及应力应变的分布情况。
该仿真结果对车削工艺效果的预测和优化具有现实的指导意义。
关键词:Deform 3D , 有限元, 高速车削, 仿真FEM Simulation of H igh 2speed Turning B ased on Deform 23DHuang Meixia Wu WengeAbstract :S imulation study of high -speed turning based on FE M analysis s oftware Deform 3D.The scraps forming process and the distributed situation of cutting force ,cutting tem perature ,stress and strain in the turning process are analyzed through an exam ple.The simulation results have practical meaning to the forecast and optimization of turning technologic effect.K eyw ords :Deform 3D , finite element , high speed turning , simulation 1 引言切削加工是机械制造行业中应用最广的零件金属成形工艺,也是国内外研究的热点和难点,世界各国投入了大量的人力和物力用于切削加工机理的研究。
近年来,随着计算机性能和运算速度的迅速提高,有限元法不但自身日趋完备,而且在与其它技术相结合方面也取得了较大进展,如自适应网格划分、三维场建模求解、耦合问题和开域问题等。
采用有限元法分析切削加工过程不仅有利于对切削机理的理解,而且也是机械加工工艺优化的有利工具。
与直接实验方法相比,该方法费用低,耗时短,在考虑多因素时其优势尤为显著,同时,随着计算机运算和视觉技术的发展,也必将促进虚拟加工的进一步发展[1,2]。
Deform 3D 是一套基于工艺模拟系统的有限元系统,是分析刀具设计和加工参数对加工性能影响的理想软件之一。
该软件能够根据刀具的几何形状、进给速度、切削速度、切削深度和冷却形式来预测切屑的形成过程、切削力大小、切削温度高低、刀具磨损形式等其他参数[3]。
目前Deform 23D 已经发展到6.1版本,它在原版本材料库中50多种常见材料的基础上又新增了几种材料,该系统在提升切削效率、提升系统刚性和精度方面也有了显著提升。
本文基于Deform 23D Ver6.1在高速车削加工仿真中的应用进行初步研究。
2 基于Deform 3D 软件高速车削加工的仿真实例 用Deform 3D 建立切削模型,生成FE M 网格,结合工程实际问题生成相应数据库得到FE M 模型,通过FE M 模型的分析可以精确地得到工件内的切削力、应力应变及温度分布等情况。
将所得到的仿真数据结果和经验公式计算的理论值进行对比,并修正FE M 模型,得到最终的有效模型。
图1所示为Deform 3D 环境下车削加工模拟分析过程的示意图。
该切削模型分别用进给量(Feed )、切削速度(Cutting speed )、被吃刀量(Depth of cut )三个主要参数来描述切削加工过程。
根据经验,三个参数给出合适的匹配值,可以模拟出理想的变形加工效果;另外通过该参数的大小,分析模拟的变化程度和模拟结果,从而分析这些参数对加工过程的影响[4]。
图1 车削加工模拟分析过程示意图 2.1 预处理设置预处理作为加工模拟分析的准备工作,主要完成前处理设置、生成数据库和模拟运算三个步骤[4]。
(1)工作条件的设定:选择机械加工类型车削(Turning ),单位标准SI ;切削参数值:切削速度800m/min ,被吃刀量015mm ,进给量013mm/r ;设定工作环境和接触面属性,设定环境温度20℃,工件接触属性(摩擦系数016和热导率45W ・m -1・℃-1)。
(2)刀具的设定:选择刀具类型,选择第二类刀具DNMA432,材料为WC ,定义刀具划分网格数,本例取35000个网格。
(3)工件的设定:工件属性为塑性(Plastic ),选定工件形状Curved 模式,即切削外圆,工件直径50mm ,弯曲角度20°,选择45钢作为工件的材料,工件表面划分网格数60000个。
(4)模拟条件设定:总共运算步数1000步,存储增量为每25步存一次,切削终止角度20°。
(5)生成数据库并完成模拟运算。
(6)刀具特性设置:选择等温状态,无其它模具组件,定义接触容差0.0231777及刀具约束面,刀具属性为刚体(Rigid ),材料和网格划分默认先前的设定。
(7)生成数据库并完成模拟运算。
2.2 在后处理中查看仿真结果及分析仿真过程中随着切削的进行,切削力、切削温度以及切削区的应力状态会发生相应变化。
图2所示为主切削力(纵轴)随着切削进行在时间(横轴)上变化的规律:随着刀具逐渐切入工件,切削力逐渐上升,在开始接触的很短范围内,切削力迅速升高(峰值达到341N ),之后随着切削的进行切削力逐渐稳定。
表1是切削力(包含主切削力F c 、进给力F f 和切深抗力F p )基于Deform 3D 的仿真数据与应用经验公式算得数据的对照表。
其中仿真数据是将切削力文本格式的数据取稳态部分后均值处理的最后结果,经验数据是代入单位切削力经验公式[5]分别求得的结果。
表1 切削力仿真与经验公式值的数据对比切削力(N )Deform 3D 仿真结果经验公式值主切削力F c 360.68294.3进给力F f 37.0656.34切深抗力F p74.1270.71图2 切削力F c 随着切削距离的变化图3a 和图3b 分别为工件转过112后工件和刀具的切削温度分布图,从两图中看出切削温度最高点不在刀尖处,而是离开刀尖一段距离。
整个切削过程中工件切削温度的峰值可达1030℃以上1180℃以下,刀具峰值可达359℃以上407℃以下。
图4为试件等效应力的分布。
图5为切削区最大主应力的分布,无论从图中的等效应力还是最大主应力分布状态的等高线都可看出刃前区应力分布状态最为复杂,在第一变形区等效应力数值最大并有较大变化梯度;第二变形区应力的分布较为均匀[6]。
图6为刀具的等效应力等值线图。
图7为刀具的位移变化分布云图。
从两图中可以看出刀具的应力和变形区域主要集中在刀尖处,向外沿区域呈逐渐减弱的趋势。
(a )工件的温度分布 (b )刀具的温度分布图3 工件转过112后的切削温度分布图4 切削区等效应力分布图5 切削区最大主应力分布图6 刀具的等效应力等值线图图7 刀具的位移变化分布云图将刀具和工件状态变量等值曲线分布下取得的部分状态变量分布值采集如下表2和表3所示。
表2 刀具状态变量分布值等值线变量应力MPa变形量mm温度℃A 0020B 2270.00032768.4C 4550.000654114D 6820.000981165E 9100.00131214F11400.00164262G 13600.00196310H15900.00229359表3 工件状态变量分布值等值线变量应力MPa 应变mm/mm 变形量mm 温度℃A 00020B 257 2.490.537165C 513 4.97 1.08310D 7707.46 1.62455E 10309.95 2.16600F 128012.4 2.70745G154014.9 3.24890H180017.43.781030 3 结语采用有限元法模拟切削加工可获得切削试验法或难以直接测量的状态变量,如工件和刀具的切削力分布、切削温度等,有利于更好地理解切削加工机理、评价和优化切削加工过程。
而采用有限元法分析和评价各种切削条件下的刀具磨损状况,费用低耗时短。
但是由于车削加工尤其是高速车削加工过程极其复杂,有关其切削机理的许多问题仍未得到解决[7]。
如车削过程中积屑瘤、分流等各种特定现象的研究;车床振动、冷却液等实际切削过程的工艺因素对车削模拟的影响;刀具材料的磨损机制、切削力、切屑变形和加工表面质量随实际加工过程中工件材料的相变而发生相应变化的研究;其模拟运算时间过长对制造车间在线控制的障碍;网格划分的疏密和步长设置的大小都会影响仿真的精度,如何设置才能实现最合理化等都有待进一步研究。
参考文献1 D omenico Umbrello ,Finite element simulation of conventionaland high speed machining of T i6Al4V alloy ,Journal of MaterialsProcessing T echnology ,V olume 196,Issues 1-3,21January (2008)79~872 邓文君,夏 伟,周照耀等.有限元法在切削加工过程分析中的应用.工具技术,2004,38(11):203 温效朔,王克琦.切削加工有限元仿真与应力分析.工具技术,2006,40(7):314 李传明,王向丽,闫华军.DEFORM5.03金属成形有限元分析实例指导教程.北京:机械工业出版社,20075 陈日曜.金属切削原理.北京:机械工业出版社,20076 J P Davim,C Maranhao.A study of plastic strain and plastic strain rate in machining of steel AISI1045using FE M analysis.Materials&Design,V olume30,Issue1,January(2008)160~1657 Y ung2Chang Y en,Anurag Jain,T aylan Altan.A finite element analysis of orthog onal machining using different tool edge geome2 tries.Journal of Materials Processing T echnology146(2004)72~81第一作者:黄美霞,中北大学机械工程与自动化学院, 030051太原市Author:Huang Meixia,C ollege of Mechanical Engineering& Automatization,N orth University of China,T aiyuan,030051收稿日期:2008年3月硬质合金群钻钻尖的试验研究张 波1 张 伟1 张占阳2 1大连工业大学 2大连吉瑞精密钻头有限公司摘 要:群钻钻尖具有较好的排屑性能,但群钻钻尖参数源于高速工具钢材料,其几何参数不适合于硬质合金。