含铟硫酸浸出液中铟的富集
从含铟硫酸钙渣中浸出铟的最佳工艺条件探讨

从含铟硫酸钙渣中浸出铟的最佳工艺条件探讨吕 昂,王邦伟,许志杰,闫晓丹(云锡文山锌铟冶炼有限公司,云南 文山 663700)摘 要:浸出率作为各种金属元素在湿法冶炼体系中的重要考核指标之一,是决定其能否取得高回收率的关键因素。
对于含量较低、价值较高的稀散金属,一套流程简洁、操作条件简单、浸出率高的浸出工艺尤为重要。
以下是针对一种含铟较低、用石灰石或石灰乳中和酸过程中产出的以硫酸钙含量为主的物料中,开展浸出实验,全面分析影响铟浸出率的主要因素,包括反应时长、反应温度、反应始酸、反应液固比等,已达到最佳铟浸出率。
关键词:铟;浸出率;酸度;粒度中图分类号:TF843.1 文献标识码:A 文章编号:1002-5065(2021)12-0153-2Discussion on the best technological conditions for leaching indium from calcium sulfate slag containing indium LV Ang, WANG Bang-wei, XU Zhi-jie, YAN Xiao-dan(Yunxi Wenshan zinc indium smelting Co., Ltd,Wenshan 663700,China)Abstract: Leaching rate, as one of the important evaluation indexes of various metal elements in wet smelting system, is the key factor to determine whether it can obtain high recovery rate. For rare metals with low content and high value, a set of leaching process with simple process, simple operating conditions and high leaching rate is particularly important. The following is a leaching experiment for a material with low indium content and mainly calcium sulfate content produced in the process of acid neutralization with limestone or lime milk, and comprehensively analyzes the main factors affecting indium leaching rate, including reaction time, reaction temperature, initial acid, reaction liquid-solid ratio, etc. Has reached the best indium leaching rate.Keywords: indium; leaching rate; acidity; particle size铟是一种稀有金属,在地壳中分布量散、含量低,无法形成含量较高的集中矿藏,主要是稀散分布于各种锌等矿脉中,在选矿中作为锌和其他一些金属中作为杂质存在。
湿法炼锌生产中铟的富集实践
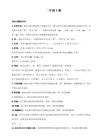
湿法炼锌生产中铟的富集实践郭天立 任益民(葫芦岛锌厂,葫芦岛,125003)摘 要 本文介绍了某湿法炼锌企业挥发窑氧化锌回收锌及铟的连续浸出工艺及生产实践,通过生产中的探索确定了最佳生产操作技术条件。
关键词 湿法炼锌 挥发窑氧化锌 综合回收 铟渣富集 湿法炼锌生产过程中,产出的各种烟尘、中间渣及溶液常含有多种有价金属,稀有金属铟便是其中之一。
铟伴生于锌精矿中,随着湿法炼锌生产过程的进行,锌精矿中的铟绝大部分进入浸出渣,并在挥发窑处理浸出渣时进入挥发窑氧化锌中。
通常挥发窑氧化锌含铟0.05%~0.09%,湿法炼锌生产中铟的综合回收,便是从挥发窑氧化锌的处理开始的。
1 传统的铟富集工艺在湿法炼锌生产过程中,传统的铟富集工艺便是传统的氧化锌浸出工艺。
我国的湿法炼锌厂,氧化锌浸出通常采用两段间断浸出,一段为中性浸出,一段为酸性浸出。
至于把中性浸出做为第一段还是把酸性浸出做为第一段,要视氧化锌中各种成份的组成及以提取哪种有价金属为主而定。
例如株洲冶炼厂,氧化锌的处理采用一段中性浸出和两段酸性浸出,生产多年,一直很顺畅。
其工艺流程见图1。
2 氧化锌连续浸出流程随着生产规模的扩大,为了减少设备,增大氧化锌处理能力,某企业采用了氧化锌连续浸出流程,其工艺流程见图2。
硫酸废电解液废电解液送矿粉系统氧化锌焙砂(送铅系统)滤液滤渣过滤中和底流上清液浓密高酸浸出In Ge Ga离心萃取滤液滤渣过滤上清液底流浓密低酸浸出滤渣滤液过滤底流上清液浓密中性浸出球磨图1 株洲冶炼厂ZnO浸出流程图氧化锌浸出槽7个,其中中浸槽4个,酸浸槽3个,单槽容积45m 3。
浸出槽采用阶梯形配置,利用槽与槽之间的高度差形成液位差保证浸出液的流动,槽内安装铅制缓冲筒,机械搅拌。
主要技术条件为: 浆化液固比:9~11∶1;中性浸出终点p H 值:5.0~5.2;中浸温度:60~70℃;中浸时间:1~1.5h ;酸浸温度:65~75℃;酸浸终点酸度:18~20g/L ;酸浸时间:8h 。
从含铟物料中提取铟

从含铟物料中提取铟一、概述我国工厂多用P204有机溶剂萃取法从冶炼中间产物中提取铟,其优点是:(一)P204对铟选择性较好,能从含铟很低的混合液中萃取铟。
(二)萃取富集倍率高达100倍以上。
(三)工艺简单,操作连续,便于实现自动化。
(四)铟的萃取回收率达高达96%~99%。
从竖罐炼锌的中间产物中回收铟的原料有1、焦结所产含铟氧化锌焦结过程中,铟随碳氢化合物燃而挥发进入氧化锌(含铟0.1%~0.2%,含锌50%~60%)中。
它是竖罐炼锌过程中数量最多、含铟品位较高的原料,约占铟总回收量的70%~80%。
2、镉系统酸浸液提镉原料中含有0.01%~0.008%的铟在中浸终点时水解,酸浸时进入酸浸液。
3、锌精馏过程副产的含铟粗铅锌精馏时,高沸点金属进入铅塔熔析炉,经熔析分离,铟富集于底层的粗铅中,含铟达0.5%~1.2%。
由于原料不同,制造萃取原液的方法也有所不同。
含铟氧化锌经酸浸、沉硅、过滤后即得萃取原液,提镉酸浸液经沉硅、过滤后即为萃取原液。
对含铟粗铅,则选经熔化,在750~800℃的温度下鼓风氧化,使铟呈氧化铟进入浮渣,用球磨机粉碎、过筛,所得粉状氧化铟以稀硫酸浸出得到硫酸铟溶液,再与氧化锌沉硅过滤后液合并。
图1为从竖罐炼锌中间产物中回收铟工艺流程实例。
图1 竖罐炼锌中间产物中回收铟工艺流程二、原料表1为竖罐炼锌的含铟中间产物成分实例。
三、技术操作条件(一)料液制备1、氧化锌浸出浸出可在机械搅拌槽内进行,采用一段酸性浸出,终点含酸20~30g/L。
氧化锌的主要成分是可溶性金属氧化物,易溶于稀硫酸溶液中,浸出率很高,渣率仅1%~5%,因此右浸出10个周期左右再排渣一次。
氧化锌浸出技术操作条件实例如下:温度85~95℃液固比(5~6)∶1始酸150~160g/L 终酸20~30g/L浸出时间2~3h 澄清时间3~4h2、沉硅氧化锌浸出液与镉酸浸液含二氧化硅(SiO2)都较高,而且波动范围很大。
实践中,原液含二氧化硅超过0.5g/L时,萃取过程中产生第三相。
铟矿石和铟的选矿冶金提取主要方法
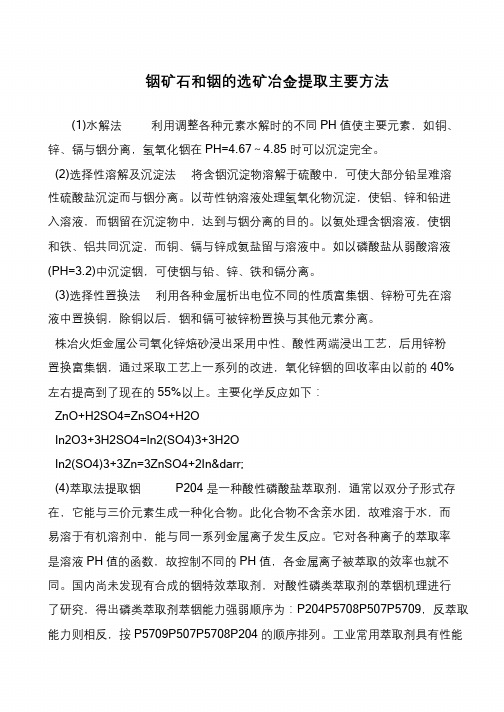
立志当早,存高远铟矿石和铟的选矿冶金提取主要方法(1)水解法利用调整各种元素水解时的不同PH 值使主要元素,如铜、锌、镉与铟分离,氢氧化铟在PH=4.67~4.85 时可以沉淀完全。
(2)选择性溶解及沉淀法将含铟沉淀物溶解于硫酸中,可使大部分铅呈难溶性硫酸盐沉淀而与铟分离。
以苛性钠溶液处理氢氧化物沉淀,使铝、锌和铅进入溶液,而铟留在沉淀物中,达到与铟分离的目的。
以氨处理含铟溶液,使铟和铁、铝共同沉淀,而铜、镉与锌成氨盐留与溶液中。
如以磷酸盐从弱酸溶液(PH=3.2)中沉淀铟,可使铟与铅、锌、铁和镉分离。
(3)选择性置换法利用各种金属析出电位不同的性质富集铟、锌粉可先在溶液中置换铜,除铜以后,铟和镉可被锌粉置换与其他元素分离。
株冶火炬金属公司氧化锌焙砂浸出采用中性、酸性两端浸出工艺,后用锌粉置换富集铟,通过采取工艺上一系列的改进,氧化锌铟的回收率由以前的40% 左右提高到了现在的55%以上。
主要化学反应如下:ZnO+H2SO4=ZnSO4+H2OIn2O3+3H2SO4=In2(SO4)3+3H2OIn2(SO4)3+3Zn=3ZnSO4+2In↓(4)萃取法提取铟P204 是一种酸性磷酸盐萃取剂,通常以双分子形式存在,它能与三价元素生成一种化合物。
此化合物不含亲水团,故难溶于水,而易溶于有机溶剂中,能与同一系列金属离子发生反应。
它对各种离子的萃取率是溶液PH 值的函数,故控制不同的PH 值,各金属离子被萃取的效率也就不同。
国内尚未发现有合成的铟特效萃取剂,对酸性磷类萃取剂的萃铟机理进行了研究,得出磷类萃取剂萃铟能力强弱顺序为:P204P5708P507P5709,反萃取能力则相反,按P5709P507P5708P204 的顺序排列。
工业常用萃取剂具有性能。
从含铟物料中提取铟

从含铟物料中提取铟一、概述我国工厂多用P204有机溶剂萃取法从冶炼中间产物中提取铟,其优点是:(一)P204对铟选择性较好,能从含铟很低的混合液中萃取铟。
(二)萃取富集倍率高达100倍以上。
(三)工艺简单,操作连续,便于实现自动化。
(四)铟的萃取回收率达高达96%~99%。
从竖罐炼锌的中间产物中回收铟的原料有1、焦结所产含铟氧化锌焦结过程中,铟随碳氢化合物燃而挥发进入氧化锌(含铟0.1%~0.2%,含锌50%~60%)中。
它是竖罐炼锌过程中数量最多、含铟品位较高的原料,约占铟总回收量的70%~80%。
2、镉系统酸浸液提镉原料中含有0.01%~0.008%的铟在中浸终点时水解,酸浸时进入酸浸液。
3、锌精馏过程副产的含铟粗铅锌精馏时,高沸点金属进入铅塔熔析炉,经熔析分离,铟富集于底层的粗铅中,含铟达0.5%~1.2%。
由于原料不同,制造萃取原液的方法也有所不同。
含铟氧化锌经酸浸、沉硅、过滤后即得萃取原液,提镉酸浸液经沉硅、过滤后即为萃取原液。
对含铟粗铅,则选经熔化,在750~800℃的温度下鼓风氧化,使铟呈氧化铟进入浮渣,用球磨机粉碎、过筛,所得粉状氧化铟以稀硫酸浸出得到硫酸铟溶液,再与氧化锌沉硅过滤后液合并。
图1为从竖罐炼锌中间产物中回收铟工艺流程实例。
图1 竖罐炼锌中间产物中回收铟工艺流程二、原料表1为竖罐炼锌的含铟中间产物成分实例。
三、技术操作条件(一)料液制备1、氧化锌浸出浸出可在机械搅拌槽内进行,采用一段酸性浸出,终点含酸20~30g/L。
氧化锌的主要成分是可溶性金属氧化物,易溶于稀硫酸溶液中,浸出率很高,渣率仅1%~5%,因此右浸出10个周期左右再排渣一次。
氧化锌浸出技术操作条件实例如下:温度85~95℃液固比(5~6)∶1始酸150~160g/L 终酸20~30g/L浸出时间2~3h 澄清时间3~4h2、沉硅氧化锌浸出液与镉酸浸液含二氧化硅(SiO2)都较高,而且波动范围很大。
实践中,原液含二氧化硅超过0.5g/L时,萃取过程中产生第三相。
高铁含铟浸出液中铟的离心萃取研究

高铁含铟浸出液中铟的离心萃取探究关键词:高铁含铟浸出液,离心萃取,铟,D2EHPA,条件优化1. 引言高铁含铟浸出液是从含矿物中萃取出来的液体,其中含有铟、铜等多种金属元素。
由于铟是一种珍贵的战略资源,在工业、光电、生物医药等领域具有广泛的应用。
因此,提高高铁含铟浸出液中铟的回收率是分外重要的。
在铟的回收过程中,萃取技术是一种被广泛应用的分离富集方法。
而离心萃取是其中一种常用的技术之一。
2. 试验部分2.1 材料与仪器试验接受的材料有:高铁含铟浸出液、N,N-二辛基甲酰胺(D2EHPA)、盐酸、氢氧化钠等。
试验接受的仪器有:电热恒温水浴、高速离心机、PH计、超声波溶解器等。
2.2 试验方法将高铁含铟浸出液转移到离心管中,加入适量的D2EHPA,调整pH值。
用超声波溶解器处理一定时间后,放入高速离心机进行离心。
将萃取液取出,测定其中铟的含量。
依据铟的回收率,确定最佳的水相pH值、D2EHPA浓度、D2EHPA用量、离心转速等最佳的操作条件。
3. 结果分析本试验中,选取了不同因素对萃取率的影响进行了试验。
如图1所示,当pH值在3-6之间时,铟的萃取率明显增加,当达到最优值时,铟的萃取率为99.2%。
进一步探究了D2EHPA的浓度、D2EHPA用量、离心转速等因素对萃取率的影响。
当D2EHPA的浓度为0.8mol/L,D2EHPA用量与高铁含铟浸出液质量比为1:1,离心转速为4000r/min时,铟的萃取率最高,达到了99.2%。
4. 结论本试验选取D2EHPA为离心萃取剂,在高铁含铟浸出液中进行了铟的提取试验。
在pH值为4,D2EHPA的浓度为0.8mol/L,D2EHPA用量与高铁含铟浸出液质量比为1:1,离心转速为4000r/min时,铟的萃取率最高,达到了99.2%。
本探究为高铁含铟浸出液中铟的回收提供了一定的理论基础和试验上的支持5. 谈论在本试验中,D2EHPA作为离心萃取剂,对高铁含铟浸出液中铟的提取效果良好。
铟锭生产工艺

铟锭生产工艺铟是一种非常重要的金属,具有良好的导电性能和耐高温性能,广泛应用于电子、航空航天、汽车和通讯等领域。
铟锭是铟生产的一种形式,现在我们来了解一下铟锭的生产工艺。
铟锭的生产主要分为以下几个步骤:1. 铟矿石的提取与净化铟主要来源于含铟矿石,例如锌矿石、银矿石和铅矿石等。
首先,将含铟矿石的矿石进行碎石,然后经过磁选、浮选和重选等工艺对矿石进行初步提取和分离。
接下来,采用氰化浸出或硫酸浸出等方法,将铟从其他杂质物质中分离出来。
最后,通过电解、浸出等工序对提取出的铟进行精炼和净化。
2. 铟锭的熔炼将提取和净化后的铟与一定比例的其他金属材料,如锡、银或铊等,按一定的配方混合均匀。
然后,将混合料放入特殊的熔炼炉中进行熔炼。
熔炼过程中需要严格控制温度和气氛,使铟和其他金属材料充分混合,并减少杂质的含量。
同时,还需通过特殊的砂型将熔融的混合料浇铸成铟锭。
3. 铟锭的冷却和加工铟锭冷却后,将其从砂型中取出,并进行表面处理和加工。
为了提高铟锭的纯度和品质,常常需要对其进行热处理或再次熔炼。
同时,还需对铟锭进行精确加工,如切割、打磨和抛光等,以达到产品要求。
4. 铟锭的包装和质检铟锭经过冷却、加工和热处理等工艺后,需要对其进行质量检测以确保其符合相关的标准和要求。
常见的检测项目包括铟锭的外观、尺寸、纯度、化学成分和线膨胀系数等。
符合要求的铟锭将被包装起来,并注明相关的标签和质保文件。
总结起来,铟锭的生产工艺主要包括铟矿石的提取与净化、铟锭的熔炼、铟锭的冷却和加工以及铟锭的包装和质检等步骤。
这些步骤相互配合,共同完成了铟锭的生产。
通过这一系列的工艺,铟锭的纯度和品质能够得到保证,以满足不同领域对铟的需求。
含铟锡烟尘硫酸氧压浸出提铟试验

加 入 氧化剂 ( HNO 、 O 等 ) 不仅 增加 成 HO 、 。 Mn ,
本, 同时在 浸 出过 程 中 , 酸 蒸 汽 挥 发 造 成 环 境 污 含 染 , 碱耗 和能 耗 也较 高 。本文 针 对 含 铟 锡 烟尘 的 酸 物 料性 质 和特点 , 用 硫 酸 氧压 浸 出 的方 法进 行 提 采
含 铟锡 烟尘 硫 酸 氧 压 浸 出提 铟试 验
黄 迎 红 王 亚雄 王 维 昌 , ,
( .云 南锡业 集 团 , 南个 旧 6 1 0 ; .昆明贵金 属研 究所 , 1 云 60 02 昆明 6 0 0 ) 5 1 6
摘要 : 对含 铟锡 烟 尘 进行 硫 酸 氧 压 浸 出 提 铟 试 验 。 考 察 了 各种 因 素 对 铟 浸 出 效 果 的 影 响 。结 果 表 明 , 含
r a h 9 . 6 u d rt ec n iin n l dn a i fl u dt oi f4:1,H2 O4ii a o c n r t no e c 3 6 % n e h o dto si cu i gr too i i os l o q d n t l n e tai f S i c o 1 0g L,la hn e e au eo 5 5 / e c i g tmp rt r f1 0℃ ,o y e a t lp e s r f0 7 MPa n e c i g tme o 5 x g n p ri r s u eo . a ,a d la hn i f1 0
中 图分 类 号 : F 4 . T 831
文献标识码 : A
文 章 编 号 :0 77 4 (0 1 1—0 50 10 —5 5 2 1 )20 3—4
I di m t a to y S lu i i e s r — i a i n Le c n n u Ex r c i n b u f r c Ac d Pr s u e Ox d to a hi g Pr c s r m n Du t wih I d u o e s f o Ti s t n i m
粗铟中铟含量的测定EDTA容量法

粗铟中铟含量的测定EDTA容量法1方法提要:试样用酸分解在有酒石酸存在下pH2~2.5的微酸性溶液中以抗坏血酸还原铁以二甲酚橙为指示剂用EDTA标准溶液滴定铟,少量的铝锌铜镉铁(Ⅱ)不干扰测定,本法适用于粗铟阳极铟电解液中等杂质较少的试样中铟的测定。
2试剂:硝酸(1+1)硫酸(1+1)20%酒石酸溶液氨水(1+1)抗坏血酸0.1%二甲酚橙溶液0.025mol/LEDTA标准溶液:称取EDTA二钠盐48g5g氢氧化钠于500mL瓶中经煮沸水溶解完全后全部倒入5000mL下口瓶中稀释至刻度混匀待标。
标定:称取纯铋(99.99%)三组分别置于500mL烧杯中,加8mL硝酸(1+2)加热至完全溶解煮沸驱除氮氧化合物,取下用水吹洗杯壁及表面皿加10mL10%的酒石酸溶液,少许抗坏血酸,加2~3滴二甲酚橙指示剂,用饱和的乙酸钠边调pH边用配制好的EDTA 标准溶液滴定至接近终点时pH1~1.5以水稀释到150mL继续用EDTA标准溶液滴定至紫红色恰变黄色为终点。
计算:T Bi=m/v N=m/(Vx0.20898)式中:T Bi:待标EDTA标准溶液对铋的滴定度(g/mL)m:称取的铋量。
V:滴定时消耗EDTA标准溶液的体积(mL)0.20898:铋的毫克原子量EDTA标准溶液对铟的滴定度按下式计算:T In=T Bi x0.5493式中0.5493为铟与铋的原子量之比3分析步骤:称取0.1500 g试样置于150mL烧杯中加8mL硝酸冷溶至激烈反应停止后,加热煮沸驱除氮氧化合物加3mL硫酸(1+1)继续加热至冒三氧化硫白烟至近干,取下冷却至室温用少量水吹洗杯壁加10mL10%酒石酸溶液加热至盐类完全溶解加水至120mL用氨水(1+1)调pH2~2.5(用精密试纸检测)加热至近沸。
取下加约0.1g抗坏血酸混匀加2mL饱和硫脲加2~3滴二甲酚橙指示剂用0.02500mol/LEDTA标准溶液滴定至红色恰变为黄色为终点4分析计算方法:In=T In V/m X 100%5注意事项:本法铋锗干扰测定但试样中含量很微可忽略不计。
离子交换法提取稀有金属铟

离子交换法提取稀有金属铟用离子交换树脂从含铟料液中吸附铟,随后解吸回收铟的过程。
工艺过程一般包括酸溶解、离子交换、洗涤和解吸铟等(见图)。
本法需要采用离子交换容量大的离子交换剂。
德国的杜依斯堡(Duisburg)铜厂采用钠型亚氨二醋酸弱酸性阳离子树脂IDA–Na(德国的商品名称为LewatitSpl00,美国的称为Dowex–Al)从含铟的锌镉渣中回收铟。
回收的方法是用硫酸溶解锌镉渣,溶液的终点酸度控制在pH2.5。
过滤所得滤液泵入盛有IDA–Na阳离子交换树脂的交换塔内进行离子交换,铟和部分锌被离子交换树脂吸附:当离子交换树脂吸附达到饱和后,先经过水洗涤,再用含硫酸1~2mol/L的溶液解吸铟:然后便可从解吸所得的In2(SO4)3解吸液中回收铟。
解吸铟后的离子交换树脂IDA–H用NaOH再生:经再生处理后的IDA–H回用。
吸附铟后的流出液和洗涤液合并后送入交换塔,控制pH4用IDA–Na离子交换树脂吸附锌,锌以硫酸解吸获得的硫酸锌溶液得以回收。
吸附锌后的流出液富含镉等,可供综合回收镉。
前苏联的车里雅宾斯克锌厂()采用离子交换法取代多次中和、溶解与富集铟的工艺从含铟料液中回收铟,铟的回收率达94%。
从含铟的盐酸料液中回收铟,可采用H型KY–2阳离子交换树脂吸附铟,再用含盐酸0.2mol/L溶液或硝酸铵解吸铟,铟与铁、锌等能得到很好分离。
也可用Amberlite IRA400或氯型Dowex–1等强碱性阴离子交换树脂吸附铟,当含铟的盐酸料液分别含盐酸3和6~7mol/L时,离子交换树脂吸附铟和镓的容量最大,而铊的吸附量则随盐酸浓度的增加而减小。
这一规律已被利用在用离子交换色谱法定量分离铝、镓、铟及铊。
本法除使铟和锌、镉、锡及铅等杂质得到有效分离外,还具有回收铟的工艺流程简短、可分别综合回收含铟料液中的其他有价金属等特点,但其应用前景在很大程度上取决于各国所生产离子交换树脂的质量和价格,也就是回收铟的经济效益如何。
萃取铟的工艺流程

萃取铟的工艺流程
1. 原料预处理
- 铟主要以伴生矿物的形式存在于其他金属矿石中,如铜矿、锌矿和铅矿等。
- 首先需要将含铟矿石进行粉碎、磨矿等物理处理,使铟矿物充分暴露出来。
2. 浸出
- 将预处理后的矿石采用酸或碱浸出,将铟溶解到溶液中。
- 常用的浸出方式包括硫酸浸出、氯化浸出和氨浸出等。
- 浸出条件如温度、浓度、时间等需要优化控制。
3. 净化溶液
- 浸出液中除了铟外,还含有其他杂质金属离子。
- 采用沉淀、萃取、离子交换等方法去除杂质,获得相对纯净的铟溶液。
4. 铟的富集
- 通过化学沉淀或溶剂萃取等方式,将净化后的溶液中的铟富集浓缩。
- 常用的富集方法有碳酸钠沉淀法、氧化锌沉淘法等。
5. 冶炼提纯
- 将富集的铟精矿或铟化合物通过热冶或湿冶的方式进行提纯。
- 采用蒸馏、电解等方法可以获得较高纯度的铟金属或铟化合物。
6. 铟产品制备
- 根据需求,将提纯后的铟制成所需形态的产品。
- 常见产品包括铟锭、铟粉、铟靶材等。
注意事项:
- 整个工艺过程需要严格控制各个环节的参数,以提高铟的回收率。
- 需要采取相应的环保措施,妥善处理产生的废料和残渣。
- 不同矿石的铟赋存状态不同,具体工艺可能有所调整。
铟的提取方法
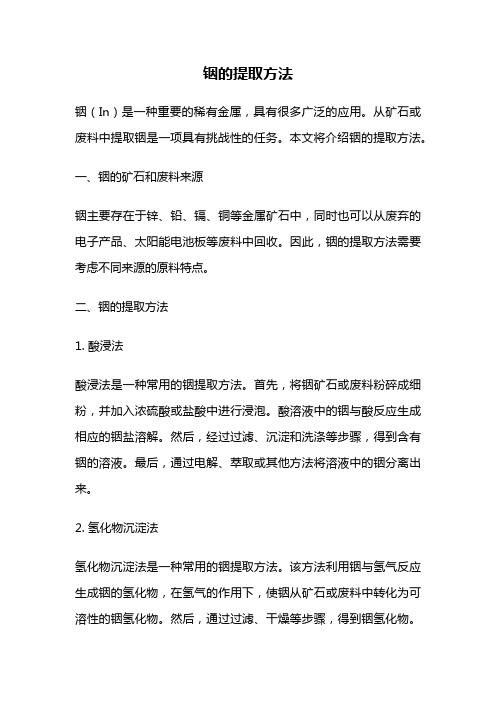
铟的提取方法铟(In)是一种重要的稀有金属,具有很多广泛的应用。
从矿石或废料中提取铟是一项具有挑战性的任务。
本文将介绍铟的提取方法。
一、铟的矿石和废料来源铟主要存在于锌、铅、镉、铜等金属矿石中,同时也可以从废弃的电子产品、太阳能电池板等废料中回收。
因此,铟的提取方法需要考虑不同来源的原料特点。
二、铟的提取方法1. 酸浸法酸浸法是一种常用的铟提取方法。
首先,将铟矿石或废料粉碎成细粉,并加入浓硫酸或盐酸中进行浸泡。
酸溶液中的铟与酸反应生成相应的铟盐溶解。
然后,经过过滤、沉淀和洗涤等步骤,得到含有铟的溶液。
最后,通过电解、萃取或其他方法将溶液中的铟分离出来。
2. 氢化物沉淀法氢化物沉淀法是一种常用的铟提取方法。
该方法利用铟与氢气反应生成铟的氢化物,在氢气的作用下,使铟从矿石或废料中转化为可溶性的铟氢化物。
然后,通过过滤、干燥等步骤,得到铟氢化物。
最后,通过煅烧或还原等方法将铟氢化物转化为纯铟。
3. 萃取法萃取法是一种常用的铟提取方法。
该方法利用萃取剂与溶液中的铟发生化学反应,形成含铟的有机相和不含铟的水相。
通过分离器将有机相和水相分离,然后再通过蒸馏或其他方法将有机相中的铟提取出来。
4. 溶剂萃取法溶剂萃取法是一种常用的铟提取方法。
该方法利用有机溶剂与溶液中的铟形成络合物,通过萃取剂的选择性提取铟。
然后,通过调整溶液的pH值或温度等条件,使络合物分解,得到含铟的溶液。
最后,通过电解、煅烧等方法将溶液中的铟分离出来。
三、铟提取方法的选择在选择铟的提取方法时,需要考虑原料特点、生产规模、成本效益等因素。
不同的方法适用于不同的场景。
酸浸法适用于矿石或废料中铟含量较高的情况;氢化物沉淀法适用于矿石或废料中铟含量较低的情况;萃取法和溶剂萃取法适用于溶液中铟含量较低的情况。
四、铟的应用铟具有良好的导电性、耐腐蚀性和热稳定性,广泛应用于电子、光电、航空航天等领域。
铟锡氧化物、铟锌氧化物等化合物被用作透明导电薄膜材料;铟磷化物被用作半导体材料;铟镓合金被用作液晶显示器的基板;铟锑合金被用作热电材料等。
含铟低酸浸出液中富集铟的研究

( c olfM tl ri l c nea dE gnei C nrl ot nvrt , h n sa4 0 8 , u a , hn ) Sh o e l gc i c n n ier g, et uh U i sy C a gh 10 3 H n n C i o au o c n r t sw s0 0 4 mm .t e e c s o m ce to n o c n r t swa 0.t e rd cin h a t e sz fZ S c n e t e a . 7 c a h x e s t e i n fZ S c n e tae s2. h e u t o tmp r t r s 9 ℃ a d rd ci n t a . . T e c n e t t n o e s l t n wa . g L a e e u t n e e au e wa 5 n e u t i w s3 0 h o me h o c n r i fF ” ou i s0 1 / f r rd ci ao o 8 t o a d t e r d c in r t fF “ w s9 . 4 .T e o t m o d t n o n i m r cp t t n b e taiain we e a n h e u t ae o e o a 7 8 % h pi mu c n i o sfr i d u p e i i i y n u r l t r s i ao z o
f l ws: t e ol o h Be ta iain i wa ni ur lz to tme s 75 ln, t e e ta ia in e e au e h n u r l to tmp r t r wa 7 o , t e x e s o f c e t f z s 0 C h e c s c ef in o i n u r lz to g n s 1 20.Un e u h o d to e taiai n a e twa . d rs c r iin.t r d f idi he g a e o n um n t e n u r l a in sa s r a h d a o e 2% i h e ta i t l g e c e b v z o
湿式硫酸化提铟
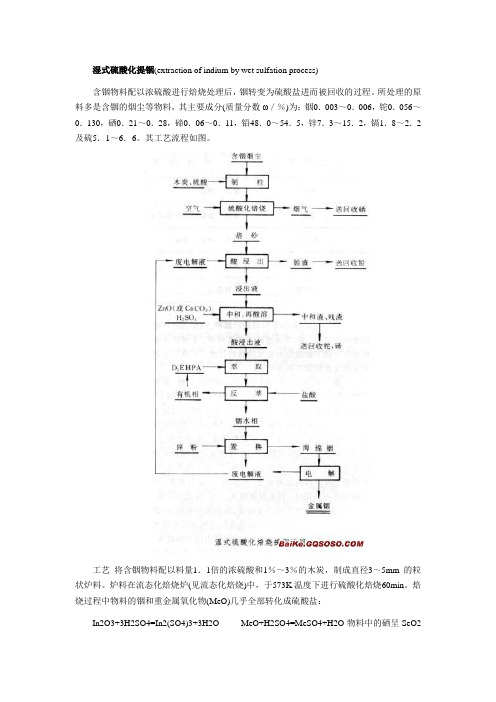
湿式硫酸化提铟(extraction of indium by wet sulfation process)含铟物料配以浓硫酸进行焙烧处理后,铟转变为硫酸盐进而被回收的过程。
所处理的原料多是含铟的烟尘等物料,其主要成分(质量分数ω/%)为:铟0.003~0.006,铊0.056~0.130,硒0.21~0.28,碲0.06~0.11,铅48.0~54.5,锌7.3~15.2,镉1.8~2.2及硫5.1~6.6。
其工艺流程如图。
工艺将含铟物料配以料量1.1倍的浓硫酸和1%~3%的木炭,制成直径3~5mm的粒状炉料。
炉料在流态化焙烧炉(见流态化焙烧)中,于573K温度下进行硫酸化焙烧60min。
焙烧过程中物料的铟和重金属氧化物(MeO)几乎全部转化成硫酸盐:In2O3+3H2SO4=In2(SO4)3+3H2O MeO+H2SO4=MeSO4+H2O物料中的硒呈SeO2形态挥发,在淋洗塔中被焙烧产生的SO2还原为单体硒而回收。
杂质氟、氯和砷等在焙烧过程中大部分挥发而除去。
产出的焙砂用废电解液或硫酸溶液浸出。
在液固比3:1、溶液终点酸度含游离酸10g/L下,加温浸出1h,得到含铟0.012g/L、铊0.18g/L、锌42g/L和镉15g/L的酸浸出液。
酸浸出液随后在318~323K温度下用ZnO中和至铟和碲几乎全部沉淀析出的程度。
所得中和渣富集铟到0.2%~0.6%,余为锌和镉等。
再用硫酸浸出中和渣,当浸出液终点酸度达到含游离酸30~40g/L时,铟便溶解,而碲仍留在渣中,实现铟、碲分离。
酸浸出液用D2EHPA萃取铟,用盐酸反萃。
所得铟反萃液用锌粉置换得海绵铟。
海绵铟再经电解可获得纯度达99.99%的金属铟。
前苏联的乌斯季•卡明诺戈尔斯克铅锌联合企业和车里雅宾斯克锌厂在含铟物料经湿式硫酸化焙烧后分别采用溶剂苹取和离子交换回收铟,铟回收率达90%左右。
展望此法具有工艺简短,易于投产,并能除去氟、氯及砷等有害杂质等特点,但存在硫酸化焙烧时需配入浓硫酸而引起操作条件差、对设备腐蚀严重等问题,故后来发展了用FeSO4替代浓硫酸的千式硫酸化法。
铟冶炼工艺操作规程

南丹县南方有色冶炼有限责任公司NDNF/JS—SC17~2010 控制状态:发放编号:铟冶炼工艺操作规程版次:A/00编制:梁世心审核:刘旭升曹晓星批准:2010年7月20日发布2010年8月1日实施南丹县南方有色冶炼有限责任公司发布目录1、范围 (2)2、概述 (2)3、生产工艺流程 (3)4、原辅材料及质量要求 (3)5、主要工序的基本原理 (4)6、工艺操作条件 (6)7、岗位操作法 (7)8、产品质量标准、验收、包装规定 (9)9、主要技术经验指标 (10)1、范围本标准规定了铟冶炼工艺流程、基本原理、原辅材料及质量要求、技术条件、岗位操作法、产出物料及质量要求,主要技术经济指标。
2、概述2.1铟的物理化学性质铟是银白色的稀散易熔金属,熔点为156.6℃,沸点2075℃,质地柔软,可塑性强,并有延展性。
原子序数49,原子量114.82,比重7.31。
金属铟在空气中是稳定的,但在加热到熔点时,表面即可生成氧化铟。
铟能缓慢溶于无机酸中,加热时溶解较快。
铟能与镓、钠、金、铝、锌、锡等形成合金,能与汞形成汞齐。
2.2铟的主要用途铟主要用于液晶显示器、半导体元件、轴承及特种合金四个方面。
还可用作原子反应堆的显示器。
涂锡的氧化铟薄膜是一种优良的防雾的遮盖外层。
2.3铟的冶炼方法至今,尚未发现具有开采和冶炼价值的独立铟矿。
铟主要从冶金和化工的副产品中回收。
均采用二大生产过程,即湿法提取部分和电解提纯部分。
低含量(1%以下)的原料提取铟有萃取法,多次置换水解法,多次中和溶解法、离子萃取法。
交换法等。
目前,较大多数生产厂均采用P2042.4铟生产的主要工艺特点2.4.1含铟原料采用高酸浸出,有较高的浸出率;萃取提纯并富集,然后置换得海绵铟。
2.4.2含铟浸出液采用P2042.4.3海绵铟熔铸得粗铟,再经氧化除铊,碘化除镉,电解提纯得四九精铟。
3、生产工艺流程(见图一)4、原辅助材料及质量要求4.1原料4.1.1铟渣4.2主要辅助材料:工业纯⑺锌块:本厂O#锌片⒀明胶:分析纯⑴P204⑵硫酸:工业纯⑻牛胶:工业纯⒁碘:分析纯⑶盐酸:工业纯⑼锰粉:工业纯⒂碘化钾:分析纯⑷草酸:工业纯⑽盐酸:分析纯⒃氯化钾:分析纯⑸烧酸:工业纯⑾硫酸:分析纯⒄煤油:200#溶剂油⑹仲辛醇:分析纯⑿甘油:工业纯图一铟生产工艺流程图5、主要工序的基本原理5.1萃取利用溶质在有机溶剂与水溶液中的溶解度不同,通过有机相与溶液混合,使水溶液中的溶质(有价金属)转入有机溶剂,以达到分离和富集有价金属的过程叫萃取。
- 1、下载文档前请自行甄别文档内容的完整性,平台不提供额外的编辑、内容补充、找答案等附加服务。
- 2、"仅部分预览"的文档,不可在线预览部分如存在完整性等问题,可反馈申请退款(可完整预览的文档不适用该条件!)。
- 3、如文档侵犯您的权益,请联系客服反馈,我们会尽快为您处理(人工客服工作时间:9:00-18:30)。
维普资讯
p ecpi ton fo r su e la hi fznc c n nta e wih fe e ti u o e sw a n si t d. n ra c ra n r i t i r m p e s r e c ng o i o ce r t t dif r n ndim c ntnt si ve tgae U de e ti a
.
.
.
.
.
文 章 编 号 : 10 —6 92 0 ) 1 1 10 0 40 0 (0 8S — 2 —5 0
含 铟 硫 酸 浸 出液 中铟 的 富集
俞小花 ,谢 刚 ,李永 刚 ,刘春侠 ,刘 康
(.昆明 理 工 大 学 材 料 与 冶 金 学 院 , 昆 明 6 0 9 :2 1 5 0 3 .云 南 冶 金 集 团 总 公 司 技 术 中心 , 昆 明 6 0 3 ) 50 1
t so e r t au , d F c n e tai n o o u i n a trr d c i n i b u . / ;t e d s g f l so e i i ft o ei v l e a e me h c n o c n t f s lto f e u t s a o t 5 g L h o a e o me t n s r o e o 0 i
摘
要:提 出从含铟硫酸溶液 中富集铟 的试验方案 :焙砂预 中和一硫化锌精矿还原一石灰石中和沉铟。在 一定 的
实 验 条 件 下 确 定 各 个 工 序 的 最 佳 条 件 :焙 砂 用 量 为 理 论 量 的 1 - ,预 中 和 后 溶 液 的酸 度 大 约 降 至 6eL 3倍 :硫 化 锌 e
Enr c i g i i ih n nd um r m u f r ca i f o s lu i cd
l a h n o u i n be r ng h g o t n f n i e c i g s l to a i i h c n e to d um i
Absr c : T e p o e s f c li e p e e t l a in z n o c n a e e u t n l so e e t l a i n f r i d u ta t h r c s o a cn r n u r i t — i c c n e t t r d ci — me t n n u r i t o n im az o r o i az o
第 1 卷专辑 1 8
Vo11 S eci11 8 p a
.
. . .
中 国 有 色 金属 学报
as The Chi es J u rn al f o n f rrou s M et l n e o o N e
. . . . . . . . . —
— — — — — — — — — — — — — — — — — —
精矿的用量为理论量的 2 ~23倍,还原后溶 液中 F ¨的浓度大 约降至 05gL 石灰石 的用量为理论量 的 20倍, . . 2 e . /: .
沉 铟 后 溶 液 中 I¨的 浓 度 降 至 l / 以 下 。 在此 最 佳 条 件 下 , 可 使 沉铟 渣 中 铟 的 品位 达 到 01 n L mg .%以上 。 关 键 词 :铟 ;预 中和 ;还 原 : 中和 沉 铟 中 图 分 类 号 :T 4 . F8 31 文献 标 识 码 :A
Kun ni 00 r ng65 93, i a; Ch n
2T c oo yC ne f u n nMe l ryGru o, u mig 50 C ia . eh lg e t o Y n a t l g o p .K n n 0 3 , hn ) n r au C 6 1
e p r n l o d t n t eo t l o d t n i v r r c d ewa u r r . e d s g fc li e i . t x e me t n i o , h p i n i o e ey p o e u sp t wa d Th o a e o ac n s 1 i so i a c i ma c i n r o f 3 me f
YU a - u XI n L n — a g , U u — i L U n Xio h a , E Ga g , I Yo g g n LI Ch n x a , I Ka g
( . a ut f tras n tl ria n ie r g Ku migUnv ri f ce c n e h oo y 1 F c l o e l dMeal gc l gn e n , n n ies o in ea dT c n lg , y Ma i a u E i y t S
t o ei a u a d e c nc n ai ol i sa u g/ h edos g fzncs fdem i r lc nc nr t s2.—2. he r tc v l e, n t o e t ton ofs uton i bo t6 L;t a e o i ul h r i ne a o e tae i 2 3
— — — — — — — — — — — — — — — —
2 0 年 6月 08
J n 20 8 u . 0
.
.
.
.
.
.
.
.
.
.
.
.
.
.
.
.
.
.
.
.
.
.
.
.
.
.
.
.
.
.
.
.
.
.
—
—
—
—
—
—
—
—
—
—
—
—
.
.
.
.
.
.
—
.
.
.
.
.
.
.
.
.
.
.
.
.
.
.
.
.
.
.
.
.
.Байду номын сангаас
.
.
.
.
.
.
.
.
.
.
.
.