2MW风机叶片梁帽与腹板的强度优化设计
2MW风力发电机轮毂优化设计

lqatf nad eic rd uawl etsad e rao t i ni nwi 厂 u i r t rsai t e t rs f m i o hjnc di ,h he l o y n re o s l h se d o t n eo to t s a n f o c 一; ; ushwt e tsad e rao t i ni n h lers whh mnh g mx sl s at rs f mtnfhjnc di a c a i e isi ai t o h h se d o i o eo to t s d e e tt i n o t n o l f -{
郑 甲红 杜 翠
( 陕西科 技大学 机 电工 程学院 , 安 70 2 ) 西 10 1
Hu p i z t n f r2 bo t mia i o MW n u bn o wid t r ie
Z HENG Ja h n , Cu i— o g DU i
(colf cai ln Eetcl nier gS axU iesy f c ne n T cnlg ,i n70 2 ,hn ) ShooMehnc d lcr aE g ei ,hni nvri Si c d eh ooyX ’ 10 1C ia aa i n n to e a a
;tr -ie i aS ta ,h h e t aily t t idm dl g en pate he d n ol ow ew i r h s ito h o i z e e i rg r i . e m s n f r c v e bi e p m e o f i nn i n e cc } K yw rsT p l yo t zt nWi ri ; u e od : o o g i a o ; n t bn H b o p mi i du e
风力发电系统中风机叶片优化设计
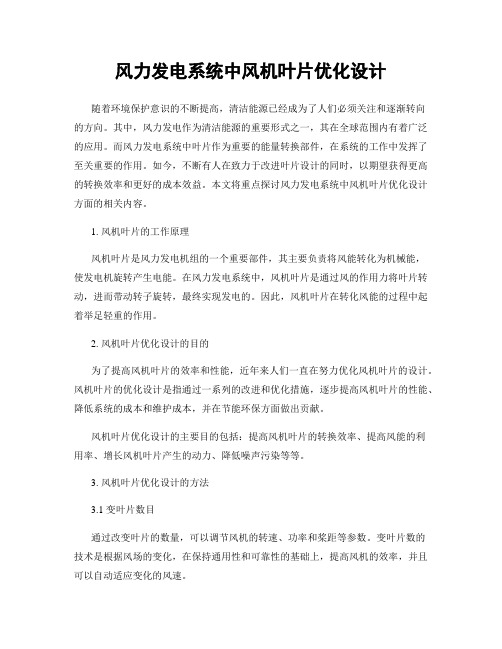
风力发电系统中风机叶片优化设计随着环境保护意识的不断提高,清洁能源已经成为了人们必须关注和逐渐转向的方向。
其中,风力发电作为清洁能源的重要形式之一,其在全球范围内有着广泛的应用。
而风力发电系统中叶片作为重要的能量转换部件,在系统的工作中发挥了至关重要的作用。
如今,不断有人在致力于改进叶片设计的同时,以期望获得更高的转换效率和更好的成本效益。
本文将重点探讨风力发电系统中风机叶片优化设计方面的相关内容。
1. 风机叶片的工作原理风机叶片是风力发电机组的一个重要部件,其主要负责将风能转化为机械能,使发电机旋转产生电能。
在风力发电系统中,风机叶片是通过风的作用力将叶片转动,进而带动转子旋转,最终实现发电的。
因此,风机叶片在转化风能的过程中起着举足轻重的作用。
2. 风机叶片优化设计的目的为了提高风机叶片的效率和性能,近年来人们一直在努力优化风机叶片的设计。
风机叶片的优化设计是指通过一系列的改进和优化措施,逐步提高风机叶片的性能、降低系统的成本和维护成本,并在节能环保方面做出贡献。
风机叶片优化设计的主要目的包括:提高风机叶片的转换效率、提高风能的利用率、增长风机叶片产生的动力、降低噪声污染等等。
3. 风机叶片优化设计的方法3.1 变叶片数目通过改变叶片的数量,可以调节风机的转速、功率和桨距等参数。
变叶片数的技术是根据风场的变化,在保持通用性和可靠性的基础上,提高风机的效率,并且可以自动适应变化的风速。
3.2 叶片弯度设计叶片弯度设计是指在保证强度和刚度的前提下,通过调整叶片剖面,轮廓和断面曲线等参数,实现风机叶片优化设计的目标。
在叶片弯度设计中,需要考虑的是叶片的剖面,以及长度、厚度、弯曲等参数的调整。
在叶片的设计中,叶片的RPM、长度,材料的选择,厚度,弯曲等因素都对性能有着深刻的影响。
3.3 叶尖形状设计叶尖形状是叶片的重要结构之一,其形状对叶片的振动、噪音和气动性能有着非常重要的影响。
因此,针对不同转速区间,需要设计最佳的叶尖形状,以达到最佳的性能和效益。
风力发电机组叶轮叶片的改进设计
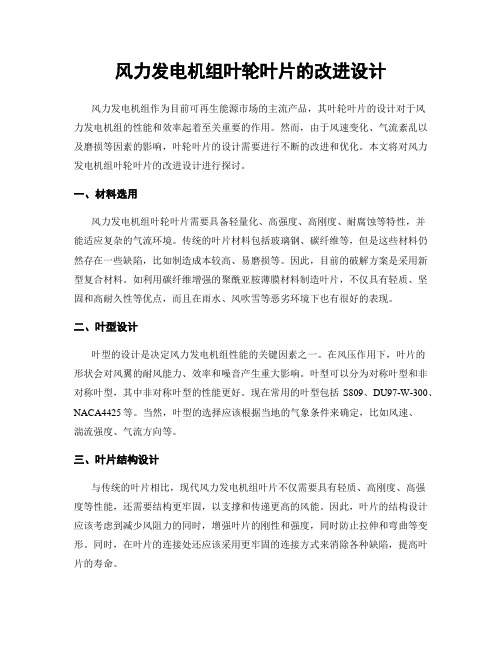
风力发电机组叶轮叶片的改进设计风力发电机组作为目前可再生能源市场的主流产品,其叶轮叶片的设计对于风力发电机组的性能和效率起着至关重要的作用。
然而,由于风速变化、气流紊乱以及磨损等因素的影响,叶轮叶片的设计需要进行不断的改进和优化。
本文将对风力发电机组叶轮叶片的改进设计进行探讨。
一、材料选用风力发电机组叶轮叶片需要具备轻量化、高强度、高刚度、耐腐蚀等特性,并能适应复杂的气流环境。
传统的叶片材料包括玻璃钢、碳纤维等,但是这些材料仍然存在一些缺陷,比如制造成本较高、易磨损等。
因此,目前的破解方案是采用新型复合材料。
如利用碳纤维增强的聚酰亚胺薄膜材料制造叶片,不仅具有轻质、坚固和高耐久性等优点,而且在雨水、风吹雪等恶劣环境下也有很好的表现。
二、叶型设计叶型的设计是决定风力发电机组性能的关键因素之一。
在风压作用下,叶片的形状会对风翼的耐风能力、效率和噪音产生重大影响。
叶型可以分为对称叶型和非对称叶型,其中非对称叶型的性能更好。
现在常用的叶型包括S809、DU97-W-300、NACA4425等。
当然,叶型的选择应该根据当地的气象条件来确定,比如风速、湍流强度、气流方向等。
三、叶片结构设计与传统的叶片相比,现代风力发电机组叶片不仅需要具有轻质、高刚度、高强度等性能,还需要结构更牢固,以支撑和传递更高的风能。
因此,叶片的结构设计应该考虑到减少风阻力的同时,增强叶片的刚性和强度,同时防止拉伸和弯曲等变形。
同时,在叶片的连接处还应该采用更牢固的连接方式来消除各种缺陷,提高叶片的寿命。
四、尾流影响多台风力发电机组并网构成风场,在这种情况下会产生大量的尾流,给设备的耐久性和维护带来很大的挑战。
在叶轮叶片的设计中应该充分考虑尾流的影响,通过优化叶片的结构和尺寸,减少尾流对叶片的影响,从而提高设备的可靠性和稳定性。
五、结论综上所述,每一次机组的重新设计和改进都是在当时的技术状态下取得的最佳结果,希望借助技术的不断发展,让风力发电机组叶轮叶片设计更加优化。
风力发电机组的叶片设计与优化策略
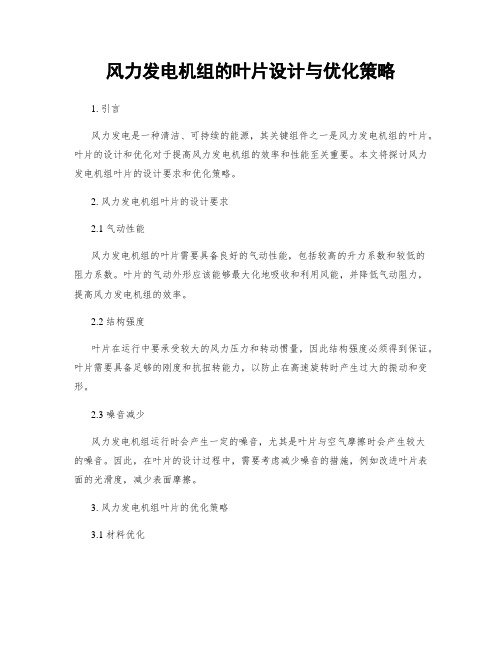
风力发电机组的叶片设计与优化策略1. 引言风力发电是一种清洁、可持续的能源,其关键组件之一是风力发电机组的叶片。
叶片的设计和优化对于提高风力发电机组的效率和性能至关重要。
本文将探讨风力发电机组叶片的设计要求和优化策略。
2. 风力发电机组叶片的设计要求2.1 气动性能风力发电机组的叶片需要具备良好的气动性能,包括较高的升力系数和较低的阻力系数。
叶片的气动外形应该能够最大化地吸收和利用风能,并降低气动阻力,提高风力发电机组的效率。
2.2 结构强度叶片在运行中要承受较大的风力压力和转动惯量,因此结构强度必须得到保证。
叶片需要具备足够的刚度和抗扭转能力,以防止在高速旋转时产生过大的振动和变形。
2.3 噪音减少风力发电机组运行时会产生一定的噪音,尤其是叶片与空气摩擦时会产生较大的噪音。
因此,在叶片的设计过程中,需要考虑减少噪音的措施,例如改进叶片表面的光滑度,减少表面摩擦。
3. 风力发电机组叶片的优化策略3.1 材料优化叶片的材料选择对于提高叶片的结构强度和抗扭转能力至关重要。
常见的叶片材料有玻璃纤维复合材料和碳纤维复合材料,这些材料具有较高的强度和轻量化的特点,是叶片制造中常用的选择。
3.2 叶片外形的优化叶片外形的优化是叶片设计中的核心问题。
一般来说,叶片的长度和弯曲度对于风力发电机组的性能有着重要的影响。
通过合理地设计叶片的曲线和扭转分布,可以达到提高风能捕捉效率的目的。
此外,还可以采用翼型优化算法,如遗传算法、粒子群算法等,来求解最佳的叶片外形。
3.3 运行参数的优化风力发电机组叶片的运行参数也可以通过优化来提高风能转化效率。
例如,通过调整叶片的旋转速度、倾斜角度和叶片的扭转分布,可以使叶片在不同风速下都能以最佳状态运行,从而最大限度地提高风能转化效率。
4. 风力发电机组叶片设计与优化的案例研究国内外许多研究人员和工程师都对风力发电机组叶片的设计和优化进行了深入研究。
例如,瑞典乌普萨拉大学的研究团队通过数值模拟和实验验证,优化了风力发电机组叶片的扭转角度分布,提高了转化效率。
风力发电机组叶片的优化设计
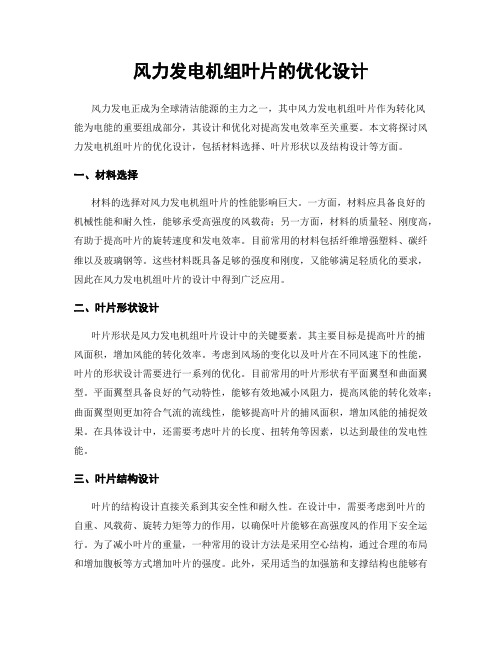
风力发电机组叶片的优化设计风力发电正成为全球清洁能源的主力之一,其中风力发电机组叶片作为转化风能为电能的重要组成部分,其设计和优化对提高发电效率至关重要。
本文将探讨风力发电机组叶片的优化设计,包括材料选择、叶片形状以及结构设计等方面。
一、材料选择材料的选择对风力发电机组叶片的性能影响巨大。
一方面,材料应具备良好的机械性能和耐久性,能够承受高强度的风载荷;另一方面,材料的质量轻、刚度高,有助于提高叶片的旋转速度和发电效率。
目前常用的材料包括纤维增强塑料、碳纤维以及玻璃钢等。
这些材料既具备足够的强度和刚度,又能够满足轻质化的要求,因此在风力发电机组叶片的设计中得到广泛应用。
二、叶片形状设计叶片形状是风力发电机组叶片设计中的关键要素。
其主要目标是提高叶片的捕风面积,增加风能的转化效率。
考虑到风场的变化以及叶片在不同风速下的性能,叶片的形状设计需要进行一系列的优化。
目前常用的叶片形状有平面翼型和曲面翼型。
平面翼型具备良好的气动特性,能够有效地减小风阻力,提高风能的转化效率;曲面翼型则更加符合气流的流线性,能够提高叶片的捕风面积,增加风能的捕捉效果。
在具体设计中,还需要考虑叶片的长度、扭转角等因素,以达到最佳的发电性能。
三、叶片结构设计叶片的结构设计直接关系到其安全性和耐久性。
在设计中,需要考虑到叶片的自重、风载荷、旋转力矩等力的作用,以确保叶片能够在高强度风的作用下安全运行。
为了减小叶片的重量,一种常用的设计方法是采用空心结构,通过合理的布局和增加腹板等方式增加叶片的强度。
此外,采用适当的加强筋和支撑结构也能够有效地提升叶片的抗风能力。
在叶片的连接结构设计中,需要采用密封、可靠的连接方式,以确保叶片在高速旋转中不会出现松动等安全隐患。
四、结论风力发电机组叶片的优化设计对提高发电效率至关重要。
在材料选择上,应考虑材料的强度、刚度以及轻质化等特性。
叶片的形状设计应注意提高捕风面积,增加风能的转化效率。
在结构设计上,需要考虑材料的强度、叶片的自重以及风载荷等因素,以确保叶片能够安全稳定地工作。
2MW风力机用47.5m叶片的结构设计的开题报告

2MW风力机用47.5m叶片的结构设计的开题报告题目:2MW风力机用47.5m叶片的结构设计的开题报告一、题目背景随着可再生能源的重要性逐渐被提高,风力发电作为其中重要的方式之一也得到了广泛的应用。
其中,风力机的叶片作为风能转换的核心组成部分,其结构设计对风力机的性能和耐久性具有至关重要的影响。
本课题将针对一款2MW风力机在47.5m叶片上的结构设计进行研究和分析。
二、研究内容1. 2MW风力机的整体架构设计2. 47.5m叶片的材料选用及结构设计3. 叶片的静态和动态分析4. 叶片的气动性能分析5. 叶片的结构优化设计三、研究意义风力机的叶片是整个机组中效率和强度影响最大的单项元件,因此对其进行科学的设计和优化可以显著提高风力机的发电效率和使用寿命,对可再生能源的开发和利用具有重要的意义。
四、研究方法1. 文献调研通过文献调研了解国内外关于2MW风力机的叶片结构设计的相关研究成果,为后续的研究提供必要的基础知识和技术参考。
2. CAD建模与静态模拟进行2MW风力机的整体架构设计和叶片的结构设计,并进行静态模拟,分析叶片的应力分布、变形情况等。
3. 气动性能分析通过计算流体力学软件对叶片进行求解,获得叶片表面的压力分布和升阻曲线等。
4. 结构优化设计结合静态模拟和气动性能分析的结果,针对叶片的结构进行优化设计,使其在保证承载性能的同时,最大化发电效率。
五、进度计划1. 第一阶段(1~2周):对相关文献进行调研,研究国内外同类项目的设计和优化情况,并对CAD建模软件和计算流体力学软件进行熟悉和学习。
2. 第二阶段(2~3周):进行整体架构设计和叶片的材料选用及结构设计,进行静态模拟,并进行初步的气动性能分析。
3. 第三阶段(2~3周):进一步完善气动性能分析,并进行叶片结构的优化设计。
4. 第四阶段(1~2周):总结优化设计的结果,撰写论文并进行答辩。
六、预期成果1. 2MW风力机用47.5m叶片的结构设计方案2. 叶片的静态和动态分析结果3. 叶片的气动性能分析结果4. 叶片的结构优化设计结果5. 一篇研究论文并进行答辩七、研究成果的意义1. 为2MW风力机用47.5m叶片的结构设计提供了一定的参考和技术支持。
风机叶片结构优化设计及性能分析

风机叶片结构优化设计及性能分析风机是一种将风能转化为机械能的装置,广泛应用于能源产业、环境保护和建筑领域。
风机的叶片结构是其重要组成部分,直接影响着风机的性能和效率。
因此,风机叶片结构的优化设计及性能分析是提高风机效率的关键。
首先,风机叶片结构的优化设计是指通过改进叶片的几何形状和构造参数,以达到最佳的风能利用效果。
优化设计应综合考虑叶片的强度、刚度和空气动力学性能等因素。
具体而言,优化设计可以从以下几个方面展开:1. 材料选择:风机叶片通常采用纤维增强复合材料制造。
不同的材料具有不同的强度和刚度特性,对叶片结构的优化设计产生重要影响。
在材料选择上,需要综合考虑成本、重量和力学性能等因素,以选择最合适的材料。
2. 几何形状设计:叶片的几何形状是影响风机性能的重要因素。
通常来说,叶片的横截面采用空气动力学优化曲线,如NACA翼型曲线。
此外,叶片的长度、扭转角度以及叶片的数量也需要根据具体的应用需求进行优化设计。
3. 加筋设计:为了增加叶片的强度和刚度,通常在叶片上设置加筋。
加筋的设计应考虑叶片的应力分布和受力情况,以提高叶片的抗弯、抗扭能力。
同时,在加筋的设计上还需注意减少结构的重量,以提高整体的轻量化效果。
其次,对风机叶片结构的性能进行分析是优化设计的重要环节。
通过性能分析,可以评估叶片在不同工况下的风能捕获能力、机械功率输出以及动力学响应等指标。
1. 流场分析:利用计算流体力学(CFD)方法,可以对风机叶片在流场中的行为进行数值模拟。
通过模拟结果,可以分析叶片的速度分布、压力分布和阻力分布等情况,从而优化叶片的气动设计。
2. 力学分析:在风机运行过程中,叶片会受到风荷载的作用,因此需要进行强度和刚度的力学分析。
通过有限元分析方法,可以模拟叶片的受力情况,预测叶片的应力分布和变形情况。
在分析中,还可以考虑动力学响应,以确保叶片在各种工况下的稳定性和可靠性。
综上所述,风机叶片结构的优化设计及性能分析是提高风能转化效率的关键。
风力机叶片结构强度复合材料力学分析方法研究

的复合 材料 及 其 规 格 参 数 和 力 学 性 能 如 表 I所 示 。
在 叶片 的设计 中 . 需 要 让 叶 片 的每 个 截 面都 承 受 所 有计 算工 况 下 的最 大 载 荷 , 并 校 核 叶 片截 面铺 层 材
其中 , 为纤维 的体积分数 , E 为纤维主方 向弹性模
量, E 为纤 维 次 方 向弹 性 模 量 , l , 为 纤 维 面 内 泊 松
料在此载荷下的强度。在 叶片的结构分析和校核计
算中. 目前主要 有 两类 分 析 方法 : A s h u r i _ 1 ] 、 王珑[ 2 ] 和 蔡新等- 3 ] 将 叶 片等 效 为 同 质悬 臂 梁 , 运 用 工 程 材 料 力 学 的方法 近 似 求 解 叶 片 截 面外 层 材 料 的正 应 力 , 称 之为 工程 材 料 力 学 分 析方 法 ; 陈进[ 4 ] 、 李慧 [ 5 ] 、 宗 楠楠 [ 6 ] 等 运 用 有 限元 软 件 对 叶 片进 行 建 模 和 分 析 ,
材料代号
材料名
/ % / M P a E r / M P a
发现 , 工程材料力学分析方法虽然具有较高
的 时间效 率 , 但它 只 能求解 叶 片截 面 的正 应力 , 不 能 计算 叶 片截 面 的剪 切 应 力 和 叶 片 各 层 材 料 的应 力 , 计算 结果 的精 度 不 高 ; 经 过 验 证 的有 限元 分 析 方 法 虽然 具有 较 高 的求 解 精度 。 但 其 时间开 销 大 , 求解 效 率较 低 , 将 其 运用 在 叶片 的优 化设 计 中时 , 一 次计 算 要耗 费较 多 的 时 间 。因 此 , 构 建 叶 片 的复 合 材 料 结
1 6
风机叶片的强度和刚度优化设计

风机叶片的强度和刚度优化设计风机叶片的强度和刚度优化设计是风机设计中关键的一步,对于提高风机的性能和安全性具有重要意义。
本文将从风机叶片的设计原理、优化方法和实际应用等方面进行探讨。
风机叶片的设计原理是基于叶片的运动原理和受力分布进行的。
在风机运行时,叶片受到来自风压和离心力等多方面的力的作用,因此叶片的强度和刚度设计必须要考虑叶片的受力情况。
较为常见的优化方法有有限元分析、拓扑优化、材料优化等。
例如,有限元分析是通过对叶片进行离散网格划分,在叶片受力情况下进行数值模拟,得到叶片应力、位移等情况,进而了解叶片的受力情况和结构响应情况。
而拓扑优化是通过对叶片结构进行形状、材料等参数的调整,以提高叶片的性能。
风机叶片的强度和刚度设计对于整个风机的性能具有重要影响。
一方面,叶片的设计直接影响到风机的动力输出和运行安全。
另一方面,叶片的设计也时刻考虑到风机的工作环境和使用寿命等因素。
因此,对于风机叶片的强度和刚度设计需要进行全面系统的考虑和优化。
实际应用中,风机叶片的强度和刚度设计需要综合考虑多方面因素。
首先,对叶片材料的选择是至关重要的。
不同的材料具有不同的强度和刚度特性,必须根据实际情况进行选择。
其次,叶片结构的设计也需要考虑叶片的外形和内部结构布局等因素。
例如,叶片的外形要尽可能减小风阻,而内部结构要保证叶片的刚度和强度。
此外,叶片的制造工艺和安装调试也对叶片的强度和刚度具有重要影响。
总之,风机叶片的强度和刚度优化设计是风机设计中的重要环节。
通过合理的设计原则和优化方法,可以提高风机的性能,延长风机的使用寿命,并且提高风机的安全性。
在实际应用中,需要综合考虑多方面因素,以确保叶片的强度和刚度设计能够满足风机的实际需要。
希望本文的探讨能给风机叶片的设计和优化提供一些帮助。
风电机组叶片维护装备的材料强度分析与优化

风电机组叶片维护装备的材料强度分析与优化随着清洁能源的迅猛发展,风电作为一种利用风能发电的可再生能源技术,受到越来越多的关注和应用。
在风力发电机组中,叶片是核心部件之一,其质量和性能的优化对于提高风电机组的效率和寿命至关重要。
为了确保风电机组叶片的安全运行和稳定性,我们需要进行材料强度分析与优化。
首先,我们需要对风电机组叶片所受到的力学负荷进行分析。
叶片在运行中会承受到弯曲、拉伸、压缩、剪切等多种力学载荷,因此需要选择耐疲劳、高强度和刚度的材料来保证叶片的可靠性。
在材料选择上,常用的叶片材料包括玻璃纤维增强聚酯树脂(GF/UP)、碳纤维增强聚合物(CFRP)、玻璃纤维增强环氧树脂(GF/EP)等。
这些材料具有良好的强度和韧性,能够承受较大的力学负荷。
然而,不同材料的强度、韧性和成本存在差异,因此需要进行材料强度分析与优化。
在材料强度分析方面,我们可以通过有限元分析方法来模拟叶片在不同载荷下的应力分布和变形情况。
有限元分析可以将复杂的结构分解为多个小元素,在每个小元素上计算受力情况,从而获得整个结构的应力分布情况。
通过分析应力分布情况,我们可以评估叶片在不同工况下的强度和疲劳寿命。
在优化材料强度方面,我们可以通过调整叶片的结构设计和材料组成来提高其强度和性能。
例如,可以通过增加叶片的截面厚度、改变纤维层的排列方式、增加纤维的含量等方式来增加材料的强度。
此外,可以结合材料强度分析的结果,选择合适的材料和加工工艺来提高叶片的疲劳寿命。
除了材料强度分析和优化,风电机组叶片的维护装备也是关键的一环。
因为叶片在使用过程中容易受到颗粒物和鸟类碰撞等外力损伤,需要进行定期的检查和维护。
维护装备应具备以下几个方面的功能:首先,维护装备应具备检测叶片损伤的能力。
可以使用红外线摄像机、超声波检测设备等技术对叶片进行全面的检测,及时发现并记录叶片上的损伤,以便后续的维护和修复。
此外,还可以使用无人机等技术进行快速的巡检,提高检测效率和精度。
风力机叶片截面刚度优化设计

风力机叶片截面刚度优化设计风力机叶片是将风能转化为机械能的关键部件,其设计对于风力机的性能具有重要影响。
叶片截面的刚度是影响叶片的结构强度和动力特性的重要指标之一。
本文将介绍风力机叶片截面刚度优化设计的相关参考内容。
1. 现状分析:首先进行风力机叶片设计的现状分析,了解目前叶片设计中存在的问题和挑战。
可以参考已有的文献和专利,分析不同设计方案的优劣势、设计的局限性等。
2. 材料力学知识:风力机叶片通常采用复合材料制造,因此对材料力学知识的理解是必要的。
需要了解不同材料的力学性能,包括拉伸强度、弹性模量、断裂韧性等。
同时,还需要了解复合材料的层合板理论和本构模型,以便进行叶片截面的刚度优化设计。
3. 结构优化方法:优化方法是进行叶片截面刚度优化设计的关键工具。
常见的结构优化方法包括有限元法、遗传算法、拓扑优化等。
有限元法可以用于叶片的力学分析,根据受力情况给出合理的叶片截面刚度分布。
遗传算法则可以采用进化搜索的方式,寻找最优的叶片截面形状。
拓扑优化方法则可用于优化材料的分布,进一步提高叶片的结构性能。
4. 设计指标选择:针对风力机叶片截面刚度优化设计,需要确定适当的设计指标。
设计指标通常包括叶片的动力特性(如自由振动频率、气动阻尼等)和结构强度(如应力、振动幅值等)。
具体的设计指标可根据具体需求确定。
5. 参数化建模:参数化建模是进行风力机叶片截面优化设计的一种常用方法。
通过将叶片的几何形状进行参数化描述,可以方便地进行优化设计。
参数化建模可以采用CAD软件(如UG、CATIA等)进行建模,或者使用专门的参数化建模软件进行建模。
6. 验证和评估:最后,对优化设计的叶片截面进行验证和评估。
可以采用有限元法进行力学分析,模拟不同风速和工况下叶片的受力情况。
也可以进行模型试验,通过对叶片的振动和结构应力进行测试,验证设计的有效性。
综上所述,风力机叶片截面刚度优化设计涉及到现状分析、材料力学知识、结构优化方法、参数化建模以及验证和评估等方面。
风电叶片二次合模用腹板粘接结构胶研究
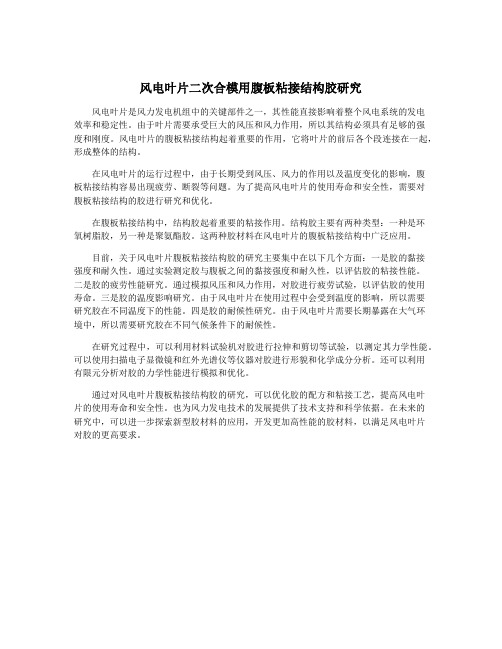
风电叶片二次合模用腹板粘接结构胶研究风电叶片是风力发电机组中的关键部件之一,其性能直接影响着整个风电系统的发电效率和稳定性。
由于叶片需要承受巨大的风压和风力作用,所以其结构必须具有足够的强度和刚度。
风电叶片的腹板粘接结构起着重要的作用,它将叶片的前后各个段连接在一起,形成整体的结构。
在风电叶片的运行过程中,由于长期受到风压、风力的作用以及温度变化的影响,腹板粘接结构容易出现疲劳、断裂等问题。
为了提高风电叶片的使用寿命和安全性,需要对腹板粘接结构的胶进行研究和优化。
在腹板粘接结构中,结构胶起着重要的粘接作用。
结构胶主要有两种类型:一种是环氧树脂胶,另一种是聚氨酯胶。
这两种胶材料在风电叶片的腹板粘接结构中广泛应用。
目前,关于风电叶片腹板粘接结构胶的研究主要集中在以下几个方面:一是胶的黏接强度和耐久性。
通过实验测定胶与腹板之间的黏接强度和耐久性,以评估胶的粘接性能。
二是胶的疲劳性能研究。
通过模拟风压和风力作用,对胶进行疲劳试验,以评估胶的使用寿命。
三是胶的温度影响研究。
由于风电叶片在使用过程中会受到温度的影响,所以需要研究胶在不同温度下的性能。
四是胶的耐候性研究。
由于风电叶片需要长期暴露在大气环境中,所以需要研究胶在不同气候条件下的耐候性。
在研究过程中,可以利用材料试验机对胶进行拉伸和剪切等试验,以测定其力学性能。
可以使用扫描电子显微镜和红外光谱仪等仪器对胶进行形貌和化学成分分析。
还可以利用有限元分析对胶的力学性能进行模拟和优化。
通过对风电叶片腹板粘接结构胶的研究,可以优化胶的配方和粘接工艺,提高风电叶片的使用寿命和安全性。
也为风力发电技术的发展提供了技术支持和科学依据。
在未来的研究中,可以进一步探索新型胶材料的应用,开发更加高性能的胶材料,以满足风电叶片对胶的更高要求。
风电叶片二次合模用腹板粘接结构胶研究

风电叶片二次合模用腹板粘接结构胶研究风电叶片是风力发电机组的关键部件,它直接影响着发电机组的性能和稳定性。
叶片的质量和耐久性是关键因素之一,而叶片的制造工艺和材料选择则直接决定了叶片的质量和性能。
而在叶片制造过程中,叶片的腹板粘接结构是至关重要的一环。
在现代的风力发电技术中,风电叶片通常采用玻璃钢材料制造,这种材料具有优良的性能和适合的重量,但是在制造过程中却存在着一些技术难题。
叶片的腹板粘接结构是一项关键的工艺,它直接影响着叶片的整体性能和稳定性。
目前,叶片的腹板粘接结构通常采用二次合模的工艺,即将腹板和叶片表面采用不同的模具分别进行成型,然后再将它们粘接在一起。
在这一工艺中,腹板粘接结构的胶水选择和粘接工艺是至关重要的。
一款优秀的腹板粘接结构胶应该具有良好的粘接性能、耐候性以及耐腐蚀性能,同时还要符合环保要求。
针对风电叶片腹板粘接结构胶的研究具有重要的意义和价值。
目前,国内外对于风电叶片腹板粘接结构胶的研究还相对较少,相关的研究成果也比较零碎。
本文就风电叶片腹板粘接结构胶进行了一系列的研究,从材料的选取、工艺的优化以及性能的测试等多个方面进行了探讨和分析。
我们对风电叶片腹板粘接结构胶的使用环境进行了分析。
叶片作为在恶劣环境下工作的部件,其腹板粘接结构胶需要具有非常良好的耐候性和耐腐蚀性能。
我们选择了一系列具有优异性能的材料作为研究对象,包括环氧树脂、聚氨酯等材料。
我们针对这些材料进行了一系列的性能测试。
包括拉伸强度、压缩强度、耐热性、耐候性、耐腐蚀性等性能指标的测试。
通过这些测试,我们可以有效地评估不同材料的适用性和性能,为后续的工艺优化和选择提供科学的依据。
然后,我们还对不同材料在实际工艺中的应用进行了研究。
我们通过实际的工艺试验,来测试不同材料在风电叶片腹板粘接结构中的表现,包括粘接性能、耐候性、耐腐蚀性能等。
通过这些试验,我们可以比较不同材料在实际工艺中的表现差异,并找出其中的优缺点。
风电叶片二次合模用腹板粘接结构胶研究

风电叶片二次合模用腹板粘接结构胶研究【摘要】本研究旨在探讨风电叶片二次合模用腹板粘接结构胶的性能及优化。
通过对材料与方法的详细描述和实验结果的分析,我们发现采用特定结构胶能够提高叶片的粘接强度和稳定性。
讨论部分对胶接工艺存在的问题进行探讨,并提出了结构优化的建议。
进一步的性能测试表明,优化后的胶接结构能够显著提升叶片的整体性能。
通过本研究,我们得出风电叶片二次合模用腹板粘接结构胶的结论,为相关领域的工程应用提供了重要参考依据。
【关键词】风电叶片、二次合模、腹板、粘接结构胶、研究、材料与方法、实验结果、讨论、结构优化、性能测试、结论1. 引言1.1 风电叶片二次合模用腹板粘接结构胶研究风电叶片是风力发电机组的主要组成部分,其叶片的质量和性能直接影响着发电效率和运行稳定性。
为了提高叶片的性能和减轻重量,目前市场上主要采用复合材料制造风电叶片。
在制造过程中,叶片需要多次合模以达到设计要求,这就需要在叶片的结构中添加腹板进行加固。
为了增强腹板与叶片的连接强度和稳定性,采用粘接结构胶来实现腹板与叶片的粘接。
本研究旨在探讨风电叶片二次合模用腹板粘接结构胶的研究。
通过对材料与方法、实验结果、讨论、结构优化和性能测试等方面的研究,我们力求找到最适合风电叶片腹板粘接的结构胶,并提出相应的结构优化建议。
希望通过本研究能够为提高风电叶片的性能和稳定性提供有效的技术支持,推动风力发电行业的健康发展。
2. 正文2.1 材料与方法风电叶片二次合模用腹板粘接结构胶的研究需要选择适合的材料和合适的方法进行实验。
在本研究中,我们选取了优质的胶粘剂,并采用了严格的实验方法进行测试。
我们选择了具有优良粘接性能的环氧树脂作为胶粘剂的主要成分。
环氧树脂在风电叶片研究中被广泛应用,具有耐高温、耐腐蚀、高强度的特点,非常适合作为风电叶片的粘接材料。
在实验过程中,我们首先对环氧树脂进行了严格的质量测试,确保其符合相关的标准要求。
然后,我们将环氧树脂与其他助剂进行了混合,并根据预先设计好的比例进行搅拌,以确保胶粘剂的均匀性和稳定性。
风电叶片二次合模用腹板粘接结构胶研究

风电叶片二次合模用腹板粘接结构胶研究风电叶片是风力发电机的重要组成部分,其性能和质量直接影响到风力发电机的发电效率和可靠性。
叶片的制造技术和材料选择对于叶片的性能有着重要的影响。
当前,腹板粘接结构被广泛应用于风电叶片的制造中,可以提高叶片的强度和刚度,增加叶片的稳定性和耐久性。
研究风电叶片二次合模用腹板粘接结构胶的性能和工艺技术具有重要的意义。
胶粘剂是连接腹板和叶片的重要材料,其性能直接决定了腹板粘接结构的可靠性和稳定性。
常用的胶粘剂有环氧树脂、聚氨酯、丙烯酸和聚酯等。
这些胶粘剂具有良好的粘接性能和强度,同时具有较好的耐候性和耐腐蚀性。
在选择胶粘剂时,需要考虑其固化时间、黏度、粘接强度、抗剪切性能和耐久性等指标。
在腹板和叶片的粘接工艺中,首先需要对腹板和叶片进行表面处理,以提高粘接的可靠性和强度。
常用的表面处理方法有机械处理、化学处理和物理处理等。
机械处理是通过打磨、抛光和喷砂等方式,清除表面的污垢和氧化物,提高粘接面的粗糙度和附着力。
化学处理是采用酸洗或碱洗等方式,去除表面的有机污染物和金属氧化物,增加粘接面的活性和吸附能力。
物理处理是通过等离子体处理或离子束辐照等方式,改变表面的化学组成和结构,增加粘接面的粘接性能和稳定性。
腹板和叶片的粘接过程中,需要考虑粘接面的匹配度和接触质量。
为了保证粘接的质量和可靠性,需要在粘接表面涂覆均匀的胶粘剂,并将腹板和叶片紧密结合,去除气泡和空隙。
在胶粘剂固化过程中,需要控制固化温度和时间,以保证胶粘剂充分固化,形成坚固的连接。
对粘接剂的质量进行测试和评估,以确保粘接过程的可靠性和稳定性。
常用的测试方法包括拉伸试验、剪切试验和剥离试验等。
这些测试可以评估粘接剂的强度、刚度和耐久性等性能指标,为叶片的制造提供科学依据。
风电叶片二次合模用腹板粘接结构胶的研究对于提高叶片的性能和质量具有重要的意义。
通过选择合适的胶粘剂和粘接工艺,可以提高叶片的强度和稳定性,延长叶片的使用寿命。
风机叶片的强度和刚度优化设计的开题报告

风机叶片的强度和刚度优化设计的开题报告一、课题背景风机作为一种常见的能源转化设备,其叶片的强度和刚度对于风机的性能和寿命起着至关重要的作用。
目前,工程实践中常采用的风机叶片设计方法多基于经验式和试错法,无法有效保证叶片的优化设计。
因此,采用数值模拟方法和优化算法,对风机叶片的强度和刚度进行优化设计,具有重要的理论和应用价值。
二、研究内容本课题旨在利用数值模拟方法和优化算法,对风机叶片的强度和刚度进行优化设计。
具体研究内容包括以下几个方面:(1)建立风机叶片的有限元模型,分析其受力情况和应力分布;(2)利用优化算法,对叶片的剖面形状和尺寸进行优化设计,以达到最佳的强度和刚度要求;(3)分析叶片的优化设计对风机性能和寿命的影响,评估优化效果。
三、研究方法和技术路线本课题将采用以下数值模拟方法和优化算法进行研究:(1)基于有限元分析软件Abaqus建立风机叶片的三维模型,并进行静态和动态分析,以获取叶片受力情况和应力分布情况;(2)采用多目标优化算法NSGA-II,对叶片的剖面形状和尺寸进行优化设计,以达到最佳的强度和刚度要求;(3)分析叶片的优化设计对风机性能和寿命的影响,评估优化效果。
四、研究进度计划本课题的研究进度计划如下:(1)第一季度:建立风机叶片的有限元模型,进行静态分析,获取叶片受力情况和应力分布情况,并对优化算法进行调研和选择;(2)第二季度:进行风机叶片的动态分析,分析叶片的振动特性,并根据振动特性优化叶片的剖面形状和尺寸;(3)第三季度:完成叶片强度和刚度的优化设计,并进行优化效果的评估;(4)第四季度:撰写研究报告和发表相关学术论文。
五、参考文献[1] Chen S J, Cai Y X, Wang M L, et al. Optimization design of wind turbine blade based on NSGA-II[J]. Applied mechanics and materials, 2014, 510-511: 976-981.[2] Lin C D, Chang Y H. Structural optimization of a horizontal-axis wind turbine blade using a multi-level optimization algorithm[C]//16th International Conference on Sustainable Energy Technologies. Setúbal, Portugal, 2017: 691-700.[3] Li Y, Li Y, Liu Y, et al. A multi-objective optimization approach for wind turbine blade design based on a genetic algorithm[C]//5th International Conference on Information Science and Control Engineering (ICISCE). Shaanxi, China, 2018: 134-138.。
- 1、下载文档前请自行甄别文档内容的完整性,平台不提供额外的编辑、内容补充、找答案等附加服务。
- 2、"仅部分预览"的文档,不可在线预览部分如存在完整性等问题,可反馈申请退款(可完整预览的文档不适用该条件!)。
- 3、如文档侵犯您的权益,请联系客服反馈,我们会尽快为您处理(人工客服工作时间:9:00-18:30)。
合成 材料 老化 与应 用
2 l
2 M W风机 叶片梁 帽与腹板 的强度优化设计术
冯 消冰 ,孙 树立 ( 北 京大 学工 学院 ,北 算 法发 展 成为 一种 比较 普及 的优 化算 法 ,遗传 算 法 的主要特 点 是 :稳定 性好 、通 用 性 强 、全 局 收敛 性较 优 。在本 篇论 文 中 ,比较详 细地 描述 了遗 传算 法 的优化 机 理 ,而 且在 大型 风机 复合 材
来表 征 。使 用整 数编 码策 略 的主 要优 点有 :直 观 、方便 、遗传 算法 的交叉 、变异 操作 比较 容 易地进 行 。在 此之 外 ,还 构造 了适 应度 函数 以用于 遗传 算法 ,最终达 到 了 叶片粱 帽和腹 板 结构 强度优 化 的 目标 。 本论 文 展示 了基 于遗 传算 法 的大 型风 机 复合 材料 叶片 梁帽 与腹 板 的强度 优化 设计 的诸 多优 势 。想 要进 行 强度优 化 设计 ,首 先要深 入 理解 力学 原 理 ,同时也 要掌 握数 值计 算方 法 。在深入 了解 单层 复合 材料 与 叠 层 复合材 料 的弹 性理 论基 础 ,以及 在 仔细研 究改进 的遗 传算 法优 化 理论基 础之 上 , 设 定 了一 定 的铺层 规则 ,
仅将 工程 中 常用 的 四种角 度作 为 限定 的铺 层角 度 ,应用 遗传 算法 对 2 MW 风机 复合 材料 叶 片的梁 帽和 腹板
进 行 了强 度优 化 设计 。本文 的 最后 计算 结果 表 明 ,由于遗 传算 法在 处理 离散 型 问题方 面 的特 有 优势 ,故在 2 MW 风机 叶 片 的梁帽 和腹 板 的强 度优 化 设计 中 ,使用遗 传 算法进 行 强度优 化 设计 是可 行和 可信 的 。 关键 词 :层 压板 ,铺 层设 计 ,遗传 算 法 ,叶 片 ,梁 帽 ,腹板 ,强度优 化 设计
a n d t o a p p l y i t o n c a p a n d b e a m o p t i mi z a t i o n o f he t l a r g e t u r b i n e c o mp o s i t e b l a d e l a mi n a t e . I n a l l u s i o n t o t h e l a mi n a t i o n s h e l l d e s i g n p a r a me t e r h a s he t s e p a r a t e c h ra a c t e r i s t i c ,p r o p o s e d i n t e g e r c o d e s t r a t e g y t h a t i s s u i t a b l e f o r GA o p t i mi z e d d e s i g n o f c o mp o s i t e l a mi n a t i o n s h e l 1 . T h i s e n c o d i n g me ho t d i s s i mp l e a n d i n ui t t i o n a l , nd a o p e r a t e c o n v e n i e n t , a n d e a s y t o c a r r y t h r o u g h t h e c r o s s o v e r a n d
h a v e t h e f e a t u r e o f r o b u s t n e s s a n d g l o b a l c o n v e r g e n c e . T h e g o a l o f t h i s d i s s e r t a t i o n i s t o s t u d y t h e t h e o r y o f g e n e t i c a l g o r i t h m( G A)
中 图分 类号 :T B 3 3 2
S t r e ng t h Op t i mi z a t i o n o f Ca p a nd Be a m o f 2 M W W i nd Tu r bi ne Bl a de
FENG Xi a o — bi ng, S UN Sh u— l i
( C o l l e g e o f E n g i n e e r i n g ,P e k i n g U n i v e r s i t y ,B e i j i n g 1 0 0 8 7 1 ,C h i n a )
Ab s t r a c t : Ge n e t i c a l g o r i t h ms h a s b e c o me a g o o d o p t i mi z a t i o n me t h o d , wh i c h h a s b e e n r a p i d d e v e l o p e d i n t h e l a s t d e c a d e s , i t
料 叶片 的梁 帽与 腹板 的强度优 化 设计 中应 用 了遗传 算法 的优 化机 理 。考虑 到层 压板 的结构参 数具 有 离散 型
特征 ,所 以在 复合 材料 层压 板 结构 优化 设计 中应 用 遗传 算法 时 ,适 宜地 提 出 了整 数编 码策 略 ,使 用整 数编 码策 略来 进 行复 合材 料层 压 结构 的遗 传算 法优 化 设计 。所 谓整 数编 码 ,即复 合材料 层压 结构 的参 数用 整数