机械加工基础知识
机械加工基本常识
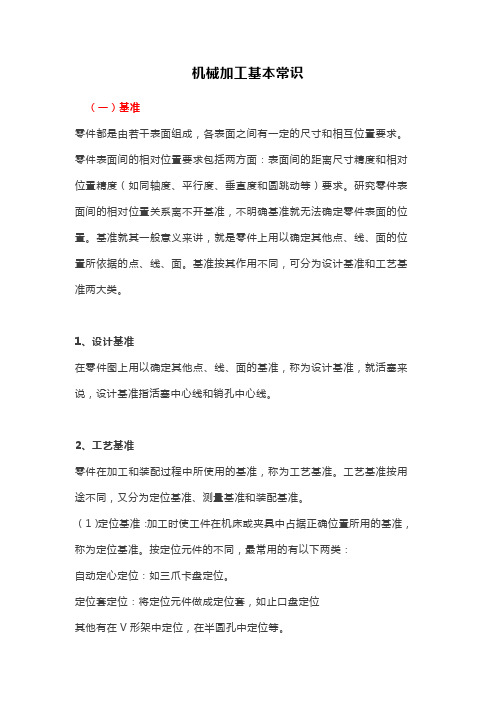
机械加工基本常识(一)基准零件都是由若干表面组成,各表面之间有一定的尺寸和相互位置要求。
零件表面间的相对位置要求包括两方面:表面间的距离尺寸精度和相对位置精度(如同轴度、平行度、垂直度和圆跳动等)要求。
研究零件表面间的相对位置关系离不开基准,不明确基准就无法确定零件表面的位置。
基准就其一般意义来讲,就是零件上用以确定其他点、线、面的位置所依据的点、线、面。
基准按其作用不同,可分为设计基准和工艺基准两大类。
1、设计基准在零件图上用以确定其他点、线、面的基准,称为设计基准,就活塞来说,设计基准指活塞中心线和销孔中心线。
2、工艺基准零件在加工和装配过程中所使用的基准,称为工艺基准。
工艺基准按用途不同,又分为定位基准、测量基准和装配基准。
(1)定位基准:加工时使工件在机床或夹具中占据正确位置所用的基准,称为定位基准。
按定位元件的不同,最常用的有以下两类:自动定心定位:如三爪卡盘定位。
定位套定位:将定位元件做成定位套,如止口盘定位其他有在V形架中定位,在半圆孔中定位等。
(2)测量基准:零件检验时,用以测量已加工表面尺寸及位置的基准,称为测量基准。
(3)装配基准:装配时用以确定零件在部件或产品中位置的基准,称为装配基准。
(二)工件的安装方式为了在工件的某一部位上加工出符合规定技术要求的表面,在机械加工前,必须使工件在机床上相对于工具占据某一正确的位置。
通常把这个过程称为工件的“定位”。
工件定位后,由于在加工中受到切削力、重力等的作用,还应采用一定的机构将工件“夹紧”,使其确定的位置保持不变。
使工件在机床上占有正确的位置并将工件夹紧的过程称为“安装”。
工件安装的好坏是机械加工中的重要问题,它不仅直接影响加工精度、工件安装的快慢、稳定性,还影响生产率的高低。
为了保证加工表面与其设计基准间的相对位置精度,工件安装时应使加工表面的设计基准相对机床占据一正确的位置。
如精车环槽工序,为了保证环槽底径与裙部轴线的圆跳动的要求,工件安装时必须使其设计基准与机床主轴的轴心线重合。
机械加工基础知识

基础知识一、基本概念1.生产过程的概念机械产品的生产过程是指将原材料转变为成品的所有劳动过程。
这里所指的成品可以是一台机器、一个部件,也可以是某种零件。
对于机器制造而言,生产过程包括:⑴原材料、半成品和成品的运输和保存;⑵生产和技术准备工作,如产品的开发和设计、工艺及工艺装备的设计与制造、各种生产资料的准备以及生产组织;⑶毛坯制造和处理;⑷零件的机械加工、热处理及其它表面处理;⑸部件或产品的装配、检验、调试、油漆和包装等。
由上可知,机械产品的生产过程是相当复杂的。
它通过的整个路线称为工艺路线。
2.工艺过程的概念工艺过程是指改变生产对象的形状、尺寸、相对位置和性质等,使其成为半成品或成品的过程。
它是生产过程的一部分。
工艺过程可分为毛坯制造、机械加工、热处理和装配等工艺过程。
机械加工工艺过程是指用机械加工的方法直接改变毛坯的形状、尺寸和表面质量,使之成为零件或部件的那部分生产过程,它包括机械加工工艺过程和机器装配工艺过程。
本书所称工艺过程均指机械加工工艺过程,以下简称为工艺过程。
在机械加工工艺过程中,针对零件的结构特点和技术要求,要采用不同的加工方法和装备,按照一定的顺序集资进行加工,才能完成由毛坯到零件的过程。
组成机械加工工艺过程的基本单元是工序。
工序又由安装、工位、工步和走刀等组成。
⑴工序一个或一组工人,在一个工作地点对同一个或同时对几个工件进行加工所连续完成的那部分工艺过程,称之为工序。
由定义可知,判别是否为同一工序的主要依据是:工作地点是否变动和加工是否连续。
生产规模不同,加工条件不同,其工艺过程及工序的划分也不同。
图1-1所示的阶梯轴,根据加工是否连续和变换机床的情况,小批量生产时,可划分为表1-1所示的三道工序;大批大量生产时,则可划分为表1-2所示的五道工序。
图1-1 阶梯轴简图表1-1 小批量生产的工艺过程表1-2 大批大量生产的工艺过程⑵安装在加工前,应先使工件在机床上或夹具中占有正确的位置,这一过程称为定位;工件定位后,将其固定,使其在加工过程中保持定位位置不变的操作称为夹紧;将工件在机床或夹具中每定位、夹紧一次所完成的那一部分工序内容称为安装。
机械加工的基础知识
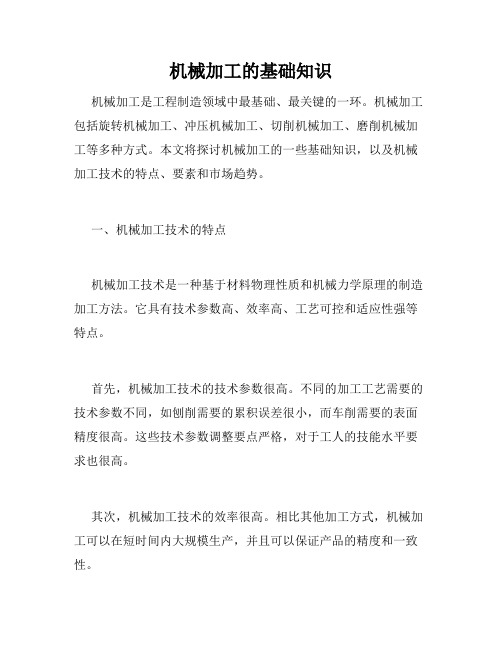
机械加工的基础知识机械加工是工程制造领域中最基础、最关键的一环。
机械加工包括旋转机械加工、冲压机械加工、切削机械加工、磨削机械加工等多种方式。
本文将探讨机械加工的一些基础知识,以及机械加工技术的特点、要素和市场趋势。
一、机械加工技术的特点机械加工技术是一种基于材料物理性质和机械力学原理的制造加工方法。
它具有技术参数高、效率高、工艺可控和适应性强等特点。
首先,机械加工技术的技术参数很高。
不同的加工工艺需要的技术参数不同,如刨削需要的累积误差很小,而车削需要的表面精度很高。
这些技术参数调整要点严格,对于工人的技能水平要求也很高。
其次,机械加工技术的效率很高。
相比其他加工方式,机械加工可以在短时间内大规模生产,并且可以保证产品的精度和一致性。
再次,机械加工技术有着很高的工艺可控性。
机械加工技术被广泛应用于各种范畴,例如餐具制造、枪械制造、汽车零部件制造、日用品制造、机械制造、电子产品制造等等。
应用于不同制造领域的机械加工技术形式也不同,如在汽车零部件制造中,机械加工技术的表面质量和尺寸精度要求都很高,而在餐具制造中,机械加工技术主要需要保证产品的稳定性和美观性。
最后,机械加工技术的适应性很强。
它可以适应很多不同材料的制造,如铜、铁、钢、铝、合金、塑料等等。
二、机械加工技术的要素机械加工技术的要素包括:加工设备、工艺参数、材料等。
首先,加工设备是机械加工技术的第一要素。
加工设备是指各种各样的加工机床,包括车床、铣床、数控加工中心、磨床、钻床等等。
选择合适的加工设备对产品的研发和生产都有着至关重要的作用。
其次,工艺参数是机械加工技术的第二要素。
工艺参数包括:切削速度、进给量、切削深度和表面质量等。
不同的加工工艺需要的工艺参数也是不同的,只有正确配置各种参数,才能保证加工的质量和效率。
第三,材料是机械加工技术的第三要素。
机械加工所应用的材料种类繁多,包括金属、非金属等。
机械加工材料的选择和合理利用,对产品的最终性质也有着非常大的影响。
机械加工基础知识

根据机床运动的不同、刀具的不同,可将去除零件毛坯多余材料的切削方法分为几种主要不同方法。
主要有:车削、刨削、磨削、钻削和特种加工等。
本节对这些主要方法逐一介绍。
一、车削车削中工件旋转,形成主切削运动。
刀具沿平行旋转轴线运动时,就形成内、外园柱面。
刀具沿与轴线相交的斜线运动,就形成锥面。
仿形车床或数控车床上,可以控制刀具沿着一条曲线进给,则形成一特定的旋转曲面。
采用成型车刀,横向进给时,也可加工出旋转曲面来。
车削还可以加工螺纹面、端平面及偏心轴等。
车削加工精度一般为IT8—IT7,表面粗糙度为6.3—1.6μm。
精车时,可达IT6—IT5,粗糙度可达0.4—0.1μm。
车削的生产率较高,切削过程比较平稳,刀具较简单。
二、铣削主切削运动是刀具的旋转。
卧铣时,平面的形成是由铣刀的外园面上的刃形成的。
立铣时,平面是由铣刀的端面刃形成的。
提高铣刀的转速可以获得较高的切削速度,因此生产率较高。
但由于铣刀刀齿的切入、切出,形成冲击,切削过程容易产生振动,因而限制了表面质量的提高。
这种冲击,也加剧了刀具的磨损和破损,往往导致硬质合金刀片的碎裂。
在切离工件的一般时间内,可以得到一定冷却,因此散热条件较好。
按照铣削时主运动速度方向与工件进给方向的相同或相反,又分为顺铣和逆铣。
顺铣铣削力的水平分力与工件的进给方向相同,工件台进给丝杠与固定螺母之间一般有间隙存在,因此切削力容易引起工件和工作台一起向前窜动,使进给量突然增大,引起打刀。
在铣削铸件或锻件等表面有硬度的工件时,顺铣刀齿首先接触工件硬皮,加剧了铣刀的磨损。
逆铣可以避免顺铣时发生的窜动现象。
逆铣时,切削厚度从零开始逐渐增大,因而刀刃开始经历了一段在切削硬化的已加工表面上挤压滑行的阶段,加速了刀具的磨损。
同时,逆铣时,铣削力将工件上抬,易引起振动,这是逆铣的不利之处。
铣削的加工精度一般可达IT8—IT7,表面粗糙度为6.3—1.6μm。
普通铣削一般只能加工平面,用成形铣刀也可以加工出固定的曲面。
机械加工的基础理论知识,平时都能遇到但你知道其中的真正含义吗
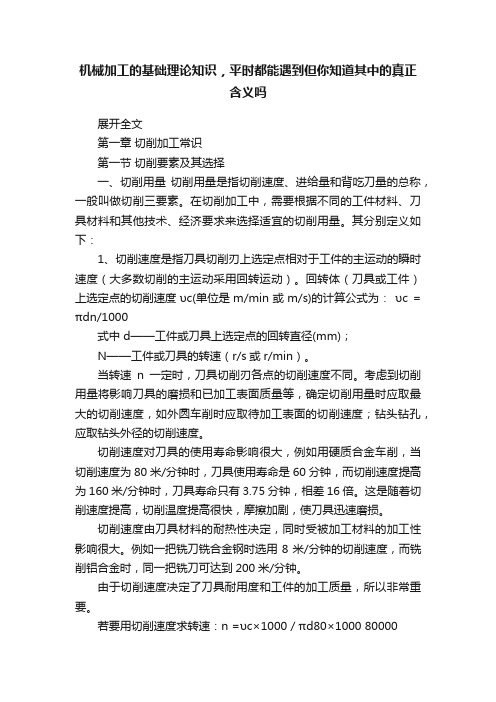
机械加工的基础理论知识,平时都能遇到但你知道其中的真正含义吗展开全文第一章切削加工常识第一节切削要素及其选择一、切削用量切削用量是指切削速度、进给量和背吃刀量的总称,一般叫做切削三要素。
在切削加工中,需要根据不同的工件材料、刀具材料和其他技术、经济要求来选择适宜的切削用量。
其分别定义如下:1、切削速度是指刀具切削刃上选定点相对于工件的主运动的瞬时速度(大多数切削的主运动采用回转运动)。
回转体(刀具或工件)上选定点的切削速度υc(单位是m/min或m/s)的计算公式为:υc = πdn/1000式中 d——工件或刀具上选定点的回转直径(mm);N——工件或刀具的转速(r/s或r/min)。
当转速n一定时,刀具切削刃各点的切削速度不同。
考虑到切削用量将影响刀具的磨损和已加工表面质量等,确定切削用量时应取最大的切削速度,如外圆车削时应取待加工表面的切削速度;钻头钻孔,应取钻头外径的切削速度。
切削速度对刀具的使用寿命影响很大,例如用硬质合金车削,当切削速度为80米/分钟时,刀具使用寿命是60分钟,而切削速度提高为160米/分钟时,刀具寿命只有3.75分钟,相差16倍。
这是随着切削速度提高,切削温度提高很快,摩擦加剧,使刀具迅速磨损。
切削速度由刀具材料的耐热性决定,同时受被加工材料的加工性影响很大。
例如一把铣刀铣合金钢时选用8米/分钟的切削速度,而铣削铝合金时,同一把铣刀可达到200米/分钟。
由于切削速度决定了刀具耐用度和工件的加工质量,所以非常重要。
若要用切削速度求转速:n =υc×1000 / πd80×1000 80000例如φ100圆钢,80m/min,求转速n,则 n = ————— = ————≈255转2、进给量(走刀量)πd 314进给量包括进给速度和每齿进给量。
进给速度进给速度是工件或刀具每回转一周时两者沿进给运动方向的相对位移,符号用f,单位mm/r(毫米/转)。
而对于刨削等主运动为往复运动的加工,进给量f的单位为mm/双行程(mm/dst)。
常用机械加工设备的基础知识

刨床
刨床是一种金属板材加工设备, 主要用于将金属板材表面刨削平
整。
刨床按照结构可以分为龙门刨床 和悬臂刨床,其中龙门刨床适用 于大型板材的刨削,而悬臂刨床
适用于小型板材的刨削。
刨床的工作原理是利用刀片对金 属板材表面进行切削,通过调整 刀片的角度和位置,可以控制刨
削的深度和表面质量。
THANKS FOR WATCHING
电阻焊的应用
广泛应用于汽车制造、家 用电器、电子设备等领域, 尤其适用于薄板和微型零 件的焊接。
激光焊接设备
激光焊接原理
激光焊接是利用高能激光束照射 工件,使金属迅速熔化并形成焊 缝。激光焊接具有高精度、高速
度和高深宽比等特点。
激光焊接设备种类
包括脉冲激光焊接机、连续激光焊 接机等。
激光焊接的应用
常用机械加工设备的基础知识
目录
• 金属切削机床 • 锻压机械 • 铸造机械 • 焊接设备 • 其他机械加工设备
01 金属切削机床
车床
车床简介
车床是机械加工中最常用的机 床之一,主要用于加工各种旋 转零件的外圆、内孔、端面等
。
工作原理
通过主轴的旋转,夹持在主轴 上的工件也跟着旋转,同时刀 具做进给运动,实现对工件的 切削加工。
感谢您的观看
落砂机是用于将铸件与砂型分离的设备,抛丸机则是 用于去除铸件表面杂质的设备。
砂型铸造是使用砂型模具进行铸造的一种工艺 ,其设备主要包括造型机、浇注机、落砂机、 抛丸机等。
浇注机是用于将熔融的金属液浇注入砂型模具中 的设备,其类型包括重力浇注机和压力浇注机。
金属型铸造设备
金属型铸造是使用金属模具 进行铸造的一种工艺,其设 备主要包括金属模具、压铸
机械加工通用基础知识

常用材料与热处理(一)判断题下列判断题中正确的请打“√”,错误的请打“ⅹ”。
1。
金属在外力作用下都要发生塑性变形。
2。
脆性材料没有屈服现象。
3。
金属材料在外力作用下产生微量塑性变形的最大应力值称为屈服点。
4。
甲乙两个零件,甲的硬度为240HBS,乙的硬度为52HRC,则甲比乙硬。
5。
用淬火钢球做压头的硬度试验都是布氏硬度试验。
6。
金属在强大的冲击力作用下,会产生疲劳现象。
7。
同种金属材料的σb值越大,表示塑性越好。
8。
同一金属材料的σs值比σb值高。
9.洛氏硬度值无单位。
10.布氏硬度试验时,工件上的压痕直径越小,其硬度值越高。
11。
铸铁的铸造性能比钢好,故常用来铸造形状复杂的工件。
12.维氏硬度值是根据测定压痕对角线长度,再查表得出的。
13.硬度越低,金属的切削加工性越好。
14.在布氏硬度值的有效范围内,HBS值越大,材料的σb值就越大15.φ是断面收缩率的符号,其数值越大,材料的韧性越强。
16。
φ值和δ值高的材料,适宜做由塑性变形加工而成型的金属构件。
( 17.σk值越大,表示金属材料的脆性越小。
(18.金属材料在受小能量多次冲击条件下,其使用寿命主要取决于材料的σk值。
19.金属材料的疲劳强度比抗拉强度低。
20.细化金属材料的表面粗糙度,可以提高材料的疲劳强度。
21.决定碳素钢性能的主要元素是碳。
22.钢中含碳量越高,其强度也越高。
23.钢铁材料中磷会使钢产生热脆性,硫会使钢产生冷脆性。
24.碳素钢的含碳量越高,钢的质量越好。
25.碳素钢是含碳量大于2.11%的铁碳合金。
26.硫是碳素钢中的主要杂质,它会引起钢的热脆性。
27.钢中含碳量的多少不仅会影响钢的力学性能,而且会影响钢的工艺性能28.碳素钢随含碳量的增加,其塑性、韧性将升高。
29.10F钢、35钢、45Mn钢、T8钢都是碳素钢。
30.08钢的含碳量为0.8%左右。
.31.45钢的含碳量为0.45%左右。
32.高碳类优质碳素结构钢的含碳量常在0.60%~0.85%之间,如60钢。
机械加工基础知识
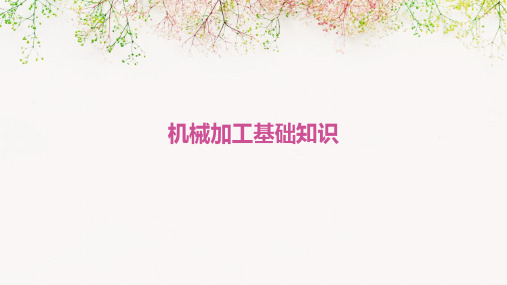
材料性能对加工的影响
硬度
硬度较高的材料加工困难,容易 损坏刀具;硬度较低的材料易于 加工,但可能影响工件加工精度;韧性差的 材料容易开裂,加工困难。
热导率
热导率高的材料在加工过程中散 热快,可减小工件变形;热导率 低的材料散热慢,工件容易变形。
刀具几何形状对加工的影响
合理的刀具几何形状可以提高加工效率、延长刀具使用寿命、提高加工 精度和减小表面粗糙度。
刀具磨损和寿命
刀具磨损的形式
包括磨料磨损、粘着磨损和热损伤等。磨料磨损是由于切屑与刀具表面之间的摩擦造成的 ;粘着磨损是由于切屑与刀具表面粘着后被撕脱造成的;热损伤是由于切削温度过高引起 的刀具表面组织变化。
、提高加工精度和减小表面粗糙度。
切削液
切削液的定义
切削液是一种用于切削加工过 程中的冷却和润滑剂,可以减 小切削力、降低切削温度、减 少刀具磨损和提高加工质量。
切削液的种类
包括油基切削液和水基切削液 两大类,其中水基切削液又可 以分为乳化液和合成切削液等 。
切削液的作用
切削液可以起到冷却、润滑、 清洗和防锈等作用,可以提高 加工效率、延长刀具使用寿命 、提高加工精度和减小表面粗 糙度。
03
机械加工工艺
切削运动
80%
切削运动定义
切削运动是指刀具与工件之间产 生相对运动,使材料被切除的过 程。
100%
切削运动的种类
包括主运动和进给运动。主运动 是刀具切入工件的主要运动,进 给运动是使切削连续进行,使多 余材料不断被切除的运动。
80%
切削运动的作用
切削运动是实现切削加工的必要 条件,通过刀具与工件的相对运 动,实现工件材料的去除和加工 表面的形成。
切削用量
机械加工工艺过程的基础知识

机械加工工艺过程的基础知识一、加工对象的选择和准备在机械加工前,需要对加工对象进行合理地选择和准备。
首先要明确加工对象的材料性质和加工要求,包括硬度、切削性能、热处理状况等。
根据加工对象的特点,选择合适的机床和切削工具,并对加工对象进行必要的前处理,如清洗、除锈、切割等。
二、机床和工具的选择机床和切削工具是机械加工的重要设备。
根据加工对象的材料性质、尺寸和形状要求,选择合适的机床和工具。
例如,对于小型零件的加工,可选择手动或半自动机床;对于大型零件的加工,可选择数控机床。
切削工具的选择要考虑材料的硬度、切削速度、切削力和切削导向性等要素。
三、工艺规范的确定机械加工工艺过程中,需要对每一道工序的加工方法、工艺参数和工艺顺序进行规范。
根据加工对象的要求,确定适当的切削速度、进给速度、切削深度和切削角度等参数。
同时,还需要根据工艺规范制定合理的送进量、给退量和回缩量等控制参数,以保证加工精度和表面质量。
四、切削原理的了解机械加工工艺过程中,切削是最常用的加工方法之一、了解切削原理有助于正确选择切削工艺和提高加工效率。
切削原理包括剪切变形、剪切应力、剪切力、刀具与工件接触面积等。
根据切削原理,可以优化刀具的结构和形状,提高切削效率和工件质量。
五、加工工艺的改进和优化机械加工过程中,通过不断地改进和优化加工工艺,可以提高加工效率和降低加工成本。
工艺改进和优化包括提高切削速度、降低切削力、改变切削轮廓和切削角度等。
同时,还可以通过改变工艺参数和工艺顺序,实现更加精密和高效的加工。
综上所述,机械加工工艺过程的基础知识包括加工对象的选择和准备、机床和工具的选择、工艺规范的确定、切削原理的了解以及加工工艺的改进和优化。
通过掌握这些基础知识,可以提高机械加工的效率和质量,满足不同加工要求。
机械加工工艺基础知识点
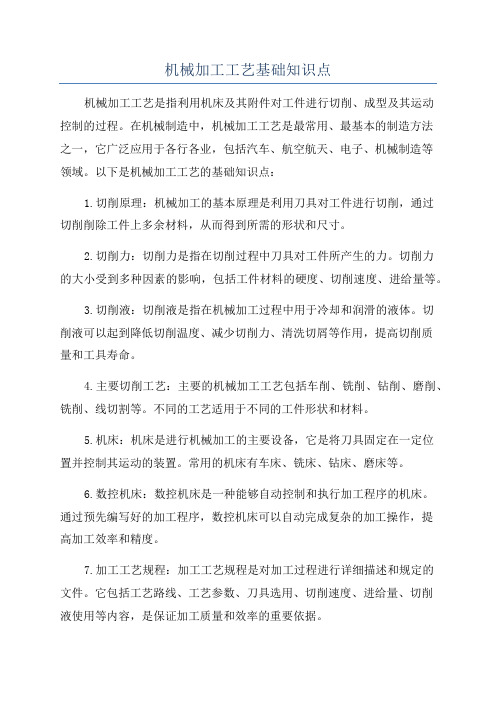
机械加工工艺基础知识点机械加工工艺是指利用机床及其附件对工件进行切削、成型及其运动控制的过程。
在机械制造中,机械加工工艺是最常用、最基本的制造方法之一,它广泛应用于各行各业,包括汽车、航空航天、电子、机械制造等领域。
以下是机械加工工艺的基础知识点:1.切削原理:机械加工的基本原理是利用刀具对工件进行切削,通过切削削除工件上多余材料,从而得到所需的形状和尺寸。
2.切削力:切削力是指在切削过程中刀具对工件所产生的力。
切削力的大小受到多种因素的影响,包括工件材料的硬度、切削速度、进给量等。
3.切削液:切削液是指在机械加工过程中用于冷却和润滑的液体。
切削液可以起到降低切削温度、减少切削力、清洗切屑等作用,提高切削质量和工具寿命。
4.主要切削工艺:主要的机械加工工艺包括车削、铣削、钻削、磨削、铣削、线切割等。
不同的工艺适用于不同的工件形状和材料。
5.机床:机床是进行机械加工的主要设备,它是将刀具固定在一定位置并控制其运动的装置。
常用的机床有车床、铣床、钻床、磨床等。
6.数控机床:数控机床是一种能够自动控制和执行加工程序的机床。
通过预先编写好的加工程序,数控机床可以自动完成复杂的加工操作,提高加工效率和精度。
7.加工工艺规程:加工工艺规程是对加工过程进行详细描述和规定的文件。
它包括工艺路线、工艺参数、刀具选用、切削速度、进给量、切削液使用等内容,是保证加工质量和效率的重要依据。
8.模具加工:模具加工是一种专门用于制造模具的机械加工工艺。
模具是用于制造复杂零件的工装,它具有高精度和复杂的形状,需要经过多道工序来完成。
9.表面处理:表面处理是对加工件表面进行涂覆、镀层或其他处理,以改善表面的性能和质量。
常见的表面处理方法包括电镀、喷涂、氮化、磷化等。
10.加工误差和精度:由于加工过程中受到各种因素的影响,加工件的尺寸和形状往往难以完全符合设计要求。
加工误差是指加工件与设计要求之间的差距,而精度是指加工件的尺寸和形状与设计要求的接近程度。
关于机械加工的认知知识
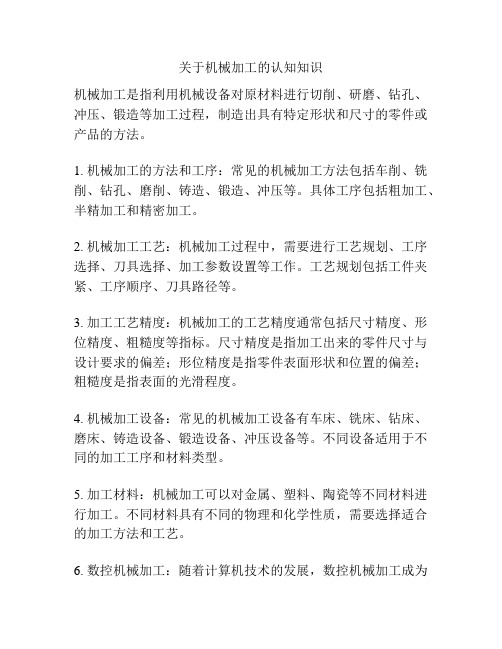
关于机械加工的认知知识
机械加工是指利用机械设备对原材料进行切削、研磨、钻孔、冲压、锻造等加工过程,制造出具有特定形状和尺寸的零件或产品的方法。
1. 机械加工的方法和工序:常见的机械加工方法包括车削、铣削、钻孔、磨削、铸造、锻造、冲压等。
具体工序包括粗加工、半精加工和精密加工。
2. 机械加工工艺:机械加工过程中,需要进行工艺规划、工序选择、刀具选择、加工参数设置等工作。
工艺规划包括工件夹紧、工序顺序、刀具路径等。
3. 加工工艺精度:机械加工的工艺精度通常包括尺寸精度、形位精度、粗糙度等指标。
尺寸精度是指加工出来的零件尺寸与设计要求的偏差;形位精度是指零件表面形状和位置的偏差;粗糙度是指表面的光滑程度。
4. 机械加工设备:常见的机械加工设备有车床、铣床、钻床、磨床、铸造设备、锻造设备、冲压设备等。
不同设备适用于不同的加工工序和材料类型。
5. 加工材料:机械加工可以对金属、塑料、陶瓷等不同材料进行加工。
不同材料具有不同的物理和化学性质,需要选择适合的加工方法和工艺。
6. 数控机械加工:随着计算机技术的发展,数控机械加工成为
现代机械加工的重要手段。
数控机床利用预先编程的指令控制机械设备进行加工,提高了加工效率和精度。
7. 刀具和切削参数:机械加工中使用的刀具包括车刀、铣刀、钻头、磨石等。
刀具的选择和切削参数的设置对加工质量和效率至关重要。
总而言之,机械加工是一种通过机械设备对原材料进行切削、研磨、钻孔、锻打等工艺过程,制造出具有特定形状和尺寸的零件或产品的方法。
掌握机械加工的基本知识非常重要,在各个制造行业中都能找到应用。
机械加工基础知识
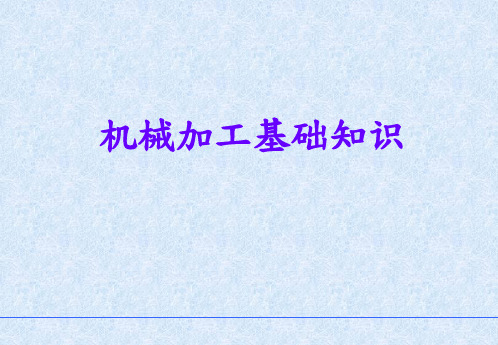
用途:用于平面磨床修整由直线和圆弧组成的各种
截面砂轮
原理:通过钻石修刀尖运动轨迹来修整砂轮圆弧内R 或外R
内 R:所需块规高度为 L=16.002+R 外 R:所需块规高度为 L=16.002-R
研磨基础知识 三. 研磨常用夹具介绍
3.3 正弦台
用途:装夹工件并配合块规使工件成一定的角度, 以便对工件进行斜面研磨加工.
3.1.2角度规:
操作:根椐工件要求调整角度垫块到所需位置,将虎钳的固定 钳口之面作为基准,角度垫块紧贴于基准上,并把工件置于v型 面定位后利用虎钳夹紧工件(铣削)。
三 铣削常用夹具介绍
角 度 规
三 铣削常用夹具介绍
直 角 尺
研磨基础知识
一 研磨机台的认知
光 学 投 影 磨 床 简 称
, P/G
原理:通过正弦台配合块规 将正弦台垫某一高度所 形成的角度来研磨工件。H=127×SINα
研磨基础知识 三. 研磨常用夹具介绍
3.4 角度成型器
用途:通过配合块规使钻石修刀的移动路线与水平 成一角度来修整砂轮、以达到砂轮至斜面成 型的目的。
工作原理图: H为所垫块规尺寸. H=L×sina L角度器之中心距为50cm A为斜面与水平面所成夹角
一 放电机台的认知
AP200
线 割 机
一 放电机台的认知
设备名称
厂牌
机器型号
AP200 NC 控制电源型号
线
加工线径(mm)
割
XYZ轴驱动方式
机 XYZ轴加工行程(mm)
加工介质
加工精度 (mm)
线切割加工机
SODICK AP200 EX21 0.07 ~~ 0.25 XYZ 轴马达驱动
- 1、下载文档前请自行甄别文档内容的完整性,平台不提供额外的编辑、内容补充、找答案等附加服务。
- 2、"仅部分预览"的文档,不可在线预览部分如存在完整性等问题,可反馈申请退款(可完整预览的文档不适用该条件!)。
- 3、如文档侵犯您的权益,请联系客服反馈,我们会尽快为您处理(人工客服工作时间:9:00-18:30)。
金属切削原理与切削刀具一、概述(一)机械制造——将原材料制成“机械零件”并装配成“机器”的一系列活动。
机械制造流程:1、市场调研→确定产品→策划→预设机构、部门;2、图样设计→编制工艺→试制→设施厂房、设备、工装;3、原材料采购→毛坯制造(铸造、锻压、冲压等)→热处理→机械加工(零件制作)→装配→调试→产品销售市场。
(二)切削加工的分类切削加工是利用切削工具从工件上切去多余材料的加工方法。
通过切削加工,使加工变成符合图样规定的形状、尺寸和表面粗糙度等方面要求的零件。
切削加工分为机械加工和钳工两大类。
1.机械加工是利用机械力对各种工件进行加工的方法。
它一般是通过工人操纵机床设备进行加工的,其方法有车削、钻削、镗削、铣削、刨削、珩削、超精加工和抛光等。
2.钳工加工一般在钳台上以手工工具为主,对工件进行加工的各种方法。
(三).切削加工的特点和作用切削加工具有如下主要特点:1.切削加工的精度和表面粗糙度的范围广泛,且可获得很高的加工精度和很低的表面粗糙度。
2.切削加工零件的材料、形状、尺寸和重量的范围较大。
3.切削加工的生产效率较高。
4.切削过程中存在切削力,刀具和工件均具有一定的强度和刚度,且刀具材料的硬度必须大于工件材料的硬度。
正是因为上述第四个特点,限制了切削加工在细微结构和高硬高强等特殊材料加工方面的应用,从而给特种加工留下了生存和发展的空间。
(四)切削加工的发展方向随着科学技术和现代工业日新月异的飞速发展,切削加工也正朝着高精度、高效率、自动代、柔性化和智能化方向发展,主要体现在以上三个方面:1.工设备朝着数控技术、精密和超精密、高速和超高速方向发展。
2.具材料朝超硬刀具材料方向发展。
3.生产规模由目前的小批量和单品种大批量抽多品种变批量的方向发展,生产方式由目前的手工操作、机械化、单机自动化、刚性流水线自动化向柔性自动化和智能自动化方向发展。
二、金属切削过程及切削原理(一).金属切削—是指机械零件中金属(黑色金属和有色金属)制品成形过程;是机械零件加工中主要部分;即:通过“机床与刀具的相对运动”,切去坯件上多余的金属材料,获得形状、位置、尺寸和表面质量符合设计图样预期要求的机械零件的全过程;金属切削过程——材料变形的过程:金属切削过程中,刀具与工件作相对运动。
在运动力(切削力)的作用下,金属材料表层首先受到刀具的挤压,发生了弹性变形,当切削力超过被切材料的弹性极限时,便发生了塑性变形(塑性材料),内部组织受到破坏,在切削力的继续作用下,金属层就被挤下来。
所以说:切屑不是切下来,而是被挤下来。
因此切削过程,实际上是个材料变形过程。
这个变形过程对被切材料的化学成份、物理性能、机械性能、热处理状态有关,也对刀具材料的性能和刀具的几何角度有关,还对机床的刚性、工艺系统的刚性、冷却液都有关。
因此是一个相当复杂的过程。
在生产实践中逐个的去认识它、分析它,也是衡量对金属切削加工理解深浅的标准。
如:①被切材料是(钢、铝、紫铜等)塑性较大的材料,切削过程有四个阶段;即:挤压(弹性变形),滑移(塑性变形)挤裂和切离而变成切屑;②被切材料是(铸铁、青铜等)脆性较大的材料,切削过程只有三个阶段;即:挤压、挤裂和切离,因为脆性材料未经塑性变形就被挤裂。
当然:切削过程中的各个阶段是连续的,非常复杂的,我们暂时不作分析。
只是对刀具有关的问题作一简单的说明——也就是磨擦和发热。
由于切削过程中,刀具前刀面与切屑的强烈磨擦,刀具主后面与切削表面的磨擦,刀具付后面与已加工表面的磨擦。
上面这些磨擦属于——外磨擦。
切削过程中,在高温高压、剧裂的变形中,材料内部分子间也发生了剧烈的磨擦这属于——内磨擦。
由于外磨擦和内磨擦产生了很高的热量,当切削热超过刀具的红热极限温度时,刀具就失去切削能力。
为了降低切削热,就要减小切屑变形和磨擦。
故是分析刀具材料、几何角度之前必须搞清的问题。
从切屑变形过程中可以知道:增大前角、主后角、付后角可以减小外磨擦,同时减小内磨擦(减小切屑变形)。
因而减小发热,有利于切削,有利于提高刀具耐用度。
但前角和后角增大,契角减小,刀具强度降低,所以是矛盾的两个方面。
因此如何合理地选择刀具材料、几何角度和切削用量是金属切削中一门主要的技术。
右图是切削过程中材料变形的示意图:切削过程示意图(二)切屑的形状 ① 崩碎切屑:(脆性材料)象:铸铁、青铜等② 挤裂切屑:(硬性材料)象:高碳钢、淬硬钢、铝铁青铜、有些铸造铝合金也属挤裂切屑。
带状切屑:(塑性材料或韧性材料),如:低碳钢、低碳合金钢、不锈钢、硅钢、镍铬钢、软铝、紫铜等。
(三)切削加工中的必备条件:1..工件与刀具必须有相对运动;2. 刀具连续不断的进给(纵向、横向、斜向或圆周);3. 主运动和辅助运动如何定义?一般:车、铣、镗、磨等----旋转运动为主运动,进给为辅助运动;创、扦、拉等-----直线运动为主运动,间接进给为辅助运动;(四)切削力的计算:切削过程中,被切金属层变形和磨擦产生了阻力——这个力称为切削力;机床必须具备足够的动力,这个动力必须大于被切材料分子结合力才能从母体上切下切屑。
刀具对被切层的挤压,迫使被切层产生弹性变形与塑性变形的力——称于变形抗力;由于切屑沿着刀具前面流出,产生了磨擦力,刀具后面与工件磨擦也产生了磨擦力,这些力合起来就是总的切削力;用P 来表示,即:P = P 2z+Px 2+Py 2 ;Pz--主切削力:作用在切削速度方向上,消耗动力占总切削力的90%以上因此设计机床、夹具、刀杆、刀具、刀片和选择切削用量时主要考虑Pz 。
切屑的形状Px--轴向力:作用在进给机构上,是设计进给机构的主要参数。
Py-- 径向力:将刀具推离被切表面,是造成让刀,引起振动的主要因素。
影响切削力的因素有:①材料性能;②刀具的几何角度;③切削用量(切削面积);切削深度与Pz成正比,进给量增加一倍时,Pz增加约70%。
切削速度对Pz影响较小。
但对切削功力N切成正比。
如N切= PzV / 6120(KW);④冷却液对切削力也有影响。
当在大面积粗加工时,要求预算切削功力N切是否小于机床系统输出功力N机输;一般用粗略公式计算:切削钢质或球墨铸铁材料时 Pz=200×t×s×K(公斤)切削铸铁或铸铝合金时 Pz=100×t×s×K(公斤)Px=0.4PzK--刀具几何角度系数;(不考虑) K=1 则: N切 = Pz V / 6120(KW);Py=0.25Pz目前我们切削的对象是压铸铝合金和铸铁,而且压铸件加工余量都较小,因此切削力或切削功力不必考虑,更不需要去计算,知道有这么回事就可以了。
(五)金属切削刀具材料:1、金属切削过程中,刀具的切削部分在高温高压和剧烈磨擦的状态下工作。
因此,刀具的切削部分应满足下列基本要求:①冷硬性:常温下具有的硬度,一般要求HRC60以上。
②耐磨性:耐磨性是指材料抵抗磨损的能力,它是材料的硬度、强度和组织结构等因素的综合反映。
③红硬性:在高温下能保持切削性能,它是评定刀具切削性能的主要指标。
④坚韧性:切削过程中,刀具受到很大的切削力,冲击和振动,刀具必须具备足够的强度和韧性,才能防止刀具脆性断裂或崩刃。
⑤抗粘附性:在高温高压下,不容易与被切金属粘结。
⑥工艺性:便于制造和热处理性能。
2、常用刀具的种类:①碳素工具钢(T12A等),或合金工具钢(9SiCr等),淬火后硬度HRC62-66,耐热温度200℃~250℃,超过250℃硬度下降,失去切削能力,目前只用于手工刀具(如锉刀、锯条、鉴子等)。
②高速钢(俗称白钢、锋钢),是含钨、铬、钒、钼等合金元素较多的,淬火后HRC64-70,耐热温度550℃~650℃,有较好的韧性、耐磨性和工艺性;常用来制造成形刀具(铣刀、铰刀、丝攻等)。
1)通用高速钢:如:W18Cr4V、W9Cr4V2、W6M O5Cr4V2等;高速钢包括2)高性能高速钢:如:W2M O9Cr4VC O8、W6M O5Cr4V2A1、W12M O3Cr4V3C O5Si等。
③硬质合金:硬质合金是由熔点很高的碳化物,如:碳化钨(WC)(3000℃~3300℃)、碳化钛(TiC)、碳化钽(TaC)、碳化铌(NbC)、碳化钒(VC)、与铁族金属钴(Co)或镍(Ni),用粉末冶金在高温高压下烧结而成。
硬质合金硬度很高,常温硬度HRA87-93(相当于HRC75-81),耐磨性好,耐热温度(800℃~1000℃),但抗弯强度和冲击韧性差,工艺性也差。
硬质合金根据材料的性能和加工对象不同分为:1)钨钻类(YG),即:WC+Co,常温硬度HRA87-92,耐热温度800℃~900℃,适用于加工铸铁、青铜和有色金属材料,如YG8(国际K30)、YG6(国际K20)、YG3(国际K01)等。
2)钨钛钻类(YT),即:WC+TiC+Co,常温硬度HRA90-93,耐热温度900℃~1000℃,在高温切削条件下比YG类耐磨,但抗弯强度比YG类差,适用于加工碳钢、合金钢等;如YT5(国际P30)、YT14(国际P20)、YT15(国际P10)、YT30(国际P01)等。
3)钨钛钽(铌)类(YW),即:WC+TiC+TaC(NbC)+Co,常温硬度HRA91-93,耐磨性、热硬性、抗粘附性、韧性和抗弯强度都较好;既可加工铸铁、有色金属也可加工碳钢、合金钢、不锈钢等,是通用性较好的刀具材料;如:YW1(国际M10)、YW2(国际M20);YA6(WC+TiC+NbC+Co)适用于加工灰口铸铁、球墨铸铁、有色金属等。
4)钢结硬质金属: WC+ TiC作为硬质相,以铬(Cr)、钼(Mo)、镍(Ni)作为粘结相,它具有良好的工艺性,淬火后硬度HRC70-73,适用于制造形状复杂的成形刀具(钻头、铰刀、滚刀、高精度量具等)。
5)碳化钛基硬质合金:即:WC+TiC+ Ni+Mo,常温硬度HRA93,耐磨性较好,但脆性大,如:YN05(国际P01)、YN10(国际P05),相当于YT30;适用于碳钢,合金钢的高精度精加工。
6)超细晶粒硬质合金YG6X(国际K10),提高了原有YG6的硬度和耐磨性,但抗弯强度有所下降,适用于有色金属、球墨铸铁、冷硬铸铁及合金铸铁的半精加工和精加工。
7)涂层刀片:用化学气相沉积的方法在韧性较好的硬质合金(YT5、YG8等)刀片上,涂复一层很薄(5-15微米)的碳化钛(TiC)或氮化钛(TiN)碳化铌(NbC)等耐磨碳化物,提高了表层硬度和耐磨性。
保持原有的抗弯强度,是目前采用最广的刀具制造工艺。
④陶瓷材料(A12O3—三氧化二铝),硬度和耐磨性都超过硬质合金,但由于脆性太大,目前很少推广。
⑤金刚石刀片(PCD):天然金刚石是目前自然界硬度最高的物质“HV10000”(硬质合金HV1500-2000),目前采用的大多数是人造金刚石(PCD),HV9000,是将金刚石粉末在极高的温度和高压下烧结聚晶而成,然后制成刀片,耐磨性很高,但抗弯强度很低,脆性很大。