封装失效分析1
FCBGA封装器件的失效分析与对策

[转帖]FCBGA封装器件的失效分析与对策Post By:2009-11-3 10:35:00以下内容只有回复后才可以浏览FCBGA封装器件的失效分析与对策摘要:FCBGA(Flip-chip ball grid array)封装形式器件是近年来集成电路封装的最佳选择,其可靠性日益引起重视。
本文简要介绍了FCBGA封装形式器件的结构特点以及相关的可靠性问题,通过两个FCBGA封装器件失效的案例,分析了两只FCBGA失效器件失效的原因,一个是芯片上的焊球间存在铅锡焊料而导致焊球短路,另一个则是因封装内填料膨胀分层而导致的焊球开路。
提出了针对这种形式封装的器件在使用过程中的注意事项及预防措施,以减少该类失效情况的发生。
关键词:FCBGA,失效机理,失效分析Failure Analysis and Precaution of FCBGA Packaged Devices Lin Xiao-ling1,2,Kong Xue-dong1,En Yun-fei1,Zhang Xiao-wen1,Yao Ruo-he2China Electronic Product Reliability and Environmental Testing Research Institu te,Guangzhou,510610South China University of Technology Physics science and technology Guangzhou, 510640Abstract:Nowadays, FCBGA (Flip-chip ball grid array )is the optimal choice for IC’s package. Focus should be put on its reliability. This paper introduced the st ructure characteristic of FCBGA packaged devices and some correlative reliability p roblems of them. By two failure analysis cases of FCBGA devices, the author found t he failure mechanisms of the two failed devices. They are short of the solder balls and open of the solder bumps on the FC die, respectively. The cause for short is t he solder melted and made the nearby solder balls linked. The cause for open is the epoxy underfill between the solder bumps expanded and made the solder bumps ruptur ed , In the end, some precautions for reducing such failures are presented.Key Words: FCBGA, failure mechanism, failure analysis1 引言随着硅单芯片集成度不断提高,对集成电路封装要求更加严格,I/O引脚数急剧增加,功耗也随之增大。
BGA失效分析报告
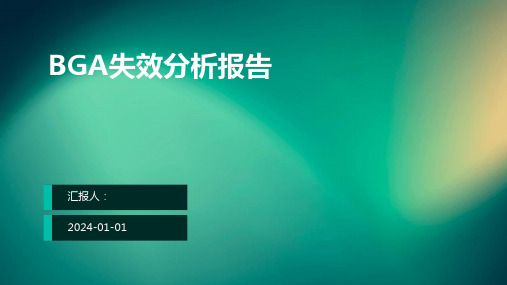
随着电子设备向高集成度、高可靠性 方向发展,BGA封装广泛应用于各类 电子产品中。然而,BGA失效问题逐 渐凸显,对产品性能和可靠性产生严 重影响。
BGA封装介绍
01
BGA封装特点
高密度、低电感、低热阻、易于 实现高速信号传输等。
02
BGA封装工艺流程
03
BGA失效类型
芯片粘接、引脚焊接、塑封固化 等。
01
03
一款笔记本电脑在使用过程中频繁出现蓝屏和死机现 象,拆解后发现芯片与BGA基板间的粘接材料老化,
芯片脱落导致电路故障。
04
一款平板电脑在使用过程中突然发生屏幕破裂,经检 查发现BGA封装体存在制造缺陷,无法承受机械冲击 。
失效影响分析
性能下降
BGA失效会导致电路性能下降,引发 各种故障现象,如死机、重启、数据 丢失等。
可靠性。
04 BGA失效预防和改进措施
优化封装设计
优化封装设计是预防BGA失效的重要 措施之一。
通过改进BGA的封装设计,可以减少 潜在的缺陷和问题,提高其可靠性和 稳定性。这包括优化焊球间距、改进 焊球材料和减小焊球直径等措施。
提升制造工艺水平
提升制造工艺水平是降低BGA失效风险的关键。
通过采用先进的制造技术和设备,提高BGA的制造精度和一致性,可以显著降低制造过程中可能出现的缺陷和问题。这包括 采用高精度的焊接设备、优化焊接工艺参数和加强过程控制等措施。
BGA失效进行分析和预测,为预防性维护提供支持。
THANKS FOR WATCHING
感谢您的观看
安全风险
对于关键性电子设备,BGA失效可能 引发严重安全问题,如设备损坏、数 据泄露或人身伤害等。
生产成本
LED封装典型失效案例分析

5. 将之前灯条上存在严重色差的两颗LED,清除外封胶后实测色温/色坐标值如下: ① TC:6591K,x/y:0.3131/0.3159; ② TC:6690K,x/y:0.3119/0.3135.对比数据可判定 灯条上LED均为同一色区材料。
外力
反弹力
当过大的外力通过封装胶体 间接作用于连接晶片与支架 的金丝线弧,将导致线弧从 B点(或D点)被拉断.
对已经出现开路的LED封装胶体施加外力时,由于金丝线弧断点临时接触,故瞬间 可点亮发光;消除外力,LED灯将再次熄灭.
除较尖锐的物体刺入胶体内,将产生痕迹外;对于大 部分情况下的外力压迫,弹性硅胶体可恢复原状,故胶 体表面一般不会遗留下明显的受力痕迹.
案例2: LED用于4灯并联线路,为小电流驱动点亮使用,存在严重的亮度明暗差异.
10mA点亮时,亮度明暗差异十分明显。理论上,单灯平均分流约为2.5mA
60mA点亮时,亮度较为接近。理论上,单灯平均分流约为15mA
案例3:用户端将VF:0.2V分档的3528白灯用于并联线路(14灯并联/组,共7组),由于单 灯分流不一致,导致灯具发出的光存在严重明暗差异.
常用的FR4线路板
左图中灯具LED密度较高,且采用的线路板导热能力较弱, 故主要依靠铜箔层传热,在加灯罩后,热量将累积上升.
·11·
铝基线路板
Copyright
案例13:3528白光LED用于户外发光字,使用一段时间后出现严重色差。
未使用前的LED
发光字安装使用后的LED
硅胶与PPA胶壳产生剥离
取 色差不良品剥掉封装胶,可观察到LED支架与硅胶界面附着有大量脏污 案例解析: 由于该户外发光字防水/防尘等级达不到使用环境的要求,而LED硅胶具有吸湿特 性,其分子间隙较环氧要大,故气密性相对较低。当LED长期在高温高湿环境点亮可能造成支架 PPA与硅胶体密封性下降,在产生剥离界面后,环境周围的水汽、粉尘等异物沿界面进入灯体 内,经长期积累造成胶体发黑,最终导致LED颜色发生改变。 预防措施:TOP LED白光产品用于户外时,LED硅胶胶体不能直接暴露在环境中,需采取符 合特定环境的防水密封措施,确保IP等级满足使用环境的各项要求。
芯片封装中的失效机理与故障分析研究
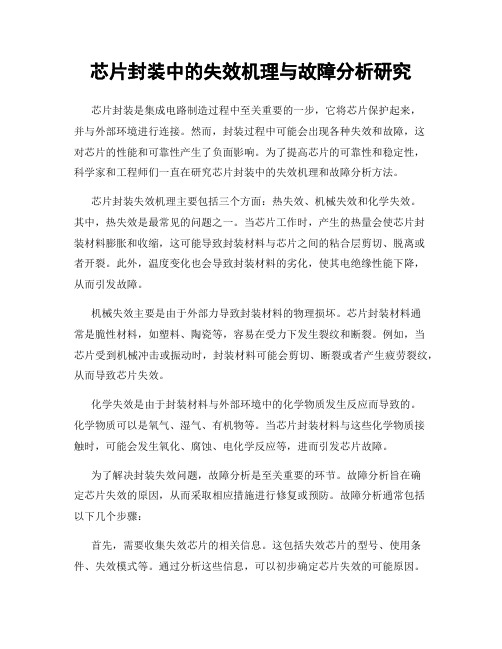
芯片封装中的失效机理与故障分析研究芯片封装是集成电路制造过程中至关重要的一步,它将芯片保护起来,并与外部环境进行连接。
然而,封装过程中可能会出现各种失效和故障,这对芯片的性能和可靠性产生了负面影响。
为了提高芯片的可靠性和稳定性,科学家和工程师们一直在研究芯片封装中的失效机理和故障分析方法。
芯片封装失效机理主要包括三个方面:热失效、机械失效和化学失效。
其中,热失效是最常见的问题之一。
当芯片工作时,产生的热量会使芯片封装材料膨胀和收缩,这可能导致封装材料与芯片之间的粘合层剪切、脱离或者开裂。
此外,温度变化也会导致封装材料的劣化,使其电绝缘性能下降,从而引发故障。
机械失效主要是由于外部力导致封装材料的物理损坏。
芯片封装材料通常是脆性材料,如塑料、陶瓷等,容易在受力下发生裂纹和断裂。
例如,当芯片受到机械冲击或振动时,封装材料可能会剪切、断裂或者产生疲劳裂纹,从而导致芯片失效。
化学失效是由于封装材料与外部环境中的化学物质发生反应而导致的。
化学物质可以是氧气、湿气、有机物等。
当芯片封装材料与这些化学物质接触时,可能会发生氧化、腐蚀、电化学反应等,进而引发芯片故障。
为了解决封装失效问题,故障分析是至关重要的环节。
故障分析旨在确定芯片失效的原因,从而采取相应措施进行修复或预防。
故障分析通常包括以下几个步骤:首先,需要收集失效芯片的相关信息。
这包括失效芯片的型号、使用条件、失效模式等。
通过分析这些信息,可以初步确定芯片失效的可能原因。
其次,进行物理分析。
物理分析是指通过观察芯片失效的外观、形态和结构,来确定失效的机理。
例如,通过显微镜观察失效芯片的微观形貌,可以确定是否存在裂纹、剥离等现象。
此外,还可以使用X射线、电子束等技术进行进一步的材料分析,以确定材料的性质和存在的异常问题。
接下来,进行电学分析。
电学分析是指通过测量失效芯片的电性能参数,来判断芯片的电路结构是否正常。
例如,使用万用表、示波器等设备对芯片进行电流、电压、功率等参数的测量,以了解失效芯片的电路状态。
死灯-LED半导体封装失效典型案例原因分析及预防措施
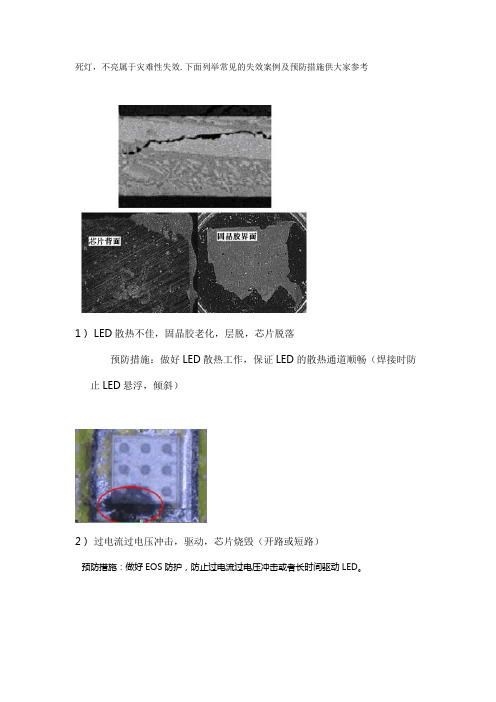
死灯,不亮属于灾难性失效.下面列举常见的失效案例及预防措施供大家参考
1)LED散热不佳,固晶胶老化,层脱,芯片脱落
预防措施:做好LED散热工作,保证LED的散热通道顺畅(焊接时防止LED 悬浮,倾斜)
2)过电流过电压冲击,驱动,芯片烧毁(开路或短路)
预防措施:做好EOS防护,防止过电流过电压冲击或者长时间驱动LED。
3)过电流冲击,金线烧断4)使用过程中,未做好ESD防静电防护,导致LED PN结被击穿。
预防措施:防止过电流过电压冲击LED。
4)使用过程未做好防静电防护,导致LED PN结被击穿。
预防措施:做好ESD防护工作
5)焊接温度过高,胶体膨胀剧烈扯断金线或者外力冲击碰撞封装胶体,扯断金
线。
预防措施:按照推荐的焊接条件焊接使用,装配过程中注意保护封装结构部分不受损坏。
6)LED受潮未除湿,回流焊过程中胶裂,金线断。
预防措施:按照条件除湿,可利用防潮箱或者烘箱进行干燥除湿。
应按照推荐的回流参
数过回流焊。
7)回流焊温度曲线设置不合理,造成回流过程胶体剧烈膨胀导致金线断。
预防措施:按照推荐的回流参数过回流焊。
8)齐纳被击穿,装配时LED正负极被短接或者PCB板短路,LED被击穿。
预防措施:做好ESD防静电保护工作,避免正负极短路,PCB要做仔细排查。
芯片封装基本流程及失效分析处理方法

芯片封装基本流程及失效分析处理方法一、芯片封装芯片封装的目的在于对芯片进行保护与支撑作用、形成良好的散热与隔绝层、保证芯片的可靠性,使其在应用过程中高效稳定地发挥功效。
二、工艺流程流程一:硅片减薄分为两种操作手段。
一是物理手段,如磨削、研磨等;二是化学手段,如电化学腐蚀、湿法腐蚀等,使芯片的厚度达到要求。
薄的芯片更有利于散热,减小芯片封装体积,提高机械性能等。
其次是对硅片进行切割,用多线切割机或其它手段如激光,将整个大圆片分割成单个芯片。
流程二:将晶粒黏着在导线架上,也叫作晶粒座,预设有延伸IC晶粒电路的延伸脚,用银胶对晶粒进行黏着固定,这一步骤为芯片贴装。
流程三:芯片互联,将芯片焊区与基板上的金属布线焊区相连接,使用球焊的方式,把金线压焊在适当位置。
芯片互联常见的方法有,打线键合,载在自动键合(TAB)和倒装芯片键合。
流程四:用树脂体将装在引线框上的芯片封起来,对芯片起保护作用和支撑作用。
包封固化后,在引线条上所有部位镀上一层锡,保证产品管脚的易焊性,增加外引脚的导电性及抗氧化性。
流程五:在树脂上印制标记,包含产品的型号、生产厂家等信息。
将导线架上已封装完成的晶粒,剪切分离并将不需要的连接用材料切除,提高芯片的美观度,便于使用及存储。
流程六:通过测试筛选出符合功能要求的产品,保证芯片的质量可靠性;最后包装入库,将产品按要求包装好后进入成品库,编带投入市场。
三、芯片失效芯片失效分析是判断芯片失效性质、分析芯片失效原因、研究芯片失效的预防措施的技术工作。
对芯片进行失效分析的意义在于提高芯片品质,改善生产方案,保障产品品质。
四、测试方法1、外部目检对芯片进行外观检测,判断芯片外观是否有发现裂纹、破损等异常现象。
2、X-RAY对芯片进行X-Ray检测,通过无损的手段,利用X射线透视芯片内部,检测其封装情况,判断IC封装内部是否出现各种缺陷,如分层剥离、爆裂以及键合线错位断裂等。
3、声学扫描芯片声学扫描是利用超声波反射与传输的特性,判断器件内部材料的晶格结构,有无杂质颗粒以及发现器件中空洞、裂纹、晶元或填胶中的裂缝、IC封装材料内部的气孔、分层剥离等异常情况。
半导体质量问题原因分析及整改措施报告

半导体质量问题原因分析及整改措施报告
1、封装失效
当管壳出现裂纹时就会发生封装失效。
机械应力、热应力或封装材料与金属之间的热膨胀系数失配可使裂纹形成。
当湿度较高或器件接触到焊剂、清洁剂等物质时,这些裂纹就成为潮气入侵管壳的通路。
化学反应可使器件劣化,从而导致器件失效。
2、引线键合失效
因大电流通过造成的热过应力、因键合不当造成的键合引线上的机械应力、键合引线与芯片之间的界面上的裂纹、硅的电迁移以及过大的键合压力都会造成引线键合失效。
芯片粘结失效
芯片与衬底之间接触不当可降低它们之间的导热性。
因此,芯片会出现过热,从而导致应力加大和开裂,最终使器件失效。
3、体硅缺陷
有时候,晶体缺陷引起的故障或硅体材料中的杂质和玷污物的存在也会使器件失效。
器件生产期间由扩散问题引起的工艺缺陷也会使器件失效。
4、氧化层缺陷
静电放电和通过引线扩展的高压瞬变可使薄氧化层即绝缘体击穿,并导致器件失灵。
氧化层的裂纹和或划痕以及氧化物中杂质的存在也能使器件失效。
5、铝-金属缺陷
这些缺陷是由下列原因造成的:
由于高电场引起的按电流方向发生的铝的电迁移。
由于大电流产生的电过应力造成的铝导体损毁。
铝腐蚀。
焊接引起的金属磨损。
接触窗口上的异常金属沉积。
小丘和裂纹的形成。
6、改进措施
器件通常要经历1个特定事件或经受1组条件才能失效。
通过了解这些原因,技术人员就可进行深入的失效分析,以生产出更可靠的产品。
然而,必须记住,器件、PCB或最终产品的设计缺陷会产生导致器件失效的条件。
封装可靠性失效原因及其改善方案阐述
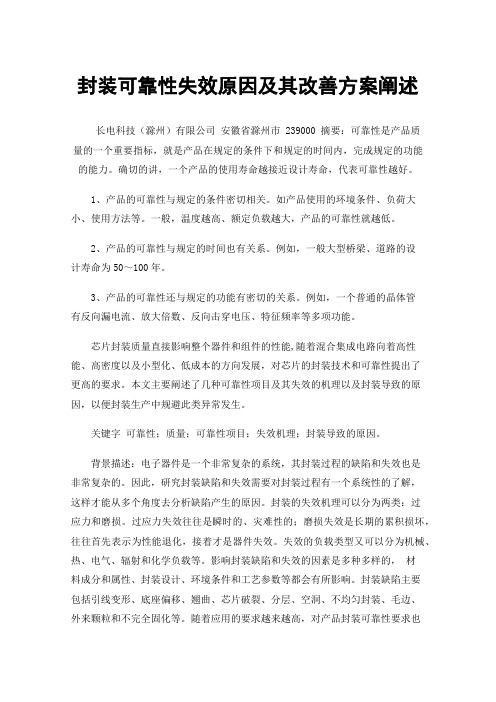
封装可靠性失效原因及其改善方案阐述长电科技(滁州)有限公司安徽省滁州市 239000 摘要:可靠性是产品质量的一个重要指标,就是产品在规定的条件下和规定的时间内,完成规定的功能的能力。
确切的讲,一个产品的使用寿命越接近设计寿命,代表可靠性越好。
1、产品的可靠性与规定的条件密切相关。
如产品使用的环境条件、负荷大小、使用方法等。
一般,温度越高、额定负载越大,产品的可靠性就越低。
2、产品的可靠性与规定的时间也有关系。
例如,一般大型桥梁、道路的设计寿命为50~100年。
3、产品的可靠性还与规定的功能有密切的关系。
例如,一个普通的晶体管有反向漏电流、放大倍数、反向击穿电压、特征频率等多项功能。
芯片封装质量直接影响整个器件和组件的性能,随着混合集成电路向着高性能、高密度以及小型化、低成本的方向发展,对芯片的封装技术和可靠性提出了更高的要求。
本文主要阐述了几种可靠性项目及其失效的机理以及封装导致的原因,以便封装生产中规避此类异常发生。
关键字可靠性;质量;可靠性项目;失效机理;封装导致的原因。
背景描述:电子器件是一个非常复杂的系统,其封装过程的缺陷和失效也是非常复杂的。
因此,研究封装缺陷和失效需要对封装过程有一个系统性的了解,这样才能从多个角度去分析缺陷产生的原因。
封装的失效机理可以分为两类:过应力和磨损。
过应力失效往往是瞬时的、灾难性的;磨损失效是长期的累积损坏,往往首先表示为性能退化,接着才是器件失效。
失效的负载类型又可以分为机械、热、电气、辐射和化学负载等。
影响封装缺陷和失效的因素是多种多样的,材料成分和属性、封装设计、环境条件和工艺参数等都会有所影响。
封装缺陷主要包括引线变形、底座偏移、翘曲、芯片破裂、分层、空洞、不均匀封装、毛边、外来颗粒和不完全固化等。
随着应用的要求越来越高,对产品封装可靠性要求也越来越高。
我们要识别一些可靠性项目考核目的、失效机理以及可能导致的原因,以便在前期FMEA中定义,从设计、生产角度来提升质量。
塑封器件常见失效模式及其机理分析总结

塑封器件常见失效模式及其机理分析总结塑封器件(Plastic Encapsulation Device,PED)是指使用塑料作为封装材料的电子器件。
由于其低成本、轻量化、易加工等优势,塑封器件被广泛应用于各种电子设备中。
然而,塑封器件也存在一些常见的失效模式,本文将对这些失效模式及其机理进行分析总结。
1.温度失效:在高温环境下,塑封器件的封装材料容易发生老化和变形,导致器件性能下降或失效。
该失效模式的机理主要是材料的热老化,其中塑料封装材料中的添加剂如稳定剂、防护剂等会因长时间高温作用而分解或迁移,导致封装材料的物理和化学性质的变化。
2.湿气失效:湿气失效是指器件在高湿环境中发生导电路径或绝缘破坏而失效。
该失效模式的机理主要是由于湿气中的氧化物、离子等与器件内部的金属导线、介质等发生化学反应,导致电阻降低、绝缘性能下降。
3.机械失效:机械失效是指塑封器件在受到机械应力、振动等外力作用下,发生封装裂纹、金属引脚断裂等损坏而失效。
该失效模式的机理主要是由于材料的强度不足、结构设计不合理等导致的。
4.电气失效:电气失效是指器件在使用过程中发生电性能下降或功能失效。
该失效模式的机理主要包括电极与封装材料之间的接触不良、氧化等导致电阻增加;电容器内部介质的老化和损坏导致容量减小或绝缘性能下降等。
5.化学失效:化学失效是指塑封器件在受到化学物质(酸、碱、溶剂等)侵蚀或与化学物质发生反应而失效。
该失效模式的机理主要是材料与化学物质发生化学反应,导致封装材料的物理性质变化或金属导线的腐蚀等。
针对上述失效模式,可以采取以下措施来减少或避免塑封器件的失效:1.选择合适的封装材料,考虑其在高温、高湿等环境下的稳定性和耐候性。
2.优化封装结构设计,增强塑封器件的抗机械振动和应力能力,避免封装裂纹和金属引脚断裂等机械失效。
3.采取防湿措施,如封装材料添加防湿剂、采用防潮包装等,以防止湿气失效的发生。
4.优化金属电极的表面处理和封装材料的加工工艺,提高接触质量和电阻、容量的稳定性,减少电气失效的可能。
塑封料\环氧塑封料工艺选择和封装失效分析流程
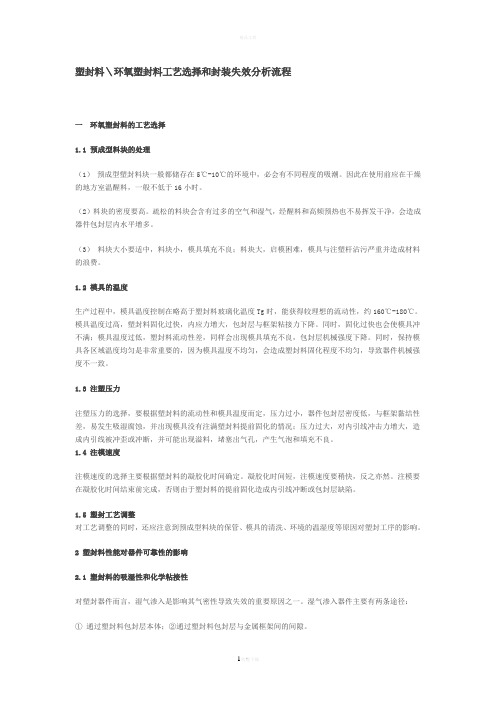
塑封料\环氧塑封料工艺选择和封装失效分析流程一环氧塑封料的工艺选择1.1 预成型料块的处理(1)预成型塑封料块一般都储存在5℃-10℃的环境中,必会有不同程度的吸潮。
因此在使用前应在干燥的地方室温醒料,一般不低于16小时。
(2)料块的密度要高。
疏松的料块会含有过多的空气和湿气,经醒料和高频预热也不易挥发干净,会造成器件包封层内水平增多。
(3)料块大小要适中,料块小,模具填充不良;料块大,启模困难,模具与注塑杆沾污严重并造成材料的浪费。
1.2 模具的温度生产过程中,模具温度控制在略高于塑封料玻璃化温度Tg时,能获得较理想的流动性,约160℃-180℃。
模具温度过高,塑封料固化过快,内应力增大,包封层与框架粘接力下降。
同时,固化过快也会使模具冲不满;模具温度过低,塑封料流动性差,同样会出现模具填充不良,包封层机械强度下降。
同时,保持模具各区域温度均匀是非常重要的,因为模具温度不均匀,会造成塑封料固化程度不均匀,导致器件机械强度不一致。
1.3 注塑压力注塑压力的选择,要根据塑封料的流动性和模具温度而定,压力过小,器件包封层密度低,与框架黏结性差,易发生吸湿腐蚀,并出现模具没有注满塑封料提前固化的情况;压力过大,对内引线冲击力增大,造成内引线被冲歪或冲断,并可能出现溢料,堵塞出气孔,产生气泡和填充不良。
1.4 注模速度注模速度的选择主要根据塑封料的凝胶化时间确定。
凝胶化时间短,注模速度要稍快,反之亦然。
注模要在凝胶化时间结束前完成,否则由于塑封料的提前固化造成内引线冲断或包封层缺陷。
1.5 塑封工艺调整对工艺调整的同时,还应注意到预成型料块的保管、模具的清洗、环境的温湿度等原因对塑封工序的影响。
2 塑封料性能对器件可靠性的影响2.1 塑封料的吸湿性和化学粘接性对塑封器件而言,湿气渗入是影响其气密性导致失效的重要原因之一。
湿气渗入器件主要有两条途径:①通过塑封料包封层本体;②通过塑封料包封层与金属框架间的间隙。
封装材料的湿气失效分析

(3)实验 A)热机械分析仪(Thermal mechanical analyzer, TMA):测量吸湿过程中的尺寸变 化; B)热重分析仪(Thermal gravitational analyzer, TGA):测量吸湿过程中的重量变化。
1.1.3 蒸汽压力分析
塑封器件吸湿后所产生的内部蒸汽压力, 被认为是引起“爆米花”开裂现象最接的 因素,也是最主要的破坏机制
2.引言
一、环氧树脂的不足之处: 当在焊接回流期间开发的总湿热应力超过界 面的附着强度时发生脱层,从而导致封装材料 的保护能力降低。
2.引言
二、用无机二氧化硅填料(石英、熔融二氧化 硅、方石英和球形二氧化硅)及一种有机填料 (即球状硅粉末)分别并入环氧树脂的封装材 料的原因: 提高了金属框架和封装材料之间的界面相互 作用,而已广泛引入无机填料,大多二氧化硅, 用以降低封装材料的热膨胀系数。
1.1 湿气分析理论
1.1.1湿气扩散理论 1.1.2 湿气膨胀应力分析 1.1.3 蒸汽压力分析
1.1.1 湿气扩散理论
常用塑封材料:一般为环氧树脂类热固性塑料 聚合物特点:多孔性、亲水性。
湿气:指进入到封装材料中的水蒸气或液态形式的水分子
湿气存在形式:(1)单一气态;(2)气液混合态;(3)结合水
2.实验
2.2 水(l)吸附和湿气(g)吸附的重力测量 材料的水吸附测量是在 85 ℃ ,通过将干燥 的矩形样品浸入到去离子水的水浴中。湿气吸 附试验是在一个保持在85℃和85%RH的环境室 进 行 的 。 所 有 的 样 品 都 是 按 20mm×20mm×0.9mm尺寸制备的,并且相同 组成的五个试样进行了分别研究以获得吸附量 的平均值。在吸附实验之前,将所有样品都彻 底洗涤,然后在真空炉中干燥至达到恒干重。
封装失效分析1

第二单元 集成电路芯片封装可靠性知识—郭小伟(60学时)第一章、可靠性试验1.可靠性试验常用术语试验名称 英文简称 常用试验条件备注温度循环 TCT (T/C ) -65℃~150℃, dwell15min, 100cycles 试验设备采用气冷的方式,此温度设置为设备的极限温度 高压蒸煮 PCT 121℃,100RH., 2ATM,96hrs 此试验也称为高压蒸汽,英文也称为autoclave热冲击 TST (T/S )-65℃~150℃, dwell15min, 50cycles 此试验原理与温度循环相同,但温度转换速率更快,所以比温度循环更严酷。
稳态湿热 THT85℃,85%RH.,168hrs 此试验有时是需要加偏置电压的,一般为Vcb=0.7~0.8BVcbo,此时试验为THBT 。
易焊性 solderability 235℃,2±0.5s此试验为槽焊法,试验后为10~40倍的显微镜下看管脚的上锡面积。
耐焊接热 SHT260℃,10±1s 模拟焊接过程对产品的影响。
电耐久 Burn inVce=0.7Bvceo,Ic=P/Vce,168hrs模拟产品的使用。
(条件主要针对三极管)高温反偏 HTRB 125℃,Vcb=0.7~0.8BVcbo,168hrs主要对产品的PN 结进行考核。
回流焊 IR reflowPeak temp.240℃(225℃)只针对SMD 产品进行考核,且最多只能做三次。
高温贮存 HTSL 150℃,168hrs产品的高温寿命考核。
超声波检测 SAT CSCAN,BSCAN,TSCAN检测产品的内部离层、气泡、裂缝。
但产品表面一定要平整。
2.可靠性试验条件和判断试验流程:F/T SAT1-4 1-5 F/T 1-6 1-72:T/S 3: T/C 4:PCT 5: THT 6:HSTL以客户为代表为例子:客户1:precondition TCT –55/125℃,5cycles for L1,l2,L3 Ac:Re=(0,1)T/S: –55/125℃,5min,100cycles sample size: 45 Ac:Re=(0,1)T/C: –55/125℃,10min,200cycles sample size: 45 Ac:Re=(0,1)PCT: 121℃/100%rh,15Psig,96hr sample size: 45 Ac:Re=(0,1)THT: 85℃/85%,168/500/1000hrs sample size: 45 Ac:Re=(0,1)客户2:precondition T/C –40/60℃,5cycles forL3 Ac:Re=(0,1)T/S: –55/125℃,5min,100cycles sample size: 45 Ac:Re=(0,1)T/C: –65/150℃,10min,500cycles sample size: 77Ac:Re=(0,1)PCT: 121℃/100%rh,15Psig,168hr sample size: 77 Ac:Re=(0,1)THT: 85℃/85%,1000hrs sample size: 77 Ac:Re=(0,1)HTSL: 150℃,1000hrs sample size:77 Ac:Re=(0,1)HAST: 130℃/85%rh,168hr sample size: 77 Ac:Re=(0,1)客户3:precondition T/C –40/60℃,5cycles forL3 Ac:Re=(0,1)T/S: –55/125℃,5min,50cycles sample size: 24 Ac:Re=(0,1)T/C: –65/150℃,15min,50cycles sample size: 24 Ac:Re=(0,1)PCT: 121℃/100%rh,15Psig,168hr sample size: 24 Ac:Re=(0,1)HTSL: 150℃,168hrs sample size:24 Ac:Re=(0,1)客户4:precondition T/C N/A ,L1 Ac:Re=(0,1)T/C: –65/150℃,15min,100/500cycles sample size: 45 Ac:Re=(0,1)PCT: 121℃/100%rh,15Psig,168/336hr sample size: 45 Ac:Re=(0,1)SOLDER DUNK: 245℃10SEC sample size: 45 Ac:Re=(0,1)客户5:QFP 做 precondition,DIP不做preconditionprecondition T/C N/A,L3 sample size:184 Ac:Re=(5,6)T/C: –65/150℃,15min,200/500cycles sample size: 45 Ac:Re=(0,1)PCT: 121℃/100%rh,15Psig,168hr sample size: 45 Ac:Re=(0,1)HTSL: 150℃,168/500/1000hrs sample size:45 Ac:Re=(0,1)SOLDER DUNK: 245℃5SEC sample size: 15 Ac:Re=(0,1)塑料密封等级塑料密封等级:在装配现场拆包后地面存放期标准试验条件LEVEL 1 在小于30C/85%相对湿度无期限 85C/85% 168小时LEVEL 2 在30C/60%条件下1年85C/60% 168小时LEVEL 3 在小于30C/60%条件下1周 30C/60% 192小时加速=60C/60% 40小时SAMPLE:50塑料密封等级试验步骤:1. DC和功能测试2.外观检查(在80倍以上显微镜下检查)3. SAT扫描4. BAKE 125C/24小时5.做LEVEL 相应条件的试验6.在15分钟后和4小时内做3次回流焊—注意温度曲线必须提供和符合JEDEC标准。
塑封器件常见失效模式及其机理分析总结
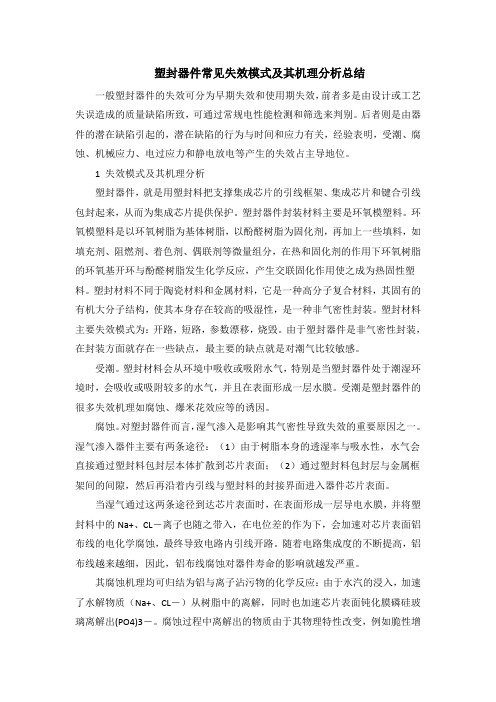
塑封器件常见失效模式及其机理分析总结一般塑封器件的失效可分为早期失效和使用期失效,前者多是由设计或工艺失误造成的质量缺陷所致,可通过常规电性能检测和筛选来判别。
后者则是由器件的潜在缺陷引起的,潜在缺陷的行为与时间和应力有关,经验表明,受潮、腐蚀、机械应力、电过应力和静电放电等产生的失效占主导地位。
1 失效模式及其机理分析塑封器件,就是用塑封料把支撑集成芯片的引线框架、集成芯片和键合引线包封起来,从而为集成芯片提供保护。
塑封器件封装材料主要是环氧模塑料。
环氧模塑料是以环氧树脂为基体树脂,以酚醛树脂为固化剂,再加上一些填料,如填充剂、阻燃剂、着色剂、偶联剂等微量组分,在热和固化剂的作用下环氧树脂的环氧基开环与酚醛树脂发生化学反应,产生交联固化作用使之成为热固性塑料。
塑封材料不同于陶瓷材料和金属材料,它是一种高分子复合材料,其固有的有机大分子结构,使其本身存在较高的吸湿性,是一种非气密性封装。
塑封材料主要失效模式为:开路,短路,参数漂移,烧毁。
由于塑封器件是非气密性封装,在封装方面就存在一些缺点,最主要的缺点就是对潮气比较敏感。
受潮。
塑封材料会从环境中吸收或吸附水气,特别是当塑封器件处于潮湿环境时,会吸收或吸附较多的水气,并且在表面形成一层水膜。
受潮是塑封器件的很多失效机理如腐蚀、爆米花效应等的诱因。
腐蚀。
对塑封器件而言,湿气渗入是影响其气密性导致失效的重要原因之一。
湿气渗入器件主要有两条途径:(1)由于树脂本身的透湿率与吸水性,水气会直接通过塑封料包封层本体扩散到芯片表面;(2)通过塑封料包封层与金属框架间的间隙,然后再沿着内引线与塑封料的封接界面进入器件芯片表面。
当湿气通过这两条途径到达芯片表面时,在表面形成一层导电水膜,并将塑封料中的Na+、CL-离子也随之带入,在电位差的作为下,会加速对芯片表面铝布线的电化学腐蚀,最终导致电路内引线开路。
随着电路集成度的不断提高,铝布线越来越细,因此,铝布线腐蚀对器件寿命的影响就越发严重。
- 1、下载文档前请自行甄别文档内容的完整性,平台不提供额外的编辑、内容补充、找答案等附加服务。
- 2、"仅部分预览"的文档,不可在线预览部分如存在完整性等问题,可反馈申请退款(可完整预览的文档不适用该条件!)。
- 3、如文档侵犯您的权益,请联系客服反馈,我们会尽快为您处理(人工客服工作时间:9:00-18:30)。
第二单元 集成电路芯片封装可靠性知识—郭小伟(60学时)第一章、可靠性试验1.可靠性试验常用术语试验名称 英文简称 常用试验条件备注温度循环 TCT (T/C ) -65℃~150℃, dwell15min, 100cycles 试验设备采用气冷的方式,此温度设置为设备的极限温度 高压蒸煮 PCT 121℃,100RH., 2ATM,96hrs 此试验也称为高压蒸汽,英文也称为autoclave热冲击 TST (T/S )-65℃~150℃, dwell15min, 50cycles 此试验原理与温度循环相同,但温度转换速率更快,所以比温度循环更严酷。
稳态湿热 THT85℃,85%RH.,168hrs 此试验有时是需要加偏置电压的,一般为Vcb=0.7~0.8BVcbo,此时试验为THBT 。
易焊性 solderability 235℃,2±0.5s此试验为槽焊法,试验后为10~40倍的显微镜下看管脚的上锡面积。
耐焊接热 SHT260℃,10±1s 模拟焊接过程对产品的影响。
电耐久 Burn inVce=0.7Bvceo,Ic=P/Vce,168hrs模拟产品的使用。
(条件主要针对三极管)高温反偏 HTRB 125℃,Vcb=0.7~0.8BVcbo,168hrs主要对产品的PN 结进行考核。
回流焊 IR reflowPeak temp.240℃(225℃)只针对SMD 产品进行考核,且最多只能做三次。
高温贮存 HTSL 150℃,168hrs产品的高温寿命考核。
超声波检测 SAT CSCAN,BSCAN,TSCAN检测产品的内部离层、气泡、裂缝。
但产品表面一定要平整。
2.可靠性试验条件和判断试验流程:F/T SAT1-4 1-5 F/T 1-6 1-72:T/S 3: T/C 4:PCT 5: THT 6:HSTL以客户为代表为例子:客户1:precondition TCT –55/125℃,5cycles for L1,l2,L3 Ac:Re=(0,1)T/S: –55/125℃,5min,100cycles sample size: 45 Ac:Re=(0,1)T/C: –55/125℃,10min,200cycles sample size: 45 Ac:Re=(0,1)PCT: 121℃/100%rh,15Psig,96hr sample size: 45 Ac:Re=(0,1)THT: 85℃/85%,168/500/1000hrs sample size: 45 Ac:Re=(0,1)客户2:precondition T/C –40/60℃,5cycles forL3 Ac:Re=(0,1)T/S: –55/125℃,5min,100cycles sample size: 45 Ac:Re=(0,1)T/C: –65/150℃,10min,500cycles sample size: 77Ac:Re=(0,1)PCT: 121℃/100%rh,15Psig,168hr sample size: 77 Ac:Re=(0,1)THT: 85℃/85%,1000hrs sample size: 77 Ac:Re=(0,1)HTSL: 150℃,1000hrs sample size:77 Ac:Re=(0,1)HAST: 130℃/85%rh,168hr sample size: 77 Ac:Re=(0,1)客户3:precondition T/C –40/60℃,5cycles forL3 Ac:Re=(0,1)T/S: –55/125℃,5min,50cycles sample size: 24 Ac:Re=(0,1)T/C: –65/150℃,15min,50cycles sample size: 24 Ac:Re=(0,1)PCT: 121℃/100%rh,15Psig,168hr sample size: 24 Ac:Re=(0,1)HTSL: 150℃,168hrs sample size:24 Ac:Re=(0,1)客户4:precondition T/C N/A ,L1 Ac:Re=(0,1)T/C: –65/150℃,15min,100/500cycles sample size: 45 Ac:Re=(0,1)PCT: 121℃/100%rh,15Psig,168/336hr sample size: 45 Ac:Re=(0,1)SOLDER DUNK: 245℃10SEC sample size: 45 Ac:Re=(0,1)客户5:QFP 做 precondition,DIP不做preconditionprecondition T/C N/A,L3 sample size:184 Ac:Re=(5,6)T/C: –65/150℃,15min,200/500cycles sample size: 45 Ac:Re=(0,1)PCT: 121℃/100%rh,15Psig,168hr sample size: 45 Ac:Re=(0,1)HTSL: 150℃,168/500/1000hrs sample size:45 Ac:Re=(0,1)SOLDER DUNK: 245℃5SEC sample size: 15 Ac:Re=(0,1)塑料密封等级塑料密封等级:在装配现场拆包后地面存放期标准试验条件LEVEL 1 在小于30C/85%相对湿度无期限 85C/85% 168小时LEVEL 2 在30C/60%条件下1年85C/60% 168小时LEVEL 3 在小于30C/60%条件下1周 30C/60% 192小时加速=60C/60% 40小时SAMPLE:50塑料密封等级试验步骤:1. DC和功能测试2.外观检查(在80倍以上显微镜下检查)3. SAT扫描4. BAKE 125C/24小时5.做LEVEL 相应条件的试验6.在15分钟后和4小时内做3次回流焊—注意温度曲线必须提供和符合JEDEC标准。
7.外观检查(在80倍以上显微镜下检查)--不可以有裂缝。
8. DC和功能测试—注意如果无法通过测试要验证是否和塑料密封有关部门9. ------可以做BAKE 150C/24小时,冷却2小时后做未通过产品的功能测试来验证10. SAT扫描----判断依据:A 芯片表面不可有离层B镀银脚精压区域不可有离层C产品内部不可有进水后离层图像(图形上表现该有图像却隐隐约约或同被划伤的痕迹)D引脚与引脚之间在胶体内部分,离层相连的面积不可超过胶体正面面积的10%或引脚通过离层相连的脚数不可超过引脚总数的1/5E芯片四周导电胶造成的离层不可超过胶体正面面积的10%集成电路封装在设计过程中可靠性的考虑封装所用主要材料:• 磨划片所用薄膜:型号、纯度、厚度、粘度• 引线框架:材质、厚度、防拖性、电性能、传热性、热膨胀系数、镀层材料、镀层厚度、镀层质量• 芯片粘接剂:型号、电性能、传热性、抗疲劳、热膨胀系数、装片牢度• 焊线:型号、HAZ、电性能、传热性、拉力、弧度• 塑封料:型号、热硬度、传热性、电性能、玻璃化温度、线膨胀系数、离子纯度、填料比例、吸水率、抗弯强度、粘结力、阻燃性、对应封装别水汽敏感等级• 电镀成份:SN/Pb的比例集成电路封装在设计过程中可靠性的考虑封装工艺控制要关注的方面:• 磨片进刀速度、转速、磨片厚度、去离子水电导率• 划片进刀速度、转速、切割深度、防静电措施• 装片压力、顶针、吸嘴、银浆头的选用• 球焊第一点参数、焊针的选用、温度、弧度• 塑封模具的设计如顶杆位置、脱模角度、侧面粗糙度及塑封温度、压强、速度• 后固化温度、时间• 冲塑刀片与胶体的距离• 电镀去飞边工艺、电镀电流、前处理、后处理、镀液成份• 切筋成形时产品胶体受力情况的监控(显微镜和SAT)、共面性、防静电• 对薄形产品激光打印打印深度的控制• 对薄形但面积较大胶体产品真空包装封装工艺控制要关注的方面(球焊后合理的金线拉力下限):• 集成电路封装中球焊后金线拉力最低要求,应该考虑金线在塑封时的受力情况和运输及操作时的合理振动。
金线在塑封时的受力不仅与金线的长度、直径有关,还与塑封料的粘度、塑封时的注射速度有关,并与塑封产品的几何尺寸、注胶口的形状和尺寸等诸多因素有关。
应该按照不同封装形式的产品给出球焊后金线拉力最低要求,并给出最佳的范围。
下面是我们对不同封装别(均指传统模要求)拉力的模拟计算结果(部分内容)在实际工艺标准控制中对25微米的金线拉力下限我们建议通常可以是5g集成电路封装在设计过程中可靠性的考虑封装工艺控制要关注的方面(超声SAT):超声图片观察和判断:• 芯片表面不可有离层• 镀银脚精压区域不可有离层• 产品内部不可有进水后离层图像(图形上表现该有图像却隐隐约约或同被划伤的痕迹)• 引脚与引脚之间在胶体内部分,离层相连的面积不可超过胶体正面面积的20%或引脚通过离层相连的脚数不可超过引脚总数的1/5• 芯片四周导电胶造成的离层在做可靠性试验通过或做Bscan时未超出芯片高度的2/3不判为不合格• 判断超声图片时要以波形为准,要注意对颜色黑白异常区域的波形检查。
下面的图片均为不正常:集成电路封装常用可靠性试验对应的缺点项目第二章、失效分析1.集成电路封装失效分析的常规流程1. 接受分析请求2. 在数据库中登记3. 收集相关的信息4. 对失效的产品确认5. 对漏电流超差的产品在125度~150度的温度下烘烤2小时,再测试是否通过对功能失效的产品在125度~150度的温度下烘烤24小时,再测试是否通过6. 在80倍显微镜下检查外观7. 开短路测试,检查对应PIN是否开短路或对应内阻异常8. X-RAY,检查打线情况9. C-SAM,检查分层情况和内部气泡10. Decapsulation (开帽)or Cross-section(做对应分层区域横切面)11. 检查芯片表面、球状质量、裂缝、扫描电子显微镜(SEM)检查焊点形貌、结构、沾污、腐球后检查是否有压区凹陷12. 更多的检查方法和试验方案13. 结论和图片记录在数据库中14. 出具报告15. 存入档案2.集成电路封装失效分析的常用方法1. 立体或金相显微镜下检查形貌、结构2. 开短路测试,检查对应PIN是否开短路或对应内阻异常3. X-RAY,检查打线情况、焊点错位、碰线、塌丝、球脱、点脱4. C-SAM,检查分层情况和内部气泡5. 扫描电子显微镜(SEM)检查焊点形貌、结构6. 红外热像仪检查温度分布集成电路封装失效分析的常用方法还有• 表面形貌:• 表面轮廓仪(Surface profiler) 器件、电路板变形等• 激光轮廓仪(Laser profiler) 焊膏印刷尺寸,引脚平整度等• 扫描超声显微镜(C-SAM)· 各种行貌观测• 力学性能:• 推力/拉力(shear/pull test) 焊线、贴片、焊接力学性能等• 材料试验机(Mircotester) 材料力学性能等• 粘度计(Viscosity measurement) 焊膏、贴片胶粘度测量等• 成份分析:• 化学分析(CA) 定量分析焊料主成份;助焊剂、稀释剂中卤素含量;封装、组装用金属合金材料的主成份等。