p031-板坯连铸带液芯压下铸坯变形特点
薄板坯连铸带液芯轻压下技术

第39卷 第2期2004年2月 钢 铁I RON AND ST EELV o l.39,N o.2Feb ruary2004薄板坯连铸带液芯轻压下技术袁集华(钢铁研究总院连铸技术国家工程研究中心,北京100081)摘 要 就薄板坯连铸带液芯轻压下过程的设备条件、控制系统、工艺要求、生产操作方式、铸坯的质量等做了简要的概述。
结构合理的扇形段和能力恰当的液压缸、先进的PL C控制系统是轻压下的技术关键;稳定及合适的连铸工艺亦是带液芯轻压下不可缺少的基本前提;扇形段采用平行缓慢方式挤压带液芯的铸坯是稳定生产的有效措施;薄板坯连铸带液芯轻压下对铸坯质量的影响比较小。
关键词 薄板坯连铸 带液芯轻压下中图法分类号 T F77717 文献标识码 ATH IN S LAB CAST ING W ITH L IQU I D CORE RED UCT I ONYU AN J ihua(N ati onal Engineering and R esearch Cen ter fo r Con tinuou s Casting T echno logy,Cen tral Iron and Steel R esearch In stitu te,Beijing100081)ABSTRACT T he equ i pm en t,con tro l system,techn ical requ irem en ts,op erati on m ode and p rod2 uct quality of th in slab casting w ith liqu id co re reducti on(L CR)are in troduced1T he segm en ts w ith reasonab le design,cylinders w ith su itab le cap acity,and advanced PL C system are the key p arts fo r L CR1T he stab le and su itab le casting techno logies are also the p reconditi on s fo r L CR1 In the segm en ts the liqu id co re th in slab shou ld be squeezed slow ly and p arallelly1L CR has a lit2 tle effect on th in slab quality1KEY WORD S th in slab casting,liqu id co re reducti on1 前言带液芯轻压下技术已成为薄板坯连铸连轧工艺流程中的一个重要组成部分,并已成熟地应用于实际生产过程中。
薄板坯连铸连轧的液芯压下技术

l I oI d eo i 】 0 r utn q耐 ee l
1 前
言
在 技 术经 济 上 的优 势 。而 从 连 铸 角 度 考 虑 , 产 生 薄 板坯 会 给结 晶器 和 浸入 式 水 口带 来 负 担 。如果 结 晶 器 内腔 厚 度 太 小 , 不 利 于 浸 入 式 水 口的插 会 入 , 且 结 晶器 内 的熔 池 也 太 小 , 加 了钢 水铸 流 而 增 对 凝 壳 的 冲刷 , 剧 了结 晶器 内 钢 液 面 的波 动 , 加 不 利 于保 护 渣 液 渣 层 的 形 成 和 稳 定 , 加 了浇 铸 的 增 难 度 , 以结 晶器 内腔 的厚 度不 应 太 小 。这 样 , 所 在 连 铸 和 连 轧之 间存 在 着对 铸 坯 厚 度 有 不 同要求 的
液 芯 压 下 技 术 最 早 应 用 于 常 规 厚板 坯 和大 方 坯连 铸 机 , 目的 是 为 了 改 善 铸 坯 中 心 疏 松 和 宏 其 观 偏 析 , 高 铸 坯 的 内部 质 量 。因 为 在 凝 固末 期 , 提 铸 坯 中 心 固化 时 产 生 收 缩 , 方 面 在 中 心 部 位 形 一
维普资讯
20 0 2年 1 2月
De e e 2 O c mb r O2
・
钢
铁
研
究
第 6期 ( 总第 19期 ) 2
N . (u 2 ) o6 Sm19
R s a c n Io & Se l e e r h o rn te
科研与实践 ・
中 心 疏 松 和宏 观 偏 析 … 。
在 薄 板坯 连 铸 中 , 于 铸 坯 较 薄 , 却 较 快 , 由 冷 其 中 心 出 现 偏 析 的 程 度 比 常 规 厚 板 坯 和 大 方 坯
连铸板坯缺陷特征和图谱(梁健)

ቤተ መጻሕፍቲ ባይዱ梁 健
炼钢厂技术科
2013-12-21
一、连铸坯质量特征综述
1、连铸坯质量定义和特征: 所谓连铸坯质量是指的到合格产品所允许的铸坯缺陷的严重程度。对 铸坯质量要求而言,主要有四项指标,即连铸坯几何形状、表面质量、 内部组织致密性和钢的洁净性;而这些质量要求与连铸机本身设计, 采取的工艺以及凝固特点密切相关。
接痕(粘结)
【定义与特征】接痕是在板坯表面呈现横向不连续性,有较宽的铸波,有着 明显的不能焊合的痕迹。 【鉴别与判定】用肉眼检查,这种缺陷非常明显,必须切尺或判废。
重皮
【定义与特征】一般在表面形成一层不规则的重皮,其面积大小不一,厚度 不等,覆盖在宽面或者窄面,一般出现的几率很小。 【鉴别与判定】用肉眼检查,这种缺陷非常明显,必须切尺或判废。
三角区裂纹
三角区定义:在板坯横截面上,以窄边为底,两底角为45℃的等角三角形范 围内。 【定义与特征】因该裂纹发生在宽面柱状晶与窄面柱状晶交汇的三角区部位 故称为三角区裂纹,外观与中心裂纹相似,一般发生在距窄边30-50 mm 厚 度的中心处,裂纹长10-60 mm。裂口宽0.1 一0.5mm,严重时两端贯穿。 【鉴别与判定】对轻微的三角区裂纹冷检时先用小锤轻除氧化铁皮,近距离 观察断面方可见到,轻微的三角区裂纹在轧制过程中一般可以焊合,不会 对热轧簿板造成影响。当裂纹有开口度时就是严重的三角区裂纹将引起钢 板开裂,须要精整切除直至裂纹消除,若无法消除则判为废坯。例如:3# 铸机生产的SS400。
气泡或气孔
【定义与特征】接近表面的皮下气孔,有时候与表面连通,形成表面细孔, 细小而密集的气孔,也叫针孔。一般发生在板坯窄面,头坯的头部,尾坯的 尾部也时有发生。 【鉴别与判定】气孔/针孔几乎是在所有铸坯上都常见的,也是最易被忽略的 板坯缺陷,只有采取了正确的火焰清理处理,才能发现板坯上的皮下气泡和 针状气孔。因为加热炉内铸坯皮下气泡表面被氧化,轧制过程不能焊合,产 品形成裂纹,所以发现在板坯表面或横截面发现气孔或气泡,必须处理,但 是如果窄面的气泡在单位范围内没有聚集,不是很深,一般情况下可以放过。
连铸板坯缺陷图谱及产生的原因分析

第二篇连铸板坯缺陷(AA)第二篇连铸板坯缺陷(AA) (1)2.1表面纵向裂纹(AA01) (4)2.2表面横裂纹(AA02) (6)2.3星状裂纹(AA03) (7)2.4角部横裂纹(AA04) (8)2.5角部纵裂纹(AA05) (10)2.6气孔(AA06) (11)2.7结疤(AA07) (12)2.8表面夹渣(AA08) (13)2.9划伤(AA09) (14)2.10接痕(AA13) (15)2.11鼓肚(AA11) (16)2.12脱方(AA10) (17)2.13弯曲(AA12) (18)2.14凹陷(AA14) (19)2.15镰刀弯(AA15) (20)2.16锥形(AA16) (21)2.17中心线裂纹(AA17) (22)2.18中心疏松(AA18) (23)2.19三角区裂纹(AA19) (25)2.20中心偏析(AA20) (27)2.21中间裂纹(AA21) (28)2.1表面纵向裂纹(AA01)图2-1-11、缺陷特征表面纵向裂纹沿浇注方向分布在连铸板坯上下表面,裂纹深度一般为2mm~15mm,裂纹部位伴有轻微凹陷。
在连铸浇注过程中,当连铸板坯坯壳在结晶器内所受到的应力超过了坯壳所能承受的抗拉强度时,即产生表面纵向裂纹。
表面纵向裂纹缺陷在结晶器内产生,出结晶器后若二次冷却不良,裂纹将进一步加剧。
2、产生原因及危害产生原因:①钢中碳含量处于裂纹敏感区内;②结晶器钢水液面异常波动。
当结晶器钢水液面波动超过10mm时,表面纵向裂纹缺陷易于产生;③结晶器保护渣性能不良。
保护渣液渣层过厚、过薄或渣膜厚薄不均,使连铸板坯凝固壳局部过薄而产生表面纵向裂纹;④中间包浸入式水口与结晶器对中不良,钢水产生偏流冲刷连铸板坯凝固壳,而产生表面纵向裂纹。
危害:轻微的表面纵裂纹经火焰清理后均能消除;表面纵向裂纹严重时可能会造成漏钢;表面纵向裂纹若送热轧进行轧制可能导致热轧产品出现分层、开裂缺陷。
宽板坯连铸机的特点与铸坯质量控制

宽板坯连铸机的特点与铸坯质量控制摘要:本文介绍了八一钢铁集团有限公司投产的宽板坯连铸机主要设备技术参数及工艺特点,并对连铸坯生产过程中的质量控制工艺措施进行探讨,例如结晶器内的钢液面的平稳控制、振动和振痕的控制、钢水的流动的控制等等。
关键词:宽板坯连铸机;特点;铸坯质量控制前言:八一钢铁4#连铸机至2008年7月份开始生产。
中等厚度宽板坯连铸机是承上启下的,生产过程中,设备装备水平的提高是确保本生产线高质量和高产量的一个重要步骤,所以,本连铸机在采用当前普通连铸机成熟技术和可靠工艺的同时,积极应用国际同类连铸机先进技术来达到工艺要求──铸坯零缺陷和热效率高。
一、八钢宽板连铸机工艺特点为确保连铸机产能,节奏和上下道工序相匹配,作业率和线上其他设备相一致以及热送热装等要求,连铸机除使用垂直结晶器、弧形连铸机外,在一般板坯连铸机上多点弯曲多点矫直,液压振动,全程保护浇注技术之外,对浸入式水口进行优化设计、实现了动态轻压下,二冷纵横分区控制和计算机动态配水,实现了铸坯质量的在线判断。
二、浸入式水口的优化设计结晶器中钢水是否畅通,不仅关系到铸坯的质量,而且有时还关系到连铸能否正常运行。
结晶器内部最佳流场应该具备如下特点:1)流股贯穿深度中等,利于夹杂物及气泡上浮;2)流股在局部坯壳上冲刷作用很小,防止了表面纵裂纹和其他缺陷;3)弯月面上的钢液面较为平稳和活跃,不仅避免了保护渣的卷入,减少了角部裂纹的产生;还利于上部钢液更新和避免钢液面结壳对保护渣融化造成影响。
结果表明:弯月面上钢水波纹的最佳高度在5~10 mm之间。
结晶器内流场的变化与结晶器的形状,拉速,通钢量,浸入式水口的形状和浸入深度等因素相关。
八钢4#连铸机不仅结晶器宽度、拉速、通钢量、当地气候环境等变化范围大,而且宽厚比最大超过8,这就对设计提出了更高的要求。
公司根据自己前两台连铸机的设计经验和应用效果,经过优化设计了一台适用于八钢宽板的连铸机,并对其水口浸入深度的最佳范围进行了研究。
连铸板坯缺陷特征和缺陷图谱

连铸板坯缺陷特征和缺陷图谱首钢京唐板坯质检编制2010年8月8日一.连铸坯质量特征综述1.1连铸坯质量定义和特征所谓连铸坯质量是指的到合格产品所允许的铸坯缺陷的严重程度。
对铸坯质量要求而言,主要有四项指标,即连铸坯几何形状、表面质量、内部组织致密性和钢的洁净性;而这些质量要求与连铸机本身设计,采取的工艺以及凝固特点密切相关。
1.2铸坯的检查和清理的意义提高钢的质量,降低成本,加强产品市场的竞争力是企业追求的目标,生产无缺陷连铸坯以保证高附加值产品优良的性能是永恒的主题,连铸坯的裂纹和夹杂物所产生的缺陷可以说是影响产品质量的两大障碍,生产无缺陷或缺陷不足以影响产品质量的连铸坯,这是要努力达到的目标,而连铸坯裂纹和夹杂物所产生的缺陷是受设备、工艺、管理等多种因素制约的。
因此设备、工艺和管理的现代化加上人的质量意识是提高产品质量的关键。
,但是在连铸生产中,铸坯的各种缺陷总是无法避免的,铸坯清理对钢厂保障铸坯质量、降低废品比例具有重要意义。
(1)火焰铸坯清理的注意事项1)一般对表面质量要求较高的钢种,铸坯清理的目的以检查铸坯表面和皮下质量为主,包括夹杂物、气泡、裂纹等分布情况,在清理检查的基础上提供铸坯的进一步处理(清除缺陷、决定铸坯表面质量级别、是否送机器去皮、决定钢种是否达到热送条件等)的意见。
2)微合金钢如Nb、V微合金钢和包晶钢等容易产生角部横裂纹,往往位于铸坯振痕谷底,也需要用火焰清理才能发现。
这方面也应引起足够重视。
3)对于包晶钢、中碳钢等钢种,则以人工清理肉眼可见缺陷为主,包括铸坯常见的表面缺陷,如纵裂、角横裂、重接、凹陷、夹渣、毛刺等,以便尽量降低铸坯判废损失。
(2)不良的火焰清理的危害虽然火焰清理是检查和去除连铸坯表面缺陷的一个极好的方法。
但是,这项操作的确需要掌握一定的技巧,一旦能够正确地操作可确保最终产品不产生额外的表面缺陷。
连铸坯表面上的深槽、凸脊和界面必须平滑以确保清理操作本身不造成额外表面缺陷。
列举一些铸坯常见的外观缺陷特征和原因[1]
![列举一些铸坯常见的外观缺陷特征和原因[1]](https://img.taocdn.com/s3/m/c44b011155270722192ef750.png)
铸坯产检的外观缺陷特征和原因分析鼓肚(Protuberance)【定义与特征】鼓肚是由于受到钢水静压力的作用而使铸坯表面鼓胀成凸面。
【原因分析】二冷喷嘴阻塞,水压不足或偏离;钢水过热度过高;拉速过快,冷却强度不足;支撑辊辊缝过大。
【鉴别与判定】用量具测量鼓肚量,如超出标准要求,做判废处理。
弯曲(Bending)【定义与特征】弯曲是铸坯沿长度方向不平直。
【原因分析】冷却不均匀;摆放不当。
【鉴别与判定】用一米直尺测量弦高,称每米弯曲度。
如超出标准规定,做改尺或判废处理。
用量具测量铸坯全长的弦高,称总弯曲度。
铸坯总弯曲度如超出标准规定,做改尺或判废处理。
表面纵裂(Surface lengthwise crack)【定义与特征】表面纵裂是在板坯表面沿浇铸方向的裂纹。
【原因分析】保护渣熔化不良、渣液层过厚或过薄导致渣膜厚薄不均,使局部凝固壳过薄;结晶器铜板水缝阻塞;结晶器液面波动;浇铸过程中保护渣恶化;结晶器振动台偏振;二冷过强,能进一步扩展纵裂;水口与结晶器厚度方向不对中;硫、磷含量过高时纵裂倾向增加;碳含量在0.12%~0.15%时,纵裂倾向增加。
【鉴别与判定】用肉眼检查,对裂纹处必须处理。
如裂纹较浅,进行火焰清理,如裂纹深度超过标准规定,则做改尺或报废处理。
表面横裂(Surface transverse cracks)【定义与特征】表面横裂是在铸坯表面横向产生的裂纹,一般发生在振痕的波谷处。
【原因分析】结晶器锥度太大;结晶器宽面与窄面冷却强度比值不合适;支撑辊对弧不准;中、高碳钢在没有缓冷的情况下,表面因产生收缩应力也会导致严重的横裂纹;结晶器液面波动;钢中铌、铝与氮形成氮化物,角部裂纹敏感;碳含量在0.10%~0.15%时,铸坯振痕深,表面易产生凹陷或横裂。
【鉴别与判定】用肉眼检查,对裂纹处必须处理。
如裂纹较浅,进行火焰清理,如裂纹深度超过标准规定,则做改尺或报废处理。
角部纵裂(Angle area lenthwise cracks)【定义与特征】角部纵裂是板坯靠近角部处有沿浇铸方向的连续或断续的裂纹。
【精品】板坯缺陷的种类形态、成因及处理办

板坯缺陷的种类形态、成因及处理办板坯常见缺陷的形态成因及处理方法技术质量部2010年8月12日前言近年来,我国中厚板的生产规模有了大幅度增长,随着市场竞争的激烈,产品质量能够满足客户的需求,节约成本成为企业的核心竞争力。
由于连铸钢坯质量决定最终产品质量,因此钢坯质量的检查和判定对钢坯质量控制以及钢板质量控制有着重要的作用,目前钢坯的质量检验主要依靠检验人员的现场观测和低倍硫印的检验。
本书由长期从事产品质量管理方面的专家、学者和有着丰富经验的现场检查判定人员通过较长时间的现场跟踪,对缺陷和生产过程的分析研究后,共同参与编写的,旨在通过概述的编写和出版为有关人员提供参考和借鉴。
本书立足于我公司的生产实际情况,以钢板质量为目标,连铸坯质量控制为核心的钢坯缺陷为例,对钢坯缺陷的形态、产生原因、影响以及处理办法给予了介绍。
随着今后钢种数量的增多和生产方式的多样化,需要对本书不断的补充和丰富。
本书将适时做进一步的补充,欢迎和感谢读者提出宝贵意见和建议。
限于编著者水平,书中难免有不足之处,望读者批评指正,编者不胜感激。
目录一、表面缺陷 (1)1、纵向裂纹 (1)2、横向裂纹 (2)3、角部横裂纹 (3)4、角部纵裂纹 (4)5、窄面横裂(侧裂) (5)6、星状裂纹 (6)7、表面夹杂 (7)8、划伤 (8)9、豁口 (9)10、重接 (10)11、毛刺 (11)二、内部缺陷 (12)1、皮下裂纹 (12)2、皮下气泡 (13)3、缩孔 (14)4、角裂纹 (15)5、三角区裂纹 (16)6、中心裂纹 (17)三、形状缺陷 (18)1、鼓肚 (18)2、凹陷 (19)3、不平度 (20)一、表面缺陷1、纵向裂纹特征:在钢坯表面沿着浇铸方向的裂纹。
纵裂容易出现在板坯宽面中央部位,长度不等,深度一般小于5mm。
实例见图1-1。
成因:主要由于钢坯在凝固过程中坯壳厚度不均,当作用在坯壳的拉应力超过钢的允许强度时,在坯壳薄弱处产生应力集中导致断裂,二冷区扩展形成。
带液芯方坯重压下的变形特点

鞍钢技术2017年第6期ANGANG TECHNOLOGY总第408期带液芯方坯重压下的变形特点张凤心,杨轶龙,宋秉钧,祁林(鞍钢股份有限公司炼钢总厂,辽宁鞍山114021)摘要:应用有限元仿真软件研究了带液芯方坯重压下的变形特点。
结果表明,施加不同压下量,铸坯的宽展变形和应变均随压下量的增加而增加,组合压下较单辊压下的宽展量大,铸坯应变最大值逐渐增大,最大应变位置逐渐向铸坯中心移动,压下量的临界值为12~14mm ,超过该值后,铸坯的最大应变位置出现在铸坯中心。
关键词:方坯;重压下;仿真;宽展;应变中图分类号:TF537文献标识码:A文章编号:1006-4613(2017)06-0017-04Deformation Characteristics of Billet with Liquid Core under Heavy ReductionZhang Fengxin ,Yang Yilong ,Song Bingjun ,Qi Lin(General Steelmaking Plant of Angang Steel Co.,Ltd.,Anshan 114021,Liaoning,China )Abstract :The deformation characteristics of a billet with liquid core under heavy reductionwere studied by the finite element simulation software.The study results showed that both the width deformation and the strain of the billet enlarged with increasing different reduction,com ⁃paring with the width deformation under the reduction by the single pair of rollers,the width de ⁃formation under combined reduction was bigger and also the biggest strain value of the billet grad ⁃ually increased and the biggest strain point gradually moved to the center of the billet,the criticalvalue of the reduction was in the range from 12to 14mm.so if the critical value of the reductionwas over this range,the biggest strain point of the billet should be in the center of the billet.Key words :billet;heavy reduction;simulation;width deformation;strain 方坯重压下是在连铸坯凝固过程中,对铸坯施加压下量,补偿凝固收缩并破碎已经形成的“晶桥”,使得铸坯内的钢水可以自由流动,最大程度地减少中心偏析和疏松,改善铸坯内部质量。
连铸坯低倍组织及缺陷特征分析
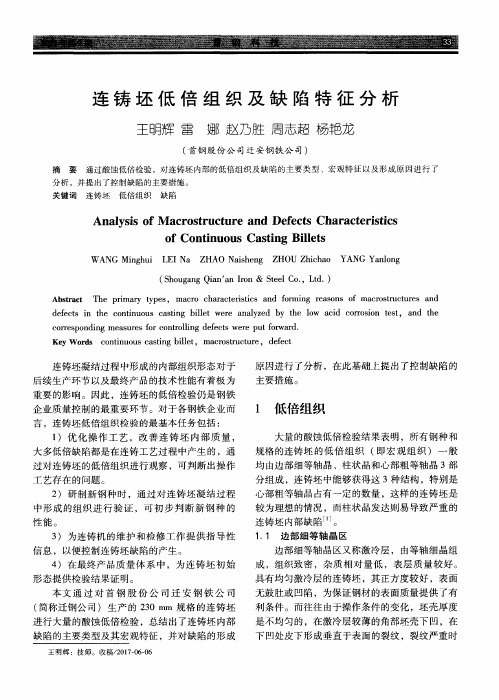
裂纹的敏感性 比等轴晶要强。另外 ,由于柱状 晶 集 溶质元 素 的母 液 流人缝 隙 中 ,因此这种 裂 纹往 不致 密 ,通过 柱状 晶搭桥 ,在 连铸坯 纵 向形 成断 往 伴有偏 析线 ,也 称其 为偏析 条纹 J。在热 加 工
断续续 的缩孔 、中心偏析 和 中心裂 纹等缺 陷 。为 过程 中偏析条 纹是 不能 消除 的 ,在 最终产 品上必
王 明 辉 :技 师 。收 稿/2017—06-06
扩 展到 连铸坯 的对 角线 ,并且 沿对 角线 向心 部延 冷却制 度和 电磁搅 拌技 术 ,可 以促 进柱状 晶 向等
伸扩展 。
轴 晶转 化 ,是减 少 中心 疏松 和改 善连铸 坯 致密 度
1.2 柱状 晶 区
的有效 措施 。
连 铸坯凝 结 过程 中形 成 的 内部 组织 形态 对 于 后续 生 产环 节 以及 最 终产 品 的技术 性能 有着 极 为 重要 的影响 。因此 ,连铸 坯 的低倍 检验 仍是 钢 铁 企业 质量 控 制 的最重 要环 节 。对于 各钢 铁企 业 而 言 ,连铸 坯 低倍 组织 检验 的最 基本 任务 包括 :
3) 为连 铸机 的维 护 和 检修 工 作 提 供 指 导 性 信 息 ,以便 控制 连铸 坯缺 陷 的产生 。
4) 在最 终产 品质 量体 系 中 ,为 连 铸 坯 初 始 形 态提 供检 验结 果证 明。
本 文 通 过 对 首 钢 股 份 公 司 迁 安 钢 铁 公 司 (简 称迁 钢公 司 ) 生产 的 230 mm 规 格 的连 铸 坯 进 行 大量 的酸蚀 低倍 检验 ,总结 出 了连 铸坯 内部 缺 陷 的主要 类 型及其 宏 观特征 ,并 对缺 陷的形 成
1) 优 化 操 作 工 艺 ,改 善 连 铸 坯 内部 质 量 , 大 多低倍 缺 陷都 是在 连铸 工艺 过程 中产 生 的 ,通 过 对连 铸坯 的低 倍组 织进 行观 察 ,可判 断 出操 作 工 艺存 在 的 问题 。
一. 钢铁冶炼、铸造、轧制、锻造和轧制钢板表面缺陷类型、特征、原因、影响
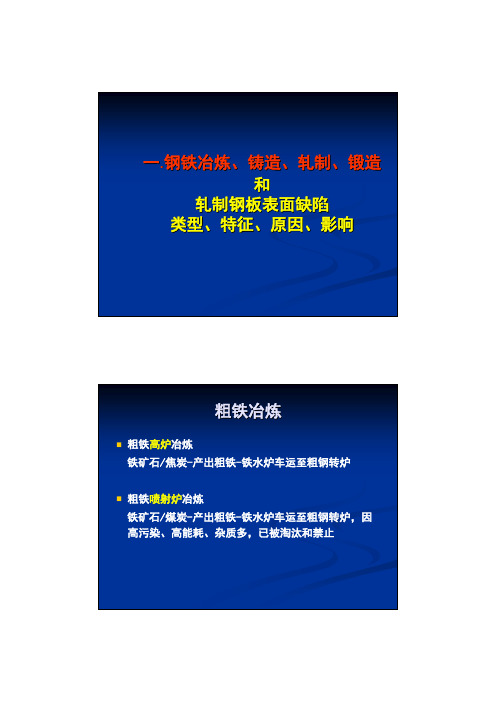
锻造
自由锻/模锻/旋锻 采用铸坯、轧制坯、锻坯 自由锻-可采用铸坯,结构简单、大型件、少批量、损
耗大、余量大、多向锻造比高、精度差,以锻造为主 模锻-需采用轧制坯、锻坯,效率高、损耗少、大批量
、小规格、余量少、结构复杂、成本高、模锻锻造比低、 精度高,以成形为主
对交替加载疲劳、冲击、应力集中部位要重视
钢板标准中都取样于纤维横向 案例
应力集中 主拉伸面 撕裂应力
扭矩 极易断裂
各种金属铸造主要成形工艺
参考网页: /s/IZLlQ-2_icwnM9Xuv3-kQ
钢板表面常见危害性现象
裂纹 分层 折叠 夹杂 皮下气泡 麻点/麻坑 机损 疏松 补焊-
炼铁:铁矿石-杂质、成分、分拣、处理,焦炭-有害气氛、粉尘,
高炉-炉壁、浮渣、沉渣,冶炼-温度、时间、有害气氛,出铁-有害气 氛、浮渣、沉渣,铁水车-有害气氛、车壁,搅拌-浮渣、沉渣、匀度, 工艺-成分、时机、温度、时间,冶炼取样,外来杂物;
炼钢:钢包-炉壁、浮渣、沉渣,冶炼-有害气氛、浮渣、沉渣,添
质保书上冶炼炉号、冶炼制度、化学分析等可精确描 述和完全追踪
形坯
浇铸至所需要的形坯 砂型铸造(件)
致密度低、缺陷多、精度差、成本低 特殊铸造(件)(相对于砂型铸造)
致密度中、缺陷少、精度高、成本高 轧制/锻造/可锻铸造(相对于砂型铸造)
视材料可轧、可锻性而定,浇铸成形后再轧制、锻造 ,目的是减少后续基本造型,以降低加工成本和耗材
钢板热轧
控温热轧(控轧)(TM) -在非奥氏体再结晶温度区域,或在铁素体与奥氏体 两相组织温度区域的温度内,对钢坯传统热轧最后一 次轧制成形进,并根据需要,控制冷却速度和控轧时 机,使晶粒/晶界和组织固熔/偏析有充分时间进行变 形/恢复和稳定/弥散的过程,目前成为世界细晶粒钢 生产现代化工艺,能细化晶粒、稳定性能、匀质厚度 ,提高室温、中温和抗疲劳实际强度及韧性、抗大气 腐蚀性能,如 GB 713中Q235R/Q345R、EN 10025和EN 10028等允许采用,美国材料体系标准中很少采用, 如ASME A20
连铸薄板坯表面变形实验研究

连铸薄板坯表面变形实验研究近年来,随着经济的发展,薄板的使用量正在快速增长,薄板的变形已成为当前制造业的一个重要的研究课题。
薄板的变形是指在表面受到外部载荷作用时,加以变形,产生不同程度的局部变形,使表面发生凹凸变形,形成曲面变化,从而影响表面精度和密封性能。
在金属薄板变形过程中,关键技术是表面变形,目前主要有两种变形方式,即挤压变形和冷滚压变形。
挤压变形是用模具把薄板坯加热成型,使薄板坯有着一定的曲面,但是模具费用高,时间较长,并且模具的设计要求比较高,精度不高,不适合大量生产;冷滚压变形是把薄板坯放在辊筒上,在水冷辊筒的作用下,被模具挤压,使薄板坯获得一定的曲面,可以满足大批量生产,但是这种变形方式会破坏材料组织,影响材料性能。
为了降低成本,提高效率,提高生产精度,研究者利用连铸技术进行薄板坯表面变形。
连铸技术是指将钢水倒入连铸机,经过连铸机的加热、熔化、冲凌、浇注等工艺步骤,获得熔体、液相、固相状态的钢铁制品,在熔体态下,通过冷滚压、热滚压、热轧等工艺,可以调整薄板坯表面形貌。
将薄板坯放入连铸机,在熔体态下,对坯料表面形貌进行调整,让坯料表面有必要的凹凸结构,使坯料表面具有必要的光洁度,提高坯料表面分类精度,大大提高了工艺精度要求,实现再创造。
此外,熔体状态下进行表面变形,不会造成内部组织的改变,大大提高了材料的使用性能,更加经济。
基于以上原因,本研究着重分析了用连铸技术对薄板坯表面变形的研究。
首先,分析了冷滚压和热滚压等技术参数,比较了不同变形工艺参数对薄板坯表面变形的影响;其次,设计了不同变形工艺的成形试验,分析不同工艺参数对变形坯料表面凸凹形态改变的影响;最后,对成形试验取出的坯料表面进行X光扫描,研究薄板坯表面变形的技术参数取得了较完善的结果,评估了技术参数在薄板坯表面变形工艺中的作用,为今后的研究奠定了较为坚实的基础。
通过本研究,可以发现使用连铸技术可以很好地实现薄板坯表面变形,大大提高了生产效率,降低了生产成本,达到了良好的精度,保证了材料性能。
铸坯质量分析.

概述
连铸方坯的缺陷一般可分为表面缺陷、内部缺陷和形状缺陷。表面 缺陷包括:表面裂纹(含横向、纵向、角部和面部裂纹)、气泡、 夹渣、双浇、翻皮、振痕异常、渗漏、冷溅,擦伤等。内部缺陷包 括:内裂、非金属夹杂物、中心偏析和中心疏松等。形状缺陷包括: 菱形变形又称“脱方”、纵向和横向凹陷等。
概述
减少钢液的气体及夹杂含量;控制过 热度、拉速;采用电磁搅拌
采用低温浇注、电磁搅拌及轻压下、 控制冷却强度;避免坯壳变形、控制 夹辊间距、严格对弧对中 控制过热度、拉速及二次冷却;采用 电磁搅拌及轻压下 检查结晶器的形状及表面损伤、水缝 的均匀及锥度情况;检查对弧及控制 冷却水量;浸入水口与结晶器对中不 形成偏流;控制矫直时铸坯角部温度
• 引起表面裂纹的主要原因是: 铸温过高,拉速过快,结晶 器变形,一次冷却过快且不 均匀。其次的原因是二次冷 却过分剧烈,二次冷却喷嘴 位置不正,铸坯矫直时温度 过低等。另外,当钢水脱氧 不完全或钢水中含有氢气时 会形成皮下气泡;钢水温度 过低,拉速太慢,结晶器保 护渣不良,钢水飞溅等还会 相应引起其它一些表面缺陷。 引起内裂的主要原因是铸坯 在二次冷却区时所承受的热 应力和机械应力过大;另外, 拉速过快会引起中心缩孔。
内部裂纹
• 各种应力作用的脆弱的凝固 界面上产生的裂纹称之为内 部裂纹。由于在凝固界面上 成分富集的钢液流入裂纹部 位,通过硫印和低倍酸浸才 可显出的这些裂纹,所以也 有的称之为偏析裂纹或偏析 条纹。除了较大的裂纹,一 般均可在随后的轧制过中焊 合。按内部裂纹的出现部位 及成因将之分为挤压裂纹、 中间裂纹、角部裂纹和中心 星状裂纹。 • 挤压裂纹是铸坯在带液相进 行拉坯或矫直时,所承受的 变形率超过了铸坯所允许的 变形率,则形成裂纹。 稳定操作、减少漏钢后的强 制拉坯;设置限位垫块,防 止过压、可避免该裂纹发生。 中间裂纹是在铸坯外侧和中 心之间的中间某一位置,在 柱状晶间产生的裂纹,其位 置一般在中间,故称为中间 裂纹。
钢坯常见缺陷图谱讲解
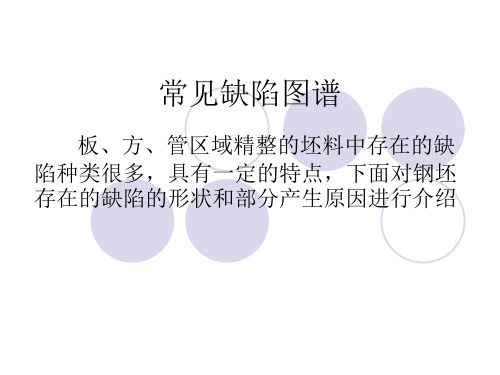
在带锯锯切过程因板坯内部应力引起的锯切断裂
缺陷名称 压痕(轧痕)
代码
缺陷特征
轧件表面压入异物,孔型掉肉或粘附异物而造成的钢坯表 面无规或有规律性分布的凹坑或凸痕。
此缺陷主要因轧机的翻钢钩引起 的表面压痕,为与钢坯长度方向 平行的纵向缺陷。
此缺陷主要由推钢机滑块突出造 成。
缺陷名称 刮伤
代码
缺陷特征
钢坯表面被划出沟痕或刮去一条金属。
产生的原因可能为钢坯在传输或轧制时碰到辊道或轧机上有异物尖锐突出,与钢坯 接触时,在表面留下一条强制的刮伤,发生此类缺陷应在过钢件上检查是否有设备 原因。
代码
缺陷特征
钢坯断面呈平行四边形、梯形等形状的缺陷。
因为轧制原因造成。
缺陷名称 代码
缺陷特征
凹面
钢坯表面呈凹面。
主要是由压缩比不够,造成的。
缺陷名称 代码
缺陷特征
切割裂纹
因火焰切割产生的裂纹
部分合金钢由于硬度比较高,在火焰切割后由于受热而产 生应力使得端部切割后产生裂缝。
缺陷名称 辊环压痕
代码
常见缺陷图谱
板、方、管区域精整的坯料中存在的缺 陷种类很多,具有一定的特点,下面对钢坯 存在的缺陷的形状和部分产生原因进行介绍
缺陷名称 角部横裂
代码
缺陷特征
钢坯角部与轧制方向近乎垂直的横向线状缺陷。
形成原因:多为角裂的扩展
缺陷名称 缩孔
代码
缺陷特征
在钢坯断面上残留的缩孔超过规定切头的部分。
ห้องสมุดไป่ตู้
钢锭浇注凝固时,发生体积收缩,先凝固部分的体积收缩可由尚未凝固的钢液 补充,当钢液由外向内,由下向上冷却的过程中,在铸锭上部中间最后凝固的 部分,因得不到钢液的补充,集中形成了倒圆锥形的收缩孔洞,称为缩孔。这 里主要因为剪切不够,在剪切端面上的缩孔。
连铸板坯和方坯表面缺陷的分析与判定

在钢板、板卷、棒材、型钢上的裂纹和其他等缺陷,大多源于板坯和方坯上的缺陷。
大多数钢厂面临的最大挑战是缺乏如何判定、检查这些缺陷及相应地采取何种对策。
令人遗憾的是,目前很多钢厂在遇到表面缺陷问题时所做的一些措施并不恰当,甚至没有对板坯和方坯进行检测分析便作出相应的判定和措施。
1.板坯和方坯的表面缺陷类型板坯和方坯上的所有表面缺陷几乎可以被分成五大类,并且在世界上大多数铸机上它们的发生位置基本上也是可以预测的。
基于经验,按照发生概率的大小顺序列出了五大类缺陷,即针状气孔/疏松、裂纹、深度振痕、不良清理、结晶器壁污染和刮伤等。
依据加热炉的氧化条件,可以确定板坯和方坯表面缺陷的临界深度,从而判定缺陷是否最终会成为板材、板卷或棒材上的轧制表面缺陷。
大部分加热炉操作会导致1%~2%厚度的铸坯氧化成氧化铁皮。
如果铸坯的厚度为220mm,就意味着在加热过程中会造成2.2mm~4.4mm的厚度损失。
这个厚度损失同样会传递到表面缺陷。
如果铸坯表面缺陷的深度小于铸坯厚度的1%~2%,那么这些缺陷将在加热过程中消除。
而那些比成为氧化铁的1%~2%厚度更深的缺陷,最终会造成轧材的表面缺陷。
1)针状气孔/疏松在所有铸机上,针状气孔/疏松几乎都是常见的,也是最容易被忽略的铸坯缺陷。
如果钢中的气体得不到合理控制,就会在板坯和方坯表面上产生针状气孔/疏松。
当凝固率达到90%而气体总压力Ar+H2+N2+CO+CO2>1atm时,针状气孔/疏松就会在板坯和方坯表面上形成。
找出表面和皮下针状气孔/疏松的形成原因并不困难。
在实际生产中,皮下通常是指表面以下10mm的深度。
根据经验,针状气孔/疏松是影响钢板、板卷表面质量的最突出问题。
举一个板坯上的针状气孔/疏松的例子,钢种是V和Nb复合微合金化的A572Gr50结构钢,含0.15%C,在铸坯上角部出现针状气孔/疏松,导致14.3mm厚的成材的上边部出现缺陷。
该板坯进行了展宽轧制以满足板宽尺寸的需要。
铸造缺陷特征、机理与防治措施

铸件拐角或冒口附近出现的由于补缩不足造成 的不规则裂纹。
1515
缩陷
铸件的厚断面或端面交界处上平面塌陷现象, 缩陷的下面有时有缩孔。 缩陷有时也出现在内缩孔附近的表面。
1601
带肉
铸件本体对应的水冒口、芯头劈缝、排气位置 去除铸件水冒口、排气等时损伤铸件本 残缺,外形不符或加工量不足。 体,致铸件形状残缺。 清除内腔残砂、外壁粘砂时敲击过度致产 品表面形状不符图纸要求
1703
针孔
1704
呛火
1705
变形
1706
起皮
1707
脏眼
1708
脉纹
1709
超重
铸件部分或全部尺寸偏大,重量超出正常。
由于模具变形、造型紧实不足、砂型变形 等原因造成
铸件分型面、活块、型芯配合处及其他工 1710 飞边毛刺 铸件分型面、活块、型芯配合处或芯头溢流位置的片状多肉。 艺措施产生的片状多肉。
1509
硬点
1510
热裂
铸件在凝固冷却过程中液固相共存时由于 铸件热结附近无规则的开裂,断口金属表面有 内应力过大产生的穿透或不穿透的晶界裂 氧化色(黑褐色),深度见底。 纹。
1511
冷裂
裂口平直,常穿过晶粒延伸到整个断面,呈金 在常温下由于内应力过大或外力作用下形 属光泽,无氧化色,裂纹较深。 成的长条形且宽度均匀的裂纹。 1、由于铸件断面过厚或壁厚不均匀,在 壁厚部分热节处补缩不良产生缩孔; 2、液体金属的含气量太高,导致在铸件 冷却过程中以气泡形式析出,阻止邻近的 液体金属向该处流动进行补缩; 3、当灰铸铁碳当量太低时,将使铁水凝 固时共晶石墨析出量减少,降低了石墨化 膨胀的作用,使凝固收缩增加,同时也降 低铁水的流动性。 4、当铁水含磷量或含硫量偏高时,磷是 扩大凝固温度范围的元素,同时形成大量 的低熔点磷共晶,凝固时减少了补缩能力 。 1、当合金结晶温度范围较宽时,在铸件 表面结壳后,内部有一个较宽的液、固两 相共存的凝固区域。继续凝固,固相不断 增多。凝固后期,先生成的树枝晶相互接 触,将合金液分割成许多小的封闭区域, 当封闭区域内合金液凝固收缩得不到补充 时,就形成了缩松。 2、缩松可以看成为许多分散的小缩孔, 合金的结晶温度范围愈宽,愈易形成缩松 1、型、芯的退让性差别大,对铸件的收 缩阻力不同造成缩裂; 2、铸件有过大热节或不利于散热结构; 3、铁水质量,如浇注温度、杂质含量等 1、原理与缩孔、缩松相似,为铸件凝固 过程中的体积亏损缺陷; 2、铁水浇注温度高会增加液态收缩。 3、(型砂含泥量、灰分不容忽略,相关 资料)
连铸坯主要表面缺陷类型

连铸坯主要表面缺陷类型
连铸坯主要表面缺陷有:深振痕、凹陷、裂纹等。
1、深振痕
连铸坯的振痕有凹陷形振痕、钩形振痕两种类型。
连铸坯振痕较浅时,一般不会对最终成品产生影响;振痕较深时,在振痕波谷处,由于受到的冷却强度较弱,铸坯皮下晶粒粗大,就可能成为连铸坯横向裂纹的根源。
影响振痕深度的因素主要有润滑方式、钢种成分、保护渣性能、结晶器振动模式等。
减小结晶器内钢液初始凝固坯壳的弯曲变形程度可以降低连铸坯的振痕深度。
2、表面凹陷缺陷
连铸坯的表面凹陷有横向凹陷和纵向凹陷两种类型。
横向凹陷的形成与结晶器内液位上升有关,当液位波动峰值超过渣圈时,带动渣圈下移,此时形成横向凹陷。
纵向凹陷是结晶器上部锥度太小和刚性的角部转动,使小偏离角凹陷形成,由于结晶器下部锥度太大,结晶器压向坯壳使凹陷增加,从而在宽面出现偏离角凹陷。
降低结晶器冷却强度,提高结晶器内凝固坯壳所受冷却强度的周向均匀性,防止结晶器液位波动过大,可以消除铸坯的表面凹陷缺陷。
3、表面裂纹缺陷
表面裂纹主要有横向裂纹、纵向裂纹、星型裂纹等。
结晶器内初始凝固坯壳厚度不均匀,在坯壳薄弱处产生应力集中,会产生纵向裂纹。
表面横裂纹一般出现在振痕波谷处。
星型裂纹一般在铸坯表面去除氧化铁皮或渣膜后才会发现,与铸坯表面吸收了结晶器的Cu,同时铸坯表面Fe的选择性氧化,使残存元素(Cu、Sn 等)残留,沿晶界渗透形成星型裂纹。
保证结晶器内初始凝固坯壳厚度的均匀性是控制纵向裂纹的关键。
控制横向裂纹的关键是降低铸坯振痕深度,避免铸坯在低温脆性区弯曲或矫直。
控制星型裂纹的关键是结晶器内壁状态是否良好,铸坯温度控制是否合理。
- 1、下载文档前请自行甄别文档内容的完整性,平台不提供额外的编辑、内容补充、找答案等附加服务。
- 2、"仅部分预览"的文档,不可在线预览部分如存在完整性等问题,可反馈申请退款(可完整预览的文档不适用该条件!)。
- 3、如文档侵犯您的权益,请联系客服反馈,我们会尽快为您处理(人工客服工作时间:9:00-18:30)。
板坯连铸带液芯压下铸坯变形特点
崔立新张家泉陈志平
北京科技大学冶金学院炼钢所
宝钢集团上海梅山有限公司
板坯连铸带液芯压下铸坯变形特点
Soft-reduction Characteristics of Continuous Cast Slabs with Liquid Core
崔立新1 张家泉1陈志平2
(1- 北京科技大学冶金学院炼钢所; 2-宝钢集团上海梅山有限公司)
摘要:采用弹塑性热力耦合有限元法,模拟板坯连铸带液芯轻压下过程中的坯壳变形,指出轻压下初始阶段坯壳较薄时铸坯纵向伸长可以忽略,但轻压下后期坯壳较厚时铸坯纵向伸长不能忽略。
分析影响铸坯纵向伸长的主要因素,给出铸坯纵向塑性应变与坯壳厚度和压下率的关系。
关键词:板坯连铸;轻压下;纵向伸长;MSC.Marc
ABSTRACT:Soft reduction characteristics of continuous cast slabs with liquid core is studied with the aid of elastic-plastic and thermal-mechanical coupled FEM.The studies show that the longitudinal tensile strain of strand can be ignored for thin shell, but it can not be ignored for thick shell.The effects of shell thickness and related height reduction on the longitudinal tensile strain of strand are analyzed.
Key words:slab casting; soft reduction;longitudinal tensile strain;MSC.Marc
轻压下过程中铸坯变形对确定轻压下过程中的轧辊转速,保证相邻轧辊转动协调,避免轧辊转动不协调而引起铸坯鼓肚或拉长有一定的影响。
本文应用有限元软件MSC.Marc,采用弹塑性热力耦合有限元法,模拟Q235A钢种板坯连铸液芯轻压下时的铸坯变形,并分析影响铸坯变形的主要因素。
l有限元模型
图1所示为铸坯的有限元离散网格,轧辊简化为刚性体。
轻压下时,宽面坯壳的伸长是轧辊与铸坯液芯对坯壳的压力和起始于铸坯侧边的剪应力共同作用的结果。
Wunnenberg已研究表明[1],在压下率等于20%时,起始于侧边的剪应力引起的宽面伸长只有1%,所以轧辊与铸坯液芯对坯壳的压力是宽面坯壳伸长的主要原因。
本文采用二维有限元模拟重点突出铸坯液芯压力对宽而坯壳纵向伸长的作用。
图1 有限元离散网格
假定轻压下是在二冷区垂直段由铸坯两侧的轧辊同时对称压下。
为了分析不同坯壳厚度对铸坯纵向伸长的影响。
冷却条件随着所在二冷区的不同位置的变化而改变,坯壳厚度随着冷却时间变化。
则分别对不同坯壳厚度的铸坯进行轻压下,分析坯壳厚度对铸坯纵向伸长的影响。
对同一坯壳厚度的铸坯分别用不同的压下率进行轻压下,分析压下率对铸坯纵向伸长的影响。
铸坯厚215 mm,由于对称,取铸坯厚度的一半为研究对象,对称面上厚度方向为对称边界条件,没有位移。
纵向取0.5米作为模拟计算长度。
拉速1.2m/min。
材料各向同性,遵守 Von Mises屈服准则。
二冷区铸坯沿拉坯方向的运动是主动辊与铸坯的摩擦力及铸坯重力共同作用的结果。
文中的模拟忽略摩擦力和重力,而假设未变形区坯壳的速度等于拉坯速度,这样大大简化模型,同时不会对铸坯变形影响太大。
为了沿用现有的弹塑性力学有限元法,可以对铸坯液芯作简化或等效处理[2]。
其中一种方法是剔除液芯单元,将其对坯壳的作用转化为相应的分布载荷;另一种方法是计算域包括坯壳与液芯,但为了避免计算域不同状态单元刚度相差悬殊造成计算收敛困难甚至刚度矩阵奇异,对液芯力学特性进行约定,即弹性模量(E)取不等于零的一个小量,泊松比(γ)接近0.5;并依据使液态体积模量(E/(1-2γ))与常温体积模量尽量接近的方法,使液态的应力状态保持与静水压相近。
本文采用第二种处理方法。
下面,以简单线弹性体为例进行说明:
,
ij ij ij p δσσ+='其中,,ij ij G εσ2'=)(0T T p V −−=βλε,)1(2γ+=E G ,)21)(1(γγγλ−+=E ,)γ21(3α
β−=E 。
因此,当δ→O.5,E 取小量时,偏应力张量
的大小受到约束,从而使'ij σij σ与静水压p
接近。
2结果与讨论
2.1坯壳厚度对铸坯纵向塑性应变的影响
带液芯轻压下时,影响铸坯变形的因素很多,其中压下率和坯壳厚度是两个主要因素。
图1所示是压下率等于18%时铸坯纵向塑性应变与坯壳厚度的关系。
从图中可以看出,坯壳较薄时,铸坯纵向塑性应变较小;坯壳较厚时,铸坯纵向塑性应变较大。
板坯连铸拉速高,带液芯轻压下时压下速度快,液芯是糊状的两相区,流动性差,目此,带液芯轻压下时不能忽略液芯对坯壳的反作用力。
在接近凝固温度时,铸坯塑性很差,不能承受很大的塑性变形,而坯壳厚度增大时,铸坯纵向塑性应变增加,这对铸坯来说是危险的。
如果铸坯纵向塑性应变大于临界应变,就会产生裂纹。
所以,对带液芯轻压下来讲,对坯壳厚度有一定要求。
图1铸坯纵向塑性应变与坯壳厚度的关系曲线
在接近凝固温度时,铸坯塑性很差,不能承受很大的塑性变形。
而坯壳厚度增大时,铸坯纵向塑性应变增加,这对铸坯来说是危险的,如果铸坯纵向塑性应变大于临界应变,就会产生裂纹。
所以,对轻压下来讲,对坯壳厚度有一定要求。
2.3压下率对铸坯纵向塑性应变的影响
图2所示是坯壳厚度等于25 mm时铸坯纵向塑性应变与压下率的关系。
从图中可以看出,纵向塑性应变随压下率的增加而增大,当压下率达到一定值时应变不再增大。
图2铸坯纵向塑性应变与压下车的关系
2.4轻压下模拟实验分析
轻压下过程中,厚坯壳液芯铸坯产生的纵向塑性应变不能忽略,除非这种应变受到抑制。
液芯铸坯轻压下时,铸坯厚度方向存在很大的温度梯度,这与传统的热轧和冷轧不同。
板坯连铸拉速高,轻压下时压下速度快,液芯是糊状的两相区,流动性差,轻压下时不能忽略液芯对坯壳的反作用力。
3结论
(1)板坯连铸液芯轻压下时不能忽略液芯对坯壳的反作用力。
(2)板坯连铸液芯一对辊轻压下在坯壳较薄时铸坯纵向伸长可以忽略,坯壳较厚时铸坯纵向伸长不能忽略。
(3)压下率一定时,铸坯纵向伸长随坯壳厚度的增加而增加;坯壳厚度一定时,铸坯纵向伸长随压下率的增加而增加。
4参考文献
[1]. Wunnenberg K,Schwerdtfeger K. Principles in Thin Slab Casting.Iron & Steel Maker,1995,22(4):25。
[2]. Kelly J E,Michalek K P,O’connor T G,et al. Initial Development of Thermal and Stress Fields inContinuously Cast Steel Billets. Metall Trans,1988,19A :2589。