注塑件常见缺陷对电镀的影响及解决方案
注塑成型各种缺陷的现象及解决方法

注塑成型各种缺陷的现象及解决方法.txt我爸说过的最让我感动的一句话:“孩子,好好学习吧,爸以前玩麻将都玩儿10块的,现在为了供你念书,改玩儿1块的了。
”注塑成型各种缺陷的现象及解决方法[塑料]一)熔接痕熔接痕是由于来自不同方向的熔融树脂前端部分被冷却、在结合处未能完全融合而产生的。
一般情况下,主要影响外观,对涂装、电镀产生影响。
严重时,对制品强度产生影响(特别是在纤维增强树脂时,尤为严重)。
可参考以下几项予以改善:l)调整成型条件,提高流动性。
如,提高树脂温度、提高模具温度、提高注射压力及速度等。
2)增设排气槽,在熔接痕的产生处设置推出杆也有利于排气。
3)尽量减少脱模剂的使用。
4)设置工艺溢料并作为熔接痕的产生处,成型后再予以切断去除。
5)若仅影响外观,则可改变烧四位置,以改变熔接痕的位置。
或者将熔接痕产生的部位处理为暗光泽面等,予以修饰。
二)放射纹放射纹(Jetting)1、表观从浇口喷射出,有灰黯色的一股熔流在稍微接触模壁后马上被随后注入的熔料包住。
此缺陷可能部分或完全隐藏在制品内部。
物理原因放射纹往往发生在当熔料进入到模腔内,流体前端停止发展的方向。
它经常发生在大模腔的模具内,熔流没有直接接触到模壁或没有遇到障碍。
通过浇口后,有些热的熔料接触到相对较冷的模腔表面后冷却,在充模过程中不能同随后的熔料紧密结合在一起。
除去明显的表面缺陷,放射纹伴随不均匀性,熔料产生冻结拉伸,残余应力和冷应变而产生,这些因素都影响产品质量。
在多数情况下不太可能只通过调节成型参数改进,只有改进浇口位置和几何形状尺寸才可以避免。
与加工参数有关的原因与改良措施见下表:1、注射速度太快降低注射速度2、注射速度单级采用多级注射速度:慢-快3、熔料温度太低提高料筒温度(对热敏性材料只在计量区)。
增加低螺杆背压与设计有关的原因与改良措施见下表:1、浇口和模壁之间过渡不好提供圆弧过渡2、浇口太小增加浇口3、浇口位于截面厚度的中心浇口复位位,采用障碍注射、工艺溢料是指用手工在模具上开一条深一些的排气槽,在生产时此槽产生出来的(批峰),又叫工艺批峰,主要是用来改善烧胶或熔接痕,可将烧胶或熔接痕调整到此批峰上,生产后将其切除。
注塑电镀缺陷分析及处理
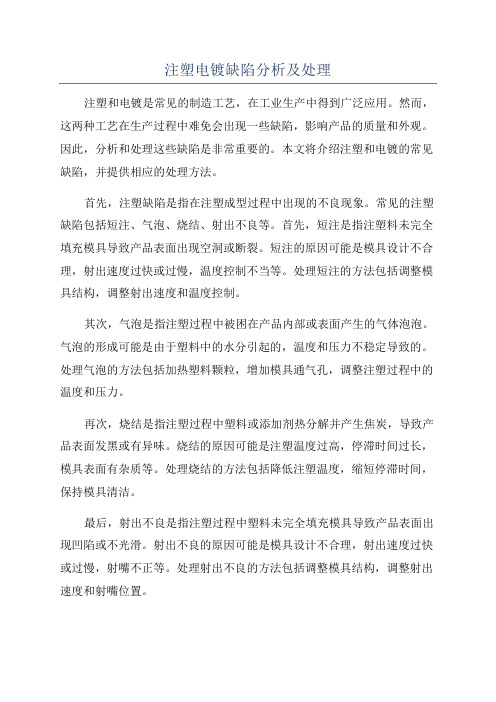
注塑电镀缺陷分析及处理注塑和电镀是常见的制造工艺,在工业生产中得到广泛应用。
然而,这两种工艺在生产过程中难免会出现一些缺陷,影响产品的质量和外观。
因此,分析和处理这些缺陷是非常重要的。
本文将介绍注塑和电镀的常见缺陷,并提供相应的处理方法。
首先,注塑缺陷是指在注塑成型过程中出现的不良现象。
常见的注塑缺陷包括短注、气泡、烧结、射出不良等。
首先,短注是指注塑料未完全填充模具导致产品表面出现空洞或断裂。
短注的原因可能是模具设计不合理,射出速度过快或过慢,温度控制不当等。
处理短注的方法包括调整模具结构,调整射出速度和温度控制。
其次,气泡是指注塑过程中被困在产品内部或表面产生的气体泡泡。
气泡的形成可能是由于塑料中的水分引起的,温度和压力不稳定导致的。
处理气泡的方法包括加热塑料颗粒,增加模具通气孔,调整注塑过程中的温度和压力。
再次,烧结是指注塑过程中塑料或添加剂热分解并产生焦炭,导致产品表面发黑或有异味。
烧结的原因可能是注塑温度过高,停滞时间过长,模具表面有杂质等。
处理烧结的方法包括降低注塑温度,缩短停滞时间,保持模具清洁。
最后,射出不良是指注塑过程中塑料未完全填充模具导致产品表面出现凹陷或不光滑。
射出不良的原因可能是模具设计不合理,射出速度过快或过慢,射嘴不正等。
处理射出不良的方法包括调整模具结构,调整射出速度和射嘴位置。
除了注塑缺陷,电镀缺陷也是制造过程中常见的问题。
常见的电镀缺陷包括气泡、孔洞、颜色不均匀和剥落等。
首先,气泡是指电镀过程中,被电解液困住的气体形成气泡。
气泡的形成可能是由于电解液中含有水分,电镀时间过长或温度不稳定。
处理气泡的方法包括预处理金属表面,控制电解液的成分和温度。
其次,孔洞是指电镀过程中金属表面出现小孔的问题。
孔洞的原因可能是金属表面存在杂质或油污,电镀液配比不当等。
处理孔洞的方法包括清洁金属表面,优化电镀液配比。
再次,颜色不均匀是指电镀后金属表面出现色差或斑点。
颜色不均匀的原因可能是电解液的浓度不一致,电镀时间不稳定或金属表面存在杂质。
塑料电镀过程中常出现的缺陷及原因分析
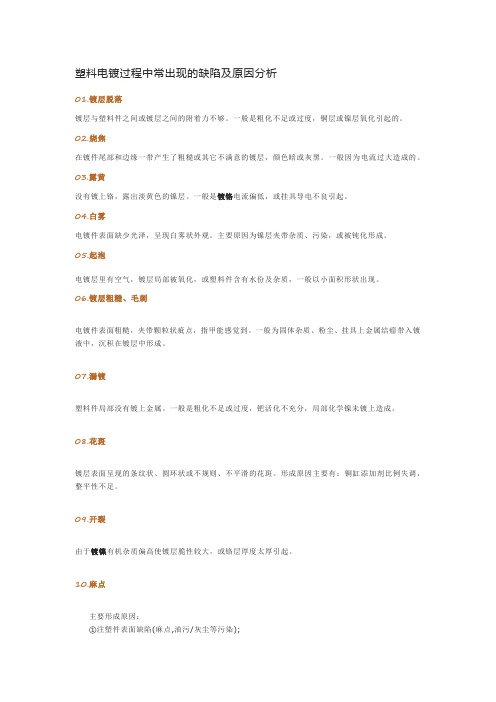
塑料电镀过程中常出现的缺陷及原因分析01.镀层脱落镀层与塑料件之间或镀层之间的附着力不够。
一般是粗化不足或过度,铜层或镍层氧化引起的。
02.烧焦在镀件尾部和边缘一带产生了粗糙或其它不满意的镀层,颜色暗或灰黑。
一般因为电流过大造成的。
03.露黄没有镀上铬,露出淡黄色的镍层。
一般是镀铬电流偏低,或挂具导电不良引起。
04.白雾电镀件表面缺少光泽,呈现白雾状外观。
主要原因为镍层夹带杂质、污染,或被钝化形成。
05.起泡电镀层里有空气,镀层局部被氧化,或塑料件含有水份及杂质,一般以小面积形状出现。
06.镀层粗糙、毛刺电镀件表面粗糙,夹带颗粒状疵点,指甲能感觉到。
一般为固体杂质、粉尘、挂具上金属结瘤带入镀液中,沉积在镀层中形成。
07.漏镀塑料件局部没有镀上金属。
一般是粗化不足或过度,钯活化不充分,局部化学镍未镀上造成。
08.花斑镀层表面呈现的条纹状、圆环状或不规则、不平滑的花斑。
形成原因主要有:铜缸添加剂比例失调,整平性不足。
09.开裂由于镀镍有机杂质偏高使镀层脆性较大,或铬层厚度太厚引起。
10.麻点主要形成原因:①注塑件表面缺陷(麻点,油污/灰尘等污染);②溶液杂质较多,杂质净化不彻底;③厂房内粉尘及其它污染物;④清洗水杂质;⑤厂房内酸雾易腐蚀镀层产生麻点;⑥设备故障造成零件掉落,产品长时间浸泡于药水中,镀层溶解,生成杂质;⑦搅拌空气源有尘埃及其它污染物;⑧挂具结瘤溶解于溶液,挂具破胶不易清洗,污染药水等。
11.露底麻点镀件微小的漏镀部分,如针孔一样大小。
主要形成原因:挂具结瘤带入杂质而溶解在钯缸及化学镍溶液;厂房内铬酸雾、盐酸雾污染零件表面;粗化,钯缸,解胶,化学镍等前处理溶液杂质。
12.针孔主要是镀镍层表面张力偏高,湿润剂量偏低而在镀层表面形成微小的孔穴,但不露出塑料基体。
注塑件外观缺陷图片及原因分析与影响
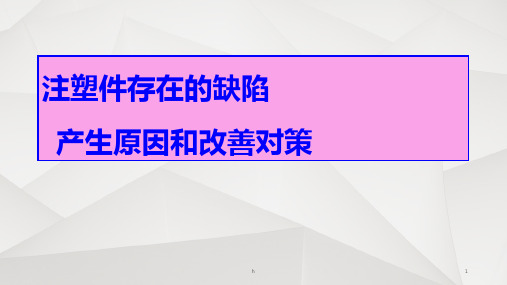
2,造成水花斜射。
3,损失扩大化 。
h
15
本体尾部毛边
毛边产生的原因: 1射出速度,压力太大。 2,保压速度,压力太大。 3模具配合不良。
改善对策: 减小射出速度,压力。 减小保压速度,压力。
维修模具。
尾部毛边产生的后果: 1,影响外观。 2,手感不好,造成刮手。
h
16
面板毛边
顶针毛边产生的原因: 1,射出压力太大。 2,射出速度太大。 3,顶针或顶针孔磨损。
裂纹产生的升后高果料管:温度。 1,影响外观。 2,电镀后影响性能。
造成电镀件报废。 3,损失扩大化。
h
10
波纹
波纹产生的原因: 1,射出速度太慢。 2,射出压力太小。 3,料温太低。 4,模温太低。
改善对策: 加快射出速度。 加大射出压力。
升高料管温度。 接模温机,调整
适当的模温。
波纹产生的后果 : 1,影响外观。 2,电镀后表面不光滑, 3,损失扩大化。
造成电镀件报废。
h
19
压白
面板压白产生的原因:
改善对策:
1,射出速度太快。
减慢射出速度。
2,射出压力太大。
减小射出压力。
3,射出时间太长。
减短射出时间。
h
6
胶口气痕
胶口气痕产生的原因: 1,进胶口处速度太快。 2,进胶口处压力太大。 3,进胶口位置不准确。 4,模温太低。 5,进胶口处排气不良。
改善对策。 减慢进胶处速度。 减小进胶处压力。 调整进胶中位置。
接模温机调整温度。 增加排气槽。
胶口气痕产生的后果: 1,影响外观。 2,电镀后镀不亮,
影响外观。 3,损失扩大化。
h
12
注塑件应力对电镀质量影响以及解决方案
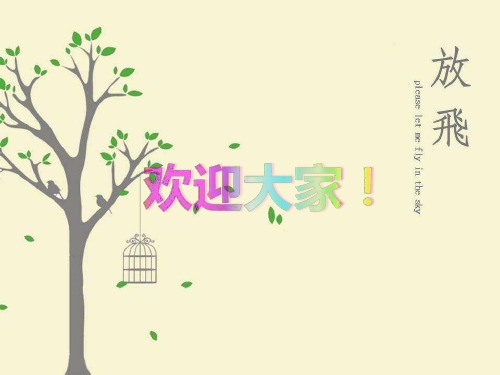
熔体凝固层
传感器与模具之间间隙0.01mm熔体与模具内壁接触后,表层迅速凝 阻止熔体进入传感器和模具之间的间
为什么要测量模腔压力
可视化功能(显示模腔压力数据、 曲线)
优化功能(优化工艺参数、成型周 期)
监测功能(监测生产过程波动、产 品质量)
控制功能(控制机械手臂、浇口阀 门等)
验证CAE软件模拟结果手段之一
实验失效基材断裂部位距离熔接线15-25mm区域,排除熔接线导 致基材开裂
注塑短射
A
B B2
B1
通过短射可以 清楚看见自浇 口处料流分为 2股(A、B), 料B 又分成两 股B1、B2。
注塑短射
B B2
A B1
欠注
熔接 线
料A和料B1交汇,料流锋面融合形成熔接线。此时料流B2产品 欠注。
注塑短射
案例一
电镀饰圈温度循环失效分析
失效
零件在温度循环实验(90℃,6h)项目中,出现基材开裂失效。
A面
B面
温度循环实验基材开裂照片
零件信息
零件名称: 电镀饰圈
材
料:ABS
表面状态:电镀
模 腔 数:一模两腔
浇口形式:斜顶式潜伏一点
进浇
原因初步分析
对前两次实验失效同批次零件用冰醋酸浸泡,失效基材开裂部 位无明显应力。
充满模腔 (保压切换降) 到大
气压后
制品开
熔体接触到传感器
时间始收缩
不同制品的模腔压力曲线
剃须刀 ABS材料
工艺参数对模腔压力曲线影响
保压压 力
保压时 间
时间 注射速度
时间
模具温 度
时间
时间
工艺参数对模腔压力曲线影响
注塑件应力对电镀质量影响以及解决方案
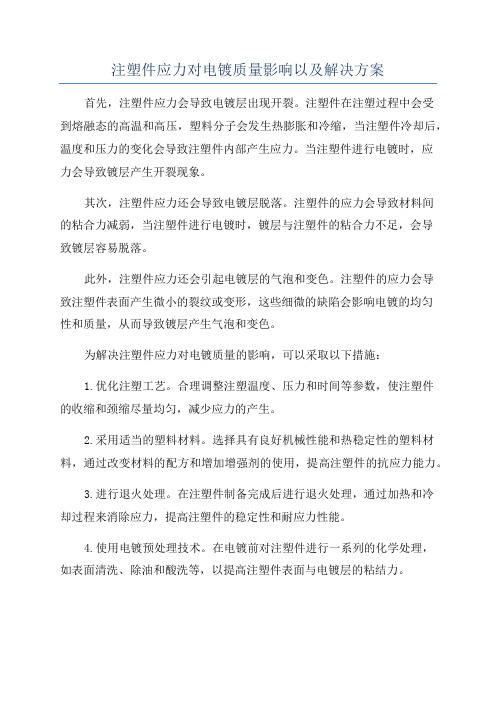
注塑件应力对电镀质量影响以及解决方案首先,注塑件应力会导致电镀层出现开裂。
注塑件在注塑过程中会受到熔融态的高温和高压,塑料分子会发生热膨胀和冷缩,当注塑件冷却后,温度和压力的变化会导致注塑件内部产生应力。
当注塑件进行电镀时,应力会导致镀层产生开裂现象。
其次,注塑件应力还会导致电镀层脱落。
注塑件的应力会导致材料间的粘合力减弱,当注塑件进行电镀时,镀层与注塑件的粘合力不足,会导致镀层容易脱落。
此外,注塑件应力还会引起电镀层的气泡和变色。
注塑件的应力会导致注塑件表面产生微小的裂纹或变形,这些细微的缺陷会影响电镀的均匀性和质量,从而导致镀层产生气泡和变色。
为解决注塑件应力对电镀质量的影响,可以采取以下措施:1.优化注塑工艺。
合理调整注塑温度、压力和时间等参数,使注塑件的收缩和颈缩尽量均匀,减少应力的产生。
2.采用适当的塑料材料。
选择具有良好机械性能和热稳定性的塑料材料,通过改变材料的配方和增加增强剂的使用,提高注塑件的抗应力能力。
3.进行退火处理。
在注塑件制备完成后进行退火处理,通过加热和冷却过程来消除应力,提高注塑件的稳定性和耐应力性能。
4.使用电镀预处理技术。
在电镀前对注塑件进行一系列的化学处理,如表面清洗、除油和酸洗等,以提高注塑件表面与电镀层的粘结力。
5.进行电镀前的表面处理。
在进行电镀之前,可以选择进行表面精加工,如抛光、喷砂等,以去除注塑件表面的缺陷和应力集中区,减少电镀层出现气泡和变色的可能性。
总之,注塑件应力会对电镀质量产生重要影响,通过优化注塑工艺、选择合适的材料、进行退火处理、使用预处理技术和表面处理等方法,可以降低注塑件应力对电镀质量的影响。
这些解决方案可以有效减少电镀层开裂、脱落、气泡和变色等问题的发生,提高电镀质量。
注塑制品常见缺陷分析及改善措施

注塑制品常见缺陷分析及改善措施注塑制品是一种常见的塑料制品,它被广泛应用于各个领域。
然而,由于注塑过程中存在很多因素的影响,注塑制品常常会出现一些缺陷。
本文将对常见的注塑制品缺陷进行分析,并提出相应的改善措施。
首先,短斑是指注塑制品表面上出现小块区域与周围区域颜色不一致的现象。
短斑的产生原因主要有以下几点:一是注塑过程中,塑料熔融不均匀,导致注塑制品的物理性能不一致;二是模具构造不合理,导致注射流道中存在死角或交叉断面,使得塑料无法均匀地填充模具。
改善措施包括调整注射温度和速度,提高熔融的均匀性;优化模具结构,避免死角和交叉断面的存在。
其次,气泡是指注塑制品中出现的气体囊泡。
气泡的产生原因主要有以下几点:一是塑料熔融时,吸附在塑料中的气体因温度升高而析出;二是模具内空气被困,形成气泡。
改善措施包括提高注料温度和压力,使气体充分溶解于塑料中;优化模具结构,改善气体的排除。
再次,翘曲是指注塑制品的形状不平整,出现弯曲或变形的现象。
翘曲的产生原因主要有以下几点:一是注塑过程中,注射压力不均匀,导致塑料流动不稳定;二是模具温度不均匀,导致塑料的冷却速度不一致。
改善措施包括提高注射速度和压力,增加注塑壁厚度的控制;优化模具温度控制系统,使模具温度均匀。
此外,色差是指注塑制品表面颜色不均匀的现象。
色差的产生原因主要有以下几点:一是注塑材料质量不均匀,导致色料分散不均匀;二是注塑过程中的温度和压力不稳定,使色料没有充分混合。
改善措施包括选用质量稳定的注塑材料;提高注塑温度和压力的稳定性;增加色料的溶解和混合时间。
最后,露胶是指注塑制品表面出现塑料外露的现象。
露胶的产生原因主要有以下几点:一是模具设计不合理,导致模具分离缺陷;二是注射流道中存在死角或结构不当,使得塑料无法完全填充模具。
改善措施包括优化模具设计,确保模具分离平整;优化注射流道结构,避免死角的存在。
综上所述,注塑制品的常见缺陷主要包括短斑、气泡、翘曲、色差和露胶等。
注塑缺陷描述及解决方案

注塑缺陷描述及解决方案注塑是一种常用的塑料加工方法,通过将熔化的塑料材料注入模具中,经过冷却固化后得到所需的塑料制品。
然而,在注塑过程中,可能会出现一些缺陷,影响产品的质量和性能。
本文将详细描述常见的注塑缺陷,并提供相应的解决方案。
一、缺陷描述1. 短射(Short Shot):指注塑过程中塑料未充满模具腔体,导致制品缺少某些部分或整体不完整。
解决方案:可能的原因包括模具温度过低、注塑速度过快、塑料材料不足等。
解决方法包括增加模具温度、调整注塑速度、增加塑料材料供给量等。
2. 翘曲(Warping):指注塑制品在冷却后产生变形,失去原本的平整形状。
解决方案:可能的原因包括模具温度不均匀、冷却时间不足、注塑压力过大等。
解决方法包括优化模具设计、增加冷却时间、减小注塑压力等。
3. 气泡(Air Traps):指注塑制品中出现气泡或空洞。
解决方案:可能的原因包括塑料材料中含有水分、注塑压力不稳定、模具排气不畅等。
解决方法包括使用干燥的塑料材料、调整注塑压力、改善模具排气系统等。
4. 热缩(Shrinkage):指注塑制品在冷却后出现尺寸缩小的现象。
解决方案:可能的原因包括模具温度过高、冷却时间不足、塑料材料收缩率不合理等。
解决方法包括降低模具温度、增加冷却时间、选择合适的塑料材料等。
5. 热裂纹(Hot Cracks):指注塑制品在冷却过程中出现裂纹。
解决方案:可能的原因包括注塑温度过高、冷却速度过快、塑料材料选择不当等。
解决方法包括降低注塑温度、控制冷却速度、选择合适的塑料材料等。
二、解决方案1. 优化模具设计:合理设计模具结构,确保充模充型均匀,避免短射、翘曲等缺陷的发生。
2. 控制注塑工艺参数:包括模具温度、注塑速度、注塑压力等。
通过调整这些参数,可以解决短射、翘曲、气泡等缺陷。
3. 选择合适的塑料材料:不同的塑料材料具有不同的性能和特点,选择合适的材料可以避免热缩、热裂纹等缺陷的发生。
4. 增加冷却时间:适当延长注塑制品的冷却时间,有助于避免翘曲、热缩等缺陷的产生。
注塑缺陷描述及解决方案

注塑缺陷描述及解决方案引言概述注塑是一种常见的塑料加工方法,但在生产过程中常常会出现一些缺陷,影响产品质量和生产效率。
本文将介绍注塑缺陷的常见描述和解决方案。
一、短射1.1 描述:短射是指注塑成型时,塑料材料未充满模具腔体,导致产品表面或内部出现缺陷。
1.2 原因:可能是注射压力不足、模具温度不稳定、料斗内塑料不足等。
1.3 解决方案:增加注射压力、调整模具温度、确保料斗内塑料充足等。
二、气泡2.1 描述:气泡是指产品表面或内部出现的气体孔洞,影响产品的外观和性能。
2.2 原因:可能是注塑过程中塑料材料中含有水分、注射速度过快、模具排气不畅等。
2.3 解决方案:使用干燥塑料材料、减慢注射速度、改进模具结构以提高排气效果等。
三、热缩3.1 描述:热缩是指产品在冷却后尺寸缩小,导致尺寸不稳定或变形。
3.2 原因:可能是模具温度不均匀、冷却时间不足、塑料材料热胀冷缩系数不匹配等。
3.3 解决方案:调整模具温度均匀性、延长冷却时间、选择合适的塑料材料等。
四、毛刺4.1 描述:毛刺是指产品表面出现的细小突起,影响产品的外观和手感。
4.2 原因:可能是模具间隙过大、注射速度过快、模具表面粗糙等。
4.3 解决方案:调整模具间隙、减慢注射速度、提高模具表面光洁度等。
五、色差5.1 描述:色差是指同一批次产品颜色不一致,影响产品的整体美观度。
5.2 原因:可能是塑料材料颜色不均匀、注射温度不稳定、色母添加不均匀等。
5.3 解决方案:使用均匀颜色的塑料材料、稳定注射温度、充分混合色母等。
结论通过对注塑缺陷的描述和解决方案的介绍,可以有效提高注塑产品的质量和生产效率。
在实际生产中,需要根据具体情况采取相应的措施,及时解决问题,确保产品质量和客户满意度。
注塑缺陷原因分析与解决方案
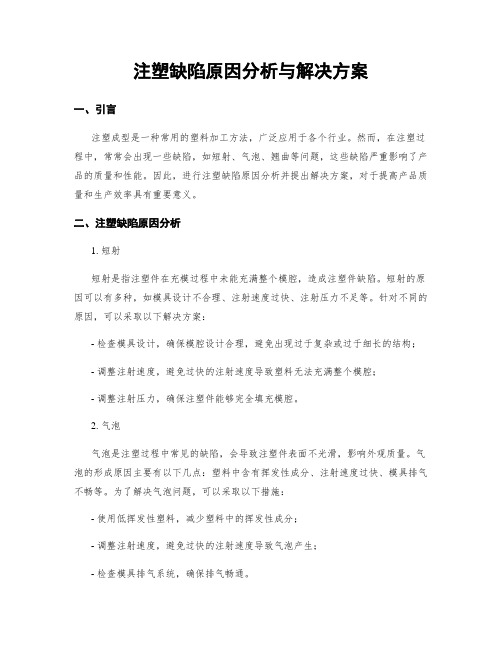
注塑缺陷原因分析与解决方案一、引言注塑成型是一种常用的塑料加工方法,广泛应用于各个行业。
然而,在注塑过程中,常常会出现一些缺陷,如短射、气泡、翘曲等问题,这些缺陷严重影响了产品的质量和性能。
因此,进行注塑缺陷原因分析并提出解决方案,对于提高产品质量和生产效率具有重要意义。
二、注塑缺陷原因分析1. 短射短射是指注塑件在充模过程中未能充满整个模腔,造成注塑件缺陷。
短射的原因可以有多种,如模具设计不合理、注射速度过快、注射压力不足等。
针对不同的原因,可以采取以下解决方案:- 检查模具设计,确保模腔设计合理,避免出现过于复杂或过于细长的结构;- 调整注射速度,避免过快的注射速度导致塑料无法充满整个模腔;- 调整注射压力,确保注塑件能够完全填充模腔。
2. 气泡气泡是注塑过程中常见的缺陷,会导致注塑件表面不光滑,影响外观质量。
气泡的形成原因主要有以下几点:塑料中含有挥发性成分、注射速度过快、模具排气不畅等。
为了解决气泡问题,可以采取以下措施:- 使用低挥发性塑料,减少塑料中的挥发性成分;- 调整注射速度,避免过快的注射速度导致气泡产生;- 检查模具排气系统,确保排气畅通。
3. 翘曲翘曲是指注塑件在冷却过程中由于内外表面温度差异引起的变形现象。
翘曲的原因主要有材料收缩率不一致、模具温度控制不当等。
为了解决翘曲问题,可以采取以下方法:- 选择具有一致收缩率的塑料材料,减少翘曲的可能性;- 控制模具温度,确保注塑件冷却均匀,避免温度差异导致翘曲。
三、解决方案的实施和效果评估在实施解决方案之前,需要进行充分的实验和测试,以验证方案的可行性和有效性。
在实施过程中,需要注意以下几点:1. 确保操作人员熟悉解决方案的具体步骤和操作要点;2. 根据实际情况,对解决方案进行适当的调整和优化;3. 对解决方案的实施效果进行评估,包括产品质量改善程度、生产效率提升等方面的指标。
通过实施解决方案,可以有效地解决注塑缺陷问题,提高产品质量和生产效率。
注塑件应力对电镀质量影响以及解决方案
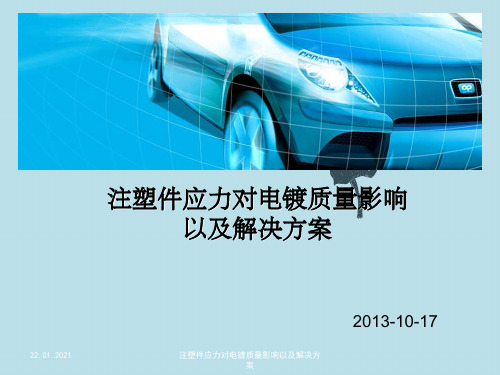
注塑件应力预防----模具设计
注塑件应力对电镀质量影响以及解决方 案
注塑件应力预防----模具设计
应力理论上讲是指分子链之间受力不均而引起的应力。
发生的地点 流动阶段
保压阶段
冷却阶段
产生的原因
应力痕
分子应力取向不均
温度应力 取向应力 收缩应力 顶出应力
注塑件应力对电镀质量影响以及解决方 案
注塑件应力预防----模具设计
成型周期 注射速度 计量时间 料垫 模腔压力积分 模腔压力最大值 熔体温度 定模板温度 动模板温度 薄壁精密制品(如各种连接器) 厚壁精密制品(齿轮等) 光学制品(镜头,导光板) 快速成型精密制品 医学制品(滴管) 包装材料(CD盒) 办公设备(尺子) 普通制品(容器,外壳,真空除尘器)
PVC制品(塑料管接头)
注塑件应力对电镀质量影响以及解决方 案
加大浇口: 改善冻结区域比较明显,浇口区域好没完全冷却,保压对改善远
注塑件应力对电镀质量影响以及解决方 案
注塑件应力预防
通过上述案例可知,Mold flow在我们公司起到着比较 重要的作用,并不是单单用一些数据能衡量他的价值。
----产品开发前期,优化产品结构 ----起到优化模具设计的作用 ----成型条件的优化,可以协助试模人员解决成型问题 ----后期进行Mold flow验证,总结经验
注塑件应力对电镀质量影响以及解决方 案
注塑件应力优化和监控
模内压力传感器使用
注塑件应力对电镀质量影响以及解决方 案
模内压力传感器使用
资料来源:KISTLER(瑞士奇石乐公司)
注塑件应力对电镀质量影响以及解决方 案
模腔压力是极其重要的成型过 程参数
1: 对制品质量影响最大的参数 / 9:对制品质量影响最小的参数
常见注塑件缺陷及解决的方法
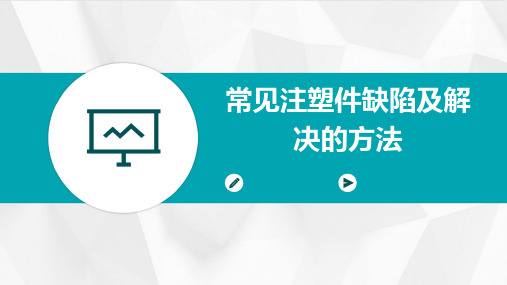
充填不足
01
总结词
充填不足是指注塑件在成型过程中未能完全填满 模具型腔,导致部分区域出现缺料或凹陷。
02
详细描述
充填不足通常是由于注射速度慢、注射压力不足、 模具温度过高或塑料流动性差等原因引起的。
缩痕
总结词
缩痕是指注塑件表面出现凹陷或收缩痕迹,影响 外观和尺寸精度。
详细描述
缩痕通常是由于塑料冷却过程中收缩率不均、模 具温度不均匀或注射压力不足等原因引起的。
常见注塑件缺陷及解 决的方法
目录
• 常见注塑件缺陷 • 注塑件缺陷原因分析 • 解决注塑件缺陷的方法 • 案例分析
01
常见注塑件缺陷
翘曲与扭曲
总结词
翘曲与扭曲是指注塑件形状发生扭曲或弯曲,不符合设 计要求。
详细描述
翘曲与扭曲通常是由于模具设计不合理、塑料收缩率差 异、注射温度和压力不适当等原因引起的。
环境条件的控制Байду номын сангаас
总结词
保持稳定的环境条件对注塑件的质量至关重 要,包括温度、湿度和清洁度等。
详细描述
确保注塑车间温度、湿度稳定,保持环境清 洁、无尘。定期对设备和环境进行清理和消 毒,防止污染和细菌滋生。同时,要关注天 气变化和季节性温差对注塑件质量的影响,
采取相应的措施进行调节。
04
案例分析
案例一:翘曲与扭曲缺陷的解决
材料选择与控制
总结词
选择合适的材料,控制材料质量是解决注塑件缺陷的重要步骤。
详细描述
根据产品使用要求和工艺特性,选择具有良好流动性和成型性的材料。同时, 要确保材料干燥、清洁,无杂质和污染。定期对材料进行质量检查,确保其性 能稳定。
模具优化与维护
注塑常见不良原因和改善对策

注塑常见不良原因和改善对策注塑是一种常见的塑料制造技术,广泛应用于各个行业中。
然而,在注塑过程中,常常会出现一些不良现象,其中包括缺陷、变形、色差等问题。
本文将介绍注塑常见的不良原因,并提出相应的改善对策。
首先,缺陷是注塑过程中最常见的不良现象之一、缺陷可能是由于模具或注塑机的设计不合理导致的,也可能是由于操作人员的疏忽或技术不足造成的。
另外,材料的选择和质量也会影响缺陷的产生。
为了改善缺陷问题,我们可以采取以下对策:1.优化模具设计:对模具进行合理的设计和优化,确保注塑产品的几何尺寸、表面质量和力学性能符合要求。
另外,采用一些特殊的模具结构,如针阀模具、气动顶出模具等,可以进一步减少缺陷的产生。
2.提升操作技术:培训操作人员,提高其注塑技术水平和操作技能,确保注塑过程的稳定性和一致性。
另外,建立严格的操作规程和品质控制流程,规范操作行为,减少人为因素的影响。
3.加强材料质量控制:选择优质的注塑原料,定期对原料进行检验和筛查,确保其符合产品要求。
另外,在注塑过程中,通过控制注射速度、温度和压力等参数,有效控制材料的熔融和流动,减少缺陷的产生。
其次,变形是另一个常见的注塑不良现象。
变形可能是由于材料的热胀冷缩引起的,也可能是由于模具设计不合理或注塑工艺参数设置不当导致的。
为了减少变形问题,我们可以采取以下对策:1.优化模具设计:改善模具的冷却系统,通过增加冷却道的数量和位置,提高材料的冷却速度,减少变形的产生。
此外,采用一些特殊的模具结构,如加厚或加固构件,可以增加产品的刚度,防止变形的发生。
2.优化注塑工艺:通过调整注射速度、温度和压力等参数,控制材料的熔融和流动,减少热胀冷缩引起的变形。
另外,选择合适的注塑工艺,如预热模具或采用热流道系统等,可以进一步减少变形的产生。
最后,色差是注塑过程中常见的外观缺陷之一、色差可能是由于原料的质量问题导致的,也可能是由于注塑工艺参数设置不当或模具表面处理不良造成的。
注塑件外观缺陷图片及原因分析与影响

料花
改善对策: 加长烘烤时间。 增大背压。 减慢射出速度。 降低料管温度。
料花产生的后果: 1,影响外观。 2,电镀后起泡。 3,损失扩大化。
精品课件
气泡
气泡产生的原因: 1,原材料烘烤不够。 2,储料背压太小。 3,射出速度太快。 4,模具排气不良。
改善对策: 加长烘烤时间,温度。 加大储料背压。 减慢射出速度。 增加排气槽。
精品课件
顶针毛边产生的原因: 1,射出压力太大。 2,射出速度太大。 3,顶针或顶针孔磨损。
面板毛边
改善对策: 减小射出压力。 减慢射出速度。 更换顶针或维修 孔
顶针毛边产生的后果: 1,包胶后TPR会渗水。 2,与其它内部件焊接,
导致内部 件报废。 3,损失扩大化。
精品课件
面盖毛边
毛边产生的原因: 1,射出速度,压力太大。 2,保压速度,压力太大。 3,模具配合不良。
精品课件
缩水产生的原因: 1,射出速度太慢。 2,射出压力太小。 3,射出料量不足。 4,射出时间太短。 5 , 冷却 时间太短。 6,保压压力,速度
太小 7,保压时间太短。
本体缩水
改善对策: 加快射出速度。 加大射出压力。 增加射出料量。 加长射出时间。 加长冷却时间。 增大保压压力, 速度。 加长保压时间。
改善对策: 减小射出速度,压力。 减小保压速度,压力。 维修模具。
毛边产生的后果: 1,与分水体焊接,容易出现假焊。 2,导致分水体报废。 3,损失扩大化。
精品课件
压伤
面板 压伤产生的原因: 1,面板表面有毛边或 杂物。 2.模具前后模残留毛边 或杂物。
改善对策: 去除面板表面的毛边 或杂物。 清理前后模残留的毛 边或杂物。
裂纹产生的后果: 1,影响外观。 2,电镀后影响性能。
注塑件缺陷的原因及其补救方法

注塑件缺陷的原因及其补救方法(1)填充不满1.注塑件缺陷的特征注塑过程不完全,因为模腔没有填满塑料或注塑过程缺少某些细节。
2.可能出现问题的原因(1).注塑速度不足。
(2).塑料短缺。
(3).螺杆在行程结束处没留下螺杆垫料。
(4).运行时间变化。
(5).射料缸温度太低。
(6).注塑压力不足。
(7).射嘴部分被封。
(8).射嘴或射料缸外的加热器不能运作。
(9).注塑时间太短。
(10).塑料贴在料斗喉壁上。
(11).注塑机容量太小(即注射重量或塑化能力)。
(12).模温太低。
(13).没有清理干净模具的防锈油。
(14).止退环损坏,熔料有倒流现象。
3.补救方法(1).增加注塑速度。
(2).检查料斗内的塑料量。
(3).检查是否正确设定了注射行程,需要的话进行更改。
(4).检查止逆阀是否磨损或出现裂缝。
(5).检查运作是否稳定。
(6).增加熔胶温度。
(7).增加背压。
(8).增加注塑速度。
(9).检查射嘴孔有没有异物或未塑化塑料。
(10).检查所有的加热器外层用安培表检验能量输出是否正确。
(11).增加螺杆向前时间。
(12).增料斗喉区的冷却量,或降低射料缸后区温度。
(13).用较大的注塑机。
(14).适当升高模温。
(15).清理干净模具内的防锈剂。
(16).检查或更换止退环。
1.注塑件缺陷的特征可以容易地在透明注塑件的“空气阱”内见到但也可出现在不透明的塑料中。
这与厚度有关,而且常因塑料收缩离开注塑件中心而引起。
2.可能出现问题的原因(1).模具未充分填充。
(2).止流阀的不正常运行。
(3).塑料未彻底干燥。
(4).预塑或注射速度过快。
(5).某些特殊材料应用特殊的设备生产。
3.补救方法(1).增加射料量。
(2).增加注塑压力。
(3).增加螺杆向前时间。
(4).降低熔融温度。
(5).降低或增加注塑速度。
(例如对非结晶体类的塑料要增加45%速度)。
(6).检查止逆阀是否裂开或无法运作。
(7).应根据塑料的特性改善干燥条件,让塑料彻底干燥。
注塑件常见品质缺陷分析及解决方法
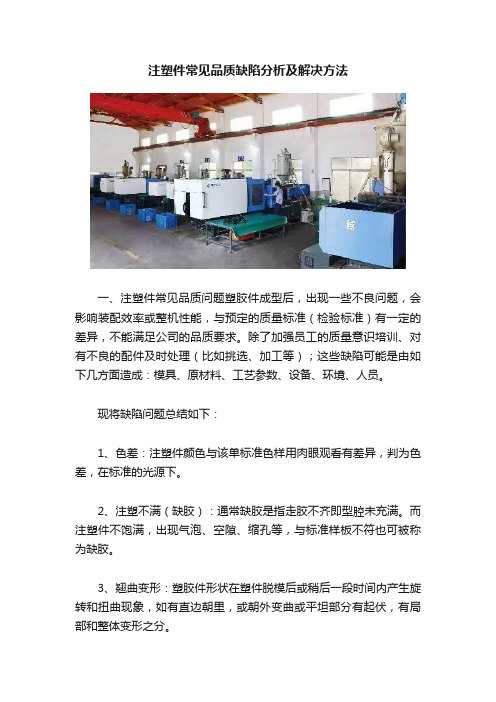
注塑件常见品质缺陷分析及解决方法一、注塑件常见品质问题塑胶件成型后,出现一些不良问题,会影响装配效率或整机性能,与预定的质量标准(检验标准)有一定的差异,不能满足公司的品质要求。
除了加强员工的质量意识培训、对有不良的配件及时处理(比如挑选、加工等);这些缺陷可能是由如下几方面造成:模具、原材料、工艺参数、设备、环境、人员。
现将缺陷问题总结如下:1、色差:注塑件颜色与该单标准色样用肉眼观看有差异,判为色差,在标准的光源下。
2、注塑不满(缺胶):通常缺胶是指走胶不齐即型腔未充满。
而注塑件不饱满,出现气泡、空隙、缩孔等,与标准样板不符也可被称为缺胶。
3、翘曲变形:塑胶件形状在塑件脱模后或稍后一段时间内产生旋转和扭曲现象,如有直边朝里,或朝外变曲或平坦部分有起伏,有局部和整体变形之分。
4、熔接痕(纹):在塑胶件表面的线状痕迹,由塑胶在模具内汇合在一起所形成,而熔体在其交汇处未完全熔合在一起,彼此不能熔为一体即产生熔接纹,多表现为一直线,由深向浅发展,此现象对外观和力学性能有一定影响。
如勾盘底部的熔接痕。
5、波纹:注塑件表面有螺旋状或云雾状的波形凹凸不平的表征现象,或透明产品的里面有波状纹,称为波纹。
6、溢边(飞边、披锋):在注塑件四周沿分型线的地方或模具密封面出现薄薄的(飞边)胶料,称为溢边。
7、银丝纹:注塑件表面的很长的、针状银白色如霜一般的细纹,开口方向沿着料流方向,在塑件未完全充满的地方,流体前端较粗糙,称为银丝纹(银纹)。
8、色泽不均(混色):注塑件表面的色泽不是均一的,有深浅和不同色相,称为混色。
9、光泽不良(暗色):注塑件表面为灰暗无光或光泽不均匀称为暗色或光泽不良。
10、脱模不良(脱模变形):与翘曲变形相似,注塑件成型后不能顺利的从模具中脱出,有变形、顶白、拉裂、拉伤等、称为脱模不良。
11、裂纹及破裂:塑胶件表面出现空隙的裂纹和由此形成的破损现象。
12、糊斑(烧焦):在塑件的表面或内部出现许多暗黑色的条纹或黑点,称为糊斑或烧焦。
注塑缺陷描述及解决方案
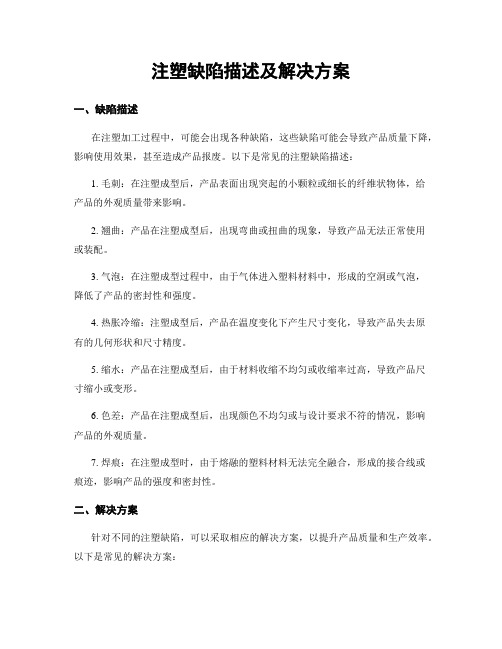
注塑缺陷描述及解决方案一、缺陷描述在注塑加工过程中,可能会出现各种缺陷,这些缺陷可能会导致产品质量下降,影响使用效果,甚至造成产品报废。
以下是常见的注塑缺陷描述:1. 毛刺:在注塑成型后,产品表面出现突起的小颗粒或细长的纤维状物体,给产品的外观质量带来影响。
2. 翘曲:产品在注塑成型后,出现弯曲或扭曲的现象,导致产品无法正常使用或装配。
3. 气泡:在注塑成型过程中,由于气体进入塑料材料中,形成的空洞或气泡,降低了产品的密封性和强度。
4. 热胀冷缩:注塑成型后,产品在温度变化下产生尺寸变化,导致产品失去原有的几何形状和尺寸精度。
5. 缩水:产品在注塑成型后,由于材料收缩不均匀或收缩率过高,导致产品尺寸缩小或变形。
6. 色差:产品在注塑成型后,出现颜色不均匀或与设计要求不符的情况,影响产品的外观质量。
7. 焊痕:在注塑成型时,由于熔融的塑料材料无法完全融合,形成的接合线或痕迹,影响产品的强度和密封性。
二、解决方案针对不同的注塑缺陷,可以采取相应的解决方案,以提升产品质量和生产效率。
以下是常见的解决方案:1. 毛刺:加强模具的冷却系统,控制注塑过程中的温度和冷却时间,避免塑料材料熔融不充分或过热,导致毛刺的产生。
2. 翘曲:优化模具结构,增加产品的支撑结构或加强产品的刚性,减少翘曲的可能性。
3. 气泡:改善塑料材料的干燥处理,减少材料中的水分含量;调整注塑工艺参数,控制注塑过程中的压力和速度,避免气泡的产生。
4. 热胀冷缩:选择合适的塑料材料,考虑其热胀冷缩系数;调整注塑工艺参数,控制注塑过程中的温度和冷却时间,减少热胀冷缩的影响。
5. 缩水:调整模具结构,增加产品的壁厚或改变产品的设计,以减少塑料材料的收缩率;优化注塑工艺参数,控制注塑过程中的温度和压力,减少缩水的发生。
6. 色差:选择合适的颜料和添加剂,确保颜色的均匀分布;优化注塑工艺参数,控制注塑过程中的温度和压力,提高产品的色彩一致性。
7. 焊痕:优化模具结构,减少注塑过程中的焊接线;调整注塑工艺参数,控制注塑过程中的温度和压力,提高熔融塑料的融合性。
注塑模具培训电镀不良对策

10 錫鉛重熔:指鍍層表面有如山丘平原狀(似起泡,但密著良好),只有錫鉛鍍層會發生. 可能發生的原因: 改善對策: 1. 錫鉛陰极過熱(電壓太高),導致錫 1. 降低電壓,并了解為何浴電壓過高,再行修正電 鉛層重熔. 鍍條件. 2. 烤箱溫度過高,且烘烤時間過長,導 致錫鉛層重熔. 11. 2. 降低烤箱溫度,并檢查溫控系統.
件發熱,造成鍍層氧化. 9. 底層電鍍不良(如燒焦),造成下一 層剝落. 10. 嚴重燒焦所形成剝落. 4. 露銅:可清楚看見銅色或黃黑色于低電流處 可能發生的原因: 改善對策: 1.前處理不良,油脂,氧化物,异物尚 1.加強前處理或降低產速. 未除去,鍍層無法析出. 1. 重新計算電鍍條件. 1. 操作電流密度太低,導致低電流 2. 處理藥水,去除過多光澤劑或更新. 區鍍層無法析出. 3. 檢查電鍍流程. 2. 鎳光澤劑過量,導致低電流區鍍 5.調整電鍍位置. 層無法析出. 3. 嚴重刮傷導致露銅 5.未鍍到. 5. 刮傷:指水平線條狀,一般在錫鉛鍍層經較容易發生 可能發生的原因: 改善對策: 1. 素材本身在沖床時,即造成刮傷. 1. 停止生產,待与客戶聯系. 2. 被電鍍設備中之金屬治具刮傷, 2. 檢查電鍍流程,适時調整設備及治具. 如陰极頭,烤箱定位器,導輪等. 3. 停止生產,立即去除晶物. 3. 被電鍍結晶物刮傷. 6.變形(刮歪):指端子形狀已經偏离原有尺寸或位置. 可能發生的原因: 改善對策: 1. 素材本原在沖床時,或運輸時,即 1. 停止生產,待与客戶聯系. 造成變形. 2. 檢查電鍍流程,适時調整設備及治具. 2. 被電鍍設備,治具刮歪(如吹气,定 3. 停止生產,适時調整盤子. 位器,震蕩器,槽口,回轉輪等). 修正傳動輪或變更傳動方式. 3. 盤子過小或卷繞不良,導致出入 料時刮歪. 4. 傳動輪輾歪. 7.壓傷:指不規則形狀之凹洞. 可能發生的原因: 1. 素材本身在沖床加工時,已經壓 傷,鍍層無法覆蓋平整. 2. 金屬傳動輪松動或故障不良,造 成壓合時傷到 可能發生的原因: 1. 前處理不良. 改善對策: 1. 停止生產,待与客戶聯系. 2. 檢查傳動机制,或更換備品.
- 1、下载文档前请自行甄别文档内容的完整性,平台不提供额外的编辑、内容补充、找答案等附加服务。
- 2、"仅部分预览"的文档,不可在线预览部分如存在完整性等问题,可反馈申请退款(可完整预览的文档不适用该条件!)。
- 3、如文档侵犯您的权益,请联系客服反馈,我们会尽快为您处理(人工客服工作时间:9:00-18:30)。
奚晓寅
注塑件常见缺陷目录
• • • • • • • • • • • • 一、缩印 二、溢边 三、缺料 四、翘曲变形 五、白印(顶高) 六、射纹(气斑) 七、银纹 八、熔接痕(熔接线) 九、烧焦 十、拉毛(拉伤) 十一、黑点 十二、颜色不均
一、缩印
缺陷描述 产品表面凹坑现象。多发生浇口部位与产品两端头部, 背面有加强筋处也易发生此类缺陷,电镀后缩印会更加明显, 易发生批量不良。
九、烧焦
缺陷描述 机械、模具或成型条件不同的原因引起的烧伤,产品表 面成黑色状,一般存在于熔料汇合处。电镀后产品该位置影 响电镀试验。
缺陷原因 料筒过热,使树脂高温分解、热流道温控故障、模具排 气不良等。 解决方案 适当降低料筒及喷嘴温度,适当降低模具温度,降低注 塑压力及速度,增设排气槽,检修热流道。
缺陷原因 注射压力大于合模力使模具密合不良时容易产生溢料飞 边。模具分型面未密着贴合,模具平行度不良,锁模力不足, 材料流动性快,注射速度太快,注射时间太长,注射压力太 高等。
解决方案 必须先从排除模具故障着手,然后再调整工艺如调整锁 模力,减小注塑压力、注塑速度等。
三、不足(缺料)
缺陷描述 制品不完整,模腔未完全充满。主要发生在熔体流动的 末端或薄壁面的地方。 缺陷原因 物料在未充满型腔之前即已固化造成不足,浇注系统设 计不合理,模具排气不良,模具温度太低,料筒温度太低, 注射压力或保压压力不足,注射速度太慢,注塑时间太短、 塑料的流动性差,储料偏少等。 解决方案 扩大流道截面和浇口面积,增设排气槽,提高模具、料 筒温度,提高注射压力、速度或保压时间,增加注塑时间, 增加计量等。
十、拉毛(拉伤)
缺陷描述 制品与模具发生摩擦,出现划痕的现象,多发生在有顶 出机构的部位,电镀后该位置容易出现毛刺和结瘤等批量不 良。
缺陷原因 模具型腔表面粗糙,脱模斜度不足或动、定模板间平行 度差,制品的成型收缩率比预期的小。
解决方案 提高模腔及流道的表面光洁度,设计和制作模具时,应 保证足够的脱模斜度,适当降低注塑压力、注塑时间等。
十二、颜色不均
缺陷描述 制品表面颜色不一样,发生在浇口附近和远处,电镀后 容易影响电镀试验性能。 缺陷原因 当成型温度过高,或料筒的残留时间太长,也容易造成 塑料的热降解,导致颜色不均,热流道温控故障等。
解决方案 是降低螺杆速度,调整料筒温度和残留时间,增加背压 等,检查热流道工作是否正常。 。
谢谢!
四、翘曲变形
缺陷描述 制品的形状在制品脱模后或稍后一段时间内产生旋转或 扭曲现象,主要发生在壁薄不均匀无加强筋处。电镀后变形 无法矫正,易发生批量不良。 缺陷原因 脱模的时候,按不同的制品形状,应力往往会造成不同 程度的变形。模具设计前未做预变形处理。
解决方案 扩大流道截面和浇口面积,增设排气槽,提高模具、料 筒温度,提高注射压力、速度或保压时间,增加注塑时间, 增加计量等。
缺陷原因 塑料凝结太慢,有效保压时间太短,保压压力太小而模 具中流动阻力太大、模具表面温度不均匀、注射速度欠佳、 注射压力欠佳等。
解决方案 增加注射压力及注射速度,调整料筒温度,延长注射和 保压时间,增加注射缓冲量。
二、溢边(飞边)
缺陷描述 凹处周围,沿分型线的地方或模具密封面出现薄薄的飞 边,多发生在制品的分型面处,电镀后会更加严重,如果是 在尖端处电镀后易发生结瘤和烧焦等批量不良。
十一、黑点
缺陷描述 制品中混入不同于制品原材料的物质,电镀后表面容易 产生凹坑及毛刺。 缺陷原因 包装、运输、预干燥等处理过程中原料混入杂质或不同 品级的原料混用,或注塑过程中,注塑机料桶和注射柱塞中 混有杂质,注塑机上的吸料防尘装置脏,未能定期清洗。 解决方案 筛除原料中的异物,选用颗粒均匀的原料。在预处理和 成型过程中,要防止粉尘和其他异物杂质从料斗、料桶及模 具处混入熔料中,用白料过滤料筒,定期清洗吸料防尘装置 。
六、射纹(气斑)
缺陷描述 产品浇口处出现的斑纹和混浊。经常发生在当熔料进入 到模腔内,流体前端停止发展的方向,电镀不易遮盖易发生 批量不良。 缺陷原因 热的熔料接触到相对较冷的模腔表面后冷却,在充模过 程中不能同随后的熔料紧密结合在一起。 解决方案 增大浇口直径,浇口重新定位,浇口与模壁之间采用圆 弧过渡,降低注射速度或采用多级注射速度,提高模具温度 ,调整料筒的温度,调整背压等。
五、白印(顶高)
缺陷描述 塑件表面应外力作用而产生白化的现象。多发生部位在 塑件的顶出位置,电镀后有凹凸感。 缺陷原因 脱模力太高或顶出杆的表面相对较小,此处的表面压力 会很高,发生变形最终造成顶出部位泛白。
解决方案 是降低注塑压力、降低保压压力、缩短保压时间、将保 压切换提前、延长冷却时间,增加脱模斜度、对脱模方向上 模具进行抛光等。
七、银纹
缺陷描述 制品表面的水迹纹,银丝的开口方向沿着材料的流动方 向,在制品完全充满的地方,流体前端很粗糙,电镀后容易 起泡。 缺陷原因 材料的吸湿性及材料在料筒内滞流时间过长。 解决方案 材料足够的预烘干,缩短材料在料筒内的时间。
八、熔接痕
缺陷描述 熔料的分流汇合处,由于汇合性能不良,产生一条明显 的痕迹,熔接缝的位置在物料的流动方向上,发生于采用多 浇口的制品及制品的封闭特征处,电镀后较深的熔接痕无法 遮盖,易发生批量不良。 缺陷原因 流体前端未均匀熔合产生弱光点,一般工艺调整不可能 完全避免熔接痕,只能降低其亮度或移到不显眼或完全看不 见的地方。 解决方案 适当提高料筒及喷嘴温度,适当提高模具温度,提高注 塑压力及速度,增设排气槽,采用分流少的浇口形式并合理 选择浇口的位置。