镀锌层精磨后腐蚀问题研究_邓建青
对镀锌层无铬钝化技术的研究进展探讨

对镀锌层无铬钝化技术的研究进展探讨文章首先对无铬钝化类别进行总结和分析,对无铬钝化技术的应用进行研究,以期对镀锌层无铬钝化技术的快速推广,起到一定的促进作用。
标签:镀锌层;无铬钝化;研究;进展1 概述现阶段,利用铬酸盐钝化的方式对镀锌产品进行处理,使得镀层具备一定的耐腐蚀性能,然而铬酸盐的使用不可避免对人体及自然环境产生严重的影响。
世界范围内已经开始限制六价铬产品的应用。
基于绿色环保的理念,对无铬钝化工艺技术进行研发,逐渐成为镀锌层钝化技术的重要方向。
基于此,文章对镀锌层无铬钝化技术进行研究,不足之处,敬请指正。
2 无铬钝化类别2.1 无机钝化2.1.1 钼酸盐钝化镀锌层进行钼酸盐钝化处理,会在其表面形成钼酸盐钝化膜。
因为钼酸盐具有较低的毒性,因此被看作是铬酸盐钝化处理的替代方式。
现阶段,对其开展的研究项目较多,适当添加一些有机物和无机物添加剂,利用复合获取一定的协同效应,从而促进钝化膜的耐腐蚀性能的提升。
目前来说,这种方式和铬酸盐钝化膜相比效果较差,而且钼酸盐的价格昂贵,因此还无法应用到大规模生产中。
2.1.2 钨酸盐钝化钨酸盐在发挥金属缓蚀剂的作用时,较为类似于钼酸盐,钨酸盐钝化处理的方式得到的钝化膜耐腐蚀性能较低,而且钨酸盐的价格偏高,所以针对钨酸盐钝化的应用较少。
2.1.3 硅酸盐钝化硅酸盐钝化处理方式不仅处理成本低,而且钝化液具有良好的稳定性,使用起来也很方便,毒性较小,然而却存在一个致命问题,就是耐腐蚀性能比较差。
为促进钝化膜耐腐蚀性能的提升,必须要在钝化液中添加有机促进剂,比如说硫脲及水溶性阴离子型丙烯酸胺等化合物。
现阶段,针对硅酸盐钝化应用也比较少。
2.1.4 钛盐钝化为达到环境保护有关标准及要求,一些地区电镀厂开始采用过钛盐钝化工艺。
钝化液的具体成分包括硫酸氧钛、硝酸、磷酸、单宁酸等,采用羟基喹啉作为稳定剂,pH 大约是1 到1.5的范围,常温下操作,具有良好的耐腐蚀性能。
2.2 有机钝化2.2.1 有机硅烷钝化硅烷分子能够在醇、水溶液中发生水解而形成一定数量的硅烷醇基团(SiOH),基团在硅烷与金属的界面上发生化学反应,而生成金属硅氧烷键(SiOMe),未参与化学反应的硅烷醇基团形成胶联的硅烷膜结构SiOSi网络结构,以上结构一方面能够有效地避免侵蚀性介质侵入其中,另一方面可以形成稳定的膜层,此特征使得有机硅烷钝化处理成为近些年研究的重要方向。
某热镀锌车间腐蚀后鉴定分析与加固措施

3 构件 的可 靠性 鉴定
根据 中华人 民共 和国国家标准 《 工业 厂房可 靠性鉴 定标 准) BI 4 9 ( ) J 4 — 9 以下 简称 《 G 1 标准》 , )对所有砼 构件及 钢构件 进行鉴定 。除按《 准》中要 求对 构件 进行 检测外 , 用 “ 标 还 钢 筋锈蚀测量仪 ” 无损 伤测 量砼 内部 钢筋锈 蚀 率 , 并用 化学 测
定法 , 出服役砼 的 P 测 H值。
. ~
2 腐 蚀情 况调 查及 腐蚀 机理 分析
( ) 试 过 程 1测
首先对厂房进 行初 级调查 , 确定南跨 厂房 的部分 1 m预 8 应力屋架腐蚀严重 , 已不安全 , 需要及时加 固。后对热镀锌 车 间所有构件进行详 细测试 , 用有 G Y—I 并 X A型 “ 钢筋 锈蚀测 量仪” 对一些 构件 进行无损伤 内部钢 筋锈蚀 率测量 。最 后又 对车间构件腐蚀情况进 行补充 调研 和复测 , 并进 行各 构件可 靠 性等级 的确定 。 () 2 腐蚀源及腐蚀机理 热浸镀锌工艺 中需要 对镀锌 铁件 酸洗 除锈 , 酸洗池 中 的 盐 酸气 雾 向厂房顶部扩散 , 因此酸洗 池上部 的屋架 和支 撑首 先受 到腐蚀。虽然砼的碱性 ( H值为 1 4 可使钢筋 表面 P 2—1 ) 形成一 层致密的固相钝化 膜保护 钢筋 , 但是 盐酸气 雾 中含大 量氯离 子( l ) 由于 c 一 c一 , l 半径很小 ( . 1 m) 其穿 透能力极 18 P , 强, 可穿过砼保护层破坏钢 筋的钝化膜 , 使钢筋 氧化并产生铁 锈 。同时盐 酸气 雾也使 砼 的碱性 降低 ( H值下 降 ) 失去对 P , 钢筋 的碱性保护 。铁 锈为 F :3F 多种 氧化铁组成 , e0 、eo 等 其 体积为原金属体 积的 2—3倍 。由于铁锈 的体 积膨胀 , 把砼保
提高热镀锌镀层质量的研究
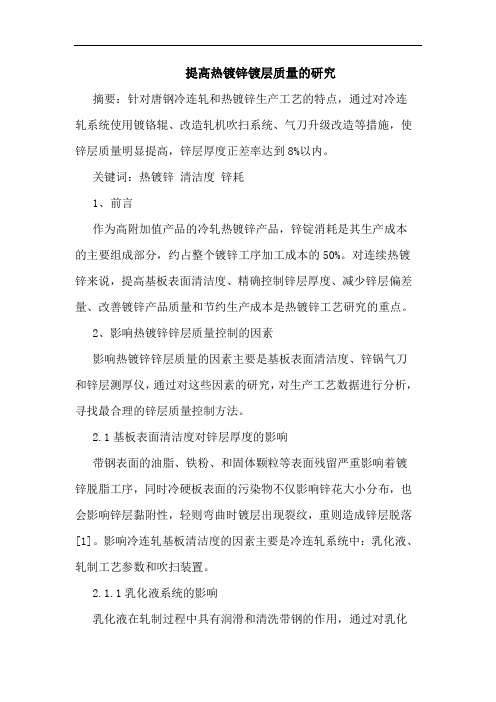
提高热镀锌镀层质量的研究摘要:针对唐钢冷连轧和热镀锌生产工艺的特点,通过对冷连轧系统使用镀铬辊、改造轧机吹扫系统、气刀升级改造等措施,使锌层质量明显提高,锌层厚度正差率达到8%以内。
关键词:热镀锌清洁度锌耗1、前言作为高附加值产品的冷轧热镀锌产品,锌锭消耗是其生产成本的主要组成部分,约占整个镀锌工序加工成本的50%。
对连续热镀锌来说,提高基板表面清洁度、精确控制锌层厚度、减少锌层偏差量、改善镀锌产品质量和节约生产成本是热镀锌工艺研究的重点。
2、影响热镀锌锌层质量控制的因素影响热镀锌锌层质量的因素主要是基板表面清洁度、锌锅气刀和锌层测厚仪,通过对这些因素的研究,对生产工艺数据进行分析,寻找最合理的锌层质量控制方法。
2.1基板表面清洁度对锌层厚度的影响带钢表面的油脂、铁粉、和固体颗粒等表面残留严重影响着镀锌脱脂工序,同时冷硬板表面的污染物不仅影响锌花大小分布,也会影响锌层黏附性,轻则弯曲时镀层出现裂纹,重则造成锌层脱落[1]。
影响冷连轧基板清洁度的因素主要是冷连轧系统中:乳化液、轧制工艺参数和吹扫装置。
2.1.1乳化液系统的影响乳化液在轧制过程中具有润滑和清洗带钢的作用,通过对乳化液温度和浓度变化的控制,来减少冷连轧带钢表面残留物乳化液的使用温度过低不利于破乳油膜的形成,造成乳化液润滑效果降低,钢板的铁粉污染程度增加;温度过高易使乳化液颗粒长大,造成因乳化液不稳定而使油耗上升,并且使过多的油脂附集在钢板表面,增加钢板的油脂污染程度。
乳化液浓度是指乳化液中轧制油的含量,是润滑重要的因素之一。
若乳化液浓度太低,带钢与轧辊之间处于润滑不足状态,产生过量磨损,钢板表面残铁过高,会增加带钢表面吸附面积,还会导致带钢表面热划伤,以及润滑不良使冷轧带钢发黑等缺陷;乳化液浓度过高,不利于轧辊冷却并且轧后板带含油多,带钢表面清洁度下降,不利于下道工序生产,并且易出现轧辊打滑。
2.1.2轧制工艺参数的影响(1)轧制速度的影响:轧制速度越快,带钢温度越高,油的粘度越小,容易被出口吹扫装置吹走,乳化液挥发越快,带钢表面清洁度越高。
热镀锌线中轴套衬瓦的锌腐蚀–磨损交互行为研究

表面技术第52卷第6期热镀锌线中轴套衬瓦的锌腐蚀–磨损交互行为研究饶思贤1,2,左竞成1,黄国辉1,石亚飞1,王孝义1(1.安徽工业大学 机械工程学院 特殊服役环境的智能装备制造国际科技合作基地,安徽 马鞍山 243032;2.合肥通用机械研究院,合肥 230031)摘要:目的明确轴套、衬瓦间锌腐蚀–磨损的交互作用机制对合理选材、有效控制磨损的重要意义。
方法使用陶瓷纤维马弗炉将纯锌粒加热到460 ℃后,对轴套、衬瓦试样进行液锌浸蚀试验,利用Ansys模拟出三辊轴套、衬瓦间的接触应力,采用多功能磨损试验机测出试样的摩擦系数以及磨损量,使用三维视频显微镜观察试样的三维形貌,使用扫描电镜对试样进行表面形貌观察和微观组织分析。
结果当316L不锈钢试样浸入高温锌液1 h后,可以看到基体外表面出现多个合金层,总厚度达600~800 μm。
在带钢张力20 kN,矫正辊插入量10 mm的常见工况下,沉没辊轴套、衬瓦间接触应力可达65.14 MPa,稳定辊轴套、衬瓦间接触应力可达17.79 MPa,矫正辊轴套、衬瓦间接触应力可达26.69 MPa。
无渗锌处理,垂直施加载荷为81 N 时,在900 s以后摩擦系数稳定到0.03;当载荷为154.5 N时,摩擦系数维持在较低水平。
渗锌处理时,无论载荷是81 N还是154.5 N,摩擦系数均在0.1上下波动。
渗锌处理并加入硬质锌渣时,摩擦系数进一步的升高,波动幅度更大。
无论施加的垂直施加载荷是81 N还是154.5 N,磨损量在无渗锌处理、渗锌处理、渗锌处理并加入硬质锌渣3种工况下依次递增。
结论 316L不锈钢经高温渗锌腐蚀形成的渗锌层、硬质锌渣显著提升了轴套、衬瓦间的摩擦系数以及磨损量,使表面低硬度合金层快速磨损。
磨损磨去合金层,使新鲜基体持续暴露,促进了高温锌腐蚀的持续进行,不断形成新的腐蚀层,又不断被磨损掉,两者间的交互协同使得不锈钢轴套磨损速率提高而迅速失效。
关键词:热镀锌线;沉没辊系统;轴套衬瓦;锌腐蚀;混合磨损失效中图分类号:TG113 文献标识码:A 文章编号:1001-3660(2023)06-0266-10DOI:10.16490/ki.issn.1001-3660.2023.06.023Interactions between Zinc Corrosion and Abrasion of Sleeves andBushings in Continuous Hot-Dip Galvanizing LineRAO Si-xian1,2, ZUO Jing-cheng1, HUANG Guo-hui1, SHI Ya-fei1, WANG Xiao-yi1(1. China International Science and Technology Cooperation Base on Intelligent Equipment Manufacturing in Special Service收稿日期:2022–05–31;修订日期:2022–10–25Received:2022-05-31;Revised:2022-10-25基金项目:安徽省教育厅重大自然科学研究项目(KJ2016SD09);安徽省自然科学基金(1908085ME148);特殊服役环境的智能装备制造国际科技合作基地开放基金(ISTC2021KF02)Fund:Major Natural Science Foundation of Anhui Provincial Education Department (KJ2016SD09); Anhui Provincial Natural Science Foundation (1908085ME148); The Open Project of China International Science and Technology Cooperation Base on Intelligent Equipment Manufacturing in Special Service Environment (ISTC2021KF02)作者简介:饶思贤(1978—),男,博士,教授,主要研究方向为金属的腐蚀与失效。
镀锌层军绿色钝化工艺研究

酸, 工业级;p 0, O一1 工业级; 铬配, 镀级; 电 锌粉, 电 镀级; 添加剂X 0B 自 重铬酸钾, Y一 , 配; 3 化学纯.
12 实验仪器 . 电子天平( 湘仪电子天平厂)D 一 9 型恒电 ;J 2 S 2 位仪( 上海雷磁有限公司)ZA一 刀1V硅整流 ;D 2 2 0
2 0一3 0
形成的 钝化膜呈军绿色, 色泽鲜艳, 装 饰性好, 附着力好 形成的钝化膜呈军绿带彩虹色, 色泽不 太均匀, 装饰效果欠佳
由 钝化时间加长, 表6 可知: 钝化膜的颜色会加 深, 附着力也会随之而提高. 但时间过长, 钝化膜又 会发生溶解, 造成钝化膜的厚度减小, 色泽不均匀; 时间过短, 钝化膜薄, 光泽差, 耐蚀性较差, 因此钝化 时间 应控制在6 一8 5 0 1 左右. 0
较差. 224 添加荆 X 0 B .. Y一 3
实验现象与结果
形成的钝化膜呈淡绿色, 色泽较暗淡, 结合力较
差
2 5一3 5
形成的钝化膜呈军绿色, 色泽光亮鲜艳, 装饰性 好, 附着力好 形成的钝化膜呈军绿色, 色泽不均匀, 装饰性欠 佳, 附着力差
D 4 一5 0
由表 1 铬醉含量控制在 2 一 扩L为 可知: 5 3 5 宜. 铬醉浓度高, 反应速度快, 生成的钝化膜厚, 光亮 度好, 色泽均匀. 但浓度过高, 会降低镀层厚度, 因为 铬配浓度增加, 会加速锌的溶解; 当铬配浓度过低 时, 反应速度会减慢, 军绿色 挽化; 格酸盐钝化; 耐独性
中图分类号: 1 . Q 4 T 74
文献标识码: A
文章编号: 61 1 x 20) 一 7 一3 1 一 1 (070 0 8 0 7 9 2( )
0 前
言
1 实验方法
镀锌金属构件腐蚀原因分析及解决措施
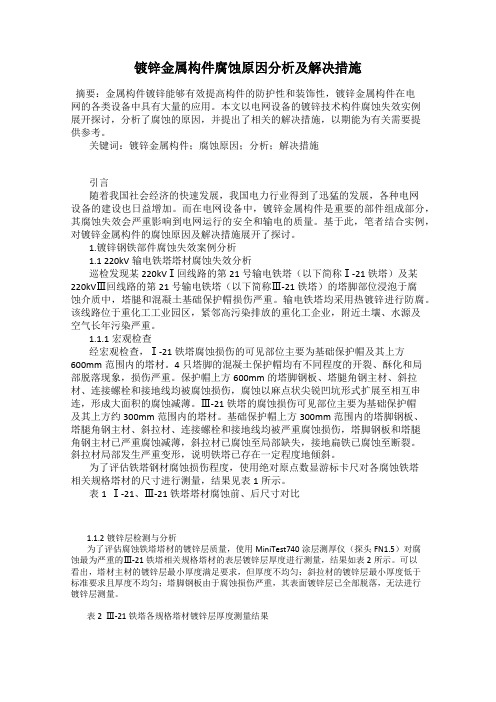
镀锌金属构件腐蚀原因分析及解决措施摘要:金属构件镀锌能够有效提高构件的防护性和装饰性,镀锌金属构件在电网的各类设备中具有大量的应用。
本文以电网设备的镀锌技术构件腐蚀失效实例展开探讨,分析了腐蚀的原因,并提出了相关的解决措施,以期能为有关需要提供参考。
关键词:镀锌金属构件;腐蚀原因;分析;解决措施引言随着我国社会经济的快速发展,我国电力行业得到了迅猛的发展,各种电网设备的建设也日益增加。
而在电网设备中,镀锌金属构件是重要的部件组成部分,其腐蚀失效会严重影响到电网运行的安全和输电的质量。
基于此,笔者结合实例,对镀锌金属构件的腐蚀原因及解决措施展开了探讨。
1.镀锌钢铁部件腐蚀失效案例分析1.1 220kV输电铁塔塔材腐蚀失效分析巡检发现某220kVⅠ回线路的第21号输电铁塔(以下简称Ⅰ-21铁塔)及某220kVⅢ回线路的第21号输电铁塔(以下简称Ⅲ-21铁塔)的塔脚部位浸泡于腐蚀介质中,塔腿和混凝土基础保护帽损伤严重。
输电铁塔均采用热镀锌进行防腐。
该线路位于重化工工业园区,紧邻高污染排放的重化工企业,附近土壤、水源及空气长年污染严重。
1.1.1宏观检查经宏观检查,Ⅰ-21铁塔腐蚀损伤的可见部位主要为基础保护帽及其上方600mm范围内的塔材。
4只塔脚的混凝土保护帽均有不同程度的开裂、酥化和局部脱落现象,损伤严重。
保护帽上方600mm的塔脚钢板、塔腿角钢主材、斜拉材、连接螺栓和接地线均被腐蚀损伤,腐蚀以麻点状尖锐凹坑形式扩展至相互串连,形成大面积的腐蚀减薄。
Ⅲ-21铁塔的腐蚀损伤可见部位主要为基础保护帽及其上方约300mm范围内的塔材。
基础保护帽上方300mm范围内的塔脚钢板、塔腿角钢主材、斜拉材、连接螺栓和接地线均被严重腐蚀损伤,塔脚钢板和塔腿角钢主材已严重腐蚀减薄,斜拉材已腐蚀至局部缺失,接地扁铁已腐蚀至断裂。
斜拉材局部发生严重变形,说明铁塔已存在一定程度地倾斜。
为了评估铁塔钢材腐蚀损伤程度,使用绝对原点数显游标卡尺对各腐蚀铁塔相关规格塔材的尺寸进行测量,结果见表1所示。
不同材料在锌液中腐蚀磨损机理的研究

( h nc u nv i cnl y 10 2 ) ( in n6 nd avnz gE u , . C . Ld 30 3 ) C a gh nU i syo T h o g 30 2 et f e o Taf og aG l in q i ̄ t o , t. 0 10 i a i p
1 2 试验 材料 .
S N 陶瓷材料 的热膨胀 系数小 , i 弯曲强 度较
图1 所示 ) 拟实 际 接 触 方式 , 试样 为加 载 端 , 模 块 固 定不动 ; 圆环试样利用调速 电机带动动态传感器进 行调 速 , 圆环 试 样 的 轴 心转 动 。 动态 传 感 器 记 录 绕 摩 擦 扭 矩 , 验 装 置 如 图 2所 示 。试 验 中压 力 为 试
图 1 块 一 式摩 擦 方 式 环
v n zn y dp i g u d r o t o od efc f i c l u d c ro i n a d a iig b i p n n e g w f l f to n i i o r so n e z q
a r s n,s l ci gH1 te ,i n b s l y o at a e aly, l o i i gmae as a s r S 4, o e c r so n b ai o e e t 3 se l r a ea l ,c b l b s l n o o o Cr2 b rdn t r l s o t i N wh s or in a d i o
维普资讯
第3卷 2
V0. 132
第4 期
№. 4
金
Se l te
属
i r e
制
提高热镀锌镀层质量的研究

2 . 2锌液 控制参数和气 刀对 锌层质量 的 影 响 带钢 的热 镀锌层在锌锅 中完成 ,因此 , 锌锅气 刀的工艺对所得镀 锌产品的质量产 生 直接 的影响。锌锅 的作用 是加热和 “ 搅拌 ” 锌液 。均匀恒定锌液温度 ,可减少锌渣 的产 生量 ,避免锌渣夹杂在镀 层中造成锌层挠性
2 、 影 响热镀锌锌层质量控制的因素
影响热镀锌 锌层质量 的因素主要是基 板 表面清洁度 、锌锅气刀和锌层 测厚仪 ,通过 对这些 因素 的研究 ,对 生产 工艺数据进行分 析,寻找最合理 的锌层质量控制方法。 2 . 1基板表面 清洁度对锌层厚度的影晌 带钢表面 的油脂 、铁粉 、和固体颗粒 等 表面残 留严重影 响着镀 锌脱脂工序 ,同时冷 硬 板 表 面 的 污 染 物 不 仅 影 响 锌 花 大 小分 布 , 也会影 响锌层 黏 附性 ,轻则弯 曲时镀层 出现 裂纹,重则造成锌层脱落口 ] 。影响冷连轧基板 清洁度的因素主要是冷 连轧系 统中:乳化液、 轧制工艺参数和吹扫装 置。 2 . 1 . 1 乳化液系统的影响 乳化 液在轧制过程 中具有润滑 和清 洗带 钢 的作 用,通过对乳化 液温度和浓度变 化的 控制,来减少冷连轧带钢表面残 留物 乳 化液的使用温 度过低不利 于破乳油膜 的形成,造成乳 化液润滑效果 降低 ,钢板的 铁粉 污染程度增 加:温度过高易使 乳化液颗 粒长大 ,造成因乳化液不稳定而 使油耗上升 , 并且使过多的油脂 附集在钢板表面 ,增加钢 板 的油脂污染程度。 乳化 液 浓 度是 指 乳化 液 中 轧制 油 的含 量,是润滑重 要的因素之一 。若 乳化液浓度 太 低,带钢与 轧辊之间处于润滑 不足状态 , 产 生过量磨损 ,钢板表面残铁过 高 ,会增加 带钢表面吸 附面积,还会导致带钢 表面热划 伤 ,以及润滑 不 良使冷轧带钢 发黑等缺 陷; 乳化液浓度过 高,不利于 轧辊冷却并且轧 后 板带含油 多,带钢表面清 洁度下降 ,不利 于 下道工序 生产 ,并且易 出现轧辊打滑 。 2 . 1 . 2轧制工艺参数 的影响 ( 1 )轧制速度 的影 响:轧制速度越快, 带钢温度越高 ,油的粘度越 小,容 易被 出口 吹扫装置 吹走 ,乳化液挥 发越快 ,带钢表 面 清洁度越 高。反之,带钢表面残留就多。 ( 2 )轧辊粗糙度 的影 响:镀锌用原板表 面粗糙度 愈高 ,锌层 的附着 性也愈好 ,提 高 了涂镀质量 ,使镀层牢 固、均匀,美观 。但 是 ,轧 辊表面 粗糙度越 高,摩擦力 大,在轧 制过程中易产生铁粉 ,带钢表面黏 附的油多, 表面清 洁度低 ,因此选 择合适的粗 糙度 极为
热镀锌合金化镀层腐蚀行为及机理研究
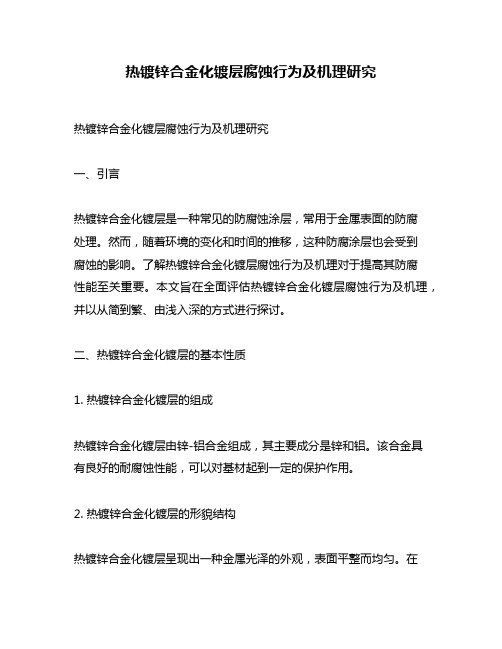
热镀锌合金化镀层腐蚀行为及机理研究热镀锌合金化镀层腐蚀行为及机理研究一、引言热镀锌合金化镀层是一种常见的防腐蚀涂层,常用于金属表面的防腐处理。
然而,随着环境的变化和时间的推移,这种防腐涂层也会受到腐蚀的影响。
了解热镀锌合金化镀层腐蚀行为及机理对于提高其防腐性能至关重要。
本文旨在全面评估热镀锌合金化镀层腐蚀行为及机理,并以从简到繁、由浅入深的方式进行探讨。
二、热镀锌合金化镀层的基本性质1. 热镀锌合金化镀层的组成热镀锌合金化镀层由锌-铝合金组成,其主要成分是锌和铝。
该合金具有良好的耐腐蚀性能,可以对基材起到一定的保护作用。
2. 热镀锌合金化镀层的形貌结构热镀锌合金化镀层呈现出一种金属光泽的外观,表面平整而均匀。
在镀层的微观结构中,锌和铝的颗粒呈现出一种交织的排列方式,形成了一种紧密的结构,这为其具备很强的耐腐蚀性能奠定了基础。
三、热镀锌合金化镀层腐蚀行为1. 典型的腐蚀类型热镀锌合金化镀层的腐蚀行为主要包括局部腐蚀和一般腐蚀。
局部腐蚀主要表现为锌和铝的局部溶解,形成孔洞、龟裂和剥落等现象。
一般腐蚀则是指整个镀层受到均匀腐蚀,降低了其防腐性能。
2. 腐蚀影响因素热镀锌合金化镀层的腐蚀行为受到多种因素的影响,主要包括环境因素和材料因素。
环境因素如大气中的氧气、湿度和污染物等都会促进腐蚀的发生。
材料因素则包括镀层的成分、结构和厚度等。
研究发现,较高的铝含量和较大的厚度可以增加镀层的耐腐蚀性能。
四、热镀锌合金化镀层腐蚀机理1. 镀层溶解镀层腐蚀的起始点是镀层中的金属离子溶解,这会降低镀层的完整性并形成腐蚀产物。
在局部腐蚀发生时,表面的钝化膜破坏,镀层就会进一步溶解。
2. 电化学反应腐蚀过程中,出现了一系列的电化学反应。
在局部腐蚀发生时,锌和铝发生了不同的电化学反应,导致了腐蚀的差异行为。
一般而言,镀层中锌的电化学反应优先进行,充当了一种牺牲阳极,保护了基材。
3. 腐蚀产物形成腐蚀产物的形成也是腐蚀过程的关键环节。
钢结构镀锌涂层冲蚀磨损表面形貌及粗糙度

钢结构镀锌涂层冲蚀磨损表面形貌及粗糙度钢结构镀锌涂层冲蚀磨损表面形貌及粗糙度摘要:我国西北地区风沙特殊环境对该地区钢结构的耐久性和安全性影响严重。
利用风沙环境侵蚀实验系统、扫描电子显微镜(SEM)和激光共聚焦显微镜(LSCM)研究钢结构镀锌涂层受风沙冲蚀磨损损伤行为和损伤形貌,并分析其表面粗糙度。
结果表明:涂层材料的冲蚀损伤行为更加依赖于冲蚀角度,在不同冲蚀角度下风沙流对涂层材料的冲蚀磨损过程同时存在类似表面划伤和挤压变形剥落;涂层材料的冲蚀坑深度随着冲蚀速度的增大而增加,在90°时冲蚀坑深度大于45°时的冲蚀坑深度;在相同的冲蚀速度下,45°时表面平均粗糙度Sa和均方差Sq较90°时大,在相同的冲蚀角度下,Sa和Sq均随速度的增大而增大。
在冲蚀中后期,粒子对凹凸不平的表面冲蚀磨损破坏严重,试件表面峰谷的形成和破坏导致冲蚀率增加。
关键词:风沙环境;镀锌涂层;冲蚀磨损;冲蚀形貌;粗糙度0 引言我国西北地区分布着广泛的沙漠,沙漠及周边地区分布着众多通信塔、输电铁塔和铁路电车输电塔等镀锌钢结构体系,由于长期遭受风沙的侵蚀作用,这些钢结构涂层受风沙冲蚀磨损破坏严重,使得其容易锈蚀,导致构件承载力下降,安全性和耐久性降低。
基于以上固体粒子冲蚀磨损问题,国内外学者对其进行了大量的研究。
目前,国外关于固体颗粒对材料的冲蚀磨损研究主要集中在金属材料、管道、工程塑料、钢结构涂层、混凝土和玻璃等方面,主要研究了不同试验工况下不同材料的冲蚀磨损对比,冲蚀形貌分析和固体颗粒对材料的冲蚀模拟研究[1-3],关于材料受单颗粒子冲击研究也较多[4-6]。
而国内关于工程材料受单颗粒子冲击研究主要集中在玻璃、陶瓷和混凝土方面[7-9], 关于风沙环境对工程材料的冲蚀磨损研究主要集中在混凝土和钢结构油漆涂层方面,研究在试验方法、冲蚀磨损机理、评价指标和材料的抗冲蚀磨损措施等方面取得了一些进展[10-13],而对于工程中常用的镀锌涂层受风沙气固两相流的冲蚀磨损损伤形貌和粗糙度研究很少。
测定钢板镀锌层质量的几种腐蚀液比较
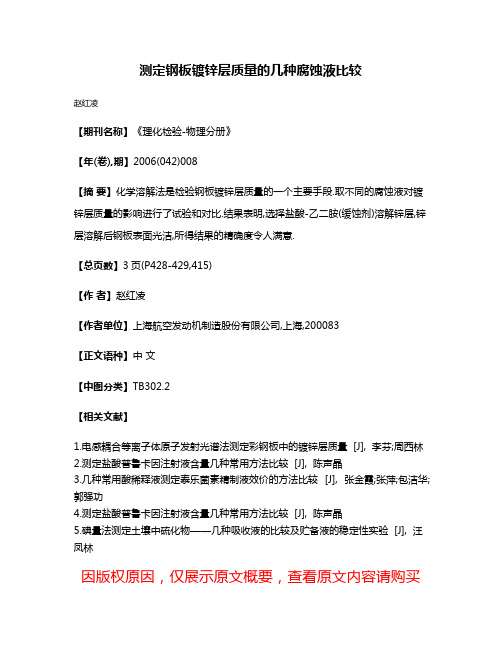
测定钢板镀锌层质量的几种腐蚀液比较
赵红凌
【期刊名称】《理化检验-物理分册》
【年(卷),期】2006(042)008
【摘要】化学溶解法是检验钢板镀锌层质量的一个主要手段.取不同的腐蚀液对镀锌层质量的影响进行了试验和对比.结果表明,选择盐酸-乙二胺(缓蚀剂)溶解锌层,锌层溶解后钢板表面光洁,所得结果的精确度令人满意.
【总页数】3页(P428-429,415)
【作者】赵红凌
【作者单位】上海航空发动机制造股份有限公司,上海,200083
【正文语种】中文
【中图分类】TB302.2
【相关文献】
1.电感耦合等离子体原子发射光谱法测定彩钢板中的镀锌层质量 [J], 李芬;周西林
2.测定盐酸普鲁卡因注射液含量几种常用方法比较 [J], 陈声晶
3.几种常用酸稀释液测定泰乐菌素精制液效价的方法比较 [J], 张金霞;张萍;包洁华;郭强功
4.测定盐酸普鲁卡因注射液含量几种常用方法比较 [J], 陈声晶
5.碘量法测定土壤中硫化物——几种吸收液的比较及贮备液的稳定性实验 [J], 汪凤林
因版权原因,仅展示原文概要,查看原文内容请购买。
镀锌层精磨后腐蚀问题研究_邓建青
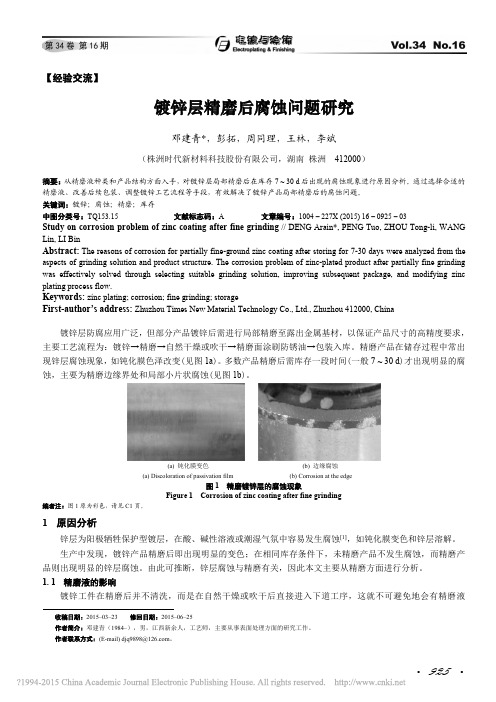
• 925 •【经验交流】镀锌层精磨后腐蚀问题研究邓建青*,彭拓,周同理,王林,李斌(株洲时代新材料科技股份有限公司,湖南 株洲 412000)摘要:从精磨液种类和产品结构方面入手,对镀锌层局部精磨后在库存7 ~ 30 d 后出现的腐蚀现象进行原因分析。
通过选择合适的精磨液、改善后续包装、调整镀锌工艺流程等手段,有效解决了镀锌产品局部精磨后的腐蚀问题。
关键词:镀锌;腐蚀;精磨;库存中图分类号:TQ153.15 文献标志码:A 文章编号:1004 – 227X (2015) 16 – 0925 – 03Study on corrosion problem of zinc coating after fine grinding // DENG Arain*, PENG Tuo, ZHOU Tong-li, WANG Lin, LI BinAbstract: The reasons of corrosion for partially fine-ground zinc coating after storing for 7-30 days were analyzed from the aspects of grinding solution and product structure. The corrosion problem of zinc-plated product after partially fine grinding was effectively solved through selecting suitable grinding solution, improving subsequent package, and modifying zinc plating process flow.Keywords: zinc plating; corrosion; fine grinding; storageFirst-author’s address: Zhuzhou Times New Material Technology Co., Ltd., Zhuzhou 412000, China镀锌层防腐应用广泛,但部分产品镀锌后需进行局部精磨至露出金属基材,以保证产品尺寸的高精度要求,主要工艺流程为:镀锌→精磨→自然干燥或吹干→精磨面涂刷防锈油→包装入库。
影响镀锌层耐腐蚀性的因素探讨

影响镀锌层耐腐蚀性的因素探讨摘要:采用中性盐雾试验来检测锌镀层的耐蚀性,以耐盐雾试验时间长短,锌镀层外观变化程度来判断锌镀层耐蚀性的好坏。
介绍了导致镀锌层耐腐蚀性差的原因,以及提高锌镀层耐性性的生产工艺及维护方法,使镀锌层耐腐蚀性能得到提高。
锌镀层对于钢铁而言,属于阳极性镀层,能提供可靠的电化学保护。
在工业生产中被广泛应用。
锌镀层经过钝化后耐蚀性可提高6-8倍,如何提高锌镀层耐蚀性是镀锌生产厂家时刻关注的问题。
锌镀层多通过中性盐雾试验(NSS试验)来检测耐蚀性。
目前许多镀锌生产厂家因电镀工件未能通过盐雾试验,大量工件返修,造成诸多浪费,生产成本增加。
如何提高锌镀层耐蚀性,对于广大镀锌生产厂家是一个十分重要的课题。
本文通过分析盐雾试验失败的原因,介绍提高锌镀层耐蚀性的方法,供广大读者借鉴。
1 与锌镀层耐蚀性有关的因素锌镀层耐蚀性与下面条件有关:1)锌镀层纯度锌镀层越纯净,耐蚀性越好;镀锌层含金属杂质越多,产生腐蚀原电池的机会越多,耐蚀性越差;锌镀层夹杂有机物越多,耐蚀性越差。
2)镀锌层的结合力镀层结合力差、起泡、脱皮、脆性区易发生腐蚀,镀锌层孔隙率也会影响镀层耐蚀性。
3)镀锌层的均匀度镀件不同部位厚度相差不应大于5um。
4)使用环境锌在干燥空气中几乎不发生变化,在通风不良,空气潮湿条件下,与非金属的挥发物(低分子梭酸、醛、酚、氨等)接触时易遭腐蚀。
2 影响镀锌层耐蚀性的原因镀锌层耐蚀性差的原因众多,除钝化液因素外,还与工件表面状态、镀液状态、前处理、电镀过程操作方式、钝化后处理、电镀生产管理、工件存放条件等众多因素有关。
镀锌层耐蚀性差的原因:2.1 前处理不良工件前处理不良,导致电镀质量差。
2.2 电镀过程操作不当1) 电镀时电流过大,造成镀层粗糙;电镀时间短,镀层太薄;2)工件出镀槽和钝化后清洗不彻底;3)工件在最后工序没有烘干;4)老化温度过高造成钝化膜龟裂;5)镀液温度过高造成镀层抗蚀能力差。
泥浆中镀锌层破损汽车钢板腐蚀的电化学腐蚀行为研究
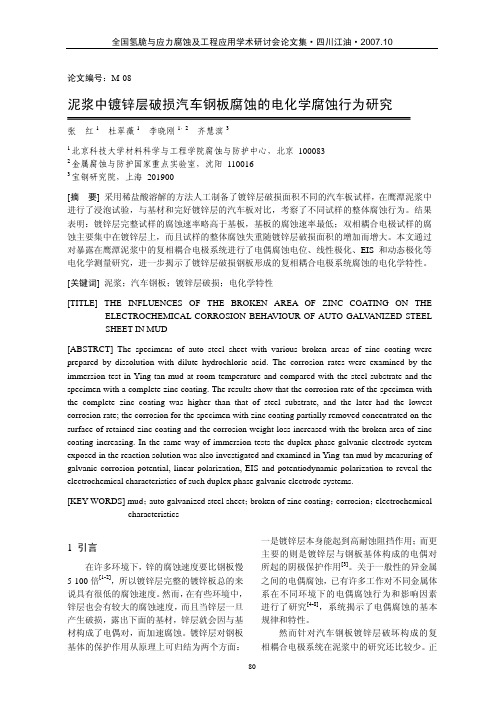
electrochemical testing device
表 1 GI 热镀锌钢板基板的化学成分
Table 1 The chemical composition of the substrate of galvanized steel sheet
0.07
4.35
corrosion rate / g.m-2.h-1
Eg / V
3 结果与讨论
3.1 化学浸泡腐蚀
5 种不同镀锌层破损比率试样浸泡 120h、 240h 和 360h 的腐蚀失重如图 2 所示。总体来 看,5 种试样在 3 个取样期的腐蚀速率的总体 趋势是相同的,镀锌层完整试样的腐蚀速率略 高于基材,这是因为锌层在酸性介质中,不容 易形成保护膜,腐蚀速率会增大,所以镀锌层 的腐蚀对试样整体腐蚀失重构成主要贡献;基 材的腐蚀速率最低,随时间变化较小,这主要 是由于产生了具有保护性的氧化物。一个明显 的试验现象是,对于镀层和基体共存(镀锌层 破损率 10%-50%)的双相试样,腐蚀速率随 着镀层破损率的提高增加明显。由于镀层破损 后镀锌层与暴露的钢板基体构成电偶对,导致 镀锌层阳极极化,因而随着基体暴露表面积的 增大,电偶作用增加,镀锌层腐蚀加重。
[KEY WORDS] mud;auto galvanized steel sheet;broken of zinc coating;corrosion;electrochemical characteristics
1 引言
在许多环境下,锌的腐蚀速度要比钢板慢 5-100 倍[1-2],所以镀锌层完整的镀锌板总的来 说具有很低的腐蚀速度。然而,在有些环境中, 锌层也会有较大的腐蚀速度,而且当锌层一旦 产生破损,露出下面的基材,锌层就会因与基 材构成了电偶对,而加速腐蚀。镀锌层对钢板 基体的保护作用从原理上可归结为两个方面:
热浸镀锌合金镀层耐腐蚀性能研究

签 : 7‘师名 名 余导签 脸 季小 从‘ \
日 期:
鞍山科技大学硕士论文
第一章
文献综述
第一章 文献综述
1 . 1热镀锌简介
钢铁的十分之一消耗于腐蚀1。人们通过各种途径来避免或减少钢铁 ’ ]
的腐蚀损失,锌是人们首先认识的既可以防钢铁腐蚀 ,又能受 自身腐蚀产
ccl e yT f Ft r s nrs t t rPr f ot gw r ea a d au t a db a l i r i eia Poe yo ca n e vl t e 毛o o o sn t i e ue c od t Eo ad c卜 aorigo c,n ir n r o T er u s hwta r t g n nZ 一 l t so htc s l ri i nA一 l ycan eo e h el s : ya as Mga o ot gbcm l i
镀锌层以使钢铁与大气腐蚀环境相隔绝的物理方式保护了钢铁不受腐2镀锌层由于腐蚀和其他原因使镀锌层中合金层部分地暴露于大气中这时钢板仍受到与第一种情况相同形式的完全地保护只是由于电极电位的不同电位较负的纯锌层将对电位较正的合金层提供电化学保护而优先腐蚀
鞍山科技大学硕士论文
摘
要
摘要
钢材的十分之一消耗于腐蚀,因此 ,提高钢铁的耐腐蚀性能具有十分 重大的意义。在众多提高钢铁耐腐蚀性能的方法 中,热镀锌是当今世界上
o ao ot gde o i r s i a ywt dio f g e E f I ycan osnt n e el er i d i l i c a n l ha t no M . nR Wh cn n sl st nol t cr s nrs t tPor yo l ycan ot ti e h e s a . %, r i eia rPe fa o ot g w o oo sn t l i
电镀污染的现状分析及治理对策研究_程社新

能源环境电镀污染的现状分析及治理对策研究【摘要】电镀行业涉及的污染种类多、涉及的企业部门较多,处理工艺复杂,历来是治污工作的难点。
本文通过对污染现状、监管机制、污染物的处理方法等深入剖析,研究治理对策,提出以科学规划布局、集中治理、运用先进的处理工艺和设备,加强管理与监督,全员参与的综合整治机制。
【关键词】电镀污染;现状分析;治理对策1、前言随着我国现代化建设的飞速发展,作为轻工业产业支柱之一的电镀业也呈现出日新月异的发展态势,涌现出了许多新的电镀工艺和镀种,极大的丰富了人们日益增长的生活和生产需要。
但同时也带来较大的污染问题,个别地方企业污染状况到了令人触目惊心的地步,由此引发一些民众集体上访事件的不断发生,甚或酝酿成严重的社会问题。
通过走访调查,查找原因、研究治理对策,彻底解决电镀行业污染的难题,对恢复自然生态环境,创建美好家园具有重大的意义。
2、现状分析笔者于2004年至2012年近九年时间走访和调查江西、浙江、安徽及江苏近30家电镀企业。
该行业所涉及的污染种类和现状剖析如下。
2.1镀种及产生污染种类电镀其镀种以及电镀过程中所产生的污染物主要有:①镀锌:含氰化镀锌、氯化钾镀锌、氯化铵镀锌、锌酸钠镀锌、热镀锌、镀达克罗等污染物:有毒废气(酸性气体、含氰毒气)、酸性废水、碱性废水、含铬废水等。
②铜、镍、铬:这一类的镀种很多污染物:有毒废气(酸性气体、含氰毒气)、酸性废水、碱性废水、重金属污染(主要是铜、镍、锡、隔等)、含铬废水等。
③铝氧化、酸洗、不锈钢电解等:污染物:有毒废气、酸性废水、碱性废水、重金属污染(主要是铜、镍、铁等)、染料、含铬废水等。
④电泳、喷涂、喷漆、烤漆等:污染物:有毒废气、酸性废水、碱性废水、产品精饰、振磨产生的皮屑污物、塑粉粉尘、二甲苯等有毒气体。
⑤钢铁氧化、磷化: 污染物:有毒废气、酸性废水、碱性废水、产品精饰、振磨产生的皮屑污物、硝酸盐、亚硝酸盐等⑥超声波清洗所带来的污染:三氯乙烯、四氯化碳等有毒气体、用于冷浸、热浸含苯类溶剂、含聚乙二醇醚类的乳化剂等上述污染物可统划分为废水;废气;废渣三大类。
镀锌层破损汽车钢板在含NaCl溶液和泥浆中的腐蚀行为与EIS研究_张红 (1)

第21卷第3期2009年5月腐蚀科学与防护技术CORROSI ON S C IENCE AND PROTECTION TECHNOLOGYV o.l 21N o .3M ay .2009收稿日期:2007-11-01初稿;2008-01-15修改稿基金项目:国家自然科学基金项目(50571022),国家科技基础条件平台建设资助项目(2005DKA10400)作者简介:张红(1966-),女,博士研究生,研究方向为腐蚀与防护.T e:l 010-********-511 E -m ai :l hongzhang0523@163.co m镀锌层破损汽车钢板在含NaC l 溶液和泥浆中的腐蚀行为与EI S 研究张红1,杜翠薇1,齐慧滨2,李晓刚1,31 北京科技大学材料科学与工程学院腐蚀与防护中心,北京100083;2 宝钢研究院,上海201900;3 金属腐蚀与防护国家重点实验室,沈阳110016摘要:采用镀锌层破损面积不同的热镀锌汽车钢板试样,在含相同3 5%C l -浓度的鹰潭泥浆和N aC l 水溶液中进行了浸泡和浸没腐蚀实验,研究了镀锌板、基板和镀锌层不同程度破损试样在两种介质中的腐蚀规律.结果表明:完整镀锌层的腐蚀速率高于基板;镀锌层破损试样的腐蚀失重随镀锌层破损面积的增加而增大;在泥浆中的腐蚀速率比在溶液中大,且腐蚀速率随时间的变化不同.E IS 分析结果表明,镀锌层破损试样的锌层在两种介质中的电荷转移电阻都比基材小得多,镀锌层的腐蚀对腐蚀失重结果起主要贡献.泥浆溶氧高和p H 值低是造成镀锌层破损试样在两种介质中腐蚀行为明显不同的主要因素.关键词:镀锌钢板;镀锌层破损;腐蚀;泥浆;E IS中图分类号:TG174 3 文献标识码:A 文章编号:1002-6495(2009)03-0333-04CORROSION PROPERTI ES OF GALVANI ZED AUTO STEEL S HEET W I TH BREAKAGES OF Z INC COATING IN NaCl CONTAIN ING S OLUTION AND M UDZ HANG H ong 1,DU Cu-i w ei 1,Q IH u-i b i n 2,LI X iao -gang1,31 C orro si on and P ro tecti on Cen ter ,Universit y of S cience and T echnology B eijin g,B eij i ng 100083;2 R &D of B aos teel ,Shanghai 201900;3 S tateK e y Laboratory for Corro sion and P rotection,Shenyang 110016Abst ract :The corrosion pr operties of the galvanized stee l sheets fo r au tos w it h various br oken areas o f their zinc coati n g w ere evalua ted and co m pared by i m m ersion tests in a m ud of Y i n g tan so il containing 3 5%NaC l and a so l u ti o n w ith the sa m e concentrati o n o fN a C.l The resu lts sho w that co rrosion w e i g h-t loss rate of the sheet w ith i n tact zi n c coati n g w as higher than that of the substrate ;t h e corrosion rate in -creased w ith the broken area i n creasi n g ,and w as higher in the m ud than in the so l u tion.I n the t w o cases ,the variati o ns o f co rrosion rate w ith ti m e w ere also differen.t The analysis of E I S diagra m s show that the e -lectric charge transfer resistances o f the spec i m ensw it h broken zi n c coati n g w ere m uch lo w er than tha t o f the stee l substrate ,so the corrosi o n o f zi n c coating played a m ajor i m portant ro le i n the w e i g ht loss .H igher oxygen concen trati o n and lo w er p H value in the m ud w ere t w o key factors to g i v e rise to t h e corrosion be -hav ior o f speci m ens w ith broken zi n c coa ti n g i n the m ud d ifferent fr o m that in the NaC l so lution .K eyw ords :ga l v an ized stee l shee,t breakage of zinc coati n g ,co rrosi o n,mud ,E I S目前,在世界范围内乘用车的外板主要采用热镀锌钢板.一般情况下,车身表面的多层涂装能为镀锌钢板提供有效的防护,但是当涂层因外力破损后就会对镀锌钢板失去保护作用,如果镀锌层也同时遭到破坏,则车身局部就会暴露出由镀锌层和钢材基板构成的复相金属耦合电极,在环境的大气、雨水和含融雪盐泥浆的作用下发生加速破坏,导致车身穿孔.实践表明,车身破坏后暴露的表面上镀锌层破损面积的不同会给其腐蚀行为带来不同的影响,为此作者曾采用人工破坏镀锌层的方法,系统研究了镀锌层破损面积从0%~100%变化试样在室温5%N aC l 溶液中的腐蚀和电化学行为,得出在腐蚀初期,镀锌层完整试样的腐蚀速率高于基板,基板的腐蚀速率最低,确定双相耦合电极试样的腐蚀主要集中在镀锌层上,而且试样的整体腐蚀失重随镀锌层破损面积的增加而增大,镀锌层破损70%时腐蚀率最大.关于镀锌板在大气和溶液中的电偶腐蚀,已有很多的研究和分析[1~4],然而,许多腐蚀现象表明,含有融雪盐成分泥浆的附着会使车体的腐蚀速度高于一般大气和雨水造成的334腐蚀科学与防护技术第21卷腐蚀,但对镀锌钢板在泥浆中的腐蚀行为和电化学特性缺少系统研究.为此本文选择典型的酸性土壤-鹰潭土壤,研究镀锌层破损试样在土壤泥浆中的基本腐蚀行为和电化学行为,并与5%N aC l溶液进行对比,揭示镀锌钢板在泥浆和水溶液介质中腐蚀表现和影响因素的异同.1实验方法1 1实验材料和试样制备实验材料为国产双面热镀纯锌(G I)汽车板和与之对应的IF钢基板.基板的化学成分为(m ass%):0 0028C,0 01S,i0 14M n,0 012P,0 0062S,0 02Cu,0 01N,i0 01C r,0 002Sn,0 001N b,0 001V,0 039A,l0 041T,i余Fe.镀锌钢板的镀锌层厚度为0 7mm.镀锌层破损试样采用在选择的表面上贴覆不同尺寸滤纸和滴定稀盐酸腐蚀的方法制备,加上镀锌层完整试样和基板可构成锌镀层破损面积分别为0%、10%、25%、50%和100%的试样.试验时试样表面为原始状态,测量试样的表面积后,仅经常规表面除油和清洗,吹干称重后待用.1 2实验介质和条件泥浆配制选用干燥的鹰潭土壤,其理化特性见表1.通过向一定量的土壤中添加40%的水和3 5%N aC l形成泥浆.泥浆经过充分搅拌均匀,迅速投入使用.在实验过程中,通过对电解池重量的定期检测,按时补充散失的水分,保证泥浆含水量不变.在电化学实验中,则需要整个体系静置一段时间(一般1小时),以使系统达到稳定状态,但要避免配制好的泥浆因在空气中敞开长期置放而发生变化.实验的对比介质是含3 5%N aC l水溶液.实验温度为(25 2) .1 3实验方法实验方法分腐蚀速率测量和E IS阻抗谱测量.腐蚀速率采用溶液全浸和泥浆浸没进行.每种试样采用3个平行试样,腐蚀120、240和360小时后取出清洗腐蚀产物,称量重量变化,确定单位面积和单位时间的腐蚀失重量.EIS测量采用美国EG&G公司的2273电化学综合测量系统.测试采用三电极体系,采用饱和甘汞电极做参比电极,P t片做辅助电极.E IS频率测量范围为100k H z~10mH z,测量幅值为10mV.2结果与讨论2 1腐蚀速率镀锌层破损面积不同的5种试样在上述泥浆和N aC l水溶液中腐蚀不同时间的失重率如图1所示.由图可见,在两种介质中,完整镀锌板试样的腐蚀速率均略高于基板并且基板的腐蚀速率基本保持恒定.T ab le1Physi ca-l che m ical data of Y i ng-tan soilC l-%NO-3%SO2-4%C a2+%M g2+%K+%Na+%电导率m S/c mp HFig.1Corros i on w eigh t-l oss rates o f va ri ous spec i m ens i m m ersedi n3 5%N aC l so luti on and mud o fY i ng tan so il a fter di-fferent periods of ti m e对于镀锌层破损试样,随着镀层破损面积的增加,试样的整体失重增加.腐蚀主要集中在试样表面的镀锌层部位,但在泥浆中,暴露基板部位的腐蚀略重于溶液的情况.在溶液中,不同试样的腐蚀速率随着暴露时间的增加而降低;而在泥浆中,腐蚀速率则随暴露时间的延长而加速.镀锌层破损试样在泥浆中的腐蚀速率明显高于在溶液中,尤其是镀锌层破损面积为25%和50%的试样.对于镀锌层破损50%的试样,长时间暴露腐蚀速率略有下降的趋势.由此可见,试样在两种介质中的腐蚀速率除了随镀锌层破损面积的增大而增加以外,腐蚀失重率大小和随时间的变化具有明显差别,这种规律和差异取决于镀锌层和基板的基本腐蚀行为,以及二者构成的复相耦合电极的腐蚀行为,特别是与溶液和泥浆的不同理化特性有关.分析讨论认为:1 镀层破损的面积效应.一般情况下,当镀锌层和钢表面均处于活化状态时,锌比铁活泼,因此在两种介质中镀锌层完好试样的腐蚀速率均略高于基板试样.对于镀锌层破损的复相耦合电极,残留的锌层与基体构成了电偶对,锌为阳极.随着镀锌层破损面积增加,阳极/阴极面积比减少,从而阳极电流密度增加,腐蚀加速.可以推断,当镀锌层只有少量残留时,镀锌层的腐蚀会很快,在很短的时间就会腐蚀完了,之后试样则呈现出基板的腐蚀行为.2 腐蚀时间的影响.如上所述,对于镀锌层破损面积较大的试样,随着腐蚀时间的延长,镀锌层的量和面积都会加速减少,而试样的腐蚀主要来自镀锌层,因此试样的腐蚀失重会逐渐降低.另外,随着腐蚀产物的形成,镀锌层表面状态发生改变,活性降低,因此在极化不是很强的情况下,例如在水溶液中,腐蚀速率会随着时间而下降.镀锌层试样在泥浆中的腐蚀行为与此相反,这主要与泥浆与水溶液不同的理化性质有关.3 泥浆特性的影响.在本研究的实验条件下,腐蚀过程均受阴极反应,即氧的去极化反应步骤控制.测试表明,实验用鹰潭泥浆的含氧量高于N aC l水溶液,氧浓度越高.氧电极电位E越正,泥浆的腐蚀性越强[5],因此在溶解氧完全消耗试样在泥浆中的腐蚀速率要明显高于溶液;而在溶解3期张红等:镀锌层破损汽车钢板在N aC l 溶液和泥浆中的腐蚀行为和EIS 研究335氧基本消耗完以后,腐蚀的进行就取决于氧从环境中向介质中的溶解和向反应前沿的扩散.除了溶氧量的差异外,泥浆的p H 值明显低于溶液,呈较强的酸性.因此,在泥浆中发生吸氧腐蚀的同时,也可能发生析氢腐蚀,特别是这种酸性有助于维持镀锌层表面的活性,所以在泥浆中的腐蚀速率要明显高于溶液,而且随着腐蚀时间的延长,腐蚀速率增加.泥浆与溶液的另一个明显的差异是电导率,二者的电导率分别为0 9m S /cm 和3 8mS /c m 尽管泥浆中的离子种类较多、离子浓度较大,但由于泥浆的含水量低,呈粘稠状,因此离子和氧在其中的迁移和扩散能力较低,容易使腐蚀局限于局部.在泥浆中钢板基体的腐蚀相对较重与此有关.2 2E IS 研究2 2 1EIS 图谱 为了进一步揭示镀锌层破损试样在两种实验介质中的电化学特性,分别测量了5种试样在泥浆和水溶液中的E IS 图,分别见图2和图3.可以明显看出:除镀锌层完整试样以外,在泥浆中的容抗弧都比在溶液的小;在同一介质中,镀锌层破损率10%~50%的容抗弧依次减小;基材的容抗弧最大.从容抗弧的形状看,只有基材试样的容抗弧形状是相似的,其他4种试样的容抗弧区别较大.2 2 2等效电路 分别对两种介质中的E IS 谱图进行等效电路拟合,结果见图4和图5.图4表明,在泥浆中,基板和镀锌层各试样的EIS 谱图都只有1个时间常数,其腐蚀等效电路都可用R s (QR t )表示,其中R s 为泥浆电阻,Q 为锌层表面与泥浆的有弥散效应的界面电容,R t 为锌层和基材表面在泥浆中的电荷转移电阻.在溶液中的等效电路比较多样化.基板和完整镀锌层试样的等效电路见图5(a),用R s (CR t )O 表示,其中R s 为溶液电阻,C 为镀锌层表面与溶液的界面电容,R t 为电荷转移电阻,O 为平面电极的有限层扩散阻抗;镀锌层破损率为10%和25%试样的等效电路见图5(b),可用R s (C 1(R t1(C 2R t 2)))表示,其中C 1为整个界面的电容,R t1为锌层表面与溶液的电荷转移电阻,C 2和R t 2分别表示基材表面与溶液的界面电容和电荷转移电阻;而50%试样的见5(c ),可用R s (C 1(R t 1(C 2(R t 2O ))))表示,与图5(b )相比多了平面电极的有限层扩散阻抗O ,这可能是由于在试样表面迅速产生了一些非致密性保护膜引起的.2 2 3电荷转移电阻 针对以上拟合出的等效电路,分别求出镀锌层试样的锌层在两种介质中的电荷转移电阻R t 值,见图6.由图6可见:对于镀锌层有破损试样上的锌层在泥浆和溶液中的电荷转移电阻都很小,说明在两种介质的腐蚀过程中,锌层腐蚀是主要贡献.电荷转移电阻R t 的变化规律,呈现了镀锌层破损面积不同对试样总体腐蚀速率的影响趋势:随着镀锌层破损面积的增大,腐蚀反应越容易进行,电偶作用越明显.在腐蚀过程中基材因其反应活性较小,相对于Zn 表面上的反应,其反应阻力很大,因而腐蚀比较缓慢.336腐蚀科学与防护技术第21卷Fig.6E lectr ic charge transfer resistances ofzi nc coati ng fo r d ifferent spec i m ens腐蚀初期,在两种介质中,镀锌层破损试样上锌层的腐蚀都是较快的.但后期腐蚀速度就会明显不同:在泥浆中,由于泥浆呈酸性,且黏性较大,锌层上难于生成有保护性的腐蚀产物[6],并且很难依附于锌层表面,又因溶解氧较大,反应会加速,腐蚀速度增加很快;而在溶液中,锌层表面易形成保护性氧化膜,依附在锌层表面不易脱落,而且溶解氧得不到及时补充,造成电偶腐蚀效应有所降低,腐蚀速度增加不大.综上所述,尽管使泥浆和溶液的腐蚀速率产生差异的因素很多,在各种影响因素中,起主要作用的应该是溶解氧和p H值的大小,溶解氧高和p H值低导致相同试样在泥浆中的腐蚀速率较大.完整锌层的试样,在两种含相同浓度的氯离子介质中,都不容易形成保护膜,腐蚀速率略高于基材,因此镀锌层的腐蚀对双相耦合试样的整体腐蚀失重构成主要贡献.对于基材来说,综合影响的结果是产生了具有保护性的氧化物,腐蚀速率低,而且腐蚀行为在两种介质中差别不大.3结论1 在泥浆和溶液中,完整镀锌层的腐蚀速率高于基板;镀锌层破损试样的腐蚀主要集中在镀锌层上,而且试样的整体腐蚀失重随镀锌层破损面积的增加而增大,在泥浆中的腐蚀速率比在溶液的大,且增长幅度也相对较大.2 由E IS图谱分析可知,在泥浆中试样的容抗弧都比在溶液中小;等效电路拟合结果表明,镀锌层破损试样上的锌层在泥浆和溶液中的电荷转移电阻都很小,说明锌层很易损失;泥浆中溶解氧含量高和p H值低是镀锌层破损试样腐蚀速率高和腐蚀随时间加速的主要原因.参考文献:[1]E-l M ahdy G A,N i sh i kat a A,T s u ru T.AC i m pedance study oncorros i on of55%A-l Zn alloy coated steel under th i n electrol ytel ayers[J].Corros i on Science,2000,42(1):183.[2]Lee J M.Num eri ca l ana l ysis of gal van i c corros i on of Zn/Fe i n-terf ace ben eat h a t h i n electrol yte[J].E lectroc h i m ica Acta,2006,51(16):3256.[3]Zhang X G.Galvan ic p rotecti on d ist ance of z i nc coated steelun-der various environm en tal conditi on s[J].C orros i on,2000,56(2):139.[4]Zhang X G,Valeriote E M.Galvan ic protection of s t eel and ga-lvan ic corros i on of zi n c under th i n layer el ectrol ytes[J].Corro-s i on Science,1993,34(12):1957.[5]傅朝阳,姚安林,李健.钻井泥浆中碳钢的腐蚀和防护[J].石油天然气化工,2000,29(5):257.[6]施彦彦,张昭,张鉴清,等.锌及其合金的大气腐蚀研究现状[J].中国腐蚀与防护学报,2005,25(6):373.。
存在锈蚀和磨损的精加工件修复及再利用技术
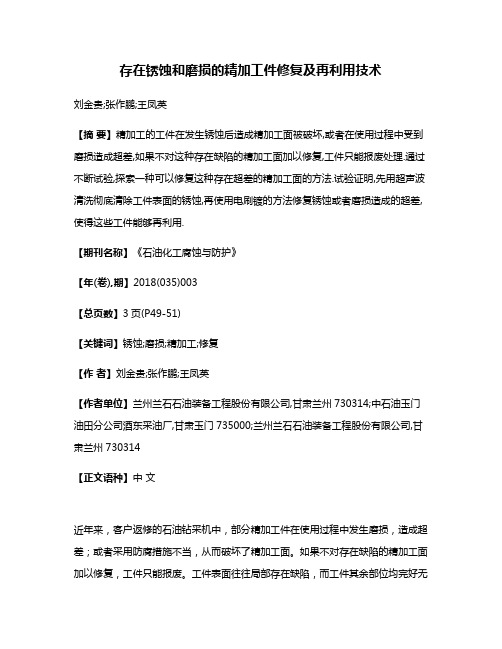
存在锈蚀和磨损的精加工件修复及再利用技术刘金贵;张作鹏;王凤英【摘要】精加工的工件在发生锈蚀后造成精加工面被破坏,或者在使用过程中受到磨损造成超差,如果不对这种存在缺陷的精加工面加以修复,工件只能报废处理.通过不断试验,探索一种可以修复这种存在超差的精加工面的方法.试验证明,先用超声波清洗彻底清除工件表面的锈蚀,再使用电刷镀的方法修复锈蚀或者磨损造成的超差,使得这些工件能够再利用.【期刊名称】《石油化工腐蚀与防护》【年(卷),期】2018(035)003【总页数】3页(P49-51)【关键词】锈蚀;磨损;精加工;修复【作者】刘金贵;张作鹏;王凤英【作者单位】兰州兰石石油装备工程股份有限公司,甘肃兰州730314;中石油玉门油田分公司酒东采油厂,甘肃玉门735000;兰州兰石石油装备工程股份有限公司,甘肃兰州730314【正文语种】中文近年来,客户返修的石油钻采机中,部分精加工件在使用过程中发生磨损,造成超差;或者采用防腐措施不当,从而破坏了精加工面。
如果不对存在缺陷的精加工面加以修复,工件只能报废。
工件表面往往局部存在缺陷,而工件其余部位均完好无损,尚有一定的利用价值。
如果置换新的零件,会增加成本,且造成不必要的浪费。
出于经济考虑,通过不断试验,探索一种可以修复这种存在超差的精加工面的方法。
目前,市场上常用的除锈剂大都是利用酸或者碱达到除锈的效果,尝试了多种国内外的除锈剂,对有蚀坑的金属表面不是除锈效果不理想,就是除锈过程中工件被过度氧化。
综合考虑之后,选择了超声波清洗除锈。
电刷镀技术在恢复磨损零件的尺寸精度和几何形状精度,填补零件表面的划伤、沟槽和压坑,补救加工中出现的超差件,精饰零件表面等方面应用广泛[1]。
超声波清洗除锈和电刷镀作为两项成熟的技术,在机械行业有着广泛的应用,但是这两项技术联合用于存在蚀坑的精加工件表面的修复,目前还没有被推广开来。
1 精加工面腐蚀及除锈原理1.1 精加工面腐蚀金属腐蚀就是金属与周围环境(介质)之间发生化学作用或电化学作用而引起的破坏或变质。
- 1、下载文档前请自行甄别文档内容的完整性,平台不提供额外的编辑、内容补充、找答案等附加服务。
- 2、"仅部分预览"的文档,不可在线预览部分如存在完整性等问题,可反馈申请退款(可完整预览的文档不适用该条件!)。
- 3、如文档侵犯您的权益,请联系客服反馈,我们会尽快为您处理(人工客服工作时间:9:00-18:30)。
• 925 •
【经验交流】
镀锌层精磨后腐蚀问题研究
邓建青*,彭拓,周同理,王林,李斌
(株洲时代新材料科技股份有限公司,湖南 株洲 412000)
摘要:从精磨液种类和产品结构方面入手,对镀锌层局部精磨后在库存7 ~ 30 d 后出现的腐蚀现象进行原因分析。
通过选择合适的精磨液、改善后续包装、调整镀锌工艺流程等手段,有效解决了镀锌产品局部精磨后的腐蚀问题。
关键词:镀锌;腐蚀;精磨;库存
中图分类号:TQ153.15 文献标志码:A 文章编号:1004 – 227X (2015) 16 – 0925 – 03
Study on corrosion problem of zinc coating after fine grinding // DENG Arain*, PENG Tuo, ZHOU Tong-li, WANG Lin, LI Bin
Abstract: The reasons of corrosion for partially fine-ground zinc coating after storing for 7-30 days were analyzed from the aspects of grinding solution and product structure. The corrosion problem of zinc-plated product after partially fine grinding was effectively solved through selecting suitable grinding solution, improving subsequent package, and modifying zinc plating process flow.
Keywords: zinc plating; corrosion; fine grinding; storage
First-author’s address: Zhuzhou Times New Material Technology Co., Ltd., Zhuzhou 412000, China
镀锌层防腐应用广泛,但部分产品镀锌后需进行局部精磨至露出金属基材,以保证产品尺寸的高精度要求,主要工艺流程为:镀锌→精磨→自然干燥或吹干→精磨面涂刷防锈油→包装入库。
精磨产品在储存过程中常出现锌层腐蚀现象,如钝化膜色泽改变(见图1a )。
多数产品精磨后需库存一段时间(一般7 ~ 30 d )才出现明显的腐蚀,主要为精磨边缘界处和局部小片状腐蚀(见图1b )。
(a) 钝化膜变色 (b) 边缘腐蚀
(a) Discoloration of passivation film (b) Corrosion at the edge 图1 精磨镀锌层的腐蚀现象
Figure 1 Corrosion of zinc coating after fine grinding
编者注:图1原为彩色,请见C1页。
1 原因分析
锌层为阳极牺牲保护型镀层,在酸、碱性溶液或潮湿气氛中容易发生腐蚀[1],如钝化膜变色和锌层溶解。
生产中发现,镀锌产品精磨后即出现明显的变色;在相同库存条件下,未精磨产品不发生腐蚀,而精磨产品则出现明显的锌层腐蚀。
由此可推断,锌层腐蚀与精磨有关,因此本文主要从精磨方面进行分析。
1. 1 精磨液的影响
镀锌工件在精磨后并不清洗,而是在自然干燥或吹干后直接进入下道工序,这就不可避免地会有精磨液
收稿日期:2015–03–23 修回日期:2015–06–25
作者简介:邓建青(1984–),男,江西新余人,工艺师,主要从事表面处理方面的研究工作。
作者联系方式:(E-mail) djq9898@ 。
• 926 •
残留于表面。
精磨液主要由缓蚀剂和表面活性剂组成,具有一定的吸湿作用,灰尘和铁屑附着处容易出现浓差
电池腐蚀[2],所以在锌层覆盖区域会出现点状腐蚀。
另外,精磨液的酸碱性不同,对锌层的腐蚀也会有很大差别。
1. 2 精磨对产品结构的影响
腐蚀均从精磨边缘迅速开始,可能是精磨边缘微孔藏液并形成电化学腐蚀所引起的,具体原因如下:
(1) 产品精磨后外套锌层面积小、裸露区域(精磨除去锌层的区域)面积大,在潮湿环境中容易形成大阴极、小阳极的电化学腐蚀[2]。
(2) 精磨边界处可能存在锌层和铁件的磨伤微裂纹和微孔,裂纹和微孔内溶液难以干燥,在库存时导致产品边缘腐蚀。
1. 3 库存包装的影响
锌层腐蚀需要氧和水,如库存所在地较潮湿,锌层破损处可能出现腐蚀。
2 工艺改进
(1) 更换精磨液,降低精磨液对锌层的腐蚀作用。
(2) 改进包装,确保产品处于干燥状态和防腐气氛中,以防止产品腐蚀。
(3) 改善工艺,由“镀锌后精磨”改为“精磨后局部镀锌”,既确保了精磨部位的尺寸精度,又避免了精磨液对锌层的腐蚀。
2. 1 更换精磨液
选取3种精磨液进行试验,结果见表1和图2。
从中可以看出,图2a 样板腐蚀明显,该样板浸泡在M3010中的锌层100%发生腐蚀;图2b 样板在Q101A 中浸泡30 d ,仅在液体界面处出现轻微腐蚀;图2c 中样板在SF-D185中浸泡30 d 后仍无明显腐蚀。
可见沈阳防锈为镀锌产品特别开发的SF-D185型切削液最适用于镀锌产品局部切削和精磨加工,该切削液可以在保证切削效果的同时对锌层和钢铁基体起到良好的防护作用。
表1 锌层在不同切削液中浸泡的腐蚀情况
Table 1 Corrosion of zinc coating after immersion in different fine-grinding solutions
切削液
浸泡4 d 后的腐蚀情况 浸泡10 d 后的腐蚀情况 浸泡30 d 后的腐蚀情况 M3010
约20%锈蚀 约50%锈蚀 100%锈蚀 SF-D185
无明显锈蚀 无明显锈蚀 无明显锈蚀 Q101A 界面轻微腐蚀 界面轻微腐蚀 界面轻微腐蚀
(a) M3010 (b) Q101A (c) SF-D185
图2 锌层在不同精磨液中浸泡1个月后的照片
Figure 2 Photos of zinc coating after immersion in different fine-grinding solution for a month
2. 2 改善包装
气相防锈纸和气相防锈袋本身含有气相缓蚀剂,能够缓慢、持久地散发出具有防锈效果的气体(如亚硝酸二环己胺、苯并三唑),这些气体吸附在裸露金属表面可形成保护层,从而阻止了氧气和湿气对金属的腐蚀。
因此,采用气相防锈纸或防锈袋密封包装镀锌产品可以保证储存环境干燥,并且提供气相防腐。
2. 3 改善工艺流程
将产品工艺由“镀锌后精磨”改为“精磨后镀锌,精磨面不镀锌”,既彻底消除了精磨液对锌层的影响,又避免了精磨操作对锌层的损伤,产品镀锌后外观良好(见图3)。
但局部镀锌对镀锌工艺的要求较高,注意事项如下:
• 927 •(1) 电镀专用封闭胶具有给基体提供绝缘保护,与金属基体之间的粘附性不强,电镀后易剥离的优点。
因此镀锌前可用电镀专用封闭胶对不需镀锌的部位进行封闭绝缘处理,并确保局部封闭完好。
(2) 在各工序操作过程中应避免损伤封闭胶层。
(3) 不需镀锌部位有非导体物质(橡胶、塑料等)隔离的,可不需进行封闭绝缘处理,但需避免镀锌后生锈,钝化后应马上吹水干燥并涂刷具有排水性能的防锈油。
实际生产中采取以上措施后,镀锌后精磨工件(剥离除去非镀锌区域封闭胶后涂油)库存22个月无异常,如图3所示。
图3 精磨后局部镀锌产品照片
Figure 3 Photo of the product partially plated with zinc coatings after fine grinding
3 结语
镀锌工件局部精磨后出现锌层腐蚀的主要原因可能是切削液对锌层具有腐蚀作用和吸湿保湿作用。
不同切削液对锌层的影响不同,选用对锌层和钢铁基体均具有防腐性能的切削液对镀锌工件进行精磨或切削加工可有效避免库存时锌层腐蚀。
采用“精磨后局部镀锌”的工艺可有效消除精磨对锌层的不良影响。
参考文献:
[1]
张允诚, 胡如南, 向荣. 电镀手册[M]. 3版. 北京: 国防工业出版社, 2007: 148. [3]
中国腐蚀与防护学会. 腐蚀与防护全书──金属的局部腐蚀: 点腐蚀•缝隙腐蚀•晶间腐蚀•成分选择性腐蚀[M]. 北京: 化学工业出版社, 1994: 139-140. [2] 曹楚南. 腐蚀电化学原理[M]. 北京: 化学工业出版社, 1985: 102-110.
[ 编辑:周新莉 ]
《电镀与涂饰》开通微信小店
《电镀与涂饰》杂志微信小店现已开通,读者可点击微信号(ddyts1982)下方菜单“编辑信箱─在线订购”,轻松下单购买。
也欢迎各位读者将您在使用过程中遇到的问题及建议通过相应菜单反馈给编辑部。