汽车零部件及材料实验室循环腐蚀试验方法
汽车零部件及材料试验室循环腐蚀试验方法-中国汽车工程学会标准

汽车零部件及材料试验室循环腐蚀试验⽅法-中国汽车⼯程学会标准《汽车零部件及材料实验室循环腐蚀试验⽅法》编制说明(标准征求意见稿)A. ⼯作简况1. 任务来源本标准依据中国汽车⼯程学会2015年10⽉16⽇印发中汽学函[2015]76号《中国汽车⼯程学会技术标准起草任务书》,任务书编号2015-1制定,标准名称《汽车零部件及材料实验室循环腐蚀试验⽅法》。
本标准主要完成单位:中国第⼀汽车股份有限公司技术中⼼,美国Q-Lab 公司中国代表处,重庆长安汽车股份有限公司等。
2. 主要⼯作过程2.12015年7⽉由中国第⼀汽车股份有限公司技术中⼼向中国汽车⼯程学会(以下简称中汽学会)提出制定《汽车零部件及材料实验室循环腐蚀试验⽅法》标准的申请,当年8⽉成⽴了标准⼯作组,提出规划并进⾏分⼯。
2.2⼯作组于2015年9⽉召开标准讨论会,确认撰写⼤纲和章节⽬录。
会后组织实验室循环腐蚀试验与户外腐蚀对⽐试验,并对对⽐试验⼯作进⾏分⼯,确定样品提供单位、实验室循环腐蚀试验单位和户外腐蚀测试试验单位。
2.3先后有10家主机⼚的参与单位,根据汽车⽣产的实际⼯艺提供了试验样品。
试验⼀共收到21种试验样品,其中有效试验样品19种(样板信息见表10)。
这19种试验样品经过对分层膜厚和总厚度的测试和记录,筛选外观合格的最终的样板数量是4257⽚。
样品准备的截⽌时间是2017年2⽉。
2.4经本标准的主要起草单位⼈员,分别是王纳新、王振尧、孙杏蕾、瞿华盛和张恒。
在各个参加单位准备样品期间,讨论通过了本标准的试验⽅案和实施路线。
⾸先,确定本标准的试验分两部分:⼏种实验室的循环腐蚀试验⽅法和验证实验室试验的户外腐蚀试验。
其中,户外腐蚀试验分为两类,⼀类是户外加速腐蚀试验,⼀类是户外⾃然腐蚀试验。
其次,通过⽐对试验和筛选,主要起草⼈员讨论决定:(1)户外加速腐蚀试验分别在2个不同的试验场进⾏,⼀个是中国船舶重⼯集团公司第七⼆五研究所厦门分部的试验场,在厦门海边,属于⾃然加速腐蚀,总的试验时间是2年;另⼀个是海南热带汽车试验有限公司的试验场,在海南琼海,⼈⼯喷洒盐⽔,属于⼈⼯加速腐蚀,总的试验时间也是2年。
汽车零部件实验室循环腐蚀试验要点

汽车零部件实验室循环腐蚀试验要点
高尚 江寅超 马文耀 李斌 上海机动车检测 中心 上海 2 0 1 8 0 5
【 摘 要l实验 室循环 腐蚀试 验是一 种气候环 境 的加 速试验 , 失
效较 为集中。 这 里针对 & M W1 4 8 7 2 — 2 0 1 O 标 准列 出了 若 干 关于试 验 的要
防 飞 溅
3
试验暴露条件 外观测试质 功能测试质 量损失要求及 量 损失要求及 试验循环数 试 验循环数 暴露条件A 暴露条件D 0 . 4 2 ±0 . 0 7 g 4 . 7 4 ± 0 . 1 9 g
3 ±l 循环 3 4  ̄4 循 环
ห้องสมุดไป่ตู้
3
暴露 条件B O . 4 4  ̄0 . 0 4 g
点, 供产品研 发和 试验人 员把 握 。
3 . 2 . 2 箱 底潮 湿法
【 关键词】G M w 1 4 8 7 2 ; 汽车零部件; 循环腐蚀; 质量损失; 腐蚀
深度
前 言 在 汽 车零 部 件 的 实 验 室 循 环 腐 蚀 试 验 中,目前 各大 汽 车 公司 的使 用 的有 以下 这些 : G MW 1 4 8 7 2 、 P V1 2 1 0 、 V D A6 2 1 - 4 1 5 、 S AE J 2 3 3 4 、 C C T I / I I / 4 、 D1 7 2 0 2 8 、 J A S O M 6 0 9 、 J AS O M 6 1 0 。 该 试 验 是一 种加 速试 验 , 是 失 效较 为集 中的 环节 。 准 确地 把 握试 验 , 可 以 免于 过/ 欠应 力, 实现 预设 的试 验检 出 目 的。 1 . 标 准 版本 目前 通 用 公 司 采 用 的 标 准 是 其 公 司 的 世 界 范 围标 准 GM W 1 4 8 7 2 - 2 0 1 0 E C y c l m C o r r o s i o n L a b o r a t o r y T e s t  ̄本文 按照此 版标 准的内容进行描述和讨论。 2 . 试 验 适用 范 围 该标 准是 _ 种对 全球 环境 地 区进 行 验 证试 验 、 开发试 验 、 质量 控制试验的循环腐蚀试验标准。 该标准适用于车身底部零件、 发动机 舱零件、 外部零件及板、 次级表面及内部零件。 3 . 试 验 描 述 该标 准除 了提 供了标 准 的循 环腐 蚀 试 验方 法 , 还 提 供 了增加 污 染 物 的循 环 腐蚀 试 验 方法 及标 准 的 剪裁使 用 建议 。 本 文 中我们 主要 介绍其 标 准试 验方 法。 每循 环试 验 由室 温阶 段、 潮 湿阶 段、 干 燥阶 段三个 阶段组 成 。 3 . 1 室温 阶段 温度 : 2 5 ℃±3 ℃I 湿度 : 4 5 %士1 0 %相对 湿 度 ( R H) ; 周期 : 8 小 时/ 循环 。 在该 阶 段需 要对 样 品施 加 喷雾 应 力。 用喷 雾装 置将 试验 试 剂 以 雾的 形式 喷 出而且 能够 将 之前一 次喷 雾 在样 品表 面 残 留的盐 分冲 刷 干净 , 样 品表 面必 须完 全湿 透 。 不 同的 产品所施 加 的喷 雾应 力的频 率 不同 , 在后 续 的章节将 进行 详细 的介 绍。 注意: 喷 雾 的力或 冲击 不得 将 样 品表面 的腐 蚀物 去 除也 不 得 破 坏 样 品的覆 盖层或 者覆 盖层 系统。 3 . 2 潮湿 阶段 温度 : 4 9 ±2 ℃; 湿度: 约1 0 0 % ̄ N 对湿度 ( R H) ; 周期: 8 小 时/ 循环 ( 由1 小 时 的转 换 时 间和 7 小 时 的保 温 时 间组 成) 。 潮 湿阶 段可 以通 过 以下三种 方式 实现 :
不同品牌汽车的零部件及材料加速腐蚀试验方法及评价对标分析
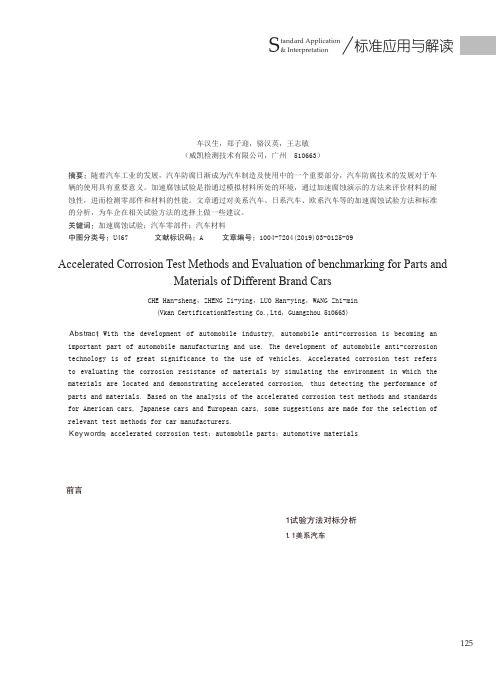
0 h 3 min
1c’
3 h 3 min
2 h 54 min
1a’ 5 h 57 min
0 h 3 min
2a
6 h 0 min
0 h 30 min
2b
6 h 30 min
2 h 0 min
3a
8 h 30 min 15 h 30 min
3a
24 h 0 min
—
重复步骤 1a-3a 4 次(不含第 1 次)
环。 盐 溶 液 成 分: 氯 化 钠 NaCl:0.9 %, 无 水 氯 化 钙
CaCl2:0.1 %,碳酸氢钠 NaHCO3:0.075 %。 1.2 欧系汽车 1.2.1 PSA 汽车 1)试验标准,D13 5486-2012,《材料和覆盖层 循
环加速腐蚀试验》。 2)具体测试条件: 喷雾阶段(如表 2) 过渡阶段(如表 3) 热循环阶段(如表 4) 盐溶液成分:氯化钠:5 %,通过 0.005 mol/L 的硫
辆的使用具有重要意义。加速腐蚀试验是指通过模拟材料所处的环境,通过加速腐蚀演示的方法来评价材料的耐
蚀性,进而检测零部件和材料的性能。文章通过对美系汽车、日系汽车、欧系汽车等的加速腐蚀试验方法和标准
的分析,为车企在相关试验方法的选择上做一些建议。
关键词:加速腐蚀试验;汽车零部件;汽车材料
中图分类号:U467
S 标准应用与解读 tandard Application & Interpretation
1.1.2 通用汽车 1) 试 验 标 准:GMW14872-2013,《 实 验 室 循 环 腐 蚀试验》。 2)具体测试条件 室温阶段:温度 25±3 ℃,相对湿度 45 %± 1 0 % R H , 持续时间 8 h; 高湿阶段:温度 49±2 ℃,相对湿度约 100 %RH, 持续时间 8 h; 干燥阶段:温度 60±2 ℃,相对湿度≤ 30 %RH,持 续时间 8 h; 盐溶液成分:氯化钠:0.9 %,氯化钙:0.1 %,碳酸 氢钠:0.075 %; 总 试 验 时 间: 根 据 样 品 的 安 装 部 位, 依 据 GMW14872 的表 A1 和 A2 规定的测试周期。见图 5 试验 流程和图 6 测试周期。 3)标准特点 喷雾方式与传统盐雾不一样,每循环喷淋 1-4 次, 通过手动或自动喷头直接喷射到样品表面,直到润湿为 止。 测试过程中需要加入标准板“coupon”控制腐蚀速率, 具体见图 7 和 8。 除了常规的汽车零部件,有些特殊的部位需要增加 环境应力,例如高温、冷凝液或泥浆等。以汽车排气管 为例,该部件的循环腐蚀测试方法,应依据标准 GMW 14872-2013 Option 4 进行试验。每个循环包含 3 个试验 阶段: 室温阶段:温度 25±3℃,相对湿度 45 %± 10 %RH,持续时间 8 h,该阶段内对样品和标准板进行 4 次盐雾喷洒,前 2 次喷洒间隔 1 h,在第 2 次喷洒结 束 0.5 h 后,对样品进行 4 h 的 482 ℃的高温试验,高温 试验结束 0.5 h 后,对样品和标准板进行 2 次间隔 1 小时 的盐雾喷洒(标准板不随样品进行高温试验); 高湿阶段:温度 49±2 ℃,相对湿度约 100 %RH, 持续时间 8 h; 干燥阶段:温度 60±2 ℃,相对湿度≤ 30 %RH,持
汽车腐蚀试验常见腐蚀问题分析与防腐优化

n vi r o nm
en
g
l 环 境 试 验— ■
抗石 击性差 ,加之钢板 搭接处 因相对 运动而 积水 ,易 引 起 钢板 大 面积锈蚀 、缝 隙腐蚀 ( 见 图 8)。通过 减少 受 冲击 的敏感 部位 ,并采 用具有一 定厚度 跟附着力 的 P V C 进行 防石 击密封喷涂来进行防护 ( 见 图 9)。 3 . 5 . 2 . 2油箱系 带多采 用 阴极 电泳处理 ,并 以黑漆涂 覆表 面 。其抗 石击性 差 ,系带 因涂镀 层破损 而锈蚀 ( 见 图 1 0)。通过工 艺对 比腐蚀试 验发现 ,油箱系带在原 有
Ab s t r a c t :T h i S p a p e r b a s e d o n t h e d a t a o f v e h i c l e a c c e l e r a t e d c o r r o s i o n r o a d t e s t , t h i S p a p e r i n t r o d u c e s s o m e p a r t s t h a t e a s i l y b e c o r r o d e d , a n d e l a b o r a t e s t h e r e l e v a n t f a c t o r s a f f e c t i n g c o r r o s i o n .A n d m o r e o v e r ,b y c o m p a r i n g wi t h t h e d i f f e r e n t c o r r o s i o n p r o c e s s e s , i t p r o p o s e s a n t i —
co rr osi ve opti miz ati o n re co mme n dati ons .
浅析循环腐蚀试验标准GMW14872—2013的应用

Zonghe 丫anjiu "综合研究 |浅析循环腐蚀试验标准GMW 14872—2013的应用黄艳(上海浩骋技术咨询有限公司,上海201906)摘要:循环腐蚀试验标准GMW 14872—2013描述了评估零部件和总成件的加速实验室耐腐蚀性测试的方法,试验程序提供了循环条件(盐溶液、各种温度、湿度和周围环境)的组合,以加速金属腐蚀。
该程序可有效评估各种腐蚀机制,如一般腐蚀、电镀腐蚀、缝隙腐蚀等,可单独调整试验曝露/环境条件,以达到任何所的腐蚀曝露 。
GMW 14872—2013实施过程,试验条件 实 到的 合盐雾在试验过程中应用到的问题以及腐蚀片在试验的应用这3个方, 实测试 的。
关键词:腐蚀 性 性0引言GMW 14872—2013循环腐蚀测试方法包括1% (近似 值)的复合盐雾在高温 湿和温 的 应用。
一试验循环等于24 h ,—测试周1成,测试曝露是标试描述的, 标准提供的产以及 ,测试 试失所循环。
ASTM B117的雾耐腐蚀的考察, 测试样品在 条件耐腐蚀 的 , 整、零部件、总成件的通用标准应用很广泛,因此这个标准的试验应用更值得 研究。
本文以底盘件控制臂的测试为例,对试验过程中遇到 的3方的问题 单 ,一测试周在环境段喷4次盐雾,外观性检查进行6个循环周期,功能性检查63个循环周,腐蚀片的腐蚀如 6测试周期 时,腐蚀 0.84 土 0.14)g ;63测试周时,腐蚀 1 (9.47 土 0.38)g 。
1试验条件设置实施中遇到的问题1.1 喷盐雾后30 min 内从100%RH 降湿至45%RH一测试循环由3测试 组成:(1) 第一 环境 温度 25 + 3)9;相对湿度为(45 土 10)%RH ;持续时间约8 h 。
(2) 第二湿温度为(49 + 2) = ;相对湿度约100%RH ;持续时间约8 ho(3)第三 温阶段。
温度为(60 土 2)>;相对湿度!30%RH ;持续时间约8 ho在第一 ,最实现的就是喷盐雾完成后迅速降湿多数箱体实情况如图1所示,达到标准要求,淋后产品曝露恒温恒湿至少1.5 h ,不被客户认可。
某汽车腐蚀工程试验规程

福特腐蚀工程试验规程简介本规程建立了乘用车和轻型卡车的整车加速腐蚀试验。
该试验用于确定整车在车身,底盘,电器件,发动机,非金属件,变速系元件,紧固件和加工过程的全面的抗腐蚀性能。
试验由100个可操纵的循环组成,包含的工况有潮湿,枯燥,盐雾喷射,和各种不同路面的行驶。
在此过程中,汽车要经受盐、灰尘、碎石和当地的温度及湿度变化的考验。
下雨天APG试验车不应该在户外操作或在道上行驶。
LPG试验车应该尽可能减少显露在雨中的时刻。
总的潮湿时刻是2550±25小时,总的枯燥时刻是375±25小时,整个试验期间试验车行驶的总里程大约为8000km,总的试验时刻大约为26周。
通用性本试验为一种可控试验,能在全世界范围内鉴不汽车和零部件是否符合WCR的标准,可在试验设备设施满足要求的任何地点进行。
对规程的任何修订都必须符合FAP03-179。
1.2零部件认可试验车应该由工程的首席工程师选择并能代表零部件开展的最高水平。
试验规程禁止使用除了与驾驶员平安相关的保卫性涂覆,然而,要是事先明白某个零件或某组零件比方紧固件和不防水的电器件会在早期损坏从而延误试验和导致其他的零件或系统产生无效的试验结果,那么在负责那个零件或这组零件的首席工程师认可后能够把那个零件或这组零件保卫起来,因此,这些部件被认为是不合格的。
1.3有效的试验结果从试验托付人的角度动身,为了保证试验和试验结果的有效性,任何被更换的零部件都要防护起来,失效后更换过的零部件要和配合件维持正常的关系和功能。
2.0使用仪器2.1潮湿室和枯燥室中用来指示温度和湿度的设备。
2.2所有试验测量设备必须按照?FAP03-015测量和试验设备的操纵,校准和维护?和APG-I-006来校准和维护。
2.3必须遵守所有适用的平安指导方针和程序。
3.0设备和设施3.1温度为50±20C,相对湿度为90%±2%的潮湿室。
3.2温度为50±20C,相对湿度小于20%的枯燥室。
汽车行业循环盐雾腐蚀试验方法

汽车行业循环盐雾腐蚀试验方法1:这是一个实验室加速腐蚀试验方法,可以用来确定汽车组件和部件的耐腐蚀性(东莞市豪恩检测仪器有限公司)。
它的性质,即是循环测试样品暴露在随时间变化的气候,试样放置在一个封闭的腔,暴露在气候变化,包括以下3个部分重复循环:4小时暴露在一个连续的间接触喷雾中性(pH值6.5至7.2)盐水溶液,属于淘汰率在1.02.0ml/80cm 2 /小时,在35度的室温中进行标准测试,其次是2小时在60度/20%到30%RH气候干燥的空气中进行测试,然后是2小时冷凝水气候曝光(润湿)的95%到100%RH在50度中周期重复,因此在测试期间的数量是可变的的,测试周期的各个部分之间最大的过渡时间也规定如下:从盐喷洒到空气中干燥30分钟内。
从空气干燥15分钟内润湿。
从润湿盐喷洒在30分钟内。
2:这是一个实验室加速腐蚀试验方法,可以用来确定汽车组件和部件的耐腐蚀性。
它的性质,即是循环测试样品暴露在随时间变化的气候,试样放置在一个封闭的腔,暴露在气候变化,包括以下3个部分重复循环。
2小时暴露在一个连续的接触喷中性(pH值6.5至7.2)盐水溶液,属于淘汰率在1.0 2.0ml/80cm 2 /小时,在35度试验室内进行标定。
其次是4小时在60度.20%到30%RH气候干燥的空气,然后是2小时冷凝水气候曝光(润湿)的95%到100%RH在50度. 周期重复,因此在测试期间的数量是可变的的,测试周期的各个部分之间的最大的过渡时间也规定如下:从盐喷洒到空气中干燥30分钟内。
从空气干燥15分钟内润湿。
从润湿盐喷洒在30分钟内。
3 这是一个实验室加速腐蚀试验方法,可以用来确定汽车组件和部件的耐腐蚀性。
它的性质,即是循环测试样品暴露在随时间变化的气候,测试样品被放置在一个封闭的腔,暴露在一个相对较短的时间,接触到热/潮湿和炎热/干燥环境,盐雾包括气候变化,整个测试周期包括一个主循环和一个子周期,整个测试周期需要24小时来执行,重复整个周期,因此在测试期间的数量是可变的的,曝光10分钟的连续喷盐水溶液的间接室温度在35度,主要测试周期开始。
循环腐蚀试验箱操作规程

1、设备功能及参数:1.1、设备功能:Corrosion循环腐蚀试验箱可运行包括时间、温度、湿度在内的测试条件都可以通过界面设置的下述四种测试循环:干燥循环、盐雾循环、100%湿度循环、相对湿度。
盐雾喷射实验:一种耐腐蚀测试方案是通过一个在测试试验箱顶部的喷嘴喷出来的水雾,箱内的盐雾散布结构可以将盐雾平均地分配到整个测试区域内。
根据箱体的容积,箱内需安装多个喷嘴,废液通过仪器底部的排水装置被收集起来,储存在测试实验箱底部,然后排出到外面。
满足高要求的实验室加速腐蚀试验此类试验:包括ASTM,DIN,IEC,CCT1,CCT2,CCT3,CCT4,VDA621-415,ISO14993,SAEJ2334等汽车厂家标准:GM9540P/GMW14872通用汽车;PVW-1200,1209,1210大众汽车;CETP00.00-L-467,福特汽车;STD423-0014/VCS1027,149,沃尔沃汽车;1.2、设备参数:●喷雾模式箱体温度范围:10~75℃盐雾收集量:0.5ml~5ml(连续可调)空气饱和温度范围:RT+10 ~+70℃●冷凝模式温度范围:40~50℃湿度范围:95%~ 100%(相对湿度)●干燥模式温度范围:RT~+70℃(可调)湿度范围:10%RH~50%RH,●喷雾方式该喷嘴为美国进口标准产品,便于后期维护,喷嘴为锥形喷雾范围,确保样品能被溶液均匀喷洒。
温度分辨率为:0.1℃,温度波动度:±0.5℃,温度偏差:±2℃,湿度偏差:±3%RH,温度均度:≥湿度均匀度:≥5%RH内部尺寸(mm):1200*920*900mm,外部尺寸(mm):2050*1230*2150mm设备型号:GRS-1000实验室作业文件文件编号实施日期2、操作流程: 面板界面介绍操作图片作业说明2.1、主界面主界面显示包括监视画面、操作设定、定值设定、程式设定、曲线显示五部分2.2监视画面:调出步骤:点击主画面的监视画面即可得左图2,点击下面操作栏中的详细即可得图3。
汽车部件环境类试验验证的方法.

汽车部件环境类试验验证的方法.摘要:汽车在使用中会长期受到严酷的外在环境和气候的影响,导致性能衰减以致失效,影响汽车的使用寿命。
介绍了气候环境对产品性能质量的影响,叙述了汽车部品件在特殊环境下进行适应性模拟试验的验证方法及试验设备的选用,说明了汽车部品件环境类试验在汽车性能优化和提升过程中的重要作用。
今后环境试验方式将更为多样化,虚拟环境仿真试验将成为试验的重点发展方向。
关键词:汽车;环境;性能;部品件;试验汽车部品件质量的优劣直接决定汽车整车的质量,故在新产品研发阶段或者在汽车生产过程中,如果材料和工艺发生变化就要进行部品件型式试验,以确保产品质量。
汽车整车可靠性试验也能考核零部件的质量,但对于多数部品件考核不一定充分,况且耗资大、周期长,这样必须对一些部品件单独做台架试验。
汽车部品件的环境类试验从汽车的研发阶段开始,延续到产品定型、投产和量产后质量提升改进,是一项重要的基础性工作。
文章阐述了汽车部品件环境类试验所需的检测项目以及设备的选择应用。
1汽车部品件环境类试验介绍汽车部品件环境类试验主要是对产品选用的材料、总成及零部件的环境适应性进行试验评价,要求汽车部品件在一定的环境因素和强度下不受损坏或能正常工作,各项功能参数符合设计要求。
试验室部品件试验的要求是根据试验条件正确地确定载荷,进行夹具设计、台架安装、试验及数据处理。
在定型阶段,应进行环境鉴定试验和必要的使用环境试验,验证所设计产品的环境适应性是否满足规定的要求,为定型鉴定提供决策依据;在生产阶段,应进行环境验收试验和环境例行试验,验证产品生产过程的稳定性,为批量生产产品验收提供决策依据;在使用阶段,应开展必要的使用环境试验和自然环境试验,为评价产品的环境适应性提供信息。
如果按照汽车构件来分类,大致可分为汽车电器件试验、底盘件试验、车身及附件试验。
若按照试验种类来分类,可分为耐高低温、湿度试验、耐腐蚀试验、耐振动试验及耐久试验等。
通过试验可以从研发阶段发现汽车设计中存在的缺陷,及时采取纠正和防护措施,从而提升汽车的环境适应能力。
循环交变腐蚀试验方法
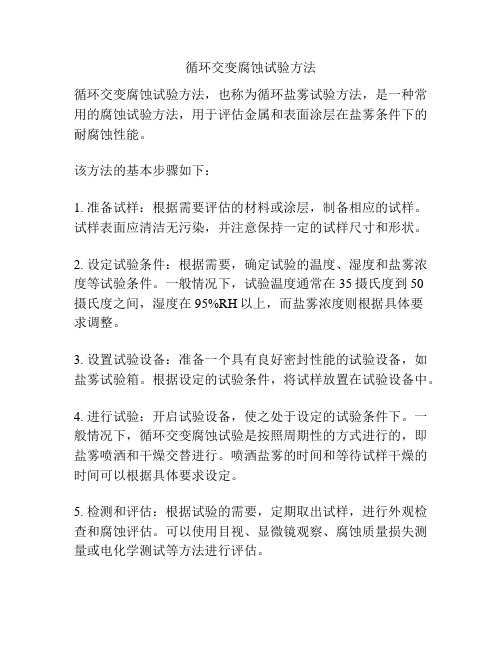
循环交变腐蚀试验方法
循环交变腐蚀试验方法,也称为循环盐雾试验方法,是一种常用的腐蚀试验方法,用于评估金属和表面涂层在盐雾条件下的耐腐蚀性能。
该方法的基本步骤如下:
1. 准备试样:根据需要评估的材料或涂层,制备相应的试样。
试样表面应清洁无污染,并注意保持一定的试样尺寸和形状。
2. 设定试验条件:根据需要,确定试验的温度、湿度和盐雾浓度等试验条件。
一般情况下,试验温度通常在35摄氏度到50
摄氏度之间,湿度在95%RH以上,而盐雾浓度则根据具体要
求调整。
3. 设置试验设备:准备一个具有良好密封性能的试验设备,如盐雾试验箱。
根据设定的试验条件,将试样放置在试验设备中。
4. 进行试验:开启试验设备,使之处于设定的试验条件下。
一般情况下,循环交变腐蚀试验是按照周期性的方式进行的,即盐雾喷洒和干燥交替进行。
喷洒盐雾的时间和等待试样干燥的时间可以根据具体要求设定。
5. 检测和评估:根据试验的需要,定期取出试样,进行外观检查和腐蚀评估。
可以使用目视、显微镜观察、腐蚀质量损失测量或电化学测试等方法进行评估。
循环交变腐蚀试验方法可以模拟一定时间内的盐雾腐蚀环境,通过观察和评估试样的腐蚀情况,从而判断材料或涂层的耐腐蚀性能。
这种方法广泛应用于许多领域,如汽车、航空航天、建筑材料等。
循环腐蚀试验方法 -回复

循环腐蚀试验方法-回复循环腐蚀试验方法(Corrosion Fatigue Test Method)引言:循环腐蚀是一种复杂的腐蚀失效形式,常发生在金属材料在交变载荷作用下经受腐蚀环境的情况下。
为了研究和评估金属材料在这种条件下的耐久性和可靠性,循环腐蚀试验方法被广泛采用。
本文将介绍循环腐蚀试验的一般步骤和关键技术。
第一步:试样准备循环腐蚀试验的第一步是准备试样。
试样的尺寸和形状应根据具体研究对象和要求进行设计。
一般情况下,试样是直立的棒状或板状,有时也可以是环形。
接下来,必须确保试样表面的清洁度。
使用有机溶剂或酸碱溶液可以去除试样表面的杂质和氧化层。
最后,进行试样的防护处理,以防止试样在试验过程中出现不必要的腐蚀。
第二步:试验设计和条件设定在循环腐蚀试验中,试验条件的设定是非常重要的,因为它们直接影响试验结果的准确性和可靠性。
关键的试验参数包括腐蚀介质、腐蚀液的温度、腐蚀液的浓度、施加的载荷类型和幅值以及试验时间等。
试验条件的选择应根据材料的特性、应用环境和预期的失效形式来确定。
第三步:试验装置设置循环腐蚀试验通常需要一套特殊的试验装置。
该装置一般由试样支架、载荷施加装置、腐蚀液循环系统和电位控制系统等组成。
试样支架应具备良好的刚度和稳定性,以确保试样在加载过程中的可靠性。
载荷施加装置可以是压力机、拉伸机或旋转装置,根据试样的形状和载荷类型而定。
腐蚀液循环系统用于将腐蚀液均匀地注入试样周围,以模拟实际应用环境。
电位控制系统用于通过控制试样表面的电位,确保试验中的恒电位条件。
第四步:试验运行和监测在试验运行阶段,试样将经历交变载荷和腐蚀液环境的共同作用。
载荷的加载可以是单轴拉伸、压缩、扭转或复合载荷。
试验过程中应及时监测和记录试样的载荷状态、腐蚀速率和失效形式等。
常用的监测手段包括应变计、电位计和表面观察等。
通过这些监测手段,可以获取试样动态应力-应变响应曲线、腐蚀速率随时间的变化以及失效形式的演化过程。
【技术帖】几种汽车循环腐蚀试验方法对比分析

【技术帖】几种汽车循环腐蚀试验方法对比分析摘要:介绍了汽车循环腐蚀试验机理,并对目前国内几种主要的循环腐蚀试验方法,包括大众汽车标准PV1210、通用汽车标准GMW14872、克莱斯勒汽车标准SAE J2334的腐蚀量进行了对比。
分析了三大循环腐蚀试验标准的差异及其影响因素。
准确把握试验过程中的关键点,将有助于试验更接近户外自然腐蚀状态。
关键词:汽车;金属;腐蚀量;腐蚀速率;影响因素汽车金属零部件的腐蚀破坏已经成为当今影响汽车寿命的重要原因之一。
早在20世纪80年代,美国每年因汽车金属腐蚀所造成的损失就高达200亿美元,因此对汽车抗腐蚀性能的研发显得越来越重要。
腐蚀一般分为2种,即化学腐蚀和电化学腐蚀。
化学腐蚀是指金属表面与非电解质直接发生纯化学作用而引起的腐蚀,这类腐蚀没有水介入;电化学腐蚀则是在电解质和水的共同作用下发生的,反应时产生电流,形成电池。
在电化学腐蚀中,电极电位较负的金属为阳极,阳极失去电子成为金属离子而进入电解液,发生氧化反应;电极电位高的为阴极,阴极接受电子,把电子转移给电解质溶液中的介质离子,发生还原反应,使得电化学反应持续进行。
循环腐蚀模拟的是大气腐蚀,是金属处于表面薄层电解液膜下的腐蚀过程,主要是电化学腐蚀。
根据腐蚀金属表面的潮湿程度可把腐蚀分为“干的”、“潮的”、“湿的”3种类型。
循环腐蚀试验过程中,上述3种腐蚀情况是交替发生的。
腐蚀初期,当金属表面形成了连续的电解液薄膜时,就开始了电化学腐蚀过程,阴极发生了氧的去极化反应。
锈层形成后,处于湿润条件下的铁锈层可以起到强氧化剂的作用。
阳极反应发生在金属/Fe3O4界面上:阴极反应发生在Fe3O4/FeOOH界面上:即锈层内发生了Fe3+→Fe2+的还原反应,锈层参与了阴极反应过程。
当锈层干燥时,即外部气体相对湿度下降时,锈层和底部基体金属的局部电池成为开路,在大气中氧的作用下锈层内的Fe2+重新氧化成为Fe3+,即发生如下反应:因此,在干湿交替的情况下,带有锈层的金属的腐蚀被加速。
汽车零部件耐腐蚀测试研究分析

汽车零部件耐腐蚀测试研究分析车汉生【摘要】本文介绍了汽车零部件的四种耐腐蚀试验,它们的用途、主要特点和评价方法.【期刊名称】《环境技术》【年(卷),期】2011(000)006【总页数】6页(P34-38,11)【关键词】汽车零部件;腐蚀;评价【作者】车汉生【作者单位】广州威凯检测技术研究院【正文语种】中文腐蚀是指材料(通常指金属)与环境间的物理-化学相互作用,其结果是使材料的性能发生变化,并常可导致材料、环境或由它们作为组成部分的技术体系的功能受损伤。
而腐蚀测试则能检验产品的防腐能力,甄别产品的质量,提高产品的竞争能力。
因此,随着全球环境污染日益严重,各类产品的防腐蚀问题越来越受到重视。
汽车零部件的腐蚀测试主要有以下几种:① 盐雾测试(中性盐雾、乙酸盐雾、铜加速乙酸盐雾、交变盐雾)② 冷凝水\水雾试验③ 气体腐蚀试验④ 循环腐蚀试验(CCT)⑤ 腐蚀膏试验⑥ 耐溶剂试验(耐酸碱、汽油等各种溶剂)其中,中性盐雾、冷凝水\水雾、气体腐蚀和循环腐蚀试验是最常用的加速腐蚀试验,在汽车零部件的防腐测试中被广泛使用。
2.1.性盐雾试验汽车零部件的中性盐雾测试标准,主要有以下几种:① ISO 9227-2006② ASTM B 117-2009③ JIS Z 2371-2000④ GMW3286-2006⑤ NES M0140-2001虽然这几个标准规定的中性盐雾试验的参数略有差异,但可以总结为:试验温度:(35±2)℃;氯化钠溶液浓度:(5±0.5)%;溶液pH值:6.5~7.2;盐雾沉降量:1~2mL / h·80cm2;样品放置方式:与垂直方向成15~30°或按正常使用状态放置。
上述标准,对于检测机构来说,需要细致科学严谨地应用,然而对于生产厂家来说,他们更关注的是产品的盐雾测试周期和合格判定。
因此,我将生产厂家的关注点分为以下两点。
2.1.1.试周期中性盐雾试验的测试周期,主要有两种,一种是试验标准推荐的周期,如ISO 9227-2006推荐的试验周期为 2h、4h、6h、8h、24h、48h、72h、96h、144h、168h、240h、480h、720h、1000h。
循环腐蚀试验标准(一)

循环腐蚀试验标准(一)循环腐蚀试验标准一、试验目的循环腐蚀试验旨在模拟实际使用条件下材料或设备在多次疲劳循环下的腐蚀情况,以判断其耐腐蚀性。
二、试验方法试验一般采用盐雾循环腐蚀试验、湿热循环腐蚀试验和干湿交替循环腐蚀试验等方法。
1. 盐雾循环腐蚀试验试验样品放入盐雾试验箱中,循环喷雾高浓度氯离子溶液。
试验周期和具体要求根据不同材料以及使用环境而定。
2. 湿热循环腐蚀试验试验样品放入恒温恒湿试验箱中,采用高温高湿环境循环,具体试验条件根据不同材料以及使用环境而定。
3. 干湿交替循环腐蚀试验试验样品放入恒温干湿交替试验箱中,在干湿交替的环境下进行试验,具体试验条件根据不同材料以及使用环境而定。
三、试验评估根据试验结果,可以进行材料或设备的耐腐蚀性评估。
评估标准一般采用国际标准或行业标准,如ASTM、ISO等。
四、试验注意事项1.试验时应按照试验标准的具体要求进行操作。
2.样品准备应注意防止污染、氧化、划痕等现象。
3.试验过程中需定期检查、记录数据。
4.试验结束后需对样品进行检查、评估并做好保存工作。
五、试验应用循环腐蚀试验是评价材料或设备在实际使用环境下的腐蚀性能的重要方法,广泛应用于航空、军工、汽车、电子、建筑等领域。
六、试验设备和设施循环腐蚀试验需要使用一定的试验设备和设施,例如盐雾试验箱、恒温恒湿试验箱、干湿交替试验箱等。
这些设备和设施必须具有准确的控温、控湿、控制系统等功能,以便准确模拟不同的环境条件,从而获得准确的试验结果。
七、试验数据分析试验结束后,需要对试验结果进行数据分析。
一般采用腐蚀速率、腐蚀程度、腐蚀形态、腐蚀产物、腐蚀机理等参数来评价材料或设备的耐腐蚀性。
通过数据分析,可以评估材料或设备在实际使用环境下的腐蚀性能,并提出改进意见和建议。
八、试验前准备工作为了确保试验的准确性和可靠性,试验前需要做好充分的准备工作,包括试验设计、试验样品的选择和制备、试验设备和设施的校验和维护、试验环境的准备等。
LF8144.1循环腐蚀测试简介
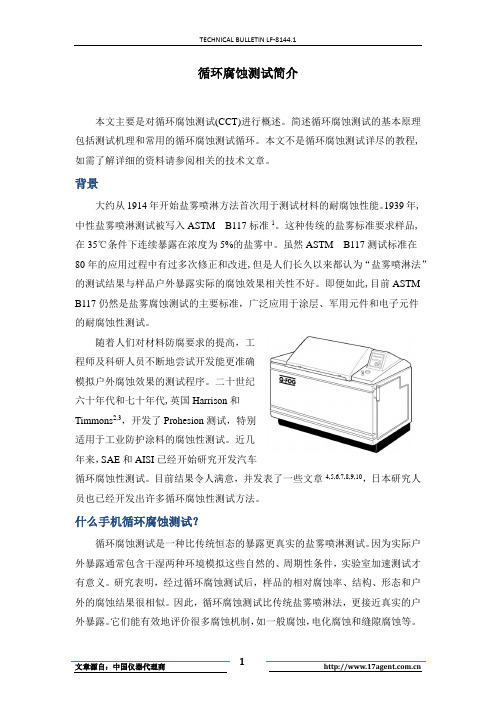
循环腐蚀测试简介本文主要是对循环腐蚀测试(CCT)进行概述。
简述循环腐蚀测试的基本原理包括测试机理和常用的循环腐蚀测试循环。
本文不是循环腐蚀测试详尽的教程,如需了解详细的资料请参阅相关的技术文章。
背景大约从1914年开始盐雾喷淋方法首次用于测试材料的耐腐蚀性能。
1939年,中性盐雾喷淋测试被写入ASTM B117标准1。
这种传统的盐雾标准要求样品,在35℃条件下连续暴露在浓度为5%的盐雾中。
虽然ASTM B117测试标准在80年的应用过程中有过多次修正和改进,但是人们长久以来都认为“盐雾喷淋法”的测试结果与样品户外暴露实际的腐蚀效果相关性不好。
即便如此,目前ASTM B117仍然是盐雾腐蚀测试的主要标准,广泛应用于涂层、军用元件和电子元件的耐腐蚀性测试。
随着人们对材料防腐要求的提高,工程师及科研人员不断地尝试开发能更准确模拟户外腐蚀效果的测试程序。
二十世纪六十年代和七十年代,英国Harrison和Timmons2,3,开发了Prohesion测试,特别适用于工业防护涂料的腐蚀性测试。
近几年来,SAE和AISI已经开始研究开发汽车循环腐蚀性测试。
目前结果令人满意,并发表了一些文章4,5,6,7,8,9,10,日本研究人员也已经开发出许多循环腐蚀性测试方法。
什么手机循环腐蚀测试?循环腐蚀测试是一种比传统恒态的暴露更真实的盐雾喷淋测试。
因为实际户外暴露通常包含干湿两种环境模拟这些自然的、周期性条件,实验室加速测试才有意义。
研究表明,经过循环腐蚀测试后,样品的相对腐蚀率、结构、形态和户外的腐蚀结果很相似。
因此,循环腐蚀测试比传统盐雾喷淋法,更接近真实的户外暴露。
它们能有效地评价很多腐蚀机制,如一般腐蚀,电化腐蚀和缝隙腐蚀等。
循环腐蚀测试的目的是再现户外腐蚀环境的腐蚀类型。
CCT测试把样品暴露于一系列不同条件的循环环境中。
简单的暴露循环,如Prohesion测试,是把样品暴露在由盐雾和干燥条件组成的循环中。
不同腐蚀机理的研究方法

石化设备腐蚀的研究和检测一、环烷酸腐蚀研究方法研究环烷酸的方法主要有实验室试验方法、现场试验方法及分析评价方法三个方面,其中实验室循环模拟试验是今后环烷酸腐蚀研究的主要方法。
影响环烷酸腐蚀的因素很多,主要有环烷酸含量、环烷酸分子结构、硫化物种类和含量、其它工艺或环境介质、操作温度、流速和流动状态、工艺物流相组成(压力)和设备材质等。
1.环烷酸腐蚀的实验室试验方法环烷酸腐蚀的影响因素很多,因此实验室内通常主要考虑主要影响因素如温度、流速、硫含量、材质等进行考察研究。
目前常用的实验室研究方法有静态高压反应釜法、动态高压反应釜法、循环模拟试验法、炉管和转油线模拟试验法等几种。
1.1 静态高压反应釜法静态高压反应釜法的主要设备为不锈钢圆柱体的高压反应釜。
该方法将事先称重的金属试片悬挂在高压反应釜内,然后加热到试验温度,维持一段时间后取下挂片进行处理计算,得到试片的腐蚀速率。
1.2 动态高压反应釜法静态反应釜试验法属于静态试验方法,未考虑流速。
但实际生产过程中介质很少处于静止状态,因此应考虑流速的影响。
动态高压反应釜法从一定程度上弥补了这个缺陷。
动态高压反应釜法的主要设备仍为高压反应釜,但增加了转动功能。
该方法将金属试片固定在高速旋转轴上,浸在环烷酸腐蚀介质中,以每分钟一定转速随轴旋转。
反应釜内的腐蚀介质被加热到试验温度并维持一段时间,然后取下试片处理,计算腐蚀速率。
Pritchard 等开发了一套动态反应釜试验装置,用于测量各种油品在不同流速条件下的腐蚀速度,试验温度可达到400°C,压力可达到70bar,试验装置示意图见图1。
Smart 等采用该装置研究了环烷酸在不同流速状态下的腐蚀行为。
图1 动态高压反应釜环烷酸试验装置示意图1.3 循环模拟试验法循环模拟试验法可以最大程度地模拟现场的温度、压力、流速、流动状态等实际情况,并可以进行喷射冲击等试验,是目前环烷酸腐蚀实验室研究的发展方向。
吴欣强、敬和民等设计并建立了一套模拟工业炼油环境高温高流速状态的循环测试装置,示意图见图2。
- 1、下载文档前请自行甄别文档内容的完整性,平台不提供额外的编辑、内容补充、找答案等附加服务。
- 2、"仅部分预览"的文档,不可在线预览部分如存在完整性等问题,可反馈申请退款(可完整预览的文档不适用该条件!)。
- 3、如文档侵犯您的权益,请联系客服反馈,我们会尽快为您处理(人工客服工作时间:9:00-18:30)。
6.4 测定质量损失
T/CSAE ××-2017
试验结束后,应立即取出参比试样,除掉试样背面的保护膜,使用物理或化学方法去除腐蚀产 物。除锈操作的具体步骤可参考GB/T 10125-2012中5.2.3章节,例如,在23 ℃±2 ℃下于20%±5% (质量分数)分析纯级别的柠檬酸二铵(NH4)2HC6H5O7水溶液中充分浸泡。浸泡后,在室温下用 水清洗试样,再用乙醇清洗,干燥后称重。除锈操作的亦可参考ISO 8407中的规定,例如,用 50%(体积分数)的盐酸溶液(密度1.18 g/mL),其中加入3.5 g/L的六次甲基四胺缓蚀剂,浸泡 试样除去腐蚀产物,之后用清水在室温下清洗,然后再用乙醇清洗,最后干燥。
5.2.2 箱内至少放置两个盐溶液收集器,一个靠近喷嘴,一个远离喷嘴。收集器用玻璃等惰性材料 制成漏斗形状,直径为100 mm,收集面积约80 cm2,漏斗管插入带有刻度的容器中,要求收集的是 盐溶液,而不是从试样或其他部位滴下的液体。
5.2.3 通过喷嘴喷淋的溶液,喷淋量可调,且均匀喷淋在试样上。试验箱的形状和尺寸应能使箱内 溶液的收集速度为:在8.1章节表1的第1步至第3步中的12分钟喷淋时间内,盐溶液平均沉降率在80 cm2的水平面积为39 mL~79 mL。
a) 试样划刻线以外部分的外观,如气泡、生锈、开裂、脱落、粉化、丝状腐蚀等;
b) 试样划刻线部位的外观、划痕层离程度、划痕腐蚀程度等;
c) 质量变化;
d) 显微形貌变化。
7
T/CSAE ××-2017 11 试验报告 11.1 试验报告必须写明采用的评价标准和得到的试验结果。如有必要,应有每个试样的试验结 果,每组相同试样的平均试验结果和试样的照片。 11.2 根据试验目的及要求,试验报告可包括如下内容:
a) 本标准号和所参照的有关标准; b) 试验使用的盐和水的类型; c) 被试材料或产品的说明; d) 试样的尺寸、形状、试样面积和表面状态; e) 试样的制备,包括试验前的清洗和对试样边缘或其他特殊区域的保护措施; f) 覆盖层的已知特征及表面处理的说明; g) 试样数量; h) 试验后试样的清洗方法,如有必要,应说明由清洗引起的失重; i) 试样放置角度; j) 试样位移的频率和次数; k) 试验周期以及中间检查结果; l) 为了检查试验条件的准确性,特地放在试验箱内的参比试样的性能; m) 试验温度; n) 盐雾沉降率; o) 试验溶液和收集溶液的 pH 值; p) 收集溶液的密度; q) 参比试样的腐蚀率(质量损失,g/m2); r) 影响试验结果的意外情况; s) 检查的时间间隔。
5.2.4 试验箱的加热系统应满足在试验的不同阶段,箱内温度达到并保持25 ℃±2 ℃、35 ℃± 2 ℃及50℃±2 ℃的要求。温度测量区应距箱内壁不小于100 mm。
6 设备校验试验 6.1 总则
为了验证不同试验设备之间或不同实验室里同类设备之间试验结果的重现性,应对设备进行验 证试验。试验条件为中性盐雾试验(NSS试验)。
25±2 --
50±2
45±5 --
90±5
温湿度控制 第 3 步至第 4 步,
重复 3 次 温湿度控制
50±2 --
50±2
70±5 --
90±5
温湿度控制
35±2
20±5
每步骤时间 (hh:mm)
0:03
1:57
步骤间 转换
-
线性
--
--
2:00
线性
2:00
线性
--
--
2:00
线性
2:00
线性
转换时间 (hh:mm)
8
T/CSAE ××-2017 附录A 试样划痕的操作规范 1. 准备 1.1 刀具 建议使用Erichsen公司产的型号为463的划痕工具,刀片宽度为0.5 mm。 (划伤后的涂层断面 为矩形切口,微观图片能看出涂层划伤很完整)。
图1 型号463划痕刀具的图片
图2 型号463划痕刀具划痕断面图片
10 结果评价
10.1 试验后试样的处理
将样板从试验箱中取出后,立即用水冲洗试样表面的盐渍、浮锈等污物。对于附着较牢固的锈 迹,可用刮刀将腐蚀物和松动的涂层除掉,之后用布胶带完全贴住划痕线并在该位置牢牢压紧(用 塑料刮板或者大拇指),将余下的末端向下掐断,之后倒拉胶带(与试板成 90 º)。确定真正的腐 蚀宽度 C 和涂层丧失附着力范围的宽度 D,以 mm 为单位。
2 规范性引用文件
下列标准对于本文件的应用是必不可少的。凡是注明日期的引用文件,其随后所有的修改(不 包括勘误内容)或修订版均不适用于本规范,但鼓励根据本规范达成协议的各方研究使用这些文件 最新版本的可能性。
GB/T 10125‐2012 人造气氛腐蚀试验 盐雾试验 GB/T 13452.2‐2008 色漆和清漆 漆膜厚度的测定 ISO 3574 商品级和冲压级冷轧碳素钢板 ISO 4628‐2 色漆和清漆 涂层破坏的评定 一般类型破坏的程度、数量和大小的评定 第2部分: 起泡等级的评定 ISO 4628‐3 色漆和清漆 涂层破坏的评定 一般类型破坏的程度、数量和大小的评定 第3部分: 生锈等级的评定 ISO 4628‐4 色漆和清漆 涂层破坏的评定 一般类型破坏的程度、数量和大小的评定 第4部分: 开裂等级的评定 ISO 4628‐5 色漆和清漆 涂层破坏的评定 一般类型破坏的程度、数量和大小的评定 第5部分: 脱落等级的评定 ISO 4628‐6 色漆和清漆 涂层破坏的评定 一般类型破坏的程度、数量和大小的评定 第6部分: 胶带法粉化等级的评定 ISO 4628‐7 色漆和清漆 涂层破坏的评定 一般类型破坏的程度、数量和大小的评定 第7部分: 丝绒法粉化等级的评定 ISO 4628‐8 色漆和清漆 涂层破坏的评定 一般类型破坏的程度、数量和大小的评定 第8部分: 划痕层离和腐蚀程度的评定 ISO 4628‐10 色漆和清漆 涂层破坏的评定 一般类型破坏的程度、数量和大小的评定 第10部 分:丝状腐蚀等级评定
注:每次清除腐蚀产物时,建议配制新溶液。
试验后的参比试样称重,精确到±1 mg,记做R1。仔细测量参比试样暴露在试验箱中的面积 S,按公式(1)计算得出单位面积质量损失(M)。
R1 R0
M=
S
(1)
6.5 设备校验结果
每块参比试样的单位面积质量损失在70 g/m2±20 g/m2范围内,说明设备校验合格,可以正常 使用。
1
T/CSAE ××-2017 ISO 8407 金属和合金的腐蚀 腐蚀试样中腐蚀产物的清除
3 术语和定义 下列术语和定义适用于本标准。 3.1 划痕层离宽度(Delamination) 划痕处涂层失去附着力的宽度。从划刻线的边缘起到涂层失去附着力最远处的距离。 3.2 划痕腐蚀宽度(Corrosion) 涂层具有可见腐蚀的宽度。从划刻线的边缘起到腐蚀最远处的距离。 3.3 划痕腐蚀深度(Hole) 涂层具有可见腐蚀点,向基材金属纵深发展的深度。
1:27
-1:00 1:00
-1:00 1:30
6
9 试验周期
T/CSAE ××-2017
9.1 试验周期应根据被试材料或产品的有关标准选择。亦可商定解决。
9.2 在规定的试验周期内尽可能不中断试验,只有需要短暂观察试样时,才能打开试验箱,开箱检 查的时间与次数应尽可能少。 9.3 如果试验终止取决于开始出现腐蚀的时间,应经常检查试样。因此,这些试样不能同要求预定 试验周期地试样一起试验。 9.4 可定期目视检查预定试验周期的试样表面,在检查过程中,不能破坏试样表面。
7.8 循环腐蚀试验后,对试样划痕的操作规范见附录A。 8 试验条件 8.1 应根据被试材料或产品选择合适的试验条件。推荐的试验条件见表1。
表1
步骤 第1步 第2步
第3步 第4步
第5步 第6步
试验操作 喷淋
箱体内温度 (℃)
25ቤተ መጻሕፍቲ ባይዱ2
相对湿度 (%)
-
温湿度控制 第 1 步至第 2 步,
重复 4 次 温湿度控制
立即用清洁的压缩空气吹干,在 30 min 内完成对试板或样件的起泡、生锈等现象评价。若在 30 min 内不能完成评价,则把试板或样件放到干燥器中保存,并尽快完成评价。
10.2 试验结果的评价
试验结果的评价见附录 B,通常应由被试材料或产品标准提出,可参考 ISO 4628-2,ISO 4628-3,ISO 4628-4,ISO 4628-5,ISO 4628-6,ISO 4628-7,ISO 4628-8 和 ISO 4628-10 进行 评价,一般试验仅考虑以下几方面:
T/CSAE ××-2017
汽车零部件及材料实验室循环腐蚀试验方法
1 范围
本标准规定了汽车零部件及材料实验室循环腐蚀试验方法。 本标准适用于各类汽车零部件及其材料,包括含金属、金属覆盖层、涂层、镀层及其他转化膜 层等防腐蚀的质量控制、性能验证、工艺验证及产品结构设计验证等过程。 本标准适用于对金属材料具有或不具有腐蚀保护时的性能对比,不适用于对不同材料进行有耐 蚀性的排序。
采用参比试样确认试验设备的稳定性。 6.2 参比试样
参比试样符合 ISO 3574 的 CR4 级冷轧钢板,表面应无缺陷,即无孔隙、划痕及氧化色。表 面粗糙度 Ra 为 0.8 μm±0.3 μm。
参比试样共 6 块,试样尺寸为 150 mm×70 mm×(1 ±0.2) mm。
3
T/CSAE ××-2017 参比试样的称重要精确到±1 mg,记做R0,然后用可剥性塑料膜保护其背面。试样的边缘亦
可用可剥性塑料膜进行保护。 6.3 参比试样的放置
用惰性材料(例如塑料)制成或涂覆的参比试样架,放置试验箱内。 参比试样的布置是在试验箱内四角和其他两个任意位置,共六个不同位置。参比试样的未用塑 料膜保护的一面朝上,并与垂直方向成 20 °±5 °的角度。 参比试样的下边缘应与盐雾收集器的上部处于同一水平面。除非特殊说明,按中性盐雾试验条 件运行试验 48 h。 在验证试验过程中,试验箱中不应有其他样品。