烧成所需设备在硅酸盐工业中称之为窑炉
工业窑炉简介
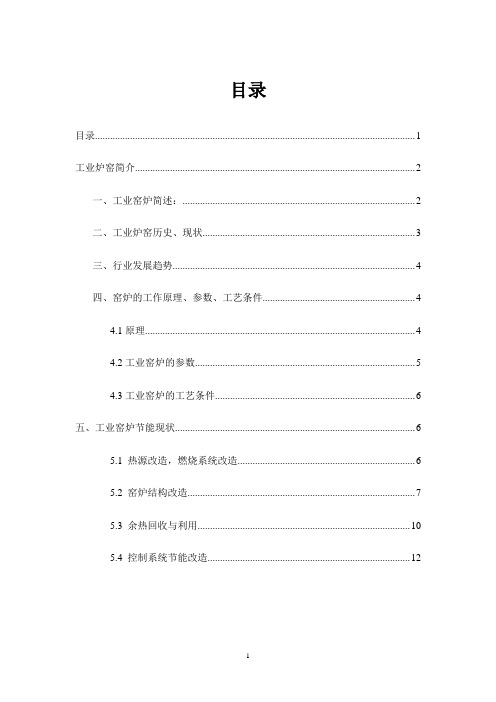
目录目录 (1)工业炉窑简介 (2)一、工业窑炉简述: (2)二、工业炉窑历史、现状 (3)三、行业发展趋势 (4)四、窑炉的工作原理、参数、工艺条件 (4)4.1原理 (4)4.2工业窑炉的参数 (5)4.3工业窑炉的工艺条件 (6)五、工业窑炉节能现状 (6)5.1 热源改造,燃烧系统改造 (6)5.2 窑炉结构改造 (7)5.3 余热回收与利用 (10)5.4 控制系统节能改造 (12)工业炉窑简介一、工业窑炉简述:窑炉是用耐火材料砌成的用以煅烧物料或烧成制品的设备。
按煅烧物料品种可分为陶瓷窑、水泥窑、玻璃窑、搪瓷窑、石灰窑等。
前者按操作方法可分为连续窑(隧道窑)、半连续窑和间歇窑。
按热原可分为火焰窑和电热窑。
按热源面向坯体状况可分为明焰窑、隔焰窑和半隔焰窑。
按坯体运载工具可分为有窑车窑、推板窑、辊底窑(辊道窑)、输送带窑,步进梁式窑和气垫窑等。
按通道数目可分为单通道窑、双通道窑和多通道窑。
一般大型窑炉燃料多为重油,轻柴油或煤气、天然气。
窑炉通常由窑室、燃烧设备、通风设备,输送设备等四部分组成。
电窑多半以电炉丝、硅碳棒或二硅化钼作为发热元件。
其结构较为简单,操作方便。
此外,还有多种气氛窑等。
在具体行业,窑炉还有更多细分类型,如水泥回转窑、玻璃池窑、钢铁的高炉和转炉,化工行业的一些设备也可归为窑炉。
但通常意义上的工业窑炉,范围主要指金属和无机材料的煅烧设备。
窑炉大致分为箱式、井式、梭式、网带式、回转式、窑车式、推板式隧道电阻炉、真空炉、气体保护炉、超高温管式推板炉(碳管炉)、钨钼粉焙烧炉、还原炉等各种高、中、低温工业窑炉,工作温度200~2500℃。
可用于ZnO压敏电阻器、避雷器阀片、结构陶瓷、纺织陶瓷、PTC&NTC热敏电阻器、电子陶瓷滤波器、片式电容、瓷介电容、厚膜电路、片式电阻、磁性材料、粉末冶金、电子粉体、稀土化工、聚焦电位器、陶瓷基板、高铝陶瓷及其金属化,触头材料、硬质合金材料、钨钼材料等的烧成。
陶瓷工艺学第十章烧成与窑具

第四节 窑具
4.1 窑具种类 匣钵、棚板、支柱、各种耐火垫、
托板、辊棒和窑车材料等。
现代窑炉的重要标志之一,就是大幅度 减少了窑具的用量,采用多种高级耐火材料 窑具,满足快速烧成的需要。
4.2窑具的性能要求 (1)足够的结构强度
常温强度和高温强度
(2)良好的抗热震性能 破坏机理:裂纹不断扩展; 热膨胀系数小,产生应力小,不易破坏 熟料和基质的相互关系;相对量的多少 影响较大。
理论温度制度曲线
1400 1200 1000 800 600 400
200
脆性生坯
厚坯 薄坯
热塑性范围
中火保温
脆性瓷器
时间
1.2.2.3 釉烧方法
(1)一次烧成时,釉料的熔化温度与坯料的氧化分解 温度相适应,中火保温防止针孔、橘釉、黑心、鼓泡 等缺陷。 (2)冷却初期依据釉料要求确定冷却速度
光泽釉——快速冷却 结晶釉——结晶温度保温处理 (3)二次烧成 高温素烧低温釉烧:釉烧时可以不考虑坯体的脱 结构水及 氧化分解排气,素烧 时不考虑与釉的关系。 低温素烧高温釉烧:釉烧时可以不考虑 坯体的脱结构 水,要考虑氧化分解,素 烧时不考虑与釉的关系。
不同烧结温度及高温保温时间对产品性能的影响
注:摘自《陶瓷研究》杨世源
烧成温度(℃) 保温时间(min) 平均吸水率(%)
1020
30
16.4
1040
30
15.7
1060
30
14.92
1080
30
14.10
1100
30
13.92
1080
5
14.96
1080
15
14.7
1080
30
工业窑炉概述简介
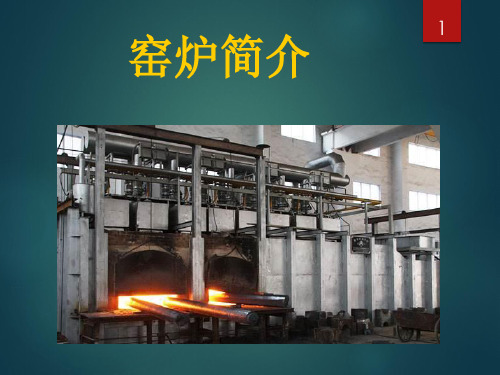
在烧制陶瓷制品时,在温度为200~ 500℃这 一阶段,排除的即为此类结构水(粘土矿物中的结 晶水和层间水),此时分解速度快,制品也不致开 裂。
8
在快速烧成窑中,若坯体干燥(入窑水分<0.5%),脱水温度提
高到700℃,只需几分钟就可以达到完全脱水的程度。
将高岭石的温度再升高,至980℃左右,遂发生放热反应而开 始生成莫来石(3A1203·2SiO2)并发生明显体积收缩。所以应将70% 左右的粘土先行煅烧成熟料,促使其体积稳定后再加工制砖。
16
固相反应是传统硅酸盐材料以及新型无机功能材料生 产过程中的基本反应,它直接影响到这些材料的生产过 程和产品质量。
固体和固体之间反应的特点是反应只在相界面上进行。 首先在相界生成一产物层,接着在相界上继续进行反应。 因此反应物在产物层中的扩散往往成为控制反应速度的 主要因素。
(四) 烧结
17
9
碳酸盐、硫酸盐类矿物在500~1000℃进行分解反应,成为多孔质的
氧化物:
CaCO3 ⎯6⎯00~⎯105⎯0C→ CaO + CO2 MgCO3 ⎯4⎯00~⎯900⎯C→ MgO + CO2 4FeCO3 + O2 ⎯⎯800⎯C→ 2Fe2O3 + 4CO2 Fe2 (SO4 )3 ⎯560~⎯750⎯C→ Fe2O3 + 3SO3 MgSO4 ⎯氧⎯化⎯焰⎯900⎯C,还⎯原焰⎯9⎯00⎯C→ MgO + SO3
如果这种氧化物不需要进一步反应,则这种反应活性是不利的,因为 它们易于水化、碳化,这就需要在更高的温度下烧成更稳定的形态, 如用做耐火材料原料时的情况。
14
陶瓷制品: 碳酸盐、硫酸盐的分解应在釉面玻化以前完成,
工业窑炉的概念

工业窑炉的概念工业窑炉是一种用于加热物体的设备,主要用于加热和处理金属、玻璃、陶瓷、石材等材料,以达到特定的物理、化学或材料学要求。
窑炉的概念涉及到其结构、工作原理、应用领域和分类等多方面内容。
下面将从这些方面详细介绍工业窑炉的概念。
窑炉的结构一般由加热室、加热元件、控制系统和排放系统组成。
加热室一般是一个封闭的空间,用于容纳待加热物体。
加热元件通常是在加热室中产生并传递热量的部件,常见的有电加热元件、气体燃烧器和燃油喷油器等。
控制系统主要负责控制加热温度、时间和其他参数,以保证加热过程的稳定和可靠性。
排放系统则用于排除燃烧产生的废气和废渣。
窑炉的工作原理主要是通过加热元件产生的热量传递给待加热物体,使其温度升高并实现特定的物质变化。
加热室中的空气和燃料在燃烧过程中产生高温气体,这些高温气体通过对流和辐射等方式传递给待加热物体。
在炉内,待加热物体接受到热量后,其内部分子开始运动,产生应力、形变或化学反应,从而实现物质的热处理、熔化或变形等目的。
工业窑炉的应用领域十分广泛,包括冶金、玻璃、陶瓷、石材、塑料、纤维和电子等行业。
在冶金行业,窑炉主要用于金属的熔炼、锻造、淬火和退火等工艺。
在玻璃行业,窑炉则主要用于玻璃的熔化、成型和退火等处理。
在陶瓷行业,窑炉被用来烧制陶瓷制品,如陶瓷器皿、砖瓦和瓷砖等。
在石材行业,窑炉用于石材的烧结、热处理和表面修饰等工艺。
此外,窑炉在塑料加工、纤维制造和电子组装等领域也有广泛应用。
根据不同的加热原理和使用目的,工业窑炉可以分为多个不同的类型。
常见的窑炉类型包括电阻加热窑炉、感应加热窑炉、燃气窑炉、燃油窑炉、煤炭窑炉和太阳能窑炉等。
在电阻加热窑炉中,通过通电的加热元件直接产生热量;在感应加热窑炉中,则利用交变电磁感应产生加热效应。
而燃气窑炉、燃油窑炉和煤炭窑炉则是通过燃料燃烧产生热能。
太阳能窑炉则是利用太阳能对待加热物体进行加热。
不同类型的窑炉适用于不同的加热需求,选择适合的窑炉类型可以提高加热效率和质量。
工业炉窑的节能
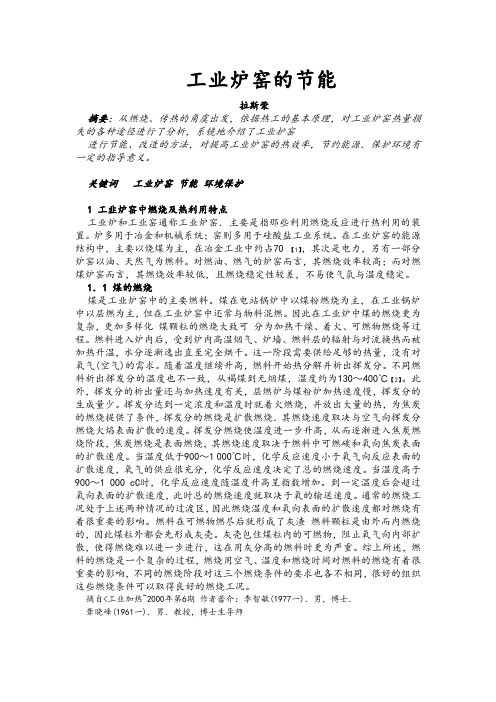
工业炉窑的节能拉斯荣摘要:从燃烧、传热的角虞出发,依据热工的基本原理,对工业炉窑热量损失的各种途径进行了分析,系镜地介绍了工业护窑进行节能、改造的方法,对提高工业炉窑的热效率,节约能源.保护环境有一定的指导意义。
关键词工业炉窑节能环境保护1 工韭炉窑中燃烧及热利用特点工业炉和工业窑通称工业炉窑.主要是指那些利用燃烧反应进行热利用的装置。
炉多用于冶金和机械系统;窑则多用于硅酸盐工业系统。
在工业炉窑的能源结构中,主要以烧煤为主,在冶金工业中约占70 【1】,其次是电力,另有一部分炉窑以油、天然气为燃料。
对燃油、燃气的炉窑而言,其燃烧效率较高;而对燃煤炉窑而言,其燃烧效率较低,且燃烧稳定性较差,不易使气氛与温度稳定。
1.1 煤的燃烧煤是工业炉窑中的主要燃料。
煤在电站锅炉中以煤粉燃烧为主,在工业锅炉中以层燃为主,但在工业炉窑中还常与物料混燃。
因此在工业炉中煤的燃烧更为复杂,更加多样化煤颗粒的燃烧大致可分为加热干燥、着火、可燃物燃烧等过程。
燃料进入炉内后,受到炉内高温烟气、炉墙、燃料层的辐射与对流换热而被加热升温,水分逐渐逸出直至完全烘干。
这一阶段需要供给足够的热量,没有对氧气(空气)的需求。
随着温度继续升高,燃料开始热分解并析出挥发分。
不同燃料析出挥发分的温度也不一致,从褐煤到无烟煤,温度约为130~400℃【2】。
此外,挥发分的析出量还与加热速度有关,层燃炉与煤粉炉加热速度慢,挥发分的生成量少。
挥发分达到一定浓度和温度时就着火燃烧,并放出大量的热,为焦炭的燃烧提供了条件,挥发分的燃烧是扩散燃烧.其燃烧速度取决与空气向挥发分燃烧火焰表面扩散的速度。
挥发分燃烧使温度进一步升高,从而逐渐进入焦炭燃烧阶段,焦炭燃烧是表面燃烧,其燃烧速度取决于燃料中可燃碳和氧向焦炭表面的扩散速度。
当温度低于900~1 000℃时,化学反应速度小于氧气向反应表面的扩散速度,氧气的供应很充分,化学反应速度决定了总的燃烧速度。
当温度高于900~1 000 cC时,化学反应速度随温度升高呈指数增加。
无机材料产品烧成设备概述

第五章 无机材料产品烧成设备概述一、 烧成设备的基本概念硅酸盐制品如陶瓷、耐火材料、水泥、玻璃以及石膏、石灰等一般都是将经过加工处理的原料置于高温下经煅烧反应而制得的。
此高温加工的过程称之为烧成。
烧成所需设备在硅酸盐工业中称之为窑炉。
烧成在硅酸盐工业生产过程中是关键的工序。
制品的产量,质量以及能耗高低在很大程度上取决于烧成工序,即与制品的烧成工艺(温度制度、气氛与压力制度)、窑炉的类型及流程等有密切的关系。
如原料在烧成过程中的物理化学变化、窑炉结构及操作原理、燃料燃烧与炉内传热等,以期达到优质、高产、低消耗和改善操作条件的目的。
1、烧成反应的分类(一) 分解反应(热分解)热分解是由氢氧化物、碳酸盐等所组成的原料,在加热到一定的温度时,逸出其中的水分或CO 2的过程。
分解后所得为无水物或氧化物。
分解反应为吸热反应,分解反有: 高岭石(Al 203·2SiO 2·2H 2O)、水铝石(Al 203· H 2O)、叶蜡石(A12O 3·4SiO 2·H 2O水滑石 (Mg(OH)2)、蛇纹石(3MgO 2SiO 2·2H 2O)、菱苦土(MgCO 3),白云石(CaCO 3·MgCO 3)及方解石(CaCO 3)加热时因脱水或分解出CO 2而呈现的吸热峰。
碳酸盐、硫酸盐类矿物在500~1000℃进行分解反应,成为多孔质的氧化物在以石灰石为主要原料的水泥熟料烧成过程中,由于碳酸盐分解吸热量很大(一般为1800 ~2060kJ /kg 料),分解反应对烧成的速度与热耗影响都很大。
这时,碳酸盐的分解不仅取决于化学反应过程,还受到热量传递和质量传递 (CO 2的扩散)的影响;在只考虑化学动力学过程时,碳酸钙分解速度可用下式表示:2、分解过程的变化分解反应的表面即两相界面,在分解过程中不断缩小,且正比于未分解碳酸钙量的2/3次方,即↑+−−−−−−−−→−↑+−−−→←↑+−−→−+↑+−−−→−↑+−−−→−︒<︒>︒︒>︒︒3900,9004332750~560342232800232900~400321050~60033)(424SO MgO MgSO SO O Fe SO Fe CO O Fe O FeCO CO MgO MgCO CO CaO CaCO C C C C C C 还原焰氧化焰分解反应的表面大小。
工业窑炉简介
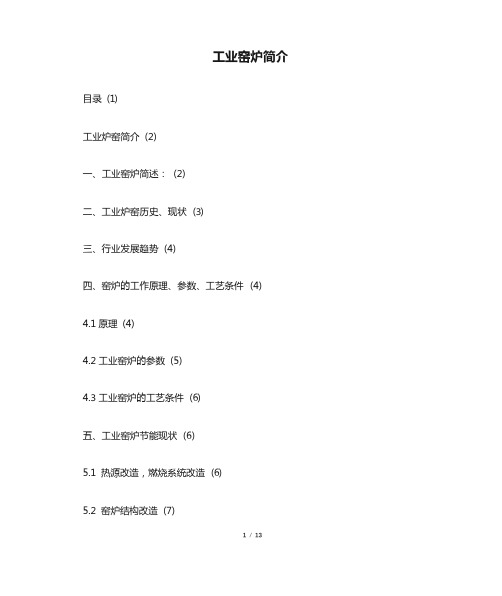
工业窑炉简介目录(1)工业炉窑简介(2)一、工业窑炉简述:(2)二、工业炉窑历史、现状(3)三、行业发展趋势(4)四、窑炉的工作原理、参数、工艺条件(4)4.1原理(4)4.2工业窑炉的参数(5)4.3工业窑炉的工艺条件(6)五、工业窑炉节能现状(6)5.1 热源改造,燃烧系统改造(6)5.2 窑炉结构改造(7)1/ 135.3 余热回收与利用(10)5.4 控制系统节能改造(12)工业炉窑简介一、工业窑炉简述:窑炉是用耐火材料砌成的用以煅烧物料或烧成制品的设备。
按煅烧物料品种可分为陶瓷窑、水泥窑、玻璃窑、搪瓷窑、石灰窑等。
前者按操作方法可分为连续窑(隧道窑)、半连续窑和间歇窑。
按热原可分为火焰窑和电热窑。
按热源面向坯体状况可分为明焰窑、隔焰窑和半隔焰窑。
按坯体运载工具可分为有窑车窑、推板窑、辊底窑(辊道窑)、输送带窑,步进梁式窑和气垫窑等。
按通道数目可分为单通道窑、双通道窑和多通道窑。
一般大型窑炉燃料多为重油,轻柴油或煤气、天然气。
窑炉通常由窑室、燃烧设备、通风设备,输送设备等四部分组成。
电窑多半以电炉丝、硅碳棒或二硅化钼作为发热元件。
其结构较为简单,操作方便。
此外,还有多种气氛窑等。
在具体行业,窑炉还有更多细分类型,如水泥回转窑、玻璃池窑、钢铁的高炉和转炉,化工行业的一些设备也可归为窑炉。
但通常意义上的工业窑炉,范围主要指金属和无机材料的煅烧设备。
窑炉大致分为箱式、井式、梭式、网带式、回转式、窑车式、推板式隧道电阻炉、真空炉、气体保护炉、超高温管式推板炉(碳管炉)、钨钼粉焙烧炉、还原炉等各种高、中、低温工业窑炉,工作温度200~2500℃。
可用于ZnO压敏电阻器、避雷器阀片、结构陶瓷、纺织陶瓷、PTCNTC热敏电阻器、电子陶瓷滤波器、片式电容、瓷介电容、厚膜2/ 13电路、片式电阻、磁性材料、粉末冶金、电子粉体、稀土化工、聚焦电位器、陶瓷基板、高铝陶瓷及其金属化,触头材料、硬质合金材料、钨钼材料等的烧成。
热工设备与工业窑炉期末考试复习总结!
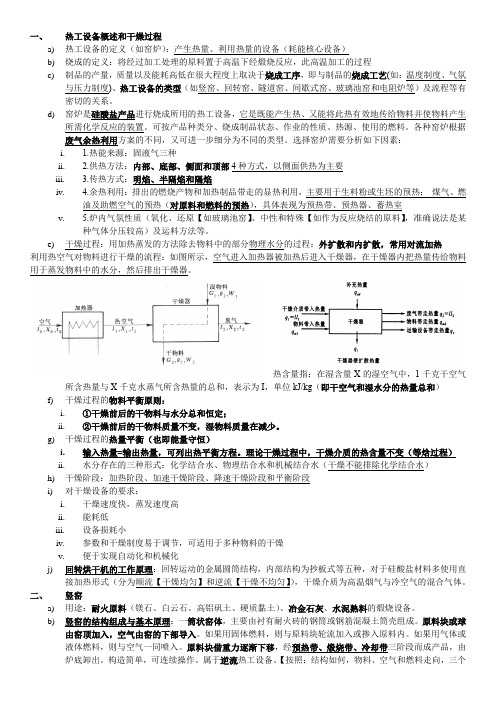
一、热工设备概述和干燥过程a)热工设备的定义(如窑炉):产生热量、利用热量的设备(耗能核心设备)b)烧成的定义:将经过加工处理的原料置于高温下经煅烧反应,此高温加工的过程c)制品的产量,质量以及能耗高低在很大程度上取决于烧成工序,即与制品的烧成工艺(如:温度制度、气氛与压力制度)、热工设备的类型(如竖窑、回转窑、隧道窑、间歇式窑、玻璃池窑和电阻炉等)及流程等有密切的关系。
d)窑炉是硅酸盐产品进行烧成所用的热工设备,它是既能产生热、又能将此热有效地传给物料并使物料产生所需化学反应的装置。
可按产品种类分、烧成制品状态、作业的性质、热源、使用的燃料。
各种窑炉根据废气余热利用方案的不同,又可进一步细分为不同的类型。
选择窑炉需要分析如下因素:i. 1.热能来源:固液气三种ii. 2.供热方法:内部、底部、侧面和顶部4种方式,以侧面供热为主要iii. 3.传热方式:明焰、半隔焰和隔焰iv. 4.余热利用:排出的燃烧产物和加热制品带走的显热利用,主要用于生料粉或生坯的预热;煤气、燃油及助燃空气的预热(对原料和燃料的预热),具体表现为预热带、预热器、蓄热室v. 5.炉内气氛性质(氧化、还原【如玻璃池窑】、中性和特殊【如作为反应烧结的原料】,准确说法是某种气体分压较高)及运料方法等。
e)干燥过程:用加热蒸发的方法除去物料中的部分物理水分的过程:外扩散和内扩散,常用对流加热利用热空气对物料进行干燥的流程:如图所示,空气进入加热器被加热后进入干燥器,在干燥器内把热量传给物料用于蒸发物料中的水分,然后排出干燥器。
热含量指:在湿含量X的湿空气中,1千克干空气所含热量与X千克水蒸气所含热量的总和,表示为I,单位kJ/kg(即干空气和湿水分的热量总和)f)干燥过程的物料平衡原则:i.①干燥前后的干物料与水分总和恒定;ii.②干燥前后的干物料质量不变,湿物料质量在减少。
g)干燥过程的热量平衡(也即能量守恒)i.输入热量=输出热量,可列出热平衡方程。
无机非金属材料热工设备介绍

主要发展方向归纳在以下几点
薄型浮法玻璃生产与加工 建筑用节能玻璃加工应用 功能薄膜玻璃新产品生产加工及应用 薄型防弹、防盗玻璃加工及应用
3.0.2.玻璃概念及生产工艺过程
• 玻璃:由熔融物冷却硬化而得到的非晶 态无金属材料。 • 生产工艺过程
原料的制备 玻璃液的熔制 玻璃产品的成型 玻璃制品的退火及载板
热工设备
2、热工设备:产生热量、利用热量的设备。 代表有窑炉。还有其它设备。
3、窑炉:指某一结构空间,其空间内能够用
加热的方法,按照工艺要求的烧成制度,使
原料经过一系列的物理化学变化变为产品。
n
n
对于一稳定系统,热 量 输 入 = 热 量 输 出
i=1
i=1
热平衡方程,简称热平衡
★对设计窑炉来说:能耗 目的 ★对运转窑炉来说:测量数据的可靠性
1 玻璃熔制部分
1.1 投料部分(投料机、投料池、前脸墙)
(2)投料池
• 投料池的结构:突出于窑池之外和窑池相通的矩形 小池,其上下与窑池池壁平齐,耐火材料品种也相同。
胸墙
大碹
池壁
投料池 池底
1 玻璃熔制部分 1.1 投料部分(投料机、投料池、前脸墙)
正面加料
(b)垄式投料机
(c)振动式投料机
(d)辊筒式投料机
特点(b)料粉成垄状,料层不均匀。 (c)加料面宽,料层薄。
(d)投料连续,平坦均匀。
1 玻璃熔制部分 1.1 投料部分(投料机、投料池、前脸墙)
发展趋势
4
(e)倾斜式投料机
布置:正面加料 特点:连续薄层加料,减少粉尘飞扬,实现液面自
动控制。
1 玻璃熔制部分 2 热源供给部分 3 余热回收部分 4 排烟供气部分 5 锡槽
13窑炉及陶瓷烧成

4. 素烧
干燥后的坯胎,用低温690-1020℃烧成,称为素 烧。目的是增加坯体强度。
5. 釉烧
经素烧后的坯胎,再上釉,经900-1000℃以
上烧成,使釉子全部熔融,成为釉烧。
6. 本烧
上釉的坯体,经高温1100-1320℃一次烧
成,使坯体完全烧结,釉子全部融化,称为本烧。
(二)保温
烧成温度不变,窑内保持一阶段的温度,既 不升温也不降温。
我们可以从“窑”这个字来分析,它是由“穴、
缶”两个部分组合, 穴就是地坑,缶是陶器。
这形象地说明了最初时期是“坑地为窑,复烧
为缶”的。 早在新石器时代,先民们就是这样“坑地为窑” 烧制陶器。其中有横穴和竖穴窑最为典型。 生活在西双版纳的傣族妇女,至今还沿用着这种 原始的治陶方式。
2. 距今6000多年前黄河流域的仰韶文化时期, 从无窑到有窑的烧制使彩陶有了明显的飞跃。
出现最早的是从西安半坡遗址中发现的“竖 穴式窑”或“横穴式窑”。(后又影响到龙山文
化
以及南北各地的陶窑。)
《彩陶船形壶》 (仰韶文化半坡 类型)
彩陶双连壶
仰韶文化时期陶器
《 彩 陶 人( 仰 面韶 鱼文 化 纹半 盆坡 类 》型
)
因为当时用的燃料是植物茎秆和木柴,在烧
造技术上不能完全控制烧成温度和气氛,因此,
梭式窑的特点:
在生产中灵活性大,可随被烧制制品的工艺要求 变更烧成制度; 窑内温度分布比较均匀,容易烧出要求严格的优 质产品; 生产安排灵活,可在周末和节假日停窑休息,烧 成周期短; 窑炉造价低,占地少,基建投资少; 随着制品的加热冷却窑炉温度随之要变,窑体蓄 热损失大,排烟温度高,排烟热损失大,增加了 产品的燃料消耗量。
古瓷器烧造工艺名词解释

古瓷器烧造工艺名词解释三足支钉解释垫具的一种。
使用时三足向下,托面朝上,以便上面放碗、盘等坯件。
这种窑具由于自重小,可以多层叠装;但由于重量往往集中在三足尖上,会使足陷件的底部,留下深深的支钉痕。
这种垫具三国时比较流行。
三角形窑具解释南朝时的一种窑具,用扁平形的泥条,中间作“Y”岔开;前端再转折成直角,作为支点。
轻巧、省料,但由于负重力小,坯件装烧不多。
不(音敦)子解释用瓷石料制瓷,必须将开采来的瓷石用水碓舂细成粉末,再经过淘洗沉淀后,制成砖状的泥块,称之为“石子”或“白不子”。
是瓷石制成砖状后的专用名词,中外陶瓷文献上一致的称谓。
支圈解释支圈窑具始创于宋代定窑,其白度为漏斗形匣钵的五分之一。
用支圈窑具烧一窑瓷,无论是燃料、时间、产量要比使用漏斗形匣钵增加五倍。
为其它瓷窑所仿效。
支钉迭烧解释用高岭土捏成“支钉”,粘于碗盘的圈足边沿,每件9~12颗,然后把瓷坯放在垫柱上,再把粘有支钉的坯件一个个迭起来,组成一柱入窑焙烧,这种方法称支钉迭烧。
支圈迭烧解释宋代的一种烧造方法。
其方法是以泥饼为底,再把瓷泥作成一个断面呈“L”形的圈,套在碗的芒口上;再把碗坯与圈翻过来,覆放在泥饼上。
这样一圈一碗的跟着覆盖,然而将圆心下凹的耐火泥饼覆盖在最后一圈上,形成上下一致的圆柱体,迭装入窑,这种方法叫支圈迭烧。
长石解释是陶瓷生产中一种熔剂性原料。
在成瓷过程中,长石溶融所形成的乳白色粘稠玻璃体。
它在冷却后不再析晶,并能在高温下溶解一部分高岭土分解物与石英颗粒,促进成瓷反应的进行,并可降低烧成温度,减少燃料消耗,这种作用通称为助熔作用。
此外,由于高温下的长石溶剂具有较大的粘度,可以起到高温热塑作用与高温胶合作用,防止高温变形。
同时,冷却后的长石熔体以透明玻璃体状态存在于瓷体中,构成瓷的玻璃态基质增加透明度,提高光泽与透光度,改善瓷的外观质量与使用效能。
长石在陶瓷生产中作坯料、釉料、色料熔剂等,用量很大,作用也很重要。
化妆土解释是一种质地细腻,呈乳白色,用于敷在胎外,以填充胎坯表面的小孔,凹点或其它病疵,使胎面变得光滑;同时能将胎的各种呈色盖住,为坯料开辟广阔的来源。
隧道窑

电热推板窑
WDSJ-0.5/1000型电热升降窑
第四章
隧道窑
• 1、定义:采用轨道窑车输送制品的连续式窑炉 • 2、分类
• 3、隧道窑的特点:
按热源分
分类根据
窑 名
特
点
• 约200℃; 1. 明焰隧道窑 火焰直接进入隧道 • 2)产品冷却之热加热空气,可助燃或作干燥 介质, 按火焰是否 2. 隔焰隧道窑 火焰在马弗道内通过固体辐射传热 进入隧道分 • 产品出窑温度低; 3. 半隔焰隧道窑 隔焰马弗板开有小孔,部分火焰入窑 1. 窑车隧道窑 • 3)连续窑,窑体温度不变,不蓄热,热耗低。
按窑内运 输设备分 2. 3. 4. 5. 6. 推板隧道窑 辊道窑 输送带隧道窑 步进隧道窑 气垫隧道窑
1. 火焰隧道窑 以煤、油或煤气为燃料 1)利用烟气余热预热坯体,废气排出温度低, 2. 电热隧道窑 利用电热元件加热
按通道多少分
1. 单孔隧道窑 2. 多孔隧道窑
推板隧道窑
第一节
形状:普通砖 异型砖
三、不定型耐火材料
• • • • 耐火混凝土, 耐火泥, 耐火喷涂料, 耐火浇注料与捣打料
四、砌窑用隔热材料:λ < 0.14 W/m · ℃。
• • • • 1、轻质粘土砖 2、轻质高铝砖 3、高铝聚轻球砖 4、陶瓷纤维材料
隔热材料
• YK系列轻质隔热砖采用ASTM标准。 • AB系列氧化铝空心球砖是由氧化铝空心 球,氧化铝微粉添加复合结合剂,经振 动成型,高温烧成得制品。 用于1650℃以下工业窑炉炉衬材料。
棚板装烧
2)车架
• 铸铁车架:刚度大,变形小,抗氧化,节约钢材,造价低, • 型钢车架:轻便,易制造,成本高,易变形,铆接成型。
硅酸盐热工设备-水泥窑炉

第五章 无机材料产品烧成设备概述无机材料产品烧成设备一、 烧成设备的基本概念硅酸盐制品如陶瓷、耐火材料、水泥、玻璃以及石膏、石灰等一般都是将经过加工处理的原料置于高温下经煅烧反应而制得的。
此高温加工的过程称之为烧成。
烧成所需设备在硅酸盐工业中称之为窑炉。
烧成在硅酸盐工业生产过程中是关键的工序。
制品的产量,质量以及能耗高低在很大程度上取决于烧成工序,即与制品的烧成工艺(温度制度、气氛与压力制度)、窑炉的类型及流程等有密切的关系。
如原料在烧成过程中的物理化学变化、窑炉结构及操作原理、燃料燃烧与炉内传热等,以期达到优质、高产、低消耗和改善操作条件的目的。
1、烧成反应的分类(一) 分解反应(热分解)热分解是由氢氧化物、碳酸盐等所组成的原料,在加热到一定的温度时,逸出其中的水分或CO 2的过程。
分解后所得为无水物或氧化物。
分解反应为吸热反应,分解反有:高岭石(Al 203·2SiO 2·2H 2O)、水铝石(Al 203· H 2O)、叶蜡石(A12O 3·4SiO 2·H 2O水滑石 (Mg(OH)2)、蛇纹石(3MgO 2SiO 2·2H 2O)、菱苦土(MgCO 3),白云石(CaCO 3·MgCO 3)及方解石(CaCO 3)加热时因脱水或分解出CO 2而呈现的吸热峰。
碳酸盐、硫酸盐类矿物在500~1000℃进行分解反应,成为多孔质的氧化物在以石灰石为主要原料的水泥熟料烧成过程中,由于碳酸盐分解吸热量很大(一般为1800 ~2060kJ /kg 料),分解反应对烧成的速度与热耗影响都很大。
这时,碳酸盐的分解不仅取决于化学反应过程,还受到热量传递和质量传递 (CO 2的扩散)的影响;在只考虑化学动力学过程时,碳酸钙分解速度可用下式表示:2、分解过程的变化分解反应的表面即两相界面,在分解过程中不断缩小,且正比于未分解碳酸钙量的2/3次方,即↑+−−−−−−−−→−↑+−−−→←↑+−−→−+↑+−−−→−↑+−−−→−︒<︒>︒︒>︒︒3900,9004332750~560342232800232900~400321050~60033)(424SO MgO MgSO SO O Fe SO Fe CO O Fe O FeCO CO MgO MgCO CO CaO CaCO C C C C C C 还原焰氧化焰分解反应的表面大小。
工业窑炉

安拓:工业炉的定义工业窑和工业炉统称为工业窑炉。
主要是指那些利用燃烧反应把材料加热的装置,“窑”多用于硅酸盐工业系统,如生产陶瓷、玻璃、水泥等产品的炉子。
“炉”多用于冶金和机械系统,主要用于冶炼和制备钢铁和各种有色金属材料,按用途可分为焙烧炉、鼓风炉、冲天炉、转炉、平炉和坩埚炉等。
窑炉主要是指回转窑,回转窑由筒体、滚圈、托轮、挡轮、传动装置热交换装置、窑头及燃烧室、窑尾、窑头及窑尾密封装置、砌体等部分组成。
会转窑筒体多采用普通钢板焊接而成。
有色冶金中由于工艺过程和气氛的要求,也有个别的窑炉选用锅炉钢板和耐热钢板焊接而成。
对通体的基本要求是应有走狗的刚度与强度。
回转窑生产能力大,机械化程度高,维护及操作简单,能适应多种工业原料的烧结、焙烧、挥发、煅烧、离析等过程,因而被广泛地应用于冶金、水泥、耐火材料、化工等部门。
回转窑按照窑型可分为直筒型、摇头扩大型、窑尾扩大型、两端扩大型四类。
①直筒型:筒体形状简单,制造和安装方便,物料在窑内填充系数一致,移动速度均匀。
②窑头扩大型:燃烧空间大,窑头的的供热能力可以增大,有利于提高产量。
③能增大物料干燥的受热面,便于安装换热器,降低热消耗及烟尘率,多用于湿法加料的窑。
④两端扩大型:兼有以上两种的优点,且中间的填充系数提高,有利于防止料层滑动;但是气流速度加快,增大了烟尘率。
此外,还有扩大高温烧成带的“大度窑”,这种窑在干燥带的能力足够时可显著提高生产能力,但缺点是操作难于掌握。
局部扩大的窑型适用于窑内各段带能力存在明显不平衡时作为调整措施,将热工上薄弱环节的部分扩大,即可获得较显著的强化生产的效果。
就目前国内外新建回转窑的情况看,目前窑型发展的趋势以直筒型为主,且筒体尺寸向大型发展。
总有一天你会渐渐明白,对自己笑的人不一定是真爱,对方表面的伪善是为博取信赖,暗里他可能会伺机将你伤害。
总有一天你会渐渐明白,不是所有人都对你心门敞开,即使你用善良和真心对待,有的人依然会悄悄将你出卖。
工业炉窑和锅炉怎么区分

工业炉窑和锅炉怎么区分
锅炉是利用燃料或其他能源的热能把水加热成为热水或蒸汽的机械设备。
锅的原义是指在火上加热的盛水容器,炉是指燃烧燃料的场所,锅炉包括锅和炉两大部分。
锅炉中产生的热水或蒸汽可直接为工业生产和人民生活提供所需要的热能,也可通过蒸汽动力装置转换为机械能,或再通过发电机将机械能转换为电能。
提供热水的锅炉称为热水锅炉,主要用于生活,工业生产中也有少量应用。
产生蒸汽的锅炉称为蒸汽锅炉,常简称为锅炉,多用于火电站、船舶、机车和工矿企业。
锅炉中的“锅”是指锅炉设备中盛装水和气并承受
压力的部分,它的作用是吸收“炉”放出的热量,把水加热到一定温度和压力(热水锅炉)或蒸发为蒸汽(蒸汽锅炉)。
“炉”是指锅炉设备中燃料与空气发生化学反应产生高温火焰和烟气的部分,它的作用是最大限度地把燃料的热能释放出来,供“锅”吸收。
工业窑和工业炉统称工业窑炉。
工业窑炉主要是指那些利用燃烧反应把材料加热的装置。
“窑”多应用于硅酸盐工业系统,如生产陶瓷、玻璃、水泥等产品的炉子。
“炉”则多用于冶金和机械系统,主要用来冶炼和制备钢铁和各种有色金属材料,按用途可分为焙烧炉、鼓风炉、冲天炉、转炉、平炉、均热炉和坩埚炉等。
锅炉和工业窑炉最大区别在于锅炉有“锅”和“炉”,而工业窑炉只有“炉”。
陶瓷习题及答案

二、填空题(每空1分共23分):1.按照坯料的性能可将陶瓷成型方法分为压制成型、可塑成型和注浆成型三类,其中注浆成型又可分为普通注浆、热压注浆、流延法2. 普通陶瓷的分类依据,常是以概念、用途为标准划分的,按此标准,普通陶瓷可分为日用陶瓷、建筑卫生陶瓷、化工陶瓷。
3.宋代的五大名窑汝窑、定窑、钧窑、哥窑、官窑4.普通陶瓷常用的石英矿物原料脉石英、石英岩、砂岩。
5.钾长石和钠长石相比:前者熔化温度范围宽,高温粘度增大,高温粘度系数降低,在熔融状态下对石英的溶解速度较慢。
6.绢云母质瓷坯的主要原料有绢云母、石英和高岭土,它们在坯料配方中的质量分数范围分别为30-50%、15-25%和30-50%。
7.影响熔融温度范围的因素釉料的组成、细度、均匀程度、烧成温度、烧成时间。
8.粘土按成因分为原生粘土、次生粘土,前者可塑性较差,耐火度较高,杂质含量较低。
9.影响可塑性的原因泥团固液相、泥团固液相的相对数量、吸附离子种类、颗粒的形状、大小。
10.釉料中提高SiO2的含量,可以使釉的成熟温度增大、高温粘度增大、热膨胀系数降低、强度增大;如果提高K2O 的含量,可以使釉的成熟温度增大、高温粘度增大、热膨胀系数降低、强度降低。
11.影响陶瓷制品白度的主要因素是坯釉料化学组成中的氧化铁和氧化铬等着色氧化物。
为缓解这些氧化物的影响一般加入磷酸盐、滑石和氧化钡物质。
12.坯料按成熟温度分为烧成温度、烧结温度。
13. 陶瓷原料按工艺特性分为可塑性原料、非可塑性原料和熔剂性原料,它们在长石坯料的示性矿物组成的质量分数范围分别为%、%和%。
14.泥浆的浇注性能包括流动性、吸浆速度、脱膜性、挺实性、加工性。
15.调节坯料性能的添加剂种类解凝剂、结合剂、润滑剂16.釉料中提高SiO2的含量,可以使釉的成熟温度增大、高温粘度增大、热膨胀系数降低、抗张强度增大;如果提高Na2O的含量可以使釉的成熟温度增大、高温粘度增大、热膨胀系数降低、抗张强度降低。
窑炉的概述

窑炉的概述水泥回转窑属于建材设备类。
回转窑按处理物料不同可分为水泥回转窑、冶金化工回转窑和石灰回转窑。
水泥回转窑是水泥熟料干法和湿法生产线的主要设备。
回转窑广泛用于冶金、化工、建筑耐火材料、环保等工业。
该回转窑由筒体,支承装置,带挡轮支承装置,传动装置,活动窑头,窑尾密封装置,喷煤管装置等部件组成。
回转窑的窑体与水平呈一定的倾斜,整个窑体由托轮装置支承,并有控制窑体上下窜动的挡轮装置,传动系统除设置主传动外,还设置了在主电源中源断时仍能使窑体转动,防止窑体弯曲变形的辅助传动装置,窑头、窑尾密封装置采用了先进的技术,保证了密封的可靠性。
水泥生产过程可概括为”两磨一烧”三大环节,其中”一烧”就是指:生料在回转窑内煅烧成水泥熟料过程。
因此回转窑技术性能和运转状况决定了水泥的质量、产量和成本,是水泥生产中的关键设备。
按入窑生料水分不同回转窑煅烧工艺可分为:湿法生产,半干法生产和干法生产三种,因此水泥窑按此分类即是1.湿法生产:湿法长窑。
特点:可生产质量优越及特种水泥熟料(如:华新窑φ3.5×145m窑等),能耗大。
2.半干法生产:立波尔窑特点:少量生产,仅在北京琉璃河水泥厂等为数不多的厂家使用,处于淘汰状态.3.干法生产:a, 中空窑(含带余热发电的中空窑) 曾是上世纪的生产窑型、能耗大、现在水泥行业已不在使用,但在化工,冶金等他行业仍在大量使用。
b,带悬浮预热器干法窑即预分解窑。
现在水泥生产的主力窑型,这也是我们现在主要的窑型。
国内外现在仍在继续探求更新的水泥煅烧方法,其目的主要是设想不采用庞大笨重的回转窑和高大的预热器框架,使烧成工序在传热效率较高的沸腾状态下进行,以便进一步缩小煅烧设备的尺寸,向体积小、结构简单、生产效率高、热耗低和投资少等方向发展。
为此,设想把生料煅烧成熟料的三个阶段都移出窑外,使生料在沸腾式立窑中,煅烧成熟料。
这种生产方式已经进入实验阶段。
尽管不断出现了各种水泥的生产方式,但人们主要以降低能耗、提高产品质量、设备大型化和实现自动化为原则加以改进,节约能源,综合利用,使其更趋完善。
烧结温度和烧结温度范围的测定实验——烧结炉法

烧结温度和烧结温度范围的测定实验——烧结炉法一、实验目的1.掌握烧结温度与烧结温度范围的测定原理和测定方法;2.了解影响烧结温度与烧结温度范围的复杂因素;3.明确烧结温度与烧结温度范围对陶瓷生产的实际意义。
二、实验原理烧成是陶瓷制品在生产中的重要环节。
为了制定最适宜的烧成条件,必须确切地了解各种陶瓷制品的烧结温度、烧结温度范围以及热过程中的重量变化、尺寸体积变化、吸水率、气孔率及处貌特征的变化,以便确定最适宜的烧成制度,选择适用的窑炉以及合理利用具有温度差的各个窑位。
对粘土类原料而言,在加热过程中坯体气孔率随温度升高而逐渐降低,当粘土坯体的密度达到最大值,吸水率不超过5%,此状态称为粘土的烧结,粘土达到此状态的温度为完全烧结温度,简称烧结温度。
自烧结温度继续升高温度,粘土坯体逐渐开始软化变形,此状态可依据过烧膨胀或坯体表面出现大的气孔或依目力观察有稠密的小气孔出现来确定,达到此状态时的温度称为软化温度(或称过烧膨胀温度),完全烧结温度和软化温度之间的温度范围称为烧结温度范围(简称烧结范围)。
中国科学院上海硅酸盐研究所在制瓷原料的研究中是:以被焙烧的粘土类原料的烧成线收缩曲线开始突然下降,即开始进行急剧收缩时的温度作为玻化温度范围的下限,当收缩进行到转向过烧膨胀的温度称为玻化温度范围的上限。
上限温度与下限温度的区间为玻化范围.该所对陶瓷坯料的研究是以坯料的烧成线收缩和显气孔率来确定的,当显气孔率开始减低到接近于零,即瓷胎密度达到最大,不再吸收水份,这个温度就是瓷胎烧成温度范围的下限,从收缩曲线开始“膨大”时的温度,为烧成温度范围的上限。
实际烧成温度不宜偏于烧成温度范围的上限,以避免有图1 坯体在加热过程中收缩与显气孔率的关系越过烧成范围而发生过烧的危险。
测定烧结温度与烧结范围是将试样于各种不同温度下进行焙烧,并对各种不同温度下焙烧的试样测定其外貌恃征、吸水、显气孔率体积密度,烧成线收缩等情况来确定。
- 1、下载文档前请自行甄别文档内容的完整性,平台不提供额外的编辑、内容补充、找答案等附加服务。
- 2、"仅部分预览"的文档,不可在线预览部分如存在完整性等问题,可反馈申请退款(可完整预览的文档不适用该条件!)。
- 3、如文档侵犯您的权益,请联系客服反馈,我们会尽快为您处理(人工客服工作时间:9:00-18:30)。
,
考虑到分解过程中ΔPCO2 的变化很小, 把它归纳到系数c’项中去,则可得:
= 1- (1- k )
'
3
(6 -1- 3)
反应速度常数k’ 是物料温度、周围环 境CO2分压和颗粒大小等因素的函数。 缪勒 (Muller)根据试验,将温度、原料 因素并入比速率常数k” 中,得到:
6
在快速烧成窑中,若坯体干燥(入窑水 分<0.5%),脱水温度提高到700℃,只需 几分钟就可以达到完全脱水的程度。 将高岭石的温度再升高,至980℃左右, 遂发生放热反应而开始生成莫来石 (3A1203· 2SiO2)并发生明显体积收缩。所 以应将70%左右的粘土先行煅烧成熟料, 促使其体积安定后再加工制砖。
8
800 C
560 ~ 750 C
氧化焰 900 C ,还原焰 900 C
在以石灰石为主要原料的水泥熟料烧成 过程中,由于碳酸盐分解吸热量很大(一般 为1800 ~2060kJ/kg料),分解反应对烧 成的速度与热耗影响都很大。 这时,碳酸盐的分解不仅取决于化学反 应过程,还受到热量传递和质量传递 (CO2 的扩散)的影响; 在只考虑化学动力学过程时,碳酸钙分 解速度可用下式表示:
4பைடு நூலகம்
水滑石
(Mg(OH)2)、 蛇纹石(3MgO 2SiO2· 2H2O)、 菱苦土(MgCO3), 白云石(CaCO3· MgCO3)及 方解石(CaCO3) 加热时因脱水或分解出CO2而呈现的吸 热峰。
5
高岭石在500—650℃左右开始脱水,放 出约14%的水分,生成偏高岭石: A12O3· 2SiO2· 2H2O→A12O3· 2SiO2+2H20 该分解属一级化学反应,温度每升高 100℃, 其分解速度就加快一倍。 在烧制陶瓷制品时,当温度为200~ 500℃这一阶段,排除的即为此类结构水 (粘土矿物中的结晶水和层间水),此时分解 速度快,制品也不致开裂。
式中
13
分解反应所生成的氧化物富于反应活性。 如果这种氧化物立即进一步反应生成所需 化合物,则这种反应活性是有利的,如在 水泥熟料烧成中那样。 如果这种氧化物不需要进一步反应,则这 种反应活性是不利的,因为它们易于水化、 碳化,这就需要在更高的温度下烧成更稳 定的形态,如用做耐火材料原料时的情况。
分解反应的表面即两相界面,在分解过 程中不断缩小,且正比于未分解碳酸钙量 的2/3次方,即
F = c( Y - y)
2 3
式中 Y - - - CaCO3的原始质量; c - - - 比例常数。 y 如果将 Y 用分解程度来表示,则有: = 1 - (1- c ,PCO2 ) 3 (6 - 1 - 2) 式中 - - - 分解率; c - - - 系数。
第六章 无机材料产品烧成设备
硅酸盐制品如:陶瓷、耐火材料、水泥、玻璃 以及石膏、石灰等, 一般都是将经过加工处理的原 料置于高温下经煅烧反应而制得的。此高温加工 的过程称之为烧成。 烧成所需设备在硅酸盐工业中称之为窑炉。 烧成在硅酸盐工业生产过程中是关键的工序。 制品的产量,质量以及能耗高低在很大程度上取 决于烧成工序,即与制品的烧成工艺(温度制度、 气氛与压力制度)、窑炉的类型及流程等有密切的 关系。
k" 1 1 k = ( - ) d k PCO2 Peq
'
(6 -1 - 4)
12
k”---比速率常数, k"=A×exp(-E/RT); dk---颗粒平均直径; Pco2---在试验条件下环境中CO2的分压 (在工业性分解炉内为CaCO3分解出的CO2 的分压与燃料燃烧生成CO2分压之 和); Peq---CO2的平衡分压力。
14
对于陶瓷制品,碳酸盐、硫酸盐的分 解应在釉面玻化以前完成,以便生成的 CO2 SO3体排除干净,否则在釉面玻化 时反应还在进行,气体排不出,就会使 制品起泡,影响制品质量。
15
(二)晶型转换
天然矿物一般均呈低温晶型,烧成时就 会转变成高温晶型。 在转换温度下,有的产生可逆的急剧变 化,如β α型之转换; 有的成非可逆的迟钝型转换。 这些转换伴有显著的体积膨胀或收缩, 如果使用会发生这类变化的原料时,在烧 成过程中,必须使其变成稳定的高温晶型。 石英就是最好的例证。
7
碳酸盐、硫酸盐类矿物在500~1000℃进行 分解反应,成为多孔质的氧化物:
600 ~1050 C 400 ~ 900 C
CaCO3 CaO CO2 MgCO3 MgO CO2 4 FeCO3 O2 2 Fe2O3 4CO2 Fe2 ( SO4 ) 3 Fe2O3 3SO3 MgSO4 MgO SO3
3
(一)分解反应(热分解)
热分解是由氢氧化物、碳酸盐等所组成 的原料,在加热到一定的温度时,逸出其 中的水分或CO2的过程。分解后所得为无水 物或氧化物。分解反应为吸热反应。 见图6-1: 高岭石(Al203· 2SiO2· 2H2O)、 水铝石(Al203·H2O)、 叶蜡石(A12O3· 4SiO2· H2O)、
9
dy = = kFPCO2 (6 - 1 - 1) d 式中 - - - 碳酸钙的分解速度; y - - - 时间后CaCO3 被分解的量; k - - - 分解速度常数
2
PCO - - - CaCO3分解压和气相中 CO 2 分压力之差;
F - - - 分解反应的表面大小。
10
1
原料的配合,成型加工过程,燃料的选 用等也至关重要。 如原料在烧成过程中的物理化学变化、 窑炉结构及操作原理、燃料燃烧与炉内传 热等,以期达到优质、高产、低消耗和改 善操作条件的目的。
2
第一节 烧成反应与煅烧的热工设备
一、烧成反应的分类
(一) 分解反应(热分解) (二)晶型转换 (三)固相反应 (四)烧结 (五)熔融 二、窑炉的分类 三、窑炉参数控制