600MW发电厂热力系统讲义(汽机)
600MW凝汽式机组全厂原则性热力系统计算
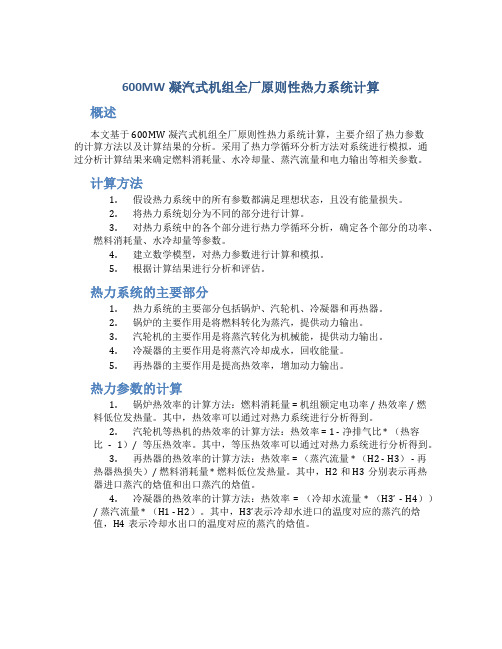
600MW凝汽式机组全厂原则性热力系统计算概述本文基于600MW凝汽式机组全厂原则性热力系统计算,主要介绍了热力参数的计算方法以及计算结果的分析。
采用了热力学循环分析方法对系统进行模拟,通过分析计算结果来确定燃料消耗量、水冷却量、蒸汽流量和电力输出等相关参数。
计算方法1.假设热力系统中的所有参数都满足理想状态,且没有能量损失。
2.将热力系统划分为不同的部分进行计算。
3.对热力系统中的各个部分进行热力学循环分析,确定各个部分的功率、燃料消耗量、水冷却量等参数。
4.建立数学模型,对热力参数进行计算和模拟。
5.根据计算结果进行分析和评估。
热力系统的主要部分1.热力系统的主要部分包括锅炉、汽轮机、冷凝器和再热器。
2.锅炉的主要作用是将燃料转化为蒸汽,提供动力输出。
3.汽轮机的主要作用是将蒸汽转化为机械能,提供动力输出。
4.冷凝器的主要作用是将蒸汽冷却成水,回收能量。
5.再热器的主要作用是提高热效率,增加动力输出。
热力参数的计算1.锅炉热效率的计算方法:燃料消耗量 = 机组额定电功率 / 热效率 / 燃料低位发热量。
其中,热效率可以通过对热力系统进行分析得到。
2.汽轮机等热机的热效率的计算方法:热效率 = 1 - 净排气比 * (热容比- 1)/ 等压热效率。
其中,等压热效率可以通过对热力系统进行分析得到。
3.再热器的热效率的计算方法:热效率 = (蒸汽流量 * (H2 - H3) - 再热器热损失)/ 燃料消耗量 * 燃料低位发热量。
其中,H2和H3分别表示再热器进口蒸汽的焓值和出口蒸汽的焓值。
4.冷凝器的热效率的计算方法:热效率 = (冷却水流量 * (H3’ - H4))/ 蒸汽流量 * (H1 - H2)。
其中,H3’表示冷却水进口的温度对应的蒸汽的焓值,H4表示冷却水出口的温度对应的蒸汽的焓值。
结论根据以上计算方法和分析结果,我们可以得到600MW凝汽式机组全厂原则性热力系统的相关参数。
通过对这些参数进行评估和分析,我们可以有效地提高系统的热效率和动力输出,减少能源消耗。
(完整版)600MW凝汽式机组全厂原则性热力系统计算

1。
本课程设计的目的热力发电厂课程设计的主要目的是要确定在不同负荷工况下各部分汽水流量及其参数、发电量、供热量及全厂性的热经济指标,由此衡量热力设备的完善性,热力系统的合理性,运行的安全性和全厂的经济性.是学生在学习热力发电厂课程后的一次综合性的训练,是本课程的重要环节。
通过课程设计是学生进一步巩固、加深所学的理论知识并有所扩展;学习并掌握热力系统全面性计算和局部性分析的初步方法;培养学生查阅、使用国家有关设计标准、规范,进行实际工程设计,合理选择和分析数据的能力;锻炼提高运算、制图、计算机编程等基本技能;增强工程概念,培养学生对工程技术问题的严肃、认真和负责的态度。
2.计算任务1。
根据给定的热力系统数据,在h—s图上汇出蒸汽的汽态膨胀线(要求出图占一页)。
2.计算额定功率下的汽轮机进汽量D0,热力系统各汽水流量D j。
3.计算机组和全厂的热经济性指标(机组汽耗量、机组热耗量、机组热耗率、机组汽耗率、绝对电耗率、全厂标准煤耗量、全厂标准煤耗率、全厂热耗率、全厂热效率).3。
计算原始资料1。
汽轮机形式及参数(1)机组形式:亚临界、一次中间再热、四缸四排气、单轴、凝汽式机组。
(2)额定功率:P e=600MW.(3)主蒸汽初参数(主汽阀前):P0=16.7Mpa,t0=537℃。
(4)再热蒸汽参数(进汽阀前):热段:P rh=3。
234Mpa,t rh=537℃冷段:P'rh=3.56Mpa,t'rh=315℃。
(5)汽轮机排气压力P c=4.4/5。
39KPa,排气比焓h c=2333.8KJ/kg。
2.回热加热系统参数(1(2)最终给水温度:t fw=274。
1℃。
(3)给水泵出口压力:P u=20。
13Mpa,给水泵效率:83%。
(4)除氧器至给水泵高差:21.6m。
(5)小汽机排汽压力:Pc=6.27kPa。
小汽机排气焓:2422.6KJ/kg。
3。
锅炉型式及参数(1)锅炉形式:英国三井2027-17。
600MW凝汽式机组全厂原则性热力系统计算

600MW凝汽式机组全厂原则性热力系统计算凝汽式机组是一种常见的发电机组,其热力系统是整个机组运行的核心。
本文将对600MW凝汽式机组全厂原则性热力系统进行计算,以探讨其热力性能。
首先,我们需要了解凝汽式机组的基本原理。
在凝汽式机组中,燃煤或燃气的燃料在锅炉中燃烧,产生高温的燃烧气体。
燃烧气体通过锅炉中的热交换器传热给水,将水蒸汽产生。
蒸汽经过扩张机进行膨胀,驱动发电机运转,然后蒸汽进入凝汽器,冷却成水并凝结,然后被泵送回锅炉中进行再次加热。
根据以上原理,我们可以计算600MW凝汽式机组的热力系统。
首先,我们需要确定机组的热效率。
热效率是指机组产生的电能与供给机组的燃料能量之间的比值。
我们可以根据燃煤或燃气的热值和机组的实际发电量来计算机组的热效率。
其次,我们需要计算机组的热损失。
热损失是指机组在能量传递和转换过程中未能被充分利用而流失掉的热量。
机组的热损失可以从锅炉、发电机、凝汽器以及其他相关设备中产生。
我们可以通过测量这些设备的热损失来估计整个机组的热损失。
然后,我们需要计算机组的热功率。
热功率是指机组所能够产生的热量。
热功率可以从锅炉中的蒸汽量以及蒸汽的压力来计算。
我们可以根据锅炉的设计参数以及实际运行数据来计算热功率。
最后,我们需要计算机组的热耗率。
热耗率是指机组所需要的热量与发电机输出的电量之间的比值。
我们可以根据热耗率来评估机组的热利用效率。
综上所述,600MW凝汽式机组全厂原则性热力系统计算涉及到热效率、热损失、热功率和热耗率的计算。
通过对这些参数的计算,可以评估机组的热力性能,并找出可能存在的问题和改进空间,提高机组的热利用效率。
汽轮机600MW汽轮机原则性热力系统设计计算
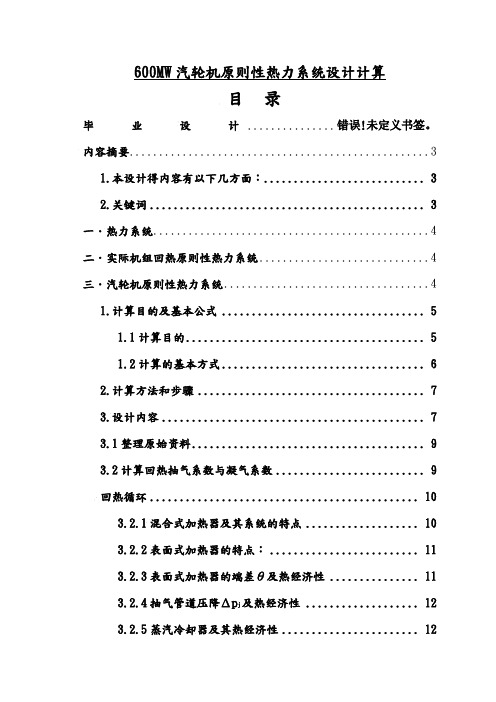
600MW汽轮机原则性热力系统设计计算目录毕业设计............... 错误!未定义书签。
内容摘要 (3)1.本设计得内容有以下几方面: (3)2.关键词 (3)一.热力系统 (4)二.实际机组回热原则性热力系统 (4)三.汽轮机原则性热力系统 (4)1.计算目的及基本公式 (5)1.1计算目的 (5)1.2计算的基本方式 (6)2.计算方法和步骤 (7)3.设计内容 (7)3.1整理原始资料 (9)3.2计算回热抽气系数与凝气系数 (9)回热循环 (10)3.2.1混合式加热器及其系统的特点 (10)3.2.2表面式加热器的特点: (11)3.2.3表面式加热器的端差θ及热经济性 (11)3.2.4抽气管道压降Δp j及热经济性 (12)3.2.5蒸汽冷却器及其热经济性 (12)3.2.6表面式加热器的疏水方式及热经济性 (13)3.2.7设置疏水冷却段的意义及热经济性指标 (14)3.2.8除氧器 (18)3.2.9除氧器的运行及其热经济性分析 (19)3.2.10除氧器的汽源连接方式及其热经济性 (19)3.3新汽量D0计算及功率校核 (23)3.4热经济性的指标计算 (26)3.5各汽水流量绝对值计算 (27)致谢 (32)参考文献 (33)600MW汽轮机原则性热力系统设计计算内容摘要1.本设计得内容有以下几方面:1)简述热力系统的相关概念;2)回热循环的的有关内容(其中涉及到混合式加热器、表面式加热器的特点,并对其具有代表性的加热器作以细致描述。
表面式加热器的端差、设置疏水冷却段、蒸汽冷却段、疏水方式及热经济性、除氧器的运行及其热经济性分析、除氧器的汽源连接方式及其热经济性)3)原则性热力系统的一般计算方法2.关键词除氧器、高压加热器、低压加热器一.热力系统热力系统的一般定义为:将热力设备按照热力循环的顺序用管道和附件连接起来的一个有机整体。
通常回热加热系统只局限在汽轮机组的范围内。
600MW电厂汽机系统图
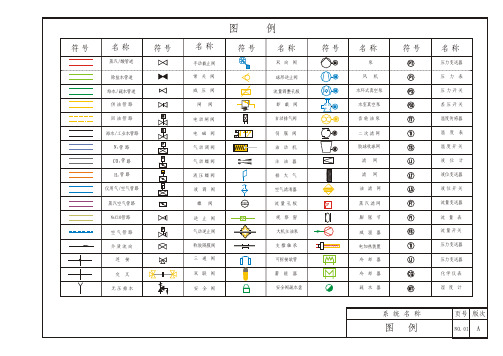
TI TT
PD P
PD P
P
M
P
M
P
P
P
M
M
M
M
P
M
H PD
M H PD
PI
PI
PI
PI
M
TT
轴封蒸汽冷却器
M
TT
M
凝结水系统排水 去有压放水母管
M
MPM
P
P
P
P
P
P
LT
采暖 至闭 至真 轴加 发电 真空 专业 式循 空泵 水封 机定 破坏
至轴封 至小
至低压 至小
供汽高
缸轴封
补水 环水 补水 补水 子冷 阀密
TI
上水泵来
PI
M
TT PT PI
M
M M
除氧器
P M
M
M
PI TI
PD
H
PI PT TT
汽动给水
M
泵前置A
PI FT PI PD PI PT
H
汽泵A
PI
PT M
M
PI TI
PD
H
PI PT TT
汽动给水
M
泵前置B
PI FT PI PD PI PT
H
汽泵B
PI
PT M
M
PI
PD
PI PT TT
锅炉 电动 启动 给水 前置泵
M
四抽来汽
M
至
发
P
M电
机
定
M
子
冷
却
水
箱
至
暖
通
至
用
磨
汽
煤
机
某600MW汽机介绍(含抽汽参数)

第一章汽机概述汽轮机为##汽轮机厂生产的2 台N600-16.7/538/538 型600MW 机组.最大连续出力可达648.624MW.这是##汽轮机厂在引进美国西屋电气公司技术的基础上,对通流部分作了设计改进后的新型机组,它采用积木块式的设计.形式为亚临界参数、一次中间再热、单轴、四缸、四排汽凝汽式汽轮机.具有较好的热负荷和变负荷适应性,采用数字式电液调节〔DEH〕系统.机组能在冷态、温态、热态和极热态等不同工况下启动.N600 汽轮机通流级数为58级.〔1+11,2X9,2X2X7〕第一节汽机系统设备简介汽轮机有一个单流的高压缸、一个双流的中压缸和两个双流的低压缸组成;总通流级数为58级.高中压汽缸为双层缸结构,低压汽缸为三层缸结构,能够节省优质钢材,缩短启动时间.汽机各转子均为无中心孔转子,采用刚性联接,,提高了转子的寿命及启动速度.汽轮机设有一个推力轴承和八个径向轴承.推力轴承为单独的滑动式自位推力轴承.高、中压转子的径向轴承采用四瓦块的可倾瓦轴承,自位性能好.#1 低压转子的前轴承采用两瓦块可倾瓦轴承,这种轴承不仅有良好的自位性能,而且能承受较大的载荷,运行稳定.低压转子的另外三个轴承为圆筒轴承,能承受更大的负荷.主机的润滑油管路采用套装式设计,可有效地防止因高压油泄漏导致的火灾事故发生.该汽轮机采用八级抽汽,分别用于4 台低加、1 台除氧器、3 台高加及小汽机、热网等的加热汽源.N600-16.7/538/538汽轮机采用一次中间再热,其优点是提高机组的热效率,在同样的初参数条件下,再热机组一般比非再热机组的热效率提高4%左右,而且由于末级蒸汽湿度较非再热机组大大降低,因此,对防止汽轮机组低压末级叶片水蚀特别有利.但是中间再热式机组的热力系统比较复杂.每台机组的给水系统配备沈阳水泵厂生产的2 台50%容量的汽动给水泵组和1 台30%容量的电动调速给水泵组.两台汽泵并列运行可满足主机带120%的额定负荷,当一台汽动给水泵和电动给水泵并列运行能满足机组在TRL工况下的给水容量要求,充分地考虑到了机组运行的可靠性和灵活性.凝结水系统为单级泵系统,每台机组设置沈阳水泵厂生产的两台全容量凝结水泵,一台运行一台备用.凝汽器是由##动力设备##制造的双背压、双壳体单流程、表面式凝汽器,采用钛管材,冷却面积为34000m2,可满足机组设计参数的要求.循环水系统采用直流循环供水系统.循环水采用岱海湖水,循环水泵为沈阳水泵厂生产的立式斜流泵,每台机组2 台,冬季工况为1 运1 备,夏季为2 台运行无备用.机组采用开闭结合的冷却水系统,管束管径较大的冷却器采用开式冷却水;对于转动机械的过瓦水和管束管径较小的冷却器采用闭式循环水,这样可在保证设备运行安全的前提下尽量减少闭式冷却水用量,采用较小的闭式冷却水换热器,从而节省了投资.##汽轮机厂生产的N600-16.7/538/538型机组采用积木块式的设计.两台机组共用一套润滑油储存补充装置,节省投资,便于布置.主厂房采用钢结构,并进行了合理优化,在保证电厂运行维护和检修条件的前提下,把主厂房和集控楼的体积合理压缩,适当安排电气和热控设备的地理分散,从而节省管道、电缆和土建三材用量,节省了投资.保证了电厂在整个寿命期内具有良好的经济性.第二节主要技术规范1、额定基本参数结构形式亚临界、一次中间再热、单轴、四缸、四排汽、反动式、冷凝式主汽温度538℃再热汽温度538℃背压11.8kPa〔a〕冷却水温18℃给水温度278.2℃转速 3000r/min旋转方向从汽轮机端向发电机端看为顺时针汽轮机抽汽级数 8级通流级数 58级高压部分级数 I+11级,叶片全部由围带固定中压部分级数2×9级,叶片全部由围带固定低压部分级数2×2×7级,其中前5级叶片由围带固定;次末级叶片为自由叶片;末级叶片由两道拉筋分组固定,为防水蚀叶片.低压缸末级叶片长度 905 mm2、热耗考核工况下各级抽汽参数:。
600MW汽机培训教材(东汽)

正常运行时,给水泵小汽轮机的汽源来自中压缸排汽,小汽轮机的排汽进入主凝汽器。 为了提高经济性,采用了双背压凝汽器。 汽封系统为典型的 SSR 自密封系统。 在额定工况运行时,汽机第 4 段抽汽作为厂用汽汽源。在低负荷时,自动切换至第 2 段抽汽供厂用汽。 3.2 润滑油系统 润滑油系统采用汽轮机主轴驱动的主油泵----油涡轮系统。该系统向汽轮机发电机的 所有轴承提供润滑油,同时还向发电机氢密封系统、盘车齿轮润滑装置供油。汽轮机润滑 油管路为全套装式。 润滑油系统包括下列主要设备: 主油箱及其附件; 主油泵; 交流电动启动油泵;
新蒸汽由炉侧的一根主蒸汽管进入汽轮机前的两根蒸汽管,再进入两个高压主 汽门和四个高压调速汽门,然后进入高压缸。做完功的蒸汽通过高压缸排汽口后经 两根排汽管后汇流到一根蒸汽管导向锅炉再热器,再热热段蒸汽 经一根蒸汽管进入 中压联合阀前的两根蒸汽管,再通过两个中联门进入中压缸,中压缸做功后的蒸汽 沿导汽管直接进入两个低压缸做功。
凝汽器设计为双壳体、双背压、单流程。 汽轮机共有八段非调整抽汽,分别供给三台高压加热器、一台除氧器、四台低 压加热器(#7、#8 低加为内置式)。 汽轮机盘车装置设在低压缸后部#6、#7 轴承盖上,保证转子转动速度 1.5rpm, 以便汽轮机启动和停机时均匀加热和冷却汽轮机转子。 主机控制油系统采用高压抗燃油,与润滑油系统完全分开,提高了调速系统动 作的快速性、可靠性、灵活性。 机组设计为中压缸启动方式,也可用高压缸启动方式。旁路系统采用二级串联 的启动旁路,容量为 40%BMCR。
波变化范围
600mw火电机组全面性热力系统简介

600MW火电机组全面性热力系统简介一、全面性热力系统概述热力系统:根据发电厂热力循环的特征,以安全和经济为原则,将汽轮机本体与锅炉本体由管道、阀门及其辅助设备连接起来的汽水系统。
按照应用目的和编制方法不同,分为原则性热力系统和全面性热力系统。
热力系统图:用特定的符号、线条等将热力系统绘制成的图形。
根据作用不同分为:原则性热力系统和全面性热力系统原则性热力系统:表明热力循环中工质能量转化及热量利用的过程,反映了火力发电厂热功转换过程中的技术完善程度和热经济性。
由于原则性热力系统只表示工质流过时状态参数发生变化的各种热力设备,一般同类型、同参数的设备只表示一个,仅表明设备之间的主要联系,备用设备、管道及附件一般不表示。
原则性热力系统的作用:用来计算和确定各设备、管道的汽水流量,发电厂的热经济指标。
原则性热力系统的组成:锅炉、汽轮机、主蒸汽及再热蒸汽管道和凝汽设备的连接系统;给水回热加热系统;除氧器和给水箱系统;补充水系统;连续排污及热量利用系统;轴封漏汽的回收利用系统。
发电厂全面性热力系统是全厂性的所有热力设备及其汽水管道的总系统,能明确地反映电厂的各种工况及事故、检修时的运行方式。
它是按设备的实际数量来绘制,并标明一切必须的连接管路及其附件。
发电厂全面性热力系统由下列各局部系统组成:主蒸汽和再热蒸汽系统、汽轮机旁路系统、回热抽汽系统。
除氧给水系统、主凝结水系统、加热器疏放水系统、辅助蒸汽系统、凝汽器抽真空系统、冷却水系统等二、全面性热力系统的组成1、主蒸汽与再热蒸汽系统采用单元制主蒸汽系统,主蒸汽管道上布置电动关断门、自动主汽门、调速汽门2、再热机组旁路系统旁路机旁路的类型高压旁路(Ⅰ级)新汽→冷再热蒸汽管道低压旁路(Ⅱ级)再过热后蒸汽→冷凝器大旁路(Ⅲ级)新汽→冷凝器旁路系统的作用(1) 保护再热器(2)协调启动参数和流量,缩短启动时间,延长汽轮机寿命(3)回收工质和热量、降低噪声。
(4)防止锅炉超压,兼有锅炉安全阀的作用。
600MW汽轮发电机结构介绍

600MW汽轮发电机结构介绍汽轮发电机作为一种传统的发电设备,具有高效、稳定和可靠的特点。
它是一种利用燃烧燃料产生高温高压蒸汽,通过透平机械设备的转轮运动,将热能转化为电能的发电机。
下面将详细介绍600MW汽轮发电机的结构。
600MW汽轮发电机主要由锅炉、汽轮机、发电机及其控制系统组成。
锅炉是汽轮发电机组的供汽装置,它负责将燃料燃烧产生的高温高压蒸汽提供给汽轮机。
在600MW汽轮发电机中,常用的锅炉类型有燃油锅炉、燃气锅炉和燃煤锅炉。
燃煤锅炉是最常见和广泛应用的一种锅炉类型,其工作原理是通过煤的燃烧产生高温高压蒸汽。
燃气锅炉则是通过燃气的燃烧产生高温高压蒸汽。
而燃油锅炉是通过燃油的燃烧产生高温高压蒸汽。
无论是哪种类型的锅炉,其目的都是产生高温高压蒸汽以驱动汽轮机发电。
汽轮机是汽轮发电机最核心的组成部分,它是将高温高压蒸汽的热能转化为机械能的装置。
通常,汽轮机的结构包括高压缸、中压缸和低压缸。
高温高压蒸汽从锅炉流入汽轮机的高压缸,通过高速旋转的叶轮将热能转化为机械能。
然后,蒸汽进入中压缸和低压缸,每一级缸都通过叶片转化剩余的热能。
最后,经过低压缸转换后的蒸汽被排入冷凝器冷却,并形成循环。
发电机是将汽轮机转动的机械能转化为电能的装置。
在600MW汽轮发电机中,通常采用同步发电机。
它由转子和定子组成。
转子包括转轴、极和励磁系统,它们通常由高强度的磁钢材料制成。
定子则由定子线圈和铁芯组成,其线圈绕制在定子磁芯上。
通过转子磁场和定子磁场之间的磁场相互作用,电能被产生并输送到电力网络中。
600MW汽轮发电机结构中还包括控制系统。
控制系统负责监测和控制发电机组的运行状态。
它通常由监控系统、过程控制系统和保护系统组成。
监控系统用于监测发电机组的各项参数并显示在控制室内的显示屏上。
过程控制系统负责控制发电机组的开关设备,以保证发电机组的正常运行。
保护系统则负责监测和保护发电机组的安全运行,如过载保护、温度保护等。
600MW火电机组汽轮机热力系统分析
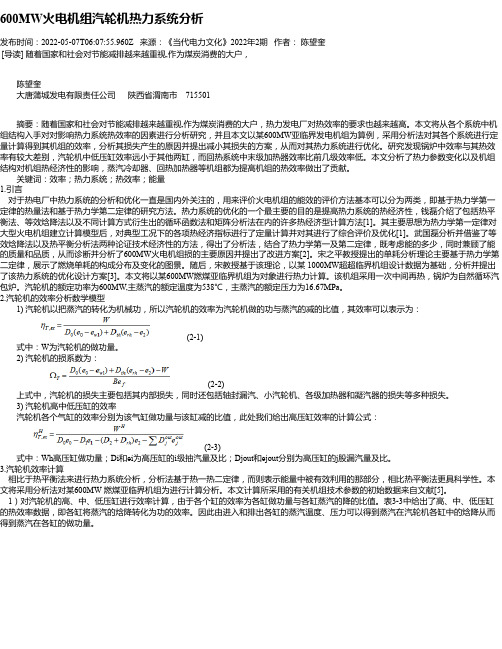
600MW火电机组汽轮机热力系统分析发布时间:2022-05-07T06:07:55.960Z 来源:《当代电力文化》2022年2期作者:陈望奎[导读] 随着国家和社会对节能减排越来越重视,作为煤炭消费的大户,陈望奎大唐蒲城发电有限责任公司陕西省渭南市 715501摘要:随着国家和社会对节能减排越来越重视,作为煤炭消费的大户,热力发电厂对热效率的要求也越来越高。
本文将从各个系统中机组结构入手对对影响热力系统热效率的因素进行分析研究,并且本文以某600MW亚临界发电机组为算例,采用分析法对其各个系统进行定量计算得到其机组的效率,分析其损失产生的原因并提出减小其损失的方案,从而对其热力系统进行优化。
研究发现锅炉中效率与其热效率有较大差别,汽轮机中低压缸效率远小于其他两缸,而回热系统中末级加热器效率比前几级效率低。
本文分析了热力参数变化以及机组结构对机组热经济性的影响,蒸汽冷却器、回热加热器等机组都为提高机组的热效率做出了贡献。
关键词:效率;热力系统;热效率;能量1.引言对于热电厂中热力系统的分析和优化一直是国内外关注的,用来评价火电机组的能效的评价方法基本可以分为两类,即基于热力学第一定律的热量法和基于热力学第二定律的研究方法。
热力系统的优化的一个最主要的目的是提高热力系统的热经济性,钱磊介绍了包括热平衡法、等效焓降法以及不同计算方式衍生出的循环函数法和矩阵分析法在内的许多热经济型计算方法[1]。
其主要思想为热力学第一定律对大型火电机组建立计算模型后,对典型工况下的各项热经济指标进行了定量计算并对其进行了综合评价及优化[1]。
武国磊分析并借鉴了等效焓降法以及热平衡分析法两种论证技术经济性的方法,得出了分析法,结合了热力学第一及第二定律,既考虑能的多少,同时兼顾了能的质量和品质,从而诊断并分析了600MW火电机组损的主要原因并提出了改进方案[2]。
宋之平教授提出的单耗分析理论主要基于热力学第二定律,展示了燃烧单耗的构成分布及变化的图景。
600MW机组主蒸汽、再热汽及旁路系统解析
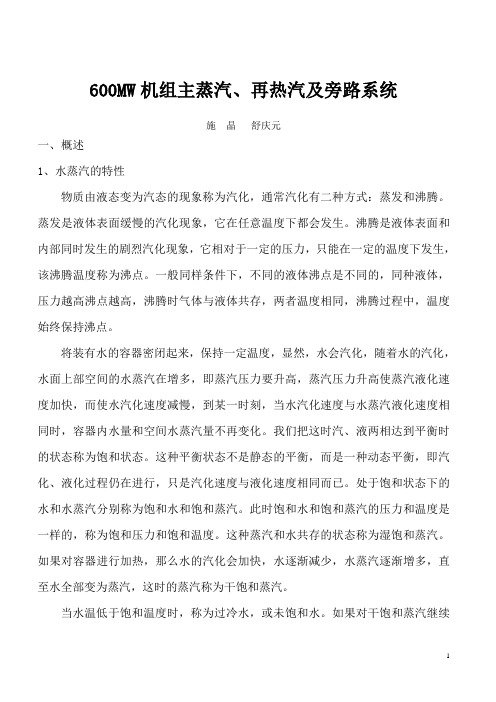
600MW机组主蒸汽、再热汽及旁路系统施晶舒庆元一、概述1、水蒸汽的特性物质由液态变为汽态的现象称为汽化,通常汽化有二种方式:蒸发和沸腾。
蒸发是液体表面缓慢的汽化现象,它在任意温度下都会发生。
沸腾是液体表面和内部同时发生的剧烈汽化现象,它相对于一定的压力,只能在一定的温度下发生,该沸腾温度称为沸点。
一般同样条件下,不同的液体沸点是不同的,同种液体,压力越高沸点越高,沸腾时气体与液体共存,两者温度相同,沸腾过程中,温度始终保持沸点。
将装有水的容器密闭起来,保持一定温度,显然,水会汽化,随着水的汽化,水面上部空间的水蒸汽在增多,即蒸汽压力要升高,蒸汽压力升高使蒸汽液化速度加快,而使水汽化速度减慢,到某一时刻,当水汽化速度与水蒸汽液化速度相同时,容器内水量和空间水蒸汽量不再变化。
我们把这时汽、液两相达到平衡时的状态称为饱和状态。
这种平衡状态不是静态的平衡,而是一种动态平衡,即汽化、液化过程仍在进行,只是汽化速度与液化速度相同而已。
处于饱和状态下的水和水蒸汽分别称为饱和水和饱和蒸汽。
此时饱和水和饱和蒸汽的压力和温度是一样的,称为饱和压力和饱和温度。
这种蒸汽和水共存的状态称为湿饱和蒸汽。
如果对容器进行加热,那么水的汽化会加快,水逐渐减少,水蒸汽逐渐增多,直至水全部变为蒸汽,这时的蒸汽称为干饱和蒸汽。
当水温低于饱和温度时,称为过冷水,或未饱和水。
如果对干饱和蒸汽继续进行加热,使蒸汽温度进一步升高,这时的蒸汽称为过热蒸汽,其温度超过饱和温度之值,称为过热度。
临界点(相变点):一个大气压下的水饱和温度为100℃。
随着压力增加,水的饱和温度也随之增加,汽化潜热(从饱和水加热到干饱和蒸汽所需热量)减小,水和汽的密度差也随之减小。
当压力提高到221.2bar时,汽化潜热为零,汽和水的密度差也为零,该压力称之为临界压力。
水在该压力下加到374.15℃时,即全部汽化,此时的饱和水和饱和蒸汽已不再有区别,该温度称之为临界温度。
600MW组汽机系统图

Q/JFD 嘉兴发电有限责任公司企业标准Q/JFD 1020701.2-2004N600-16.7/538/538-13、4号汽轮机组系统图2005-6-24发布2005-6-24实施嘉兴发电有限责任公司 发布Q/JFD 1020701.2-2004发电机密封油系统T34-01 主蒸汽、再热蒸汽和旁路系统 T34-11 给水系统 T34-22小机轴封、疏水系统 T3-23 闭式循环冷却水系统T34-02 主机轴封系统 T34-12给泵密封水系统 T4-23 闭式循环冷却水系统T3-03 辅汽系统 T34-13小机润滑油系统 T34-24厂内循环水及开冷水系统T4-03 辅汽系统 T3-14小机润滑油系统 T34-25 厂外循环水系统T3-04 凝结水系统 T4-14小机调节油系统 T34-26 循泵冷却及润滑水系统T4-04 凝结水系统 T34-15电泵润滑油系统 T34-27 循泵油系统T3-05 凝结水输送水系统 T34-16主机润滑油系统 T34-28 汽机房仪用空气系统T4-05 凝结水输送水系统 T3-17主机润滑油系统T3-06 汽机抽汽系统 T4-17汽轮机润滑油净油系统T4-06 汽机抽汽系统 T3-18汽轮机润滑油净油系统T34-07 高加疏水、放气系统 T4-18T34-08 低加疏水、放气系统 T34-19 EH油系统发电机定子冷却水系统T34-09 凝汽器疏水回收系统 T3-20发电机定子冷却水系统T3-10 凝汽器真空系统 T4-20T4-10 凝汽器真空系统 T34-21发电机氢气控制系统注:T3为3号机,T4为4号机。
T34为3、4号机通用。
国电都匀项目600MW级汽机专业讲义

通过这次优化,在凝汽器背压不变情况下,
600MW汽轮发电机组的热耗由7595kJ/kW.h 降为7583kJ/kW.h,折合发电煤耗下降 0.44g/kW.h。
2009年5月6日,在福泉市召开《都匀发电有
限公司前期工作汇报会》。会上提出煤耗需 要降低3g/kW.h。我们的机组优化的技术指标 达不到要求。同时提出: 汽轮发电机组单机容量由600MW/台改为 660MW/台。
4. 冷却塔考虑因素 (1)造价 (2)占地面积 (3)冷却塔处循环水提升高度,影响厂用电率
冷端系统优化结果:
1.冷却塔面积8500m2,并对冷却塔配水方式、 填料厚度优化设计。 2.凝汽器面积41000m2 3.循环水管径为DN3200、循环水倍率为 55/46.75倍 4.在大气平均温度为14.7℃,THA工况下,凝 汽器背压5.5kPa,汽机对应热耗 7514kJ/kW.h,主蒸汽流量1875t/h
汽轮机启动方式比较
东汽机组主要采用中压缸启动的能力,也可高中压 缸联合启动。哈汽厂机组可以采用高中压缸联合启
动或高压缸启动方式,比较灵活,汽机旁路推荐采 用30%容量。上汽厂启动方式采用高中压缸联合启 动汽机旁路推荐采用30%容量。 汽轮机启动时间东汽最短,上汽次之,哈汽最长。 东汽机组设置有高压缸预暖系统,而上汽和哈汽机 组没有高压缸预暖系统。
2.凝汽器背压:由5.9kPa(a)降低为 5.5kPa (a) 3. 再热系统压损由10%降为7% ,中压缸进汽 压力提高 汽轮机各段抽汽压损如下:1、2、3段抽汽压 损3%,4~8段抽汽压损4% (原来5%)。 4.小汽轮机效率由80%提高到82% 。
600MW汽轮机最终协议
通过准备,2009年7月31日,我方与东 汽在西南电力设计院就有关技术协议内容进 行了修改。 1. 国电都匀发电有限公司机组单机容量由 600MW增容为660MW。 2. 汽轮机THA(额定工况)热耗由 7595kJ/kW.h降为7514kJ/kW.h。全厂机组 发电煤耗降低2.99g/kW.h。
600MW发电机构造原理等讲义(一期及故障)

定子
机座内汽端的风路隔板与转子风扇、导风环、冷却器等构成 氢气循环和热交换通路。在机座的励端下部,装焊有把合出 线盒的底座,在机座的汽端上、下部,各装焊有装配氢气冷却 器的底座。位于机座下部的出线盒底座和冷却器底座同时又 作为定子运输时挂货钩的钩挂位置。 此外,在机座的上部开设有夹紧环调节人孔,下部开设有清 理孔及充排氢气、二氧化碳的管路接口及漏水探测器管路接 口。在机座的两侧开设有供测温元件引出端子板的安装孔, 而发电机的定子冷却水汇流管的进出法兰均设在机座的上部。 排污法兰设在机座下部。 定子机座两侧的底脚将支撑整个发电机的重量,它们具有足 够的强度和刚度。在靠近机座中心处两侧的底脚上开设有轴 向固定键槽,以装配机座与座板间的轴向固定键,机座两侧 共设有4个吊攀。
定子
2、 定子铁芯 定子铁芯(见图6)由涂有耐高温的磷酸铝无机绝缘的 高导磁、低损耗的0.45mm(0.018in)厚扇形硅钢冲片 叠装而成沿圆周分布10.5片冲片。定子槽数为42槽。 定子铁芯通过装焊在机座内夹紧环上的42根定位螺 杆与机座的隔振结构件相连接。铁芯的两端设有无 磁性铸钢齿压板。在齿压板的外侧设有硅钢冲片叠 装成的磁屏蔽,磁屏蔽内圆表面为阶梯形多齿表面, 以有效地分导定子端部的轴向漏磁通,防止主铁芯 过热。在磁屏蔽的外侧设有无磁性铸钢分块压板。 铁芯轴向紧固由定位螺杆及42根高强度无磁钢圆(直 径32mm)制成的绝缘穿心螺杆以及齿压板和分块压 板来实现。穿心螺杆的紧固,经液压拉伸器拉伸后 再紧定螺帽,使铁芯受压均匀,其轴向压力为 1.37×105Pa。
600MW汽轮发电机 结构原理简介
2008年7月10日
概述
我公司发电机为哈尔滨电机厂引进美国西屋技术的国产首台600MW汽轮 发电机,机组型号为QFSN-600-2型汽轮机直接拖动、隐极式、二极、 三相同步汽轮发电机。发电机冷却方式为水-氢-氢,采用无刷励磁系 统。 水氢氢冷却方式:定子线圈(包括定子引线)直接水冷、转子线圈直接 氢冷(轴向通风冷却),定子铁心氢冷。发电机采用密闭循环通风冷却, 机座内部的氢气由装于转子汽轮机端轴上的多级高压轴流式风扇驱动。 轴承为强迫润滑(由汽机润滑油系统供油)。 发电机配有氢油水控制系统,以提供和控制发电机冷却用氢气,密封油 和定子线圈冷却用水。 发电机型号表示意义: Q-汽轮机拖动 F-发电机 S-定子绕组水冷 N-转子绕组氢内冷 600-额定容量 2-两极
- 1、下载文档前请自行甄别文档内容的完整性,平台不提供额外的编辑、内容补充、找答案等附加服务。
- 2、"仅部分预览"的文档,不可在线预览部分如存在完整性等问题,可反馈申请退款(可完整预览的文档不适用该条件!)。
- 3、如文档侵犯您的权益,请联系客服反馈,我们会尽快为您处理(人工客服工作时间:9:00-18:30)。
600MW发电厂热力系统第一章 600MW机组热力系统总的介绍第一节概述火力发电厂的生产过程,从能量的观点看,就是能量的转化和转移的过程,即:燃料化学能→热能→机械能→电能,以下重点从能量的角度介绍一下火力发电厂的生产过程。
煤场的煤经碎煤机处理后由皮带输送至煤仓间原煤斗,在磨煤机的研磨作用下变成煤粉,被一次风携带至锅炉各层燃烧器,喷入炉膛,二次风则提供燃烧所必须的氧气,组织良好的燃烧,产生高温烟气。
这一过程是燃料的化学能转化为热能的过程。
锅炉内的工质吸收燃料燃烧所释放的热能,在锅炉受热面中不断被加热,从不饱和水变为高温过热蒸汽。
这一过程是能量的转移过程,即炉内的热能由辐射,对流等形式传给炉内的工质。
具有一定能量的过热蒸汽进入汽机高缸,对高缸转子做功使之转动。
这一过程是能量的转化过程,蒸汽的热能转化为转子的机械能。
高缸的排汽(冷再)进入锅炉的再热器,吸收烟气热量之后引入汽机中,低压缸做功,完成能量由化学能向中,低压转子机械能转化的过程。
具有一定动能的汽机转子带动发电机转子,产生旋转磁场,最终以电流形式由定子线圈输出,经主变送往线路。
这一过程完成机械能向电能的转化。
在上述的能量转化过程中,存在各种能量损失,有锅炉损失,管道损失,冷源损失,汽机损失,机械损失和发电机损失。
在以上损失中,各项所占比例不相同,冷源损失最大,相对应的循环热效率也最低,只有40%多,因此全厂的总效率也只有30%多。
但是从运行的角度可以通过采取各种方法,减小各项损失,达到机组优化运行,降低供电煤耗率的目的。
以下,对工质在热力系统中的循环过程作一简单介绍。
低压缸排汽被循环水冷却后,凝结成水,汇集至热井,经过凝泵升压,进入除盐装置,除去凝水中的盐份。
除盐装置出口至轴封加热器,利用轴封汽回汽对凝水加热,再到除氧器水位调节站,控制除氧器水位的稳定。
再依次经过#8,#7,#6,#5低加,对凝水加热,之后进入除氧器。
除氧器也是一加热器,一是对凝水加热,二是除去水中的溶氧,防止设备的腐蚀。
除氧器底部接有给水泵吸入管。
给水泵有两台各为50%容量的汽泵和一台容量为30%的电泵。
给水经过泵的升压之后,依次经过#3,#2,#1高加,最后被加热至272℃,进入锅炉省煤器。
在凝水及给水回路中,采用抽汽回热系统,高低加的热源为汽机的各级抽汽,目的是提高循环热效率及经济性。
给水进入省煤器被烟气加热,由三根管道进入汽包,进行炉水循环。
炉水循环的作用是使炉水吸收炉辐射热,产生饱和蒸汽,并且可以保证受热面的安全。
饱和汽离开汽包进入过热器,在过热器中继续吸收炉的辐射热和烟气对流热,形成过热蒸汽,经高压主汽门和调门进入高缸,推动高压转子。
高缸排汽回到再热器继续加热,此过程可提高循环的热效率。
再热器出口蒸汽引至中,低压缸做功,做完功的排汽由低缸排至凝器。
至此,完成一个工质的热力循环。
工质在循环过程中不可避免要产生一些损失,如连排,定排,除氧器排汽等,这就需要对工质补充。
我厂的补水管接在凝器,水源为大水箱除盐水,通过补水,可以保证凝器水位的正常。
第三章 600MW机组热力系统汽机部分第一节主汽、再热蒸汽系统1.1系统作用主、再热蒸汽系统为汽轮机提供新蒸汽和再热蒸汽,并将新蒸汽、再热蒸汽的一部分热能转变为机械能。
另外,该系统还作为一部分用户的汽源。
如小机的高压汽、辅汽、轴封系统等。
1.2 系统的组成及流程1.2.1系统的组成主、再热蒸汽系统由主、再热蒸汽管道,高、中、低压缸以及管道上的阀门测点等组成。
1.2.2系统的流程1.4系统及辅机隔离措施正常运行中,主、再热蒸汽管道泄漏,一般都进行申请停机处理。
个别情况,可降负荷,带压堵漏,有条件时进行彻底处理。
该系统管道上的疏水系统隔离也较困难,一方面系统处于高压状态,阀门不一定关得严。
另一方面因疏水至扩容器,若阀门关得太严,可能泄漏真空,影响机组安全,但对再热器管道上的液位开关,有可能关闭其隔离阀进行隔离。
1.5主、再热蒸汽系统中设置再热蒸汽系统的原因①热力发电厂生产过程的实质是将燃料中的化学能,经热能的释放、传递,工质的迁移和热功转换等过程最终转变为电能。
在这些能量转换的过程中,总有数量不等。
原因不同的各项损失,如:锅炉损失,管道损失,冷源损失,汽轮机内部损失,发电机损失等,使得燃料中的化学能只有一部分转变为电能。
要提高发电厂的热经济性,设置再热蒸汽系统是一个有效的办法。
再热参数选择合理,可提高整个热循环的平均吸热温度,相应增加循环热效率。
通常再热温度提高10℃,循环热效率可提高0.2%~0.3%,采用一次中间再热,可使得机组的热经济性约提高5%左右。
②主蒸汽通过高、中、低缸做功后,在后几级,随着压力和温度的下降,一部分蒸汽凝结成水,使蒸汽温度增大,湿蒸汽中的水珠打在叶片上,使该处受到冲蚀,叶片表面将被冲蚀成许多密集的细毛孔,严重者造成叶片缺损,严重威胁汽轮机的安全,采用中间再热系统,降低了后几级的蒸汽温度,使汽机后几级叶片的安全得到了保证。
综上设置中间再热系统的原因有三个,一是提高机组的经济性,二是提高汽轮机未级的蒸汽温度。
使之在允许的范围内,三是汽耗率降低。
1.6我公司汽机本体的简介1.6.1主要规范型式:亚临界中间再热,单轴四缸四排汽冷凝或高中压缸分缸。
中压缸和二只低压缸都是分流布置。
级数:计57级。
高压缸:1级冲动级+10级反动级=11级中压缸:2×9级反动级=18级低压缸:2×2×7级反动级=28级末级叶片长度:869mm(#1机)/1000 mm(#2机,经过通流改造)低压缸排汽面积4×7.11m2(#1机)汽轮机额定转速:3000r/min临界转速高压 1760 r/min中压2170 r/min低压1700 r/min超速跳闸转速 111%额定转速汽轮机长度:31m最大宽度:9.146m重量:1123吨机组计8级抽汽即三高、四低、一除氧。
1.6.2汽缸介绍高压缸:内外缸采用合金钢铸造,采取双层缸布置,其特点较单层缸随的蒸汽压力分摊内外层缸,可减少汽缸厚度和法兰尺寸,内缸水受高温,内外缸共同承受压力,内外缸之间有蒸汽流动。
中压缸:合金钢铸件,水平中分成上、下缸,双层结构,内缸支撑前五级静叶栅,外缸支撑后四级静叶栅。
低压缸:分三层缸,一个外缸,两个内缸,第一个内缸装低压前五级,第二个内缸装低压后二级。
三个缸承受的排汽温度分别为高压缸:224℃,中压缸200℃,低压缸303℃。
1.6.3进汽部分高压缸进汽设两个主汽门,分别对应用2个调节汽门。
中压缸进汽设两个中压主汽门,分别对应用2个中压调节汽门。
中压缸排汽通过连通管直接与低压缸相连。
整个机组共有11个轴承;整个机组滑销系统主要由纵销、横销、立销和猫爪压板销组成。
1.7 汽轮机本体特点1.7.1 整机设计特点整机采用积木块(BUILDING BLOCK)式设计原则。
主机由BB034(单流高压部分)、BB051(双流中压部分)和两个BB074(双流低压部分)四个积木组成。
配套设备也大都是组装式结构:如EH油系统、润滑油系统、发电机冷却水系统、高压主汽门及调速汽门、中压主汽门及调整汽门等都是组合成一体,独立布置。
由于采用积木块设计原则,有效的解决了产品的通用化、系列化和标准化的问题,对制造、安装和使用都比较方便。
1.7.2汽缸、转子和通流部分的特点1、高中压汽缸都采用双层缸结构,高压内外缸夹层有少量来自调节级后的漏汽流过,中压内外缸夹层间有少量来自反流第5级后的蒸汽流过,以冷却汽缸进汽部分的高温区。
设计上考虑内缸的内外侧温差较小,压差较大,主要承受压应力。
而外缸内外侧温差较大,压差较小,主要承受热应力,温差大的缸体压差较小,因而可采用较簿的外缸壁,较小的法兰。
加之,内外缸水平中分面螺栓靠近缸壁中心线,使缸壁与法兰厚度差别减少,汽缸、法兰、螺栓都容易加热,所以对法兰、螺栓等未采取加热或冷却措施。
此外,由于上、下汽缸结构基本对称,形状比较简单,尤其是内缸尺寸较小,所有静叶片组成的隔板都安装在隔板套(静叶环)上,结构的这些特点,使汽缸在机组启停和运行中,热膨胀比较均匀和自由,减少了汽缸的热应力和热变形,又给制造带来了方便。
2、低压缸虽然压力、温低较低,但进汽与排汽温差最大(303℃),为减少缸壁的温度梯度,所以也遵循高温设计原则,采用了多层缸钢板焊接结构,在进汽部分设计成三层缸,通流部分为二层缸,以减少汽缸的应力和变形。
3、通流部分除调节级采用冲动级外,其他均为反动级。
但高中压缸静叶环采用类似冲动式汽轮机的隔板结构,并没有弹性汽封,减少级间的漏汽损失。
反动级动、静叶片型线的进汽边,采用了对进汽角度变化范围适应性较大的大园弧进汽边的叶型。
这种出汽边薄,进汽边园弧半径大的厚叶片,具有良好的汽动性能,同时在较小的进汽角和进汽角在较宽范围内(65--95°)变化时,仍具有良好的汽动性能。
故即使在级数少,速比较低的情况下,仍能保持相当水平的效率。
这样,就使得本汽轮机的级数比典型的反动式汽轮机少得多,结构较为简单。
4、除低压缸的最后三级动叶和二级静叶片采用变截面的扭叶片外,其余各级动静叶片全部采用等截面直叶片。
为使高、中压最后几级叶片的径高比大于8,满足采用直叶片的条件,对机组效率不致影响过大。
高、中压缸通流部分的囝向流道,均设计成斜通道结构,既转子的根径沿汽流流动方向逐级增大,且静叶和动叶根部及顶部的流道与轴向成一定的倾斜角度一致,外侧仍与转轴的轴线保持平行。
这样转子围带的制造复杂一些,但叶片制造较为简单,而且可使叶片通道轮廓平滑,提高通流部分的效率。
为防止低压末级叶片水冲刷,在其进汽侧加焊有硬质合金防防磨片。
5、除末叶片用拉筋连接,次末级为自由叶片外,其他各级动、静叶片均设有围带和叶根的径向汽封。
整个流通部分,轴向间隙都设计得比较大,而各级围带的轴向汽封齿数多,间隙比较小,且围带与汽封齿的密封面保持与转子的轴向平行。
这样,使得机组在保证经济性的前提下,允许有较大的相对膨胀,从而提高了启停的灵活性和可靠性。
6、除调节级叶片采用三销钉、三叉叶根外,其余各级都采用轴向装入式枞树型叶根。
次末级和末级为四齿园弧枞树型叶根,其他各级则为三齿直结枞树型叶根。
7、高、中、低(I)、低(II)四根转子均为整锻结构,全部用刚性联轴器连接。
两个低压转子及低(II)与发电机转子之间,还带有尺寸不同的中间轴连接。
这样。
两根低压转子尺寸完全相同,使低压缸部分可以采用同样的积木块部件。
8、为降低中压转子进汽部分高应力区的热应力,中压转子的中段和第一级叶片的根部,用低温蒸汽进行冷却。
此蒸汽来自高压缸排汽,参数为3.657MPa,313.4℃,流量为30.53t/h。
该蒸汽从中压外缸引入,穿过内缸和进汽室导流环内的通道,沿转子的中段表面和第一级叶片的进汽侧叶根区流过,进入中压首级动叶片的工作流道。