8D Check list
8D Evaluation Checklist

Completed ________ ________ ________ ________ ________ Completed ________ ________ ________ ________ ________ ________ ________ Completed ________ ________ ________ ________ ________ ________ ________ ________ Completed ________ ________ ________ ________ ________ ________ ________ ________ ________ ________ Completed ________ ________ ________ ________ ________ ________ ________ ________ ________
1. Use the Team Approach Champion named Sub-suppliers on the team Customer on the team Other pertinent personnel on the team Indication of team brainstorming 2. Problem Description Common/Special cause determined Problem stated in the customer terms Start/End dates listed Percent defective listed Frequency of problem listed Actual measurements reported Specifications listed 3. Containment and Short Term Corrective Action All stock locations purged (____Supplier's site, ____warehouse, ______sub-supplier, ____customer's site, _____next customer, _____other) Percent effectiveness of containment listed Dates of contaiment actions listed Sort results listed ____#sorted, _____#found, ______% defective Method of sort is _____stated, ______unsatisfactory Short term corrective actions listed 4. Root Cause Cause & Effect diagram Is/Is-Not analysis "Why" 5X Unacceptable root cause: ___operator error, ____Set-up piece Stated root cause is a root cause (rather than symptom or effect) Percent contribution of each root cause listed RROCESS Root Cause recognized SYSTEM Root Cause recognized Root Cause verified Process flow diagram available 5./6. Implement & Verify Permanent Corrective Action Dates of the actions indicated Stated actions cover all PROCESS root causes Stated actions cover all SYSTEM root causes Actions adequately address timing of problem Actions adequately address magnitude of problem Percent effectiveness listed (corrective actions) Chart available to verify effectiveness (____Throughput, _____Scrap, _____Dock Audit, _______IR's, _____Return sales sort results, _____Warranty)
8D报告格式模板(英文)
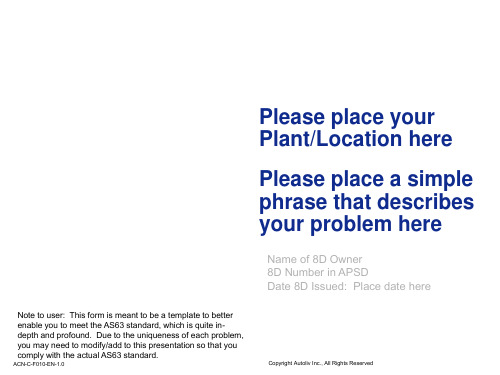
Copyright Autoliv Inc., All Rights Reserved
Step 2 Describe the Problem
Picture of Non Conforming Condition Picture of Conforming Condition
Condition Is:
ACN-C-F010-EN-1.0
Copyright Autoliv Inc., All Rights Reserved
Step 3 Implement Containment Actions
Copy of Inspection Sorting and/or Containment instructions to workers responsible
ACN-C-F010-EN-1.0 Copyright Autoliv Inc., AllTeam
(Members should include all pertinent groups - Cross-Functional)
Roles
Why
Why
Detection Cause
Occurrence Root Cause
Why
Why
Why
Why
Detection Root Cause
ACN-C-F010-EN-1.0
Copyright Autoliv Inc., All Rights Reserved
Step 4 Root Cause Analysis – Fault Tree Analysis
ACN-C-F010-EN-1.0
Copyright Autoliv Inc., All Rights Reserved
芯片(IC)行业 8D报告模板

序v号erification
No
改善措施Corrective measures
措施:注:如优化程序
Measures: Eg: Optimization program
改善前Before measures taken 改善后After measures taken
1
改善前后措施描述及证据 Description and evidence of measures
完成时间: Finish date:
状态: Status:
措施: 2 Action:
责任人: Resp:
完成时间: Finish date:
状态: Status
D4: Root Cause Analysis
鱼骨图分析Fishbone diagram analysis
Why Happened? (Occur Path)
Man
Machi ne
Materia l
缺陷 Defect name
Measur Environme
e
nt
Metho d
Why Undetected? (Escape Path)
Material
Machin e
Man
Method
Environme nt
Measur e
D4: Root Cause Analysis
责任人:Resp:
完成时间:Finishing date: 状态:Status:
措施: 改善前 Before measures taken
改善后 After measures taken
人员Resp: xxx 时间Date: xxx
验证方式 Verification method: 验证结果 Verification results:
8D改进报告资料

四.8D报告的编写
最后,消防队认为引起这起火灾的根本原因是 用电量严重超过电线的载荷量,电线超期限使 用是这次火灾地次要因素。根据消防队的建议, 该单位立即将这条电线更换为更大载荷量的电 线,并要求对线路的载荷量定期查看,发现载 荷量不足时及时更换,同时将该单位所有超期 限使用的电线全部更新。
通过上述例子可以看出,如果仅仅更换新的相 同载荷量的电线是根本不可能保证火灾不会再 次发生。
四.8D报告的编写
6.确认对策的有效性 1)临时对策的有效性 因为临时对策仅针对问题发生后所引起的后果,
所以临时对策实施后,收效很快,效果也很显 著。但不能因为它收效快、显著就把它当作救 命良药。临时对策通常只能实施一次,不能转 化为长期对策,在长期对策实施生效后,应尽 快废止。
四.8D报告的编写
记住:成立团队应尽量找与这个问题关系密切 的人,并且这些人掌握一定的知识技能,能独 立的处理问题和开展工作。
四.8D报告的编写
2.描述问题 问题描述得清楚与否,对问题能否得到
迅速解决影响很大,甚至能决定问题是 否能得到最终解决。因此,在描述问题 时应尽量将问题描述清楚,必要时要提 供佐证,如照片,图片,数据等。 描述问题时应注意:
这一部分主要是用来陈述对参加解决问题的团 队的评价。
从根本上来说,用8D方法解决问题的流程与传 统的问题解决流程基本上是一致的,但8D方法 更强调团队作用,而且形成了一种固定的模式, 使得操作起来更加容易方便,因此现在比较流 行。
三.用8D处理问题的流程
了解问题 成立团队
分析问题 寻找根本原因
8.恭贺团队 在确定问题已处理结案后,此时可以对
团队进行表彰或嘉奖,以调动团队成员 和其他人参与改善活动的积极性。可以 用公予一定 的奖励。
8D CHECKOFF LIST-Chinese

如果有现场风险,要求有可靠性数据。
D7
预防性措施包括了完成日期和责任人吗?
FMEA被更新了吗?有更新的证据吗?
责任人
完成日期
ECN
FMEA的更新产生了过程控制的改变吗?(这一点应在报告中提及)
责任人
完成日期
ECN
D5和D6中的纠正措施适于所有顾客订购的相似的产品吗?
D8
祝贺你的团队
批准
各区域质量经理应使用此检查表对8D进行审阅。在将8D发至IR质量专职组之时应明确谁评审过该8D。评审分为D1-D3, D4-D5,和D6-D8三个层次。评审此8D的人应该是区域质量经理或其直接上级,而不能是8D小组领导或8D报告的拟制者。如果收到的e-mail无区域质量经理的批准,质量专职组会拒绝接收。
纠正措施编号:
要求
拒绝
总则
8D不应包含缩写、简称或术语
报告的版本被用于更新8D的状态吗?
D0
D0应在初步的失效分析响应或8D报告中被发出。如果该8D包含D0,在D3评审时需评价D0的内容。
标题
标题包含了以下内容吗?
标识和团体或工厂名称
题目(包括基本的失效机理)
顾客名称
RDA序号
顾客参考编号(如果适用,见失效分析报告)
确定产品是怎么样和为什么逃脱工艺控制的?
批准
D4
原因描述表现了最根本的原因吗?问题是怎么样、为什么和在哪里发生的?
问题被“接通和关断”了吗?
如果问题不能被“接通和关断”需包括以下内容之一或更多:鱼刺图,分析/没有分析, DOE结果,或5 Whys分析(Delphi要求)
确定怎么样和为什么产品逃脱控制
8D-Check-list

Checklist
D1-组建团队 1.有否组建团队? 2.团队是否具有合适的技能? 3.团队成员需4-8人 4.有无指定团队负责人?
8D report: Checklist
D2-描述问题
1.4W( Who/what/where/when) 是否清晰?
2.2H(How much/How)是否清晰? -不良延伸的数量及严重程度 -如何发生的?什么样的操作模式下使这个问题发生?
D3-围堵措施 1.有否确定有效的围堵措施并有文件/相关信息予以证明? 2.有否明确临时措施的时间? 3.措施是否被核实?(需要提供改前和改后的数据对比作为证 4.是否已经选择了最好的临时围堵措施?成本最优化,风险最小 5.所涉及的产品是否已被排查?(供应商端,原材料、半成品、在 制品、在途品,仓库及客户处) 6、所有相关排查是否100%做到,避免遗漏。
D7-预防再发生 1.预防措施是否针对业务、制造、工程、质量、体系控制等环节 的基础流程? 2.涉及方是否都同意此预防措施?是否有改进的承诺日期? 3.预防措施是否被完全标准化? 4.是否有计划实施预防措施? 5、是否点检及评估了系统改进情况?
D8-结案并祝贺 1、有没有总结相关经验和教训? 2、有没有选择一种适当的方式来认可团队取得的成果? istYesNo
qc七大手法及8d

QC七大手法检查表(Data collection form)分层法(Stratification)散布图(Scatter)排列图(Pareto)直方图(Histogram)因果图(Cause-Effect diagram)控制图(Control Chart)1. 查检表(Check List)以简单的数据或容易了解的方式,作成图形或表格,只要记上检查记号,并加以统计整理,作为进一步分析或核对检查用,其目的在於『现状调查』。
2. 柏拉图(Pareto Diagram)根据所搜集之数据,以不良原因、不良状况、不良发生或客户抱怨的种类、安全事故等,项目别加以分类,找出比率最大的项目或原因并按照大小顺序排列,再加上累积值的图形。
用以判断问题症结之所。
3. 特性要因图(Characteristic Diagram)一个问题的特性(结果)受一些要因(原因)的影响时,将这些要因加以整理,而成为有相互关系而且有条且有系统的图形。
其主要目的在阐明因果关系,亦称『因果图』,因其形状与鱼骨图相似故又常被称作『鱼骨图』。
4. 散布图(Scatter Diagram)把互相有关连的对应数据,在方格上以纵轴表示结果,以横轴表示原因,然后用点表示分布形态,根据分析的形态未研判对应数据之间的相互关系。
5. 管制图(Control Chart)一种用於调查制造程序是否在稳定状态下,或者维持制造程序在稳定状态下所用的图。
管制纵轴表产品品质特性,以制程变化数据为分度;横轴代表产品的群体号码、制造曰期,依照时间顺序将点画在图上,再与管制界限比较,以判别产品品质是否安定的一种图形。
6. 直方图(Histogram)将搜集的数据特性值或结果值,在一定的范围横轴上加以区分成几个相等区间,将各区间内的测定值所出现的次数累积起来的面积用柱形画出的图形。
因此也叫柱形图。
7. 层别法(Stractification)针对部门别、人别、工作方法别、设备、地点等所搜集的数据,按照它们共同特徵加以分类、统计的一种分析方法.二: 8D 8D 的原名叫做 8 Disciplines,意思是8 个人人皆知解决问题的固定步骤。
8D 报告的检查清单列表
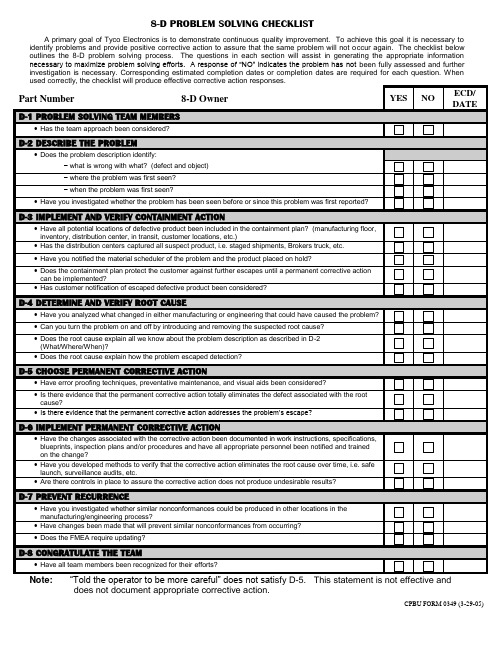
does not document appropriate corrective action.
Have you developed methods to verify that the corrective action eliminates the root cause over time, i.e. safe launch, surveillance audits, etc.
Are there controls in place to assure the corrective action does not produce undesirable results?
Does the root cause explain all we know about the problem description as described in D-2 (What/Where/When)?
Does the root cause explain how the problem escaped detection?
8-D PROBLEM SOLVING CHECKLIST
A primary goal of Tyco Electronics is to demonstrate continuous quality improvement. To achieve this goal it is necessary to identify problems and provide positive corrective action to assure that the same problem will not occur again. The checklist below outlines the 8-D problem solving process. The questions in each section will assist in generating the appropriate information necessary to maximize problem solving efforts. A response of “NO” indicates the problem has not been fully assessed and further investigation is necessary. Corresponding estimated completion dates or completion dates are required for each question. When used correctly, the checklist will produce effective corrective action responses.
8D手法的概念讲解

8D 的本质: 问题解决程序
当我们观察到 或发现………时 这现象是否正常 跟标準或目标比较的差 异(偏离程度) 其差异是否不能接受? 为什么会发生异常 ?
现
象
确认并定义问题 WHAT, WHEN, WHERE, WHO, WHY, HOW, HOW MUCH
例如: 人员出勤率93% 人员出勤率的目标为95% 低了2个百分比,而此差 异幅度根据以往资料判断 差异过大为异常状况。 请假人数太多
征兆 / 紧急反应措施 成立改善小组 描述问题 暂时性的对策实施及确认 原因分析及証实 永久改善行动效果确认 永久改善行动的对策实施及确认 避免再发生/ 系统性预防建议 完成
掌握“问题”之要领
z 1)什麼是“问题”? z 问题是实际与理想之间的差距 (Gap). z 2)什麼是问题的型态? z 1.异常性问题 (s 太大) z 2.结构性问题 (Xbar 太低) z 3)如何发掘问题? z 把问题视作一座冰山 z ( 使用工具: 5 Why, 亲和图法,关连图法..)
D0 Emergency Response Action
紧急反应措施
Emergency Response Action (ERA) 紧急反应 措施 指客户端的產品的紧急处理方式。產品紧急处 理方式通常是 Hold 或退回製造厂处理
D0 与D3 的比较
Compaq VIA ASEK
成 品
半成品
D2
DESCRIBE THE PROBLEM/ 问题描述
WHEN(时):第一次发生及随后再出现的时间。 WHO(谁):发现部门或人员。 How Big/ How Much:问题发生的影响程度。 例:尺寸,数目, 比例,趋势, YIELD LOSS (收益损 失)…
8D预防思维方法论
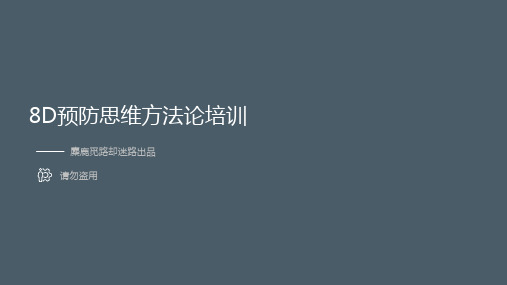
what
终端用户(攻螺纹):∮5孔端口位置细小破损 品质:∮5孔存在破损,不对产品功能与性能等因素产生影响
度不符,要求焊接平面水平(0度),实测:-5度。
8D预防思维方法论
问题描述:五要点
用户角度/描述要细/来源要广/数据要全/不含分析
要点3:来源要广
1)市场(客户)情况
客户IQC 退货率 2)内部调查 出货检验记录 外协情况
客户产线 退货问题占比
过程检验记录 运输包装情况
维修记录 问题导致的退货率
来料检验情况 库存情况
要将以上的“市场情况”、“内部调查”,分别归纳总结,形成清晰的结论
8D预防思维方法论
问题描述:五要点
用户角度/描述要细/来源要广/数据要全/不含分析 要点4:数据要全——包含两层含义
1.不能缺
共检多少个? 20个?50%怎 么来的
1)不能缺少问题/失效的数量、总数、比例以及失效
一估
目的:避免拆机时破坏失效细节,导致原因找不到或难找
做法:根据失效现象,个人经验,同类问题,鱼骨图,估计:1)可能失效零件 2)可能失效部位,从而得出:拆机注意点
二拆
目的:搞清失效相关子系统或模块及零件的表明状态,缩小分析范围,为测量提供线索,同时为后续提供事实依据
做法:根据一估的内容,小心层层拆解,如有必要直到零件状态
失效现象
一次因(紧扣现象)
二次因(紧扣 XXX(该事实得出的客观 结论或者仍然是事实)
(事实/数据)XXX……. (结论/事实)XXX
8D报告解说及范例
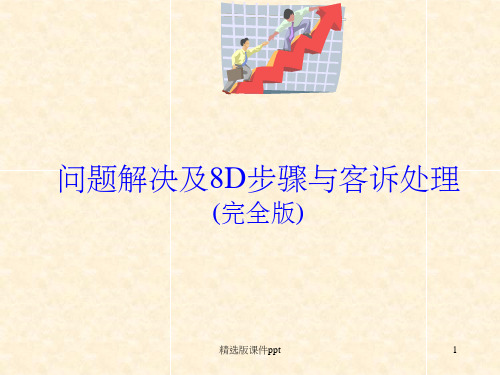
77.95 78.95 7精9.选95版课件p8p0t.95 81.95 82.95 83.9531
柏拉图 (Pareto Chart)
• 目的:为便于判断产品较重要之不良原 因所绘制之图形
• 通常先以层别法与查检表为前置作业
精选版课件ppt
32
• 实例
xx工程不良分析表
项目
不良数 累积不良数 比率 % 累积比率%
表格之依据 • 通常可做为柏拉图及直方图之前置作业 • 重点在设计表格
精选版课件ppt
25
查检表 (Check List)
地区
FAB 1
机
台
项目
ABC
温度不足
压力不足
转速不足 其他
精选版课件ppt
FAB 2 ABC
26
直方图 (Histogram)
• 目的:为便于判断产品质量特性之分配 状态,及其与规格之关系所绘制 之图形
精选版课件ppt
19
壹. 问题篇 2 目标设定
• 决定具有挑战性的目标值 • 决定目标完成期限 • 预估成效
精选版课件ppt
20
壹. 问题篇 设定目标方法
• 根据公司或内部方针及计划,考量目前 水平,由全体自主的设定
• 活用统计方法来决定目标,如柏拉图… • 目标尽可能数量化、明确化 • 不能收集数据时,以文字来叙述欲达成
检测问题 为何100%Q1测试不良 为何测试ok之产品重测4
壹. 问题篇
问题的特性
问题的特性
问题的大小
(Magnitude)
问题的严重性 (Serverity)
发生频率
(Occurance)
侦测性
(Detectability)
质量管理分析详解-8D等七大品质手法
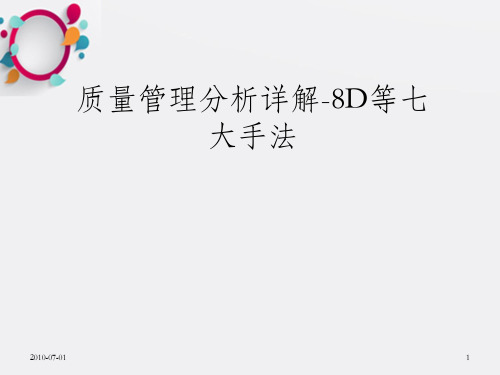
这必须包括统计技术在内的适用方法和应用程度的确 定。
8.1.1 统计工具的识别 在先期产品质量策划时必须确定每一个过程适用的统计 工具,并包含于控制计划中。
8.1.2 基础统计概念知识 基本的统计概念,例如变异,控制(稳定性),过程能力和 过度调整必须在整个组织被了解和使用。
2021/8/17
5
检查表
品
柏拉图
管
七
特性要因图
大
手
散布图
法
分层法
-
旧
直方图
控制图
2021/8/17
关联图
品
系统图
管 七
亲和图
大
矩阵图
手
法
PDPC法
-
箭条图
新
矩阵数据解析法
6
• 品管七大手法的目的:
– 根据事实、数据发言——图表(Graph)、检查表(Check List)
– 并非对所有原因采取措施,而是先从影响较大的2~3項 采取措施,即所谓管理重点——柏拉图(Pareto Dragram)。
• 柏拉图是美国品管大师朱兰博士运用意大利经济学家柏拉图 (Pareto)的统计图加以延伸所创造出来的,柏拉图又称排列图。
二、柏拉图的应用
• 作为降低不合格的依据:想降低不合格率,先绘柏拉图看看。 • 决定改善目标,找出问题点。 • 确定主要因素、有影响因素和次要因素。 • 抓主要因素解决质量问题。 • 确认改善效果(改善前、后的比较)。
合计件数
不合格件数 51 36 15 10 5 7 124
不合格比率 41.1% 29.0% 12.1% 8.1% 4.0% 5.7%
博世供应商8D-质量检查表-Bosch-problem-solving-sheet-en

If considered measures are not in use, it’s required to give a clear explanation of the risk (proof by data, e.g. quantity, costs).
Tracking of implementation of defined action? Is the expected efficiency described?
* Evaluation of efficieons are done.
Has it been ensured that the implemented containment actions will not initiate or cause new additional problems?
Is the customer informed, if necessary?
D3 – Containment Actions
Customer is protected against further problems by respective measures.
Secure the current ongoing production; all internal production lines, processes, locations, products, blocking of inventory and work plan, information to employees, action is fixed.
Was the failure verified at inspection? Is the problem clearly described? (Defect / defect location, Smallest Possible Object - SPO) Are all relevant data available? (Type, Serial-no., 0h/field failure, delivered quantity, complained quantity, tool-No, mould No, returned quantity, production date period, concerning products/product families, concerned customers, repetitive failure yes/no)
8D报告简单教材

D-8: Congratulate Your Term
相關單位審核/承認 相關單位審核 承認 Approval/Review by Related Department
A. 8 D Definition
What is 8D (Discipline)?
Definition of 8D
8D 是解決問題的哲學
B.Contents of 8D
D-1:問題解決團隊 問題解決團隊 D-2:問題描述 問題描述 D-3:暫時消除此現象之對策 暫時消除此現象之對策 D-4:原因分析 原因分析 D-5:問題對策及執行日期 問題對策及執行日期 D-6:對策效果確認 對策效果確認 D-7:防範再發生之對策 防範再發生之對策 D-8:相關單位審核 相關單位審核
D-1: Term Approach- 問題解決團隊
處理團隊成立 確立專案Leader Nhomakorabea立專案 工作分配 宣佈Deadline 宣佈 進度掌握
▓
Internal & External Members Discussion with Related Person before Writing
▓
D-2: Problem Description- 問題描述
D-5: Corrective Actions- 改善對策 改善對策
問題對策描述 & 各項對策執行日期、 各項對策執行日期、對策品識別 & 相關執行文件(編號 編號) 相關執行文件 編號
範例: 範例:
對策 嚴格要求作業人員須注意…” “嚴格要求作業人員須注意 ”
範例: 範例:
SOP
對策 注意…” “嚴格 要求 作業人員 須 注意 ”
D-4: Root Cause Finding- 原因分析
A客户验厂各部门准备Check list

1、准备车间6S(整理、整顿、清扫、清洁、素养、安全)、更衣室、物料房、车间内部流水线 等; 2、依据客户关注的产品尺寸排产,专线审核对应; 3、制造部负责人需要通知厂长安排生产、工程、品质对应客户审核人员,在客户审核前一天动 员布置安排客户审核的相关要求和注意事项;并指定专人负责根据客户前期审核的问题点进行 检查确认是否改善关闭; 4、生产负责人务必保证现场的整理、整顿、现场物料、产品状态标识,区域定位、不良品管理 识别、返修品的管理、流程单填写规范、设备点检表的填写、生产各工位的填写报表、品质巡 查检验报表等; 5、生产预警报表的管理、异常单的管理追踪、TOP3前三项的改善报告、良率/直通率的报表; 6、温湿度监控记录、尘埃粒子测试记录、流水线线清洁记录、设备清洁记录、ESD接地测试记 录、检查工位环境照度测试记录等; 7、员工上岗资格的确认,是否有新入职员工?是否有转岗移动人员?上岗证是否更新?培训记 录和考核记录是否齐全? 8、离子风扇点检、摆放位置、风速、校验是否正常? 9、员工无尘服穿着是否规范?静电手环是否佩戴? 10、车间所有货架、流水线、手推车、设备、仪器、电测治具、烙铁等是否有效接地处理; 11、车间化学的管理是否区域标识?定位?MSDS报告?使用的化学分装瓶子是否标识清楚? 12、车间各工位作业人员、检查人员是否清楚产品的检验标准?判定标准?抽样水准?是否有 检验检查记录?超出预警标准是否开立异常单?追踪改善? 13、班拉长、技术员、工程师主管、经理是否清楚涉及到车间相关管理制度和要求,如:无尘 车间管理规定、无尘服穿着规定、车间6S管理规定、生产预警管理规定、制程异常管理规定、 部门的考核质量目标指标KPI、特产流程、试产管理规定、AQL抽样标准、出货检验标准、各工 位输出哪些报表? 14、所有工位的SOP是否存在现场,对应的岗位? 1、需要准备什么资料,QS第一时间通知; 2、依据公司管理要求和部门管理要求,按照规定和流程执行作业;
8D报告5W2H(幻灯片)

欲追踪之改善品的供应数量及每批数量
P9
Present:Vinson
报告完毕
谢谢各位
WHERE
状况发生的地点 等待处理的地点 改善实施的地点
P4
Present:Vinson
5W2H Checking List
存放区 数量 地点 协力商 国内 公司 国外 组装厂 OEM 品牌客户 通路商 Sea Air IQC 零件仓 Line (WIP) 暂存区 (Line) 成品仓
P5
Present:Vinson
Present:Vinson
5W WHY WHERE WHEN WHO WHAT
P2
2H HOW MANY HOW MUCH
Present:Vinson
WHAT
事或物的发生起源, 事或物的发生起源,影响范围 现地.现物.现状) (现地.现物.现状)
待处理的状况 改善实施的状况
P3
Present:Vinson
WHEN
状况发现的时间 暂时对策实施的时间 永久对策实nson
WHO
何人发现状况(公司同仁、协力厂、 何人发现状况(公司同仁、协力厂、 组装厂、OEM、品牌客户、通路商、 组装厂、OEM、品牌客户、通路商、 消费者) 消费者) 何人执行暂时对策 何人执行永久对策
P7
Present: Vinson
8 Discipline
1.内 1.内/外部成员 2.问题的详细描述 2.问题的详细描述 3.围堵计划 3.围堵计划 4.根本原因分析 4.根本原因分析
P1
5.长期改善对策 5.长期改善对策 6.成果验证 6.成果验证 7.预防再发生措施 7.预防再发生措施 8.祝贺 8.祝贺
8D报告填写及手法运用

鱼骨图 / 因果图
❖ 功能分析
➢ 系统/零部件/生产过程
单独列出所有功能 应用技术:
➢ 功能树 ➢ 过程流程分析
应用资料:
➢ 设计要求书 ➢ 产品规范 ➢ 过程流程图
五个为什么方法 The Five Why Method
根 由 R oot C ause 为什麽?
真正原因
为什麽?
D3:临时措施 (1)
围堵/隔离问题 采取即时行动或应变对策控制问题影响范围 跟进客户或后序品质、生产要求 对不良品进行分析并追溯到相关工序或个人 对异常隐患批次在制品或库存停止流转或外发
(如有需要) 清理仓库、工厂及现场中的不良品或可疑产品
D3:临时措施(2)
为防止问题恶化并波及其他产品必须举一反三 尽快恢复客户信心 预先布置应变方案 采用产品追溯到生产批次和受影响范围
1问: 为什么缺划不良会从完检流到出货检? 1答: 因为缺划产品经分析多数为弧倒造成,
而个别弧倒产品造成的颈部受伤不稳定,有时亮有时不亮 。
2问: 为什么会有弧倒产生? 2答: 因为部分晶片在边缘,拿放时碰倒弧线 。 3问: 为什么会碰倒弧线? 3答: 因为按照常规要求去取放PCB。 4问: 为什么按常规要求去取放PCB? 4答: 因为并未在文件中明确取放要求 。 5问: 为什么未明确要求在技术文件中? 5答: 因为文件按常规要求编制 。 由上可见,经常利用问5次为什么,就可以确认出问题的原因以及
D2:问题的描述
以外部客户或内部部门反馈的述语进行描述 清楚明白客戶投诉或内部异常的不合格之处 只有数据才能准确说明问题,但来源必须真实 使用5W2H的方法去定义及收集问题的资料 定义问题时可用-图片、形象、图表
何谓 “5W 2H” ?
8D 报告完整版

CUSTOMER COMPLAINT #DATE OPENED ROLE NAMEROLE NAMEROLE NAMECHAMPION MEMBER MEMBER LEADER MEMBER MEMBER MEMBER MEMBER MEMBER MEMBERMEMBERMEMBER(First Date non-No.LOCATIONTOTAL QUANTITYAMOUNTNONCONFORMINGRESPONSIBLE DATE FINISHED1234( WhenconformingNo.RESPONSIBLEDATEIMPLEMENTEDICA #1ICA #2ICA #3No.OCCURRENCE ORESCAPERESPONSIBLE DATE VERIFIEDPRC #1PRC #2PRC #3PRC #4TOOLS USED (CHECK ALLNo.ADDRESSING PRC #__ FROM D4RESPONSIBLETARGET DATECOMPLETION DATEPCA #1CMT / DEVIATION #HALDEX P/N CORRECTIVE / PREVENTIVE ACTION (CAPA) RESPONSED0 - GENERAL INFORMATIONACTION TYPE 8D NUMBERPRODUCT FAMILY 8D SITE OWNER CUSTOMER P/N SOURCECUSTOMER / SUPPLIER NAMEWHO?WHAT?WHERE?WHEN?HOW?HOW OFTEN?HOW MANY?RETURN QUANTITYDATE CLOSEDTITLETITLED2 - PROBLEM DESCRIPTION / STATEMENT(Describe the problem from the customer’s point of view: who, what, when, where, how, how often and how many. This information establishes the focus of the investigation. Recommend use of the "Is / Is Not" methodology to generate the problem statement. )PROBLEM DESCRIPTION / STATEMENTD1 - TEAM(Name individuals responsible for root-cause analysis & corrective action implementation. Add additional team members as necessary to address the problem)TITLECLEAN DATE:CONTAINMENT ACTION #REF!D5 - PERMANENT CORRECTIVE ACTIONS(Describe how operating systems, practices, procedures, or processes have been changed to prevent recurrence.)D4 - OCCURRENCE AND ESCAPE ROOT CAUSES(Use Fishbone, 5-Why, Pareto, Brainstorming…etc. to determine potential root causes. For each cause identified, question WHY this is a cause to the original problem. For each new answer to the WHY question, pose the question over again until no new answers result. This last cause is potentially the problem’s root cause. Repeat this procedure for each possible cause. Detail the investigation activities into each/all potential root causes as they are either verified or eliminated.POTENTIAL ROOT CAUSE(S) AND VERIFICATION RESULTS(ADD ROWS AS NECESSARY BELOW TO CAPTURE ALL POTENTIAL ROOT CAUSES)RMA #UPDATED TO D3 (A) - CONTAINMENT ACTIONS(Describe steps taken to contain the problem within the department and correct those parts already produced. Define who is responsible and date(s)enacted. Verify effectiveness of the containment action. Definition of the containment action exit criteria is required.)D3 (B) - SHORT TERM CORRECTIVE ACTION (INTERIM ACTION)(Describe the interim corrective actions taken. Define who is responsible and date(s) enacted. Verify effectiveness of the interim corrective actions taken.)SPECIFIC DETAILS OF INTERIM CORRECTIVE ACTION ACTIVITIESAND THE SPECIFIC CRITERIA TO ALLOW EXIT FROM THOSE INTERIM ACTIVITIES(ADD ROWS AS NECESSARY BELOW TO CAPTURE ALL INTERIM CORRECTIVE ACTIONS)PERMANENT CORRECTIVE ACTION TAKEN(ADD ROWS AS NECESSARY BELOW TO ADDRESS ALL PERMANENT CORRECTIVE ACTIONS TAKEN)ESCAPE DATE:BRAINSTORMING PARETO ANALYSIS FISHBONE IS / IS NOT 5-WHY ANALYSIS CHECK SHEET HISTOGRAM FLOWCHARTING。
实用的8D管理工具课件

求解決3問. 方策題擬的定 對策, 與CA-PDCA
的邊尋4. 找最適對策追策究處理問題有所不同
5. 最適策實施
CA-PDCA
活動計劃的製作 2. 現況把握 3. 要因分析 4. 對策擬定 5. 對策實施
6. 效果確認 7. 效果維持 8. 反省及今後計劃
实用的8D管理工具
解決問題的QC Story種類
標準替代的過程 • 運用PDCA改善前, 應以SDCA來做標準化 • 四個步驟是一體的,連續的.由相同人或單位所負責,
否則常會導致無法銜接 • 改善行動要有“有效性”驗証
实用的8D管理工具
PDCA 循環輪
1.主題選定
7.效果A
P
管理人員 管理人員
3.方策擬定 4.最適策追究
不良率的 p-Chart 趨勢圖
0.250 0.200 0.150 0.100 0.050 0.000
Lot
实用的8D管理工具
UCL=0.1253 Avg=0.0704 LCL=0.0155
Sigma Rule
99-100% 90-98% 60-75%
-s
+s
-2s
+2s
-3s
+3s
实用的8D管理工具
複雜的或許要5 Why, 6 Why, 7 Why…最後要加 1H,How to fix it.
实用的8D管理工具
5 Why 範例: 為何停機
• 問1:為什麼機器停了? • 答1:因為機器超載, 保 險絲燒斷了
实用的8D管理工具
5 Why 範例: 為何停機
• 問1:為什麼機器停了? • 答1:因為機器超載, 保 險絲燒斷了
ACTION PLAN CHECK DO
8D质量工具交流(检查清单)

6
FMEA
3、S、O、D的定级 XXXX的各工程师在讨论编制FMEA文件时,对S、O、D的定级的理解 都不一样,都是依靠以前类似零件的FMEA文件来参考,没有一个统一 的标准。现在结合总部的程序文件,修订了XXXX的FMEA作业指导书, 对S、O、D的定级标准加以明确,使大家得到了统一的标准。现在讨论 编制FMEA文件时,对S、O、D的定级除了参靠文件规定外,还可以请 教FMEA主持人——技术组长(提供FMEA方法的支持和指导 )。 4、FMEA正文以外的相关文件 XXXX原有的文件就只是光溜溜的一套正文,没有签字评审用的PFMEA封面,没有P-FMEA-的汇总表。 而对于FMEA的评价也没有开展,现在准备定期对FMEA的RPN值进行 统计,通过每年RPN值的下降,体现FMEA工作的有效性,体现现场改 进的有效性,并形成报告,在下次管理评审时向管理层展示。
7
谢 谢!
8
2
8D
3、D3遏制措施: 缺陷被确认后,为了防止客户继续收到缺陷件,应立即实施临时措施。 控制措施须考虑多个方面(顾客方面、运输方面、中转站、供应商); 为了避免采取措施时遗漏某个环节的零件,可借助check list来策划 临时措施(例如DCEC的7步工作法中的表格) 如果无法实施临时措施的,则注明原因,相应的风险评估;同样也需 要考虑风险零件的涉及面(数量),让管理层及客户对风险有较为准 确的认识。 4、D4根本原因: 找到根本原因才是8D的根本,应用系统的分析方法,如鱼骨图、 5why方法、故障树分析,KT分析等,不仅仅是使8D报告变得“页数 足够多”,WFAC的体会是:最大的好处,是能使团队成员锻炼提高 系统的分析问题的能力;其次,分析获得的根本原因(问题的症结所 在)也能使团队的成员都信服,然后提出的纠正预防措施能获得相关 责任人员的理解,进而在执行上没有质疑。
- 1、下载文档前请自行甄别文档内容的完整性,平台不提供额外的编辑、内容补充、找答案等附加服务。
- 2、"仅部分预览"的文档,不可在线预览部分如存在完整性等问题,可反馈申请退款(可完整预览的文档不适用该条件!)。
- 3、如文档侵犯您的权益,请联系客服反馈,我们会尽快为您处理(人工客服工作时间:9:00-18:30)。
Checklist
D1-组建团队 1.有否组建团队? 2.团队是否具有合适的技能? 3.团队成员需4-8人 4.有无指定团队负责人? D2-描述问题 1.4W( Who/what/where/when) 是否清晰? 2.2H(How much/How)是否清晰? -不良延伸的数量及严重程度 -如何发生的?什么样的操作模式下使这个问题发生? D3-围堵措施 1.有否确定有效的围堵措施并有文件/相关信息予以证明? 2.有否明确临时措施的时间? 3.措施是否被核实?(需要提供改前和改后的数据对比作为证据) 4.是否已经选择了最好的临时围堵措施?成本最优化,风险最小化. 5.所涉及的产品是否已被排查?(供应商端,原材料、半成品、在制品、在途品,仓库及客户处) 6、所有相关排查是否100%做到,避免遗漏。 D4-根本原因 1.是否已经确认了问题“流出”的根本原因及“失效”的根本原因? 2.有否做到了现场,现时,现物 “三现” 3、检查问题是否涉及到设计、过程、材料、环境、产线及人员等各方面因素 4、检查过去的原始相关数据/记录是否与投诉问题相关联; 5、检查是否不止一个根本原因; 6、检查相似产品/部件是否有同样问题; 7、用5W的方法找出根本原因; 8、尽量尝试让问题重现 9、当根本原因找到时,再重新确认D2看是否相符合。 D5-制定纠正对策 1.纠正措施是否针对根本原因?(加强检验的提法不可以接受) 2.有否考虑实施纠正措施带来的副作用? 3、执行纠正措施后的产品是否有相应的标识?是否可追溯? 4、跟踪执行纠正措施前后的不良趋势 D6-确认执行纠正措施的效果 1.检查执行纠正措施当前是否有效? 2.确认纠正措施有效后是否废除临时措施? 3.是否跟踪一段时间的失效率来确认纠正措施是否持续有效? D7-预防再发生 1.预防措施是否针对业务、制造、工程、质量、体系控制等环节的基础流程? 2.涉及方是否都同意此预防措施?是否有改进的承诺日期?
3.预防措施是否被完全标准化? 4.是否有计划实施预防措施关经验和教训? 2、有没有选择一种适当的方式来认可团队取得的成果?
ist
Yes No
,仓库及客户处)