药品生产过程防止差错与混淆管理质量风险评估报告
制药企业防止生产过程中的污染、交叉污染及混淆的措施(GMP课件)
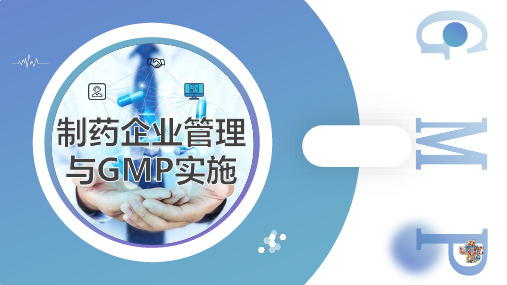
三、培训防止生产过程中的污染、交叉污染及其混淆的措施
2.生产区域专一 在同一生产区域包括相应的辅助生产区域,只能生产同一批号、同一规格的相同产品。在同一
生产区域包括相应的辅助生产区域同时生产不同品种、规格或批号的药品是混淆产生的最主要的原 因,必须坚决制止,以防止混叉污染及其混淆的措施
3.生产前检查 每品种或每批号生产开始前,应认真检查设备、器械、容器等是否洁净或灭菌,以
及是否有前次生产的遗留物,否则不能进行新的生产操作。 4.状态标志明确
每一生产操作间、每一台生产设备、每一盛物容器均应有能够指明正在加工的 产品或物料、批号及数量等的状态标志。在生产中无状态标志是造成混药事故的主要原 因之一。
⑤在易产生交叉污染的生产区内,操作人员应当穿戴该区域专用的防护服; ⑥采用经过验证或已知有效的清洁和去污染操作规程进行设备清洁;必要时,应当对与物料直接接触的 设备表面的残留物进行检测; ⑦采用密闭系统生产; ⑧干燥设备的进风应当有空气过滤器,排风应当有防止空气倒流装置; ⑨生产和清洁过程中应当避免使用易碎、易脱屑、易发霉器具;使用筛网时,应当有防止因筛网断裂而 造成污染的措施; ⑩液体制剂的配制、过滤、灌封、灭菌等工序应当在规定时间内完成;软膏剂、乳膏剂、凝胶剂等半固 体制剂以及栓剂的中间产品应当规定贮存期和贮存条件。
二、混淆的产生
(一)混淆: 混淆是指一种或一种以上的其他原材料或成品已标明品名等的原材
料或成品相混,通俗的说法,称为“混药”。 如原料与原料,成品与成品,标签与标签,有标志的与未标志的,
已包装的与未包装的混淆等。 (二)产生混淆的原因: 1、厂房:生产区域狭小、拥挤,同一区域有不同规格、品种、批号的 药品同时生产;生产中物料流向不合理,生产线交叉;生产、运贮、 仓贮无保证措施;非生产人员进入等造成无意或有意混淆事件等。 2、设备:生产中使用的设备、容器无状态标志,清场不彻底等造成。
发药差错分析制度和改进措施范文(五篇)
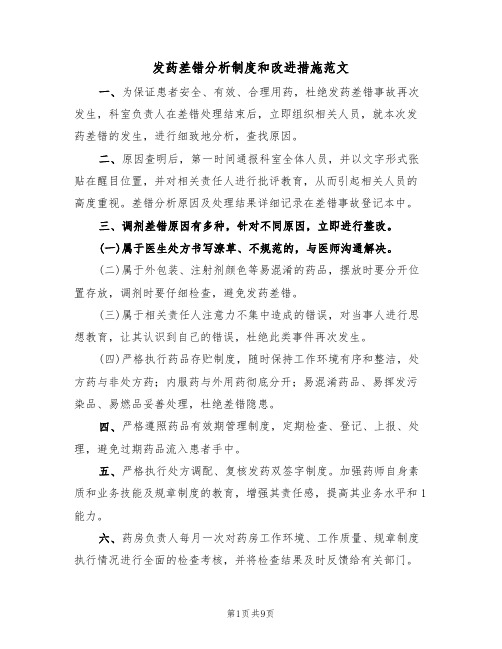
发药差错分析制度和改进措施范文一、为保证患者安全、有效、合理用药,杜绝发药差错事故再次发生,科室负责人在差错处理结束后,立即组织相关人员,就本次发药差错的发生,进行细致地分析,查找原因。
二、原因查明后,第一时间通报科室全体人员,并以文字形式张贴在醒目位置,并对相关责任人进行批评教育,从而引起相关人员的高度重视。
差错分析原因及处理结果详细记录在差错事故登记本中。
三、调剂差错原因有多种,针对不同原因,立即进行整改。
(一)属于医生处方书写潦草、不规范的,与医师沟通解决。
(二)属于外包装、注射剂颜色等易混淆的药品,摆放时要分开位置存放,调剂时要仔细检查,避免发药差错。
(三)属于相关责任人注意力不集中造成的错误,对当事人进行思想教育,让其认识到自己的错误,杜绝此类事件再次发生。
(四)严格执行药品存贮制度,随时保持工作环境有序和整洁,处方药与非处方药;内服药与外用药彻底分开;易混淆药品、易挥发污染品、易燃品妥善处理,杜绝差错隐患。
四、严格遵照药品有效期管理制度,定期检查、登记、上报、处理,避免过期药品流入患者手中。
五、严格执行处方调配、复核发药双签字制度。
加强药师自身素质和业务技能及规章制度的教育,增强其责任感,提高其业务水平和1能力。
六、药房负责人每月一次对药房工作环境、工作质量、规章制度执行情况进行全面的检查考核,并将检查结果及时反馈给有关部门。
发药差错分析制度和改进措施范文(二)发药差错分析制度是为了提高发药工作的准确性和安全性,避免药品发放过程中出现错误,保障患者用药的正确性和合理性。
以下是一些常见的发药差错分析制度和改进措施:1. 建立健全药品发放审核制度:药师在发药前应进行仔细核对患者的处方和用药信息,确保准确无误。
2. 强调医嘱规范:医生开具处方时,应明确规定药品的名称、剂量、用法以及是否有特殊注意事项,减少因医嘱不规范导致的发药差错。
3. 引入电子发药系统:电子发药系统能够自动识别药品信息和患者信息,减少人为差错的机会,提高发药的准确性。
生产过程防止污染交叉污染混淆和差错的管理规程

生产过程防止污染、交叉污染、混淆和差错的管理规程目的:建立防止污染、交叉污染、混淆和差错管理规程,规定了在药品生产活动过程中防止污染、交叉污染、混淆和差错管理内容和要求适用范围:适用于药品生产活动过程中防止污染、交叉污染、混淆和差错的管理职责:生产技术部、质保部、车间对实施本规程负责内容:1.定义1.1污染:在生产、取样、包装或重新包装、贮存或运输等操作过程中,原辅料、中间产品、待包装产品、成品受到具有化学或微生物特性的杂质或异物的不利影响。
1.2 交叉污染:不同原料、辅料及产品之间发生的相互污染。
1.3混淆:在生产或包装的过程中,误将一种或一批物料当成了另一种或另一批物料进行使用、操作。
1.4 差错:在生产过程中,因为计量器具未调试到位、或计量方式不正确、或计数不准确而造成的错误2. 产生污染、交叉污染、混淆和差错的原因2.1 人员:操作人员患有传染病、皮肤病等,或未接受卫生方面的培训,未按要求穿戴工作服,行为不规范、人员带来外部污染,生产人员未按工艺规程和SOP 要求操作,工作责任心不强,工作量过大,操作中随意性大等。
2.2 设备:表面不光洁、平整,材质不稳定,不易清洁,设备选型不合理,维修、保养不及时,没有定期验证或没有保持验证状态。
生产中使用的设备、容器无状态标志,清场不彻底等造成混淆。
2.3 物料:购进的原辅料本身质量不好,或在运输、贮存、检验取样、配料过程中造成污染。
原辅料微生物指标超限。
原辅料、包装材料、半成品、中间体等无明显标志,放置混乱,散装或放在易破损的包装中,印刷性包装材料管理不善等。
2.4 文件:文件管理制度不健全,或执行不力,无复核、监控,发现问题未及时查找原因等,特别是配料、包装等重要部门管理不严格。
2.5 环境:厂房设计不合理,生产环境如空气中粒子过多,车间地面、墙壁、天花板等不平整、易脱落、长霉、消毒不严格等造成污染。
2.6 清洁:清洁效果不能保证微生物除去水平及残留限度,清洁剂残留、消毒剂效果不能保证;生产结束后不及时清洁清场等造成污染。
关于药房药品差错原因及防止措施范文示例

关于药房药品差错原因及防止措施范文示例关于药房药品差错原因及防止措施范文示例在近年来的媒体报道中,医疗卫水平的影响很大。
然而,由于各种原因的存在,关于药房药品发生的差错事件的报道依然居高不下,这也是当下医疗卫生单位重点关注的问题之一。
1药品差错的分类及原因分析。
1.1处方错误。
处方错误是常见的药品差错之一,多是和开药的医生有关。
由于工作的特殊性,医生一般是采用手写的方法,将药品名称写在纸上。
一方面,手写的字迹往往没有打印稿那么明显,所以相关人员在抓药的时候,由于没有看清药品名称而拿错药的现象是时有发生的。
另一方面,多是由医生自身因素所导致,如在繁忙的时候,容易出现视觉性的疲劳,对于患者的年龄和性别等分辨不清,对于孕妇或者是血糖高的特殊人群,在开药的时候也是需要特殊对待的,而这也是很多医生在工作中所忽略的地方。
此外,对于一些新型的药品,尤其是西药,它的用法和用量都有着严格的规定,但是很多的医生都是凭借着自己以往的经验,将用量或者是用法擅自更改,这对患者的健康造成了极大的威胁。
在开药的过程中,患者的病情与所开药品不符也是常见的现象,也就是说没有对症下药,这不仅浪费了大量的钱财,对患者的身心健康也是一个极大的损害。
1.2调剂错误。
调剂错误的分类有很多,如名称相似的药品差错,同名但不同剂型药品差错,同名但不同厂家生产的厂家药品差错等。
有的药品虽然在成分上有很大的相似之处,但是由于加工方法不同,其性质发生了很大的变化,药品在功能以及用法和用量上都有所不同,调剂人员在取药的时候若是没有多加注意,就会发生工作上的失误。
此外,药品摆放的位置也直接影响到调剂员在工作中是否会出现差错。
在补充药品的时候,有的药品在外观上极为相似,调剂师在工作过程中容易出现混淆的现象。
加上有的相似药品摆放的位置都比较相近,不但会造成摆放时的错误,在调剂上也会出现差错。
1.3管理错误。
药品管理上的差错是常见的问题。
引起管理上差错的因素有很多,如贮藏不当引起的药品受潮,药品过期引起的药性改变,工作纪律引起的配药过程中的差错。
药品生产过程中防止差错与混淆管理质量风险评估报告
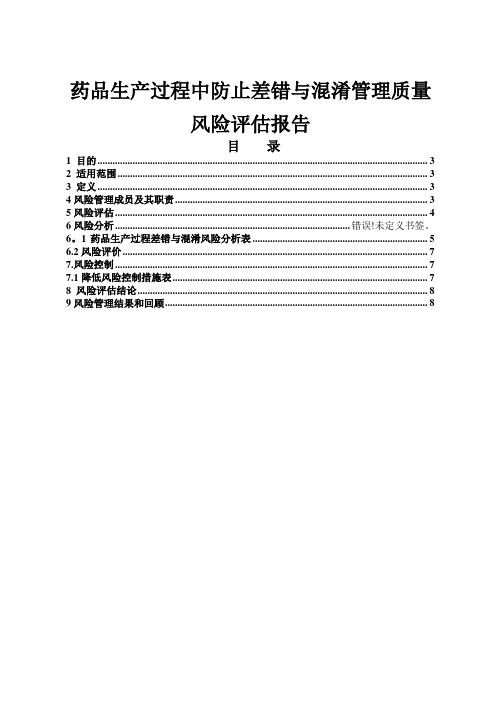
药品生产过程中防止差错与混淆管理质量风险评估报告目录1 目的 (3)2 适用范围 (3)3 定义 (3)4风险管理成员及其职责 (3)5风险评估 (4)6风险分析.............................................................................................. 错误!未定义书签。
6。
1药品生产过程差错与混淆风险分析表 . (5)6.2风险评价 (7)7.风险控制 (7)7.1降低风险控制措施表 (7)8 风险评估结论 (8)9风险管理结果和回顾 (8)1 目的:本次风险管理主要是按《药品生产质量管理规范》(2010年修订)要求,对药品生产过程中产生差错与混淆的风险进行管理活动的策划。
通过风险评估确认药品生产中差错与混淆的潜在风险,以及应采用的控制措施以最大限度地降低风险.2 适用范围:适用于药品生产过程中防止产生差错与混淆措施的质量风险评估。
3 定义:3。
1风险:危害发生的可能性和严重性组合.3。
2质量风险管理:在整个产品生命周期中采用前瞻和回顾的方式,对质量风险进行评估、控制、沟通和审核的过程。
3。
3质量风险:质量风险为危害出现的可能性和危害严重性的结合。
3.4风险识别:系统的使用信息以确定危害的可能来源,是关于风险问题或问题描述.3.5风险分析:与一些确定危害相关的风险估计.3。
6风险评估:在质量风险管理过程中,用于支持风险决定的信息进行组织的系统程序. 3。
7风险控制:执行质量风险管理决定的措施3.8风险降低:为了降低伤害出现的可能性和严重性而所采取的措施3。
9风险接受:接受风险的决定3。
10风险沟通:在决策者和相关方之间进行风险和质量风险管理方面的交流和共享。
5风险评估5。
1风险评估方法【遵循FMEA技术(失效模式与影响分析)】:5。
1。
1 风险确认:可能影响产品质量、产量、工艺操作或数据完整性的风险;5.1。
药品生产过程控制与风险管理

药品生产过程控制与风险管理药品生产管理基本要求防止污染和交叉污染的措施药品生产关键工艺控制(固体制剂案例 )验证状态的维护生产工艺和质量标准符合法规要求《药品注册管理办法》第 29 条申请人获得药品批准文号后 ,应当按照国家食品药品监督管理局批准的生产工艺生产。
药品监督管理部门根据批准的生产工艺和质量标准对申请人的生产情况进行监督检查。
2022 年版 GMP 第 184 条:所有药品的生产和包装均应当按照批准的工艺规程和操作规程进行操作并有相关记录,以确保药品达到规定的质量标准,并符合药品生产许可和注册批准的要求。
对生产过程中影响产品质量的各个因素进行控制 ,确保能够持续稳定地生产出符合预定用途和注册要求的药品 .※洁具管理:分类、整洁※工衣清洗:按时、区分※更衣要求 :标准程序更衣※清洁、消毒:规定、执行和记录※状态标识明确、信息完整※数量、帐、卡和物一致※放行控制明确,质量参预※特殊物料管理 (不合格物料、召回产品),规定区域、标识、隔离和记录※储存条件※文件、记录标识:有效版本控制※设备状态标识 :完好/运行/待修/停用※各种容器标识:已清洁/待清洁/有效期限※生产区域标识 :已清洁/待清洁/相关生产区域使用※生产状态标识:生产品名/批号/规格 /生产开始时间※管道内介质名称及流向※计量标识等:校验合格/有效期/停用/校验不合格等※是否进行基本知识、基本技能的培训※是否经培训与考核合格允许上岗※记录及时规范※规范执行现场整洁、有序;标识完整、清晰;记录填写完整、清晰、及时;行为符合 SOP采取措施最大限度减少生产过程中污染、交叉污染以及混淆、差错的风险 .※污染来源:硬件固有风险(布局、材料、空调系统、设备选型)人员及其操作引入风险 (物料流转、清洁、环境监控)※基于产品生产特点查找污染的风险点并采取措施普通制剂 :易产尘(交叉污染)和辅料多(混淆、差错)无菌制剂:污染(微生物、尘粒、热源)包装操作 :同时包装多个规格品种等情况第 185 条应当建立划分产品生产批次的操作规程 ,生产批次的划分应当能够确保同一批次产品质量和特性的均一性 .第 186 条应当建立编制药品批号和确定生产日期的操作规程。
药品生产的质量风险的分类及控制与管理

药品生产的质量风险的分类及控制与管理江苏奥赛康药业股份有限公司技术部唐建华药品生产中的风险主要存在以下七个方面问题:一、污染(包含微粒污染、微生物污染)这类风险主要是指增加产品中微粒或者不溶性微粒的风险。
虽然产品的质量标准最终只有不溶性微粒,但考虑到微生物污染的控制、环境洁净度级别的要求,同时也需要考虑微粒的风险。
比如,大批量药液泵转移的时候,转移前的罐体(容器)就应该考虑密封的同时加上呼吸器,以保证药液在转移过程中,没有环境中的微粒(微生物)无意间进入到药液中去。
这类质量风险因素的管理措施主要是密封容器或采取保护措施,以隔绝外界潜在的污染。
二、交叉污染主要是同一设备(生产线)用于生产不同产品时,可能带来的产品间彼此污染而出现质量问题的风险。
这里的生产不是单纯意义的生产,比如共用的容器或者搅拌桨都可能造成交叉污染。
这类质量风险因素的管理措施主要有:进行有效的更换品种的清洁验证;对于可拆卸的部件,应分品种独立密封保管,分品种使用;一次性的部件或用品,应坚决一次性使用后废弃。
三、混淆。
这类质量风险是将不同标识的原辅料或标签混合在一起。
可以采用一定的方法将其逐一区分开。
四、差错张冠李戴这类质量风险可造成严重的后果,且不容易识别。
需要高度警惕和内部控制。
混淆及差错类质量风险因素的主要管理措施有:生产前后做好清场及生产现场的检查;及时更换有关的标识及标签管理;采取切实有效的隔断措施。
五、质量可控在原料药生产过程中,所有造成副反应或者逆反应增加的因素都属于这一类质量风险,因为它们使得产品质量受控的程度降低。
这类质量风险的后果很严重,一般需要进行相关的确认与验证活动,在保证产品质量的同时提高生产效益。
六、人员危害。
这类质量风险要求企业强化生产人员的劳动保护。
这在GMP及其他法规中都有明文规定。
七、环境污染。
这类质量风险将污染环境,带来各种的环境问题,要求企业从源头做好环境保护。
2.药品生产过程风险评估报告

药品生产管理风险评估报告盘县三特中药饮片厂二零一四年九月药品生产管理风险评估报告目录一、质量风险评估报告批准页二、质量风险管理概述三、风险评估小组四、风险评估目的五、评估流程六、风险等级评估方法(FMEA)说明七、风险评估实施八、风险评估结论九、风险管理结果和回顾一、质量风险评估报告批准页二、质量风险管理概述1、《药品生产质量管理规范》所控制的目标就是基于质量风险的控制,通过对药品生产风险分析这一工具来“设计质量”,避免质量问题出现。
2、质量风险管理是通过掌握足够的知识、事实、数据后,前瞻性地推断未来可能会发生的事件,通过风险控制,避免事故发生。
3、有效的质量风险管理可以对可能发生的失败有更好的计划和对策,便于对生产过程中有更多的了解,可以有效的识别对关键生产过程参数,帮助管理者进行战略决策。
4、定义:4.1 风险:是危害发生的可能性及其危害程度的综合体。
4.2 风险管理:即系统性的应用管理方针、程序实现对目标任务的风险分析、评价和控制。
4.3 风险分析:即运用有用的信息和工具,对危险进行识别、评价。
4.4 风险控制:即制定减小风险的计划和对风险减少计划的执行,及执行后结果的评价。
4.5 高风险水平:此为不可接受风险。
必须尽快采用控制措施,通过提高可检测性及/或降低风险产生的可能性来降低最终风险水平。
验证应首先集中于确认已采用控制措施且持续执行。
4.6 中等风险水平:此风险要求采用控制措施,通过提高可检测性及/或降低风险产生的可能性来降低最终风险水平。
所采用的措施可以是规程或技术措施,但均应经过验证。
4.7 低风险水平:此风险水平为可接受,无需采用额外的控制措施。
5、风险管理的特点是很重要,识别、分析和评价很困难且不准确,相对于获得精确的答案,全面的考量,选用足够知识和判断力的人员进行有效的管理主要风险更为重要。
6、描述质量风险的评估目标和方法,对质量风险的评估应该基于科学性和实验,与保护使用者相关联。
防止生产过程污染与交叉污染的管理规程

防止生产过程污染和交叉污染的管理规程1目的:建立防止生产过程污染和交叉污染的管理规程,最大限度地降低药品生产过程中污染、交叉污染的风险。
2范围:适用于防止生产区、化验区与仓贮区在生产过程污染和交叉污染的管理。
3职责:生产区、化验区与仓贮区人员负责实施,QA检查员及各部门负责人负责监督执行。
4内容4.1定义4.1.1污染:在生产、取样、包装或重新包装、贮存或运输等操作过程中,原辅料、中间产品、待包装产品、成品受到具有化学或微生物特性的杂质或异物的不利影响。
4.1.2 交叉污染:不同原料、辅料及产品之间发生的相互污染。
4.2防止人员污染和交叉污染:4.2.1所有人员都应当接受卫生要求的培训,人员操作严格执行《人员卫生操作规程》,最大限度地降低人员对药品生产造成污染的风险。
4.2.2 各级管理人员严格监控防止体表有伤口、患有传染病或其他可能污染药品疾病的人员从事直接接触药品的生产。
可能患有污染药品疾病的人员必须积极主动地配合主管部门的管理要求。
4.2.3控制进入洁净区的人和物的数量。
执行《参观人员进出生产区的管理规程》。
4.2.4进入洁净区的人和物严格执行《人员进出洁净区的净化程序》和《物料、容器、工具进出洁净区的净化程序》。
4.2.5进入洁净区的操作人员不得随意离开自己的工作区域(需对岗位培训)而进入其它操作间,确需进入时,应再次执行《人员进出洁净区净化程序》后方可进入。
4.2.6 工作人员在需要进出公共区时,不能同时进出,防止交叉污染。
4.3 防尘措施:生产中对洁净区产尘操作区域进行控制,采取以下方法防止粉尘扩散、避免交叉污染的,并在此基础上不断改进防止尘埃产生和扩散的有效措施。
4.3.1工艺过程产生粉尘的工序的操作应在负压称量室进行,负压称量室设置独立的除尘系统。
4.3.2洁净室密闭,不使外界未经净化的空气进入洁净厂房,必须定期检查送风口、灯罩、安全门等是否有泄漏点。
4.3.3洁净室的地面,墙壁和顶棚等要保持无尘、光滑、无静电,并能经得起清洁、消毒,一旦发生涂层脱落应及时修补。
GMP知识竞赛试题(二)--判断题
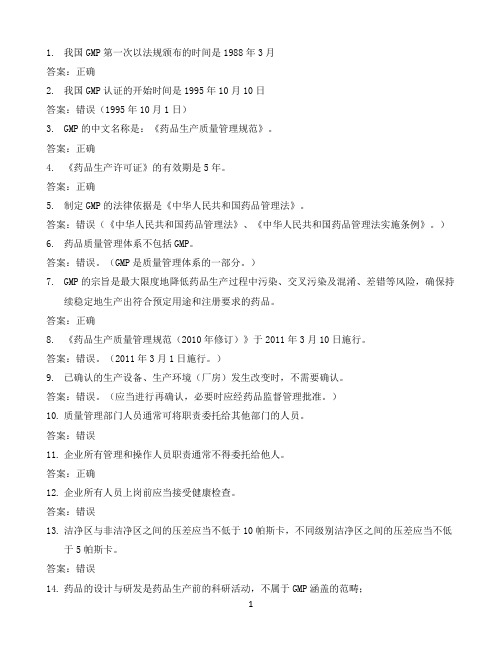
1.我国GMP第一次以法规颁布的时间是1988年3月答案:正确2.我国GMP认证的开始时间是1995年10月10日答案:错误(1995年10月1日)3.GMP的中文名称是:《药品生产质量管理规范》。
答案:正确4.《药品生产许可证》的有效期是5年。
答案:正确5.制定GMP的法律依据是《中华人民共和国药品管理法》。
答案:错误(《中华人民共和国药品管理法》、《中华人民共和国药品管理法实施条例》。
)6.药品质量管理体系不包括GMP。
答案:错误。
(GMP是质量管理体系的一部分。
)7.GMP的宗旨是最大限度地降低药品生产过程中污染、交叉污染及混淆、差错等风险,确保持续稳定地生产出符合预定用途和注册要求的药品。
答案:正确8.《药品生产质量管理规范(2010年修订)》于2011年3月10日施行。
答案:错误。
(2011年3月1日施行。
)9.已确认的生产设备、生产环境(厂房)发生改变时,不需要确认。
答案:错误。
(应当进行再确认,必要时应经药品监督管理批准。
)10.质量管理部门人员通常可将职责委托给其他部门的人员。
答案:错误11.企业所有管理和操作人员职责通常不得委托给他人。
答案:正确12.企业所有人员上岗前应当接受健康检查。
答案:错误13.洁净区与非洁净区之间的压差应当不低于10帕斯卡,不同级别洁净区之间的压差应当不低于5帕斯卡。
答案:错误14.药品的设计与研发是药品生产前的科研活动,不属于GMP涵盖的范畴;答案:错误15.每批产品经质量受权人批准后方可放行。
答案:正确16.企业应当根据科学知识及经验对质量风险进行评估,以保证产品质量。
答案:正确17.企业的厂房、设施、设备和检验仪器应当经过确认,应当采用经过验证的生产工艺、操作规程和检验方法进行生产、操作和检验,并保持持续的验证状态。
答案:正确18.制药用水应当适合其用途,并符合《中华人民共和国药典》的质量标准及相关要求。
制药用水至少应当采用纯化水。
答案:错误19.每批药品的检验记录应当包括中间产品、待包装产品和成品的质量检验记录,可追溯该批药品所有相关的质量检验情况。
生产过程防止污染、交叉污染、混淆和差错的管理规程

生产过程防止污染、交叉污染、混淆和差错的管理规程目的:建立防止污染、交叉污染、混淆和差错管理规程,规定了在药品生产活动过程中防止污染、交叉污染、混淆和差错管理内容和要求适用范围:适用于药品生产活动过程中防止污染、交叉污染、混淆和差错的管理职责:生产技术部、质保部、车间对实施本规程负责内容:1.定义1.1污染:在生产、取样、包装或重新包装、贮存或运输等操作过程中,原辅料、中间产品、待包装产品、成品受到具有化学或微生物特性的杂质或异物的不利影响。
1.2 交叉污染:不同原料、辅料及产品之间发生的相互污染。
1.3混淆:在生产或包装的过程中,误将一种或一批物料当成了另一种或另一批物料进行使用、操作。
1.4 差错:在生产过程中,因为计量器具未调试到位、或计量方式不正确、或计数不准确而造成的错误2. 产生污染、交叉污染、混淆和差错的原因2.1 人员:操作人员患有传染病、皮肤病等,或未接受卫生方面的培训,未按要求穿戴工作服,行为不规范、人员带来外部污染,生产人员未按工艺规程和SOP要求操作,工作责任心不强,工作量过大,操作中随意性大等。
2.2 设备:表面不光洁、平整,材质不稳定,不易清洁,设备选型不合理,维修、保养不及时,没有定期验证或没有保持验证状态。
生产中使用的设备、容器无状态标志,清场不彻底等造成混淆。
2.3 物料:购进的原辅料本身质量不好,或在运输、贮存、检验取样、配料过程中造成污染。
原辅料微生物指标超限。
原辅料、包装材料、半成品、中间体等无明显标志,放置混乱,散装或放在易破损的包装中,印刷性包装材料管理不善等。
2.4 文件:文件管理制度不健全,或执行不力,无复核、监控,发现问题未及时查找原因等,特别是配料、包装等重要部门管理不严格。
2.5 环境:厂房设计不合理,生产环境如空气中粒子过多,车间地面、墙壁、天花板等不平整、易脱落、长霉、消毒不严格等造成污染。
2.6 清洁:清洁效果不能保证微生物除去水平及残留限度,清洁剂残留、消毒剂效果不能保证;生产结束后不及时清洁清场等造成污染。
药品生产过程质量控制

GMP之生产过程中防污染和交叉污染
对人员进行GMP基础知识培训、基础微生物学、人员卫生培训。生产厂房应仅限于经批准的人员出入。应严格按照相关的操作规程着装和进入洁净室。定期清洗和灭菌洁净服。穿着洁净服要收好袖口和领口,洁净服的下摆不应露在外面。帽子应能完全盖住头发并按照正确的方式佩戴口罩。直接接触药品和设备表面时要带手套。
在线检查/参数控制/记录与复核
干燥整粒
1.温度;2.湿度;3.空气流速;4.整粒筛网。
设备使用前检查/参数控制/检测水分
片剂生产过程关键参数控制
因素
关键参数
控制
总混
1.总混量;2.总混时间;3. 崩解剂加入量
设备使用前检查/参数控制/记录与复核
压片
1.预压力;2.主压力;3.释料速度;4.压片速度;5.填充深度;6.机器安装;7.进料方式。
药品生产过程控制
GMP对药品生产过程控制的基本要求
第一百八十四条 所有药品的生产和包装均应当按照批准的工艺规程和操作规程进行操作并有相关记录,以确保药品达到规定的质量标准,并符合药品生产许可和注册批准的要求。第一百八十七条 每批产品应当检查产量和物料平衡,确保物料平衡符合设定的限度。如有差异,必须查明原因,确认无潜在质量风险后,方可按照正常产品处理。第一百八十九条 在生产的每一阶段,应当保护产品和物料免受微生物和其他污染。
制药企业实施药品生产质量管理规范中存在的问题与对策

制药企业实施药品生产质量管理规范中存在的问题与对策摘要:本篇文章重点研究了药企在产品生产质量管理规范中,制度存在的问题以及质量管理的薄弱之处,为了进一步提高GMP的质量水平,在本篇文章也提出了相应的提升策略,研究了企业的生产质量管理认证资料和质量管理规范存在的缺陷,并做出全面统计。
企业在使用GMP质量机制时,同时还对质量管理机制、生产制度、人员培训等各方面工作作出了细致改良和提高。
关键词:制药企业;药品生产;质量管理规范;认证缺陷引言:药品生产质量管理规范是企业控制药品生产过程的一个重要文件资料,它可以保证药品生产稳定,而且整个生产过程都符合国家相关规定和要求,及质量标准。
在最大限度上,减少药品生产时,产生各类型污染和危害,及出现了一些交叉性污染、混淆,易出现差错的风险,这也是当前学国家制药企业和专家一致公认,在当前制药企业内,药品生产制造要建立起行之有效管理机制。
一、制造企业实施的药品生产质量管理规范在1988年,国家卫生部就发布了药品生产质量管理规范,在1995年开始逐步认证,这也就是我国的药企实施药品质量监管准则,使药品监管迈入了法制化轨道。
目前,国家执行的药品GMP都是在1992年修订的,为了便于认真执行检查,我国药监局也编制出来最新型药品生产质量认证规范标准,在2007年10月,并对检查评定标准进行了修订,在2008年1月,开始实行新修订后检查评定标准,而且该评定标准还是依据1998年版本。
但是新修订后评定标准更加细化,也更加严格,而且取消了限期整改,增加了人员、质量、生产物料及文件管理的各项检查项目,还强调了质量GMP与药品注册文件要求匹配,同时要求原料药和制剂都必须按照注册批准的工艺来生产,结合国家对药品GMP认证总体部署。
目前,我国药品制剂原料药和中药饮片都已在质量规范标准条件下来生产,也使药品生产质量得到更大保障[1]。
二、存在的问题在近两年药品的生产质量检查中,有近50%企业存在着药品质量管理规范缺陷问题,还有一些药企内部质量管理部门并没有严格去履行留样观察机制,部分项目检验和技术不太规范,未能够严格履行仪器试剂、滴定液,及培养基的管理职责。
药品生产企业的产品质量问题案例分析

药品生产企业的产品质量问题案例分析一、案例概述近年来,随着人们对医疗健康的关注持续增加,药品市场需求不断扩大。
然而,一些药品生产企业在追求利益最大化的同时,忽视了产品质量的重要性,导致产品质量问题日益突出。
本文将以某药品生产企业的产品质量问题为案例,分析其中的原因并提出相关对策措施。
二、案例分析某药品生产企业生产的某款抗生素药品被检测出含有过量的有害物质,严重威胁患者的健康。
经调查发现,该企业的产品质量问题主要集中在以下几个方面:1. 供应链问题:该企业采购的原材料中掺入了劣质物质,或者与合格原材料混淆。
这可能是由于企业在采购过程中未进行严格把关,未对供应商进行充分的审核和质量监控。
2. 生产过程问题:生产过程中缺乏科学管理,质量控制不严格,导致药品的处理、储存、包装等环节存在问题。
如药品的生产温度不符合规定,药品在储存过程中受到污染等。
3. 质量检验问题:质量检验环节存在问题,负责检验的人员技术水平低下或负有不正当行为,使得不合格药品未能被及时发现。
这可能是由于企业对质量检验流程和人员素质的管理不到位。
三、案例分析原因从以上案例中可以看出,药品生产企业的产品质量问题主要由供应链问题、生产过程问题和质量检验问题三个方面因素引起。
其原因如下:1. 利益驱动:药品生产企业往往追求利润最大化,导致在采购原材料时选择劣质物质或者与合格原材料混淆,从而降低成本。
2. 监管力度不足:监管部门对药品生产企业的监管力度不够,缺少对供应链、生产过程和质量检验的有效监管和审核,给企业留下了可乘之机。
3. 内部管理不善:企业在供应链管理、生产过程管理和质量检验管理方面存在缺失,对人员素质的要求和培训不到位,导致质量问题层出不穷。
四、对策措施针对以上问题,针对该药品生产企业的产品质量问题,可以采取以下对策措施:1. 强化监管力度:加强对药品生产企业的监管,确保企业在供应链、生产过程和质量检验环节的合规操作。
监管部门应提高监管水平,充实监管力量,建立健全监督检查机制。
药品差错和接近失误管理制度范本

药品差错和接近失误管理制度范本一、引言药品差错和接近失误是医疗领域中常见的问题,如果不及时有效地管理,可能对患者的健康造成严重影响甚至导致不可逆转的后果。
因此,建立一套科学合理的药品差错和接近失误管理制度是医疗机构必须重视和推行的重要措施。
二、管理目标本制度的目标是通过规范药品使用流程,提高医务人员和药师的工作质量和安全性,减少药品差错和接近失误的发生,并及时、妥善地处理已经发生的药品差错,以防范和减少患者伤害的风险。
三、管理原则1.严格遵循药品管理法规和伦理准则,保证医疗行为的合法性和伦理性。
2.注重药师和医务人员的培训和教育,提高专业素质和技术水平。
3.强调团队合作,加强沟通和协作,减少信息传递环境中的不确定性。
4.建立全面的差错和失误报告机制,鼓励全员参与,及时发现和纠正问题。
四、管理流程1.药品使用规范(1)药品使用必须按照医嘱和规定的剂量进行,禁止未经医师允许或私自增加、减少剂量。
(2)医务人员在使用药品前必须仔细阅读药品说明书或相关资料,了解副作用和注意事项。
(3)药师必须准确核对患者信息,确保将正确的药品发放给患者。
2.药品管理制度(1)建立完善的药品分类和存储管理制度,确保药品的有效性和安全性。
(2)定期检查药品的过期情况,及时清理和处理过期药品。
(3)严禁将药品留在护士站或医生办公室,必须按照规定的流程将药品归还药房。
3.药品差错和接近失误报告与处理(1)药师和医务人员发现药品差错或接近失误时,应立即向上级汇报,并填写相关报告。
(2)药房负责人在接到报告后,应及时调查核实,找出差错的原因并提出改进措施。
(3)对于已经发生的药品差错,药房负责人应及时采取补救措施,并向医务部门和患者说明情况。
(4)针对药品差错和接近失误,药房负责人应组织相关人员进行评估,总结经验教训,提出改进意见。
五、培训和教育(1)定期开展药品差错和接近失误的培训,提高医务人员和药师的意识和技能。
(2)加强对新员工的培训,使其熟悉操作流程和规范要求。
药品生产偏差管理探讨

药品生产偏差管理探讨摘要:近年来,我国的制药企业有了很大进展,药品生产也越来越受到重视。
通过在制药企业里进行药品生产偏差管理的实践,从遇到的实际问题入手提出偏差管理存在的问题,以及在管理理念上需要提高偏差管理认识,建立符合企业实际情况和科学的偏差管理程序,加强偏差管理现场培训及跟进处理,让偏差能够得到及时报告、调查和处理,通过偏差管理不断加深对工艺过程的理解和管控,防止污染、交叉污染、混淆和差错的发生。
关键词:药品;生产;GMP;偏差管理引言为了更好对药品质量进行监督管理,对影响药品质量的药事管理活动进行有效监管,国家药品监督管理部门按照《中华人民共和国药品管理法》有关条款具体规定,制定了一系列药品质量管理规范对药品进行监管,主要包括《药品生产质量管理规范》(GMP)《药品经营质量管理规范》(GSP)《药物非临床研究质量管理规范》(GLP)《药物临床试验质量管理规范》(GCP)《中药材生产质量管理规范》(GAP)。
1我国制药企业质量管理体系现状分析1)国家法规层面上制药工业相关质量管理法规建设不到位。
相关法律法规的建设目前还十分的简陋,没有完善的法规体系作支撑。
无相关制药企业的质量管理体系指南指导药品生产企业质量管理体系的建立和运行。
2)许多药品生产企业最高管理者把获得GMP证书作为企业经营的唯一目的,对建立一个有效运行质量管理体系的重大意义认识不足。
3)按GMP条款建立的质量管理机构在合法性和完整性近乎完美,但实际各层次的质量管理人员大多局限于自己的工作范畴,质量保证(QA)和质量控制(QC)之间缺乏有机联系和信息交流,也没有有效解决问题的途径,易存在质量管理的疏漏。
质量管理体系运行机制不健全,难以有效运行。
4)质量管理体系中质量保证(QA)和质量控制(QC)管理人员和工作人员专业素质参差不齐。
质量监督和检验工作多流于形式。
部分QA不懂或不了解生产工艺流程,生产记录数据有明显错误,也无法及时发现和纠正;不熟悉药政法规,对违法违规行为也无法及时制止,也起不到监督作用。
药品生产现场防止污染差错和混淆管理规程
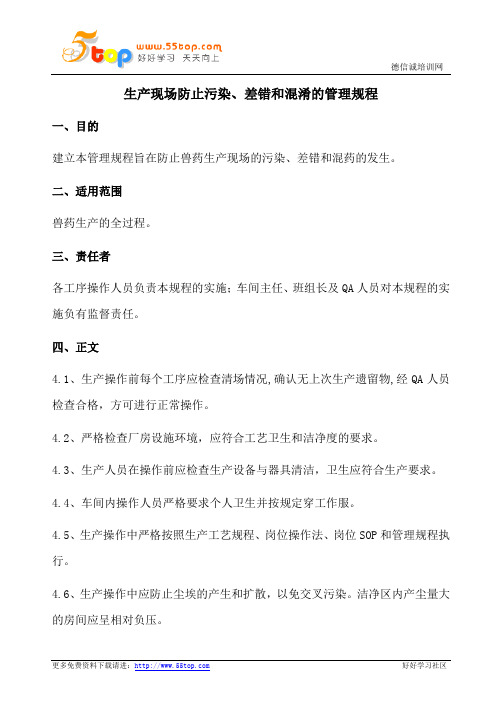
生产现场防止污染、差错和混淆的管理规程一、目的建立本管理规程旨在防止兽药生产现场的污染、差错和混药的发生。
二、适用范围兽药生产的全过程。
三、责任者各工序操作人员负责本规程的实施;车间主任、班组长及QA人员对本规程的实施负有监督责任。
四、正文4.1、生产操作前每个工序应检查清场情况,确认无上次生产遗留物,经QA人员检查合格,方可进行正常操作。
4.2、严格检查厂房设施环境,应符合工艺卫生和洁净度的要求。
4.3、生产人员在操作前应检查生产设备与器具清洁,卫生应符合生产要求。
4.4、车间内操作人员严格要求个人卫生并按规定穿工作服。
4.5、生产操作中严格按照生产工艺规程、岗位操作法、岗位SOP和管理规程执行。
4.6、生产操作中应防止尘埃的产生和扩散,以免交叉污染。
洁净区内产尘量大的房间应呈相对负压。
4.7、不同产品品种、规格、批号的生产操作不得在同一生产操作间同时进行。
4.8、有数条包装线同时进行不同产品品种、规格、批号的包装时,应采取隔离或其它有效防止差错或混淆的措施。
4.9、生产过程中防止物料及产品所产生的气体、蒸汽、喷雾物或生物体等引起的交叉污染。
4.10、每一生产操作间或生产用设备、容器应有所生产的产品或物料名称、批号、数量等状态标志。
4.11、无菌兽药的药液从配制到灭菌时间应符合规定。
4.12、无菌兽药生产用直接接触兽药的包装材料不得回收使用。
4.13、无菌兽药生产中,应采取措施避免物料、容器和设备最终清洗后的二次污染。
4.14、无菌兽药生产用直接接触兽药的包装材料、设备和其他物品的清洗、干燥、灭菌的使用时间应符合规定。
4.15、生产用物料、容器、设备或其他物品需进入洁净区时应经过消毒或灭菌处理。
4.16、非无菌兽药液体制剂配制、过滤、灌封、灭菌等过程应在规定时间内完成。
4.17、中药材使用前应按规定进行拣选、整理、剪切、炮制、洗涤等加工,需要浸润的中药材应做到药透水尽。
4.18、中药制剂生产过程中,中药材不应直接接触地面。
药物生产车间污染、交叉污染、混淆的防控
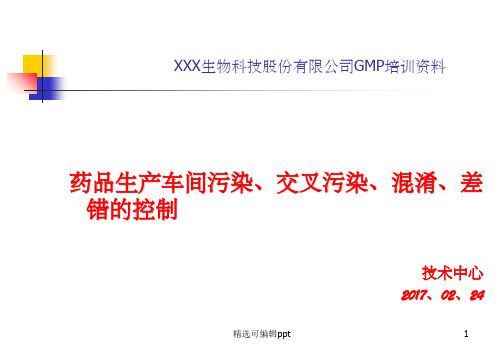
从原辅料来料检查一直到产品使用前的整过时间段的任何环节、产品( 物料)以任何状态存在的情况下都可能出现污染问题;
污染包括化学特性物质污染、微生物污染及异物(物理特性)污染;
污染的结果是对产品质量造成不利影响,由此给企业造成损失;
污染是指对某一种物质或一批次产品造成的影响,结果可能造成劣药、 甚至假药
************* 混淆是发生至少涉及两种/批及两种/批以上物料、产品; 混淆造成的后果可能是污染,甚至产生劣药、假药;
精选可编辑ppt
13
差错
主要是指错误或意外的变化。质量事故中人 为差错占15%左右;产生的原因主要是:
*************** 差错是错误,不等同于误差; 产生差错的因素主要有计量器具调试、计量方式、计数等计量方面;也
精选可编辑ppt
24
三、GMP有关交叉污染控制的相关条款
《生产管理》主要内容
•生产管理的原则(第184~196条,共13条) •防止生产过程中的污染和交叉污染(第197~198条,共2条) •生产操作(第199~201条,共3条) •包装操作(第202~216条,共15条)
•GMP附录一:无菌药品共15章81条 •GMP附录二:原料药共11章49条
第一节 原 则
第七十一条 设备的设计、选型、安装、改造和维护必须符合预定用途,应当尽可能降 低产生污染、交叉污染、混淆和差错的风险,便于操作、清洁、维护,以及必要时进行 的消毒或灭菌。
第二节 设计和安装
第七十四条 生产设备不得对药品质量产生任何不利影响。与药品直接接触的生产
设备表面应当平整、光洁、易清洗或消毒、耐腐蚀,不得与药品发生化学反应、吸附药
第六章物料与产品共有原则、原辅料、中间 产品和待包装产品、包装材料、成品、特殊 管理的物料和产品、其它计七节36条从原辅 料购进、接收、储运、分发等方面强调降低 污染、交叉污染的风险
药品生产企业质量风险管理

药品生产企业质量风险管理摘要:药品质量目前是制药企业最为重视的一项,因为近几年由于药品质量问题造成的事故屡见不鲜,所以为了社会的安定与人民的安全,药品质量管理刻不容缓。
在现阶段,我国的药品监管制度还不是很完善,药品在生产过程中的依然有混淆差错的风险。
本文就药品生产企业如何进行药品质量监管进行简要说明。
关键词:药品质量;药品生产;风险管理引言:在国家实行GMP标准的大背景下,我国制药产业取得了阶段性成效。
GMP标准是对制药过程中的一系列因素进行规范,包括制药厂房的环境、设备、卫生以及人员培训,旨在让药品产业生产出合格的药品,减少不合格的药品出现在市场上的概率。
药品作为人们治病的必需品,对于其质量应该严格把控,而药品的质量取决于药品生产企业的技术水准,其实更重要的是药品生产企业在内部应建立完善的药品监管制度。
对各方面因素进行调查记录,整合出企业内药品生产的各因素数据,统一规划管理,对药品质量进行严格把控。
1.质量风险管理是什么质量风险管理是对一个产品的各种因素进行系统化的研究,从而得出结论,为产品所可能发生的或已经发生的风险作评估,从而在质量上入手,降低风险。
总体而言,质量风险管理是基于一个产品的多方面因素而进行研究的系统程序。
这个系统包括风险识别、风险分析、风险评估,从而进行风险控制,使风险减少以及让风险处于可接受的范围,并且在后面要进行风险回顾,对产品总体做一个总结[1]。
2.质量风险管理的流程2.1风险识别运用相关方法进行风险分析以及对各种可能发生风险的总结,首先需要感知风险,了解各类风险,这需要风险管理部门有较强的洞察力,能够认识到企业生产过程中可能发生的各种风险,然后是分析风险,要分析风险发生的因素,要了解为什么会发生这样的风险。
2.2风险衡量在进行风险识别后,先对风险的发生率进行调查,然后对风险的大小进行衡量,分析风险可能造成的各种后果,对风险有了一定的认识后再根据风险可能性协助相关部门工作。
- 1、下载文档前请自行甄别文档内容的完整性,平台不提供额外的编辑、内容补充、找答案等附加服务。
- 2、"仅部分预览"的文档,不可在线预览部分如存在完整性等问题,可反馈申请退款(可完整预览的文档不适用该条件!)。
- 3、如文档侵犯您的权益,请联系客服反馈,我们会尽快为您处理(人工客服工作时间:9:00-18:30)。
贵州柏强制药有限公司Guizhou Berkin Pharmaceutical Co., Ltd.
关于成立防止差错与混淆管理质量风险评估小组的决定
司属各部门:
为了防止生产过程产生差错与混淆的影响,同时能够达《药品生产质量管理规范》2010版的要求,引入风险管理机制,差错与混淆的风险因素进行评估,对可能的危害进行判定,对于每种危害可能产生损害的严重性和危害的发生概率进行了估计,在某一风险水平不可接受时,建议采取了降低风险的措施,并在验证或日常监督管理中进行控制。
经质量风险管理委员会研究决定,成立质量风险评估小组。
组长:苏荣礼
成员:
质量部-------- 刘甫兴蔡晓梅李政田伟叶利
生产部-------- 李华邱金梁
工程部-------- 方红明方燎
物资部-------- 冉瑞模
行政部-------- 张志超
质量风险管理委员会
年月日
目录
1 目的................................................. 错误!未定义书签。
2 适用范围............................................. 错误!未定义书签。
3 定义................................................. 错误!未定义书签。
4风险管理成员及其职责 ................................. 错误!未定义书签。
5风险评估............................................. 错误!未定义书签。
6风险分析............................................. 错误!未定义书签。
药品生产过程差错与混淆风险分析表 ...................... 错误!未定义书签。
风险评价............................................... 错误!未定义书签。
7.风险控制............................................. 错误!未定义书签。
降低风险控制措施表..................................... 错误!未定义书签。
8 风险评估结论......................................... 错误!未定义书签。
9风险管理结果和回顾 ................................... 错误!未定义书签。
1 目的:
本次风险管理主要是按《药品生产质量管理规范》(2010年修订)要求,对药品生产过程中产生差错与混淆的风险进行管理活动的策划。
通过风险评估确认药品生产中差错与混淆的潜在风险,以及应采用的控制措施以最大限度地降低风险。
2 适用范围:
适用于药品生产过程中防止产生差错与混淆措施的质量风险评估。
3 定义:
风险:危害发生的可能性和严重性组合。
质量风险管理:在整个产品生命周期中采用前瞻和回顾的方式,对质量风险进行评估、控制、沟通和审核的过程。
质量风险:质量风险为危害出现的可能性和危害严重性的结合。
风险识别:系统的使用信息以确定危害的可能来源,是关于风险问题或问题描述。
风险分析:与一些确定危害相关的风险估计。
风险评估:在质量风险管理过程中,用于支持风险决定的信息进行组织的系统程序。
风险控制:执行质量风险管理决定的措施
风险降低:为了降低伤害出现的可能性和严重性而所采取的措施
风险接受:接受风险的决定
风险沟通:在决策者和相关方之间进行风险和质量风险管理方面的交流和共享。
5风险评估
风险评估方法【遵循FMEA技术(失效模式与影响分析)】:
风险确认:可能影响产品质量、产量、工艺操作或数据完整性的风险;
风险判定:包括评估先前确认风险的后果,其基础建立在严重程度、可能性及可检测性上;
严重程度(S):测定风险的潜在后果,主要针对可能危害产品质量、患者健康及数据完
可能性程度(P):测定风险产生的可能性。
根据积累的经验、工艺/操作复杂性知识或小
风险级别评判标准
RPN=严重性(S)×可能性(P)×可检测性(D)
6风险分析
风险评价:
药品生产过程防止差错与混淆的质量风险主要中高风险点存在于人员资质、清场管理、物料状态标志管理、生产操作、称量误差、配料中间站管理两个批号以上(含两个)同时包装未采取有效隔离措施、产品领头包装管理不规范及批记录信息传递错误等,因此。
在药品生产中应作为检查监控的重点,防止药品生产过程产生差错与混淆。
7.风险控制
8 风险评估结论
生产过程产生差错和混淆可考虑到的质量风险,都以FMEA的方式进行了辨识。
所有的风险以及相关推荐的防范措施已在FMEA表格中按影响差错和混淆的质量因素进行分析,所有可能产生的风险可以进行控制并在可接受范围内。
将存在的中高风险作为药品生产过程防止差错和混淆的监控重点,防止产生新的风险。
9风险管理结果和回顾
通过对药品生产过程防止差错和混淆的风险评估结论,针对不同等级的风险采取不同的控制措施,并通过人员资质、药品生产现场监控、生产状态标识管理、文件执行情况和批记录信息审核等进行控制,将质量风险管理的机制引入,对所有已知的风险均采取了针对性措施:硬件方面从设计、安装杜绝风险的发生,软件方面通过文件规定、培训、检查监控来降低风险。
计划回顾周期每3年开展一次,如果在评估之后详细设计发生了变更或生产的过程中有任何偏差产生,必须重新对系统进行部件关键性回顾性评估,以保证之前被判定为关键部件或非关键部件没有新获得任何关键功能。