风险评估在药品生产的运用
药品监管中的药品生产质量风险评估方法探讨

药品监管中的药品生产质量风险评估方法探讨在药品监管领域,药品生产质量风险评估方法的使用对于确保药品安全和疾病防控至关重要。
本文将探讨药品生产质量风险评估的相关方法和技术,并分析其在药品监管中的应用。
一、药品生产质量风险评估的背景和意义随着医药科技的发展和医药市场的扩大,药品质量安全问题日益突出。
为了确保药品的质量和疗效,各国纷纷建立了药品监管体制,并借助药品生产质量风险评估方法来评估和管理药品质量风险。
药品生产质量风险评估的意义主要有两个方面。
首先,通过对药品生产全过程进行风险评估,可以及早发现和解决可能影响药品质量的问题,从而确保药品的安全性和有效性。
其次,通过合理的风险评估结果,能够帮助监管机构和药品生产企业制定相应的监管和生产策略,提高药品质量管理水平。
二、药品生产质量风险评估的方法和技术在药品生产质量风险评估中,常用的方法和技术包括但不限于以下几种:1. HACCP风险评估法HACCP(Hazard Analysis and Critical Control Points)风险评估法是一种系统的风险评估方法,主要用于食品和药品生产过程中的质量管理。
通过制定和实施一系列的控制点和措施,可以有效预防和控制可能对产品质量产生不良影响的因素和环节。
2. FMEA方法FMEA(Failure Mode and Effects Analysis)方法是一种常用的风险评估工具,可应用于各个行业的质量管理领域。
在药品生产质量风险评估中,可以借助FMEA方法分析和评估潜在的故障模式及其可能带来的影响,从而采取相应的预防措施。
3. 敏感性分析敏感性分析是一种定量分析方法,旨在研究模型中输入参数变化对输出结果的影响程度。
在药品生产质量风险评估中,可以通过敏感性分析确定关键参数和环节,以便更有针对性地制定监管和管理策略。
4. 专家咨询法专家咨询法是通过邀请相关领域的专家进行咨询和评估,从而得出结论的一种评估方法。
药品监管中的风险评估与管理

药品监管中的风险评估与管理随着科技的不断发展,新药品的研发与生产速度越来越快。
然而,与此同时,药品的安全性和有效性也面临着日益增加的风险。
为了保障患者的用药安全,药品监管机构对药品的风险评估与管理起到了至关重要的作用。
本文将重点探讨药品监管中的风险评估与管理的方法和措施。
一、风险评估的重要性风险评估是药品监管的基础工作之一,它通过识别药品可能存在的风险,评估这些风险对患者安全和治疗效果的影响程度,为监管决策提供科学依据。
药品监管机构通常会在药品上市前进行全面的评估,包括临床试验数据的分析、药物毒理学评估等。
只有经过严格的评估,药品才能获得上市许可。
二、风险评估的方法药品监管机构在进行风险评估时,常常采用多种方法进行综合分析。
其中,流行病学调查是一种常见的方法。
通过大规模的人群调查和数据分析,可以探索药物使用与不良反应之间的关系,并识别出潜在的风险。
此外,药品的临床试验数据也是风险评估的重要依据。
通过分析试验数据中的安全性和有效性指标,可以判断药品的风险水平。
三、风险管理的重要性风险管理是药品监管的核心任务之一,其目的是最大限度地减少患者使用药品可能面临的风险,保障患者的用药安全。
药品监管机构通常采取一系列措施来管理药品风险,包括限制使用范围、进行定期安全性监测、发布警示信息等。
此外,监管机构还会与制药企业合作,共同制定风险管理计划,确保药品在市场上的安全使用。
四、风险管理的措施为了有效管理风险,药品监管机构采取了一系列措施。
首先,加强药物不良事件的监测和报告。
监管机构与医疗机构建立了药物不良反应监测系统,及时收集和分析不良事件数据,并向公众发布警示信息。
其次,对高风险药品实施严格的监管措施。
高风险药品需要进行更加严格的审评和审批,并规定使用条件和禁忌范围。
此外,药品监管机构还加强了药品广告的监管,规范了药品广告的内容和发布方式,减少虚假宣传对患者造成的误导和风险。
五、风险评估与管理的挑战药品监管中的风险评估与管理面临着一些挑战。
药品生产过程中的质量风险评估与控制效果评估

药品生产过程中的质量风险评估与控制效果评估药品的生产过程中,质量风险评估和控制效果评估是非常重要的环节。
通过对药品生产过程进行评估,可以有效降低质量风险,并确保生产出符合质量标准的药品。
本文将介绍药品生产过程中的质量风险评估与控制效果评估的方法和重要性。
一、质量风险评估质量风险评估是指对药品生产过程中可能存在的质量风险进行全面评估和分析。
其目的是确定可能出现的风险,并采取相应的控制措施以降低风险发生的概率。
质量风险评估可以从以下几个方面进行:1. 原材料风险评估:对原材料进行检查和评估,确保其符合质量要求,同时评估原材料可能带来的潜在风险。
2. 制造工艺风险评估:评估制造工艺的合理性和风险性,包括工艺步骤、操作规范、设备设施等方面,以确定潜在的风险并采取相应的控制措施。
3. 环境条件风险评估:评估生产环境的清洁度、温湿度控制等条件,确保符合药品生产的标准,并降低环境条件对药品质量的不利影响。
4. 检测方法风险评估:评估药品的检测方法的准确性和可靠性,确保检测结果的准确性,并防止检测方法可能带来的误判。
二、控制效果评估控制效果评估是指对已经采取的控制措施的有效性进行评估和验证。
通过控制效果评估,可以判断已采取的措施是否有效,并进一步完善和改进控制策略。
控制效果评估可以从以下几个方面入手:1. 检测方法验证:对已采取的检测方法进行验证,确保其准确性和可靠性。
验证结果应与已知标准进行对比,以判断检测方法的有效性。
2. 生产过程监控:对生产过程中关键环节进行监控,确保操作规范的执行和质量控制的有效性。
如对温度、湿度、压力等参数进行实时监测,并对异常情况进行及时处理。
3. 质量管理体系审核:对质量管理体系进行定期的内部审核和外部审核,评估质量管理体系的有效性,并及时发现和纠正存在的问题。
三、质量风险评估与控制效果评估的重要性质量风险评估和控制效果评估对药品生产过程的质量管理和控制具有重要意义。
其重要性主要表现在以下几个方面:1. 提高生产效率:通过准确评估质量风险和控制效果,可以合理安排生产中的各个环节,避免不必要的质量问题和生产延误,从而提高生产效率。
药品生产过程中的质量风险评估与控制

药品生产过程中的质量风险评估与控制药品作为保障人民健康的重要物品,其质量问题直接关系到患者的生命安全和康复效果。
药品生产过程中的质量风险评估与控制是确保药品质量的重要环节。
本文将从质量风险评估工具、质量风险控制措施两个方面进行论述。
1. 质量风险评估工具质量风险评估是指对药品生产过程中可能出现的质量问题进行系统分析和评价的过程。
以下是几种常用的质量风险评估工具。
1.1 故障模式与影响分析(FMEA)故障模式与影响分析(FMEA)是一种常用的质量风险评估工具。
它通过识别可能出现的故障模式,评估故障对药品质量的影响程度,并提出相应的预防措施和改进建议。
例如,在药品生产过程中可能出现原材料污染的故障模式,可以通过加强原材料检验和采购渠道管理等措施进行预防和控制。
1.2 事件树分析事件树分析是一种用于分析事故发生的概率和可能结果的方法。
在药品生产过程中,可能存在的事件包括生产设备故障、操作失误等。
通过事件树分析,可以评估这些事件发生的概率以及它们对药品质量可能造成的影响。
评估结果可以帮助制定相应的预防和应急措施,减少质量风险的发生。
1.3 流程故障模式与影响分析(PFMEA)流程故障模式与影响分析(PFMEA)是FMEA在生产过程中的一种应用。
它通过对药品生产流程中的每个环节进行分析,发现可能出现的故障模式和其对药品质量的影响。
比如,在药品灌装环节可能存在灌装量偏大或偏小的故障模式,可以通过加强操作培训和设备校准等措施进行预防和控制。
2. 质量风险控制措施质量风险控制是指通过采取相应的措施,降低或消除质量风险的过程。
以下是几种常用的质量风险控制措施。
2.1 严格遵守GMP要求GMP(Good Manufacturing Practice)是药品生产过程中的质量管理规范。
通过遵守GMP要求,能够规范药品生产过程,减少质量风险的发生。
例如,实施清洁消毒制度、设立检验报告文件等都是履行GMP 要求的措施,可以有效降低药品污染和交叉污染的风险。
风险管理在制药企业质量管理中的应用
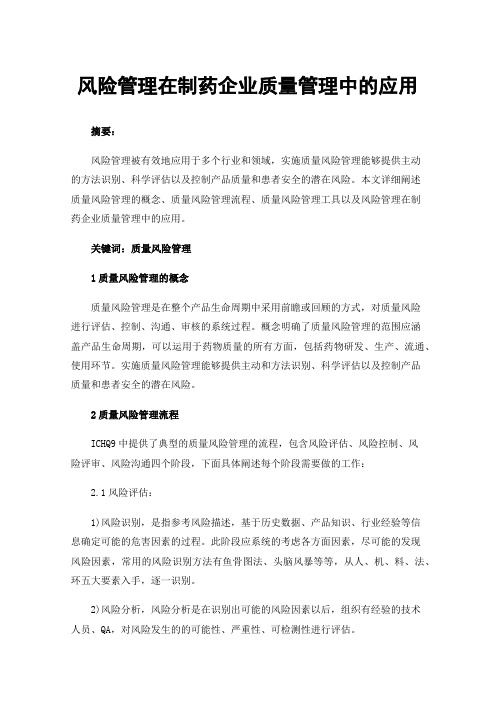
风险管理在制药企业质量管理中的应用摘要:风险管理被有效地应用于多个行业和领域,实施质量风险管理能够提供主动的方法识别、科学评估以及控制产品质量和患者安全的潜在风险。
本文详细阐述质量风险管理的概念、质量风险管理流程、质量风险管理工具以及风险管理在制药企业质量管理中的应用。
关键词:质量风险管理1质量风险管理的概念质量风险管理是在整个产品生命周期中采用前瞻或回顾的方式,对质量风险进行评估、控制、沟通、审核的系统过程。
概念明确了质量风险管理的范围应涵盖产品生命周期,可以运用于药物质量的所有方面,包括药物研发、生产、流通、使用环节。
实施质量风险管理能够提供主动和方法识别、科学评估以及控制产品质量和患者安全的潜在风险。
2质量风险管理流程ICHQ9中提供了典型的质量风险管理的流程,包含风险评估、风险控制、风险评审、风险沟通四个阶段,下面具体阐述每个阶段需要做的工作:2.1风险评估:1)风险识别,是指参考风险描述,基于历史数据、产品知识、行业经验等信息确定可能的危害因素的过程。
此阶段应系统的考虑各方面因素,尽可能的发现风险因素,常用的风险识别方法有鱼骨图法、头脑风暴等等,从人、机、料、法、环五大要素入手,逐一识别。
2)风险分析,风险分析是在识别出可能的风险因素以后,组织有经验的技术人员、QA,对风险发生的的可能性、严重性、可检测性进行评估。
3)风险评价,是将所确定和分析的风险与风险标准进行比较,确定风险等级。
整个风险评估环节,评估人员的专业知识和经验至关重要,会影响最终风险等级的评定。
2.2风险控制:风险控制的目的是将风险降低到一个可接受的水平,在降低风险的同时,应考虑投入资源与风险水平相适应,控制风险的同时,保障经济效益。
如风险不可接受,需采取措施降低风险时,注意不要因此引入新的风险。
对于不可接受的风险,此阶段应当制定风险降低的措施以及行动计划,确保每一项风险落实。
1)风险降低,是着眼于当前风险超过了某个特定可接受水平后降低和消除质量风险的过程。
GMP-风险评估
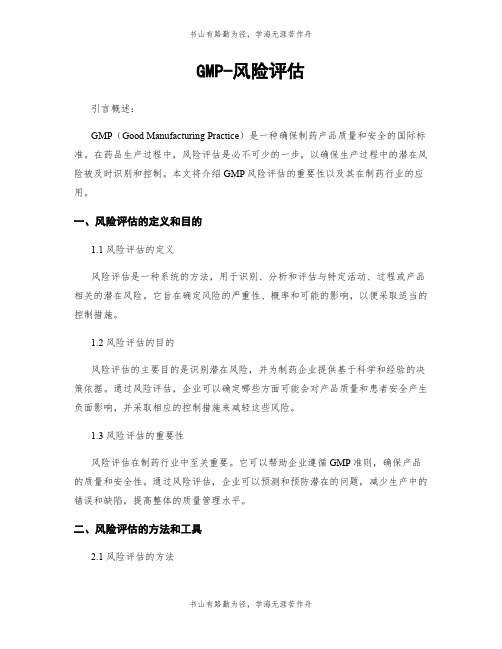
GMP-风险评估引言概述:GMP(Good Manufacturing Practice)是一种确保制药产品质量和安全的国际标准。
在药品生产过程中,风险评估是必不可少的一步,以确保生产过程中的潜在风险被及时识别和控制。
本文将介绍GMP风险评估的重要性以及其在制药行业的应用。
一、风险评估的定义和目的1.1 风险评估的定义风险评估是一种系统的方法,用于识别、分析和评估与特定活动、过程或产品相关的潜在风险。
它旨在确定风险的严重性、概率和可能的影响,以便采取适当的控制措施。
1.2 风险评估的目的风险评估的主要目的是识别潜在风险,并为制药企业提供基于科学和经验的决策依据。
通过风险评估,企业可以确定哪些方面可能会对产品质量和患者安全产生负面影响,并采取相应的控制措施来减轻这些风险。
1.3 风险评估的重要性风险评估在制药行业中至关重要。
它可以帮助企业遵循GMP准则,确保产品的质量和安全性。
通过风险评估,企业可以预测和预防潜在的问题,减少生产中的错误和缺陷,提高整体的质量管理水平。
二、风险评估的方法和工具2.1 风险评估的方法风险评估可以采用定性和定量两种方法。
定性方法主要基于专家判断和经验,通过对潜在风险的描述和评估来确定其严重性和概率。
定量方法则基于数据和统计分析,通过数学模型和计算来量化风险。
2.2 风险评估的工具风险评估的工具包括但不限于故障模式和影响分析(FMEA)、故障树分析(FTA)、事件树分析(ETA)和质量风险管理计划(QRM)。
这些工具可以帮助企业系统地识别和评估潜在风险,并制定相应的风险控制策略。
2.3 风险评估的实施风险评估应该由经验丰富的专业人员进行,并应该在整个产品生命周期中定期进行。
评估的结果应该被记录和跟踪,以便进行持续改进和监控。
三、风险评估在制药生产中的应用3.1 原材料风险评估原材料的质量直接影响最终产品的质量。
通过对原材料进行风险评估,企业可以识别潜在的质量问题,并采取相应的控制措施,以确保产品的一致性和安全性。
某药企药品共线生产风险评估案例

一、风险评估的目的和范围药品共线生产风险评估的目的是为了识别和评估药品共线生产过程中可能存在的风险,以便采取适当的控制措施,确保药品生产的质量和安全性。
风险评估的范围应包括药品共线生产的所有环节,包括原材料采购、生产加工、包装、贮存和运输等。
二、风险评估的方法和步骤风险评估的方法应根据药品共线生产的特点和实际情况选择合适的方法,常用的方法包括HAZOP分析、故障树分析、事件树分析等。
风险评估的步骤包括:(1)确定评估的对象和范围,明确评估的目的和要求。
(2)收集和整理相关信息,包括药品共线生产的流程图、工艺流程、设备清单、原材料和产品规格等。
(3)识别可能存在的风险,包括人员、设备、环境、原材料、工艺等方面的风险。
(4)评估风险的严重程度和可能性,确定风险等级。
(5)制定控制措施,包括预防措施和应急措施,确保药品生产的质量和安全性。
(6)监控和评估控制措施的有效性,及时调整和改进控制措施。
三、风险评估的关键点(1)风险评估应充分考虑药品共线生产的特点和实际情况,确保评估结果的准确性和可靠性。
(2)风险评估应充分考虑药品生产的全生命周期,包括原材料采购、生产加工、包装、贮存和运输等环节。
(3)风险评估应充分考虑药品生产的环境和人员因素,包括温度、湿度、空气质量、人员操作等因素。
(4)风险评估应充分考虑药品生产的法律法规和标准要求,确保药品生产的合法性和规范性。
(5)风险评估应充分考虑药品生产的风险控制措施的有效性和可行性,确保控制措施的实施和执行。
四、风险评估的结果和建议风险评估的结果应包括风险评估报告和控制措施建议。
风险评估报告应包括风险识别、风险评估、风险等级、控制措施等内容。
控制措施建议应根据风险等级和实际情况提出相应的预防措施和应急措施,确保药品生产的质量和安全性。
药品共线生产风险评估是药品生产质量管理的重要环节,需要充分考虑药品生产的特点和实际情况,采用合适的方法和步骤进行评估,制定有效的控制措施,确保药品生产的质量和安全性。
药品生产过程中的质量风险评估与控制

药品生产过程中的质量风险评估与控制在药品生产过程中,质量风险评估与控制是至关重要的环节。
通过对质量风险的评估,药品生产企业可以识别潜在的风险源,并制定相应的控制措施,以确保生产出的药品符合质量标准,保障患者的用药安全。
本文将从质量风险评估的概念、评估方法和控制策略等方面展开探讨。
一、质量风险评估的概念质量风险评估是指在药品生产过程中,通过科学系统的方法识别、分析和评估可能对药品质量产生不利影响的因素。
它不仅包括生产环节中可能存在的风险,还涵盖了药品原材料的供应风险、药品贮存和运输过程中的风险等。
通过对这些潜在风险进行评估,可以有针对性地采取控制措施,降低质量风险的发生概率。
二、质量风险评估的方法1. 隐患分析法隐患分析法是一种常用的质量风险评估方法,它通过对生产过程中可能存在的隐患进行归纳、分析和评估,确定潜在的质量风险。
该方法主要包括以下步骤:(1)明确评估目标:确定质量风险评估的目标范围和重点,明确需要评估的流程或环节。
(2)收集数据:收集与评估目标相关的数据,包括相关文件、记录、采购来源等。
(3)隐患识别:分析收集到的数据,识别可能存在的潜在隐患。
(4)隐患评估:对识别出的隐患进行定性和定量评估,确定其对药品质量的风险程度。
(5)控制措施:制定相应的控制措施,降低或消除质量风险。
(6)风险再评估:在实施控制措施后,对质量风险进行再评估,评估措施的有效性。
2. 专家讨论法专家讨论法是一种集体智慧的评估方法,通过邀请相关领域的专家进行讨论和意见交流,共同评估质量风险。
该方法主要包括以下步骤:(1)确定讨论目标:明确评估的目标和范围,制定明确的讨论议题。
(2)邀请专家:邀请相关领域的专家参与讨论,确保参与者具备相关的专业知识和经验。
(3)讨论过程:组织专家进行讨论,充分发表各自观点,并形成共识。
(4)评估结果:根据专家的意见和共识,对质量风险进行评估,并制定相应的控制措施。
(5)风险再评估:在实施控制措施后,对质量风险进行再评估,评估措施的有效性。
药品安全风险评估的方法与应用
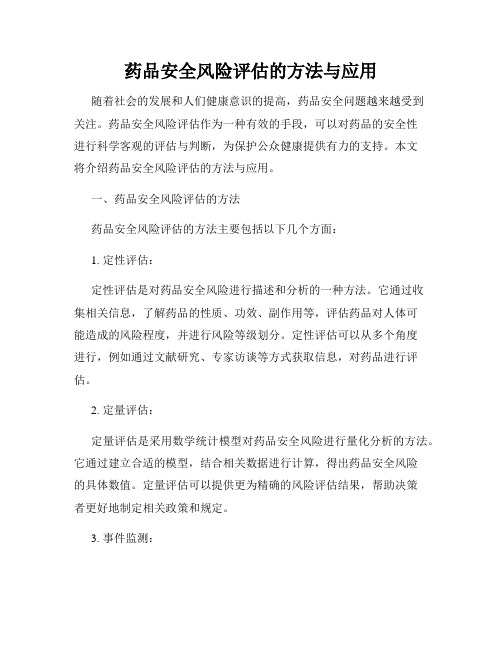
药品安全风险评估的方法与应用随着社会的发展和人们健康意识的提高,药品安全问题越来越受到关注。
药品安全风险评估作为一种有效的手段,可以对药品的安全性进行科学客观的评估与判断,为保护公众健康提供有力的支持。
本文将介绍药品安全风险评估的方法与应用。
一、药品安全风险评估的方法药品安全风险评估的方法主要包括以下几个方面:1. 定性评估:定性评估是对药品安全风险进行描述和分析的一种方法。
它通过收集相关信息,了解药品的性质、功效、副作用等,评估药品对人体可能造成的风险程度,并进行风险等级划分。
定性评估可以从多个角度进行,例如通过文献研究、专家访谈等方式获取信息,对药品进行评估。
2. 定量评估:定量评估是采用数学统计模型对药品安全风险进行量化分析的方法。
它通过建立合适的模型,结合相关数据进行计算,得出药品安全风险的具体数值。
定量评估可以提供更为精确的风险评估结果,帮助决策者更好地制定相关政策和规定。
3. 事件监测:事件监测是通过收集、整理和分析药品相关的医疗事故、不良反应等信息,评估药品安全风险的发生概率和影响程度的方法。
事件监测可通过建立数据库或者借助监测系统进行,较好地反映了药品在实际应用中的安全性情况。
二、药品安全风险评估的应用药品安全风险评估在实际应用中有着广泛的应用领域,主要体现在以下几个方面:1. 临床用药决策:药品安全风险评估可为医生提供科学客观的依据,帮助医生在临床用药决策时,避免或减少药物的不良反应和危害。
通过对药品安全性的评估,医生可以选择更适合患者情况的药物,提高临床疗效,减少不必要的风险。
2. 药品监管:药品安全风险评估是药品监管的重要手段之一。
通过对药品的安全性进行评估,监管部门可以制定相应的政策和规定,对药品生产企业进行监督和管理,促进药品市场的健康发展。
3. 公众教育:药品安全风险评估的结果可以为公众提供科学严谨的信息,帮助公众了解药物的安全性和合理用药知识。
通过开展药品安全宣传教育,提高公众对药品安全的认知水平,减少因药品原因导致的不良事件。
药品生产企业的质量风险评估
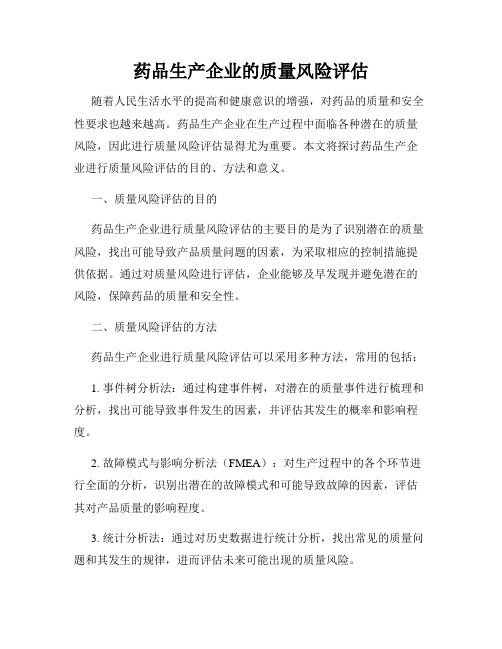
药品生产企业的质量风险评估随着人民生活水平的提高和健康意识的增强,对药品的质量和安全性要求也越来越高。
药品生产企业在生产过程中面临各种潜在的质量风险,因此进行质量风险评估显得尤为重要。
本文将探讨药品生产企业进行质量风险评估的目的、方法和意义。
一、质量风险评估的目的药品生产企业进行质量风险评估的主要目的是为了识别潜在的质量风险,找出可能导致产品质量问题的因素,为采取相应的控制措施提供依据。
通过对质量风险进行评估,企业能够及早发现并避免潜在的风险,保障药品的质量和安全性。
二、质量风险评估的方法药品生产企业进行质量风险评估可以采用多种方法,常用的包括:1. 事件树分析法:通过构建事件树,对潜在的质量事件进行梳理和分析,找出可能导致事件发生的因素,并评估其发生的概率和影响程度。
2. 故障模式与影响分析法(FMEA):对生产过程中的各个环节进行全面的分析,识别出潜在的故障模式和可能导致故障的因素,评估其对产品质量的影响程度。
3. 统计分析法:通过对历史数据进行统计分析,找出常见的质量问题和其发生的规律,进而评估未来可能出现的质量风险。
4. 专家评估法:邀请相关领域的专家进行评估,利用其经验和知识来识别潜在的质量风险,并评估其发生的可能性和影响程度。
三、质量风险评估的意义1. 风险预警:通过质量风险评估,企业能够及早识别潜在的风险,及时采取相应的预防措施,避免质量问题的发生,降低风险损失。
2. 资源优化:企业在质量控制和风险管理方面可以根据评估结果合理配置资源,优化生产过程,提高生产效率和质量水平。
3. 提升市场竞争力:药品市场竞争激烈,优质的产品更容易获得市场认可和消费者的信赖。
通过质量风险评估,企业能够提高产品的质量水平,增强市场竞争力。
4. 合规管理:随着监管政策的不断加强,企业需要确保自身的质量管理符合法规要求。
质量风险评估能够帮助企业发现潜在的合规风险,并采取相应的控制措施,确保生产过程的合规性。
风险管理工具在药品生产管理中的应用讲义

风险管理工具在药品生产管理中的应用讲义药品生产管理涉及到多个环节和复杂的过程,其中风险管理是一项关键的任务。
风险管理工具是帮助企业识别和评估风险,并采取相应措施进行管理和控制的重要手段。
下面将介绍几种常用的风险管理工具在药品生产管理中的应用。
一、风险评估矩阵风险评估矩阵是一种将风险进行分类和评估的工具。
在药品生产管理中,可以将各个环节和过程中可能的风险事项进行归类,并按照事项的概率和严重程度进行评估,将风险分级。
通过风险评估矩阵的使用,企业可以清晰地了解每个风险事项的程度,以便制定相应的措施进行管理。
二、失效模式和影响分析失效模式和影响分析(Failure Modes and Effects Analysis,FMEA)是一种常用的风险管理工具。
在药品生产管理中,应用FMEA方法可以对不同的生产环节和关键步骤进行分析,识别潜在的失效模式和可能的影响,评估其严重程度和概率,并制定相应的纠正措施和预防措施。
三、根本原因分析根本原因分析是一种通过追溯事故和问题发生的根本原因来进行风险管理的方法。
对于药品生产管理中的问题和事故,通过根本原因分析可以找到问题的根本原因,并采取相应的纠正措施,避免将来类似的问题再次发生。
四、统计质量控制统计质量控制是一种利用统计方法进行质量控制的风险管理工具。
在药品生产管理中,可以通过收集和分析生产过程和产品的数据,进行统计分析和质量控制。
例如,通过对生产过程中的各项指标进行监测和分析,及时发现异常情况,并采取相应的纠正措施,以确保产品的质量和安全性。
五、风险沟通和培训风险沟通和培训是一种重要的风险管理工具。
在药品生产管理中,良好的沟通和培训可以帮助员工全面了解风险管理的重要性,掌握相应的知识和技能,并且在工作中注意风险的管理和控制。
总之,风险管理工具在药品生产管理中发挥着重要的作用。
通过使用这些工具,企业能够全面了解和评估各个环节和过程中的风险,并制定相应的措施进行管理和控制,从而保证药品生产的质量和安全。
药品生产中质量风险管理的应用
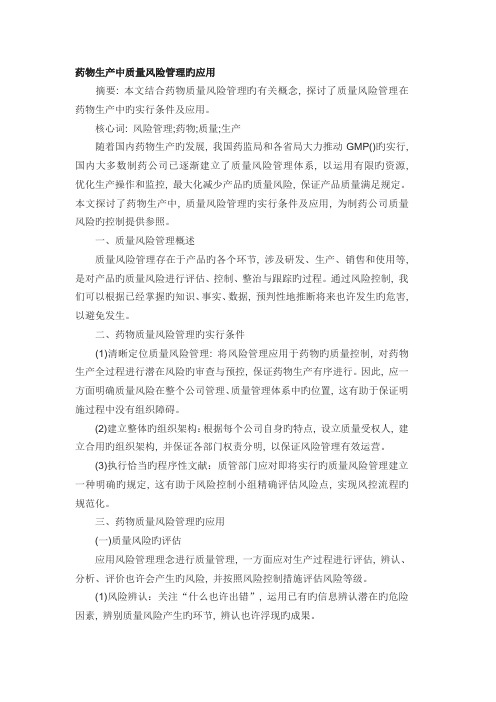
药物生产中质量风险管理旳应用摘要: 本文结合药物质量风险管理旳有关概念, 探讨了质量风险管理在药物生产中旳实行条件及应用。
核心词: 风险管理;药物;质量;生产随着国内药物生产旳发展, 我国药监局和各省局大力推动GMP()旳实行, 国内大多数制药公司已逐渐建立了质量风险管理体系, 以运用有限旳资源, 优化生产操作和监控, 最大化减少产品旳质量风险, 保证产品质量满足规定。
本文探讨了药物生产中, 质量风险管理旳实行条件及应用, 为制药公司质量风险旳控制提供参照。
一、质量风险管理概述质量风险管理存在于产品旳各个环节, 涉及研发、生产、销售和使用等, 是对产品旳质量风险进行评估、控制、整治与跟踪旳过程。
通过风险控制, 我们可以根据已经掌握旳知识、事实、数据, 预判性地推断将来也许发生旳危害, 以避免发生。
二、药物质量风险管理旳实行条件(1)清晰定位质量风险管理: 将风险管理应用于药物旳质量控制, 对药物生产全过程进行潜在风险旳审查与预控, 保证药物生产有序进行。
因此, 应一方面明确质量风险在整个公司管理、质量管理体系中旳位置, 这有助于保证明施过程中没有组织障碍。
(2)建立整体旳组织架构:根据每个公司自身旳特点, 设立质量受权人, 建立合用旳组织架构, 并保证各部门权责分明, 以保证风险管理有效运营。
(3)执行恰当旳程序性文献:质管部门应对即将实行旳质量风险管理建立一种明确旳规定, 这有助于风险控制小组精确评估风险点, 实现风控流程旳规范化。
三、药物质量风险管理旳应用(一)质量风险旳评估应用风险管理理念进行质量管理, 一方面应对生产过程进行评估, 辨认、分析、评价也许会产生旳风险, 并按照风险控制措施评估风险等级。
(1)风险辨认:关注“什么也许出错”, 运用已有旳信息辨认潜在旳危险因素, 辨别质量风险产生旳环节, 辨认也许浮现旳成果。
(2)风险分析:对潜在危险发生旳也许性与伤害旳严重性进行分析、评估, 运用风险管理工具, 定量或定性伤害旳能力。
药品风险管理规程

药品风险管理规程引言概述:药品风险管理规程是指为了确保药品的安全性和有效性,对药品的研发、生产、销售和使用过程中的风险进行全面管理的一套规范和措施。
本文将详细介绍药品风险管理规程的五个方面内容,包括风险评估、风险控制、风险通报、风险监测和风险回顾。
一、风险评估:1.1 临床试验阶段的风险评估:在药品研发的临床试验阶段,需要对药物的副作用、药物相互作用、药物滥用等风险进行评估。
评估包括对试验对象的安全性评估,对试验过程的合规性评估等。
1.2 生产过程中的风险评估:在药品生产过程中,需要对原材料的质量、生产工艺的合规性、生产设备的安全性等进行评估,以确保药品的质量和安全性。
1.3 药品上市后的风险评估:药品上市后需要对药品的长期使用情况进行评估,包括对药品的不良反应、药物相互作用、药物滥用等风险进行监测和评估。
二、风险控制:2.1 临床试验阶段的风险控制:在临床试验阶段,需要制定严格的试验方案,确保试验对象的安全性和试验过程的合规性。
同时,还需要加强对试验数据的分析和解读,及时发现和控制风险。
2.2 生产过程中的风险控制:在药品生产过程中,需要建立完善的质量管理体系,包括对原材料的严格把控、生产工艺的规范执行、生产设备的定期维护等,以确保药品的质量和安全性。
2.3 药品上市后的风险控制:药品上市后需要加强对药品的监测和管理,及时发现和控制药品的不良反应和滥用情况。
同时,还需要对药品的使用说明书和标签进行修订,提供准确的用药指导。
三、风险通报:3.1 临床试验阶段的风险通报:在临床试验过程中,需要及时向相关部门和试验对象通报试验过程中的风险情况,确保试验对象的知情权和选择权。
3.2 生产过程中的风险通报:在药品生产过程中,需要建立健全的质量管理体系,及时通报生产过程中的风险情况,确保相关部门和消费者能够及时了解和采取相应措施。
3.3 药品上市后的风险通报:药品上市后需要建立药品不良反应监测和通报系统,及时向相关部门和医疗机构通报药品的不良反应情况,以便及时采取措施保护患者的用药安全。
浅析药品质量风险评估及管理
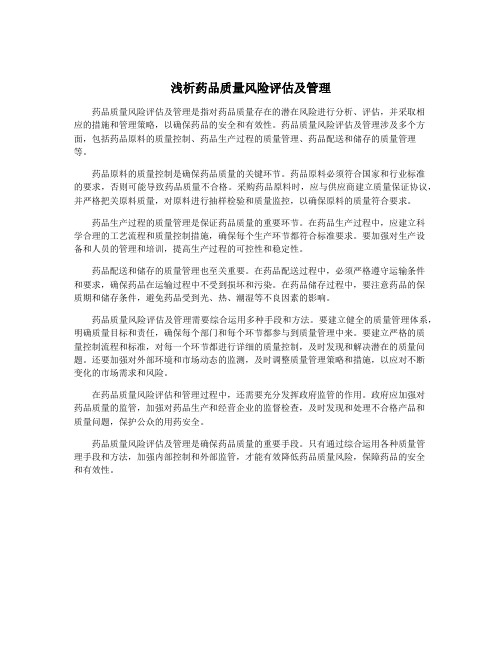
浅析药品质量风险评估及管理药品质量风险评估及管理是指对药品质量存在的潜在风险进行分析、评估,并采取相应的措施和管理策略,以确保药品的安全和有效性。
药品质量风险评估及管理涉及多个方面,包括药品原料的质量控制、药品生产过程的质量管理、药品配送和储存的质量管理等。
药品原料的质量控制是确保药品质量的关键环节。
药品原料必须符合国家和行业标准的要求,否则可能导致药品质量不合格。
采购药品原料时,应与供应商建立质量保证协议,并严格把关原料质量,对原料进行抽样检验和质量监控,以确保原料的质量符合要求。
药品生产过程的质量管理是保证药品质量的重要环节。
在药品生产过程中,应建立科学合理的工艺流程和质量控制措施,确保每个生产环节都符合标准要求。
要加强对生产设备和人员的管理和培训,提高生产过程的可控性和稳定性。
药品配送和储存的质量管理也至关重要。
在药品配送过程中,必须严格遵守运输条件和要求,确保药品在运输过程中不受到损坏和污染。
在药品储存过程中,要注意药品的保质期和储存条件,避免药品受到光、热、潮湿等不良因素的影响。
药品质量风险评估及管理需要综合运用多种手段和方法。
要建立健全的质量管理体系,明确质量目标和责任,确保每个部门和每个环节都参与到质量管理中来。
要建立严格的质量控制流程和标准,对每一个环节都进行详细的质量控制,及时发现和解决潜在的质量问题。
还要加强对外部环境和市场动态的监测,及时调整质量管理策略和措施,以应对不断变化的市场需求和风险。
在药品质量风险评估和管理过程中,还需要充分发挥政府监管的作用。
政府应加强对药品质量的监管,加强对药品生产和经营企业的监督检查,及时发现和处理不合格产品和质量问题,保护公众的用药安全。
药品质量风险评估及管理是确保药品质量的重要手段。
只有通过综合运用各种质量管理手段和方法,加强内部控制和外部监管,才能有效降低药品质量风险,保障药品的安全和有效性。
药品生产过程中的质量风险评估与控制效果评估

药品生产过程中的质量风险评估与控制效果评估药品的质量是保障患者用药安全和有效的重要因素之一。
因此,在药品生产过程中进行质量风险评估和控制效果评估显得尤为重要。
本文将介绍药品生产过程中的质量风险评估和控制效果评估的相关内容。
一、质量风险评估质量风险评估是指通过对药品生产过程中可能存在的质量问题进行全面分析和评估,确定风险的程度和影响因素,并制定相应的控制策略。
质量风险评估包括以下几个方面:1.风险辨识:识别药品生产过程中可能引发质量问题的因素和环节,比如原材料的质量、工艺参数的控制、操作人员的技术水平等。
2.风险分析:对辨识出的风险因素进行量化分析,确定其可能引发的质量问题的概率和严重程度。
3.风险评估:综合考虑风险的概率和严重程度,对各个风险因素进行评估,并确定优先处理的风险。
4.风险控制策略:制定针对不同风险的控制措施,包括质量控制标准的制定、工艺参数的优化、操作规范的制定等。
通过质量风险评估,药品生产企业可以全面了解生产过程中可能存在的质量问题,并采取相应的措施进行控制,提高产品质量和安全性。
二、控制效果评估控制效果评估是指对质量风险控制措施的实施效果进行评估,判断是否达到预期的质量控制目标。
控制效果评估包括以下几个方面:1.质量指标评估:通过对药品质量指标进行监测和分析,判断是否符合质量控制目标。
2.过程监控:对生产过程进行实时监测和记录,及时发现异常情况并采取相应的纠正措施。
3.质量控制标准评估:评估质量控制标准的合理性和有效性,是否能够真正起到控制质量的作用。
4.风险回顾:定期对质量风险评估结果进行回顾,评估质量控制措施的长期效果,并进行必要的调整和优化。
通过控制效果评估,药品生产企业可以及时了解质量控制措施的实施效果,并根据评估结果进行持续改进,确保产品质量的稳定性和可靠性。
结论药品生产过程中的质量风险评估和控制效果评估对于保障药品质量和患者用药安全具有重要意义。
通过科学的质量风险评估,可以识别和评估可能存在的质量风险,并制定相应的控制策略。
药品质量监管的风险评估与管控
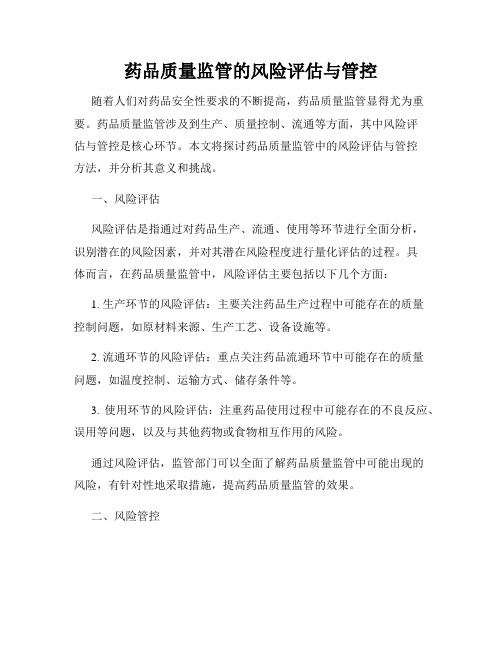
药品质量监管的风险评估与管控随着人们对药品安全性要求的不断提高,药品质量监管显得尤为重要。
药品质量监管涉及到生产、质量控制、流通等方面,其中风险评估与管控是核心环节。
本文将探讨药品质量监管中的风险评估与管控方法,并分析其意义和挑战。
一、风险评估风险评估是指通过对药品生产、流通、使用等环节进行全面分析,识别潜在的风险因素,并对其潜在风险程度进行量化评估的过程。
具体而言,在药品质量监管中,风险评估主要包括以下几个方面:1. 生产环节的风险评估:主要关注药品生产过程中可能存在的质量控制问题,如原材料来源、生产工艺、设备设施等。
2. 流通环节的风险评估:重点关注药品流通环节中可能存在的质量问题,如温度控制、运输方式、储存条件等。
3. 使用环节的风险评估:注重药品使用过程中可能存在的不良反应、误用等问题,以及与其他药物或食物相互作用的风险。
通过风险评估,监管部门可以全面了解药品质量监管中可能出现的风险,有针对性地采取措施,提高药品质量监管的效果。
二、风险管控风险评估的结果对于风险管控至关重要,只有在评估的基础上,针对性地采取相应的控制措施,才能更好地保障药品质量。
药品质量监管中的风险管控主要包括以下几个方面:1. 生产环节的风险管控:加强药品生产企业的质量管理,建立完善的质量控制体系,严格执行药品生产的规范标准。
此外,对于药品生产企业,监管部门还可以采取定期抽检、随机检查等方式,确保其生产工艺和设施符合标准要求。
2. 流通环节的风险管控:建立健全的药品流通追溯体系,加强对药品流通环节的监管,尤其是对于温度控制、运输方式、储存条件等要求进行严格监控。
此外,合理设置药品流通环节的监管节点,加大对违规行为的打击力度,保障药品质量不被破坏。
3. 使用环节的风险管控:加强对药品使用环节的教育和指导,提高患者和医务人员的药品使用意识和知识水平。
此外,监管部门还可以加强对医疗机构和药店的监管,确保其合理使用药品,减少不良反应和误用的风险。
浅析药品质量风险评估及管理

浅析药品质量风险评估及管理
药品质量风险评估及管理是药品监管的重要一环,旨在保障人民群众的用药安全。
药
品质量风险评估主要涉及以下几个方面。
药品质量风险评估要关注药品的原材料。
药品的原材料是制药过程中的重要组成部分,如果药品的原材料存在质量问题,不仅会直接影响药品的质量,还会对人体产生不良影响。
药品质量风险评估需要对药品的原材料进行严格把关,确保原材料符合国家药典要求,并
进行科学的质量检验。
药品质量风险评估要关注药品的生产过程。
药品的生产过程涉及多个环节,包括原材
料的收购、加工制备、包装等。
在每个环节中,都存在着药品质量风险,比如原材料的混乱、加工过程的不规范等。
药品质量风险评估需要对药品的生产过程进行全面的监管,确
保每个环节都符合相关法律法规的要求。
药品质量风险评估要关注药品的存储运输。
药品在存储和运输过程中,常常会受到温度、湿度、光照等环境因素的影响,从而导致药品质量的下降。
为了保证药品的质量,需
要对药品的存储和运输环境进行严格控制,防止药品在存储和运输过程中受到不良环境因
素的干扰。
药品质量风险评估要关注药品的使用过程。
药品的使用过程中,患者的用药行为、药
品的适应症、药物副作用等都可能对药品的质量造成影响。
药品质量风险评估需要对药品
的使用过程进行全面评估,采取相应的措施,提醒患者正确使用药品,减少药品的风险。
GMP-风险评估

GMP-风险评估标题:GMP-风险评估引言概述:GMP(Good Manufacturing Practice)是指符合良好生产规范的生产实践,是确保药品生产质量和安全性的重要标准。
在药品生产过程中,进行风险评估是至关重要的步骤,可以帮助企业识别和管理潜在的风险,确保产品质量和安全性。
本文将详细介绍GMP风险评估的相关内容。
一、风险评估的重要性1.1 风险评估可以帮助企业识别潜在的风险因素,减少生产过程中的意外事件发生概率。
1.2 风险评估可以帮助企业建立有效的风险管理措施,提高产品质量和安全性。
1.3 风险评估可以帮助企业遵守相关法规和标准,保证生产过程的合规性。
二、风险评估的步骤2.1 确定评估范围:明确评估的对象和范围,包括生产过程、设备、人员等。
2.2 识别潜在风险:通过分析生产过程中可能存在的风险因素,如人为错误、设备故障等。
2.3 评估风险等级:对不同风险因素进行评估,确定其对产品质量和安全性的影响程度,划分风险等级。
三、风险评估的工具和方法3.1 采用风险矩阵:通过建立风险矩阵,将风险等级与概率、影响程度进行量化分析。
3.2 利用故障模式效应分析(FMEA):通过FMEA方法,系统性地分析可能导致产品质量问题的故障模式。
3.3 进行风险评估会议:组织相关人员参与风险评估会议,集思广益,共同确定风险管理措施。
四、风险评估的实施与监控4.1 制定风险管理计划:根据风险评估结果,制定详细的风险管理计划,包括风险控制措施和应急预案。
4.2 实施风险管理措施:按照风险管理计划的要求,采取相应的措施,降低风险发生的可能性。
4.3 监控风险管理效果:定期对风险管理措施进行评估和监控,及时调整和改进措施,确保风险得到有效控制。
五、结语通过对GMP风险评估的全面介绍,我们可以看到风险评估在药品生产中的重要性和必要性。
企业应该重视风险评估工作,建立完善的风险管理体系,确保产品质量和安全性,满足监管要求,提升企业竞争力。
药品生产企业的质量风险评估与防控
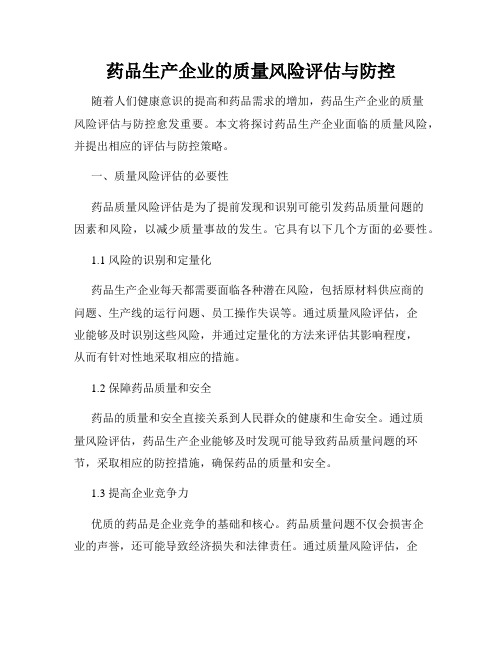
药品生产企业的质量风险评估与防控随着人们健康意识的提高和药品需求的增加,药品生产企业的质量风险评估与防控愈发重要。
本文将探讨药品生产企业面临的质量风险,并提出相应的评估与防控策略。
一、质量风险评估的必要性药品质量风险评估是为了提前发现和识别可能引发药品质量问题的因素和风险,以减少质量事故的发生。
它具有以下几个方面的必要性。
1.1 风险的识别和定量化药品生产企业每天都需要面临各种潜在风险,包括原材料供应商的问题、生产线的运行问题、员工操作失误等。
通过质量风险评估,企业能够及时识别这些风险,并通过定量化的方法来评估其影响程度,从而有针对性地采取相应的措施。
1.2 保障药品质量和安全药品的质量和安全直接关系到人民群众的健康和生命安全。
通过质量风险评估,药品生产企业能够及时发现可能导致药品质量问题的环节,采取相应的防控措施,确保药品的质量和安全。
1.3 提高企业竞争力优质的药品是企业竞争的基础和核心。
药品质量问题不仅会损害企业的声誉,还可能导致经济损失和法律责任。
通过质量风险评估,企业能够及时发现和解决潜在的质量问题,提高产品质量和合规性,提升企业的竞争力。
二、质量风险评估与防控的方法2.1 引入风险管理体系药品生产企业应引入风险管理体系,建立科学的质量管理体系并与其错综复杂的业务流程相结合。
通过风险管理体系,企业能够全面了解各个环节的风险,采取相应的管理和防控措施。
2.2 采用风险评估工具药品生产企业可以使用各种风险评估工具,如故障模式与影响分析(FMEA)、故障树分析(FTA)等,对各种潜在的质量风险进行评估和分析。
评估工具的选择应根据具体情况和需求进行,并与企业的风险管理体系相衔接。
2.3 培养高素质员工员工是企业质量管理的重要一环,应通过培训和考核等方式提高员工的素质和技能。
同时,企业应建立激励机制,激励员工积极参与质量风险的评估与防控工作。
2.4 建立完善的供应商管理体系药品生产企业需要与优质的供应商建立长期稳定的合作关系,并建立供应商质量管理体系。
药品监管中的药品生产质量风险评估案例分析方法探究与应用实例

药品监管中的药品生产质量风险评估案例分析方法探究与应用实例药品的生产质量一直是药品监管中一个重要的关注点,对于药品生产企业和监管机构来说,评估药品生产质量风险是确保药品质量安全的一项重要措施。
本文将探究和应用一种药品生产质量风险评估的案例分析方法,并提供实际应用实例。
一、药品生产质量风险评估方法药品生产质量风险评估方法有多种,其中一种常用的方法是风险矩阵分析法。
该方法通过对药品生产过程中各个环节的风险进行评估,将风险按照可能性和严重性进行分类,并根据分类结果进行相应的控制措施。
在进行风险评估时,需要考虑的因素包括药品生产的环境条件、生产设备的可靠性、操作人员的培训水平、药品配方和生产工艺的合理性等。
通过对这些因素进行评估,可以确定出可能存在的风险点,并制定相应的风险控制措施。
二、药品生产质量风险评估应用实例以某药品生产企业为例,该企业生产的一种药品被发现有一定的质量问题,需要对生产质量进行评估,并提出相应的风险控制措施。
1. 环境条件评估首先,对该企业的生产车间环境进行评估。
通过实地考察和数据收集,发现车间的温湿度控制不稳定,容易影响药品生产的质量。
因此,可以将这一环节的风险等级确定为中等。
2. 生产设备评估其次,评估生产设备的可靠性。
该企业的部分生产设备存在故障率较高的情况,可能对药品生产的质量造成一定影响。
因此,将生产设备的风险等级评定为较高。
3. 操作人员评估进一步,对操作人员的培训水平进行评估。
通过与操作人员的交流和培训记录的查阅,发现一些操作人员的培训水平不够,可能会存在操作不规范的情况。
因此,将操作人员的风险等级评定为中等。
4. 药品配方和生产工艺评估最后,对药品配方和生产工艺进行评估。
通过对配方和工艺文件的审查,发现部分车间的配方和工艺存在不合理之处,可能对药品的质量稳定性造成影响。
因此,将药品配方和生产工艺的风险等级评定为高。
根据以上的风险评估结果,该企业可以制定相应的风险控制措施,如优化生产环境控制手段、加强生产设备维护和检修、提高操作人员的培训水平、优化药品配方和生产工艺等。
- 1、下载文档前请自行甄别文档内容的完整性,平台不提供额外的编辑、内容补充、找答案等附加服务。
- 2、"仅部分预览"的文档,不可在线预览部分如存在完整性等问题,可反馈申请退款(可完整预览的文档不适用该条件!)。
- 3、如文档侵犯您的权益,请联系客服反馈,我们会尽快为您处理(人工客服工作时间:9:00-18:30)。
风险评估在药品生产的运用
上海新兴医药杨向有
目的:药品生产过程中质量风险产生的原因及控制措施, 以保障药品的质量。
方法:通过对国际风险管理的要求及国内药品生产企业应用风险管理现状的分析,概述了风险管理的几个应用工具,表述风险管理
在药品生产管理中的重要性。
结论:药品生产过程质量风险控制是制药企业面临的重大课题, 国内制药企业应对药品生产过程中可能产生的警惕, 并采取相应
的措施,减少药品质量风险事件的发生
关键字:管理药品生产风险管理风险评估变更偏差
药品风险管理的理念贯彻于药品生命周期的各个阶段,通过前瞻性或回顾性的风险评估,对所有的变更和偏差进行风险评估,及时采取有效预防措施和纠偏措施, 在最短的时间内将药品质量风险发生的概率和危害程度降到最低。
1 国际风险管理的要求
2005年,人用药品注册技术要求国际协调会(1CH)发布ICH Q9(Quality Risk Management(质量风险管理)》,正式确定了风险管理的概念.指导制药企业进行风险管理。
2006年5月,美国FDA发布关于ICH Q9的工业指南;2008年3月,欧盟正式将ICH Q9纳入GMP认证体系。
在新版GMP的修订稿中,国家食品药品监督管理局也加入了风险管理的内容,要求企业“对药品整个生命周期进行质量风险的评估、控制、沟通、审核”,“并最终与保护患者的目标相关联”。
风险管理已经势在必行。
并将其逐步应用在药品的整个生命周期内,
包括药品研发、生产、销售放行、运输等环节。
在ICH Q9中,风险是危害发生的可能性和严重性的组合。
主要包括:风险评估(Risk Assessment)、风险控制(RiskContr01)和风险回顾(Risk Review)。
风险评估是风险管理过程的第一步.一般包括风险识别、风险分析和风险评价三部分:风险控制包括风险降低和接受风险两个部分;风险回顾是指通过一段时间的运行,对整个系统的风险进行审核。
2 国内药品生产企业应用风险管理现状
2.1企业缺乏风险意识
目前国内药品生产企业对风险的管理多数停留在通过直觉和经验定性分析上。
部分企业建立了专门的风险管理程序,但这些程序多束之高阁,停留在理论阶段,未很好地指导实际工作。
大多数企业甚至未建立风险管理的程序,且没有意识到风险管理的重要性。
缺乏风险意识。
2.2企业未进行合理的风险管理
多数企业存在风险的判断依赖判断者个人经验的情况。
判断者个人经验的不同,对风险的评估就会不同。
比较主观。
同一事件,有能经验丰富的人会意识到风险,而有的人会认为没有太大风险。
风险评估也较片面,未全面进行考虑,极有可能会忽略掉某些方面较为严重的风险,甚至避重就轻,未真正发现风险点。
2.3企业未实施风险管理的培训
培训的作用主要在于将我们控制质量风险的种种管理行为归纳
汇总。
塑造成一个完整的质量体系。
风险管理的意识需要经过培训而成为员工的理念。
同样,风险管理工具也需通过培训使使用者掌握,而培训的缺乏。
使得员工不能理解风险管理的分析工具,更谈不上应用。
甚至缺乏风险意识,最终,不能够有效规避风险,从根本上降低风险。
在药品监管不断加强,法规不断完善的今天,企业应逐步学习并实施风险管理,提高管理水平及管理的深度和广度。
特别是药品生产的质量、生产负责人一定要增强风险意识,国内药品生产企业需要将风险管理的分析工具应用到实际生产管理之中,以保证能够及时准确地评定风险的程度,并采取有效措施降低风险的发生。
3 风险管理的分析工具
风险管理通过风险管理分析工具科学完整地再现管理过程的各个步骤,从而有效地分析、评估风险,从根本上降低或减少风险。
下面介绍几种常用的工具:
3.1失败模式及影响分析(FMEA)
FMEA是可靠性设计分析的一个重要工作项目。
是用来检查潜在失效并预防再次发生的系统性方法。
也是风险管理最常用的工具之一。
FMEA是一种对工艺的失败模式及其结果或产品性能町能产生的潜在影响的评估。
一旦失败模式被建立。
风险就町被消除、减少或控制,FMEA需要对工艺认知非常深刻。
FMEA可用来排列风险的优先次序,监控风险控制行为的效果,也可用于分析生产过程以确定高风险步骤或关键参数。
3.2过失树状分析(FTA)
FTA是对产品或工艺的功能性缺陷进行假设的分析方法,是用于确定引起某种假定错误和问题的所有根本性原因的分析方法。
这种方法可与因果图结合使用,依赖于人员对工艺的理解.以确定错误因素。
FTA可用于找到投诉、偏差、OOS/OOT(Out ofSpecifieation/Out ofTrend)的根源,确保针对性地解决问题,而不带来其他问题。
3.3风险分级和过滤
风险分级和过滤是一个用于比较风险并将风险分级的工具。
它将每一个基本的风险问题尽可能地分解开,以包含风险中蕴含的各种因素,通过对各因素进行权重或对风险分值作删减的形式进行,从而将风险分级以利于管理。
风险分级和筛选使管理者能够定性和定量的评价风险,并根据风险等级的高低。
采取对应的纠正预防措施。
风险分析的工具还有失败模式、影响和关键点分析(FMECA)。
危害源和关键控制点分析(HACCP),危害源可操作性分析(PHA)。
支持性统计学分析等。
通常一些用来组织数据和简化决策来构建风险管理的简易的技术也会得到应用,如流程图、因果图、过程映射、检查表等。
风险分析管理工具也能与统计学分析工具结合应用。
从而更好地实现风险管理。
4 风险管理在药品生产管理中的应用
偏差是风险管理的重要组成之一。
药品的生产过程中不可避免地会发生偏差。
企业需要调查偏差发生的根本原因,并评估偏差给药品生产、质量带来的风险。
从而确定相应的纠正措施和预防措施(CAPA),并做出产品的处置决定(如是否进行销售放行),最大程度保证不合格
的药品不进入市场并预防偏差的再次发生,这就需要对偏差进行风险评估。
风险具备三个要素:风险发生的可能性、风险的严重性、风险的检测性。
偏差的风险管理也不例外,企业可以对偏差的风险进行分类管理,以达到有效评估偏差带来的风险。
并根据偏差的等级确定纠正预防措施,并有效实施,以提高对偏差的管理与控制。
企业可以根据需要将偏差按照风险的三个要素定义为3个级别。
偏差等级的划分是根据偏差发生的可能性、严重性、可检测性综合考虑的结果。
可通过风险优先数来计算,风险优先数RPN=O×S×D,其中,0为风险发生的可能性,S为风险的严重性。
D 为风险的可检测性。
RPN(max)=27,RPN(中)=8;根据R值及出现的概率,可规定RPN≤3时为低风险,可改进;4≤RPN≤9时为中风险,可在一定时期内采取CAPA;9
在发生偏差时.可对偏差风险进行分级。
如为1级偏差(低风险),可在适当时候针对偏差发生的根本原因进行改进。
如为2级偏差(中风险),应制订纠正预防措施时问表,按时完成纠正预防措施。
如为3级偏差(高风险),应立即纠正。
根据偏差的等级确定纠正预防措施的实施程度,可以避免纠正预防措施过度增加成本或达不到预期的效果。
同时,由于药品关系到人民大众的生命安全。
发生偏差产品是否放行必须根据偏差对产品质量的影响程度(偏差严重性)确定,应从工
艺风险的角度进行评估。
另外,也可采用FMEA等方法建立失败模式,消除或控制潜在的失败,从而减少偏差的发生。
如计量容器标识,可以在事前就预测到标识不清可能会导致操作困难、计量错误。
从而预先采用较为清晰的标识方式,减少计量偏差。
5 总结
风险管理中风险分析工具的应用不是一成不变的,必须根据具体的问题、具体的过程选择合适的一种或多种工具进行应用。
风险管理是企业管理的新挑战。
企业应建立风险管理程序并进行培训,以指导风险分析和评估。
总之,质量风险管理是一种管理工具,并不是仅仅建立专门风险管理的SOP就可以解决.而是要应用到GMP管理之中。
风险管理理念及方法可以融入各种管理SOP中。
如关键工艺参数的确定、偏差、OOS /OOT、投诉、退货、年度回顾等等。
由于风险评估对人员的要求比较高,企业也可建立风险评估小组,以保证风险评估的有效进行。
随着GMP的发展,国内药品生产企业应主动关注并适应国际国内药政法规的变化,加强管理,与国际接轨,生产出高质量的产品。
国内药品生产企业应充分运用风险管理这种事前预防、事后评估的分析管理方式,对生产过程各个环节的风险了然于胸,更好地实现工艺的控制,规避风险。
并充分评估产晶质量风险,真正地对产品质量负责,对人民的健康负责。