IQCIPQCOQC检验方法
IQC、IPQC、FQC、OQC、QAQE质量检验有关的概念
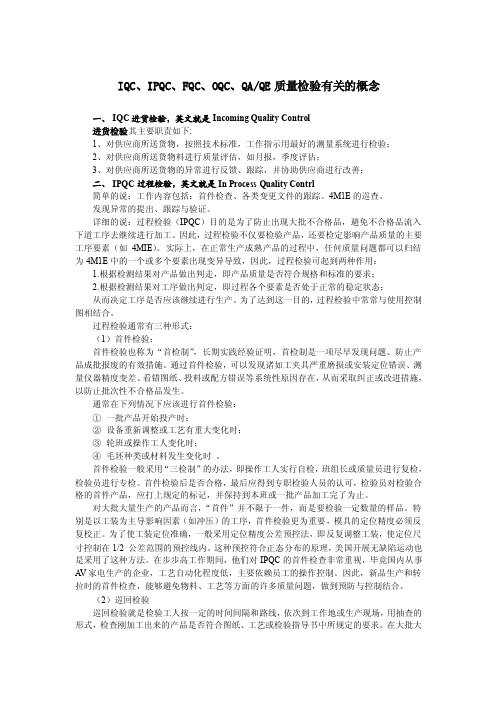
IQC、IPQC、FQC、OQC、QA/QE质量检验有关的概念一、IQC进货检验,英文就是Incoming Quality Control进货检验其主要职责如下:1、对供应商所送货物,按照技术标准,工作指示用最好的测量系统进行检验;2、对供应商所送货物料进行质量评估,如月报,季度评估;3、对供应商所送货物的异常进行反馈、跟踪,并协助供应商进行改善;二、IPQC过程检验,英文就是In Process Quality Contrl简单的说:工作内容包括:首件检查、各类变更文件的跟踪。
4M1E的巡查。
发现异常的提出、跟踪与验证。
详细的说:过程检验(IPQC)目的是为了防止出现大批不合格品,避免不合格品流入下道工序去继续进行加工。
因此,过程检验不仅要检验产品,还要检定影响产品质量的主要工序要素(如4MIE)。
实际上,在正常生产成熟产品的过程中,任何质量问题都可以归结为4M1E中的一个或多个要素出现变异导致,因此,过程检验可起到两种作用:1.根据检测结果对产品做出判走,即产品质量是否符合规格和标准的要求;2.根据检测结果对工序做出判定,即过程各个要素是否处于正常的稳定状态;从而决定工序是否应该继续进行生产。
为了达到这一目的,过程检验中常常与使用控制图相结合。
过程检验通常有三种形式:(1)首件检验:首件检验也称为“首检制”,长期实践经验证明,首检制是一项尽早发现问题、防止产品成批报废的有效措施。
通过首件检验,可以发现诸如工夹具严重磨损或安装定位错误、测量仪器精度变差、看错图纸、投料或配方错误等系统性原因存在,从而采取纠正或改进措施,以防止批次性不合格品发生。
通常在下列情况下应该进行首件检验:①一批产品开始投产时;②设备重新调整或工艺有重大变化时;③轮班或操作工人变化时;④毛坯种类或材料发生变化时。
首件检验一般采用“三检制”的办法,即操作工人实行自检,班组长或质量员进行复检,检验员进行专检。
首件检验后是否合格,最后应得到专职检验人员的认可,检验员对检验合格的首件产品,应打上规定的标记,并保持到本班或一批产品加工完了为止。
品质部岗位职责及检验流程

质量部岗位职责及检验内容目录管理:AZL—01-2017—18目的:IQC/IPQC/FQC/OQC检验方法原材料检验(IQC )原进厂检验包括三个方面:①库检:原材料品名规格、型号、数量等是否符合实际,一般由仓管人员完成.②质检:检验原材料物理,化学等特性是否符合相应原材料检验规定,一般采用抽检方式.③试检:取小批量试样进行生产,检查生产结果是否符合要求。
来料不合格的处理:①标识:在外包装上标明“不合格”,堆置于“不合格区”或挂上“不合格”标识牌等。
②处置:退货或调货或其他特采。
③纠正措施:对供应商提供相关要求或建议防止批量不合格的再次出现。
2紧急放行:因生产急需,在检验报告出来前需采用的物资,为紧急放行。
需留样检验,并对所放行物资进行特殊标识并记录,以便需要时进行追踪。
3特采:从非合格供应商中采购物资--加强检验。
②检验不合格而采用的物资-—挑选或修复后使用。
4应特别关注不合格品所造成的损失:①投入阶段发现,损失成本为1元。
②生产阶段发现,损失成本为10元。
③在客户手中发现,损失成本为100元。
二、过程检验(IPQC )lPQC 的检验范围包括:①产品:半成品、成品的质量。
②人员:操作员工艺执行质量,设备操作技能差。
③设备:设备运行状态,负荷程度。
④工艺、技术:工艺是否合理,技术是否符合产品特性要求.⑤环境:环境是否适宜产品生产需要。
2工序产品检验:对产品的检验,检验方式有较大差异和灵活性,可依据生产实际情况和产品特性,检验方式更灵活。
质检员全检:适用于关键工序转序时,多品种小批量,有致命缺陷项目的工序产品。
工作量较大,合格的即准许转序或入库,不合格则责成操作员工立即返工或返维。
质检员抽检:适用于工序产品在一般工序转序时,大批量,单件价值低,无致命缺陷的工序产品.员工自检:操作员对自己加工的产品先实行自检,检验合格后方可发出至下道工序。
可提高产品流转合格率和减轻质检员工作量,不易管理控制,时有突发异常现象。
IQC、SIP、IPQC、FQC.OQC定义及解释

IQC、SIP、IPQC、FQC/OQC方法大解析一、IQC 的内容及应用方法是什么IQC是Incoming Quality Control 的缩写,意思是来料检验,主要指:从供应商处采购的材料、半成品或成品零部件在加工和装配之前,应进行检查,以确定其完全符合生产的要求。
IQC对于所购进的物料,可分为全检、抽检、免检等几种形式,主要取决于以下因素。
①物料对成品质量的重要程度;②供料厂商的品质保证程度;③物料的数量、单价、体积、检验费用;④实施IQC检验的可用时间;⑤客户的特殊要求等;二、IQC的实施特点是什么IQC并不意味着必然对产品进行实物检查,有时仅仅是对供应方提供的附属检验材料的验证上。
IQC的宽严程度与供应商的质量保证程度有一定的关联。
对于一家刚刚供货的新供应商的产品,一般按正常抽样标准来检验,甚至对一些关键物料进行100% 全检;对于供货史很长,极少出现质量问题的供应商,则会放宽检验,直至免检。
绝大多数进厂材料是依据检验报告来接收的。
①如果进货符合检验标准,则进行标识后转入货仓或进入正常生产程序。
②如果IQC发现来料不符合检验标准,应对货物进行隔离。
并及时通知供应商处理。
③如果时间紧迫,来不及对进料判定就必须下线生产时,则必须加以明确标识并具有可追溯性;万一发现来料不合格时,应隔离用此批物料加工的产品,并采取措施加以补救。
三、IQC与供应商的选择与管理的关系IQC检验的程度与选择供应商的程度成反比,即:①供应商的评估较松,则IQC的检验就要严一些;②供应商的评估严格,则IQC的检验适当放松;对于供应商评估相当严格,或长期供货品质优良者,也可实行“免检”或称“STS(ship to stock)“只作货物名称、数量、型号等的验证即可。
四、如何理解来料检验规范(SIP)(1)SIP的对象及实施SIP即:standard inspection procedure 检验标准,也可译为检验规范。
IQC--IPQC--FQC--OQC检验控制流程图
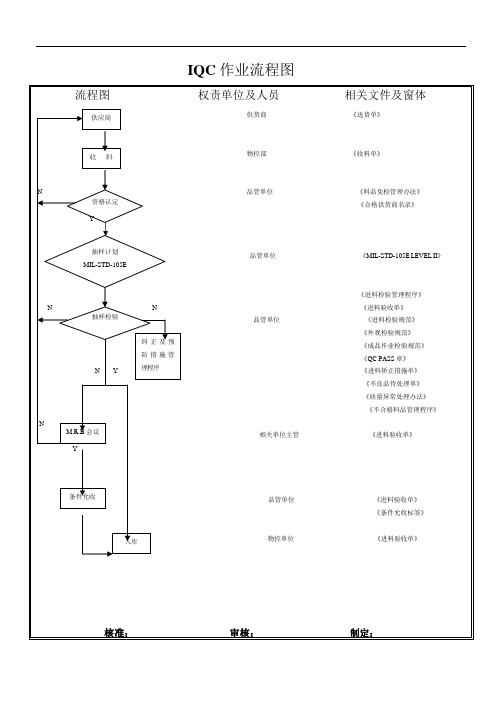
纠 正 及 预防 措 施 管
理程序
IQC 作业流程图
流程图
权责单位及人员
相关文件及窗体
供货商
《送货单》
物控部
《收料单》
N
品管单位
《料品免检管理办法》 资格认定
Y
《合格供货商名录》
抽样计划 MIL-STD-105E
品管单位 《MIL-STD-105E LEVEL II 》
《进料检验管理程序》
N
N
《进料验收单》 抽样检验
品管单位
《进料检验规范》 《外观检验规范》 《成品作业检验规范》 《QC PASS 章》 N
Y
《进料矫正措施单》 《不良品待处理单》 《质量异常处理办法》 《不合格料品管理程序》
N
相关单位主管
《进料验收单》
Y
品管单位
《进料验收单》 《条件允收标签》
物控单位 《进料验收单》
核准: 审核: 制定:
供应商
收
料
入库
M.R.B 会议 条件允收
核准:审核:制定:。
QC检验流程

QC检验流程
流程,检验
一,原材料检验(IQC)
1,原进厂检验包括3个方面。
①,库检:原材料品名.型号.规格.数量等是否符合实际与要求。
②,质检:检验原材料物理.化学等特性是否符合原材料检验规定。
③,实验:取小批量进行现场实验,并检查实验结果是否符合要求。
2,来料不合格处理,
①标示:在外包装上标明“不合格”,并及时给出检验报告,
②处置:退货或调货或其他特采,
③纠正错误:对供应商提供相关要求或建议防止批量不合格的再次出现,
3,紧急放行,因生产急需,在检验报告出来前需采用的物质,为紧急放行,需留样检验,并对紧急放行物资进行特殊标志并记录,以便需要时进行追踪。
4,特采,
①从非合格供应产品中采购物资——加强检验
②检验不合格而采用的物质——挑选或修复后使用,
二,过程检验(IPQC)
1,IPQC的检验范围包括,
①,半成品.成品的质量,
②,人员:操作工艺员执行质量,避免生产过程中的细节问题出现,
③,品质员检验:最关键的工作程序,有致命质量问题的项目,发现当即纠正操作人员进行修改,合格则
入库,不合格则责操作人员再次维返,直至合格,
三,成品出厂前检验(OQC)
①成品包装检验:包装是否牢固,是否符合运输要求,
②成品标示检验:如商标批号是否正确,
③成品外观按验:外观是否被损,破裂,划伤等…
④对成品功能.性能检查,批量合格则放行,不合格则应及时返工直至检查合格,
④。
IQC、IPQC、QA检验方法

IQC、IPQC、QA检验方法一、原材料检验(IQC)1.原材料检验(IQC)u库检:原材料品名规格、型号、料号、数量是否符合实际,一般由仓管人员完成。
v质检:检验原材料物理,化学等特性是否符合相应原材料检验规定,一般采用抽验方式。
w试检:取小批量试样进行生产、检查生产结果是否符合要求。
2.来料不合格的处理标识:在外包装箱上标明“ 不合格”,堆转置于“不合格区“或挂上“不合格”标识牌等。
处置:退货、调货或其它特采纠正措施:对供应商提出相关要求,并要求防止批量不合格的再次出现。
3.紧急上线:因生产急需,在检验报告出来前需采用的物资,为紧急放行,需留样检验,并对所放行物资进行特殊标识并记录,以便需要时进行追踪。
4.特采:u从非合格供应商中采购的物资——加强检验;v检验不合格而采用物资——挑选或加工后使用。
5.应特别关注不合格品所造成的损失:u投入阶段发现,损失成本为1元;v生产阶段发现,损失成本为10元;w在客户手中发现,损失成本为100元二、过程检验(IPQC)1.IPQC的检验范围包括:l 产品:半成品、成品的质量;l 人员:操作员工艺执行质量,设备技能差;l 设备:设备运行状态,负荷程度;l 工艺、技术:工艺是否合理,技术是否符合产品特性要求;l 环境:环境是否适宜产品生产需要。
2.工序产品检验:对产品的检验,检验方式有较大差异和灵活性,可依据生产实际情况和产品特性,检验方式更灵活。
3.质检员全检:适用于关键工序转序时,多品种小批量,有致命缺陷项目的工序产品。
工作量较大,合格的即准许转序或入库,不合格则责成操作员工立即返工或返修。
4.质检员抽检:适用于工序产品在一般工序转序时,大批量,单件价值低,无致命缺陷的工序品。
5.员工自检:操作员对自己加工的产品先实行自检,检验合格后方可发出至下道工序,可提高产品流转合格率和减轻质检员工作量,不易管理控制,时有突发异常现象。
6.员工互检:下道工序操作人员对上道工序产品先实行检验,可以不予接收上道工序的不良品,互相监督,有利于调动积极性,但也会引起包庇,争执等造成品质异常现象。
制程(IQCIPQCFQCOQC)品賍检验作业流程

責任單位改善﹐不良品處理 NG
改善后確認
五 成品檢驗流程
成品檢驗作業流程
成品送檢
依不合格品管制程序處理 依不合格品管制程序處理
檢格票或蓋合格章
成品入庫
倉庫接到交管"銷單"清點出貨料件數量 後備料在OQC待檢區知會OQC
檢驗準備
NG
OQC執行檢驗
OK 貼合格票或蓋合格章
3.成品檢驗作業,確保成品符合客戶要求,執行成品最終產 品檢驗及出貨檢驗。(FQC/OQC)
二 各段職責:
1.進料段職責: a IQC:進料窗口管理,IQC檢驗人員按工標制定的檢驗標准 IS/SIP/樣品進行檢驗﹐正確做出合格與不合格的判定并 做相關的記錄及標識。 b 倉管:負責進料數量清點﹐按品管進料檢驗之狀態標識 進行存放。 c 采購:負責緊急采購原物料對不合格進料品質的特采申 請提出﹐負責不合格進料品的退貨及換貨。 d SQE:負責對進料品質的異常處理及供應商改善后品質 效果確認與追蹤﹔負責對外購新機種SIP制做及樣品承認。
交貨
d 制造:負責按檢驗規范或樣品對在制品進行自檢、互 檢監控,確保產品品質,並對檢驗信息進行收集、偉遞、 反饋、上報,務必及時準確。 e 制工﹕依據《AMS SOP/POP制作作業指導書》制定制 造作業規范,內容包括使用材料、使用設備、作業條件、 作業步驟、作業自主檢查,作業規范應配合圖面或圖片 說明使作業人員更易了解。制定出貨包裝作業規范配合 搬運、儲存及交付之需要 ,以上文件需是在量產說明會 之前制作完畢;對制程異常之責任判定及對責任單位提 出制程異常原因之處理對策作評估確認。 f 設備單位﹕負責設備維修﹑驗收﹑保養、保管等。
2.制程段職責: a 工標﹕負責品質工程計劃、品質檢驗規范等品管文件 之制作,品質驗收標準之制定,以上文件需是在量
IQC,QA,FQC,OQC,IPQC的定义和职责

IQC,QA,FQC,OQC,IPQC的定义和职责IQC:INCOMING QUALITY CONTROL其主要职责如下: 1、对供应商所送货物,按照技术标准,工作指示用最好的测量系统进行检验;2、对供应商所送货物料进行质量评估,如月报,季度评估;3、对供应商所送货物的异常进行反馈、跟踪,并协助供应商进行改善;QA:QUALITY ASSURANCEQA是质量保证,英文就是quality assurance,在CMMI中QA的主要工作是质量评审和产品评审,在ISO8402:1994中的定义是“为了提供足够的信任表明实体能够满足品质要求,而在品质管理体系中实施并根据需要进行证实的全部有计划和有系统的活动”。
有些推行ISO9000的组织会设置这样的部门或岗位,负责ISO9000标准所要求的有关品质保证的职能,担任这类工作的人员就叫做QA人员;QE是品质工程的意思,英文就是quality engineer,主要从事品质工程的文件制定,QE是建立、分析、完善品质控制程序的人,不会去查每一单货品;QC是品质管理的意思,英文就是quality controller,主要按照QE指定的品质文件进行品质控制,是质量管理的一部分,致力于满足质量要求,qc是对人事、对物,直接致力于满足质量要求。
具备必要资质的qa是组织中的高级人才,需要全面掌握组织的过程定义,熟悉所参与项目所用的工程技术;qc则既包括软件测试设计员等高级人才,也包括一般的测试员等中、初级人才。
OQC:OQC=Outgoing Quality Control “出货检验”,这种情况下一般只有存在库存的时候才会有的,没有库存的情况下不需要OQC的,FQC就可以了,因为FQC就是最终检验了。
如果你们的产品库存周期比较长的话,那么这个抽样标准一般不是根据GB2828,而是根据GB2829来的,属于监督性的质量检查。
1 }, D2 ^7 r' s5 O8 \ ~7 k% g, y. oFQC:有两种情况:第一种是最终检验Final Qulaity Cotrol,也就是成品的入库前的“最终检验”(没有库存的情况下属于出货前的检验了)。
IQC和OQC抽样检验规范

来料、成品抽样检验规范1.目的:规范来料检验、成品检验之抽样水准、抽样方案以统一检验标准,确保来料及成品的质量稳定、良好。
2.范围:适用本公司IQC进料检验、OQC成品出货检验的所有产品。
3.职责:a)IQC、OQC负责执行本规定b)品管部负责监督执行并视产品实际情况制定、修改本规定4.程序:A.来料检验1)抽样标准:按MIL-STD-105E Ⅱ级检查水平一次抽样进行2)合格质量水准AQL规定:MAJOR:0.65(性能);MINOR:2.5(外观)3)检查严格度:正常检验4)抽样方式:随机抽样(抽样时尽量选取包装破损、变形严重或目视有问题的包装箱内取样)5)抽样批量:每一订单作为一个检查批次以上规定了来料检验通用抽样检验标准,部分物料特别规定的除外,特殊情况生产、技术、品质协商决定。
B.成品出货检验1)抽样标准:按MIL-STD-105EⅡ级检查水平一次抽样方案进行2)合格质量水准AQL规定:信息采集盒MAJOR:0.65(性能);MINOR:2.5(外观)3)检验严格度:正常检验4)抽样方式:随机抽样5)抽样批量一般以生产一个订单量作为一个批次,每次抽检的数量≥抽样计划。
①新开发的机型或新开发的供应商提供物料时,由生产经理及品质主管决定加严抽检或全检;②当日产量≤50pcs时,抽检数量不得低于日产量的一半。
附件附件一附件二IQC检验流程供应商来料仓库通知检验IQC检验判定仓库点收OK 入仓NG填写来料不良报表(开来料异常单)主管确认特采拒收挑选仓库点收不良品退给供应商仓库点收入仓注:特采时,需两个或以上部门协商决定(生产、技术、品质)。
OK附件三来料检验表单供应商物料名称到货日期到货数量检验数量检验日期项目检验结果不良描述判定产品外观产品性能品质判定:口接受口退货检验员/检验日期:品质主管/日期:部门姓名处理意见相关部门意见最终判定:PCB检验项目及规范1 目的建立本标准的目的为了本公司产品外观有一定的检验依据,有效控制外购PCB板的品质2 范围本规范适用于公司所有PCB原材料的交收检验标准。
IQC、IPQC、FQC、OQC知识分享

IQC/IPQC/FQC/OQC知识分享QA (Quality Assurance)质量保证QC (Quality Control)品质控制员,质量控制,就是质检,通俗说就是检验,QC的层次要比QA低IQC(Incoming Quality Control)来料检验,就是原材料检验IPQC(In-Process Quality Control)品质管理项目制程检验FQC(Finish or Final Quality Control)成品质量检验OQC(Outgoing Quality Control)出货检验一、原材料检验(IQC)1、原料进厂检验包括三个方面①库检原材料品名规格、型号、数量等是否符合实际,一般由仓管人员完成。
②质检检验原材料物理,化学等特性是否符合相应原材料检验规定,一般采用抽检方式。
③试检取小批量试样进行生产,检查生产结果是否符合要求。
2、来料不合格的处理①标识在外包装上标明“ 不合格” ,堆置于“ 不合格区” 或挂上“ 不合格” 标识牌等。
②处置退货或调货或其他特采。
③纠正措施对供应商提供相关要求或建议防止批量不合格的再次出现。
3、紧急放行因生产急需,在检验报告出来前需采用的物资,为紧急放行。
需留样检验,并对所放行物资进行特殊标识并记录,以便需要时进行追踪。
4、特采①从非合格供应商中采购物资---加强检验。
②检验不合格而采用的物资---挑选或修复后使用。
5、应特别关注不合格品所造成的损失①投入阶段发现,损失成本为1元。
②生产阶段发现,损失成本为10元。
③在客户手中发现,损失成本为100元。
二、过程检验(IPQC)1、IPQC 的检验范围包括①产品半成品、成品的质量。
②人员操作员工艺执行质量,设备操作技能差。
③设备设备运行状态,负荷程度。
④工艺、技术工艺是否合理,技术是否符合产品特性要求。
⑤环境环境是否适宜产品生产需要。
2、工序产品检验对产品的检验,检验方式有较大差异和灵活性,可依据生产实际情况和产品特性,检验方式更灵活。
IQC,QA,FQC,OQC,IPQC的定义与职责

IQC,QA,FQC,OQC,IPQC的定义与职责IQC:INCOMING QUALITY CONTROL其主要职责如下: 1、对供应商所送货物,按照技术标准,工作指示用最好的测量系统进行检验;2、对供应商所送货物料进行质量评估,如月报,季度评估;3、对供应商所送货物的异常进行反馈、跟踪,并协助供应商进行改善;QA:QUALITY ASSURANCEQA是质量保证,英文就是quality assurance,在CMMI中QA的主要工作是质量评审和产品评审,在ISO8402:1994中的定义是“为了提供足够的信任表明实体能够满足品质要求,而在品质管理体系中实施并根据需要进行证实的全部有计划和有系统的活动”。
有些推行ISO9000的组织会设置这样的部门或岗位,负责ISO9000标准所要求的有关品质保证的职能,担任这类工作的人员就叫做QA人员;QE是品质工程的意思,英文就是quality engineer,主要从事品质工程的文件制定,QE是建立、分析、完善品质控制程序的人,不会去查每一单货品;QC是品质管理的意思,英文就是quality controller,主要按照QE指定的品质文件进行品质控制,是质量管理的一部分,致力于满足质量要求,qc是对人事、对物,直接致力于满足质量要求。
具备必要资质的qa是组织中的高级人才,需要全面掌握组织的过程定义,熟悉所参与项目所用的工程技术;qc则既包括软件测试设计员等高级人才,也包括一般的测试员等中、初级人才。
OQC:OQC=Outgoing Quality Control “出货检验”,这种情况下一般只有存在库存的时候才会有的,没有库存的情况下不需要OQC的,FQC就可以了,因为FQC就是最终检验了。
如果你们的产品库存周期比较长的话,那么这个抽样标准一般不是根据GB2828,而是根据GB2829来的,属于监督性的质量检查。
1 }, D2 ^7 r' s5 O8 \ ~7 k% g, y. oFQC:有两种情况:第一种是最终检验Final Qulaity Cotrol,也就是成品的入库前的“最终检验”(没有库存的情况下属于出货前的检验了)。
一次性使用医用口罩IQC、IPQC、FQC及OQC检验规范

一次性使用医用口罩IQC、IPQC、FQC及OQC检验规范IQC进料检验规范1.目的和范围1.1目的规范一次性使用医用口罩的原材料进货检验操作,确保原材料符合规定要求,保证产品质量。
1.2范围适用于本公司一次性使用医用口罩产品的原材料进货检验。
2.工作程序2.1原材料进厂后应放原材料仓库待检区,由仓库填写请检单,送交质量部,质量部收到请检单后派员到现场进行检验或取样。
2.2质量部收集产品质量证明书。
3检验项目、要求、方法及抽样方案3.1熔喷布3.1.1外观质量3.1.2理化性能3.1.3徼生物3.2鼻夹3.3口罩带3.4包装袋IPQC过程检验1.目的规范一次性使用医用口罩产品生产过程中的检验项目、检验方法与检具、抽样方案及判定准则的要求,确保产品在生产过程中的质量要求。
2.范围适用于本公司一次性使用医用口罩生产过程检验。
3.检验项目、要求、检验方法、检验规则见下表FQC及OQC成品检验1.目的规范一次性使用医用口罩产品岀厂前检验项目、检验内容与要求、检验方法、抽样方案判定准则及检验记录的要求,桷保出厂成品符合注册标准要求。
2.范围适用于本公司一次性使用医用口罩成品出厂前检验。
3.检验依据3.1一次性使用医用口罩技术要求4.检测项目、质量要求、检验方法检测包括出厂检验和型式检验。
出厂检验项目项目:4.1外观、4.2结构与尺寸、4.3鼻夹、4.4口罩带、4.7微生物指标。
其中4.7为委托第三方检测项目,每批原材料送检一次。
型式检验应为产品标准的全性能检验。
4.1外观4.1.1口罩外观应整洁、形状完好,表面不得有破损、污渍。
4.1.2口罩的超声波复合应均匀、平直、牢固、无明显皱折。
4.1.3口罩超声波复合处粘合应牢固。
检验方法:随机抽取3个样品进行试验。
目视检查,结果应符合要求。
4.2结构与尺寸口罩佩戴好后,应能罩住佩戴者的口、鼻至下颌。
应符合表1的规定尺寸,最大偏差应不超过士5%表1口罩规格型号和基本尺寸单位:mm检验方法:随机抽取3个样品进行试验。
IOC,IPQC,OQC

AQL:接收质量限AC:合格判定数RE:不合格判定数CR:严重缺陷MA:主要缺陷MI:次要缺陷IQC:Incoming Quality Control 进料检验.IPQC(InPut Process Quality Control)中文意思为制程控制OQC,是Outgoing Quality Control的简写。
即:成品出厂检验(OQC)FQC:制造过程最终检查验证(最终品质管制, Final Quality Control), 亦称为制程完成品检查验证(成品品质管制)QE:quality engineer质量工程师AQL、允收值AC、接受RE、拒绝CR、致命缺陷MA、严重缺陷MI、轻微缺陷NG、不好,不行。
IQC:Incoming Quality Control 进料检验 .也就是指来料的质量控制,简称来料控制。
其主要职责如下: 1、对供应商所送货物,按照技术标准,工作指示用最好的测量系统进行检验;2、对供应商所送货物料进行质量评估,如月报,季度评估;3、对供应商所送货物的异常进行反馈、跟踪,并协助供应商进行改善;IPQCIPQC(InPut Process Quality Control)中文意思为制程控制,是指产品从物料投入生产到产品最终包装过程的品质控制。
目录1简介2IPQC目的3IPQC方法4相关介绍5岗位职责1简介制程中质量控制(IPQC):英文全称是InPut Process Quality Control;也叫制造过程中的质量控制,或生产过程中的质量控制。
由于IPQC采用的检验方式是在生产过程中的各工序之间巡回检查,所以又称为巡检。
IPQC一般采用的方式为抽检,检查内容一般分为对各工序的产品质量进行抽检、对各工序的操作人员的作业方式和方法进行检查、对控制计划中的内容进行点检。
2IPQC目的产品实现的过程是一个复杂的人机交互的系统,由不同的工序构成, 在这个过程中,既有物流,又有信息流,要想使输出满足客户要求,就必须做到如下几个方面:1.保证输入质量2.机器设备稳定,有充分的能力,人员严格按标准作业3.与产品质量密切相关的各关键参数(CTQ)处于稳定受控状态4.信息准确,完整,及时,能发挥指导作用5.有效的工序监控机制,能及时发现过程的异常6.向前反馈机制使过程能及时对异常进行修正7.向后反馈机制能有效防止不良流失8.产品初末件审核,提供班次质量保证9.工序接口顺畅,防止资源浪费以上各方面的执行有赖于IPQC的持续努力,而正是有了以上的支持,过程才是真正意义上的,保证输出质量的过程,所以IPQC的工作,实现了流程向过程的过渡,使输出不再是输入的简单相加,而是数量和质量上增值.3IPQC方法主要有以下几方面的方法:.1.依审核清单执行过程审核---过程基本状况,不依产品而变2.工序作业检查---物料,工具,辅料,方法,人员确认3.首件确认检查---依产品而有别,工艺,设备,软件,参数检查4.记录---真实,清楚,及时5.各工序间反馈机制---及时反馈相关信息6.预警机制起作用7.不合格品控制---标识,隔离,区分放置,统计分析8.物料投入---将正确的物料,在正确的时间,投入到正确的产品,并及时准确记录以方便追溯9.产品标准---工艺标准,功能要求10.各工序输出抽样检查---确认工序稳定,有充分能力,产品合格[1]4相关介绍IPQC制程巡检工作内容介绍产前工作准备1.根据生产计划,确定生产机型的BOM及ECN及配色方案与在线物料是否一致,确定检验规范,若IQC进料有样品,则将样品提供IPQC及生产检验员,确认进料检验是否有上线挑选;若是上线挑选,根据样品由IQC指导在线操作员挑选的方法.2.上线物料是否符合产品BOM要求,小到螺丝大到纸箱,每换一箱(袋)物料是否及时确认,根据产品BOM及ECN核对上线物料种类是否齐全,型号及规格是否正确.3.是否悬挂SOP/WI,排拉是否按工序流程安排制程控制中工作内容1.认真按时填写巡检报表,检测、记录静电环佩带,检测、记录电批扭力1次/1H2.测量、记录烙铁温度1次/1H,烙铁是否有接地防漏电措施3.确定有合格的首件、样板4..用首件、样板校对仪器、治具是否正常;确定在仪校有效期内;确认设置的参数与产品要求一致5.员工操作是否与作业指导书一致,下拉前5个产品是否从前跟到后,再次抽检5个/2H/工位,进行确认6.新产品、新员工是否重点巡查,特采、代用、试产、让步放行的必须重点稽核、记录情况及结果反馈7.作业定格定位摆放,无堆积,轻拿轻放,员工是否自检、互检合格品才下拉8.不合格品是否有标识,不合格品是否准时记录9.任何来料及作业不良造成物料无法正常使用、影响订单完成的,要及时发<<异常单>>反馈10.测试工位(如:半成品测试与功能测试及外观检验工位)不良比例超过品质目标要填写<<品质异常反馈单>>并要追踪处理结果A.正常生产(量产)每小时出现单项不良率3%--5% 需开品质异常处理反馈单----工程分析每小时出现总不良率 5%-10% 需开品质异常处理反馈单----工程分析B.试产总不良率 10% 需开品质异常处理反馈单----工程分析C.停线通知单每小时单项不良率≥5%每小时总项不良率≥8%要求:工程分析1小时内在线提供解决方案,若无回复,停线11.物料、半成品、成品摆放是否有落实状态标识及签名12.检验报表记录是否完整,清晰,是否一目了然,是否每小时核算记录一次“总数”,“不良数”,“不良率”,是否每日产线QC测试报告有“测试总数”“不良总数”“总不良比率”?13.有客诉及退货情况是否了解及跟进。
一次性使用医用口罩IQC、IPQC、FQC及OQC检验规范

一次性使用医用口罩IQC、IPQC、FQC及OQC
检验规范
IQC进料检验规范
1.目的和范围
1.1目的
规范一次性使用医用口罩的原材料进货检验操作,确保原材料符合规定要求,保证产品质量。
1.2范围
适用于本公司一次性使用医用口罩产品的原材料进货检验。
2.工作程序
2.1原材料进厂后应放原材料仓库待检区,由仓库填写请检单,送交质量部,质量部收到请检单后派员到现场进行检验或取样。
2.2质量部收集产品质量证明书。
3检验项目、要求、方法及抽样方案
3.1熔喷布
3.1.1外观质量
3.1.2理化性能。
IQCIPQCOQC检验方法

IQCIPQCOQC检验方法IQC、IPQC和OQC是产品质量管理中常用的检验方法。
IQC代表着入厂质量控制,是产品在进入生产工序之前进行的检验;IPQC代表着生产中质量控制,是在产品生产过程中进行的检验;OQC代表着出厂质量控制,是在产品生产完成后进行的最终检验。
下面将分别介绍这三种检验方法。
IQC(入厂质量控制)是为了保证供应商提供的原材料和零部件的质量符合产品要求,以减少后续生产过程中的缺陷和问题。
IQC的主要任务是对原材料和零部件的外观、尺寸、材料成分、机械性能等指标进行检验和评估。
常用的IQC检验方法包括外观检查、尺寸测量、物理性能测试和化学成分分析等。
通过对原材料和零部件进行IQC检验,可以及时发现不合格品,并采取相应的措施,如退货、返修或更换供应商,以确保产品的质量和性能。
IPQC(生产中质量控制)是在产品生产过程中进行的质量控制活动。
IPQC的主要任务是监测和控制生产过程中的各个环节,确保产品按照要求进行加工和组装,并及时发现和纠正生产过程中的缺陷和问题。
常用的IPQC检验方法包括外观检查、尺寸测量、功能测试、寿命测试等。
通过对生产过程中的关键环节进行IPQC检验,可以避免生产过程中的不良品积累,提高产品的质量稳定性和生产效率。
OQC(出厂质量控制)是产品生产完成后进行的最终检验,目的是确保产品达到客户的要求和标准。
OQC的主要任务是对产品的外观、尺寸、性能等指标进行全面检测和评估,并进行可靠性测试和耐久性测试等。
常用的OQC检验方法包括外观检查、尺寸测量、功能测试、可靠性测试和耐久性测试等。
通过对产品进行OQC检验,可以减少不良品的流出,确保产品的质量稳定性和一致性,并提高用户的满意度和忠诚度。
综上所述,IQC、IPQC和OQC是产品质量管理中常用的检验方法。
IQC主要用于原材料和零部件的检验,IPQC用于生产过程中的质量控制,OQC用于产品生产完成后的最终检验。
不同的检验方法适用于不同的环节,在整个质量控制过程中起到保障产品质量的重要作用。
品质部IQC、IPQC、OQC工作职责
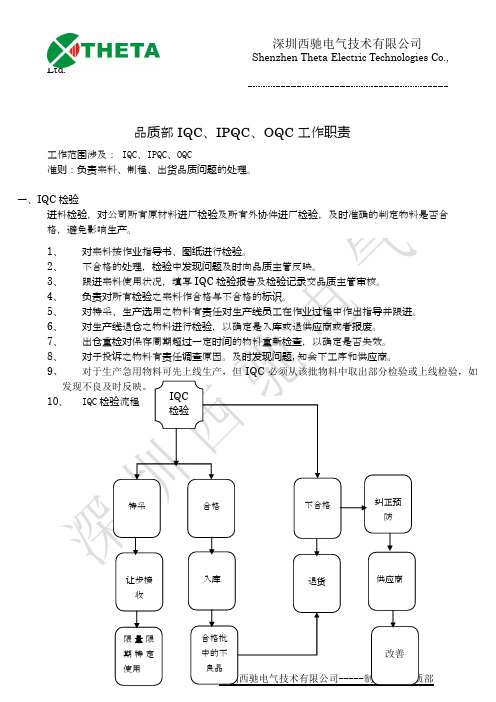
品质部IQC、IPQC、OQC工作职责工作范围涉及: IQC、IPQC、OQC准则:负责来料、制程、出货品质问题的处理。
一、IQC检验进料检验,对公司所有原材料进厂检验及所有外协件进厂检验,及时准确的判定物料是否合格,避免影响生产。
1、对来料按作业指导书、图纸进行检验。
2、不合格的处理,检验中发现问题及时向品质主管反映。
3、跟进来料使用状况,填写IQC检验报告及检验记录交品质主管审核。
4、负责对所有检验之来料作合格与不合格的标识。
5、对特采、生产选用之物料有责任对生产线员工在作业过程中作出指导并跟进。
6、对生产线退仓之物料进行检验,以确定是入库或退供应商或者报废。
7、出仓重检对保存周期超过一定时间的物料重新检查,以确定是否失效。
8、对于投诉之物料有责任调查原因。
及时发现问题,知会下工序和供应商。
9、对于生产急用物料可先上线生产,但IQC必须从该批物料中取出部分检验或上线检验,如发现不良及时反映。
10、IQC检验流程IQC检验合格入库合格批不合格退货供应商特采让步接收限量限纠正预防11、IQC的检验方式全检:数量少,单价高,如模块等,所有的半成品板。
抽检:数量多,或经常性之物料。
试装:对新物料、新产品或改规格后产品一定要进行确认12、单板测检(1)、外发加工的半成品板进行检验。
(2)、在检验过程中必须佩带静电手环。
(3)、上电检查前首先要目测。
(4)、按要求进行测试,每一步要检查到位。
(5)、测试无误的板进行老化。
(6)、老化后板入库需要用气泡袋包好。
13、特采情况:(1)项物料生产急需使用时。
(2)该项缺陷对后续加工、生产影响甚微时。
(3)出货时间紧迫。
(4)产品缺陷轻微,不致影响使用特性和销售。
(5)特殊状况时,特采批准。
(6)客户验货之订单,应由客户核准。
二、 IPQC 检查1、 对生产制程按各工序之作业指导书进行巡查并作好记录,对有违作业指导书规定要求要及时对该岗位员工提出纠正,并向生产主管反映。
IQCIPQCOQC检验方法

IQC/IPQC/OQC检验方法一、原材料检验(IQC)原进厂检验包括三个方面:①库检:原材料品名规格、型号、数量等是否符合实际,一般由仓管人员完成。
②质检:检验原材料物理,化学等特性是否符合相应原材料检验规定,一般采用抽检方式。
③试检:取小批量试样进行生产,检查生产结果是否符合要求。
来料不合格的处理:①标识:在外包装上标明“不合格”,堆置于“不合格区”或挂上“不合格”标识牌等。
②处置:退货或调货或其他特采。
③纠正措施:对供应商提供相关要求或建议防止批量不合格的再次出现。
2紧急放行:因生产急需,在检验报告出来前需采用的物资,为紧急放行。
需留样检验,并对所放行物资进行特殊标识并记录,以便需要时进行追踪。
3特采:①从非合格供应商中采购物资——加强检验。
②检验不合格而采用的物资——挑选或修复后使用。
4应特别关注不合格品所造成的损失:①投入阶段发现,损失成本为1元。
②生产阶段发现,损失成本为10元。
③在客户手中发现,损失成本为100元。
二、过程检验(IPQC)lIPQC的检验范围包括:①产品:半成品、成品的质量。
②人员:操作员工艺执行质量,设备操作技能差。
③设备:设备运行状态,负荷程度。
④工艺、技术:工艺是否合理,技术是否符合产品特性要求。
⑤环境:环境是否适宜产品生产需要。
2工序产品检验:对产品的检验,检验方式有较大差异和灵活性,可依据生产实际情况和产品特性,检验方式更灵活。
质检员全检:适用于关键工序转序时,多品种小批量,有致命缺陷项目的工序产品。
工作量较大,合格的即准许转序或入库,不合格则责成操作员工立即返工或返维。
质检员抽检:适用于工序产品在一般工序转序时,大批量,单件价值低,无致命缺陷的工序产品。
员工自检:操作员对自己加工的产品先实行自检,检验合格后方可发出至下道工序。
可提高产品流转合格率和减轻质检员工作量,不易管理控制,时有突发异常现象。
员工互检:下道工序操作人员对上道员工的产品进行检验,可以不予接收上道工序的不良品,相互监督,有利于调动积极性,但也会引起包庇、吵执等造成品质异常现象。
QC检验流程

QC检验流程流程, 检验一、原材料检验(IQC)l原进厂检验包括三个方面:①库检:原材料品名规格、型号、数量等是否符合实际,由仓管人员完成。
②质检:检验原材料物理,化学等特性是否符合相应原材料检验规定,一般采用抽检方式③试检:取小批量试样进行生产,检查生产结果是否符合要求。
l来料不合格的处理:①标识:在外包装上标明“不合格”,堆置于“不合格区”或挂上“不合格”标识牌等。
②处置:退货或调货或其他特采。
)③纠正措施:对供应商提供相关要求或建议防止批量不合格的再次出现。
2紧急放行:因生产急需,在检验报告出来前需采用的物资,为紧急放行。
需留样检验,并对所放行物资进行特殊标识并记录,以便需要时进行追踪。
3特采:? ? ①从非合格供应商中采购物资——加强检验。
②检验不合格而采用的物资——挑选或修复后使用。
4应特别关注不合格品所造成的损失①投入阶段发现,损失成本为1元。
②生产阶段发现,损失成本为10元。
③在客户手中发现,损失成本为100元。
二、过程检验(IPQC)lIPQC的检验范围包括:①产品:半成品、成品的质量。
②人员:操作员工艺执行质量,设备操作技能差。
③设备:设备运行状态,负荷程度.④工艺、技术:工艺是否合理,技术是否符合产品特性要求。
⑤环境:环境是否适宜产品生产需要。
2工序产品检验:对产品的检验,检验方式有较大差异和灵活性,可依据生产实际情况和产品特性,检验方式更灵活。
质检员全检:适用于关键工序转序时,多品种小批量,有致命缺陷项目的工序产品。
工作量较大,合格的即准许转序或入库,不合格则责成操作员工立即返工或返维。
质检员抽检:适用于工序产品在一般工序转序时,大批量,单件价值低,无致命缺陷的工序产品。
员工自检:操作员对自己加工的产品先实行自检,检验合格后方可发出至下道工序。
可提高产品流转合格率和减轻质检员工作量,不易管理控制,时有突发异常现象。
员工互检:下道工序操作人员对上道员工的产品进行检验,可以不予接收上道工序的不良品,相互监督,有利于调动积极性,但也会引起包庇、吵执等造成品质异常现象。
IQC和OQC抽样检验规范

来料、成品抽样检验规范1.目的:规范来料检验、成品检验之抽样水准、抽样方案以统一检验标准,确保来料及成品的质量稳定、良好。
2.范围:适用本公司IQC进料检验、OQC成品出货检验的所有产品。
3.职责:a)IQC、OQC负责执行本规定b)品管部负责监督执行并视产品实际情况制定、修改本规定4.程序:A.来料检验1)抽样标准:按MIL-STD-105E Ⅱ级检查水平一次抽样进行2)合格质量水准AQL规定:MAJOR:0.65(性能);MINOR:2.5(外观)3)检查严格度:正常检验4)抽样方式:随机抽样(抽样时尽量选取包装破损、变形严重或目视有问题的包装箱内取样)5)抽样批量:每一订单作为一个检查批次以上规定了来料检验通用抽样检验标准,部分物料特别规定的除外,特殊情况生产、技术、品质协商决定。
B.成品出货检验1)抽样标准:按MIL-STD-105EⅡ级检查水平一次抽样方案进行2)合格质量水准AQL规定:信息采集盒MAJOR:0.65(性能);MINOR:2.5(外观)3)检验严格度:正常检验4)抽样方式:随机抽样5)抽样批量一般以生产一个订单量作为一个批次,每次抽检的数量≥抽样计划。
①新开发的机型或新开发的供应商提供物料时,由生产经理及品质主管决定加严抽检或全检;②当日产量≤50pcs时,抽检数量不得低于日产量的一半。
附件附件一附件二IQC检验流程供应商来料仓库通知检验IQC检验判定仓库点收OK 入仓NG填写来料不良报表(开来料异常单)主管确认特采拒收挑选仓库点收不良品退给供应商仓库点收入仓注:特采时,需两个或以上部门协商决定(生产、技术、品质)。
OK附件三来料检验表单供应商物料名称到货日期到货数量检验数量检验日期项目检验结果不良描述判定产品外观产品性能品质判定:口接受口退货检验员/检验日期:品质主管/日期:部门姓名处理意见相关部门意见最终判定:PCB检验项目及规范1 目的建立本标准的目的为了本公司产品外观有一定的检验依据,有效控制外购PCB板的品质2 范围本规范适用于公司所有PCB原材料的交收检验标准。
- 1、下载文档前请自行甄别文档内容的完整性,平台不提供额外的编辑、内容补充、找答案等附加服务。
- 2、"仅部分预览"的文档,不可在线预览部分如存在完整性等问题,可反馈申请退款(可完整预览的文档不适用该条件!)。
- 3、如文档侵犯您的权益,请联系客服反馈,我们会尽快为您处理(人工客服工作时间:9:00-18:30)。
IQC/IPQC/OQC检验方法一、原材料检验(IQC)原进厂检验包括三个方面:①库检:原材料品名规格、型号、数量等是否符合实际,一般由仓管人员完成。
②质检:检验原材料物理,化学等特性是否符合相应原材料检验规定,一般采用抽检方式。
③试检:取小批量试样进行生产,检查生产结果是否符合要求。
来料不合格的处理:①标识:在外包装上标明“不合格”,堆置于“不合格区”或挂上“不合格”标识牌等。
②处置:退货或调货或其他特采。
③纠正措施:对供应商提供相关要求或建议防止批量不合格的再次出现。
2紧急放行:因生产急需,在检验报告出来前需采用的物资,为紧急放行。
需留样检验,并对所放行物资进行特殊标识并记录,以便需要时进行追踪。
3特采:①从非合格供应商中采购物资——加强检验。
②检验不合格而采用的物资——挑选或修复后使用。
4应特别关注不合格品所造成的损失:①投入阶段发现,损失成本为1元。
②生产阶段发现,损失成本为10元。
③在客户手中发现,损失成本为100元。
二、过程检验(IPQC)lIPQC的检验范围包括:①产品:半成品、成品的质量。
②人员:操作员工艺执行质量,设备操作技能差。
③设备:设备运行状态,负荷程度。
④工艺、技术:工艺是否合理,技术是否符合产品特性要求。
⑤环境:环境是否适宜产品生产需要。
2工序产品检验:对产品的检验,检验方式有较大差异和灵活性,可依据生产实际情况和产品特性,检验方式更灵活。
质检员全检:适用于关键工序转序时,多品种小批量,有致命缺陷项目的工序产品。
工作量较大,合格的即准许转序或入库,不合格则责成操作员工立即返工或返维。
质检员抽检:适用于工序产品在一般工序转序时,大批量,单件价值低,无致命缺陷的工序产品。
员工自检:操作员对自己加工的产品先实行自检,检验合格后方可发出至下道工序。
可提高产品流转合格率和减轻质检员工作量,不易管理控制,时有突发异常现象。
员工互检:下道工序操作人员对上道员工的产品进行检验,可以不予接收上道工序的不良品,相互监督,有利于调动积极性,但也会引起包庇、吵执等造成品质异常现象。
多种方式的结合:有机结合各种检验方案,取长补短,杜绝不良品流入下道工序或入库,但检验成本较高。
3工序品质检验:对人员、设备工艺技术环境等的检验。
三、成品出厂检验(OQC)成品出厂前必须进行出厂检验,才能达到产品出厂零缺陷客户满意零投诉的目标。
检验项目包括:①成品包装检验:包装是否牢固,是否符合运输要求等。
②成品标识检验:如商标批号是否正确。
③成品外观检验:外观是否被损、开裂、划伤等。
④成品功能性能检验。
批量合格则放行,不合格应及时返工或返修,直至检验合格。
QA和QC的区别QA=Quality Assurance, 质量保证QC=Quality Control,质量控制区别:1.QA偏重于质量管理体系的建立和维护,客户和认证机构质量体系审核工作,质量培训工作等;QC主要集中在质量检验和控制方面。
QA的工作涉及公司的全局,各个相关职能,覆盖面比较宽广,而QC主要集中在产品质量检查方面,只是质量工作的其中一个方面。
2.QA并不是立法机构立法机构应该是R&D,或工艺工程部门QA主要是保证生产过程受控或保证产品合格,着重于维护,而QC一般是实际质量控制,如检验,抽检,确认,很多公司只有质量部只包括QA的职责,把QC的工作放入生产部门QC品管新七大手法:品管新七大手法,也叫品管新七大工具,其作用主要是用较便捷的手法来解决一些管理上的问题,与原来的“旧”品管七大手法相比,它主要应用在中高层管理上,而旧七手法主要应用在具体的实际工作中。
因此,新七大手法应用于一些管理体系比较严谨和管理水准比较高的公司。
品管新七大手法是指:亲和图(也称KJ法)、关联图、系统图、过程决定计划图(PDPC 法)、矩阵图、矩阵数据解析法、箭线图七种。
亲和图:将资料或信息分类归纳,理顺关系关联图:把与现象和问题有关系的各种因素串联起来系统图:将要实现的目的展开寻找最恰当的方法。
过程决定计划图:如何做一个完整的计划矩阵图:找出众因素之间关系和相关程度的大小。
矩阵数据解析法:对多个变动且复杂的因素进行解析箭线图:对事件做好进程及计划管理某公司的IQC培训教材第二节IQC来料检查常见不良点综述:IQC在来料检查时,经常会遇到各种各样的不良,检查时要从来料整体和抽取样品两方面来进行检查,就整体来说,可分为如下几类:一、来料错:来料错不良主要有来料的规格要求不符,即来料的一些相关参数与要求不符,如电阻、电容等的误差值,三极管的放大倍数等;另外有要求来此料,而实际来成彼料,如本要求来电阻,而实际来成电容等;也有没有PO的料——即多余物料。
二、数量错:此不良主要是指来料时数量不符,包括多料(如超ITV数等)、少料(如总数比GRN数少、包装实数比标示数少等)、无料等。
三、标示错:此不良是指来料本身没有不良,而只是在内外包装,LABEL等的标示时出现错误,如标示时P/N写错,多字符或少字符等。
四、包装乱:此不良包括一次来料的多个物料混装、标示不对应、包装破损以及一个物料的包装松散、摆放不整齐等。
此不良易造成IQC检查物料时找料难、整理麻烦、降低工作效率等,另也容易造成物料变形、划伤、破损等其它不良。
IQC来料检查,除整体检查外,更重要,花时间更多,不良内容更复杂多变的是抽样样品的检查,抽样样品的不良主要分为两大类,即外观不良和功能不良。
现试总结叙述于下:一、外观不良:外观不良项目较多,从不同的方面有不同的不良内容,不同的原材料其外观不良也有各自的特点。
从检查的内容分,不良情形有:(1)包装不良:有外包装破损、未按要求包装(如要求真空包装而没有真空包装一步要求卷带而来成托盘装、单个包装的数量有要求而没按要求等)、料盘料带不良(如料盘变形、破裂;料带薄膜粘性过强机器难卷起、易撕裂、撕断、粘性弱松开致元件掉出等;)、摆放凌乱等。
(2)标示不良:有无标示、漏标示、标示错(多字符、少字符、错字符等)、标示不规范(未统一位置、统一标示方式)、不对应(标示有实物无或有实物无标示,即多箱物料乱装)等。
(3)尺寸不良:即相关尺寸或大或小超出要求公差,包括相关长、宽、高、孔径、曲度、厚度、角度、间隔等。
(4)装配不良:有装配紧、装配松、离缝、不匹配等。
(5)表面处理不良:A、本体不良:有破裂、残缺、刮花、划伤、针孔、洞穿、剥离、压伤,印痕、凹凸、变形、批锋、断折等。
B、清洁不良:有脏污、黑点、白点、异物、水纹、指印、花点、霉点等。
C、颜色不良:有错误、不均、差异等。
D、丝印不良:有错、漏、缺、淡、模糊、重影、偏位、反印、附着不牢等。
E、电镀不良:有薄、漏、不均、粗糙、颗粒、氧化、脱落等。
F、油漆不良:有多漆、堆漆、漆粒、附着不牢、印痕、杂质、不均、缺漏、补油、补漆等。
G、其它不良。
某公司的IQC作业标准书什么是5S管理活动5S管理源于日本,指的是在现场,对材料,设备人员等生产要素开展相应的整理、整顿、清扫、清洁、修养等活动。整理、整顿、清扫、清洁、素养的罗马文第一个字母都为S,所以日本人称之为5S。近年来,随着人们对这一活动的不断深入认识,有人又添加了“坚持、习惯”等两项内容,分别称为6S或7S活动。5S具体内容:1) 整理:工作现场,区别要与不要的东西,只保留有用的东西,撤除不需要的东西;2) 整顿:把要用的东西,按规定位置摆放整齐,并做好标识进行管理;3) 清扫:将不需要的东西清除掉,保持工作现场无垃圾,无污秽状态;4) 清洁:维持以上整理、整顿、清扫后的局面,使工作人员觉得整洁、卫生;5) 修养:通过进行上述4s的活动,让每个员工都自觉遵守各项规章制度,养成良好的工作习惯,做到“以厂为家、以厂为荣”的地步。
整理、整顿、清扫、清洁的对象是“场地”,“物品”。
修养的对象则是人,而“人”是企业最重要的资源,我们可以从“企业”的“企”字中分析人在企业中的重要,所谓“企”字是由“人”和“止”组成,“人”走了企业也就停“止”,所以在企业经营中,人的问题处置的好,人心稳定,企业就兴旺发达。
在5s活动中,做好整理、整顿、清扫工作,其目的不只是希望员工将东西摆好,设备擦干净,最主要的是通过细锁单调的动作中,潜移默化,改变员工的思想,使它们养成良好的习惯,进而能依照规定的事项(各种规章制度,标准化作业规程)来行动,变成一个有高尚情操的真正优秀员工。
总之,5s活动是种人性的素质的提高,道德修养的提升,最终目的在于“教育”育新“人”。
8D具体是指什么?8D最早是福特公司使用的很经典的分析手法1D: 成立团队公司明确团队队长由第一副总亲自担任;质保部负责召集和组织团队的活动;团队成员由包含与问题密切相关的技术人员或管理人员、相关的质量工程师组成。
2D:描述问题为了容易找到问题症结所在防止问题再发生,应使用合理的思考及统计工具来详细地描述问题:发生了什么问题?发生地点?发生时间?问题的大小和广度?从这几方面收集关键资料。
3D: 围堵行动为使外部或内部的客户都不受到该问题的影响,制定并执行临时性的围堵措施,直到已采取了永久性的改进。
要确保围堵行动可收到预期的效果。
4D: 找根本原因就问题的描述和收集到的资料进行比较分析,分析有何差异和改变,识别可能的原因,测验每一个原因,以找出最可能的原因,予以证实。
5D: 永久性纠正针对已确认的根本原因制订永久性的纠正措施,要确认该措施的执行不会造成其它任何不良影响。
6D: 验证措施执行永久性的纠正措施,并监视其长期效果7D:预防再发生修正必要的系统,包括方针、运作方式、程序,以避免此问题及类似问题的再次发生。
必要时,要提出针对体系本身改善的建议。
8D: 肯定贡献完成团队任务,衷心地肯定团队及个人的贡献,并加以祝贺。
由最高领导者签署。