线束检验规范
线束成品检验规范

4.3 接收标准
本公司对线束最终成品检验中各缺陷等级接收标准为:
a.CR缺陷, AQL=0。
b.MA缺陷,AQL=0.65
c.MI缺陷,AQL=1.0
4.4不合格品处理
对判定为不合格的产品作以下处理:
4.4.1报废:如不合格品有严重的缺陷,品质部开出产品监视跟进单交技术部等相关部门进行评
审后作报废处理。
4.4.2返工或返修:由品质部开出产品监视跟进单,交相关部门评审后进行返工或返修。
4.4.3让步接收:当产品个别指标低于检验标准,而又不影响产品的基本性能时,由品质部开出
产品监视跟进单,技术部根据检测结果认定可行,则应进行工艺验证,确认无误后方可同意特别采用,品质部复核后报请总经理批准后方可放行出货,但必须作好记录。
5.引用标准:相关线束加工工艺图纸。
6.相关记录
详见批次检验报告表单编号:CZCY/QC/FORM1
编制:审核:批准:。
线束成品出厂检验规范

检验方法
用直尺或游标卡尺测量
抽样方案
按 GB/T2828.1-2003,一 次正常抽样方案, 特殊检 查水平 S-3,A
目测
按 GB/T2828.1-2003,一 次正常抽样方案, 一般检 查水平Ⅱ,
严重不良(AC=0) 主要不良(AQL=0.4) 次要不良(AQL=1.0)
文件编号: QL/QR0001-2009 QL/QR0001-2009 01
版本:A/1
页次:
共2页 第2页
3
电气性能 导通性能好,无接触不良现象
精密低压测试仪
按 GB/T2828.1-2003,一 次正常抽样方案, 特殊检 查水平 S-3,AC =0 按 GB/T2828.1-2003,一 次正常抽样方案, 特殊检 查水平 S-3,AC =0
4
① 端子与导线拉力 物理性能 ② 端子与塑件拉力 ③ 阴接触件与阳接触件插拔力
拉力器
严重不良:涉及主体结构安全,造成永久性缺陷,严重影响使用功能的产品 主要不良:指产品质量未达到质量评定合格标准,但不涉及产品主体结构安全,经过修整返工处置可达到质量评定合格标准要求,不影响使用功能的产品。 次要不良:不影响使用性及功能﹐外观轻微不良。
编制/日期:
审核/日期:
批准/日期:
浙 江 乾 龍 线 缆 有 限 公 司
线束成品出厂检验规范
文件编号: QL/QR0001-2009 QL/QR0001-2009 0001 版本:A/1 页次: 共2页 第1页
序号 检验项目
尺 寸
标准要求
应符合相应图纸要求 ①线材 线材 印字正确、清晰,表面无损伤。 ②塑件 塑件 无缺料、飞边、变形、是否为图纸指定供 应商塑件。 ③端子 端子 有无到位、脱孔、露铜丝、端子尾部五金 露出塑件外、端子反冲等不良现象 ④线材冲孔颜色 线材冲孔颜色 有无错色、错位等不良现象。 ⑤浸锡 浸锡: 浸锡 ⒈表面浸锡均匀、光亮。 ⒉无大头、连锡现象。 ⒊浸锡到位且绝缘皮不能有烫焦现象。 ⒋锡头不能有分叉、少铜丝现象。
线缆及线束组件检验标准
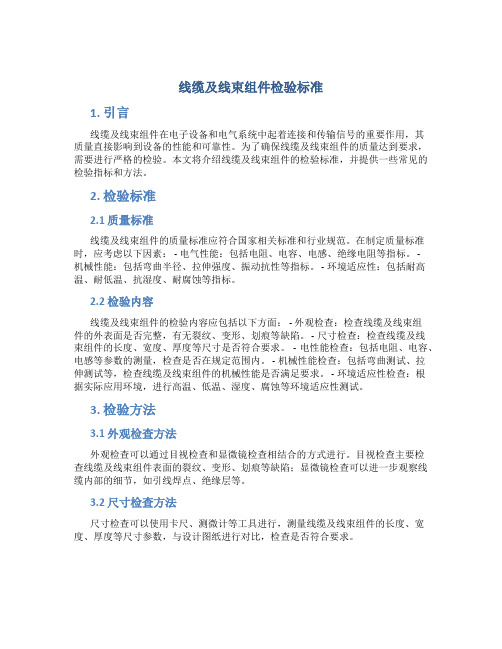
线缆及线束组件检验标准1. 引言线缆及线束组件在电子设备和电气系统中起着连接和传输信号的重要作用,其质量直接影响到设备的性能和可靠性。
为了确保线缆及线束组件的质量达到要求,需要进行严格的检验。
本文将介绍线缆及线束组件的检验标准,并提供一些常见的检验指标和方法。
2. 检验标准2.1 质量标准线缆及线束组件的质量标准应符合国家相关标准和行业规范。
在制定质量标准时,应考虑以下因素: - 电气性能:包括电阻、电容、电感、绝缘电阻等指标。
-机械性能:包括弯曲半径、拉伸强度、振动抗性等指标。
- 环境适应性:包括耐高温、耐低温、抗湿度、耐腐蚀等指标。
2.2 检验内容线缆及线束组件的检验内容应包括以下方面: - 外观检查:检查线缆及线束组件的外表面是否完整,有无裂纹、变形、划痕等缺陷。
- 尺寸检查:检查线缆及线束组件的长度、宽度、厚度等尺寸是否符合要求。
- 电性能检查:包括电阻、电容、电感等参数的测量,检查是否在规定范围内。
- 机械性能检查:包括弯曲测试、拉伸测试等,检查线缆及线束组件的机械性能是否满足要求。
- 环境适应性检查:根据实际应用环境,进行高温、低温、湿度、腐蚀等环境适应性测试。
3. 检验方法3.1 外观检查方法外观检查可以通过目视检查和显微镜检查相结合的方式进行。
目视检查主要检查线缆及线束组件表面的裂纹、变形、划痕等缺陷;显微镜检查可以进一步观察线缆内部的细节,如引线焊点、绝缘层等。
3.2 尺寸检查方法尺寸检查可以使用卡尺、测微计等工具进行,测量线缆及线束组件的长度、宽度、厚度等尺寸参数,与设计图纸进行对比,检查是否符合要求。
3.3 电性能检查方法电性能检查需要使用专用的测试仪器,如万用表、LCR表等。
根据线缆及线束组件的不同类型和要求,选择相应的测量方法和参数,进行电阻、电容、电感等参数的测量。
3.4 机械性能检查方法机械性能检查可以根据具体要求进行,如弯曲测试、拉伸测试等。
弯曲测试可以使用弯曲试验机进行,拉伸测试可以使用拉力试验机进行,根据测试结果判断线缆及线束组件的机械性能是否达到要求。
线束检验规范标准
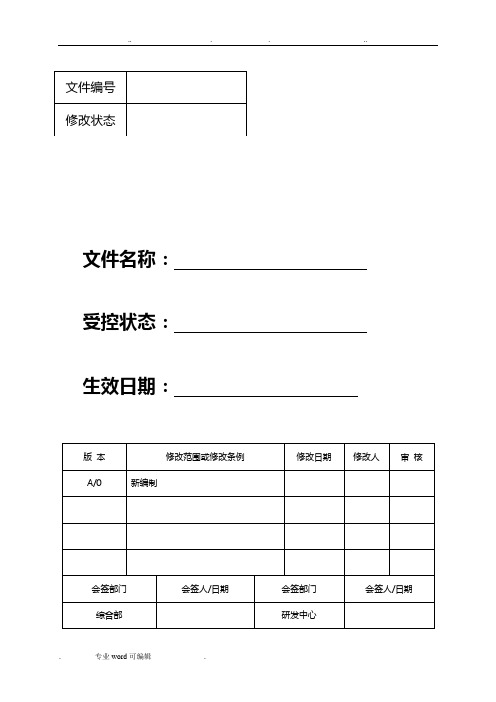
文件名称:受控状态:生效日期:1目的为了确保线束的质量及元器件与导线连接的可靠性,特制定此规范。
2范围本规范适用于本公司所有产品所用导线的检验。
3 定义目标条件:一种近乎完美的情况。
是一种理想状况,而非总能达到,且对于保证组件在其运行条件下可靠性并非必要条件。
可接受条件:组件不必完美但要在其使用环境下保持完整性和可靠性的条件。
制程警示条件:没有影响产品的外形、装配、功能或可靠性的情况。
缺陷条件:产品在其最终使用情况下不足以确保外形、装配或功能的情况。
4 线束检验要求4.1导线长度检验长度误差如下表线长(单位:mm)误差范围(单位:mm)0<L≤100 +3 - 0100<L≤500 +5 - 0500<L≤3000 +10 - 03000<L≤7500 +20 - 07500<L +2% - 0%4.2 导线检验4.2.1 外观检验:查看导线型号、规格、颜色等是否符合图纸和下线表的要求。
外观目标条件判定导线的导体切断面垂直于导线纵轴线所有股线长度一致;导线没有刮伤、刻痕、断开、压扁或其他损伤。
可接收条件判定导线的导体切断面大致垂直于导线纵轴线;所有股线长度大约一致;存在的毛刺不会在后续加工和装配期间脱落;股线散开,但未超过1倍股线直径或绝缘皮外径;股线未打结;绝缘皮允许留下轻微而规则的压痕,允许热处理引起的轻微变色但不允许烧焦、破裂或开裂。
制程警示条件判定股线有刮伤、刻痕或以切断,但单根导线损伤或断开的股线数未超过表一规定范围缺陷条件判定各股线的长度不一致影响到导线压接区全深度安装;作为表一的列外,股线的部分或不完全切口处于压接区域;作为表一的列外,股线的部分或不完全切口处于焊接连接区或没有接触全部需要缠绕的股线;损伤的股线数超过了表一的规定范围。
表一:股线允许损伤范围股线根数允许的最多刮伤、刻痕或切断的股线根数<7 07-15 116-25 326-40 440-60 561-120 6≥121 6%注一:对于工作在6千伏或更高电压下的导线不允许有股线损伤注二:对于有镀层的导线,不暴露金属基材的视觉异常不看做是损伤剥线后绝缘皮不合格现象说明:4.2.2 尺寸检验:下线长度按下线表要求、剥线长度要求见下表。
厨卫用线束检验规范
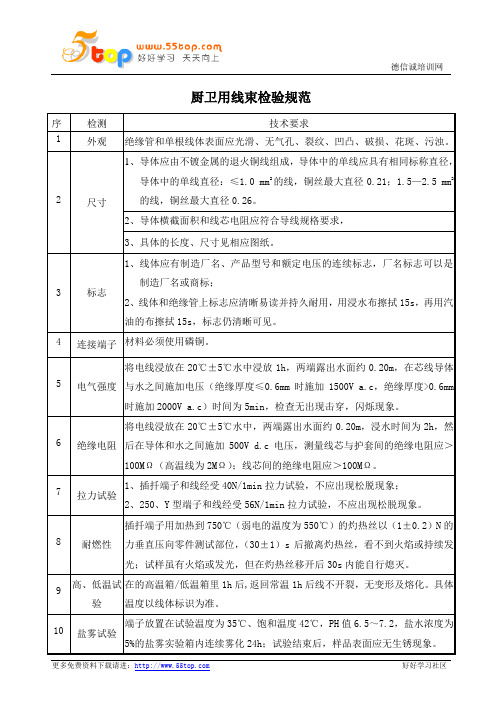
P △ P
5
通过
P
6
通过
P
7
P
8耐燃性通过P9无变形及熔化。 高、 低温试 在的高温箱/低温箱里 1h 后,返回常温 1h 后线不开裂, 验 具体温度以线体标识为准。
通过
P
端子放置在试验温度为 35℃、饱和温度 42℃,PH 值 6.5~7.2,盐水 10 盐雾试验 浓度为 5%的盐雾实验箱内连续雾化 24h;试验结束后,样品表面应无 生锈现象。
图 区
尺寸规格
实 1
测 2
数
据 3
结果 P P P P P P
更多免费资料下载请进:
好好学习社区
更多免费资料下载请进:
通过
P
好好学习社区
德信诚培训网 判定结果:合格 试验员: 日期: 审核: 日期:
更多免费资料下载请进:
好好学习社区
德信诚培训网
尺寸测量结果(附表)
序 号
1 2 3 4 5 6 7 8 9 10 11 12 13 14 15 16 17 18 19 20 21 22 23 24 25 P
好好学习社区
更多免费资料下载请进:
德信诚培训网
厨卫用线束检测报告表
样品名称 样品型号 生产单位 检测日期 判定说明 序 号 1 检测 项目 外观 以下判定 P 表示合格项、F 表示不合格项、△表示不作判定、 “/”表示不适用或未检测 技术要求 绝缘管和单根线体表面应光滑、无气孔、裂纹、凹凸、破损、花斑、 污浊。 3、 导体应由不镀金属的退火铜线组成,导体中的单线应具有相同标 2 称直径, 导体中的单线直径: ≤1.0 mm 的线, 铜丝最大直径 0.21; 2 1.5—2.5 mm 的线,铜丝最大直径 0.26。 2 尺寸 4、 导体横截面积和线芯电阻应符合导线规格要求, 3、具体的长度、尺寸见相应图纸。 2、 线体应有制造厂名、产品型号和额定电压的连续标志,厂名标志 可以是制造厂名或商标; 3 标志 2、线体和绝缘管上标志应清晰易读并持久耐用,用浸水布擦拭 15s, 再用汽油的布擦拭 15s,标志仍清晰可见。 4 连接端子 材料必须使用磷铜。 将电线浸放在 20℃±5℃水中浸放 1h,两端露出水面约 0.20m,在芯 线导体与水之间施加电压(绝缘厚度≤0.6mm 时施加 1500V a.c,绝 电气强度 缘厚度>0.6mm 时施加 2000V a.c)时间为 5min,检查无出现击穿, 闪烁现象。 将电线浸放在 20℃±5℃水中,两端露出水面约 0.20m,浸水时间为 2h,然后在导体和水之间施加 500V d.c 电压,测量线芯与护套间的 绝缘电阻 绝缘电阻应>100MΩ (高温线为 2MΩ ) ;线芯间的绝缘电阻应>100M Ω。 拉力试验 2、 插扦端子和线经受 40N/1min 拉力试验,不应出现松脱现象; 2、250、Y 型端子和线经受 56N/1min 拉力试验,不应出现松脱现象。 插扦端子用加热到 750℃ (弱电的温度为 550℃) 的灼热丝以 (1±0.2) N 的力垂直压向零件测试部位, (30±1)s 后撤离灼热丝,看不到火 焰或持续发光;试样虽有火焰或发光,但在灼热丝移开后 30s 内能自 行熄灭。 符合 P 符合 P 见尺寸测量结 果 测试结果 符合 判定 P 检测项目 合格项 不合格项 10 10 0 物料编码 样品数量 不做判定 5piece 1
线束技术要求及检测内容

技术要求一:测量线束的长度:1.主干线的长度,2.支线的长度,3.分支点的长度,4.保护套管与护套的距离(即裸露电源线的长度),以上线束的基本尺寸极限偏差应符合表一规定表一基本尺寸极限偏差mm二:压接处及牢固性检测:1.电线无损伤。
2.采用无特殊要求压接方法时,端子应分别压紧在导体和绝缘层上,导体不应压断,绝缘层不应压入导体压接部位,在图一所示的a区中可见电线导体,但不能妨碍插接。
3.绝缘层压接部位经不少于3个循环的弯折试验后,在图一所示的b 区中仍可见绝缘层。
30°图一4.端子与电线连接应牢固,在规定的拉力下不应损伤和脱开,其拉力值应不小于表二规定。
表二 拉力值三: 端子与电线压接处的电压降应不大于表三的规定。
表三 电压降值四:接点出要求:1.采用无焊料焊接方法时焊接处表面不允许出现氧化、断丝、缺损和绝缘层熔化现象。
2.采用无焊料焊接方法时撕裂力应不小于表四规定。
表四撕裂力值五:密封塞在压接时不应损伤。
电线与密封塞之间、密封塞与护套之间不应有目视可见的间隙。
电线和密封塞与端子压接后,在下图所示的 a区内应可见密封塞和电线绝缘层的端部。
六:电线束包扎时,应紧密、均匀,不应松散。
采用保护套管时,无位移和影响电线束弯曲现象。
七:电线束中电线与端子连接处的绝缘套管应紧密套在连接部位上,无位移、脱开现象。
八:电线束中电线及零部件应正确装配,不应有错位现象,端子在护套中不应脱出。
九:电线束中线路导通率为100%,无短路、错路现象。
十:标志1. 电线束应附有不易脱落的明显标志。
2. 产品标志的内容如下:a ) 产品名称b ) 型号或适用机组或空调成品检验内容1.线束经检验合格后,应附有证明产品质量合格的文件或标记,2. 线束经检验合格后方能使用。
附录A( 规范性附录)端子与电线导体压接处和压接接点处横断面的要求A1 端子与电线导体压接处和压接接点处横断面应符合下列要求A 1.1 如图A1所示,导体中所有单线的断面应呈不规则多边形,导体与端子相接部位、单线与单线之间应无明显缝隙,端子压接部位应包住全部导体。
线束检验标准
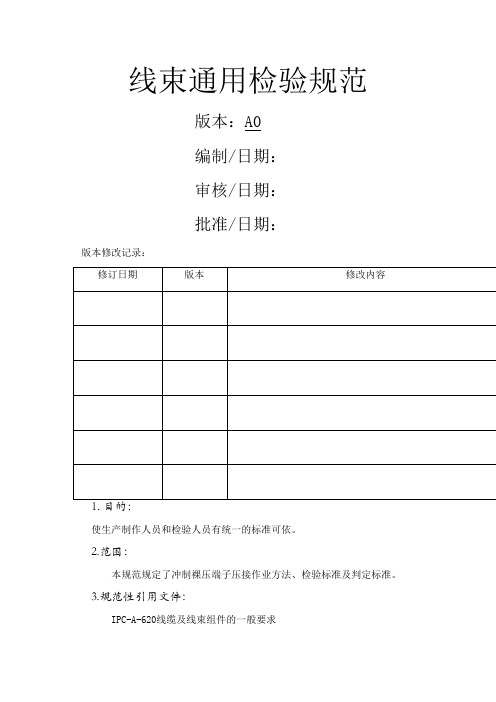
线束通用检验规范版本:A0编制/日期:审核/日期:批准/日期:版本修改记录:使生产制作人员和检验人员有统一的标准可依。
2.范围:本规范规定了冲制裸压端子压接作业方法、检验标准及判定标准。
3.规范性引用文件:IPC-A-620线缆及线束组件的一般要求UL486A电线与端子压接拉力测试标准4.术语与定义:4.1端子拉脱力:端子和导体压接后,将导体从端子中拉脱时的所需最小分离力。
4.2压接高度:端子和导体压接后,在导体压接区所形成的闭合压接截面的最大高度。
5.制作与检验要求5.1端子各部分区域的示意图:理想状态导体没有划伤,缺口,被切断或者其他损伤匀收状态导体划伤,缺口和被切断的程度不能超出表1范围拒收状态划伤,缺口或被切断的导体程度超出表1范围5.2.2绝缘损伤:状态图示描述理想状态绝缘层被切的整齐且沒有被收缩,变长,碎屑,变色,腐蚀或烧伤。
匀收状态绝缘层经过剥皮后有轻微的均衡的印痕。
绝缘层的厚度減少不超过20%。
绝缘层的不平整度要小于绝缘层外径的50%或者小于1mm。
绝缘层在剥皮过程中产生变色。
拒收状态绝缘层被切开或损伤绝缘层的厚度減少超过20%绝缘层的不平整度大于绝缘层外径的50%或者或1mm绝缘层烧焦绝缘层熔到导体里5.3线材处理—沾锡先沾锡以确保被锡焊的芯线形成一个统一的、可焊性的表面。
多股芯线沾锡有一个附加的好处:能将单股的芯线沾在一起,以使整个的芯线能够焊在端子上或附件的焊点上,而不是单股的芯线外露。
控制要求:芯线需要焊锡的部分,装配、焊接前要沾锡。
锡液应沾到整个沾锡部分,并渗透到内部的芯线。
沾锡过程中,锡液上浸至绝缘层部分,只要线材保持原有的柔韧性,少量的锡液上浸是允许的。
沾锡后锡面应光滑,轮廓应分明。
多根线束不得浸锡后连在一起。
高度H高度5.4冲压成型端子压接作业标准:5.4.1绝缘皮压接区:高度高度H线束脏污、锡线束烫5.4.2绝缘皮检查窗:5.4.3导体铆压区域:5.4.4刷尾检查区域:5.4.5料带残耳检查区域:5.4.6端子结合区/装配功能区:5.4.7端子外模绝缘外被压着检验方式:导体外被压着后需将导线做上下90度弯曲三次,检查绝缘被覆是否有损伤或滑出,若有表面损伤或滑出,则压着高度须重新调整。
线束检验标准
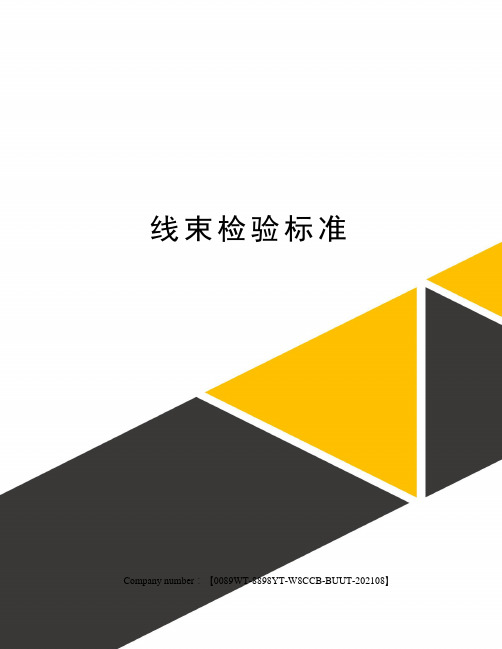
线束检验标准Company number:【0089WT-8898YT-W8CCB-BUUT-202108】线束通用检验规范版本: A0编制/日期:审核/日期:批准/日期:使生产制作人员和检验人员有统一的标准可依。
2. 范围:本规范规定了冲制裸压端子压接作业方法、检验标准及判定标准。
3.规范性引用文件:IPC-A-620 线缆及线束组件的一般要求UL486A 电线与端子压接拉力测试标准4. 术语与定义:端子拉脱力:端子和导体压接后,将导体从端子中拉脱时的所需最小分离力。
压接高度:端子和导体压接后,在导体压接区所形成的闭合压接截面的最大高度。
5. 制作与检验要求端子各部分区域的示意图:裁线检验标准导体损伤:状态图示描述理想状态导体没有划伤,缺口,被切断或者其他损伤匀收状态导体划伤,缺口和被切断的程度不能超出表1范围2 喇叭口3 刷尾检查窗4 锁紧翼/锁紧舌/锁紧弹片5 绝缘皮压接区6 导体压接区7 端子结合区/装配功能区8 料带残耳/料带头9 接线柱挡耳/止位挡片拒收状态划伤,缺口或被切断的导体程度超出表1范围导体数量(根)对于导线有划伤,缺口和切断的最大范围对于铆压端子可以接受导线有划伤,缺口和切断的最大范围对于焊接端子可以接受导线有刻痕、切断的最大范围小于7 0 0 07-15 1 0 1 16-25 3 0 2 26-40 4 3 3 41-60 5 4 4 61-120 6 5 5 大于121 6% 5% 5% 绝缘损伤:状态图示描述理想状态绝缘层被切的整齐且没有被收缩,变长,碎屑,变色,腐蚀或烧伤。
匀收状态绝缘层经过剥皮后有轻微的均衡的印痕。
绝缘层的厚度减少不超过20%。
绝缘层的不平整度要小于绝缘层外径的50%或者小于1mm。
绝缘层在剥皮过程中产生变色。
拒收状态绝缘层被切开或损伤绝缘层的厚度减少超过20%绝缘层的不平整度大于绝缘层外径的50%或者或1mm 绝缘层烧焦绝缘层熔到导体里线材处理—沾锡先沾锡以确保被锡焊的芯线形成一个统一的、可焊性的表面。
线束检验规范

标识齐全:包括安全件标识、分供方检验专用标记、电线束的编号及其执行标准号、认证标志
干线和保护套管长度应不小于100 mm
AQL =1.0
卷尺
支线长度应不小于50 mm 接点之间距离、接点与分支点之间距离应不小于20 mm
每批次压接 前做1件试样 进行检验
拉力机
电线与端子连接处的绝缘套管长为20 mm±5 mm 端子与电线连接应牢固,在规定的拉力下不应损伤和脱开
⑶ 不合格品按照退到制造部再选别后 再检查.
图
8. 异常发生时措施要领
⑴ 不合格 按不合格产品处理流程进行处理.
10. 记录管理
⑴ 进料检验记录表 : 纸档管理, 电子档管理
重缺点 重缺点
轻缺点
重缺点
重缺点 重缺点
连接力 导通
每批次压接 前做1件试样 进行检验
全检
拉力机 万用表
线束接点表面绝缘应良好,导体不应压断 电线束中线路导通率为100%,无短路、错路现象
包
装 检
包装 , Label,铭牌
AQL=1.0
目视(外 外包装箱应无受潮、挤压破损变形等缺陷(小包装中的真空层压包装不得有破损);品名、型号、规格、数 观) 量等标识清晰无误;有无产品出厂检验报告
纱线保护层表面的疏松程度应均匀一致
塑料套管、波纹管均应用胶粘带固
电线与端子在连接处的绝缘套管应紧套在连接部位上,无脱开、移位现象
电线束中电线及零部件应正确装配,不应有错位现象,端子在护套中应到位,不应脱出
插接件应符合Q/FT A095的规定或者本公司允许的指定规格的产品
线束检验规范
1.适用范围 该基准适用于公司生产的所有产品。
2.抽样方法 GB/T 2828.1-2012 一般水平II
线束加工外观的检验规范
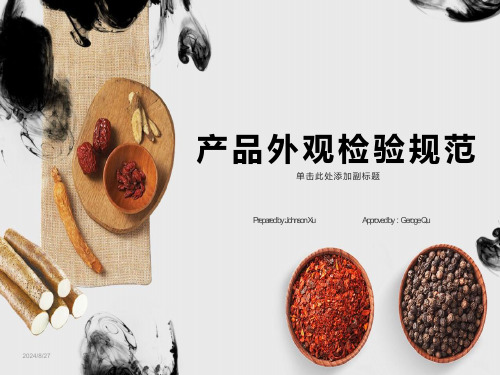
产品外观检验规范
单击此处添加副标题
Prepared by :Johnson Xu
Approved by:Geroge Qu
线材外观检验 图1,线材印字不清,无发辩认,NG 图3,线材外被严重变形,NG 图4,线材表面起鼓>0.5mm,发白,NG
图2,同一线材外被颜色明显不同, 色差 大于1,NG
page 8 /25 2024/8/27
二、端子外观检验GOOD
page 9 /25 2024/8/27
端子外观检验NG
三、IDC外观检验
图1, NG压接,压线片未扣到位,有间隙 图2, NG压接,折叠部分与连接器之间的间 隙大于2.0 倍芯线绝缘外径 图3, NG压接,排线伸出压线片的长度不在 0~1倍线径范围内 图4, 合格压接,导体位于刀口中间位置 图5, NG压接,导体超过刀口最下边位置
五、焊接外观检验
图1, NG,假焊, 焊锡表面未完全 浸锡,表面有锡 孔,锡点易脱落, 且不饱满。
图2, NG, 冷焊,焊 丝未完全 熔化,焊 点大,成 堆不光滑
图3, NG,多股铜线未完全焊入焊点
图4,5, NG,搭 焊长度过短,多 锡,焊点脏
五、焊接外观检验
图6, NG,导体 搭接在焊垫/杯 上太短
page 5 /25 2024/8/27
二、端子外观检验
图1, 标准压接,外皮处于导体包筒和绝缘包筒之间 图2, 合格压接,外皮刚好与导体包筒或绝缘包筒平 齐 图3, NG压接,外皮压入导体包筒或绝缘包筒内 图4, NG压接,导体伸入到功能区内 图5, NG压接,绝缘包筒刺破线皮
page 6 /25 2024/8/27
page 12 /25 2024/8/27
线束检验标准

线束通用检验规范版本:A0编制/日期:审核/日期:批准/日期:1. 目的:使生产制作人员和检验人员有统一的标准可依。
2. 范围:本规范规定了冲制裸压端子压接作业方法、检验标准及判定标准。
3.规范性引用文件:IPC-A-620 线缆及线束组件的一般要求UL486A 电线与端子压接拉力测试标准4. 术语与定义:4.1 端子拉脱力:端子和导体压接后,将导体从端子中拉脱时的所需最小分离力。
4.2 压接高度:端子和导体压接后,在导体压接区所形成的闭合压接截面的最大高度。
5. 制作与检验要求5.2 裁线检验标准5.3 线材处理—沾锡先沾锡以确保被锡焊的芯线形成一个统一的、可焊性的表面。
多股芯线沾锡有一个附加的好处:能将单股的芯线沾在一起,以使整个的芯线能够焊在端子上或附件的焊点上,而不是单股的芯线外露。
控制要求:芯线需要焊锡的部分,装配、焊接前要沾锡。
锡液应沾到整个沾锡部分,并渗透到内部的芯线。
沾锡过程中,锡液上浸至绝缘层部分,只要线材保持原有的柔韧性,少量的锡液上浸是允许的。
沾锡后锡面应光滑,轮廓应分明。
多根线束不得浸锡后连在一起。
图示上锡端光滑、平整,无拉尖、开叉、上锡过多、破皮、线束锡渣等现象开叉、拉尖、上锡过多等最大高度≤线径的配套线路板以能轻松装进去为准。
注:直接焊线(不用穿孔焊接)可放宽。
浸锡后线束上不得有锡渣、线束烫伤、变软等现象。
5.4 冲压成型端子压接作业标准: 5.4.1 绝缘皮压接区: 高度H高度H高度H高度H线束脏污、锡渣线束烫伤绝缘完全包住并延伸到绝缘的铆压片如果是多股线则应该所有线都应该穿过的绝缘的铆压片绝缘皮处的铆压不能切断或破坏绝缘绝缘铆压片完全包住并支撑绝缘皮绝缘端子铆压不伤及绝缘的基础上使其和导线的连接紧铆压片穿过绝缘皮而且接触到导体绝缘铆压片没有在绝缘周围提供最小铆压片环绕但会形成一个大于45两块铆压片环绕但没有压到绝缘皮5.4.2 绝缘皮检查窗:绝缘皮和导体线在检查窗的中间位置绝缘皮平齐但没有进入导线的铆压区域绝缘皮与铆压片检察窗口的边平齐但是没有进入到检查窗口的区域绝缘皮延伸入导体铆压区域绝缘皮和导体的交接线在绝缘铆压范围内5.4.3 导体铆压区域:没有绝缘在导体铆压区域导体延伸到平齐区域的中间没有导线断开导体铆压片所压住在铆压区域的铆压中心有正确的喇叭口铆压印痕统一并按照厂家要求连接在铆压后没有香蕉状的变形锁片没有变形或损坏导线没有扭曲导体在导体铆压区域终端平齐铆压印痕不统一但是不会影响到结构导体没有延伸到铆压区域外并在喇叭口的平齐边缘终端不可见端子或连接的变形响到结构性在铆压区域外有未压到的导线折返的线和多余的线5.4.4 刷尾检查区域:导线通过导体铆压区后有轻微的突起并形成”导体平齐的刷子形状”导线聚集在一起形成平齐一并不会张开有导线延伸到端子之外导线延伸至端子止耳片进入功能区收)绝缘端子的绝缘皮破坏金属底材外露5.4.5 料带残耳检查区域:连接器或端子没有损伤残余料带不会影响连接器残余料带片的长度大于其金属厚度的响和接头的完全连接除去残余料带时损伤到连接或端子连接插入到连接器后残余料片突起5.4.6 端子结合区/装配功能区:端子结合区不得存在弯曲、扭曲、残料、氧化等现象5.4.7 端子外模绝缘外被压着检验方式:导体外被压着后需将导线做上下90度弯曲三次,检查绝缘被覆是否有损伤或滑出,若有表面损伤或滑出,则压着高度须重新调整。
电线束成品检验规范
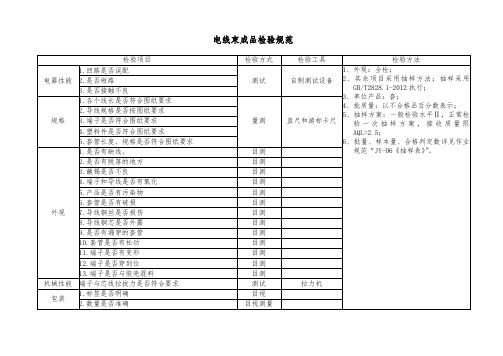
检验项目
检验方式
检验工具
检验方法
电器性能
1.回路是否误配
测试
自制测试设备
1、外观:全检;
2、其余项目采用抽样方法;抽样采用GB/T2828.1-2012执行;
3、单位产品:套;
4、批质量:以不合格品百分数表示;
5、抽样方案:一般检验水平Ⅱ,正常检验一次抽样方案,接收质量限AQL=2.5;
6、批量、样本量、合格判定数详见作业规范“JY-06《抽样表》”。
2.是否短路
3.是否接触不良
规格
1.各个线长是否符合图纸要求
量测
直尺和游标卡尺
2.导线规格是否按图纸要求
3.端子是否符合图纸要求
4.塑料件是否符合图纸要求
5.套管长度、规格是否符合图纸要求
外观
1.是否有缺线。
目测
2.是否有脱落的地方
目测
测试
拉力机
包装
1.标签是否明确
目视
2.数量是否准确
目视测量
3.蘸锡是否不良
目测
4.端子和导线是否有氧化
目测
5.产品是否有污染物
目测
6.套管是否有破损
目测
7.导线铜丝是否损伤
目测
8.导线铜芯是否外露
目测
9.是否有漏穿的套管
目测
10.套管是否有松动
目测
11.端子是否有变形
目测
12.端子是否穿到位
目测
13.端子是否与胶壳混料
目测
机械性能
端子与芯线拉拔力是否符合要求
线束工程检验规范标准

不良原因 端压脚过长不良,或端子与孔座不配 后果:短路,或外观不良
孔座不良
不良原因 来料不良 后果:性能与外观不良
250
不良原因 端压不良、端子不良或运输过程中损坏 后果:无法插入基板
长短线
不良原因 端压返工、裁线时线材有长短 后果:外观不良
电源。 6. 非压端组人员与工程人员不得调试、启动机器。
机器的故障与排除
序号 部件名称 故障现象
产生原因
排除方法
排除人员
1. 润滑情况不良。
1. 检查润滑清理油路。 操作工
1
曲轴 轴承发热 2. 轴和轴瓦咬住,曲轴与轴 2. 修刮轴瓦调整间隙。 机修工
瓦间隙太小。
1. 导 轨 润 滑 不 良 或 内 有 屑 1. 清查屑末加足润滑 操作工
2. 调整挡销位置。
作用。
4
离合器 离 合 器 产 1. 制动器太松。
1. 调整制动器紧松。 操作工
生 剧 烈 冲 2. 离合器零件磨损
2. 卸开飞轮,检查六角 机修工
击或有明
凸轮与滚柱的磨损
显噪声。
情况。
操 作 过 程 机体背部四只紧固螺栓松开。 拧紧紧固螺栓。
操作工
5
机体
中机体松 动。
6
电气
操 作 过 程 电机故障或电路不通。 式中电机 停止运转。
乐清市乐沪无线电厂
连接线束工程规范标准 行业标准
编 号: YH2008JB
编 制:
核 准:
一、冲压原理
内容及质量要求
(受训人员 :工程技术人员 .机修工 )
二、端子压着原理
(受训人员 :工程技术人员 .机修工 )
线束工程检验规范标准

芯线修剪过短、过长不符合图纸要求 或需修剪的芯线颜色错误
UL2547#28
UL2547#28
芯线剥头过短、过长不符合图纸要求
UL2547#28
UL2547#28
四、机器调试、故障排除与安全
(受训人员 :工程技术人员 .机修工 )
五、刀片设计原理
(受训人员 :工程技术人员 .机修工 )
六、裁线质量要求
(受训人员 :工程技术人员、机修工、品检、拉长、裁线工 )
七、端子压着成型质量要求
(受训人员 :工程技术人员、机修工、品检、拉长、端压工 )
八、装配质量要求
(受训人员 :品检 .拉长 .工程技术员、装配工 )
UL1007#28
UL1007#28 UL1007#28 UL1007#28 UL1007#28
切头不齐
UL1007#28
UL1007#28
铜丝杂乱
UL1007#28
铜丝切断
UL1007#28
UL1007#28 UL1007#28
线材夹伤或刮伤
UL1007#28
UL1007#28
未剥到皮
UL1007#28
端子插不到位
不良原因 插孔操作时端子未插到位 后果:无拉力引起端子松脱
误配交插
不良原因 插孔操作时线材位置装配错误 后果:装机后引起短路烧坏线路板等
孔座或线材等材料用错
不良原因 插孔操作时线材装配错误 后果:线材标记错误,致使安装错误
孔座装配方向错误
不良原因 插孔操作时孔座装配错误 后果:致使无法安装,或装机后引起短路烧坏线路板等 孔座插反
C
图4
FG
HJ
图5
3.下外刀(图6)与下内刀(图7)主要接触点的设计
线束成品检验规范
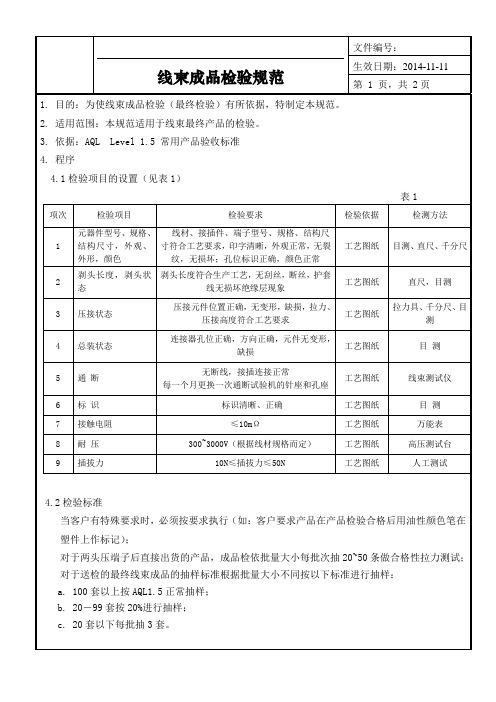
4.3 接收标准
本公司对线束最终成品检验中各缺陷等级接收标准为:
a.CR缺陷, AQL=0。
b.MA缺陷,AQL=0.65
c.MI缺陷,AQL=1.0
4.4不合格品处理
对判定为不合格的产品作以下处理:
4.4.1报废:如不合格品有严重的缺陷,品质部开出产品监视跟进单交技术部等相关部门进行评
审后作报废处理。
4.4.2返工或返修:由品质部开出产品监视跟进单,交相关部门评审后进行返工或返修。
4.4.3让步接收:当产品个别指标低于检验标准,而又不影响产品的基本性能时,由品质部开出
产品监视跟进单,技术部根据检测结果认定可行,则应进行工艺验证,确认无误后方可同意特别采用,品质部复核后报请总经理批准后方可放行出货,但必须作好记录。
5.引用标准:相关线束加工工艺图纸。
6.相关记录
详见批次检验报告表单编号:CZCY/QC/FORM1
编制:审核:批准:
Welcome To Download !!!
欢迎您的下载,资料仅供参考!。
线束通用检验规范

1、测试一条线两端,不可有开路(阻值无穷大)
2、测相邻的两条线,不可有短路(阻值为零)
3、测对应一条线两端,不可有接触不良之现象
4、接线方式错不可接受(线序)
5、接触不良或不能运行不可接受
万用表
LCR测试仪
插拔测试检验
公母端对接,是否能完全卡合
实际操作
端子拉力测试
压接的端子拉力符合客户要求
拉力计
绝缘强度
带电与非带电之间施加电压,是否击穿
LCR、万用表
绝缘电阻测试
采用DC500V的兆欧表对线束进行绝缘电阻测试,测试值小于100兆欧不可接受
ቤተ መጻሕፍቲ ባይዱ万用表
线束成品
电器性能
根据性能测试要求进行性能功能测试
线束通用检验规范
检验项目
检验内容
标准
检验工具
外观检验
包装
1、包装干净、整齐,无破损
目测
标识
2、标识清晰完整
线皮
3、线皮不可有破损现象,表面圆滑,无编织纹
4、线束不可裸漏铜丝,破皮等
5、线皮颜色符合客户、图纸要求
6、压接端子无脱落、断裂、破损、变形,氧化等不良
线材尺寸
尺寸符合客户、图纸要求
卡尺、盒尺
功能检验
- 1、下载文档前请自行甄别文档内容的完整性,平台不提供额外的编辑、内容补充、找答案等附加服务。
- 2、"仅部分预览"的文档,不可在线预览部分如存在完整性等问题,可反馈申请退款(可完整预览的文档不适用该条件!)。
- 3、如文档侵犯您的权益,请联系客服反馈,我们会尽快为您处理(人工客服工作时间:9:00-18:30)。
文件名称:受控状态:生效日期:1目的为了确保线束的质量及元器件与导线连接的可靠性,特制定此规范。
2范围本规范适用于本公司所有产品所用导线的检验。
3 定义目标条件:一种近乎完美的情况。
是一种理想状况,而非总能达到,且对于保证组件在其运行条件下可靠性并非必要条件。
可接受条件:组件不必完美但要在其使用环境下保持完整性和可靠性的条件。
制程警示条件:没有影响产品的外形、装配、功能或可靠性的情况。
缺陷条件:产品在其最终使用情况下不足以确保外形、装配或功能的情况。
4 线束检验要求4.1导线长度检验长度误差如下表线长(单位:mm)误差范围(单位:mm)0<L≤100 +3 - 0100<L≤500 +5 - 0500<L≤3000 +10 - 03000<L≤7500 +20 - 07500<L +2% - 0%4.2 导线检验4.2.1 外观检验:查看导线型号、规格、颜色等是否符合图纸和下线表的要求。
外观目标条件判定导线的导体切断面垂直于导线纵轴线所有股线长度一致;导线没有刮伤、刻痕、断开、压扁或其他损伤。
可接收条件判定导线的导体切断面大致垂直于导线纵轴线;所有股线长度大约一致;存在的毛刺不会在后续加工和装配期间脱落;股线散开,但未超过1倍股线直径或绝缘皮外径;股线未打结;绝缘皮允许留下轻微而规则的压痕,允许热处理引起的轻微变色但不允许烧焦、破裂或开裂。
制程警示条件判定股线有刮伤、刻痕或以切断,但单根导线损伤或断开的股线数未超过表一规定范围缺陷条件判定各股线的长度不一致影响到导线压接区全深度安装;作为表一的列外,股线的部分或不完全切口处于压接区域;作为表一的列外,股线的部分或不完全切口处于焊接连接区或没有接触全部需要缠绕的股线;损伤的股线数超过了表一的规定范围。
表一:股线允许损伤范围股线根数允许的最多刮伤、刻痕或切断的股线根数<7 07-15 116-25 326-40 440-60 561-120 6≥121 6%注一:对于工作在6千伏或更高电压下的导线不允许有股线损伤注二:对于有镀层的导线,不暴露金属基材的视觉异常不看做是损伤剥线后绝缘皮不合格现象说明:4.2.2 尺寸检验:下线长度按下线表要求、剥线长度要求见下表。
线规(mm 2)端子型号 剥线长度(mm ) 范围(mm )工具0.25H0.25/10 8 7.5-8.5 电脑切线剥皮机0.5H0.5/1411 10-12 FUT/FOT1.25 13(对折)12-14 ZH0.75/15 11 10-12 0.75H0.75/1411 10-12 FOT2、FUT2 13(对折)12-14 ZH1.0/15 12 11-13 OT1.513 12-14 1.0H1.0/141110-12185 JG185 30 29~31 网线 网线接头 13 12-14 网线压接钳0.75 GTC2L-24 -09PC-Y 插针、插孔 15(对折)14-16 电脑切线剥皮机2.5 9 8.5-9.5 0.5 12芯针、孔13(对折)12-14 0.75 7 6.5-7.5 0.75 20芯针、孔 13(对折)12-14 电脑切线剥皮机1.5 7 6.5-7.5 0.5 1601760 000孔 8 7.5-8.5 0.75 8 7.5-8.5 0.5 IGBT 插片5 4.5-5.5 0.75 54.5-5.54.3 导线的压接4.3.1 导线、压接端子、压接工具的组合与图纸及工艺文件相一致。
4.3.2 导线需要焊接时,导线芯线必须预上锡。
4.3.3 冲压成形接头开口连接筒外观检验: 端子各区域图示4.3.3.1 绝缘皮支撑压接部分外观:外观目标条件判定单根或多根导线压接时绝缘皮完全进入并伸过绝缘皮压接翼;绝缘皮压接不能切断或损坏绝缘皮;绝缘皮压接翼需全部包覆并加紧绝缘皮可接受条件判定绝缘皮表面有轻微变形但未切入或割破绝缘皮表面;绝缘皮压接翼夹住绝缘皮至少达180度并且两压接翼均接触到绝缘皮顶部;压接翼包住了大部分导线但未在顶部会合,顶部留下的开口只有45度或更小缺陷条件判定压接翼刺破绝缘皮;对绝缘皮的支撑不够180度;两个压接翼没有接触绝缘皮顶部;压接翼区域内夹有导体;压接翼包围导体但在顶部留的开口大于45度。
4.3.3.2 绝缘皮检查窗部分外观:外观目标条件判定绝缘皮和导体的界线位于检查窗的中间。
可接受条件判定在检查窗内可同时看到绝缘皮和导体。
制程警示条件判定绝缘皮与导体压接区平齐但未进入压接区(1);绝缘皮与压接翼平齐但未进入绝缘皮检查窗区域(2)。
缺陷条件判定绝缘皮进入导体压接区域;绝缘皮和导体分界线在绝缘皮压接区域内。
(箭头所示位置)4.3.3.3 导体压接部分外观:外观目标条件判定导体压接区域内没有绝缘皮;导体末端伸到刷尾检查窗中间;没有破损的或折返进入到压接区的或没有被导体压接翼夹住的导体股线;压接点位于压接区中央、压痕均匀、接头或锁紧翼未变形;导体股线没有被扭曲、切断或改变,以适合与接线柱的配接。
可接受条件判定接头的轻微变形未改变外形、装配、功能或可靠性。
制程警示条件判定压痕不均匀但未改变外形、装配、功能或可靠性。
缺陷条件判定绝缘皮伸入到导体压接区域内;接头或接线柱的变形影响了外形、装配、功能或可靠性;在压接区外有松散的、残留的或折返的导体股线。
4.3.3.4 钟形压口部分外观:外观目标条件判定导体压接区两端都有钟形压口;导体入口端的钟形压口高度是接头/接线柱金属材料厚度的2倍。
可接受条件判定导体压接端只在导体入口端有钟形压口(1),导体刷尾端没有(2);导体入口端的钟形压口可辨认,但其高度小于接头/接线柱金属材料厚度的2倍。
缺陷条件判定压接区导体入口端没有钟形压口(1);由于压接过度或导线规格过小导致钟形压口过大(2)。
4.3.3.5 导体刷部分外观:外观目标条件判定导体股线从导体压接端稍微伸出一点,形成“导体刷”;导体刷聚集在一起为向外张开。
可接受条件判定导体末端齐平于钟形压口末端(1);导体股线没有深入到接线柱的配接区;导体股线张开但未超过压接筒的外周边(2)。
缺陷条件判定导线末端没有伸出钟形压口的末端;导体股线超出了压接筒的外周边;导体股线伸入到接头配接区。
4.3.4冲压成形接头闭口连接筒外观检验: 端子各区域图示4.3.4.1 绝缘皮支撑压接外观:外观目标条件判定导线绝缘皮伸入到绝缘压接筒内;绝缘压接被均匀地成型并且接触导线绝缘皮且未损坏导线绝缘皮;接线柱绝缘套压痕清晰未损坏。
可接受条件判定不规则的绝缘压接接触到导体绝缘皮起到支撑作用;接线柱绝缘套压痕清晰;导线绝缘皮未损伤;缺陷条件判定导线绝缘皮不在绝缘压接区内;绝缘皮支撑压接不能支撑导线;导线股线折回或可见于绝缘压接区;接线柱的绝缘套没有牢固的包住接线柱。
4.3.4.2 导体压接和钟形压口外观:外观目标条件判定导体股线略微突出导体压接末端;压接点位于导体压接区的中心;接线柱绝缘套没有损坏两端有明显的钟形压口;导线全部被包住且伸出的导线平齐。
可接受条件判定导线与钟形压口平齐或伸出的长度不等且没有伸入配接区;两端有明显的钟形压口。
缺陷条件判定导线末端没有伸出钟形压口或伸入到配接区;绝缘套损坏露出金属;压痕不清晰。
4.3.5 机制接头外观检验:端子各区域图示:4.3.5.1 绝缘间隙外观:外观目标条件判定导线绝缘皮与接线筒之间的间隙(C)小于导线外径(D)的50%可接受条件判定在绝缘皮和接线筒之间可看到导体,但不大于1倍导线线径。
缺陷条件判定绝缘间隙大于1倍导线线径;暴露的导体违反最小电气间隙;绝缘皮伸进接线筒内。
4.3.5.2 导体定位:外观目标条件判定导体伸进接头底部;导体股线占满了检查窗;接头外没有导体股线。
可接受条件判定导体只占了检查窗的一部分;接头外没有导体股线。
缺陷条件判定在接头的检查窗内看不到导体股线或可以看到导线的绝缘皮;导体压接区域外有导体股线。
4.3.5.3 压接外观:外观目标条件判定压痕位于压接区中间;接线筒四周压痕分布均匀且深度一致;导线股线没松散;接头无裂纹、裂缝或暴露的金属基材。
可接受条件判定检查窗或导线入口边缘未因压接而变形。
缺陷条件判定导线没有压紧;接头上有裂纹、裂缝;接线筒变形弯曲;压痕位于压接区以外。
4.3.6 裸压接端子的压接连接外观:外观目标条件判定压接端子与绝缘皮间的间隙小于导线线径;压痕清晰且位于中间位置;导线全被包住。
可接受条件判定压接端子和包皮之间的间隙为0.1-1.0mm。
缺陷条件判定导线未被全部包住;压接位置偏移;导线伸入配接区或断面不能看到导线末端;压接端子与绝缘皮间隙大于1mm。
4.3.6.1 导线伸出紧固孔端面要求:当线束的线径为0.5mm2-16mm2时,芯线伸出端子紧固孔端面的长度为1.0~2.0mm;当线束的线径大于或等于16mm2时,芯线伸出端子紧固孔端面的长度:2.0~3.0mm。
4.3.7 JG端子压接连接外观:外观目标条件判定压接端子与绝缘皮间的间隙小于导线线径;压痕清晰且位于中间位置。
可接受条件判定压接端子与绝缘皮间隙线缆规格为16-95时,压接端子和包皮之间的间隙为0-2.0mm;线缆规格为120-300时,压接端子和包皮之间的间隙为0-3.0mm。
缺陷条件判定压接端子与绝缘皮超过要求间隙值或包住绝缘皮,压痕不清晰。
4.3.8 屏蔽线的屏蔽层处理后,不得留有金属毛刺,不得损伤内芯线的绝缘层,外层套热缩管。
屏蔽线去除屏蔽层长度要求表工作电压去除屏蔽层长度备注600V以下20-30mm 工艺文件中有特殊要求600V-3000V 30-50mm 的按照工艺文件操作。
3000V以上50-70mm4.3.9 排线外观检验4.3.10 网线外观检验4.3.11 IGBT插片焊接要求a)焊锡不能过多或过少,加锡位置见下图;b)焊锡之后周边要干净、光滑、平整,无毛刺、拉尖、锡瘤等现象;c)焊接完毕要吹上一层Φ3的黑色热缩套管(长度23~26mm),进行隔热绝缘保护;d)短接IGBT插片一般要求整根吹上一层Φ3的黑色热缩套管。
焊接高度不能超过此位置锡不能超过此位置线芯位置4.3.12 管状端子芯线伸出端子端面的长度为0 ~1.0mm。
将前端的芯线剪平齐。
长度为0 ~1.0mm4.4 线号:4.4.1 带“+”线用棕色套管,带“-”线用蓝色套管,U、V、W用黄、绿、红,接地线用黄绿套管,其它无特殊要求一般用白色。
如有特殊情况,应在工艺文件中标注。
4.4.2 导线标记字体为宋体,字体清晰,热缩后字高不小于2.5mm。
导线标记热缩管的长度和内径的确定应符合下表数值。
线规(mm2)端子种类热缩管规格热缩管长度0.25 H0.25 φ3 200.5 H0.5 φ3 20FOT1.25 φ5 200.75 H0.75 φ3 20FOT2 φ6 201.0 H1.0 φ4 20FOT1.25 φ5 201.5 H1.5 φ4 20FOT1.25 φ5 202.5 H2.5 φ5 20FOT2 φ6 204 H4.0 φ6 20FOT3.5 φ8 256 H6.0 φ8 25FOT5.5 φ8 2510 H10 φ8 25FOT10 φ8 20 16 H16 φ12 25JG16 φ12 25 25 H25 φ12 25JG25 φ12 25 35 H35 φ16 50JG35 φ16 50 50 JG50φ18 50 70 JG70φ30 50 95 JG95φ30 60 JG120 JG120φ30 60 JG150 JG150φ40 60 JG185 JG185φ40 604.5 线号外观:外观目标条件判定字体清晰且不能歪斜;热缩后与端子压接区末端平齐且不松动;线号无破损。