SPC 讲义20071220update
SPC我的讲义

3 σ 原理
6
正态分布概率
变量范围 μ±σ μ±2σ μ±3σ μ±4σ μ±5σ μ±6σ
正态分布概率 0.682649 0.954499 0.997300
0.99993657 0.999999742 0.999999998
备注
7
3 σ 原理
8
SPC的作用
合理使用管制图能: 供正在进行过程控制的操作者使用; 有助于过程在质量上和成本上能持续地, 可预测地保持下去; 使过程达到: ——更高的质量; ——更低的成本; ——更高的过程能力。 为讨论过程的性能提供共同的语言; 区分变差的特殊原因和普通原因,作为采 取局部措施或对系统采取措施的依据。
9
SPC的作用
• “SPC就像房屋中的烟雾探测器:只要这 种装置备有电池,并且被正确安置以及 旁边有人监听,那么它就可以提前发出 警报使你有足够时间阻止房屋起火”
10
SPC常用术语解释
名称
平均值 (X) 极差(Range) σ(Sigma) 标准差 (Standard Deviation)
分布宽度 (Spread)
12 34 56
计量单位:(mm, kg等)
管制图举例
X图 R图
27
测量方法必须保证始终产生准确和精密的结果
不精密
不准确
••••••••
准确
•••••
• ••••
精密
•••••• •••••
28
使用管制图的准备
1、建立适合于实施的环境
a 排除阻碍人员公正的因素
b 提供相应的资源
c 管理者支持
2、定义过程
中位数 ˜x
单值 (Individual)
解
SPC详细培训资料说课讲解
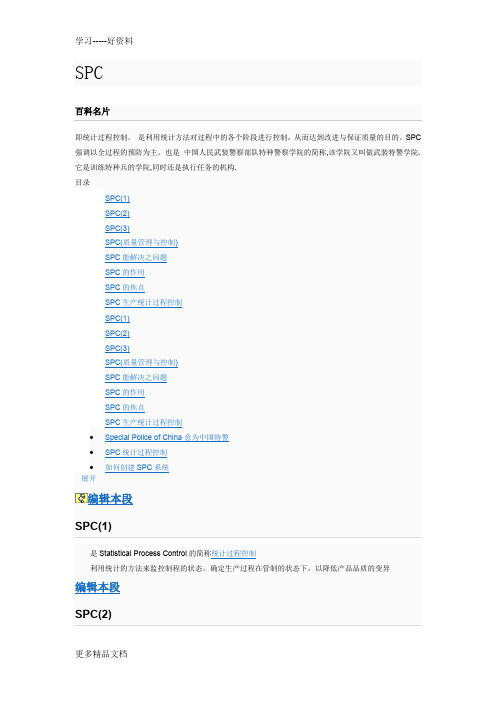
SPC编辑本段soy protein concentrate,大豆浓缩蛋白。
在大豆压榨过程中的产品,比豆粕蛋白含量高,且更易吸收。
常用于乳猪、水产、幼禽、犊牛、宠物等饲料制作。
是理想的饲料原料。
SPC(3) 增量脉冲编码器,编辑本段SPC(3)中国人民武装警察部队特种警察学院的简称,同时又叫做武装特警学院.它是训练特种兵的学院,同时还是执行任务的机构.编辑本段SPC(质量管理与控制)统计工序控制即SPC(Statistical Process Control)。
它是利用统计方法对过程中的各个阶段进行控制,从而达到改进与保证质量的目的。
SPC强调以全过程的预防为主。
编辑本段SPC能解决之问题1.经济性:有效的抽样管制,不用全数检验,不良率,得以控制成本。
使制程稳定,能掌握品质、成本与交期。
2.预警性:制程的异常趋势可即时对策,预防整批不良,以减少浪费。
3.分辨特殊原因:作为局部问题对策或管理阶层系统改进之参考。
4.善用机器设备:估计机器能力,可妥善安排适当机器生产适当零件。
5.改善的评估:制程能力可作为改善前後比较之指标。
利用管制图管制制程之程序1.绘制「制造流程图」,并用特性要因图找出每一工作道次的制造因素(条件)及品质特性质。
2.制订操作标准。
3.实施标准的教育与训练。
4.进行制程能力解析,确定管制界限。
5.制订「品质管制方案」,包括抽样间隔、样本大小及管制界限。
6.制订管制图的研判、界限的确定与修订等程序。
7.绘制制程管制用管制图。
8.判定制程是否在管制状态(正常)。
9.如有异常现象则找出不正常原因并加以消除。
10.必要时修改操作标准(甚至於规格或公差)。
分析用管制图主要用以分析下列二点:(1)所分析的制(过)程是否处於统计稳定。
(2)该制程的制程能力指数(Process Capability Index)是否满足要求。
-控制图的作用1.在质量诊断方面,可以用来度量过程的稳定性,即过程是否处于统计控制状态;2.在质量控制方面,可以用来确定什么时候需要对过程加以调整,而什么时候则需使过程保持相应的稳定状态;3.在质量改进方面,可以用来确认某过程是否得到了改进。
SPC培训PPT课件讲义

Control
计量值:
均值极差图 s规格标准差图 直方图
LSL
s
LCL
a
Ca Cp Cpk
四.SPC的基本观念
世上没有任何两件事.人员.产品是完全一样 制造过程中所产生之变异是可以衡量的 事情.产品的变异通常根据一定的模式而产 生 宇宙万物及工业产品大都呈常态分配 例如 :身高.体重.智力.考试成绩.所得分配 变异的原因可分为偶因及异因 偶因属管理系统的范围 异因却是作业人员本身就能解决的 应用SPC可以确保作业人员的自尊 应用SPC可以指出制程最需要改善的地方
正态分布中,任一点出现在 μ + σ内的概率为P(μ-σ<X< μ+σ) = 68.27% μ + 2σ内的概率为P(μ-2σ<X< μ+2σ) = 95.45% μ + 3σ内的概率为P(μ-3σ<X< μ+3σ) = 99.73%
不同的常态分配
(a)μ 1≠ μ 2,σ 1=σ
2
μ
1
μ
X
2
不同的常态分配
控制圖原理的第二種解釋
根據來源的不同,質量因素可以分成4M1E五個方 面。 但從對質量的影響大小來看,質量因素可分成 偶然因素(簡稱偶因)與異常因素(簡稱異因)兩類。偶 因是始終存在的,對質量的影響微小,但難以除去, 例如機床開動時的輕微振動等。異因則有時存在,對 質量影響大,但不難除去,例如車刀磨損、固定機床 的螺母鬆動等。
偶然因素(偶波)和異常因素(異波)
偶然因素之變異
1.大量之微小原因所引起,不可避免
2.不管發生何種之偶然原因,其個別 之變異極為微小 3.幾個較代表性之偶然原因如下: (1)原料之微小變異 (2)機械之微小掁動 (3)儀器測定時不十分精確之作 法
spc经典讲义(ppt文档)

Statistical Process Control
It is a capital mistake to theorize before you have all the evidence. It biases the judgment.
Willianli
随机抽样 指总体中每一个个体都有同等可能的机会被抽到。这种抽样方法事先不能考 虑抽取哪一个样品,完全用偶然方法抽样,常用抽签或利用随机数表来抽取 样品以保证样品代表性。
抽样
当总体容量不大时,随机抽样是一种有效的抽样方法
©S.R.A.T.O.A Consulting ®
7
思瑞达管理咨询有限公司
Statistical Process Control
抽样方法
分层抽样
分层抽样是先将总体按照研究内容密切有关的主要因素分类或分层,然 后在各层中按照随机原则抽取样本。分层抽样可以减少层内差异,增加 样本的代表性。
抽样
样本
当获得的资料不均匀,或呈偏态分布时,分层抽样是一种有效的抽样方法
©S.R.A.T.O.A Consulting ®
8
思瑞达管理咨询有限公司
统计基础
It is a capital mistake to theorize before you have all the evidence. It biases the judgment.
©S.R.A.T.O.A Consulting ®
3
思瑞达管理咨询有限公司
什么是有意义的情报?
Statistical Process Control
- 直方图与正态分布 - 制程能力的概念 - 计量值数据的制程能力解析 - 计数值数据的制程能力解析
SPC讲义
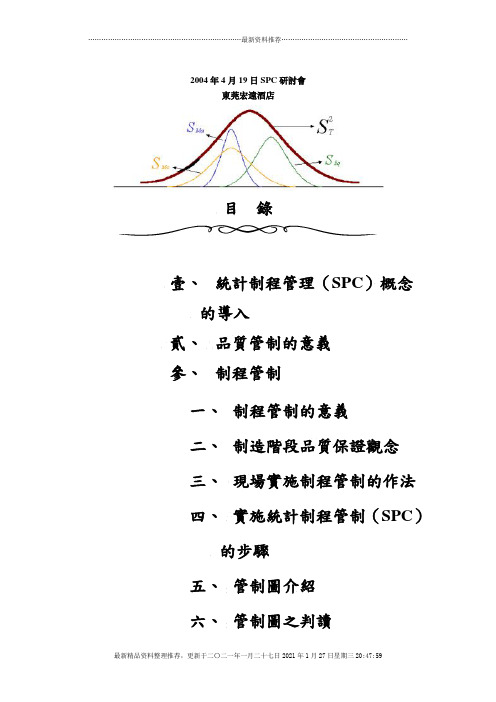
2004年4月19日SPC研討會東莞宏遠酒店目錄壹、統計制程管理(SPC)概念的導入貳、品質管制的意義參、制程管制一、制程管制的意義二、制造階段品質保證觀念三、現場實施制程管制的作法四、實施統計制程管制(SPC)的步驟五、管制圖介紹六、管制圖之判讀七、制程能力分析肆、演練伍、結論壹、統計制程管制(SPC)概念導入一、SPC之演進1.什麼是SPC(STATISTICAL PROCESS CONTROL)利用統計各種方法來管制製造程序,使產品一次做好。
SPC=SQC+QUALITY PLANNING AND DESIGN2.什麼是SQC(STATISTICAL QUALITY CONTROL)?由SHEWHART在1937年提出“以統計方法協助分析品質問題,進而找出解決問題方案的品管方法”。
這些方法主要有:*管制圖*直方圖*柏拉圖*查檢表*制程能力分析*實驗計劃法*可靠度方法3.SQC的精神——制程能力的穩定維持——事後制程(AFTER PROCESS)之品質改善分析——阻擋不良品進入/流出(IQC/OUTGOING CONTROL)……………………………………………………………最新资料推荐…………………………………………………4.演進史(參見附圖一)SPC之演進史1950 1970 1980最新精品资料整理推荐,更新于二〇二一年一月二十七日2021年1月27日星期三20:47:59二、基本統計概念1.數據的性質(1)數據的差異因為沒有兩個產品(或制成品)是完全一樣的,就算是同一條生產線上用同樣的原料,同樣的方法做出來的,還是會有變動因素所構成的差異。
因此,對於製造者而言,每一零件之各品質規格特性,所能做的是:a.瞭解差異一定存在;b.找出差異的可能原因(原料、儀器、設備、隨機、人為,亦或是「不適當」之組織機能營運下所潛藏的因素),所以,必須將隨機誤差保持在一可容忍的範圍里,統計品管便由此誕生。
(2)可靠度、精密度、正確度檢討數據時,應先考慮是否具備a.可靠度;b.精密度;c.正確度等三個要素。
SPC讲义
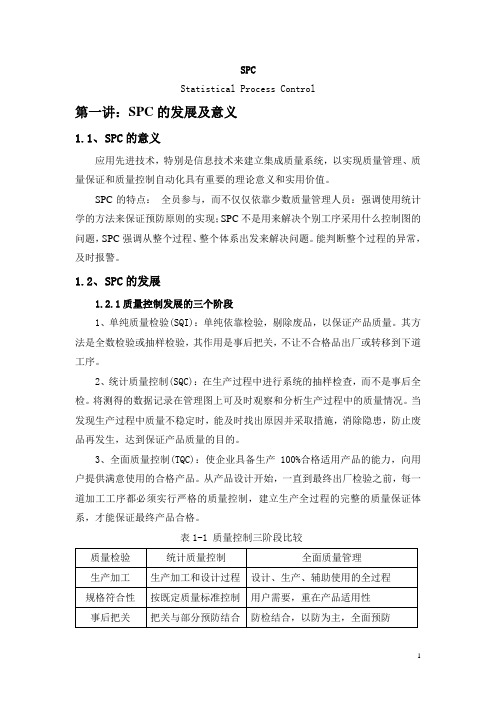
SPCStatistical Process Control第一讲:SPC的发展及意义1.1、S PC的意义应用先进技术,特别是信息技术来建立集成质量系统,以实现质量管理、质量保证和质量控制自动化具有重要的理论意义和实用价值。
SPC的特点:全员参与,而不仅仅依靠少数质量管理人员:强调使用统计学的方法来保证预防原则的实现;SPC不是用来解决个别工序采用什么控制图的问题,SPC强调从整个过程、整个体系出发来解决问题。
能判断整个过程的异常,及时报警。
1.2、S PC的发展1.2.1质量控制发展的三个阶段1、单纯质量检验(SQI):单纯依靠检验,剔除废品,以保证产品质量。
其方法是全数检验或抽样检验,其作用是事后把关,不让不合格品出厂或转移到下道工序。
2、统计质量控制(SQC):在生产过程中进行系统的抽样检查,而不是事后全检。
将测得的数据记录在管理图上可及时观察和分析生产过程中的质量情况。
当发现生产过程中质量不稳定时,能及时找出原因并采取措施,消除隐患,防止废品再发生,达到保证产品质量的目的。
3、全面质量控制(TQC):使企业具备生产100%合格适用产品的能力,向用户提供满意使用的合格产品。
从产品设计开始,一直到最终出厂检验之前,每一道加工工序都必须实行严格的质量控制,建立生产全过程的完整的质量保证体系,才能保证最终产品合格。
表1-1 质量控制三阶段比较1.2.2质量控制的发展趋势质量控制还将继续吸取经济学、心理学、社会学等自然科学和社会科学的成果,向更广阔的领域发展,质量控制部门对其它职能部门的协调作用将更加增大,产品质量检验的技术水平和准确性,以及机械化、自动化程度就大大提高,质量保证体系在搜集、处理、储存、传递质量信息中的作用更加突出,质量反馈更加重要,对质量控制业务更加标准化,程序化的要求更加严格;质量控制的重点,要从制定过程质量控制逐步转移到产品开发研制,设计质量越来越成为提高产品质量的关键,技术服务工作更将提到质量控制举足轻重的地位;质量控制机构的设置,质量检验部门和综合质量管理机构趋向分开,各自担负不同的质量控制职能保证产品质量和发展新品种将越来越紧密结合,成为从根本上提高产品质量的发展方向。
SPC基础知识培训讲义

SPC基础知识培训讲义SPC基础知识⼀、什么是SPCSPC是英⽂Statistical Process Control的前缀简称。
即统计过程控制。
SPC就是应⽤统计技术对过程中的各个阶段进⾏监控。
从⽽达到改进与保证质量的⽬的。
SPC强调全过程的预防。
SPC的特点是:1.SPC是全系统的,全过程的,要求全员参加,⼈⼈有责。
这点与全⾯质量管理的精神完全⼀致。
2.SPC强调⽤科学⽅法(主要是统计技术,尤其是控制图理论)来保证全过程的预防。
3.SPC不仅⽤于⽣产过程,⽽且可⽤于服务过程和⼀切管理过程。
⼆、SPC发展简史过程控制的⽅法早在20世纪20年代就由美国的休哈特提出。
迄今为⽌已经经历了三个发展阶段,即:SPC,SPCD和SPCDA。
1.SPC(Statistical Process Control):它能使⼈们采取措施,消除异常,恢复过程的稳定。
这就是科学地区分出⽣产过程中产品质量的正常波动与异常波动,从⽽对过程的异常及时告警,谓统计过程控制。
2.SPCD(Statistical Process Control and Diagnosis)的前缀简称,即统计过程与诊断。
SPC虽然能对过程的异常进⾏告警,但是它并不能告诉我们是什么异常,发⽣于何处,即不能进⾏诊断。
1982年我国张公绪⾸创两种质量诊断理论,突破了传统的美国休哈特质量控制理论,开辟了统计质量诊断的新⽅向。
3.SPCDA(Statistical Process Control , Diagnosis and Adhustment)的前缀简称,即统计过程控制、诊断与调整。
正如同病⼈确诊后要进⾏治疗,过程诊断后⾃然要加以调整。
⽬前尚⽆实⽤性的成果。
三、成都公司在TS16949标准基础上建⽴的《统计技术应⽤规定》中推荐了⼏种⽤于质量改进的统计⼯具和技术序号⼯具和技术应⽤1调查表系统地收集资料,以得到真实清晰的实况⽤于⾮数字资料的⼯具和技术2因果图分析和表达因果图解关系;通过从症状到原因分析到寻找答案的过程,促进问题的解决3流程图描述现存的过程;设计新的过程4特性要因图表⽰某个论题与其组成要素之间的关系⽤于数字资料的统计⼯具和技术5控制图诊断:评估过程的稳定性;控制:决定何时某⼀过程需要调整,何时该过程需要继续保持下去。
{品质管理SPC统计}SPC培训讲义PPT66页

σ(Sigma) 用于代表标准差的希腊字母
标准差
(Standard Deviation)
过程输出的分布宽度或从过程中统计抽样值(例如: 子组均值)的分布宽度的量度,用希腊字母σ或字母 s(用于样本标准差)表示。
分布宽度 一个分布中从最小值到最大值之间的间距 (Spread)
中位数 ˜x
将一组测量值从小到大排列后,中间的值即为中位数。 如果数据的个数为偶数,一般将中间两个数的平均值 作为中位数。
我们工作 的方式/ 资源的融 合
产品或 服务
输入
过程/系统
输出
顾客
识别不断变化的 需求量和期望
顾客的呼声
过程:所谓过程指的是共同作用,以产生输出的供应商、 生产者、人、设备、输入材料、方法和环境,以及使用 输出的客户的集合,如上图。
变差 为了有效地使用过程控制的测量数据,了解变差的概念 是很重要的 变差:过程的单个输出之间不可避免的差别;可以理解 为两个产品之间的差别。 变差的原因可分为两类:普通原因和特殊原因。 普通原因:是指过程在受控的状态下,出现的具有稳 的且可重复的分布过程的变差的原因。 普通原因表现为一个稳定系统的偶然原因。 只有过程变差的普通原因存在且不改变时,过程的输出 才可以预测。 特殊原因:(通常也叫可查明原因)是指造成不是始终 作用于过程的变差的原因,即当它们出现时将造成(整 个)过程的分布改变。 只用特殊原因被查出且采取措施,否则它们将继续不可 预测的影响过程的输出。
稳定地满足顾客的要求。
SPC的作用
SPC可以: · 对过程作出可靠的评估; · 确定过程的统计控制界限,判断过程是否失控和过 程是否有能力; · 为过程提供一个早期报警系统,及时监控过程的情 况以防止废品的发生; · 减少对常规检验的依赖性,定时的观察以及系统的 测量方法替代了大量的检测和验证工作;
SPC讲义
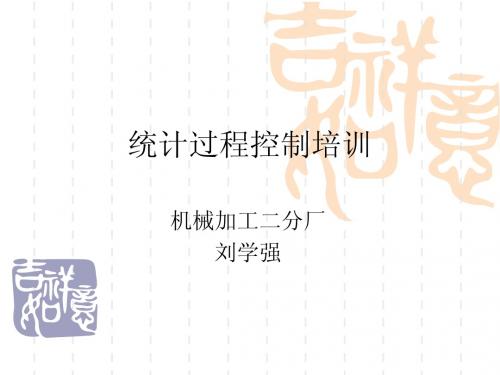
普通原因 (CommonCause)
过程能力 (Process apability)
移动极差 (Moving Range)
两个或多个连续样本值中最大值和最小值之 差。
控制图类型
X-R 均值和极差图 计 量 X-δ均值和标准差图 型 数 X -R 中位值极差图 据 X-MR 单值移动极差 图 计 数 型 数 据 P chart 不良率管 制图 nP chart 不良数 管制图 C chart 缺点数 管制图 U chart 单位缺 点数管制图
分别算出Pzusl 和 Pzlsl 的百分比,再将其相加。
4-3 评价过程能力
当 Cpk<1 说明制程能力差,不可接受。 1≤Cpk≤1.33,说明制程能力可以,但需改善。 1.33≤Cpk≤1.67,说明制程能力正常。
中位数极差图(X - R)
中位数图易于使用和计算,但统计结果不精确 可用来对几个过程的输出或一个过程的不同阶段的输出进行比 较 数据的收集 一般情况,中位数图用于子组的样本容量小于或等于10的情 况, 当子组样本容量为偶数时,中位数是中间两个数的均值。 只要描一张图,刻度设置为下列的较大者: a 产品规范容差加上允许的超出规范的读数 b 测量值的最大值与最小值之差的1.5到2倍。 c 刻度应与量具一致。 将每个子组的单值描在图中一条垂直线上,圈上子组的中位数, 并连接起来。 将每个子组的中位数˜X和极差R填入数据表. 控制限的计算
对系统采取措施
通常用来消除变差的普通原因 几乎总是要求管理措施,以便纠正 大约可纠正85%的过程问题
SPC常用术语解释
名称
平均值 (X)
解释 一组测量值的均值 一个子组、样本或总体中最大与最小值之差 用于代表标准差的希腊字母
SPC讲义

敘述统计介绍 – 极差(2)
离散的程度:极差(Range)、标准差(Standard Deviation)
➢极差=最大值-最小值
➢样本方差Variance =
(x x)2 i
,
i=1,2,…..n
n 1
x
其中
x
i
n
➢样本标准差 s = 样本方差
敘述统计介绍 – 极差(3)
极差是一组数据的最大值和最小值之差。 R=Xmax-Xmin
SPC的作用
保持(控制)过程
● 当过程已被了解,必须保持在适当的能力水平 ● 过程是动态会发生变化的 ● 对过程的表现必须监控以预防不良变化 ● 好的变化亦应了解并把它固定下来 ● 控制可监控过程 ● 当过程发出讯号时,应立即而有效地找出原因和采取行动 ● 很多时候会留在此阶段,因为公司的资源限制 ● 要达到“世界级”的成就,必须坚持计划努力进入过程改进循环
1994年美国FORD、GM、CHRYSLER三大汽车厂公布QS-9000的品质系统要求 ,向全球推广应用,正式将SPC的应用提升到实际的生产活动中。
SPC的作用
ISO/TS 16949 的目标
缺陷预防 减少变差及浪费 持续改善
QC七大工具简介
QC七大工具是指:
查检表
Check List
不受控(存在特殊原因)
SPC统计过程控制基本知识
过程能力
受控且有能力符合规范 (普通原因造成的变差已减少)
规范下限
规范上限
时间
范围
受控但没有能力符合规范 (普通原因造成的变差太大)
SPC统计过程控制基本知识
过程分类 (按其能力和是否受控)
满足能力 可接受
不可接受
SPC课程讲义(doc 43页)_New

SPC课程讲义(doc 43页)47 檢定導引個案詹昭雄編著 2003.03檢定導引個案為了改善產品厚度之均一性,莊進行了下列工作:(1)現況分析:(略)結果得知 C a ok ,C p=1.27,分佈近似常態(2)原因分析:C p不足噴口式不合(3)真因驗証:為了証實噴口型式是否影響C p,莊將噴口型式從A型改為B型做了n=18個之試驗經推定B型厚度之標準差σn-1=0.93而原來A型所生產厚度之σ=1.24因為:σb<σa且相差0.31所以莊工程師建議全面將A型改為B型(經費約需二萬五千元),經批准後於假日加班全部改為B型。
B型在生產一週後,週報上顯示厚度之標準差σ=1.19與原來A型幾乎無差別,令人覺得二萬五似乎白花變成學費了。
請問:(1)為什麼會這樣?A:(2)如何在實驗數、樣本數不大(例如n<20)之下,依據 n-1或X n能有「相當程度之把握」(例如九成)判斷大量生產後之σ(或μ)有差別或有效果?(3)假如莊工程之老闆在改善建議報告上批示α=?,你知道是什麼意思嗎?A:49 計 量 值 檢 定 Ⅰ 詹昭雄 編著 2003.07統計判斷 ─ 檢定作法一此例如以母平均檢定來做判斷,其作法如下:S 1:設立假設H o :(無差假設) μ(新)=μo (原來) (58.31)H 1:(替代假設) μ>μo (依專業技術採單邊檢定)S 2:決定否定H o 時所願冒的α值(α大小為Case by Case)經考慮本判斷α之損失成本,決策者決定α=5%S 3:選定統計量分配及計算統計量(a)因目前之σ已知為4.82,而且就專業技術而言,改變了條件只會 影響μ,不會影響σ,故選用常態分配。
(b)87.015/82.431.584.5915/=-=-=σμo o X U (1.66)S 4:比較發生H o 之機率P ho 與α值(a)查U(α)=U(0.05)=1.64(b)因為U o <U(α),表示μ=μo 之機率>α(5%)(>) (<)S 5:判斷(a) 因μ=μo 之機率>α,所以在現有資訊量n =15及合理之α=5%(信心度95%)(<)要求下,尚不能(已可以)否定μ=μo 之假設,亦即條件改變後,母平均尚不能(可以)判斷顯著提高了。
SPC培训讲义(第二版)

控制图的要素
控制图的表现形式没有“批准的”唯一形式, 然而应牢记拥有控制图的原因,包含以下内 容的任何形式都是可接受的: • 适当的刻度:确保分辨出过程变差。 • 控制限(UCL、LCL):分析过程的出界点。 • 中心线:分析过程的非随机图形的特殊原因。 • 失控值的标识:从整体角度上分析过程。 • 事件日志:记录过程变化,确定纠正措施。
• 事件的记录; 包含详细的事件记录,如过程调整、工装更换、材料更换或其
他可能影响过程变差的事件。
31
记录原始数据
• 记录每个子组的单值和标识; • 记录任何观察到的相关事件。
32
计算每个子组的样本控制统计量 根据测量的数据进行描点和计算控制统计量。
这些统计量可以是样本均值、中位数、极差、标准 差、不合格率等 ,按照所用控制图类型的公式来计 算这些统计量。
• 控制图(Control Chart):对过程质量特性记录评估, 以监察过程是否处于受控状态的一种统计方法图。
17
控制图原理
3原则
• 不论与取值为何,只要上下限距中心值(平均值) 的距离各为3 ,则产品质量特征值落在范围内的为 99.73%。
• 产品质量特征值落在[ -3 , +3 ]之外的概 率为0.27%,其中单侧的概率分别为0.135%。
• 休哈特正是据此发明了控制图。
18
产品质量波动及其统计描述
产
定量
连续
计量值
品 质
离散
计数值
计
量
数
特 性
定性
值 计件值
19
计量型数据---计量型控制图
• 计量型数据是由过程特性决定的,来自 过程的数据是连续的,如直径、长度。 是一个量化的数据,是实际生产过程的 过程现象的反映。
- 1、下载文档前请自行甄别文档内容的完整性,平台不提供额外的编辑、内容补充、找答案等附加服务。
- 2、"仅部分预览"的文档,不可在线预览部分如存在完整性等问题,可反馈申请退款(可完整预览的文档不适用该条件!)。
- 3、如文档侵犯您的权益,请联系客服反馈,我们会尽快为您处理(人工客服工作时间:9:00-18:30)。
知识点
3、能力指标及其执行状况指标 3.1、理解变量数据的过程能力和执行状况;
3.2、过程术语定义、可预测的过程进行过程测量;
3.3、特性数据的能力指标; 3.4、其它知识。
第一部分
持续改进和统计过程控制
过程控制模式——无反馈的过程
1、最终检测——容忍浪费
隐藏工厂/浪 费
返修
能 能返修?
不能
报废
知识点
1、持续改进及统计过程控制
1.1、预防与最终检查;
1.2、过程控制系统; 1.3、变差:普通原因和特殊原因; 1.4、局部措施和系统措施; 1.5、过程控制和过程能力; 1.6、过程改进循环和过程控制; 1.7、控制图:过程控制和改进的工具。 2、控制图 2.1、控制图类型和控制图要素; 2.2、控制图的制定过程; 2.3、确定失控信息; 2.4、控制图公式;
超出控制限之外的点
UCL
A B
6s 4s 2s
在中心线同一边有7个连续的点 7个连续点上升或下降
C C B A
LCL
3个点中有2个同在A区或是之外
5个点中有4个同在B区或是之外 14个连续的点交互上下 14个连续的点任一C区
为运行和趋势 分析确定的规则
Nelson 测试特殊原因
UCL A B 6s 4s 2s C C B A
Xbar-R 和子组数据
X1 43.8 44.7 45.3 45.4 43.8 45.7 46.5 46.1 44.5 47.8 45.5 46.8 44.2 44.6 46.0 46.3 43.2 45.2 44.6 45.6 X2 43.7 43.2 43.8 44.1 45.6 46.0 45.6 45.8 44.0 43.6 45.4 43.5 44.7 44.7 46.0 43.7 43.0 45.1 44.5 44.2 X3 47.2 45.7 44.3 44.6 44.6 45.6 45.7 45.5 45.4 44.5 42.8 43.4 46.1 45.2 45.0 44.8 45.6 46.9 44.6 46.0 X4 46.3 45.8 46.2 45.3 44.8 45.9 46.9 45.9 45.8 46.0 47.0 46.0 44.5 43.0 44.5 46.0 44.8 45.0 43.7 43.5 X5 44.4 44.4 46.6 45.0 45.0 46.5 45.6 45.1 44.7 44.5 45.1 45.0 45.8 45.5 47.2 45.4 45.4 44.8 45.1 45.9
SPC 在整个工业生产中的角色
1、产品开发; 2、确定每个产品生产中的关键点;
3、确定控制计划;
4、利用SPC进行过程控制; 5、通过SPC监控过程的变化趋势; 6、通过SPC识别特殊原因,并利用各种解决问题的工具加以消除,以便维 持过程持续稳定的运行; 7、通过SPC 识别过程普通原因的变化状况,以便确定过程什么时候应该进 行机器及其技术的更新。 8、利用SPC后,最终归结到一点:为解决问题提供信息,并可以最后利用 一个工具——6-Sigma,进行对问题的解决,然后再利用SPC对改进的成 果进行监控。
它是在过程受控时进行设定的
– 固定在基准值
– 过程改变了就要做调整
– 决不会变宽
控制限同公差带不相关
控制限不是公差带
控制的定义
受控是
过程变化的一个统计术语
– 在均值的3倍标准偏差之内;
– 它不呈现某种运行趋势;
– 偶然原因变化导致。
Western Electric Rules for Control Overview 伟世通
Nelson 测试 1
A B C C B A
规则 1: 超出控制限之外的任意点
Nelson 测试 2
A B C C B A
规则 2: 9 个连续的点在中心线的同一边
Nelson 测试 3
A B C C B A
规则 3: 6 个连续的点连续上升或下降
Nelson 测试 4
A B C C B A
1984年日本名古屋工业大学调查了115家日本各行业的中小型工 厂,结果发现平均每家工厂采用137张控制图。而有些大公司应 用的控制图就更多了,如美国柯达彩色胶卷公司有5000名职工, 一共应用了35000张控制图。这是因为彩色胶卷的工艺很复杂, 在胶卷的片基上需要分别涂上8层厚度为1~2μm的药膜;此外, 对于种类繁多的化工原料还要应用SPC控制。
人
机器
材料
变差
方法
环境
测量
变差概念
2、过程中的变差可能引起短期的、件与件之间的差异; 3、过程中也有变差可能对输出有长期的影响;
4、这些变差可能逐渐发生,比如:工具或是机器的磨损;
这些变差可能跳跃性的发生,比如:操作程序上的改变; 这些变差可能不规则的发生,比如:环境的改变; 5、要减小变差,首先就要区分下面两个概念: A、特殊原因; B、普通原因。 最终目标是:向目标值靠近,变差越小越好;
上控制限
观测值
均值 下控制限
0
0
5
观测序号
10
15
20
非任意变化区域
控制图的关键要素
3、子组顺序/时间序列 要维持数据收集的顺序,以提供“什么时候”发生一个特殊原因和 特殊原因是否跟时间相关的信息
4、识别失控的数值
5、事件记录
控制图的关键要素——5
确定过程控制限
控制限是
统计控制限均值 +/- 3 标准偏差
可能没有能力始终生产出合格产品!! 可能正在改进过程, 或者相对公差带来说过程变差还算小
O? P
可能需要稳定
需要稳定, 减小变差, 和/或者均值需要移动
不可接受
随时都可能生产不合格产品。
O
O
随时都可能生产不合格产品!!
控制图的组成部分
观测点 10
10 9 8 7 6 5 4 3 2 1
任意变化区域
返修
不能
报废
工作方式/ 融合所有的资源
是
合格?
顾客
识别顾客不断改
输入
过程/系统
输出
变的需求和期望
顾客的声音
预防与检查的差异
讨论预防为过程所带来的好处: 1.成本上的差异;
2.解决问题速度上的差异;
3.效果上的差异。
过程为什么需要控制?
变差概念
1、同一过程生产出来的产品或是特性不可能完全相同,因为过程中 存在变差源(6大变差源),这种差异也许很大,也许很小。
人 设备 材料 方法 测量 环境
工作方式/ 融合所有的资源
是
合格?
顾客
输入
过程/系统
输出
过程控制模式----有反馈的过程控制系统
2、预防——避免浪费
过程的声音
Do it right the first time
统计方法
人 设备 材料 方法 测量 环境
工作方式/ 融合所有的资源
产品或是服务
顾客
输入
过程/系统
1.
2. 3. 4.
在控制限之外的任何点
9 个连续的点在中心线的同一边 6 个连续的点连续上升或下降 3个点中有2个都在A区或之外
5.
6.
5个点中有4个都在B区或之外
14 个连续的点交互上升和下降 15 个连续的点在任一个C区 8个点在C区之外的成一行,并在 中心线的同一边
LCL
7. 8.
Tests proposed by Lloyd Nelson (1984) and used by MINITAB™ for run and trend analysis
特殊原因
间隙性的 作用于过程 影响小(15%)
对总体的影响趋势可以预 对总体的影响趋势不可预 测 测
局部措施
消除特殊原因
系统措施
减小普通原因引起的变差
由流程负责人去执行
只能解决15%的流程问 题
需要管理层来参与执行 能解决85%的流程问题
第二部分、控制图
变化源
环
境
统计过程控制
KPIVs
机 材 器 料 方 法
过程控制模式——无反馈的过程
1、最终检测——容忍浪费
隐藏工厂/浪 费
返修
能 能返修?
不能
报废
人 设备 材料 方法 测量 环境
工作方式/ 融合所有的资源
是
合格?
顾客
输入
过程/系统
输出
过程控制模式
3、预防和检测相结合——现在运作模式
过程声音
能
能返修?
隐藏工厂/浪费
统计方法
人 设备 材料 方法 测量 环境
在控制限之外的任何点 9 个连续的点在中心线的同一边 6 个连续的点连续上升或下降 3个点中有2个都在A区或之外 5个点中有4个都在B区或之外 14 个连续的点交互上升和下降 15 个连续的点在任一个C区
•
8个点在C区之外的成一行,
并在中心线的同一边
发错误警报的比率是关键的
Nelson
• • • • 在控制限之外的任何点 9 个连续的点在中心线的同一边 6 个连续的点连续上升或下降 3个点中有2个都在A区或之外
错误警报率
.0027 大约 .003 大约 .003 .00305 .0043 大约 .004
•
• • •
5个点中有4个都在B区或之外
14 个连续的点交互上升和下降 15 个连续的点在任一个C区 8个点在C区之外的成一行,
大约 .003
大约 .003
并在中心线的同一边
Nelson的所有测试错误警报率基本相同。 Western Electric 规则没有这个特性。