挤压铝型材课程设计
挤压铝型材 截面设计
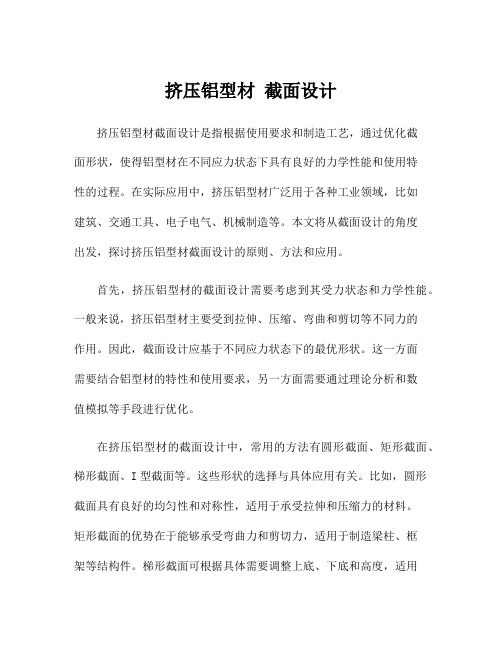
挤压铝型材截面设计挤压铝型材截面设计是指根据使用要求和制造工艺,通过优化截面形状,使得铝型材在不同应力状态下具有良好的力学性能和使用特性的过程。
在实际应用中,挤压铝型材广泛用于各种工业领域,比如建筑、交通工具、电子电气、机械制造等。
本文将从截面设计的角度出发,探讨挤压铝型材截面设计的原则、方法和应用。
首先,挤压铝型材的截面设计需要考虑到其受力状态和力学性能。
一般来说,挤压铝型材主要受到拉伸、压缩、弯曲和剪切等不同力的作用。
因此,截面设计应基于不同应力状态下的最优形状。
这一方面需要结合铝型材的特性和使用要求,另一方面需要通过理论分析和数值模拟等手段进行优化。
在挤压铝型材的截面设计中,常用的方法有圆形截面、矩形截面、梯形截面、I型截面等。
这些形状的选择与具体应用有关。
比如,圆形截面具有良好的均匀性和对称性,适用于承受拉伸和压缩力的材料。
矩形截面的优势在于能够承受弯曲力和剪切力,适用于制造梁柱、框架等结构件。
梯形截面可根据具体需要调整上底、下底和高度,适用于承受不同比例压缩力的结构。
I型截面则常用于承受大跨度梁的弯曲力。
此外,挤压铝型材的截面设计还需要考虑到材料的节能性能和强度。
对于建筑领域的铝型材来说,节能是一个重要指标。
截面设计可以通过减小型材的外壁厚度,增加空腔的使用,减轻铝材的重量,提高铝材的节能性能。
同时,合理的截面设计还能够提高铝材的屈服强度和抗拉强度。
在实际应用中,挤压铝型材的截面设计需要结合制造工艺和可加工性进行考虑。
为了实现设计要求,挤压铝型材的截面形状需要符合挤压成形的要求。
比如,截面的尺寸应尽量避免突变,避免内外壁厚度的突变,避免造成挤压后型材在成型过程中出现溶胀和折叠等问题。
总之,挤压铝型材截面设计是一个综合考虑材料特性、使用要求和制造工艺的过程。
通过充分理解材料的受力状态和力学性能,合理选择截面形状,并结合制造工艺进行设计优化,可以提高挤压铝型材的力学性能、可加工性和经济性。
挤压铝型材课程设计讲解

一. 题目:铝合金型材挤压工艺及模具设计二. 设计基本内容:设计一件实心型材制品和一件空心型材制品的工艺工艺过程及模具设计,包括挤压工艺参数,模具结构,制造工艺等要求三. 完成后应缴的资料:课程设计说明书一份实心型材模零件图空心型材模上模零件图空心型材模下模零件图空心型材模装配图四. 设计完成期限:2007年6月11日------2007年6月22日指导老师_______签发日期___________教研室主任_______批准日期___________课程设计评语:成绩:设计指导教师_________ _____年_____月____日目录一、绪论 (4)二、总设计过程概论 (7)2.1挤压工艺流程 (7)2.2挤压工艺条件 (7)三、实心型材模设计 (9)3.1所要设计的实心型材制品 (9)3.2选坯和选设备 (10)3.3挤压力的计算 (11)3.4实心型材模具体结构设计 (12)3.5.实心模尺寸数据设计 (13)四、空心型材模设计 (18)4.1所要设计的制品 (18)4.2选坯和选设备 (18)4.3挤压力的计算 (19)4.4模组及模子外形尺寸确定 (20)4.5组合模相关参数的确定 (20)4.6 模子内形尺寸的确定 (23)4.7模孔工作带长度h g的确定 (24)4.8模芯的设计 (24)4.9上模凸台设计 (24)4.10定位销,螺钉 (24)4.11模子强度校核 (25)4.12零件图装配图 (26)五、总结与体会 (26)参考文献 (26)一. 绪论近20年来,随着建筑行业的高速发展,我国民用建筑铝型材工业也从无到有,从弱到强地迅猛前进。
至今,广东省的建筑铝型材产品已约占全国的三分之二左右,铝型材的生产能力超过社会的需求,如何提高产品质量,降低成本是取得市场竞争胜利的关键环节。
铝合金型材具有强度高、重量轻、稳定性强、耐腐蚀性强、可塑性好、变形量小、无污染、无毒、防火性强,使用寿命长(可达50—100年),回收性好,可回炉重炼。
铝型材挤压车间工艺设计解析

一、课程设计题目:年产13580吨铝型材挤压车间工艺设计二、课程设计绪论随着市场经济的发展,各种新型的高科技建筑材料相继出现,所有的基础工程均需要大量的建筑,需要大量门窗和建筑材料,而铝及其铝合金在其中占有重要的地位。
铝合金型材具有强度高、重量轻、稳定性强、耐腐蚀性强、可塑性好、变形量小、无毒无污染、防火性强、回收性好、可回炉重炼、使用寿命长(可达50—100年)等特点。
多年来世界各国均采用6063铝合金(铝合金近百种)做为门窗框架。
主要是因为该金属表面阳极氧化效果好,开始阳极氧化是白色,后进一步改变电解质才达到古铜色,这两种主体颜色在国内用了十多年。
铝材在挤压过程中,如挤压模具不是很好或模具挤压铝材过多,铝材表面会产生挤压痕,用手可能触摸到铝材表面不平,因此,在现代化大生产中实施挤压加工技术,其成败的关键是模具设计,事关产品的质量、成本。
在车间设计的过程中应考虑到的因素包括:产品的型号、模孔数的确定、选择挤压机、铸锭的选用、年产量、年水电费、设备投资费、人工费等等。
其中,选择挤压机是一个最核心的问题,具体可见设计步骤。
三、课程设计分析这次的设计任务是设计一个年产量不少于5000吨的铝型材挤压车间,生产的产品有:窗帘导轨、卷闸、纱窗铝合金型材,汽车装饰铝合金型材,90系列推拉窗等。
挤压制品所用的材料是6063合金。
1、6063合金化学成分及性能表1:6063合金化学成份及性能532、产品的截面图及主要尺寸表2:产品截面图形及主要尺寸型号 D302、0.877 kg/mH110、1.524 kg/mC522、0.905 kg/m截 面 图 形 及 主 要 尺 寸型号BC6257、0.318 kg/mH103、0.406 kg/mAT4047、0.639 kg/m截 面 图 形 及 主 要 尺 寸型号 H209、0.284 kg/m H202、0.448 kg/m截 面 图 形 及 主 要 尺 寸3、产品的主要常数表3:产品代号参数其中:单位重量是表2给出的;外接圆直径是通过AUTO CAD 模孔设计时测出的;截面积=单位重量×1000/铝型材的密度,密度取2.69千克/立方分米;模孔面积=截面积×(1+1.5%);模孔数本次设计可以单孔的都单孔,除非单孔不符合挤压机的选择原则。
铝型材挤压模具设计课件

铝型材挤压模具设计课件一、铝型材挤压工艺概述二、铝型材挤压模具结构三、铝型材挤压模具设计原则1.尺寸精度:铝型材挤压模具设计时要保证挤压后的铝型材尺寸精度。
模具的内芯设计需考虑材料的收缩率和强度,确保挤压后的铝型材尺寸准确。
2.结构合理:铝型材挤压模具设计时应尽量减小模具的重量和尺寸,提高模具的使用寿命。
同时,要增加模具的刚度和强度,确保在挤压过程中不会变形或断裂。
3.表面质量:铝型材挤压模具的表面光洁度直接影响到挤压后的铝型材表面质量。
因此,在设计模具壳和模具翼时应注意表面的光洁度,减少表面缺陷。
4.降低生产成本:铝型材挤压模具的设计应考虑降低生产成本。
例如,可以采用可更换模具芯片的设计来替换整个模具,从而降低维修和更换模具的成本。
四、铝型材挤压模具制造工艺1.材料选择:铝型材挤压模具一般选用高硬度、高强度的工具钢,如优质合金工具钢或高速工具钢等。
2.预先加工:将选定的工具钢进行粗加工,包括锻造、切割、拉伸等工艺,将模具的初始形状制作出来。
3.精密加工:通过数控加工等精密加工技术,对模具进行精细加工,包括车削、铣削、镗削、磨削等工艺,保证模具的尺寸精度和表面质量。
4.表面处理:对模具进行表面处理,如热处理、氮化等工艺,提高模具的硬度和耐磨性。
5.装配调试:将各个组成部分进行装配,并进行调试,保证模具的合理性和可靠性。
五、铝型材挤压模具的维护与保养1.清洁:定期对铝型材挤压模具进行清洁,除去铝屑和污垢,保持模具的清洁度。
2.润滑:对铝型材挤压模具的摩擦部位进行润滑,减少磨损和摩擦力,并延长模具的使用寿命。
3.定期检查:定期对铝型材挤压模具进行检查,发现问题及时修理,确保模具的正常使用。
4.储存:将不使用的铝型材挤压模具储存到干燥、防尘的环境中,避免受潮和污染。
六、铝型材挤压模具的发展趋势1.高精度:随着制造业对产品精度要求的提高,铝型材挤压模具的精度也将不断提高。
2.高效率:铝型材挤压模具的开发将更加注重提高生产效率和降低能耗。
挤压铝型材 截面设计
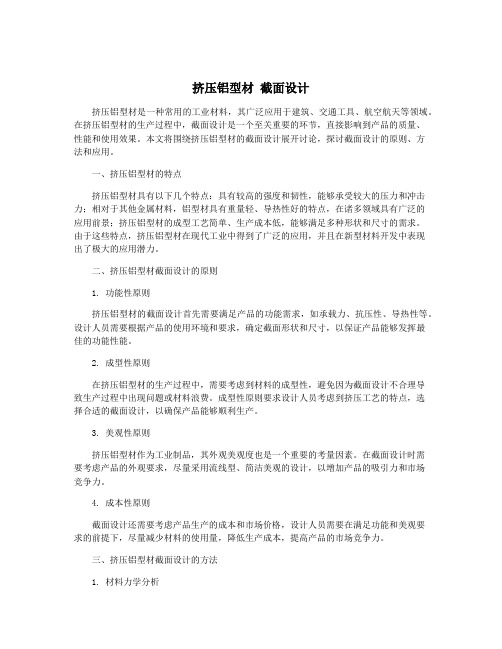
挤压铝型材截面设计挤压铝型材是一种常用的工业材料,其广泛应用于建筑、交通工具、航空航天等领域。
在挤压铝型材的生产过程中,截面设计是一个至关重要的环节,直接影响到产品的质量、性能和使用效果。
本文将围绕挤压铝型材的截面设计展开讨论,探讨截面设计的原则、方法和应用。
一、挤压铝型材的特点挤压铝型材具有以下几个特点:具有较高的强度和韧性,能够承受较大的压力和冲击力;相对于其他金属材料,铝型材具有重量轻、导热性好的特点,在诸多领域具有广泛的应用前景;挤压铝型材的成型工艺简单、生产成本低,能够满足多种形状和尺寸的需求。
由于这些特点,挤压铝型材在现代工业中得到了广泛的应用,并且在新型材料开发中表现出了极大的应用潜力。
二、挤压铝型材截面设计的原则1. 功能性原则挤压铝型材的截面设计首先需要满足产品的功能需求,如承载力、抗压性、导热性等。
设计人员需要根据产品的使用环境和要求,确定截面形状和尺寸,以保证产品能够发挥最佳的功能性能。
2. 成型性原则在挤压铝型材的生产过程中,需要考虑到材料的成型性,避免因为截面设计不合理导致生产过程中出现问题或材料浪费。
成型性原则要求设计人员考虑到挤压工艺的特点,选择合适的截面设计,以确保产品能够顺利生产。
3. 美观性原则挤压铝型材作为工业制品,其外观美观度也是一个重要的考量因素。
在截面设计时需要考虑产品的外观要求,尽量采用流线型、简洁美观的设计,以增加产品的吸引力和市场竞争力。
4. 成本性原则截面设计还需要考虑产品生产的成本和市场价格,设计人员需要在满足功能和美观要求的前提下,尽量减少材料的使用量,降低生产成本,提高产品的市场竞争力。
三、挤压铝型材截面设计的方法1. 材料力学分析在进行截面设计之前,首先需要进行材料力学分析,确定产品在使用过程中受到的力学性能要求,如承载力、弯曲强度、抗压性等。
仅在了解了产品受力情况的基础上,才能够进行合理的截面设计。
2. 三维建模设计采用计算机辅助设计(CAD)软件进行三维建模设计,模拟产品的外观和结构,快速、直观地展现产品的设计思路,以及对截面设计进行初步方案。
挤压铝型材教学设计方案
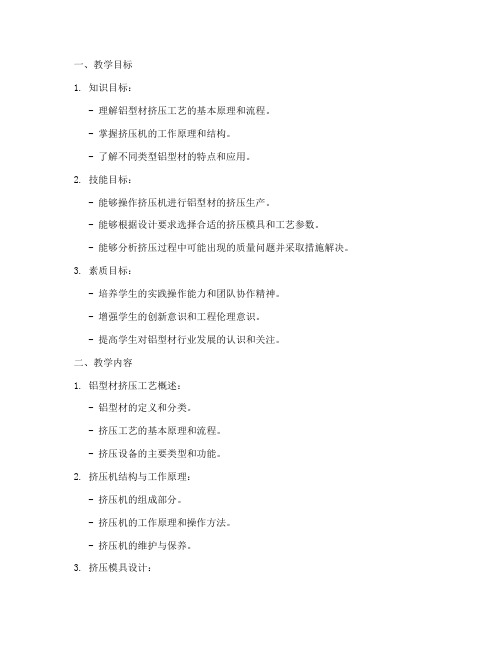
一、教学目标1. 知识目标:- 理解铝型材挤压工艺的基本原理和流程。
- 掌握挤压机的工作原理和结构。
- 了解不同类型铝型材的特点和应用。
2. 技能目标:- 能够操作挤压机进行铝型材的挤压生产。
- 能够根据设计要求选择合适的挤压模具和工艺参数。
- 能够分析挤压过程中可能出现的质量问题并采取措施解决。
3. 素质目标:- 培养学生的实践操作能力和团队协作精神。
- 增强学生的创新意识和工程伦理意识。
- 提高学生对铝型材行业发展的认识和关注。
二、教学内容1. 铝型材挤压工艺概述:- 铝型材的定义和分类。
- 挤压工艺的基本原理和流程。
- 挤压设备的主要类型和功能。
2. 挤压机结构与工作原理:- 挤压机的组成部分。
- 挤压机的工作原理和操作方法。
- 挤压机的维护与保养。
3. 挤压模具设计:- 模具的结构和材料选择。
- 模具的设计原则和计算方法。
- 模具的调试与优化。
4. 铝型材挤压工艺参数:- 挤压温度、速度、压力等参数的选择。
- 挤压过程中常见问题的分析和解决方法。
5. 铝型材的应用:- 不同类型铝型材的特点和应用领域。
- 铝型材在建筑、交通运输、电子电器等行业的应用实例。
三、教学方法1. 理论教学:- 讲授法:讲解铝型材挤压工艺的基本知识和原理。
- 案例分析法:通过实际案例讲解挤压模具设计、工艺参数选择等。
2. 实践教学:- 观摩法:组织学生观摩挤压机操作和铝型材挤压过程。
- 实验法:让学生动手操作挤压机,进行铝型材挤压实验。
- 模拟训练法:利用模拟软件进行挤压工艺参数的模拟和优化。
3. 讨论法:- 组织学生讨论挤压过程中可能出现的问题及解决方案。
- 鼓励学生提出创新性观点,分享实践经验。
四、教学评价1. 理论知识考核:- 通过闭卷考试或开卷考试形式,考核学生对铝型材挤压工艺理论知识的掌握程度。
2. 实践操作考核:- 通过现场操作考核,评估学生操作挤压机和解决实际问题的能力。
3. 创新性评价:- 考核学生在实践过程中的创新意识和创新能力。
挤压铝型材模具课程设计

挤压铝型材模具课程设计一、课程目标知识目标:1. 学生能够掌握铝型材挤压模具的基本结构及其工作原理;2. 学生能够理解并描述挤压过程中金属流动特性及对模具设计的影响;3. 学生能够了解并运用模具设计的相关技术参数和标准。
技能目标:1. 学生能够运用CAD软件进行铝型材模具的基本设计;2. 学生能够分析实际工程问题,提出合理的模具设计方案;3. 学生能够通过实验和模拟,对模具设计进行优化和改进。
情感态度价值观目标:1. 学生能够培养对模具设计及制造工作的兴趣,增强工程意识;2. 学生能够认识到模具设计在制造业中的重要性,树立质量意识;3. 学生能够通过团队协作,培养沟通、交流和解决问题的能力。
本课程针对高中年级学生,结合学科知识深度,注重理论联系实际,培养学生实际操作能力。
课程性质为实践性较强的设计课程,要求学生在掌握基础知识的基础上,运用所学技能解决实际问题。
通过本课程的学习,使学生能够达到以上所述的具体学习成果,为后续相关专业课程的学习打下坚实基础。
二、教学内容1. 铝型材挤压模具基础知识- 模具的分类、结构及其工作原理;- 铝型材挤压工艺流程及其对模具的影响;- 模具设计的相关技术参数和标准。
2. 铝型材模具设计方法- CAD软件在模具设计中的应用;- 模具设计的基本原则和步骤;- 模具设计中金属流动分析及优化。
3. 模具设计实例分析- 分析实际工程中的铝型材模具设计案例;- 针对不同类型的铝型材,讨论模具设计的要点和注意事项;- 通过实例,引导学生运用所学知识解决实际问题。
4. 模具设计的实验与模拟- 实验室进行铝型材挤压实验,观察金属流动现象;- 利用模拟软件进行模具设计验证,优化设计方案;- 分析实验与模拟结果,提出改进措施。
教学内容依据课程目标,结合教材相关章节进行组织。
教学进度安排如下:第1周:铝型材挤压模具基础知识学习;第2周:铝型材模具设计方法及CAD软件应用;第3周:模具设计实例分析;第4周:模具设计的实验与模拟。
铝型材挤压工艺及模具设计

铝型材挤压工艺及模具设计1. 挤压工艺铝型材挤压是一种利用压力对铝型材进行塑性变形的加工工艺。
其基本工艺是:铝棒坯料通过加热软化后,被压入模头,通过模头出口挤出成需要的截面形状。
铝型材挤压工艺的优点包括:高成形精度、高表面质量、操作简便,高生产效率等等。
2. 模具设计铝型材挤压的模具主要包括模头、辅助金属件、固定板、滑动板、胚料夹持装置等组成。
其中,模头是铝型材挤出的关键装置,包括卡箍板、模板、模板底部垫片、模座、模膜等部分。
模头的最重要的特点是不同形状的铝型材需要不同形状的模头;其次需要各个部位的设计匹配度高,精度要求高。
滑动板和固定板是模具的基础结构,他们需要耐压、耐磨,同时需要精度高、边缘无毛刺。
辅助金属件在滑动板、固定板及模头之间起到了加强固定的作用,除此之外还需要具有良好的导向功能。
2.2. 理论参数的确定合理的选择合适的挤压荷载能够很好的保证挤压过程中的质量,同时也能够最大限度的提高生产效率。
因此,在模具设计阶段,应尽可能的确定相应的理论参数。
此外,应还需根据压力、速度、保压时间等因素来确定合适的机器配置,以及最优的辅助系统。
为了达到最优的效果,这些参数需要经过实验验证。
2.3. 模具材料的选择对于铝型材挤压模具来说,常见的材料包括H13钢、特种合金钢、定向硅钢、硬质合金等材料。
如:H13钢:具有高的耐磨性、硬度和强度,适用于铝型材的大批量生产。
特种合金钢:高抗氧化性、高强度、高磨损性,这些特性使其适用于生产高性能和高质量的铝型材。
硬质合金:它具有高硬度和强度、高耐磨性和高耐蚀性,是生产大规模、高复杂度的模具的首选。
2.4. 设计注意事项在模具设计过程中还需要注意以下问题:1)要防止铝材在挤压过程中发生撕裂断裂,因此要注意模具底部的角度把控2)要避免孔洞过大过小,且要容易拆卸,之所以拆卸是为了清洁铝型材上残余物。
3)在设计过程中,要考虑铝型材的变形,保证材料截面和尺寸的均匀性。
4)在滑动板部位,还需要考虑降低铝型材与模具接触时所产生的不良效果,例如顶出口和顶料等问题。
铝型材挤压模具设计书

铝型材挤压模具设计书一、前言铝型材挤压模具是铝型材生产的核心设备之一,其设计质量直接影响到产品的质量和生产效率。
铝型材挤压模具的设计书是非常重要的,它不仅包含了模具的结构、尺寸、工艺等方面的信息,还需要考虑到生产实际情况和经济效益等因素。
本文将从以下几个方面介绍铝型材挤压模具设计书。
二、设计书内容1. 模具结构模具结构是指模头、挤出孔、定位销、导向柱等部件的组合方式。
在设计时需要考虑到产品形状、尺寸和特殊要求等因素,以确定最合适的结构方案。
2. 尺寸参数尺寸参数是指模具各部件的尺寸大小,包括了长度、宽度、高度等方面。
在设计时需要根据产品要求和加工工艺等因素进行计算,以确保各部件尺寸精确合理。
3. 工艺流程工艺流程是指产品从原材料到成品的加工过程,在设计时需要考虑到每个环节所需的设备和工序,并根据实际情况进行调整和优化。
4. 材料选用材料选用是指模具各部件所使用的材料,需要根据模具的使用环境、产品要求和经济效益等因素进行选择。
5. 加工精度加工精度是指模具各部件的加工精度要求,包括了尺寸精度、表面光洁度等方面。
在设计时需要考虑到加工设备和技术水平等因素,以确保模具的质量和生产效率。
6. 维护保养维护保养是指模具在使用过程中需要进行的维护保养工作,包括了清洗、润滑、更换零部件等方面。
在设计时需要考虑到维护保养的便捷性以及对生产效率的影响。
三、设计书编写步骤1. 确定产品要求和加工工艺在编写设计书之前,需要明确产品形状、尺寸和特殊要求等方面的信息,并确定加工工艺流程。
2. 设计模具结构根据产品要求和加工工艺流程,确定最合适的模具结构方案,并进行初步设计。
3. 计算尺寸参数根据初步设计确定各部件尺寸大小,并进行计算和校验。
4. 选择材料根据模具使用环境、产品要求和经济效益等因素,选择合适的材料。
5. 确定加工精度要求根据产品要求和加工工艺流程,确定模具各部件的加工精度要求。
6. 考虑维护保养在设计时需要考虑到模具的维护保养便捷性,以及对生产效率的影响。
铝合金挤压车间课程设计

一、铝合金挤压车间设计(自己选择合金牌号,和规格)1.产品的确定根据市场需求及应用背景,选择铝合金的种类(如建筑用铝合金型材为6063),产品的规格,管、棒、型、线材,以及大致的市场需求量,设计产能。
2.工艺流程的确定根据产品的选择制定详细的生产工艺流程。
铸锭—车皮(工厂里有扒皮机)—加热—挤压(镦粗、穿孔、挤压)—挤压制品风冷或水冷—进行拉矫—锯切定尺—部分产品固溶淬火(需要淬火炉)—部分产品人工时效—表面处理—包装—出厂。
3.设备的选择根据工艺流程及产品的特点、所需要的挤压比、产品的变形抗力选择挤压机的类型(正向或是反向),并根据挤压机特点计算所需挤压机的吨位、挤压筒直径长度等(可以留出一定余量)。
根据产品所需的工艺特点(是否需要穿水冷却,是否需要拉矫,定尺,固溶时效等)选择与挤压机配套的辅助设备(如模具加入炉,铸锭加热炉,挤压见牵引装置,冷床,拉矫机,淬火炉,时效炉,定尺锯等),还应考虑车间的辅助原件,天车、机加车间,办公室,卫生间等。
4.成本核算根据工作时间以及挤压速度,产品横截面,计算挤压机的年产量,计算挤压车间的年产量,成品率,并结合设备折旧对产品的成本进行核算。
二、铝合熔铸压车间设计1.熔铸产品规格及铸造方式的确定根据挤压机,挤压筒外径设计铸锭尺寸,根据挤压产品的规格,产量确定熔铸车间的产品规格、产量。
并选择铸造方式(竖直铸造,还是水平铸造,几根几流?)。
2.工艺流程的确定依据产品的规格尺寸制定详细的工艺流程,主要包括熔化-加料-成分确定-除气-静止—扒渣—炉外精炼—浇铸—均火—锯切等。
3.熔铸设备的确定根据工艺选择相应的设备,熔炼炉,除气机,均火,锯切等设备。
以及天车,机械加工车间,办公室等设施。
主要包括熔炼炉的加热方式、吨位、熔化时间,最高加热温度等参数(还应考虑是否需要附加搅拌装置)。
铸造机的牵引方式(主要有丝杠、钢丝绳、液压型),考虑所需的成本。
均火炉的尺寸,控温范围、加热速度等。
铝型材挤压车间工艺设计

一、课程设计题目:年产13580吨铝型材挤压车间工艺设计二、课程设计绪论随着市场经济的发展,各种新型的高科技建筑材料相继出现,所有的基础工程均需要大量的建筑,需要大量门窗和建筑材料,而铝及其铝合金在其中占有重要的地位。
铝合金型材具有强度高、重量轻、稳定性强、耐腐蚀性强、可塑性好、变形量小、无毒无污染、防火性强、回收性好、可回炉重炼、使用寿命长(可达50—100年)等特点。
多年来世界各国均采用6063铝合金(铝合金近百种)做为门窗框架。
主要是因为该金属表面阳极氧化效果好,开始阳极氧化是白色,后进一步改变电解质才达到古铜色,这两种主体颜色在国内用了十多年。
铝材在挤压过程中,如挤压模具不是很好或模具挤压铝材过多,铝材表面会产生挤压痕,用手可能触摸到铝材表面不平,因此,在现代化大生产中实施挤压加工技术,其成败的关键是模具设计,事关产品的质量、成本。
在车间设计的过程中应考虑到的因素包括:产品的型号、模孔数的确定、选择挤压机、铸锭的选用、年产量、年水电费、设备投资费、人工费等等。
其中,选择挤压机是一个最核心的问题,具体可见设计步骤。
三、课程设计分析这次的设计任务是设计一个年产量不少于5000吨的铝型材挤压车间,生产的产品有:窗帘导轨、卷闸、纱窗铝合金型材,汽车装饰铝合金型材,90系列推拉窗等。
挤压制品所用的材料是6063合金。
1、6063合金化学成分及性能表1:6063合金化学成份及性能532、产品的截面图及主要尺寸表2:产品截面图形及主要尺寸型号 D302、0.877 kg/mH110、1.524 kg/mC522、0.905 kg/m截 面 图 形 及 主 要 尺 寸型号BC6257、0.318 kg/mH103、0.406 kg/mAT4047、0.639 kg/m截 面 图 形 及 主 要 尺 寸型号 H209、0.284 kg/m H202、0.448 kg/m截 面 图 形 及 主 要 尺 寸3、产品的主要常数表3:产品代号参数其中:单位重量是表2给出的;外接圆直径是通过AUTO CAD 模孔设计时测出的;截面积=单位重量×1000/铝型材的密度,密度取2.69千克/立方分米;模孔面积=截面积×(1+1.5%);模孔数本次设计可以单孔的都单孔,除非单孔不符合挤压机的选择原则。
铝合金型材的挤压生产设计

模子内型尺寸的确定 挤压比λ=32.2<λmax=82,故采用单孔挤压即可 确定模孔尺寸: 型材外形尺寸公式:Ak=Am×(1+C1)+△1 壁厚尺寸公式: Ak=Am+C2+△2 Ak-----------------------模孔实际尺寸 Am----------------------型材名义尺寸 C1 C2----------------------欲量系数,铝合金外形尺寸取0.010~0.017,壁厚尺寸 取0.05~0.15,本次设计正偏差不计,故预量系数取大值0.017,0.15
铝合金型材加工通常采用热挤压,这是因为热挤压时,金属进行充 分的再结晶,消除内应力,不产生加工硬化;金属或合金的塑性好,可 以采用大变形量;金属的变形抗力降低,所需的挤压机吨位可以减小。 此外热挤压工艺比较简单,一般是一次挤压成形,加工工序少,生产效 率比模锻高 另外,考虑到挤压断面较为复杂且不对称,同时也为了降低挤压 力,减小变形区,提高流动的均匀性,减少挤压缩尾和压余,选 用反挤压加工。
孔形在模子断面位置的确定
模孔几何中心的求解
S1 X 0
S2 0
S3 4.792
S4 -4.904
S5 -5
Y
21
9.5
4.792
4.904
1
模孔实际加工中心应向左下方偏移 一定距离,薄壁中心位于(-5,1), 兼顾重心位置及增加薄壁处金属流 动性,不妨取上述两点中点(1.4392,3.025)为模孔加工中心。
△1 △2----------------------型材外形尺寸和计算
6.15 4.15
15.26
40.7
30.5
L1=40×1.017=40.7 L2=30×1.017=30.5 D=2+0.15=2.15 H=25×1.017=25.43 h=15×1.017=15.26 R1=13×1.017=13.22 R2=12.5×1.017=12.71 a=4×0.15=4.15 b=6+0.15=6.15
铝型材挤压模具设计课件

以便于管理和使用。
(3)模具外形尺寸标准化和系列化
四、挤压模具设计应考虑的因素
模子设计者确定的要素 模子制造者确定的因素 挤压生产者确定的因素 在设计前,拟定合理的工艺流程和选择最佳的工艺 参数,综合分析影响模具效果的各种因素,是合理
设计挤压模具的必要和充分条件。
五、模具设计的原则与步骤
确定设计模腔参数
一般平面模 舌型模和平面分流
六、模具设计的技术条件及基本要求
有适中而均匀的硬度
有足够高的制造精度
有足够低的表面粗糙度
有良好的对中性、平行度、直线度和垂直度
模具无内部缺陷
不得出现棱角
七、铝型材挤压模具的种类及组装形式
1、挤压工具分类
a)大型基本挤压工具 b)模具 c)辅助工具
2、挤压模具分类及特点
定义:
模子轴线与其工作端面所构成的夹角
模角α的特点及作用
a)平模的模角α等于90°——较大的死区,阻止铸锭表面的 杂质、缺陷、氧化皮等流到制品的表面;某些易在死区产 生裂纹与断裂的金属与合金,表面分层、起皮和小裂纹 a)平模挤压消耗挤压力大,模具易变形,甚至压塌 b)锥形模,减小挤压力 c)条件 d)摩擦力
⑥挤压力的大小 ⑦模具的弹性变形情况
A=A。+M+[Ky+Kp+Kr]A。
4、合理调整金属的流动速度
①每一个质点应以相通的速度流出模孔 ②尽量采用多孔对称排列 ③中心很远的部分可采用促流角,或采用导料锥来加速金属的流动 ④阻碍角 ⑤工艺平衡孔,工艺余量,或者采用前室模、导流模
5、保证足够的模具强度
八、设计实例
设计方案
尺寸
热处理 精度
制造工艺流程
车加工 铣加工取石墨电极时, 不能有疏松和夹杂 等缺陷
(完整版)挤压铝型材毕业课程设计

(完整版)挤压铝型材毕业课程设计一. 题目:铝合金型材挤压工艺及模具设计二. 设计基本内容:设计一件实心型材制品和一件空心型材制品的工艺工艺过程及模具设计,包括挤压工艺参数,模具结构,制造工艺等要求三. 完成后应缴的资料:课程设计说明书一份实心型材模零件图空心型材模上模零件图空心型材模下模零件图空心型材模装配图四. 设计完成期限:指导老师_______签发日期___________教研室主任_______批准日期___________课程设计评语:成绩:设计指导教师______________年_____月____日目录一、绪论 (4)二、总设计过程概论 (7)2.1挤压工艺流程 (7)2.2挤压工艺条件 (7)三、实心型材模设计 (9)3.1所要设计的实心型材制品 (9)3.2选坯和选设备 (10)3.3挤压力的计算 (11)3.4实心型材模具体结构设计 (12)3.5.实心模尺寸数据设计 (13)四、空心型材模设计 (18)4.1所要设计的制品 (18)4.2选坯和选设备 (18)4.3挤压力的计算 (19)4.4模组及模子外形尺寸确定 (20)4.5组合模相关参数的确定 (20)4.6 模子内形尺寸的确定 (23)4.7模孔工作带长度h g的确定 (24)4.8模芯的设计 (24)4.9上模凸台设计 (24)4.10定位销,螺钉 (24)4.11模子强度校核 (25)4.12零件图装配图 (26)五、总结与体会 (26)参考文献…………………………………………………26一. 绪论近20年来,随着建筑行业的高速发展,我国民用建筑铝型材工业也从无到有,从弱到强地迅猛前进。
至今,广东省的建筑铝型材产品已约占全国的三分之二左右,铝型材的生产能力超过社会的需求,如何提高产品质量,降低成本是取得市场竞争胜利的关键环节。
铝合金型材具有强度高、重量轻、稳定性强、耐腐蚀性强、可塑性好、变形量小、无污染、无毒、防火性强,使用寿命长(可达50—100年),回收性好,可回炉重炼。
挤压铝型材 截面设计
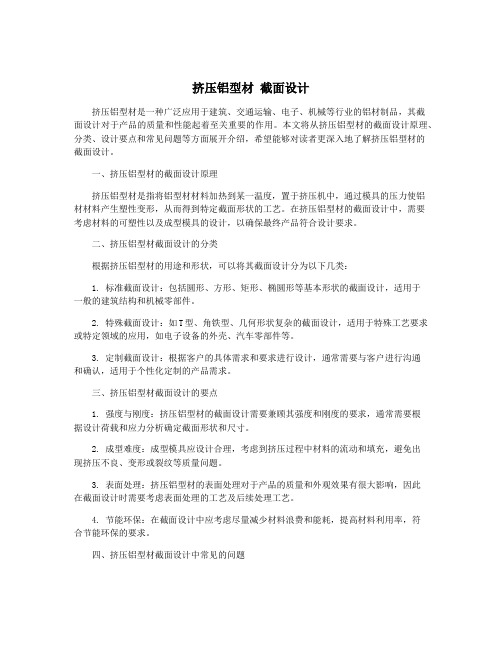
挤压铝型材截面设计挤压铝型材是一种广泛应用于建筑、交通运输、电子、机械等行业的铝材制品,其截面设计对于产品的质量和性能起着至关重要的作用。
本文将从挤压铝型材的截面设计原理、分类、设计要点和常见问题等方面展开介绍,希望能够对读者更深入地了解挤压铝型材的截面设计。
一、挤压铝型材的截面设计原理挤压铝型材是指将铝型材材料加热到某一温度,置于挤压机中,通过模具的压力使铝材材料产生塑性变形,从而得到特定截面形状的工艺。
在挤压铝型材的截面设计中,需要考虑材料的可塑性以及成型模具的设计,以确保最终产品符合设计要求。
二、挤压铝型材截面设计的分类根据挤压铝型材的用途和形状,可以将其截面设计分为以下几类:1. 标准截面设计:包括圆形、方形、矩形、椭圆形等基本形状的截面设计,适用于一般的建筑结构和机械零部件。
2. 特殊截面设计:如T型、角铁型、几何形状复杂的截面设计,适用于特殊工艺要求或特定领域的应用,如电子设备的外壳、汽车零部件等。
3. 定制截面设计:根据客户的具体需求和要求进行设计,通常需要与客户进行沟通和确认,适用于个性化定制的产品需求。
三、挤压铝型材截面设计的要点1. 强度与刚度:挤压铝型材的截面设计需要兼顾其强度和刚度的要求,通常需要根据设计荷载和应力分析确定截面形状和尺寸。
2. 成型难度:成型模具应设计合理,考虑到挤压过程中材料的流动和填充,避免出现挤压不良、变形或裂纹等质量问题。
3. 表面处理:挤压铝型材的表面处理对于产品的质量和外观效果有很大影响,因此在截面设计时需要考虑表面处理的工艺及后续处理工艺。
4. 节能环保:在截面设计中应考虑尽量减少材料浪费和能耗,提高材料利用率,符合节能环保的要求。
四、挤压铝型材截面设计中常见的问题1. 挤压变形不均匀:可能是由于成型模具设计不合理、挤压过程中材料流动不畅或加热温度不足等原因导致的,需要通过优化模具结构、加热控制和挤压工艺等手段解决。
2. 截面尺寸不准确:可能是由于挤压机调整不当、模具磨损或变形、材料弹性变形等原因导致的,需要加强挤压机和模具的维护保养,优化工艺参数。
挤压铝型材 截面设计
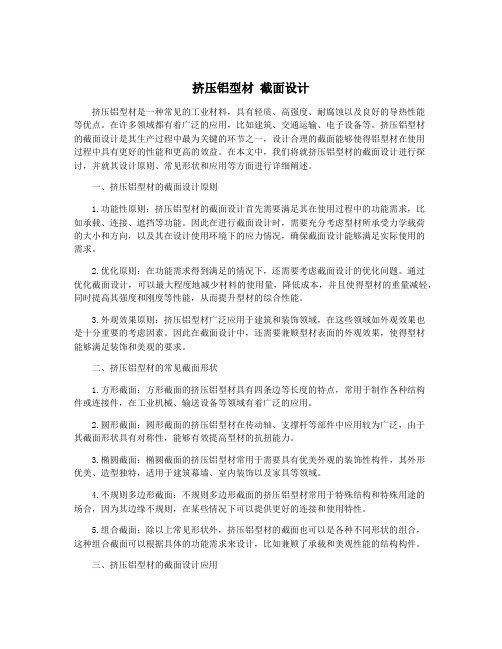
挤压铝型材截面设计挤压铝型材是一种常见的工业材料,具有轻质、高强度、耐腐蚀以及良好的导热性能等优点。
在许多领域都有着广泛的应用,比如建筑、交通运输、电子设备等。
挤压铝型材的截面设计是其生产过程中最为关键的环节之一,设计合理的截面能够使得铝型材在使用过程中具有更好的性能和更高的效益。
在本文中,我们将就挤压铝型材的截面设计进行探讨,并就其设计原则、常见形状和应用等方面进行详细阐述。
一、挤压铝型材的截面设计原则1.功能性原则:挤压铝型材的截面设计首先需要满足其在使用过程中的功能需求,比如承载、连接、遮挡等功能。
因此在进行截面设计时,需要充分考虑型材所承受力学载荷的大小和方向,以及其在设计使用环境下的应力情况,确保截面设计能够满足实际使用的需求。
2.优化原则:在功能需求得到满足的情况下,还需要考虑截面设计的优化问题。
通过优化截面设计,可以最大程度地减少材料的使用量,降低成本,并且使得型材的重量减轻,同时提高其强度和刚度等性能,从而提升型材的综合性能。
3.外观效果原则:挤压铝型材广泛应用于建筑和装饰领域,在这些领域如外观效果也是十分重要的考虑因素。
因此在截面设计中,还需要兼顾型材表面的外观效果,使得型材能够满足装饰和美观的要求。
二、挤压铝型材的常见截面形状1.方形截面:方形截面的挤压铝型材具有四条边等长度的特点,常用于制作各种结构件或连接件,在工业机械、输送设备等领域有着广泛的应用。
2.圆形截面:圆形截面的挤压铝型材在传动轴、支撑杆等部件中应用较为广泛,由于其截面形状具有对称性,能够有效提高型材的抗扭能力。
3.椭圆截面:椭圆截面的挤压铝型材常用于需要具有优美外观的装饰性构件,其外形优美、造型独特,适用于建筑幕墙、室内装饰以及家具等领域。
4.不规则多边形截面:不规则多边形截面的挤压铝型材常用于特殊结构和特殊用途的场合,因为其边缘不规则,在某些情况下可以提供更好的连接和使用特性。
5.组合截面:除以上常见形状外,挤压铝型材的截面也可以是各种不同形状的组合,这种组合截面可以根据具体的功能需求来设计,比如兼顾了承载和美观性能的结构构件。
挤压课程设计湖南工业大学

挤压课程设计湖南工业大学一、课程目标知识目标:1. 学生能够掌握挤压工艺的基本概念、原理及在工业生产中的应用。
2. 学生能够理解并描述挤压过程中材料性质、工艺参数对产品质量的影响。
3. 学生能够掌握挤压设备的基本构造、工作原理及操作方法。
技能目标:1. 学生能够运用所学知识,分析实际工业生产中的挤压工艺问题,并提出合理的解决方案。
2. 学生能够熟练操作挤压设备,完成给定材料的挤压实验,并对结果进行分析。
3. 学生能够运用专业软件或工具进行挤压工艺参数的优化设计。
情感态度价值观目标:1. 学生通过学习挤压课程,培养对制造业的热爱,增强工程意识。
2. 学生在学习过程中,培养团队协作、沟通交流的能力,提高解决问题的自信心。
3. 学生能够关注挤压技术在工业发展中的应用,认识到其在国家经济建设中的重要性。
课程性质:本课程为专业课,以理论教学与实践操作相结合的方式进行,旨在培养学生的实际操作能力和工程素养。
学生特点:学生为湖南工业大学相关专业的本科生,具备一定的专业基础知识,学习兴趣较高,但实践经验不足。
教学要求:结合课程性质和学生特点,注重理论与实践相结合,提高学生的实际操作能力和解决实际问题的能力。
通过课程学习,使学生能够达到上述具体的学习成果。
后续教学设计和评估将以此为基础,确保课程目标的实现。
二、教学内容1. 挤压工艺基本原理:包括挤压的定义、分类,金属塑性变形原理,挤压过程中的应力与应变分析。
教材章节:第1章 挤压工艺概述2. 挤压设备与工艺参数:介绍挤压设备的基本构造、工作原理,挤压工艺参数的设定与调整。
教材章节:第2章 挤压设备与工艺参数3. 挤压过程中的材料变形行为:分析不同材料在挤压过程中的变形行为,探讨材料性质对挤压产品质量的影响。
教材章节:第3章 挤压过程中的材料变形行为4. 挤压工艺在实际应用中的案例分析:结合实际工业生产案例,分析挤压工艺在制造业中的应用。
教材章节:第4章 挤压工艺在实际应用中的案例分析5. 挤压工艺参数优化设计:运用专业软件或工具,进行挤压工艺参数的优化设计。
铝合金型材挤压模具设计和维修

NG ─ 轻易造成流量集中到 料厚旳底部迅速出料;細薄 旳葉片供料不足無法出料, 最後因不能同時擠出而導致 塞模。嚴重時鋼料扭曲變形 或斷裂。
OK ─ 底部及中間減少供料, 兩端加大供料空間,能够調整 流量往兩邊分佈,以取得整體 均勻擠出旳效果。
設計者可控制旳原因-3
3) 擺放位置 模具擠壓旳受力會由中心往外遞減,所以設計一開始就要 考量擺放位置,使得供料流往細薄處,以取得 ─ 控制尺寸及形狀。模面(Die)為實際承受擠壓力 及培林所在,在整套模中應選用最佳旳鋼料。
取段原則有下列主要5點: 1) 由培林最短處開始設計,一般在最薄料旳端點處
最小厚度(0.5mm) ≦ 培林 ≦ 最大厚度*3 (25mm↓) 2) 由外向中心設計
最外圍因壓力最小一般進料不足,所以要先考慮外圍旳取段 3) 配合模罩旳流量控制
60% 80% 100%
NG ─ 料厚處太近中心 OK ─ 料薄處先受力 造成立即擠出;料薄處 供料,易取得與料厚 供料不足易導致塞模。 處同時出料旳均衡。
設計者可控制旳原因-4
4) 朝向方位 料型旳朝向主要在考量擠出成形後,是否會磨損客戶需要旳 主要面而作轉向調整。
4-1) 底平面一般是接觸熱源旳 主要面,改為葉片朝下, 可预防底面磨損∕碰傷。
焊补螺孔
修模技巧11—返修加工2
局部放大
放电加工后
修模技巧12—存料室打光面
处理多孔料长短(5:4以内),或开脚问题
影響擠型模旳原因
模具設計者当然要分配好流量控制,但應進一步了解各項 影響模具性能表現旳原因,以達到設計與實際擠出相符合 旳理想。
影響擠型模性能表現旳原因,可分下列4大項來說明:
❖ 設計者可控制旳原因
修模─試模後依據料頭旳快慢/偏轉程度,進行修改 模罩/培林作最佳化細部微調,影響度30%。
铝型材挤压模具设计书
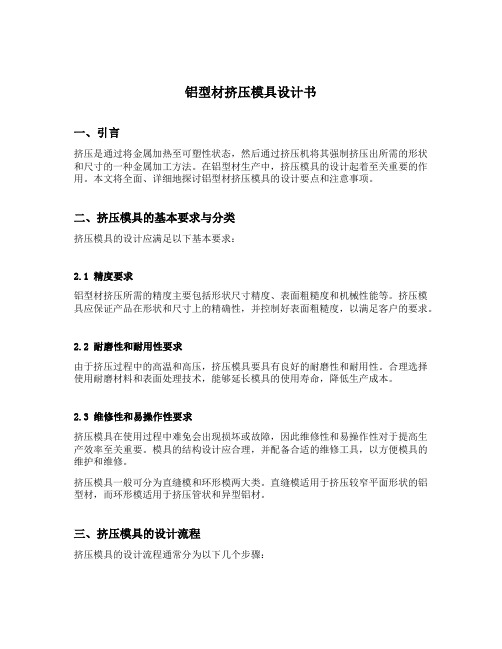
铝型材挤压模具设计书一、引言挤压是通过将金属加热至可塑性状态,然后通过挤压机将其强制挤压出所需的形状和尺寸的一种金属加工方法。
在铝型材生产中,挤压模具的设计起着至关重要的作用。
本文将全面、详细地探讨铝型材挤压模具的设计要点和注意事项。
二、挤压模具的基本要求与分类挤压模具的设计应满足以下基本要求:2.1 精度要求铝型材挤压所需的精度主要包括形状尺寸精度、表面粗糙度和机械性能等。
挤压模具应保证产品在形状和尺寸上的精确性,并控制好表面粗糙度,以满足客户的要求。
2.2 耐磨性和耐用性要求由于挤压过程中的高温和高压,挤压模具要具有良好的耐磨性和耐用性。
合理选择使用耐磨材料和表面处理技术,能够延长模具的使用寿命,降低生产成本。
2.3 维修性和易操作性要求挤压模具在使用过程中难免会出现损坏或故障,因此维修性和易操作性对于提高生产效率至关重要。
模具的结构设计应合理,并配备合适的维修工具,以方便模具的维护和维修。
挤压模具一般可分为直缝模和环形模两大类。
直缝模适用于挤压较窄平面形状的铝型材,而环形模适用于挤压管状和异型铝材。
三、挤压模具的设计流程挤压模具的设计流程通常分为以下几个步骤:3.1 铝型材挤压工艺分析在开始设计挤压模具之前,需要进行铝型材挤压工艺的分析。
包括材料的选择、预热温度的确定、挤压压力和速度的设定等。
3.2 模具结构设计模具结构设计是挤压模具设计的关键。
需要考虑挤压过程中的应力分布、热传导和冷却等因素,并确定模具的主要结构尺寸。
3.3 模具材料选择挤压模具的材料应具有良好的耐热性、耐磨性和冲击韧性。
常用的模具材料包括高速工具钢、合金工具钢和硬质合金等。
3.4 模具加热与冷却设计为了保证挤压过程的顺利进行,模具需要进行加热和冷却。
合理的加热和冷却设计能够提高铝型材的形状精度和表面质量。
四、挤压模具的制造和调试挤压模具的制造和调试过程中需要注意以下事项:4.1 制造工艺的选择根据不同模具的要求,选择合适的制造工艺,包括数控加工、热处理和表面处理等。