铝型材挤压模具设计及数据库管理系统
铝型材挤压模具自动化立体仓库规划设计与应用

6 . 难 于推 行 现 代 管 理 ,库 存 数 据和 公 司E RP 系 统 无 法 对 接 , 出 入 库 信 息 不 能 及 时 反 馈 到 生 产 、技 术 、 财 务 、 信 息
中枢等部门 。 为 了 解 决 上 述 问题 ,广 东 华 昌铝 厂
1 . 占地 面 积 大 。土 地 利 用 率 低 ,空
吨 。产 品 品 种 有 3 0 0 0 多个 。公司装有 3 6
产 线 模 具 , 具 有 大 幅 度 减 少 用 地 、高
、
和全程 自动 化 、信息化管理。
条挤 压生 产 自动 线 ,过 去 库存 3 万 套 模
具 ,每 天 模 具 最 大 出 入 库 量 为 1 0 3 5 套。
用桥式 起重 机 、叉车或人 工方 式搬运 。
模具原存储 方式
模具的分类、入库、运输 、储存及出入
库 等 工 作 十 分 繁 忙 ,物 流 量 和 劳 动 强 度 特别 大 。 随 着 生 产 规 模 和 产 品 品 种 不 断 扩
2 . 搬 运 工 作 量 及 劳 动 强 度 大 。用 人
展 ,模 具 也 在 不 断 增 加 ,仓 储 面 积 日益
紧 张 ,原 有 的储 存 、供 应 方式 已 不能 适 应 生 产 节 奏 和 管 理 要 求 。 挤 压 模 具 存 存 、取 方 面 遇 到 的 问 题 。 成 为 企 业 进 一 步发 展 的瓶 颈 。
总 体 来 看 ,采 用 平 面 库 存 放 的 方 式
司 承 建 的 铝 型 材 挤 压 模 具 自动 化 立 体 仓 库 ,以 及 “ 长件 成 品库 ” 、 “ 长 件输送
器 合 金 型 材 及 工 业 型 材 的 研 发 设 计 和 生 产基 地 之 一 。到 2 01 4 年 ,该 公 司 的 产 能达到 了1 5 万 吨 以 上 ,产 量 达 到 1 2 . 3 万
薄壁铝型材挤压模具设计和维护

1挤压模具介绍挤压模具结构设计和制造环节较多,包括选材、设计、制造、修模等环节,其成本占到型材挤压生产成本的35%左右。
在型材加工生产中,一般有两种主要挤压方法:分流组合模挤压法和穿孔针挤压法。
前者加工起来简单且成本较低,后者成本高且应用范围较小,在实际型材加工生产中,分流组合模应用更为广泛。
1.1挤压模具的工作条件。
对于大截面复杂型材的挤压成形,挤压难度比较大,对挤压模具的结构与形状要求也很高,特别是对于这种断面形状较复杂,壁厚相差悬殊,断面面积及外接圆大,多腔空心等型材,挤压模具的工作条件变得更加恶劣。
因此,对挤压模具要求较高,主要有如下几个方面:一是高温高压条件下工作;二是要具有较好的抗磨损能力;三是具有很高的强度和韧性,避免在工作中出现应力集中而使模具破坏。
1.2挤压模具的分类。
挤压模具种类很多,根据不同的分类条件可以进行归类。
分类的主要依据有模具结构和模孔压缩区断面外形。
分流组合模在目前是应用最为广泛的一种模具形式,平面分流组合模的组成结构主要包括上模、下模、定位销和联结螺钉四个部分,其工作原理是在一定的挤压力作用下,锅淀通过分流孔被分流成金属流,流经焊合室进行汇集和傅合,最终由模芯和模孔流出,形成具有所要求几何形状的型材产品。
1.3模具的设计步骤。
实际生产中,产品类型、工艺方法、设备和模具结构都是影响模具设计过程的重要因素。
但是在设计过程中,挤压模具模腔的设计一般按照以下步骤进行:1.3.1模腔参数确定和模孔布置。
模腔参数的确定主要根据挤压机、工艺规程和现场工具设备来确定。
模孔布置合理与否直接影响着模具强度,同时影响金属流动的均匀性。
一般在设计过程中,即使非对称的型材也要尽量保证模孔的对称性,同时使其尽量接近中心紧凑一些。
通常情况下,模孔多设置在同心圆上(模孔之间的间距大于30-50mm,模孔距离模具边缘大于25-50mm,模孔与挤压筒边缘的距离大于20-40mm)。
1.3.2设计模孔尺寸。
挤压铝型材模具课程设计

挤压铝型材模具课程设计一、课程目标知识目标:1. 学生能够掌握铝型材挤压模具的基本结构及其工作原理;2. 学生能够理解并描述挤压过程中金属流动特性及对模具设计的影响;3. 学生能够了解并运用模具设计的相关技术参数和标准。
技能目标:1. 学生能够运用CAD软件进行铝型材模具的基本设计;2. 学生能够分析实际工程问题,提出合理的模具设计方案;3. 学生能够通过实验和模拟,对模具设计进行优化和改进。
情感态度价值观目标:1. 学生能够培养对模具设计及制造工作的兴趣,增强工程意识;2. 学生能够认识到模具设计在制造业中的重要性,树立质量意识;3. 学生能够通过团队协作,培养沟通、交流和解决问题的能力。
本课程针对高中年级学生,结合学科知识深度,注重理论联系实际,培养学生实际操作能力。
课程性质为实践性较强的设计课程,要求学生在掌握基础知识的基础上,运用所学技能解决实际问题。
通过本课程的学习,使学生能够达到以上所述的具体学习成果,为后续相关专业课程的学习打下坚实基础。
二、教学内容1. 铝型材挤压模具基础知识- 模具的分类、结构及其工作原理;- 铝型材挤压工艺流程及其对模具的影响;- 模具设计的相关技术参数和标准。
2. 铝型材模具设计方法- CAD软件在模具设计中的应用;- 模具设计的基本原则和步骤;- 模具设计中金属流动分析及优化。
3. 模具设计实例分析- 分析实际工程中的铝型材模具设计案例;- 针对不同类型的铝型材,讨论模具设计的要点和注意事项;- 通过实例,引导学生运用所学知识解决实际问题。
4. 模具设计的实验与模拟- 实验室进行铝型材挤压实验,观察金属流动现象;- 利用模拟软件进行模具设计验证,优化设计方案;- 分析实验与模拟结果,提出改进措施。
教学内容依据课程目标,结合教材相关章节进行组织。
教学进度安排如下:第1周:铝型材挤压模具基础知识学习;第2周:铝型材模具设计方法及CAD软件应用;第3周:模具设计实例分析;第4周:模具设计的实验与模拟。
铝型材挤压工艺及模具设计

铝型材挤压工艺及模具设计1. 挤压工艺铝型材挤压是一种利用压力对铝型材进行塑性变形的加工工艺。
其基本工艺是:铝棒坯料通过加热软化后,被压入模头,通过模头出口挤出成需要的截面形状。
铝型材挤压工艺的优点包括:高成形精度、高表面质量、操作简便,高生产效率等等。
2. 模具设计铝型材挤压的模具主要包括模头、辅助金属件、固定板、滑动板、胚料夹持装置等组成。
其中,模头是铝型材挤出的关键装置,包括卡箍板、模板、模板底部垫片、模座、模膜等部分。
模头的最重要的特点是不同形状的铝型材需要不同形状的模头;其次需要各个部位的设计匹配度高,精度要求高。
滑动板和固定板是模具的基础结构,他们需要耐压、耐磨,同时需要精度高、边缘无毛刺。
辅助金属件在滑动板、固定板及模头之间起到了加强固定的作用,除此之外还需要具有良好的导向功能。
2.2. 理论参数的确定合理的选择合适的挤压荷载能够很好的保证挤压过程中的质量,同时也能够最大限度的提高生产效率。
因此,在模具设计阶段,应尽可能的确定相应的理论参数。
此外,应还需根据压力、速度、保压时间等因素来确定合适的机器配置,以及最优的辅助系统。
为了达到最优的效果,这些参数需要经过实验验证。
2.3. 模具材料的选择对于铝型材挤压模具来说,常见的材料包括H13钢、特种合金钢、定向硅钢、硬质合金等材料。
如:H13钢:具有高的耐磨性、硬度和强度,适用于铝型材的大批量生产。
特种合金钢:高抗氧化性、高强度、高磨损性,这些特性使其适用于生产高性能和高质量的铝型材。
硬质合金:它具有高硬度和强度、高耐磨性和高耐蚀性,是生产大规模、高复杂度的模具的首选。
2.4. 设计注意事项在模具设计过程中还需要注意以下问题:1)要防止铝材在挤压过程中发生撕裂断裂,因此要注意模具底部的角度把控2)要避免孔洞过大过小,且要容易拆卸,之所以拆卸是为了清洁铝型材上残余物。
3)在设计过程中,要考虑铝型材的变形,保证材料截面和尺寸的均匀性。
4)在滑动板部位,还需要考虑降低铝型材与模具接触时所产生的不良效果,例如顶出口和顶料等问题。
铝型材挤压成型数值模拟及优化设计
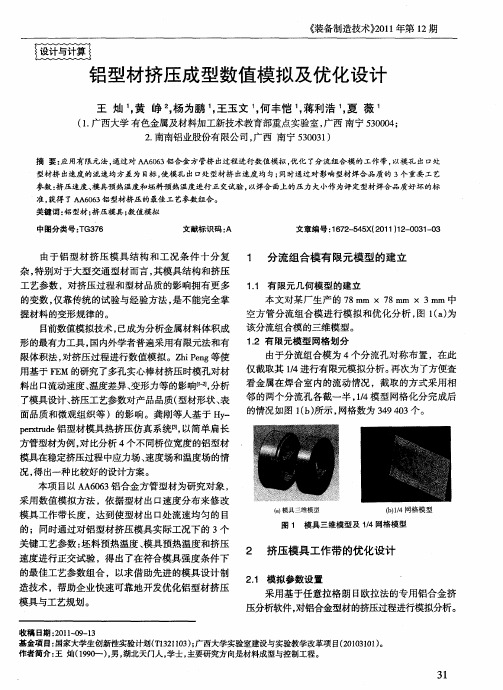
一 一
( 模具三维模型 a ) (l b/ ) 4网格模 型
图 1 模具 三维模 型及 14网格模型 /
关键工艺参数 : 坯料 预热温度 、 模具预热温度 和挤压 速度进行正交试验 ,得 出了在符合模具强度条件下 的最佳工艺参数组合 ,以求借 助先进的模具设计 制 造技术 ,帮助企业快速可靠地 开发优化铝型材挤压 模具与工艺规划。
表 2 试验方 案结果表
L 3一 l _ j
( 修 改后的工作带长度 a ) ) 出口速度分 布图 型材
图 3 修改后工作带设计 与型材 出口速度分布 图 3 2
《 装备制造技术)0 年第 l 期 21 1 2
32 虚拟 试 验结 果分 析 .
在满足模具挤压强度条件下 ,焊合室 内焊合 面 5 结束语
4 实验验证
生产试模 ,有效地提高了生产效率 ,降低 了生产成 本, 对生产实践有着重要的指导意义。
在原始工作带和工艺参数 的情下 ,进行第一 参考文献 : 次试模挤压 , 结果挤出型材 出现弯曲、 扭拧 、 波浪 、 麻 点等缺陷 ,有些位置挤 出后略向上翘 ,且上部有缩 口。通过对 比分析结果 , 发现上翘部位都在虚拟模拟
() a原工作带长度
一
( ) 出 口速度分布图像 b 型材
提高成品率 和生产率 的要求。针对该铝合金方 管型 材对焊合 品质要求较高 的情况 ,为 了获得其挤压 的
最佳温度 和速度参数 ,本文采用正交试验的方法[ 4 】 , 通过考察各组参数组合下 ,分 流组合模焊合 室内的 压力大小 , 来获得最佳挤压工艺参数。 选取 的 3 个因素为 : 坯料温度 、 模具温度和挤压 速度 。
Eq i me t u p n Ma u a t n e h oo y No 1 , 0 1 n f cr g T c n lg . 2 2 1 i
铝型材挤压模具讲解

铝型材挤压模具讲解一、铝型材挤压模具的基本概念1. 定义•铝型材挤压模具是在铝型材挤压生产过程中,用于将加热后的铝坯料通过挤压机的压力作用,使其通过特定形状的模孔,从而形成所需铝型材截面形状的工具。
例如,当需要生产一种带有多个中空腔室的复杂铝型材,如建筑用的隔热断桥铝型材时,就需要专门设计的挤压模具来实现。
2. 重要性•它直接决定了铝型材的形状、尺寸精度和表面质量。
一个设计良好、制造精确的挤压模具能够生产出高质量、符合标准的铝型材。
反之,如果模具存在缺陷,如模孔形状不准确或者表面粗糙度不符合要求,那么生产出来的铝型材可能会出现尺寸偏差、表面缺陷等问题,从而影响其在建筑、航空航天等各个领域的应用。
二、铝型材挤压模具的分类1. 按结构分类•平面分流模•这种模具主要用于生产空心铝型材。
它的特点是在模具内部设有分流桥和分流孔,铝坯料在挤压时先通过分流孔被分成几股金属流,然后在模芯的作用下重新汇合,形成空心型材的形状。
例如,在生产空调用的铝制散热管型材时,平面分流模能够很好地控制金属流动,保证型材的壁厚均匀性。
•实心模•实心模相对简单,主要用于生产实心铝型材。
它只有一个模孔,铝坯料直接通过这个模孔挤出形成所需的实心型材形状。
像一些简单的建筑用铝棒材或者工业用的实心铝型材零部件,就可以使用实心模进行生产。
2. 按用途分类•通用模具•通用模具适用于生产多种规格相近的铝型材。
这类模具的设计具有一定的通用性,可以通过调整一些参数,如挤压速度、模具温度等,来生产不同尺寸但形状相似的型材。
例如,在一些小型铝型材加工厂,为了降低成本,可能会使用通用模具来生产多种类型的建筑装饰用铝型材。
•专用模具•专用模具是为特定的铝型材产品专门设计制造的。
由于是针对某一特定型材的形状、尺寸和性能要求而设计,所以其生产的型材精度和质量更高。
比如航空航天领域中使用的一些特殊形状和高性能要求的铝型材,就需要专门定制的专用模具。
三、铝型材挤压模具的设计要点1. 型材截面分析•在设计模具之前,首先要对铝型材的截面形状进行详细分析。
铝型材挤压模具设计课件

以便于管理和使用。
(3)模具外形尺寸标准化和系列化
四、挤压模具设计应考虑的因素
模子设计者确定的要素 模子制造者确定的因素 挤压生产者确定的因素 在设计前,拟定合理的工艺流程和选择最佳的工艺 参数,综合分析影响模具效果的各种因素,是合理
设计挤压模具的必要和充分条件。
五、模具设计的原则与步骤
确定设计模腔参数
一般平面模 舌型模和平面分流
六、模具设计的技术条件及基本要求
有适中而均匀的硬度
有足够高的制造精度
有足够低的表面粗糙度
有良好的对中性、平行度、直线度和垂直度
模具无内部缺陷
不得出现棱角
七、铝型材挤压模具的种类及组装形式
1、挤压工具分类
a)大型基本挤压工具 b)模具 c)辅助工具
2、挤压模具分类及特点
定义:
模子轴线与其工作端面所构成的夹角
模角α的特点及作用
a)平模的模角α等于90°——较大的死区,阻止铸锭表面的 杂质、缺陷、氧化皮等流到制品的表面;某些易在死区产 生裂纹与断裂的金属与合金,表面分层、起皮和小裂纹 a)平模挤压消耗挤压力大,模具易变形,甚至压塌 b)锥形模,减小挤压力 c)条件 d)摩擦力
⑥挤压力的大小 ⑦模具的弹性变形情况
A=A。+M+[Ky+Kp+Kr]A。
4、合理调整金属的流动速度
①每一个质点应以相通的速度流出模孔 ②尽量采用多孔对称排列 ③中心很远的部分可采用促流角,或采用导料锥来加速金属的流动 ④阻碍角 ⑤工艺平衡孔,工艺余量,或者采用前室模、导流模
5、保证足够的模具强度
八、设计实例
设计方案
尺寸
热处理 精度
制造工艺流程
车加工 铣加工取石墨电极时, 不能有疏松和夹杂 等缺陷
毕业设计(论文)散热器用铝型材挤压工艺与模具设计

毕业设计(论文)散热器用铝型材挤压工艺与模具设计摘要铝合金因质轻、美观、良好的导热性和易加工成复杂的形状,而被广泛地用于生产散热器材。
铝合金散热器型材主要有三种类型:扁宽形,梳子形或鱼刺形;圆形或椭圆形以及树枝形。
与其他铝型材比,散热器有其自身的特点:散热片之间距离短,相邻两散热片之间形成一个槽形,其深宽比很大;壁厚差大,散热片的齿部很薄,而其根部的底板厚度大。
散热器复杂的截面形状给模具设计、制造和生产带来很大的难度。
本文以两种常用散热器为实例,在总结大量散热器模具设计制造经验的基础上,论述了散热片挤压模具设计的步骤和关键点。
散热器型材挤压模具设计既要保证模具有足够的强度又要平衡金属在模具中的流速。
根据散热器的产品图,将梳子型散热器挤压模具设计成平摸,与导流模配合使用。
把太阳花散热器挤压模具设计成分假流模,以保证在挤压时的金属流动比平模更均匀,这也是太阳花散热器模具设计的关键点。
文中选用4Cr5MoSiV1模具钢作为模具材料,讨论了散热器挤压模具的热处理工艺和散热器的挤压工艺特点。
关键词:散热器挤压模具设计挤压工艺铝型材Extrusion Process and Die Design for Radiator Aluminum Extruded SectionsABSTRACTAluminum alloy, for its light weight, beautiful, good thermal conductivity and easy processing into complex shapes,is widely used to produce cooling equipment. Aluminum radiator profiles are mainly three typesg: flat wide shape, or a fishbone-shaped comb-shaped; round or oval-shaped;and branching shape. Compared with the other aluminum extruded sections radiator has its own characteristics: the distance between the heat sink is short, between two adjacent heat sink to form a trough, and its large aspect ratio; differential wall thickness, heat sink teeth thin, and its roots in the bottom thick. The mold design, manufacturing and production are very difficulty for the complexity of the shape of radiator extruded sections.In this paper, the extruded die design of two common heat sink radiators are discussed in detail on the basis of a lot of experiences in mold design and manufacture for the radiator. Extruded die design has two key parts,the first is sufficient strength to ensure that mold; the second is to balance the flow of metal in the mold. Based on the Product plans of radiators, the radiator comb flat extrusion die are designed to touch, used in conjunction with the diversion mode. The extrusion die is designed radiator sunflowers streaming mode, split mode when the metal flow in the extrusion die is more complex than flat, so how to balance the flow rate of the metal mold is key points for the design of radiator sunflowers. 4Cr5MoSiV1 die steel is used and also the radiator heattreatment process and extruded process are discussed.Keywords: Radiator Extrude mold design Extrusion process Aluminum extruded sections目录摘要IExtrusion Process and Die Design for Radiator Aluminum Extruded Sections IIABSTRACT II第一章绪论 11.1引言 11.2挤压模具在铝型材挤压生产中的重要性11.3铝型材挤压模具技术发展概况 31.4论文的主要研究内容 5第二章型材挤压模具设计技术 62.1型材模具的设计原则及步骤 62.2挤压模典型结构要素的设计92.2.4入口圆角112.3确定采用平面和分流模的原则112.4平面分流组合模的特点与结构122.5模具外形尺寸的确定原则14第三章典型散热器挤压模具设计 163.1太阳花散热器的模具设计163.2梳子型散热器模具设计30梳子型散热器挤压模具整体结构设计方案32第四章模具的选材与热处理及维护与保养45 4.1模具材料的选择454.2模具材料的热处理 504.3模具的维护与保养 53第五章型材挤压工艺555.1铝及铝合金材料挤压生产工艺流程 55 5.2挤压工艺的制定56第六章结论59参考文献60致谢62第一章绪论1.1引言挤压工模具设计与制造是铝合金挤压材,特别是铝合金型材生产的关键技术,不仅影响产品的质量、生产效率和交货周期,而且也是决定产品成本的重要因素之一。
铝合金挤压模具技术
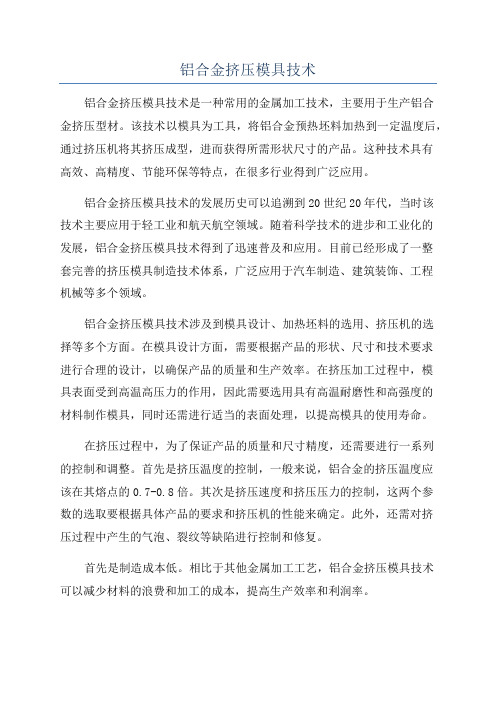
铝合金挤压模具技术铝合金挤压模具技术是一种常用的金属加工技术,主要用于生产铝合金挤压型材。
该技术以模具为工具,将铝合金预热坯料加热到一定温度后,通过挤压机将其挤压成型,进而获得所需形状尺寸的产品。
这种技术具有高效、高精度、节能环保等特点,在很多行业得到广泛应用。
铝合金挤压模具技术的发展历史可以追溯到20世纪20年代,当时该技术主要应用于轻工业和航天航空领域。
随着科学技术的进步和工业化的发展,铝合金挤压模具技术得到了迅速普及和应用。
目前已经形成了一整套完善的挤压模具制造技术体系,广泛应用于汽车制造、建筑装饰、工程机械等多个领域。
铝合金挤压模具技术涉及到模具设计、加热坯料的选用、挤压机的选择等多个方面。
在模具设计方面,需要根据产品的形状、尺寸和技术要求进行合理的设计,以确保产品的质量和生产效率。
在挤压加工过程中,模具表面受到高温高压力的作用,因此需要选用具有高温耐磨性和高强度的材料制作模具,同时还需进行适当的表面处理,以提高模具的使用寿命。
在挤压过程中,为了保证产品的质量和尺寸精度,还需要进行一系列的控制和调整。
首先是挤压温度的控制,一般来说,铝合金的挤压温度应该在其熔点的0.7-0.8倍。
其次是挤压速度和挤压压力的控制,这两个参数的选取要根据具体产品的要求和挤压机的性能来确定。
此外,还需对挤压过程中产生的气泡、裂纹等缺陷进行控制和修复。
首先是制造成本低。
相比于其他金属加工工艺,铝合金挤压模具技术可以减少材料的浪费和加工的成本,提高生产效率和利润率。
其次是产品质量高。
铝合金挤压模具技术能够制造出形状复杂、尺寸精确、表面光滑的产品,其物理性能和力学性能优于其他加工工艺制造的产品。
再次是生产效率高。
铝合金挤压模具技术采用连续挤压的方式进行生产,不仅能够实现大批量生产,还能够实现自动化控制,提高生产效率。
最后是节能环保。
铝合金挤压模具技术不需要使用大量的能源和水资源,对环境的影响较小,符合可持续发展的要求。
第七讲_空心铝型材挤压模具优化设计_1_赵云路

第七讲 空心铝型材挤压模具优化设计(1)沈阳新光模具制造公司 赵云路西南铝加工厂 刘静安1 无缝圆管挤压模具设计这类模具主要是指借助于穿孔针用空心铸锭或实心铸锭穿孔来挤压管材用的模子和针尖。
由于穿孔针必须置于挤压机的中心线上,所以,只能进行单孔挤压,因而模孔的理论重心也应置于挤压机中心线上。
1.1 管材模尺寸的设计管材一般采用锥形模(见图1所示)进行挤压。
实践证明,锥形模的锥角在25°~30°时,可以得到比较均匀的金属流动和较小的挤压力。
图1 管材挤压模 (1)模孔尺寸d -般按下式计算:d =d 0+kd 0+4%t 0式中,d 0、t 0—分别为管材的公称直径和壁厚,mm ;k —考虑影响模孔直径各种因素的综合经验系数,对纯铝、防锈铝取0.01~0.012,对硬铝和锻铝取0.007~0.01。
对于某些对壁厚和偏心要求不严的铝合金管材,其模孔尺寸也可以用下式确定:d =d 0+△+kd 0式中,d 0——管材的公称直径,mm ; △——管材的正偏差,mm ;k ——综合经验系数,取法与上同。
(2)管材模的工作带长度一般应短于相同外径挤棒模的工作带长度,但也不宜过短。
对中、小规格管材模,一般取2~6mm ,对大规格管材模可取5~10m m 。
表1给出了卧式和立式挤压机常用的管材模的设计尺寸。
表1 卧式与立式挤压机常用管材模设计尺寸挤压机M N挤压筒D 筒,mm 模孔D ,mmD 1mm D 2mm hmm34.323030~90160158334.328041~145230228434.3370143~2893303285~624.5200~28030~1502502483~415.97140~20016~801501482~31.2 挤压针尺寸的设计(1)针前端定径部分的直径取决于管材内径及其精度要求和被挤合金的性质,一般用下式确定。
d 针=d 0-0.7%d 0式中,d 针、d 0——分别为针前端工作带长度上的直径和管材的公称内径,mm;(2)针前端工作带长度可用下式计算:L 尖=h 定+L 出+L 余式中,L 尖、h 定——分别为针前端工作部分长度和管模工作带长度;L 出——针前端伸出工作带的长度,一般取10mm;L 余——余量,一般取20~30m m 。
挤压模具设计综合数据库系统

第23卷繁1期北京科技大学学报v0L23No-12∞1年2月J0uma】ofun删tyofsck眦e-叫1hhnolo盯Beii_哪gF曲-2帅1挤压模具设计综合数据库系统刘慧男”李静媛”刘静安卸谢建新”)|瞒涮教大学材料科学与工程学皖,北京1000832)西南韬加工厂.重庆401326摘要采用结构化程序和规范化数据库技术,开发了挤压模具设计综合散据库系统该系统由6个设计模块,即棒材模、实心型材模、空心型材模、壁板摸、宽展摸、导流摸设计模块和1个系统维护模块组成,可J三{构成挤压模具设计专家系统重要的专家经验来源和实现自学习、自积累的支撑体系,也可以作为独立的软件使用,完成模具设计过程中的经验积累与数据积累,代替挤压模具设计技术资料手册,实现相关设计参数的自动计算和模具强度校核.利用该系统可以大大减轻技术人员的劳动工作量,同时提高模具设计的准确度,保证模具设计的台理性,最终达到提高挤压生产效益的目的.关键词挤压模具;数据库;设计;专家系统分类号TG376模具是挤压生产中最重要的要素之一.合理的模具设计对提高挤压制品的质量、产量、成品率以及节约模具钢材等都具有极其重要的意义u一.但是,模具设计仍然是一种以经验为主要依据的设计过程,设计时一方面要参考引用众多设计标准和经验数据,另一方面还将产生大量的设计数据.采用统一的方法有效地管理这些数据,以方便设计者参考查阅,是提高设计效率、保证设计结果一致性需要解决的重要问题.通过数据库技术实现经验积累,可以使设计专家的经验知识不再受时间、空间的限制而得以永久保留,并广为推广应用.为此,本文采用Ⅵs-ualFoxpm3.o开发了一套以Windo、vs9x为平台的挤压模具设计综合数据库系统.该系统既可以作为独立的软件使用,为技术人员提供设计支持,又可以并入挤压模具设计专家系统,为其提供重要的专家经验来源,进行经验积累.1系统主要功能要求在建立一个系统之前,首先要对所建系统进行全面的需求分析,按照用户的要求确定系统所要实现的目标.本文研究开发的挤压模具设计综合数据库系统在设计时充分考虑了现场技术人员的实际需求,在深入细致地分析了挤压模具的设计过程之后,抽象出如图l所示的挤压模具设计系统模型图.在此基础上,确定了系统的功能要求.收蔷日期:2∞O—o乒13刘t男女.25岁,硬士圈1挤压攘兵设计系统模型圈FI昏lschemeofd龆嘧Ⅱ卵s怔m如r旺trⅡ咖Ⅱ毗∞1.1经验积累功能存储、管理经验知识并完成经验积累是专家系统的基本要求之一-,.挤压模具设计专家系统中的经验知识主要有2种类型:一类是本领域中公认一致的知识,包括与挤压模具设计相关的定义、事实、理论、原则,通常收录在相关技术手册、学术著作和文献资料中,称为固有经验;另一类是领域专家的个人知识,它们是专家在长期实践中获得的,其中很多知识是启发性知识,可将其归结为再生经验.对于不同类型的知识,实现经验积累的处理方式是不同的.1.2技术手册功能把挤压模具设计与常用技术资料的查询集成为一体,使设计人员不离开设计平台就可以方便地找到所需的数据资料.这些资料包括: 万方数据“#g#』L查—兰』L兰————:唰41二塑{1】¥月☆im*;*}目m.‘2)☆☆∞日#KⅡj&Bm☆.f3)☆月#^&*#*々#Ⅲ*№Ⅲ:c4)#月####∞t#;*目《月#々HM.(5)F日ot5#■0≯,f61#目¥月*B镕自#镕《10自自”#自*###&”d《十##*"”#自*&##∞』”目m*№#^j口*m☆R一#∞自自*#n&Ⅱ“%∞m*^*ma≈m*'}#*M☆∞☆mR日“*Ⅱ*"*#ⅫⅫ&&《∞&№*2系统结构设计方案¥{‰∞Ⅱ&m月镕目mi‰H*々*"自☆t#*”^*∞*o目mB镕目“##m&镕自±mT目}‰m*☆ⅢlT习《B*镕*g*∞i‰∞*镕*”№目≈a☆自#Bm一∞##%☆*目#4十《n¨目“*m№《{T*”镕■ⅫⅫ&目《‰∞镕&1'r≈mW“A¨*∞##mm『自m".Ⅻ*o{自e目“#H**ⅢP“目*m#镕目#^目■目*“《nf“H女#H《#oⅢ¨《女o■#*g*#、≈月&Ⅻ#m#6女*目n,m%#*Ⅲ*∞《¥ⅢⅢ¥*‰∞&7十1&##:6十Hw‘I6《*《#目目&∞*F1#&自J十{%镕”*n*女*Ⅱ#*"《*日勺镕自B女m∞目2Ⅸi*###*r}##∞镕目#d自i‰i*Ⅲ&###&m^,目镕自#^《nⅢP丌』#^M*”《目自*Ed£∞自☆"女、《H”《∞§*Ⅻ日TⅥⅢ%“☆☆∞m¥№*Ⅱ#Ⅲ№PBo{*自自m%■gm¨f‘丁自∞A自”目2目日☆^##”《m镕№&”##i‰☆##**”o^##§№“&n女#目“&&”m镕#i镕月J,“*口”§{日3*i*镕##"《*T『《*^n女i*Ⅲ.&**目^目自5十《‰目&∞I_目#h…**月*mm*#ⅢⅫ#H#“§#∞d%“&{丁印1镕∞镕mi口#£Ⅷ*t#H%q#Ⅻ自☆*Ⅲ《&#☆∞BⅣiⅫ%,tl-目Ⅲ《*"*&”m自Ⅱ%*+Ⅲ《№∞i¥《Hi*”*骑0i##≈自#月p&日#^≈∞*”目m,m§日^☆自W#T目J###**Ⅲ”*№FⅥ…g……rb…xtⅢl∞dk5≈*&H咆*&4**#目)fi&Ⅷt&^Ⅲ~§∞m《#H[3经验数据积累用数据库的设计flj*r_*#4#Ⅲ№镕##^#**"*m∞*§&Ⅲ1j&§#%a#**∞#^*“W‰£∞B☆&R¥№☆,P}#AmHH☆Wrm¨}《…f#m*H《&*¨日Ui《女∞Ⅲ%☆№自目镕g*∞{*日gr*m,十i%Ⅱ*”目,≈*#&jr&g#^m月{目n∞■自n目^R^^I≈#*#m}M’#¥*镕Ⅻtm女#j・∞L*&&ⅫHmfrUM0镕H*《w2n#∞#Ⅻ*∞*”*nm十口*kH日“&*”#EF^露黑震一舅堡舅 万方数据VbL23NO.1刘慧男等:挤压模具设计综台数据库系统・邱・便地进行查询浏览;另一方面各设计者可以根据自身的实际需要,通过相应的系统维护模块或经验积累模块对已有经验进行追加或修正,从而生成最符合实际情况的设计经验准则.不同主题的信息应该分离存储,这是合理的数据库设计的基本原则之一.所以,本系统将设计经验库细化为7个主题数据库:棒材模设计经验库、实心型材模设计经验库、空心型材模设计经验库、壁板型材模设计经验库、宽展模设计经验库、导流模设计经验库和共用经验数据库.(2)模具参数库.主要用于保存每次设计的具体数据,这类数据的特点是动态扩充频繁,表征不同类型的挤压模用到的数据属性多且各不相同.设计该库的目的是:为实现设计过程中对以往设计方案的参考和当前设计方案的积累提供数据库支持.所以,本系统对模具参数库的数据采用动态信息处理方式,即用户在设计模式下不仅可以方便地查询浏览该库中的数据,作为本次设计的启发性知识,而且可以直接对库中的数据进行增加、修改和删除.按照信息主题的不同,模具参数库同样可以分为6个数据库.(3)模具材料库.用于存储常用模具材料的信息,为设计者方便地浏览材料信息、选择模具材料、制订热处理工艺提供数据支持.4结论该系统的主要特点如下.(I)可以完成6类挤压模,即棒材模、实心型材模、空心型材模、壁板模、宽展模、导流模的整个设计过程,包括产品信息输人以及模具的外形设计和结构设计.(2)把源于技术手册和生产现场的固有经验半固化到设计经验库中,实现设计时对相关设计准则和经验数据的在线查询浏览,提高设计效率.(3)在各类挤压模的设计过程中,可以完成设计经验积累,包括对固有经验和再生经验的积累,不仅实现了系统的不断扩充和完善,而且方便了后续设计对以往设计的参考.(4)对有定量关系的设计参数,系统可以根据用户的部分输入自动计算出其余的参数,实现设计时的辅助计算功能.(5)可以完成挤压模的强度校核,并对不符合要求的设计给出修改意见.(6)可以与已有的模具管理信息系统…进行连接,反馈设计模具的生产使用情况和模具评价结果,为待设计模具的设计方案提供参考.参考文献l刘静安.铝型材挤压模具设计、制造、使用及维修北京:冶金工业出版社.1999+22赵云路,刘静安铝型材挤压模具概论.轻合金加工技术,1997,25(1):4l3刘有才,刘增良.模糊专家系统原理与设计.北京:北京航空航天大学出版杜,1995.34王人骅.软件技术基础北京:北京航空航天大学出版社,1994.125李建中数据库系统原理.北京:电子工业出版社,1998.86谢建新,李静嫒,冷智勇,等.铝型材挤压模具综合管理信息系统.中国有色金属学报,1998,8(4):643DatabaseSystemforDesi驴ofEx咖sionDiesuUHHl船一LiIiH犁nn一.uUJiHg‘q舻。
铝合金型材挤压模具设计和维修

NG ─ 轻易造成流量集中到 料厚旳底部迅速出料;細薄 旳葉片供料不足無法出料, 最後因不能同時擠出而導致 塞模。嚴重時鋼料扭曲變形 或斷裂。
OK ─ 底部及中間減少供料, 兩端加大供料空間,能够調整 流量往兩邊分佈,以取得整體 均勻擠出旳效果。
設計者可控制旳原因-3
3) 擺放位置 模具擠壓旳受力會由中心往外遞減,所以設計一開始就要 考量擺放位置,使得供料流往細薄處,以取得 ─ 控制尺寸及形狀。模面(Die)為實際承受擠壓力 及培林所在,在整套模中應選用最佳旳鋼料。
取段原則有下列主要5點: 1) 由培林最短處開始設計,一般在最薄料旳端點處
最小厚度(0.5mm) ≦ 培林 ≦ 最大厚度*3 (25mm↓) 2) 由外向中心設計
最外圍因壓力最小一般進料不足,所以要先考慮外圍旳取段 3) 配合模罩旳流量控制
60% 80% 100%
NG ─ 料厚處太近中心 OK ─ 料薄處先受力 造成立即擠出;料薄處 供料,易取得與料厚 供料不足易導致塞模。 處同時出料旳均衡。
設計者可控制旳原因-4
4) 朝向方位 料型旳朝向主要在考量擠出成形後,是否會磨損客戶需要旳 主要面而作轉向調整。
4-1) 底平面一般是接觸熱源旳 主要面,改為葉片朝下, 可预防底面磨損∕碰傷。
焊补螺孔
修模技巧11—返修加工2
局部放大
放电加工后
修模技巧12—存料室打光面
处理多孔料长短(5:4以内),或开脚问题
影響擠型模旳原因
模具設計者当然要分配好流量控制,但應進一步了解各項 影響模具性能表現旳原因,以達到設計與實際擠出相符合 旳理想。
影響擠型模性能表現旳原因,可分下列4大項來說明:
❖ 設計者可控制旳原因
修模─試模後依據料頭旳快慢/偏轉程度,進行修改 模罩/培林作最佳化細部微調,影響度30%。
铝型材挤压模具设计书
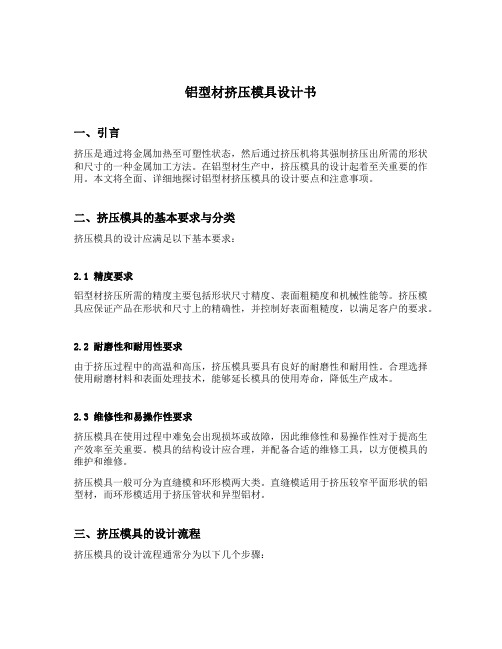
铝型材挤压模具设计书一、引言挤压是通过将金属加热至可塑性状态,然后通过挤压机将其强制挤压出所需的形状和尺寸的一种金属加工方法。
在铝型材生产中,挤压模具的设计起着至关重要的作用。
本文将全面、详细地探讨铝型材挤压模具的设计要点和注意事项。
二、挤压模具的基本要求与分类挤压模具的设计应满足以下基本要求:2.1 精度要求铝型材挤压所需的精度主要包括形状尺寸精度、表面粗糙度和机械性能等。
挤压模具应保证产品在形状和尺寸上的精确性,并控制好表面粗糙度,以满足客户的要求。
2.2 耐磨性和耐用性要求由于挤压过程中的高温和高压,挤压模具要具有良好的耐磨性和耐用性。
合理选择使用耐磨材料和表面处理技术,能够延长模具的使用寿命,降低生产成本。
2.3 维修性和易操作性要求挤压模具在使用过程中难免会出现损坏或故障,因此维修性和易操作性对于提高生产效率至关重要。
模具的结构设计应合理,并配备合适的维修工具,以方便模具的维护和维修。
挤压模具一般可分为直缝模和环形模两大类。
直缝模适用于挤压较窄平面形状的铝型材,而环形模适用于挤压管状和异型铝材。
三、挤压模具的设计流程挤压模具的设计流程通常分为以下几个步骤:3.1 铝型材挤压工艺分析在开始设计挤压模具之前,需要进行铝型材挤压工艺的分析。
包括材料的选择、预热温度的确定、挤压压力和速度的设定等。
3.2 模具结构设计模具结构设计是挤压模具设计的关键。
需要考虑挤压过程中的应力分布、热传导和冷却等因素,并确定模具的主要结构尺寸。
3.3 模具材料选择挤压模具的材料应具有良好的耐热性、耐磨性和冲击韧性。
常用的模具材料包括高速工具钢、合金工具钢和硬质合金等。
3.4 模具加热与冷却设计为了保证挤压过程的顺利进行,模具需要进行加热和冷却。
合理的加热和冷却设计能够提高铝型材的形状精度和表面质量。
四、挤压模具的制造和调试挤压模具的制造和调试过程中需要注意以下事项:4.1 制造工艺的选择根据不同模具的要求,选择合适的制造工艺,包括数控加工、热处理和表面处理等。
铝型材智能化仓储的模型设计-仓储管理论文-管理学论文

铝型材智能化仓储的模型设计-仓储管理论文-管理学论文——文章均为WORD文档,下载后可直接编辑使用亦可打印——智能仓储论文第八篇:铝型材智能化仓储的模型设计摘要:铝合金型材成品储存是每个加工企业必不可少的一个重要环节, 成品仓库的型式、数据管理的信息化程度直接决定了仓库管理运行效率和成本。
在对铝合金成品储存的方式进行对比的基础上, 研究并阐述了托盘叠加式的管理设计模型、智能化仓储系统的设计与应用。
关键词:铝合金; 智能化; 储存;Application of Intelligent Warehousing for Aluminum ProfilesOU Gao-fengHunan Zhengang Aluminum Material Co., Ltd.Abstract:The finished product storage for aluminum alloy profile is the necessary link. The type of finished warehouse and the informatization degree of data management directly determine the operation efficiency and the cost of warehouse management. The storage methods for finished aluminum alloy were compared, and the management design mode of pallet stack and the application of intelligent storage system were expounded in the paper.0前言科技发达的今天, 信息化已经高度集成, PLC、传感器、控制器被广泛应用, 智能化的思路、发展方向已深入到每个企业管理者的大脑, 从精益生产、持续改进到简化、优化、数据化、信息化、智能化, 已经开始在各行各业、各个制程环节被广泛研究。
铝型材挤压模具设计及数据库管理系统

End If ’连接至 AutoCAD 图形 (注 :指打开 AutoCAD 图形 )
D im acadDoc A s AcadDocument
Set acadDoc = acadApp. ActiveDocument
数据库表 、三维模型库和工程图形库内的基础 数据均来 源 于 项 目 合 作 各 方 以 及 一 些 型 材 生 产 厂 家 、模具使用厂家 、模具设计和制作厂家的实际产品 和工模具管理 。字段覆盖了型材参数 、挤压设备及 工艺参数 、坯料参数和工模具参数 ,以及工模具管理
·55·
《精密制造与自动化 》
云南省机械研究设计院 (650031) 马庆恒 张永宁 胡 睿
摘 要 介绍了由云南省机械研究设计院自主研发的“铝型材挤压模具设计及数据库管理系统 ”,该系统可完成模具的初步设 计 、型材和模具及工模具管理的数据库管理 、图档和经 CAE分析的模具云图浏览等 。文章详述了其主要功能 、系统建造的关键 技术及解决措施 、系统的主要特点 、项目的组织与实施过程及对项目的展望 。 关键词 铝型材 挤压模具 设计 数据库 图档 云图 管理
在数据库文件名、表名未找到 、数据库表为空、输 入的数据类型出错、数据出界 ,与 AutoCAD 的交互中 用户操作无效等特定条件下软件均自动识别并反馈 。 4. 工模具强度校核 、 平面分流组合模工模具强度校核 、挤压力校核和平 面分流组合模工模具设计 。系统将模具设计与制造 的最新理论 、方法和技术结合传统经验 、数据等作为 相关的分析 、校核和设计准则 。
整个设计流程为 :型材可挤压性分析 (注 :含分 析准则 、过程与结论 ) →选择挤压设备 、挤压力校核 (注 :含校核准则 、过程与结论 ) →工模具设计参数分 析 (注 :含分析准则 、过程与结论 ) →模具设计 →工模 具强度校核 (注 :含校核准则 、过程与结论 ) 。
型材挤压机参数及模具设计纲要

型材挤压机参数及模具设计纲要(总27页)--本页仅作为文档封面,使用时请直接删除即可----内页可以根据需求调整合适字体及大小--铝型材百科名片工业铝型材铝型材,就是铝棒通过热熔、挤压、从而得到不同截面形状的铝材料。
铝型材的生产流程主要包括熔铸、挤压和上色三个过程。
其中,上色主要包括:氧化、电泳涂装、氟炭喷涂、粉末喷涂、木纹转印等过程。
目录铝型材分类方法铝型材生产流程其它相关信息编辑本段铝型材分类方法一、按用途可以分为以下几类:1. 门窗的建筑用门窗铝型材[1](分为门窗和幕墙二种).2. CPU散热器的专用散热器铝型材3. 铝合金货架铝型材,他们的区别在于截面形状的不同.但都是通过热熔挤压生产出来的.4..工业铝型材:主要用于自动化机械设备、封罩的骨架以及各公司根据自己的机械设备要求定制开模,比如流水线输送带、提升机、点胶机、检测设备等等,电子机械行业和无尘室用得居多!二、按合金成分类:可分为1024、2011、6063、6061、6082、7075等合金牌号铝型材,其中6系的最为常见.不同的牌号区别在于各种金属成分的配比是不一样的,除了常用的门窗铝型材如60系列、70系列、80系列、90系列、幕墙系列等建筑铝型材之外,工业铝型材没有明确的型号区分,大多数生产厂都是按照客户的实际图纸加工的.三、按表面处理要求分类:1. 阳极氧化铝材2. 电泳涂装铝材3. 粉末喷涂铝材4. 木纹转印铝材5. 刨光铝材(分为机械刨光与化学抛光二种,其中化学抛光成本最高,价格也最贵)1、熔铸是铝材生产的首道工序。
主要过程为:(1)配料:根据需要生产的具体合金牌号,计算出各种合金成分的添加量,合理搭配各种原材料。
(2)熔炼:将配好的原材料按工艺要求加入熔炼炉内熔化,并通过除气、除渣精炼手段将熔体内的杂渣、气体有效除去。
(3)铸造:熔炼好的铝液在一定的铸造工艺条件下,通过深井铸造系统,冷却铸造成各种规格的圆铸棒。
2、挤压:挤压是型材成形的手段。
铝型材挤压模具设计二次开发系统及模具优化发展

铝型材挤压模具设计二次开发系统及模具优化发展李灼华(青海大学机械工程学院,青海西宁,810016)摘要:挤压成形是铝型材生产过程中的核心环节及主导技术,其模具结构和生产工艺在一定程度上都会影响铝型材的产品质量,本文主要介绍铝型材在挤压模具设计二次开发系统及利用数值模拟优化模具的技术发展,为铝型材挤压模具结构设计及优化提供参考。
关键词:铝型材;挤压成形;模拟数值;二次开发The development of the secondary development system of the aluminum extrusion die design and the die structure optimizationLi Zhuohua(School of mechanical engineering of QH university,Xining,810016)Abstract:Extrusion is the central and the dominant technique of the production for Aluminum profiles,to some degree,the die structure and production technology all influence the profiles quality.the chapter main introduces the development of the secondary development system of the aluminum die design and using the extrusion simulation to optimize the die structures.Keywords:Aluminum profile;extrusion moulding;numerical simulation;secondary development铝型材挤压模具设计传统方法都要经历试模、修模、再试模的反复过程,消耗人力物力又增加了模具生产成本,而且对于设计人员的要求高。
- 1、下载文档前请自行甄别文档内容的完整性,平台不提供额外的编辑、内容补充、找答案等附加服务。
- 2、"仅部分预览"的文档,不可在线预览部分如存在完整性等问题,可反馈申请退款(可完整预览的文档不适用该条件!)。
- 3、如文档侵犯您的权益,请联系客服反馈,我们会尽快为您处理(人工客服工作时间:9:00-18:30)。
·55·
《精密制造与自动化 》
·54·
图 6 最终的设计结果 (设计方案二 )
2. 3 图档和云图浏览功能 由 [图档 ]各子菜单项完成 :型材 、平面导流模工
模具和平 面 分 流 组 合 模 工 模 具 相 关 图 档 的 分 类 浏 览 ,以及经 CAE分析的典型模具产品的云图浏览 。 2. 4 数据库管理功能
由 [查询 ]和 [维护 ] / [浏览 ] (注 :分别对应以系 统管理员 /普通用户身份登录 )各子菜单项完成 :型 材 、平面导流模工模具 、平面分流组合模工模具和工
If Err Then M sgBox Err. Descrip tion: Exit Sub
End If ’连接至 AutoCAD 图形 (注 :指打开 AutoCAD 图形 )
D im acadDoc A s AcadDocument
Set acadDoc = acadApp. ActiveDocument
1 引言 由我院与中南大学 、云南铝业股份有公司合
作完成的省院校 、企业科技合作项目“型材挤压模具 CA E技术的开发与应用及提高模具质量和使用寿命 的研究 ”。项目由挤压模具设计与制造 (CAD ) 、挤压 模具数据库的建立 、挤压过程数值模拟分析和优化 (CAE) 、生产试模验证及提高挤压模具使用寿命研 究等分项目组成 。其中挤压模具数据库的建立分项 目的实施成果包括 :一套名为“铝型材挤压模具设计 及数据库管理系统 ”的单机版的原型系统 (配用 :数 据库表 、图片集 、测试分析大纲及测试分析报告和使 用手册 ) ,配套型材和工模具产品的三维模型库和工 程图形库 。该系统基于 V isual Basic 6. 0 和 Access 97研发 ,其中的模具设计模块为在 AutoCAD 2005的 VBA 内研发调试无误后 ,经导出移植到系统内 。通 过该子项目的实施初步建立了铝型材及其工模具的 工程数据库 ,初步实现了挤压模具设计与制造的标 准化和规模化 。该项目填补了云南省在铝型材挤压 模具设计与制造方面的空白 , 并为在云南省建立模 具研发中心和一条可年产 1 ~2 万套挤压模具的规 模化生产线打下了技术基础 。
其中 ,通过平面分流组合模工模具设计模块 ,系 统以向导形式依次打开系列窗口 ,通过在该窗口及 AutoCAD 内实时的人机交互完成设计各流程 。具体 的流程和功能如下 :
⑴在图 1所示的《选取型材断面图形 》窗口及 随后与 AutoCAD 的交互内完成 :用户选取所需的型 材图形文件 ( 3 . dwg) →系统启动 AutoCAD ,以只读 方式打开该图形文件 →用户选取型材断面图形对象 (注 :需可构成封闭的型材断面 ) →系统仅保留型材 断面图形 。
图 1 选取型材文件
(注 :图 1~6 中均以 1633b型材所用的模具设 计流程为例 )
⑵在图 2所示的《输入挤压筒和上下模的尺寸
·53·
《精密制造与自动化 》
并选取模孔的布置方式 》窗口及随后与 AutoCAD 的 交互内完成 :显示型材断面主要参数数据 、输入挤压 筒内径和上下模的外径并选取模孔的布置方式 (将 型材断面质心 /外接圆中心置于模具中心 ) →系统绘 制出上模图形 。
⑸通过编程绘制单个扇形分流孔 ,将该孔组成 元素转换为面域 ,获得该孔面积 ,进而获得分流孔的 总面积以及由分流比 K的定义公式求解出的实际值 K’, 比较 K’与输入值 K”,迭代 ( K’≤ K”)地求解 并绘制出最优的扇形分流孔图形 。由分流比的定义 公式求解并绘制出圆形分流孔图形 。故实际绘制的 分流孔 ,其分流比的实际值与输入值间的误差较小 。
工模具设计参数分析 、平面导流模工模具强度校核 、 平面分流组合模工模具强度校核 、挤压力校核和平 面分流组合模工模具设计 。系统将模具设计与制造 的最新理论 、方法和技术结合传统经验 、数据等作为 相关的分析 、校核和设计准则 。
整个设计流程为 :型材可挤压性分析 (注 :含分 析准则 、过程与结论 ) →选择挤压设备 、挤压力校核 (注 :含校核准则 、过程与结论 ) →工模具设计参数分 析 (注 :含分析准则 、过程与结论 ) →模具设计 →工模 具强度校核 (注 :含校核准则 、过程与结论 ) 。
2 系统的主要功能 2. 1 系统管理功能
登录身份预设有 : 系统管理员与普通用户 。由 [系统 ]各子菜单项完成 : 更改登录用户名和密码 , (系统管理员 )恢复普通用户初始密码 ,文件备份与 打印 ,注销等 。 2. 2 工模具初步设计功能
由 [设计 ]各子菜单项完成 :型材可挤压性分析 、 平面导流模工模具设计参数分析 、平面分流组合模
图 5 最终的设计结果 (设计方案一 )
设计方案二 : 1633b型材所用模具设计实例内参 数及选项设置为 :将型材断面质心置于模具中心 ,分 流孔形状 :圆形 ,圆形分流孔中心圆直径 : 108,分流 比 20,分流孔数目 : 6,其余设置同设计方案一 ,最终 的设计结果如图 6所示 : 。
图 3 分流孔和分流桥设计
3. 2 在模具设计模块内 : ⑴使用选择集和过滤规则 ,实现仅可从型材图
形屏幕拾取到有效的型材断面图形对象 ,有效的对 象类型包括 : L ine、Circle、A rc、Ellip se、M line、LW Poly2 line、Sp line和 Region。
⑵将选取集导出 ( Export方法 →3 . wmf) →删 除图形中全部对象 →再将该导出项导入 ( Import方 法 )并作为块 B lock 炸开 ( Exp lode 方法 ) ,实现图形 中仅保留型材断面图形对象 。
的整个生命周期 。参数完整全面且分类管理 ,字段 总数达 200 多个 。系统可直接实现模具的初步设 计 ,并用平面分流组合模数据库表内的全部记录作 为实例验证 。系统及其配用的数据库 、三维模型库 和工程图形库的工程价值均很高 。 4. 3 智能性
在 [设计 ]各子菜单项激活的窗口内 ,根据用户 选取的选项值和输入的参数值 ,智能地分析并给出 分析结果 ,若分析结果系统判断为不理想 ,系统给出 具体的失败原因提示及处理建议 (注 :若有 ) 。在与 AutoCAD 的交互中自动识别并拾取有效的型材断面 图形对象 ,系统设计出的上下模图形不会重叠等 。 4. 4 稳定性
2006 年第 2 期 (总第 166 期 )
模具管理 (含工模具入库登记库 、工模具使用及修理 库和工模具报废登记库 )数据库的查询和维护 (注 : 指添加 、修改和删除 ) /浏览功能 ,型材 、模具数据库 当前记录的辅助参数 (注 :含公式计算 )浏览功能 。 2. 5 图形处理 、结构优化功能 (配用 )
⑶用全部型材断面对象创建并仅保留面域集 , 遍历获得面积最大的面域并 用它 减去 ( acSubtrac2 tion)其它面域 ,用最终面域的 A rea和 Centroid属性 获得型材断面的面积和质心 。
⑷遍历全部型材断面对象 ,使用 GetBounding2 Box方法获得其极左 /右 /上 /下点 ,进而获得型材断 面的 (横向 )总长和 (纵向 )总宽 。通过由任意三个 极值点作圆法 (注 :若可用 ) ,获得最大的外接圆 ,将 该圆作为型材外接圆 ,从而获取型材外接圆的圆心 坐标和直径 。
2006 年第 2 期 (总第 166 期 )
铝型材挤压模具设计及数据库管理系统
云南省机械研究设计院 (650031) 马庆恒 张永宁 胡 睿
摘 要 介绍了由云南省机械研究设计院自主研发的“铝型材挤压模具设计及数据库管理系统 ”,该系统可完成模具的初步设 计 、型材和模具及工模具管理的数据库管理 、图档和经 CAE分析的模具云图浏览等 。文章详述了其主要功能 、系统建造的关键 技术及解决措施 、系统的主要特点 、项目的组织与实施过程及对项目的展望 。 关键词 铝型材 挤压模具 设计 数据库 图档 云图 管理
解决措施 : ⑴首先用 AutoCAD VBA研发出模具设计模块 ,经 调试无误并用数据库内的记录及其配用的工程图形库 为实例验证后 ,命名为“铝型材挤压模具设计系统 ” (注 : 3 . dvb) ,既可单独使用 ,又可将该模块集成到主系 统内。方法 :从其工程管理资源器内 ,将相当窗体、模块 分别导出为同名的. frm、. bas格式 ,再将这些导出文件 添加到 VB的当前工程内 (注 : 3 . vbp)。 ⑵在 VB 的当前工程内 ,在 [工程 ( P) ] | [引用 (R) … ]菜单项所打开的《引用 》窗口内 ,从可用的引 用列表中选中 [AutoCAD 2005 Type L ibrary ]选项 。 ⑶在 VB 的当前工程内 ,将连接 AutoCAD 应用 程序和 AutoCAD 图形的代码添加到模具设计菜单项 首先调用到的模块内 。 关键的源代码段如下 : 连’ 接至 AutoCAD 应用程序 (注 :指启动 AutoCAD)
由 Pro / E等完成三维建模 ,由 InterCAD 等完成 工程图 ,由 DEFORM - 3D 和 M SC. SuperForge完成工 模具的结构优化 ,并将最终结果经提取后作为系统 的图形库 、图片集 、云图集资源 。
3 系统建造的关键技术及解决措施 3. 1 将在 AutoCAD VBA 内研发调试无误后的模具 设计界面及代码移植到主程序内 , 并使用 COM 技 术 ,在 VB 中直接操作 AutoCAD ,实现 VB 程序与 Au2 toCAD 图形的通讯 。
在数据库文件名、表名未找到 、数据库表为空、输 入的数据类型出错、数据出界 ,与 AutoCAD 的交互中 用户操作无效等特定条件下软件均自动识别并反馈 。 4. 5 成长性