小直径薄壁变径段的制作
tekla自定义薄壁变径截面
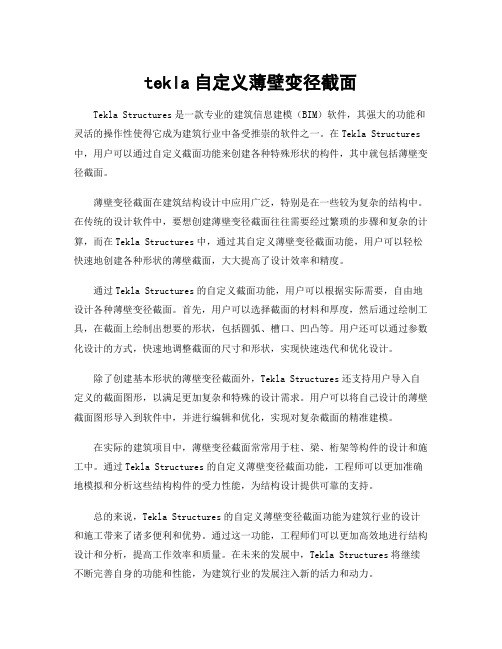
tekla自定义薄壁变径截面Tekla Structures是一款专业的建筑信息建模(BIM)软件,其强大的功能和灵活的操作性使得它成为建筑行业中备受推崇的软件之一。
在Tekla Structures 中,用户可以通过自定义截面功能来创建各种特殊形状的构件,其中就包括薄壁变径截面。
薄壁变径截面在建筑结构设计中应用广泛,特别是在一些较为复杂的结构中。
在传统的设计软件中,要想创建薄壁变径截面往往需要经过繁琐的步骤和复杂的计算,而在Tekla Structures中,通过其自定义薄壁变径截面功能,用户可以轻松快速地创建各种形状的薄壁截面,大大提高了设计效率和精度。
通过Tekla Structures的自定义截面功能,用户可以根据实际需要,自由地设计各种薄壁变径截面。
首先,用户可以选择截面的材料和厚度,然后通过绘制工具,在截面上绘制出想要的形状,包括圆弧、槽口、凹凸等。
用户还可以通过参数化设计的方式,快速地调整截面的尺寸和形状,实现快速迭代和优化设计。
除了创建基本形状的薄壁变径截面外,Tekla Structures还支持用户导入自定义的截面图形,以满足更加复杂和特殊的设计需求。
用户可以将自己设计的薄壁截面图形导入到软件中,并进行编辑和优化,实现对复杂截面的精准建模。
在实际的建筑项目中,薄壁变径截面常常用于柱、梁、桁架等构件的设计和施工中。
通过Tekla Structures的自定义薄壁变径截面功能,工程师可以更加准确地模拟和分析这些结构构件的受力性能,为结构设计提供可靠的支持。
总的来说,Tekla Structures的自定义薄壁变径截面功能为建筑行业的设计和施工带来了诸多便利和优势。
通过这一功能,工程师们可以更加高效地进行结构设计和分析,提高工作效率和质量。
在未来的发展中,Tekla Structures将继续不断完善自身的功能和性能,为建筑行业的发展注入新的活力和动力。
tekla自定义薄壁变径截面

一、概述Tekla Structures 是一个专业的建筑信息建模(BIM)软件,能够帮助工程师和设计师轻松地进行建筑结构的建模和设计。
在 Tekla Structures 中,有很多自定义功能,其中包括薄壁变径截面功能。
本文将介绍 Tekla 自定义薄壁变径截面的相关内容,帮助读者了解其特点和应用。
二、Tekla 自定义薄壁变径截面的概述1. 什么是薄壁变径截面?薄壁变径截面是指在截面的横截面上,材料在一定区域内逐渐变薄或变厚的截面形式。
这种截面形式可以提高材料的使用率和减轻结构的自重,同时也能够提高结构的强度和稳定性。
2. Tekla 自定义薄壁变径截面的特点- 可以根据实际工程需求进行自定义设计,满足不同项目的特定要求。
- 能够在建模过程中减少材料的浪费,降低工程成本。
- 可以应用于各种类型的结构设计,包括钢结构、混凝土结构等。
三、Tekla 自定义薄壁变径截面的设计流程1. 确定截面的几何形状和尺寸在 Tekla Structures 中,根据实际工程要求确定薄壁变径截面的几何形状和尺寸。
可以通过绘图工具和参数设置等功能,对截面的各项参数进行调整和优化。
2. 添加材料属性在设计薄壁变径截面时,需要添加材料属性,包括材料的弹性模量、屈服强度、密度等参数。
这些参数将影响到最终结构的强度和稳定性。
3. 进行分析和优化设计完成后,可以进行结构分析和优化。
Tekla Structures 提供了强大的模拟和分析工具,可以对设计的薄壁变径截面进行力学和结构性能的分析,从而优化设计方案。
四、Tekla 自定义薄壁变径截面的应用案例1. 钢结构设计中的应用在钢结构设计中,薄壁变径截面经常被用于梁和柱的设计。
通过合理设计和优化,可以实现在保证结构稳定性和强度的前提下,减轻结构自重,降低钢材的使用量,降低工程成本。
2. 混凝土结构设计中的应用在混凝土结构设计中,薄壁变径截面也有着广泛的应用。
通过采用薄壁变径截面设计,可以改善混凝土构件的受力性能,提高混凝土构件的承载能力和延性,从而提高整体结构的抗震性能。
变径段的设计与制造
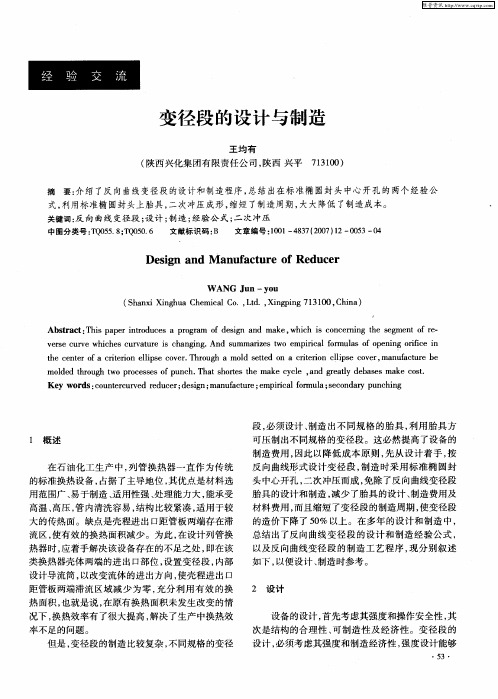
变径段 的设 计与制 造
王均 有
( 陕西 兴化集 团有 限责 任公 司 , 陕西 兴平
730 ) 110
摘 要: 绍 了反 向 曲线变径 段 的设 计 和制造 程 序 , 介 总结 出在 标 准椭 圆封 头 中心 开 孔 的两个 经 验公
式, 利用标 准椭 圆封 头上 胎具 , 次冲压 成形 , 短 了制造 周期 , 大 降低 了制造成 本 。 二 缩 大
W ANG u —y u J n -o
( hn i ig u h m cl o , t. X n pn 1 10, hn ) S ax Xn h aC e ia C . Ld , ig ig7 3 0 C ia
Ab t a t T sp p ri to c s a p o r m fde in a d ma e, c s c n e ni g t e s g n f r — s r c : hi a e n rdu e r g a o sg n k whih i o c r n h e me t o e v re c r e wh c e u v t r s c a g n . d s e s u v i h sc r au e i h n i g An umma z s t mp rc lfr l s o p n n rfc n i r e wo e i a o mu a f o e i g o i e i i i
无论二次冲压出现哪种现象都存在反向曲线变径段被报废的可能图2反向曲线变径段简图性因此在多年的设计和制造中积累了许多实践经验总结出制造反向曲线变径段中心开孔的经验3制造公式从此结束了采用展开作图法确定开孔尺寸的历史也从比较复杂而又繁琐的展开作图法中解脱反向曲线变径段的制造由于设计时就按标准出来使开孔尺寸的准确率由原来的80提高到椭圆封头中心开孔二次冲压成形来设计的所以100而且在280多件反向曲线变径段的制造中在制造时必须按设计图纸尺寸及制造技术要求来制全部获得成功其开孔直径见图3的经验公式如造无须设计整体反向曲线变径段的制造专用胎具下
变径制作
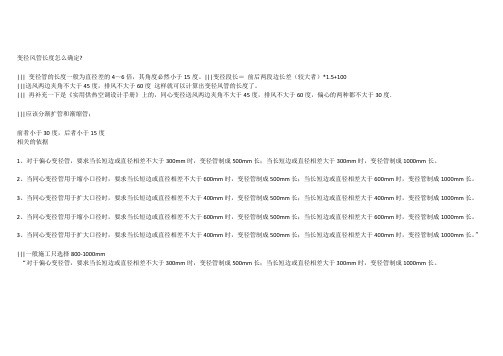
变径风管长度怎么确定?
||| 变径管的长度一般为直径差的4~6倍,其角度必然小于15度。
|||变径段长=前后两段边长差(较大者)*1.5+100
|||送风两边夹角不大于45度,排风不大于60度这样就可以计算出变径风管的长度了。
||| 再补充一下是《实用供热空调设计手册》上的,同心变径送风两边夹角不大于45度,排风不大于60度,偏心的两种都不大于30度.
|||应该分渐扩管和渐缩管;
前者小于30度,后者小于15度
相关的依据
1、对于偏心变径管,要求当长短边或直径相差不大于300mm时,变径管制成500mm长;当长短边或直径相差大于300mm时,变径管制成1000mm长。
2、当同心变径管用于缩小口径时,要求当长短边或直径相差不大于600mm时,变径管制成500mm长;当长短边或直径相差大于600mm时,变径管制成1000mm长。
3、当同心变径管用于扩大口径时,要求当长短边或直径相差不大于400mm时,变径管制成500mm长;当长短边或直径相差大于400mm时,变径管制成1000mm长。
2、当同心变径管用于缩小口径时,要求当长短边或直径相差不大于600mm时,变径管制成500mm长;当长短边或直径相差大于600mm时,变径管制成1000mm长。
3、当同心变径管用于扩大口径时,要求当长短边或直径相差不大于400mm时,变径管制成500mm长;当长短边或直径相差大于400mm时,变径管制成1000mm长。
”
|||一般施工只选择800-1000mm
“对于偏心变径管,要求当长短边或直径相差不大于300mm时,变径管制成500mm长;当长短边或直径相差大于300mm时,变径管制成1000mm长。
薄壁细管加工工艺流程

薄壁细管加工工艺流程一、材料选择与准备在薄壁细管加工的第一步,需要选择适合的材料。
通常,考虑到强度、耐腐蚀性、成本等因素,常用的材料包括不锈钢、铝合金、铜合金等。
在选择好材料后,需要对其进行质量检查,确保其符合加工要求,如检查材料的厚度、直径、表面质量等。
二、管材切割与定长根据加工需求,将选定的管材进行切割,以获得所需长度的管段。
切割过程中,需使用精确的切割设备,如激光切割机、机械切割机等,确保管段的长度准确。
同时,对切割后的管段进行质量检验,检查是否存在毛刺、裂纹等缺陷。
三、管壁薄化技术薄壁细管的关键特性在于其管壁较薄。
因此,需要通过专门的薄化技术来实现。
常用的薄化方法包括机械薄化、化学薄化、激光薄化等。
在薄化过程中,需要严格控制薄化速度和深度,确保管壁均匀减薄,避免产生变形或破裂。
四、精度控制与校直经过薄化处理后,需要对管段进行精度控制和校直。
精度控制主要包括对管段的内径、外径、壁厚等尺寸进行精确测量,确保其符合设计要求。
校直则是通过专门的校直设备,对管段进行弯曲度、直线度等形状调整,确保管段平直度达到要求。
五、表面处理与清洁为了提高薄壁细管的耐腐蚀性和外观质量,需要进行表面处理,如抛光、喷砂、阳极氧化等。
处理过程中,需要选择合适的处理方法和材料,确保处理效果均匀一致。
同时,对处理后的管段进行清洁,去除表面的污渍、油污等杂质。
六、质量检测与评估在完成上述工艺步骤后,需要对薄壁细管进行全面的质量检测与评估。
检测内容包括管段的尺寸精度、形状精度、表面质量、力学性能等。
评估过程中,需采用专业的检测设备和方法,确保检测结果准确可靠。
对于不合格的管段,需进行返工或报废处理。
七、包装与储存管理经过质量检测合格的薄壁细管,需要进行妥善的包装和储存管理。
包装过程中,需使用符合要求的包装材料和方法,确保管段在运输过程中不受损伤。
储存管理则需要控制储存环境的温度、湿度等条件,避免管段受潮、生锈等问题。
同时,对储存的管段进行定期检查和翻动,确保其处于良好的状态。
管道变径制作方法
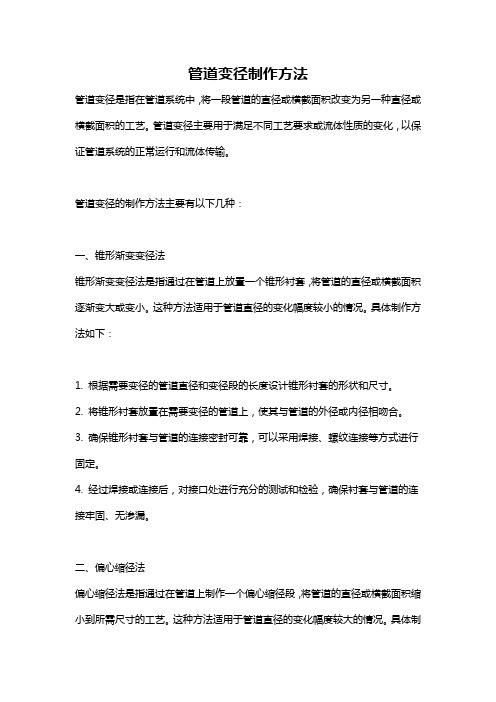
管道变径制作方法管道变径是指在管道系统中,将一段管道的直径或横截面积改变为另一种直径或横截面积的工艺。
管道变径主要用于满足不同工艺要求或流体性质的变化,以保证管道系统的正常运行和流体传输。
管道变径的制作方法主要有以下几种:一、锥形渐变变径法锥形渐变变径法是指通过在管道上放置一个锥形衬套,将管道的直径或横截面积逐渐变大或变小。
这种方法适用于管道直径的变化幅度较小的情况。
具体制作方法如下:1. 根据需要变径的管道直径和变径段的长度设计锥形衬套的形状和尺寸。
2. 将锥形衬套放置在需要变径的管道上,使其与管道的外径或内径相吻合。
3. 确保锥形衬套与管道的连接密封可靠,可以采用焊接、螺纹连接等方式进行固定。
4. 经过焊接或连接后,对接口处进行充分的测试和检验,确保衬套与管道的连接牢固、无渗漏。
二、偏心缩径法偏心缩径法是指通过在管道上制作一个偏心缩径段,将管道的直径或横截面积缩小到所需尺寸的工艺。
这种方法适用于管道直径的变化幅度较大的情况。
具体制作方法如下:1. 根据需要缩径的管道直径和缩径段的长度设计缩径段的形状和尺寸。
2. 在管道上切割出一个缩径段,使其形状为偏心圆锥体。
3. 将缩径段与管道的中心轴偏心,使其与原管道的外径或内径相吻合。
4. 确保缩径段与管道的连接密封可靠,可以采用焊接、螺纹连接等方式进行固定。
5. 经过焊接或连接后,对接口处进行充分的测试和检验,确保缩径段与管道的连接牢固、无渗漏。
三、换径补焊法换径补焊法是指通过在管道上切割出一个换径段,将管道的直径或横截面积变大或变小到所需尺寸的工艺。
这种方法适用于直径较大的管道或需要多次变径的情况。
具体制作方法如下:1. 根据需要变径的管道直径和变径段的长度设计换径段的形状和尺寸。
2. 在管道上切割出一个换径段,并保证切割面平整、光滑。
3. 将换径段与管道的连接密封可靠,可以采用焊接、螺纹连接等方式进行固定。
4. 经过焊接或连接后,对接口处进行充分的测试和检验,确保换径段与管道的连接牢固、无渗漏。
变径管的制作过程

变径管的制作过程嘿,咱今儿就来唠唠变径管的制作过程。
你可别小瞧这变径管,它在好多地方都能派上大用场呢!咱先得准备好材料啊,那管子得质量过硬,不然咋能经得住用呢。
然后就开始动手啦!就好像咱要做一件精美的艺术品一样。
先把管子按照需要的尺寸裁好,这就好比是给它初步塑形。
这一步可得仔细咯,尺寸要是错了,那后面可就全乱套啦。
接着呢,要对管子进行加工处理。
就像是给它梳妆打扮一样,让它变得更精致。
要把边缘打磨光滑,不能有毛刺啥的,不然多不美观,也不安全呀。
然后呢,就到了关键的焊接环节啦。
这就像是给变径管注入灵魂一样。
焊接的时候得特别小心,要保证焊缝牢固,不能有缝隙,不然到时候漏了可就麻烦大了。
你想想,要是在一个重要的管道系统里,变径管出了问题,那不就跟人身体里的血管出了毛病似的,那整个系统都得受影响啊。
焊接完了还不算完事儿,还得再检查检查。
就跟咱出门前照照镜子似的,看看有没有啥地方没弄好。
要是有问题,赶紧修补。
这制作变径管啊,真不是个简单的事儿。
每一个步骤都得认真对待,不能有丝毫马虎。
就跟咱做人做事一样,得踏踏实实,一步一个脚印。
你说这变径管,平时看着不咋起眼,可在很多地方都少不了它呢。
它能让不同管径的管子连接起来,让整个管道系统更加顺畅地运行。
这不就跟咱生活中的那些默默奉献的人一样吗,虽然不显眼,但是却很重要。
咱在制作变径管的时候,得带着那份责任心和耐心,把它做好。
这样它才能在该发挥作用的时候发挥出最大的价值呀。
总之呢,变径管的制作过程可不简单,从选材到最后的检查,每一步都很关键。
咱可不能小瞧了这小小的变径管,它背后可有着大大的学问呢!。
变径制作方法

变径制作方法
变径是一种制作圆锥形或椭圆形标准件的方法,可以通过以下步骤进行:
1.确定变径的形状和大小,需要根据具体要求进行计算和设计。
2.选取适合的材料,一般使用金属材料,如钢板、铝板等。
3.将选定材料切割成一定大小的工件,这一步需要注意切割的精度,以保证后续加工的顺利进行。
4.利用压力机、成形机等设备进行成型,通过调整设备的参数,逐渐将工件加工成预定形状。
5.使用焊接设备进行焊接,将不同直径的管子或板材焊接在一起,使其形成需要的变径过渡形状。
6.进行后期处理,如去除毛刺、打磨、喷漆等,以美观和保护材料。
以上是变径制作的基本步骤,需要根据实际情况作出相应的调整和改进。
为保证质量和安全,应该加强设备维护和人员培训,严格执行操作规程和安全规定。
管道变径制作方法

管道变径制作方法
管道变径是指将管道的直径从一种尺寸改变为另一种尺寸。
下面是一种常见的管道变径制作方法:
1. 准备工作:确定需要变径的管道段长度,选取合适的变径段长度,确保材质和强度符合要求。
准备好所需的工具和设备,如手工工具、焊接设备等。
2. 测量标记:在待变径的管道上进行测量标记,确定所需变径的位置和尺寸。
可以使用卷尺、量角器等工具进行精确测量。
3. 切割:使用适当的切割工具(如锯子、电锯等)沿着测量标记线割断管道。
确保切割面平整,与管道轴线垂直。
4. 加工变径段:将所需直径的变径段与切断的管道两端连接起来。
可以采用焊接、螺纹连接、法兰连接等方法。
5. 焊接:如果需要进行焊接,首先清除管道两端的锈迹和杂质。
然后使用合适的焊接材料(如焊条、焊丝等)进行焊接。
确保焊接点牢固、无漏气现象。
6. 完成:等焊接完全冷却,然后进行检查。
对焊接点进行可视和非破坏性检测,确保焊接质量符合标准。
如果需要,可以进行更进一步的涂漆或防腐处理。
需要注意的是,在进行管道变径制作时,应遵循相关的安全操作规程,确保人身安全和设备安全。
同时,按照相关标准和规范进行操作,保证管道的质量和可靠性。
大小头变径的下料方法

大小头变径的下料方法
那咱就直接唠唠。
先说说步骤哈,你得根据大小头的尺寸要求,精确测量出大端和小端的直径。
这就像裁缝量体裁衣一样,尺寸不准可不行。
然后根据测量结果,在材料上画出下料线,接着用合适的工具进行切割。
注意啦,切割的时候可不能马虎,一定要保证切口平整。
这就好比切蛋糕,要是切得歪歪扭扭,那可就难看啦。
再讲讲安全性和稳定性。
下料的时候可得注意安全,戴上防护手套、护目镜啥的。
万一不小心受伤了,那可疼得要命啊!而且要保证下料的过程稳定,不能让材料晃动,不然尺寸就不准啦。
就像盖房子,地基不稳可不行。
大小头变径的应用场景可多啦!比如在管道连接中,不同直径的管道需要用大小头来过渡。
这就像交通枢纽一样,连接着不同的道路。
它的优势也很明显啊,能实现不同尺寸的连接,让管道系统更加灵活。
而且安装方便,节省时间和成本。
这不是美滋滋吗?
咱再说说实际案例。
我之前见过一个工厂的管道系统,就用了大小头变径。
安装得那叫一个漂亮,管道连接得严丝合缝。
这效果,简直绝了!要是没有大小头变径,那可就麻烦大啦。
我觉得大小头变径下料这事儿吧,只要认真仔细,按照步骤来,就没啥问题。
它真的是个很实用的方法,能在很多场合发挥大作用。
变径制作方法
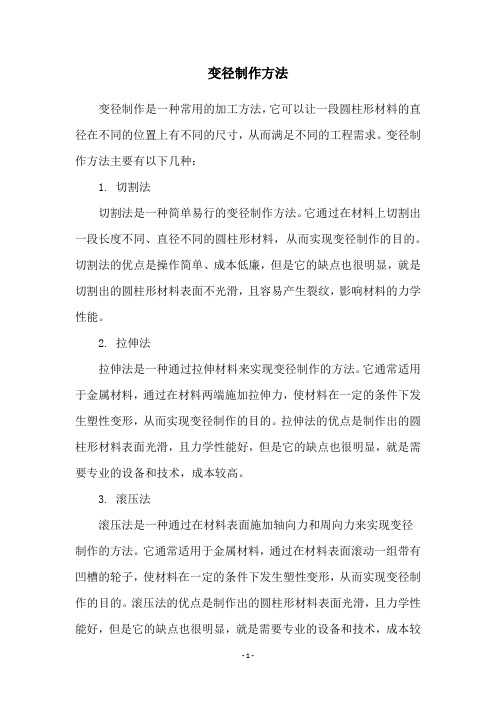
变径制作方法变径制作是一种常用的加工方法,它可以让一段圆柱形材料的直径在不同的位置上有不同的尺寸,从而满足不同的工程需求。
变径制作方法主要有以下几种:1. 切割法切割法是一种简单易行的变径制作方法。
它通过在材料上切割出一段长度不同、直径不同的圆柱形材料,从而实现变径制作的目的。
切割法的优点是操作简单、成本低廉,但是它的缺点也很明显,就是切割出的圆柱形材料表面不光滑,且容易产生裂纹,影响材料的力学性能。
2. 拉伸法拉伸法是一种通过拉伸材料来实现变径制作的方法。
它通常适用于金属材料,通过在材料两端施加拉伸力,使材料在一定的条件下发生塑性变形,从而实现变径制作的目的。
拉伸法的优点是制作出的圆柱形材料表面光滑,且力学性能好,但是它的缺点也很明显,就是需要专业的设备和技术,成本较高。
3. 滚压法滚压法是一种通过在材料表面施加轴向力和周向力来实现变径制作的方法。
它通常适用于金属材料,通过在材料表面滚动一组带有凹槽的轮子,使材料在一定的条件下发生塑性变形,从而实现变径制作的目的。
滚压法的优点是制作出的圆柱形材料表面光滑,且力学性能好,但是它的缺点也很明显,就是需要专业的设备和技术,成本较高。
4. 冷拔法冷拔法是一种通过在材料内部施加拉伸力来实现变径制作的方法。
它通常适用于金属材料,通过将圆柱形材料放入一组带有不同直径的模具中,然后施加拉伸力,使材料内部发生塑性变形,从而实现变径制作的目的。
冷拔法的优点是制作出的圆柱形材料表面光滑,且力学性能好,但是它的缺点也很明显,就是需要专业的设备和技术,成本较高。
总之,变径制作方法是一种常用的加工方法,它可以让一段圆柱形材料的直径在不同的位置上有不同的尺寸,从而满足不同的工程需求。
不同的变径制作方法各有优缺点,需要根据具体的工程需求选择合适的方法。
变径制作方法
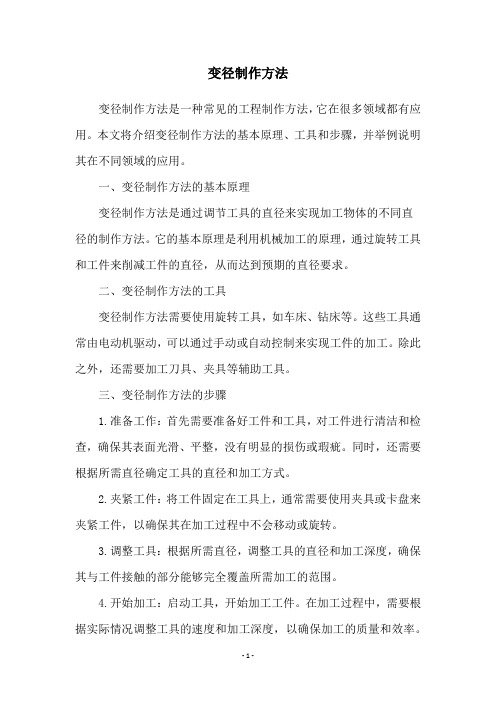
变径制作方法变径制作方法是一种常见的工程制作方法,它在很多领域都有应用。
本文将介绍变径制作方法的基本原理、工具和步骤,并举例说明其在不同领域的应用。
一、变径制作方法的基本原理变径制作方法是通过调节工具的直径来实现加工物体的不同直径的制作方法。
它的基本原理是利用机械加工的原理,通过旋转工具和工件来削减工件的直径,从而达到预期的直径要求。
二、变径制作方法的工具变径制作方法需要使用旋转工具,如车床、钻床等。
这些工具通常由电动机驱动,可以通过手动或自动控制来实现工件的加工。
除此之外,还需要加工刀具、夹具等辅助工具。
三、变径制作方法的步骤1.准备工作:首先需要准备好工件和工具,对工件进行清洁和检查,确保其表面光滑、平整,没有明显的损伤或瑕疵。
同时,还需要根据所需直径确定工具的直径和加工方式。
2.夹紧工件:将工件固定在工具上,通常需要使用夹具或卡盘来夹紧工件,以确保其在加工过程中不会移动或旋转。
3.调整工具:根据所需直径,调整工具的直径和加工深度,确保其与工件接触的部分能够完全覆盖所需加工的范围。
4.开始加工:启动工具,开始加工工件。
在加工过程中,需要根据实际情况调整工具的速度和加工深度,以确保加工的质量和效率。
5.完成加工:在加工完成后,停止工具,检查工件的直径和表面质量,确保其符合预期要求。
如果需要进一步加工,可以重复上述步骤,直到达到所需的直径和表面质量。
四、变径制作方法的应用变径制作方法在工业、制造、建筑等领域都有应用。
以下是一些典型的应用场景:1.机械制造:在机械制造中,变径制作方法常用于制作轴、齿轮、轮毂等零部件,以满足不同机械设备的要求。
2.建筑工程:在建筑工程中,变径制作方法常用于制作管道、钢筋等建筑材料,以满足不同建筑结构的要求。
3.医疗设备:在医疗设备制造中,变径制作方法常用于制作医疗器械、假肢等产品,以满足不同患者的需求。
4.艺术品制作:在艺术品制作中,变径制作方法常用于制作雕塑、装饰品等产品,以满足不同艺术家的创作要求。
小直径薄壁变径段的制作
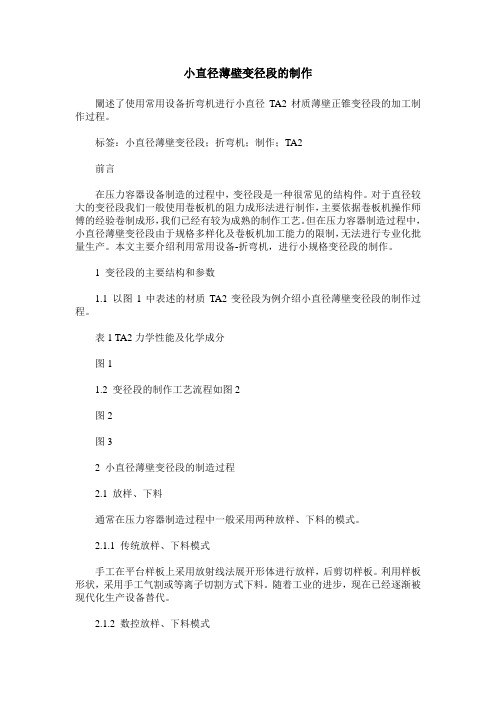
小直径薄壁变径段的制作闡述了使用常用设备折弯机进行小直径TA2材质薄壁正锥变径段的加工制作过程。
标签:小直径薄壁变径段;折弯机;制作;TA2前言在压力容器设备制造的过程中,变径段是一种很常见的结构件。
对于直径较大的变径段我们一般使用卷板机的阻力成形法进行制作,主要依据卷板机操作师傅的经验卷制成形,我们已经有较为成熟的制作工艺。
但在压力容器制造过程中,小直径薄壁变径段由于规格多样化及卷板机加工能力的限制,无法进行专业化批量生产。
本文主要介绍利用常用设备-折弯机,进行小规格变径段的制作。
1 变径段的主要结构和参数1.1 以图1中表述的材质TA2变径段为例介绍小直径薄壁变径段的制作过程。
表1 TA2力学性能及化学成分图11.2 变径段的制作工艺流程如图2图2图32 小直径薄壁变径段的制造过程2.1 放样、下料通常在压力容器制造过程中一般采用两种放样、下料的模式。
2.1.1 传统放样、下料模式手工在平台样板上采用放射线法展开形体进行放样,后剪切样板。
利用样板形状,采用手工气割或等离子切割方式下料。
随着工业的进步,现在已经逐渐被现代化生产设备替代。
2.1.2 数控放样、下料模式直接使用数控机床软件进行放样,或使用CAD软件绘制。
在数控水切割等设备上不留余量进行下料(如果是用气割或等离子切割下料的话,还需要留氧化区余量),此工作模式效率高、节约料,且劳动强度低。
通过计算机放样得出如图3所示扇形。
本次放样使用的是AutoCAD,下料实际采用数控水切割下料成形。
具体作图过程不再赘述。
经过对此小规格锥体的形体及折弯机的加工特点分析,下料必须采用至少二拼一的方法来进行制作。
2.2 刨边按图2中描述的坡口形式,刨直边坡口成形。
2.3 压制2.3.1 划线首先在板料上利用手工作图的方法将内外弧做16等分(等分越多,成品曲面越圆滑),并按图4所示划7条母线。
制作简易角度样板。
2.3.2 折弯机压制调试折弯机各参数,采用自由弯曲法按母线逐条进行压制,以158°样板检查,压弯角度成形,见图5。
铁皮变径的下料方法

铁皮变径的下料方法
铁皮变径是一种常见的加工方法,它可以将铁皮的直径变小或变大,
以适应不同的需求。
下面介绍一种常用的铁皮变径的下料方法。
首先,需要准备好所需的工具和材料,包括铁皮、尺子、铅笔、剪刀、锤子和钳子等。
然后,根据需要变径的铁皮的直径和长度,用尺子和
铅笔在铁皮上画出所需的尺寸和形状。
接下来,根据所画的尺寸和形状,用剪刀将铁皮剪成相应的形状。
在
剪的过程中,需要注意保持剪切线的平直和整齐,以确保铁皮的变径
效果。
然后,将剪好的铁皮放在一个平整的硬表面上,用锤子和钳子将铁皮
的边缘轻轻敲打和弯曲,以使其变成所需的形状和尺寸。
在敲打和弯
曲的过程中,需要注意力度的掌握,以免将铁皮弄坏或变形。
最后,检查铁皮的变径效果是否符合要求,如有需要,可以进行微调
和修整。
完成后,将铁皮清洗干净,以便后续的使用。
总之,铁皮变径是一种常见的加工方法,它可以将铁皮的直径变小或
变大,以适应不同的需求。
在下料和加工的过程中,需要注意保持剪切线的平直和整齐,以及力度的掌握,以确保铁皮的变径效果。
铁皮变径的下料方法

铁皮变径的下料方法
铁皮变径是一种常见的加工方法,它可以将一段铁皮变成不同直径的圆形或圆锥形。
下料是铁皮变径的第一步,下面我们来介绍一下铁皮变径的下料方法。
我们需要准备好需要加工的铁皮和下料工具。
下料工具一般有手动下料机和自动下料机两种。
手动下料机需要手动调整下料刀的位置和角度,而自动下料机可以通过电脑程序自动调整下料刀的位置和角度。
接下来,我们需要测量铁皮的直径和长度,确定需要下料的位置和角度。
一般来说,下料位置应该在铁皮的中心位置,下料角度应该与铁皮的切口垂直。
然后,我们需要将铁皮固定在下料机上,调整下料刀的位置和角度。
在调整下料刀的位置时,应该注意下料刀的切口应该与铁皮的切口垂直,以保证下料的精度和质量。
我们可以开始下料了。
在下料的过程中,应该保持下料刀的速度和力度稳定,以避免铁皮变形或者下料不均匀的情况发生。
同时,应该注意下料刀的切口应该与铁皮的切口垂直,以保证下料的精度和质量。
铁皮变径的下料方法是一项需要技巧和经验的工作。
只有掌握了正确的下料方法,才能够保证下料的精度和质量,从而满足客户的需
求。
- 1、下载文档前请自行甄别文档内容的完整性,平台不提供额外的编辑、内容补充、找答案等附加服务。
- 2、"仅部分预览"的文档,不可在线预览部分如存在完整性等问题,可反馈申请退款(可完整预览的文档不适用该条件!)。
- 3、如文档侵犯您的权益,请联系客服反馈,我们会尽快为您处理(人工客服工作时间:9:00-18:30)。
e C N H O
2 . 2刨边 按图 2中描述 的坡 口形式 , 刨 直边坡 口成形 。 2 - 3压制 2 . 3 . 1划线
首先在 板料 上利用 手工作 图 的方法将 内外 弧做 1 6 等分 ( 等 分越 多, 成 品 曲面越 圆滑 ) , 并按 图 4 所示划 7 条 母线 。制作简 易角度样板 。
工 业 技 术
2 0 1 3 年 第3 4 期 l 科技创 新 与应用
小直 径 薄壁 变径段 的制作
李 益 生 范 翰
( 宝鸡钛业股份 有限公 司, 陕西 宝鸡 7 2 1 0 1 4 ) 摘 要: 阐述 了使用常用设备折 弯机进行 小直径 T A 2 材质薄壁 正锥变径段的加工制作过程。 关 键词 : 小直 径 薄壁 变径段 ; 折 弯机 ; 制作 ; T A 2
前言
在 压力容器 设备制造 的过程 中 , 变 径段是一种 很常见 的结构件 。 对 于直 径较 大 的变径段 我们 一般 使用卷 板机 的阻力 成形 法进 行制作 , 主 要依据卷板机操作师傅的经验卷制成形 ,我们已经有较为成熟的制作 工艺。 但在压力容器制造过程中, 小直径薄壁变径段 由于规格多样化及 卷板 机加工能 力的限制 , 无 法进行专业 化批量 生产 。 本文 主要介绍利用 常用设备— 折弯机, 进行小规格变径段的制作。 1变径段 的 主要 结构和参数 1 . 1以 图 1 中表述 的材质 T A 2 变 径段为 例介绍 小直径 薄壁 变径段 的制 作过程 。 袁1 T A 2力学 陛能及化 学成分
项目 抗 拉强度 延伸率 Y i
A / 5 6
2 . 1放样 、 下料 通常在压力容 器制造过程 中一般采用两 种放样 、 下料 的模 式。 2 . 1 . 1传统放 样 、 下料模式 手工在平 台样 板上采 用放射线 法展开 形体进行放 样 , 后剪切 样板 。
利用样板形状,采用手工气割或等离子切割方式下料。随着工业的进 步, 现在已经逐渐被现代化生产设备替代。 2 . 1 . 2数控放 样 、 下料模式 直接使用数 控机床 软件进行放 样 , 或使用 C A D软件 绘制 。在 数控 水切 割等设 备上不 留余 量进 行下料 ( 如果是用气 割或等 离子切 割下料 的话 , 还需 要 留氧化 区余 量 ) , 此工 作模 式效 率高 、 节约 料 , 且 劳动强 度
一
8 5 一
科技创新与应用 l 2 0 1 3 年 第 3 4 期
工 业 技 术
西 门子 6 S E 7 0系列常 见故 障维修 技巧
何 寒 冰
( 安徽 省马 鞍 山 市 马钢 第 四钢 轧 总 厂 , 安徽 马 鞍 山 2 4 3 0 0 0 ) 摘 要: 变频 调 速是 现代 工 业应 用较 为理 想 的调 速 方 式 , 在 改造 工 艺流 程提 高 自动化 水 平 方 面起 着 重要 作 用 。西 门子 6 S E 7 0系 列变频器是应用较为广泛的一种 变频 器, 了解其常见故障维修方法能帮助技术人员更快更好 的解决故障, 保证 生产过程正常进 行 。文 章就 西 门子 6 S E 7 0系列 常见故 障维修 技 巧进 行 了探 讨 , 供 维修人 员借鉴 。 关 键词 : 变频 器 ; 6 S E 7 0 ; 常见 故 障 ; 维修 技 巧
/ \
/ /
\ \
/ . f l f l
f l /
一
\ \ \
1
一
f
Hale Waihona Puke 图4 图 1 图5
1 . 2变径段 的制作工 艺流程如 图 2
图2
^
2 . 3 . 2折弯 机压制 调试折弯机 各参数 , 采用 自由弯 曲法 按母线逐 条进行 压制 , 以1 5 8 。 样板检查 , 压弯 角度成形 , 见图 5 。 折弯 时发现所划母线 数量偏1 锥体棱 角明显 。 将母 线的数量增加 1 倍, 到3 2 条时 , 曲面近 圆滑 。 2 . 4焊接 依据 J B / F 4 7 4 5 - 2 0 0 2 ( ( 钛 制焊 接容 器 》 标 准选 用 S T A 2 R焊丝 , 将两 半锥 体组焊 成形 。 表2 S T A 2 R焊 丝化学成分
、
2 - 5测量
h、—噩—
组焊 、 手 工校形后 的锥体 大 、 小端 口内径及外 展实 际测量 得 出表 3 中的尺寸 : 表 3锥体 大、 小端 口内径及外展 实测
图3
2小 直径薄壁 变径段 的制造过程
由表 1 可以看出, 大小端 口尺寸在公差范围内, 符合 G B 1 5 0 . 4 - 2 0 1 0 中规定 的范 围 , 不影响下工 序的组装 。 2 . 6 R T检测 按J B t T 4 7 3 0 . 2 - 2 0 0 5 对焊缝 进行 1 0 0 %R T检测 , 合格 级别 I I 级, 未
,
项目 抗拉强度 延伸率 Y i
R a A / %
F
e
C
N
H
O
s T A 2 R
/
/
/
≥4 0 0
≥2 5 余量 ≤0 . 3 0 ≤ O . 0 8 ≤0 . 0 3 ≤O . O 1 5 ≤O . 2 5
\
\
低。
T A 2
≥4 0 0
通过计算机 放样得 出如 图 3 所示扇形 。 本次放样使 用的是 A u t o C A D, 下料 实际采用数 控水切割下料 成形 。 具体 作 图过程 不再赘述 。 ≥2 5 余量 ≤0 . 3 0 ≤0 . 0 8 ≤0 . O 3 ≤0 . 0 1 5 ≤o . 2 5 经过对此小 规格锥体 的形 体及折 弯机 的加工特点 分析 ,下料 必须 采用 至少二 拼一的方法来 进行制作 。