超声波振动精密切削GFRP的实验研究
超声波在精密加工中的应用研究

超声波在精密加工中的应用研究超声波技术是一种在材料加工过程中非常重要的工艺技术,它可以增强处理效果,优化工件质量,缩短加工周期,降低能源消耗。
近年来,随着科学技术的进步和工业化生产的不断发展,超声波技术在精密加工领域发挥的作用越来越大。
本文将探讨超声波在精密加工中的应用研究。
一、超声波在金属加工中的应用1. 拉伸加工中的应用超声波在拉伸加工中的应用较为普遍,它可以使金属材料在最小的变形条件下达到极限变形程度。
超声波是基于共振原理,在振幅足够大时,其作用力可以远远超过传统的拉伸加工。
目前,超声波拉伸加工已广泛应用于锻造、压铸、拉伸等金属加工领域。
2. 表面处理中的应用超声波在金属表面处理中的应用主要包括超声波磨料、超声波打磨、超声波除锈等。
这些处理方式可以使金属表面更加平滑,减少金属表面的缺陷,提高金属表面的质量和稳定性。
3. 金属切削加工中的应用超声波在金属切削加工中的应用与其他技术相比具有独特的优势,它可以提高加工质量,缩短加工周期,降低加工成本等。
目前,超声波在金属切削领域已得到广泛应用,如超声波加工中心、超声波切割机、超声波皮带磨削机等。
二、超声波在非金属加工中的应用除了在金属加工中广泛应用之外,超声波技术在非金属加工领域中也发挥了不同的作用。
1. 塑料加工中的应用超声波技术在塑料加工领域中具有广泛的应用前景,主要包括超声波焊接、超声波水处理和超声波清洗等。
这些应用可以提高产品的品质和稳定性,同时缩短生产周期。
2. 陶瓷加工中的应用超声波在陶瓷加工中的应用主要包括超声波破碎、超声波磨料和超声波鼓磨等。
这些应用可以提高陶瓷工件的质量和精度,同时降低加工难度和成本。
三、超声波在医疗领域中的应用除了在工业领域中应用之外,超声波技术在医疗领域中也具有广泛的应用。
超声波在医疗领域中的优点在于非侵入性、无放射性、低成本和可重复使用等方面。
目前,超声波医疗设备已非常普及,主要包括超声波诊断仪、超声波手术机和超声波治疗仪等。
超声振动辅助磨削-脉冲放电复合加工磨削力模型研究
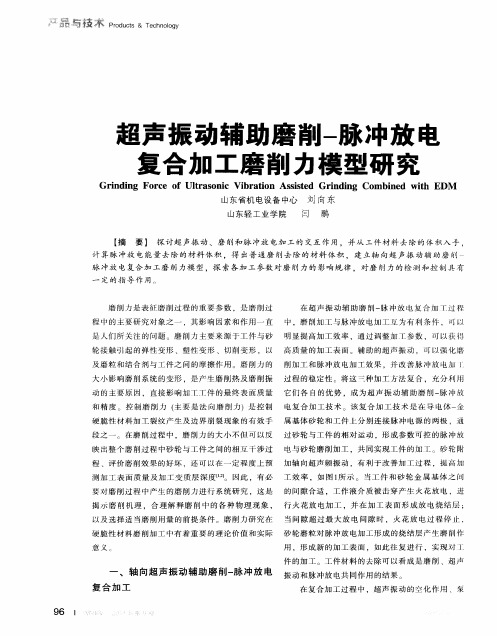
所 测 加 工 表 面 质 量 及 加 工 变 质 层 深 度 _. 因 此 ,有 必 工 效 率 , 如 图 1 示 。 当 工 件 和 砂 轮 金 属 基 体 之 间 1。 2 1 要 对磨 削 过 程 中产 生 的磨 削 力 进 行 系统 研 究 ,这 是 的 间 隙 合适 ,工作 液 介 质被 击 穿 产 生 火 花 放 电 ,进 揭示 磨 削 机 理 ,合 理 解 释 磨 削 中 的 各 种 物 理 现 象 , 行 火 花 放 电加 工 ,并 在 加 工 表 面 形 成 放 电 烧 结 层 ; 以及 选 择 适 当 磨 削 用 量 的前 提 条 件 。磨 削 力 研 究 在 当 间 隙 超 过 最 大 放 电 间 隙 时 ,火 花 放 电过 程 停 止 , 硬 脆 性 材料 磨 削 加 工 中有 着 重 要 的 理 论 价 值 和 实 际 砂 轮磨 粒对 脉 冲 放 电 加 工形 成 的 烧 结 层 产 生 磨 削 作
论 ,单位 时间内放 电痕熔化体积为 :
W
V=
K
c ( T P , C ( +q p o q p 一 )+ p,
式 中 , 为单 位 时 间 内 ,工 件 吸 收 的 电火 花 放
电 能 量 ;C为 热 容 量 ;P 密 度 ; 为 熔 点 ; 为 原 为
压 、放 电 电 流 和放 电 持 续 时 间 。 一 个 加 工 周 期 内 ,
等 ,在 建 立磨 削力 数学模 型 时 ,把 磨 削力分 成 切 屑 变 形 力 和 摩 擦 力 两 项 。磨 削力 可 写 成 如 下 形
式:
= +
电火 花 加 工 放 电总 能 量 为 :
Q∑ “ ) d = oi t )
液 等 密 切 相 关 ,通 过 大 量 的 试 验 总 结 获 得 。 在 电火 花 加 工 中 , 电极 与 工 件 材 料 的物 理 特
超声振动辅助磨削技术应用研究进展

合加工性能。
术
发展趋势
❖超声振动辅助磨削技术是一个新的研究领域,
其加工机理、加工方法及加工装置的研究还有待
于深入和完善。
发 展 趋 势
发展趋势
高效稳定超声振动系统研究
现有的实验及实用振动切削加工系统输出功率小
、能耗高,因此,期待实用的大功率振动系统到
发 展
目前为止,输出能量为4kW的振动系统已研制出
超声振动辅助磨削技术应用研 究进展
内容
1
前言
2
发展回顾
3
研究现状
4
发展趋势
前言
不足
概念
优势
前言
❖航空、电子、光学及通信工业的新技术迅猛发展,对 硬脆性材料、难加工材料和新型先进材料的需求日益增 多,对关键零件的加工效率、加工质量和加工精度提出 了更高的要求。
前言
❖传统加工方法是超精密磨削和单点金刚石切削; ❖产生较大的磨削力以及磨削热,引起工件表面、亚表面损 伤以及砂轮寿命低;
优点 提高材料去除率,延长工具的寿命
UV优AM点
提高脆性与研性域发生转变的临界切削深度, 实现脆性材料的延性域加工,使复杂光学元件 表面超精密加工可以不须采用磨削和抛光的方 法完成加工。
发展回顾
超 声
首先是应用在材料的切削加工
振
动 1927年,R.W.Wood和A.L.Loomis发表了有关
磨
削 超声波加工的论文,超声加工首次提出。
维 超
期分离现象,磨削刃作用时间变短,摩擦系数大幅
声 振
度降低,从而促使磨削力大幅度减小,材料去除率
动 磨
显著增大。
削
技
术
研究现状
轴向振动使不同磨削刃的切削轨迹互相干涉而产生
超声波加工机床在精密机械加工中的应用研究

超声波加工机床在精密机械加工中的应用研究超声波加工机床是一种利用高频振动将声波能量转化为机械能的专用设备。
它在精密机械加工领域具有广泛的应用,可以用于加工各种材料,如金属、陶瓷、塑料等。
本文将对超声波加工机床在精密机械加工中的应用进行深入研究,并探讨其优势和发展前景。
一、超声波加工机床的基本原理超声波加工机床利用高频振动的原理进行加工,其基本原理可以概括为以下几点:1.1 超声波传导:超声波在材料中的传导速度较高,使得能量传递到工件表面时能够迅速产生切削效果。
1.2 液体介质:超声波加工通常是在液体介质中进行的,液体可有效传导声波,减少工件表面的摩擦和磨损。
1.3 脉冲能量:超声波加工机床通常以脉冲形式输出能量,利用脉冲能量的瞬时冲击力来实现加工效果。
二、超声波加工机床在精密机械加工中的应用领域2.1 集成电路加工:超声波加工机床可以用于集成电路的微细加工,例如微孔加工、蚀刻、刻蚀等。
2.2 珠宝首饰加工:超声波加工机床在珠宝首饰加工中具有较大的优势,可以用于切割、打磨、雕刻等工艺。
2.3 高硬度材料加工:超声波加工机床可以用于高硬度材料的切削和表面处理,如金刚石、硬质合金等。
2.4 医疗器械加工:超声波加工机床可以用于医疗器械的加工和组装,保证产品的精度和质量。
三、超声波加工机床的优势超声波加工机床相比传统机床在精密机械加工中具有以下几个优势:3.1 高精度:超声波加工机床可以实现精细加工和高精度加工,提高产品质量和精度。
3.2 低热影响区:超声波加工机床所产生的热影响区较小,不会对工件产生过多的热变形和残余应力。
3.3 切削力小:超声波加工机床采用脉冲形式输出能量,切削力小,不易造成刀具磨损和工件表面损伤。
3.4 特殊材料加工:超声波加工机床可以用于加工各种特殊材料,如玻璃、陶瓷等,具有广泛的适应性。
四、超声波加工机床的发展前景超声波加工机床作为一种高效、高精度的加工设备,在精密机械加工领域有着广阔的应用前景。
超声振动减摩性能的实验研究及理论分析

图 1 振幅测量装置图
将实验测得的数据进行分析 、整理 ,画出电压 不同时振幅随频率变化的曲线 ,见图 2 。
中国机械工程第 15 卷第 9 期 2004 年 5 月上半月
数 。可调节标尺与铰链的水平距离为 L ( L = 305mm) 。此时 ,压电振子与可倾斜平板之间的 静摩擦系数为 f = tanθ= H/ L 。
衡量减摩性 能 的 主 要 参 数 之 一 是 摩 擦 系 数 。 为此 ,我们测量压电振子在超声振动状态下与其 他零件组成摩擦副时 ,其摩擦系数随振幅及频率 的变化趋势 。
摩擦系数测量装置见图 3 。将压电振子放置
1. 压电振子辐射端面 2. 压电振子 3. 可倾斜平面 4. 可调节标尺 图 3 摩擦系数测量装置图
1 实验研究
1. 1 压电振子基本参数及辐射端振幅的测量 实验的核心元件是压电振子 ,本文以典型的
中心紧固型郎之万振子为研究对象 ,首先测量压 电振子的基本参数 。测量仪器为精密阻抗分析 仪 ,型号为 HP4294A 。测量结果见表 1 。
收稿日期 :2003 - 05 - 19 基金项目 :国家自然科学基金资助项目 (50175047)
与特定的工作表面间的摩擦系数的变化规律 ,通过有限元法计算压电振子
的振动模态 ,分析超声振动的减摩机理 ,以便进行适当的结构设计 ,利用超
声振动的减摩性能制造出超声波悬浮轴承 。研究证明 ,超声振动具有良好 的减摩性能 ,压电振子处于纵向振动模态时减摩效果最好 。
吴博达 教授
关键词 :超声振动 ;压电振子 ;减摩 ;摩擦系数
提取的模态共有 4 个 ,当频率 ω = 20. 218kHz 时 , 其模态为纵向振动模态 。
表 2 压电振子相关参数
超声振动切削报告

超声振动切削报告关键信息项:1、超声振动切削的原理和技术特点原理:____________________________技术特点:____________________________2、应用领域和优势应用领域:____________________________优势:____________________________3、设备和工具要求设备类型:____________________________工具规格:____________________________4、切削参数和工艺控制切削参数:____________________________工艺控制要点:____________________________ 5、质量检测和评估标准检测方法:____________________________评估标准:____________________________6、安全注意事项和防护措施安全风险:____________________________防护措施:____________________________11 超声振动切削的原理超声振动切削是一种在传统切削加工基础上引入超声振动的先进加工技术。
其原理是通过在刀具或工件上施加高频振动,使切削过程中的切削力、切削热等发生显著变化,从而改善切削性能。
具体来说,超声振动使得刀具与工件之间的接触状态发生周期性改变,实现了断续切削,减少了刀具与工件之间的摩擦和粘结,降低了切削力和切削温度。
111 技术特点超声振动切削具有以下显著特点:1111 降低切削力由于断续切削和摩擦的减少,切削力大幅降低,这有助于减少机床的负荷,提高加工精度和表面质量。
1112 减小切削热振动切削过程中的热量产生减少,有利于防止工件的热变形和热损伤,提高加工精度。
1113 改善表面质量能够获得更光滑、更低粗糙度的加工表面,提高零件的使用性能和寿命。
超声振动辅助铣削加工实验研究
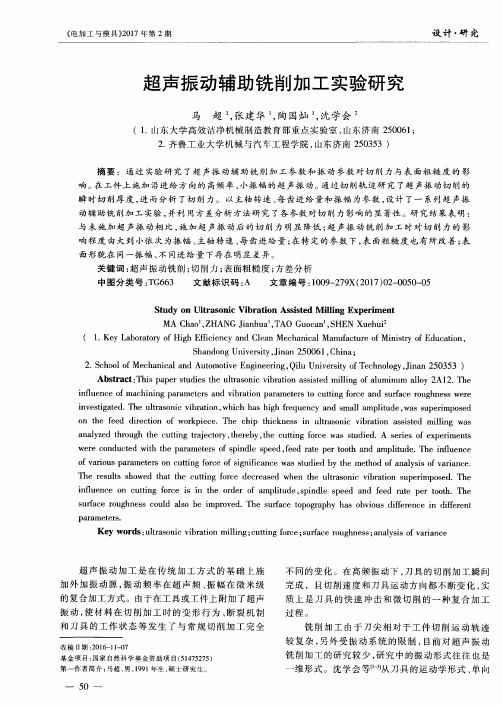
摘 要 :通过 实验研 究 了超 声振 动辅 助 铣 削加 工参 数 和振 动参 数 对 切 削 力 与表 面粗 糙 度 的影 响。 在 工件 上施 加 沿进给 方 向的 高频 率 、 小振 幅的 超 声振 动 。 通 过切 削轨 迹研 究 了超 声振动 切 削的 瞬时切 削厚度 , 进 而 分析 了切 削力 。 以主轴 转速 、 每 齿 进给 量 和振 幅 为参 数 , 设计 了一 系列超 声振 动 辅助 铣 削加 工 实验 , 并 利 用方 差分 析 方法研 究 了各参 数 对切 削 力影响 的显 著性 。研 究结果表 明 : 与 未施加 超 声振 动相 比 , 施 加超 声振 动后 的切 削力 明显 降低 ; 超 声振 动 铣 削加 工 时 对切 削力 的影 响程 度 由 大到 小依 次 为振 幅 、 主轴 转速 、 每 齿进 给 量 ; 在特 定的 参数 下 , 表 面粗糙 度 也 有所 改善 ; 表
高频超声椭圆振动切削切削力分析

高频超声椭圆振动切削切削力分析0前言振动切削技术由日本宇都宫大学隈部淳一郎教授于20 世纪50 年代初期提出,根据刀具振动的轨迹,可分为普通振动切削和椭圆振动切削。
椭圆振动切削技术是日本学者社本英二等最早提出的,具有一系列优点,能有效降低切削力,提高表面加工精度,延长刀具寿命,特别适合精密和超精密加工领域。
传统振动切削加工中刀具后刀面与工件已加工表面的高频摩擦使刀具承受交变拉压应力,导致刀具疲劳崩刃。
超声椭圆振动切削技术使刀具以椭圆振动轨迹对工件进行切削,避免了刀具后刀面与已加工表面的摩擦,有效抑制了刀具的崩刃破损同时,将刀具前刀面与切屑之间有害的摩擦力变为有利的切削力,增加了刀具的剪切角,降低了切削过程中的吃刀杭力,提高了加工精度。
1超声椭圆振动切削机理1.1传统超声振动切削超声振动切削是在普通切削加工的基础上利用超声振动驱动装置激励切削刀具产生一个附加的强迫振动(通常,频率为20~40kHz,振动幅度为5~20um),使刀具形成一种脉冲式往复变速断续切削过程。
断续切削具有切削力明显下降、工件表面残余应力减小、切削区温度下降、有效抑制积屑瘤的产生、明显提高加工质量等优点。
但是,普通超声振动切削的往复断续切削过程也有负面影响,即切削刀具在切削过程中要承受一个随超声振动不断变化的交变应力。
如图1(a)所示当刀具与工件接触进人切削状态时,刀具要承受主切削力N r、吃刀抗力N f、切屑在前刀面上流动产生的摩擦力F r、已加工工件表面与刀具后刀面的摩擦力F f,从而使刀具承受切削合力F;图1(b)所示,当刀具与工件处于分离状态时,刀具只承受吃刀抗力N f和已加工工件表面与刀具后刀面的摩擦力F f,这时刀具承受的切削力合力F使刀具刀尖处承受一个向上的拉应力,产生拉应力集中区,正是由于刀具刀尖处承受的随超声振动高频变化的交变拉压应力,使刀具很容易在短时间内发生疲劳破损,对于天然金刚石、PCD、CBN 这类硬度高、抗弯强度差的刀具材料,刀具刀尖尤其是前刀面会在很短的时间内发生崩刃现象。
超声振动辅助磨削技术研究进展ppt课件

磨 界上首次提出并实现采用超声频调制电火花与
削
技 超声波复合的研磨、抛光加工技术。与纯超声
术
发 波研磨、抛光相比,效率提高5倍以上,并节约
展 回
了大量的金刚石磨料。
顾
发展回顾
超 声
20世纪80年代后期,天津大学李天基等人在
振 动
高速磨削的同时对磨头施以超声振动,提出了
磨 高效的超声磨削复合加工方法,效率比传统的
削 技
主要由垂直方向粗糙度决定,通过改变加工参数
术 方法很难显著降低表面粗糙度。
研究现状
一 维
Denkena研究发现在轴向振动磨削过程中,砂轮
轴 轴向分布的不同磨粒对工件起重复研磨作用,从
向
超 而能获得高质量加工表面。还指出使用普通粒径
声
振 大小的砂轮磨粒进行超声波磨削时,超声波辅助
动 磨
作用对表面质量不会有积极影响。
削
技 1945年,L.Balamuth申请了关于超声加工的
术
发 专利。
展
回
顾
发展回顾
超 声
20世纪50~60年代日本学者隈部淳一郎对振
振 动
动切削进行系统研究,提出了振动切削理论,
磨 并成功实现了振动磨削加工 。
削
技 20世纪60年代,英国Hawell原子能研究中心
术
发 的科学家发明了新的超声磨削复合加工方法。
超声振动辅助磨削技术研究 进展
内容
1
前言
2
发展回顾
3
研究现状
4
发展趋势
前言
不足
概念
优势
前言
航空、电子、光学及通信工业的新技术迅猛发展, 对硬脆性材料、难加工材料和新型先进材料的需求 日益增多,对关键零件的加工效率、加工质量和加 工精度提出了更高的要求。
超声振动辅助铣削仿真及表面性质研究

超声振动辅助铣削仿真及表面性质研究现代科学技术的迅猛发展促使着新型材料领域的兴起,新型材料在市场中所占的地位越来越突出。
特别是航天、航海、电子、国防等现代工业部门对于具有高性能的新型材料更是迫切需求。
这些新材料具有高的应力应变、高硬度、高脆性、耐磨耐腐蚀等特点,更能适应现代尖端产品的性能。
虽然这些材料有着良好的机械性能,却给传统制造业带来了极大的挑战。
新的制造技术也在新型材料的驱动下不断涌现。
超声振动辅助加工就是新型制造技术当中的一个主要代表。
超声振动辅助加工是将高频率、小振幅的超声简谐运动与传统的制造技术相结合的一种特种加工技术。
超声振动辅助加工按照振动施加的方式可以划分成单方向振动辅助加工和正交式振动辅助加工。
通过施加超声振动,在加工的过程当中改变了刀具和工件两者之间的接触方式,促使切削力和表面质量均有一定程度的改善。
切削过程中由于刀具在工件上进行高频率的简谐运动,工件表面上会被加工出具有一定规律的表面微观织构,这些织构随着加工参数和振动参数的不同会呈现出很大的差异,同时也会对表面的性能产生很大的影响。
本文利用有限元仿真和实验研究的方法分析了超声振动辅助铣削加工的过程以及切削表面形貌和性质。
分析了超声振动辅助铣削加工的运动轨迹和受力情况。
利用切削仿真软件AdvantEdge对加工过程仿真进行了具体的实现。
包括加工参数的设置,材料本构参数、失效参数以及刀具和切屑接触模型的设置。
将超声振动加工与传统切削过程相对比,对比分析研究了切削加工中应力、应变、温度、切削力等参数。
变幅杆是超声振动辅助加工过程中非常关键的单元。
为了保证其在使用过程中的稳定性能,对变幅杆进行了振型分析和扫频分析。
振型分析获得变幅杆的不同阶共振频率和模态响应。
扫频分析研究其在外加超声振动载荷下的位移变化情况,提取变幅杆的端面位移,最终求解出变幅杆的放大倍数。
对铝合金2A12、45钢、Ti-6Al-4V三种材料进行超声振动辅助铣削实验。
超声振动切削报告
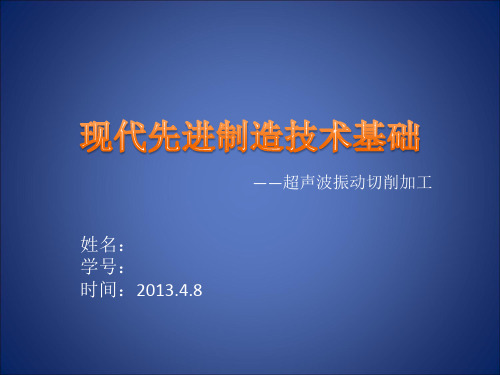
超声波振动切削与传统切削刀具磨 损的比较
切削速度: 90m/min 进给量: 0.1mm/rev 切削时间: 20min 刀具材料: CBN 加工材料: 低合金钢
超声波振动切 削与传统切削 切削力的比较
超声波振动切削与传统切削加工表 面粗糙度的比较
加工零件成品
6、结论
• 超声波振动在很大程度上改善了传统的加工方法, 在各种非金属脆硬材料加工方面得到广泛应用,取 得了卓越的成绩。大量的试验研究和加工结果表明, 超声振动加工有能量集中、瞬间作用、快速切削的 特性,能有效地改变传统加工的切削机制,具有独 特的加工工艺效果。 • 和源远流长的切削技术相比,超声振动切削技术在 短暂的发展历程中已经取得了令人欣慰的成绩,在 工业的不同方面得到了的应用。随着社会对材料提 出更高的要求, 随着新型难加工材料的不断出现, 超声加工技术将得到更大的发展, 有理由相信这门 技术的未来是很有前景的。
• 近年来, 科研人员尝试用超声振动切削来 加工上述难加工材料,取得了一定的效果。 实验表明,超声振动切削技术在相当大的 程度上可以解决难加工材料切削中很多关 键的技术问题,比传统切削技术有明显的 优势。
Hale Waihona Puke 、超声波振动切削技术基本概念超声波振动切削技术是把超声波振动的力 有规律地加在刀具上,使刀具周期性地切 削和离开工件的加工技术,是结合超声波 技术和传统切削工艺的一种新型切削技术。
2、超声波振动切削技术基本原理
• 超声波振动切削的基本原理就是通过在切削刀具上施加某 种有规律的、可控的振动,使切削速度、背吃刀量发生周 期性的改变,从而得到特殊的切削效果的方法。
振动切削实验设备
3、振动的方式
切 向 振 动
径 向 振 动
超声波振动辅助多线锯加工设备开发及实验研究

超声波振动辅助多线锯加工设备开发及实验研究目前单、多晶硅等光电子材料已大量采用多线锯进行切片加工,但由于设备以及加工工艺复杂性,加工的晶片容易产生翘曲、崩边,钢丝也容易断线等现象,急需开发一种新型的加工工艺来解决传统多线切割机的加工问题,因此,研究振动辅助多线切割的加工工艺与设备具有重要意义。
振动辅助多线切割是通过振动的作用改善切割时磨粒的运动状态及切削性能,能很好的解决普通多线切割的排屑、散热、断线等问题,使其加工得到的切片表面质量更高,损伤层的厚度大大降低,为实现更高精度的多线锯加工提供了1条新的方法。
本课题通过多线切割的原理开发了一种新型多线切割加工设备,该设备搭载了超声波振动辅助装置,可很好的完成振动辅助多线切割任务,并对K9光学玻璃进行切割实验,实验结果验证了振动辅助多线锯的加工效果。
本文的主要工作和成果如下:1、介绍了课题的研究背景和意义、多线切割机的工作原理和其走线原理图、游离磨料线切割和固着磨料线切割的加工机理、国内外多线锯加工设备的研究现状、超声波振动辅助多线锯切割的理论基础。
2、根据实验要求的多线切割机设计指标和设计要求,设计出了具有超声波振动辅助系统的ZGD100A多线切割机,该部分包括多线切割机的结构总体设计方案和多线切割机控制系统总体设计方案,重点对加工系统、导轮系统、排线系统、进给系统、供浆系统、收放线系统、线张力控制装置、箱体的结构进行了具体的分析设计,通过SolidWorks软件建立了各个系统的三维模型图,完成了整机的虚拟装配,并且对主要的零部件进行了详细的强度校核。
3、根据ZGD100A多线切割机的控制总体设计方案,完成了控制系统各功能模块的设计和选型,对各功能模块的作用和参数进行了说明。
并对多线切割机的多电机速度同步控制和张力控制两个关键技术的程序设计进行了介绍说明。
4、根据超声波振动系统的总体设计方案,完成了超声波电源选型、超声波换能器和超声波变幅杆的材料选择和结构设计,并根据密封和装配规则,完成了超声波振动台的虚拟装配,对超声波振动台的制造有非常重要的指导意义。
超声波以及径向振动技术在制备材料方面的应用研究

超声波以及径向振动技术在制备材料方面的应用研究材料制备技术一直是人类科技发展的重要环节之一。
而随着科技的不断发展,越来越多先进的制备技术被引入到各个工业领域。
其中,超声波以及径向振动技术因其独特的特点及优越的性能而被广泛应用于材料制备领域。
本文将重点探讨这两种技术在材料制备方面的应用研究。
一、超声波的应用研究1. 原理介绍超声波指的是声波频率高于20kHz的一种机械波。
由于其频率高、波长短,能量密度大以及对材料的非接触性加工等优点,因此广泛应用于材料制备领域。
2. 超声波的作用机制超声波在材料中的传播与射频电磁场在材料中的传播类似,同样会在材料中产生各种各样的物理效应。
这些效应包括:振动效应、温升效应和化学效应。
其中,超声波振动效应又分为机械效应和声学效应。
机械效应使得材料中的颗粒、固体、液体等发生位移和变形,从而加速反应过程和增强材料的均质化程度;而声学效应则可使得材料中的气泡瞬间塌缩和产生剪切力,从而加速反应和增加粒子表面积。
3. 超声波在材料制备中的应用(1)溶剂交换:利用超声波技术可以快速地将不同溶剂中的材料进行转移。
(2)合成材料:超声波技术加速了反应过程,提高了反应物之间的碰撞能力,从而加快了材料的合成速度。
(3)制备纳米材料:超声波依靠声学效应产生强烈的液体剪切力,可以制备出具有更小颗粒尺寸和更好分散度的纳米颗粒。
(4)清洗材料:利用超声波振荡和气泡塌缩的效应,可以彻底清洗表面粘附的杂质、氧化和沉积物等。
二、径向振动技术的应用研究1. 原理介绍径向振动技术是一种通过机械振动来带动材料移动的技术。
利用径向振动技术能够实现不同颗粒之间的强制混合,加快反应而得出纯度较高的产物。
2. 径向振动技术的作用机制径向振动技术能够通过主激振器带动整个容器中的物质进行振荡,并且系统能够自适应地控制和调整运动状态,从而达到不同的混合效果。
3. 径向振动技术在材料制备中的应用(1)混合材料:径向振动技术可达到混合过程精确化,提高了材料的均质化程度,可以得到纯度较高的产物。
硬脆材料的超声频振动切削机理及应用研究

硬脆材料的超声频振动切削机理及应用研究引言:硬脆材料具有高硬度和脆性的特性,传统机械加工方法难以满足其加工的要求。
而超声频振动切削作为一种新型的加工方法,通过施加超声频振动切削力来改善硬脆材料的切削性能。
本文旨在探讨硬脆材料的超声频振动切削机理及其应用研究。
一、硬脆材料的超声频振动切削机理超声频振动切削是一种利用超声波作用于切削刀具实现切削目标的加工方法。
在硬脆材料的加工过程中,通过施加超声振动力,可以激发材料颗粒之间的滑动和变形,从而改善切削过程中的切削状态。
具体来说,超声频振动切削机理主要包括以下几个方面的影响因素:1. 振幅效应:超声振动切削中的振幅大小对切削过程的影响非常显著。
适当的振幅可以改变材料的切削角度和切削力,提高切削效率。
2. 减摩效应:超声波的作用可以降低切削力和摩擦阻力,减少工具与工件界面的磨损。
这是由于超声波振动产生的微小滑动和摩擦热可以在工具刀具与工件之间形成一层固体润滑膜。
3. 超声冷却效应:超声波振动可以在切削过程中产生微小的振动幅度和频率变化,使切削区域得到均匀的冷却。
这有助于减小切削温度,提高材料切削的质量和精度。
二、硬脆材料的超声频振动切削应用研究超声频振动切削在硬脆材料的加工中已得到广泛的应用。
以下分别从切削效率、切削质量和切削精度三个方面介绍了该方法的应用研究情况。
1. 切削效率提升:超声频振动切削的振动作用可以有效降低硬脆材料的切削力,提高切削效率。
研究发现,超声波振动切削技术可以提高硬脆材料的切削深度和切削速度,提高生产效率。
2. 切削质量改善:超声频振动切削减摩效应可以降低工具与工件的摩擦,减少工具磨损和表面质量的损伤。
研究表明,在超声频振动切削下,硬脆材料的表面粗糙度得到明显改善,切削面质量得到提高。
3. 切削精度提高:超声频振动切削可以实现对硬脆材料的精密加工。
由于超声振动切削能够在微观尺度上改变材料的切削状态,因此可以实现更精细的切削控制和更高的加工精度。
超声波振动辅助车削加工机理分析

建立了超声振动切削系统。
本文进行了超声振动辅助车削试验。
验证了振幅、切削速度与切削力的关系,验证了切削热分布的规律;并对超声波振动切削45号钢的切削参数进行了优化分析;对比了超声振动车削与普通车削的功率、表面粗糙度、切削力等;试验结果表明,振动车削可以降低切削力,表面粗糙度值在振动车削条件下明显减小。
关键词:超声波,振动切削,净切削比,有限元分析RESEACH ON ULTRASONIC VIBRATION TURNINGABSTRACTWith the development of the science and technology, precision and super-precision machining technologies have an important increasing position. For some workpieces of specific material and complex shape, it is difficult to use the conventional machining method, so non-traditional machining is developed rapidly. One of them is ultrasonic machining technology. It is indicated that ultrasonic technology has provided an huge help to improve the quality of product, reduce the costs of production, increase efficiency and so on. Now it is already entered into national defense and economy, science and technology, people’s life and other domains.Secondly, ultrasonic vibration cutting systems are studied theoretically. Net cutting time ratio r is defined, and relationship between r and cutting force is studied. The analysis indicates that the force increases as the r increases. With the software MARC, the temperature field variation rule of vibration cutting process is studied. The results of simulations show that heat dissipation when the tool comes off the workpiece is the mian reseon.Finally, the cutting experiment with and without ultrasonic vibrationis made. The superior ranges of cutting parameters are recommended. The cutting speed and ultrasonic amplitude between cutting force is verified. The results of experiments show that the cutting force and surface roughness are lower with ultrasonic vibration than without ultrasonic vibration.Keywords : ultrasonic, vibration turning, net cutting time ratio, finite element目 录摘要 (I)ABSTRACT (III)目录 (V)第一章绪论 (1)1.1课题背景 (1)1.2国内外研究发展现状 (2)1.2.1 超声振动系统 (2)1.2.2 超声振动切削理论 (4)1.2.3 超声车削加工系统 (7)1.3论文的主要研究内容 (9)第二章超声波辅助振动车削理论研究 (10)2.1超声波的基本原理及特点 (10)2.2超声波加工的基本原理 (10)2.2.1超声振动切削原理 (11)2.2.2切削力 (14)2.2.3 振幅的影响 (16)2.2.4 切削速度的影响 (17)2.2.5振动车削温度场的模拟 (18)2.3本章小结 (20)第三章超声波振动辅助车削系统的建立 (22)3.1超声装置概述及其选用 (22)3.2超声波发生器的选用 (24)3.3换能器 (27)3.3.1磁致伸缩换能器 (27)3.3.2压电式换能器 (28)3.3.3 换能器的匹配与选型 (28)3.4调幅器 (29)3.5超声波车刀的设计 (31)3.5.1 超声车刀特性 (31)3.5.2 采用F.E.A方法设计刀杆 (31)3.5.3实体建模 (34)3.5.4 软件ANSYS模态分析 (35)3.5.5 分析结果 (38)3.6连接与固定方案 (46)3.7本章小结 (48)第四章超声波振动辅助车削试验研究 (49)4.1切削试验方案 (49)4.1.1切削试验系统 (49)4.1.2切削试验步骤 (54)4.2.1切削深度对切削过程的影响 (56)4.2.2进给量对切削过程的影响 (57)4.2.3切削速度对切削过程的影响 (58)4.2.4参数优化 (59)4.3试验结果验证 (62)4.3.1 对振幅影响的验证 (62)4.3.2 对转速影响的验证 (64)4.3.3对温度仿真的验证 (65)4.4本章小结 (67)第五章总结与展望 (69)5.1全文总结 (69)5.2前景展望 (69)参考文献 (71)致谢 (75)攻读硕士学位期间发表的论文 (76)第一章 绪论1.1课题背景超声技术出现在20世纪初期。
超声振动辅助磨削CFRP复合材料薄管撕裂损伤研究

Schoo
lo
fMe
chan
i
c
a
lEng
i
ne
e
r
i
ng,
Da
l
i
anUn
i
ve
r
s
i
t
fTe
chno
l
ogy,
yo
,
,
Da
l
i
an L
i
aon
i
ng 116024
,
,
2.
Shangha
iCompos
i
t
eTe
chno
l
ogyCo.
Lt
d.
Shangha
i,
201112
:
Ab
s
t
r
a
c
t Aimi
量及主轴转速对磨削力和撕裂尺寸的影响规律,通过对磨削过程的受力分 析 和 对 最 大 未 变 形 切 屑 厚 度
的计算,分析了撕裂位置的形成原因和撕裂尺寸的变化规律.结果表明:磨削力随超声振幅的增大而减
小,随进给量的增大而增大,与主轴转 速 的 关 联 性 较 小;撕 裂 易 出 现 于 CFRP 薄 管 内 壁,其 长 度 与 高 度
图 1 阵列复材管示意图
F
i
1 S
ch
ema
t
i
cd
i
a
r
amo
fCFRPt
h
i
nc
i
r
c
u
l
a
r
g.
g
c
e
l
lhon
e
c
omb
超声波技术在机械加工中的应用研究

超声波技术在机械加工中的应用研究引言机械加工领域一直以来都是工业发展的重要组成部分。
随着科技的不断进步,各种新技术应运而生,其中超声波技术作为一种创新型的加工方法,逐渐受到了研究者们的关注。
本文将探讨超声波技术在机械加工领域中的应用以及其对加工效率和质量的影响。
超声波技术的原理超声波指的是大于人类能听到的20千赫(kHz)频率的声波。
超声波技术利用超声波在介质中传播时的物理效应,实现对物体的加工、清洗、焊接等作用。
超声波具有高频、高能、高效的特点,可用于加工和处理利用传统方法难以实现的材料和工艺。
超声波在机械加工中的应用1. 振动加工超声波振动加工是超声波技术中的一项重要应用。
通过将超声波的机械振动传导至刀具上,可以提高刀具的切削性能和加工精度。
超声波振动加工可用于薄壁零件的薄切削加工、坚硬材料的高速切削加工等。
研究表明,超声波振动加工可以显著降低加工力和磨损,提高表面质量。
2. 清洗技术超声波清洗技术是超声波技术的另一项常见应用。
超声波在液体中产生的高频振动可以有效地使污垢与物体表面分离,从而实现高效的清洗效果。
在机械加工中,超声波清洗技术可用于清洗零件表面的油污、金属屑等杂质,使加工过程更为干净、快捷。
3. 精密焊接超声波焊接是超声波技术在机械加工中的另一项应用领域。
通过超声波的高频振动和热作用,可以将材料接触表面的分子间距离减小,使其发生塑性变形,从而实现焊接目的。
超声波焊接主要应用于精密仪器、电子元器件等领域,能够实现高强度、高效率的焊接效果。
超声波技术对机械加工的影响1. 提高加工效率超声波技术在机械加工中的应用可以提高加工效率。
例如,在超声波振动加工中,由于超声波的振动作用,切削力可以减小,切削速度可以增加,从而有效提高了加工效率。
此外,超声波清洗技术的应用也可以实现零件表面的快速清洗,减少了加工中的停留时间,进一步提高了加工效率。
2. 提高加工质量超声波技术的应用还可以提高加工质量。
- 1、下载文档前请自行甄别文档内容的完整性,平台不提供额外的编辑、内容补充、找答案等附加服务。
- 2、"仅部分预览"的文档,不可在线预览部分如存在完整性等问题,可反馈申请退款(可完整预览的文档不适用该条件!)。
- 3、如文档侵犯您的权益,请联系客服反馈,我们会尽快为您处理(人工客服工作时间:9:00-18:30)。
第11卷 第6期2003年12月光学精密工程Opt ics and Precision EngineeringVol.11 No.6Dec.2003文章编号 1004 924X(2003)06 0591 05超声波振动精密切削GFRP的实验研究高印寒1,于向军2,王连武3,李东旭4,王立江4(1.吉林大学测试科学实验中心,吉林长春130025;2.长春工程学院机械工程系,吉林长春130022;3.吉林大学辊锻件厂,吉林长春130025;4.吉林大学机械工程学院,吉林长春130025)摘要:为改善玻璃纤维增强塑料(Glass F ibr e Reinforced Plastics)的切削加工性,提高加工精度和质量,采用超声波振动切削的方式对GFR P进行了精密切削加工。
介绍了超声波振动切削的特性和GFR P的纤维束与切削速度方向的相位参数,相位参数沿圆周方向成周期性变化,变化周期为 。
通过实验获得了不同切削条件下表面粗糙度的变化规律,粗糙度随相位角变化基本呈正弦规律,但在45 时粗糙度最大。
振幅增大导致粗糙度明显下降。
切削速度对粗糙度的变化曲线呈极值状态,在速度为100m/min时粗糙度最小。
进给量小于0.06mm时,粗糙度呈下降趋势;大于0.06mm时,粗糙度增加较快;而大于0.09mm后粗糙度上升趋缓。
切削深度对粗糙度的影响呈单调上升趋势。
实验结果表明超声波振动切削可以使GFR P的加工表面粗糙度减少1倍,使加工质量得以提高。
关 键 词:超声波振动;切削;玻璃纤维增强塑料;粗糙度中图分类号:T G506.5 文献标识码:AFinish cutting of GFRP by ultrasonic vibrationGAO Yin han YU Xiang jun WANG Lian wu LI Dong x u WANG Li jiang(1.Center o f Test Science,Jilin University,Changchun130025,China;2.Dep ar tment of Mechanical Engineer ing,Changchun I nstitute of Engineering,Changchun130022,China;3.Rolling Forge Factory of J ilin Univer sity,Changchun130025,China;4.College o f M achinery and E ngineering,Jinlin University,Changchun130025,China)Abstract:In order to improve the machinability and m achining accuracy of glass fibre reinforced plastic (GFRP),GFRP is finish cut using ultrasonic vibration.Experimental results indicate that the phase pa rameters of GFRP fibres w ith respect to cutting direction change in the circumferential direction at cycle; the v ariation of surface roug hness w ith the phase angle under different cutting conditions is sinusoidal w ith max imum roughness at45 ;an increase in amplitude causes an obvious drop in roug hness;the variation of roug hness w ith cutting speed is extremal,and roughness is minimum at100m/m in;the surface roug hness g oes dow n w hen the feed is less than0.06mm,the roughness increases much faster w hen the feed is more than0.06mm,and the increase in roughness slows dow n when the feed is more than0.09mm;the influ ence of cutting depth on roug hness is a monotonous rising trend.It is concluded from the experimental re sults that ultrasonic vibration cutting can half the surface roughness and improve the machining quality of GFRP.Key words:ultrasonic v ibration;cutting;glass fiber reinforced plastics;surface roughness收稿日期:2003 05 12;修订日期:2003 10 20.基金项目:国家自然科学基金资助项目(No.58975173)1 引 言GFRP是由强度高,硬度大的玻璃纤维和树脂基体混合而成的二相结构,是一种新型工程材料。
作为增强材料的玻璃纤维是韧而硬的材料,难以切削、不易切断,容易产生拉伸或弯曲,切削时容易产生切削残余或剥离,切削表面产生毛刺。
它的基体是较软的合成树脂,而且软的基体中夹有硬的纤维,切削时使刀具承受冲击。
在普通车削时,若用硬质合金刀具容易过早地造成磨损,导致加工表面加工质量变差,加工精度不好。
再有GFRP的热传导率和体积比热小,与金属材料相比在同样的切削速度下温升高,且随着切削速度增加使切削温度急剧上升,直接影响到加工表面质量。
针对上述问题,使用硬质合金刀具对GFRP进行了超声波振动精密切削的实验研究。
2 超声波振动切削特性2.1 分离特性Z向(切削速度方向)分离型超声波振动车削时,车刀前刀面与切屑之间不像传统车削过程那样总是紧密接触,而是周期性的分离。
长期以来,普通车削时切屑与前刀面不分离接触形成了高温高压区,对切削液和空气来说是很难进入的禁区,给切削过程带来了一系列恶劣影响。
而振动车削的分离特性终于打开了这个禁区,从根本上改善了车削条件[1 3]。
在忽略进给运动的条件下,振动车刀刀刃与工件之间的相对速度V r为:V r=V0+ u A cos,(1)式中:V0为工件回转的线速度,即普通车削速度;u为车刀刀刃的振动角速度;为振动的相位角,= u t。
刀具切削刃振动的正弦曲线V u与水平线V0合成得相对速度曲线V r,见图1。
当V0< u A 时,在1到1区间V r为负值,其意义是刀具前刀面由1点开始脱离与切屑的接触,并逐渐加大与切屑之间的距离,到1又开始接近切屑,直到2点刀具才重新与切屑接触,进入切削过程。
V r的最大值为 u A,故当V0! u A时,将不出现上述的前刀面与切屑分离的过程,令k=V0/ u A,称之为速度系数。
当k!1时为不分离超声波振动车削,其切削速度曲线是连续函数,见图1中的虚线,其表达式如公式(1)。
当k<1时为分离型的超声波振动车削,其切削速度曲线是具有第1类间断点的分段连续的周期函数,见图1中的实线,其表达式如下:V r=02n +1<<2n +2n=0,1,2,...V0+ u A cos2n +2∀∀2(n+1) +1n=0,1,2,... ,(2)因为V r是周期函数,所以区间[0,1]与区间[2 ,2 +1]完全相同。
图1 振动切削的相对速度曲线F ig.1 Relative velocity curv es of v ibration cutting分离型的超声波振动切削完全脱离了传统的连续切削过程,刀具的前刀面与切屑之间存在着完全分离的现象。
应该指出,虽然在微观上分离型的超声波振动切削是一种时切时不切的断续切削过程,但是在宏观上它仍是连续切削。
分离特性彻底改变了车削时前刀面的接触条件,使前刀面与切屑间摩擦时间缩短,摩擦系数明显下降,剪切角增大,变形减小,特别是高频的分离使被切材料间的亲和作用和黏结作用显著减弱,切屑底层材料很难粘贴于前刀面上,从而使积屑瘤无法生成。
因此,切削过程比普通车削稳定得多,出现了切削力下降,表面质量和加工精度提高等一系列的加工效果。
2.2 冲击特性振动车削过程是宏观上连续,微观上高频断续的冲击切削。
F=20kH z时,每秒钟冲击切削20000次,每次冲击的期间极短,但其动能比普通车削的动能要大得多。
冲击特性引起振动车削592光学 精密工程 第11卷过程中切屑形成机理发生很大变化,使切削的能量集中,切屑变形减弱,切削力下降,即使是在低速切削时也可以得到稳定的带状切屑,提高了加工表面质量[4 5]。
2.3 变速特性振动车削是一种周期性的变速度和变加速度切削过程,而且形态也是多变的。
振动车削虽然也是一种断续切削,但却与传统的断续切削(如铣削)大不相同。
振动车削的实质是把切削速度在极短的周期内做了重新分布,使之在一段时间内的速度减到零,而把它移到另一段时间内,提高实际切削速度,速度的这种分配是振动车削所特有的功能。
变速特性的优点是对车削过程中的积屑瘤和颤振现象有抑制作用,可在低速车削时获得较高速车削的一些效果。
这对在低速下车削的零件加工,例如GFRP车削、C FRP车削、凸轮车削、螺纹车削等是很有利的,可提高其加工质量和加工精度。
2.4 往复熨压特性振动车削的另一特性是刀具相对于工件的运动不是单方向前进,而是周期的往复运动。
因此,已加工表面在形成以后又经过刀具后退和再前进的重复熨压作用。
后退时的熨压主要是由刀具的后刀面进行的,前进时的熨压主要是由刀具刃口圆角完成的。
振动车削的这种熨压作用与普通的熨压加工不同,振动切削熨压的特点是:(1)熨压作用是脉冲的,非连续的;(2)熨压速度是变速的;(3)熨压作用是往复的。
振动车削的往复熨压特性使车削的实质变成切削与熨压的联合作用,能明显提高加工表面质量,降低表面粗糙度。
综上所述,Z向分离型振动车削的4大特征明显改善了振动切削的工艺效果,使切削力小,切削温度低,刀具耐用度提高,并使加工精度和质量提高,这些特性非常有利于GFRP的切削加工。