丙烯—丙烷板式精馏塔设计
化工原理课程设计-处理量70kmolh丙烯丙烷精馏筛板塔设计

化工原理课程设计处理量70kmol/h丙烯丙烷精馏筛板塔设计处理量:70kmol/h产品质量:(以丙稀摩尔百分数计)进料:x=65%f=98%塔顶产品:xD塔底产品: x≤2%w安装地点:大连总板效率:0.6塔板位置:塔底塔板形式:筛板回流比:1.6前言本设计说明书包括概述、流程简介、精馏塔、再沸器、辅助设备、管路设计和控制方案共七章。
说明中对精馏塔的设计计算做了详细的阐述,对于再沸器、辅助设备和管路的设计也做了正确的说明。
鉴于本人经验有限,本设计中还存在许多错误,希望各位老师给予指正感谢老师的指导和参阅!目录第一章概述 (4)第二章流程简介 (5)第三章精馏塔工艺设计 (5)第四章再沸器的设计 (15)第五章辅助设备的设计 (21)第六章管路设计 (26)第七章控制方案 (26)附录一主要符号说明 (27)附录二参考文献 (29)第一章概述精馏是分离过程中的重要单元操作之一,所用设备主要包括精馏塔及再沸器和冷凝器。
1.精馏塔精馏塔是一圆形筒体,塔内装有多层塔板或填料,塔中部适宜位置设有进料板。
两相在塔板上相互接触时,液相被加热,液相中易挥发组分向气相中转移;气相被部分冷凝,气相中难挥发组分向液相中转移,从而使混合物中的组分得到高程度的分离。
简单精馏中,只有一股进料,进料位置将塔分为精馏段和提馏段,而在塔顶和塔底分别引出一股产品。
精馏塔内,气、液两相的温度和压力自上而下逐渐增加,塔顶最低,塔底最高。
本设计为筛板塔,筛板的突出优点是结构简单、造价低、塔板阻力小且效率高。
过去认为它易漏液,易堵塞。
然而经长期研究发现,只要设计合理和操作适当,晒斑人能够满足生厂上所需的操作弹性,而且效率比较高。
小筛孔孔径一般3~6mm,大筛孔孔径一般10~25mm。
如果采用大筛板,堵塞问题即可解决。
目前已发展成为日趋广泛的一种塔板。
2.再沸器作用:用以将塔底液体部分汽化后送回精馏塔,使塔内气液两相间的接触传质得以进行。
丙烯——丙烷精馏塔的机械设计
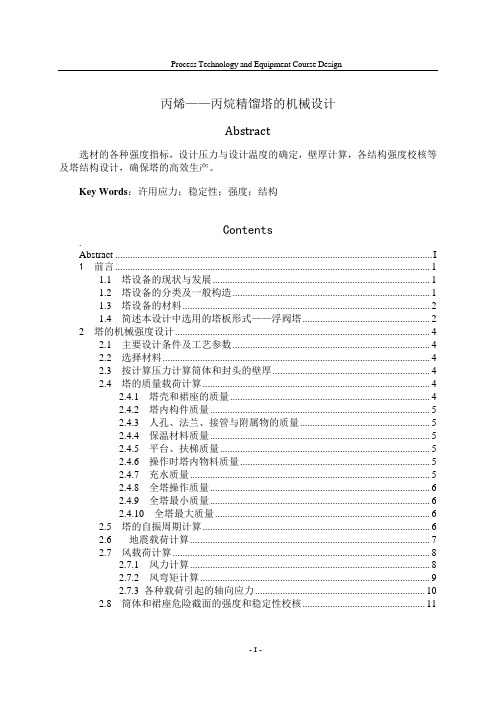
丙烯——丙烷精馏塔的机械设计Abstract选材的各种强度指标,设计压力与设计温度的确定,壁厚计算,各结构强度校核等及塔结构设计,确保塔的高效生产。
Key Words:许用应力;稳定性;强度;结构Contents.Abstract (I)1 前言 (1)1.1 塔设备的现状与发展 (1)1.2 塔设备的分类及一般构造 (1)1.3 塔设备的材料 (2)1.4 简述本设计中选用的塔板形式——浮阀塔 (2)2 塔的机械强度设计 (4)2.1 主要设计条件及工艺参数 (4)2.2 选择材料 (4)2.3 按计算压力计算筒体和封头的壁厚 (4)2.4 塔的质量载荷计算 (4)2.4.1 塔壳和裙座的质量 (4)2.4.2 塔内构件质量 (5)2.4.3 人孔、法兰、接管与附属物的质量 (5)2.4.4 保温材料质量 (5)2.4.5 平台、扶梯质量 (5)2.4.6 操作时塔内物料质量 (5)2.4.7 充水质量 (5)2.4.8 全塔操作质量 (6)2.4.9 全塔最小质量 (6)2.4.10 全塔最大质量 (6)2.5 塔的自振周期计算 (6)2.6地震载荷计算 (7)2.7 风载荷计算 (8)2.7.1 风力计算 (8)2.7.2 风弯矩计算 (9)2.7.3 各种载荷引起的轴向应力 (10)2.8 筒体和裙座危险截面的强度和稳定性校核 (11)2.8.1 筒体的强度与稳定性校核 (11)2.8.2 裙座的稳定性校核 (11)2.9 筒体和裙座水压试验应力校核 (11)2.9.1 筒体水压试验应力校核 (11)2.9.2 裙座水压试验应力校核 (12)2.10 基础环设计 (13)2.10.1 基础环尺寸 (13)2.10.2 基础环应力校核 (13)2.10.3 基础环厚度 (13)2.11 地脚螺栓设计 (13)2.11.1 地脚螺栓承受的最大拉应力 (13)2.11.2 地脚螺栓直径 (13)2.12 补强计算(此处只对人孔进行补强计算) (15)2.12.1 部分参数: (15)2.12.2 补强及补强方法判断 (15)2.12.3 有效补强范围 (15)2.12.4 有效补强面积 (15)2.12.5 计算结果 (15)3 标准化零部件的选择 (17)3.1 塔体人孔设计 (17)3.2 裙座人孔设计 (17)4 辅助装置及附件 (18)4.1 丝网除沫器的结构 (18)4.2 进出料接管 (18)4.2.1 进料管和回流管 (18)4.2.2 塔底出料管 (18)4.2.3 气体进出口管 (18)4.3管法兰 (18)5.4吊柱 (18)5.5保温结构 (18)总结 (19)参考文献 (20)附录A 主要符号说明 (21)致谢 (22)1 前言塔设备是石油化工等生产中的重要设备之一。
年处理量为2万吨丙烯-丙烷分离过程精馏塔设计--文献综述
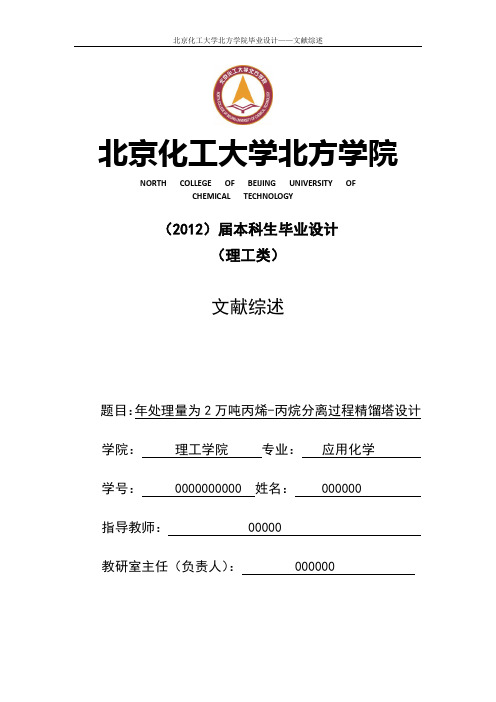
北京化工大学北方学院NORTH COLLEGE OF BEIJING UNIVERSITY OFCHEMICAL TECHNOLOGY(2012)届本科生毕业设计(理工类)文献综述题目:年处理量为2万吨丙烯-丙烷分离过程精馏塔设计学院:理工学院专业:应用化学学号: 0000000000 姓名: 000000 指导教师: 00000 教研室主任(负责人): 000000文献综述前言丙烯,是三大合成材料的基本原料,在化工生产中扮演着重要的角色。
主要用于生产丙烯腈、异丙烯、丙酮和环氧丙烷等。
[1]丙烷脱氢制备丙烯技术是现在最常用的技术之一,比烃类蒸汽裂解技术能产生更多的丙烯。
但当使用丙烷脱氢制备丙烯技术制备丙烯时,总收率只有74%~86%,丙烷不能全部转化为丙烯,反应产物会是丙烷与丙烯的混合物[2]。
因此,研究丙烯与丙烷的分离技术至关重要。
精馏是分离液体混合物最常用的一种单元操作,在化工、炼油、石油化工等工业中具有广泛应用。
精馏过程在能量计的驱动下,使气,液两相多次直接接触和分离,利用液相混合物中各相组分挥发度的不同,使易挥发组分由液相向气相转移,难挥发组分由气相向液相转移。
实现原料混合物中各组成成分的分离过程是同时进行传质传热的过程[3]。
本文就将对丙烯和丙烷的精馏塔设计进行相关的研究,以便今后能设计出更为高效安全的精馏塔。
一、精馏原理利用混合物中各组分挥发能力的差异,通过液相和气相的回流,使气、液两相逆向多级接触,在热能驱动和相平衡关系的约束下,使得易挥发组分(轻组分)不断从液相往气相中转移,而难挥发组分却由气相向液相中迁移,使混合物得到不断分离,称该过程为精馏。
该过程中,传热、传质过程同时进行,属传质过程控制。
其精馏塔如图所示。
原料从塔中部适当位置进塔,将塔分为两段,上段为精馏段,不含进料,下段含进料板为提留段,冷凝器从塔顶提供液相回流,再沸器从塔底提供气相回流。
气、液相回流是精馏重要特点。
在精馏段,气相在上升的过程中,气相轻组分不断得到精制,在气相中不断地增浓,在塔顶获轻组分产品。
化工原理课程设计丙烯丙烷筛板精馏塔

化工原理课程设计丙烯丙烷筛板精馏塔化工原理课程设计是化学工程专业学生学习的重要门课,它涉及到了化学工程领域中的各种基础理论和实际操作技能。
而其中的丙烯丙烷筛板精馏塔是化学工程中常见的分离设备,其设计和操作都非常重要。
本文将介绍化工原理课程设计中丙烯丙烷筛板精馏塔的相关知识和实践操作。
一、丙烯丙烷的物理化学性质丙烯和丙烷是两种结构相近的烃类化合物,它们都是无色、无味、无毒的气体。
它们的分子量分别为42 g/mol和44 g/mol。
它们的熔点和沸点都比较低,分别为-185.2℃和-47.6℃以及-42.1℃和-0.5℃。
在常温常压下,丙烯和丙烷都是易燃的气体,丙烯比丙烷更易燃,爆炸极限范围也更广。
二、筛板精馏塔的原理和结构筛板精馏塔是分离和提纯液体混合物的一种常见设备,它的热和质量传递效果、节能效果和运行稳定性都非常优秀。
它的基本结构由筛板、塔板、液相收集管、汽相收集管、塔体、进出料口和附件组成。
其中,筛板用于液相在塔内的分布和降温,塔板用于汽相的分布和降温,液相收集管和汽相收集管用于收集液相和汽相,进出料口用于引入和排出混合物,附件包括冷凝器、换热器、加热器、泵等。
筛板精馏塔的工作过程是:混合物通过进料口进入精馏塔,在筛板上分布后冷凝成液滴,通过塔板向上蒸发,在塔体中逐渐升温,汽相不断往上移动并在顶部冷凝成液体,液体沿着液相收集管流入下一层筛板,整个过程不断循环直至成品收集。
三、丙烯丙烷的筛板精馏塔设计丙烯和丙烷的物理化学性质较为相近,但在某些方面又有所不同,比如其沸点的差异较小等。
因此,设计丙烯丙烷精馏塔时需要根据实际情况进行合理的结构和操作参数的选择。
1. 塔板和筛板的选择:由于丙烷较丙烯更易于液相和汽相的分离,因此在塔内,丙烷往往会优先偏向于下方的液面。
为了更好地控制液体的分布和温度,建议使用细孔筛板,以增加液滴的表面积和扩散速度。
同时,也可以加装搅拌器或者微波辐射器以增加筛板上的流动力和混合效果。
化工原理课程设计丙烯-丙烷筛板精馏塔资料

化工原理课程设计丙烯-丙烷精馏装置设计处理量:50kmol/h产品质量:(以丙稀摩尔百分数计)=65%进料:xf塔顶产品:x=98%D≤2%塔底产品: xw安装地点:大连总板效率:0.6塔板位置:塔底塔板形式:浮阀回流比:1.2班级:姓名:学号:指导老师:设计日期:成绩:前言本设计说明书包括概述、流程简介、精馏塔、再沸器、辅助设备、管路设计和控制方案共七章。
说明中对精馏塔的设计计算做了详细的阐述,对于再沸器、辅助设备和管路的设计也做了正确的说明。
鉴于本人经验有限,本设计中还存在许多错误,希望各位老师给予指正感谢老师的指导和参阅!目录第一章精馏过程工艺设计概述 ............................................................................ - 1 -一、概述 (1)二、工艺设计基本内容 (1)1、塔型选择...................................................................................................... - 1 -2、板型选择...................................................................................................... - 1 -3、进料状态...................................................................................................... - 2 -4、回流比.......................................................................................................... - 2 -5、加热剂和再沸器的选择.............................................................................. - 2 -6、冷凝器和冷却剂选择.................................................................................. - 3 -三、工艺流程(见丙烯——丙烷工艺流程图) (3)第二章筛板塔的工艺设计 .................................................................................... - 4 -一、物性数据的确定 (4)1、塔顶、塔底温度确定.................................................................................. - 4 -2、回流比计算.................................................................................................. - 5 -3、全塔物料衡算.............................................................................................. - 5 -4、逐板计算塔板数.......................................................................................... - 6 -5、确定实际塔底压力、板数:...................................................................... - 6 -二、塔板设计 (7)1、塔高计算...................................................................................................... - 7 -2、塔径计算...................................................................................................... - 7 -3、塔板布置和其余结构尺寸的选取.............................................................. - 8 -4、塔板校核...................................................................................................... - 9 -5、负荷性能图................................................................................................ - 11 -第三章立式热虹吸再沸器的工艺设计 .............................................................. - 14 -一、设计条件及物性参数 (14)二、工艺设计 (14)1、估算再沸器面积........................................................................................ - 14 -2、传热系数校核............................................................................................ - 15 -3、循环流量校核............................................................................................ - 18 -第四章管路设计 .................................................................................................. - 22 -一、物料参数 (22)二、设计 (22)第五章辅助设备的设计 ...................................................................................... - 24 -一、储罐设计 (24)二、传热设备 (25)三、泵的设计 (26)第六章控制方案 .......................................................................................... - 30 -附录1.理论塔板数计算 ........................................................................................ - 31 -附录2.过程工艺与设备课程设计任务书 ............................................................ - 33 -附录3.主要说明符号 ............................................................................................ - 37 -参考资料: ............................................................................................................ - 38 -第一章精馏过程工艺设计概述一、概述化学工程项目的建设过程就是将化学工业范畴的某些设想,实现为一个序列化的、能够达到预期目的的可安全稳定生产的工业生产装置。
丙烯—丙烷板式精馏塔设计1

丙烯—丙烷板式精馏塔设计1丙烯—丙烷板式精馏塔设计1丙烯和丙烷是石油行业中常见的烃类化合物,丙烯主要用于合成塑料和合成橡胶等工业原料,而丙烷则广泛用于燃料和热能生产。
在石油提炼过程中,需要对丙烯和丙烷进行分离,以满足不同的工业需求。
这就需要使用精馏塔进行分离和提纯。
丙烯-丙烷板式精馏塔是一种常见的精馏塔设计,以下是其设计过程和要点:1.确定塔的尺寸和设计参数:首先,需要确定塔的高度、内径和塔板数量等尺寸参数。
这些参数的选择将取决于丙烯和丙烷的物理和化学性质,以及分离程度和生产要求。
同时,还需要确定塔板的类型,常用的有平板、筛板和节流孔板等。
2.计算塔的理论板数:根据丙烯和丙烷的物理性质,可以使用理论计算方法来确定塔的理论板数。
常见的方法有经验法、Fenske方法和McCabe-Thiele方法等。
这些方法基于馏分的蒸发和重新凝结过程,并考虑到物料的挥发性和沸点差异。
3.优化精馏塔结构:在确定了理论板数后,可以对精馏塔的结构进行优化。
优化的目标是降低能耗和提高分离效果。
常见的优化措施包括增加回流比、优化塔底和塔顶的设计、增加中间进料点和中间产品抽取点等。
这些措施可以提高馏分在塔内的接触和分离效果。
4.确定换热与冷凝方式:精馏过程中,需要进行热量交换和冷凝,以提供蒸汽和冷凝液。
根据工艺和能耗要求,可以选择合适的换热器和冷凝器类型进行热交换。
常见的方式有喷射器冷凝、外换热器冷凝和内换热器冷凝等。
5.进行流程模拟和动态调整:一旦确定了精馏塔的设计参数和结构,可以使用流程模拟软件进行流程计算和模拟。
通过模拟,可以评估塔内各个部位的温度、压力和塔板效率等参数,并进行相应的调整和优化。
流程模拟也可以用于优化操作条件和改进分离效果。
6.进行安全评估和应急设计:精馏塔是一种高温高压设备,需要进行安全评估和应急设计。
这包括确定安全阀和过压保护装置、制定应急排放和泄漏处置计划等。
同时,还需要考虑火灾和爆炸等事故的防范和应对措施。
化工原理课程设计丙烯—丙烷精馏装置设计(浮阀)

大连理工大学化工原理课程设计丙烯---丙烷精馏装置设计学生:班级:学号:指导老师:前言本设计说明书包括概述、流程简介、精馏塔、再沸器、辅助设备、管路设计和控制方案共七章。
说明中对精馏塔的设计计算做了详细的阐述,对于再沸器、辅助设备和管路的设计也做了正确的说明。
鉴于设计者经验有限,本设计中还存在许多错误,希望各位老师给予指正感谢老师的指导和参阅!目录第一章概述 (3)第二章方案流程简介 (5)第三章精馏过程系统分析 (7)第四章再沸器的设计 (21)第五章辅助设备的设计 (30)第六章管路设计 (37)第七章控制方案 (40)设计心得及总结 (41)附录一主要符号说明 (42)附录二参考文献 (45)第一章概述精馏是分离过程中的重要单元操作之一,所用设备主要包括精馏塔及再沸器和冷凝器。
1.精馏塔精馏塔是一圆形筒体,塔内装有多层塔板或填料,塔中部适宜位置设有进料板。
两相在塔板上相互接触时,液相被加热,液相中易挥发组分向气相中转移;气相被部分冷凝,气相中难挥发组分向液相中转移,从而使混合物中的组分得到高程度的分离。
简单精馏中,只有一股进料,进料位置将塔分为精馏段和提馏段,而在塔顶和塔底分别引出一股产品。
精馏塔内,气、液两相的温度和压力自上而下逐渐增加,塔顶最低,塔底最高。
本设计为浮阀塔,浮阀的突出优点是效率较高取消了结构复杂的上升管和泡罩。
当气体负荷较低时,浮阀的开度较小,漏夜量不多;气体负荷较高时,开度较大,阻力又不至于增加较大,所以这种塔板操作弹性较大,阻力比泡罩塔板大为减小,生产能力比其大。
缺点是使用久后,由于频繁活动而易脱落或被卡住,操作失常。
所以塔板和浮阀一般采用不锈钢材料。
2.再沸器作用:用以将塔底液体部分汽化后送回精馏塔,使塔内气液两相间的接触传质得以进行。
本设计采用立式热虹吸式再沸器,它是一垂直放置的管壳式换热器。
液体在自下而上通过换热器管程时部分汽化,由在壳程内的载热体供热。
立式热虹吸特点:▲循环推动力:釜液和换热器传热管气液混合物的密度差。
丙烯—丙烷板式精馏塔设计1讲解
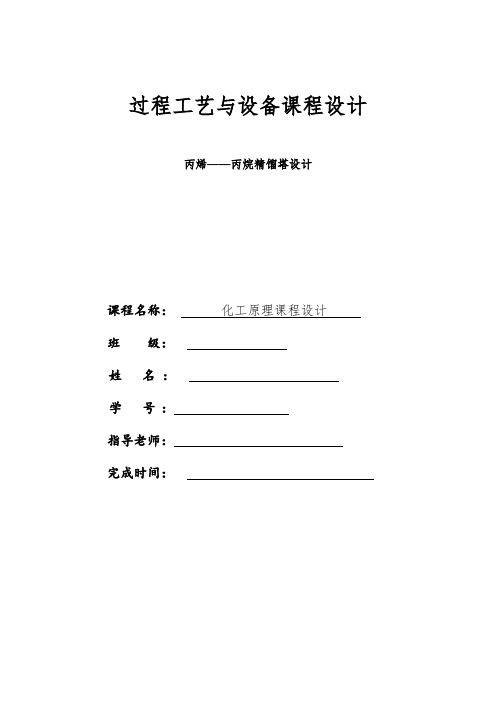
过程工艺与设备课程设计丙烯——丙烷精馏塔设计课程名称:化工原理课程设计班级:姓名:学号:指导老师:完成时间:前言本设计说明书包括概述、流程简介、精馏塔、再沸器、辅助设备、管路设计和控制方案共7章。
说明中对精馏塔的设计计算做了详细的阐述,对于再沸器、辅助设备和管路的设计也做了正确的说明。
鉴于设计者经验有限,本设计中还存在许多错误,希望各位老师给予指正感谢老师的指导和参阅!目录第一节:标题 丙烯—丙烷板式精馏塔设计第二节:丙烯—丙烷板式精馏塔设计任务书第三节:精馏方案简介第四节:精馏工艺流程草图及说明第五节:精馏工艺计算及主体设备设计第六节:辅助设备的计算及选型第七节:设计结果一览表第八节:对本设计的评述第九节:工艺流程简图第十节:参考文献第一章 任务书设计条件1、工艺条件: 饱和液体进料进料丙烯含量%65x F (摩尔百分数)。
塔顶丙烯含量%x98≥D釜液丙烯含量%≤x2W总板效率为0.62、操作条件:塔顶操作压力1.62MPa(表压)加热剂及加热方法:加热剂——热水加热方法——间壁换热冷却剂:循环冷却水回流比系数:R/Rmin=1.23、塔板形式:浮阀4、处理量:F=50kml/h5、安装地点:烟台6、塔板设计位置:塔顶安装地点:烟台。
处理量:64kmol/h产品质量:进料65%塔顶产品98%塔底产品<2%1、工艺条件:丙烯—丙烷饱和液体进料进料丙烯含量65% (摩尔百分数)塔顶丙烯含量98%釜液丙烯含量<2%总板效率为0.62、操作条件:塔顶操作压力1.62MPa(表压)加热剂及加热方法:加热剂——热水加热方法——间壁换热冷却剂:循环冷却水回流比系数:1.2 1.4 1.63、塔板形式:浮阀4、处理量:F=64kml/h5、安装地点:烟台6、塔板设计位置:塔顶第二章精馏过程工艺及设备概述精馏是分离液体混合物最常用的一种单元操作,在化工,炼油,石油化工等工业中得到广泛应用,精馏过程在能量剂驱动下(有时加质量剂),使气液两相多次直接接触和分离,利用液相混合物中各组分挥发度不同,使易挥发组分由液相向气相转移,难挥发组分由气相向液相转移,实现原料混合液中各组分的分离,该过程是同时传热,传质的过程。
过程工艺与设备课程设计任务书_丙烯-丙烷精馏装置设计

过程工艺与设备课程设计任务书——丙烯--丙烷精馏装置设计前言本设计说明书包括概述、流程简介、精馏塔、再沸器、辅助设备、管路设计和控制方案共七章。
说明中对精馏塔的设计计算做了详细的阐述,对于再沸器、辅助设备和管路的设计也做了说明。
鉴于设计者经验有限,本设计中还存在许多错误,希望各位老师给予指正。
感谢老师的指导和参阅!目录1. 概述 (3)2. 方案流程简介 (5)3. 精馏过程系统分析 (6)4. 再沸器的设计 (18)5. 辅助设备的设计 (24)6. 管路设计 (30)7. 控制方案 (33)设计心得及总结 (34)附录一主要符号说明 (35)附录二参考文献 (37)附录三塔计算结果表 (38)附录四再沸器主要结构尺寸和计算结果表 (39)附录五工艺流程图 (40)1. 概述蒸馏是分离液体混合物(含可液化的气体混合物)常用的一种单元操作,在化工、炼油、石油化工等工业中得到广泛的应用。
其中,简单蒸馏与平衡蒸馏只能将混合物进行初步的分离。
为了获得较高纯度的产品,应使得混合物的气、液两相经过多次混合接触和分离,使之得到更高程度的分离,这一目标可采用精馏的方法予以实现。
精馏过程在能量剂驱动下,使气、液两相多次直接接触和分离,利用液相混合物中各组分由液相向气相转移,难挥发组分由`气相向液相转移,实现原料中各组分的分离。
该过程是同时进行的传质、传热的过程。
为实现精馏过程,必须为该过程提供物流的存储、输送、传热、分离、控制等的设备、仪表。
所用设备主要包括精馏塔及再沸器和冷凝器等。
1.1 精馏塔精馏塔是一圆形筒体,塔内装有多层塔板或填料,塔中部适宜位置设有进料板。
两相在塔板上相互接触时,液相被加热,液相中易挥发组分向气相中转移;气相被部分冷凝,气相中难挥发组分向液相中转移,从而使混合物中的组分得到高程度的分离。
简单精馏中,只有一股进料,进料位置将塔分为精馏段和提馏段,而在塔顶和塔底分别引出一股产品。
精馏塔内,气、液两相的温度和压力自上而下逐渐增加,塔顶最低,塔底最高。
丙烯—丙烷板式精馏塔设计

丙烯—丙烷板式精馏塔设计丙烯-丙烷分离是石油炼制过程中的重要操作之一、丙烯-丙烷板式精馏塔是进行该分离的常见设备之一、本文将介绍丙烯-丙烷板式精馏塔的设计。
一、塔内结构设计1.塔径和塔高:根据丙烯-丙烷的物理性质和进出料的要求,决定塔径和塔高。
一般来说,塔径选择在0.5到2.5米范围内,塔高选择在20到30米范围内。
2.装塔板设计:为了提高分离效率,常采用板式结构。
根据工艺要求和流体性质,确定装塔板的类型、布置和数量。
常用的板式结构有筛板和壳程板。
筛板形状为圆形孔,使得流体分布更均匀;壳程板则是在板上装置隔流器,使流体分配均匀。
塔板的数量根据物料组分和分离要求确定。
3.塔壳设计:塔壳一般采用圆筒形结构,确保塔内压力稳定。
根据设计要求和工艺条件,确定壳体材料和厚度。
二、热量平衡设计1.进料和出料的热量平衡计算:根据进出料的温度和流量,计算出料的焓值,从而得到进出料之间的热量差。
2.塔板的热量平衡计算:根据进出料的温度和流量,在塔板上进行热量平衡计算,以确定塔板上液体和气体的温度和流量。
3.塔壳的热量平衡计算:根据进出料的温度和流量,在塔壳内进行热量平衡计算,以确定塔壳内的温度和流量。
三、物料平衡设计1.塔板的物料平衡计算:根据塔板上液体和气体的温度和流量,计算塔板上液体和气体的物料平衡,以确定各组分的质量分数。
2.塔壳的物料平衡计算:根据塔壳内的温度和流量,计算塔壳内的物料平衡,以确定各组分的质量分数。
四、压力平衡设计1.压力损失计算:根据装塔板和塔壳的结构参数,计算出塔板和塔壳内的压力损失,以确定塔板和塔壳的工作压力。
2.压力平衡设计:根据丙烯-丙烷的物理性质和工艺要求,确定塔板和塔壳的工作压力,从而确保各部分之间的流体压力平衡。
五、其他设计考虑因素1.材料的选择:根据工艺要求和流体性质,选择适当的材料,以确保设备的耐腐蚀性和机械性能。
2.设备的安全性和可靠性:考虑设备的安全性和可靠性,采取必要的安全措施,如设置安全阀、温度传感器等。
丙烯精馏

第三章 精馏过程系统设计————丙烯、丙烷精馏装置设计3.1 设计条件1. 工艺条件:饱和液体进料,进料丙烯含量xf =65%(摩尔分数) 塔顶丙烯含量xD =98%,釜液丙烯含量xw≤2%,总板效率为0.6。
2.操作条件:1)塔顶操作压力:P=1.62MPa (表压) 2)加热剂及加热方法:加热剂——水蒸气 加热方法——间壁换热 3)冷却剂:循环冷却水 4)回流比系数:R/Rmin=1.4。
3.塔板形式:筛板 4.处理量:qnfh=70kmol/h 6.塔板设计位置:塔底3.2 物料衡算及热量衡算1物料衡算:w d f Wx Dx Fz WD F +=+= 其中: D ——塔顶采出 W ——塔底采出 F ——进料量Xd ——塔顶产品组成,摩尔分数Xw ——塔底产品组成,摩尔分数 Zf ——进料组成,摩尔分数解得结过果: h kmol D /9375.45= h kmol W /0625.24= 2.求质量流量:Md=0.98*42+0.02*44=42.04 kg/kmol; Mw=0.02*42+0.98*44=43.964 kg/kmol; Mf=0.65*42+0.35*44=42.7 kg/kmol则 qMd = D •Md/3600 =0.5364kg/s ; qMw = W•Mw/3600 =0.2939kg/s qf=F•Mf/3600=0.8303 kg/s 其中:Md ,Mw ,Mf ——塔顶,塔底,进料物流摩尔质量kg/kmol ; qMd ,qMd ,qf ——塔顶。
塔底,进料物流质量流量kg/s 。
3. 塔内气、液相流量:1)精馏段:L =R •D; V =(R+1)•D;2)提馏段:L'=L+q •F; V'=V-(1-q)•F; L'=V'+W; 其中q=1;则:L’=L+F; V’=V 4. 热量衡算1)再沸器热流量:Qr=V'•r'再沸器加热蒸气的质量流量:Gr= Qr/Rr2)冷凝器热流量:Qc=V •Cp •(t2-t1)冷凝器冷却剂的质量流量:Gc= Qc/(Cl •(t2-t1))3.3 塔板数的计算1 相对挥发度的计算:通过对给定的温度—组成表格,计算相对挥发度α α=Ka/Kb=(ya*xb)/(yb*xa)计算后平均,算得,1.72Mpa (绝)下α=1.131583 1.82Mpa (绝)下α=1.127408 平衡关系:x=y/(α-(α-1)y). 2 估算塔底的压力:已知塔顶的压力为1.62Mpa (表) 即1.72Mpa (绝) 工程经验每块塔板压降100mm 液柱,丙烷-丙烯:密度 460。
丙烯丙烷精馏塔课程设计
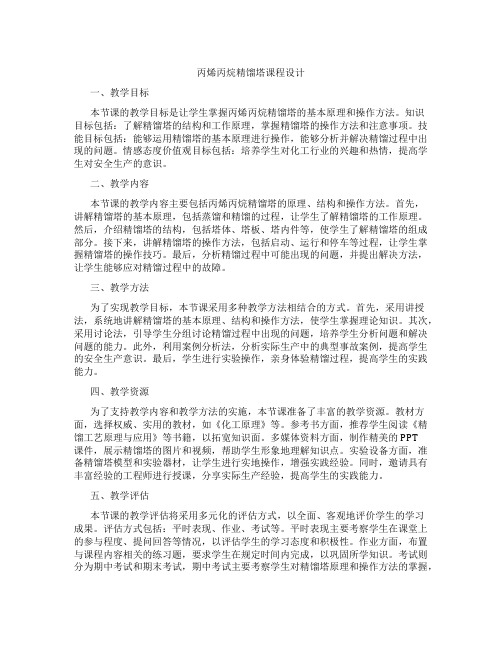
丙烯丙烷精馏塔课程设计一、教学目标本节课的教学目标是让学生掌握丙烯丙烷精馏塔的基本原理和操作方法。
知识目标包括:了解精馏塔的结构和工作原理,掌握精馏塔的操作方法和注意事项。
技能目标包括:能够运用精馏塔的基本原理进行操作,能够分析并解决精馏过程中出现的问题。
情感态度价值观目标包括:培养学生对化工行业的兴趣和热情,提高学生对安全生产的意识。
二、教学内容本节课的教学内容主要包括丙烯丙烷精馏塔的原理、结构和操作方法。
首先,讲解精馏塔的基本原理,包括蒸馏和精馏的过程,让学生了解精馏塔的工作原理。
然后,介绍精馏塔的结构,包括塔体、塔板、塔内件等,使学生了解精馏塔的组成部分。
接下来,讲解精馏塔的操作方法,包括启动、运行和停车等过程,让学生掌握精馏塔的操作技巧。
最后,分析精馏过程中可能出现的问题,并提出解决方法,让学生能够应对精馏过程中的故障。
三、教学方法为了实现教学目标,本节课采用多种教学方法相结合的方式。
首先,采用讲授法,系统地讲解精馏塔的基本原理、结构和操作方法,使学生掌握理论知识。
其次,采用讨论法,引导学生分组讨论精馏过程中出现的问题,培养学生分析问题和解决问题的能力。
此外,利用案例分析法,分析实际生产中的典型事故案例,提高学生的安全生产意识。
最后,学生进行实验操作,亲身体验精馏过程,提高学生的实践能力。
四、教学资源为了支持教学内容和教学方法的实施,本节课准备了丰富的教学资源。
教材方面,选择权威、实用的教材,如《化工原理》等。
参考书方面,推荐学生阅读《精馏工艺原理与应用》等书籍,以拓宽知识面。
多媒体资料方面,制作精美的PPT课件,展示精馏塔的图片和视频,帮助学生形象地理解知识点。
实验设备方面,准备精馏塔模型和实验器材,让学生进行实地操作,增强实践经验。
同时,邀请具有丰富经验的工程师进行授课,分享实际生产经验,提高学生的实践能力。
五、教学评估本节课的教学评估将采用多元化的评估方式,以全面、客观地评价学生的学习成果。
丙烯-丙烷板式精馏塔设计
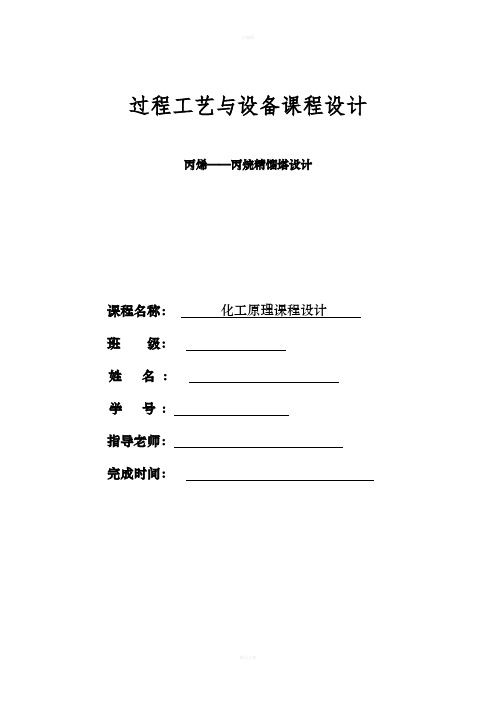
过程工艺与设备课程设计丙烯——丙烷精馏塔设计课程名称:化工原理课程设计班级:姓名:学号:指导老师:完成时间:前言本设计说明书包括概述、流程简介、精馏塔、再沸器、辅助设备、管路设计和控制方案共7章。
说明中对精馏塔的设计计算做了详细的阐述,对于再沸器、辅助设备和管路的设计也做了正确的说明。
鉴于设计者经验有限,本设计中还存在许多错误,希望各位老师给予指正感谢老师的指导和参阅!目录第一节:标题丙烯—丙烷板式精馏塔设计第二节:丙烯—丙烷板式精馏塔设计任务书第三节:精馏方案简介第四节:精馏工艺流程草图及说明第五节:精馏工艺计算及主体设备设计第六节:辅助设备的计算及选型第七节:设计结果一览表第八节:对本设计的评述第九节:工艺流程简图第十节:参考文献第一章任务书设计条件1、工艺条件:饱和液体进料x65进料丙烯含量%=(摩尔百分数)。
F塔顶丙烯含量%x98≥D釜液丙烯含量%x2≤W总板效率为0.62、操作条件:塔顶操作压力1.62MPa(表压)加热剂及加热方法:加热剂——热水加热方法——间壁换热冷却剂:循环冷却水回流比系数:R/Rmin=1.23、塔板形式:浮阀4、处理量:F=50kml/h5、安装地点:烟台6、塔板设计位置:塔顶安装地点:烟台。
处理量:64kmol/h产品质量:进料65%塔顶产品98%塔底产品<2%1、工艺条件:丙烯—丙烷饱和液体进料进料丙烯含量65% (摩尔百分数)塔顶丙烯含量98%釜液丙烯含量<2%总板效率为0.62、操作条件:塔顶操作压力1.62MPa(表压)加热剂及加热方法:加热剂——热水加热方法——间壁换热冷却剂:循环冷却水回流比系数:1.2 1.4 1.63、塔板形式:浮阀4、处理量:F=64kml/h5、安装地点:烟台6、塔板设计位置:塔顶第二章精馏过程工艺及设备概述精馏是分离液体混合物最常用的一种单元操作,在化工,炼油,石油化工等工业中得到广泛应用,精馏过程在能量剂驱动下(有时加质量剂),使气液两相多次直接接触和分离,利用液相混合物中各组分挥发度不同,使易挥发组分由液相向气相转移,难挥发组分由气相向液相转移,实现原料混合液中各组分的分离,该过程是同时传热,传质的过程。
丙烯-丙烷化工课程设计-- 8.3万吨年丙烯-丙烷板式精馏塔设计

班级 01 学生姓名
殷祥
发题时间: 2014 年 6 月 17 日
一、 课题名称
8.3 万吨/年丙烯-丙烷板式精馏塔设计
二、 课题条件(文献资料、仪器设备、指导力量)
1. 课程设计参考书:
(1) 陈敏恒,丛德兹,方图南,齐鸣斋. 化工原理(上、下册)(第二版). 北京:
化学工业出版社,2000
(2) 化学工程手册编辑委会. 化学工程手册,第 1 篇化工基础数据;第 13 篇
项
目
成绩综合评定栏 权分
项 重值
记录人: 年月日
答辩情况 目
权分 重值
1、计算和绘图能力 3 1、回答问题能力 20 5
2、综合运用专业知 1
识能力
0
2、表述能力(逻辑
性、条理性)
10
3、运用计算机能力 1
和外语能力
0
-5-
4、查阅资料、运用
工具书的能力
5
5、独立完成设计能
力
5
6、书写情况(文字
能力、整洁度)
-3-
指导教师(签名): 陈苏芳 学科部主任(签名):
2014 年 6 月 16 日 2014 年 6 月 16 日
《课程设计》综合成绩评定表
学生姓名 殷祥
指导教师评语
学生班级 化工 01
设计题目 8.3 万吨/年丙酮-水板式精馏塔设计
指导教师签字: 年月日
-4-
答辩记录
答辩组成员签字:
设计情况
气液传质设备. 北京:化学工业出版社,1986
(3) 柴诚敬,刘国维,李阿娜. 化工原理课程设计. 天津:天津科学技术出版
社,1995
(4) 陈维杻,传递过程与单元操作. 杭州:浙江大学出版社,1993
化工原理课程设计-丙烯-丙烷-筛板-精馏塔

化工原理课程设计丙烯-丙烷精馏装置设计处理量:60kmol/h产品质量:(以丙稀摩尔百分数计)=65%进料:xf=98%塔顶产品:xD≤2%塔底产品: xw安装地点:总板效率:0.6塔板位置:塔底塔板形式:筛板回流比:1.2班级:姓名:学号:指导老师:设计日期:成绩:前言本设计说明书包括概述、流程简介、精馏塔、再沸器、辅助设备、管路设计和控制方案共七章。
说明中对精馏塔的设计计算做了详细的阐述,对于再沸器、辅助设备和管路的设计也做了正确的说明。
鉴于本人经验有限,本设计中还存在许多错误,希望各位老师给予指正感谢老师的指导和参阅!目录第一章精馏过程工艺设计概述- 1 -一、概述-1-二、工艺设计基本内容-1-1、塔型选择- 1 -2、板型选择- 1 -3、进料状态- 2 -4、回流比- 2 -5、加热剂和再沸器的选择- 2 -6、冷凝器和冷却剂选择- 3 -三、工艺流程(见丙烯——丙烷工艺流程图)-3-第二章筛板塔的工艺设计- 3 -一、物性数据的确定-3-1、塔顶、塔底温度确定- 3 -2、回流比计算- 4 -3、全塔物料衡算- 4 -4、逐板计算塔板数- 5 -5、确定实际塔底压力、板数:- 6 -二、塔板设计-6-1、塔高计算- 6 -2、塔径计算- 6 -3、塔板布置和其余结构尺寸的选取- 7 -4、塔板校核- 9 -5、负荷性能图- 10 -第三章立式热虹吸再沸器的工艺设计- 12 -一、设计条件及物性参数-12-二、工艺设计-13-1、估算再沸器面积- 13 -2、传热系数校核- 14 -3、循环流量校核- 16 -第四章管路设计- 20 -一、物料参数-20-二、设计-20-第五章辅助设备的设计- 22 -一、储罐设计-22-二、传热设备-23-三、泵的设计-24-第六章控制方案- 27 -附录1.理论塔板数计算- 28 -附录2.过程工艺与设备课程设计任务书- 30 -附录3.主要说明符号- 34 -参考资料:- 34 -第一章精馏过程工艺设计概述一、概述化学工程项目的建设过程就是将化学工业X畴的某些设想,实现为一个序列化的、能够达到预期目的的可安全稳定生产的工业生产装置。
丙烯—丙烷板式精馏塔设计1详解

丙烯—丙烷板式精馏塔设计1详解过程工艺与设备课程设计丙烯——丙烷精馏塔设计课程名称:化工原理课程设计班级:姓名:学号:指导老师:完成时间:前言本设计说明书包括概述、流程简介、精馏塔、再沸器、辅助设备、管路设计和控制方案共7章。
说明中对精馏塔的设计计算做了详细的阐述,对于再沸器、辅助设备和管路的设计也做了正确的说明。
鉴于设计者经验有限,本设计中还存在许多错误,希望各位老师给予指正感谢老师的指导和参阅!目录第一节:标题丙烯—丙烷板式精馏塔设计第二节:丙烯—丙烷板式精馏塔设计任务书第三节:精馏方案简介第四节:精馏工艺流程草图及说明第五节:精馏工艺计算及主体设备设计第六节:辅助设备的计算及选型第七节:设计结果一览表第八节:对本设计的评述第九节:工艺流程简图第十节:精馏过程必须在适当的位置设置一定数量不同容积的原料储罐,泵和各种换热器,以暂时储存,运输和预热所用原料,从而保证装置能连续稳定的运行。
必要的检测手段为了方便解决操作中的问题,需在流程中的适当位置设置必要的仪表,以及时获取压力,温度等各项参数。
另外,常在特定地方设置人孔和手孔,以便定期的检测维修。
调节装置于实际生产中各状态参数都不是定值,应在适当的位置放置一定数量的阀门进行调节,以保证达到生产要求,可设双调节,即自动和手动两种调节方式并存,且随时进行切换。
3、设备简介及选用精馏塔选用浮筏塔,配以立式热虹吸式再沸器。
精馏塔精馏塔是一种圆形筒体,塔内装有多层塔板或填料,塔中部适宜位置没有进料板。
本设计为浮筏塔,它已广泛的应用于精馏,吸收,解吸等过程。
其主要特点是在塔板的开孔上装有可浮动的浮筏,可以根据气体或液体的大小上下浮动,自动调节。
再沸器再沸器的作用是将塔底液体部分汽化后送回精馏塔,使塔内汽液两相间接触传质得以进行。
本设计采用立式热虹吸式再沸器,它是一垂直放置的管壳式换热器。
液体在自下而上通过换热器管程时部分汽化,在壳程内的载热体供热。
第三章精馏塔工艺设计第一节设计条件1、工艺条件:饱和液体进料,进料丙烯含量xF?65% (摩尔百分数)。
丙烯-丙烷精馏装置设计

目录任务书 (1)第一章精馏概述 (1)1.1精馏概述 (1)1.2设计原则 (1)1.3精馏塔说明 (2)1.3.1精馏塔主体 (2)1.3.2 再沸器 (2)1.3.3 冷凝器 (2)第二章方案流程简介 (3)2.1工艺流程。
(3)2.2 系统保障与维护 (4)2.2.1物料的储存和运输 (4)2.2.2必要的检测手段 (4)2.2.3 调节装置 (4)2.3工艺参数与操作条件 (4)2.4流程简图 (5)第三章工艺计算 (6)3.1工艺计算 (6)3.1.1物料衡算3.1.2塔板计算 (6)3.2计算机计算 (7)3.3。
1物性数据 (9)3。
3精馏塔工艺设计 (9)3.3.2塔径与塔高估算 (9)3.3.3塔径初步核算 (11)3.3.4堰及降液管设计 (11)3.3.5孔布置 (12)3.3.6干板压降h d (12)3.3.7稳定性 (13)3.3.8塔板压降 (13)3.3.9降液管内液面高度H d (13)3.3.10雾沫夹带量e V (14)3.3.10负荷曲线 (14)3.3.10.1过量液沫夹带线 (14)3.3.10.2液相下限线 (15)3.3。
10.3液相上限线 (15)3.3.10.4严重漏液线 (15)3。
3.10.5浆液管液泛线 (15)3.4再沸器设计 (16)3。
4.1物性数据 (16)3.4。
1.1壳程凝液在温度(100℃)下的物性数据 (16)3。
4.1。
2管程流体在(C o 25.62,2。
84bar )下的物性数据 (17)3.4.2估算设备尺寸 (17)3.5。
1塔顶冷凝器 (18)3。
5。
2泵的设计 (18)3.5.3管路设计........................。
. (20)3。
5.3.1进料管线 (20)3。
5.3.2塔顶蒸汽管 (20)3。
5.3。
3塔顶产品管 (21)3.5。
3.4 回流管 (21)3.5。
3。
5釜液流出管 (21)3.5。
丙烯—丙烷板式精馏塔设计

过程工艺与设备课程设计丙烯——丙烷精馏塔设计课程名称:化工原理课程设计班级:姓名:学号:指导老师:完成时间:前言本设计说明书包括概述、流程简介、精馏塔、再沸器、辅助设备、管路设计和控制方案共7章;说明中对精馏塔的设计计算做了详细的阐述,对于再沸器、辅助设备和管路的设计也做了正确的说明;鉴于设计者经验有限,本设计中还存在许多错误,希望各位老师给予指正感谢老师的指导和参阅目录第一节:标题丙烯—丙烷板式精馏塔设计第二节:丙烯—丙烷板式精馏塔设计任务书第三节:精馏方案简介第四节:精馏工艺流程草图及说明第五节:精馏工艺计算及主体设备设计第六节:辅助设备的计算及选型第七节:设计结果一览表第八节:对本设计的评述第九节:工艺流程简图第十节:参考文献第一章任务书设计条件1、工艺条件:饱和液体进料进料丙烯含量%=摩尔百分数;x65F塔顶丙烯含量%≥x98D釜液丙烯含量%x2W总板效率为2、操作条件:塔顶操作压力表压加热剂及加热方法:加热剂——热水加热方法——间壁换热冷却剂:循环冷却水回流比系数:R/Rmin=3、塔板形式:浮阀4、处理量:F=50kml/h5、安装地点:烟台6、塔板设计位置:塔顶安装地点:烟台;处理量:64kmol/h产品质量:进料 65%塔顶产品 98%塔底产品 <2%1、工艺条件:丙烯—丙烷饱和液体进料进料丙烯含量 65% 摩尔百分数塔顶丙烯含量 98%釜液丙烯含量 <2%总板效率为2、操作条件:塔顶操作压力表压加热剂及加热方法:加热剂——热水加热方法——间壁换热冷却剂:循环冷却水回流比系数:3、塔板形式:浮阀4、处理量:F=64kml/h5、安装地点:烟台6、塔板设计位置:塔顶第二章精馏过程工艺及设备概述精馏是分离液体混合物最常用的一种单元操作,在化工,炼油,石油化工等工业中得到广泛应用,精馏过程在能量剂驱动下有时加质量剂,使气液两相多次直接接触和分离,利用液相混合物中各组分挥发度不同,使易挥发组分由液相向气相转移,难挥发组分由气相向液相转移,实现原料混合液中各组分的分离,该过程是同时传热,传质的过程;为实现精馏过程,必须为该过程提供物流的贮存,输送,传热,分离,控制等的设备,仪表;1、精馏装置流程原料丙烯和丙烷的混合液体经进料管由精馏塔中的某一位置进料板处流入塔内,开始精馏操作;当釜中的料液建立起适当液位时,再沸器进行加热,使之部分汽化返回塔内;气相沿塔上升直至塔顶,由塔顶冷凝器将其进行全部或部分冷凝;将塔顶蒸汽凝液部分作为塔顶产品取出,称为馏出物;另一部分凝液作为回流返回塔顶;回流液从塔顶沿塔流下,在下降过程中与来自塔底的上升蒸汽多次逆向接触和分离;当流至塔底时,被再沸器加热部分汽化,其气相返回塔内作为气相回流,而其液相则作为塔底产品采出;2,、工艺流程1物料的储存和运输精馏过程必须在适当的位置设置一定数量不同容积的原料储罐,泵和各种换热器,以暂时储存,运输和预热或冷却所用原料,从而保证装置能连续稳定的运行;2必要的检测手段为了方便解决操作中的问题,需在流程中的适当位置设置必要的仪表,以及时获取压力,温度等各项参数;另外,常在特定地方设置人孔和手孔,以便定期的检测维修;3调节装置由于实际生产中各状态参数都不是定值,应在适当的位置放置一定数量的阀门进行调节,以保证达到生产要求,可设双调节,即自动和手动两种调节方式并存,且随时进行切换;3、设备简介及选用精馏塔选用浮筏塔,配以立式热虹吸式再沸器;1精馏塔精馏塔是一种圆形筒体,塔内装有多层塔板或填料,塔中部适宜位置没有进料板;本设计为浮筏塔,它已广泛的应用于精馏,吸收,解吸等过程;其主要特点是在塔板的开孔上装有可浮动的浮筏,可以根据气体或液体的大小上下浮动,自动调节;2再沸器再沸器的作用是将塔底液体部分汽化后送回精馏塔,使塔内汽液两相间接触传质得以进行;本设计采用立式热虹吸式再沸器,它是一垂直放置的管壳式换热器;液体在自下而上通过换热器管程时部分汽化,由在壳程内的载热体供热;第三章 精馏塔工艺设计第一节 设计条件1、 工艺条件:饱和液体进料,进料丙烯含量%65x F = 摩尔百分数;塔顶丙烯含量%98x D ≥ ,釜液丙烯含量%2x W ≤ ,总板效率为;2、操作条件:1塔顶操作压力表压加热剂及加热方法:加热剂——热水加热方法——间壁换热冷却剂:循环冷却水回流比系数:R/Rmin=3、塔板形式:浮阀4、处理量:F=50kml/h5、安装地点:烟台6、塔板设计位置:塔顶 第二节 精馏过程工艺计算1、全塔物料衡算q nDh +q nWh =q nFh q nDh x d +q nWh x w =q nFh x f解得: q nDh =h ; q nWh =h2、塔顶、塔底温度确定①、塔顶压力Pt=1620+=;假设塔顶温度Tto=316K 经泡点迭代计算得塔顶温度Tt=查P-T-K 图 得K A 、K B 因为Y A =结果小于10-3;所以假设正确,得出塔顶温度为;用同样的计算,可以求出其他塔板温度; α1=KA/KB=②、塔底温度设NT=120含塔釜则NP=NT-1/ =198按每块阻力降100液柱计算 pL=470kg/m3则P底=P顶+120×100×÷1000 =假设塔顶温度Tto=324K 经泡点迭代计算得塔顶温度T=查P-T-K图得KA 、KB因为XA=结果小于10-3;所以假设正确,得出塔顶温度为;用同样的计算,可以求出其他塔板温度;α2=KA/KB=所以相对挥发度α=α1+α2/2=3、回流比计算泡点进料:q=1q线:x=xf = 65%代入数据,解得 xe=;ye=;R===1 精馏塔的物料衡算;2 塔板数的确定:3 精馏塔的工艺条件及有关物件数据的计算;4 精馏塔的塔体工艺尺寸计算;5 塔板主要工艺尺寸的计算;6 塔板的流体力学验算:7 塔板负荷性能图;8 精馏塔接管尺寸计算;9 绘制生产工艺流程图;10 绘制精馏塔设计条件图;11 对设计过程的评述和有关问题的讨论;设计方案的确定及工艺流程的说明原料液由泵从原料储罐中引出,在预热器中预热至84℃后送入连续板式精馏塔筛板塔,塔顶上升蒸汽流采用强制循环式列管全凝器冷凝后一部分作为回流液,其余作为产品经冷却至25℃后送至产品槽;塔釜采用热虹吸立式再沸器提供气相流,塔釜残液送至废热锅炉;第四节:精馏工艺流程草图及说明一、流程方案的选择1.生产流程方案的确定:原料主要有三个组分:C2°、C3=、C3°,生产方案有两种:见下图A,B如任务书规定:C2° C3= C3° iC4° iC4=∑W% 100A为按挥发度递减顺序采出,图B为按挥发度递增顺序采出;在基本有机化工生产过程中,按挥发度递减的顺序依次采出馏分的流程较常见;因各组分采出之前只需一次汽化和冷凝,即可得到产品;而图B所示方法中,除最难挥发组分外;其它组分在采出前需经过多次汽化和冷凝才能得到产品,能量热量和冷量消耗大;并且,由于物料的内循环增多,使物料处理量加大,塔径也相应加大,再沸器、冷凝器的传热面积相应加大,设备投资费用大,公用工程消耗增多,故应选用图A所示的是生产方案;2.工艺流程分离法的选择:在工艺流程方面,主要有深冷分离和常温加压分离法;脱乙烷塔,丙烯精制塔采用常温加压分离法;因为C2,C3在常压下沸点较低呈气态采用加压精馏沸点可提高,这样就无须冷冻设备,可使用一般水为冷却介质,操作比较方便工艺简单,而且就精馏过程而言,获得高压比获得低温在设备和能量消耗方面更为经济一些,但高压会使釜温增加,引起重组分的聚合,使烃的相对挥发度降低,分离难度加大;可是深冷分离法需采用制冷剂来得到低温,采用闭式热泵流程,将精馏塔和制冷循环结合起来,工艺流程复杂;综合考滤故选用常温加压分离法流程;二、工艺特点:1、脱乙烷塔:根据原料组成及计算:精馏段只设四块浮伐塔板,塔顶采用分凝器、全回流操作2、丙烯精制塔:混合物借精馏法进行分离时它的难易程度取决于混合物的沸点差即取决于他们的相对挥发度丙烷-丙烯的沸点仅相差5—6℃所以他们的分离很困难,在实际分离中为了能够用冷却水来冷凝丙烯的蒸气经常把C3馏分加压到20大气压下操作,丙烷-丙烯相对挥发度几乎接近于1在这种情况下,至少需要120块塔板才能达到分离目的;建造这样多板数的塔, 高度在45米以上是很不容易的,因而通常多以两塔串连应用,以降低塔的高度;三、操作特点:1、压力:采用不凝气外排来调节塔内压力,在其他条件不变的情况下,不凝气排放量越大、塔压越低:不凝气排放量越小、塔压越高;正常情况下压力调节主要靠调节伐自动调节;2、塔低温度:恒压下,塔低温度是调节产品质量的主要手段,釜温是釜压和物料组成决定的,塔低温度主要靠重沸器加热汽来控制;当塔低温度低于规定值时,应加大蒸汽用量以提高釜液的汽化率塔低温度高于规定值时,操作亦反;四、改革措施:丙烯精制塔顶冷却器由四台串联改为两台并联,且每台冷却器设计时采用的材质较好,管束较多,传热效果好;五、设想:若本装置采用DCS控制操作系统,这样可以使操作者一目了然,可以达到集中管理,分散控制的目的;能够使信息反馈及时,使装置平稳操作,提高工作效率;为了降低能耗丙烯塔可以采用空冷 ;第五节:精馏工艺计算及主体设备设计精馏塔的工艺设计计算,包括塔高、塔径、塔板各部分尺寸的设计计算,塔板的布置,塔板流体力学性能的校核及绘出塔板的性能负荷图;1 物料衡算与操作线方程通过全塔物料衡算,可以求出精馏产品的流量、组成和进料流量、组成之间的关系;物料衡算主要解决以下问题:1根据设计任务所给定的处理原料量、原料浓度及分离要求塔顶、塔底产品的浓度计算出每小时塔顶、塔底的产量;2在加料热状态q和回流比R选定后,分别算出精馏段和提馏段的上升蒸汽量和下降液体量;3写出精馏段和提馏段的操作线方程,通过物料衡算可以确定精馏塔中各股物料的流量和组成情况,塔内各段的上升蒸汽量和下降液体量,为计算理论板数以及塔径和塔板结构参数提供依据;通常,原料量和产量都以kg/h或吨/年来表示,但在理想板计算时均须转换为kmol/h;在设计时,汽液流量又须用m3/s来表示;因此要注意不同的场合应使用不同的流量单位;2、塔物料衡算F=D+WFXf=DXD+WXw则代入数据为64=D+W6465%=D98%+W2%解得D=h,W=h塔内气、液相流量精馏段:L=RD,V=L+D提留段:L’=L+F,V’=V3.热量衡算再沸器热流量:qr=V’rv再沸器加热蒸汽质量流量:Gr=Qr/rR冷凝器热流量:Qc=Vrv冷凝器冷却剂的质量流量:Gc=Qc/Cvt1-t2塔板数的计算相对挥发度利用试差法求相对挥发度表压P=1620kpa,则塔顶绝压Ptop=+= LnPA’=同理得PB’==Y A=P-PB’/PA’-PB’=KA=PA’/P=XA=y A/KA==同理得y B=,KB=,XB=y B/KB=∑X=y A/KA+y B/KB=∑y-1==<,符合要求故塔顶温度Ttop=塔顶挥发度阿a AB=KA/KB==1.塔底挥发度a’AB由xn=yn/a-a-1yn得,xn=查资料得表如下:液相组分质量分数为WA=,WB=塔顶液相密度为m3气相密度为m3设理论塔板数位NT=150,设每块塔板上的压降为100mm液柱;经计算得latm=液柱塔底压力P=Ptop+NT100mm=设塔底温度为由lnPA’=A-B/T+C得, lnPA’=同理得PB’==所以XA=P-PB’/PA’-PB’=, y B=所以,塔底温度为a AB=KA/KB==2.计算回流比R由相平衡方程ye=a xe/1+a-1xe和q线方程q=1,计算得xe=时,ye=Rmin=XD-ye/ye-xe=则R=,Rmin=3.计算精馏段操作方程精馏段操作线方程yn+1=R/R+1xn+XD/R+1代入数据得该精馏操作方程为yn+1=+4.计算塔板数经过模拟计算得所需理论板数为NT=95理论进料板位置Nf=44已知总办效率为ET=进料板位置Nf/=73所以实际塔板数为Np=NT-1/ET=95-1/=155实际塔板数和初设塔板数150比较接近,故所设值比较合理;5.塔径计算两相流动参数=Ls/Vs√p1/pv=设间距Ht=,查图知C20=气体负荷因子C=C20ó/20{方}=液泛气速Uf=C√p L-pv/pv=su/Uf=,则u=s则流道截面积A=Vs/u= m2孔隙率Ad/At=,A/At=1-Ad/At=则At==塔径D=√4At/=查表知D=,Ht=,与设的吻合,则合理;6.塔高计算实际板数为155,塔有效高度Z=155=釜液流出量W=h=h=s则釜液高度△ Z=4W/DD =143块塔板,共设8个人孔,每个人孔处板间距增大200mm 进料板板间距增大100mm裙坐取3m塔顶与釜液上方气液分离高度取塔顶与釜液上方气液分离空间高度均取总塔高Z=+++8+2=7.溢流装置设计计算弓形降液管所占面积Ad=At-A=Lw/D=,降液管宽度Bd=D1-√1- Lw/d Lw/d/2=取底隙h=确定堰长Lw=D==堰上液头高How=Lh/Lw2/3=>6mm满足E取1的条件取Hw=,清夜层高度Hl由选取的堰高Hw确定Hl=Hw+How=+=液流强度Lh/lw==<100降液管底隙液体流速u=Ls/lwhb=s<s,符合要求8.塔板流动性能的校核所得泛点率低于,故不会产生过量的液沫夹带计算干板阻力由以上3个阻力之和求塔板阻力=12.塔板负荷性能图1.过量液沫夹带线2.液相下限线How=Lh/lw2/3=取E=1,lw=,Lh==h此为液相下限线3.严重漏液线3.液相上限线4、精馏塔主体设备设计计算、再沸器精馏塔底的再沸器可分为:釜式再沸器、热虹吸式再沸器及强制循环再沸器;1釜式式再沸器如图6-2a和b所示;a是卧式再沸器,壳方为釜液沸腾,管内可以加热蒸汽;塔底液体进入底液池中,再进入再沸器的管际空间被加热而部分汽化;蒸汽引到塔底最下一块塔板的下面,部分液体则通过再沸器内的垂直挡板,作为塔底产物被引出;液体的采出口与垂直塔板之间的空间至少停留8~10分钟,以分离液体中的气泡;为减少雾沫夹带,再沸器上方应有一分离空间,对于小设备,管束上方至少有300mm高的分离空间,对于大设备,取再沸器壳径为管束直径的~倍;b是夹套式再沸器,液面上方必须留有蒸发空间,一般液面维持在容积的70%左右;夹套式再沸器,常用于传热面较小或间歇精馏中;2热虹吸式再沸器如图6-2c、D、e所示;它是依靠釜内部分汽化所产生的汽、液混合物其密度小于塔底液体密度,由密度差产生静压差使液体自动从塔底流入再沸器,因此该种再沸器又称自然循环再沸器;这种型式再沸器汽化率不大于40%,否则传热不良;3强制循环再沸器如图6-2中f所示;对于高粘度液体和热敏性气体,宜用泵强制循环式再沸器,因流速大、停留时间短,便于控制和调节液体循环量;原料预热器和产品冷却器的型式不象塔顶冷凝器和塔底再沸器的制约条件那样多,可按传热原理计算;图6-2 再沸器的型式、管路尺寸的确定、管路阻力计算及泵的选择接管直径各接管直径由流体速度及其流量,按连续性方程决定,即:d= 6-7式中:V S——流体体积流量,m3/ s;u——流体流速,m/ s;d——管子直径,m;1塔顶蒸气出口管径D V蒸气出口管中的允许气速U V应不产生过大的压降,其值可参照表6-1;表6-1 蒸气出口管中允许气速参照表2回流液管径D R冷凝器安装在塔顶时,冷凝液靠重力回流,一般流速为~s,速度太大,则冷凝器的高度也相应增加;用泵回流时,速度可取~s;3进料管径d F料液由高位槽进塔时,料液流速取~s;由泵输送时,流速取为~m/s;4釜液排除管径d W釜液流出的速度一般取~s;5饱和水蒸气管饱和水蒸气压力在295kPa表压以下时,蒸气在管中流速取为20~40m/s;表压在785 kPa以下时,流速取为40~60m/s;表压在2950 kPa以上时,流速取为80m/s;加热蒸气鼓泡管加热蒸气鼓泡管又叫蒸气喷出器若精馏塔采用直接蒸气加热时,在塔釜中要装开孔的蒸气鼓泡管;使加热蒸气能均匀分布与釜液中;其结构为一环式蒸气管,管子上适当的开一些小孔;当小孔直径小时,汽泡分布的更均匀;但太小不仅增加阻力损失,而且容易堵塞;其孔直径一般为5~10mm ,孔距为孔径的5~10倍;小孔总面积为鼓泡管横截面积的~倍,管内蒸气速度为20~25m /s;加热蒸气管距釜中液面的高度至少在以上,以保证蒸气与溶液有足够的接触时间;离心泵的选择离心泵的选择,一般可按下列的方法与步骤进行:1确定输送系统的流量与压头 液体的输送量一般为生产任务所规定,如果流量在一定范围内波动,选泵时应按最大流量考虑;根据输送系统管路的安排,用柏努利方程计算在最大流量下管路所需的压头;2选择泵的类型与型号 首先应根据输送液体的性质和操作条件确定泵的类型,然后按已确定的流量Q e 和压头H e 从泵的样本或产品目录中选出合适的型号;显然,选出的泵所提供的流量和压头不见得与管路要求的流量Q e 和压头H e 完全相符,且考虑到操作条件的变化和备有一定的裕量,所选泵的流量和压头可稍大一点,但在该条件下对应泵的效率应比较高,即点Q e 、H e 坐标位置应靠在泵的高效率范围所对应的H-Q 曲线下方;另外,泵的型号选出后,应列出该泵的各种性能参数;3核算泵的轴功率 若输送液体的密度大于水的密度时,可按,102QH N kW ρη=核算泵的轴功率;第六节:辅助设备的计算及选型精馏装置的主要附属设备包括蒸气冷凝器、产品冷凝器、塔底再沸器、原料预热器、直接蒸汽鼓管、物料输送管及泵等;前四种设备本质上属换热器,并多采用列管式换热器,管线和泵属输送装置;下面简要介绍;回流冷凝器按冷凝器与塔的位置,可分为:整体式、自流式和强制循环式;1整体式如图6-1a和b所示;将冷凝器与精馏塔作成一体;这种布局的优点是上升蒸汽压降较小,蒸汽分布均匀,缺点是塔顶结构复杂,不便维修,当需用阀门、流量计来调节时,需较大位差,须增大塔顶板与冷凝器间距离,导致塔体过高;该型式常用于减压精馏或传热面较小场合;图6-1 冷凝器的型式2自流式如图6-1c 所示;将冷凝器装在塔顶附近的台架上,靠改变台架的高度来获得回流和采出所需的位差;3强制循环式如图6-1D 、e 所示;当冷凝器换热面过大时,装在塔顶附近对造价和维修都是不利的,故将冷凝器装在离塔顶较远的低处,用泵向塔提供回流液;需指出的是,在一般情况下,冷凝器采用卧式,因为卧式的冷凝液膜较薄,故对流传热系数较大,且卧式便于安装和维修;管壳式换热器的设计与选型管壳式换热器的设计与选型的核心是计算换热器的传热面积,进而确定换热器的其它尺寸或选择换热器的型号;.1流体流动阻力压强降的计算1管程流动阻力管程阻力可按一般摩擦阻力公式求得;对于多程换热器,其阻力ΣΔp i 等于各程直管阻力、回弯阻力及进、出口阻力之和;一般情况下进、出口阻力可忽略不计,故管程总阻力的计算式为12()i t s p p p p F N N ∑∆=∆+∆ 6-1 式中 ΔP 1、ΔP 2——分别为直管及回弯管中因摩擦阻力引起的压强降,P a ;F t ——结垢校正因数,对Φ25mm ×的管子取;对Φ19mm ×2mm 的管子取;N P ——管程数;N s ——串联的壳程数;上式中直管压强降ΔP 1可按第一章中介绍的公式计算;回弯管的压强降ΔP 2由下面的经验公式估算,即 2232u p ρ⎛⎫∆= ⎪⎝⎭6-22壳程流动阻力壳程流动阻力的计算公式很多,在此介绍埃索法计算壳程压强降ΔP 0的公式,即012S p p p N ∑∆=∆+∆’’S ()F 6-3式中 ΔP 1’——流体横过管束的压强降,Pa ;ΔP 2’——流体通过折流板缺口的压强降,Pa ;F S ——壳程压强降的结垢校正因数;液体可取,气体可取;2'0102'02(1)22(3.5)2c B B u p Ff n N u h p N D ρρ∆=+∆=- 6-4 式中 F ——管子排列方法对压强降的校正因数,对正三角形排列F =,对转角三角形为,正方形为;f0——壳程流体的摩擦系数;N c——横过管束中心线的管子数;N c值可由下式估算:管子按正三角形排列:n=c管子按正方形排列:n=c式中 n——换热器总管数;N B——折流挡板数;h——折流挡板间距;u0——按壳程流通截面积A0计算的流速,m/s,而A0=hD-n c d0;2管壳式换热器的选型和设计计算步骤1计算并初选设备规格a.确定流体在换热器中的流动途径b.根据传热任务计算热负荷Q;c.确定流体在换热器两端的温度,选择列管换热器的形式;计算定性温度,并确定在定性温度下的流体物性;d.计算平均温度差,并根据温度差校正系数不应小于的原则,决定壳程数;e.依据总传热系数的经验值范围,或按生产实际情况,选择总传热系数K值;f.由总传热速率方程Q = KSΔt m,初步计算出传热面积S,并确定换热器的基本尺寸如D、L、n及管子在管板上的排列等,或按系列标准选择设备规格;2计算管程、壳程压强降根据初定的设备规格,计算管程、壳程流体的流速和压强降;检查计算结果是否合理或满足工艺要求;若压降不符合要求,要调整流速,在确定管程数或折流板间距,或选择另一规格的换热器,重新计算压强降直至满足要求为止;3核算总传热系数计算管程、壳程对流传热系数,确定污垢热阻R si和R so,在计算总传热系数K’,比较K 的初设值和计算值,若K’ /K=~,则初选的换热器合适;否则需另设K值,重复以上计算步骤;第七节:设计结果一览表1、操作条件及物性系数操作压力:塔顶塔底 MPa操作温度:塔顶塔底2、塔板主要工艺尺寸水力学核算第八节:对本设计的评述作为本学期难得的一次大型作业报告,我个人而言,收获良多,首先是看到了自己的不足,例如一些以前学习过的内容能够得到复习,毕竟差不多一年过去了,CAD课程内容所教授的内容,许多都已经不记得了,通过这次大型课题报告,让我们重新学习和掌握CAD课程;而且由于类似这种大型作业报告,需要考虑多方面的问题,必须多方面考虑周全,所以这次作业,也让我在做事方面想得更加周全,面面俱到,这对于我们这些学生而言,是非常难得的;本人参照了指导老师给我们的指导资料,并参考了其他学长的个人设计格式,查阅了较多的关于本专业的相关资料文献,花费了不少的时间勉强完成了这个设计方案,但由于个人专业知识缺乏和时间上比较仓促,所以未能完成得很好;通过这次课程设计使我充分理解到化工原理课程的重要性和实用性,更特别是对精馏原理及其操作各方面的了解和设计,对实际单元操作设计中所涉及的个方面要注意问题都有所了解;通过这次对精馏塔的设计,不仅让我将所学的知识应用到实际中,而且对知识也是一种巩固和提升充实;在老师和同学的帮助下,及时的按要求完成了设计任务,通过这次课程设计,使我获得了很多重要的知识,同时也提高了自己的实际动手和知识的灵活运用能力;至此,对于里面一些不当的操作及数据,我总结出了以下原因:1、物料平衡的影响和制约根据精馏塔的总物料衡算可知,不能任意增减,否则进、出塔的两个组分的量不平衡,必然导致塔内组成变化,操作波动,使操作不能达到预期的分离要求;2、塔顶回流的影响回流比是影响精馏塔分离效果的主要因素,生产中经常用回流比来调节、控制产品的质量;3、进料热状况的影响当进料状况xF和q发生变化时,应适当改变进料位置,并及时调节回流比R;一般精馏塔常设几个进料位置,以适应生产中进料状况,保证在精馏塔的适宜位置进料;如进料状况改变而进料位置不变,必然引起馏出液和釜残液组成的变化;4、塔釜温度的影响釜温是由釜压和物料组成决定的;精馏过程中,只有保持规定的釜温,才能确保产品。
- 1、下载文档前请自行甄别文档内容的完整性,平台不提供额外的编辑、内容补充、找答案等附加服务。
- 2、"仅部分预览"的文档,不可在线预览部分如存在完整性等问题,可反馈申请退款(可完整预览的文档不适用该条件!)。
- 3、如文档侵犯您的权益,请联系客服反馈,我们会尽快为您处理(人工客服工作时间:9:00-18:30)。
过程工艺与设备课程设计丙烯——丙烷精馏塔设计课程名称:化工原理课程设计班级:姓名:学号:指导老师:完成时间:前言本设计说明书包括概述、流程简介、精馏塔、再沸器、辅助设备、管路设计和控制方案共7章。
说明中对精馏塔的设计计算做了详细的阐述,对于再沸器、辅助设备和管路的设计也做了正确的说明。
鉴于设计者经验有限,本设计中还存在许多错误,希望各位老师给予指正感老师的指导和参阅!目录第一节:标题丙烯—丙烷板式精馏塔设计第二节:丙烯—丙烷板式精馏塔设计任务书第三节:精馏方案简介第四节:精馏工艺流程草图及说明第五节:精馏工艺计算及主体设备设计第六节:辅助设备的计算及选型第七节:设计结果一览表第八节:对本设计的评述第九节:工艺流程简图第十节:参考文献第一章 任务书设计条件1、 工艺条件:饱和液体进料进料丙烯含量%65x F = (摩尔百分数)。
塔顶丙烯含量%98x D ≥釜液丙烯含量%2x W ≤总板效率为0.62、操作条件:塔顶操作压力1.62MPa(表压)加热剂及加热方法:加热剂——热水加热方法——间壁换热冷却剂:循环冷却水回流比系数:R/Rmin=1.23、塔板形式:浮阀4、处理量:F=50kml/h5、安装地点:6、塔板设计位置:塔顶安装地点:。
处理量:64kmol/h产品质量:进料65%塔顶产品98%塔底产品<2%1、工艺条件:丙烯—丙烷饱和液体进料进料丙烯含量65% (摩尔百分数) 塔顶丙烯含量98%釜液丙烯含量<2%总板效率为0.62、操作条件:塔顶操作压力1.62MPa(表压)加热剂及加热方法:加热剂——热水加热方法——间壁换热冷却剂:循环冷却水回流比系数:1.2 1.4 1.63、塔板形式:浮阀4、处理量:F=64kml/h5、安装地点:6、塔板设计位置:塔顶第二章精馏过程工艺及设备概述精馏是分离液体混合物最常用的一种单元操作,在化工,炼油,石油化工等工业中得到广泛应用,精馏过程在能量剂驱动下(有时加质量剂),使气液两相多次直接接触和分离,利用液相混合物中各组分挥发度不同,使易挥发组分由液相向气相转移,难挥发组分由气相向液相转移,实现原料混合液中各组分的分离,该过程是同时传热,传质的过程。
为实现精馏过程,必须为该过程提供物流的贮存,输送,传热,分离,控制等的设备,仪表。
1、精馏装置流程原料(丙烯和丙烷的混合液体)经进料管由精馏塔中的某一位置(进料板处)流入塔,开始精馏操作;当釜中的料液建立起适当液位时,再沸器进行加热,使之部分汽化返回塔。
气相沿塔上升直至塔顶,由塔顶冷凝器将其进行全部或部分冷凝。
将塔顶蒸汽凝液部分作为塔顶产品取出,称为馏出物。
另一部分凝液作为回流返回塔顶。
回流液从塔顶沿塔流下,在下降过程中与来自塔底的上升蒸汽多次逆向接触和分离。
当流至塔底时,被再沸器加热部分汽化,其气相返回塔作为气相回流,而其液相则作为塔底产品采出。
2,、工艺流程(1)物料的储存和运输精馏过程必须在适当的位置设置一定数量不同容积的原料储罐,泵和各种换热器,以暂时储存,运输和预热(或冷却)所用原料,从而保证装置能连续稳定的运行。
(2)必要的检测手段为了方便解决操作中的问题,需在流程中的适当位置设置必要的仪表,以及时获取压力,温度等各项参数。
另外,常在特定地方设置人孔和手孔,以便定期的检测维修。
(3)调节装置由于实际生产中各状态参数都不是定值,应在适当的位置放置一定数量的阀门进行调节,以保证达到生产要求,可设双调节,即自动和手动两种调节方式并存,且随时进行切换。
3、设备简介及选用精馏塔选用浮筏塔,配以立式热虹吸式再沸器。
(1)精馏塔精馏塔是一种圆形筒体,塔装有多层塔板或填料,塔中部适宜位置没有进料板。
本设计为浮筏塔,它已广泛的应用于精馏,吸收,解吸等过程。
其主要特点是在塔板的开孔上装有可浮动的浮筏,可以根据气体或液体的大小上下浮动,自动调节。
(2)再沸器再沸器的作用是将塔底液体部分汽化后送回精馏塔,使塔汽液两相间接触传质得以进行。
本设计采用立式热虹吸式再沸器,它是一垂直放置的管壳式换热器。
液体在自下而上通过换热器管程时部分汽化,由在壳程的载热体供热。
第三章 精馏塔工艺设计第一节 设计条件1、 工艺条件:饱和液体进料,进料丙烯含量%65x F (摩尔百分数)。
塔顶丙烯含量%98x D ≥ ,釜液丙烯含量%2x W ≤ ,总板效率为0.6。
2、操作条件:(1)塔顶操作压力1.62MPa(表压)加热剂及加热方法:加热剂——热水加热方法——间壁换热冷却剂:循环冷却水回流比系数:R/Rmin=1.23、塔板形式:浮阀4、处理量:F=50kml/h5、安装地点:6、塔板设计位置:塔顶 第二节 精馏过程工艺计算1、全塔物料衡算q nDh +q nWh =q nFhq nDh x d +q nWh x w =q nFh x f解得: q nDh =32.81kmol/h ; q nWh =17.19kmol/h2、塔顶、塔底温度确定①、塔顶压力Pt=1620+101.325=1721.325KPa ;假设塔顶温度Tto=316K 经泡点迭代计算得塔顶温度Tt=316.145K查P-T-K 图 得K A 、K B 因为Y A =0.98()0006.01/1/1x=---⨯=-=∑B A A A n i i K Y K Y ε结果小于10-3。
所以假设正确,得出塔顶温度为316.145。
用同样的计算,可以求出其他塔板温度。
α1=KA/KB=1.15②、塔底温度设NT=120(含塔釜)则NP=(NT-1)/0.6 =198按每块阻力降100液柱计算 p L =470kg/m 3则P 底=P 顶+120×100×9.8÷1000 =1838.925KPa假设塔顶温度Tto=324K 经泡点迭代计算得塔顶温度T=324.37K查P-T-K 图 得K A 、K B 因为X A =0.02()0004.01/11y=---⨯=-=∑B A A A n i i K X K X ε结果小于10-3。
所以假设正确,得出塔顶温度为324.37。
用同样的计算,可以求出其他塔板温度。
α2=KA/KB=1.116所以相对挥发度α=(α1+α2)/2=1.1333、回流比计算泡点进料:q=1q 线:x=xf = 65%2.2115.60-77.6077.60-8.90min ==--=e e e D x y y x R 代入数据,解得 xe=0.65;ye=0.677;R=1.2Rmin=13.47原料液由泵从原料储罐中引出,在预热器中预热至84℃后送入连续板式精馏塔(筛板塔),塔顶上升蒸汽流采用强制循环式列管全凝器冷凝后一部分作为回流液,其余作为产品经冷却至25℃后送至产品槽;塔釜采用热虹吸立式再沸器提供气相流,塔釜残液送至废热锅炉。
第四节:精馏工艺流程草图及说明一、流程方案的选择1.生产流程方案的确定:原料主要有三个组分:C2°、C3=、C3°,生产方案有两种:(见下图A,B)如任务书规定:C2°C3=C3°iC4°iC4=∑W% 5.00 73.20 20.80 0.52 0.48 100A)为按挥发度递减顺序采出,图(B)为按挥发度递增顺序采出。
在基本有机化工生产过程中,按挥发度递减的顺序依次采出馏分的流程较常见。
因各组分采出之前只需一次汽化和冷凝,即可得到产品。
而图(B)所示方法中,除最难挥发组分外。
其它组分在采出前需经过多次汽化和冷凝才能得到产品,能量(热量和冷量)消耗大。
并且,由于物料的循环增多,使物料处理量加大,塔径也相应加大,再沸器、冷凝器的传热面积相应加大,设备投资费用大,公用工程消耗增多,故应选用图(A)所示的是生产方案。
2.工艺流程分离法的选择:在工艺流程方面,主要有深冷分离和常温加压分离法。
脱乙烷塔,丙烯精制塔采用常温加压分离法。
因为C2,C3在常压下沸点较低呈气态采用加压精馏沸点可提高,这样就无须冷冻设备,可使用一般水为冷却介质,操作比较方便工艺简单,而且就精馏过程而言,获得高压比获得低温在设备和能量消耗方面更为经济一些,但高压会使釜温增加,引起重组分的聚合,使烃的相对挥发度降低,分离难度加大。
可是深冷分离法需采用制冷剂来得到低温,采用闭式热泵流程,将精馏塔和制冷循环结合起来,工艺流程复杂。
综合考滤故选用常温加压分离法流程。
二、工艺特点:1、脱乙烷塔:根据原料组成及计算:精馏段只设四块浮伐塔板,塔顶采用分凝器、全回流操作2、丙烯精制塔:混合物借精馏法进行分离时它的难易程度取决于混合物的沸点差即取决于他们的相对挥发度丙烷-丙烯的沸点仅相差5—6℃所以他们的分离很困难,在实际分离中为了能够用冷却水来冷凝丙烯的蒸气经常把C3馏分加压到20大气压下操作,丙烷-丙烯相对挥发度几乎接近于1在这种情况下,至少需要120块塔板才能达到分离目的。
建造这样多板数的塔,高度在45米以上是很不容易的,因而通常多以两塔串连应用,以降低塔的高度。
三、操作特点:1、压力:采用不凝气外排来调节塔压力,在其他条件不变的情况下,不凝气排放量越大、塔压越低:不凝气排放量越小、塔压越高。
正常情况下压力调节主要靠调节伐自动调节。
2、塔低温度:恒压下,塔低温度是调节产品质量的主要手段,釜温是釜压和物料组成决定的,塔低温度主要靠重沸器加热汽来控制。
当塔低温度低于规定值时,应加大蒸汽用量以提高釜液的汽化率塔低温度高于规定值时,操作亦反。
四、改革措施:丙烯精制塔顶冷却器由四台串联改为两台并联,且每台冷却器设计时采用的材质较好,管束较多,传热效果好。
五、设想:若本装置采用DCS控制操作系统,这样可以使操作者一目了然,可以达到集中管理,分散控制的目的。
能够使信息反馈及时,使装置平稳操作,提高工作效率。
为了降低能耗丙烯塔可以采用空冷。
第五节:精馏工艺计算及主体设备设计精馏塔的工艺设计计算,包括塔高、塔径、塔板各部分尺寸的设计计算,塔板的布置,塔板流体力学性能的校核及绘出塔板的性能负荷图。
1 物料衡算与操作线方程通过全塔物料衡算,可以求出精馏产品的流量、组成和进料流量、组成之间的关系。
物料衡算主要解决以下问题:(1)根据设计任务所给定的处理原料量、原料浓度及分离要求(塔顶、塔底产品的浓度)计算出每小时塔顶、塔底的产量;(2)在加料热状态q和回流比R选定后,分别算出精馏段和提馏段的上升蒸汽量和下降液体量;(3)写出精馏段和提馏段的操作线方程,通过物料衡算可以确定精馏塔中各股物料的流量和组成情况,塔各段的上升蒸汽量和下降液体量,为计算理论板数以及塔径和塔板结构参数提供依据。
通常,原料量和产量都以kg/h或吨/年来表示,但在理想板计算时均须转换为kmol/h。