板坯漏钢概述
漏钢

漏钢是指连铸初期或浇注过程中,铸坯坯壳凝固情况不好或因其他外力作用引起坯壳断裂或破漏使内部钢水流出的现象。
主要类型:1、开浇漏钢原理:由于生产准备不足,出现引锭头密封不严、结晶器角缝超标、中包或浸入式水口烘烤温度不达标,开浇时在塞棒头与水口碗部结冷钢使塞棒控流失败,钢流过小多次开浇或出苗时间控制过短、过长,开浇钢水温度过低、过高等均容易造成开浇漏钢。
特征:开浇起步期间,引锭头刚拉出结晶器就发生漏钢。
2、裂纹漏钢原理:浇铸时,由于初生坯壳在结晶器内产生纵裂、角裂或横裂,出结晶器后,因二次冷却强度不匹配,产生裂纹扩大或由于铸坯在二冷段产生严重的变形,随着钢水静压力的增大坯壳破裂,造成漏钢。
特征:漏钢后在残坯部位可看到明显的裂纹,漏钢部位通常在二冷段。
3、粘结漏钢原理:在结晶器弯月面处,钢水与结晶器铜板直接接触,初生坯壳与结晶器铜板的摩擦力大于坯壳的抗拉强度,导致粘结处被拉裂,钢液从裂口流出,形成新的坯壳,新坯壳再次被拉裂,此过程反复进行,若坯壳到了结晶器下口仍无法焊合裂口,出结晶器下口后坯壳撕裂发生漏钢。
特征:粘结漏钢多为结晶器内坯壳上厚下薄,坯壳的振痕是呈不对称分布,振痕紊乱,结晶器内坯壳呈V字型或倒三角状,粘结点明显。
4、卷渣漏钢原理:由于结晶器保护渣、夹杂物、耐火材料等卷入凝固坯壳局部区域,造成坯壳厚薄不均匀,坯壳出结晶器进格栅之前,由于卷渣部位的坯壳强度较低,不熔于基体的高熔点夹杂物被冲刷,在坯壳上产生漏洞,坯壳失去支撑,在钢水静压力导致漏钢。
特征:漏钢后一般可在残坯漏钢部位看到明显的结渣,漏钢部位一般在结晶器出口与格栅之间。
5、飞边(悬挂)漏钢原理:由于结晶器角缝大或铜板划伤,钢水渗入结晶器角缝,凝固后铸坯边角部产生带毛刺的飞边,造成结晶器内边部拉坯阻力增大,坯壳极易被撕裂,产生漏钢。
特征:漏钢后在残坯部位窄边有带毛刺的飞边,漏点多在边部且有明显的撕裂痕迹,振痕呈角拉斜状,可见飞边悬挂。
各类漏钢所占比例:开浇9.1%,夹渣2.3%,粘结54.%,裂纹22.7%,鼓肚4.6%,水口凝钢2.3%,其他4.5%。
板坯连铸机粘结漏钢的原因分析及预防 刘雷锋

板坯连铸机粘结漏钢的原因分析及预防刘雷锋摘要:随着连铸技术的发展和广泛应用,连铸坯的质量和品质受到了人们的广泛关注,提高连铸坯的质量成为连铸生产中重点关注的问题之一。
连铸过程开始广泛运用于有色金属行业,尤其是铜和铝。
连铸技术迅速发展起来。
本文对此进行了分析研究。
关键词:坯;连铸;连铸工艺连铸漏钢是个常见现象。
钢水在结晶器内形成坯壳,连铸坯出结晶器后,薄弱的坯壳抵抗不住钢水静压力,出现断裂而漏钢。
对于薄板坯连铸来说更易发生漏钢事故。
漏钢对连铸生产危害很大。
即影响了连铸车间的产量,又影响了连铸坯的质量,更危及操作者的安全。
因此,降低薄板坯连铸漏钢率是提高生产效率,提高产量,提高产品质量,降低成本的重要途径。
现对某厂自2008~2013年薄板坯漏钢率进行统计。
2008年漏钢率达0.56%;2009年漏钢率达0.19%;2010年漏钢率达0.19%;2011年漏钢率达0.19%;2012年漏钢率达0.15%;2013年漏钢率达0.07。
1 工艺流程某厂第一钢轧厂工艺流程为:鱼雷罐供应铁水/混铁炉供应铁水→铁水预处理→转炉炼钢→氩站→精炼→薄板坯连铸2 薄板坯漏钢类型某厂薄板坯连铸漏钢主要有:粘结漏钢、裂纹漏钢、卷渣漏钢、开浇漏钢、鼓肚漏钢五个类型。
3 薄板坯漏钢特征、原因及预防措施3.1 粘结漏钢粘结漏钢是指钢水直接与结晶器铜板接触形成粘结点,粘结点处坯壳与结晶器壁之间发生粘结,此处在结晶器振动和拉坯的双重作用下被撕裂,并向下和两侧扩展,形成倒“V”形破裂线,钢水补充后又形成新的粘结点,这一过程反复进行,粘结点随坯壳运动不断下移,此处坯壳较薄,出结晶器后,坯壳不能承受上部钢水的静压力,便会发生漏钢事故。
据统计,粘结漏钢发生率最高,高达50%以上。
(1)铸坯粘结漏钢后特征。
粘结漏钢后铸坯特征。
坯壳呈“V”字型或“倒三角”状,粘结点明显。
(2)粘结漏钢的原因:1)保护渣性能不好。
保护渣在结晶器铜板与凝固坯壳之间起润滑的效果。
板坯连铸机漏钢原因分析及控制措施

板坯连铸机漏钢原因分析及控制措施1.操作不当:操作人员操作不规范或经验不足,如操作时间过长、操作不准确等,容易导致板坯连铸机漏钢。
为了避免操作不当导致漏钢,应加强操作人员培训,提高他们的技术水平和操作经验,严格遵循操作规程,并进行必要的考核和监督。
2.连铸结晶器破损:连铸结晶器是冷却板坯的关键部件,如果结晶器破损,冷却水可能会直接进入铸坯中,导致漏钢。
为了避免这种情况,应定期对结晶器进行检查和维修,及时发现并更换破损的部件。
3.气孔:气孔是指铸坯内部存在的空隙,通常由于钢水中的氢气无法完全逸出而形成。
气孔会影响铸坯的质量,导致漏钢。
为了减少气孔,可以采取以下措施:(1)控制钢水的合金成分,控制钢水中的氢含量。
(2)在铸造过程中加入除氧剂,提高钢水中的溶解氧含量,减少气体生成。
(3)合理设计结晶器,使气泡易于从铸坯中升出。
4.结晶器堵塞:连铸结晶器内部可能会堵塞,导致冷却水无法均匀地冷却铸坯,造成漏钢。
为了避免结晶器堵塞,应定期对结晶器进行清洗和维修,保证结晶器内部的冷却水流通畅。
5.铸坯温度过高:铸坯温度过高会导致铸坯内部产生过多的气体,增加气孔的形成,从而引起漏钢。
为了控制铸坯温度,可以在连铸过程中控制冷却水的流量和温度,以达到合理的冷却效果;同时,在连铸过程中加强温度监控,及时调整连铸速度和冷却水的冷却效果。
6.铸模破损:铸模破损会导致铸坯内部形成孔洞和裂缝,导致漏钢。
为了避免铸模破损,应定期进行铸模的检查和维修,及时更换破损的部件。
7.其他原因:除了以上几点外,板坯连铸机漏钢还可能受到其他因素的影响,如连铸设备的老化、设备维护不当等。
为了确保连铸机的正常运行和减少漏钢,应加强设备的维护保养,定期进行设备的检修和更换关键部件。
综上所述,要控制板坯连铸机漏钢,需要从操作规范、设备维护、冷却控制等多个方面着手,以保证连铸过程的正常进行和铸坯质量的提高。
只有在整个生产过程中严格按照操作规程进行操作,定期维护检修设备,并加强钢水质量控制,才能有效控制和减少板坯连铸机漏钢的发生。
板坯连铸机漏钢成因分析及预防措施

;: 常规板坯连铸机参数及漏钢情况
; 5 9: 常规板坯连铸机的主要工艺参数 酒钢第二炼钢常规板坯连铸机主要工艺参数见 表 8。
第 ! 期8 8 8 8 8 8 8 8 8 8 8 8 程子建: 板坯连铸机漏钢成因分析及预防措施8 8 8
表 !" !##$ % !##& 年逐月漏钢情况
项目 产量 ( +) 综合合格率 (, ) 漏钢次数 !""# 年 %月 )’ """ **- )) ’ !月 $* #’* **- ) % &月 )) %#" **- $ ! ’月 $$ ("" **- )# % (月 ** ’&# **- ) % #月 )# &!$ **- )’ % $月 )" ((’ **- *’ & )月 $% $&# **- *& " *月 #% *&* **- *& " %" 月 !* ($& **- *! " %% 月 ($ )&" **- *$ " %! 月 $$ !’) **- *) " !""$ 年 %月 #"#&) **- *) " !月 #"""" **- *( " 合计
(
% "%’ (*" **- )* %&
表 ’" 漏钢情况统计结果
次数 % ! & ’ ( # $ ) * %" %% %! %& 时间 !""#."%."! !""#."%.%" !""#."%.&" !""#."%.&" !""#."!.%! !""#."&.") !""#."&.%# !""#."’.%! !""#."(.%( !""#."#.!( !""#."$."$ !""#."$.%$ !""#."$.%) 钢种 //’"" //’"" //’"" //’"" //’"" //’"" 5!&(67 5!&(6 5!&(6 ( 改) 5!&(67 ( 改) 5!&(67 ( 改) 5!&(67 ( 改) 5!&(67 ( 改) 规格 %#" 0 (!" %#" 0 (!" !!" 0 (&" !!" 0 (&" !!" 0 (&" !!" 0 (&" !!" 0 (&" !!" 0 (&" !!" 0 (&" !!" 0 (&" !!" 0 (&" !!" 0 (&" !!" 0 (&" 炉次 换包第 ! 炉 换包第 ! 炉 换包第 ! 炉 第( 炉 第) 炉 第 %& 炉 第( 炉 第# 炉 第 %! 炉 第* 炉 第# 炉 第) 炉 第( 炉 拉速 %- ! 1 2 134 %- !& 1 2 134 %- "( 1 2 134 %- " 1 2 134 %- "( 1 2 134 %- "& 1 2 34 %- "( 1 2 134 "- $( 1 2 134 "- *( 1 2 134 %- ") 1 2 134 %- " 1 2 134 %- " 1 2 134 "- $( 1 2 134 漏钢位置 内弧距坯头 #(" 11, 中间位置 内弧出结晶器, 距坯头 )%" 11, 中间位置 内弧中部距坯头 *"" 11 处 内弧中部偏西距结晶器上口 *"" 11 处 漏钢部位位于窄右出结晶器足辊位置 内外弧距结晶器上口 % &)" 11 外弧正中部, 漏钢点距结晶器上口 )(" 11 外弧中部偏西距结晶器上口 )"" 11 处 内弧出结晶器, 距坯头 )%" 11, 中间位置 内弧出结晶器下口位置 外弧宽面下口处 漏钢位置在结晶器窄左距上口 % 1 处 外弧宽面结晶器下口中部 漏钢形式 粘结漏钢 粘结漏钢 粘结漏钢 粘结漏钢 粘结漏钢 卷渣漏钢 粘结漏钢 粘结漏钢 粘结漏钢 粘结漏钢 粘结漏钢 机械外力划破坯壳 粘结漏钢
浅析漏钢的原因及预防

浅析漏钢的类型及预防连铸二车间技术组-郭幼永一、前言:板坯漏钢的形式多种多样但重点主要集中在粘结漏钢和开浇起步后的漏钢。
本文简要介绍常见漏钢的类型、漏钢的起因及相应的预防措施。
为各班组在实际浇钢过程中提供参考便于降低漏钢事故的发生。
二、漏钢的类型1、粘结漏钢粘结漏钢是连铸生产过程中的主要漏钢形式,据统计诸多漏钢中粘结漏钢占50%以上。
所谓粘结的引起是由于结晶器液位波动,弯月面的凝固壳与铜板之间没有液渣,严重时发生粘结。
当拉坯时磨擦阻力增大,粘结处被拉断,并向下和两边扩大,形成V型破裂线,到达出结晶器口就发生漏钢。
粘结漏钢的发生有以下情况:内弧宽面漏钢发生率比外弧宽面高(大约3:1);宽面中部附近(约在水口左右300mm)更易发生粘结漏钢;大断面板坯容易发生宽面中部漏钢;而小断面则发生在靠近窄面的区域;铝镇静钢比铝硅镇静钢发生漏钢几率高;保护渣耗量在0.25kg/t钢以下,漏钢几率增加。
2、发生粘结漏钢的原因:1)、形成的渣圈堵塞了液渣进入铜管内壁与坯壳间的通道;2)、结晶器保护渣Al2O3含量高、粘度大、液面结壳等,使渣子流动性差,不易流入坯壳与铜板之间形成润滑渣膜。
3)、异常情况下的高拉速。
如液面波动时的高拉速,钢水温度较低时的高拉速。
4)、结晶器液面波动过大,如浸入式水口堵塞,水口偏流严重,更换钢包时水口凝结等会引起液面波动。
3、防止粘结性漏钢预防措施在浇注过程中防止粘结漏钢的对策有:(1)监视保护渣的使用状况,确保保护渣有良好性能。
如测量结晶器液渣层厚度经常保持在8~15mm,保护渣消耗量不小于0.4kg/t钢,及时捞出渣中的结块等。
(2)提高操作水平,控制液位波动。
(3)确保合适的拉速,拉速变化幅度要小。
升降拉速幅度以0.05m/min为宜。
(4)严格控制钢水质量,提高钢水洁净度,减少钢中夹杂物。
(5)加强对结晶器铜板的检查,发现有龟裂或其他影响铜板平整度的因素,必须进行打磨处理,如果问题严重必须下线。
板坯连铸机粘接漏钢的原因与预防措施
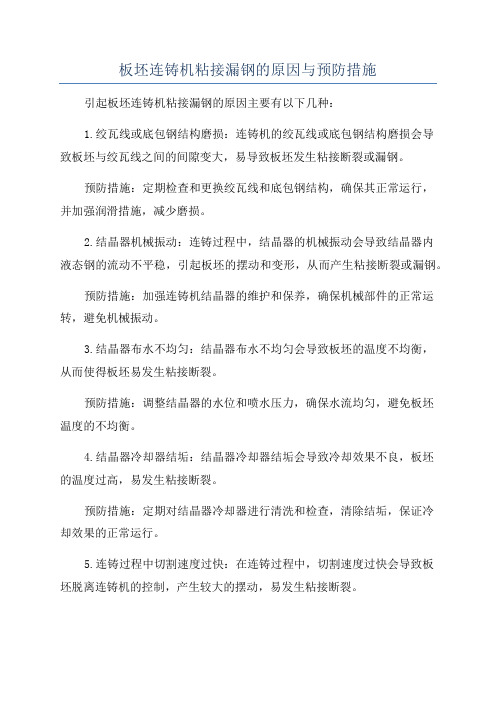
板坯连铸机粘接漏钢的原因与预防措施引起板坯连铸机粘接漏钢的原因主要有以下几种:1.绞瓦线或底包钢结构磨损:连铸机的绞瓦线或底包钢结构磨损会导致板坯与绞瓦线之间的间隙变大,易导致板坯发生粘接断裂或漏钢。
预防措施:定期检查和更换绞瓦线和底包钢结构,确保其正常运行,并加强润滑措施,减少磨损。
2.结晶器机械振动:连铸过程中,结晶器的机械振动会导致结晶器内液态钢的流动不平稳,引起板坯的摆动和变形,从而产生粘接断裂或漏钢。
预防措施:加强连铸机结晶器的维护和保养,确保机械部件的正常运转,避免机械振动。
3.结晶器布水不均匀:结晶器布水不均匀会导致板坯的温度不均衡,从而使得板坯易发生粘接断裂。
预防措施:调整结晶器的水位和喷水压力,确保水流均匀,避免板坯温度的不均衡。
4.结晶器冷却器结垢:结晶器冷却器结垢会导致冷却效果不良,板坯的温度过高,易发生粘接断裂。
预防措施:定期对结晶器冷却器进行清洗和检查,清除结垢,保证冷却效果的正常运行。
5.连铸过程中切割速度过快:在连铸过程中,切割速度过快会导致板坯脱离连铸机的控制,产生较大的摆动,易发生粘接断裂。
预防措施:调整切割速度,使其适应板坯的尺寸和形状,减少切割过程中的摆动。
6.进料辊道制动控制不当:进料辊道制动控制不当会导致板坯的速度不稳定,易产生粘接断裂。
预防措施:加强对进料辊道的制动控制,确保板坯的进料速度平稳,减少速度变化造成的影响。
为了预防板坯连铸机粘接漏钢问题1.定期检查和更换关键部件,确保设备的正常运行。
2.加强润滑措施,减少设备磨损。
3.定期对连铸机进行维护和保养,避免机械振动。
4.调整结晶器的水位和喷水压力,保证水流均匀。
5.定期清洗结晶器冷却器,确保冷却效果的正常运行。
6.调整切割速度,使其适应板坯的尺寸和形状。
7.加强对进料辊道的制动控制,保证板坯的进料速度平稳。
综上所述,板坯连铸机粘接漏钢问题的原因多种多样,但通过采取相应的预防措施,可以有效减少粘接漏钢问题的发生,提高连铸工艺的稳定性和良品率。
板坯粘结漏钢分析

5 结束语
1)降低保护渣熔化温度、粘度,提高熔速, 对减少粘结漏钢有利; 2)采用非正弦振动,对减少粘结漏钢有利; 3)提高钢水纯净度,对避免粘结漏钢有利; 4)稳定拉速和液面,“黑渣”操作,可减少粘 结漏钢; 5)温度过低,拉速不宜过高。
3.1 保护渣性能及耗量的影响 3.2 钢水纯净度的影响 3.3 结晶器液面波动的影响 当结晶器内钢液面上升到与渣圈相接触时,液 渣向下的通道将被堵住,当钢液面继续上升时, 会把渣圈向上推,将渣圈与固态渣膜分开,使钢 液直接和结晶器壁接触,并粘结在一起;正滑脱 时,坯壳强度大于粘结力,坯壳被拉走,如果坯 壳强度小于粘结力时,坯壳被拉断,在结晶器出 口产生漏钢。 3.4 拉速变化的影响 拉速发生变化后,温度变化滞后,液渣层厚度 变化、固态渣膜变化和恢复到最佳状态所需时间 推迟,在高拉速时,更易出现这种漏钢。
Nhomakorabea保护渣熔化速度低,单位时间内熔化的保护渣量小,进入铸坯与铜板缝隙的 液渣量就少。 保护渣熔化温度对钢液面上溶渣层厚度的影响如图1。 保护渣熔化温度h、钢液面温度t,、保护渣表面温度h。在钢液面上的熔渣层 与粉渣层间形成一个温度为t:的等温面,在稳定态传热的条件下,通过双层 平板的传热,在粉渣层内带走的热量应等于熔渣层所传导的热量。 即 通过粉渣层传热 q1= 1(t 2 t1); (1) S1 通过熔渣层传热 q2= 2(t 3 t 2 ) ; (2) S2 按稳定态传热条件,则ql=q2由此得出:
板坯粘结漏钢分析
1 2 3 4 5
前言 生产条件 影响粘结漏钢的因素及原因 粘结漏钢的预防措施 结束语
1 前言
漏钢是连铸生产中严重的生产事故, 影响铸机作业率,降低钢水收得率并 使设备严重损坏。 粘结漏钢在板坯连铸漏钢原因中所 占比例大,2000年我厂板坯连铸漏钢 25次,其中粘结漏钢13次,占漏钢次 数的52%。
板坯连铸粘结漏钢的特点与分析

磷是降低钢液表面张力的元素 , 易聚在晶粒 边界处, 随着含磷量的增加, 钢的表面张力降低, 从而降低了钢的热裂纹性能。 由表 1 钢中硫和磷的含量越高, 看出, 漏钢几 率就越高。
表 1 钢中(P +C7 % 与漏钢几率的关系 CS S )
(P + ) 上 习 C]0 S o
37 结晶器振动 .
结晶器振动装置是连铸机非常重要的设备, 结晶器有规律的往复振动可以防止坯壳与铜板发 生粘结, 同时还可以获得 良好的铸坯质量。 结晶器 向上运动时, 减少新生的坯壳与结晶器壁产生粘 结, 以防止坯壳受到较大的应力, 减少铸坯表面出 现裂纹 ; 而结晶器向下运动时, 借助结晶器壁与坯 壳的摩擦, 在坯壳上施加一定的压力, 愈合结晶器 上升时拉出的裂痕。 如结晶器振动不平衡 , 初生坯 壳的摩擦阻力增大, 易把坯壳拉裂, 导致漏钢。
线, 1b ; 如图 ()随着铸坯往下移动, 钢水直接与铜
板接触, 由于冷却水的作用, 形成新的坯壳, 如图 1c ; ()随着结晶器的振动和铸坯的继续下移, 此过 程重复出现, 如图 1d ; () 直到薄坯壳在出结晶器 下 口时被拉裂, 出现漏钢现象, 如图 1e . ()
根据文献[ 所述, 2] , 3 粘结性漏钢约占漏钢总数 粘 的6写^80。 5 ' 0 可见, 0 在板坯连铸生产过程中
硫在钢中的溶解度很大, 而在固态钢中的溶 解度很小, 而且随着温度降低而降低, 出硫化 析
时, 在初生晶粒边界上析出, 形 成包围铁素体的连续或不连续的网状组织 , 引起
晶界脆性。
波痕, 即每一个振动周期将有两个表面凹痕 , 而不 是一个振痕。
常的液面波动在士2 粘结发生时则超过 士5 m m, m m。粘钢坯壳上观察到的弯曲或不规则 的排布 密集的振痕是液面波动所致。 在正常浇注条件下 , 每个周期产生一个振痕。 可是, 当液面波动导致粘 结, 在钢水进人撕裂的空隙时 , 将形成两个弯月形
板坯角裂和边裂漏

2 现状调查
安钢二炼钢现有的一台超低头板坯连铸机,基本弧形 半径为5700mm,铸坯断面尺寸1050mm×180mm;组 合 式 可 调 结 晶 器 长 度 9 0 0 mm, 上 口 尺 寸 187.7mm×l078mm、下口尺寸187.0mm×l070mm,宽 度方向上有8mm的倒锥度、厚度方向上有0.7mm的倒 锥度,下部安装有足辊,侧面和内外弧铜板之间有一 条厚3~5mm带角度的铜带,在侧面和内外弧铜板之间 起平滑过渡作用。1999年漏钢13次,有10次属于边裂 和角裂漏钢;2000年前8个月漏钢9次,有7次属于边裂 和角裂漏钢;每次漏钢都会造成10~20万元的损失, 所以降低板坯边裂和角裂漏钢次数是减少板坯生产事 故的重要手段。
结晶器侧面倒锥度较大时,使坯壳在结晶器内 运动的阻力增大,易引起角部横裂纹(如图3), 严重时造成漏钢事故。
图3 角横裂漏钢
1)宽面辊弯曲造成的边裂漏钢是无规律的, 要保证生产顺行,就必须保证设备的状态 良好,及时点检是发现隐患和避免事故的 有效办法,停机后必须进行检查,发现隐 患立即处理。 2)窄面足辊和侧面铜板不在一个平面上可 以避免。此问题受人为因素影响,结晶器 在使用前,必须将侧面足辊和结晶器侧面 板调整到一个平面上,铸坯出结晶器后才 能得到有效的支撑,避免坯壳发生鼓肚变 形或角裂边裂现象。铸机停机后进行点检, 发现问题立即处理。 3)
5)结晶器侧面倒锥度小或冷却强 5)结晶器侧面倒锥度小或冷却强 度小造成的边裂漏钢
结晶器倒锥度小或冷却强度小,坯壳不能紧 贴铜板,热阻大,热量不能及时传走,边部 的坯壳较薄,由于热应力和收缩应力的集中, 出结晶器后在钢水静压力的作用和失去支撑 力的情况下,坯壳会在最薄弱处裂开引起边 裂漏钢。
6)结晶器侧面倒锥度较大引起 6)结晶器侧面倒锥度较大引起 的角裂漏钢
漏钢分析报告

漏钢分析报告1. 引言漏钢是指钢铁制品在加工过程中或使用过程中出现的钢材缺陷,其具体表现为钢材表面或内部出现不连续性的裂纹、砂眼、气孔等。
漏钢不仅会影响钢材的外观质量,还会降低钢材的强度、韧性和使用寿命。
本报告旨在对漏钢问题进行分析,排查漏钢的原因,并提出解决方案。
2. 漏钢原因分析2.1 材料原因钢材的成分和质量直接影响到钢材的使用性能。
如果钢材中存在夹杂物、夹杂气泡、非金属夹杂物等,在加工过程中很容易导致漏钢问题的发生。
因此,我们首先要检查钢材的材料质量,确保其符合相关的标准和要求。
2.2 设备原因钢材的加工设备也可能是导致漏钢问题的原因之一。
设备因老化、磨损、维护不到位等原因,可能导致钢材的加工过程中产生过大的摩擦或应力集中,进而引起钢材的缺陷。
因此,我们需要对加工设备进行定期的检修和维护,确保设备的正常运行。
2.3 工艺原因工艺参数的不合理设置也可能是导致漏钢问题的原因之一。
比如,熔炼温度过高或过低、加热时间过长或过短等,都可能导致钢材组织的不均匀或含有过多的气体,从而引起漏钢问题。
因此,我们需要对工艺流程进行优化,确保每一步的参数设定合理。
3. 解决方案3.1 完善原材料检测加强对钢材原材料的检测,确保原材料的质量符合要求。
可以采用无损检测技术,如超声波检测、X射线检测等,对钢材进行全面、准确的检测。
3.2 加强设备维护定期对加工设备进行检修和维护,确保设备的正常运行。
及时更换老化和磨损的配件,保证设备的精度和稳定性。
3.3 优化工艺流程对工艺参数进行优化,确保每一步的参数设定合理。
可以借助数值模拟和实验分析来确定最佳的工艺参数,减少漏钢问题的发生。
4. 漏钢监控与预警4.1 建立漏钢监控系统建立漏钢监控系统,通过实时检测、分析漏钢相关数据,提前发现潜在的漏钢问题。
可以采用传感器、图像识别等技术手段,对钢材进行在线监测。
4.2 制定漏钢预警方案针对漏钢问题制定相应的预警方案,在出现漏钢问题之前能够及时发出预警信号。
大板坯连铸机粘结漏钢的原因分析及预防
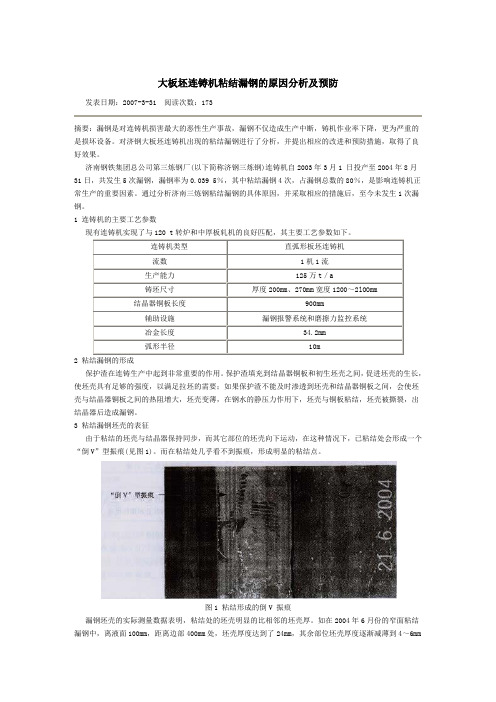
大板坯连铸机粘结漏钢的原因分析及预防发表日期:2007-3-31 阅读次数:173摘要:漏钢是对连铸机损害最大的恶性生产事故,漏钢不仅造成生产中断,铸机作业率下降,更为严重的是损坏设备。
对济钢大板坯连铸机出现的粘结漏钢进行了分析,并提出相应的改进和预防措施,取得了良好效果。
济南钢铁集团总公司第三炼钢厂(以下简称济钢三炼钢)连铸机自2003年3月1 日投产至2004年8月31日,共发生5次漏钢,漏钢率为0.039 5%,其中粘结漏钢4次,占漏钢总数的80%,是影响连铸机正常生产的重要因素。
通过分析济南三炼钢粘结漏钢的具体原因,并采取相应的措施后,至今未发生1次漏钢。
1 连铸机的主要工艺参数现有连铸机实现了与120 t转炉和中厚板轧机的良好匹配,其主要工艺参数如下。
连铸机类型直弧形板坯连铸机流数1机1流生产能力125万t/a铸坯尺寸厚度200mm、270mm宽度1200~2lOOmm结晶器铜板长度900mm辅助设施漏钢报警系统和磨擦力监控系统冶金长度34.2mm弧形半径10m2 粘结漏钢的形成保护渣在连铸生产中起到非常重要的作用。
保护渣填充到结晶器铜板和初生坯壳之间,促进坯壳的生长,使坯壳具有足够的强度,以满足拉坯的需要;如果保护渣不能及时渗透到坯壳和结晶器铜板之间,会使坯壳与结晶器铜板之间的热阻增大,坯壳变薄,在钢水的静压力作用下,坯壳与铜板粘结,坯壳被撕裂,出结晶器后造成漏钢。
3 粘结漏钢坯壳的表征由于粘结的坯壳与结晶器保持同步,而其它部位的坯壳向下运动,在这种情况下,已粘结处会形成一个“倒V”型振痕(见图1)。
而在粘结处几乎看不到振痕,形成明显的粘结点。
图1 粘结形成的倒V 振痕漏钢坯壳的实际测量数据表明,粘结处的坯壳明显的比相邻的坯壳厚。
如在2004年6月份的窄面粘结漏钢中,离液面100mm,距离边部400mm处,坯壳厚度达到了24mm,其余部位坯壳厚度逐渐减薄到4~6mm的正常厚度,这个数据与理论符合的很好。
板坯连铸机漏钢原因分析及控制措施

钢种优化
钢种选择与优化
根据实际生产需求,选择合适的钢种,并进行优化,以降低因钢种问题导致的漏钢风险 。
钢种质量检测与控制
加强钢种的质量检测和控制,确保钢种的质量稳定,降低因钢种质量波动导致的漏钢风 险。
04
结论与展望
研究结论
板坯连铸机漏钢的主要原因包括:钢 水成分、温度和浇注工艺控制不当, 结晶器设计、维护和操作不当,以及 保护渣性能和质量问题等。
设备老化
随着设备使用年限的增加,铸机 内部零件可能发生磨损、老化或 疲劳断裂,导致设备性能下降, 容易出现漏钢事故。
设备维护不当
缺乏定期的设备检查和维护,可 能导致铸机内部零件出现故障或 潜在的安全隐患,从而引发漏钢 事故。
操作因素
操作失误
操作工人在生产过程中出现失误,如 错误地调整铸机参数、操作顺序不当 等,可能导致铸机运行异常,引发漏 钢事故。
操作不规范
操作工人未按照规定的操作规程进行 操作,可能对铸机造成损伤或引发漏 钢事故。
钢种因素
钢种特性
某些特殊钢种可能具有较高的结晶温度和凝固温度范围,增加了铸机操作的难 度,容易引发漏钢事故。
钢水成分
钢水中含有杂质或有害元素,可能影响钢的流动性和铸机的正常操作,从而增 加漏钢的风险。
03
控制措施
02
在控制措施方面,虽然本文提出了一些具体的建议,但实 际应用效果还需要进一步验证和完善。
03
未来研究可以针对不同类型的板坯连铸机进行更深入的调 查和研究,以制定更加具体和针对性的控制措施,提高铸 机的生产效率和产品质量。同时,可以探索更加智能和自 动化的监测和控制系统,实现铸机生产的全面优化和升级 。
THANKS
谢谢您的观看
板坯漏钢概述

3)结晶器表面结冷钢(即结壳)造成的漏钢 当低拉速时间长或流场不好时,结晶器内 向上流股小,液面钢水不活跃,保护渣吸收热量 少,故熔渣层薄,钢液散热快;又因钢水在结晶 器内停留时间长,冷却强度大,结晶器的四个角 部或浸入式水口附近,会出现局部结冷钢的现 象,当冷钢块较大时,就可能与结晶器或浸入式 水口连结在一起,致使铸坯向下拉,坯壳被拉断 而漏钢。
板坯漏钢概述
漏钢是连铸生产中的恶性事故 , 不仅影响铸机作业率 , 降低钢水收 得率;而且会造成设备损坏,甚至是 严重损坏 , 尤其是设备较多、较复 杂、造价高的板坯连铸机 , 漏钢造 成的损失更大 , 同时也增加了工人 的劳动强度。因此在组织生产中应 千方百计的避免漏钢事故的发生 , 是降成本增效益的有效途径之一。
• 2、注重对塞棒氩气的调节。 • 2.1 改善流场,解决偏流。偏流后流场不活跃的 一侧易发生粘结,需尽量避免出现偏流现象。塞 棒氩气的主要作用有调节注流和冷却塞棒,其中 第一个作用最有意义。氩气泡从棒头吹出后,会 顺着钢流一起沿浇注路线流入结晶器。氩气泡的 比重没有钢水大,因此相对于钢水来说,氩气泡 是注流中的空白区域,若此空白区域较为集中于 一侧,则易产生偏流等现象。相反地,合理的调 解氩气压力以获得合理的氩气泡分布能减轻或避 免偏流的出现,因此塞棒氩气作为调节偏流的一 个方法而得到广泛使用。
漏钢类型 粘结漏钢 裂纹漏钢 开浇漏钢 鼓肚漏钢 夹渣漏钢 水口凝钢 悬挂漏钢 切断漏钢 其他
所占比例 54.5% 22.7% 9.1% 4.6% 2.3% 2.3%
4.5%
• 2.裂纹漏钢 • 坯壳在结晶器内产生严重的纵裂、角 裂,当铸坯冷却强度不够,承受不住钢水静 压力及各种外力作用时,就会造成漏钢事故。 这种大
• 6 加强操作。 • 组织操作人员学习保护渣的相关知识,重 点对保护渣在结晶器内的情况进行学习; 阐明相关规程的制定理由和依据,解释操 作工提出的技术和操作疑点。
板坯连铸机漏钢原因分析及控制措施

⑦液面不稳,波动较大,破坏了保护渣的正常流入和弯月面处初生坯壳的 形成条件。
⑧浇钢操作不规范:保护渣加入不均匀;挑渣条过深,破坏了初生坯壳; 给Ar气量不够或过大,造成液面死板或大翻等。
⑨钢水成分: 包晶钢及裂纹敏感钢,钢中S、P含量高等
三、漏钢的识别和控制
2、由设备原因造成的漏钢
跑锥度和偏振等设备故障是常见的引起漏钢的因素。
•跑锥度引起的漏钢 在结晶器液面和铸坯上没有黏结漏钢的特征,而在漏钢后的结晶器 上,可以测得窄面锥度较明显的变小(负锥度)。其控制是采取措施,固定好窄面锥 度。 •偏振引起的漏钢 产生偏振有如下三个原因: ①偏心轮轴承间隙大或轴承磨损 由于偏心轮轴承间隙大或轴承磨损,造成四个偏心轮在同一时刻不能产生相等的振幅,造
③拉速或温度的波动较大,造成保护渣无法适应Байду номын сангаас注条件的急剧变化
④推渣工不按要求加入保护渣,液面覆盖不均匀,时多时少,人为造成保 护渣性能不良。 ⑤浸入式水口的插入深度不合适,引起结晶器内流场状态不良, 造成保护渣融化不好,甚至卷渣,产生了可能漏钢的条件。
二、造成漏钢的原因
A、工艺及操作原因造成的漏钢:
产生表面裂纹或坯壳脱离不彻底,严重时,会产生漏钢
⑦结晶器宽、窄面水量不匹配,产生较严重的角部裂纹,引起漏钢。 ⑧结晶器冷却水水质差,造成结晶器铜板水槽结垢、藻类堵塞等,引起坯壳冷却 不均匀,甚至坯壳脱离不彻底,导致漏钢。
三、漏钢的识别和控制
1、由保护渣熔化不良造成的漏钢
•看渣面
• 性能好的保护渣 ①粉渣的铺展性好,渣面平整而均匀,②渣面活跃,有小火苗均匀跳 动,③渣层具有均匀的三层结构:30毫米左右的粉渣层、5毫米左右的烧结层、15毫米
漏钢的类型及预防措施
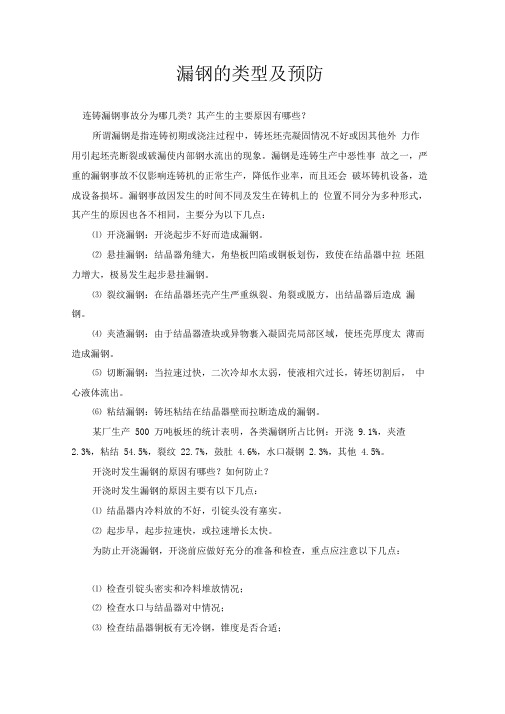
漏钢的类型及预防连铸漏钢事故分为哪几类?其产生的主要原因有哪些?所谓漏钢是指连铸初期或浇注过程中,铸坯坯壳凝固情况不好或因其他外力作用引起坯壳断裂或破漏使内部钢水流出的现象。
漏钢是连铸生产中恶性事故之一,严重的漏钢事故不仅影响连铸机的正常生产,降低作业率,而且还会破坏铸机设备,造成设备损坏。
漏钢事故因发生的时间不同及发生在铸机上的位置不同分为多种形式,其产生的原因也各不相同,主要分为以下几点:⑴ 开浇漏钢:开浇起步不好而造成漏钢。
⑵ 悬挂漏钢:结晶器角缝大,角垫板凹陷或铜板划伤,致使在结晶器中拉坯阻力增大,极易发生起步悬挂漏钢。
⑶ 裂纹漏钢:在结晶器坯壳产生严重纵裂、角裂或脱方,出结晶器后造成漏钢。
⑷ 夹渣漏钢:由于结晶器渣块或异物裹入凝固壳局部区域,使坯壳厚度太薄而造成漏钢。
⑸ 切断漏钢:当拉速过快,二次冷却水太弱,使液相穴过长,铸坯切割后,中心液体流出。
⑹ 粘结漏钢:铸坯粘结在结晶器壁而拉断造成的漏钢。
某厂生产 500 万吨板坯的统计表明,各类漏钢所占比例:开浇 9.1%,夹渣2.3%,粘结 54.5%,裂纹 22.7%,鼓肚 4.6%,水口凝钢 2.3%,其他 4.5%。
开浇时发生漏钢的原因有哪些?如何防止?开浇时发生漏钢的原因主要有以下几点:⑴ 结晶器内冷料放的不好,引锭头没有塞实。
⑵ 起步早,起步拉速快,或拉速增长太快。
为防止开浇漏钢,开浇前应做好充分的准备和检查,重点应注意以下几点:⑴ 检查引锭头密实和冷料堆放情况;⑵ 检查水口与结晶器对中情况;⑶ 检查结晶器铜板有无冷钢,锥度是否合适;⑷ 检查二冷喷嘴是否畅通完好;⑸ 了解钢水的流动性、钢水温度状态,中间包和水口是烘烤状态,保护渣的质量。
⑹ 要根据铸坯断面决定注流大小和钢水在结晶器停留时间。
⑺ 起步拉速一般保持为 0.5m/min ,增速要慢( 0.15 m/min ),防止结晶器液面波动过大。
浇注过程中发生漏钢的原因有哪些?如何防止?浇注过程中发生漏钢的根本原因在于铸坯出结晶器后局部凝固壳过薄,承受不住钢水静压力而破裂导致漏钢。
板坯漏钢原因

板坯漏钢原因
嘿,你问板坯漏钢原因啊?那咱就来聊聊。
这板坯漏钢啊,可不是啥好事。
首先呢,可能是结晶器的问题。
要是结晶器的内壁不光滑,有坑坑洼洼的地方,那板坯在里面凝固的时候就容易出问题。
就像人走在坑坑洼洼的路上容易摔跤一样,板坯也会在不光滑的结晶器里“栽跟头”,然后就漏钢了。
然后呢,保护渣也很重要哦。
如果保护渣的性能不好,不能很好地起到润滑和保温的作用,也会导致漏钢。
保护渣就像是板坯的“小棉袄”,要是“小棉袄”不暖和或者不滑溜,板坯就不舒服啦,就容易漏钢。
接着呢,拉速太快也不行。
如果拉速太快,板坯还没凝固好就被拉出来了,那肯定容易漏钢啊。
就像你跑步太快,不小心就会摔倒一样。
板坯被拉得太快,也会“跟不上节奏”,然后就漏了。
还有啊,钢水的温度不合适也会漏钢。
要是钢水温度太高,板坯凝固得慢,也容易出问题。
要是温度太低呢,板坯可能会凝固得不均匀,也会漏钢。
就像做饭的时候,
火候掌握不好,饭就容易做糊或者夹生。
我给你讲个事儿吧。
我有个朋友在钢厂上班,他们有一次板坯漏钢了,大家都很着急。
后来一检查,发现是结晶器内壁有点损坏,保护渣也没选好。
他们赶紧把结晶器修好,换了好的保护渣,然后调整了拉速和钢水温度。
从那以后,就很少再出现板坯漏钢的情况了。
总之呢,板坯漏钢的原因有结晶器问题、保护渣不好、拉速太快、钢水温度不合适等。
只要我们注意这些问题,认真检查和调整,就能减少板坯漏钢的情况发生。
让我们一起努力,把板坯生产得好好的吧。
板坯连铸机漏钢事故的原因分析及防止 精品
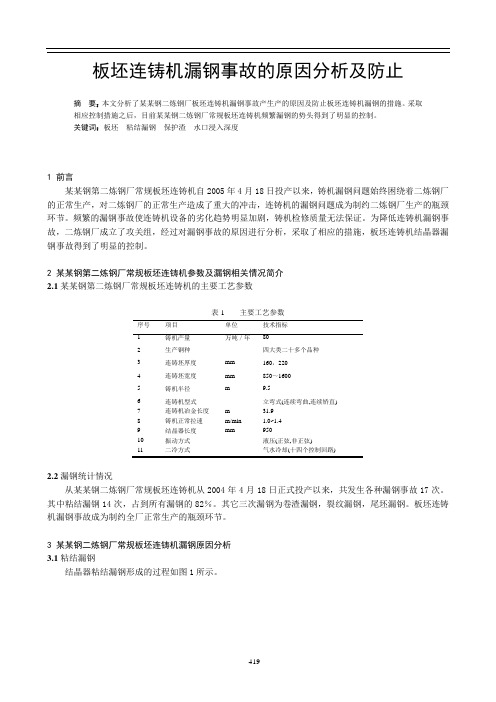
板坯连铸机漏钢事故的原因分析及防止摘要:本文分析了某某钢二炼钢厂板坯连铸机漏钢事故产生产的原因及防止板坯连铸机漏钢的措施。
采取相应控制措施之后,目前某某钢二炼钢厂常规板坯连铸机频繁漏钢的势头得到了明显的控制。
关键词:板坯粘结漏钢保护渣水口浸入深度1 前言某某钢第二炼钢厂常规板坯连铸机自2005年4月18日投产以来,铸机漏钢问题始终困绕着二炼钢厂的正常生产,对二炼钢厂的正常生产造成了重大的冲击,连铸机的漏钢问题成为制约二炼钢厂生产的瓶颈环节。
频繁的漏钢事故使连铸机设备的劣化趋势明显加剧,铸机检修质量无法保证。
为降低连铸机漏钢事故,二炼钢厂成立了攻关组,经过对漏钢事故的原因进行分析,采取了相应的措施,板坯连铸机结晶器漏钢事故得到了明显的控制。
2 某某钢第二炼钢厂常规板坯连铸机参数及漏钢相关情况简介2.1某某钢第二炼钢厂常规板坯连铸机的主要工艺参数表1 主要工艺参数铸机产量万吨/年2 生产钢种四大类二十多个品种3 连铸坯厚度mm 160,2204 连铸坯宽度mm 850~16005 铸机半径m 9.56 连铸机型式立弯式(连续弯曲,连续矫直)7 连铸机冶金长度m 31.98 铸机正常拉速m/min 1.0~1.49 结晶器长度mm 95010 振动方式液压(正弦,非正弦)11 二冷方式气水冷却(十四个控制回路)2.2漏钢统计情况从某某钢二炼钢厂常规板坯连铸机从2004年4月18日正式投产以来,共发生各种漏钢事故17次。
其中粘结漏钢14次,占到所有漏钢的82%。
其它三次漏钢为卷渣漏钢,裂纹漏钢,尾坯漏钢。
板坯连铸机漏钢事故成为制约全厂正常生产的瓶颈环节。
3 某某钢二炼钢厂常规板坯连铸机漏钢原因分析3.1粘结漏钢结晶器粘结漏钢形成的过程如图1所示。
在钢水浇注过程中,结晶器弯月面的钢水处于异常活跃的状态。
如图1所示,由于各种原因,浇铸过程中流入坯壳与结晶器铜壁之间的液态渣被阻断,当结晶器铜板与初生坯壳的摩擦力大于初生坯壳的强度时,初生坯壳被拉断,与铜板产生粘结。
板坯连铸机漏钢原因分析及控制措施
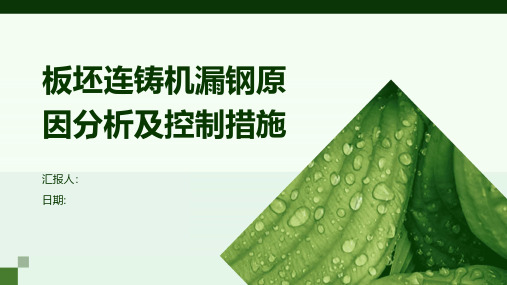
板坯连铸机漏钢原因分析及控制措施汇报人:日期:•板坯连铸机漏钢现象概述•漏钢原因分析•控制措施目录•实际应用与效果评估板坯连铸机漏钢现象概述01•漏钢现象:在板坯连铸过程中,高温钢水从铸机内部的裂缝或缺陷处泄漏出来的现象。
漏钢可能导致高温钢水接触工人或设备,引发严重的人身伤害和设备损坏。
安全风险产品质量下降生产效率降低漏钢会造成铸坯表面缺陷,严重影响板坯的质量和后续加工性能。
漏钢事故会中断连铸生产,导致生产效率降低,增加生产成本。
030201铸坯表面出现裂纹、孔洞或凹陷。
钢水泄漏导致的烟雾、火花或燃烧现象。
铸坯局部或整体形状变形。
设备异常声音或振动。
漏钢现象的常见表现漏钢原因分析02设备老化01连铸机设备长时间运行,关键部件磨损严重,未能及时更换或维修,容易导致漏钢。
设备安装精度02设备在安装过程中,如果存在安装精度不达标或者关键部位的紧固不牢固,会在运行过程中产生缝隙,进而导致漏钢。
冷却系统失效03连铸机的冷却系统对于防止漏钢起到关键作用,如果冷却系统发生故障,如冷却水流量不足、冷却水管破裂等,都会导致铸坯在凝固过程中受热不均,产生裂纹,从而引起漏钢。
拉坯速度过快在追求高效率的生产过程中,如果拉坯速度过快,会导致铸坯在凝固过程中的应力分布不均,增加漏钢的风险。
浇注温度过高如果浇注温度过高,超过了连铸机的设计能力,会导致铸坯在凝固过程中内部应力增大,容易产生裂纹,进而引发漏钢。
保护渣性能不佳保护渣对于防止铸坯表面氧化和吸气具有重要作用,如果保护渣的性能不佳,会导致铸坯表面质量下降,容易产生裂纹,从而引发漏钢。
操作人员在操作过程中,如果没有按照操作规程进行,如浇注速度控制不当、冷却水调节不及时等,都会导致连铸机运行不稳定,增加漏钢的风险。
操作不规范对于新上岗的操作人员,由于缺乏经验,对于异常情况反应不及时,也容易导致漏钢事故的发生。
缺乏经验在生产过程中,如果监控人员对于连铸机的运行状态监控不到位,如未能及时发现设备异常、工艺参数偏离等情况,也会导致漏钢事故的发生。
- 1、下载文档前请自行甄别文档内容的完整性,平台不提供额外的编辑、内容补充、找答案等附加服务。
- 2、"仅部分预览"的文档,不可在线预览部分如存在完整性等问题,可反馈申请退款(可完整预览的文档不适用该条件!)。
- 3、如文档侵犯您的权益,请联系客服反馈,我们会尽快为您处理(人工客服工作时间:9:00-18:30)。
• 4、促进保护渣润滑方面 • 保护渣主要有五大作用:避免钢水二次氧 化;覆盖在钢水液面保温;吸附夹杂;改 善铸坯润滑;填充在铸坯与铜板间的缝隙 内改善传热。其中改善铸坯润滑这一作用 对于避免板坯粘结有重要意义
• 5、研究合理的振动参数 • 结晶器振动相当于一种脱模作用。其目的 是建立良好的润滑条件,防止铸坯与结晶 器壁粘结而发生拉裂或漏钢,同时也可改 善铸坯的表面质量。选择合理的振动曲线 能够有效防止漏钢,有能得到合格范围内 的表面质量。
3)结晶器表面结冷钢(即结壳)造成的漏钢 当低拉速时间长或流场不好时,结晶器内 向上流股小,液面钢水不活跃,保护渣吸收热量 少,故熔渣层薄,钢液散热快;又因钢水在结晶 器内停留时间长,冷却强度大,结晶器的四个角 部或浸入式水口附近,会出现局部结冷钢的现 象,当冷钢块较大时,就可能与结晶器或浸入式 水口连结在一起,致使铸坯向下拉,坯壳被拉断 而漏钢。
板坯漏钢概述
漏钢是连铸生产中的恶性事故 , 不仅影响铸机作业率 , 降低钢水收 得率;而且会造成设备损坏,甚至是 严重损坏 , 尤其是设备较多、较复 杂、造价高的板坯连铸机 , 漏钢造 成的损失更大 , 同时也增加了工人 的劳动强度。因此在组织生产中应 千方百计的避免漏钢事故的发生 , 是降成本增效益的有效途径之一。
• 1.3防止粘结漏钢的措施: • 1) 设备的精度:结晶器锥度、 铜板的表面平 整度、 振动台偏摆量等振动参数要符合理论 设计要求。 • 2 )生产工的操作水平:严格执行工艺操作规 程,操作过程也是经验积累的过程,任何粘结 漏钢都有其外观的表现,观察很重要,火焰的 变化反映了结晶器内流场的变化,出现异常情 况首先要降速,必要时摁急停! • 3 )监视保护渣使用情况,确保保护渣良好的 润滑性能。液渣层厚度保持在8—15mm,保护 渣消耗量不低于 0.4kg/t 钢,及时捞出渣中的结 块。
• 2.2 促进整个液面活跃。严实的钢流从侧孔流出 冲向两个窄面时,水口附近的液面钢水流动小会 形成低温区,易发生结壳和化渣不良等现象。氩 气泡从水口侧孔流出后,受到钢流的强烈冲击, 同时受到是钢水的浮力而急速上浮,并带动一部 分钢水向上流动,促进该低温区域的传质和传热, 改善保护渣的化渣和润滑效果,减少粘结。 • 2.3 氩气调节标准。调节塞棒氩气压力受很多因 素影响,比如:水口插入深度、浇注拉速、钢水 粘度(钢种和钢水质量)、钢水温度等等。因此 现场调节时以水口两侧微冒火但不翻钢、不偏流 为宜。不同的浇注条件均力求达到上述效果。
• 1.4合理选择第一道渣线位置。 • 浸入式水口的渣线料位于工艺预设的渣线位置, 添加了ZrO2复合材料,耐侵蚀性强,将渣线控制 在渣线料上并适当更换渣线侵蚀位有利于提高水 口的使用寿命,降低更换水口的频率,利于稳定 浇注。而水口的插入深度是有限制的,不能过深 或过浅;能更换出渣线侵蚀位的最短距离也是有 限制的,目前2#、3#机需30mm才能更换出渣线 侵蚀位。这就要求水口插入深度与渣线料宽度之 间形成一定的深度关系,让插入深度较浅时渣线 在预设渣线料的下部,在更换渣线侵蚀位(实际 操作时通过提升结晶器液面来实现)后,渣线在 预设渣线料的上部。这也是确定出合理插入深度 的跨度的一个重要依据。
• 6 加强操作。 • 组织操作人员学习保护渣的相关知识,重 点对保护渣在结晶器内的情况进行学习; 阐明相关规程的制定理由和依据,解释操 作工提出的技术和操作疑点。
• 1.1 检查合适的尺寸形状,包括外径、内腔及内 腔对中、侧孔、底部倒角和其他缺陷等。水口的 尺寸直接影响到钢水在结晶器内的流场分布趋势, 因此要求在烘烤使用前仔细检查水口。 • 1.2调整水口为垂直。经现场察看,3#机由于基 建等原因导致中间包车出现不水平的情况,最大 偏差达到5mm。这使得挂于中间包底部的水口 的插入方向不是垂直的,而是沿结晶器宽面方向 出现倾斜。钢水流入不垂直的水口后,会冲刷一 个壁,从侧孔出来后两侧流股大小和方向会不均 匀,出现偏流等险情。因此重新校正垫平了中间 包位,确保水口垂直插入结晶器。
• 2)渣线更换造成的漏钢 如果渣线更换是通过中间包车的上升来实现的, 中间包车上升时,使浸入式水口随之上升,结晶器内 向上的流股冲击结晶器四周的渣圈,既堵塞了熔渣的 流入通道,又搅乱了保护渣的三层结构。当渣线更换 高度>25 mm时,会产生两种后果:其一,冲击渣圈的动 力大,把渣圈与固态渣膜分开,使钢液直接与结晶器 接触,导致摩擦力增大,坯壳被拉断,出结晶器下口即 造成粘性漏钢;其二,如果结晶器壁上有大的渣条,就 会被卷入坯壳形成夹渣,造成坯壳热阻增大,使凝固 速度减慢,坯壳厚度减薄,其强度减弱,致使出结晶器 时,坯壳承受不住钢水的静压力,造成卷渣漏钢。此 两种漏钢,都是在换渣线1~2 min之后发生的。
• 1.3优化水口的插入深度。 • 水口的插入深度是指水口侧孔上沿距液面的距离。 钢流从水口的侧孔流出后,沿水口斜台倒角方向 流去,在碰到窄面后分流并形成反弹,一部分往 上,一部分往下。 • 水口插入过浅,液面波动较大,不利于液面自控 的使用,易发生卷渣,液渣润滑不好;水口插入 过深,钢流主要向下流去,往上的钢水较少,液 面的整个传质和传热均较慢,保护渣得不到足够 的热量来熔化,化渣不良润滑不好,易发生粘结, 而且易产生纵裂纹等缺陷。
• 1.2发生粘结漏钢的原因: • 1)结晶器保护渣Al2O3含量高、粘度大、液面 结壳等,使保护渣流动性差,不易流入坯壳与 结晶器间形成润滑渣膜。 • 2)异常情况下的高拉速。如液面波动过大时的 高拉速,中包温度过低时的高拉速。 • 3)结晶器液面波动过大,如塞棒氩气流量过大、 浸入式水口堵塞、水口偏流严重、更换钢包时 水口周围凝结严重等,都会引起液面波动。
漏钢类型 粘结漏钢 裂纹漏钢 开浇漏钢 鼓肚漏钢 夹渣漏钢 水口凝钢 悬挂漏钢 切断漏钢 其他
所占比例 54.5% 22.7% 9.1% 4.6% 2.3% 2.3%
4.5%
• 2.裂纹漏钢 • 坯壳在结晶器内产生严重的纵裂、角 裂,当铸坯冷却强度不够,承受不住钢水静 压力及各种外力作用时,就会造成漏钢事故。 这种漏钢事故如果发生在扇形段处,对设 备的危害性很大
• 1.1粘结漏钢是连铸生产过程中的主要漏钢形 式,据统计诸多漏钢中粘结漏钢占 50%以上, 所谓粘结的引起是由于结晶器液位波动,弯月 面的凝固壳与铜板之间没有液渣,严重时发生 粘结。当拉坯阻力增大,粘结处被拉断,并向 下和两边扩展,形成典型的“V”字型撕裂线, 在出结晶器口后发生漏钢。明显的特点是漏钢 部位坯壳厚度不均匀,形成粘结的位置由于坯 壳的不断撕裂、焊合、再撕裂使得粘结漏钢处 坯壳异常增厚。且伴随分层叠加状。 •
• 2、注重对塞棒氩气的调节。 • 2.1 改善流场,解决偏流。偏流后流场不活跃的 一侧易发生粘结,需尽量避免出现偏流现象。塞 棒氩气的主要作用有调节注流和冷却塞棒,其中 第一个作用最有意义。氩气泡从棒头吹出后,会 顺着钢流一起沿浇注路线流入结晶器。氩气泡的 比重没有钢水大,因此相对于钢水来说,氩气泡 是注流中的空白区域,若此空白区域较为集中于 一侧,则易产生偏流等现象。相反地,合理的调 解氩气压力以获得合理的氩气泡分布能减轻或避 免偏流的出现,因此塞棒氩气作为调节偏流的一 个方法而得到广泛使用。
• 4)针对不同的钢种选择合适的拉速,拉 速变化幅度要小。 • 5)采用非正弦振动。与正弦振动相比,结 晶器采用非正弦振动时会延长负滑脱时 间,增加负滑脱量,减少正滑脱时间。从而, 保证了铸坯的“焊合”程度 , 增加了保护 渣的耗量,减少了摩擦阻力。
1.4几种典型粘结情况 1)结晶器振动形式不当造成粘结漏钢 生产中采用正弦振动时铸坯拉速提高,振频提高,负滑脱 时间减少,坏壳的“焊合”能力减弱,保护渣的耗量减少,摩 擦力增大;此时若坯壳的强度承受不住摩擦阻力,则坯壳就会 被拉断,造成粘结漏钢事故。在浸入式水口附近,因钢水流动 不活跃,热交换不充分,保护渣熔化不良,易结渣条,这些渣条 往往堵塞熔渣通向坯壳与结晶器之间的通道,使熔渣消耗量 减少,导致坯壳与结晶器接触摩擦力增大。当坯壳因上述原 因与结晶器铜板粘结到一起时,铸坯拉速应降低,以促使坯壳 与结晶器铜板脱离,如果坯壳与结晶器铜板不能很好的分开, 则此处的晶器水缝堵塞、角缝过大造成铸坯的冷 却不均匀极易产生纵裂或角部裂纹,如果 二冷区域冷却强度跟不上就会造成铸坯内 液态的钢水由于静压力作用穿透裂纹区域 发生漏钢事故。
• 防止粘结漏钢的一些体会 • 1、规范浸入式水口的使用。 • 浸入式水口(SEN)在连铸生产中起到分流、 防止二次氧化、稳定结晶器内钢水流场、 提高铸坯质量、防止卷渣及漏钢等多重作 用。莱钢板坯连铸机用浸入式水口经过长 期的实践已经基本定形,但在使用时还须 正确的使用才能满足工艺要求。主要有:
• 2.1裂纹漏钢:坯壳在结晶器内产生严重的 纵裂、角裂,出结晶器造成的漏钢。 对于拉钢工来讲此类漏钢难于发现, 难于从结晶器表面观察出异常情况,但是 对于设备监控的主要岗位如主控室可以通 过电脑画面上观察到结晶器水温差会有上 升的趋势,水量发生波动,台下切割工密 切关注铸坯表面缺陷,有时能够及时的发 现问题采取相应的措施,避免此类对设备 损伤严重的事故。