6.6车间布局与机加生产线教程
生产线机加工艺流程设计
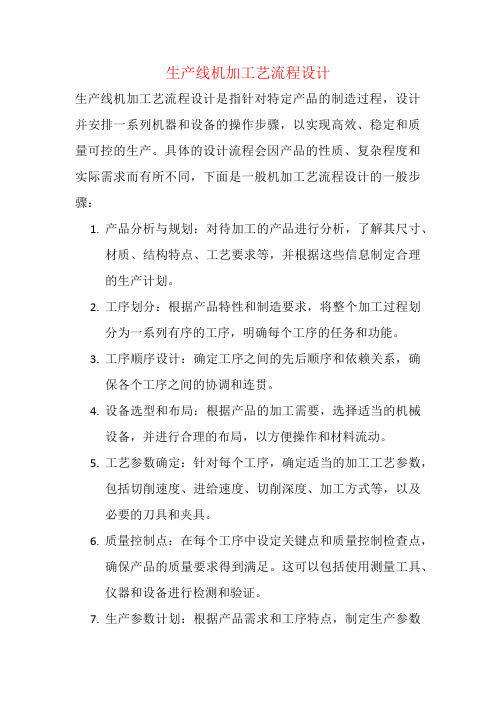
生产线机加工艺流程设计生产线机加工艺流程设计是指针对特定产品的制造过程,设计并安排一系列机器和设备的操作步骤,以实现高效、稳定和质量可控的生产。
具体的设计流程会因产品的性质、复杂程度和实际需求而有所不同,下面是一般机加工艺流程设计的一般步骤:1.产品分析与规划:对待加工的产品进行分析,了解其尺寸、材质、结构特点、工艺要求等,并根据这些信息制定合理的生产计划。
2.工序划分:根据产品特性和制造要求,将整个加工过程划分为一系列有序的工序,明确每个工序的任务和功能。
3.工序顺序设计:确定工序之间的先后顺序和依赖关系,确保各个工序之间的协调和连贯。
4.设备选型和布局:根据产品的加工需要,选择适当的机械设备,并进行合理的布局,以方便操作和材料流动。
5.工艺参数确定:针对每个工序,确定适当的加工工艺参数,包括切削速度、进给速度、切削深度、加工方式等,以及必要的刀具和夹具。
6.质量控制点:在每个工序中设定关键点和质量控制检查点,确保产品的质量要求得到满足。
这可以包括使用测量工具、仪器和设备进行检测和验证。
7.生产参数计划:根据产品需求和工序特点,制定生产参数计划,包括产量、生产速度、工时等,确保生产能力和资源的合理利用。
8.安全考虑:在设计流程中要考虑员工的安全和劳动保护,防止事故和伤害发生。
这包括提供安全设备和培训,确保操作员的操作规范和安全意识。
9.持续改进:根据实际生产情况,定期评估流程的效率和质量,并进行持续改进。
这可以包括优化工序顺序、改善设备性能和加工工艺等。
需要注意的是,不同的生产线机加工艺流程设计涉及到不同的工艺和设备。
因此,在设计流程时,应根据具体的产品和工艺要求进行调整和优化。
同时,与生产线相关的各个部门和人员之间的协调和沟通也至关重要,以确保流程的顺畅和高效。
机加生产线设计流程
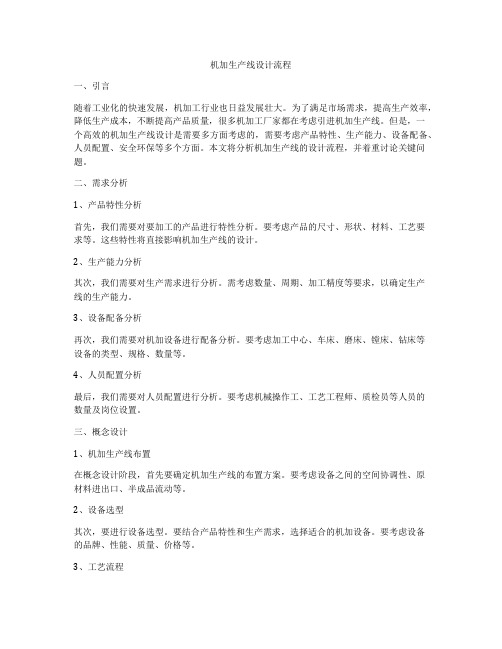
机加生产线设计流程一、引言随着工业化的快速发展,机加工行业也日益发展壮大。
为了满足市场需求,提高生产效率,降低生产成本,不断提高产品质量,很多机加工厂家都在考虑引进机加生产线。
但是,一个高效的机加生产线设计是需要多方面考虑的,需要考虑产品特性、生产能力、设备配备、人员配置、安全环保等多个方面。
本文将分析机加生产线的设计流程,并着重讨论关键问题。
二、需求分析1、产品特性分析首先,我们需要对要加工的产品进行特性分析。
要考虑产品的尺寸、形状、材料、工艺要求等。
这些特性将直接影响机加生产线的设计。
2、生产能力分析其次,我们需要对生产需求进行分析。
需考虑数量、周期、加工精度等要求,以确定生产线的生产能力。
3、设备配备分析再次,我们需要对机加设备进行配备分析。
要考虑加工中心、车床、磨床、镗床、钻床等设备的类型、规格、数量等。
4、人员配置分析最后,我们需要对人员配置进行分析。
要考虑机械操作工、工艺工程师、质检员等人员的数量及岗位设置。
三、概念设计1、机加生产线布置在概念设计阶段,首先要确定机加生产线的布置方案。
要考虑设备之间的空间协调性、原材料进出口、半成品流动等。
2、设备选型其次,要进行设备选型。
要结合产品特性和生产需求,选择适合的机加设备。
要考虑设备的品牌、性能、质量、价格等。
3、工艺流程再次,要进行工艺流程设计。
要对产品的加工流程进行分析,并确定加工顺序、工艺参数、加工工序等。
4、人员配置最后,要进行人员配置设计。
要结合生产能力和设备布置,确定人员的数量及岗位设置。
四、详细设计1、生产线布置图详细设计阶段,首先要完成机加生产线的布置图。
要按照概念设计的布置方案,绘制出详细的机加生产线布置图。
2、设备选型表其次,要制定设备选型表。
要按照概念设计的设备选型结果,确定每一台设备的品牌、型号、规格、数量等。
3、工艺流程图再次,要绘制工艺流程图。
要将概念设计的工艺流程进行细化,确定每一道工序的加工参数、加工顺序、工艺要求等。
机械加工中的生产线布置和优化技术

机械加工中的生产线布置和优化技术随着现代机械加工技术的发展,生产线布置和优化技术也变得越来越重要。
机械加工是生产制造的重要环节之一,而生产线布置和优化技术则是生产制造中至关重要的环节。
因此,本文将介绍机械加工中的生产线布置和优化技术,并探讨其对机械加工行业的影响,以及未来的发展趋势。
一、生产线布置技术生产线布置技术是指在机械加工生产线上合理安排和布置每个工序的设备、物料、工人等资源,以达到最高的生产效率和质量稳定性。
生产线布置技术是一项非常复杂的工作,需要考虑各种因素,如生产数量、产品结构、设备性能、工人技能、物料存储等等。
1. 管理人员需要仔细观察每个环节的设备使用情况和工人操作效率,制定计划和规划流程,合理安排设备和工人。
2. 选用适当的自动化技术和灵活的生产设备,以加快生产效率,减少工人劳动强度。
3. 根据不同的生产批次设置合理的物料储存区,以保证生产无故障、无停机,避免制造过程中的瓶颈。
4. 严格遵守安全规定,保护生产设备,保障工人安全。
生产线布置技术可以使机械加工生产线效率更高、质量更稳定、成本更低、工期更短,是机械加工生产中不可或缺的工作。
但是,生产中可能会遇到无法预料的事件,需要快速反应和解决,以保证生产的顺利进行。
二、生产线优化技术生产线优化技术是通过优化生产线上各个工序的流程和设备,提高生产效率、降低生产成本、提高产品质量和生产安全。
生产线优化技术需要综合考虑各种因素,如工人技能、设备性能、生产模式等等。
1. 消灭生产线上的浪费,例如设备闲置和过程中的瓶颈。
2. 通过流程优化和设备升级提高生产率,例如减少生产周期和工人劳动强度。
3. 采用绿色工艺和环保材料,防止易损件焊接拉动重量及误用工具等机械加工产生较大噪音。
4. 实施标准化生产,促进生产效率和产品质量稳定,提高生产企业的竞争力。
5. 开展员工培训和技能提高,使员工具备生产加工方面的技术素质。
优化生产线可以有效提高机械加工的生产效率和产品质量,降低生产成本,提高工作安全,优化利润,这对机械加工行业的发展有着非常重要的影响。
发动机缸体机加生产线培训教程PPT课件
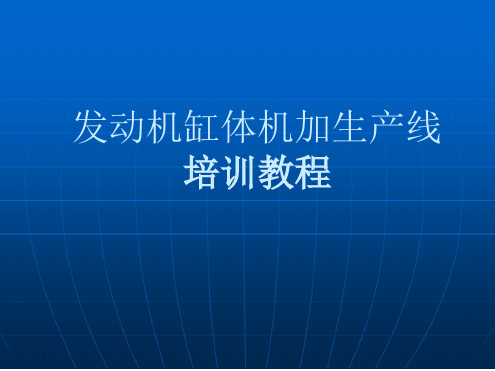
发动机缸体机加生产线培训教程一、概述?发动机是汽车最主要的组成部分,它的性能好坏直接决定汽车的行驶性能,故有汽车心脏之称。
而缸体又是发动机的基础零件,通过它把发动机的曲轴连杆机构和配气机构以及供油、润滑、冷却等系统联接成一个整体。
它的加工质量直接影响发动机的性能。
?本教程主要介绍发动机缸体机加生产线的工艺方案思路及生产线建设。
二、缸体的结构特点和技术要求? ?? ?1.缸体的结构特点由于缸体的功用决定了其形状复杂、壁薄、呈箱形。
其上部有若干个仅机械加工的穴座,供安装汽缸套用。
其下部与曲轴箱体上部做成一体,所以空腔较多,但受力严重,所以它应有很高的刚性,同时也要减少铸件壁厚,从而减轻其重量,而汽缸体内部复杂的水道外尚有直径6-8mm的油道。
2.缸体的技术要求:由于缸体是发动机的基础件,它的许多平面均作为其他零件的装配基准,这些零件之间的相对位置基本上是由缸体来保证的。
缸体上的很多螺栓孔、油孔、出沙孔、气孔以及各种安装孔都直接影响发动机的装配质量和使用性能,所以对缸体的技术要求相当严格。
3.缸体的材料:?根据发动机的原理可以知道缸体的受力情况很复杂,需要有足够的强?度、刚度、耐磨性和抗振性,因此对缸体材料有较高的要求。
缸体的材料有普通铸铁、合金铸铁及铝合金等。
我国发动机缸体采用?HT200、HT250灰铸铁、合金铸铁和铝合金。
灰铸铁具有足够的韧性和良好的耐磨性,多用于不镶缸套的整体缸体。
由于价格较低,切削性能较好,故应用较广。
近年来随着发动机转速和功率的提高,为了提高缸体的耐磨性,国内、外都努力推行铸铁的合金化,即在原有的基础上增加了炭、硅、锰、铬、镍、铜等元素的比例,严格控制硫和磷的含量,其结果不仅提高了缸体的耐磨性和抗拉强度,而且改善了铸造性能。
用铝合金铸造缸体、不但重量轻、油耗少,而且导热性、抗磁性、抗?蚀性和机械加工性均比铸铁好。
但由于铝缸体需镶铸铁缸套或在缸孔表面上加以涂层,原材料价格较贵等原因,因此其使用受到一定程度的限制。
机加生产线设计工艺流程设计

机加生产线设计工艺流程设计Designing a machining production line requires careful consideration of the technology, equipment, and workflow to ensure efficient production. 机加生产线的设计需要对技术、设备和工作流程进行认真考虑,以确保生产效率。
One of the key elements in designing a machining production line is determining the optimal layout of the equipment and workstations. The layout should be organized in a way that minimizes the distance between workstations, reduces material handling, and maximizes workflow efficiency. 在设计机加生产线时,确定设备和工作站的最佳布局是其中的关键要素之一。
布局应该以使工作站之间的距离最小化、减少物料搬运以及最大化工作流程效率为目标。
In addition to layout design, selecting the appropriate machining equipment is crucial for the success of a production line. The equipment should be capable of meeting the production requirements, while also being reliable, easy to operate, and maintain. 除了布局设计,选择适当的机加设备对于生产线的成功至关重要。
机加车间平面布置图说明

机械加工车间整理方案说明注:车间布局详情见图纸1.机械加工车间公用工具箱:按人数分配工具箱个数,每人一个带锁的工具箱(钥匙给对应的负责人员),对应箱子上面贴有负责人姓名。
相应负责人上班前到公用工具箱领取所需工具,下班之后按时归还上班使用的工具。
若工具损坏或不能使用可以到仓库以旧换新,若是由于其他原因丢失工具的,由该负责人自己承担。
2.加工零件便利箱:置于每台机床旁边,按照加工工序把零件分别放置于货架的上中下三层上,方便生产。
3.工具架:分类放置个机床加工时所需要的工具或者其他加工工具。
把经常用的工具放置在工具架上层,不经常使用的工具放在下层。
方便师傅随手使用。
在工具架边上醒目位置做上标签,方便急用时查找。
4.托盘:托盘分为成品托盘和待加工品托盘,分别用于放置加工成品和待加工零件。
如果成品需要使用则可随时使用,若是零件一时半会不用,就将不用的零件登记入库,不要占用空间。
5.机床:使用频繁的机床要定期检查、维修、保养(一般一个星期为一个周期)。
不经常使用的机床,应在使用完毕之后对其进行护养,以便下次使用。
6.车间卫生:按机床操作人员把厂房区域划分成块,给每个人员说清楚、讲明白,负责好自己负责区域的卫生。
每天下班前要对自己负责的区域进行清理干净,垃圾可以是车间操作人员轮流换班倒垃圾。
7.加工废品区:应该按照不锈钢、碳钢做好相应的垃圾分类,便于垃圾的处理。
8.砂轮机:由于磨刀会产生铁沫,掺杂灰尘在一起比较脏,应该每次磨完刀具后先扫后拖,以防灰尘扩散到常去其他区域,造成今后的清理难题。
9.由于车床车削量比较大,应该及时清理车削铁屑,不能将垃圾累计到一定量后才处理。
车间布局图 布线 版
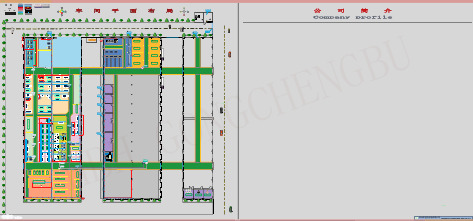
408防锈包装区
Y3180
Y3180
检测室
C
磨棱机 倒角机
HBH 倒角 4 齿轮待剃齿放置区
4232剃齿 机
4232剃齿 机
剃齿
5
4332剃齿 机
4332剃齿 机
5.7米
检验包装
C
6
齿 轮 待 检 放 置 区
齿 轮 检 测 工 作
成形磨齿机
C s
台
C D
成品库
7 10
207防锈包装区
齿 轮 防 锈 包 装 区
主电柜
8号:六角冷拔管
1号车间
公司大 门
GON试用限制 GCHENGBU
食堂
男更衣间
女更衣间
试用限制
Company name/Author
常州华宝恒齿轮有限公司 CHANGZHOU HUABAOHENG GEAR CO.,LTD
兰溪数控车 6986粗车
兰溪数控车 6986粗车
3
D
粗车 AB
2
粗车 AB
D C
圆管割料
4号:冷拔圆管
原材料
1
3.3米
九源数控车 6986精 A
沈阳数控车 6986精 B
九源数控车 6986精 A
沈阳数控车 6986精 B
九源数控车 6986精 A
北道数控车 6986精 B
精车 AB
4
宝鸡数 控车 6207精 B
兰溪数控车 986铆压 D
带 轮 待 滚 齿 产 品 放 置 区
滚齿
5
兰溪数控车 986去毛刺
打 毛 刺 工 作 台
油压机 986挡边
预装
去除毛刺
6
生产线布局培训

生产线布局培训1. 引言生产线布局是在制造业中非常重要的一项工作。
优化和改进生产线布局可以提高生产效率、降低成本、减少浪费,并增强企业的竞争力。
因此,为了帮助员工掌握生产线布局的基本原理和方法,本文档将对生产线布局进行详细阐述,并提供一些实用的培训建议。
2. 生产线布局的意义生产线布局是将一个工厂或车间的机器、设备、人员和原材料等资源合理地组织起来,形成一个高效、流畅的生产流程。
合理的生产线布局能够最大程度地减少物料的搬运、等待和运输时间,从而提高产品生产的速度和质量。
生产线布局的意义主要包括以下几个方面:2.1 提高生产效率通过合理的生产线布局,可以最大限度地减少工人和设备之间的移动距离和时间,降低产品制造过程中的等待时间,从而提高生产效率。
2.2 降低生产成本通过合理的生产线布局,可以减少生产线上的不必要的物料运输、搬运和等待时间,有效降低生产成本。
2.3 提高产品质量通过合理的生产线布局可以减少生产过程中的不必要的停滞时间,降低因生产线拥堵造成的产品品质问题。
3. 生产线布局的原则在进行生产线布局时,有几个基本原则需要遵守:3.1 流程优化原则生产线布局应按照产品的制造流程进行优化。
即使不同产品制造过程中的工序不同,但是在设计生产线布局时应考虑产品制造过程中的主要流程,减少物料的移动和等待时间。
3.2 地面利用率原则生产线布局应尽可能合理地利用地面空间。
合理规划设备和工作站的位置,最大限度地利用生产区域的空间,并确保工人和设备之间的活动空间充足。
3.3 柔性生产原则生产线布局应具备一定的柔性,能够适应不同产品和生产需求的变化。
合理规划物料存储区域和工作站之间的距离,以便快速调整生产线布局以满足不同的生产要求。
3.4 安全和环保原则生产线布局应具备良好的安全性和环保性。
设备和工作站之间应有足够的安全间距,避免事故发生。
此外,应注意合理配置物料存储区域和废料处理区域,确保对环境的保护。
4. 生产线布局的步骤进行生产线布局时,可以按照以下几个步骤进行:4.1 收集信息首先,需要收集相关的生产数据和信息,包括产品制造流程、生产需求、产品特性和质量要求等。
机加工生产车间计划步骤和注意事项

机加工生产车间计划步骤和注意事项《机加工生产车间的那些事儿》嘿,咱今儿就来说说机加工生产车间计划步骤和注意事项这些个事儿。
这就好比咱过日子,也得有个规划不是?首先啊,你得有个明确的目标,咱不能瞎干对吧。
就像咱要盖房子,得先知道盖个啥样的,这就是计划的第一步。
想好咱要生产啥玩意儿,要达到啥标准,有个谱心里才不慌嘛。
然后呢,就得把这目标细细拆分喽。
这就跟切西瓜一样,把大目标切成小块块,每一块都有具体的任务,谁负责啥都得安排得明明白白的。
就像张三负责车这个零件,李四负责铣那个部件,大家分工合作,干活不累嘛。
接着,材料得准备好啊,巧妇难为无米之炊嘛。
可别小看这一步,要是料没备齐,到时候工人干得正起劲儿呢,没材料了,那不是抓瞎嘛。
所以啊,要像给自己准备好吃的一样,把材料都准备得足足的。
说到这工人啊,那可得找靠谱的。
别找那种迷迷糊糊的,不然一不留神给你整个次品出来,那损失可就大咯。
招人的时候就得瞪大眼,找那些手艺好、又细心的。
在车间里还得注意安全哦,那可不是闹着玩的。
这就跟过马路一样,得小心来往的车。
各种机器设备都得小心伺候着,该戴手套戴手套,该戴护目镜戴护目镜。
安全第一,可不能拿生命开玩笑啊。
还有啊,质量检查可得重视起来。
可不能生产一堆次品出来。
咱得像检查自己出门穿的衣服一样,仔细看看有没有线头啥的,可不能有瑕疵。
质量好了,咱的口碑才能立起来,客户才会越来越多嘛。
另外,环境也得搞好。
不能车间脏兮兮、乱糟糟的。
咱自己家都还得打扫干净呢,这车间也得弄得整洁点,大家在里面干活也舒心不是。
总之啊,机加工生产车间的计划和注意事项可不少,但只要咱一步一个脚印,把这些事儿都做好,那咱的车间肯定能顺顺利利地生产出高质量的产品。
咱就等着数钱吧,哈哈!大家都提起精神来,加油干吧!。
6.6 车间布局与机加生产线
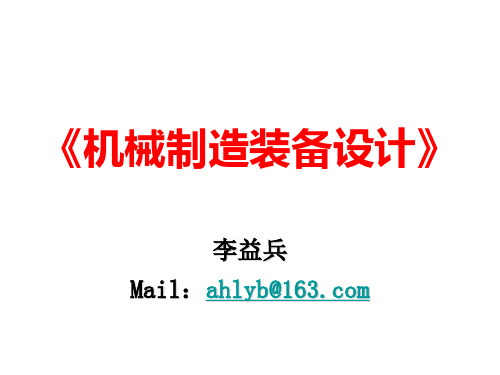
图示是具有三个平行加工位的生产线的布局型式,可以在一条生 产线上实现几个较大工件的同时加工。 这种布局可使每道工序都有三个工件在三个工位上进行加工,而 每个工件则都只在两个工位上由两台机床完成加工。工件输送带 经过五次移动(每次移动工)后送出三个加工完毕的工件。
•
在受到车间面积或排 屑要求的限制时,或 由于有立式机床而不 能采用水平返回、正 上方返回、正下方返 回等方案时,可考虑 采用随行夹具沿生产 线斜上方或斜下方返 回的布局型式。
用架空机械手输送工件时生产线的布局
由架空机械手在机床之间同时进行输送和装卸工件,使采用卧式四面机床 和设置中间导向等成为可能,结构较为复杂,生产线的敞开性变差,不便 于维护保养。 适用于外形复杂、尺寸庞大,且无合适的输送基面工的件(如曲轴)。
内容一:车间布局
常见典型车间布局介绍
U字型制造流程 生产线作异向平行排列,成U字型。
内容一:车间布局
常见典型车间布局介绍
S或Z型制造流程 生产线作迂回布置成S型或Z型,旨在
适应定型而又有限的厂房空间。
内容一:车间布局
常见典型车间布局介绍
奇角型制造流程
制造流程没有一定形式,以缩短物料搬运距离,利于从事 数种工作,适用于小零件的生产或用人不多的制造业。
按加工装备的联接方式分类
柔性联接的生产线 根据需要可在两台或多 台机床之间设置储料装置 (见图1—84c、d) 。在储料
装置中储存有一定数量的被 加工工件,当某一台机床因 故障停机时,其余的机床可 在一定时间内继续工作;或 当前后两台机床的节拍相差 较大时,储料装置可以在一 定时间内起着调剂平衡作用。
工件直接输送时生产线的布局
a为只在两组输送带的一侧配 置动力头的框型生产线,采 用这种布局时,工件在前进 和返回的过程中分别完成两 个侧面上的有关工序的加工。 b为在两组输送带的两侧都配 置动力头的框型生产线,这 种布局虽然缩短了生产线的 长度,但其宽度则大大增加 了。当既要完成工件两侧面 上的有关工序,又要在其顶 面上进行加工时,可在框型 生产线的中央设置装有立式 动力头的中央立柱。
机加生产线的工艺流程
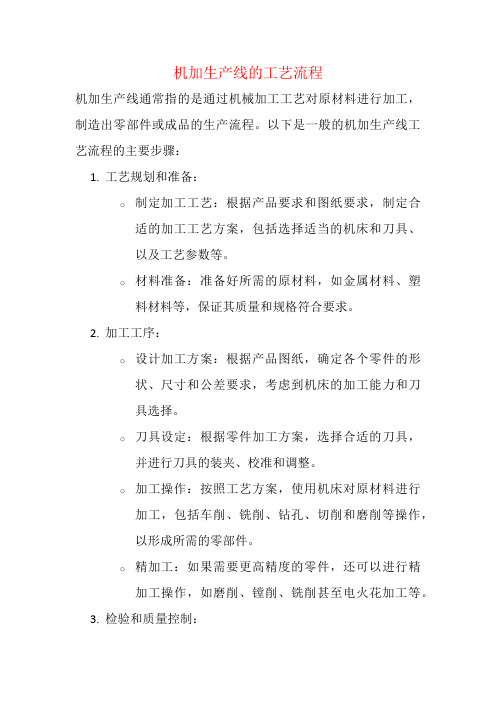
机加生产线的工艺流程机加生产线通常指的是通过机械加工工艺对原材料进行加工,制造出零部件或成品的生产流程。
以下是一般的机加生产线工艺流程的主要步骤:1.工艺规划和准备:o制定加工工艺:根据产品要求和图纸要求,制定合适的加工工艺方案,包括选择适当的机床和刀具、以及工艺参数等。
o材料准备:准备好所需的原材料,如金属材料、塑料材料等,保证其质量和规格符合要求。
2.加工工序:o设计加工方案:根据产品图纸,确定各个零件的形状、尺寸和公差要求,考虑到机床的加工能力和刀具选择。
o刀具设定:根据零件加工方案,选择合适的刀具,并进行刀具的装夹、校准和调整。
o加工操作:按照工艺方案,使用机床对原材料进行加工,包括车削、铣削、钻孔、切削和磨削等操作,以形成所需的零部件。
o精加工:如果需要更高精度的零件,还可以进行精加工操作,如磨削、镗削、铣削甚至电火花加工等。
3.检验和质量控制:o在加工过程中,根据质量控制要求,对零部件进行检验和测量,以确保其尺寸、形状和表面质量的符合要求。
o根据检验结果,对加工工序进行必要的调整和纠正,以提高产品的质量稳定性。
4.组装和包装:o对加工好的零部件进行组装,根据产品要求,进行装配、焊接、螺栓连接、粘接等工序,最终形成成品产品。
o对成品进行必要的清洁、调试和包装,以确保产品的完整性和外观。
5.质量检测和测试:o进行最终产品的全面检测和测试,以验证其质量和性能是否符合要求。
以上是一般机加生产线的工艺流程,具体的工艺流程会根据不同的产品和加工要求而有所不同。
在实际生产中,需要根据产品要求和生产设备的能力,进行详细的工艺规划和流程控制,以确保产品的质量和生产效率。
机加车间作业流程

冲压车间作业流程
编 号:Yatin/ QI -13-01 版 本 号:A 修改次数:0 受控状态: 分 发 号:
实施日期: 2009年 10月5日
批 准 日 期
审 核 日 期
编 制 日 期
雅鼎卫浴股份有限公司
为有效的控制生产过程,以保证产品质量和交期满足顾客的期望和要求。
2、适用范围
适用于机加车间产品生产过程的控制管理。
3、定义
机加车间生产过程中各工序的操作规程。
4、职责和权限
4.1计划部门负责对机加车间的生产计划,入库计划进行编制和审核;
4.2机加车间负责按照生产计划组织进行加工生产;负责生产过程中设备的管理和维护;负责生
产前物料准备以及人员组织;负责监督生产过程的现场管理等;
4.3品管部门负责监视和测量装置的控制管理;负责组织人员进行产品的检验;及对特殊及关键
过程进行监控等。
6、附件
无
7、相关支持性文件
《生产过程控制程序》
《设备控制程序》
《制程检验管理规定》
8、相关记录
《生产任务单》
《转序单》
《冲压首检巡检记录》
《半成品检验记录》
《报废、次品、不良品处理单》。
机加生产线设计流程
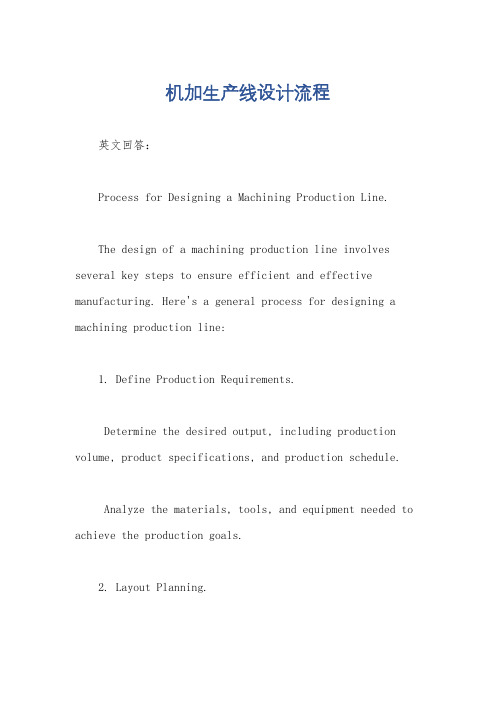
机加生产线设计流程英文回答:Process for Designing a Machining Production Line.The design of a machining production line involves several key steps to ensure efficient and effective manufacturing. Here's a general process for designing a machining production line:1. Define Production Requirements.Determine the desired output, including production volume, product specifications, and production schedule.Analyze the materials, tools, and equipment needed to achieve the production goals.2. Layout Planning.Design the physical layout of the production line, considering factors such as workflow, equipment placement, and material flow.Optimize the line layout for efficient movement of materials, operators, and finished products.3. Equipment Selection.Select the appropriate machining equipment based on production requirements, workpiece size, and material properties.Consider factors such as machine capabilities, accuracy, speed, and automation levels.4. Tooling and Fixturing.Design and implement tooling and fixturing to secure and guide workpieces during machining.Optimize tooling for efficient cutting, reduced cycletimes, and improved product quality.5. Process Planning.Develop detailed process plans for each machining operation, including cutting parameters, tool paths, and cycle times.Optimize process parameters for efficiency, accuracy, and surface finish.6. Automation and Integration.Explore automation options to improve productivity, reduce labor costs, and enhance safety.Integrate automation systems, such as conveyors, robots, or CNC controllers, into the production line.7. Quality Control.Establish quality control measures to ensure productquality and consistency.Implement inspection and testing procedures to monitor production output and identify any deviations.8. Maintenance and Operations Management.Develop a maintenance and operations management plan to ensure efficient operation of the production line.Establish schedules for regular maintenance, equipment calibration, and operator training.9. Continuous Improvement.Continuously monitor and evaluate the production line to identify areas for improvement.Implement lean manufacturing principles and process optimization techniques to enhance efficiency and reduce costs.中文回答:机加生产线设计流程。
工厂车间现场布局图操作方法

工厂车间现场布局图操作方法
操作方法如下:
1. 首先,您需要确定车间的尺寸和形状,并确保您有足够的平面图或图纸来进行布局设计。
2. 在平面图上标出现有的固定设备,如机器、设备、货架等,并确定它们的位置。
3. 确定流线布局,即确定原材料的输入、加工工序和成品的输出流程。
根据产品生产流程的要求,将与生产流程相关的设备和工作区域放置在相应的位置上。
4. 确定人员工作区域,根据工序和工作内容,确定员工的工作站和工作区域。
确保员工的工位布局合理且符合人体工程学原理。
5. 设计通道和空间布局,以保证工人和设备之间的安全通行和操作空间。
确保通道宽度足够,不会妨碍设备和人员的正常操作。
6. 对于需要存储物料和成品的货架和仓库区域,根据库存量和出入库流程设计相应的存储空间和路线。
7. 考虑工厂的环境因素,如通风、照明和安全设备等,并确保布局设计符合相
关安全标准和法规。
8. 可以使用专业的绘图软件或在线工具进行布局设计,以便更好地规划和调整布局。
9. 在进行最终布局前,最好进行实地考察和讨论,以便根据实际情况进行相应的调整和优化。
10. 最后,根据布局设计图,按照图纸上的位置指引进行设备和工位摆放,并确保设备的正常运转和员工的安全操作。
机械加工生产线的总体布局设计
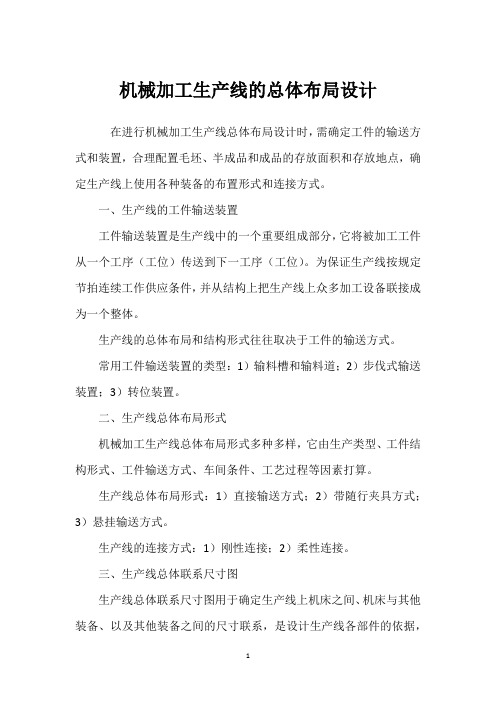
机械加工生产线的总体布局设计
在进行机械加工生产线总体布局设计时,需确定工件的输送方式和装置,合理配置毛坯、半成品和成品的存放面积和存放地点,确定生产线上使用各种装备的布置形式和连接方式。
一、生产线的工件输送装置
工件输送装置是生产线中的一个重要组成部分,它将被加工工件从一个工序(工位)传送到下一工序(工位)。
为保证生产线按规定节拍连续工作供应条件,并从结构上把生产线上众多加工设备联接成为一个整体。
生产线的总体布局和结构形式往往取决于工件的输送方式。
常用工件输送装置的类型:1)输料槽和输料道;2)步伐式输送装置;3)转位装置。
二、生产线总体布局形式
机械加工生产线总体布局形式多种多样,它由生产类型、工件结构形式、工件输送方式、车间条件、工艺过程等因素打算。
生产线总体布局形式:1)直接输送方式;2)带随行夹具方式;3)悬挂输送方式。
生产线的连接方式:1)刚性连接;2)柔性连接。
三、生产线总体联系尺寸图
生产线总体联系尺寸图用于确定生产线上机床之间、机床与其他装备、以及其他装备之间的尺寸联系,是设计生产线各部件的依据,
也是检查各部件相互关系的重要资料。
当选用的机床和其他装备的形式和数量确定之后,依据拟定的布局就可绘制生产线总体联系尺寸图。
四、机械加工生产线其他装备的选择与配置
1)输送带驱动装置的布置;2)小螺纹孔加工检查装置;3)精加工工序的自动测量装置;4)装卸工位掌握机构;5)毛坯检查装置;6)液压站、电气柜及管路布置;7)桥梯、操纵台和工具台的布置;8)清洗设备布置。
机械加工生产线总体布局设计

5.4 机械加工生产线总体布局设计
• 一、托盘及托盘交换器
• ——应用托盘交换器可以大幅度缩减装卸工件的辅助时间。
• 1.托盘
• 托盘是用来固定夹具的,结构形状类似于加工中心的工作台
• →相当于机床与工件间的硬件接口。用于柔性生产线中。
• 在同一个FMS系统中,托盘应统一结构和尺寸。
• 2.托盘交换器
通用悬挂系统的滑架小车 1 轨道 2 滑架小车 3 牵引链 4 挂吊具
20
5.4 机械加工生产线总体布局设计
•悬挂传送机——可在运行过程中通过架空线路的升降实现自动
•
上、下料作业。图6-56自动上料的悬挂输送机:
21
5.4 机械加工生产线总体布局设计 积放式悬挂输送线
22
5.4 机械加工生产线总体布局设计 •喷漆生产线应用的悬挂传送机——上、下料作业由人工完成 •
• 摆杆上设有刚性 • 棘爪和限位挡块。 • • 输送摆杆有前进、 • 往复摆动、后退 • 三种动作。
特点: ①有限位挡块,传送终止位置准确; ②传送速度较高→速度20m/min。
27
5.4 机械加工生产线总体布局设计
•工作原理: •①摆杆摆动一定角度,使刚 性棘爪和限位挡块转到工件 的前后方位置(A-A图中实 线位置); •②输送摆杆在驱动液压缸5 的推动下前行一个步距,完 成输送;
5.4 机械加工生产线总体布局设计
• 1.特点 • ①柔性好:可以较方便地修改和扩充小车的移动路线; • ②可实现实时监控:利用小车与控制计算机之间的双向通讯功
能,实现对小车运行状态的实时监控; • ③安全可靠; • ④定位精度高:有定位传感器,精确定位的AGV可达±3mm; • ⑤维护方便。
机加生产线工艺流程步骤

机加生产线工艺流程步骤英文回答:The process steps in a machining production line can vary depending on the specific product being manufactured. However, there are some common steps that are typically followed in most machine shops. These steps include:1. Receiving and inspection of raw materials: When raw materials are delivered to the production line, they are first inspected to ensure that they meet the required specifications. This may involve checking for dimensions, material composition, and other quality requirements.2. Material preparation: Once the raw materials are deemed acceptable, they are prepared for machining. This may involve cutting, shaping, or any other necessary processes to achieve the desired form.3. Machining: This is the main step in the productionline where the actual machining operations are carried out. This can include processes such as milling, drilling, turning, grinding, and others, depending on the requirements of the product.4. Quality control: Throughout the machining process, quality control measures are implemented to ensure that the finished product meets the required standards. This may involve using gauges, measuring tools, and other inspection techniques to check for dimensional accuracy, surface finish, and other quality parameters.5. Assembly and finishing: Once the machining operations are completed, the machined components are assembled together if required. This may involve using fasteners, adhesives, or other joining methods. Additionally, any necessary finishing processes such as polishing, painting, or coating may be performed at this stage.6. Final inspection and testing: Before the finished product is released, a final inspection and testing areconducted to ensure that it meets all the required specifications and performance criteria. This may involve functional testing, durability testing, or any other relevant tests.7. Packaging and shipping: Once the product has passed all the necessary inspections and tests, it is packaged and prepared for shipping to the customer. This may involve using suitable packaging materials to protect the product during transportation.8. Documentation and record-keeping: Throughout the entire process, documentation and record-keeping are important to track the progress, quality, and other relevant information. This helps in maintainingtraceability and ensuring compliance with regulations and customer requirements.中文回答:机加生产线的工艺流程步骤可以根据所制造的具体产品而有所不同。
- 1、下载文档前请自行甄别文档内容的完整性,平台不提供额外的编辑、内容补充、找答案等附加服务。
- 2、"仅部分预览"的文档,不可在线预览部分如存在完整性等问题,可反馈申请退款(可完整预览的文档不适用该条件!)。
- 3、如文档侵犯您的权益,请联系客服反馈,我们会尽快为您处理(人工客服工作时间:9:00-18:30)。
品,但建立这种生产线投资大,技术要求高。
按加工装备的联接方式分类
刚性联接的生产线 由于各工位之间没有缓 冲环节(即中间储料装置见 图1—84a、b )工件的加工
和运送过程有严格的节拍要 求,线上一台机床发生故障 就会引起全线停止工作,因 而,这种生产线中的机床和 各种辅助装置应有较高的稳 定性和可靠性。
工件直接输送时生产线的布局
(3) 旁通式 优点是可以配置三面或立卧复合的四面加工机床,以提 高工序集中的程度,减少机床的台数,但由于多出了横向输 送装置,增加了占地面积,延长了生产线的节拍时间。
工件装在随行夹具上输送时生产线的布局
(1) 在水平面内返回 这种布局型式就是将主输送带和返回输送带在水平 面内组成封闭的框型。主要缺点是占地面积较大。
内容一:车间布局
常见典型车间布局介绍
U字型制造流程 生产线作异向平行排列,成U字型。
内容一:车间布局
常见典型车间布局介绍
S或Z型制造流程 生产线作迂回布置成S型或Z型,旨在
适应定型而又有限的厂房空间。
内容一:车间布局
常见典型车间布局介绍
奇角型制造流程
制造流程没有一定形式,以缩短物料搬运距离,利于从事 数种工作,适用于小零件的生产或用人不多的制造业。
工件直接输送时生产线的布局
(1) 直通式 型式简洁、工件输送方便,占地面积少。输送带将工件 从生产线的起始端依次运送到各台机床的夹具上,进行不同 工序的加工,最后从生产线的末端送出。
工件直接输送时生产线的布局
(2) 折线式 如果工件的加工工序较多致使生产线很长,采用 直线布局型式将受到车间长度的限制,这时可以采用按 折线布局的方案。折线布局的生产线又可以分为“L型”、 “II型”和“框型”。
内容一:车间布局
工艺流程法
产品布局法
混合布局法
相关分析法
内容一:车间布局
工艺 流程法
例:将
车床
将同一制造过程中制品所经过
的部门中的所用的机器或同类
的机器布置在一起。
排在一
起加 工称为 车工车间。
内容一:车间布局
5
内容一:车间布局
产品 布局法
适会于所从 事制 造工作本 身具 有重复性、 连 续性的生 产工 厂。
相关 分析法
根据工厂个部门之间的相关性及其 大小进行部门的布局,这种布局方法符 合上述原则,宜于实现工厂布局的目标, 因此为现代企业在进行工厂设计时广泛 采用。
内容一:车间布局
常见典型车间布局介绍
依照制造过程的顺序,将生产线做 直线的安排,通常最有利于运用输 送带搬运物料与在制品。
直线型制造流程
•
在受到车间面积或排 屑要求的限制时,或 由于有立式机床而不 能采用水平返回、正 上方返回、正下方返 回等方案时,可考虑 采用随行夹具沿生产 线斜上局
由架空机械手在机床之间同时进行输送和装卸工件,使采用卧式四面机床 和设置中间导向等成为可能,结构较为复杂,生产线的敞开性变差,不便 于维护保养。 适用于外形复杂、尺寸庞大,且无合适的输送基面工的件(如曲轴)。
工件装在随行夹具上输送时生产线的布局
(2) 沿生产线的正上方返回 可以减少占地面积,而且还可以采用倾斜滚道使随 行夹具依靠自重滑返,从而大大简化随行夹具的返回系 统。
•
当生产线上有立 式机床时一般不 宜采用这种布局 型式,否则会使 倾斜滚道太高而 不便于维护保养。
工件装在随行夹具上输送时生产线的布局
《机械制造装备设计》
李益兵
Mail:ahlyb@
内容一:车间布局
车间布局概述
车间布局即是将工厂内的所有设备、工具、原料、工 作台、附属设施(如工具室、更衣室、厕所、升降机等) 和各种作业(如仓储、品检、搬运等),依生产流程, 作一番适当的安排与布置,使工厂的生产活动能顺利而 流畅。 采用科学的方法合理的进行车间平面布局可以使得人 流和物流有序的流动,缩短路径、避免人流与物流的交 叉和折返,减少搬运时间,提高工作效率。
(3) 沿生产线的正下方返回 既可减少占地面积、使外观整齐,又能使全线敞开 而便于调整维护,适用于车间的使用面积受限制、工件 和随行夹具又较小的场合。
工件装在随行夹具上输送时生产线的布局
(4) 沿斜上方或斜下方返回 主要适用于尺寸较大的工件和随行夹具。采用随行 夹具沿斜下方返回的方案时,返回通道设置在卧式机床 的尾部,这种布局适用于尺寸较小的工件和随行夹具。
图示是具有三个平行加工位的生产线的布局型式,可以在一条生 产线上实现几个较大工件的同时加工。 这种布局可使每道工序都有三个工件在三个工位上进行加工,而 每个工件则都只在两个工位上由两台机床完成加工。工件输送带 经过五次移动(每次移动工)后送出三个加工完毕的工件。
按工件的输送方式分类
• (1) 直接输送的生产线 线上工件由输送装置直接带动,输送基面为工件上的某一 表面。加工时工件从生产线的始端送入,完成加工后从生产线 的末端输出。
按工件的输送方式分类
• (2) 带随行夹具的生产线 将工件安装在随行夹具上,由主输送带将随行夹具依次 输送到各个工位,完成工件的加工。加工完毕后,随行夹具由 返回输送带将其送回到主输送带的起始端。
按加工装备的联接方式分类
柔性联接的生产线 根据需要可在两台或多 台机床之间设置储料装置 (见图1—84c、d) 。在储料
装置中储存有一定数量的被 加工工件,当某一台机床因 故障停机时,其余的机床可 在一定时间内继续工作;或 当前后两台机床的节拍相差 较大时,储料装置可以在一 定时间内起着调剂平衡作用。
从至表
记录车间内各设备间
物料运输情况的矩阵式图 表,应用广泛。
内容二:机加生产线
定义:为实现工件的机械加工工艺过程,以机床为主要装备, 再配以相应的输送和辅助装置,按工件的加工顺序排列而成的 生产作业线。 在生产线中,工件以一定的生产节拍,按照工艺顺序经过各个 工位,完成其预定的工艺过程,从而成为合乎设计要求的零件。
按生产品种分类
• 2)成组产品可调生产线 由按成组技术设计制造的可调的专用加工装备等组成。 按成组工艺流程布局,具有较高的生产效率和自动化 程度,用于结构和工艺相似的成组产品的生产。 适用于批量生产,当产品更新时,生产线可进行改造
或重组以适应产品的变化。
按组成生产线的加工装备分类
• (1) 通用机床生产线 由通用机床经过一定的自动化改装后联接而成。 • (2) 组合机床生产线 由各种组合机床联接而成。它的设计、制造周期短,工 作可靠,这类生产线有较好的使用效果和经济效益,在大批
依产品的种类将生产设备按制 造过程的先后秩序排成生产线,自 材料、零件的投人至产品的产出, 经过一连串的步骤,将产品制造出 来 。
内容一:车间布局
混合 布局法
在重复性很高的标准品工厂里,有时 可以将特别昂贵的机器集中在一起充分 加以利用,而有时可将易于发生震动或 噪音的机器集中,以防止震动和噪音。
工件多次通过的生产线的布局
图示是发动机缸体的 工件两次通过生产线 的布局型式,工件经 过生产线的第一次加 工后转180。再次进 入生产线,对换其两 侧表面的加工内容。 适用于加工一些产量 不大、工序很多的箱 体类零件。 可缩短生产线的长度, 减少资金投入,提高 生产线的利用率。
设置平行加工工位的生产线的布局
大量生产中得到广泛应用。
按组成生产线的加工装备分类
• (3) 柔性制造生产线 由高度自动化的多功能柔性加工设备(如数控机床、加工 中心等)、物料输送系统和计算机控制系统等组成。 生产线的设备数量较少,在每台加工设备上,通过回转 工作台和自动换刀装置,能完成工件多方位、多面、多工序
的加工,以减少工件的安装次数,减少安装定位误差。主要
按生产品种分类
• 1)单一产品生产线 由具有一定自动化程度的高效专用加工装备、工艺装 置、输送装备和辅助装备等组成。 按产品的工艺流程布局,工件沿固定的生产路线从一 台设备输送到下一台设备,接受加工、检验、清洗等。 生产效率高,产品质量稳定,适用于大批大量生产。 但其专用性强,投资大,不易进行改造以适应其它产品的 生产。
工件直接输送时生产线的布局
a为只在两组输送带的一侧配 置动力头的框型生产线,采 用这种布局时,工件在前进 和返回的过程中分别完成两 个侧面上的有关工序的加工。 b为在两组输送带的两侧都配 置动力头的框型生产线,这 种布局虽然缩短了生产线的 长度,但其宽度则大大增加 了。当既要完成工件两侧面 上的有关工序,又要在其顶 面上进行加工时,可在框型 生产线的中央设置装有立式 动力头的中央立柱。